QP18检验及试验控制程序
QP18质量数据分析控制程序

1.0 目的采用适当的统计技术,确保产品质量及产品质量形成过程得到有效分析、维护并达到持续改进的目的。
2.0 适用范围产品质量特性及质量形成的过程特性。
3.0 职责3.1各部门负责有关数据的收集、分析及统计技术应用。
3.2 管理者代表负责组织数据分析。
4.0工作程序4.1质量目标数据分析和统计4.1.1管理者代表组织各部门经理按公司的宗旨和总经理的要求将公司质量目标在每一部门进行分解,形成《质量目标一览表》。
4.1.2各部门每月对部门质量目标实现情况进行数据统计分析,形成书面质量目标达成分析记录,做为管理评审输入信息和数据。
4.1.2管理者代表负责每月汇总分析一次公司质量目标实现情况,并作为管理评审的重要评审输入信息。
4.2其他需收集的数据资料包括:4.2.1客户满意情况和投诉处理情况。
4.2.2过程和产品的特性及趋势,品质目标达成情况。
4.2.3供应商交货达成情况,与产品要求的符合性。
4.2.4本公司确认的其他分析资料。
4.3质量管理体系改进过程中信息与数据的分析4.3.1行政部负责收集分析内审、外审不符合项及其验证有关的数据。
4.4常用统计方法常用统计方法有:随机抽样法、数理统计法、调查表法、因果分析法、排列图法等。
4.4.1 随机抽样法:主要运用于材料检查、产品质量检查、内部审核,抽取具有代表性的子样,用以评定工作质量和管理体系运行的充分性、有效性。
4.4.2数理统计法:按有关规定应用于产品质量趋势分析统计。
4.4.3调查表:对影响产品质量的不稳定因素进行调查,列表分析,找出原因,采取措施。
4.4.4因果图:主要运用于分析表达结果或问题与影响因素之间的因果关系,找出根源,解决问题,常用于外包过程中的质量和不合格的原因分析等。
4.4.5排列图:适用于分析主要外包过程不合格的原因,对比采取措施前后的效果。
4.5管理体系改进要求4.5.1各部门在各种管理信息和数据分析过程中,发现需采取相应措施进行改进,应制订必要措施实施改进,并验证改进效果。
QP-18外发加工控制程序

1.0目的为加强公司产品外发作业控制,特制定本作业指导。
2.0适用范围适用于公司所有产品外发作业全过程。
3.0工作职责3.1 客户部:对客户产品资料、有效样板做准确、规范处理并以书面形式及时传达到相关部门。
3.2 PMC:负责统筹外发作业。
3.3品管部:外发产品相关资料、有效样板的提供,并对外发过程品质进行有效监控,确保质量合乎规定要求。
3.4 仓库:负责外发物品发货、收货的规范运作并对物品进行有效保管和处理。
4.0作业程序4.1外发加工计划4.1.1PMC负责编制外发加工生产计划并及时开具《外发生产通知单》,COPY二份分送仓库和品管部,以便协调组织外发生产,原件生产部保存留档。
4.1.2生产部主管根据《外发生产通知单》统筹安排备料工作以供外协厂及时组织生产。
4.1.2.1如属公司生产工单中部分外发,且相关物料已全部或大部分已被相关生产车间领用,则由生产部统筹相关工场备料,仓库管理员经过复验无误后交付外协厂组织生产。
4.1.2.2如属外发生产单全部外发物料均在仓库,则由仓库统一备料交付外协厂使用。
4.2送料作业4.2.1当需送料至外协厂进行加工生产时,由仓库根据物料清单上的物料开具《送货单》,连同物料交与送货员送交外协厂。
4.2.2送货员按相关程序完成审批手续后,于规定时间内将物料送至指定地点,未按程序运作或签名手续不完备,保安可拒绝放行。
4.2.3送货员送货至目的地后,按相应程序完成物料的交接工作。
并将经收货单位负责人签收后单据在规定时间送仓库、财务部存档并做相应处理。
4.3外发生产过程的品质控制4.3.1如外协厂首次生产,由品管部外派品管人员负责召集外协厂相关人员进行产品质量相关介绍,以便达成共识顺利组织生产。
4.3.2外协厂首件产品生产出来时,公司外派品管人员依据产品质量相关标准要求第一时间签署二份首件样板,一份留外协厂作为生产时参考依据,一份带回公司妥善保管以备日后查验。
4.3.3外派品管人员根据外协厂生产产品的难易程度及生产状况确定品质监控频率和品质监控方式,以帮助外协厂生产正常、品质稳定。
XXX-QP-18管理评审控制程序OK

