甲醇变换催化剂应用小结
C307型甲醇合成催化剂使用总结

我厂低压合成甲醇系统是以德士古煤气为原料气,经中温变换、NHD脱硫、脱碳、精脱硫后,压缩至5.15MPa 送合成,精馏系统采用三塔精馏工艺。
该系统于2000年6月投产,合成塔规格为φ2800mm(以下简称为大塔),装填南化院研制的C306型低压甲醇催化剂。
该炉催化剂一直运行至2003年7月,实际运行时间为1021 d,生产精甲醇297252t,优等品率为91%。
2003年10月,该系统进行了扩产改造,新增1台φ1800mm同类型合成塔(以下简称为小塔),双塔并联运行,装填南化院新开发的C307型低压甲醇催化剂,至2004年12月,共生产精甲醇197569.7t。
目前使用的是第三炉催化剂,依然采用南化院 C307型低压甲醇催化剂。
1 C307型甲醇合成催化剂的性能及装填(1)物化性能C307型甲醇合成催化剂外观为两端球面的黑色圆柱体,规格为φ5mm×4~5 mm,堆密度为 1.587 kg /L,比表面积90~110m2/g,平均径向抗压碎力≥185 N/cm。
其成分主要由铜、锌、铝等的氧化物组成,其中CuO 55%~60%、ZnO 35%~45%、Al2O3 8%~10%,另外还含有少量石墨和水。
(2)催化剂装填第三炉催化剂装填情况如下。
①大塔:下部封头装φ25mm、φ10mm耐火铝球共9.025t;装填C307型催化剂35.25t,装填体积21.197 m3,其中绝热层高度170 mm,C307型催化剂装填体积为1.046m3。
②小塔:下部封头装φ25mm、φ11 mm耐火铝球共5.45 t;装填C307型催化剂12.70t,装填体积8.107m3,其中绝热层高度170mm,C307型催化剂装填体积为0.432m3。
2 催化剂升温还原情况(1)本次2台合成塔的升温还原同时进行,为使整个升温还原工作顺利进行,在总结前2炉催化剂升温还原经验基础上,制定了详细的升温还原方案(表1),同时对还原气提出了具体要求:O2<0.2%,S<0.1mg /m3(标态),NH3<10×10-6,CO2<1%。
C207型甲醇合成催化剂使用小结

免引起系统压差及塔温波动。轻负荷生产 2d 后
维普资讯
第 4期 20 0 6年 7月
中 氮
肥
No. 4
M - ie to e o sFetl e r g es S zd Ni g n u riz rP o rs r i
J1 0 6 u .2 0
1 问题 提 出
全运行 ,给水溶解氧含量过高 , 引起热力设备 会 的管道 、省煤器、锅炉炉管、热交换器 等腐蚀 , 降低设 备 的使用 寿命 。如果 给水 中溶解 氧超过 0 0 / ,给水 管道 和 省煤 器 会 在 短 时期 内 出 .3mg L 现点状 腐 蚀 穿 孑 。 我公 司 锅 炉 给 水 于 2 0 L 0 1年 4 月开始出现溶解氧严重超标 ,最高达 3 2 / , 5 L 最低为 6, / ,合格 率仅 1 %,成为威 胁锅炉 u L g 2 稳 定运 行 的隐患 。
年 5月 投 人 生 产 ,20 0 5年 1月退 出 ,更 换 新 一
()当合成塔热点温度在 10℃以上时 ,要 3 0 定期 检 测 系统 中 的 C 2 量 ( 酸 盐 相 的分 0 含 碳 解) ,高于 25 .%时 ,要在保持 系统 压力平稳 的
前 提下 进行 放空 置换 。
( )还原过 程 中要遵 循 提温 不提 压 、提压 不 4
论出水量的 2 %, 0 连续 2h 不再出水 ,塔进出 口
H 含量不变时 ,视为还原结束 。 2
( )换 4 气
( )控 制 还 原 反 应 速度 ,这 是还 原 的关 键 。 1 还 原 反应 速度 的快 慢与 氢浓 度 、温度及 空 速有 密
还原结束后将热点温度降 至 20 3 ±5℃ ,按
C307型甲醇合成催化剂使用总结

