Key Characteristics Designation System - KCDS
KCDS
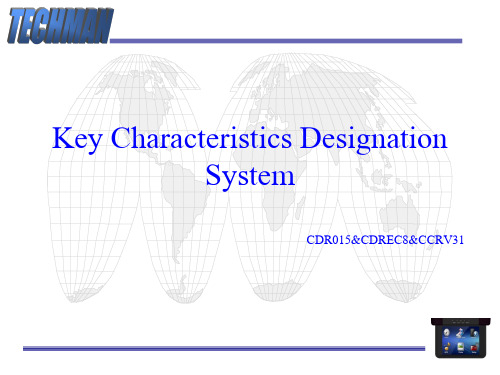
1. 作業員戴防靜電手套 2. 作業員戴防靜電手環 3. 作業員的防靜電手環 需要時時監控 4. 電動起子的接地電阻/ 交直流電壓,每天檢測一 次. 5. 工作臺面有防靜電措 施,並且每周測量一次. 6. 此站為重點工位,並且 有明確的標示. 7. 在Flow char/Control plan上注明重點工位.
組裝
83243015003R1
82543015005R1
小板
SFC
82543015001R1
主板
SFC
82543015002R1
前面板ห้องสมุดไป่ตู้
SFC
82543015004R1
GPS板
SFC
1. 上料作業員戴防靜電手套作業 2. 使用周轉用的防靜電托盤. 3. 防靜電托盤上注明料號
1. 上料作業員戴防靜電手套作業 2. 使用周轉用的防靜電托盤. 3. 防靜電托盤上注明料號 1. 上料作業員戴防靜電手套作業 2. 使用周轉用的防靜電托盤. 3. 防靜電托盤上注明料號
Key Characteristics Designation System
CDR015&CDREC8&CCRV31
Key Characteristics Designation System Diagram
Parts Require Additional Care
CDR015重要零部件
料號
中文 名稱
CPK≧1.67
影响产品 功能
♁♁
检验/cpk
♁♁
1.CPK/GR&R 2.爐溫參數測量
CPK≧1.67
影响产品 功能
CD 頻率 響應
♁♁
检验/cpk
♁♁
《关键产品特性(KCDS)的识别与传递》-20131105-杨佳音付艳玲

关键产品特性(KCDS)的识别与传递工程质量部2013.11.05⏹讲师生活照⏹姓名:杨佳音⏹部门/科室:工程质量部/开发质量科⏹联系电话: 021-********(办公电话)⏹E-mail: yangjiayin @⏹主要职责:DFMEA、DFSS、KCDS等质量工具的推广与应用⏹讲师生活照⏹姓名:付艳玲⏹部门/科室:工程质量部/开发质量科⏹联系电话: 021-********(办公电话)⏹E-mail: fuyanling@⏹主要职责:DFMEA、DFSS、KCDS等质量工具的推广与应用通过学习本课程,您将掌握:Know-What Know-WhyKnow-When Know-WhereKnow-How四.SMTC 的KCDS 相关文档 一.KCDS 的定义二.KCDS 的目的三.KCDS 标识与传递的工作流程 五.KCDS 识别方法第一部分KCDS的定义第二部分KCDS的目的第三部分KCDS标识与传递的工作流程第四部分SMTC的KCDS相关文档第五部分KCDS识别方法特性:在工程技术资料中所描述的零部件或总成的性质,如尺寸、材质、性能等。
属性特性:可被测量或检查并且结果是Yes/No 的产品特性,离散分布数据。
变量特性:可用恒定度量衡测量的产品特性,连续分布数据。
什么是关键特性?体系:体落实有物质保障和有具体工作内容的有机整体,应明确有关部门和人员的职责和权力,以及规定完成任务所必需的各项程序和活动。
如:工作流程,规范、记录等。
Designation :指示、指定、标名。
应区别于Identification产品特性特殊产品特性一般产品特性属性特性AQC变量特性VQC产品可追溯性TRA安全相关SAF法规要求COM选装防错ERP特殊零部件处理SCH功能检查FCKPCPQCKCCKey Characteristic Designation System,关键特性识别系统。
是一个用于统一上汽内部及供应商标识、记录、传递产品“需要特殊关注的产品特性”的工作流程。
SGM供应商质量要求

2006 年 5 月 23 日
2006 年 5 月 23 日
Page 1 of 30
仅限 SGM 及供应商内部使用,不能擅自复制、转发!
上海通用汽车对供应商质量要求的规定
(2006 年 5 月版)
主要修订记录
2004 年 10 月,第一版制订
2005 年 6 月主要修订内容: 1. SGM 供应商质量声明参考 GM2005 年 3 月版本更新,并增补 SGM 对
3. General Motors Procedures and Reference Documents: 通用汽车的程序和参考文件:
• Suppliers are to adhere to the requirements contained in the following documents:
ITEZ1401H – KCDS Manual for ITDC Application ITEZ1401H– ITDC 应用 KCDS 手册
GP-5 Supplier Quality Processes and Measurements Procedure. GM-1746 GP-5 供应商质量过程和测量程 序 GM-1746
painting or other finishing services directly to Shanghai General Motors must be certified to ISO/TS 16949 or QS-9000 and have a current certificate available demonstrating compliance to GM supplements. All suppliers should migrate to ISO/TS 16949 at the expiration of their current QS9000 certificate but before December 14, 2006.. 所有向通用直接提供a)生产材料,b)生产或服务件,或c)热处理、涂镀、油漆或其他最终服务的供应 商必须通过ISO/TS 16949 或QS-9000 标准的认证, 并且取得相应证书。在现行的QS9000 证书 2006 年 12 月 14 日到期之前,所有供应商应该通过ISO/TS16949 认证。
《关键产品特性(KCDS)的识别与传递》-20131105-杨佳音付艳玲

关键产品特性(KCDS)的识别与传递工程质量部2013.11.05⏹讲师生活照⏹姓名:杨佳音⏹部门/科室:工程质量部/开发质量科⏹联系电话: 021-********(办公电话)⏹E-mail: yangjiayin @⏹主要职责:DFMEA、DFSS、KCDS等质量工具的推广与应用⏹讲师生活照⏹姓名:付艳玲⏹部门/科室:工程质量部/开发质量科⏹联系电话: 021-********(办公电话)⏹E-mail: fuyanling@⏹主要职责:DFMEA、DFSS、KCDS等质量工具的推广与应用通过学习本课程,您将掌握:Know-What Know-WhyKnow-When Know-WhereKnow-How四.SMTC 的KCDS 相关文档 一.KCDS 的定义二.KCDS 的目的三.KCDS 标识与传递的工作流程 五.KCDS 识别方法第一部分KCDS的定义第二部分KCDS的目的第三部分KCDS标识与传递的工作流程第四部分SMTC的KCDS相关文档第五部分KCDS识别方法特性:在工程技术资料中所描述的零部件或总成的性质,如尺寸、材质、性能等。
属性特性:可被测量或检查并且结果是Yes/No 的产品特性,离散分布数据。
变量特性:可用恒定度量衡测量的产品特性,连续分布数据。
什么是关键特性?体系:体落实有物质保障和有具体工作内容的有机整体,应明确有关部门和人员的职责和权力,以及规定完成任务所必需的各项程序和活动。
如:工作流程,规范、记录等。
Designation :指示、指定、标名。
应区别于Identification产品特性特殊产品特性一般产品特性属性特性AQC变量特性VQC产品可追溯性TRA安全相关SAF法规要求COM选装防错ERP特殊零部件处理SCH功能检查FCKPCPQCKCCKey Characteristic Designation System,关键特性识别系统。
是一个用于统一上汽内部及供应商标识、记录、传递产品“需要特殊关注的产品特性”的工作流程。
GM质量体系的英文缩写
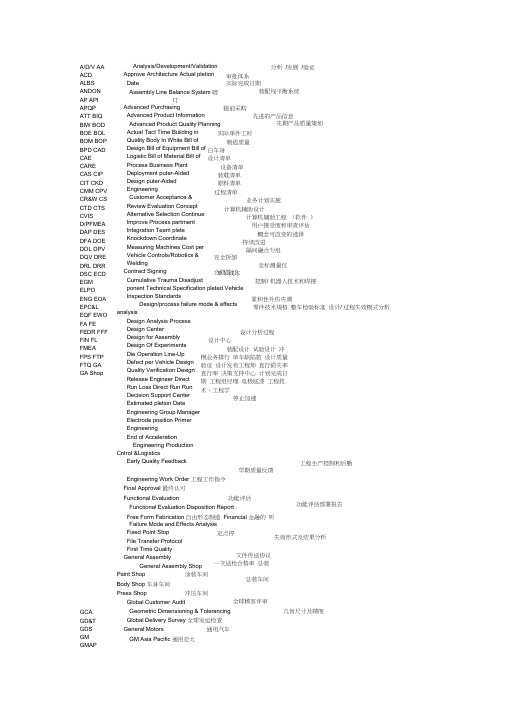
Analysis/Development/Validation Approve Architecture Actual pletion Date Assembly Line Balance System 暗灯 Advanced Purchasing Advanced Product Information Advanced Product Quality Planning Actual Tact Time Building in Quality Body In White Bill of Design Bill of Equipment Bill of Logistic Bill of Material Bill of Process Business Plant Deployment puter-Aided Design puter-Aided Engineering Customer Acceptance & Review Evaluation Concept Alternative Selection Continue Improve Process partment Integration Team plete Knockdown Coordinate Measuring Machines Cost per Vehicle Controls/Robotics & Welding Contract Signing Cumulative Trauma Disadjust ponent Technical Specification pleted Vehicle Inspection Standards Design/process failure mode & effects analysis Design Analysis Process Design Center Design for Assembly Design Of Experiments Die Operation Line-Up Defect per Vehicle Design Quality Verification Design Release Engineer Direct Run Loss Direct Run Run Decision Support Center Estimated pletion Date Engineering Group Manager Electrode position Primer Engineering End of Acceleration Engineering Production Cntrol &Logistics Early Quality Feedback 早期质量反馈 Engineering Work Order 工程工作指令 Final Approval 最终认可 Functional Evaluation 功能评估 Functional Evaluation Disposition Report Free Form Fabrication 自由形态制造 Financial 金融的 听 Failure Mode and Effects Analysis Fixed Point Stop File Transfer Protocol First Time Quality General Assembly General Assembly Shop Paint Shop 涂装车间 Body Shop 车身车间 Press Shop 冲压车间 Global Customer Audit Geometric Dimensioning & Tolerancing 几何尺寸及精度 Global Delivery Survey 全球发运检查 General Motors 通用汽车 GM Asia Pacific 通用亚太 A/D/V AAACDALBSANDONAP APIAPQPATT BIQBIW BODBOE BOLBOM BOPBPD CADCAECARECAS CIPCIT CKDCMM CPVCR&W CSCTD CTSCVISD/PFMEADAP DESDFA DOEDOL DPVDQV DREDRL DRRDSC ECDEGMELPOENG EOAEPC&LEQF EWOFA FEFEDR FFFFIN FLFMEAFPS FTPFTQ GAGA Shop分析 /发展 /验证 审批体系 实际完成日期 装配线平衡系统 提前采购 先进的产品信息 先期产品质量策划 实际单件工时 制造质量 白车身 设计清单 设备清单 装载清单 原料清单 过程清单 业务计划实施 计算机辅助设计 计算机辅助工程 (软件 ) 用户接受度和审查评估 概念可改变的选择 持续改进 隔间融合为组 完全拆缷 单车成本 坐标测量仪 控制/ 机器人技术和焊接 累积性外伤失调 零件技术规格 整车检验标准 设计/ 过程失效模式分析GCAGD&TGDSGMGMAP 设计分析过程 设计中心 装配设计 试验设计 冲模业务排行 单车缺陷数 设计质量验证 设计发布工程师 直行损失率 直行率 决策支持中心 计划完成日期 工程组经理 电极底漆 工程技术、工程学 停止加速 工程生产控制和后勤 功能评估部署报告 失效形式及结果分析 文件传送协议 一次送检合格率 总装 总装车间 合同签订 定点停 全球顾客评审General Motors Europe General Motors International Operations General Motors Initial Quality General Motors Powertrain Group Global Manufacturing System General Procedure 通用程序 Global Quality Tracking System 全球质量跟踪系统 Global Strategy Board 全球战略部 Heating, Ventilation ,and Air Conditioning Instrument Panel 仪表板 Initiate Charter 初始租约 Interface Control Document Industrial Engineering International Export Market Analysis Indirect Labor Reporting System International Operations Inspection Operation Mathod Inspection Operation Summary International Product Center Incidents Per Thousand Vehicles Initial Quality Survey Incident Report 事故报告 Integrated Scheduling Project Integrated Training Process Interior Technical Specification Drawing International Uniform Vehicle Audit Job Element Sheet Job Issue Sheet Just in Time Job per hour Key Control Characteristics Key Characteristics Designation System Key product Characteristic Look at 看 Metal Fabrication Division Manufacturing Operations Marketing Information Center Manufacturing Integration Engineer Marketing 营销 Material Labor Balance System Manufacturing Major Subsystem Technical Specifications Manufacturing Engineering Milford Proving Ground Master Process Index Master Parts List Material Planning System Material Required Date Material Safery Data Sheets Manufacturing System Engineer Market Segment Specification Mean Time Between Failures Manufacturing Technical Specification Motor Vehicle Safety Standards North American Market Analysis North American Operations NAO Containerization Numerically Controlled Notice of Authorization NAO Strategy Board Organization and Employee Development组织和员工发展Occupational Safety & Health 职业安全健康Occupational Safety & Health Act 职业安全与健康法案Occupational Safety & Health Management System 职业安全健康管理体系 Occupational Safety & Health Standards 职业安全标准Production Achievement 生产结果Product Action Authorization 产品临时授权Performance Assessment mittee 绩效评估委员会Program Assessment and Control Environment 项目评估和控制条件 Product Assembly Document 产品装配文件Part Readiness Tracking System 零件准备跟踪系统 Problem munication 问题信息 GMEGMIOGMIQGMPTGGMS GPGQTSGSBHVACI/P ICICD IEIEMAILRS IOIOM IOSIPCIPTVIQS IRISP ITPITSDIUVAJES JISJIT JPHKCCKCDSKPC LTMFDMFGMIC MIEMKTMLBSMMSTSMNGMPGMPIMPLMPSMRDMSDSMSEMSSMTBFMTSMVSSNAMANAONAOCNC NOANSBOEDOSHOSHAOSHMSOSHSPA PAAPACPACEPADPARTSPC 通用汽车欧洲 通用汽车国际运作 通用汽车初始质量 通用汽车动力组 通用全球制造系统 界面控制文件 工业工程 加热、通风及空调 国际出口市场分析 间接劳动报告系统 国际业务 检验操作方法 检验操作概要 国际产品中心 每千辆车的故障率 初始质量调查 综合计划 综合培训方法 内部技术规范图 国际统一车辆审核 工作要素单 工作要素单 准时制 每小时工作量 关键控制特性 关键特性标识系统 关键产品特性 金属预制件区 制造过程 市场信息中心 制造综合工程师 物化劳动平衡系统 北美业务部制造重要子系统技术说明书制造工程 试验场 主程序索引 主零件列表 原料计划系统 物料需求日期 化学品安全数据单 制造系统工程 市场分割规范 平均故障时间 生产技术规范 汽车发动机安全标准 北美市场分析 北美业务 NAO 货柜运输 用数字控制 授权书Production Control and Logistics Process Control Manager Problem munication Report Portfolio Development Center Product Data Management Product Description System Product Development Team Production Engineering Department Product Evaluation Program Personnel 人员 Program Execution Team Program Management People Involement Project Incident Monitoring and Resolution Process Production Launch Process 生产启动程序 Process Modeling Integration 加工建模一体化 Program Manufacturing Manager 项目制造经理 Product Manufacturability Requirements 产品制造能要求 Product Management Team 产品车管理小组 Production Order Management System 产品指令管理小组 Point of Purchase Push - Pull 推拉 Production Part Approval Process 个人防护用品 Problems Per Hundred Problems Per Million Practical Problem Solving Performance Review Problem Reporting and Resolution Problem Resolution Portfolio Strategy Council Plant Support Team Primary Tryout Production Trial Run Purchasing Production Vehicle Development Programmable Vehicle Model Quality Audit 质量评审 Quality Assessment Process Quality Build Concern Quality Characteristic Quality Control Operation Sheets Quality Engineering Team Quality Function Deployment Quality, Reliability,andDurability Quality System 质量体系 Quality 质量 Review Charter 评估特许 Required pletion Date Request For Quotation Reliability Growth Management Return on Net Assets Regular Production Option Routing Quality Assessment Rigorous Tracking and Throughout Managment 严格跟踪和全程管理 Strategic Decision Center 战略决策中心Styling Freeze 造型冻结Single Issue List 单一问题清单Stansardized Inspection Process 标准化检验过程Summing It All Up 电子求和结束System Layouts 系统规划Short Leading Team 缩短制造周期Synchronous Math-Based ProcessSubject Matter Expert Systems Management Team 坏路实验 Start of Production Safe Operating Practice Statementof Requirements PCLPCMPCRPDCPDMPDS PDTPED PEPPER PETPGM PIPIMREPPLP PMIPMMPMRPMTPOMSPOP PPPPAPPPE PPHPPMPPS PRPR/RPRTSPSC PSTPTO PTRPURPVDPVM QAQAPQBC QCQCOSQE QETQFDQRD QSQUA RCRCDRFQRGMRONARPORQART&TMSDC SFSIL SIPSIU SLSLTSMARTSMBPSMESMTSNRSOPSOPSOR 生产控制和支持 工艺控制负责人 问题交流报告 证券发展中心 产品资料管理 产品说明系统 产品发展小组 产品工程部 产品评估程序 项目执行小组 项目管理 人员参与 采购点 百辆车缺陷数 百万辆车缺陷数 实际问题解决 绩效评估 生产零部件批准程序 事故方案跟踪和解决过程 问题报告和解决 and Tracking System 问题解决跟踪系统 部长职务策略委员会 工厂支持小组 第一次试验 生产试运行 采购 Quality Engineer 质量工程师 生产汽车发展 可设计的汽车模型 质量评估过程 质量体系构建关系 质量特性 质量风险控制 质量工程小组 质量功能配置 质量、可靠性和耐久力 必须完成日期 报价请求 可靠性增长小组净资产评估 正式产品选项程序安排质量评定理论同步过程主题专家系统管理小组生产启动安全操作规程技术要求Standardization