5.3.8管理体系及相应文件是否需修改;
5.3.9组织机构的适宜性及资源(人、财、设施、环境)需求;
5.3.10管理体系的适宜性、充分性和有效性,法律法规的符合性;
5.3.11外部供方的绩效;
5.3.12应对风险和机遇所采取措施的有效性;
5.3.13适用时的保修绩效;
5.3.14适用时,顾客计分卡评审;
5.2.3产品质量出现重大事故或顾客反映信息非常强烈时,须进行管理评审。
5.3评审内容:
5.3.1.管理体系内部审核的结果(可见《内部审核程序》);
5.3.2.重要的客户投诉、相关方的意见和要求及期望(包括满意度及有益的建议等);
5.3.3第三方监督审核结果、工艺过程方法改进等过程和产品监视和测量的结果;
5.3.15实际使用现场失效及其对安全的影响;
5.3.16检讨与评估管理体系绩效;
5.3.17重大品质事故及有关纠正与预防措施的有效性检讨;
5.3.18可能影响管理体系的变更,检讨变更后的适合性;
5.3.19资讯回馈处理情形,包括实际使用现场失效及其对安全的影响;
5.3.20过程有效性和效率的衡量;
文件发行及分发状况
分发部门
营销中心
研发中心
制造中心
资材中心
企划中心
知识产权中心
品质中心
人力行政中心
财务中心
受控章
份数
变更履历
No.
版本
修订日期
修订内容
责任者
1
A00
2018-4-2
初版发行
xxx
2
3
4
5
6
7
8
9
10
11
12
QP-18设计输入控制程序

W文e m件ake编the号world
flexible.
LX-QP-18
机密等级
□機密■一 般
版本
A0
页次 类别
第1页,共2页
二阶
1.目的
对过程设计输 入形成的文件进
2.范围 适用于本厂全
部产品的样件问 3.职责
业务部:收集 客工户程信部息:;负责 设计过程的输
4.流程描述
4.1生产过程输 入控制流程图
生产部/品检部
相关检 验报告
文件编号
机密等级
版本 页次 类别 5.过程图
LX-QPN-NO1G8 □機密■一
般 A0
第2页,共2页
二阶
设计输入控制程序
制訂日 修訂日 主辦 審核 核准
2008/12/15 肖萍招
相关文件资讯
用什么资源(设备、材料等)?谁来做? 业务部门主导,其他 部门配合
产品制造过程的需求 输入 制造过程设计 输入过程图
生产部/品检部 /工程部
产品/相 关检验记
录表单
1天
6.设计输出 YES
7.评审
NO
YES
8.试生产
9.检验
NO
YES NO10.确认Fra bibliotekYES
11. 批量生产
6.工程部负责地对产品过程设计按照《APQP作业规 范》《FMEA作业规范》进行设计输出
工程部
设计的相 关项目
1天
7.再由工程部将设计输出的记录交由APQP小组进行 多方论证评审,评审不合格时将重新更改生产过程设 计.
流程图
设计输入控制程序
作业说明
1.根据以往产品的 生产工艺提出设计
1.APQP小组根据新项目的实施需求进行设计
HC-QP-18标识及批次控制程序(质量管理体系)-陶瓷厂

1.0 目的对物资及产品划分批次并实施必要的标识,以便识别和区分状态,以确保需要时对产品质量形成过程实现可追溯性,确保物资及产品不致混淆和错用。
2.0 适应范围本程序适用于对产品形成全过程的产品批次划分及标识,实施可追溯性控制。
3.0 术语3.1 本程序采用ISO9000:2015《质量管理体系·基础和术语》和本公司《质量手册》中的有关术语及其定义。
4.0 职责4.1 销售部负责设定产品批次(合同号)4.2 质检部负责标识系统的建立,确定标识的手段和方法以及适应范围,负责对标识工作的控制和管理。
4.3 各相关部门实施批次的记录和产品标识。
5.0 工作程序5.1 标识手段及方法5.1.1本公司的产品标识主要有:挂牌、标签、记录、标记、贴标等。
5.1.2对产品存放划分区域并挂牌标识。
5.1.3工序过程的产品可采用标记方式,最终产品和产品外包装采用标记或贴标方式。
5.1.4记录的方式可以同其它的标识方法同时使用。
5.2 物资标识5.2.1进货物资由仓管员根据物资的包装和贮存方式,选用合适的方式进行标识。
标识的内容可在相关的记录上体现,对不同检验或试验状态的物资的存放场所,应对应地划分区域。
5.2.2生产过程物资的标识,参照进货物资的标识。
生产过程的物资均为检验合格物资,对物资标识内容主要有品名(型号)等。
5.3 生产过程的产品标识5.3.1本公司生产各类陶瓷产品,其品种、规定及花面、色彩所构成的外观形态及特征明显,易于辨识,不易混淆,不必要直接对产品采用外观状态标识。
而采用记录的方式。
5.3.2 日用瓷产品采用“成型生产记录表”方式,附随相关的产品车。
土坯检验后,合格品用食品红色以“√”标示,不合格品存入有标识的容器中,返工产品以透明卡标示。
成品采用挂卡方式标示,内容包括:合同号、生产批次、时间、产品编号、产品名称、布产数量、生产人员等作为追溯的依据。
烧成白胎检验后,质检部用红橙绿三种颜色标示存放产品的检验状态,红色表示‘报废产品’,橙色表示‘返工产品’,绿色表示‘合格品’。
量测仪器管理程序QP-18