精甲醇 2722t优等品率为 9 %。20 9 5 , 1 03年 1 0 月 , 系统进 行 了扩产 改造 , 该 新增 1台 180m 0 m 同类型合 成塔 ( 以下 简称 为小塔 ) 双塔并联运 , 行, 装填南化院新开发 的 C 0 37型低压 甲醇催化 剂 , 20 至 04年 l , 生 产 精 甲醇 1759 7t 2月 共 9 6 . 。 目前使用 的是第 三炉催化剂 , 然采用南化 院 依
2 催化 剂升温 还原情 况
1 C 0 甲醇合 成催 化剂 的性 能及装填 37型
() 1 物化 性能
( ) 次 2台合 成 塔 的 升 温还 原 同时 进 行 , 1本
为使整个升温还原工作顺 利进行 , 在总结前 2炉
催化 剂 升温还 原经 验 基 础上 , 定 了详 细 的 升温 制
束, 转人轻负荷期。整个还原过程历时9 , 6h有效 升温还 原时 间约 9 。在 整个 还 原过 程 中 , 0h 进展
比较 顺 利 , 化 剂 还 原 比较 彻底 , 催 累计 出 水 量 为
C 0 型 甲醇合成催化剂外观 为两端球面的 37 黑色圆柱体 , 规格为 0 m× 5m 堆密度为 5m 4— m,
15 7k/ , .8 gL 比表 面积 9 0—10m / , 1 g平均 径向抗
还原方案( 1 , 表 ) 同时对还原气提出了具体要求:
O < . %, 2 0 2 S<0 1m,m ( 态 ) N <1 . e 标 / ,H 0×
1’ 3 7m tao snh s a l t hog eueo trecagso ect yt esrsa r eC 0 e n l y tei ct y .T r ht s f he h re f h a l aue r ) p h s as u h t a sm e
甲醇催化剂工程实训报告
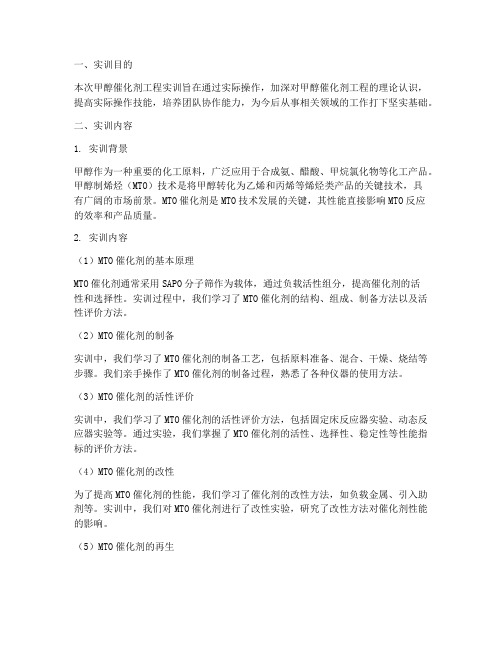
一、实训目的本次甲醇催化剂工程实训旨在通过实际操作,加深对甲醇催化剂工程的理论认识,提高实际操作技能,培养团队协作能力,为今后从事相关领域的工作打下坚实基础。
二、实训内容1. 实训背景甲醇作为一种重要的化工原料,广泛应用于合成氨、醋酸、甲烷氯化物等化工产品。
甲醇制烯烃(MTO)技术是将甲醇转化为乙烯和丙烯等烯烃类产品的关键技术,具有广阔的市场前景。
MTO催化剂是MTO技术发展的关键,其性能直接影响MTO反应的效率和产品质量。
2. 实训内容(1)MTO催化剂的基本原理MTO催化剂通常采用SAPO分子筛作为载体,通过负载活性组分,提高催化剂的活性和选择性。
实训过程中,我们学习了MTO催化剂的结构、组成、制备方法以及活性评价方法。
(2)MTO催化剂的制备实训中,我们学习了MTO催化剂的制备工艺,包括原料准备、混合、干燥、烧结等步骤。
我们亲手操作了MTO催化剂的制备过程,熟悉了各种仪器的使用方法。
(3)MTO催化剂的活性评价实训中,我们学习了MTO催化剂的活性评价方法,包括固定床反应器实验、动态反应器实验等。
通过实验,我们掌握了MTO催化剂的活性、选择性、稳定性等性能指标的评价方法。
(4)MTO催化剂的改性为了提高MTO催化剂的性能,我们学习了催化剂的改性方法,如负载金属、引入助剂等。
实训中,我们对MTO催化剂进行了改性实验,研究了改性方法对催化剂性能的影响。
(5)MTO催化剂的再生MTO催化剂在使用过程中会发生积炭、失活等现象,影响催化剂的性能。
实训中,我们学习了MTO催化剂的再生方法,如氧化、酸洗等。
三、实训过程1. 实训准备在实训前,我们查阅了大量相关文献,了解了MTO催化剂工程的基本知识。
同时,我们熟悉了实验室的仪器设备,掌握了实验操作技能。
2. 实训实施实训过程中,我们严格按照实验步骤进行操作,认真记录实验数据。
在实验过程中,我们遇到了一些问题,通过查阅资料、请教老师等方式解决了这些问题。
3. 实训总结实训结束后,我们对实验数据进行了整理和分析,总结了MTO催化剂工程实训的收获。
甲醇合成催化剂更换总结

[收稿日期]2020 04 04[作者简介]王 龙(1989—),男,河北辛集人,工程师。
甲醇合成催化剂更换总结王 龙(晋煤金石化工投资集团有限公司石家庄循环化工园区分公司,河北石家庄 050000)[摘 要]甲醇合成催化剂更换涉及钝化、卸出、装填、升温还原等一系列工作,每一阶段的操作都决定着后续工作开展的顺利与否,并直接影响着装置开车后的运行状况、消耗、产能等。
以晋煤金石化工投资集团有限公司石家庄循环化工园区分公司200kt/a甲醇合成系统2019年6—7月进行的甲醇合成催化剂更换为例,详细介绍更换过程涉及到的催化剂钝化、催化剂卸出与装填、催化剂升温还原等各环节的操作过程,总结本次甲醇合成催化剂更换各环节的操作(作业)经验,并针对存在的不足提出相应的改进建议,以利今后甲醇合成催化剂更换工作的优质、高效完成。
[关键词]甲醇合成催化剂;更换;催化剂钝化;催化剂卸出与装填;催化剂升温还原;经验总结;建议[中图分类号]TQ223 12+1 [文献标志码]B [文章编号]1004-9932(2020)06-0045-040 引 言晋煤金石化工投资集团有限公司石家庄循环化工园区分公司200kt/a甲醇项目共设2台甲醇合成气压缩机(并联运行),装置分两期建设,一期100kt/a装置于2015年3月投产,二期100kt/a装置于2017年11月投产,两期装置共用一套甲醇合成系统。
2019年6月,利用全厂年度大检修契机进行甲醇合成催化剂的更换,甲醇合成催化剂的更换涉及钝化、卸出、装填、升温还原等一系列工作,每一阶段的操作都决定着后续工作开展的顺利与否,并直接影响着装置开车后甲醇合成塔的反应效率以及系统的消耗与产能。
以下对本次甲醇合成催化剂更换各环节工作中的经验教训及有关情况作一总结。
1 甲醇合成塔及催化剂使用情况简介200kt/a甲醇合成系统采用6 4MPa低压合成工艺,甲醇合成塔采用成都通用工程技术有限公司生产的“螺旋管-直管复合串联外冷式”结构;甲醇合成塔分为上、下两段,上段为直管管壳型,下段为螺旋管管壳型,上、下段分别设立汽包,用以调节床层温度。
一甲醇装置合成催化剂(NC307)使用小结已有