Operation Sheet Statement of Work 工作说明 Shipping Priority Audit 发运优先级审计 Statistical Process Control 统计过程控制 Surface and Prototype Engineering 表面及原型工程 Service Parts Operations 配件组织 Single Point Team 专一任务小组 Supplier Quality Assurance 供应商质量保证(供应商现场工程师) Supplier Quality Control 供方质量控制 Supplier Quality Development 供应方质量开发 Supplier Quality Engineer 供方质量工程师 Supplier Quality Improvement Process 供应商质量改进程序 Start of System Fill 系统填充 Subsystem Leadership Team 子系统领导组 Subsystem Technical Specification 技术参数子系统 Standardization 标准化 Secondary Tryout 二级试验 安全作业指导书 Standard Unit of Work Simulated Work Environment Timing Analysis Group To Be Determined Traction Control System Technology Development Centre Text Data Management Facility Tooling 工具 Test Incident Management System Test Incident Report Total Manufacturing Integration Engineer Total Ownership Experience Total Production Maintenance Trade Study Methodology Tact Time 单件工时 Total Vehicle Dimensional Engineer Total Vehicle Integration Engineer Tire and Wheel System United Auto Workers Uniform Criteria List Unverified Data Release Uniform Parts Classification Vehicle Assembly Engineer Vehicle & Progress Integration Review Team 汽车发展综合评审小组 Vehicle Assembly Standard Time Data 汽车数据标准时间数据 Vehicle Chief Designer 汽车首席设计师 Vehicle Chief Engineer 汽车总工程师 Validation Cross-Reference Index 确认交叉引用索引 Vehicle Development Process 汽车发展过程 Vehicle Development Production Process 汽车发展生产过程 Verified Data Release 核实数据发布 Vehicle Description Summary 汽车描述概要 Vehicle Development Team 汽车发展组 Vehicle Development Technical Operations Vehicle Engineering Center Vehicle Integration Engineer Vehicle Identification Number Vehicle Information System Vehicle Line Executive Vehicle Launch Manager Vehicle and Manufacturing Requirements Review Voice of Customer 顾客的意见 Voice of Design 设计意见 Validation Station 确认站 Vehicle Synthesis,Analysis,and Simulation Vehicle System Engineer 汽车系统工程师 Vehicle Technical Specification 汽车技术说明书 Worldwide Benchmarking and Business Analysis 全球基准和商业分析Wide Open Throttle 压制广泛开放Work Place Organization 工作场地布置 Worldwide Purchasing 全球采购SOSSOWSPASPCSPESPOSPTSQASQCSQDSQESQIPSSFSSLTSSTSSTDSTOSUISUWSWETAGTBDTCSTDCTDMFTGTIMSTIRTMIETOETPMTSM TTTVDETVIETWSUAWUCLUDRUPCVAEVAPIRVASTDVCDVCEVCRIVDPVDPPVDRVDSVDTVDTOVECVIE VINVIS VLEVLMVMRRVOCVOD VSVSASVSEVTSWBBAWOTWPOWWP 标准化工作操作单 标准工作单位 模拟工作环境 定时分析组 下决定 牵引控制系统 技术中心 文本数据管理设备 试验事件管理系统 试验事件报告 总的制造综合工程 总的物主体验 全员生产维护 贸易研究方法 整车外型尺寸工程师 整车综合工程师 轮胎和车轮系统 班组 统一的标准表 未经核对的资料发布 统一零件分级 车辆装配工程师 汽车发展技术工作 汽车工程中心 汽车综合工程师 车辆识别代码 汽车信息系统 总装线主管 汽车创办经理 汽车制造必要条件评审 汽车综合、分析和仿真MWIP Correction 纠错浪费过量生产浪费 过度物料移动浪费 过度移动浪费 等待浪费 过度库存浪费 过度加工浪费 Overproduction Material Flow Motion WaitingInventoryProcessing。
GM质量体系的英文缩写

A/D/V Analysis/Development/Validation分析/发展/验证AA Approve Architecture审批体系ACD Actual Completion Date实际完成日期ALBS Assembly Line Balance System装配线平衡系统ANDON暗灯AP Advanced Purchasing提前采购API Advanced Product Information先进的产品信息APQP Advanced Product Quality Planning先期产品质量策划ATT Actual Tact Time实际单件工时BIQ Building in Quality制造质量BIW Body In White白车身BOD Bill of Design设计清单BOE Bill of Equipment设备清单BOL Bill of Logistic装载清单BOM Bill of Material原料清单BOP Bill of Process过程清单BPD Business Plant Deployment业务计划实施CAD Computer-Aided Design计算机辅助设计CAE Computer-Aided Engineering计算机辅助工程(软件)CARE Customer Acceptance & Review Evaluation用户接受度和审查评估CAS Concept Alternative Selection概念可改变的选择CIP Continue Improve Process持续改进CIT Compartment Integration Team隔间融合为组CKD Complete Knockdown完全拆缷CMM Coordinate Measuring Machines坐标测量仪CPV Cost per Vehicle单车成本CR&W Controls/Robotics & Welding控制/机器人技术和焊接CS Contract Signing合同签订CTD Cumulative Trauma Disadjust累积性外伤失调CTS Component Technical Specification零件技术规格CVIS Completed Vehicle Inspection Standards整车检验标准D/PFMEA Design/process failure mode & effects analysis设计/过程失效模式分析DAP Design Analysis Process设计分析过程DES Design Center设计中心DFA Design for Assembly装配设计DOE Design Of Experiments试验设计DOL Die Operation Line-Up冲模业务排行DPV Defect per Vehicle单车缺陷数DQV Design Quality Verification设计质量验证DRE Design Release Engineer设计发布工程师DRL Direct Run Loss直行损失率DRR Direct Run Run直行率DSC Decision Support Center决策支持中心ECD Estimated Completion Date计划完成日期EGM Engineering Group Manager工程组经理ELPO Electrode position Primer电极底漆ENG Engineering工程技术、工程学EOA End of Acceleration停止加速EPC&L Engineering Production Cntrol &Logistics工程生产控制和后勤EQF Early Quality Feedback 早期质量反馈EWO Engineering Work Order工程工作指令FA Final Approval最终认可FE Functional Evaluation功能评估FEDR Functional Evaluation Disposition Report功能评估部署报告FFF Free Form Fabrication自由形态制造FIN Financial金融的FL听FMEA Failure Mode and Effects Analysis失效形式及结果分析FPS Fixed Point Stop定点停FTP File Transfer Protocol文件传送协议FTQ First Time Quality一次送检合格率GA General Assembly总装GA Shop General Assembly Shop总装车间Paint Shop涂装车间Body Shop车身车间Press Shop冲压车间GCA Global Customer Audit全球顾客评审GD&T Geometric Dimensioning & Tolerancing几何尺寸及精度GDS Global Delivery Survey全球发运检查GM General Motors通用汽车GMAP GM Asia Pacific通用亚太GME General Motors Europe通用汽车欧洲GMIO General Motors International Operations通用汽车国际运作GMIQ General Motors Initial Quality通用汽车初始质量GMPTG General Motors Powertrain Group通用汽车动力组GMS Global Manufacturing System通用全球制造系统GP General Procedure通用程序GQTS Global Quality Tracking System全球质量跟踪系统GSB Global Strategy Board全球战略部HVAC Heating, Ventilation ,and Air Conditioning加热、通风及空调I/P Instrument Panel仪表板IC Initiate Charter初始租约ICD Interface Control Document界面控制文件IE Industrial Engineering工业工程IEMA International Export Market Analysis国际出口市场分析ILRS Indirect Labor Reporting System间接劳动报告系统IO International Operations国际业务IOM Inspection Operation Mathod检验操作方法IOS Inspection Operation Summary检验操作概要IPC International Product Center国际产品中心IPTV Incidents Per Thousand Vehicles每千辆车的故障率IQS Initial Quality Survey初始质量调查IR Incident Report事故报告ISP Integrated Scheduling Project综合计划ITP Integrated Training Process综合培训方法ITSD Interior Technical Specification Drawing内部技术规范图IUVA International Uniform Vehicle Audit国际统一车辆审核JES Job Element Sheet工作要素单JIS Job Issue Sheet工作要素单JIT Just in Time准时制JPH Job per hour每小时工作量KCC Key Control Characteristics关键控制特性KCDS Key Characteristics Designation System关键特性标识系统KPC Key product Characteristic关键产品特性LT Look at看MFD Metal Fabrication Division金属预制件区MFG Manufacturing Operations制造过程MIC Marketing Information Center市场信息中心MIE Manufacturing Integration Engineer制造综合工程师MKT Marketing营销MLBS Material Labor Balance System物化劳动平衡系统MMSTS Manufacturing Major Subsystem Technical Specifications制造重要子系统技术说明书MNG Manufacturing Engineering制造工程MPG Milford Proving Ground试验场MPI Master Process Index主程序索引MPL Master Parts List主零件列表MPS Material Planning System原料计划系统MRD Material Required Date物料需求日期MSDS Material Safery Data Sheets化学品安全数据单MSE Manufacturing System Engineer制造系统工程MSS Market Segment Specification市场分割规范MTBF Mean Time Between Failures平均故障时间MTS Manufacturing Technical Specification生产技术规范MVSS Motor Vehicle Safety Standards汽车发动机安全标准NAMA North American Market Analysis北美市场分析NAO North American Operations北美业务NAOC NAO Containerization NAO货柜运输NC Numerically Controlled用数字控制NOA Notice of Authorization授权书NSB NAO Strategy Board北美业务部OED Organization and Employee Development组织和员工发展OSH Occupational Safety & Health职业安全健康OSHA Occupational Safety & Health Act职业安全与健康法案OSHMS Occupational Safety & Health Management System职业安全健康管理体系OSHS Occupational Safety & Health Standards职业安全标准PA Production Achievement生产结果PAA Product Action Authorization产品临时授权PAC Performance Assessment Committee绩效评估委员会PACE Program Assessment and Control Environment项目评估和控制条件PAD Product Assembly Document产品装配文件PARTS Part Readiness Tracking System零件准备跟踪系统PC Problem Communication问题信息PCL Production Control and Logistics生产控制和支持PCM Process Control Manager工艺控制负责人PCR Problem Communication Report问题交流报告PDC Portfolio Development Center证券发展中心PDM Product Data Management产品资料管理PDS Product Description System产品说明系统PDT Product Development Team产品发展小组PED Production Engineering Department产品工程部PEP Product Evaluation Program产品评估程序PER Personnel人员PET Program Execution Team项目执行小组PGM Program Management项目管理PI People Involement人员参与PIMREP Project Incident Monitoring and Resolution Process事故方案跟踪和解决过程PLP Production Launch Process生产启动程序PMI Process Modeling Integration加工建模一体化PMM Program Manufacturing Manager项目制造经理PMR Product Manufacturability Requirements产品制造能要求PMT Product Management Team产品车管理小组POMS Production Order Management System产品指令管理小组POP Point of Purchase采购点PP Push - Pull推拉PPAP Production Part Approval Process生产零部件批准程序PPE个人防护用品PPH Problems Per Hundred百辆车缺陷数PPM Problems Per Million百万辆车缺陷数PPS Practical Problem Solving实际问题解决PR Performance Review绩效评估PR/R Problem Reporting and Resolution问题报告和解决PRTS Problem Resolution and Tracking System问题解决跟踪系统PSC Portfolio Strategy Council部长职务策略委员会PST Plant Support Team工厂支持小组PTO Primary Tryout第一次试验PTR Production Trial Run生产试运行PUR Purchasing采购PVD Production Vehicle Development生产汽车发展PVM Programmable Vehicle Model可设计的汽车模型QA Quality Audit质量评审QAP Quality Assessment Process质量评估过程QBC Quality Build Concern质量体系构建关系QC Quality Characteristic质量特性QCOS Quality Control Operation Sheets质量风险控制QE Quality Engineer质量工程师QET Quality Engineering Team质量工程小组QFD Quality Function Deployment质量功能配置QRD Quality, Reliability,andDurability质量、可靠性和耐久力QS Quality System质量体系QUA Quality质量RC Review Charter评估特许RCD Required Completion Date必须完成日期RFQ Request For Quotation报价请求RGM Reliability Growth Management可靠性增长小组RONA Return on Net Assets净资产评估RPO Regular Production Option正式产品选项RQA Routing Quality Assessment程序安排质量评定RT&TM Rigorous Tracking and Throughout Managment严格跟踪和全程管理SDC Strategic Decision Center战略决策中心SF Styling Freeze造型冻结SIL Single Issue List单一问题清单SIP Stansardized Inspection Process标准化检验过程SIU Summing It All Up电子求和结束SL System Layouts系统规划SLT Short Leading Team缩短制造周期SMARTSMBP Synchronous Math-Based Process理论同步过程SME Subject Matter Expert主题专家SMT Systems Management Team系统管理小组SNR坏路实验SOP Start of Production生产启动SOP Safe Operating Practice安全操作规程SOR Statement of Requirements技术要求SOS Standardization Operation Sheet标准化工作操作单SOW Statement of Work工作说明SPA Shipping Priority Audit发运优先级审计SPC Statistical Process Control统计过程控制SPE Surface and Prototype Engineering表面及原型工程SPO Service Parts Operations配件组织SPT Single Point Team专一任务小组______________________________________________________________________________________________________________SQA Supplier Quality Assurance供应商质量保证(供应商现场工程师)SQC Supplier Quality Control供方质量控制SQD Supplier Quality Development 供应方质量开发SQE Supplier Quality Engineer供方质量工程师SQIP Supplier Quality Improvement Process供应商质量改进程序SSF Start of System Fill系统填充SSLT Subsystem Leadership Team子系统领导组SSTS Subsystem Technical Specification技术参数子系统STD Standardization标准化STO Secondary Tryout二级试验SUI安全作业指导书SUW Standard Unit of Work标准工作单位SWE Simulated Work Environment模拟工作环境TAG Timing Analysis Group定时分析组TBD To Be Determined下决定TCS Traction Control System牵引控制系统TDC Technology Development Centre技术中心TDMF Text Data Management Facility文本数据管理设备TG Tooling工具TIMS Test Incident Management System试验事件管理系统TIR Test Incident Report试验事件报告TMIE Total Manufacturing Integration Engineer总的制造综合工程TOE Total Ownership Experience总的物主体验TPM Total Production Maintenance全员生产维护TSM Trade Study Methodology贸易研究方法TT Tact Time单件工时TVDE Total Vehicle Dimensional Engineer整车外型尺寸工程师TVIE Total Vehicle Integration Engineer整车综合工程师TWS Tire and Wheel System轮胎和车轮系统UAW United Auto Workers班组UCL Uniform Criteria List统一的标准表UDR Unverified Data Release未经核对的资料发布UPC Uniform Parts Classification统一零件分级VAE Vehicle Assembly Engineer车辆装配工程师VAPIR Vehicle & Progress Integration Review Team汽车发展综合评审小组VASTD Vehicle Assembly Standard Time Data汽车数据标准时间数据VCD Vehicle Chief Designer汽车首席设计师VCE Vehicle Chief Engineer汽车总工程师VCRI Validation Cross-Reference Index确认交叉引用索引VDP Vehicle Development Process汽车发展过程VDPP Vehicle Development Production Process汽车发展生产过程VDR Verified Data Release核实数据发布VDS Vehicle Description Summary汽车描述概要VDT Vehicle Development Team汽车发展组VDTO Vehicle Development Technical Operations汽车发展技术工作VEC Vehicle Engineering Center汽车工程中心VIE Vehicle Integration Engineer汽车综合工程师VIN Vehicle Identification Number车辆识别代码VIS Vehicle Information System汽车信息系统VLE Vehicle Line Executive总装线主管VLM Vehicle Launch Manager汽车创办经理VMRR Vehicle and Manufacturing Requirements Review汽车制造必要条件评审VOC Voice of Customer顾客的意见VOD Voice of Design设计意见VS Validation Station确认站VSAS Vehicle Synthesis,Analysis,and Simulation汽车综合、分析和仿真VSE Vehicle System Engineer汽车系统工程师VTS Vehicle Technical Specification汽车技术说明书WBBA Worldwide Benchmarking and Business Analysis全球基准和商业分析WOT Wide Open Throttle压制广泛开放WPO Work Place Organization工作场地布置WWP Worldwide Purchasing全球采购COMMWIP Correction纠错浪费Overproduction过量生产浪费Material Flow过度物料移动浪费Motion过度移动浪费Waiting 等待浪费Inventory过度库存浪费Processing过度加工浪费Welcome To Download !!!欢迎您的下载,资料仅供参考!。