發行日期: 制作: 審查:核准:1、目的保證檢驗、試驗和測量儀器能夠達到所需的測量能力,確保産品符合規格要求及環境規定要求。
2、適用範圍適用於本公司範圍內用於産品與環境測量、測試用的量測儀器。
3、權責3.1品保部:負責本公司所有計量儀器的校正、送修、驗收和管理等工作。
3.2各部門:負責測量和監控設備的請購、使用和日常維護。
4、定義(無)5、內容5.1儀器的請購5.1.1各部門依實際需要,提出量測儀器的請購。
5.1.2請購單經品保部儀校室會簽,必要時呈總經理或副總批准後交採購部門處理。
5.2儀器的驗收、登錄5.2.1新購入的量測儀器均須經品保部驗收,並填寫《驗收單》。
5.2.2驗收合格的儀器,由品保部記錄在《量測儀器一覽表》上,並確定其校驗周期及校驗方式。
5.2.3品保部依據CT後接流水號四位,如CT-□□□□進行編號,並在量測儀器或其包裝上適當的位置標示此編號後,交請購部門使用。
5.3儀器校驗交歸程式5.3.1校驗人員根據《量測儀器一覽表》須在每月25日前向量測儀器使用部門發出下一個月的《校驗通知書》。
5.3.2量測儀器使用部門依據《校驗通知書》於校驗到期日,將量測儀器交到校驗室,若有特殊原因,需知會校驗人員並于到期日後儘快送校。
5.3.3逾期未送校儀器由校驗管理人員至使用單位貼上“暫停使用”標簽或強制收回。
5.3.4當儀器校驗完成後,由校驗人員送回使用部門。
5.3.5儀器使用人如果發現使用儀器故障或誤差過大,使用單位應填寫維修單,並詳注各種不良現象,經單位課長確認後,連同儀器交品保單位元處理。
5.4儀器的免校5.4.1品保部依據儀器設備之使用狀況,如未使用於産品質量及環境質量直接判定或與産品質量及環境質量無直接關係者,可列入“免校”。
5.4.2列入免校的儀器設備需貼上“免校驗”標簽。
5.5儀器的內校5.5.1校驗人員應至少具有高中以上學歷,國家級單位培訓之合格人員。
5.5.2內校溫、濕度除另有特殊規定外,以溫度25±5°C,濕度爲65%±10%爲准。
设备管理控制程序LM-QP-18

设备管理控制程序1.目的确定提供和维护为实现产品的符合性所需的设施,确定并管理为实现产品符合性所需的工作环境中人和物的因素。
2.范围适用于为实现产品符合性所需的设施,如工作场所、硬件和软件、模具和设备、支持性服务如通讯、运输设施等的控制;对工作环境中的人和物的因素进行控制。
3.职责3.1生产中心是本公司设施和工作环境的归口管理部门,负责对实现产品符合性所需的设施和工作环境进行控制。
3.2行政部负责公司办公设施和工作环境的管理控制。
3.3各部门负责本部门的设施管理,并对产品符合性所需的工作环境进行管理。
4.术语及定义无5.工作程序5.1对设施及工作环境确定5.1.1生产中心组织对本公司的所有设施和工作环境进行确定,设施包括:工作场所(车间、办公场所等)、设备和治具模具、支持性服务(水、电、气供应)、通讯设施、运输设施等。
5.2生产设施的提供和维护5.2.1设施的提供a)生产中心根据生产的使用要求及公司发展的需要,填写《设备购置申请单》,注明设施名称、用途、型号规格、技术参数、单价、数量等,报董事长批准,采购人员具体实施采购;b)通讯和运输设施由行政部根据需要写出计划,报副总经理批准后实施采购。
5.2.2设施的验收a)采购的设施,生产中心组织有关部门进行安装调试,确认满足要求后,由使用部门在《设备验收记录》上签字验收,并记录设施名称、型号规格、技术参数、数量、随机附件及资料等内容。
《设备验收记录》由设备车间保存。
通讯和办公设施由行政部组织进行验收; b)验收不合格的设施,由采购人员与供方协商解决,并在《设施验收记录》上记录处理结果;c)设备车间根据合格的设施验收单进行编号,建立《设备台帐》和设施档案;5.2.3设施的使用、维护和保养a)根据生产需要,由设备车间组织编写设施的操作规程,并打印上墙,以便操作。
对于大型、精密设备或关键、特殊过程所用的设施必须有操作规程,相关操作人员应由各车间负责人组织培训、考核合格后,持证上岗;b)设备车间制定《设备日常保养记录》,规定保养项目、频次,发给使用班组执行,各岗位负责人监督检查执行情况。
印刷QP18过程及最终检验控制程序