甲醇装置NC307合成催化剂使用技术王会强武汉理工大学摘要:本文讲述了NC-307甲醇合成催化剂在大庆油田甲醇厂一甲醇装置的实际应用情况;阐述了NC307合成催化剂所具有的特点,总结了NC307在生产操作及管理中的使用经验,具有一定的指导意义。
主题词:甲醇装置合成反应 NC307催化剂保护周期一、合成塔简介大庆油田化工有限公司甲醇分公司一甲醇装置合成塔,采用鲁奇固定管板列管式甲醇合成反应器,年设计生产能力精醇10万吨,日产精醇333吨,日粗醇400吨。
合成塔规格:二、合成触媒装填及升温还原情况1、目前一甲醇装置使用合成的触媒型号为NC307 ,触媒生产厂家:南化院;2、NC307规格:规格:∮5.0×(4.~5)mm外观:两端为球面的黑色圆柱体堆密度:1.40-1.6kg/l比表面:90-110m2/g耐热后甲醇时空产率:≥1.0g/mL催化剂.小时3、装填时间:2007年4月12日,装填重量:34.8吨(23.2立方)。
4、触媒升温还原情况:07年4月13日完成触媒的装填工作,从4月14日22:00开始进行触媒的升温还原,18日19:30升温还原结束,还原时间累计117.5小时。
在整个还原过程中物理出水量为1.1328吨,化学出水量 3.802 吨,还原结束经72小时低负荷运转后转入正常生产,初始使用温度为控制合成塔出口温度232±1℃运行。
三、运行情况:本炉触媒自07年4月18日——09年3月25日共计运行16570小时,累计生产精醇21.26万吨,日产精醇最高产量412吨/日,目前合成塔进口温度217.63℃,出口温度249℃,预计触媒还有5个的使用时间。
1、合成塔触媒提温情况:2、触媒不同时期的相关操作数据:合成触媒初期:239-240℃工况四、NC-307催化剂的特点:在NC-307催化剂使用过程中,我们总结出该催化剂具有以下特点:一是易还原,整个还原过程易于控制。
C307型甲醇催化剂使用小结

( )温 度 。C 0 2 3 7型铜 基 催 化剂 应 严 格控 制
热 点温度 , 不得超过 2 0℃ 。在 还原过程 中 , 口 3 人
温度最 好 控 制 在 10~10℃ , 7 9 床层 温 度控 制 在 2 0℃ 。升温过程 严格控 制升温速度 ( 5o 。 1 ≤2 C) ( )空速 。C 0 3 3 7型 铜基 催 化剂 的升 温 还原
反应 为强 放热 反应 , 空速 大 , 可带 走大量 的热量 , 有效地避 免床层温 度 的升高 。为 了控制好 床层 的 温度, 空速 越大 越好 , 又受 系统 压力 的限制 , 但 还
原 过程实 际循环量 为 2 00 0~ 7 0 h 实 4 0 200 0 m / ,
2 2 还 原过程 .
C0 3 7型 甲醇 催化 剂 使 用小 结
兖矿 国泰化工 公司 甲醇生产采 用低温低 压气 固相催化技 术 , 用 C0 采 37型铜 基催 化 剂 , 催化 剂
的升温还 原将影 响 以 后 的使用 活性 及 生产 能 力 , 因此就催化 剂 的装 填 、 温还原作 如下小结 。 升 1 主要 设 备及工 艺 公 司采用 的是 双塔 并联 生 产 , 中合 成塔 为 其 0 0 13 32 9 MT, 34 0/1 ×】 8 I 催化 剂分 两层 填 装 , 1 1 I 一 L
2 4
小氮肥 第 3 6卷 第 l O期 20 1 J 08 0 】
如床温 过高 可加 大 引风 量 , 热 量后 移 。流 化 床 使 锅炉 正常燃烧 料层厚 度应 以 40~50m 为 宜。 5 0 m 不 同的料层 厚度对 应 有不 同的风 室 压力 , 控制 其
手段 可根据 风室压力情 况采取增 加给煤 量或放 渣
多类型甲醇合成催化剂应用总结

(3) 2011年 2月, 汽 包 压 力 设 置 在 25 MPa,催 化 剂 床 层 温 度 控 制 在 242~245 ℃; 2011年 5月,汽包压力设置在 23MPa,催化剂 床层温度控制在 245~250℃;2011年 8月,汽 包压力设置在 24MPa,催化剂床层温度控制在 250~260℃;2011年 11月,汽 包 压 力 设 置 在 31MPa,催化剂床层温度控制在 260~270℃; 日产精甲醇 1975t。
2012年 2月,榆林能化甲醇厂通过与德国 南方化学、庄信万丰、托普索、南化院等 4家催 化剂厂家进行交流,并对兖矿国宏 500kt/a甲醇 装置、江苏索普 500kt/a甲醇装置、南京惠生 500kt/a甲醇装置、中海建滔 600kt/a天然气制 甲醇装置进行调研考察后认为,德国南方化学的 C797GL型催化剂和庄信万丰的 JM517S型催化 剂均能满足装置运行要求,最终通过商务比价及 售后服务比较,选用了庄信万丰的 JM517S型催 化剂。 123 JM517S型催化剂的运行情况
第 2炉 催 化 剂 选 用 的 是 英 国 庄 信 万 丰 的 JM517S型进口甲醇合成催化剂,自 2012年 7 月使用至 2014年 6月,共使用 700d,生产精甲 醇 12195kt。 121 催化剂 (JM517S) 的主要物化特性
甲醇合 成 催 化 剂 型 号 为 庄 信 万 丰 的 JM51 7S;催化剂形状为圆柱状颗粒,尺寸 54mm× 36mm;主要成分 CuO64%、Al2O310%、ZnO 24%、MgO2%,其中部分铜和锌是以碳酸盐的 形态 存 在 的;堆 密 度 14~16kg/L,装 填 量 805m3。 122 第 2炉采用庄信万丰催化剂的原因
变换工段更换催化剂及技术改造总结

变换工段催化剂升温硫化及技术改造总结曹安军马九会(山西永济中农化工有限公司044500)0 前言山西永济中农化工有限公司是以煤为原料的中型氮肥厂,目前生产能力为:合成氨140 kt/a ,尿素180kt/a ,甲醇60kt/a 。
共有两套变换系统,一套为中低低工艺;一套为0.8Mpa全低变工艺。
该全低变工艺系2005年6月投运,至今已运行四年,催化剂已到后期,出现变化气中co含量超标、蒸汽消耗上升、系统阻力高等影响生产的因素。
同时由于甲醇价格持续下滑,想进一步降低甲醇进口co已不太可能。
为了最大限度地调整氨醇比,经公司研究决定对该全低变系统进行改造,由湖北双雄催化剂有限公司提供催化剂和技术指导。
1.全低变工艺流程1.1气体流程来自压缩二段的半水煤气,经煤气冷却器将煤气温度降至45℃以下进入油分,气体在丝网作用下除去油污,然后从饱和塔下部入塔并与塔顶下来的热水逆流充分接触,增湿、提温后进入汽水分离器中,分离掉气体中的水分。
在分离器出口补加蒸汽,使气体温度达到120℃左右,进入预热交换器管内与管间来自热交的变换气换热,使气体温度达到170--180℃,再进入热交管内与来自低变二段的变换气换热,使气体温度达到210,经系统内电炉进入低变炉一段上端的净化层处理其中的有害物质。
然后进入催化剂层反应,出低变一段的气体温度高达380℃,然后进入喷水净化器,经喷水降温后进入低变炉二段,出低变二段温度为290℃的变换气经热交、预热交与管内的半水煤气换热后,进入低变炉三段进行反应后,进入一水加热器与来自热水泵的热水换热降温后进入热水塔,出来后进入冷却器,然后经气水分离器分离掉部分冷凝水后送至变脱工段。
1.2热水流程循环热水从热水塔出来,经热水泵加压后送至一水加热器管内回收变换气热量后,进入合成水加热器加热后,送入饱和塔上部,增温、增湿半水煤气后,从饱和塔下部出来进入水水换热器,与软水岗位来的软水间接换热后,进入热水塔再次回收热量后,从下部出来进入热水泵依次循环。
甲醇合成催化剂应用浅析

