Adding Ribbon Control To Your Application
ADLRAN ATLAS 800PLUS 使用手册说明书
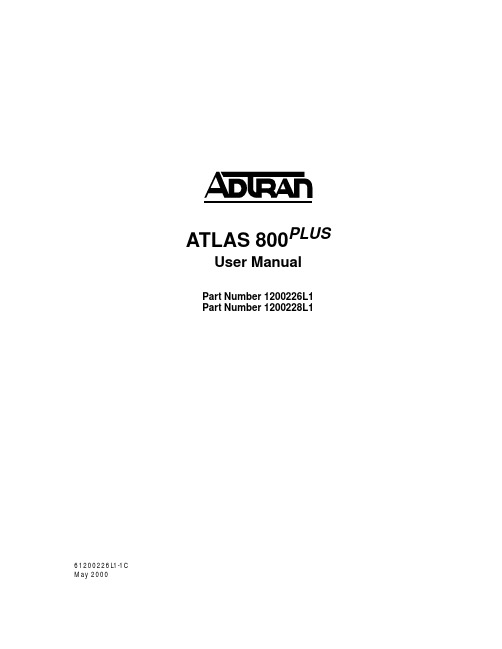
iv
Affidavit Requirements for Connection to Digital Services • An affidavit is required to be given to the telephone company whenever digital terminal equipment
901 Explorer Boulevard P.O. Box 140000
Huntsville, AL 35814-4000 (256) 963-8000
© 2000 ADTRAN, Inc. All Rights Reserved.
Prinns require that in this manual the following information be provided to the customer:
6. This unit contains no user-serviceable parts. 7. The following information may be required when applying to your local telephone company for
leased line facilities.
without encoded analog content and billing protection is used to transmit digital signals containing encoded analog content which are intended for eventual conversion into voiceband analog signals and transmitted on the network. • The affidavit shall affirm that either no encoded analog content or billing information is being transmitted or that the output of the device meets Part 68 encoded analog content or billing protection specifications. • End user/customer will be responsible for filing an affidavit with the local exchange carrier when connecting unprotected customer premise equipment (CPE) to 1.544 Mbps or subrate digital services. • Until such time as subrate digital terminal equipment is registered for voice applications, the affidavit requirement for subrate services is waived.
Windows Vista Parental Controls 用户指南说明书
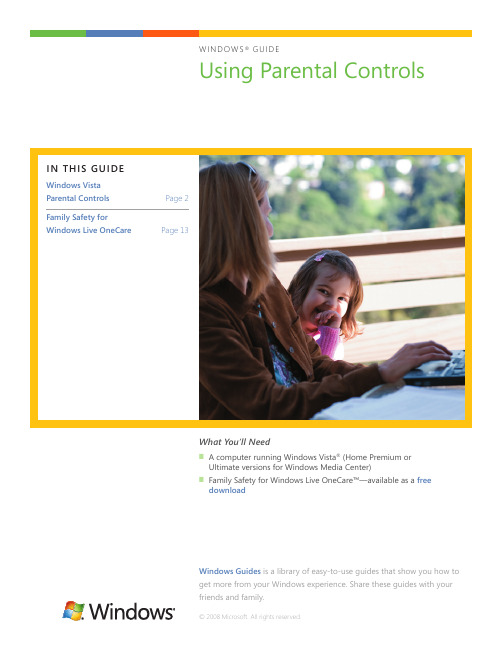
Learn more about how you can use Windows to simplify your life with Windows Guides
2
W I N D O W S G U I D E Using Parental Controls
Windows Vista Parental Controls (continued)
Ultimate versions for Windows Media Center) n Family Safety for Windows Live OneCare™—available as a free
download
Windows Guides is a library of easy-to-use guides that show you how to get more from your Windows experience. Share these guides with your friends and family.
n Set up Web restrictions
n Set program limits
n Set up which games your children can play
n Set time limits for computer use
Parental Controls, part of the User Accounts and Family Safety Control Panel, centralizes all of the key settings of the Windows Vista Parental Controls. From this one location, you can configure the parental controls for your computer and applications, setting appropriate limits on your children’s game playing, Web browsing, and overall computer use. You can review activity reports that show how your children have been using the computer. Monitoring your children’s computer behavior not only makes it easy for you to keep track of what they are seeing, hearing, and doing, but it also enables you to refine and modify parental controls based on actual feedback. For your children, the Parental Controls icon in the system tray is always visible to let them know that the Parental Controls feature is on.
HP Color LaserJet Enterprise MFP M776用户指南说明书
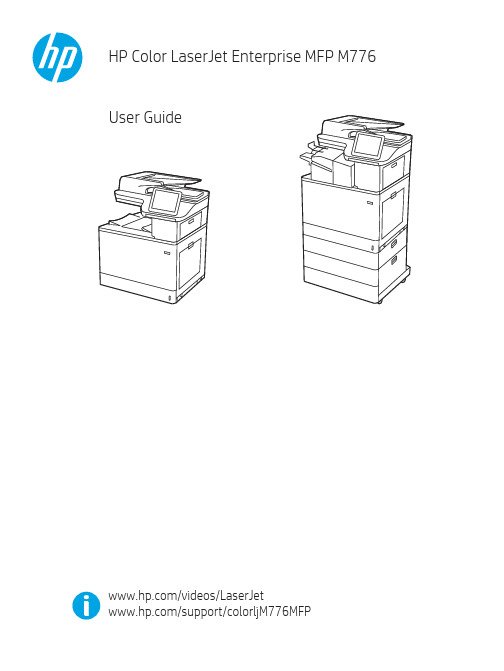
Legal informationCopyright and License© Copyright 2019 HP Development Company, L.P.Reproduction, adaptation, or translation without prior written permission is prohibited, except as allowedunder the copyright laws.The information contained herein is subject to change without notice.The only warranties for HP products and services are set forth in the express warranty statementsaccompanying such products and services. Nothing herein should be construed as constituting anadditional warranty. HP shall not be liable for technical or editorial errors or omissions contained herein.Edition 1, 10/2019Trademark CreditsAdobe®, Adobe Photoshop®, Acrobat®, and PostScript® are trademarks of Adobe Systems Incorporated.Apple and the Apple logo are trademarks of Apple Inc., registered in the U.S. and other countries.macOS is a trademark of Apple Inc., registered in the U.S. and other countries.AirPrint is a trademark of Apple Inc., registered in the U.S. and other countries.Google™ is a trademark of Google Inc.Microsoft®, Windows®, Windows® XP, and Windows Vista® are U.S. registered trademarks of MicrosoftCorporation.UNIX® is a registered trademark of The Open Group.iiiT able of contents1 Printer overview (1)Warning icons (1)Potential shock hazard (2)Printer views (2)Printer front view (2)Printer back view (4)Interface ports (4)Control-panel view (5)How to use the touchscreen control panel (7)Printer specifications (8)T echnical specifications (8)Supported operating systems (11)Mobile printing solutions (12)Printer dimensions (13)Power consumption, electrical specifications, and acoustic emissions (15)Operating-environment range (15)Printer hardware setup and software installation (16)2 Paper trays (17)Introduction (17)Load paper to Tray 1 (multipurpose tray) (17)Load Tray 1 (multipurpose tray) (18)Tray 1 paper orientation (19)Use alternative letterhead mode (24)Enable Alternative Letterhead Mode by using the printer control-panel menus (24)Load paper to Tray 2 (24)Load Tray 2 (24)Tray 2 paper orientation (26)Use alternative letterhead mode (29)Enable Alternative Letterhead Mode by using the printer control-panel menus (29)Load paper to the 550-sheet paper tray (30)Load paper to the 550-sheet paper tray (30)550-sheet paper tray paper orientation (32)Use alternative letterhead mode (35)Enable Alternative Letterhead Mode by using the printer control-panel menus (35)ivLoad paper to the 2 x 550-sheet paper trays (36)Load paper to the 2 x 550-sheet paper trays (36)2 x 550-sheet paper tray paper orientation (38)Use alternative letterhead mode (41)Enable Alternative Letterhead Mode by using the printer control-panel menus (41)Load paper to the 2,700-sheet high-capacity input paper trays (41)Load paper to the 2,700-sheet high-capacity input paper trays (41)2,700-sheet HCI paper tray paper orientation (43)Use alternative letterhead mode (45)Enable Alternative Letterhead Mode by using the printer control-panel menus (45)Load and print envelopes (46)Print envelopes (46)Envelope orientation (46)Load and print labels (47)Manually feed labels (47)Label orientation (48)3 Supplies, accessories, and parts (49)Order supplies, accessories, and parts (49)Ordering (49)Supplies and accessories (50)Maintenance/long-life consumables (51)Customer self-repair parts (51)Dynamic security (52)Configure the HP toner-cartridge-protection supply settings (53)Introduction (53)Enable or disable the Cartridge Policy feature (53)Use the printer control panel to enable the Cartridge Policy feature (54)Use the printer control panel to disable the Cartridge Policy feature (54)Use the HP Embedded Web Server (EWS) to enable the Cartridge Policy feature (54)Use the HP Embedded Web Server (EWS) to disable the Cartridge Policy feature (55)Troubleshoot Cartridge Policy control panel error messages (55)Enable or disable the Cartridge Protection feature (55)Use the printer control panel to enable the Cartridge Protection feature (56)Use the printer control panel to disable the Cartridge Protection feature (56)Use the HP Embedded Web Server (EWS) to enable the Cartridge Protection feature (56)Use the HP Embedded Web Server (EWS) to disable the Cartridge Protection feature (57)Troubleshoot Cartridge Protection control panel error messages (57)Replace the toner cartridges (58)T oner-cartridge information (58)Remove and replace the cartridges (59)Replace the imaging drums (62)Imaging drum information (62)Remove and replace the imaging drums (63)Replace the toner-collection unit (66)T oner-collection unit information (66)vRemove and replace the toner-collection unit (67)Replace the staple cartridge (M776zs model only) (70)Staple cartridge information (70)Remove and replace the staple cartridge (71)4 Print (73)Print tasks (Windows) (73)How to print (Windows) (73)Automatically print on both sides (Windows) (74)Manually print on both sides (Windows) (74)Print multiple pages per sheet (Windows) (75)Select the paper type (Windows) (75)Additional print tasks (76)Print tasks (macOS) (77)How to print (macOS) (77)Automatically print on both sides (macOS) (77)Manually print on both sides (macOS) (77)Print multiple pages per sheet (macOS) (78)Select the paper type (macOS) (78)Additional print tasks (79)Store print jobs on the printer to print later or print privately (79)Introduction (79)Create a stored job (Windows) (79)Create a stored job (macOS) (80)Print a stored job (81)Delete a stored job (81)Delete a job that is stored on the printer (81)Change the job storage limit (82)Information sent to printer for Job Accounting purposes (82)Mobile printing (82)Introduction (82)Wi-Fi, Wi-Fi Direct Print, NFC, and BLE printing (82)Enable wireless printing (83)Change the Wi-Fi Direct name (83)HP ePrint via email (83)AirPrint (84)Android embedded printing (85)Print from a USB flash drive (85)Enable the USB port for printing (85)Method one: Enable the USB port from the printer control panel (85)Method two: Enable the USB port from the HP Embedded Web Server (network-connectedprinters only) (85)Print USB documents (86)Print using high-speed USB 2.0 port (wired) (86)Method one: Enable the high-speed USB 2.0 port from the printer control panel menus (86)Method two: Enable the high-speed USB 2.0 port from the HP Embedded Web Server (network-connected printers only) (87)vi5 Copy (88)Make a copy (88)Copy on both sides (duplex) (90)Additional copy tasks (92)6 Scan (93)Set up Scan to Email (93)Introduction (93)Before you begin (93)Step one: Access the HP Embedded Web Server (EWS) (94)Step two: Configure the Network Identification settings (95)Step three: Configure the Send to Email feature (96)Method one: Basic configuration using the Email Setup Wizard (96)Method two: Advanced configuration using the Email Setup (100)Step four: Configure the Quick Sets (optional) (104)Step five: Set up Send to Email to use Office 365 Outlook (optional) (105)Introduction (105)Configure the outgoing email server (SMTP) to send an email from an Office 365 Outlookaccount (105)Set up Scan to Network Folder (108)Introduction (108)Before you begin (108)Step one: Access the HP Embedded Web Server (EWS) (108)Step two: Set up Scan to Network Folder (109)Method one: Use the Scan to Network Folder Wizard (109)Method two: Use Scan to Network Folder Setup (110)Step one: Begin the configuration (110)Step two: Configure the Scan to Network Folder settings (111)Step three: Complete the configuration (118)Set up Scan to SharePoint (118)Introduction (118)Before you begin (118)Step one: Access the HP Embedded Web Server (EWS) (118)Step two: Enable Scan to SharePoint and create a Scan to SharePoint Quick Set (119)Scan a file directly to a SharePoint site (121)Quick Set scan settings and options for Scan to SharePoint (122)Set up Scan to USB Drive (123)Introduction (124)Step one: Access the HP Embedded Web Server (EWS) (124)Step two: Enable Scan to USB Drive (124)Step three: Configure the Quick Sets (optional) (125)Default scan settings for Scan to USB Drive setup (126)Default file settings for Save to USB setup (126)Scan to email (127)Introduction (127)Scan to email (127)Scan to job storage (129)viiIntroduction (129)Scan to job storage on the printer (130)Print from job storage on the printer (132)Scan to network folder (132)Introduction (132)Scan to network folder (132)Scan to SharePoint (134)Introduction (134)Scan to SharePoint (134)Scan to USB drive (136)Introduction (136)Scan to USB drive (136)Use HP JetAdvantage business solutions (138)Additional scan tasks (138)7 Fax (140)Set up fax (140)Introduction (140)Set up fax by using the printer control panel (140)Change fax configurations (141)Fax dialing settings (141)General fax send settings (142)Fax receive settings (143)Send a fax (144)Additional fax tasks (146)8 Manage the printer (147)Advanced configuration with the HP Embedded Web Server (EWS) (147)Introduction (147)How to access the HP Embedded Web Server (EWS) (148)HP Embedded Web Server features (149)Information tab (149)General tab (149)Copy/Print tab (150)Scan/Digital Send tab (151)Fax tab (152)Supplies tab (153)Troubleshooting tab (153)Security tab (153)HP Web Services tab (154)Networking tab (154)Other Links list (156)Configure IP network settings (157)Printer sharing disclaimer (157)View or change network settings (157)Rename the printer on a network (157)viiiManually configure IPv4 TCP/IP parameters from the control panel (158)Manually configure IPv6 TCP/IP parameters from the control panel (158)Link speed and duplex settings (159)Printer security features (160)Introduction (160)Security statements (160)Assign an administrator password (160)Use the HP Embedded Web Server (EWS) to set the password (160)Provide user access credentials at the printer control panel (161)IP Security (161)Encryption support: HP High Performance Secure Hard Disks (161)Lock the formatter (161)Energy-conservation settings (161)Set the sleep timer and configure the printer to use 1 watt or less of power (161)Set the sleep schedule (162)Set the idle settings (162)HP Web Jetadmin (163)Software and firmware updates (163)9 Solve problems (164)Customer support (164)Control panel help system (165)Reset factory settings (165)Introduction (165)Method one: Reset factory settings from the printer control panel (165)Method two: Reset factory settings from the HP Embedded Web Server (network-connectedprinters only) (166)A “Cartridge is low” or “Cartridge is very low” message displays on the printer control panel (166)Change the “Very Low” settings (166)Change the “Very Low” settings at the control panel (166)For printers with fax capability (167)Order supplies (167)Printer does not pick up paper or misfeeds (167)Introduction (167)The printer does not pick up paper (167)The printer picks up multiple sheets of paper (171)The document feeder jams, skews, or picks up multiple sheets of paper (174)Clear paper jams (174)Introduction (174)Paper jam locations (174)Auto-navigation for clearing paper jams (175)Experiencing frequent or recurring paper jams? (175)Clear paper jams in the document feeder - 31.13.yz (176)Clear paper jams in Tray 1 (13.A1) (177)Clear paper jams in Tray 2 (13.A2) (182)Clear paper jams in the fuser (13.B9, 13.B2, 13.FF) (188)ixClear paper jams in the duplex area (13.D3) (194)Clear paper jams in the 550-sheet trays (13.A3, 13.A4) (199)Clear paper jams in the 2 x 550 paper trays (13.A4, 13.A5) (206)Clear paper jams in the 2,700-sheet high-capacity input paper trays (13.A3, 13.A4, 13.A5, 13.A7) (213)Resolving color print quality problems (220)Introduction (220)Troubleshoot print quality (221)Update the printer firmware (221)Print from a different software program (221)Check the paper-type setting for the print job (221)Check the paper type setting on the printer (221)Check the paper type setting (Windows) (221)Check the paper type