IQC进料检验作业规范2020
IQC测试作业指导书

IQC测试作业指导书一、引言IQC(Incoming Quality Control)是指对进货物料进行质量控制的过程,旨在确保供应商提供的原材料、零部件或者成品的质量符合公司的要求。
本作业指导书的目的是为了提供一份详细的IQC测试流程,以确保所有的进货物料都能够经过严格的质量检验。
二、测试范围本次IQC测试的范围包括但不限于以下几个方面:1. 原材料的外观、尺寸、分量等基本属性;2. 零部件的装配质量、材料成份等;3. 成品的功能性能、耐久性等。
三、测试流程1. 来料检验1.1 收货确认:接收到进货物料后,检查货物的数量是否与采购定单一致,并确认是否有损坏或者异常情况。
1.2 外观检查:对进货物料的外观进行检查,包括表面是否有划痕、变形、污渍等。
1.3 尺寸测量:对进货物料的尺寸进行测量,使用合适的测量工具,确保尺寸符合要求。
1.4 分量检验:对进货物料的分量进行检验,使用称重设备进行准确测量,确保分量符合要求。
1.5 样品保留:对每一批进货物料,保留一定数量的样品,用于后续的功能性能测试。
2. 功能性能测试2.1 样品准备:从样品保留中选择合适数量的样品,准备进行功能性能测试。
2.2 测试设备准备:根据进货物料的特点,准备相应的测试设备和工具。
2.3 功能性能测试:根据产品的要求,进行相应的功能性能测试,例如电气性能测试、力学性能测试等。
2.4 结果记录:记录每一个样品的测试结果,包括通过与否、数值数据等。
3. 材料分析3.1 样品准备:从样品保留中选择合适数量的样品,准备进行材料分析。
3.2 分析方法选择:根据进货物料的特点,选择合适的材料分析方法,例如化学分析、光谱分析等。
3.3 分析过程:按照选定的分析方法进行材料分析,确保分析结果准确可靠。
3.4 结果记录:记录每一个样品的材料分析结果,包括成份、含量等。
四、测试记录与报告1. 测试记录:每一次IQC测试都应有详细的测试记录,包括测试日期、测试人员、测试设备、测试方法、测试结果等。
IQC来料检验规范
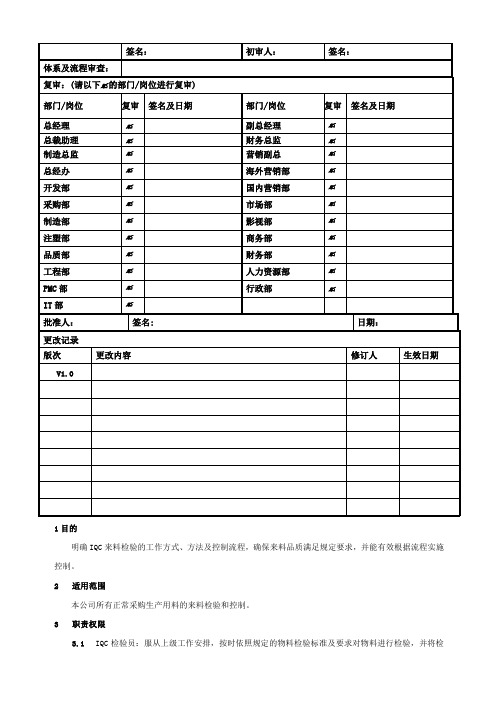
1目的明确IQC来料检验的工作方式、方法及控制流程,确保来料品质满足规定要求,并能有效根据流程实施控制。
2适用范围本公司所有正常采购生产用料的来料检验和控制。
3职责权限3.1IQC检验员:服从上级工作安排,按时依照规定的物料检验标准及要求对物料进行检验,并将检验结果准确的记录在相关报表上。
3.2IQC组长:服从上级工作安排和IQC检验员日常管理,负责IQC日常工作安排并对下属检验员工作进行指导、监督、考核,对检验记录报表进行确认,对不合格物料处理进行跟进,并协助IQC主管工作。
3.3SQE:负责供应商品质管理和来料检验物料异常确认、来料物料异常的处理,并推动供应商改善。
3.4IQC主管:负责检验员和SQE的日常管理,工作安排和指导,标准的制订,物料异常的处理和裁决,部门之间的沟通协调等。
4术语定义4.1缺陷等级定义4.1.1致命缺陷(Critical):有可能造成顾客生命或财产安全之缺陷,产品的极重要质量特性不符合规定或不符合国家法律法规之要求的,简称CR。
4.1.2严重缺陷(Major):产品主要功能受影响或丧失其使用功能,且不能达成其使用目的之缺陷。
不构成致命缺陷但可能导致功能失误或降低原有使用功能的缺陷,简称MA。
4.1.3次要缺陷(Minor):产品外观受轻度损伤但不影响产品使用性能之缺陷,简称MI。
5工作程序5.1仓库收料员在收到物料后,依供应商送货清单点数收货,确认无误后把物料按规定要求放在相应的待检区域内,并生成《采购收货单》移交至IQC对应检验员。
5.2IQC检验员在接到《采购收货单》时确认物料承认状况,对于已承认物料则找到对应物料零件承认书、样品、检验标准等相关文件进行检验。
对于未承认物料由IQC检验员填写《未承认物料验证单》,然后将《未承认物料验证单》,《采购收货单》和样品一起送至开发部对应衔接人员,由开发部衔接人员分发至对应工程师进行临时签样,紧急物料开发工程师需在2H内完成确认签样工作,非紧急物料需在8H内完成确认签样工作,并附带临时样品和图纸(样品无法签字时需作上标记识别),IQC检验员依《未承认物料验证单》给出的处理意见结合临时样品和图纸进行检验。
IQC进料检验作业指导书

IQC进料检验作业指导书模板1.适用范围:凡本公司生产之成品﹑半成品及供应商所交入之原材料﹑注塑件﹑委外喷漆加工品等。
2.目的:为确保公司产品的品质,降低生产成本,从所购进之原物料﹑注塑件﹑委外喷漆品﹑特采不合格品之量测和监控,来执行品质的管制作业及做成完整的检验报告,并针对产品发生品质异常作纠正及改善措施,以避免误用及防止不良品的再次发生。
3.检验参考资料:3.1制定符合公司品质标准之原物料﹑注塑件﹑委外加工品之检验规范。
3.2原物料依所需之规格制定,作为供应商供料验收之标准,以利双方品质确认。
3.3委外加工品依检验标准书.样品作为进料检验之依据。
4.定义:4.1目标管理:4.1.1 按照供应商的品质目标实现方案管理,及管理每月实绩。
4.1.2 对未达成的供应商制定对策并实施,必要时纠正和预防措施,定期对供应商点检。
4.1.3 召开每月供应商品质会议,发表每月业务计划和业绩,以保证和业体沟通、信息共享。
4.1.4 品质保证协议书签定,制约供应商必须按我司的品质目标要求去实施,以达到品质保证目的。