甲醇合成催化剂应用浅析摘要:合成催化剂应用、操作。
关键词:甲醇、铜基1、概述甲醇是最简单的化学品之一,是重要的化工基础原料和清洁液体燃料,广泛用于有机合成、染料、医学、农药、汽车、国防等领域。
在20世纪70年代前,甲醇最早由木材和木质素干馏制得,故称木醇,但是,生产一公斤的甲醇约需70公斤左右的木材,1923年德国BASF公司首先用锌铝催化剂在高温高压的操作条件下实现了由CO和H2合成甲醇的工业化生产。
1966年,英国ICI公司成功实现了铜基催化剂的低压甲醇合成工艺,随后又实现了更为经济的中压法甲醇合成工艺。
到1982年世界各国采用中低压生产甲醇总能力已经达到占80%。
随着甲醇合成工艺的发展,合成催化剂也在不断研究改进,各国实验室研究出了多种甲醇合成催化剂,但工业上使用的催化剂只有锌铬和铜基催化剂。
2、两类催化剂2.1锌铬催化剂锌铬催化剂活性较低,要获得较高的催化活性,操作温度在600K左右,为了获得较高的转化率,需要控制压力25~35MPa,锌铬催化剂的耐热性、抗毒性以及机械性都较好,使用寿命也长,使用范围宽,操作容易控制,由于操作压力高,对设备的要求就高,投资大,目前逐渐被淘汰。
2.2铜基催化剂2.2.1性质铜基催化剂是一种低压催化剂。
主要组分:CuO/ZnO/AL2O3是由英国ICI公司和Lurgi公司先后研制成功,操作温度500~530K,压力:5~10MPa,此条件对甲醇反应平衡有利。
2.2.2生产方法铜基催化剂是选用高纯度的Cu(NO3)2,、Zn(NO3)2,溶解在NaCO3溶液中,用共沉淀法的到(Cu,Zn)2(OH)2CO3,然后进行高温热还原,形成具有多孔结构,并再加入促进热稳定的及其它助剂,就是目前使用非常普遍的新一代铜基催化剂,铜基催化剂加入Al2O3可以减小铜晶体,活性进一步提高,少量Cr2O3存在可以阻止一小部分CuO,可以保护催化剂的活性中心,国外专家研究发现,420k时纯ZnO、CuO活性为零,但是大大提高抗老化能力,目前铜锌铝系和铜锌铬系应用的最多,由于铬对人体有害,此系催化剂逐渐被淘汰。
甲醇合成催化剂更换过程总结及优化建议

21 2013年甲醇合成催化剂钝化情况 2013年 甲 醇 合 成 催 化 剂 钝 化 原 计 划 用 时
80h,实际用时 56h(见表 1)。整个催化剂钝 化过程中,前期加空气较谨慎,耗时较长;中后 期入塔 气 (入 塔 气 为 N2 中 加 入 空 气 的 混 合 气 体,而与催化剂发生钝化反应的是空气中的 O2, 故钝化过程中的主要任务是控制入塔气中的 O2 含量) O2浓度提升较快,耗时短。
1 甲醇合成系统工艺流程及催化剂钝化、升温 还原原理
开一备) 冷却到 40℃后,进入甲醇分离器 A/B (2台并联,一开一备,通过开关出入口阀进行 切换,也可同时使用) 进行气液分离。甲醇分 离器顶部出来的分离掉甲醇的大部分气体作为循 环气去合成气压缩机,经合成气压缩机增压并补 充新鲜气后送入甲醇合成塔进行下一轮反应;一 小部分作为弛放气送往氢回收系统回收 H2。甲 醇分离器分离出的粗甲醇则通过一级过滤器 A/B (2台,一 开 一 备) 和 二 级 过 滤 器 A/B (2台, 一开一备) 除去其中的固体杂质后送至闪蒸槽, 之后粗甲醇经粗甲醇泵送至甲醇精馏系统或粗甲 醇罐区。
第 1期 2019年 1月
中 氮 肥 MSizedNitrogenousFertilizerProgress
No1 Jan.2019
甲醇合成催化剂更换过程总结及优化建议
文惠萍
(云南解化清洁能源开发有限公司解化化工分公司,云南 开远 661699)
[摘 要]甲醇合成催化剂更换情况的好坏将直接影响甲醇合成系统的运行状况,也关乎粗甲醇产品的 产量及消耗的高低。云南解化清洁能源开发有限公司解化化工分公司 200kt/a甲醇装置 2008年建成投产, 分别于 2013年 3月和 2017年 8月更换了甲醇合成催化剂,介绍这两次甲醇合成催化剂的更换过程,包括 旧甲醇合成催化剂的钝化及卸出、新甲醇合成催化剂的装填及升温还原等情况,在更换过程经验总结的基 础上对下一次的催化剂更换提出优化建议。
我公司50kt/a甲醇合成装置催化剂使用总结

