OEE表格
202009设备综合效率(OEE)

0
其它
min
0
故障停机 min
0
换型停机 min
0
非计
划停 首件确认 min
0
机时 待料停机 min
0
间
品质异常 min
0
其它
min
0
负荷时间
min
0
开动时间
min
0
时间开动率
%
理论加工周期
min/ 件
实际加工周期
min/ 件
实际加工时间 min
速度开动率
%
净开动率
%
性能开动率
%
生产总数
件
0
不良品数
14
15
16
17
18
19
20
21
22
23
24
25
26
27
28
29
30
合计
设备综合效率(OEE)统计表
设备名称
设备编号
生产线别
国六生产线
月份
2020 2020 年
9
月
日期
1
2
3
4
5
6
7
8
9
10
11
12
13
14
15
16
17
18
19
20
21
22
23
24
25
26
27
28
29
30
合计
工作时间
h
0
保养停机 min
0
计划 调模停机 min
0
停机 工间休息 min
0
时间
停产停机 min
设备综合效率OEE统计表
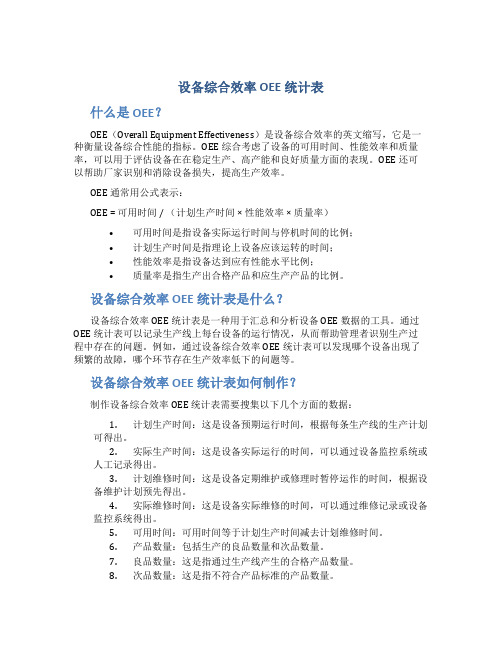
设备综合效率 OEE 统计表什么是 OEE?OEE(Overall Equipment Effectiveness)是设备综合效率的英文缩写,它是一种衡量设备综合性能的指标。
OEE 综合考虑了设备的可用时间、性能效率和质量率,可以用于评估设备在在稳定生产、高产能和良好质量方面的表现。
OEE 还可以帮助厂家识别和消除设备损失,提高生产效率。
OEE 通常用公式表示:OEE = 可用时间 / (计划生产时间 × 性能效率 × 质量率)•可用时间是指设备实际运行时间与停机时间的比例;•计划生产时间是指理论上设备应该运转的时间;•性能效率是指设备达到应有性能水平比例;•质量率是指生产出合格产品和应生产产品的比例。
设备综合效率 OEE 统计表是什么?设备综合效率 OEE 统计表是一种用于汇总和分析设备 OEE 数据的工具。
通过OEE 统计表可以记录生产线上每台设备的运行情况,从而帮助管理者识别生产过程中存在的问题。
例如,通过设备综合效率 OEE 统计表可以发现哪个设备出现了频繁的故障,哪个环节存在生产效率低下的问题等。
设备综合效率 OEE 统计表如何制作?制作设备综合效率 OEE 统计表需要搜集以下几个方面的数据:1.计划生产时间:这是设备预期运行时间,根据每条生产线的生产计划可得出。
2.实际生产时间:这是设备实际运行的时间,可以通过设备监控系统或人工记录得出。
3.计划维修时间:这是设备定期维护或修理时暂停运作的时间,根据设备维护计划预先得出。
4.实际维修时间:这是设备实际维修的时间,可以通过维修记录或设备监控系统得出。
5.可用时间:可用时间等于计划生产时间减去计划维修时间。
6.产品数量:包括生产的良品数量和次品数量。
7.良品数量:这是指通过生产线产生的合格产品数量。
8.次品数量:这是指不符合产品标准的产品数量。
9.损失时间:包括故障时间、换线时间、停机时间等。
在收集完以上数据后,可以按以下步骤制作设备综合效率 OEE 统计表:1.在电子表格软件(如 Excel)中新建一个表格,用于记录各设备的OEE 数据。
车间OEE报表

14 3月14日 14 4000 2
32 56
13 6.58 692 100.0% 89% 87.8% 77.9% 0.0%
15 3月15日 12 4000 7
44 30
汇总
177 56174 708 R=d/[
M=X*60-
备注: (Nd=+Me+/[fX+*g6
XO*=610--
b/a
0-
1613
6 3月6日 10 3465 56
44 30
12
13 4.70 694 98.4% 89% 106.2% 93.0% 0.0%
7 3月7日 9 2345 67
4 454
13 4.23 322 97.1% 41% 172.2% 69.0% 0.0%
8 3月8日 12 3452 2
44 30
342
13 5.64 364 99.9% 83% 168.1% 139.7% 0.0%
合格 率%
设备故
时间效 性能效 OEE 障停机
率% 率% 率
1 3月1日 14 4500 33
3 58
13 6.58 719 99.3% 92% 95.1% 87.0% 0.0%
2 3月2日 9 3000 56Fra bibliotek44 30
13 4.23 706 98.1% 91% 100.5% 89.2% 0.0%
3 3月3日 12 3467 67
时间效率%
88.1%
89.9%
92.0%
89.3%
90.7%
性能效率%
OEE
90.8%
160.0% 140.0% 120.0% 100.0%
1起50始%日期:
OEE表格

1440
100.0%
1440 1440 1440
1440
100.0%
1440 1440 1440
1440
100.0%
1440 1440 1440
1440
100.0%
1440 1440 1440
1440
100.0%
1440 1440 1440
1440
100.0%
1440 1440 1440
1440
100.0%
0
#DIV/0!