印刷QP18过程及最终检验控制程序1.前期准备:在印刷QP18之前,需要完成以下准备工作:-准备所需的印刷QP18图纸和规格要求。
-准备印刷机器和设备,确保其正常运行。
2.材料准备:-根据图纸和规格要求,准备所需的QP18材料。
包括纸张、油墨、印版等。
-检查材料的质量和数量,并进行记录。
3.印刷准备:-将所需的印版安装到印刷机上,并进行调整和测试,确保其位置和运行正常。
-调整印刷机的其他参数,如印刷压力、颜色阈值等,以满足QP18的规格要求。
4.印刷过程:-将所需的纸张放入印刷机中,调整其位置和张力。
-根据印版上的图案,将油墨喷在印版上,并通过印刷机的滚筒将油墨转移到纸张上。
-控制印刷机的速度和运行时间,确保质量和产量的平衡。
-按照图纸上的要求,进行多次印刷,以确保QP18的质量和颜色一致。
5.最终检验:-在印刷完成后,将印刷QP18取出,并进行最终检验。
-检查QP18的质量和尺寸是否符合规格要求。
-使用光谱仪和颜色比较器等工具,检查QP18的颜色是否与图纸要求一致。
-检查QP18的印刷质量,如是否有印刷漏墨、油墨分散不均等问题。
-检查QP18的外观质量,如有无折痕、划痕等。
-将检验结果进行记录,并进行分类和分析,以便后续改进和控制。
最终检验控制程序:1.制定最终检验标准:根据图纸和规格要求,制定QP18的最终检验标准。
明确检验项目和要求,以及合格和不合格的判定标准。
2.建立检验记录表:建立QP18最终检验的记录表格,包括检验项目、检验方法、检验员、检验日期等信息。
3.检验设备和工具准备:准备所需的检验设备和工具,如光谱仪、颜色比较器、显微镜、千分尺等,确保其正常运行和准确度。
4.检验流程:执行最终检验流程,并按照标准和要求进行检验。
包括以下步骤:-根据检验记录表,检查QP18的外观质量,如有无折痕、划痕等。
-使用光谱仪和颜色比较器等工具,检查QP18的颜色是否与图纸要求一致。
-检查QP18的尺寸和形状是否符合规格要求。
QP-18 不合格品控制程序

XX/QP-18 不合格品控制程序A版1. 目的建立不合格品控制程序,对不合格品进行识别和控制,防止不合格品的非预期使用或交付。
2. 适用范围适用于对原材料、半成品、成品及交付产品所发生的不合格的控制3.职责3.1 质管部负责不合格的识别,并跟踪不合格品的处理结果。
3.2 相关部门负责人在各自职责范围内,对不合格品作处理决定。
3.3 相关部门负责对不合格品采取纠正措施。
4. 正文4.1 不合格品定义本文所指的不合格品是经检验不符合质量标准的原材料、半成品及成品;超过有效期的原辅料、半成品、成品;在制造、储存过程中由于偏离相关标准并经质管部确认存在或潜在质量风险而不放行的物料、半成品、成品。
4.2 不合格品的类别:4.2.1 经检验不合格的原辅料。
4.2.2 经检验不合格的包装材料。
4.2.3 生产中产生的不合格半成品、成品。
4.2.4 退货和收回经检验不合格的成品。
4.3 不合格品管理的基本原则4.3.1 不合格原辅料、包装材料不得投入生产,不合格半成品不得流入下道工序,不合格成品不得出厂。
4.3.2 应设立不合格品区,对不合格品实施单独存放,避免发生混淆引起差错。
4.3.3 不合格品的处理按各自特性以不对卫生、环境造成危害进行处理。
4.4 当发现不合格原辅料、包装材料、半成品和成品时应按下列要求管理4.4.1 发生不合格品后立即将不合格品放置在不合格品库(区),挂上不合格标识牌。
4.4.2 所有不合格品的处理需由质管部门开具《产品不合格通知单》,查明原因并书面给出处理意见后由相关部门进行处理。
必要时,由质管部按照《纠正和预防措施控制程序》对产生不合格的原因作出分析后采取纠正及预防措施,发送相关部门《纠正/预防措施处理单》,质管部跟踪后续执行情况并记录。
4.4.3 对于进货检验时发现的不合格原辅料、包装材料应拒收,并由供销部门做退货处理;对于在物料储存期间复检时发现的不合格物料应做报废、销毁处理。
印刷QP18过程及最终检验控制程序
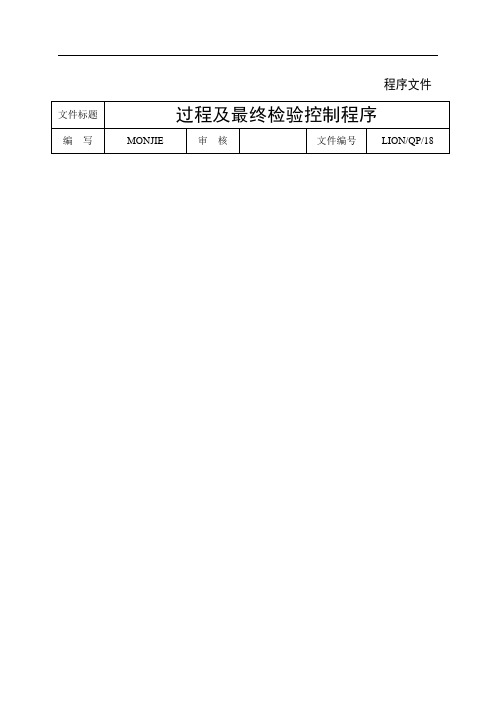
5.1.2 机台自检 机台操作人员要在生产中进行自检,并在“产品物流标签”中记录,自检中操
作人员如发现产品质量异常,应及时暂停作业,并向机长/车间主任报告,以寻求 改善的措施。 5.1.3 巡回检验
文件标题 编写
程序文件
过程及最终检验控制程序
MONJIE
审核
文件编号 LION/QP/18
程序文件
文件标题
过程及最终检验控制程序
编写
MONJIE
审核
文件编号 LION/QP/18
1 目的 保证所有产品在生产过程中都通过规定的检验后才进入下一道工序或入仓。
2 适用范围 本程序适用于公司内所有在制品、半成品、成品。
5 作业程序 5.1 过程检验 5.1.l 首件签样 a. 各工序/机台在正式生产前必须进行首件签样,第一次生产的新产品由生产部经理和
品管部经理、技术部经理共同签样;重复生产的产品由各工序车间主任、品质主任(或 其授权人)签首件样。 b. 机台操作人员照样生产。 c. 巡检员应对首件样进行校对,发现问题及时报告。
3. 定义 3.1 过程:一组将输入转化为输出的相互关联或相互作用的活动。 3.2 检验:通过观察和判断,适当时结合测量、试验所进行的符合性评价。
4 职责 4.1 生产车间各机台负责自检工作。 4.2 生产部会同品管部一道做好首件签样。 4.3 品管部负责巡检和成品的抽检与成品抽查工作。 4.4 生产部检标车间做好成品的检验和包装入库工作。
QP-18数据分析控制管理流程(A0版16-06)