4.2检查基准书:依据各客户产品的外观检验基准和信赖性检验基准的要求,并结合公司内部的检验规范要求而制定出的一套检验操作标准。
5.职责和权限:5.1主管:5.1.1 来料检验规范及流程的监控、管理,新品、承认书检讨及检验基准制定并实施。
5.1.2 收集、统计各类质量数据,制作各类日报、周报、月报,跟踪质量目标达成情况。
5.1.3 定期对检验人员进行上岗培训和考核,使检验人员具有相应的技术水平和检验能力。
5.1.4 管理好供应商的来料品质状况,依据收集、统计的来料数据,对供应商做出定期考核、评比。
5.2 检查员:5.2.1 对入料的原材料、注塑件、辅材(保护膜气泡袋纸箱胶框)、委外加工产品等核对外箱标签:品名、料号、日期、数量及包装规范进行核对。
5.2.2 按照相关的检验基准,承认样件,依照检验流程进行检验并详细记录检验结果。
IQC-电子料检验规范
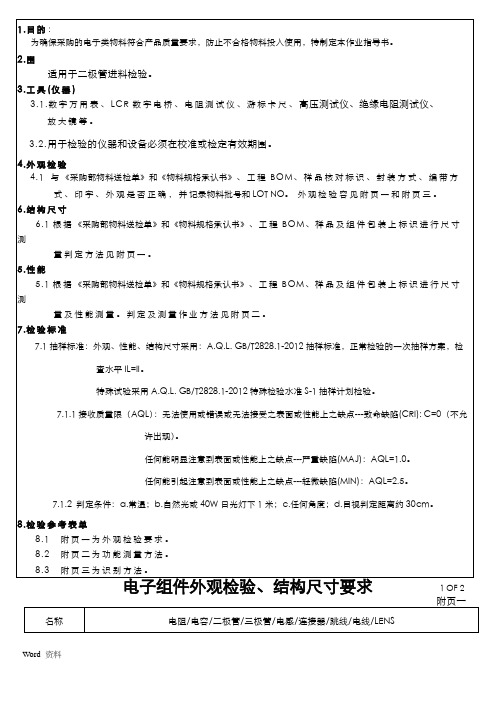
ˇ
c. 不能有脱皮现象,即脱皮面积露出里面之金属部分超过 1mm2
为不符合标准。
外 观 B.饼仔电容(温度补偿电容) 特性:无极性
结构尺寸 a.印字清晰,不能模糊、漏印。
ˇ
(电容) b.PIN 及其它表面不能破损,露出里面之金属部分。
C.可调电容: 即容量可以调动,从最低值至最高值围可以任意改变
D.电解电容、饼仔电容的容值要与规格要求一致。
查水平 IL=II。
特殊试验采用 A.Q.L. GB/T2828.1-2012 特殊检验水准 S-1 抽样计划检验。
7.1.1 接收质量限(AQL):无法使用或错误或无法接受之表面或性能上之缺点---致命缺陷(CRI): C=0(不允
许出现)。
任何能明显注意到表面或性能上之缺点---严重缺陷(MAJ):AQL=1.0。
ˇ
游标卡尺 放大镜 目视 数字万 用表
目视
目视 电容表 电容表
外观 (LED)
Word 资料
A. LED 两 PIN 脚应无氧化生锈而有光泽。 B. 发光颜色及亮度要与实际要求一致。 C. LED 本体不得有破损、污渍、划伤等现象。
电子组件外观检验要求
ˇ
目视
ˇ
万用表
ˇ
2 OF 2
目视
名称
附页一 电阻/电容/二极管/三极管/电感/连接器/跳线/电线/LENS
名称 抽样计划
AQL 检验项目
色环电阻 识别法
电子组件识别方法
1 OF 2
附页三
电阻/电容/二极管/三极管/电线
GB2828-2003 II 单次抽样
MAJ:0.65
MIN:1.5
颜色 银色 金色 黑色 棕色 红色 橙色 黄色 绿色 蓝色 紫色 灰色 白色 无色
IQC进料检验作业规范
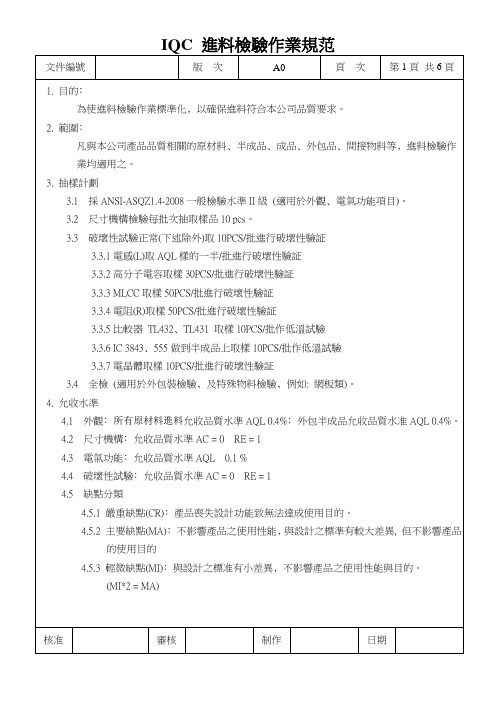
4.6 外包鐵芯繞線功能檢驗按批量檢驗:
批量從1~~~~100KPCS﹐抽檢樣本量為50PCS﹔
批量從100001~~~~1000KPCS﹐抽檢樣本量為100PCS﹔
批量從1000K以上PCS﹐抽檢樣本量為150PCS﹔
4.7 漆包線檢驗按批量檢驗﹕
批量從1~~~~~100卷﹐抽檢樣本量為10卷﹔
批量從101~~~~~200卷﹐抽檢樣本量為20卷﹔
批量200卷以上﹐抽檢樣本量按10%比例進行抽檢﹔
4.8 包裝管功能檢驗按批量檢驗﹕
批量從1~~~~~~5000PCS,抽檢樣本量為10PCS﹔
批量從50001~~~~~~10000PCS,抽檢樣本量為20PCS﹔
批量從10001~~~~~~15000PCS,抽檢樣本量為30PCS﹔
批量從15000PCS以上,抽檢樣本量為40PCS。
4.9 包裝盤功能檢驗每批進料試裝5PCS。
5.0 包裝帶功能檢驗每批進料試作1卷。
5.1 化工膠類功能檢驗按批量檢驗﹕
批量從1~~~~~~50桶﹐抽檢樣本量為2桶﹔
批量從51~~~~~~100桶﹐抽檢樣本量為4桶﹔
批量從100桶以上﹐抽檢樣本量為2%比例進行抽檢﹔
5.2 包裝紙箱功能檢驗每批進料試裝5PCS。
5.3 進料箱抽樣要求﹕
5.3.1 進料5箱以內(包括5箱)﹐全部開箱取樣。
5.3.2 進料6~10箱(包括10箱)﹐需開7箱取樣。
5.3.3進料11~15箱(包括15箱)﹐需開9箱取樣。
5.3.4進料16箱以上﹐需開12箱取樣。
5.3.5 IQC針對已開箱取樣之外箱,需使用藍色封箱膠帶進行標示。
如下圖:。
IQC进料检验规范

文件制修订记录1、目的为严格执行ISO9001质量体系管理要求、确保物料符合本公司之使用要求,保证生产顺利进行,制订本规范。
2、范围公司自行生产零部品及采购物料。
3、职责进料检验(IQC检验员)负责执行检验、负责品质异常开立“品质异常处理单、负责客户抱怨、制程不良的分析/查核、处理并记录”。
品质部经理负责对检验结果进行核准。
4、工作流程4.1检验依据检验卡(图纸)、进料检验规范。
4.2送检所有物品(外购、自制)来料时,应整齐摆放于待检区适宜位置,报仓库管理员进行产品名称、型号、数量及其他随货相应文件进行收料确认(暂存),仓库管理员在物料接收确认后应立即开《送检单》通知品质部,必要时提醒物料紧急程度,由品质安排进行检验。
4.3检验品质部应快速对报送物品进行外观、尺寸、结构、性能等的检验、试验,并做出正确判定。
4.4判定/标识A、进货物料所有检验、试验项目无任何缺陷,或存在缺陷但在允收范围内,应在产品标识单签名确认,后将物料移至合格区报仓库入库。