0
#DIV/0!
0
#DIV/0!
0
#DIV/0!
0
#DIV/0!
0
#DIV/0!
0
#DIV/0!
0
#DIV/0!
0
#DIV/0!
0
#DIV/0!
0
#DIV/0!
0
#DIV/0!
0
#DIV/0!
0
#DIV/0!
0
#DIV/0!
0
#DIV/0!
0
#DIV/0!
K
OEE设备综合效率 =E*J*G
#DIV/0! #DIV/0! #DIV/0! #DIV/0!
#DIV/0! #DIV/0! #DIV/0! #DIV/0! #DIV/0! #DIV/0! #DIV/0! #DIV/0! #DIV/0! #DIV/0! #DIV/0! #DIV/0! #DIV/0! #DIV/0! #DIV/0! #DIV/0! #DIV/0! #DIV/0! #DIV/0! #DIV/0! #DIV/0! #DIV/0! #DIV/0! #DIV/0! #DIV/0!
1440 1440 1440
OEE怎么算看完这篇文章你就明白了~附OEE计算表格
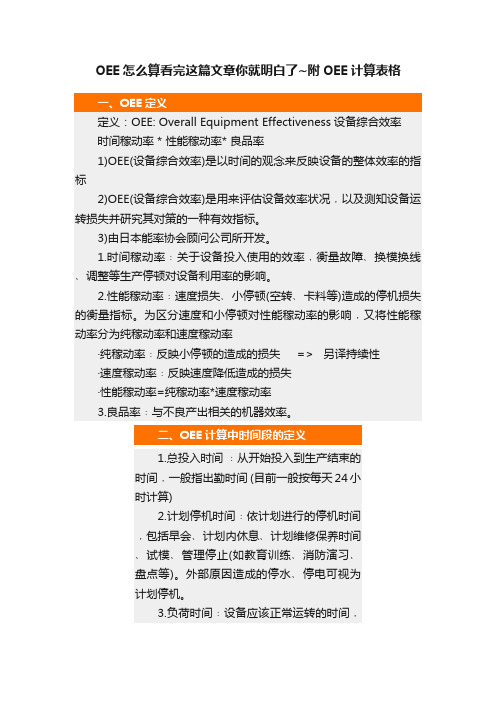
OEE怎么算看完这篇文章你就明白了~附OEE计算表格定义:OEE: Overall Equipment Effectiveness设备综合效率时间稼动率 * 性能稼动率* 良品率1)OEE(设备综合效率)是以时间的观念来反映设备的整体效率的指标2)OEE(设备综合效率)是用来评估设备效率状况﹐以及测知设备运转损失并研究其对策的一种有效指标。
3)由日本能率协会顾问公司所开发。
1.时间稼动率﹕关于设备投入使用的效率﹐衡量故障﹑换模换线﹑调整等生产停顿对设备利用率的影响。
2.性能稼动率﹕速度损失﹑小停顿(空转﹑卡料等)造成的停机损失的衡量指标。
为区分速度和小停顿对性能稼动率的影响﹐又将性能稼动率分为纯稼动率和速度稼动率·纯稼动率﹕反映小停顿的造成的损失 => 另译持续性·速度稼动率﹕反映速度降低造成的损失·性能稼动率=纯稼动率*速度稼动率3.良品率﹕与不良产出相关的机器效率。
1.总投入时间﹕从开始投入到生产结束的时间﹐一般指出勤时间 (目前一般按每天24小时计算)2.计划停机时间﹕依计划进行的停机时间﹐包括早会﹑计划内休息﹑计划维修保养时间﹑试模﹑管理停止(如教育训练﹑消防演习﹑盘点等)。
外部原因造成的停水﹑停电可视为计划停机。
3.负荷时间﹕设备应该正常运转的时间﹐为总投入时间减去计划停机时间 (计算OEE 的分母)4.当机时间﹕指由于设备故障﹑模具故障﹑换模换线﹑暖机﹑换料等造成的生产停止时间。
1)设备故障时间﹕因设备故障造成机器停机的总时间。
包含维修时间和调试时间﹐直至可正常生产2)换线损失时间﹕机器因切换不同产品或为达成产品最终特性而进行调整的总时间﹐包括从前一个产品停止到新产品第一个良品产出所花费所有的时间3)模具故障时间﹕因模具原因造成的停机的总时间4)暖机时间﹕暖机时间是指﹐要开始生产时﹐启动﹑调整运转﹑直至加工条件安定前所需要的时间5.稼动时间﹕设备实际用于生产的时间﹐等于负荷时间减去当机时间6.净稼动时间﹕稼动时间中扣除速度损失﹑小停顿损失后的产出时间。
设备综合效率OEE统计表
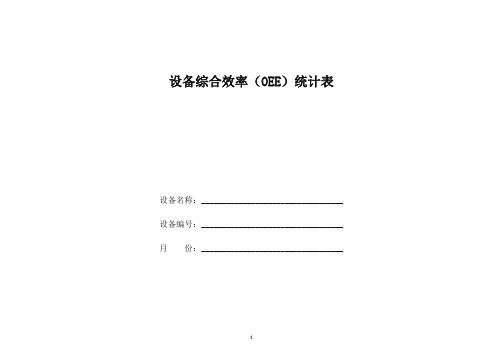
月生产数量 =min
设备理论加工时间 =min
月实际生产时间 =min
月性能开动率 = (生产数量×理论加工时间)/净生产时间 =min
月产品合格率 =min
当月设备综合效率OEE = 月时间开动率×月性能开动率×月合格品率 =min
统计人/日期: 复核人/日期
产品/批次:___________________
数量:_______________________
组长签名:___________________
5
10
15
20
25
30
35
40
45
50
55
60
5
10
15
20
25
30
35
40
45