Wing Shing Toys(H.K)Limited
数据分析控制管理流程
文件编号:YS/QP-18受控状态:
编制
审批
文件发放部门:
工程部QA/QC 部
PPC 生产计划部
采购部
仓库部维设部所有生产部
HK 来源部
HK 成本部
HK PPMC
版本生效(发布)日期
修订编制概述记要备注A/0
2016/06
首次发布
生效日期2016年06月01日
1.目的:
提供符合要求和质量管理体系有效运行的证据,规范数据资料的收集、分析和统计技术的使用,以支持产品、过程和质量管理体系的策划、实施和持续改进,增强顾客满意,增强供应商的管理及改进,以改进公司的业绩。
2.范围:
适用于质量管理体系运行过程中的测量、监视和其他活动与过程的数据收集、分析和评价的控制管理。
3.职责:
3.1质检部负责公司质量数据、外部供方绩效数据的收集、分析及统计技术的推广、应用和效果验证;
3.2工程部负责公司产品设计开发、产品改进、制造过程设计开发、过程能力监控和过程改进的数据收
集、分析及统计技术应用;
3.3PPMC销售/业务部负责公司生产经营数据、顾客满意程度的收集、分析;
3.4各单位负责业务范围内的数据收集、分析和统计技术应用,并按规定向相关部门传递、交流。
4.数据分析管理工作流程及工作流程说明:
生效日期2016年06月01日5.2数据分析控制工作流程标准
生效日期2016年06月01日
5.0引用文件
《产品检验放行控制管理流程》
《文件信息控制管理流程》
《持续改进控制管理流程》
6.0引用表单
《统计技术应用表》。
18,QP18纠正措施管理程序 word9001程序

文件修改记录
1目的
通过本程序的实施,对发现的不符合采取有效的纠正措施要求,避免或降低公司经营管理风险,实现管理体系的持续改进。
2范围
C确定类似的不符合是否存在,或可能潜在发生的不符合;
e制定纠正措施。
制定的纠正措施应充分考虑实施的风险
5. 3.2组织实施纠正措施。
5.4验证纠正措施
5. 4.1验证人填写验证效果等情况,得出结论并签字确认。
6. 4.2验证不通过的重新发出《纠正措施报告》
5.5内审不合格项的纠正和纠正措施
内审发现的不合格项的编制和责任部门纠正、内审小组的验证等要求见《内部审核管理程序》。
6记录
5.1《纠正措施报告》
5.2《不合格项报告》。
WAYOUT-QP-18测量设备控制程序

WAYOUT-QP-18测量设备控制程序为使检验测量、监控设备能达到所需的测量能力要求,以确保产品符合规定的要求。
2适用范畴公司内的检验测量、监控设备治理。
3职责和权限3.1质量治理部: 负责检验测量、监控设备治理、验证、修理申请、内外部校验和调整、日常点检及爱护保养。
4有关术语4.1计量检验测量、监控设备:进行测试所需的计量检测仪器,计量标准,标准物质,辅助装置及规程,包括试验、检验及标准所用的计量设备。
4.2校正:在规定条件下,为确定计量检测仪器、系统的示值或实物量具及标准物质所代表的量值与相对应的由参考标准所获得的量值之间关系的一组操作。
4.3调整:为使测量仪器达到性能正常,排除偏差而适用于状态所进行的操作。
5作业程序5.1检验、测量、监控设备采购5.1.1使用部门按照产品、过程监视和测量的需要填写采购审请单交商务进行采购,采购应确保所购设备的准确度和周密度符合要求。
需要有仪器外表的校准证书。
5.2 检验、测量、监控设备的治理所有检验测量、监控设备列入内部校验或外部校验,新购入量规仪器由计量人员对其检验状态是否符合要求进行判定。
关于不符合要求量规仪器交由采购部门办理退货,关于符合要求的量规仪器由计量人员贴上“校正合格”标签。
填写《校验记录表》并记入《量规仪器一览表》送质量治理部经理确认。
5.3计量设备的校验方法5.3.1计量设备的内部校验量规仪器检定人员资格应由国家认定计量机构培训合格人员。
量规仪器检定人员按照量规仪器有效期进行校验。
量规仪器检定环境应满足《计量检定规程》所规定。
检定人员完成校正后,关于符合要求的量规仪器由计量人员贴上“校正合格”标签。
填写《校验记录表》并记入《量规仪器一览表》、送质量治理部经理确认。
关于校验不符合要求,先贴上不合格标签进行标识,再通知仪器使用部门对此仪器将临时停用,并要求对此仪器所检验的产品再进行确认。
检定人员按照仪器不合格缘故进行差不多修理、调整,若无法修理、调整则进行外部修理。
模具检验过程控制程序

