拉延模制造流程
拉延模设计顺序标准
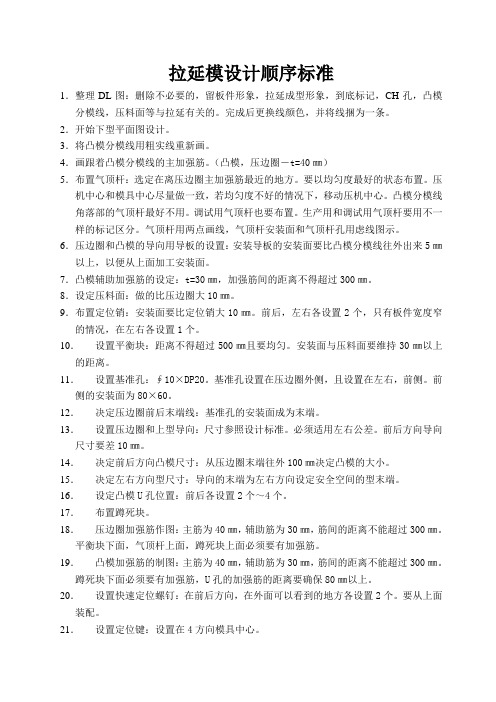
拉延模设计顺序标准1.整理DL图:删除不必要的,留板件形象,拉延成型形象,到底标记,CH孔,凸模分模线,压料面等与拉延有关的。
完成后更换线颜色,并将线捆为一条。
2.开始下型平面图设计。
3.将凸模分模线用粗实线重新画。
4.画跟着凸模分模线的主加强筋。
(凸模,压边圈-t=40㎜)5.布置气顶杆:选定在离压边圈主加强筋最近的地方。
要以均匀度最好的状态布置。
压机中心和模具中心尽量做一致,若均匀度不好的情况下,移动压机中心。
凸模分模线角落部的气顶杆最好不用。
调试用气顶杆也要布置。
生产用和调试用气顶杆要用不一样的标记区分。
气顶杆用两点画线,气顶杆安装面和气顶杆孔用虑线图示。
6.压边圈和凸模的导向用导板的设置:安装导板的安装面要比凸模分模线往外出来5㎜以上,以便从上面加工安装面。
7.凸模辅助加强筋的设定:t=30㎜,加强筋间的距离不得超过300㎜。
8.设定压料面:做的比压边圈大10㎜。
9.布置定位销:安装面要比定位销大10㎜。
前后,左右各设置2个,只有板件宽度窄的情况,在左右各设置1个。
10.设置平衡块:距离不得超过500㎜且要均匀。
安装面与压料面要维持30㎜以上的距离。
11.设置基准孔:∮10×DP20。
基准孔设置在压边圈外侧,且设置在左右,前侧。
前侧的安装面为80×60。
12.决定压边圈前后末端线:基准孔的安装面成为末端。
13.设置压边圈和上型导向:尺寸参照设计标准。
必须适用左右公差。
前后方向导向尺寸要差10㎜。
14.决定前后方向凸模尺寸:从压边圈末端往外100㎜决定凸模的大小。
15.决定左右方向型尺寸:导向的末端为左右方向设定安全空间的型末端。
16.设定凸模U孔位置:前后各设置2个~4个。
17.布置蹲死块。
18.压边圈加强筋作图:主筋为40㎜,辅助筋为30㎜,筋间的距离不能超过300㎜。
平衡块下面,气顶杆上面,蹲死块上面必须要有加强筋。
19.凸模加强筋的制图:主筋为40㎜,辅助筋为30㎜,筋间的距离不能超过300㎜。
拉延模

1. 什么是拉延将平板料,在拉延成型过程中,产生塑性变形,从而获得所需几何形状制件的冲模1.1 拉延在冲压件中的用途采用拉延工艺,能使板料拉延成为不规则的形状的制件;如:筒形,梯形,锥形,球形,盒形等1.2 拉延的基本过程拉延模是由凸模,凹模,压边圈三部分组成的,其凸模与凹模的结构和形状与冲裁模不同,他们的工作部分没有锋利的刃口,而是做成圆角(利于板料的流动)。
凸模与凹模的间隙大于板料的厚度。
在拉延开始时,凹(上)模首先形成往下至压边圈,将板料压紧在延边圈的压料面上,继续行程往下;此时拉延开始,板料通过凹模圆角经凸模拉入凹模,直至下死点,拉延成凸模形状,拉延完成。
拉延的过程是使板料的每一小单元体内产生内应力,在内应力的作用下,产生应变状态,使得板料产生塑性变形的过程;获得较好的刚度的制件。