50
55
60
5
10
15
20
25
30
35
40
45
50
55
60
5
10
15
20
25
30
35
40
45
50
55
60
12:00 13:00 14:00 15:00 16:00
5
10
15
20
25
30
35
40
45
50
55
60
5
10
15
20
25
30
35
40
45
50
55
60
5
10
15
20
25
30
35
40
生产综合效率OEE报表

开机时间 (min)
良品数
不良 数
生产数 量
良品率%
早会 定保 其他
小计
换模
机械 故障
模具 故障
异 常
停 工
0 审核:0 0 0 源自 0 0 0 00文件编号/Dc.No.:DG-PD-Form-14 A/1
时间记录(min)
时间运转率 性能运转率 设备综合效
其 他
小计
(%)
(%)
率(%)
备注
00
核准:
部门: 日期 机台
组别:
模具/ 班次 工单号
生产数据 料号
□ 白班
标准工时
总出勤时间
模穴
标准周 期
开机起 完成生 始时间 产时间
小计
制表: 计算 方 时间 运转 性能 运转 设备 综合 良品 率=良
审核
生产综合效率报表
□ 夜班
总出勤时间
产量记录(PCS)
计划停机时间(Min)
无效停机时间记录(min)
设备综合效率OEE统计表
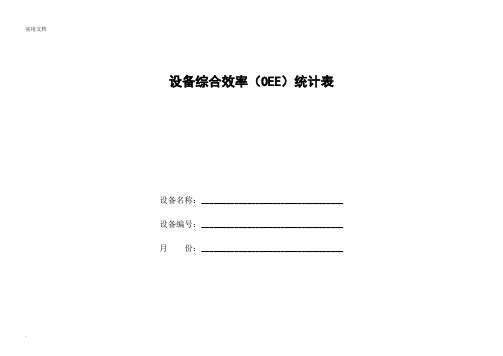
当天班次总时间=min
计划生产时间=当天班次总时间-计划停机时间=当天班次总时间- A - I =min
净生产时间=计划生产时间-非计划停机时间=计划生产时间- B - C - E - F - G -H =min
OEE =时间开动率×性能开动率×合格品率
=【净生产时间/计划生产时间】×【净开动率×速度开动率】×【合格品数量/总产量】
25
30
35
40
45
50
55
60
12:00 13:00 14:00 15:00 16:00
5
10
15
20
25
30
35
40
45
50
55
60
5
10
15
20
25
30
35
40
45
50
55
60
5
10
15
20
25
30
35
40
45
50
55
60
5
10
15
20
25
30
35
40
45
50
55
60
中班
16:00 17:00 18:00 19:00 20:00
25
30
35
40
45
50
55
60
04:00 05:00 06:00 07:00 08:00
5
10
15
20
25
30
35
40
45
50
55
60
5
10
15
20
oee分析表

工序 4(振机,烘干) 71.429% 107.692% 98.810% 76.007%
工序 5(CNC1) 71.429% 106.410% 96.386% 73.260%
工序 7(CNC2) 90 30 1 30
30 120
工序 8(机加工) 5 15 1 15
30 90
工序 7(CNC2) 85.714% 263.333% 94.937% 214.286%
1.333333333 1440 10080 8000
9947.368421 1142.857143 1421.052632
24.34%
工序 2(冲水口) 14 6
1.714285714 1440 8640 8000 7480
1333.333333 1246.666667
-6.50%
工序 3(磨边) 14 6 2
=C - D =A x E =F x G
零件名称 零件编号
工序 1(压铸) 2 10
600
60 540 1080
7 7560
工序 2(冲水口) 2 8
480
60 420 840
6 5040
ECL ECL日期
工序 3(磨边) 2 8
480
60 420 840
6 5040
工序 4(振机,烘干) 2 8
480
1000
900
850
840
830
790
750
0
L.