模具检验过程控制程序文件编号:WG-QP-18版本号:B/0编制:审核:批准:1.目的:为确保产品能满足客户要求,在产品实现过程中运用适当的检验对模具制作过程进行品质控制,确保模具质量符合客户要求。
2.适用范围:此程序适用于本部门进料、制模过程及模具验收过程所进行的一系列检验。
3.权责:3.1工模仓库:负责收发和存放物料。
3.2模具QC:负责对整个制模过程及模具试模前及入库时的检验。
3.3跟模工程师:对模具运行状况(试模中)进行检查及对样品进行检测。
3.4相关部门:负责检验后的处理。
4.定义:检验:对产品实现前的物料及实现后的产品进行一系列检查、测量及试验的技术控制。
5.程序内容:5.1物料检验5.1.1工模仓库接收供应商物料后,物料放置于待检区,确认数量后通知模具QC检验。
5.1.2模具QC根据采购订单的要求及《模具进料检验规范》对物料进行外观、规格、尺寸等检测。
原则上工模物料执行全检,对于顶针、螺丝等采购数量较大的物料可按2%-5%比例抽样检查。
5.1.3检验完毕后模具QC将检验结果记录于《来料检验记录》,当供应商所送物料有品质异常时,模具QC首先对不合格物料进行标识、隔离并在《来料检验记录》中记录不合格项目,经相关人员评审处理后交采购文员联系供应商需找解决和控制措施。
5.1.4仓库发现产品有异常或超过库存期限时,需要重新使用时,则通知模具QC进行重检。
5.2制模过程检验5.2.1在模具制作过程中,模具QC应根据《模具制作过程检验规范》对制程进行检验控制。
模具制作过程检验又分为对加工件的检验和巡回检验。
5.2.2制模过程中,各加工组加工完毕的工件置于各相应待检区,由模具QC进行检验,并将结果记录于《加工工件检验记录表》上,对于检测尺寸需要进行详细记录的则填写到《模具加工工件检测报告》中。
5.2.3加工工件经检验合格,进行标识并放置于合格区,可以进入下道工序;检验不合格的工件,则由QC进行标识、隔离,并立即出具《模具制作过程检验不合格处理表》,经相关人员评审处理,经评审判定为返工的,由责任人进行返工,若确认不能使用需报废的,则填写《报废单》,由部门主管确认并评估成本,成本在2000元以下,可以由部门主管批准报废;成本在2000元以上(含2000元),则经厂长/总经理审批后方可报废处理。
QP-18数据分析控制程序
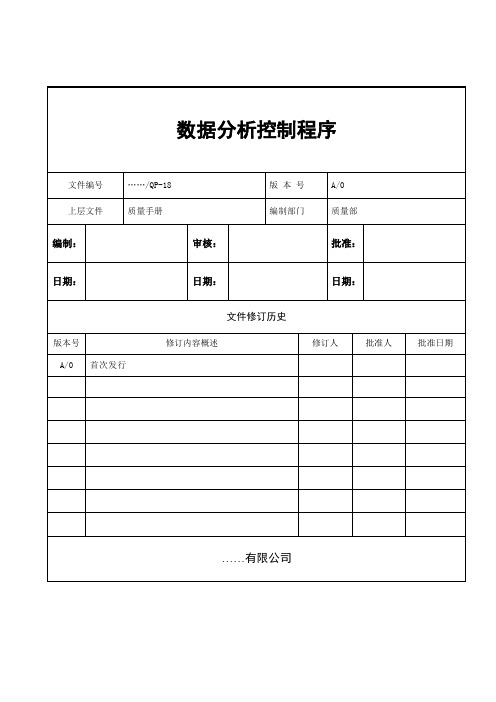
数据分析控制程序1 目的采用适当的统计技术,对数据进行分析,以积极寻找质量管理体系持续改进的有效性。
2 适用范围适用于厂内、外与质量有关的数据的分析。
3 术语和定义无4 职责与权限4.1 质量部:负责统筹公司对内、对外相关数据的传递与分析、处理。
4.2 各相关部门:负责各自相关的数据收集、传递、交流。
5 内容及流程5.1 数据是指能够客观地反映事实的资料和数字等信息。
5.2 数据的来源5.2.1 外部来源a)政策、法规、标准等;b)行业机构检查的结果及反馈;c)市场、新产品、新技术发展方向;d)相关方(如顾客、供方等)反馈及投诉等。
5.2.2 内部来源a)日常工作,如质量目标完成情况、检验试验记录、内部质量审核与管理评审报告及体系正常运行的其他记录;b)存在、潜在的不合格,如质量问题统计结果、纠正预防措施处理结果等;c)紧急信息,如突发事故等;5.2.3 数据可采用已有的记录、书面资料、讨论交流、等方式。
5.3 数据的收集、分析与处理5.3.1 对数据的收集、分析与处理应提供如下信息:a)反馈;b)与产品要求的符合性;c)过程和产品的特性及趋势,包括采取预防措施的机会;d)供方的信息等。
5.3.2 外部数据的收集、分析与处理5.3.2.1 管理者代表负责食品药品监督管理局的监督检查结果及反馈数据、收集分析,并负责传递到相关部门。
对出现的不合格项,执行《纠正和预防措施控制程序》。
5.3.2.2 政策法规信息由行政部及相关部门收集、分析、整理、传递。
5.3.2.3 市场及其他相关部门积极与顾客进行信息沟通,以满足顾客需求,妥善处理顾客的投诉,执行《反馈控制程序》的有关规定。
5.3.2.4 各部门直接从外部获取的其他数据,应在一周内报告质量部,由其分析整理,根据需要传递、协调处理。
5.3.3 内部数据的收集、分析与处理5.3.3.1 质量方针、质量目标的系统管理,执行《质量方针和目标管理规定》。
5.3.3.2 质量部和行政人事组依照相应规定传递质量方针、质量目标、管理方案、内审结果、更新的法律法规等信息。
QP18产品标识和可追溯性控制程序(品质)