甲醇 生产 系统 采 用低 压 甲醇 合 成工 艺 , 套相 配 关 工艺 为 固定 床 造 气 、 法 脱 硫 、. a变 换 、 湿 08MP 变 压 吸 附脱碳 、 心饼 精 脱硫 、 压缩 机 加 压 , 产 夹 4段 生
工艺流 程见 图 1 。
圜一 一 圜 一 一 圜 圈 圜
维普资讯
・
1 6・ 5
全 国气体净化信息站 20 0 7年技术交流会论文集
我 公 司 5 ta甲醇 合成 装 置 催 化 剂使 用总 结 0k/
张 庆 海 , 祥 权 林
( 久泰能源科技有 限公 司 , 山东 临沂 261) 以新 型 绿色 能源— —
0× 4/ 8 0 e 2 3 8 / 1 甲醇合成塔 1 0 4 , 1 00V 一 5 m
1
,
艺 管理 、生 产 管 理 、设 备 管 理 制 度 全 面 ,落 实 到
置于合 成塔内
2 电加热器
1 0 W 0k 5
位 ,生 产稳定 有序 ,产 量 由以前 满量 20td提 高 4 / 到 2 0td以上 ,最高 班产 达 到 26td 7 / 7 。合 成 炉温 / 易 于控制 ,波 动范 围稳定 在 3℃ 以内 ,但 系统 压力 仍 有接 近 0 1M a的波动 ,合成 新鲜 气气体 成 分无 . P 大 的改 变 。运行 中因合成水 冷却 器换 热效果 差 ,夏 季生 产 水 冷 后 温 度 5 O℃ 以上 ,合 成 醇 分 效 果 差 , 影 响产量 。
圈国圜 一 一 一 一一 圈 圈 圈
图 1 甲醇生产 工艺 流程示意
1 2 设 计 工 艺 流 程 .
合成系统采用了南京国昌公司化工科技有限公
司设 计 的 G C型 轴 径低 压 甲醇 合 成 反 应器 , 计 工 设
甲醇-7-新型铜基甲醇催化剂使用小结

新型铜基甲醇催化剂使用小结郭新法1)、唐海亮2)1、山西省·灵石中煤化工有限公司2、河南省·南阳德润化工有限公司摘 要:本文介绍了改进催化剂的升温还原方法,以及生产过程中的优化措施,从而达到了延长催化剂使用寿命的目的。
关键词:催化剂;联醇;升温还原;使用南阳德润化工有限公司现已发展成为年产12万t合成氨联产6万t甲醇的企业,现有甲醇合成系统三套,其中两套φ800甲醇系统,一套φ1200甲醇系统(原两套φ600甲醇系统已拆除),三个甲醇合成塔均使用新型C207联醇催化剂。
1 甲醇合成系统的概况1.1 工艺流程来自压缩五段出口气,经洗氨塔、油水分离器进入甲醇合成塔,合成塔出口气体经冷排降温至40℃以下进入醇分,分离粗甲醇后去洗醇塔脱除气体中夹带的少量甲醇等有毒气体再到铜洗岗位,然后去压缩机六段进口,其流程见图1。
图11.2 工艺流程特点三套甲醇系统工艺配置根据催化剂使用情况可灵活运用,即三个甲醇合成塔进气量可随意调节,也可停用其中的任意一套甲醇系统,不影响生产的平衡稳定(其它两套甲醇系统正常使用)。
循环机的配置可三塔大循环,也可单塔小循环。
1.3 甲醇系统的主要设备(见表1)表1设备 规格型号 数量 设备 规格型号 数量 合成塔 φ1200 1 冷排 F=200m2 2 合成塔 φ800 2 冷排 F=400m 21 甲醇分离器 φ800 1 电加热器 1200kW 1 甲醇分离器 φ6002 电加热器 600kW 2 油水分离器 φ800 1 循环机 4.0m 3/min 3 油水分离器 φ6002循环机2.0m 3/min42 新型C207甲醇催化剂的升温还原 2.1 催化剂的装填情况2007年6月φ800系统A 塔用新型C207甲醇催化剂装填6.8t,2008年8月φ800系统B 塔使用新型C207甲醇催化剂装填6.6t,去年4月新上的φ1200塔也用新型C207甲醇催化剂装填16.6t。
甲醇合成催化剂应用小结
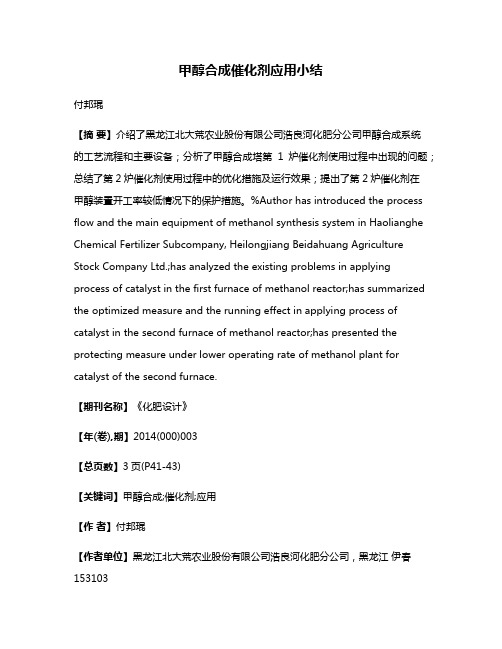
甲醇合成催化剂应用小结付邦琨【摘要】介绍了黑龙江北大荒农业股份有限公司浩良河化肥分公司甲醇合成系统的工艺流程和主要设备;分析了甲醇合成塔第1炉催化剂使用过程中出现的问题;总结了第2炉催化剂使用过程中的优化措施及运行效果;提出了第2炉催化剂在甲醇装置开工率较低情况下的保护措施。
%Author has introduced the process flow and the main equipment of methanol synthesis system in Haolianghe Chemical Fertilizer Subcompany, Heilongjiang Beidahuang Agriculture Stock Company Ltd.;has analyzed the existing problems in applying process of catalyst in the first furnace of methanol reactor;has summarized the optimized measure and the running effect in applying process of catalyst in the second furnace of methanol reactor;has presented the protecting measure under lower operating rate of methanol plant for catalyst of the second furnace.【期刊名称】《化肥设计》【年(卷),期】2014(000)003【总页数】3页(P41-43)【关键词】甲醇合成;催化剂;应用【作者】付邦琨【作者单位】黑龙江北大荒农业股份有限公司浩良河化肥分公司,黑龙江伊春153103【正文语种】中文【中图分类】TQ426.64黑龙江北大荒农业股份有限公司浩良河化肥分公司10万t/a甲醇合成塔采用φ3 400 mm等温反应器,第1炉甲醇合成催化剂运行2年,2008年大检修期间更换了甲醇合成催化剂,以下将合成催化剂的使用、更换情况小结如下。
南京诚志甲醇合成催化剂应用总结