试产总的合格品数量 (一次直通,不含返工)
900
850
840
830
800
750
730
M.
试产总的不合格品数量
=K - L
oee统计表格

oee统计表格
OEE(Overall Equipment Effectiveness)是一个用于评估设备效率的指标,它可以帮助企业了解设备的性能和潜在的改进空间。
以下是一个简单的OEE统
●日期:评估的日期。
●设备名称:被评估的设备名称。
●运行时间:设备实际运行的时间。
●停机时间:设备因故障、维护等原因停止运行的时间。
●故障次数:设备在评估期间发生的故障次数。
●实际产量:设备在评估期间的实际产出数量。
●理论产量:设备在评估期间的理想产出数量(假设无故障、无停机)。
●OEE:设备的整体设备效率,计算公式为(实际产量/理论产量)*(运
行时间/总时间)*100%。
OEE计算标准表

此行请填写实际现场每 时间记录之和,同时请 将基础记录做好。
ห้องสมุดไป่ตู้
此处填写时,一线多产 和标准工时逐个计算总 计算加权节拍,总生产 良品。
此行为休息时间,不应包含没有排 班的时间,没排班的应算计划停止; 休息时间只是上班期间,中途休息 和吃饭时间。
此行请填写实际现场每天的开停机 时间记录之和,同时请生产部配合 将基础记录做好。
此处填写时,一线多产品的用产量 和标准工时逐个计算总工时,然后 计算加权节拍,总生产数要包含不
OEE和OPE指标计算统计表

月
统计月份:2017年5Fra bibliotek月9日 10日 11日 12日 13日 14日 15日 16日 17日 18日 19日 20日 21日 22日 23日 24日 25日 26日 27日 28日 29日 30日 31日
实际OEE=时间稼动率×性能稼动率×良品率 OEE指标要求
注明:1、 基准周期时间:设备(生产线)原设计产出单位产量所需的时间(C/T)。实际周期时间:目前设备(生产线)实际产出单位产量所需的时间;
OEE指标计算表:
线别:发泡1#线
编号 1 2 3 4 5 6 7 8 9 10 11 12 13 14 15 16 17 18 19 20 21 22 23 24 25 26 27 28 29 30 31 良品率 性能稼 动率 速度稼 动率A 异常停 机时间 时间稼 动率 各项指标计算/日期 计划点检保养时间(H) 休息时间(H) 计划停 计划停产时间(H) 机时间 员工培训时间(H) 会议时间(H) 设备计划检修时间(H) 计划停机合计时间M(H) 设备应开动时间N(H) 设备负荷时间K=N-M(H) 设备故障时间(H) 品质异常停机时间(H) 来料异常停机时间(H) 夹具异常停机(H) 换型、换线时间(H) 员工请假影响时间(H) 其他突发事故时间(H) 异常停机时间合计S(H) 时间稼动率=(K-S)/K×100% 设备异常降速运行影响时 间O(H) 短暂停影响时间P(H) 基准周期时间T1 实际周期时间T2=T1-O-P 速度稼动率A=T2/T1 生产产量W 单台实际周期时间(S) 实质稼 动率B 稼动时间=设备负荷时间 K-S(异常停机时间) B=W*单台周期/稼动时间 性能稼动率=A*B×100% 该线良品率(100%) 1日 2日 3日 4日 5日 6日 7日 8日
(完整版)OEE记录表格(设备综合效率)
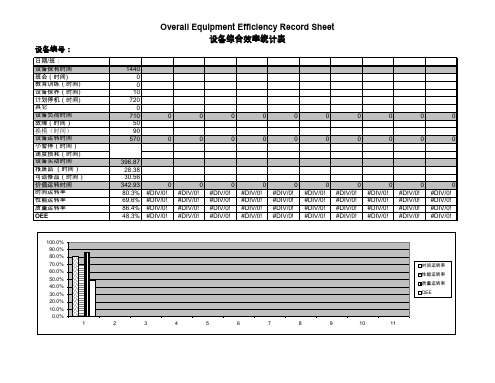
1440
0
0
10
720
0
710
0
0
0
0
0
0
0
0
0
0
50
90
0
0
0
0
0
396.87 28.38 30.56
342.93 80.3% 69.6% 86.4% 48.3%
0 #DIV/0! #DIV/0! #DIV/0! #DIV/0!