1、目的为了保证在产品实现过程中各个阶段,品质状态均能获得明确的标识,并实现产品的可追溯性,防止在生产过程混淆和误用。
2、范围本程序适用于原材料、半成品和最终产品的标识和追溯。
3、定义3.1产品标识指以文字形式挂牌、贴标签的方式来标识产品,如“状态标识牌”“首检标签”等。
3.2检验状态标识以不同颜色的标签(“合格品”、“不合格品”等)、盖章(“QA PASS”、“返工”)或标识(红色标签)的方式对产品的检验状态进行标识。
3.3状态标识牌用来标识和记录产品的状态的文字形式的挂牌,通常放置于该产品的盛装容器或包装上。
3.4物料标签用来标识公司产品所使用物料的标签,包括品名、数量、供应商等基本信息。
4、职责4.1仓管员:负责对物料、产品进行有效标识。
4.2品质部:负责原材料、半成品及成品的检验状态的标识,各过程标识的监督管理。
产品有追溯性需求时,组织进行产品的追溯。
4.3生产部:负责产品在生产过程中的状态标识和相关的产品标识。
4.4各部门:负责配合进行相关的标识和追溯工作。
5、产品标识与追溯流程图.1产品标识流程图职责流程图备注IQC 检验员IQC 检验员仓管员生产组长/车间主任,IQC 组长,生产工程师IPQC 检验员生产部作业员OQC 检验员仓库收到供应商来料后,先将来料放置在送检区。
由仓管员开“来料送检单”给IQC ,IQC 检验员对来料进行检验,并在单位包装上贴上与检验结果相对应的检验状态标签。
合格证(绿)首件检验合格方可投入批量生产合格(绿)只有经OQC 检验合格的产品仓库人员才可办理入库手续。
☞OQC PASS☞OQC REJECT6.程序内容6.1进料及检验状态标识6.1.1来料时仓管员应要求供应商将物料放置待检区,标识应齐全,核对型号、数量及生产日期,无误后,挂上“待检”标识牌,若为客供品则在外箱上贴“客户供应品”标签,连同“进货送检单”一起送IQC检验。
6.1.2经检验后,检验员应在单位包装上贴上与检验结果相对应状态标签,填写“进料检验报告”。
QP-18样品管理程序

1、目的管理样品的制作、使用、保管及更改,加强过程控制。
2、范围适用于公司内生产、检验用及提交PPAP的所有产品样品的控制; 包括公司自制样品及客户提供的样品。
3、职责1.1生产部根据生产、品质等需求部门提出的样品需要配发样品材料;1.2生产部负责制作样品并保管经确认批准后的样品及正确使用;1.3工程部负责对做出的样品进行确认;1.4品管部负责样品检验与确认,保管经确认批准的样品及正确使用。
4、工作程序4.1 公司内自制样品的控制 :4.1.1 公司内制作的产品样品根据保存时间和使用性质分为两类: 永久性样品和临时性样品 .4.1.2永久性样品分为三种:标准样品、限度样品、识别用样品。
4.2.3限度样品用于比对各零件之最大限度要求。
如物料之颜色、外观、毛刺等的判定参考.4.1.4标准样品有良品与不良品用于必要情况下,如尺寸检验不易或辅助检验、校验测试机时用以比对使用。
4.1.5识别用样品用于各成品、半成品、组立装配时识别装配位置、方向、角度之用。
4.1.2 永久性样品的制作:4.1.2.1 品管部根据实际控制需要,向生产部提出样品制做的材料申请;除非因材料短缺、产品较为贵重不适宜保留、客户不同意保留样品等特殊情况外, 原则上每种产品都应尽可能的制作至少一个标准样品以作为生产和检查参考使用及作为公司所有生产过程产品的历史追溯。
4.1.2.2 必要时生产部人员负责把样品材料需求安排入生产计划中。
4.1.2.3 生产部根据品质计划制作样品,样品完成后交给品管部。
4.1.3 永久性样品的确认:4.1.3.1 品管部在收到样品后由检查员根据品质计划和参照相关资料确认,合格后填写样品卡并用绳子挂于产品上,再由品检负责人确认, 管理代表批准,登录于“样品管理总表”。
4.1.3.2 在以上确认完成后,此产品可以作为正式样品在检验、生产、测试等控制时参考使用。
4.1.4永久性样品的保管 :4.1.4.1品管部应妥善保管好样品,填写样品一览表予以记录,并提供适当贮存环境和控制手段保管样品以防止丢失、损坏、误用。
MH-QP-18监视和测量设备控制程序