B、进货物料所有检验、试验项目存在任何一项质量缺陷,在允收范围外,应在产品标识单上判定为不合格状态并签名确认后将物料移至不合格区,外购件报采购部、仓库协作采购部做好退货事宜。
4.5信息反馈进货物料所有检验、试验项目存在任何一项质量缺陷,在允收范围外,由品质部开立品质异常处理单、常规状况下,产品出现异常时品管部直接批准不合格处理,转发(外购件采购部)、仓库,由采购部与供应商进行退货事宜沟通,特殊情况可由相关部门提出评审。
4.6质量评审进货物料所有检验、试验项目存在任何一项质量缺陷,在允收范围外,由品质部开立品质异常处理单判定结果为不合格,若出现严重生产断料、销售进度紧张,可由采购部、生产部、或销售部向品质部提出评审申请,由申请部门填写相应项目申请单,会同相关部门进行评审,品质部若认同申请项目则评审直接通过,若品质部评审未通过提出部门可报总/副总经理进行终批复、列出处理意见并签字确认。
IQC进料检验规范

1.目的:对所有材料进行检验,以保证材料符合其规格要求,同时为确保生产制程中各项作业程序及作业内容得到正确实施。
2. 适用范围:由本公司采购用于生产或与产品品质有关的原材料均包括在内,同时也包括客供料、其它部分不合格部品的管理。
3. 职责:3.1 品管部IQC检验员负责对原材料的品质进行检验,并作记录。
3.2 物控人员负责对库存原材料进行控制。
3.3 采购部负责材料的采购、与来料供应商联系不合格品进行退货事宜。
3.4 MRB负责对所需特采的原材料进行判定.3.5 SQE/IQC副理负责对原材料的品质异常进行处理及判定3.6 仓管人员负责原物料的搬运堆放,保管与发放管理。
4. 定义:IQC(Incoming Quality Control):进料品质控制。
SQE:(Supplier Quality Engineer)供货商管理品质工程师。
致命缺陷(Critical Defect):产品不合格现象会影响人身安全及导致其它破坏性事故或有可能引起火灾为致命缺陷。
严重缺陷(Major Defect):不合格现象足以使产品功能失常,性能降低或使用困难者为重缺点。
轻微缺陷(Minor Defect):轻微之组装结构与外观不良而不影响产品功能。
5. 作业流程: IQC检验流程图(见相关文件)6. 作业内容:6.1来料检验;6.1.1 接收进料仓库管理人员接收进料,核对其规格、数量及标识后置于进料待检区(来料必须有环保标识和物料标贴,否则不给予收货)。
并根据送货单及实物打印《采购入库待检单》给IQC。
6.1.2 检验来料;6.1.2.1 品管部IQC人员确认《采购入库待检单》后,对相应材料进行检验。
6.1.2.2 IQC检验前,全数确认包装,检查包装是否符合规格书要求,是否有对物料保护作用,会不会互相碰撞摩擦,如有破损或者潮湿的现象做不合格品处理并作好记录,反馈给供应商。
6.1.2.3 IQC根据供应商提供的合格出货检查报告或同等资料证明,核对实际来料的名称,型号,产地批号,环保标识及生产日期和我司研发与品质提供的样品、图纸、BOM、合格供方名单、检验作业指导书、部品规格书以及本规范,一致时判定合格,并记录《进料检验报告》,不一致时判定不合格并填写《供应商品质不良反馈单》参照《不合格品控制程序》作业.结果按6.1.2.6执行,并给到采购与PMC会签,会签后让采购把《供应商品质不良反馈单》以电子邮件的方式发送给供应商,要求改善,并要求3天内回复8D改善对策。
IQC检验作业规范
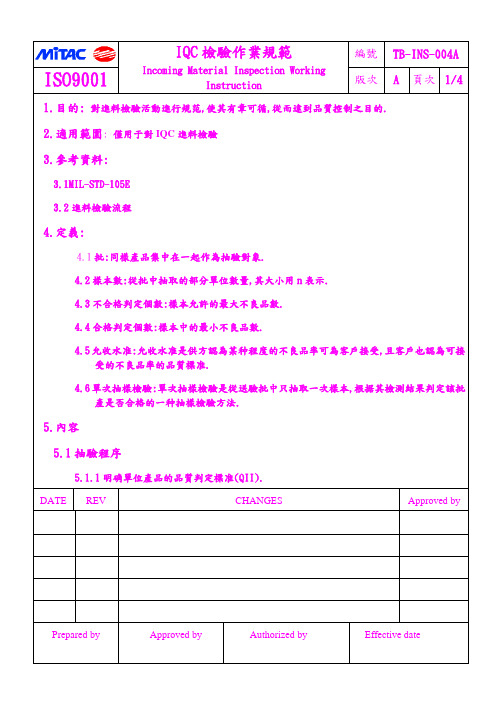
5.4.3.2 從正常檢驗到加嚴檢驗 當進行正常檢驗時,若在連續 2 批初次檢驗不合格或較嚴重客戶投訴,則從下一批檢驗轉 到加嚴檢驗. 5.4.3.3 從加嚴檢驗到正常檢驗 當進行加嚴檢驗時,若連續 5 批初次檢驗合格,,則從下一批檢驗轉到正常檢驗. 5.4.3.4 從正常檢驗到放寬檢驗 當進行正常檢驗時,若下列條件均可滿足,則從下一批轉到放寬檢驗. a.連續 10 批或更多批初次檢驗合格. b.生產正常.. 5.4.3.5 從放寬檢驗到正常檢驗 當進行放寬檢驗時,若出現下列任何一种情況,則從下一批來貨轉為正常檢驗. a.有一批放寬檢驗不合格 b.有一批放寬檢驗時其不良品數超過 Ac 但小于 Re. c.生產不正常
5.4.檢驗嚴格度的規定
一般情況下按如下程序進行. 5.4.1 檢驗的開始 除非另有規定,在檢驗開始時應使用正常檢驗Ⅱ 級. 5.4.2 檢驗的繼續 除需按 6.3 轉移規則改變檢驗的嚴格度外,下一批檢驗的嚴格度繼續保持不變. 5.4.3.轉移規則
漢達精密電子科技(順德)有限公司
IQC 檢驗作業規範
6. 附表.
-STD-105E《正常單次抽樣計划.水准Ⅱ 》 -STD-105E《加嚴單次抽樣計划.水准Ⅱ 》 6.3 MIL-STD-105E《減量單次抽樣計划.水准Ⅱ 》
7.紀錄保存:無
漢達精密電子科技(順德)有限公司
版次 A 頁次
5.5.3.樣本的檢驗 根据內部標准(QII),對樣本逐個檢驗,并累計不合格品總數. 5.5.4.對此批產品作出合格或不合格的判斷 5.5.5 逐批檢驗后的處理參閱進料檢驗流程。 5.5.6. 記錄維護. 每批檢驗完畢后,須把對此產品所采用的檢驗方式及其結果記錄于 《進料檢驗報告》 中. 5.5.7.特殊情形 5.5.7.1 當抽樣方案的樣本大小等于或大于批量時,將該批量看作樣本大小,抽樣方案的判定 數組保持不變. 5.5.7.2.放寬檢驗時,批中不良品數超過 Ac 但小于 Re 則該批合格,但下批應調整為正常檢 驗.