0 #DIV/0! #DIV/0! #DIV/0! #DIV/0!
4
符号:
P 设备保养 D 无生产计划
C 换模 T 模具或设备故障(需注明故障名称)
R 休息 W 待料
A 调试新模具 O 其它
维修和处理结果及验证 最终解决方案和验证
0 #DIV/0! #DIV/0! #DIV/0! #DIV/0!
0 #DIV/0! #DIV/0! #DIV/0! #DIV/0!
0 #DIV/0! #DIV/0! #DIV/0! #DIV/0!
0 #DIV/0! #DIV/0! #DIV/0! #DIV/0!
0 #DIV/0! #DIV/0! #DIV/0! #DIV/0!
0 #DIV/0! #DIV/0! #DIV/0! #DIV/0!
0 #DIV/0! #DIV/0! #DIV/0! #DIV/0!
0 #DIV/0! #DIV/0! #DIV/0! #DIV/0!
100.0%
90.0%
80.0%
70.0% 60.0% 50.0% 40.0% 30.0%
时间运转率 性能运转率 质量运转率 OEE
20.0%
10.0%
0.0%
设备综合效率OEE计算(附计算表格)

OEE(设备综合效率)
OEE计算(文末附计算表格)
1、OEE=时间开动率x性能开动率x合格率
2、时间开动率=实际操作时间/计划工作时间
计划工作时间=总可用时间-计划停机时间
(计划停机时间为员工休息、吃饭时间,计划保养时间)
实际操作时间=计划工作时间-计划外停机时间
(计划外停机时间为计划工作时间中设备故障、设备调整、设备紧急换型等非计划性时间)
3、性能开动率=实际产量/(实际操作时间/理想节拍时间)
4、合格率=良品数量/实际总产量
例如:某设备1天工作时间为24h,员工用餐、休息时间90min,班中计划保养停机60min,故障停机20min,生产中工艺调整30min,产品的理论加工周期为1.2min/件,一天加工产品1000件,有100件废品,求这台设备的设备综合效率OEE
备注:浅绿色为需要输入数据。
OEE记录表
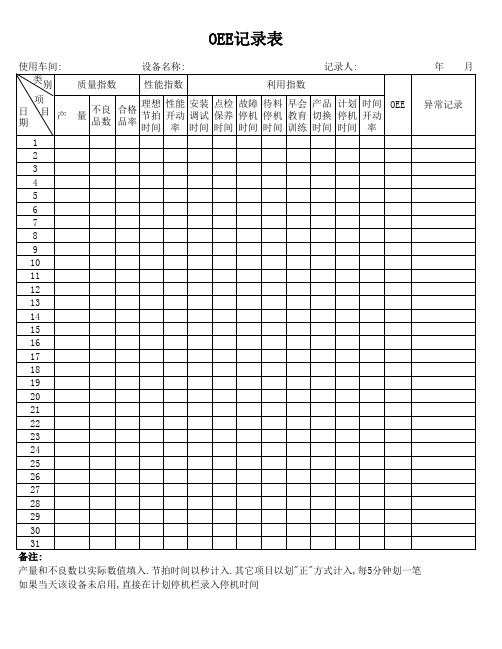
1 2 3 4 5 6 7 8 9 10 11 12 13 14 15 16 17 18 19 20 21 22 23 24 25 26 27 28 29 30 31 备注: 产量和不良数以实际数值填入.节拍时间以秒计入.其它项目以划"正"方式计入,每5分钟划一笔 如果当天该设备未启用,直接在计划停机栏录入停机时间
合格品率=合格品数/生产数量 性能开动率=生产数量/(60/理想节拍时间 X 实际生产时间) 时间开动率=实际生产时间/计划工作时间
OEE记录表
使用车间: 类别 项 设备 日 目 产 期 设备名称: 质量指数 性能指数 利用 待料 早会 产品 计划 时间 OEE 不良 合格 量 节拍 开动 调试 保养 停机 停机 教育 切换 停机 开动 品数 品率 时间 率 时间 时间 时间 时间 训练 时间 时间 率
OEE计算公式表