碳效率高、副产物含量低、结蜡少,大大提高了装置的经济效益。
关键词: 甲醇合成催化剂;庄信万丰 KATALCOJM51-7S;碳效率;高活性
中图分类号: TQ223.12+1
文献标识码: A
文章编号: 2095-0802-(2019)10-0177-03
Summary of the Application of Methanol Synthesis Catalyst in Nanjing Chengzhi Clean Energy Co., Ltd.
1 诚志甲醇装置工艺
诚志甲醇装置以煤为原料,经气化生成合成气后
收稿日期:2019-08-29 第一作者简介:纪 涛,1984年生,男,江苏南京人,2006年毕业 于南京科技职业学院有机化工专业,工程师。
再经变换、低温甲醇洗后进入合成单元,合成气由循环 气经压缩机升压后进入合成回路,合成塔采用华东理工 大学的副产蒸汽列管式合成塔,产出的粗甲醇经精馏单 元后最终得到甲醇产品。在此过程中,副产气体提供给 下游装置和园区内其他公司。诚志甲醇装置具体工艺流 程见图 1。
尾气去火炬
O2 水
富氢 压缩机
/S回收
丙烯制冷 废气
循环压缩机 分离膜
煤 水煤浆 气化 制备
渣 渣水处理
废水
变换 热回收
低 温
甲醇合成
甲醇 精馏
甲
醇
富氢气
洗
CO深冷分离 CO气体
S回收尾气
硫磺 S回收Biblioteka 图 1 诚志甲醇装置工艺流程图
2 KATALCOJM51-7S 催化剂简介及还原操作
2.1 催化剂简介 KATALCOJM51-7S 是一种以 ZnO-Al2O3 为载体并加
甲醇的转化与功能化应用研究
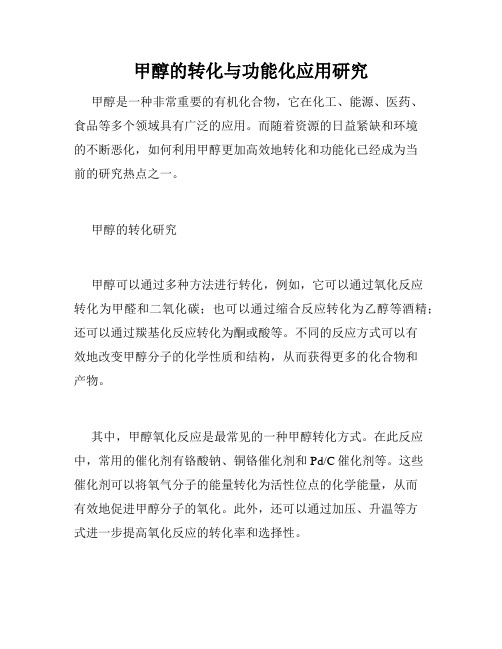
甲醇的转化与功能化应用研究甲醇是一种非常重要的有机化合物,它在化工、能源、医药、食品等多个领域具有广泛的应用。
而随着资源的日益紧缺和环境的不断恶化,如何利用甲醇更加高效地转化和功能化已经成为当前的研究热点之一。
甲醇的转化研究甲醇可以通过多种方法进行转化,例如,它可以通过氧化反应转化为甲醛和二氧化碳;也可以通过缩合反应转化为乙醇等酒精;还可以通过羰基化反应转化为酮或酸等。
不同的反应方式可以有效地改变甲醇分子的化学性质和结构,从而获得更多的化合物和产物。
其中,甲醇氧化反应是最常见的一种甲醇转化方式。
在此反应中,常用的催化剂有铬酸钠、铜铬催化剂和Pd/C催化剂等。
这些催化剂可以将氧气分子的能量转化为活性位点的化学能量,从而有效地促进甲醇分子的氧化。
此外,还可以通过加压、升温等方式进一步提高氧化反应的转化率和选择性。
甲醇的功能化应用研究除了转化之外,甲醇还可以通过功能化方式进行应用。
功能化是一种将甲醇分子中的某些官能团进行化学修改,从而获得新的化合物或者改变甲醇分子的性质和用途的技术。
例如,对甲醇进行羟甲基化反应,即可得到羟甲基甲醇,这种新型化合物在某些领域的应用具有非常优秀的性能和效果。
此外,甲醇还可以通过液相氧化、氧化加氢、加氢调制、液相环氧化等方式进行功能化。
液相氧化是一种将甲醇分子中的羟基化为羰基的反应,这种方式可以获得更多的酮和酸等。
氧化加氢是一种将甲醇分子中的羰基还原为醇的反应,这种方式常用于制备高品质的杂环化合物和医药中间体。
加氢调制是一种将甲醛进行加氢转化为甲醇的反应,这种转化能够生产高品质的甲醇和酮等产物。
液相环氧化则是一种利用环氧甲烷进行化学反应,从而获得一系列新型的环氧化合物的技术。
这些技术和方法已经成为了甲醇转化和功能化领域的常用工具。
总结在甲醇的转化与功能化应用研究中,不仅需要关注其性质、构造、反应机理等基础理论问题,还需要在实际应用中探索创新的技术和新型材料,以满足现代产业和人民生活的日益增长的需求。
DC207、DC503甲醇催化剂应用总结
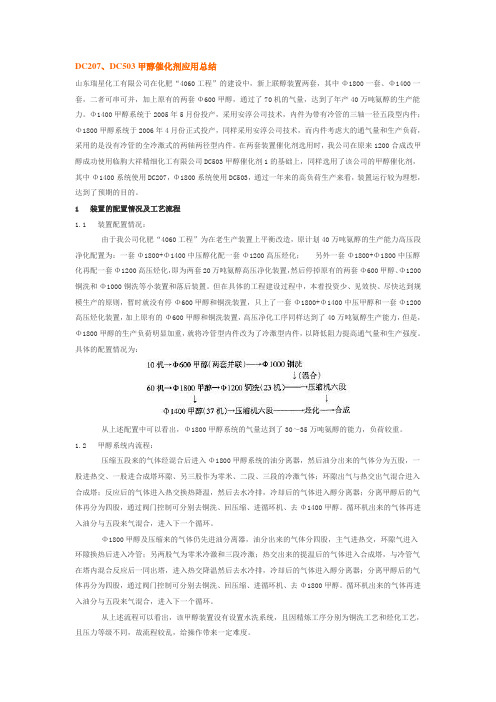
DC207、DC503甲醇催化剂应用总结山东瑞星化工有限公司在化肥“4060工程”的建设中,新上联醇装置两套,其中Φ1800一套、Φ1400一套,二者可串可并,加上原有的两套Φ600甲醇,通过了70机的气量,达到了年产40万吨氨醇的生产能力。
Φ1400甲醇系统于2005年5月份投产,采用安淳公司技术,内件为带有冷管的三轴一径五段型内件;Φ1800甲醇系统于2006年4月份正式投产,同样采用安淳公司技术,而内件考虑大的通气量和生产负荷,采用的是没有冷管的全冷激式的两轴两径型内件。
在两套装置催化剂选用时,我公司在原来1200合成改甲醇成功使用临朐大祥精细化工有限公司DC503甲醇催化剂1的基础上,同样选用了该公司的甲醇催化剂,其中Φ1400系统使用DC207,Φ1800系统使用DC503,通过一年来的高负荷生产来看,装置运行较为理想,达到了预期的目的。
1 装置的配置情况及工艺流程1.1 装置配置情况:由于我公司化肥“4060工程”为在老生产装置上平衡改造,原计划40万吨氨醇的生产能力高压段净化配置为:一套Φ1800+Φ1400中压醇化配一套Φ1200高压烃化;另外一套Φ1800+Φ1800中压醇化再配一套Φ1200高压烃化,即为两套20万吨氨醇高压净化装置,然后停掉原有的两套Φ600甲醇、Φ1200铜洗和Φ1000铜洗等小装置和落后装置。
但在具体的工程建设过程中,本着投资少、见效快、尽快达到规模生产的原则,暂时就没有停Φ600甲醇和铜洗装置,只上了一套Φ1800+Φ1400中压甲醇和一套Φ1200高压烃化装置,加上原有的Φ600甲醇和铜洗装置,高压净化工序同样达到了40万吨氨醇生产能力,但是,Φ1800甲醇的生产负荷明显加重,就将冷管型内件改为了冷激型内件,以降低阻力提高通气量和生产强度。
具体的配置情况为:从上述配置中可以看出,Φ1800甲醇系统的气量达到了30~35万吨氨醇的能力,负荷较重。
1.2 甲醇系统内流程:压缩五段来的气体经混合后进入Φ1800甲醇系统的油分离器,然后油分出来的气体分为五股,一股进热交、一股进合成塔环隙、另三股作为零米、二段、三段的冷激气体;环隙出气与热交出气混合进入合成塔;反应后的气体进入热交换热降温,然后去水冷排,冷却后的气体进入醇分离器;分离甲醇后的气体再分为四股,通过阀门控制可分别去铜洗、回压缩、进循环机、去Φ1400甲醇。
MK_121型甲醇合成催化剂应用总结_钱海林