setting (macOS) (222)Check toner-cartridge status (222)Step one: Print the Supplies Status Page (222)Step two: Check supplies status (222)Print a cleaning page (222)Visually inspect the toner cartridge or cartridges (223)Check paper and the printing environment (223)Step one: Use paper that meets HP specifications (223)Step two: Check the environment (223)Step three: Set the individual tray alignment (224)Try a different print driver (224)Troubleshoot color quality (225)Calibrate the printer to align the colors (225)Troubleshoot image defects (225)Improve copy image quality (233)Check the scanner glass for dirt and smudges (233)Calibrate the scanner (234)Check the paper settings (235)Check the paper selection options (235)Check the image-adjustment settings (235)Optimize copy quality for text or pictures (236)Edge-to-edge copying (236)Improve scan image quality (236)Check the scanner glass for dirt and smudges (237)Check the resolution settings (238)Check the color settings (238)Check the image-adjustment settings (239)Optimize scan quality for text or pictures (239)Check the output-quality settings (240)Improve fax image quality (240)Check the scanner glass for dirt and smudges (240)Check the send-fax resolution settings (242)Check the image-adjustment settings (242)Optimize fax quality for text or pictures (242)Check the error-correction setting (243)xSend to a different fax machine (243)Check the sender's fax machine (243)Solve wired network problems (244)Introduction (244)Poor physical connection (244)The computer is unable to communicate with the printer (244)The printer is using incorrect link and duplex settings for the network (245)New software programs might be causing compatibility problems (245)The computer or workstation might be set up incorrectly (245)The printer is disabled, or other network settings are incorrect (245)Solve wireless network problems (245)Introduction (245)Wireless connectivity checklist (245)The printer does not print after the wireless configuration completes (246)The printer does not print, and the computer has a third-party firewall installed (246)The wireless connection does not work after moving the wireless router or printer (247)Cannot connect more computers to the wireless printer (247)The wireless printer loses communication when connected to a VPN (247)The network does not appear in the wireless networks list (247)The wireless network is not functioning (247)Reduce interference on a wireless network (248)Solve fax problems (248)Checklist for solving fax problems (248)What type of phone line are you using? (249)Are you using a surge-protection device? (249)Are you using a phone company voice-messaging service or an answering machine? (249)Does your phone line have a call-waiting feature? (249)Check fax accessory status (249)General fax problems (250)The fax failed to send (250)No fax address book button displays (250)Not able to locate the Fax settings in HP Web Jetadmin (250)The header is appended to the top of the page when the overlay option is enabled (251)A mix of names and numbers is in the recipients box (251)A one-page fax prints as two pages (251)A document stops in the document feeder in the middle of faxing (251)The volume for sounds coming from the fax accessory is too high or too low (251)Index (252)xiPrinter overview1Review the location of features on the printer, the physical and technical specifications of the printer,and where to locate setup information.For video assistance, see /videos/LaserJet.The following information is correct at the time of publication. For current information, see /support/colorljM776MFP.For more information:HP's all-inclusive help for the printer includes the following information:●Install and configure●Learn and use●Solve problems●Download software and firmware updates●Join support forums●Find warranty and regulatory informationWarning iconsUse caution if you see a warning icon on your HP printer, as indicated in the icon definitions.●Caution: Electric shock●Caution: Hot surface●Caution: Keep body parts away from moving partsPrinter overview1●Caution: Sharp edge in close proximity●WarningPotential shock hazardReview this important safety information.●Read and understand these safety statements to avoid an electrical shock hazard.●Always follow basic safety precautions when using this product to reduce risk of injury from fire orelectric shock.●Read and understand all instructions in the user guide.●Observe all warnings and instructions marked on the product.●Use only a grounded electrical outlet when connecting the product to a power source. If you do notknow whether the outlet is grounded, check with a qualified electrician.●Do not touch the contacts on any of the sockets on the product. Replace damaged cordsimmediately.●Unplug this product from wall outlets before cleaning.●Do not install or use this product near water or when you are wet.●Install the product securely on a stable surface.●Install the product in a protected location where no one can step on or trip over the power cord.Printer viewsIdentify certain parts of the printer and the control panel.Printer front viewLocate features on the front of the printer.2Chapter 1 Printer overviewPrinter front view3Printer back viewLocate features on the back of the printer.Interface portsLocate the interface ports on the printer formatter. 4Chapter 1 Printer overviewControl-panel viewThe control panel provides access to the printer features and indicates the current status of the printer.NOTE:Tilt the control panel for easier viewing.The Home screen provides access to the printer features and indicates the current status of the printer.screens.NOTE:The features that appear on the Home screen can vary, depending on the printerconfiguration.Control-panel view5Figure 1-1Control-panel view?i 12:42 PM6Chapter 1 Printer overviewHow to use the touchscreen control panelPerform the following actions to use the printer touchscreen control panel.T ouchT ouch an item on the screen to select that item or open that menu. Also, when scrolling T ouch the Settings icon to open the Settings app.How to use the touchscreen control panel 7SwipeT ouch the screen and then move your finger horizontally to scroll the screen sideways.Swipe until the Settings app displays.Printer specificationsDetermine the specifications for your printer model.IMPORTANT:The following specifications are correct at the time of publication, but they are subject to change. For current information, see /support/colorljM776MFP .T echnical specificationsReview the printer technical specifications.Product numbers for each model ●M776dn - #T3U55A ●Flow M776z - #3WT91A ●Flow M776zs - #T3U56APaper handling specificationsPaper handling features Tray 1 (100-sheet capacity)Included Included Included Tray 2 (550-sheet capacity)IncludedIncludedIncluded8Chapter 1 Printer overview550-sheet paper trayOptional Included Not included NOTE:The M776dn models accept one optional550-sheet tray.Optional Included Included2 x 550-sheet paper tray and standNOTE:The M776dn models accept one optional550-sheet tray that may be installed on top of thestand.Optional Not included Not included2,700-sheet high-capacity input (HCI) paper trayand standNOTE:The M776dn models accept one optional550-sheet tray that may be installed on top of theoptional printer stand.Printer standOptional Not included Not included NOTE:The M776dn models accept one optional550-sheet tray that may be installed on top of theoptional printer stand.Inner finisher accessory Not included Not included Included Automatic duplex printing Included IncludedIncludedIncluded Included Included10/100/1000 Ethernet LAN connection with IPv4and IPv6Hi-Speed USB 2.0Included Included IncludedIncluded Included IncludedEasy-access USB port for printing from a USBflash drive or upgrading the firmwareIncluded Included Included Hardware Integration Pocket for connectingaccessory and third-party devicesHP Internal USB Ports Optional Optional OptionalOptional Optional OptionalHP Jetdirect 2900nw Print Server accessory forWi-Fi connectivity and an additional Ethernet portOptional IncludedIncludedHP Jetdirect 3100w accessory for Wi-Fi, BLE, NFC,and proximity badge readingPrints 45 pages per minute (ppm) on Letter-sizepaper and 46 ppm on A4-size paperEasy-access USB printing for printing from a USBIncluded Included Includedflash driveT echnical specifications9Included Included Included Store jobs in the printer memory to print later orprint privatelyScans 100 pages per minute (ppm) on A4 andIncluded Included Included letter-size paper one-sidedIncluded Included Included 200-page document feeder with dual-headscanning for single-pass duplex copying andscanningNot included Included Included HP EveryPage T echnologies including ultrasonicmulti-feed detectionNot included Included Included Embedded optical character recognition (OCR)provides the ability to convert printed pages intotext that can be edited or searched using acomputerIncluded Included Included SMART Label feature provides paper-edgedetection for automatic page croppingIncluded Included Included Automatic page orientation for pages that haveat least 100 characters of textIncluded Automatic tone adjustment sets contrast,Included Includedbrightness, and background removal for eachpageIncluded Included Includedfolders on a networkIncludedSend documents to SharePoint®Included IncludedIncluded Included Included NOTE:Memory reported on the configurationpage will change from 2.5 GB to 3 GB with theoptional 1 GB SODIMM installed.Mass storage: 500 GB hard disk drive Included Included IncludedSecurity: HP Trusted Platform Module (TPM)Included Included IncludedT ouchscreen control panel Included Included IncludedRetractable keyboard Not included Included Included 10Chapter 1 Printer overviewFax Optional Included IncludedSupported operating systemsUse the following information to ensure printer compatibility with your computer operating system.Linux: For information and print drivers for Linux, go to /go/linuxprinting.UNIX: For information and print drivers for UNIX®, go to /go/unixmodelscripts.The following information applies to the printer-specific Windows HP PCL 6 print drivers, HP print driversfor macOS, and to the software installer.Windows: Download HP Easy Start from /LaserJet to install the HP print driver. Or, go tothe printer-support website for this printer: /support/colorljM776MFP to download the printdriver or the software installer to install the HP print driver.macOS: Mac computers are supported with this printer. Download HP Easy Start either from /LaserJet or from the Printer Support page, and then use HP Easy Start to install the HP print driver.1.Go to /LaserJet.2.Follow the steps provided to download the printer software.Windows 7, 32-bit and 64-bit The “HP PCL 6” printer-specific print driver is installed for this operating system aspart of the software installation.Windows 8.1, 32-bit and 64-bit The “HP PCL-6” V4 printer-specific print driver is installed for this operating systemas part of the software installation.Windows 10, 32-bit and 64-bit The “HP PCL-6” V4 printer-specific print driver is installed for this operating systemas part of the software installation.Windows Server 2008 R2, SP 1, 64-bit The PCL 6 printer-specific print driver is available for download from the printer-support website. Download the driver, and then use the Microsoft Add Printer tool toinstall it.Windows Server 2012, 64-bit The PCL 6 printer-specific print driver is available for download from the printer-support website. Download the driver, and then use the Microsoft Add Printer tool toinstall it.Windows Server 2012 R2, 64-bit The PCL 6 printer-specific print driver is available for download from the printer-support website. Download the driver, and then use the Microsoft Add Printer tool toinstall it.Windows Server 2016, 64-bit The PCL 6 printer-specific print driver is available for download from the printer-support website. Download the driver, and then use the Microsoft Add Printer tool toinstall it.Windows Server 2019, 64-bit The PCL 6 printer-specific print driver is available for download from the printer-support website. Download the driver, and then use the Microsoft Add Printer tool toinstall it.Supported operating systems11macOS 10.13 High Sierra, macOS 10.14 MojaveDownload HP Easy Start from /LaserJet , and then use it to install the print driver.NOTE:Supported operating systems can change.NOTE:For a current list of supported operating systems and HP’s all-inclusive help for the printer, go to /support/colorljM776MFP .NOTE:For details on client and server operating systems and for HP UPD driver support for this printer, go to /go/upd . Under Additional information , click Specifications .●Internet connection●Dedicated USB 1.1 or 2.0 connection or a network connection● 2 GB of available hard-disk space ●1 GB RAM (32-bit) or2 GB RAM (64-bit)●Internet connection●Dedicated USB 1.1 or 2.0 connection or a network connection●1.5 GB of available hard-disk spaceNOTE:The Windows software installer installs the HP Smart Device Agent Base service. The file size is less than 100 kb. Its only function is to check for printers connected via USB hourly. No data is collected. If a USB printer is found, it then tries to locate a JetAdvantage Management Connector (JAMc) instance on the network. If a JAMc is found, the HP Smart Device Agent Base is securelyupgraded to a full Smart Device Agent from JAMc, which will then allow printed pages to be accounted for in a Managed Print Services (MPS) account. The driver-only web packs downloaded from for the printer and installed through the Add Printer wizard do not install this service.T o uninstall the service, open the Control Panel , select Programs or Programs and Features , and then select Add/Remove Programs or Uninstall a Programto remove the service. The file name isHPSmartDeviceAgentBase.Mobile printing solutionsHP offers multiple mobile printing solutions to enable easy printing to an HP printer from a laptop, tablet, smartphone, or other mobile device.T o see the full list and to determine the best choice, go to /go/MobilePrinting .NOTE:Update the printer firmware to ensure all mobile printing capabilities are supported.●Wi-Fi Direct (wireless models only, with HP Jetdirect 3100w BLE/NFC/Wireless accessory installed)●HP ePrint via email (Requires HP Web Services to be enabled and the printer to be registered with HP Connected)●HP Smart app ●Google Cloud Print12Chapter 1 Printer overview。
IBM SPSS Statistics Version 28 授权用户许可管理员指南说明书

To push to the local desktops running Windows
Because IBM SPSS Statistics installations are compatible with Microsoft Windows Installer (MSI), you can push an installation to the end-user desktop computers.