IQC进料检验规范
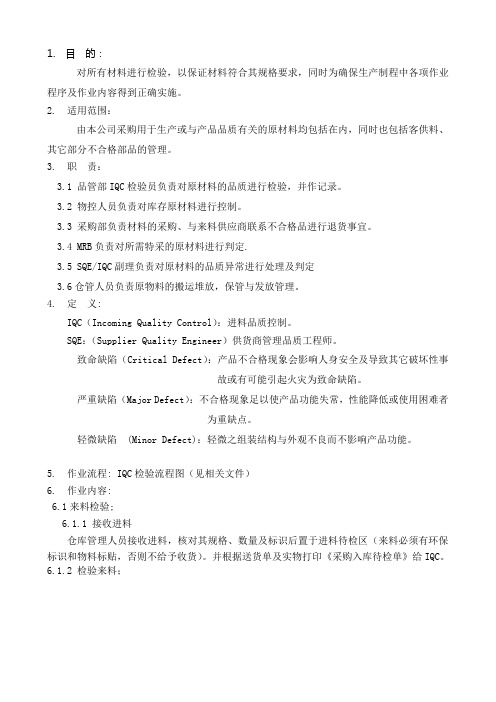
1. 目的:对所有材料进行检验,以保证材料符合其规格要求,同时为确保生产制程中各项作业程序及作业内容得到正确实施。
2. 适用范围:由本公司采购用于生产或与产品品质有关的原材料均包括在内,同时也包括客供料、其它部分不合格部品的管理。
3. 职责:3.1 品管部IQC检验员负责对原材料的品质进行检验,并作记录。
3.2 物控人员负责对库存原材料进行控制。
3.3 采购部负责材料的采购、与来料供应商联系不合格品进行退货事宜。
3.4 MRB负责对所需特采的原材料进行判定.3.5 SQE/IQC副理负责对原材料的品质异常进行处理及判定3.6仓管人员负责原物料的搬运堆放,保管与发放管理。
4. 定义:IQC(Incoming Quality Control):进料品质控制。
SQE:(Supplier Quality Engineer)供货商管理品质工程师。
致命缺陷(Critical Defect):产品不合格现象会影响人身安全及导致其它破坏性事故或有可能引起火灾为致命缺陷。
严重缺陷(Major Defect):不合格现象足以使产品功能失常,性能降低或使用困难者为重缺点。
轻微缺陷 (Minor Defect):轻微之组装结构与外观不良而不影响产品功能。
5. 作业流程: IQC检验流程图(见相关文件)6. 作业内容:6.1来料检验;6.1.1 接收进料仓库管理人员接收进料,核对其规格、数量及标识后置于进料待检区(来料必须有环保标识和物料标贴,否则不给予收货)。
并根据送货单及实物打印《采购入库待检单》给IQC。
6.1.2 检验来料;6.1.2.1 品管部IQC人员确认《采购入库待检单》后,对相应材料进行检验。
6.1.2.2 IQC检验前,全数确认包装,检查包装是否符合规格书要求,是否有对物料保护作用,会不会互相碰撞摩擦,如有破损或者潮湿的现象做不合格品处理并作好记录,反馈给供应商。
6.1.2.3 IQC根据供应商提供的合格出货检查报告或同等资料证明,核对实际来料的名称,型号,产地批号,环保标识及生产日期和我司研发与品质提供的样品、图纸、BOM、合格供方名单、检验作业指导书、部品规格书以及本规范,一致时判定合格,并记录《进料检验报告》,不一致时判定不合格并填写《供应商品质不良反馈单》参照《不合格品控制程序》作业.结果按6.1.2.6执行,并给到采购与PMC会签,会签后让采购把《供应商品质不良反馈单》以电子邮件的方式发送给供应商,要求改善,并要求3天内回复8D改善对策。
IQC进料检验作业规范

8.1必要时,IQC针对供应商来料异常状况开出《物料品质异常改善报告》,并通过采购部交供应商填写后回复品管部。
8.2检验员每天将相应供应商来料检验品质状况记录于《供应商质量记录表》中,并每月汇总到《供应商每月质量考核表》中,对供应商进行质量考核。考核结果交采购部对供应商进行相应之扣款或其它作业。
6.2抽样前先确认所抽物料规格型号要与送检单一致,对不符合送检单描述的物料可拒绝抽检,并即时反馈仓库人员处理.
6.3抽样计划采用GB2828-2003正常检查一次抽样方案,详见《正常检查一次抽样方案(GB2828-2003)》,必要时可采用加严或全检作业.
6.4检验项目:
6.4.1一般包括外观目检、尺寸标识、功能测试、实装判定、实验确认中的几项或更多内容.
9.统计分析
9.1 IQC检验员按周月将检验结果进行统计汇总,形成IQC检验周报及月报,直观的展现进料品质状况。
10.相关流程及附件:
10.1 IQC进料检验作业流程图
10.2 IQC进料检验标识单图示
11.记录表单
11.1《IQC检验送检单》
11.2《IQC检验报告》
11.3《物料品质异常改善报告》
《技术更改通知》
《特采作业办法》
《零件规书》
《BOM》
4.承认样品
对于文字难以叙述清楚或不易判定合格与否的外观缺点,则以样品、图纸及说明图片,作为来料检验时判定的依据。
5.仓库送检
5.1供应商送交公司的物料,仓库人员首先要确认所送物料型号规格是否符合采购订单要求:若不符合,则拒绝接收,若合格则由仓库暂收并清点数量,入暂存库.
c.次要缺点( Mi.):指不影响产品的使用、功能的外观缺点,并对产品的使用者不会造成不良影响之缺点。
IQC进料检验规范
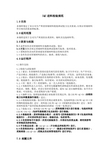
IQC进料检验规范1.0目的本规程规定了本公司生产所需原辅材料检验和试验方法及要求,以保证原辅材料符合相关的要求和标准。
2.0适用范围本规程适用于公司生产所需的各类原料、辅料及包装材料等。
3.0职责与权限3.1品管部负责对原辅材料实施核对试验、验证3.2开发部负责制定原辅材料检验和试验相关标准、技术要求。
3.3采购部负责向供货商索取原辅材料验证的相关资料3.4仓库负责对原辅材料的清点、抽查、报检与标识。
4.0运行程序4.1操作流程4.2检验与试验规程4.2.1索证:各原辅料供货商应提供相关的有效档,如卫生许可证、生产许可证、产品合格证、检验报告、产品执行标准等,由采购部﹑开发部﹑品管部负责备案。
4.2.2验证:查验供货商提供有效档的可靠性,如发证机关、业务范围、有效期限、检验报告、执行标准等。
如有疑问,应及时向采购部反应。
4.2.3同一批次(号)的原辅料,以一次入库量为一检验批次。
4.2.4每批原料进入公司后,仓管首先根据物料请购通知单或客送货单,核对来料品名、规格、数量,并进行初步质量检查,通知IQC进行抽样检验;如不符合要求,可以拒收,并由采购部与客户联系。
4.2.5抽样方法:除国家标准或行业标准另有规定外,按CSB/WI-QC-04《品检抽检方法和数量操作规范》进行。