上海通用术语

AHE:外观颜色匹配工程师APQP:产品质量先期策划DRE:设计发布工程师DTS:尺寸技术准备ETR:工程试装要求EWO:工程更改FE:功能评估GCA:全球顾客评审GD&T:主要尺寸相关的零件、总成和整车的形位公差图纸,几何尺寸及公差图纸。
GMGlobalAAR---GM全球外观认可报告GP4:生产件批准状况通知-MC0/1基准必须与PTRTE:试验工程师TVE:(动力总成)总认证工程师VPM:整车性能经理IV:工程认可(需要提供零件尺寸报告、材料试验报告、总成性能报告等所有试验报告)MC1/2:尺寸匹配(提交尺寸报告,合格率80%/90%)PVV:产品验证,小批量制造(尺寸报告,零件必须通过GP12)NS:非销售车制造(零件必须通过GP12-100%检验)S:销售车制造(零件通过PPAP人认可,零件必须通过GP12-100%检验)SORP:量产开始(具体数量根据订单,一般IV80套,MC10套,PVV几套到几十套不等。
)AQC:AttributeQualityCharacteristic属性质量特性ASQE:AdvancedSupplierQualityEngineer先期供应商质量工程师BIW:uallythebaremetalshellofthebodyincludingdoorsanddecklidpriortopaintandtrim.白车身BOM:BillofMaterials材料清单BOP:BillofProcess过程清单BrownfieldSite:Anexpansionofanexistingfacility.扩建场地CMM:CoordinateMeasuringMachine三坐标测试仪Cpk:CapabilityIndexforastabileprocess过程能力指数CTC:ComponentTimingChart(DREdocument)零部件时间表(DRE文件)CTS:ComponentTechnicalSpecifications零部件技术规范CVER:ConceptVehicleEngineeringRelease概念车工程发布DC:DesignComplete设计完成Defectoutflowdetection:AphraseusedintheSupplierQualityStatementofRequirementsthatreferstoin-processorsu bsequentinspectionusedtodetectdefectsinparts.缺陷检测DFM/DFA:DesignforManufacturability/DesignforAssembly可制造性/可装配性设计DFMEA:DesignFailureModesandEffectsAnalysis.Itisusedtoidentifythepotentialfailuremodesofapart,associated withthedesign,andestablishaprioritysystemfordesignimprovements.设计失效模式和后果分析DPV:Defectspervehicle每辆车缺陷数DR:DocumentationRequiredDR特性DRE:DesignReleaseEngineer设计释放工程师DV:DesignValidation设计验证E&APSP:Engineering&AdvancePurchasingSourcingProcess.工程&先期采购定点程序EP:E-Procurement电子采购流程)LAAM:(GeneralMotors)LatinAmerican,Africa&MeddleEast(通用汽车)拉丁美洲、非洲及中东LCR:LeanCapacityRate.ItistheGMdailycapacityrequirement.正常生产能力MCR:MaximumCapacityRate.ItistheGMmaximumcapacityrequirement.最大生产能力MOP:MakeorPurchase制造/采购MPC:MaterialProductionControl物料生产控制MPCE:MaterialProductionControlEurope欧洲物料生产控制MRD:MaterialRequiredDate;datematerialmustbedeliveredinordertoallowabuildeventtobegin.物料需求日期MSA:MeasurementSystemsAnalysis测量系统分析MVBns:ManufacturingValidationBuildnon-saleable非销售车制造验证MVBs:ManufacturingValidationBuildsaleable销售车制造验证NBH:NewBusinessHold停止新业务OEM:OriginalEquipmentManufacturer主机客户PAD:ProductionAssemblyDocuments生产装配文件PC&L:ProductionControl&Logistics生产控制&物流PDT:ProductDevelopmentTeam产品开发小组PFMEA:ProcessFailureModesandEffectsAnalysis.Itisusedtoidentifypotentialfailuremodesassociatedwiththema nufacturingandassemblyprocess.过程失效模式和后果分析PPAP:ProductionPartApprovalProcess生产件批准程序Ppk:Performanceindexforastableprocess过程能力指数PPM:1)ProgramPurchasingManager,2)PartsperMillion(rejectsandreturnstosuppliers)1)项目经理2)每百万件的产品缺陷数PPV:Product&ProcessValidation产品及过程验证PQC:ProductQualityCharacteristic产品质量特性SSTS:Sub-systemTechnicalSpecifications子系统技术规范Sub-Assembly/Sub-System:Anassemblyofsub-componentsdeliveredtotheSGMmainproductionlineforinstallationtothevehicleasasingleunit.Subcontractor:Thesupplierofasub-componenttoaComplexSystem/Subassemblysupplier(Tier2,3,etc).分供方SVE:Sub-SystemValidationEngineer子系统验证工程师SVER:StructureVehicleEngineeringRelease.结构车工程发布TeamFeasibilityCommitment:AnAIAGAPQPformthatisprovidedwiththeRequestforQuotation.Itisthesupplier’sconcernswiththefeasibilityofmanufacturingthepartasspecified.小组可行性承诺TKO:ToolingKick-Off模具启动会议UG:UnigraphicsUG工程绘图造型系统VLE:VehicleLineExecutive车辆平台负责人VTC:ValidationTestingComplete验证试验完成WO:EngineeringWorkOrder工程工作指令。
术语词汇表(GM)
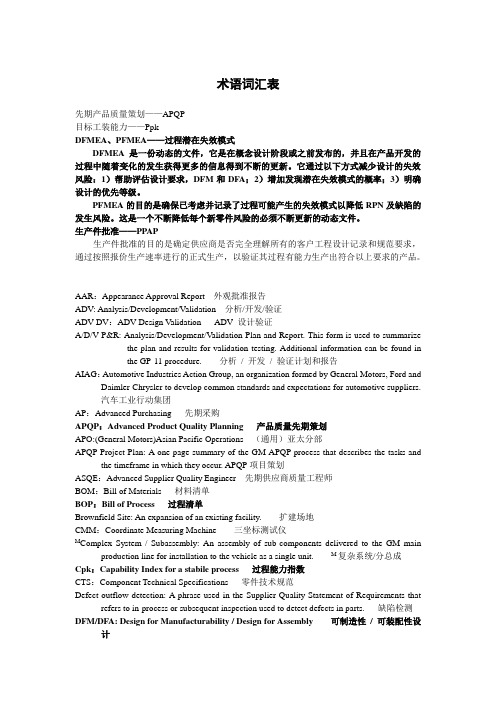
术语词汇表先期产品质量策划——APQP目标工装能力——PpkDFMEA、PFMEA——过程潜在失效模式DFMEA是一份动态的文件,它是在概念设计阶段或之前发布的,并且在产品开发的过程中随着变化的发生获得更多的信息得到不断的更新。
它通过以下方式减少设计的失效风险:1)帮助评估设计要求,DFM和DFA;2)增加发现潜在失效模式的概率;3)明确设计的优先等级。
PFMEA的目的是确保已考虑并记录了过程可能产生的失效模式以降低RPN及缺陷的发生风险。
这是一个不断降低每个新零件风险的必须不断更新的动态文件。
生产件批准——PPAP生产件批准的目的是确定供应商是否完全理解所有的客户工程设计记录和规范要求,通过按照报价生产速率进行的正式生产,以验证其过程有能力生产出符合以上要求的产品。
AAR:Appearance Approval Report 外观批准报告ADV: Analysis/Development/Validation 分析/开发/验证ADV-DV:ADV Design Validation ADV 设计验证A/D/V P&R: Analysis/Development/Validation Plan and Report. This form is used to summarize the plan and results for validation testing. Additional information can be found inthe GP-11 procedure. 分析/ 开发/ 验证计划和报告AIAG:Automotive Industries Action Group, an organization formed by General Motors, Ford and Daimler-Chrysler to develop common standards and expectations for automotive suppliers.汽车工业行动集团AP:Advanced Purchasing 先期采购APQP:Advanced Product Quality Planning 产品质量先期策划APO:(General Motors)Asian Pacific Operations (通用)亚太分部APQP Project Plan: A one-page summary of the GM APQP process that describes the tasks and the timeframe in which they occur. APQP项目策划ASQE:Advanced Supplier Quality Engineer 先期供应商质量工程师BOM:Bill of Materials 材料清单BOP:Bill of Process 过程清单Brownfield Site: An expansion of an existing facility. 扩建场地CMM:Coordinate Measuring Machine 三坐标测试仪M Complex System / Subassembly: An assembly of sub-components delivered to the GM main production line for installation to the vehicle as a single unit. M复杂系统/分总成Cpk:Capability Index for a stabile process 过程能力指数CTS:Component Technical Specifications 零件技术规范Defect outflow detection: A phrase used in the Supplier Quality Statement of Requirements that refers to in-process or subsequent inspection used to detect defects in parts. 缺陷检测DFM/DFA: Design for Manufacturability / Design for Assembly 可制造性/ 可装配性设计DFMEA:Design Failure Modes and Effects Analysis. It is used to identify the potential failure modes of a part, associated with the design, and establish a priority system for design improvements. 设计失效模式分析MPC:Material Production Control 物料生产控制MPCE: Material Production Control Europe 欧洲物料生产控制MRD:Material Required Date; date material must be delivered in order to allow a build event to begin (Pilot, SOR, etc.)物料需求日期MSA:Measurement Systems Analysis 测量系统分析MVBns: Manufacturing Validation Build non-saleable 非销售车制造验证MVBs: Manufacturing Validation Build saleable 销售车制造验证NAO:(General Motors)North American Operations (通用)北美分部NBH:New Business Hold 停止新业务N.O.D.: Notice of Decision 决议通知OEM: Original Equipment Manufacturer 主机客户PAD: Production Assembly Documents 生产装配文件PC&L: Production Control & Logistics 生产控制&物流PDT:Product Development Team 产品开发小组PFMEA:Process Failure Modes and Effects Analysis. It is used to identify potential failure modes associated with the manufacturing and assembly process. 潜在失效模式分析PPAP: Production Part Approval Process 生产件批准程序PPM:1)Program Purchasing Manager 项目采购经理2)Parts per Million(rejects and returns to suppliers) 每百万件的产品缺陷数Ppk: Perfomance index for a stable process 过程能力指数PQC:Product Quality Characteristic 产品质量特性PR/R:Problem Reporting & Resolution 问题报告及解决PSA: Potential Supplier Assessment, a subset of the Quality System Assessment(QSA) 潜在供应商评审QSA:Quality System Assessment 质量系统评审QTC:Quoted Tool Capacity 工装报价能力RASIC:Responsible, Approve, Support, Inform, Consult 负责,批准,支持,通知,讨论RFQ:Request For Quotation 报价要求RPN: Risk Priority Number relater to FMEA development 风险顺序数RPN Reduction Plan: An action plan that describes what is being done to reduce the risk priority number for items listed in the DFMEA or PFMEA. 降低RPN值计划DPV:Defects per vehicle 每辆车缺陷数DRE:Design Release Engineer 设计发放工程师Error Occurrence Prevention: A phrase used in the Supplier Quality Statement of Requirement that refers to poke yoke or error-proofing devices used to prevent errors in the manufacturing process from occurring. 防错EWO:Engineering Work Order 工程更改指令FE 1,2,3: Functional Evaluations 1,2, and 3 功能评估GD&T: Geometric Dimensioning & Tolerancing 几何尺寸&公差GM: General Motors 通用汽车公司GME:General Motors Europe 通用汽车欧洲分部GM 9000:A document provided through Boise Cascade that houses GM specific requirements (General Procedures-GPs) that are referenced in QS 9000.GP: General Procedure 总体步骤GPDS:Global Purchasing System 全球采购系统GQTS:Global Quality Tracking System 全球质量跟踪系统G R&R: Gage Repeatability and Reproducibility 量具的重复性与再现性Greenfield Site: A new supplier facility that is built to support a program. 新建工厂GVDP:Global Vehicle Development Process 全球车辆开发过程IPTV:Incidents per Thousand Vehicles 每千辆车缺陷数KCC:Key Control Characteristics. It is a process characteristic where variation can affect the final part and/or the performance of the part. 关键控制特性KCDS: Key Characteristic Designation System 关键特性指示系统Kick-Off Meeting: The first APQP supplier program review. 启动会议KPC: Key Product Characteristic. It is a product characteristic for which reasonably anticipated variation could significantly affect safety, compliance to governmental regulations, or customer satisfaction. 关键产品特性LAO:(General Motors)Latin American Operations (通用)拉丁美洲分部LCR:Lean Capacity Rate. It is the GM daily capacity requirement. 最低生产能力MCR:Maximum Capacity Rate. It is the GM maximum capacity requirement. 最大生产能力MOP:Make or Purchase 制造/采购SDE:Supplier Development Engineer 供应商开发工程师SCC: Standard Control Characteristics 关键控制特性SFMEA:System Failure Mode and Effects Analysis 系统失效模式分析SMT:System Management Team 系统管理小组SOA:Start of Acceleration 加速开始SOP:Start of Production 正式生产SOR:Statement of Requirements 要求声明SPC:Statistical Process Control 统计过程控制SPC: Standard Product Characteristic 标准产品特性SPO:(General Motors)Service and Parts Operations (通用汽车)零件与服务分部SQ:Supplier Quality 供应商质量SQE:Supplier Quality Engineer 供应商质量工程师SQIP:Supplier Quality Improvement Process 供应商质量改进过程SSF:Start of System Fill 系统填充开始SSTS:Sub-system Technical Specifications 分系统技术规范S.T.E.P: Sourcing Team Evaluation Process, a supplier assessment focused on a specific technology or process at a supplier’s facility. 