惠普彩色激光打印机 Pro M454 和惠普彩色激光多功能一体机 Pro M479 维修手册说明书
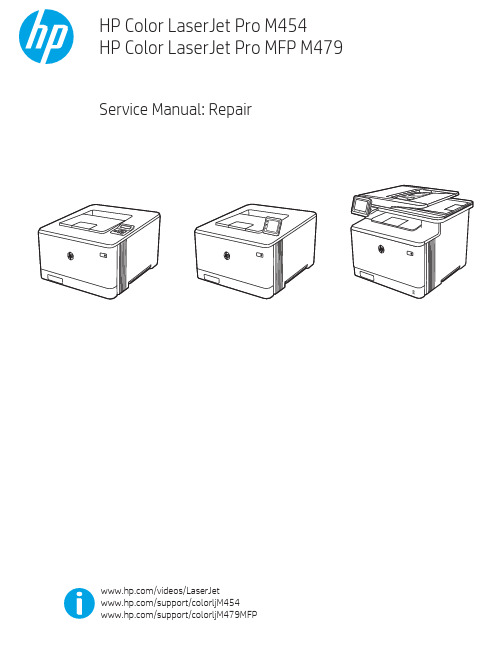
Table -1 Revision history Revision number 1
Revision date 6/2019
Revision notes HP LaserJet Pro M454 HP LaserJet Pro MFP M479 Repair manual initial release
Additional service and support for HP internal personnel HP internal personnel, go to one of the following Web-based Interactive Search Engine (WISE) sites: Americas (AMS) – https:///wise/home/ams-enWISE - English – https:///wise/home/ams-esWISE - Spanish – https:///wise/home/ams-ptWISE - Portuguese – https:///wise/home/ams-frWISE - French Asia Pacific / Japan (APJ) ○ https:///wise/home/apj-enWISE - English ○ https:///wise/home/apj-jaWISE - Japanese ○ https:///wise/home/apj-koWISE - Korean ○ https:///wise/home/apj-zh-HansWISE - Chinese (simplified)
Find information about the following topics ● Service manuals ● Service advisories ● Up-to-date control panel message (CPMD) troubleshooting ● Install and configure ● Printer specifications ● Solutions for printer issues and emerging issues ● Remove and replace part instructions and videos ● Warranty and regulatory information
LTE系统消息翻译
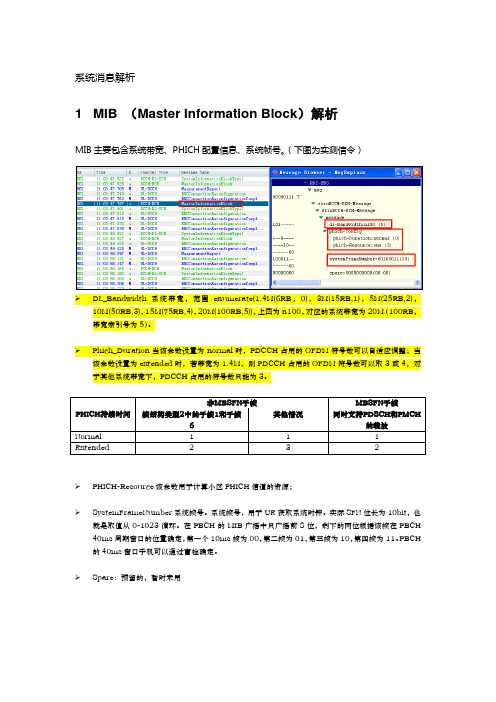
系统消息解析1 MIB (Master Information Block)解析MIB主要包含系统带宽、PHICH配置信息、系统帧号。
(下图为实测信令)➢DL_Bandwidth系统带宽,范围enumerate(1.4M(6RB,0),3M(15RB,1),5M(25RB,2),10M(50RB,3),15M(75RB,4),20M(100RB,5)),上图为n100,对应的系统带宽为20M(100RB,带宽索引号为5)。
➢Phich_Duration当该参数设置为normal时,PDCCH占用的OFDM符号数可以自适应调整;当该参数设置为extended时,若带宽为1.4M,则PDCCH占用的OFDM符号数可以取3或4,对于其他系统带宽下,PDCCH占用的符号数只能为3。
➢PHICH-Resource该参数用于计算小区PHICH信道的资源;➢SystemFrameNumber系统帧号。
系统帧号,用于UE获取系统时钟。
实际SFN位长为10bit,也就是取值从0-1023循环。
在PBCH的MIB广播中只广播前8位,剩下的两位根据该帧在PBCH 40ms周期窗口的位置确定,第一个10ms帧为00,第二帧为01,第三帧为10,第四帧为11。
PBCH 的40ms窗口手机可以通过盲检确定。
➢Spare:预留的,暂时未用2 SIB1 (System Information Block Type1)解析SIB1上主要传输评估UE能否接入小区的相关信息及其他系统消息的调度信息。
主要包括4部分:➢小区接入相关信息(cell Access Related Info)➢小区选择信息(cell Selection Info)➢调度信息(scheduling Info List)➢TDD配置信息(tdd-Config)SIB1消息解析(UE侧):RRC-MSG..msg....struBCCH-DL-SCH-Message......struBCCH-DL-SCH-Message........message..........c1............systemInformationBlockType1..............cellAccessRelatedInfo//小区接入相关信息................plmn-IdentityList//PLMN标识列表..................PLMN-IdentityInfo....................plmn-Identity ......................mcc//460 ........................MCC-MNC-Digit:0x4 (4) ........................MCC-MNC-Digit:0x6 (6) ........................MCC-MNC-Digit:0x0 (0) ......................mnc//00 ........................MCC-MNC-Digit:0x0 (0) ........................MCC-MNC-Digit:0x0 (0) ....................cellReservedForOperatorUse:notReserved (1) ................trackingAreaCode:11100(890C)//TAC跟踪区(890C)为16进制数,转换成十进制为35084,查TAC在该消息中可以查到,此条信元重要。
mds_user_guide
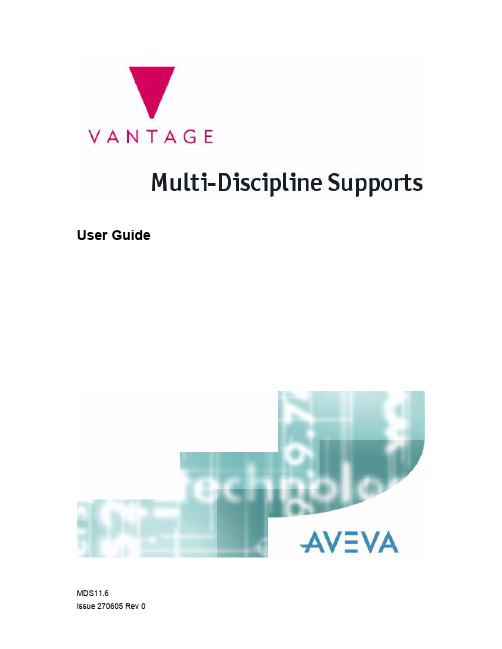
User GuideMDS11.6 Issue 270605 Rev 0NOTE: AVEVA Solutions has a policy of continuing product development: therefore, the information contained in this document may be subject to change without notice. AVEVA SOLUTIONS MAKES NO WARRANTY OF ANY KIND WITH REGARD TO THIS DOCUMENT, INCLUDING BUT NOT LIMITED TO, THE IMPLIED WARRANTIES OF MERCHANTABILITY AND FITNESS FOR A PARTICULAR PURPOSE. While every effort has been made to verify the accuracy of this document, AVEVA Solutions shall not be liable for errors contained herein or direct, indirect, special, incidental or consequential damages in connection with the furnishing, performance or use of this material.This manual provides documentation relating to products to which you may not have access or which may not be licensed to you. For further information on which Products are licensed to you, refer to your license conditions. Copyright 1991 through 2005 AVEVA Solutions LimitedAll rights reserved. No part of this document may be reproduced, stored in a retrieval system or transmitted, in any form or by any means, electronic, mechanical, photocopying, recording or otherwise, without prior written permission of AVEVA Solutions. The software programs described in this document are confidential information and proprietary products of AVEVA Solutions or its licensors.For details of AVEVA's worldwide sales and support offices, see our website at: MDS11.6 User GuideContents1 Introduction ...........................................................................................................11.1 1.2 1.3 1.4 About this User Guide .............................................................................................................. 1 Overview of the MDS application ............................................................................................. 1 Administrator’s role .................................................................................................................. 2 MDS catalogues and specifications ......................................................................................... 22Starting the application ........................................................................................32.1 Creating a multi discipline support ........................................................................................... 6 2.1.1 2.1.2 2.1.3 2.2 2.3 2.4 2.5 2.6 2.7 2.8 2.9 Create by Cursor ..................................................................................................... 14 Create by Clearance................................................................................................ 15 Create by Dimensions ............................................................................................. 16Changing the size of the steelwork ........................................................................................ 17 Adding a packing piece .......................................................................................................... 18 Creating and manipulating connections to external steelwork .............................................. 19 Ending the creation of a support ............................................................................................ 20 Modifying a support................................................................................................................ 21 Deleting a support .................................................................................................................. 25 Copying a support .................................................................................................................. 26 Modifying an ancillary type..................................................................................................... 272.10 Modifying ancillary dimensions .............................................................................................. 27 2.11 Modifying a support name...................................................................................................... 28 2.12 Viewing the application defaults............................................................................................. 29 2.13 Adding a drawing note ........................................................................................................... 30 2.14 Adding a support to the drawlist............................................................................................. 30 2.15 MDS administration options ................................................................................................... 30 2.15.1 Reloading defaults ................................................................................................... 31 2.16 Align a guide to a support ...................................................................................................... 32 2.17 Associate a pad with a shoe .................................................................................................. 32 2.18 Querying the size of an ancillary............................................................................................ 33 2.19 Special supports..................................................................................................................... 34 2.19.1 2.19.2 2.19.3 2.19.4 2.19.5 Creating a special support ....................................................................................... 34 Creating a special support from a combination of standards .................................. 36 Creating a project special support ........................................................................... 38 Creating a special SCTN from the copy section icon .............................................. 40 Including a section into a special support using the Include a Section into SpecialContents-iMDS11.6 User Guideicon .......................................................................................................................... 40 2.19.6 2.19.7 2.19.8 2.19.9 Creating a stiffener box in a special support using the Create a Stiffener Box icon 40 Modifying a stiffener box material or size from the Modify Stiffener Box Material/Size icon .......................................................................................................................... 41 Moving an HVAC project special joint or SCTN with the Move a Project Special Joint/SCTN icon ....................................................................................................... 42 Modifying a special section with the Modify Section icon........................................ 423 4Trunnions.............................................................................................................44 Hangers................................................................................................................484.1 4.2 4.3 4.4 Creating a hanger .................................................................................................................. 48 4.1.1 Using the filter buttons ............................................................................................. 50 Selecting a creation mode...................................................................................................... 52 Ending the creation of a hanger ............................................................................................. 54 Modifying a hanger................................................................................................................. 54 4.4.1 4.4.2 4.4.3 4.5 Rotating all hanger members................................................................................... 55 Rotating a hanger member ...................................................................................... 55 Additional modification options ................................................................................ 56Creating an MDS hanger using a manufacturer’s interface................................................... 605Branch reinforcements .......................................................................................615.1 Creating a branch reinforcement ........................................................................................... 616 7Preliminary supports ..........................................................................................63 Welding application ............................................................................................657.1 7.2 Creating a weld on a framework or special............................................................................ 65 Positioning welds on a framework or special pick ................................................................. 678 9Isometric material list control ............................................................................69 Data access control ............................................................................................709.1 9.2 9.3 Application entry..................................................................................................................... 70 Create mode........................................................................................................................... 70 Additional requirements for MDS with DACS......................................................................... 7110Application data sheets ......................................................................................72Contents-iiMDS11.6 User Guide11 12MDS Wizard .........................................................................................................73 MDS reports.........................................................................................................7412.1 Basic report ............................................................................................................................ 74 12.2 Extended report...................................................................................................................... 75 12.2.1 12.2.2 Extra run-time filter expressions .............................................................................. 75 Customised report headings.................................................................................... 76Contents-iiiMDS11.6 User Guide11.1IntroductionAbout this User GuideThis document provides guidance to the design engineer on how to create supports using the Multi Discipline Supports (MDS) application. It is assumed that the design engineer has a basic understanding of the program.1.2Overview of the MDS applicationThe MDS application allows you to create supports for piping, cable racks, and HVAC. It is highly interactive, enabling you to design supports with the minimum of effort. The MDS application is also highly configurable, allowing the administrator to define project-related defaults, to control the design of supports, and to determine the range and types of ancillary components that can be used on a project. The standard framework supports in the MDS application are designed using structural sections and are template driven. A default set of structural templates based on British Standard steelwork sections is supplied with the MDS application. Any relevant national standard for steelwork sections can be used by configuring the supplied templates. For further information refer to the Framework Template Administration Guide. If the templates supplied do not suit your project or company requirements, get your MDS administrator to configure them, or contact AVEVA Solutions to investigate your requirements and create a special. The requirement to add an extra member to an existing template configuration is an example of a special. The extra member would be designed as, or converted to, a special and then added to the template with the standard Beams and Columns application. Ancillaries are elements, such as u-bolts, bolt-on shoes, anchors, or slip-units, which are attached to pipes. Ancillaries associated with the template are those suitable for, or available with the standard. Ancillaries for cable trays and HVAC, sometimes referred to as fixings, are deemed to be the responsibility of the relevant contractor and are not dealt with in this application. The creation of every support follows this process: 1. Select a support type from a menu or icons. 2. Enter a name for the support. 3. Create a datum atta (attachment) and select an ancillary type. 4. Set distance and/or position for the datum atta. 5. Choose the steelwork from a list of available sizes. 6. Create using the required creation method. 7. Select miscellaneous options. 8. Select the packing if required. 9. Complete the process (the Integrity Checker runs automatically at this point).Draft1MDS11.6 User Guide1.3Administrator’s roleThe administrator is responsible for the initial setup of the default files and the design template database associated with the MDS application.1.4MDS catalogues and specificationsThe MDS application is supplied with a catalogue and specification. The range of bores and components in the catalogue are fixed. The /MDS specification contains all ancillary types, and the /MDF specification contains the SREF attachments for standard frameworks. The /MDP specification contains the preliminary support type available within the MDS application. The /RPAD-MDS-PLATE-MATERIAL specification contains the material used for reinforcing pad type supports. Caution: The catalogue and associated specifications must NOT be modified.Draft2MDS11.6 User Guide2Starting the application1. Start the Design General Application (default start-up). The Design General Application start-up form (Figure 1) is displayed.Figure 1 General Application form 2. Select Design>Multi Discipline Supports… from the main menu (Figure 2).Figure 2 Design pull-down menuDraft3MDS11.6 User GuideThe start-up form re-initialises to become the main menu bar (Figure 3), which includes all functions specific to the MDS module. The system tests for the existence of the design template database /MDS/TEMPLATES and the /MDS and /MDF specifications. If neither of these exists, MDS entry is stopped, an error message is displayed, and you re-enter the Design General Application. If this occurs, ask your administrator to add these databases to your MDB (Multiple Database).Figure 3 Main Menu Bar form Simultaneously, the application overlays a form (Figure 4) listing all valid zones found in the current MDB. The default file DES-SUPP-ID controls the selection of which zones are displayed. For more information on how these zones are selected, refer to the MDS Administration User Guide.Figure 4 Default Creation Zone form 3. Select a zone in which to create your support structures. Two tool bars (Figure 5) are located under the main menu bar.Draft4MDS11.6 User GuideIcons which control the general setup and display operations are positioned on the left. The icons to the tight of centre are short cuts to all the available menus in the MDS application. Place the cursor over each of these icons to display an associated tool tip. Note: Toolbars now conform to standard Windows operation and can be repositioned in a number of ways. Beware that some icons may be hidden if you re-arrange the toolbars. The hidden icons on any toolbar can be accessed using the drop-down arrow at the right-hand end of the toolbar.Figure 5 General setup and shortcut toolbars Each icon and its assigned action or purpose is listed in Table 1 below. Multi discipline supports Cable racking supports Anchors Variable hangers Guides and stops Specials Trunnions Branch reinforcements Modify support Preliminary support Defaults General supports HVAC supports Fixed hangers Constant hangers Slip units Springs Vessels supports Copy supports Delete support