4.2.6检验验收依据:除合同另有规定或要求外,包装材料按CSB/WI-QC-03《来料物料检验标准》进行﹐原料按CSB/WI-QC-13《原辅料质量标准》进行﹐客供原材料按客户提供的标准或相应的国家(行业)标准进行。
4.2.7检验方法﹕原料按CSB/WI-QC-12《原料检测方法》进行检验﹐包装材料按CSB/WI-ENG-02《包材性能检测方法及标准》进行检验。
4.2.8检验结果﹕原材料检验合格后﹐应填写《原料检验报告》和《包装材料检验报告》﹐并对原材料进行标示﹐检验状态﹑保质期等。
4.2.9供货商每半年提供一次型式检验报告﹐内容应包括重金属﹑溶剂残留等有害物质的控制情况。
iqc进料检验作业指导书
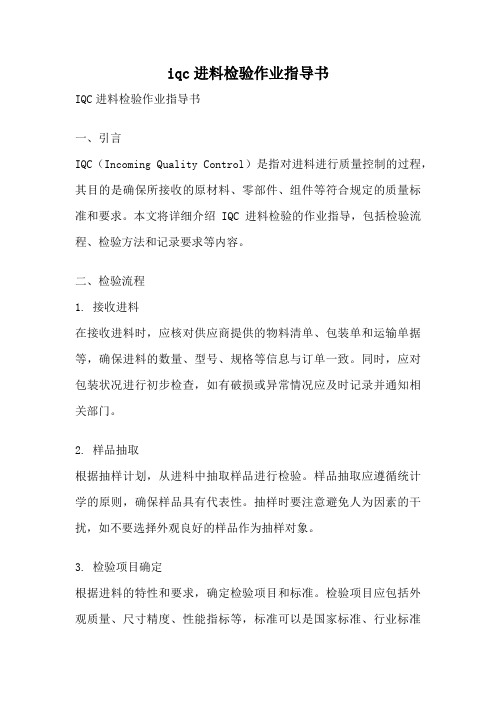
iqc进料检验作业指导书IQC进料检验作业指导书一、引言IQC(Incoming Quality Control)是指对进料进行质量控制的过程,其目的是确保所接收的原材料、零部件、组件等符合规定的质量标准和要求。
本文将详细介绍IQC进料检验的作业指导,包括检验流程、检验方法和记录要求等内容。
二、检验流程1. 接收进料在接收进料时,应核对供应商提供的物料清单、包装单和运输单据等,确保进料的数量、型号、规格等信息与订单一致。
同时,应对包装状况进行初步检查,如有破损或异常情况应及时记录并通知相关部门。
2. 样品抽取根据抽样计划,从进料中抽取样品进行检验。
样品抽取应遵循统计学的原则,确保样品具有代表性。
抽样时要注意避免人为因素的干扰,如不要选择外观良好的样品作为抽样对象。
3. 检验项目确定根据进料的特性和要求,确定检验项目和标准。
检验项目应包括外观质量、尺寸精度、性能指标等,标准可以是国家标准、行业标准或企业内部标准。
对于有特殊要求的进料,还需要制定专门的检验方案。
4. 检验方法选择根据检验项目的不同,选择合适的检验方法。
常用的检验方法包括目测检查、测量仪器检测、化学分析、物理性能测试等。
在选择检验方法时,要确保方法的准确性、可靠性和可操作性。
5. 检验执行按照检验项目和方法,对样品进行检验。
在检验过程中,要严格按照操作规程进行,避免人为因素的影响。
如有需要,可以采取多次抽样、多次检验的方式,提高检验的可靠性。
6. 检验结果评判根据检验结果和标准要求,对样品进行评判。
评判结果可以分为合格、不合格和待定三种情况。
对于不合格品,需要及时与供应商联系,协商处理方式。
7. 检验记录对每次检验的结果进行记录,并保留相关资料。
检验记录应包括进料信息、抽样情况、检验项目、检验方法、检验结果和评判等内容。
记录要求清晰、准确,方便后续的追溯和分析。
三、注意事项1. 检验人员应熟悉相关的工艺和技术要求,具备一定的专业知识和技能。
IQC进料检验工作标准
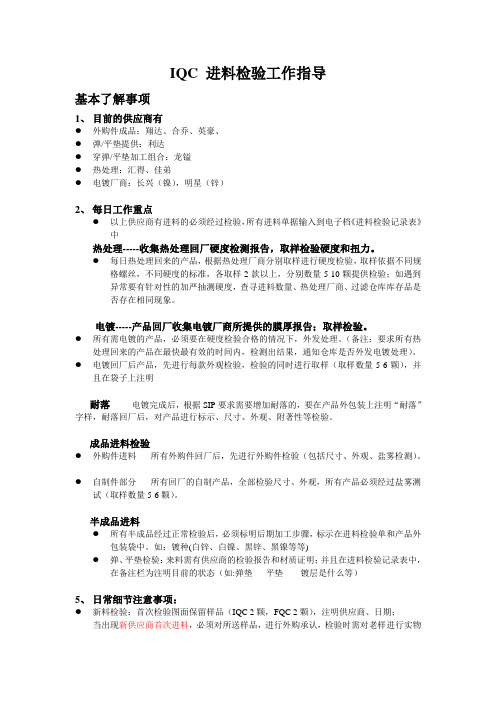
IQC 进料检验工作指导基本了解事项1、目前的供应商有●外购件成品:翔达、合乔、英豪、●弹/平垫提供:利达●穿弹/平垫加工组合:龙镒●热处理:汇得、佳弟●电镀厂商:长兴(镍),明星(锌)2、每日工作重点●以上供应商有进料的必须经过检验,所有进料单据输入到电子档《进料检验记录表》中热处理-----收集热处理回厂硬度检测报告,取样检验硬度和扭力。
●每日热处理回来的产品,根据热处理厂商分别取样进行硬度检验,取样依据不同规格螺丝,不同硬度的标准,各取样2款以上,分别数量5-10颗提供检验;如遇到异常要有针对性的加严抽测硬度,查寻进料数量、热处理厂商、过滤仓库库存品是否存在相同现象。
电镀-----产品回厂收集电镀厂商所提供的膜厚报告;取样检验。
●所有需电镀的产品,必须要在硬度检验合格的情况下,外发处理。
(备注:要求所有热处理回来的产品在最快最有效的时间内,检测出结果,通知仓库是否外发电镀处理)。
●电镀回厂后产品,先进行每款外观检验,检验的同时进行取样(取样数量5-6颗),并且在袋子上注明耐落------ 电镀完成后,根据SIP要求需要增加耐落的,要在产品外包装上注明“耐落”字样,耐落回厂后,对产品进行标示、尺寸、外观、附著性等检验。
成品进料检验●外购件进料-----所有外购件回厂后,先进行外购件检验(包括尺寸、外观、盐雾检测)。
●自制件部分-----所有回厂的自制产品,全部检验尺寸、外观,所有产品必须经过盐雾测试(取样数量5-6颗)。
半成品进料●所有半成品经过正常检验后,必须标明后期加工步骤,标示在进料检验单和产品外包装袋中。
如:镀种(白锌、白镍、黑锌、黑镍等等)●弹、平垫检验:来料需有供应商的检验报告和材质证明;并且在进料检验记录表中,在备注栏为注明目前的状态(如:弹垫平垫镀层是什么等)5、日常细节注意事项:●新料检验:首次检验图面保留样品(IQC 2颗,FQC 2颗),注明供应商、日期;当出现新供应商首次进料,必须对所送样品,进行外购承认,检验时需对老样进行实物比对,然后填写《外购承认单》承认。
IQC作业准则IPQC作业准则QE作业准则及OQC作业准则
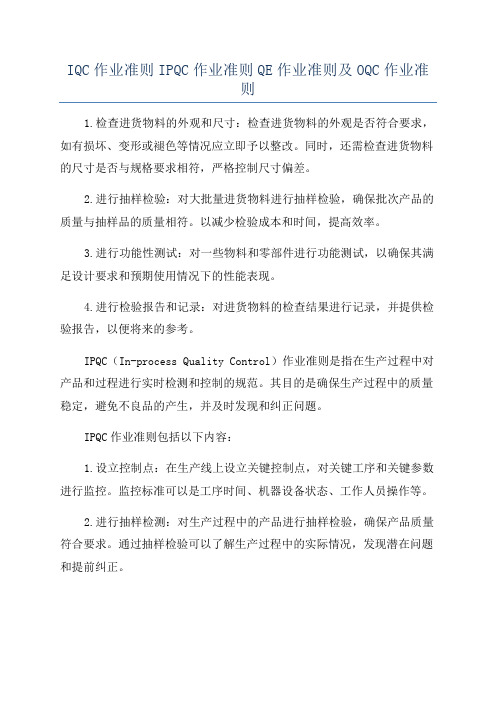
IQC作业准则IPQC作业准则QE作业准则及OQC作业准则1.检查进货物料的外观和尺寸:检查进货物料的外观是否符合要求,如有损坏、变形或褪色等情况应立即予以整改。
同时,还需检查进货物料的尺寸是否与规格要求相符,严格控制尺寸偏差。
2.进行抽样检验:对大批量进货物料进行抽样检验,确保批次产品的质量与抽样品的质量相符。
以减少检验成本和时间,提高效率。
3.进行功能性测试:对一些物料和零部件进行功能测试,以确保其满足设计要求和预期使用情况下的性能表现。
4.进行检验报告和记录:对进货物料的检查结果进行记录,并提供检验报告,以便将来的参考。