采购定点小组评估过程M Subcontractor: The supplier of a sub-component to a Complex System/ Subassembly supplier(Tier 2,3,etc). M分供方Team Feasibility Commitment: An AIAG APQP form that is provided with the Request for Quotation. It is the supplier’s concerns with the feasibility of manufacturing the part as specified. 小组可行性承诺UG:Unigraphics UG工程绘图造型系统VDP:Vehicle Development Process 车辆开发过程VLE:Vehicle Line Executive 车辆平台负责人WWP:Worldwide Purchasing 全球采购Supplier DUNS No.: 供应商邓氏编码Commodity:产品Engineering Change Level: 工程更改级别Model Year: 年型----应用于哪年的车型MPC:Main product characteristic 主要产品特性MCC:Main control characteristic 主要过程特性ME:Manufacturing engineer 制造工程师PE:Project engineer 项目工程师PQE:Project quality engineer 项目质量工程师TM:Technical manager 技术经理DRE: Design release engineer 设计发放工程师GP-12 Early Production Containment GP-12早期生产遏制Error proofing:防错Pre-Launch Control Plan: 试生产控制计划PRR:Problem Report and Resolution 问题报告与解决CS:Controlled Shipping 受控发运Appearance Approval Report 外观件批准报告Design engineering approval: 工程设计批准N/A:NOT Applicable 不适用的Conforming: 合格数Non-conforming: 不合格数Product Specification : 产品规格书PCR: Problem Communication Report 问题交流报告Trial mould 软模(试验模),Formal mould硬模(正式模)IMDS : International Material Data SystemCoaxial tolerance: 同轴度,Round corner :圆角环保要求:Environment requirementRetention/contact force:固定力未注尺寸:unspecified dimension/non specified dimension DR:Dimension requirement 尺寸要求APQP 和PPAP过程专业术语AAR Appearance Approval Report 外观批准报告ADV Analysis/Development/Validation 分析/开发/验证ADV-DV ADV Design Validation A D V 设计验证A/D/V P&R Analysis/Development/Validation Plan and Report, This from is used to summarize the plan and results for validation testing. Additional informationCan be found in the GP-11procedure. 分析/开发/验证计划和报告AEC Additional Engineering Changes 附加工程更改ADV-PV ADV product Validation A D V产品验证AIAG Automotive Industries Action Group, an organization formed by General Motors, Ford and Daimler Chrysler to develop common standards and expectationsfor automotive suppliers.汽车工业行动集团AP Advanced Purchasing 先期采购APO (General Motors) Asian Pacific Operations (通用)亚太分部APQP Advanced Product Quality Planning 产品质量先期策划AQE Advanced Quality Engineer 先期质量工程师ASQE Advanced Supplier Quality Engineer 先期供应商质量工程师ANOVA Analysis of Variance方差分析法ASDE Advanced Supplier Development Engineer 高级供应商开发工程师BOM Bill of Materials 材料清单BOP Bill of Process 过程清单CCAR Concern ed and Corrective Action Report 相关整改报告CAR Corrective Action Request 整改需求CFT Cross function Team 多方论证小组CMM Coordinate Measuring Machine三坐标测试仪CPV Weekly Production Volume 周产能CPK Capability Index for a Stabile process 过程能力指数CR Customer Requirements 客户要求CM Commodity Manager 产品经理CCM Corporate Commodity Manager 公司产品经理CS Customer Satisfaction 客户满意度CS 1/2 Level 1/2 Controlled Shipping 1/2级受控发运CTS Component Technical Specifications 零件技术规范DFM/DFA Design for Manufacturability/Design for Assembly 可制造性/可装配性设计DCP Dimension Control Plan (Dynamic Control Plan) 尺寸控制计划(动态控制计划) DOE Design of Experiment试验设计DPV Daily Production Volume 日产量DVP&R Design Validation Plan and Report 设计验证计划和报告DV Design Validation 设计验证DRE Design Release Engineer设计发放工程师DFMEA Design Failure Mode and Effects Analysis设计失效模式及后果分析EWO Engineering Work Order 工程更改指令EDI Electronic Data Interchange 电子数据交换FE1,2,3 Functional Evaluations1,2,and 3 功能评估ES Engineering Specification工程规范EPC Early Production Containment 早期生产遏制FAI First Article Inspection 首件检验FCR Field Call of RateFE Function Evaluation 功能评估FTA Failure Tree Analysis 故障树状分析FTC First Time Capability 试生产能力FTQ First Time Quality 直通率(一次合格率)GR&R Gage Repeatability and Reproducibility 量具的重复性与再现性GD&T Geometric Dimensioning & Tolerancing 几何尺寸&公差GM General Motors 通用汽车公司GME General Motors Europe 通用汽车欧洲部分GP General Procedure 总体步骤GPDS Global Product Description System 全球产品描述系统GPS Global Purchasing System 全球采购系统GQTS Global Quality Tracking System 全球质量跟踪系统GVDP Global Vehicle Development Process 全球车辆开发过程ISIR initial Sample Inspection Report 首次样品检验报告IPTV Incidents per Thousand Vehicles 每千辆车缺陷数IAA Interim Approval Authorization 临时批准授权ICAL Integral Corrective Action List 整体整改列表LCL Lower Control Limit 下控制限控制下限LSL Lower Specification Limit工程规范下限KCC Key Control Characteristic 关键控制特性KCDS Key Characteristics Designation System 关键特性指示系统KPC (GM)Key Product Characteristic关键产品特性LAO (General Motors) Latin American Operations (通用)拉丁美洲分部LCR Lean Capacity Rate, It is the GM daily capacity requirement 最低生产能力MCR Maximum Capacity Rate, It is the GM maximum capacity requirement 最大生产能力MPP Modified Production Part (Nissan Form) 改良生产零件MOP Make or Purchase 制造/采购MRP Manufacturing / Materials Resource Planning 加工/物料资源计划MRR Material Reject Report 物料拒收报告MPC Material Production Control 物料生产控制MPCE Material Production Control Europe 欧洲物料生产控制MRB Material Review Board物料评审MRD Material Required Date 物料需求日期MSA Measurement Systems Analysis 测量系统分析NAO (General Motors) North American Operations (通用)北美分部NCC Non Conformity Cost不良品成本NBH New Business Hold 停止新业务NDA/O Non Disclosure Agreement/Obligation保密协议/和约N.O.D Notice of Decision 决议通知OEE Operating Equipment Effectiveness 操作装置效率OEM Original Equipment Manufacturer原始设备制造商(整车厂)OTS Off Tooling Sample 正式工装/模具生产样品PPAP Production Part Approval Process 生产件批准程序PAD Production Assembly Documents 生产装配文件PC&L Production Control & Logistics 生产控制&物流PSW Part Submission Warrant 零件提交保证书PDT Product Development Team 项目开发组PFMEA Process Failure Modes and Effects Analysis 过程失效模式及后果分析PPM Parts per Million 每百万PSA Potential Supplier Assessment 潜在供应商评审PPK Performance index for a stable process 过程能力指数PFC Process Flow Chart 过程流程图PQC Product Quality Characteristic 产品质量特性PFD Process Flow Diagram 过程流程图PTC Pass Through Characteristic 过程特性?PTR Production Trial Run 生产试行PVP&R Production Validation Plan and Report 产品验证计划与报告PR/R Problem Reporting & Resolution 问题报告及决策PV Production Validation 生产产品验证PRR Problem Resolution Report 问题决策报告QSA Quality System Assessment 质量系统评审QSB Quality System Base 质量体系基础QSR Quality System Requirement质量体系要求QTC Quotes Tool Capacity 工装报价能力QFD Quality Function Deployment质量功能展开QOS Quality Operating System 质量运行体系QR Quality Reject/Report 质量拒收/报告?R@R Run at Rate 产能审核(产能审核指的是按照正常的生产状态进行审核,其中包括人员,设备,工装,材料和工艺。
APQP-和PPAP过程专业术语(1)
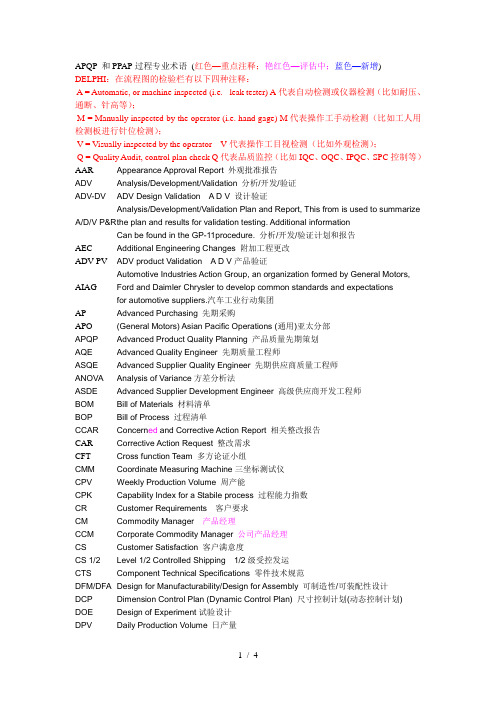
APQP 和PPAP 过程专业术语 (红色—重点注释;艳红色—评估中;蓝色—新增) DELPHI :在流程图的检验栏有以下四种注释:A = Automatic, or machine inspected (i.e. leak tester) A 代表自动检测或仪器检测(比如耐压、通断、针高等);M = Manually inspected by the operator (i.e. hand gage) M 代表操作工手动检测(比如工人用检测板进行针位检测);V = Visually inspected by the operator V 代表操作工目视检测(比如外观检测); Q = Quality Audit, control plan check Q 代表品质监控(比如IQC 、OQC 、IPQC 、SPC 控制等)AARAppearance Approval Report 外观批准报告 ADV Analysis/Development/Validation 分析/开发/验证 ADV-DVADV Design Validation A D V 设计验证A/D/V P&R Analysis/Development/Validation Plan and Report, This from is used to summarizethe plan and results for validation testing. Additional informationCan be found in the GP-11procedure. 分析/开发/验证计划和报告AECAdditional Engineering Changes 附加工程更改 ADV-PV ADV product Validation A D V 产品验证AIAG Automotive Industries Action Group, an organization formed by General Motors,Ford and Daimler Chrysler to develop common standards and expectations for automotive suppliers.汽车工业行动集团 APAdvanced Purchasing 先期采购APO(General Motors) Asian Pacific Operations (通用)亚太分部 APQP Advanced Product Quality Planning 产品质量先期策划 AQE Advanced Quality Engineer 先期质量工程师ASQE Advanced Supplier Quality Engineer 先期供应商质量工程师 ANOVA Analysis of Variance 方差分析法ASDE Advanced Supplier Development Engineer 高级供应商开发工程师 BOM Bill of Materials 材料清单 BOP Bill of Process 过程清单CCARConcern ed and Corrective Action Report 相关整改报告 CAR Corrective Action Request 整改需求 CFTCross function Team 多方论证小组CMM Coordinate Measuring Machine 三坐标测试仪 CPV Weekly Production Volume 周产能CPK Capability Index for a Stabile process 过程能力指数 CR Customer Requirements 客户要求 CM Commodity Manager 产品经理CCM Corporate Commodity Manager 公司产品经理 CS Customer Satisfaction 客户满意度CS 1/2 Level 1/2 Controlled Shipping 1/2级受控发运CTS Component Technical Specifications 零件技术规范DFM/DFA Design for Manufacturability/Design for Assembly 可制造性/可装配性设计DCP Dimension Control Plan (Dynamic Control Plan) 尺寸控制计划(动态控制计划) DOE Design of Experiment 试验设计 DPVDaily Production Volume 日产量DVP&R Design Validation Plan and Report 设计验证计划和报告DV Design Validation 设计验证DRE Design Release Engineer设计发放工程师DFMEA Design Failure Mode and Effects Analysis设计失效模式及后果分析EWO Engineering Work Order 工程更改指令EDI Electronic Data Interchange 电子数据交换FE1,2,3 Functional Evaluations1,2,and 3 功能评估ES Engineering Specification工程规范EPC Early Production Containment 早期生产遏制FAI First Article Inspection 首件检验FCR Field Call of RateFE Function Evaluation 功能评估FTA Failure Tree Analysis 故障树状分析FTC First Time Capability 试生产能力FTQ First Time Quality 直通率(一次合格率)GR&R Gage Repeatability and Reproducibility 量具的重复性与再现性GD&T Geometric Dimensioning & Tolerancing 几何尺寸&公差GM General Motors 通用汽车公司GME General Motors Europe 通用汽车欧洲部分GP General Procedure 总体步骤GPDS Global Product Description System 全球产品描述系统GPS Global Purchasing System 全球采购系统GQTS Global Quality Tracking System 全球质量跟踪系统GVDP Global Vehicle Development Process 全球车辆开发过程ISIR initial Sample Inspection Report 首次样品检验报告IPTV Incidents per Thousand Vehicles 每千辆车缺陷数IAA Interim Approval Authorization 临时批准授权ICAL Integral Corrective Action List 整体整改列表ICR Interface Change Request LCL Lower Control Limit 控制下限LSL Lower Specification Limit工程规范下限KCC Key Control Characteristic 关键控制特性KCDS Key Characteristics Designation System 关键特性指示系统KPC (GM)Key Product Characteristic关键产品特性LAO (General Motors) Latin American Operations (通用)拉丁美洲分部LCR Lean Capacity Rate, It is the GM daily capacity requirement 最低生产能力MCR Maximum Capacity Rate, It is the GM maximum capacity requirement 最大生产能力MPP Modified Production Part (Nissan Form) 改良生产零件MOP Make or Purchase 制造/采购MRP Manufacturing / Materials Resource Planning 加工/物料资源计划MRR Material Reject Report 物料拒收报告MPC Material Production Control 物料生产控制MPCE Material Production Control Europe 欧洲物料生产控制MRB Material Review Board物料评审MRD Material Required Date 物料需求日期MSA Measurement Systems Analysis 测量系统分析NAO (General Motors) North American Operations (通用)北美分部NCC Non Conformity Cost不良品成本NBH New Business Hold 停止新业务NDA/O Non Disclosure Agreement/Obligation保密协议/和约N.O.D Notice of Decision 决议通知OEE Operating Equipment Effectiveness 操作装置效率OEM Original Equipment Manufacturer原始设备制造商(整车厂)OTS Off Tooling Sample 正式工装/模具生产样品PPAP Production Part Approval Process 生产件批准程序PAD Production Assembly Documents 生产装配文件PC&L Production Control & Logistics 生产控制&物流PSW Part Submission Warrant 零件提交保证书PDT Product Development Team 项目开发组PFMEA Process Failure Modes and Effects Analysis 过程失效模式及后果分析PPM Parts per Million 每百万PPEI Platform to Powertrain Electrical Interface PSA Potential Supplier Assessment 潜在供应商评审PPK Performance index for a stable process 初试过程能力指数PFC Process Flow Chart 过程流程图PQC Product Quality Characteristic 产品质量特性PFD Process Flow Diagram 过程流程图PTC Pass Through Characteristic 过程特性PTR Production Trial Run 生产试行PVP&R Production Validation Plan and Report 产品验证计划与报告PR/R Problem Reporting & Resolution 问题报告及决策PV Production Validation 生产产品验证PRR Problem Resolution Report 问题决策报告QSA Quality System Assessment 质量系统评审QSA Quality System Base 质量体系基础QSR Quality System Requirement质量体系要求QTC Quotes Tool Capacity 工装报价能力QFD Quality Function Deployment质量功能展开QOS Quality Operating System 质量运行体系QR Quality Reject/Report 质量拒收/报告R@R Run at Rate 产能审核(产能审核指的是按照正常的生产状态进行审核,其中包括人员,设备,工装,材料和工艺。