Lock/unlock support WizardReportsManualsTable 1 Menu shortcut iconsDraft52.1 Creating a multi discipline support1. Select the Create pull-down menu (Figure 6).Figure 6 Create menu2. Click on Multi Discipline Frame…. A form similar to the example shown in Figure 7 isdisplayed.Figure 7 Multi-discipline Frameworks selection formThis form contains all the available supports for the MDS application default file DES-SUPP-DEFS, which is located in the project default directory.You can also create support groups using the icon. Group names are identified by the suffix, [1]. Hangers can be added to the main framework support group and detailed as one entire MDS support drawing.Any unavailable support requires a different description to be displayed, or requires adifferent name to the standard name supplied. Such names can be modified in this file.Refer to the Administrators User Guide for further information.In the example shown in Figure 7, the prefix X has been added to all support default names.3. Enter a name as follows:a. Enter the name of the support to be created.If you enter a legal name in the Name field then click the OK button, the form becomes active. Notice that in Figure 7, no name is specified and so the OK button is inactive.or…b. Click on the AutoName button at the top of the form. An automatically generatedname is filled in (Figure 8) and the OK button is now active.Figure 8 Multi Discipline Frameworks selection form, with auto-naming4. Click on the required support type.Note:Do NOT click on OK at this time.At any time when the form shown in Figure 7 or Figure 8 is displayed, you can click on the View button to see the engineering drawing corresponding to the selected support. See the example in Figure 9.Figure 9 Engineering drawing for the selected support5. Right-click on the AutoName button and the button bar shown in Figure 10 is displayed.Figure 10 Initiate selecting a different naming file.6. Click on the Select Naming File… panel. The AutoNaming File form (Figure 11) isdisplayed. This allows you to select:a. a different AutoNaming file for the session,or…b. a different AutoNaming file set for the zone.Refer to the MDS Administration User Guide for further information.Note:Figure 8 remains displayed.Figure 11 AutoNaming File formYou can also select a zone, which is used to create all the support structures, by clicking on the Default Creation Zone button on the Multi Discipline Frames form.7. Select the support type required.8. Click on the OK button. The type is selected and the form closes. Refer to the MDSAdministration User Guide for further information.Example: Creating a support typeIn this example you will create support type XFT09, using the name FT09 1. Click on the OK button shown in Figure 8. A form similar to that shown in2.3. Figure 12 is displayed.Figure 12 XFT09 formSee section 2.6 for a descriptive overview of the icon functions.4. Ensure that the pipes, cable rack, or HVAC you need to support are added to the Drawlist,along with any other elements needed to create the support. This may include steelwork and panels, depending on the creation mode that is to be used. They must be added to the graphical view to be identified.5. Create the datum atta. This is the attachment on the first pipe that is associated with thesupport structure. This must be a pipe, not a cable rack or HVAC element.To create the datum atta select the Create datum support atta button at the top of the form. You are presented with the cursor so that you can identify a pipe. When you have done this, the Ancillary Selection form containing a filtered list of all the available ancillaries at the selected pipe bore, is displayed (Figure 13). These may be restricted for eachframework type. For more information refer to the MDS Administration User Guide.Figure 13 Ancillary Selection form6. Select the ancillary XAT16 (Bolt on Shoe) from the form. Click on the OK button. Theapplication now creates the pipe shoe on the selected pipe and positions it at the previous component or branch start, with a graphical tag of Datum for easy recognition. The Create Datum support Atta button is deactivated.7. Position the shoe on the pipe using:a. the Distance button, with a distance value placed in the text field next to it,or:..b. any of the Through button available options. These include; Through ID Cursor,Through Back Mark, and so on.8. Continue to add all the pipes, HVAC, and cable racks to the support. These can be addedThe application now positions the new attachments with respect to the datum atta.The example in Figure 14 shows two pipes, HVAC, and cable rack elements added to thesupport.Figure 14 Design screen 1Notice that the HVAC and cable rack support attachments have a ‘lollipop’ representation.This is because the fixings to the steelwork are regarded as supplied by the HVAC and cable rack contractor; no allowance is made for the selection of different fixings in the MDS application. The ‘lollipop’ representation is removed when the support is completed,returning to its original drawing level before the support was created. There are noobstruction properties associated with the lollipop representation and no clashes arereported.9. Choose the template required to create the support.10. Select the steelwork size icon .11. Select a template available from the list presented on the form (Figure 15). The template listshows all available templates. For this exercise, choose the second option, 80x80x10Angle, Internally Welded.Figure 15 Set Steelwork Size selection form12. Click Dismiss to access the selection and return to the Ancillary Selection form (Figure 13).13. Click on OK.There are three different options that you can use to create the steel framework:•Create by Cursor•Create by Clearance•Create by DimensionsYou will now create the framework with all three options and see what differences they make.2.1.1 Create by CursorOn the XFT09 form:1. Select the Create by Cursor icon. You are presented with the cursor and prompted from thestatus form to identify steelwork, boxes, or panels.2. Select the horizontal steelwork member parallel to the pipes on the left.3. Select the horizontal steelwork member to the right of the pipes.The application now creates the support using dimensions gained from the positions of theidentified steelwork. The view appears as shown in Figure 16. When complete, theapplication fills in all the dimensions with their correct values. These are stored against thesupport when it has finished, enabling future modifications of the support.Figure 16 Design screen 2Now add a cross member to support the HVAC and cable rack.4. Select the Add Cross Bar icon . You are presented with the cursor and asked to identifythe support attachment(s) to support with a cross bar.5. Identify the HVAC and cable rack ‘lollipop’.6. Click the Cancel button on the status form. The application creates the crossbar andpositions it at the correct elevation.Identify both attachments to which the cross will be attached. This information is used laterin the support Integrity Checker to check the packing distance between the cross bar andthe support attachment. The support Integrity Checker is executed whenever you press theOK button. The view is then as shown in Figure 17.Note:The elements to which the cross-beam is attached must be parallel to the piperun.Figure 17 Design screen 32.1.2 Create by ClearanceUsing the Create by Cursor method, two separate elements must be identified and theseelements must be parallel to the pipe run. Using the Create by Clearance method, only oneelement needs to be identified.1. Select the Create by Clearance icon. You are presented with the cursor to identify asteelwork member, box or, panel.2. Select the horizontal steelwork member that is perpendicular to, and above, the pipes.The application now creates the support using the dimensions gained from the position ofthe identified steelwork member. The clearances are calculated from the default values,obtained from the support Application Default form, and are used to calculate the positionsof the vertical members.These values and all other default values can be queried by displaying the MDS ApplicationDefaults form, from the Settings>Defaults>Applications menu item. For more informationon this and the other defaults used, refer to the MDS Administration User Guide.The application fills in all the dimensions with their correct values. The view is then asshown in Figure 18.MDS11.6 User Guide3 2Datum Pipe1ElevationFigure 18 Design screen 42.1.3 Create by DimensionsUse this method when the required steelwork is not yet entered into the 3D model, enabling you to continue working. 1. Enter the following dimensions in the MDS Framework form: Dimension 1 Dimension 2 Dimension 3 Dimension 4 = = = = 1300mm 350mm 1000mm 1100mmThe location of each dimension can be viewed by clicking on the View... button. This displays a plotfile with the dimensions shown. 2. Select the Create by Dimensions icon .The application now creates the support using the dimensions entered. The view is then as shown in Figure 19.Draft16MDS11.6 User Guide3 2Datum Pipe1ElevationFigure 19 Design screen 52.2Changing the size of the steelworkTo modify the size of the steelwork: 1. Select the Set Steelwork Size form (Figure 15). 2. Select the size required. The application recreates the support using the dimensions that are entered on the form. Try this by selecting option 4, “152 x 89 Channel Internally Welded”. The view is then as shown in Figure 20.3 2Datum Pipe1ElevationFigure 20 Design screen 5Draft17MDS11.6 User Guide2.3Adding a packing piecePacking pieces are used to make up height differences between the cross bar and support attachments. 1. Select the Add Packer icon from the MDS XFT09 form. You are presented with the cursor and a status line prompt to identify the support atta to add the packing piece to. The Packing Piece form (Figure 21) is displayed. 2. Fill in the form as required.Figure 21 Packing Piece formDraft18MDS11.6 User Guide2.4Creating and manipulating connections to external steelworkAfter the structural steelwork has been created, it may be necessary to connect it to external steelwork. To add a connection to external steelwork: 1. Select the Create Connections icon . This creates a connection only if the application knows the identity of the steelwork to connect to. If you used the Create by Cursor or Create by Clearance methods the connection to the external steelwork is made automatically. Note: It is essential that you have write access to create SNOD/SJOI elements on the necessary external steelwork.The SNOD is represented in the graphical view. The MDS application defaults control to the level at which joists can be made to the external steelwork. Refer to the MDS Administration User Guide for more details. 2. Select the Modify Joints icon available joints. . You are presented with a form that displays all the3. Select the joint for the joints connected to the external steelwork. If you have identified the external steelwork to connect to with either Create by Cursor or Create by Clearance, it is possible that the application will connect to the wrong Pline. This can happen in the case of the SCTN having floating Plines (X) (Figure 22a).RT0BFloating Pline XLT05TO5This is the Pline on the int. This is the Pline on the owning SCTN. X(a)X(b)Figure 22 Forced connection to SCTN with floating Plines You can force-connect the joint to a specific Pline (Figure 22b) by selecting the Force Connect joint icon . You are prompted to identify the required Pline using the cursor.Draft19。
境外旅客购物离境退税申请单
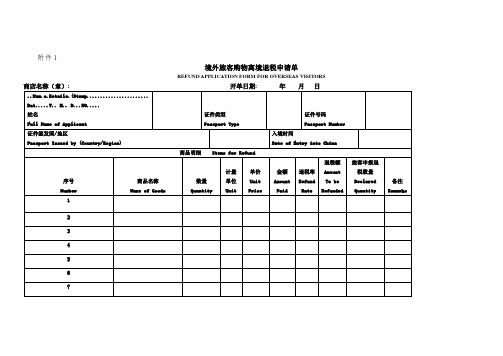
证件类型
Passport Type
证件号码
Passport Number
证件签发国/地区
Passport Issued by (Country/Region)
入境时间
Date of Entry into China
商品明细 Items for Refund
旅客退税
申请
Tourist Application
1.退税方式.. 现金.......转账...开户行........... 银行账号:
Refun.Mode...Cas..... Ban.Transfe..Ban. Nam......... Accoun. No..........2.退税币种..... 人民.. 美....欧...日元
附件1
境外旅客购物离境退税申请单
REFUND APPLICATION FORM FOROVERSEASVISITORS
商店名称(章):开单日期:年月日
..Nam.o.Retaile.(Stamp....................... Dat.....Y.. M.. D...NO.....
姓名
Preferred Currency RMB□ USD□ EUR□ JPY□
3. 电话: 旅客签名:
Tel............. Applicant’. Signatur............ 日期.... ..日
........................................Dat...Y.. M.. D.
序号
Number
商品名称
Name of Goods
数量
Quantity
Adobe Acrobat SDK 开发者指南说明书
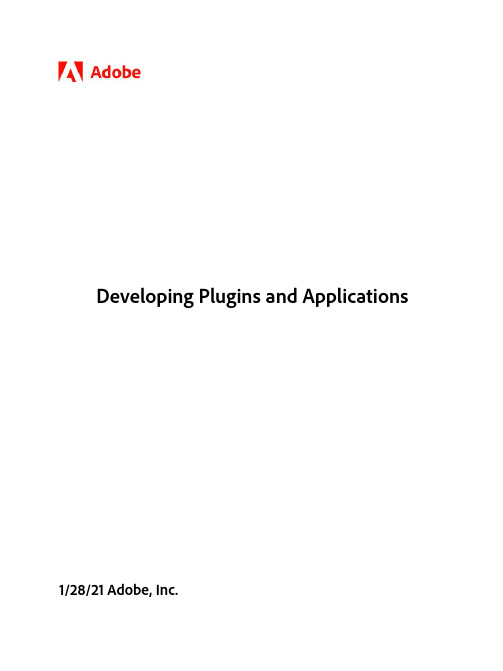
This guide is governed by the Adobe Acrobat SDK License Agreement and may be used or copied only in accordance with the terms of this agreement. Except as permitted by any such agreement, no part of this guide may be reproduced, stored in a retrieval system, or transmitted, in any form or by any means, electronic, mechanical, recording, or otherwise, without the prior written permission of Adobe. Please note that the content in this guide is protected under copyright law.
诺基亚智能手机使用指南说明书
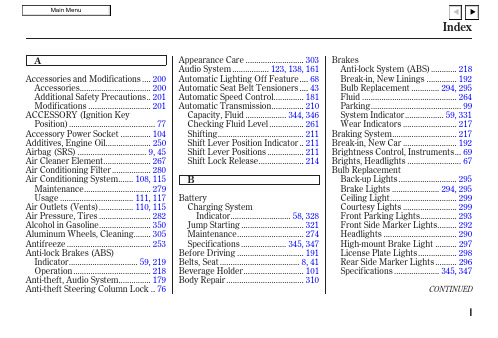
C
Capacities Chart .................... 344, 346 Carbon Monoxide Hazard .............. 52 Carrying Cargo .............................. 202 Cassette Player
Charging System Indicator .... 58, 328 Checklist, Before Driving............. 206 Child Safety ...................................... 20 Child Seats........................................ 25
Before Driving ............................... 191 Belts, Seat ..................................... 8, 41 Beverage Holder............................ 101 Body Repair .................................... 310
Maintenance............................... 279 Usage .................................. 111, 117 Air Outlets (Vents)................ 110, 115 Air Pressure, Tires ........................ 282 Alcohol in Gasoline........................ 350 Aluminum Wheels, Cleaning........ 305 Antifreeze ....................................... 253 Anti-lock Brakes (ABS) Indicator................................ 59, 219 Operation .................................... 218 Anti-theft, Audio System............... 179 Anti-theft Steering Column Lock .. 76
LabelManager 210D 使用指南说明书
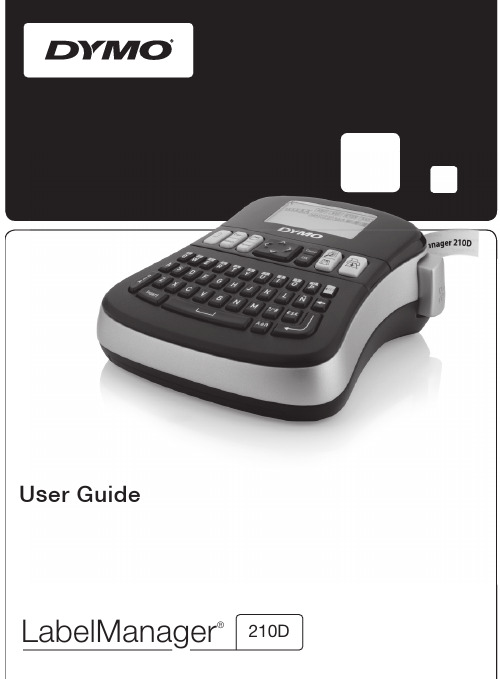
User GuideCopyright© 2011-2018 Newell Rubbermaid Europe, LLC. All rights reserved. Rev. 12/6/18No part of this document may be reproduced or transmitted in any form or by any means or translated into another language without the prior written consent of Newell Rubbermaid Europe, LLC.TrademarksDYMO and LabelManager are registered marks in the US and other countries. All other trademarks are the property of their respective holders.FCC StatementCaution: The user is cautioned that changes or modifications not expressly approved by the party responsible for compliance could void the user's authority to operate the equipment.Note: This equipment has been tested and found to comply with the limits for a Class B digital device, pursuant to part 15 of the FCC Rules. These limits are designed to provide reasonable protection against harmful interference in a residential installation. This equipment generates, uses and can radiate radio frequency energy and, if not installed and used in accordance with the instructions, may cause harmful interference to radio communications. However, there is no guarantee that interference will not occur in a particular installation. If this equipment does cause harmful interference to radio or television reception, which can be determined by turning the equipment off and on, the user is encouraged to try to correct the interference by one or more of the following measures:•Reorient or relocate the receiving antenna.•Increase the separation between the equipment and receiver.•Connect the equipment into an outlet on a circuit different from that to which the receiver is connected.•Consult the dealer or an experienced radio/TV technician for help.Figure 1 DYMO® LabelManager® 210D Electronic Label Maker1Tape cutter 9Accented character17AC power connector 2Print10Punctuation18Clear3Save11Space bar19Open4OK12Insert20Navigation5Number lock13Caps21LCD display6Backspace14Format22Cancel7Currency15Settings23Preview8Return16On/Off2About Your New Label MakerWith the DYMO® LabelManager® 210D electronic label maker, you can create a wide variety of high-quality, self-adhesive labels. You can choose to print your labels in many different font sizes and styles. The label maker uses DYMO D1 tape cassettes in widths of 6mm (1/4”), 9mm (3/8”), or 12mm (1/2”). These tape cassettes are available in a wide range of colors.Visit for information on obtaining labels and accessories for your label maker.Product RegistrationVisit /registration to register your label maker online. Getting StartedFollow the instructions in this section to print your first label.Connecting the PowerThe label maker is powered by standard batteries or an AC power adapter. To save power, the label maker automatically turns off after two minutes of inactivity.Inserting the BatteriesThe label maker uses six high-capacity AA alkaline batteries.To insert the batteries1.Slide the battery compartment cover away fromthe label maker. See Figure 2.2.Insert the batteries following the polaritymarkings (+ and –).3.Replace the cover.Figure 2ÇRemove the batteries if the label maker will notbe used for a long period of time.34Connecting the Optional Power AdapterAn optional 9 Volt, 1.5 A power adapter can also be used to power the label maker. Connecting the AC adapter to the label maker disconnects the batteries as a power source.Use only power the adapter listed in this user guide:Adapter model DSA-18PFM-09 Fc 090200 (note: “c” can be EU, UP , UK, US, UJ, JP , CH, IN, AU, KA, KR, AN, AR, BZ, SA, AF or CA) from Dee Van Enterprise Co., Ltd.To connect the power adapter1.Plug the power adapter into the power connector onthe top, left side of the label maker.2.Plug the other end of the power adapter into a power outlet.