总投入时间 计划停机时间 故障 调机 换线 暖机 总产出量 总不良数 理论周期 实际周期 模具故障时间 设备故障次数 模具故障次数 调机次数 设备故障时间 故障次数 MTBF MTTR 4104 180 20 0 0 45 2365 0 1.430769231 1.735306554 30 2 1 3 50 6 643.1666667 8.333333333
0.876851317 纯稼动率 1.06348795 速度稼动率 0.824505173 良品率 1 OEE1 86.23% OEE 82.45%
0.824505173 总产出量 2365 理论周期 1.430769231 总产出量 2365 时间稼动率 0.98343527 OEE1 0.862326511
换线 0 暖机 45
稼动时间 385率 1 总投入时间 4104
负荷时间 3924 当机时间 65 稼动时间 3859 时间稼动率 0.98343527 性能稼动率 0.876851317 总投入时间 4104 故障 20 负荷时间 3924 稼动时间 3859 理论周期 1.430769231 速度稼动率
公式表
计划停机时间 180 调机 0 当机时间 65 负荷时间 3924 总产出量 2365 纯稼动率
1.06348795 实际周期 1.735306554 实际周期 1.735306554 总不良数 0 性能稼动率 0.876851317 负荷时间 3924
理论周期 1.430769231 实际周期 1.735306554
理论产量 325 总产出量 2365
理论时间 465 总投入时间 4104
式表
设备综合效率OEE统计表(使用)
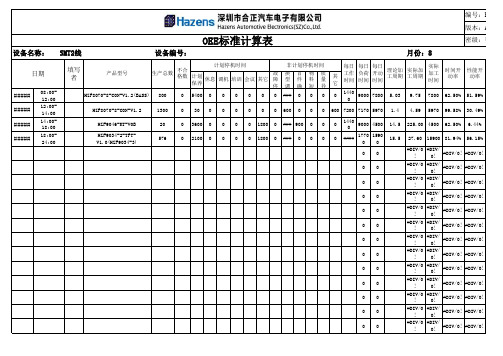
HZF8070-8-CON-V1.2(BASS) 800
0 5400 0 0 0 0 0 0 ### 0 0 0
其 它
每日 工作 时间
每日 每日 负荷 开动 时间 时间
理论加 工周期
实际加 工周期
实际 加工 时间
0
1440 0
9000
7800
5.03
#DIV/0! #DIV/0! #DIV/0! #DIV/0! #DIV/0! #DIV/0! #DIV/0! #DIV/0! #DIV/0! #DIV/0! #DIV/0! #DIV/0! #DIV/0! #DIV/0! #DIV/0! #DIV/0! #DIV/0! #DIV/0!
00
#DIV/0 !
#DIV/ 0!
#DIV/0!
#DIV/0!
00
#DIV/0 !
#DIV/ 0!
#DIV/0!
#DIV/0!
00
#DIV/0 !
#DIV/ 0!
#DIV/0!
#DIV/0!
00
#DIV/0 !
#DIV/ 0!
#DIV/0!
#DIV/0!
00
#DIV/0 !
#DIV/ 0!
#DIV/0!
#DIV/ 0!
#DIV/0!
#DIV/0!
00
#DIV/0 !
#DIV/ 0!
#DIV/0!
#DIV/0!
00
#DIV/0 !
#DIV/ 0!
#DIV/0!
#DIV/0!
00
#DIV/0 !
#DIV/ 0!
#DIV/0!
#DIV/0!
00
#DIV/0 !