MK -121型甲醇合成催化剂应用总结钱海林,樊 飞(河南龙宇煤化工有限公司 永城 476600)摘要 介绍了MK-121型低压甲醇合成铜基催化剂的装填、升温还原及1年来的运行情况。
实践证明,该催化剂具有较好的转化率、活性和稳定性,具备良好的操作稳定性,可以满足生产负荷、气体成分不稳定等工艺条件的要求。
关键词 M K-121 催化剂 甲醇 应用本文作者的联系方式:ssitxhong @163.co mSu m-Up of U se of Type MK -121M ethanol Synthesis Catal ystQ i a n H a ilin ,Fan Fe i(H e c nan Longyu Coa lChe m ica lCo .,Ltd . Yongcheng 476600)Abstract A descri p tion is g i v en o f the MK-121copper -based catalyst for l o w -pressure m ethanol synthesis ,inc l u d i n g its char g ing ,reduction by heating and operati o n for a year .Practice proves that it sho w s a h i g h conversi o n rate ,acti v ity and stab ility ,w ith good stab ility i n operation ,able to m eet the require m en ts for process conditi o ns of unstab le producti o n load and gas co m position .K eyw ords MK-121 cata l y st m ethano l use河南龙宇煤化工有限公司(简称龙宇煤化工)500k t/a 甲醇装置以煤为原料,采用Shell 粉煤气化制取甲醇合成原料气。
甲醇合成催化剂使用经验总结