汽车行业关键词(英文简写)大全

OEM生产,即贴牌生产,也称为定牌生产,俗称“贴牌”,由于其英文表述为Original Equipment/Entrusted Manufacture(译为原始设备制造商或原产地委托加工),因此简称为OEM。
基本含义为品牌生产者不直接生产产品,而是利用自己掌握的关键的核心技术负责设计和开发新产品,控制销售渠道,具体的加工任务通过合同订购的方式委托同类产品的其他厂家生产。
之后将所订产品低价买断,并直接贴上自己的品牌商标。
这种委托他人生产的合作方式简称OEM,承接加工任务的制造商被称为OEM厂商,其生产的产品被称为OEM产品。
可见,贴牌生产属于加工贸易中的“代工生产”方式,在国际贸易中是以商品为载体的劳务出口。
OEM的特征就是:技术在外,资本在外,市场在外,只有生产在内。
ODM是英文Original Design Manufacturer (原始设计制造商)的缩写,指一家厂家根据另一家厂商的要求,为其生产产品和产品配件,亦称为定牌生产或授权贴牌生产.即可代表外委加工,也可代表转包合同加工.国内习惯称为协作生产,三来加工。
ODM的厂商设计方案分为买断或不买断的方式供应:1.买断方式:有品牌拥有方买断ODM厂商现成的某型号产品的设计,或品牌拥有方单独要求ODM厂商为自己设计产品方案。
2.不买断方式:品牌拥有方不买断ODM厂商某型号产品的设计,ODM厂商可将同型号产品的设计采取不买断的方式同时卖给其它品牌。
当这两个或多个品牌共享一个设计时,两个品牌产品的区别主要在于外观。
SOP (small-outline package,批量生产,为上市积累一定的库存)SOP =Standard Operating Procedure 标准操作程序OBD是英文On-Board Diagnostics的缩写,中文翻译为“车载自动诊断系统”。
这个系统将从发动机的运行状况随时监控汽车是否尾气超标,一旦超标,会马上发出警示。
当系统出现故障时,故障(MIL)灯或检查发动机(Check Engine)警告灯亮,同时动力总成控制模块(PCM)将故障信息存入存储器,通过一定的程序可以将故障码从PCM中读出。
汽车行业关键词(英文简写)大全

OEM生产,即贴牌生产,也称为定牌生产,俗称“贴牌”,由于其英文表述为Original Equipment/Entrusted Manufacture(译为原始设备制造商或原产地委托加工),因此简称为OEM。
基本含义为品牌生产者不直接生产产品,而是利用自己掌握的关键的核心技术负责设计和开发新产品,控制销售渠道,具体的加工任务通过合同订购的方式委托同类产品的其他厂家生产。
之后将所订产品低价买断,并直接贴上自己的品牌商标。
这种委托他人生产的合作方式简称OEM,承接加工任务的制造商被称为OEM厂商,其生产的产品被称为OEM产品。
可见,贴牌生产属于加工贸易中的“代工生产”方式,在国际贸易中是以商品为载体的劳务出口。
OEM的特征就是:技术在外,资本在外,市场在外,只有生产在内。
ODM是英文Original Design Manufacturer (原始设计制造商)的缩写,指一家厂家根据另一家厂商的要求,为其生产产品和产品配件,亦称为定牌生产或授权贴牌生产.即可代表外委加工,也可代表转包合同加工.国内习惯称为协作生产,三来加工。
ODM的厂商设计方案分为买断或不买断的方式供应:1.买断方式:有品牌拥有方买断ODM厂商现成的某型号产品的设计,或品牌拥有方单独要求ODM厂商为自己设计产品方案。
2.不买断方式:品牌拥有方不买断ODM厂商某型号产品的设计,ODM厂商可将同型号产品的设计采取不买断的方式同时卖给其它品牌。
当这两个或多个品牌共享一个设计时,两个品牌产品的区别主要在于外观。
SOP (small-outline package,批量生产,为上市积累一定的库存)SOP =Standard Operating Procedure 标准操作程序OBD是英文On-Board Diagnostics的缩写,中文翻译为“车载自动诊断系统”。
这个系统将从发动机的运行状况随时监控汽车是否尾气超标,一旦超标,会马上发出警示。
当系统出现故障时,故障(MIL)灯或检查发动机(Check Engine)警告灯亮,同时动力总成控制模块(PCM)将故障信息存入存储器,通过一定的程序可以将故障码从PCM中读出。
电子厂常用的英文单词
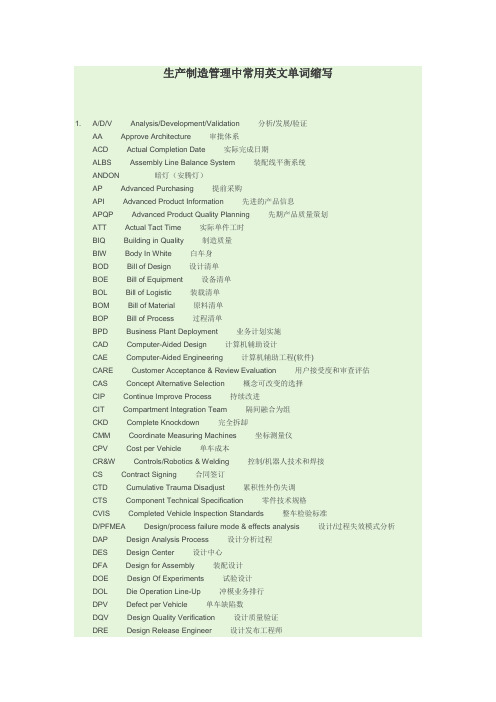
生产制造管理中常用英文单词缩写1. A/D/V Analysis/Development/Validation 分析/发展/验证AA Approve Architecture 审批体系ACD Actual Completion Date 实际完成日期ALBS Assembly Line Balance System 装配线平衡系统ANDON 暗灯(安腾灯)AP Advanced Purchasing 提前采购API Advanced Product Information 先进的产品信息APQP Advanced Product Quality Planning 先期产品质量策划ATT Actual Tact Time 实际单件工时BIQ Building in Quality 制造质量BIW Body In White 白车身BOD Bill of Design 设计清单BOE Bill of Equipment 设备清单BOL Bill of Logistic 装载清单BOM Bill of Material 原料清单BOP Bill of Process 过程清单BPD Business Plant Deployment 业务计划实施CAD Computer-Aided Design 计算机辅助设计CAE Computer-Aided Engineering 计算机辅助工程(软件)CARE Customer Acceptance & Review Evaluation 用户接受度和审查评估CAS Concept Alternative Selection 概念可改变的选择CIP Continue Improve Process 持续改进CIT Compartment Integration Team 隔间融合为组CKD Complete Knockdown 完全拆缷CMM Coordinate Measuring Machines 坐标测量仪CPV Cost per Vehicle 单车成本CR&W Controls/Robotics & Welding 控制/机器人技术和焊接CS Contract Signing 合同签订CTD Cumulative Trauma Disadjust 累积性外伤失调CTS Component Technical Specification 零件技术规格CVIS Completed Vehicle Inspection Standards 整车检验标准D/PFMEA Design/process failure mode & effects analysis 设计/过程失效模式分析DAP Design Analysis Process 设计分析过程DES Design Center 设计中心DFA Design for Assembly 装配设计DOE Design Of Experiments 试验设计DOL Die Operation Line-Up 冲模业务排行DPV Defect per Vehicle 单车缺陷数DQV Design Quality Verification 设计质量验证DRE Design Release Engineer 设计发布工程师DRL Direct Run Loss 直行损失率DRR Direct Run Run 直行率DSC Decision Support Center 决策支持中心ECD Estimated Completion Date 计划完成日期EGM Engineering Group Manager 工程组经理ELPO Electrode position Primer 电极底漆ENG Engineering 工程技术、工程学EOA End of Acceleration 停止加速EPC&L Engineering Production Cntrol &Logistics 工程生产控制和后勤EQF Early Quality Feedback 早期质量反馈EWO Engineering Work Order 工程工作指令FA Final Approval 最终认可FE Functional Evaluation 功能评估FEDR Functional Evaluation Disposition Report 功能评估部署报告FFF Free Form Fabrication 自由形态制造FIN Financial 金融的FL 听FMEA Failure Mode and Effects Analysis 失效形式及结果分析FPS Fixed Point Stop 定点停FTP File Transfer Protocol 文件传送协议FTQ First Time Quality 一次送检合格率GA General Assembly 总装GA Shop General Assembly Shop 总装车间Paint Shop 涂装车间Body Shop 车身车间Press Shop 冲压车间GCA Global Customer Audit 全球顾客评审GD&T Geometric Dimensioning & Tolerancing 几何尺寸及精度GDS Global Delivery Survey 全球发运检查GM General Motors 通用汽车GMAP GM Asia Pacific 通用亚太GME General Motors Europe 通用汽车欧洲GMIO General Motors International Operations 通用汽车国际运作GMIQ General Motors Initial Quality 通用汽车初始质量GMPTG General Motors Powertrain Group 通用汽车动力组GMS Global Manufacturing System 通用全球制造系统GP General Procedure 通用程序GQTS Global Quality Tracking System 全球质量跟踪系统GSB Global Strategy Board 全球战略部HVAC Heating, Ventilation ,and Air Conditioning 加热、通风及空调I/P Instrument Panel 仪表板IC Initiate Charter 初始租约ICD Interface Control Document 界面控制文件IE Industrial Engineering 工业工程IEMA International Export Market Analysis 国际出口市场分析ILRS Indirect Labor Reporting System 间接劳动报告系统IO International Operations 国际业务IOM Inspection Operation Mathod 检验操作方法IOS Inspection Operation Summary 检验操作概要IPC International Product Center 国际产品中心IPTV Incidents Per Thousand Vehicles 每千辆车的故障率IQS Initial Quality Survey 初始质量调查IR Incident Report 事故报告ISP Integrated Scheduling Project 综合计划ITP Integrated Training Process 综合培训方法ITSD Interior Technical Specification Drawing 内部技术规范图IUVA International Uniform Vehicle Audit 国际统一车辆审核JES Job Element Sheet 工作要素单JIS Job Issue Sheet 工作要素单JIT Just in Time 准时制JPH Job per hour 每小时工作量KCC Key Control Characteristics 关键控制特性KCDS Key Characteristics Designation System 关键特性标识系统KPC Key product Characteristic 关键产品特性LT Look at 看MFD Metal Fabrication Division 金属预制件区MFG Manufacturing Operations 制造过程MIC Marketing Information Center 市场信息中心MIE Manufacturing Integration Engineer 制造综合工程师MKT Marketing 营销MLBS Material Labor Balance System 物化劳动平衡系统MMSTS Manufacturing Major Subsystem Technical Specifications 制造重要子系统技术说明书MNG Manufacturing Engineering 制造工程MPG Milford Proving Ground 试验场MPI Master Process Index 主程序索引MPL Master Parts List 主零件列表MPS Material Planning System 原料计划系统MRD Material Required Date 物料需求日期MSDS Material Safery Data Sheets 化学品安全数据单MSE Manufacturing System Engineer 制造系统工程MSS Market Segment Specification 市场分割规范MTBF Mean Time Between Failures 平均故障时间MTS Manufacturing Technical Specification 生产技术规范MVSS Motor Vehicle Safety Standards 汽车发动机安全标准NAMA North American Market Analysis 北美市场分析NAO North American Operations 北美业务NAOC NAO Containerization NAO货柜运输NC Numerically Controlled 用数字控制NOA Notice of Authorization 授权书NSB NAO Strategy Board 北美业务部OED Organization and Employee Development 组织和员工发展OSH Occupational Safety & Health 职业安全健康OSHA Occupational Safety & Health Act 职业安全与健康法案OSHMS Occupational Safety & Health Management System 职业安全健康管理体系OSHS Occupational Safety & Health Standards 职业安全标准PA Production Achievement 生产结果PAA Product Action Authorization 产品临时授权PAC Performance Assessment Committee 绩效评估委员会PACE Program Assessment and Control Environment 项目评估和控制条件PAD Product Assembly Document 产品装配文件PARTS Part Readiness Tracking System 零件准备跟踪系统PC Problem Communication 问题信息PCL Production Control and Logistics 生产控制和支持PCM Process Control Manager 工艺控制负责人PCR Problem Communication Report 问题交流报告PDC Portfolio Development Center 证券发展中心PDM Product Data Management 产品资料管理PDS Product Description System 产品说明系统PDT Product Development Team 产品发展小组PED Production Engineering Department 产品工程部PEP Product Evaluation Program 产品评估程序PER Personnel 人员PET Program Execution Team 项目执行小组PGM Program Management 项目管理PI People Involement 人员参与PIMREP Project Incident Monitoring and Resolution Process 事故方案跟踪和解决过程PLP Production Launch Process 生产启动程序PMI Process Modeling Integration 加工建模一体化PMM Program Manufacturing Manager 项目制造经理PMR Product Manufacturability Requirements 产品制造能要求PMT Product Management Team 产品车管理小组POMS Production Order Management System 产品指令管理小组POP Point of Purchase 采购点PP Push - Pull 推拉PPAP Production Part Approval Process 生产零部件批准程序PPE 个人防护用品PPH Problems Per Hundred 百辆车缺陷数PPM Problems Per Million 百万辆车缺陷数PPS Practical Problem Solving 实际问题解决PR Performance Review 绩效评估PR/R Problem Reporting and Resolution 问题报告和解决PRTS Problem Resolution and Tracking System 问题解决跟踪系统PSC Portfolio Strategy Council 部长职务策略委员会PST Plant Support Team 工厂支持小组PTO Primary Tryout 第一次试验PTR Production Trial Run 生产试运行PUR Purchasing 采购PVD Production Vehicle Development 生产汽车发展PVM Programmable Vehicle Model 可设计的汽车模型QA Quality Audit 质量评审QAP Quality Assessment Process 质量评估过程QBC Quality Build Concern 质量体系构建关系QC Quality Characteristic 质量特性QCOS Quality Control Operation Sheets 质量风险控制QE Quality Engineer 质量工程师QET Quality Engineering Team 质量工程小组QFD Quality Function Deployment 质量功能配置QRD Quality, Reliability,andDurability 质量、可靠性和耐久力QS Quality System 质量体系QUA Quality 质量RC Review Charter 评估特许RCD Required Completion Date 必须完成日期RFQ Request For Quotation 报价请求RGM Reliability Growth Management 可靠性增长小组RONA Return on Net Assets 净资产评估RPO Regular Production Option 正式产品选项RQA Routing Quality Assessment 程序安排质量评定RT&TM Rigorous Tracking and Throughout Managment 严格跟踪和全程管理SDC Strategic Decision Center 战略决策中心SF Styling Freeze 造型冻结SIL Single Issue List 单一问题清单SIP Stansardized Inspection Process 标准化检验过程SIU Summing It All Up 电子求和结束SL System Layouts 系统规划SLT Short Leading Team 缩短制造周期SMARTSMBP Synchronous Math-Based Process 理论同步过程SME Subject Matter Expert 主题专家SMT Systems Management Team 系统管理小组SNR 坏路实验SOP Start of Production 生产启动SOP Safe Operating Practice 安全操作规程SOR Statement of Requirements 技术要求SOS Standardization Operation Sheet 标准化工作操作单SOW Statement of Work 工作说明SPA Shipping Priority Audit 发运优先级审计SPC Statistical Process Control 统计过程控制SPE Surface and Prototype Engineering 表面及原型工程SPO Service Parts Operations 配件组织SPT Single Point Team 专一任务小组SQA Supplier Quality Assurance 供应商质量保证(供应商现场工程师)SQC Supplier Quality Control 供方质量控制SQD Supplier Quality Development 供应方质量开发SQE Supplier Quality Engineer 供方质量工程师SQIP Supplier Quality Improvement Process 供应商质量改进程序SSF Start of System Fill 系统填充SSLT Subsystem Leadership Team 子系统领导组SSTS Subsystem Technical Specification 技术参数子系统STD Standardization 标准化STO Secondary Tryout 二级试验SUI 安全作业指导书SUW Standard Unit of Work 标准工作单位SWE Simulated Work Environment 模拟工作环境TAG Timing Analysis Group 定时分析组TBD To Be Determined 下决定TCS Traction Control System 牵引控制系统TDC Technology Development Centre 技术中心TDMF Text Data Management Facility 文本数据管理设备TG Tooling 工具TIMS Test Incident Management System 试验事件管理系统TIR Test Incident Report 试验事件报告TMIE Total Manufacturing Integration Engineer 总的制造综合工程TOE Total Ownership Experience 总的物主体验TPM Total Production Maintenance 全员生产维护TSM Trade Study Methodology 贸易研究方法TT Tact Time 单件工时TVDE Total Vehicle Dimensional Engineer 整车外型尺寸工程师TVIE Total Vehicle Integration Engineer 整车综合工程师TWS Tire and Wheel System 轮胎和车轮系统UAW United Auto Workers 班组UCL Uniform Criteria List 统一的标准表UDR Unverified Data Release 未经核对的资料发布UPC Uniform Parts Classification 统一零件分级VAE Vehicle Assembly Engineer 车辆装配工程师VAPIR Vehicle & Progress Integration Review Team 汽车发展综合评审小组VASTD Vehicle Assembly Standard Time Data 汽车数据标准时间数据VCD Vehicle Chief Designer 汽车首席设计师VCE Vehicle Chief Engineer 汽车总工程师VCRI Validation Cross-Reference Index 确认交叉引用索引VDP Vehicle Development Process 汽车发展过程VDPP Vehicle Development Production Process 汽车发展生产过程VDR Verified Data Release 核实数据发布VDS Vehicle Description Summary 汽车描述概要VDT Vehicle Development Team 汽车发展组VDTO Vehicle Development Technical Operations 汽车发展技术工作VEC Vehicle Engineering Center 汽车工程中心VIE Vehicle Integration Engineer 汽车综合工程师VIN Vehicle Identification Number 车辆识别代码VIS Vehicle Information System 汽车信息系统VLE Vehicle Line Executive 总装线主管VLM Vehicle Launch Manager 汽车创办经理VMRR Vehicle and Manufacturing Requirements Review 汽车制造必要条件评审VOC Voice of Customer 顾客的意见VOD Voice of Design 设计意见VS Validation Station 确认站VSAS Vehicle Synthesis,Analysis,and Simulation 汽车综合、分析和仿真VSE Vehicle System Engineer 汽车系统工程师VTS Vehicle Technical Specification 汽车技术说明书WBBA Worldwide Benchmarking and Business Analysis 全球基准和商业分析WOT Wide Open Throttle 压制广泛开放WPO Work Place Organization 工作场地布置WWP Worldwide Purchasing 全球采购COMMWIP Correction 纠错浪费Overproduction 过量生产浪费Material Flow 过度物料移动浪费Motion 过度移动浪费Waiting 等待浪费Inventory 过度库存浪费Processing 过度加工浪费。