OEE水准评价表
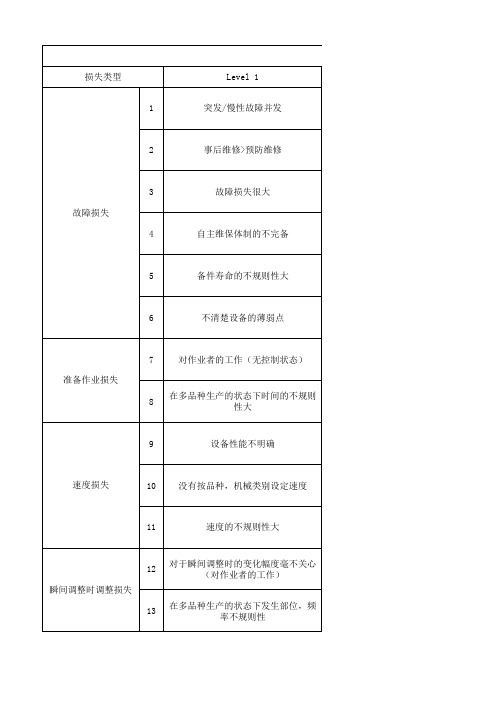
Level 1 突发/慢性故障并发
2
事后维修>预防维修
3 故障损失
4
故障损失很大 自主维保体制的不完备
5
备件寿命的不规则性大
6
不清楚设备的薄弱点
准备作业损失
7
对作业者的工作(无控制状态)
8
在多品种生产的状态下时间的不规则 性大
9
设备性能不明确
速度损失
10 没有按品种,机械类别设定速度
11
依据调整排除 改良设备性能异常的开动速度 按品种类别设定速度(标准)加以维
持 速度损失“0” 瞬间停止“0”状态(无人操作)
不合格损失0.1%-0
速度的不规则性大
瞬间调整时调整损失
12
对于瞬间调整时的变化幅度毫不关心 (对作业者的工作)
13
在多品种生产的状态下发生部位,频 率不规则性
OEE水准评价表
不合格损失
14
机制造成慢性不合格品
15 虽然准备了各种对策,但效果不好
OEE水准评价表 Level 2
大部分是偶发故障
Level 3 基于时间的维修体制的确立
事后维修=预防维修
事后维修<预防维修
发生故障损失
故障损失1%以下
自主维保体制的正在完备中
开展自主维保体制的活动
按推荐的备件寿命
延长备件的寿命
已知设备弱点实施CMΒιβλιοθήκη 对可靠性,维修性关系程度高
实施作业规范化(内外作业分顺序)
内准备作业规范化,外准备作业条理 化
存在时间不规则性
充分考虑调整机理和与其对应的要求
针对速度损失集中问题点(设备/品质 的)
对于集中的问题实施改善,试行中
OEE计算规则(OEE计算对照表)

=0.25H/D*26D =0.25H/D*26D
日
计划保养 1号下午安排保养4H 4H
历 时 间
上 班 时 间
计 划 开 机 时 间
新产品试做
正常损失 换型(模)
设备故障
模治具故障
异常损失 工艺异常
异常等待
其他损失
开机 时间
产能损失时间 合理产 不良品工时 能时间 合格品工时
3号下午试做4H
4H
换型5次,每次1H =1H/次*5
OEE计算对照表
时间分布
时间列举 说明(30天)
公式
放假时间 4个周日不上班
=24H/D*4D
休息时间
单班生产
夜班休自(白班上 10H)
=(2410)H/D*26D
班前会 每班开会15分钟 =0.25H/D*26D
吃饭 两餐,两个30分钟 =1H/D*26D
计划停机时间
开机点检 开机点检15分钟 首末件 检测15分钟
1.合格率=A/(A+B) 2.性能稼动率=(A+B)/(A+B+C) 3.时间稼动率 =(A+B+C)/(A+B+C+D+E) OEE(狭义)=1*2*3=A/(A+B+C+D+E)
我们目前所统计的每日产量 完成率=A/(A+B+C+D)
26
6.5 6.5
53.5
F
2.广义OEE: =A/(A+B+C+D+E+F)
4
4
5 5E
5
3
4 15 D 1.狭义OEE:
2
- 1、下载文档前请自行甄别文档内容的完整性,平台不提供额外的编辑、内容补充、找答案等附加服务。
- 2、"仅部分预览"的文档,不可在线预览部分如存在完整性等问题,可反馈申请退款(可完整预览的文档不适用该条件!)。
- 3、如文档侵犯您的权益,请联系客服反馈,我们会尽快为您处理(人工客服工作时间:9:00-18:30)。
#DIV/0! #DIV/0! #DIV/0! #DIV/0! #DIV/0! #DIV/0! #DIV/0! #DIV/0! #DIV/0! #DIV/0! #DIV/0! #DIV/0! #DIV/0! #DIV/0! #DIV/0! #DIV/0! #DIV/0! #DIV/0! #DIV/0! #DIV/0! #DIV/0! #DIV/0! #DIV/0! #DIV/0! #DIV/0! #DIV/0! #DIV/0! #DIV/0! #DIV/0! #DIV/0! #DIV/0!