IPQC(In-process Quality Control)作业准则是指在生产过程中对产品和过程进行实时检测和控制的规范。
其目的是确保生产过程中的质量稳定,避免不良品的产生,并及时发现和纠正问题。
IPQC作业准则包括以下内容:1.设立控制点:在生产线上设立关键控制点,对关键工序和关键参数进行监控。
监控标准可以是工序时间、机器设备状态、工作人员操作等。
2.进行抽样检测:对生产过程中的产品进行抽样检验,确保产品质量符合要求。
通过抽样检验可以了解生产过程中的实际情况,发现潜在问题和提前纠正。
3.进行过程能力分析:对生产过程进行能力分析,评估生产过程的稳定性和可靠性。
通过过程能力分析可以确定生产过程是否稳定,是否需要进行调整和改进。
4.进行异常处理:对生产过程中出现的异常情况进行及时处理和纠正,防止异常情况扩大影响产品质量。
QE(Quality Engineering)作业准则是指执行质量管理体系和质量改进活动的规范。
其目的是提供质量管理的基础,确保质量管理体系的有效运行,并持续改进产品和生产过程。
QE作业准则包括以下内容:1.建立质量管理体系:制定和实施符合国际标准的质量管理体系,包括质量政策、质量目标、作业程序、质量记录等。
2.进行质量改进活动:制定和实施质量改进计划,通过分析数据和问题,确定改进的方向和措施,并进行跟踪和评估。
IQC进料检验规范
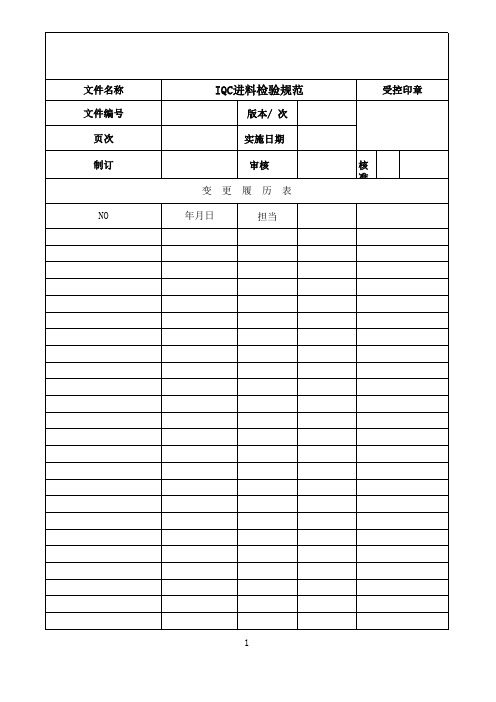
四、允收水准: MIL-STD-105E ,CR =0 MA = 0.4 MI =1.0 。
执行
五、检验步骤: 1.IQC依据送检单对送检之物料确认品名、规格、数量;并确认是否与承认书、BOM一致。 2.确认包装方式(防静电、防潮、防振)及标识(标签、条码、ROHS、FCC、CE)是否符合要求 3.根据抽样计划进行抽样以及依据检验标准进行检测和判定。 4.经检验OK后,检验结果记录于进料检验记录表中;在规定位置加盖:IQC PASS 章,并在 ERP系统中进行入库。 5.如经检验及判定异常时,须作不良标识及记录,则依据进料检验异常程序执行,填写进 料检验品质异常报告。
4.耐压须与承认书规格值相
符;
1.厂商出货 报告 附件 2.样品SGS报 一份 告(限样 品)
目视
1.厂商出货报告内容须与承认 书规格相符; 2.样品SGS报告须与样品一致。
6
√ √
文件编号:XG-QI-QC-015
贴片电感检测标准
项目 检验内容 抽样 检验方法/工具
判定标准
不良等级 CR MA MI
√
收。
尺寸
依据承认书/ 样品
5PCS
目视/游标卡尺
尺寸须与承认书及样品标示尺 寸相符。
√
1.上锡面须光亮、平滑、上锡
面大于95%,OK;不吃锡则不可
1.可焊性
性能
2.容值/DF值 3.漏电流
4.耐压
5PCS
1.锡炉260±5℃ /3~5S); 2.LCR数字电桥 3.漏电测试仪 4.耐压测试仪
接收; 2.容值及DF值须符合承认书规 格值; 3.漏电流须与承认书规格值相 符;
℃检测的电阻值)
1.厂商出货 报告 附件 2.样品SGS报 一份 告(限样 品)
IQC进料检验作业规范(含表格)
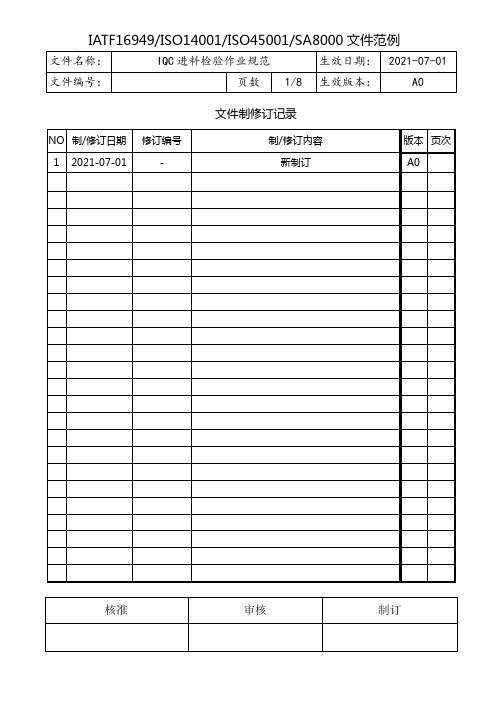
文件制修订记录1.0目的为管制采购物料品质,使其符合设计规格及允收品质水准。
2.0范围凡本公司采购物料或本公司自制加工产品均适用。
3.0权责单位3.1品管部负责本规定制定、修改、废止之起草工作。
3.2总经办负责本规定制定、修改、废止之核准。
3.3作业部门:品管部IQC。
4.0检验规定4.1抽样计划依据MIL-STD-105E单次取样计划。
4.2品质特性品质特性分为一般特性和特殊特性。
4.2.1一般特性符合下列条件之一者属一般特性4.2.1.1检验工作容易者,如外观特性4.2.1.2品质特性对产品品质有直接而重大之影响者4.2.1.3品质特性变异大者4.2.2特殊特性符合下列条件之一者属特殊特性4.2.2.1检验工作复杂,费时或费用高者4.2.2.2品质特性可由其他特性之检验参考判断者4.2.2.3品质特性变异小者4.2.2.4破坏性之试验4.3检验水准4.3.1一般特性采用MIL-STD-105E正常单次抽样一般II级水准。
4.3.2特殊特性采用MIL-STD-105E正常单次抽样特殊S-2级水准。
4.4缺陷等级抽样检验中发现之不符品质标准之瑕砒,称为缺陷,其等级有下列三种:4.4.1致命缺陷(CR)4.4.2主要缺陷(MAJ)不能达成支配的使用目的之缺陷,称为主要缺陷,或重缺陷,MAJ表示。
4.4.3次要缺陷(MIN)并不影响支配使用目的之缺陷,称为次要缺陷或轻微缺陷,用MIN表示4.5允收水准(AQL)4.5.1AQL定义AQL即Acceptable Quality Leval,是何以接收的品质不良比率的上限,也称为允许接收品质水准,简称允收水准。
4.5.2允收水平本公司对进料检验时个缺陷等级之进料允收水准为:4.5.2.1CR缺陷,AQL=04.5.2.2 MAJ缺陷,AQL=0.4%,具体按分类物料检验规范之要求4.5.2.3MIN缺陷,AQL=1.5%进料允收水准应严于或同于客户对成品的允收水准,因此,如客户对成品的允收水准高于上述标准,应以客户标准为依据。
IQC进料检验作业规范(A版)

IQC进料检验作业规范1目的为了确保公司采购的所有原材料、外协件、装配件等能够满足生产及客户要求,保证生产秩序的顺利进行,特制定本程序。
2 适用范围适用于生产用原材料、外协件、外购装配件等。
3 定义3.1按MIL-STD-105E LEVELII:抽样计划表。
外观检查按一般检验水准II级,尺寸按5件/每批抽样。