2拉延模设计程序依据冲压工艺的工序数型,冲压工艺的工序卡(参数,数据),涉及构思图(结构形式)。
确定结构形式2.2.1 凹(上)模与凸(下)模导向A.上凹(上)模与凸(下)模的导腿(三面)导向。
B.上凹(上)模与凸(下)模得导板(长导板)导向。
C.凹(上)模与压边圈导向:凹(上)模与压边圈(导腿)导向压边圈与凸(下)模导向:A. 压边圈与凸(下)模的内导向B. 压边圈与凸(下)模的外导向2.2.2凹模的作用凹模的主要作用:是通过凹模压料面和凹模圆角进行拉延2.2.3 压边圈的作用:主要是起压料作用。
板料被压边圈的压料面与凹模的压料面压紧。
在拉延过程中,拉延变形区的板料凸缘部分的料仅在压边圈的压料面与凹模压料面的间隙中通过3确定定位形式A.封闭定位(一周)B.三面定位4 确定定位装置导轮定位,挡料板,翻转定位等5 确定调压块的位置及数量依据压边力,且沿压边圈的压料面的轮廓,布置调压块的位置及数量。
6确定气顶孔的位置及数量根据客户提供的冲床(设备)参数,依据压边圈压料面的轮廓尺寸,确定气顶孔的位置及数量(尽量靠近压边圈的内轮廓)。
拉延模设计
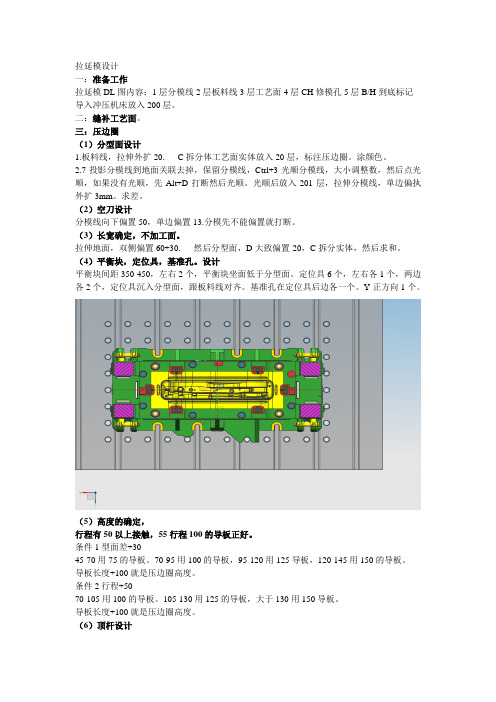
拉延模设计一:准备工作拉延模DL图内容:1层分模线2层板料线3层工艺面4层CH修模孔5层B/H到底标记导入冲压机床放入200层。
二:缝补工艺面。
三:压边圈(1)分型面设计1.板料线,拉伸外扩20. C拆分体工艺面实体放入20层,标注压边圈。
涂颜色。
2.7投影分模线到地面关联去掉,保留分模线,Ctrl+3光顺分模线,大小调整数,然后点光顺,如果没有光顺,先Alt+D打断然后光顺。
光顺后放入201层,拉伸分模线,单边偏执外扩3mm。
求差。
(2)空刀设计分模线向下偏置50,单边偏置13.分模先不能偏置就打断。
(3)长宽确定,不加工面。
拉伸地面,双侧偏置60+30. 然后分型面,D大致偏置-20,C拆分实体,然后求和。
(4)平衡块,定位具,基准孔。
设计平衡块间距350-450,左右2个,平衡块坐面低于分型面。
定位具6个,左右各1个,两边各2个,定位具沉入分型面,跟板料线对齐。
基准孔在定位具后边各一个。
Y正方向1个。
(5)高度的确定,行程有50以上接触,55行程100的导板正好。
条件1型面差+3045-70用75的导板。
70-95用100的导板,95-120用125导板,120-145用150的导板。
导板长度+100就是压边圈高度。
条件2行程+5070-105用100的导板。
105-130用125的导板,大于130用150导板。
导板长度+100就是压边圈高度。
(6)顶杆设计分模线外两侧,均匀排布。
可以Y向移动。
不可以X向移动,坐面60.厚度10.垫块厚度20. (7)导引设计导板宽度板料线1/8。
位置在分模线1/6处。
两边放1个,长边放2个。
.导板面到分模线5-10.先40厚的长方体。
C拆分10,20,10. 3块。
1.导板面:上面9倒10mm斜角。