汽车制造业英文专业术语整理(非常好)

序号
1 2 3 4
术
3G 3M 5M AAR
语
5
Action plan
6 7 8 9 10 11 12 13 14 15 16 17 18 19 20
ADV ADV–DV A/D/V P&R ADV–PV AEM AIAG Andon AP APQP APO AS ASQE ATT Audit Bidlist
152
Prototype Vehicle (Sample)
153 154 155 156
QCC QCD QCOS QFD
157
QRK
158 159 160
QSA QSDT QTC
161 162 163 164 165 166 167 168 169 170 171 172 173 174 175 176
Problem Reporting & Resolution 问题报告和解决程序 Supplier Requirement for Match Check Material 供应商材料认可程序 Supplier Requirement for Comp. Verification & Trace. 供应商零部件认可和追溯要求程序 Continuous Improvement Procedure 持续改进程序 Run @ Rate Process 节拍生产 Evaluation & Accreditation of Supplier Testing Facility 供应商实验/试验室认可程序 Prototype Material Certification Procedure 手工样件认可程序 Early Production Containment Procedure 早期生产遏制程序 Global Product Description System 全球产品描述系统 Global Purchasing System 全球采购系统 Global Quality Tracking System 全球质量跟踪系统 Gage Repeatability and Reproducibility 量具的重复性与再现性 Global Vehicle Development Process 全球车辆开发过程 Human Resource 人力资源 Incidents per Thousand Vehicles 每千辆车缺陷数 GP12程序中使用的自检记录表 Industry Engineering 工业工程 Inspection Operator Method 操作视察方法 Inspection Operator Summary 操作视察要领 Internal Rate of Return 内部收益率 Index Time 指数时间 Job Element Sheet 工作要素单 Just In Time Manufacturing Process 拉动式(及时)生产
顾客特殊要求有关管理程序
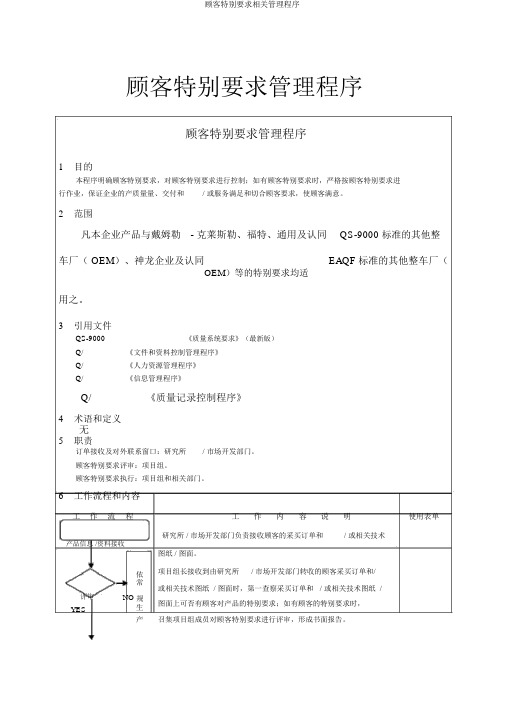
顾客特别要求管理程序顾客特别要求管理程序1目的本程序明确顾客特别要求,对顾客特别要求进行控制;如有顾客特别要求时,严格按顾客特别要求进行作业,保证企业的产质量量、交付和/ 或服务满足和切合顾客要求,使顾客满意。
2范围凡本企业产品与戴姆勒- 克莱斯勒、福特、通用及认同QS-9000 标准的其他整车厂( OEM)、神龙企业及认同EAQF标准的其他整车厂(OEM)等的特别要求均适用之。
3引用文件QS-9000《质量系统要求》(最新版)Q/《文件和资料控制管理程序》Q/《人力资源管理程序》Q/《信息管理程序》Q/《质量记录控制程序》4术语和定义无5职责订单接收及对外联系窗口:研究所/ 市场开发部门。
顾客特别要求评审:项目组。
顾客特别要求执行:项目组和相关部门。
6工作流程和内容工作流程工作内容说明使用表单研究所 / 市场开发部门负责接收顾客的采买订单和/ 或相关技术产品信息 /资料接收评审YES图纸 / 图面。
依项目组长接收到由研究所/ 市场开发部门转收的顾客采买订单和/常或相关技术图纸 / 图面时,第一查察采买订单和 / 或相关技术图纸 / NO 规图面上可否有顾客对产品的特别要求;如有顾客的特别要求时,生产召集项目组成员对顾客特别要求进行评审,形成书面报告。
建立顾客特别要求档案资料:建立顾客特别要求档案资料项目组对评审后的顾客特别要求按顾客种类建立相关顾客特别要求的档案资料, 并由项目组负责归档管理;当顾客的特别要求有发A生更正时,由项目组负责对其进行更正和换新作业,以保证企业随时掌握顾客特别要求的最新状态,满足顾客要求。
工作流程A顾客特别要求刊行顾客特别要求宣传和沟通顾客特别要求培训顾客特别要推行和执行资料归档工作内容说明使用表单项目组按 Q/《文件和资料控制管理程序》进行管理,并将其发散至相关部门。
顾客特别要求宣传、沟通:项目组将按《信息管理程序》之沟通和宣传的路子和方法对顾客的特别要求进行宣传和沟通,以便让企业所有员工认识和理解。
QS9000顾客特殊要求
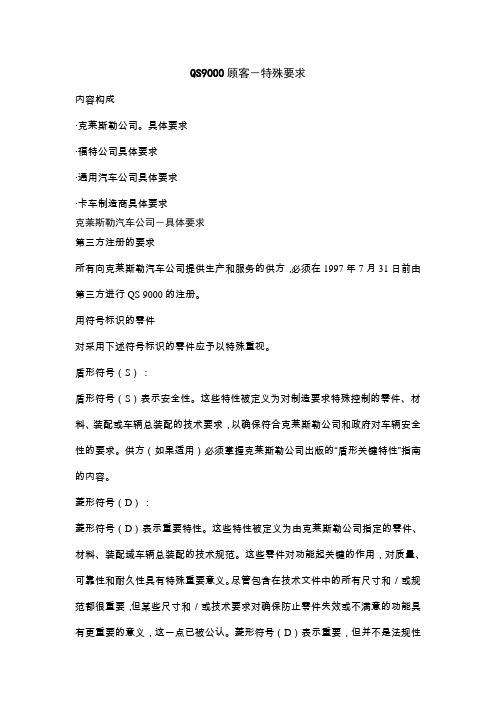
QS9000顾客-特殊要求内容构成·克莱斯勒公司。
具体要求·福特公司具体要求·通用汽车公司具体要求·卡车制造商具体要求克莱斯勒汽车公司-具体要求第三方注册的要求所有向克莱斯勒汽车公司提供生产和服务的供方,必须在1997年7月31日前由第三方进行QS 9000的注册。
用符号标识的零件对采用下述符号标识的零件应予以特殊重视。
盾形符号(S):盾形符号(S)表示安全性。
这些特性被定义为对制造要求特殊控制的零件、材料、装配或车辆总装配的技术要求,以确保符合克莱斯勒公司和政府对车辆安全性的要求。
供方(如果适用)必须掌握克莱斯勒公司出版的“盾形关键特性”指南的内容。
菱形符号(D):菱形符号(D)表示重要特性。
这些特性被定义为由克莱斯勒公司指定的零件、材料、装配域车辆总装配的技术规范。
这些零件对功能起关键的作用,对质量、可靠性和耐久性具有特殊重要意义。
尽管包含在技术文件中的所有尺寸和/或规范都很重要,但某些尺寸和/或技术要求对确保防止零件失效或不满意的功能具有更重要的意义,这一点已被公认。
菱形符号(D)表示重要,但并不是法规性的要求。
同一文件上菱形符号(D)的出现并不影响盾形(S)的重要性。
供方(如果适用)必须掌握克莱斯勒公司出版的“菱形-关键特性南”的。
五连形符号(P):五边形符号(P)是表示工装夹具、量具、在开发零件和试生产零件重要特性的主要工具符号,详细内容请参考克莱斯勒公司出版的PS一8335和“五边形一关键验证符号指南。
重点特性重点特性是供方运用产品和过程的知识选出的重要特性。
盾形、菱形和五边形符号的出现或使用,并不削弱供方选择的其它尺寸和/或特性的重要性,所有特性都必须写入在控制计划内。
年度图纸审核为了确保持续地满足所有克莱斯勒公司的要求,需要进行全面的年度图纸审核,例外情况需要有克莱斯勒公司有关代表的书面同意。
内部质量审核除非克莱斯勒公司有关代表另有规定,供方必须每年至少一进行一次内部质量体系审核。
特殊特性讲义

Key Characteristic DesignationSystem关键特性指示系统1什么是KCDS:KCDS是一个系统,旨在统一GM和供应商对于关键特性的识别和记录方法。
2目的:KCDS明确了对如下要求的识别、记录和交流方法:•零件的安全、符合性要求•功能检测要求•产品识别/确认/追溯性要求•零件处理要求•特殊特性及其特殊关注的识别和指定要求(KPC、PQC、KCC3目的:KCDS适用于项目策划、产品/工艺设计、制造和装配过程、产品发运等;无论是在GM主机厂内,还是在提供产品或工序过程的内/外部供应商处。
4目的:KCDS积极支持:•产品设计的有效性、合理性、实用性;•制造和/或装配过程中,对变差的降低和保持、监控活动等,从而改进产品的质量和制造经济性。
56零件处理功能检测需额外关注的零件追溯性零件级别安全 / 符合性其余零件需一般关注所有产品 & 过程KPCKCC特殊特性特殊关注特性级别PQCKCC一般特性一般关注(所有零件KCDS 程序:零件的额外关注要求不能替代对其特殊特性和特殊关注的具体要求及评审,二者缺一不可!!!7E x t r a d t PQCFunctional Checks, Verification/Traceability, Safety Compliance and Component HandlingAll Products and Processes KPCA d i i o n a l S t a n d a r d 特殊额外一般所有产品/过程关注级别KCDS 金字塔:功能检测识别/确认/可追溯性安全、符合性零件处理产品级别:追溯性要求零件处理FMVSS:联邦机动车安全标准8特性级别:产品特性:工程文件中定义的零件、(子系统的特征,包括尺寸、性质、功能、化学成分、外观或涂层等。
特性是可测量的。
-标准产品特性Standard Product Characteristics-产品质量特性Product Quality Characteristics-关键产品特性Key Product Characteristics过程特性:过程参数,其变差必须被减少或保持/监控在目标值附近以确保产品特性符合客户要求。
- 1、下载文档前请自行甄别文档内容的完整性,平台不提供额外的编辑、内容补充、找答案等附加服务。
- 2、"仅部分预览"的文档,不可在线预览部分如存在完整性等问题,可反馈申请退款(可完整预览的文档不适用该条件!)。
- 3、如文档侵犯您的权益,请联系客服反馈,我们会尽快为您处理(人工客服工作时间:9:00-18:30)。
Key Characteristics DesignationSystemKCDS PyramidTable of RevisionsJanuary 1991: 1st IssueJune 1996: 1st RevisionNovember 1998: 2nd RevisionApplicable to Vehicle Groups through MY 2003Applicable to all Powertrain programs which end by Jan 2006March 2003: 3rd RevisionApplicable to Vehicle Groups for 2004 MY and beyondApplicable for all Powertrain programs in production after January2006The Key Characteristics Designation System reference manual GM 1805 QN was developed by a joint UAW-GM Quality Network TeamTable of ContentsSection1. Scope2. Purpose3. General: Benefits, Fundamental Concept for Characteristics4. Definitions5. Product Variation (includes Loss Function)6. Levels of Care7. The Three Stages of KCDS8. Selection Criteria for Parts9. Product Characteristics Pyramid10. Selection Criteria for Product Characteristics11. Tools12. Team Approach13. Objectives of the Team14. Composition of the Team15. Data Responsibility16. Documentation and Communication17. Reference SectionFigures and Tables1A GM KCDS Process2A Summary of Levels of Care vs. Cost4A Characteristic Definition7A Three Stages of KCDS8A GM Mandated Parts & Components: Product Identification & Verification 8B General Application Guidelines: Product Id, Traceability & Verification9A Product Characteristic Pyramid9B Relationship between KPC/PQC and KCC10A KCDS KCC Worksheet10B KPC/PQC/KCC Fishbone Diagram12A Part and Characteristic Action Steps Chart1.0 Scope1.1 This Reference Manual applies to:A. General Motors planning, product and process designs, manufacturingand assembly processes; andB. Suppliers (internal and external) of products and processes to GeneralMotors that are used in the design, manufacture, assembly, anddistribution of GM products.1.2 The Key Characteristic Designation System (KCDS) will commonize GeneralMotors’ approach for the identification and documentation of parts with SafetyCompliance Relationships, Functional Check Requirements, Product Identification,Verification & Traceability Requirements and Component Handling Requirements(additional care) and product characteristics that are designated as SpecialCharacteristics (extra care).1.3 KCDS also sets forth the methods and requirements for communication of partsrequiring additional care and Special Characteristics requiring extra care throughoutGeneral Motors and its supplier community1.4 The Key Characteristic Designation System Reference Manual is referenced inQuality System requirements ISO-9000, QS-9000 and the other elements ofAIAG/ASQ “7-Pack”.1.5 Additional/Extra Care in Manufacturing/Assembly is required at both the Part andCharacteristic levels.A. Functional Check, Product Traceability, Safety/Compliance and ComponentHandling requirements (additional care) do not replace the need to review apart for Special Characteristics (extra care).2.0 Purpose2.1 Employees are responsible for ensuring that GM products are designed, produced, anddelivered to meet the Voice of the Customer and to comply with applicable governmentstandards and regulations.A. As a means of exercising this responsibility and achieving conformance toother customer requirements, the implementation of KCDS in theorganization requires that the use of Standard Care and Additional or ExtraCare be designed into the Quality Systems.B. Standard Care describes the usual and customary practices that are appliedin the manufacturing and/or assembly environment to ensure specificationand print requirements are consistently met. Usual and Customary Careencompasses all of the basic methods and systems necessary to ensure thatthe product meet the Voice of the Customer based on loss function andsafety/ compliance requirements with government regulations.2.2 The Key Characteristic Designation System will aid in the economical manufacture ofquality products by:A. Establishing and managing a uniform system of identifying, documenting andcommunicating parts requiring Additional Care and Special Characteristicsthat require Extra Care. This is done to ensure consistency and complianceto customer requirements and government regulations within General Motorsand it’s supplier community.B. Supporting the reduction and maintenance/control of variation in themanufacturing and/or assembly process.C. Supporting the development of robust designs.2.3 Many parts require additional levels of checks and documentation. The following arepart level checks and documentation that are over and above Standard Care:A. Functional Checks are controls used by manufacturing and/or assemblyplants to ensure that parts, sub-systems, systems or completed vehiclescomply with requirements that are subject to, or have an effect on FederalMotor Vehicle Safety Standard (FMVSS), critical performance objectives,customer satisfaction, State Statutes, various Regional Complianceprocedures and/or Corporate Policies.B. Product Traceability identifies and verifies individual parts for correct usageby scanning individual major components for traceability associated witheach vehicle. Other parts/components supplied in labeled containers aretraced to groups of vehicles. This manual is intended to ensure that parts/components that must be verified and traced consistently by GM and itssuppliers. Traceability is a key tool in identifying parts related to vehiclesinvolved in campaign research.C. Safety/C ompliance parts may need Additional Care to ensure the product’ssafety and/or compliance with