SDDS电子有限公司阶文件监视和测量设备控制程序文件编号:MH-QP-18版次:A/0 _______________页数: 共8页制订部I' 1: 品管课制订人:SASASA制订日期:2019.05.04核准/日期常核/日期文件发行章2019 2019监视和测量设备申购、采购、验收与登录管制5.3监视与测量设备的校验5.3.1使用中的仪器设备依据规定的周期(外校仪器设备校正周期为一年一次,内校仪器设备校正周期为半年一次)进行校准或验证,校验的基准可追溯到国际或国家基准,如不存在上述基准时,记录校验或验证的依据。
校验包括内校和外校,在《仪器设备管理活册》中规定内部校验与外部校验,外部校验包括送外部专业校验机构校验,选择专业的外部校验机构校验时,要确认其具备国家认可的校验资格。
5.3.2内部校验:本公司届丁长度计量范围内的所有测量仪器由仪校人员定期进行校验,如:数显卡尺/游标卡尺/厚薄规等,并记录丁《仪器校验记录表》中。
a)内校人员资格:执行内部监视和测量设备校验的人员必须持有国家认可的对该类仪器有校验资格的仪校员资格证方可。
b)品管课制订监测设备的校验规程,仪校员按照校验规程进行校验。
5.3.3 内校之标准件:用丁内校使用的标准件(标准件也是监视与测量设备,其管理亦然),其有效性应可追溯到国家/行业标准或国际原级标准,其校验追溯体系为:5.3.4外部校验本公司所有长度计量范围之外的测量仪器由仪校人员定期提出外校申请,并安排送具备资格的计量机构对仪器进行外校,如:石去码/二次元/拉力计/扭力计/ 温度计等。
a)品管课仪校员根据计划校验日期安排适当时间(比如提前两周)通知监视和测量设备使用单位准备,以便按时送外校验。
b)监测设备在搬运过程中要做好防护,防止振动,磕碰,倾斜,翻倒,挤压等造成监测设备损坏或失效;9.相关标签图示:Ti9oinixim免校编号:名称:无须校准图四:免校标签图三:限制使用标签。
- 1、下载文档前请自行甄别文档内容的完整性,平台不提供额外的编辑、内容补充、找答案等附加服务。
- 2、"仅部分预览"的文档,不可在线预览部分如存在完整性等问题,可反馈申请退款(可完整预览的文档不适用该条件!)。
- 3、如文档侵犯您的权益,请联系客服反馈,我们会尽快为您处理(人工客服工作时间:9:00-18:30)。
4.1检验依据
检验依据为国家有关家具规范、验收标准及产品标准等,以及相关技术文件和操作规程等。
4.2来料检验
品质部负责进货检验,按进货检验的规定进行进货检验。品质部应记录抽检结果。发现不合格一般要求采购人员负责退货。
4.3首件确认
产品上线品管专员应对首件进行确认检查,一般检查4-5件产品。
4.7.2确认及交付
产品生产完成后,品质部人员先组织全面自检,合格后报请生产部主管组织内部验收。内部验收合格后,通知顾客具体交付日期及其他安排事项,交付后如发现不合格按不合格品处理程序执行。
5.相关文件
《不合格品控制程序》
6.相关记录
《品质检验报告》
《不合格处理单》
拟制:审核:批准:
4.4生产过程自检
作业人员在作业过程中应自检,发现不合格应立即整改,不能马上整改的应起动不合格处理程序。
4.5过程的检验
班组长应在生产线上巡检。发现不符合,应马上调整。
4.6制程目视检验
品管专员对产品全检,发现问题要求生产部返工。
4.7产品终检
4.7.1品管专员依据检验要求对产品进行抽样检查,发现问题交由生产厂长进行处理,如Байду номын сангаас来料问题,还需反馈采购进行处理。
1.目的
本程序规定了对产品及过程的监视和测量的方法及实施程序,以确保每个过程都能持续满足其预期的目的,保证产品质量。
2.范围
适用于产品生产的全过程,从原材料采购到产品交付。
3.职责
3.1品质部负责生产过程的质量监督、产品验收及产品生产质量的内部评定;
3.2作业人员负责产品生产过程的自检;
3.3生产部、品质部负责产品生产质量的全面实施控制。