第2期
杨玉兰等 : 甲醇合成催化剂使用经验总结
收稿日期 : 1999 - 07 - 15; 修订日期 : 1999 - 12 - 16
38
天然气化工
2000 年第 25 卷
车时间 ) , 单炉产甲醇 5 16~ 9 87 t , 催化剂基 本达到了设计保证使用寿命和产量。
用效率; 三是优选适合于工艺条件的催化剂 , 以期 达到最大限度地发挥催化剂和工艺装置的潜力、 增加产量、 延长寿命及节能降耗的目的。 3 1 减少原料气中的毒物 根据原料和用后催化剂的分析数据, 确定本 装置 甲 醇 合 成 催 化 剂 的 毒 物 为 S、 Cl、 Fe 、 Ni、 NH 3 , 结果见表 1。为了减少毒物, 对装置进行如 下改造 : ( a) 增加了常温氧化锌, 使精脱硫气中总 S< 0 05mg/ m 3 ; ( b) 加高常温脱硫槽, 增装羰基铁 镍吸附剂 K306; ( c) 对水洗塔实施加高改造, 增加 一段新鲜水洗涤, 将 NH 3 拦截在净化以前; ( d) 通 过增加预洗甲醇量, 加强对羰基铁镍的脱除。 通过以上改造 , 有效地降低了原料气中的毒 物。
37
甲醇合成催化剂使用经验总结
杨玉兰 , 刘振洪 , 左继功 , 吴良泉 ( 齐鲁石化公司 第二化肥厂 , 山东 255400) 摘要 : 甲醇合成催化剂在山东齐鲁石 化第二 化肥厂使 用时存 在寿命 短、 产 量低等 问题。 通过对 催化 剂进行 剖析 研 究 , 找到了原因 , 并采取了相应的改进措施 , 最终使甲醇合成催化 剂使用寿命从半年延长到一年半 , 单炉催 化剂甲醇产 量 从 3 万 t 增加到 9 9 万 t, 催化剂的甲醇生产能力达到了 5500t/ m3 cat, 从而解决了甲醇合成催化剂使用寿命短、 产量低的 问题。 关键词 : 甲醇合成催化剂 ; 使用寿命 ; 毒物 中图分类号 : T Q 223 12 1
- 1、下载文档前请自行甄别文档内容的完整性,平台不提供额外的编辑、内容补充、找答案等附加服务。
- 2、"仅部分预览"的文档,不可在线预览部分如存在完整性等问题,可反馈申请退款(可完整预览的文档不适用该条件!)。
- 3、如文档侵犯您的权益,请联系客服反馈,我们会尽快为您处理(人工客服工作时间:9:00-18:30)。
()升温硫化方法 :用半水煤气作载气,蒸 1
[ 收稿 日期 】 061 20 — 3 00 [ 作者简介 】段向华(94 , , 17 一)男 河南 安阳人 , 助理工程师。
换管间一变煮器一变冷器一变分器一排液。
维普资讯
・
2 O・Βιβλιοθήκη 中 氮 肥 段 向华 。邢 艳红 。李 勇
( 安阳化学工业集 团有 限责任公司 ,河南 安阳 4 53 ) 5 13
[ 中图分类号】Tq 2 3 1 1 [ 2 .2 文献标识码】B [ 文章编号 】10 —9 2 2 0 )20 1.2 0 49 3 (0 70 .0 90
我公司甲醇系统是 1 套以煤为原料 的单醇装 置 ,采用 低压鲁奇合成工艺 ,设 计 能力为年产 3 t 0k 精甲醇。该系统 19 年 9 95 月一次开车成功 产出合格 的精 甲醇 ,第二年生产能力突破设计能 力 ,达到 3 ta以上 ,后 经 过 多 次 挖 潜 改 造 , 1k/ 现在生产能力已达到 6 ta 2k/ 以上。该 系统变换 工序 原采用 中温 变 换工 艺 ,使 用 B 1 l2中温 变 换 催 化剂 ,但 该工艺 应用 于 甲醇生 产存 在蒸 汽消 耗 高、变换效率低 、催化剂使用寿命短 、催化剂易 粉化 、塔 阻力大等诸 多缺点。为进一步优 化工 艺 ,19 97年初 将 中 温变 换 工 艺 改 为 低 温 变 换 工
表2 HB3低变催化剂升温硫化进程 -
时
间
0 T4 4 A1
A2
A
℃
℃
℃
℃
3
署 害
( ( ℃ ℃ ℃ T ℃ ℃ 1 23℃ 2 3 D 3 4 2 3 D I 0
出
量
注:T 0 4 4为低变炉入 口温度 ,A 、A 、A 、B 、1 、B 分别为低变炉上段床层温度 ,C 、 、( 、D 、D 、D 分别 为低变 1 2 3 1 3 3 2 1 3 3 1 2 3 炉 下段床层温度 ,T 0 为低变炉出 口温度。 45
艺 ,催 化 剂更 换 为 m 0 Q 低 变 催 化 剂 ,催 化 剂 3
换气进入第二和第一换热器管间加热水煤气 。过 热蒸汽 ( . a 7 2 5MP ,30℃)在 出第一换热器 的 水 煤气 管线 上加 入 。
2 中变及 低变 工艺 的特 点
甲醇生产中 C o变换 和合成氨生产 中 C o变 换不 同。合成氨生产 中 C o作为有害气体要求全 部变换 ,以最大限度地产 生 H 和 c 2 2 o ,达到精
第 2期
3. 升 温硫 化 进 程 2
达 到 1 .8ng m3 10 a/ 。下 段炉 温在 4 0℃ 时进 人强 2
催化剂的升温硫化在常压下进行 ( 其进程如
表 2 。2 0 年 3月 2 ) 01 6日 4 0压 缩机 送气 ,开 -0 始升 温 ,1 :0 4 0低 变炉 上 、下 段 均 升 至 20℃ 0 以上 ,开 始 配 人 C 2 行 硫 化 ,2 日 1 0低 S进 7 :0 变 炉 出 口开 始 出现 H2 S,2 :4 S质 量 浓 度 2 0H2
使用寿命 明显延长。2 0 0 1年在低变工艺改造 的 基础上又将催化剂更换为 H - 低变催化剂 ,取 B3 得了较好经济效益。现就几种催化剂在我公司的 实际使用情况进行分析、总结 ,供大家参考 。
1 变换 工 艺流程 简述
水 煤气 ( . a 0℃ )经滤 油器 除去 夹 19MP ,4
维普资讯
第 2期 20 0 7年 3月
中 氮
肥
No. 2 M a .2 0 r 0 7
M - ie to e o sF riz rP o rs S zd Ni g n u etl e r g es r i
甲醇 变换 催 化 剂应 用小 结
制气 中 C 含 量 小 于 1 O 0×1 的 目的 ;而 甲醇 0
生产则要求保持相当浓度的 C ,以满足甲醇合 O 成对原料气氢碳 比的要求 。我公 司原料气 中 C O 含量在 3 %左右 ,要求控制变换气 中 C 含量在 7 O 1 %~2 %,变换 率 3 %左 右。以往 几炉 中温 8 6 0 变换催化剂存在操作温区窄、抗氧性能差 、变换 阻力高 、蒸汽消耗高等缺点。而耐硫低变催化剂 优点则十分 明显 ,操作温区宽 、低温活性好 、抗 氧抗毒性好 、蒸汽消耗量小 ,而且活性下降时可 以通过再硫化来加以提高。相对来说 ,低温变换 变换率 较 低 ,但 由于 我公 司 甲醇 生产 中 C 为 活 O 性组分 ,要求新鲜气氢碳 比控制在 2 0 ~2 1 , .5 .5 所以采用低温变换工艺更为合适 。我公司低温变 换与中温变换工艺技术参数对比见表 1 。
带 的油污、灰尘、水等杂质 ,然后依次进入第一 和第二换热器管内与出塔的变换气换热 ,水煤气 升 温 至 20℃左右 , 由顶部 进入 变换 炉 ,出炉 变 2
表 1 低 温变换 与中温变换 工艺技 术参数对 比
3 I - 变催化 剂 的升温 硫化 - 3低 t B 3 1 升温硫 化操作 控 制原 则 .
制硫化阶段 ,炉温提到 4 0℃后开始带硫降温 , 8 2 日 3 0停 止 配 人 C , 1 0炉 温 降 至 8 :0 S ,1 :0 201时转人 正常开 车阶段 。本次硫 化共 耗时 6 2 5 ,消耗 C 2 . t 5 h S 6 ,基本符合硫化方案 ,实际 1 硫化参数记录如表 3 。
汽作热源加 热 ,在 变换 炉入 1加 入 c 2 : 2 1 s 进行 硫 化 ,变脱前放空。 ()煤气流程为 :水煤气一滤油器一一换管 2 内一二换管内一低变炉一二换管问一一换 管问一 变煮器一变冷器一变分器一放空 。 ()蒸 汽加 热流程 为 :水蒸 气一 二换 管 间一 3
一