3.2 AQL:即品质允收水准;批量:同一时间收货的整体数量作为一个检查批;样本:即从批量中批取一定数量为本体作业为检查对象。
3.3致命缺陷:在使用过程中会导致人体触电、伤害等致命缺陷3.4主要缺陷:在正常使用或安装下不能发挥其本身特有功能或会降低其本身可靠性的缺陷。
3.5 次要缺陷:发挥了其本身性能作用,便在外观表面上影响客户或顾客感观的轻微缺陷。
3.6 重工:生产原材料、半成品、外协件因有瑕疵或不良超出允收水平而判拒收,针对此批物料做出相应改善返修处理动作。
4 职责4.1 IQC负责人负责本文件的完善和执行,并为检验员提供必要的培训、技术支持及不良处理/追踪,供应商的评估及辅导。
4.2 IQC检验员负责来料检查,填写检查报告并对进料进行相应的标识。
5作业流程5.1 采购:按照计划及品质要求采购相应的物料。
5.2仓库保管员按采购计划接受物料进货,挂上标识卡,写明货名、规格、数量、进货批号,并通知质量部检验员对物料进行检查。
5.3 IQC在收到送检单后到仓库暂存物料的区域按AQL要求抽取样本执行检验作业。
抽样前先确认样品规格型号是否与报检物料一致,否则可拒绝抽检并及时反馈仓库、采购等相关人员。
5.4检验前需根据报检物料核对相应图纸、检验作业指导书、客户要求、检具量仪等,然后执行检验作业。
5.5 检验员完成所有检验项目,判定合格后认真填写《进料检验记录表》并给主管签字确认并将样品归还给仓库。
同时在报检单上签字后送还仓库并对合格物料标示合格标签;仓库保管员看到合格标识后方可办理入库手续。
5.6 检验员检验物料不合格或在检验过程中发现异常时及时知会QE确认并做出物料合格与否的判定,必要时由QE联络PE共同分析确认。
IQC物料检验规范

IQC物料检验规范1. 引言IQC(Incoming Quality Control)是指对进货物料进行检验的过程,旨在确保所采购的物料符合公司的质量要求和标准。
本文档旨在制定IQC物料检验的规范,以确保物料的质量稳定和公司产品的质量可控性。
2. 检验流程IQC物料检验包括以下步骤:1.接收:接收进货物料,并记录物料的数量和批次信息。
2.样品抽检:从接收到的批次中随机抽取样品进行检验。
3.检验项目确定:根据物料的特性和要求,确定适用的检验项目。
4.检验方法制定:制定具体的检验方法和标准。
5.检验执行:按照检验方法和标准执行检验。
6.检验结果记录:记录检验结果,包括合格品数量、不合格品数量及具体不合格项。
7.判定与处理:根据检验结果判定物料的合格性,并对不合格品进行处理。
8.报告与存档:生成检验报告,并将报告存档。
3. 物料分类和检验要求根据物料的特性和要求,将物料分为以下几类,并对各类物料的检验要求进行规范。
3.1 原材料类原材料是产品制造过程中的基础材料,对产品的质量和稳定性具有重要影响。
对原材料的检验要求如下:•外观检验:检查原材料外观是否符合要求,如有伤痕、污染等。
•尺寸检验:测量原材料的尺寸是否符合要求。
•化学成分检验:对原材料进行化学成分分析,确保成分符合要求。
•物理性能检验:对原材料进行物理性能测试,如抗拉强度、硬度等。
3.2 零部件类零部件是产品的组成部分,对产品的功能和性能起着重要作用。
对零部件的检验要求如下:•外观检验:检查零部件外观是否有缺陷、变形等。
•尺寸检验:测量零部件的尺寸是否符合要求。
•材料检验:对零部件的材料进行检验,确保材料质量合格。
•组装及连接检验:检查零部件的组装及连接情况是否正确、牢固。
3.3 包装材料类包装材料是产品运输和保护的重要环节,对产品的外观和完整性影响较大。
对包装材料的检验要求如下:•外观检验:检查包装材料外观是否完好,如有破损、污渍等。
•尺寸检验:测量包装材料的尺寸是否符合要求。
- 1、下载文档前请自行甄别文档内容的完整性,平台不提供额外的编辑、内容补充、找答案等附加服务。
- 2、"仅部分预览"的文档,不可在线预览部分如存在完整性等问题,可反馈申请退款(可完整预览的文档不适用该条件!)。
- 3、如文档侵犯您的权益,请联系客服反馈,我们会尽快为您处理(人工客服工作时间:9:00-18:30)。
8.6 《供應商品質排行榜》 8.5.1 統計每月各供應商進料品質結果。 8.5.2 品質月報中 IQC 的附屬統計報表。
8.5.3 制式表單﹐使用電子檔。 9. 檢驗流程
供應商來料 → 資材點收 NG 退回供應商﹐OK 收貨單通知 IQC 檢驗 → IQC 檢驗員依據收 貨單核對實物與來料是否相符﹐依據《抽樣檢驗作業指導書》進行抽樣檢驗﹑相關資料、 規定、樣本進行檢驗 → 檢驗員填寫《進料檢驗結果報告表》→檢驗合格由班、組長確認 再由課長審核 →檢驗不合格時由品質工程師確認(如異常為尺寸或功能不良) →品檢班、 組長確認再由課長審核 → 品工經理核准→如品工經理判定不合格且資材部需求不急用則 確認退貨 → 如資材部需求急用開出<MRB 申請單>(系統單)《特采作業規范》→ (依序)由 生產資材部﹑品工部進行 MRB 會簽→ 最終結果由廠管理者代表核准。 10.檢驗時效:急件材料 1-3 檢驗完,不急材料 3-5 天之內檢驗完入庫,一天連續進料 40 批以 上﹐7 天之內檢驗完畢﹐遇到特殊情況除外。
核准
審核
制作
日期
文件編號
IQC 進料檢驗作業規范
版次
A0
頁次
第6頁 共6頁
責任者
資材
品保
進料檢驗流程圖
使用表單/ 文件/说明
供应商來料 ooug
NG
資材收料
OK 待检区
收貨單
IQC 检验
OK 記錄/標示
QC 檢驗結 果報告表
品保/工程 生産/資材
NG 物料是否急用
品保/工程
NG 不急用 急用
MRB 申請單
8.2 《廠商品質改善報告》 8.2.1 進料檢驗已經品保經理判定“拒收”時即需填出﹐不論 MRB 處理結果。 8.2.2 經部門主管核准後即可發出給供應商。 8.2.3 SQE 負責追蹤﹑收回及結案。