设备:
项目
对象品种:全品种
生产准备(L) 条件确认 夹架治具准备 升降温 设备、品质故障(N) 生产设备故障 公共设备故障 计划安排停机(O) 管理停止(P) 磨损更换(Q)
时间(min)
分类
待机(等待洗 全废液、半废液、 SD、装置停止、计划 净、玻璃不 清洗(更换)发泡 停机、试验 足) 交接班、 管、加液、循环、 指示 其他
20.0 10.0
0.0 日期
性能稼动率
H G
步留
实际能力生 理论能力生产性 产性<100um (100um枚/h) 枚/h> =F/D 0 0 0 0 0 0 0 0 0 0 0 0 0 0 0 0 0 0 0 0 0 0 0 0 0 0 0 0 0 0 0
I
J
性能 稼动率 =H/I
K
OEE设备综合效率 =E*J*G
1 2 3 4 5 6 7 8 9 10 11 12 13 14 15 16 17 18 19 20 21 22 23 24 25 26 27 28 29 30 合计
0
0
0
0
0
1.各类时间定义 A 正常出勤时间=12h=1440MiN B 可用稼动时间=A-休息吃饭时间 C 计划稼动时间=B-计划停机 D 实际稼动时间=C- 试验时间-品种更换停机-设备、品质故障停机-管理上的停止-生产准备 2.计算公式 时间稼动率=D/C 性能稼动率=G/H 设备综合效率(OEE)=时间稼动率*性能稼动率*步留(F) *各设备损耗定义参照计算方法中说明
F
作业数 <100um枚>
100.0% 100.0% 100.0% 100.0% 100.0% 100.0% 100.0% 100.0% 100.0% 100.0% 100.0% 100.0% 100.0% 100.0% 100.0% 100.0% 100.0% 100.0% 100.0% 100.0% 100.0% 100.0% 100.0% 100.0% 100.0% 100.0% 100.0% 100.0% 100.0%
xxxxOEE设备综合效率
OEE设备综合 效率 100.0% 90.0% 80.0%
70.0%
xxOEE设备综合效率
60.0% 50.0% 40.0% 30.0% 20.0% 10.0% 0.0% 日期 1 2 3 4 5 6 7 8 9 10 11 12 13 14 15 16 17 18 19 20 21 22 23 24 25 26 27 28 29 30 合 计
时间稼动率
OEE设备综合效率
B C E
时间 稼动率 =D/C 加工数 良品数
休息吃饭 (R)
可用稼动 计划稼 正常出勤 时间 动时间 时间 =A-R =B-O 1440 1440 1440 1440 1440 1440 1440 1440 1440 1440 1440 1440 1440 1440 1440 1440 1440 1440 1440 1440 1440 1440 1440 1440 1440 1440 1440 1440 1440 1440 43200 1440 1440 1440 1440 1440 1440 1440 1440 1440 1440 1440 1440 1440 1440 1440 1440 1440 1440 1440 1440 1440 1440 1440 1440 1440 1440 1440 1440 1440 1440 43200 1440 1440 1440 1440 1440 1440 1440 1440 1440 1440 1440 1440 1440 1440 1440 1440 1440 1440 1440 1440 1440 1440 1440 1440 1440 1440 1440 1440 1440 1440 43200
#DIV/0! #DIV/0! #DIV/0! #DIV/0! #DIV/0! #DIV/0! #DIV/0! #DIV/0! #DIV/0! #DIV/0! #DIV/0! #DIV/0! #DIV/0! #DIV/0! #DIV/0! #DIV/0! #DIV/0! #DIV/0! #DIV/0! #DIV/0! #DIV/0! #DIV/0! #DIV/0! #DIV/0! #DIV/0! #DIV/0! #DIV/0! #DIV/0! #DIV/0!
A
D
实际稼动时间 =C-L-N-P 1440 1440 1440 1440 1440 1440 1440 1440 1440 1440 1440 1440 1440 1440 1440 1440 1440 1440 1440 1440 1440 1440 1440 1440 1440 1440 1440 1440 1440 1440 43200
0
0
0
0.0
管理上的停止-生产准备停机
xxx机性能稼动率
性能稼动率%
100.0%
xxx机性能稼动率
OEE设备综合 效率 100.0
90.0
90.0% 80.0% 70.0% 60.0%
50.0%
80.0 70.0
60.0%
50.0 40.0
30.0
40.0% 30.0% 20.0% 10.0% 0.0% 日期 1 2 3 4 5 6 7 8 9 10 11 12 13 14 15 16 17 18 19 20 21 22 23 24 25 26 27 28 29 30 合 计
xxx间稼动率
xxx间稼动率
时间稼动率% 100.0% 90.0% 80.0% 70.0%
60.0%
50.0% 40.0% 30.0% 20.0%
10.0%
0.0% 日期 1 2 3 4 5 6 7 8 9 10 11 12 13 14 15 16 17 18 19 20 21 22 23 24 25 26 27 28 29 30 合 计
OEE设备综合效率
#DIV/0! #DIV/0! #DIV/0! #DIV/0! #DIV/0! #DIV/0! #DIV/0! #DIV/0! #DIV/0! #DIV/0! #DIV/0! #DIV/0! #DIV/0! #DIV/0! #DIV/0! #DIV/0! #DIV/0! #DIV/0! #DIV/0! #DIV/0! #DIV/0! #DIV/0! #DIV/0! #DIV/0! #DIV/0! #DIV/0! #DIV/0! #DIV/0! #DIV/0!