governmental regulations.D. Component Handling Best Practices identifies assembly and handlingrequirements that are necessary in addition to standard handling practices.E. Any part having a safety and/or compliance relationship must comply withgovernmental regulations and may require Functional Checks, ProductTraceability or Component Handling.2.4 When we unnecessarily require Additional Care on parts, we add to the product's costwithout increasing its value.2.5 All products, and the processes that are used to make them, have characteristics (orfeatures) that meet requirements.A. Special Characteristics (Key Product Characteristics (KPC) and ProductQuality Characteristics (PQC)) require Extra Care because excessivevariation could result in product quality losses or affect quality in subsequentmanufacturing operations.2.6 The reasons Characteristics are distinguished between Standard Care and those thatrequire Extra Care are:A. When we give equal attention to all product characteristics, thecharacteristics sensitive to manufacturing variation (i.e., those that requireExtra Care) may not receive sufficient attention. By focusing on the featuresthat are sensitive to manufacturing variation, greater improvements can bemade in product quality, cost and performance, thus improving customersatisfaction with the product.B. To achieve optimum cost and quality, appropriate attention in addition toStandard Care, should be given to the “critical few” rather than the “non-critical many”.2.7 Product Characteristics designated as KPC, which have consistently demonstratedtheir capability over time may be reduced to that of a PQC.2.8 Product Characteristics designated as PQC, which have consistently demonstratedtheir capability over time may be reduced to that of Standard Characteristics.2.9 When we require Extra Care on product characteristics that have consistentlydemonstrated capability over time, we add to the product's cost without increasing its value.Summary of the KCDS Pyramid3.0 General3.1 BenefitsA. KCDS helps ensure product quality during the product design phase, process design phase, and during the ongoing manufacturing and assembly operations.B.Beliefs & Values - The Key Characteristic Designation System (KCDS) facilitates the use of the UAW-GM Quality Network Beliefs & Valu es. It also supports the GM global community while improving customer satisfaction, communication, efficiency, and GM products. a. KCDS facilitates response to the Voice of the Customer, utilizingteamwork to improve customer satisfaction.b. When the KCDS template is used early in the development of aproduct, it helps ensure robust designs and processes that are less sensitive to variation, thus leading to increased customer satisfaction and ultimately greater job security.C.Communication - KCDS supports the concurrent (simultaneous)engineering process by use of standardized definitions, procedures, work instructions and documents. This improves communication betweenengineering, suppliers, production plants and other supporting activities. D.Product Design - KCDS improves product design and development methods. It identifies safety and compliance requirements early. It alsoreveals design areas that may not be robust and may need additional efforts during the development process.E.Process Design - KCDS improves process design and development methods by aligning process strengths with Safety/ Compliancerequirements, product traceability, functional checks, component handling, KPC, PQC and Standard Characteristics.F.Manufacturing and Assembly – KCDS helps improve manufacturing and assembly operations. The focus is on Quality Improvement, Variation Reduction and Maintenance efforts on products and processes that haveAs CARE Increases, COST increasesDetail of Levels of Care vs Costbeen identified as important to customer satisfaction and/or related toSafety/Compliance.G. Standardized Work Processes - KCDS supports the implementation ofStandardized Work Processes through the use of Process Flow Diagrams,Process Control Plans and People Focused Practices.3.2 Fundamental Concepts for CharacteristicsA. Basic concepts for the classification of characteristics are summarized inTable 4A.a. There are two kinds of characteristics:Product–There are three basic categories of ProductCharacteristics:- Standard Product Characteristics- Product Quality Characteristics- Key Product CharacteristicsProcess - There are two basic categories of ProcessCharacteristics:-Standard Control Characteristics-Key Control Characteristicsb. Control of Process Characteristics ensures that variation of aProduct Characteristic is reduced or maintained/controlled.B. The designations of “additional care” and “extra care” are based on theprinciple that GM’s minimum level of standard care is in place.C. The identification of Special Product Characteristics involves judgment andexperience and is best done in the concurrent (simultaneous) engineeringprocess, which involves all functions and a broad range of experience.4.0 Definitions4.1 Part LevelA. Safety/Compliance– Regulatory or corporate requirements on a part, sub-system or system that can affect compliance with government regulations orvehicle/product safety performance to said regulations.B. Functional Checks - Checks performed by manufacturing and/or assemblyplant personnel to observe, verify and help ensure that the operations of a part,sub-system, system or completed vehicle comply to requirements that aresubject to or have an effect on FMVSS, critical performance objectives,customer satisfaction or State Statutes.C. Product Verification and Traceability – A tracking method used in the GMmanufacturing process to track and document parts and components from thepoint and time of manufacture to a specific vehicle/vehicle identification number(VIN).D. Component Handling Best Practices - Identifies assembly and handlingrequirements that are necessary in addition to standard practices. Thesebest practices are intended to provide direction to the assembly plantsregarding critical components.4.2 Characteristic LevelA. A Product Characteristic is a feature of a part, sub-system or system (suchas dimension, property, function, chemistry, appearance, or finish) onengineering documentation. The characteristic is classified as Special orStandard and can be measured.B. A Key Product Characteristic (KPC) is a special characteristic where theloss function shows that reasonably anticipated variation within specificationcould significantly affect customer satisfaction with a product.a. Maintaining/controlling the process within the target zone canoptimize customer satisfaction.b. For organizations that use symbols to designate specialcharacteristics, use the symbols in Table 4A.C. A Product Quality Characteristic (PQC) is a special characteristic in whichthe customer is equally satisfied across the entire specification, but the lossfunction is steep just outside of the specification limits.a. Variation within the tolerance does not significantly affectcustomer satisfaction, whereas variation outside the tolerancemay significantly impact customer satisfaction.b. For organizations that use symbols to designate specialcharacteristics, use the symbols in Table 4A.D. A Standard Product Characteristic is a characteristic where the lossfunction shows no incremental economic or customer satisfaction loss insidethe tolerance. The customer is equally satisfied across the tolerance.a. Variation within the tolerance does not significantly affectcustomer satisfaction.E. Special Product Characteristics must be identified on engineeringdocuments such as: drawings, Global Product Description System (GPDS),specifications, Product Assembly Documents (PADS), layouts, process flowdiagrams, process control plans and/or other primary engineering documentsper local Engineering requirements.Characteristic Sumary Table 4Aσσ)The above definitions are based on the principle that Standard Care is followed duringmanufacturing and assembly. This principle applies to characteristics measured by attribute or variable data.4.3 Target Zone - the area within specifications that satisfies the customer. This may or maynot be the nominal value.4.4 Variable data – data that is continuous and measurable relative to the specificationson a continuous scale such as millimeters, kilograms, etc.4.5 Attribute data– data for characteristics measured with and resulting from correct partor incorrect part, present or not present, etc., and is generally synonymous withconformance or nonconformance and when designated as a special productcharacteristic an attribute control method shall be used.4.6 Process Characteristics related to Special Product Characteristics must be documentedon process control plans, process flow diagrams or manufacturing and/or assembly workinstructions.A. A Process Characteristic is a Process Parameter for which variation must bereduced or maintained/controlled around a target value to ensure thatcustomer requirements are met.a. Process Characteristics are further classified as Key ControlCharacteristics or Standard Control Characteristics.b. A Key Control Characteristic (KCC) is a process parameter(such as temperature, speed, pressure, viscosity, etc.) thathas a strong causal relationship to a Key ProductCharacteristic or Product Quality Characteristic. Variation mustbe reduced around some target value to ensure that variationin a Key Product Characteristic is reduced around its targetvalue. Variation must be maintained/controlled around sometarget value to ensure that variation in a PQC ismaintained/controlled around its target value.c. A Standard Control Characteristic is a process parameter thatcontrols or affects one or more product characteristics.d. When Process Characteristics are controlled to requirements,product quality levels are predictable.5.0 Product Variation5.1 The designation of Special Characteristics - Key Product Characteristics (KPC) andProduct Quality Characteristics (PQC) - provides additional information to product andprocess design, pre-production, production and monitoring/inspection organizationsthat can be used to direct “extra care” on characteristics according to theconsequences of the Loss Function.A. Loss Function is “The incremental economic / customer satisfaction loss forany deviation from a customer specified target zone. The target zone is thetolerance zone that will lead a customer to praise the product.” (Ref. TheDeming Route by William W. Scherhenback )5.2 Variation is inherent in any manufacturing and/or assembly process. Knowledge of themagnitude and consequences of this variation will help Engineers design appropriateproducts and processes within appropriate parameters that meet or exceed customerrequirements. Manufacturing and/or assembly can then control the processesaccordingly.A. The concept of “reasonably anticipated” variation stresses