核准
審核
制作
日期
文件編號 8.3 檢驗狀態標籤﹕
IQC 進料檢驗作業規范
版次
A0
頁次
第4頁 共6頁
直接上线标签是绿色底(Φ3x3cm)
核准
審核
制作
日期
文件編號
IQC 進料檢驗作業規范
版次
A0
頁次
第5頁 共6頁
8.4 《進料檢驗月報表》 8.3.1 用於統計每月進料檢驗結果。 8.3.2 品質月報中 IQC 的附屬統計報表。 8.3.3 制式表單﹐使用電子檔。
8.5 《IQC 品質記錄維護作業》 8.4.1 限用於原材料﹑外包半成品﹑成品之進料檢驗結果報告。 8.4.2 此為 ERP 入庫表單﹐不列印。
文件編號
IQC 進料檢驗作業規范
版次
A0
頁次
第1頁 共6頁
1. 目的﹕ 為使進料檢驗作業標準化﹐以確保進料符合本公司品質要求。
2. 範圍﹕ 凡與本公司產品品質相關的原材料﹑半成品﹑成品﹑外包品﹑間接物料等﹐進料檢驗作 業均適用之。
3. 抽樣計劃 3.1 採 ANSI-ASQZ1.4-2008 一般檢驗水準 II 級 (適用於外觀﹑電氣功能項目)。 3.2 尺寸機構檢驗每批次抽取樣品 10 pcs。 3.3 破壞性試驗正常(下述除外)取 10PCS/批進行破壞性驗証 3.3.1 電感(L)取 AQL 樣的一半/批進行破壞性驗証 3.3.2 高分子電容取樣 30PCS/批進行破壞性驗証 3.3.3 MLCC 取樣 50PCS/批進行破壞性驗証 3.3.4 電阻(R)取樣 50PCS/批進行破壞性驗証 3.3.5 比較器 TL432﹑TL431 取樣 10PCS/批作低溫試驗 3.3.6 IC 3843﹑555 做到半成品上取樣 10PCS/批作低溫試驗 3.3.7 電晶體取樣 10PCS/批進行破壞性驗証 3.4 全檢 (適用於外包裝檢驗﹐及特殊物料檢驗﹐例如: 網板類)。
重工 項目: 檢驗日期: 年 月 日 檢 驗 員:
重工标签是橙色底(Φ3x3cm)
禁用 項目: 禁用日期: 年 月 日 檢 驗 員:
拒收标签是红色底(Φ3x3cm)
緊急放行
內聯單號: 檢 驗 員: 放行日期:
緊急放行标签是白色底(3x7cm)
禁用标签是红色底(Φ3x3cm)
直接上线 項目: 檢驗日期: 年 月 日 檢 驗 員:
4.9 包裝盤功能檢驗每批進料試裝 5PCS。 5.0 包裝帶功能檢驗每批進料試作 1 卷 。 5.1 化工膠類功能檢驗按批量檢驗﹕
批量從 1~~~~~~50 桶﹐抽檢樣本量為 2 桶﹔ 批量從 51~~~~~~100 桶﹐抽檢樣本量為 4 桶﹔ 批量從 100 桶以上﹐抽檢樣本量為 2%比例進行抽檢﹔ 5.2 包裝紙箱功能檢驗每批進料試裝 5PCS。 5.3 進料箱抽樣要求﹕ 5.3.1 進料 5 箱以內(包括 5 箱)﹐全部開箱取樣。 5.3.2 進料 6~10 箱(包括 10 箱)﹐需開 7 箱取樣。 5.3.3 進料 11~15 箱(包括 15 箱)﹐需開 9 箱取樣。 5.3.4 進料 16 箱以上﹐需開 12 箱取樣。 5.3.5 IQC 針對已開箱取樣之外箱,需使用藍色封箱膠帶進行標示。如下圖:
核准
審核
制作
日期
IQC 進料檢驗作業規范
文件編號
版次
A0
頁 次 第2頁 共6頁
4.6 外包鐵芯繞線功能檢驗按批量檢驗: 批量從 1~~~~100KPCS﹐抽檢樣本量為 50PCS﹔ 批量從 100001~~~~1000KPCS﹐抽檢樣本量為 100PCS﹔ 批量從 1000K 以上 PCS﹐抽檢樣本量為 150PCS﹔
6.4 電氣功能:以儀器設備依各材料/產品之功能需求進行測試檢驗。 7. 檢驗設備
依據作業規范所要求的檢驗設備。 8. 使用表單、標示
8.1 《進料檢驗結果報告表》 8.1.1 每批進料檢驗均需填寫此報告表。 8.1.2 檢驗結果為“允收”時﹐由課級主管核准。 8.1.3 檢驗結果“拒收”時﹐由理級主管核准。 8.1.4 不合格材料急用時﹐依《不合格品管理程序》(MRB)進行會簽。 8.1.5 每批材料檢驗完成后將結果輸入 ERP 系統
4.7 漆包線檢驗按批量檢驗﹕ 批量從 1~~~~~100 卷﹐抽檢樣本量為 10 卷﹔ 批量從 101~~~~~200 卷﹐抽檢樣本量為 20 卷﹔ 批量 200 卷以上﹐抽檢樣本量按 10%比例進行抽檢﹔
4.8 包裝管功能檢驗按批量檢驗﹕ 批量從 1~~~~~~5000PCS,抽檢樣本量為 10PCS﹔ 批量從 50001~~~~~~10000PCS,抽檢樣本量為 20PCS﹔ 批量從 10001~~~~~~15000PCS,抽檢樣本量為 30PCS﹔ 批量從 15000PCS 以上,抽檢樣本量為 40PCS。
核准
審核
制作
日期
文件編號
IQC 進料檢驗作業規范
版次
A0
頁次
5. 檢驗依據 5.1 《承認樣品》 5.2 《進料檢驗基準書》 5.3 《材料承認書》 5.4 《抽樣檢驗作業指導書》
第3頁 共6頁
6. 檢驗方法 6.1 外觀﹕以放大鏡﹑顯微鏡﹑目視(距離 30cm) 檢驗。 6.2 尺寸﹕以數顯卡尺﹑千分尺﹑塞規﹑投影機﹑治具等量具檢驗。 6.3 機構: 依相關之規定、指導書等進行檢驗﹐如試組裝。
退
回
品保/工程 供
重
生産/資材 应
工
商
NG
挑 OK 选
特采/記錄/標示
MRB 申 請單
NG
IQC 重检
OK
入库 ooug
核准
審核
制作
日期
特采 項目: 檢驗日期: 年 月 日 檢 驗 員:
挑选 項目: 檢驗日期: 年 月 日 檢 驗 員:
特采标签是黄色底(Φ3x3cm)
允收 檢驗日期: 年 月 日 檢 驗 員: 再驗日期: 年 月 日
允收标签是绿色底(Φ3x3cm)
拒收 項目: 檢驗日期: 年 月 日 檢 驗 員:
挑选标签是浅蓝色底(Φ3x3cm)