ÇMake sure the label maker power is turned off before you disconnect the power adapter from the main power source. Otherwise, your most recent memory settings will be lost.Inserting the Tape CassetteYour label maker comes with one tape cassette. You can purchase additional tape cassettes from yourlocal office supply retailer.Cutter blade is extremely sharp. Whilereplacing the label cassette, keep fingers and other body parts away from cutter blade and do not press the cutter button.To insert the tape cassette1.Lift the tape cassette cover to open the tape compartment. See Figure 3.2.Insert the cassette with the label facing up and positioned between the guideposts.Figure 4Figure 53.Press firmly until cassette clicks into place. See Figure 5.4.Close the tape cassette cover.Using the Label Maker for the First TimeThe first time you turn on the power, you are asked to select the language. This selection will remain set until you change it, or until the label maker is reset. You can change this selection using the I key.To set up the label maker1.Press A to turn on the power.2.Select the language and press }.By default, the language is set to English. The language option you choose determines the character set that is available.3.Select inches or mm and press }.4.Select the width of the tape cassette currently in the label maker and press }. You are now ready to print your first label.To print a label1.Enter text to create a simple label.2.Press G.3.Select the number of copies.4.Press } to print.5.Press the cutter button to cut the label.Congratulations! You printed your first label. Continue reading to learn more about the options available for creating labels.Getting to Know the Label MakerBecome familiar with the location of the feature and function keys on your label maker. Refer to Figure1. The following sections describe each feature in detail.56PowerThe A button turns the power on and off. After two minutes of no activity, the poweris switched off automatically. The last label created is remembered and displayed when the power is turned back on. The previously selected style settings are also restored.LCD DisplayYou can enter up to 99 characters and spaces. The display shows about 13 characters at a time. The number of characters displayed will vary due to proportional spacing. With DYMO’s exclusive graphical display, most of the formatting you add is visible instantly. For example, the italics and rounded border added to the text below is clearly displayed.Feature indicators along the top of the LCD display appear black to let you know when a feature is selected.FormatThe 2 key displays the Font Size, Clear Format, Mirror, Label Length, Alignment,Underline, Borders, and Style submenus. These formatting features are described later in this User Guide.InsertThe 8 key allows you to insert symbols or saved text on your label. These featuresare described later in this User Guide.SettingsThe I key displays the Language, Units, Label Width and Contrast submenus.These features are described later in this User Guide.Thedefault setting is Caps mode on. When Caps mode is off, all letters appear in lower case.the numbers 0 through 9 appear when you press the corresponding letter keys. Num Lock is turned off by default.BackspaceThe 0 key removes the character to the left of the cursor.ClearThe 6 key gives you a choice to clear all label text, just the text formatting, or both. Navigation KeysYou can review and edit your label using the left and right arrow keys. You can also navigate through menu selections using the up and down arrow keys, and then press } to make a selection.CancelThe 7 key allows you to exit from a menu without making a selection or to cancel an action.Formatting Your LabelYou can choose from several format options to enhance the appearance of your labels. Changing the Font SizeSix font sizes are available for your labels: Extra Small, Small, Medium, Large, Extra Large, and Extra Extra Large. The font size applies to all characters on a label.78To set the font size 1.Press 2.2.Select Font Size and press }.3.Select the desired font size and press }.The font size indicator on the display changes as you select font sizes.Adding Font StylesYou can choose from six different font styles:The style you select applies to all characters. Styles can be used with alphanumeric characters and some symbols.To set the font style1.Press2.2.SelectStyle and press}.3.Select a font style and press }.Adding Borders and Underline StylesYou can highlight your text by choosing a border or underline style.A label can be underlined or enclosed in a border, but not both together.To add a border style 1.Press 2.Normal Outline Bold Shadow ItalicVerticalUnderline ParchmentSquare Call Out Rounded FlowersEdged CrocodilePointed2.Select Borders and press }.3.Select a border style and press }.When using borders on two-line labels, both lines are enclosed in one border.To add an underline1.Press2.2.Select Underline and press }.3.Press } again when the underlined text is shown in the display.On two-line labels, both lines are underlined.Creating Two-Line LabelsYou can print a maximum of two lines on labels.To create a two-line label1.Type the text for the first line and press D.A new-line symbol ë is inserted at the end of the line, but will not print on the label.2.Type the text for the second line.3.Press G to print.Aligning the TextYou can align the text to print left or right justified on the label. The default alignment is centered.To change the alignment1.Press2.2.Select Alignment and press }.3.Select right, left, or centered alignment and press }.Using Mirror TextThe mirror format allows you to print text which reads from right to left, as you would see it in a mirror.To turn on mirror text1.Press the 2key.2.Select Mirror and press }.93.Select On and press }.Using Symbols and Special CharactersSymbols, punctuation, and other special characters can be added to your labels. Adding SymbolsThe label maker supports the extended symbol set shown below.To insert a symbol1.Press 8, select Symbols, and press }.2.Select the symbol category and press }.e the left and right arrow keys to move to your desired symbol.The left and right arrows move horizontally along a row of symbols. The up and down arrow keys scroll vertically through the rows of symbol types.4.When you locate the symbol, press } to add the symbol to your label.Adding PunctuationYou can quickly add punctuation using the punctuation shortcut key.1.2.}.Using the Currency KeyYou can quickly add a currency symbol using the currency shortcut key.To insert a currency symbol1.2.}.Adding International CharactersThe label maker supports the extended Latin character set using RACE technology.After pressing the Accent key, repeatedly pressing a letter scrolls through the available variations of that letter.For example, if French is selected as the language and you press the letter a , you will see a à â æ and so on through all the variations available. The character variations and the order in which the variations appear depend on the language you use.1.2.3.When the desired accented character appears, wait a few seconds for the cursor to move beyond the character to continue entering text.Printing OptionsYou can preview your label, print multiple labels, and adjust the printing contrast.Previewing Your LabelYou can preview the text or format of your label prior to printing. A two-line label is previewed as a single-line label with a line break character between the two lines.To preview your labelPress 5.The label length is displayed, then the text of the label scrolls across the display. Printing Multiple LabelsEach time you print, you are asked how many copies to print. You can print up to ten copies at one time.To print multiple labels1.Press G.2.Select the number of copies to print, and press }.When printing is finished, the number of copies to print returns to the default value of 1. Creating Fixed-Length LabelsNormally, the length of the label is determined by the length of the text. However, you can choose to set the length of the label for a specific application.When you choose a fixed label length, the label text is automatically resized to fit the label. If the text cannot be adjusted to fit within the fixed label length, a message is displayed showing the smallest possible label length for this text. You can choose a fixed length label up to 400 mm (15”) long.To set the label length1.Press the 2 key.2.Select Label Length and press }.3.Select Fixed and press }.4.Select the length for your label and press }.Adjusting the Print ContrastYou can adjust the print contrast to fine tune the print quality of your label.To set the contrast1.Press I.2.Select Contrast and press }.e the arrow keys to select a contrast setting between 1 (less contrast) and 5 (more contrast), and press }.Using the Label Maker MemoryThe label maker has a powerful memory feature that allows you to save the text of up to nine frequently-used labels. You can recall saved labels and you can insert saved text into a label.Saving a LabelYou can save up to nine frequently-used labels. When you save a label, the text and all formatting are saved.To save the current label1.Press 3.The first available memory location is displayed.e the arrow keys to move through the locations.You can store new text in any of the memory locations.3.Select a memory location and press }.Your label text is saved and you are returned to the label.Opening Saved LabelsYou can easily open labels saved in memory to use at a later time.To open saved labels1.Press4.A message is displayed to confirm you want to overwrite the current label.2.Press }.The first memory location is displayed.e the arrow keys to select a label to open and press }.A message is displayed to confirm you want to overwrite the current label.To clear a memory location, first select a memory location and then press Clear. Inserting Saved TextYou can insert the text of a saved label into the current label. Only the saved text is inserted, not the formatting.To insert saved text1.Position the cursor at the location in the label where you want to insert the text.2.Press 8.The first memory location is displayed.e the arrow keys to select the text you want to insert.4.Press }. The text is inserted in the current label.Caring for Your Label MakerYour label maker is designed to give you long and trouble-free service, while requiring very little maintenance. Clean your label maker from time to time to keep it working properly. Clean the cutter blade each time you replace the tape cassette.Cutter blade is extremely sharp. Avoid direct contact with the cutter blade while cleaning the blade.To clean the cutter blade Array1.Remove the tape cassette.2.Press and hold the cutter button to exposethe cutter blade. See Figure 6.e a cotton ball and alcohol to clean bothsides of the blade.To clean the print head1.Remove the tape cassette.Figure 62.Remove the cleaning tool from inside thelabel compartment cover.If you do not have a cleaning tool, contact DYMO Customer Care().3.Gently wipe the padded side of the tool across the print head.See Figure 6.TroubleshootingReview the following possible solutions if you encounter a problem while using your label maker.If you still need assistance, contact DYMO Customer Support. Problem/Error Message Solution No display •Ensure the label maker is turned on.•Replace discharged batteries.Poor Print Quality •Replace batteries or attach power adapter.•Set Contrast to higher level. See Adjusting the PrintContrast.•Ensure tape cassette is installed properly.•Clean the print head.•Replace the tape cassette.Poor Cutter Performance Clean the cutter blade. See Caring for Your Label Maker .Printing . . .No action required. Message disappears when printing is finished.Too many characters Exceeded maximum number of characters in buffer.Delete some or all of the buffer text.Too many lines Exceeded maximum number of lines •Delete a line to fit on the tape width.•Insert a wider tape cassette.Replace batteries or connect AC power adapter.Tape Jam Motor is stalled due to label jam.•Remove jammed label; replace tape cassette. •Clean cutter blade.Environmental InformationThe equipment that you have bought requires the extraction and use of natural resources for its production. It may contain substances that are hazardous to health and the environment.In order to avoid the dissemination of those substances in our environment, and to diminish the pressure on natural resources, we encourage you to use the appropriate take-back systems. These systems will reuse or recycle most of the materials of your end-of-life equipment in an environmentally sound way.The crossed-bin symbol marked on your device indicates you should use these systems. If you need more information on the collection, reuse, and recycling of this product, please contact your local or regional waste administration.You can also contact us for more information on the environmental performance of our products.This product is CE marked in accordance with the EMC directive and the low voltage directive and is designed to conform with the following international standards:US FCC Class B CompatibilitySafety - UL, CUL, TUV, CE, T-Mark, SAA, BABT, C-TickEMC - EMI CompatibilityEN 55022; EN 61000 (+ addendums)RoHS 2002/95/EC。
华为数据卡安装指南说明书
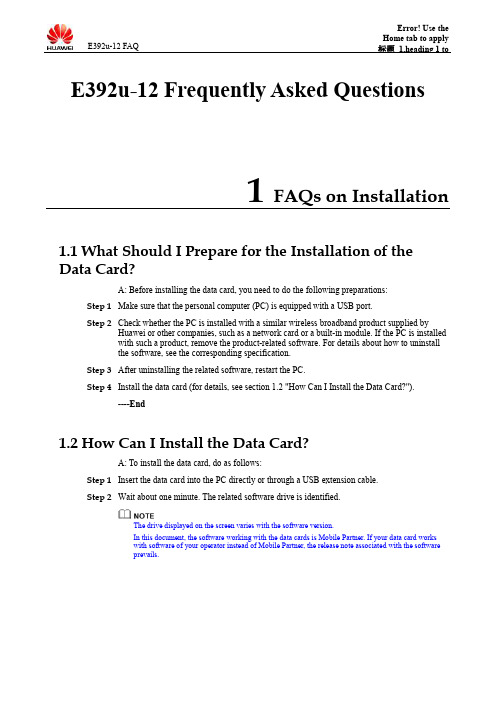
Step 3 The operating system (OS) automatically runs the setup program and installs the Mobile Partner step by step. If the automatic setup fails, see section 1.4 "How Can I Enable Automatic Installation?" or section 1.5 "If Automatic Installation Is Not Enabled, How Can I Install the Data Card Manually?". Figure 1-2 Installer Language
The Group Policy Object Editor window is displayed.
Error! Use the
E392u-12 FAQ
Home tab to apply 标题 1,heading 1 to
the text that you
want to appear
Step 2 In the left pane, choose Local Computer Policy > Computer Configuratihoenre>.Error! Use the
Huawei or other companies, such as a network card or a built-in module. If the PC is installed with such a product, remove the product-related software. For details about how to uninstall the software, see the corresponding specification. Step 3 After uninstalling the related software, restart the PC. Step 4 Install the data card (for details, see section 1.2 "How Can I Install the Data Card?"). ----End
ArcSight Connector Appliance 初次设置指南说明书

Getting Started Connector ApplianceSummaryThis document describes how to set up the ArcSight Connector Appliance for the first time.Use the detailed rack installation instructions included in the appliance shipment to rackmount your appliance.Installation Instructions1Unpack the appliance and its accessories. 2Follow the rack installation instructions to securely mount the appliance.3Make the rear panel connections.4Power on the appliance.5Optional: Configure the appliance for out-of-band remote access so that ArcSightCustomer Support can access and troubleshoot the appliance if it becomesunresponsive. All appliance models are equipped with HP Integrated Lights-Out (iLO)Advanced. Visit /go/iLO for detailed information anddocumentation.6Configure the Connector Appliance. Refer to “Configuring Connector Appliance for theFirst Time.”Configuring Connector Appliance for the First TimeYou can configure the ArcSight Connector Appliance for the first time in one of two ways:⏹With the command-line interface (CLI), as described in Using the CLI. ⏹With the graphical-user interface (GUI), as described in Using the GUI.Using the CLIThe Connector Appliance ships with the following default IP addresses. If you are alreadyusing these IP addresses, configure the appliance before connecting it to the network toavoid conflicts.Eth0: 192.168.35.35 (subnet mask 255.255.255.0)Eth1: 192.168.36.35 (subnet mask 255.255.255.0)Eth2: 192.168.37.35 (subnet mask 255.255.255.0)Eth3: 192.168.38.35 (subnet mask 255.255.255.0)Read carefully through the instructions, cautions, and warnings included withthe appliance shipment. Failing to do so can result in bodily injury or appliance malfunction.1Use one of the following methods to connect to the appliance:◆Connect a keyboard and monitor to the rear panel connectors on the appliance.◆Connect a terminal to the serial port on the appliance using a null modem cablewith a DB-9 connector. The serial port expects a standard VT100-compatibleterminal: 9600 bps, 8-bits, no parity, 1 stop bit (8N1), no flow control.◆If iLO is configured, use the remote console feature. 