the importance ofanticipated variation and likelihood of occurrence in determining theclassification.a. Reasonably anticipated variation within the KCDS process is interpretedto mean the expected variation from a given process.b. To develop robust designs, engineers must have knowledge of themagnitude of the inherent variation in the manufacturing and orassembly process as early as possible in the design process.B. It is necessary to anticipate, through the use of historical data and otherengineering tools, the magnitude and consequence of the variation thatcould reasonably be expected to occur during manufacturing and/orassembly, if Standard Care were to be used.6.0 Levels of Care are intended to define the requirements in the manufacturing andassembly environment needed to ensure economical manufacture of quality products.These requirements must be described in local quality procedures, business unitprocedures and other quality procedures. The relationship between part andcharacteristic levels of care is described below:Level of CareAll Products & Processes Standard CarePart LevelProduct Safety/Compliance Additional CareFunctional Checks Additional CareProduct Traceability Additional CareComponent Handling Additional CareCharacteristic LevelKey Product Characteristics Extra CareProduct Quality Characteristics Extra Care6.1 Standard Care describes the usual and customary practices that are applied in themanufacturing and/or assembly environment to ensure requirements are consistentlymet. Standard Care encompasses all of the basic methods and systems necessary toensure that the product meets the Voice of the Customer and safety/ compliancerequirements with government regulations. These practices should be described in thelocal procedures, business unit procedures and other quality procedures. StandardCare is typically interpreted to mean that the basic quality system should describe thefundamental administrative, product, and process practices and systems. StandardCare requires that the production system be designed to manufacture products thatmeet requirements, as well as protect our customers from any nonconforming material.A. Standard Carea. Process Related Practices and Systems:-Detailed Job Instructions-Gage Certification, Calibration and ControlPrograms-Planned Maintenance Procedures-Operator Training-System for Ensuring that Processes are Capableof Consistently Producing Parts/Assemblies withinEngineering Specificationsb. Product-Related Practices and Systems:- A System for Implementing Engineering Changes-Production Part Approval-Systems that Identify Nonconformance,Communicate the Nonconformance, and MakeDisposition and Corrective Action for theNonconformance (Containment)-Systems for the Identification and Control ofMaterial- A System for Ensuring that Purchased Parts andProcesses Meet Engineering Requirements-Measurement and Feedback Systems Relative toAchieving Engineering Requirements-Quality System that Meets the Requirements ofthe Appropriate International Standardc. Administrative Practices and Systems:-Systems to Ensure Adherence to Corporate,Group, Divisional, and Local Procedures-Quality Procedures that Describe the QualityPractices and Systems-Record Control and Retention System6.2 Additional Care is required in the manufacturing and or assembly process. It is a setof methods/controls employed to ensure processes are producing parts which meet customer requirements for Safety/ Compliance, Functional Checks, ProductTraceability and Component Handling.A. A Process Flow Diagram and a Process Control Plan describe each process.Quality is focused on meeting customer requirements.B. Safety/Compliance level of care includes those parts, that may affect thesafety of the product or compliance with any government standards orregulations. These parts require ongoing controls in manufacturing.a. If the product does not meet the requirements, local and corporateprocedures regarding containment and documentation should befollowed.b. Communication, problem resolution, and disposition should followvarious regional requirements.c. Specific documentation retention requirements apply to allSafety/Compliance parts.C. Functional Checks are focused on ensuring the reliability, consistency ofoperations as intended and customer satisfaction through in-line checks andaudits. If the product does not meet the requirements, local and corporateprocedures regarding containment and documentation should be followed.D. Product Traceability is focused on ensuring that parts requiring traceabilityare properly identified and verified in the manufacturing/assembly process.The process needs to be error proofed to ensure the necessary data iscaptured and stored. If the product and/or process does not meet therequirements, the organization shall follow local and corporate proceduresregarding containment and documentation.E. Component Handling Best Practices (Do’s and Don’ts) are focused onensuring that parts requiring special assembly and handling practices areconsistently communicated and implemented at manufacturing/assemblyplants.6.3 Extra Care applies to Special Characteristics. It defines the level of care required formanaging and controlling variation in manufacturing and/or assembly.A. If manufacturing and/or assembly variation with Standard Care is likely tohave significant impact to the customer, based on the loss function, thenExtra Care must be used to ensure customer satisfaction.B. If the characteristic is designated as a Key ProductCharacteristic, variation shall be reduced.- Variation reduction is not required during the period when you are provingstability. Refer to Section 2.7.C.If the characteristic is designated as a Product Quality Characteristic, variation shall be maintained/controlled at a designated level above Standard Care. D. Controls should be applied at the process characteristic level (KCC).7.0 The Three Stages of KCDSFigure 7A summarizes the concept behind KCDS. It displays the three stages of the system within the Global Vehicle Development Process.Stage 1 Stage 2 Concurrent (Simultaneous) Engineering Figure 7AA. In Stage One, the team identifies which parts require additional care(Functional Checks/Product Traceability/Safety Compliance/ComponentHandling) in manufacturing and Assembly and which characteristics areSpecial Characteristics. Product Engineering leads the team thatdesignates parts requiring additional care and extra care. Ideally thisoccurs during the Planning and Concept Stages of the GVDP. However,it could be prolonged through the Structure and Integration Releaseperiods within the GVDP.B. In Stage Two, controls and/or process requirements are determined for allparts requiring additional and extra care. Manufacturing Engineeringleads the team that establishes the process requirements for partsrequiring additional and extra care (and control plans to document thereduction or maintenance/control of KPC/PQC variation).C. In Stage Three, controls of the parts requiring additional care areimplemented into the manufacturing and/or assembly process to ensureproduct conformance. Controls on the KCC are implemented to ensurethat variation is reduced or maintained/controlled. Manufacturing appliesand improves these controls from Prototype and through Productionwithin the GVDP.7.2 Details of the Stages in the Global Vehicle Development ProcessA. Planning Stage: Shared Vision Development and Concept/Product Formationand Manufacturing System Concept Development and Refinement. During thisPlanning Stage, parts that need to go through the KCDS process are selected.B. Stage 1: Product Engineeringa. Lead Responsibility – Design Release Engineer (DRE/DE)b. Support Activities:-Manufacturing Engineer-Plant Representative-Supplier Quality Engineer-KCDS Engineer-Product Development Quality Representative-Dimensional Engineer-Service Engineer-Product Safety Representative-Fastening Engineerc. The following steps are used to identify, document and communicateall parts requiring additional and extra care.-Define customer satisfaction needs and focus on product and systemdefinitions. The method for doing this uses Voice of the Customer tools.-Define customer requirements, both internal (use reliability, quality,performance and manufacturing records) and retail (use marketresearch).-Define product requirements. Consider government regulations andQuality, Reliability and Durability (QRD) targets.-Do the appropriate design analyses and development to ensurefunction and robustness, depending on the newness and complexity ofthe product? Here are some design analysis techniques:o Design Failure Modes and Effects Analysis (DFMEA)o Risk Analysiso Design of Experiments (DOE)o Loss Functiono DFSS (Design for Six Sigma) – (i.e., Critical to Quality(CTQ))o Fault Tree Analysis (FTA)o Monte Carlo Studiesd. Use criteria in, Sections 8 & 10, to determine the partsrequiring additional and extra care, respectively.e. Record all parts requiring additional care and KPC/PQCs inGPDS, on drawings, PADS, product specifications, and/or otherprimary engineering documents, as required by localEngineering Procedures. To do this the DRE is to write a workorder (WO) authorizing the change. The DRE also uses theWO process to authorize the deletion of unnecessary redundantor obsolete additional care requirements & KPC/PQCs.f. Validate requirements by testing the parts requiring additionalcare and KPC/PQCs against the initial process parameters at alllevels: part, subsystem, system and vehicle, per the AssemblyPlant Quality Manual.C. Stage 2: Manufacturing Engineeringa. Lead Responsibility - Manufacturing Engineerb. Support Activities:-Design Release Engineer (DRE/DE)-Plant Representative-Supplier Quality Engineer-KCDS Engineer-Product Development Quality Representative-Dimensional Engineer-Service Engineer-Product Safety Representative-Fastening Engineerc. Define the process design and release requirements using the partsrequiring additional care and KPC/PQCs as input.d. Do the appropriate process analyses and development to ensurecapability and robustness, depending on the newness and complexity ofthe product? Here are some process analysis techniques:-Process Failure Modes and Effect Analysis (PFMEA)-Failure Prevention Analysis (FPA)-Fault Tree Analysis (FTA)e. Complete the Process Flow Diagram.f. Record parts requiring additional care and KPC/PQCs on the ProcessFlow Diagram and Process Control Plan.g. Set target values for KPC/PQCs and KCCs and provide amethod for control.h. Determine controls and/or process requirements for partsrequiring additional care and KPC/PQCs.i. Perform Measurement System Analysis.j. Do capability studies for KPC/PQC and, as appropriate for KCCs.D. Stage 3: Manufacturing and Assemblya. Lead Responsibility - Manufacturing/Assembly Representativeb. Support Responsibility:-Manufacturing Engineer-Product Release Engineer (DRE/DE)。