2Use the following username and password to log in as the administrator:Username: adminPassword: password3Enter set password to change the default administrator password. Enter the current and new password at the prompts.4Configure network settings for the appliance.You can enter ? for a list of the CLI commands available.a Enter set ip eth0 ip/prefix , where ip is the IP address you want to use forthe appliance and prefix is the number of bits in the subnet mask (for example,/24 = 255.255.255.0).bEnter set hostname hostname where hostname is the fully-qualified domain name (FQDN) you want to use for the appliance.c Enter set dns search_domain_name1,search_domain_name2,…nameserver1 nameserver2, where each search_domain_nameN is a search domain and each nameserverN is the IP address of a name server.For example: set dns ,192.0.2.12 192.0.2.14.dEnter set defaultgw ip , where ip is the IP address of your default gateway.eEnter show config to confirm that the settings are correct for your environment.5Verify the date and time settings:aEnter show date to view the settings.b If the displayed date or time is incorrect, enter set date date , where date isthe date and time in yyyyMMddHHmmss format. For example, set date20110105155509.6If you have not already done so, connect the Connector Appliance to the network port on a switch or router on which you want your appliance to be located.7Copy the license file you received from ArcSight to a computer on your network from which you want to access the Connector Appliance UI.8Open a Flash-enabled browser on the computer and enter the URL: https://ipwhere ip is the IP address you provided in Step 4.You need to change at least one of the default IP addresses to an address that is valid on your network.9At the login screen, log in to Connector Appliance as the administrator with the newpassword you provided in Step 3.10Apply the license file. A valid license file is required on the Connector Appliance beforeyou can access most of the features.aClick Setup > System Admin from the top-level menu bar. bClick License & Update in the System section in the left panel.c Browse to the license file and click Upload Update .11The Connector Appliance Deployment Wizard opens. Follow the steps in the wizard toconfigure additional settings.Using the GUIThe Connector Appliance ships with the following default IP addresses. If you are alreadyusing these IP addresses, use the CLI to configure the Connector Appliance. Refer to“Using the CLI” above.Eth0: 192.168.35.35 (subnet mask 255.255.255.0)Eth1: 192.168.36.35 (subnet mask 255.255.255.0)Eth2: 192.168.37.35 (subnet mask 255.255.255.0)Eth3: 192.168.38.35 (subnet mask 255.255.255.0)1Copy the license file you received from ArcSight to a computer from which you want toconfigure the appliance. The computer must have a Flash-enabled web browserinstalled.2Using an Ethernet cable, connect the Eth0 port of the appliance to your network porton a switch or a router on which you want your appliance to be located.3Using a cross-over cable, connect the Eth1 port of the appliance to the computer.Configure the computer to be on the 192.168.36.0/24 network. For example,192.168.36.10.4Open the web browser on the computer and enter the default appliance URL:https://192.168.36.35/ to access the Connector Appliance GUI.5At the login screen, use the following username and password to log in as theadministrator:Username: adminPassword: password6Apply the license file. A valid license file is required on the Connector Appliance beforeyou can access most of the features.aClick Setup > System Admin from the top-level menu bar.bClick License & Update in the System section in the left panel.c Browse to the license file and click Upload Update.The first page of the deployment wizard guides you through configuring thenetwork settings on the appliance. These are the same settings youconfigured in Step 4. Skip this page and continue to configure the additional settings.7The Connector Appliance Deployment Wizard opens. Follow the steps in the wizard toconfigure the Connector Appliance.Using Connector ApplianceRefer to the ArcSight Connector Appliance Administrator’s Guide and the Release Notes,found on the Support Web site referenced below, for information about using ConnectorAppliance. Online Help is also available from the Help link in the Connector Appliance GUI.Contact Information© Copyright 2012 Hewlett-Packard Development Company, L.P.Confidential computer software. Valid license from HP required for possession, use or copying. Consistent with FAR 12.211 and 12.212, Commercial Computer Software, Computer SoftwareDocumentation, and Technical Data for Commercial Items are licensed to the U.S. Government under vendor's standard commercial license.The information contained herein is subject to change without notice. The only warranties for HPproducts and services are set forth in the express warranty statements accompanying such products and services. Nothing herein should be construed as constituting an additional warranty. HP shall not be liable for technical or editorial errors or omissions contained herein.Follow this link to see a complete statement of copyrights and acknowledgements: /copyrightnoticeThe network information used in the examples in this document (including IP addresses and hostnames) is for illustration purposes only.This document is confidential.March 2012Be sure to configure an IP address for the appliance that is valid on yournetwork and to change the default administrator password.Phone1-866-535-3285 (North America)+44 (0)870 141 7487 (EMEA)Support Web Site Protect 724 Community https://。
laicpms的的操作流程
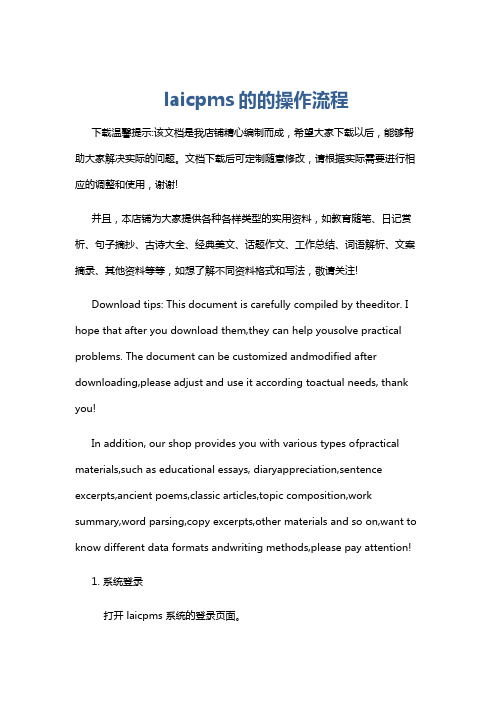
laicpms的的操作流程下载温馨提示:该文档是我店铺精心编制而成,希望大家下载以后,能够帮助大家解决实际的问题。
文档下载后可定制随意修改,请根据实际需要进行相应的调整和使用,谢谢!并且,本店铺为大家提供各种各样类型的实用资料,如教育随笔、日记赏析、句子摘抄、古诗大全、经典美文、话题作文、工作总结、词语解析、文案摘录、其他资料等等,如想了解不同资料格式和写法,敬请关注!Download tips: This document is carefully compiled by theeditor. I hope that after you download them,they can help yousolve practical problems. The document can be customized andmodified after downloading,please adjust and use it according toactual needs, thank you!In addition, our shop provides you with various types ofpractical materials,such as educational essays, diaryappreciation,sentence excerpts,ancient poems,classic articles,topic composition,work summary,word parsing,copy excerpts,other materials and so on,want to know different data formats andwriting methods,please pay attention!1. 系统登录打开 laicpms 系统的登录页面。
输入正确的用户名和密码。
Akai Professional MPD18 快速上手指南英文版说明书
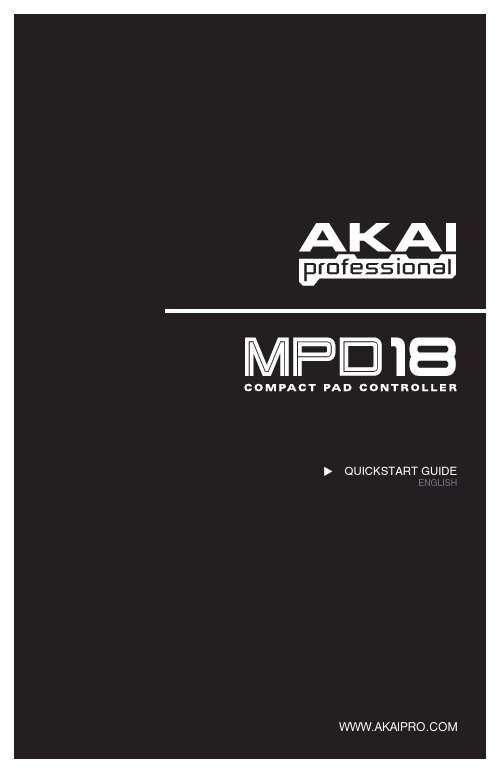
y MPD18 y Software CDy USB cable y Safety Instructions & Warranty InformationPC Users: To install the Akai Professional MPD18 Editor, open the contents of the disc, double-click Setup.exe, and follow the on-screen instructions. To open the editor, connect the MPD18 to your computer with a standard USB cable (included) then double-click MPD18 Editor.exe.Mac Users: Drag the contents of the disc to an appropriate location on your hard drive. To open the editor, connect the MPD18 to your computer with a standard USB cable (included) then double-click the MPD18 Editor.Note: Always connect the MPD18 to your computer before opening the editor. ArrayB CO NNECTIO N – Plug a standardUSB cable into this outlet and into the USBport of your computer. The computer’sUSB port will provide power to the MPD18.2.VELOCITY SENSITIVE PADS – The padscan be used to trigger drum hits or othersamples in your software. The pads arepressure and velocity sensitive, whichmakes them very responsive and intuitiveto play.3.NOTE REPEAT – Holding this button whilestriking a pad causes the pad to retrigger ata rate based on the current Tempo, TimeDivision, and Swing settings. Note Repeatcan be synced to an internal or externalMIDI Clock source. It can also function asa momentary or toggle switch. Thesesettings are configurable for each Preset(see NR CONFIG).4.ASSIGNABLE FADER – This fader can beused to send continuous control data to adesktop audio workstation.5.PAD BANK – This button switches between pad banks A, B, and C. Each bank can address a unique set of 16 sounds,giving you access of up to 48 different sounds you can trigger with the pads. The currently selected pad bank will be indicated with a lit LED.6.PRESETS – This button allows you to select different preset mappings (of the pads and assignable button and fader).Press and hold it then press the pad with the number of the preset you want (1-16). You can customize these presets in the software editor (see the SOFTWARE EDITOR section for more information). See the PRESETS section for descriptions of the available default presets.7.MIDI CH – This button allows you to change the master MIDI channel the MPD18 sends. Press and hold it then pressthe pad with the channel number you want (1-16).8.FULL LEVEL – When FULL LEVEL is activated, the pads always play back at a maximum velocity (127), no matter howhard or soft you hit them.9.NR CONFIG (Note Repeat Configuration) – This button is used to adjust the current Note Repeat parameters.Note: Ch anges made with th e NR CONFIG button will not be stored in th e Preset. For th ese (and additional) parameters to be stored in the Preset, edit them in the software editor.y Time Division: Hold down NR CONFIG and press any one of Pads 1 through 8 to set the desired Time Division – the rate of Note Repeat. The Time Division value is next to the pad number on the MPD18.y Swing: Hold down NR CONFIG and press any one of Pads 9 through 15 to set the desired Swing setting for Note Repeat. The Swing value is next to the pad number on the MPD18. (For finer adjustments to the Swingvalue, use the software editor.)y Tempo: If Note Repeat is set to the internal clock (the default), the LED above NR CONFIG will flash at the current Note Repeat tempo. To enter a new tempo, hold down NR CONFIG and tap Pad 16 ("Tap Tempo") intime with the desired tempo. (The LED will not flash if Note Repeat is synced to an external clock.)Always connect the MPD18 to your computer before opening the software editor.After opening the software editor, you will need to select the MPD18 from the drop-down menu on the opening screen and click "Done."y For Mac or Windows Vista users, it will be listed as Akai MPD18.yFor Windows XP users, it will be listed as USB Audio Device . (If you have other USB audio devices connected to your computer, which may have identical names, you may need to try selecting each one until the MPD18 is recognized.)The editor lets you edit, save, or load presets for the MPD18 on your computer. These buttons and fields are shown at the top of the editor window.1. GET PRESET – Click on this field to select the number of a preset currently on the MPD18 (1-16).When you select it, its settings will be shown on the software interface. 2. EDIT PRESET – Click on this field to select the number that the currently shown preset will use if you upload it to the MPD18 (by clicking COMMIT – UPLOAD).3. COMMIT – UPLOAD – Click this button to send the currently shown preset to the MPD18. The number of this preset is determined by the EDIT PRESET field.4.SAVE PRESET – Click this button to save the currently shown preset to your computer.5.LOAD PRESET – Click this button to load a saved preset from your computer. Once it loads, you will see its settings in the software interface.TO COPY A PRESET: 1. Load the preset you want to copy from the MPD18 by clicking GET PRESET field and selecting it. 2. Set the preset you want to copy it to on the MPD18 by clicking EDIT PRESET field and selecting it. 3.Click COMMIT – UPLOAD to send the copied preset to the MPD18.IMPORTANT!: The first time you use the software editor, even if the correct device is already shown in the drop-down menu, you still need to click on the menu and select the device. (You will also need to do this if you move your files to a new location.) In future sessions, though, you can simply click "Done" if the correct device is shown in this window.Note: When you save a preset, the current EDIT PRESET number will be saved with it. Wh en you load th at preset later, th e EDIT PRESET field will be updated with th at number. If you want to change the preset number before uploading it to th e MPD18, simply select a new EDIT PRESET number before clicking COMMIT – UPLOAD.This section outlines the editable items for each preset.Items #1-4 are editable for every pad.1.PAD TYPE – Click this button to select Note orProg Change. When Note is selected, pressingthat pad will send the MIDI Note Number you haveselected (see NO TE #). When Prog Change isselected, pressing that pad will send the ProgramChange Number you have selected (see PC #).2.AFTERTOUCH – Click this button to open a drop-down menu with three options: No Aftertouch, Ch.AftrTch, and Poly AftrTch:y No Aftertouch: The pad will send no Aftertouchinformation.y Ch. AftrTch (Channel Aftertouch): The pad willsend Aftertouch information over the MPD18'sglobal MIDI channel. If multiple buttons with Channel Aftertouch are pressed simultaneously, their affect is cumulative.y Poly AftrTch (Poly Aftertouch): The pad will send Aftertouch information for that pad's assigned MIDI Note Number only. Poly Aftertouch pads will send Aftertouch information independently from Channel Aftertouch pads and from other Poly Aftertouch pads. (If multiple Poly Aftertouch pads are sending the same MIDI Note Number, though, their affect is cumulative.)3.NO TE # – Click on this field and drag up or down with the mouse (or use your keyboard's or keys) tochange the MIDI Note Number the pad will send. (You will also have to select Note as its PAD TYPE for it to transmit this note.)4.PC # – Click on this field and drag up or down with the mouse (or use your keyboard's or keys) to changethe MIDI Program Change number the pad will send. (You will also have to select Prog Change as its PAD TYPE for it to transmit this message.)5.NO TE DISPLAY TYPE – Click this button todisplay either the MIDI Note Number or the actualmusical note the pad will send.6.PAD BANK – Click this button to switch throughthe three available banks on the MPD18. Thesettings for the pads in these other banks will beshown on the interface.7.ASSIGNABLE FADER – This fader on the MPD18 can send a Control Change number or Channel Aftertouch.Click on the first button underneath it to select Control Change or Ch. AfterTouch.Click on the number next to CC# and drag up or down with the mouse (or use your keyboard's or keys) to change the Control Change number the button will send.8.NR CO NFIG (Note Repeat Configuration) –Click this button to open a new window where youcan adjust the Note Repeat parameters for thecurrent Preset. Click on a field to select a settingfor that parameter:y BPM (Tempo): Click on this field and drag upor down with the mouse (or use yourkeyboard's or keys) to set the desiredtempo of Note Repeat when the MPD18 is synced to the internal clock. Select a value between 30 and 300 BPM (beats per minute).y Time Division: Click this button to open a drop-down menu and select the desired Time Division – the rate of Note Repeat. Select 1/4, 1/8, 1/16, 1/32, 1/4 Triplet, 1/8 Triplet, 1/16 Triplet, or 1/32 Triplet.y NR Button Behavior: Click this button to select whether the MPD18's NOTE REPEAT button will function as a "Momentary" or "Toggle" switchy Swing: Click on this field and drag up or down with the mouse (or use your keyboard's or keys) to set the desired Swing value for Note Repeat. Select a value from 50 to 75. (At 50, Swing is turned off. The most "even" Swing feel is at 67.)y MIDI Clock: Click this button to select "Internal" (the default) to sync it to the internal MIDI clock, then remember to select a Tempo. Select "External" to sync the Note Repeat function to an external MIDI clock.To select a Preset, press and hold the MPD18's PRESETS button then press the pad with the number of the Preset you want (1-16). Each Preset comes with a pre-assigned mapping for the 16 pads, as shown below. You can change and save any of these mappings in the software editor.PRESET #NAME DESCRIPTION1 Chromatic The 16 pads are mapped to a chromatic scale from C to D#Eb, ascending a half-stepWith each pad number (e.g., Pad 1 = C, Pad 2 = C#/Db, Pad 3 = D, Pad 4 = D#/Eb,etc.).2 GM / MPC The 16 pads are mapped to conventional default MPC pad mappings.1-48 The 16 pads are mapped to transmit Program Change messages 1-48 across all three 3 Progbanks.pad4 Prog49-96 The 16 pads are mapped to transmit Program Change messages 49-96 across allpadbanks.threeScale The 16 pads are mapped to a C major scale from C to D, ascending a scale degree5 Cwith each pad number (e.g., Pad 1 = C, Pad 2 = D, Pad 3 = E, Pad 4 = F, etc.).6 C# / Db Scale The 16 pads are mapped to a C#/Db major scale from C#/Db to D#/Eb, ascending aScale degree with each pad number (e.g., Pad 1 = Db, Pad 2 = Eb, Pad 3 = F,Pad 4 = Gb, etc.).Scale The 16 pads are mapped to a D major scale from D to E, ascending a scale degree7 Dwith each pad number (e.g., Pad 1 = D, Pad 2 = E, Pad 3 = F#, Pad 4 = G, etc.).8 D# / Eb Scale The 16 pads are mapped to a D#/Eb major scale from D#/Eb to E#/F, ascending aScale degree with each pad number (e.g., Pad 1 = Eb, Pad 2 = F, Pad 3 = G,Pad 4 = Ab, etc.).Scale The 16 pads are mapped to an E major scale from E to F#/Gb, ascending a scale9 Edegree with each pad number (e.g., Pad 1 = E, Pad 2 = F#, Pad 3 = G#, Pad 4 = A,etc.).Scale The 16 pads are mapped to an F major scale from F to G, ascending a scale10 Fdegree with each pad number (e.g., Pad 1 = F, Pad 2 = G, Pad 3 = A, Pad 4 = Bb,etc.).11 F# / Gb Scale The 16 pads are mapped to an F#/Gb major scale from F#/Gb to G#/Ab, ascending ascale degree with each pad number (e.g., Pad 1 = F#, Pad 2 = G#, Pad 3 = A#,Pad 4 = B, etc.).Scale The 16 pads are mapped to a G major scale from G to A, ascending a scale degree12 Gwith each pad number (e.g., Pad 1 = G, Pad 2 = A, Pad 3 = B, Pad 4 = C, etc.)13 G# / Ab Scale The 16 pads are mapped to a G#/Ab major scale from G#/Ab to A#/Bb, ascending ascale degree with each pad number (e.g., Pad 1 = Ab, Pad 2 = Bb, Pad 3 = C,Pad 4 = Db, etc.)Scale The 16 pads are mapped to an A major scale from A to B, ascending a scale degree 14 Awith each pad number (e.g., Pad 1 = A, Pad 2 = B, Pad 3 = C#, Pad 4 = D, etc.)15 A# / Bb Scale The 16 pads are mapped to an A#/Bb major scale from A#/Bb to B#/C, ascending ascale degree with each pad number (e.g., Pad 1 = Bb, Pad 2 = C, Pad 3 = D,Pad 4 = Eb, etc.)16 BScale The 16 pads are mapped to a B major scale from B to C#/Db, ascending a scaledegree with each pad number (e.g., Pad 1 = B, Pad 2 = C#, Pad 3 = D#, Pad 4 = E,etc.)Number of presets:16MIDI output channels over USB: 16pressure-sensitive)and(velocity-Drum pads: 16Drum pad banks: 3Faders: 1Switches: 1Inputs/outputs: 1 USB portPower:< 100mA, 5V DC via USBDimensions (W x D x H): 255mm x 205mm x 42mmWeight: 0.8 kgManufacturer: Akai Professional Model: MPD18 Version: 1.0 Date: 2009.04.02Transmit/Export Recognize/Import Remarks1. Basic InformationMIDI channels 16 n/a Editor only Note numbers 000-127 n/aProgram change 000-127 n/a Editor only Bank Select response? (Yes/No)If yes, list banks utilized in remarks columnNoModes supported: Mode 1: Omni-On, Poly (Yes/No)Mode 2: Omni-On, Mono (Yes/No)Mode 3: Omni-Off, Poly (Yes/No)Mode 4: Omni-Off, Mono (Yes/No)Multi Mode (Yes/No)n/a n/aNote-On Velocity (Yes/No) Y n/aNote-Off Velocity (Yes/No) N n/aChannel Aftertouch (Yes/No) Y n/aPoly (Key) Aftertouch (Yes/No) Y n/aPitch Bend (Yes/No) N n/aActive Sensing (Yes/No) N n/aSystem Reset (Yes/No) N n/aTune Request (Yes/No) N n/aUniversal System Exclusive:Sample Dump Standard (Yes/No)Device Inquiry (Yes/No)File Dump (Yes/No)MIDI Tuning (Yes/No)Master Volume (Yes/No)Master Balance (Yes/No)Notation Information (Yes/No)Turn GM1 System On (Yes/No)Turn GM2 System On (Yes/No)Turn GM System Off (Yes/No)DLS-1 (Yes/No)File Reference (Yes/No)Controller Destination (Yes/No)Key-based Instrument Ctrl (Yes/No) Master Fine/Coarse Tune (Yes/No) Other Universal System Exclusive Yes Yes EditoronlyManufacturer or Non-Commercial System Exclusive N NNRPNs (Yes/No) N NRPN 00 (Pitch Bend Sensitivity) (Yes/No)RPN 01 (Channel Fine Tune) (Yes/No)RPN 02 (Channel Coarse Tune) (Yes/No)RPN 03 (Tuning Program Select) (Yes/No)RPN 04 (Tuning Bank Select) (Yes/No)RPN 05 (Modulation Depth Range) (Yes/No)N N2. MIDI Timing and SynchronizationMIDI Clock (Yes/No) N NSong Position Pointer (Yes/No) N NSong Select (Yes/No) N NStart (Yes/No)Continue (Yes/No)Stop (Yes/No)N N MIDI Time Code (Yes/No) N NMIDI Machine Control (Yes/No) N NMIDI Show Control (Yes/No)If yes, MSC Level supportedN N 3. Extensions CompatibilityGeneral MIDI compatible? (Level(s)/No)Is GM default power-up mode? (Level/No)N N DLS compatible? (Levels(s)/No)(DLS File Type(s)/No)N N Standard MIDI Files (Type(s)/No) N NXMF Files (Type(s)/No) N NSP-MIDI compatible? (Yes/No) Y Y。
Royal Mail Despatch Manager Online Printer Install
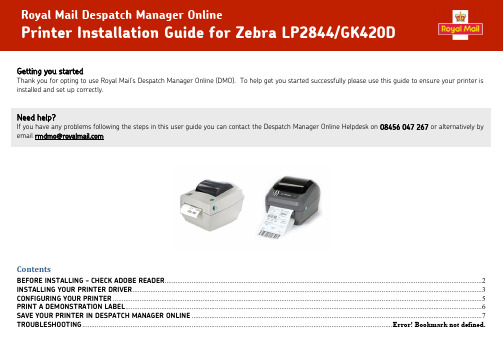
Getting you startedThank you for opting to use Royal Mail’s Despatch Manager Online (DMO). To help get you started successfully please use this guide to ensure your printer is installed and set up correctly.ContentsBEFORE INSTALLING – CHECK ADOBE READER .................................................................................................................................................................................2 INSTALLING YOUR PRINTER DRIVER ...................................................................................................................................................................................................3 CONFIGURING YOUR PRINTER ..............................................................................................................................................................................................................5 PRINT A DEMONSTRATION LABEL . (6)SAVE YOUR PRINTER IN DESPATCH MANAGER ONLINE..................................................................................................................................................................7 TROUBLESHOOTING ............................................................................................................................................................................. E rror! Bookmark not defined.ROYAL MAIL DESPATCH MANAGER ONLINE PRINTER INSTALLATION GUIDE FOR ZEBRA LP2844/GK420DBEFORE INSTALLING – CHECK ADOBE READERBefore installing your printer please check you have Adobe Reader version 11.0.00 or later.You can check this by selecting the following options - Control Panel > Progams > Programs and FeaturesYou will now be presented with the Window below.This window shows a list of programs installed on your computer. You will normally see Adobe Reader towards the top of the list.If you do not see Adobe Reader in this window, you will need to install the program from /uk/If you do not have the correct version of Adobe Reader, you will need to uninstall the program and then install the correct version from /uk/In this instance you can see that Adobe Reader 11.0.00 is installed.ROYAL MAIL DESPATCH MANAGER ONLINE PRINTER INSTALLATION GUIDE FOR ZEBRA LP2844/GK420DUsing DMO in FirefoxIf you opt to use DMO through Firefox, you will need to make a change to your internet options to enable Adobe Reader as the PDF viewer. If you do not do this, you may experience issues with your labels scanning.Click on the 3 horizontal lines in thetop right hand corner of Firefox andthen select ‘Options’Select ‘Applications’ and look for ‘Portable Document Format (PDF)’ on the lefthand side. Directly to the right of that it will say ‘Preview in Firefox’. In thedrop down box select ‘Use Adobe Reader (default)’ and press OKROYAL MAIL DESPATCH MANAGER ONLINE PRINTER INSTALLATION GUIDE FOR ZEBRA LP2844/GK420DINSTALLING YOUR PRINTER DRIVERTo begin, turn on your computer and ensure the printer is NOT connected. Once the computer has finished ‘Start Up’, co nnect the printer and turn the printer on using the switch at the back. Your computer should install the appropriate drivers for your printer automatically, if this does not happen try re-starting the computer.If your computer has not installed the drivers automatically you will need to download the drivers. For LP2844 click /gb/en/support-downloads/desktop/lp-2844.html#mainpartabscontainer_40af=drivers and for GK420D click /gb/en/support-downloads/desktop/gk420d.html#mainpartabscontainer_ce8a=drivers - Then click on ‘Download’ as shown below.Click ‘Download’.PORTOnce the driver has downloaded, follow the on screeninstructions to install the printer . During the installation setup you may be asked to choose a port, please ensure you select ‘USB001’. The image to the left shows this particular step.ROYAL MAIL DESPATCH MANAGER ONLINE PRINTER INSTALLATION GUIDE FOR ZEBRA LP2844/GK420DCONFIGURING YOUR PRINTERNext you will need to configure the printer for use with DMO by applying various changes to its Printing Preferences. To get to this section you will need to find the printer on the computer. On Windows XP it is found under Printers and Faxes and on Windows 7 or 8 it is found under Devices and Printers . Once you have found the printer please follow the steps below.STEP 1 STEP 2 STEP 3and click Printing Preferences .IMPORTANT This will ensure that the 2D barcode on yourLabel can be scanned for Delivery Confirmation.Click on the Dithering tab and select None .You will now be on the Options tab. Changethe paper f ormat to ‘inches’ and the size to6” x 4”ROYAL MAIL DESPATCH MANAGER ONLINE PRINTER INSTALLATION GUIDE FOR ZEBRA LP2844/GK420DPRINT A DEMONSTRATION LABELNext you will need to print a demonstration (test) label from Despatch Manager Online. From here there will be additional preferences to set.Please follow the steps below.STEP 1STEP 2STEP 3Open Internet Explorer and go to A message may appear at the top of the broswer statingthat Pop-Ups have been block, please ensure you allowPop-Ups for this site, Please also ensure there is a greencheck light against the Plug-In for Adobe Acrobat (Reader).Then click on the button.A label should appear, right click on the labeland select Print.Ensure you have correct printer chosen.Then select Shrink oversized pages andPortrait.There shouldn’t be any other changesneeded but double check that your windowlooks the same as the one on this step andthen click Print.ROYAL MAIL DESPATCH MANAGER ONLINE PRINTER INSTALLATION GUIDE FOR ZEBRA LP2844/GK420DSAVE YOUR PRINTER IN DESPATCH MANAGER ONLINEOnce you have successfully printed a label, you should save the printer in Despatch Manager Online. This will reduce the time it takes to print a label. You will first need to log into Despatch Manager Online ( ) and then follow the steps below.STEP 1 STEP 2 STEP 3Hover your mouse over the tab and click Printer Settings . Select Print Labels Immediately (circled on the diagram), select Specify another printer and click Select .(circled on the diagram).A message may appear in front of the Window below stating ‘Cannot Save Form information’. On this Window tick Don’t show this again and click the Close button. If you only see the Window below then ignore that instruction and select the Zebra printer and then click Submit Printer Selection .The above message will now appear, click YesSTEP 4You should now be back at Printer Settings.To finish saving your printer clickROYAL MAIL DESPATCH MANAGER ONLINE PRINTER INSTALLATION GUIDE FOR ZEBRA LP2844/GK420D。
configure for iMessage services
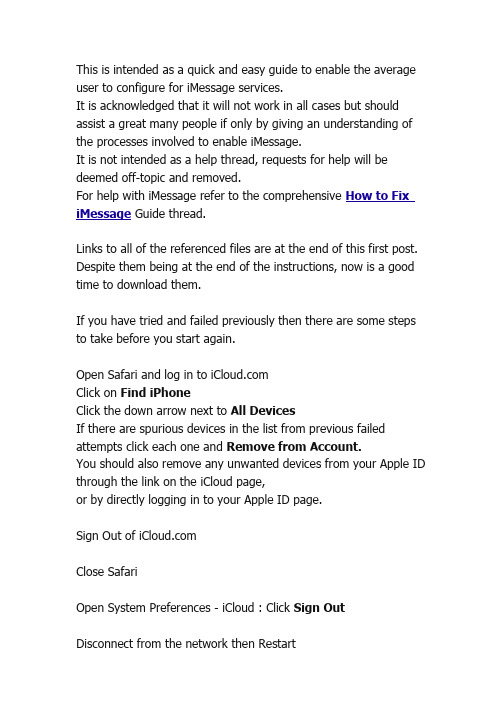
This is intended as a quick and easy guide to enable the average user to configure for iMessage services.It is acknowledged that it will not work in all cases but should assist a great many people if only by giving an understanding of the processes involved to enable iMessage.It is not intended as a help thread, requests for help will be deemed off-topic and removed.For help with iMessage refer to the comprehensive How to Fix iMessage Guide thread.Links to all of the referenced files are at the end of this first post. Despite them being at the end of the instructions, now is a good time to download them.If you have tried and failed previously then there are some steps to take before you start again.Open Safari and log in to Click on Find iPhoneClick the down arrow next to All DevicesIf there are spurious devices in the list from previous failed attempts click each one and Remove from Account.You should also remove any unwanted devices from your Apple ID through the link on the iCloud page,or by directly logging in to your Apple ID page.Sign Out of Close SafariOpen System Preferences - iCloud : Click Sign OutDisconnect from the network then RestartOpen a Finder window and click on your User Name then in a blank area right click and selectShow View Options and from the resulting window select Show Library Folder.Open the newly revealed Library folder and select CachesFrom the Caches folder delete all files and folders beginning with :◦com.apple.iCloudHelper◦com.apple.imfoundation.IMRemoteURLConnectionAgent◦com.apple.MessageIn Finder navigate to Username/Library/Preferences and delete all files and folders beginning with◦com.apple.iChat.◦com.apple.icloud.◦com.apple.ids.service◦com.apple.imagent.◦com.apple.imessage.◦com.apple.imservice.Empty the Trash and Restart.****************************************************** ********************Start hereIt has been said that you must have a credit card registered with your AppleID in order to use iMessage,I can neither confirm or deny this as I have never tried it without.You must have a working Ethernet connection which is defined as BuiltIn and en0.An easy way to determine this is with the DPCIManager app.It is possible to connect with a Wireless adaptor but you must have working Ethernet which is BuiltIn and en0 too.This is the most basic fundamental and the one that is overlooked most by laptop users although it is equally valid for desktop users too.The exception to this is when you have a machine that does not have Ethernet, in this case it is acceptable (with the appropriate SMBIOS) to have the Wireless adaptor as en0 but it must be identified as BuiltIn too.The next requirement is a correctly configured SMBIOS.In the interests of simplicity the examples shown will use the CloverConfigurator app but it should be noted that this is not the only (or best) way to achieve the required result.What is certain is that you should never edit your config.plist file with a text editor as this can corrupt the formatting. A corrupt config.plist is the same as having no config.plist at all.You should already have determined the optimum System Definition for your hardware.If you subsequently change your System Definition you must run through the procedure detailed in this guide again.Before starting to configure for iMessage you should ensure that your config.plist is otherwise correctly set up for your specific hardware.The following examples refer only to changes required to your existing config.plist.It is not suggested that anything not shown in the examples should be removed from your own config.plist unless specifically mentioned.If you haven't already, install CloverConfigurator to your/Applications folder.From the /Applications folder run Clover Configurator Mount the EFI partitionFile - Open - EFI/CLOVER/config.plistIn the left pane select Rt VariablesFrom the ROM dropdown list select UseMacAddr0 Make sure that the MLB box is emptySet BooterConfig to 0x28Set CsrActiveConfig to 0x67In the left pane select SMBIOSClick the Magic Wand toolClick on the picture appropriate for your intended System Definition.From the dropdown list, choose the desired System Definition. Click the shake buttons several times to generate a Serial Number - Click OK.Copy the Serial Number and check it on/ultimate-mac-lookup/ Paste the Serial Number into the box and click Lookup Prove that you are not a robotIf you see this response your serial number is invalid - Go back to the magic wand and generate another one.If you see a response similar to this it means that you have generated a serial number in a recognisable format and it is ok to proceed to the next stage.Open the https:// site and paste your Serial Number into the boxEnter the required code and click ContinueThis is the part of the process which confuses people the most so pay particular attention :If you see the message "Your Service and Support Coverage" and a picture of a computerthen you have generated the Serial Number of a computer that is already recorded in Apple's database.Do not use this Serial Number - Go back to the Magic Wand tool and generate a new one.If you see the message "We're sorry, but this serial number is not valid. Please check your information and try again" andthe Serial Number has passed verification at then it is OK to use this Serial Number for your config.plist.This is so important that it is worth repeating :You need a Serial Number that confirms is in the correct format and that Apple says is not valid.It does not mean that it is not a valid Serial Number - It means that it is not already registered.Quit SafariOpen a Terminal window and type uuidgen (and press Return) several times to generate some random UUIDs.Copy one of your random UUID numbers from the Terminal window and paste it into the SmUUID box in Clover Configurator.In Clover Configurator select File - SaveQuit Clover Configurator.RestartFrom your /Applications folder run Clover Configurator,Mount the EFI partition.Select File - Open - EFI/CLOVER/config.plistOnce your config.plist file has loaded into Clover Configurator : Open a Terminal windowOpen a Finder window and browse to the location where you downloaded simpleMLB.shDrag simpleMLB.sh from Finder onto the Terminal window, click inside the Terminal window and press ReturnCopy the generated number then paste it into Clover Configurator - SMBIOS - Board Serial Number.In Clover Configurator select File - SaveQuit Clover Configurator and Terminal.RestartOpen a Finder window, browse to the location where you downloaded iMessageDebug and run it.Press y and Return to save a copy called iMessageDebug.txt. RestartOpen a Finder window and browse to the location where you downloaded iMessageDebug and run it.Compare the output with the saved copy.If the two copies are the same you may reconnect to the network and proceed to set up iMessage.The last line in the output of iMessageDebug is subject to change but does not appear to be a cause for concern.If you follow the guide and get a failed ROM in iMessageDebug you may need to install EmuVariableUefi-64 and RC Scripts with the Clover installer. This seems to particularly apply to those with 100 series motherboards.****************************************************** ********************The examples shown are for the Clover boot loader that has been installed in UEFI mode.If you have installed Clover in Legacy mode then the procedure is the same except that your config.plistis located in the /EFI/CLOVER folder on your System disk.For brevity the guide is for users of El Capitan as this is the operating system that most people will be using at the time of writing.If you use a different version of the operating system then you should adapt these instructions to your own requirements.This is not intended as a help thread, requests for help will be deemed off-topic and removed.For help with iMessage refer to the comprehensive How to Fix iMessage Guide thread.Clover Configurator- iMessageDebugv2- simpleMLB- DPCIManager。
Origin Effects DELUXE61 用户手册说明书
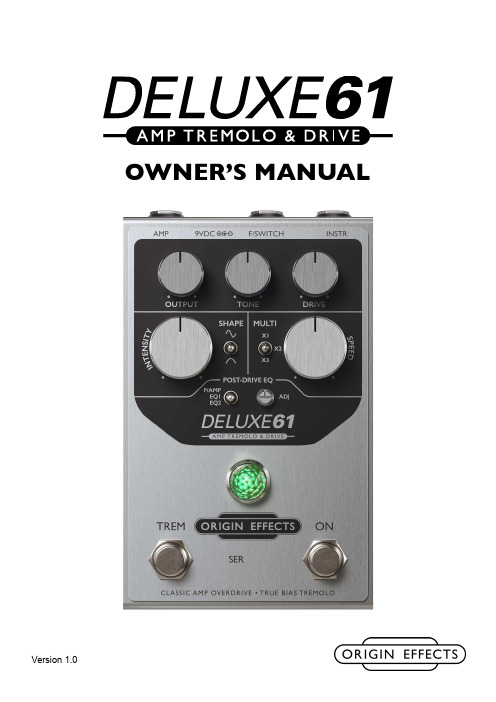
OWNER’S MANUALVersion 1.0ORIGIN EFFECTS® is a registered trademark of Origin Effects Limited.All other product names and trademarks are the propertyof their respective owners and are hereby acknowledged.MARSHALL® is a registered trademark of Marshall Amplification PLC.Origin Effects has no affiliation with Marshall Amplification PLC.BOSS® is a registered trademark of the Roland Corporation.Origin Effects has no affiliation with the Roland Corporation.FENDER® is a registered trademark of Fender Musical Instruments Corporation.Origin Effects has no affiliation with Fender Musical Instruments Corporation.No part of this publication may be reproduced in any form or by any means,whether mechanical or electronic,without the written permission of Origin Effects Limited. Origin Effects Limited reserves the right to change the features and specifications described herein without notice or obligation.Origin Effects Limited cannot be held responsible for any loss or damage arising directly or indirectly from any error or omission in this manual.PLEASE READ ALL INSTRUCTIONS,PAY ATTENTION TO SAFETY WARNINGS.Document version 1.0© Origin Effects Limited 2021IMPORTANT:This product is designed to be powered from a 9VDC, >100mApower supply with 2.1mm centre-negative barrel connector.ContentsIntroducing the DELUXE61 4 Connecting the DELUXE61 5 Main Controls: 6 POST-DRIVE EQ Controls 7 Setting Your POST-DRIVE EQ 8 Sample Settings 9 Appendix A: Physical Specification 10 Appendix B: Performance Specification 10 Appendix C: Connector Pin Out 10 Appendix D: Safety Notices11 Appendix E: Warranty 12Introducing the DELUXE61The DELUXE61 is an all-analogue amp recreation which captures the thick overdrive tones and beautiful bias tremolo of the revered Fender® Brown Deluxe amp. We have gone to great lengths to recreate every detail of this iconic amplifier, bringing you the tones, feel and response of this classic combo in one industrial-grade pedal.First released in 1961, this modest, little amp is still one of history’s most sought-after guitar tones, thanks largely to its tremolo circuit. Bias tremolo is considered by many to be the most musical of all the tremolo types due to its natural, pulsating character. Because the tremolo acts on the amp’s output valves, overdriven sounds will let you “play through” the tremolo. The effect disappears when you pick hard, slowly fading back in as the note dies away – you can control the tremolo effect with your picking dynamics or your guitar’s volume knob! The DELUXE61’s circuit includes an entire push-pull output stage, complete with an output transformer and reactive load, which means this pedal’s tremolo is every bit as responsive as the real thing – but with the added versatility of tap tempo and a speed multiplier switch.With our powerful Post-Drive EQ, the warm cleans and gritty overdrive of the DELUXE61 will always sound their best, whether it’s plugged into an amp, a flat power amp or direct to a recording interface or PA. Key Features:All-Analogue Amp Recreation Including:• Rich clean tones and growly overdrive voiced after the 1961 Fender® Brown Deluxe• True bias tremolo with authentic, touch-sensitive dynamic response• Complete valve amp-style signal pathusing discrete, transistor-based circuitry Flexible, Intuitive Controls:• Footswitch input jack for tap tempo and effects swither integration• Powerful tone-shaping POST-DRIVE EQ Peerless Build Quality:• High-current, low-noise electronics • Ultra-high input impedance• High-quality buffered bypass• Advanced power supply filtering and protection• Premium components throughout • Designed and built in EnglandConnecting the DELUXE61Main ControlsON (footswitch):independently.DRIVE:TONE:-cies above the 12 o’clock poisition and cut highs below 12 o’clock. With DRIVE pushed past 12 o’clock, the TONE control progressively loses the ability to boost until, with DRIVE at maximum, it’s essentially a high cut control.OUTPUT: The output control sets the pedal’s overall output level. This control comes after the pedal’s simulated valve amp circuitry, meaning that you can adjust output level without affecting the tone or character of the overdrive.SPEED: Turn clockwise to increase the rate of the tremolo effect. The range of the SPEED control is set by the three-position MULTI switch.INTENSITY: The INTENSITY knob controls the depth of the tremolo – in other words, how much the tremolo will vary the amplitude of the signal. Turn clockwise to increase the depth of the effect.Main Controls (continued)MUL TI: The MULTI switch multiplies the tremolo speed set by the SPEED knob (x1, x2 or x3). This is par-ticularly useful when using an external tap tempo footswitch, letting you set tremolo speeds much faster than your foot can tap.SHAPE: The SHAPE switch allows you to choose between two different LFO waveforms.SINE WAVE (up) – This is the classic bias tremolo sound – ultra-smooth, rounded and musical.FULL WAVE (down) – This setting uses an asymmetrical waveform with a ‘choppier’ feel. Thismore obvious tremolo sound can be useful at slower speeds or when playing with more overdriven sounds.POST-DRIVE EQ ControlsThe POST-DRIVE EQ ensures compatibility with a wide range of amplifiers. Instead of altering your amp or its tone controls to suit the DELUXE61, set your amp for the desired clean sound then use the EQ controls to tailor the pedal’s output accordingly.POST-DRIVE EQ switch: This switch offers a choice of three different output filters.P/AMP: Use this setting when plugging into a flat-response power amp, mixer or recording interface. Select-ing the P/AMP setting disengages the ADJ variable filter control (see below).EQ1: Designed to suit the response of a Black Panel Fender®-style amp, EQ1 applies a low-pass filter to roll off excessive highs. Use this setting when plugging into a bright-voiced guitar amp.EQ2: Voiced for connecting to a Marshall®-style amp, EQ2 applies a high shelf cut to gently rein in high fre-quencies. Use this setting when plugging into a fuller-sounding, mid-rich amp.POST-DRIVE EQ Controls (continued)ADJ: When EQ1 or EQ2 is selected, the ADJ knob lets you fine-tune the pedal’s output to suit the individ-ual response of your amp and the way its controls are set. As you turn the ADJ knob counterclockwise, this proprietary filter design gradually rolls off bass and adjusts the high shelf response. The end result is a very powerful and intuitive control. If your amp sounds too bright or thin with the DELUXE61 engaged, turn the ADJ control clockwise. If it sounds too dark and wooly, turn the ADJ control counterclockwise. Setting Y our POST-DRIVE EQUse the tables below to help you set up the DELUXE61 for the first time with a new guitar amplifier orflat-response device. Working through Steps 1 and 2 allows you to “set-and-forget” the POST-DRIVE EQ controls and move on to having fun dialling in your ideal tone with the main controls.Step 1: Set POST-DRIVE EQ switch for the connected amp or device.Step 2: Fine-tune the POST-DRIVE EQ with the ADJ control**Please note: the ADJ control is not active when the POST-DRIVE EQ switch is in the P/AMP position.Sample SettingsAppendix A: Physical SpecificationAppendix B: Performance SpecificationAppendix C: Connector Pin Out Footswitch 1/4” TRS socket:Instrument & Amplifier 1/4” TS Sockets:Appendix D: Safety NoticesGeneral SafetyKeep these instructions and heed all warnings. Do not use this apparatus near water. Clean only witha dry cloth. Do not install near any heat sources such as radiators, heat registers, stoves or other apparatus (including amplifiers) that produce heat. Refer all servicing to qualified service personnel. When using an external power supply, use only attachments/accessories specified by Origin Effects. Protect the power cord from being walked on or pinched particularly at plugs, convenience receptacles, and the point where they exit from the apparatus. Do not defeat the safety purpose of the polarised or grounding-type plug. A polarised plug has two blades with one wider than the other. A grounding type plug has two blades and a third grounding prong. The wide blade or the third prong are provided for your safety. If the provided plug does not fit into your outlet, consult an electrician for replacement of the obsolete outlet. Unplug this apparatus during lightning storms or when unused for long periods of time.CAUTION! No user-servicable parts inside. In the event of damage to the unit service orrepair must be done by qualified service personnel only.This Product is CE compliant.This product is UKCA compliant.FCC CertificationThis equipment has been tested and found to comply with the limits for a Class B digital device, pursuant to part 15 of the FCC Rules. These limits are designed to provide reasonable protection against harmful interference in a residential installation. This equipment generates, uses and can radiate radio frequency energy and, if not installed and used in accordance with the instructions, may cause harmful interference to radio communications. However, there is no guarantee that interference will not occur in a particular installation. If this equipment does cause harmful interference to radio or television reception, whichcan be determined by turning the equipment off and on, the user is encouraged to try to correct the interference by one or more of the following measures:• Reorient or relocate the receiving antenna.• Increase the separation between the equipment and receiver.• Connect the equipment into an outlet on a circuit different from that to which the receiver is connected.• Consult the dealer or an experienced radio/TV technician for help.Appendix D: Safety Notices (continued)The crossed out wheely bin symbol indicates this product is classified as Waste Electricaland Electronic Equipment (WEEE) in the European Union and should not be discardedwith household waste. Other territories may vary. Contact your local authority or OriginEffects for more information.This product conforms to the European Union’s directive 2011/EU on Restrictions ofHazardous Substances (RoHS).WARNING: This product can expose you to chemicals including nickel, which is known to the State of California to cause cancer. For more information, go to Evaluation of apparatus based on altitude not exceeding 2000m. There may be some potential safety hazard if the apparatus is operated at altitude exceeding 2000m. Evaluation of apparatus based on temperate climate conditions only. There may be some potential safety hazard if the apparatus is operated in tropical climate conditions.Appendix E: WarrantyThis product is covered by a 2-year manufacturer’s warranty from the date of purchase. This applies only to original purchasers who have bought their product from an authorised Origin Effects dealer or directly from Origin Effects.All returns or servicing should be arranged through the original dealer. Proof of original ownership may be required in the form of a purchase receipt.For full warranty details visit /warranty .RoHS。
Hubport 2.0 自电 USB 集线器用户手册说明书

Hubport Installation GuideIntroductionThank you for purchasing the Hubport ™, a self-powered Universal Serial Bus (USB) hub designed to provide a convenient and effective means of bringing USB connectivity to your PC, server, or laptop. The Hubport also delivers the potential of Inside Out Network’s flagship product — the Edgeport ™ USB to Serial (RS-232) expansion module.Hubs, critical components in the plug-and-play architecture, are wiring concentrators that enable the attachment of multiple devices, thus converting a single attachment point into multiple attachment points. USB architecture allows a cascaded multiple hub configuration with certain power limitations (explained later in this section). See figure 1.Each hub has an upstream port, connecting to the host, and multiple downstream ports, connecting to downstream devices,including other hubs. A hub can detect attachment and detachment of downstream devices and enable and monitor the distribution of the power to downstream devices via their integral hardware and the operating system.Each USB device reports its power requirements to the operating system, which then enables and disables the device as a function of its power requirements and the amount of available power. High-speed devices typically need to be connected to a self-powered hub, such as the Hubport, which obtains power from its external power supply and provides up to 500 mA for each downstream port. Only simple devices, such as a mouse, can be connected to a bus-powered hub, which obtains power from its upstream host and provides up to 100 mA for each downstream port.Due to the limited available power for bus-powered hubs, cascading two bus-powered hubs is an illegal topology, and devices connected to the second hub will not function. (USB specifications limit the connection of a bus-powered hub to a self-powered hub or host only.) Since the Hubport is a self-powered hub, it is not affected by this limitation.Verifying Correct Installation of USBSupportIf you are using Windows 98, which fully supports USB, you may proceed to “Installing Hubport.” If you are using Windows 95 OSR2.1 or above,please continue with the section below.Checking for Full USB Support in the Device Manager1)From the main desktop area of Windows, right click on the My Computer icon and choose Properties to open the System Properties window.2)Click once on the Device Manager tab to view a listing of installed hardware devices.Figure 1: Example of a Typical Hub ConfigurationPCHOST HubportHubportEdgeportEdgeportEdgeportscannerbus-powered hubjoystick mouseFigure 2: Example of the USB Devices Listed in theDevice Manager Tab3)In the Device Manager tab, your hardware devices are in alphabetical order and should include a Universal serialbus controller toward the bottom of the list. Double click on this device to open it.In order for the Hubport and other USB devices to work properly at least two devices are required and will be listed. Although the exact name of each manufacturer’s device listing can vary, the names of these two required USB devices should include the following descriptive words:•USB Root Hub•USB Host ControllerFigure 2 shows an example of what you might see listed under the Universal serial bus controller. If you do not see one or both of these devices, go to “Determining Why Support Is Not Present.”Installing HubportPlugging Hubport Into Your PCPlug in the power supply. Plug the flat end of the UBS cable into the downstream A connector located in the back of your computer or USB hub port. Plug the D-shaped end into the Hubport.If previously installed, the Hubport will be listed in the System Device Manager and is ready for immediate use. With the initial installation, the Update Device Driver Wizard automatically appears and you may continue with “Installing the Drivers” below. If the Update Device Driver Wizard does not appear, go to the preceeding section, “Verifying Correct Installation of USB Support.”Installing the DriversTo install your Hubport drivers:1Click on NEXT to initiate a search for the updated driver device.2)Click on FINISH to continue with the installation.You have now successfully installed your Hubport!Determining Why Support Is Not PresentTo verify that the necessary hardware, a USB Host Controller, is installed in your system, make sure that your PC has USB connectors. If not, then this system will not support USB regardless of the Windows version. You will need to purchase a PCI USB controller card, such as the Step Up Kit™ from Inside Out Networks. If your PC has USB connectors, verify that the USB hardware is enabled in your system BIOS configuration.In some cases your manufacturer may have elected to ship your PC without the USB support drivers installed. If the two USB device manager hardware listings are absent in your Device Manager, proceed to the next section, “Installing Microsoft USB Support.”After installing USB Support from your Microsoft Windows 95 OEM system disk, check your Device Manager again. If the two devices are not present or Windows Plug & Play does not auto detect the Hubport, try the following:1)If only the HOST Controller is listed in the Device Manager then remove it and reboot.2)From the Control Panel, open the System Properties and select “Check for a device labeled ?UNKNOWN.” IfROOT HUB and HOST Controller are listed, then remove them and reboot.If, after rebooting, the Add Hardware Wizard finds the USB devices and requires new drivers, such as UHCD.SYS, you can locate the drivers in the C:\WINDOWS\SYSTEM directory. If, after following the proceedures decribed in this guide, you still cannot install you Hubport, please call (512)301-7080 and ask for Technical Support.Installing Microsoft USB SupportMicrosoft provides a supplemental program (usbsupp.exe) to allow users to upgrade Windows 95 version OSR2 to support the Universal Serial Bus. In order to install this support perform the following steps:1)Insert your Microsoft Windows 95 OEM system disk into your CD drive.2)In the START menu, select RUN.3)Type <CD drive letter>:\other\usb\usbsupp.Follow the instructions on the screen.After rebooting, continue with the “Installing Hubport” section.Note that Windows 95 version 4.0.950 and 4.0.950a do not support the upgrade path to USB. Unfortunately, Microsoft has not provided an upgrade path to OSR2 from earlier versions of Windows. OSR2 must be preinstalled by your PC vendor. Contact your PC vendor for more information.Copyright © 1998 by Inside Out Networks. All rights reserved.Version 2.0 November 1998Hubport, Edgeport, and Step-Up Kit are trademarks of Inside Out Networks. All other products are trademarks or registered trademarks of their respective owners. Information in this documentation is subject to change without notice and does not represent a commitment on the part of Inside Out Networks Inc.Inside Out Networks provides this document “as is,” without warranty of any kind, either expressed or implied, including, but not limited to, the particular purpose. Inside Out Networks may make improvements and/or changes to this documentation or to the product(s) and/or program(s) described in this documentation at any time.Inside Out Networks assumes no responsibility of any errors, technical inaccuracies, or typographical errors that may appear in this documentation, nor liability for any damages arising out of its use. Changes are made periodically to the information herein; these changes may be incorporated in new editions of the publication.For U.S. Government use:Any provision of this document and associated computer programs to the U.S. Government is with “Restricted Rights.” Use, duplication, or disclosure by the gov-ernment is subject to the restrictions set forth in, subparagraph (c) (1) (ii) of the Rights in Technical Data and Computer Software clause of DFARS 52.277-7013.For non-U.S. Government use:These programs are supplied under a license. They may be used, disclosed, and/ or copied only as supplied under such license agreement. Any copy must contain the above copyright notice and restricted rights notice. Use, copying, and/or disclosure of the programs is strictly prohibited unless otherwise provided for in the license agreement.Federal Communications Commission (FCC)Regulatory Information (USA only)This equipment has been tested and found to comply with the limits for a Class B digital device, pursuant to Part 15 of the FCC Rules. These limits are designed to provide reasonable protection against harmful interference in a residential installa-tion. This equipment generates, uses, and can radiate radio frequency energy and, if not installed and used in accordance with the instructions, may cause harmful inter-ference to radio communications. However, there is no guarantee that interference will not occur in a particular installation. If this equipment does cause harmful inter-ference to radio or television reception, which can be determined by turning the equipment off and on, the user is encouraged to correct the interference by one or more of the following measures:±Reorient or relocate the receiving antenna.±Increase the separation between the equipment and the receiver.±Connect the equipment into an outlet that is on a circuit different from the receiver.±Consult the dealer or an experienced radio/TV technician for help.Warning: The connection of a non-shielded interface cable to this equipment will invalidate the FCC Certification for this device.Department of Communication (DOC) Notice(Canada only)This Class B digital apparatus meets the requirements of the Canadian Interfer-ence-Causing Equipment Regulations.Cet appareil numérique de la Classe B respecte toutes les exigences du Règlement sur le matériel brouiller du Canada.Declaration of Conformity (DOC)according to ISO/IEC Guide 22 and EN 45014Manufacturer’s Name:Inside Out NetworksManufacturer’s Address:8313 Highway 71 West, Suite BAustin, Texas 78735 USAdeclares that the productProduct Name:Hubport/7, Hubport/4Model Number(s):301-1010-07, 301-1010-04, 301-1011-04Product Options:Allconforms to the following Product Specifications:Safety:IEC 950:1991 +A1, A2, A3/EN 60950:1992 + A1, A2, A3UL 1950, 3rd edition, CSA No. 950EMC:FCC Title 47 CFR, Part 15 Class BFCC/CISPR 22/85 Class B (ANSI C63.4 1992)EN 55022 Class B (1994 w/A1 1995)EN 50082-1:1992 - Generic ImmunityIEC 801-2:1991/prEN 55024-2:1992 - kV CD, 8 kV ADIEC 801-3:1994/prEN 55024-3:1991 - 3V/mIEC 801-4:1988/prEN 55024-4:1992 - 0.5 kV Signal Lines,1 kV Power LinesSupplementary InformationThe Product herewith complies with the requirements of the following Direc-tives and carries the CE marking accordingly.±the EMC Directive 89/336/EEC (including 93/68/EEC)±the Low V oltage Directive 73/23/EEC (including 93/68/EEC)This device complies with Part 15 of the FCC Rules. Operation is subject to the following two conditions: (1) this device may not cause harmful interference, and (2) this device must accept any interference received, including interference that may cause undesired operation.Quality ManagerAustin, Texas April, 1998To Contact Inside Out Networks...Our Web Page is located at , where you may download drivers and get current product information.For more information on Inside Out Networks’ products, you may contact us by E-Mail at ******************* or at the address and telephone number below. For sales, you may contact us by E-mail at ********************.For technical support, you may contact us at (512) 301-7080.Inside Out Networks, 8313 Hwy. 71 West, Suite B, Austin, TX 78735 ph: (512) 301-7080 fax: (512) 301-7060。