下面偏置15,倒20圆角。
2.背托面:上面偏置5-10,下面拉伸40,向里偏置10。
3.导入导板。
涂颜色。
拉伸导板面,左40右40上30.倒圆角25.(8)淘沙减重处理5偏置底面轮廓线40。
拉延模制作规范
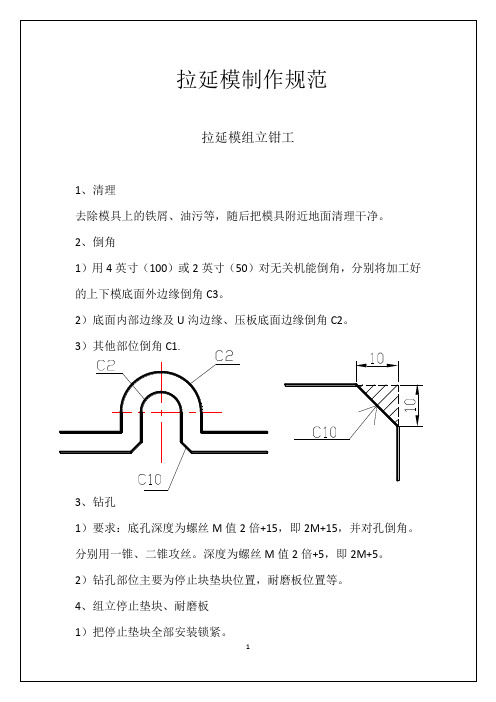
1)把压边圈放在下模上锁紧(放到底),模仁涂红丹,导板(耐磨板)涂红丹,要求薄而均匀。
2)把下模反转放在上模上,上机台合模、
3)先合导板,要求接触率80%以上,均匀接触。同组立时导板研配。
4)模仁部分的研配
要求压机不加压,上模模仁水平面部分红丹接触率为90%以上,均匀接触。基准面接触率为100%,斜面放铅丝确认间隙。
B.顶杆压力设定——根据图面设定压力,与设计协商(经过计算)
3.素材摆放位置确认
素材放在压边圈上,根据模仁形状初步设定素材位置,并划线作为标记
4.管理面间隙确认
A.先压出阻条痕迹(没有阻条怎么办?)
B.素材管理面位置涂红丹
C.采用分段拉延的方法确认管理面间隙、观察素材走料状况
5.板件成型下死点前10mm观察并确认板件的褶皱发生与破裂发生,参照板件褶皱与破裂发生的简单对策
5)钻行程螺栓孔。
6)以上完毕后,在行程螺栓的位置把压边圈锁紧固定。
6、组好后,准备加工
7、如果模仁、压边圈,上模有镶块的情况。
1)将磨好的钢块与机能无关的棱角倒角C2.
2)清理钢料,将钢块与安装面和背托面进行研磨,用红丹检测,85%以上的接触率要均匀,间隙MAX0.03。
3)有定位键的要先配好定位键。
10.扣除料厚后,抛光。
11.再次试模,确认成形极限。平衡块高度,模具高度确认
12.试模完成
13.如果是镶块的拉延模具,就要送出热处理
1),热处理前做如图处理
2),热处理回来后,做平面度研磨。组立。
3),合模确认各部位间隙。
4),再次试模确认。
C研磨抛光后要预留刀花0.02-0.04以保证精度,特别是基准面及板件搭接面。
2)R角研磨抛光
拉延类模具三维设计流程

PPT文档演模板
拉延类模具三维设计流程
•利用基准面进行装配位置的调整,图中为调整 定位板位置。
PPT文档演模板
拉延类模具三维设计流程
装配完各种标准件后,压边圈的基本结构就已经清楚了。但由于 我们的标准件是装配进来的,其安装部分也是装配进来的,而它
们本来属于铸件,而且可能还需要和模具本体进行布尔运算。所 以我们必须运用ASSEMBLIES 中WAVE GEOMETRY LINKER命 令将装配进来的标准件中属于铸件的部分LINK到模具本体上。
w 由于压边圈上的挖空大部分是侧挖空,所以先通过草图中的各个 曲线拉伸出下底板,导腿。
w 调整局部可能需要补出的下挖空。圈的铸件轮廓基本完成。如图:
PPT文档演模板
拉延类模具三维设计流程
装配标准件,运用ASSEMBLIES 中ADD EXISTING COMPONENT命令
w 压边圈中的导板、起重棒、定位板、调整垫块等标准件的安装是 通过装配命令来实现的。装配时应注意用基准面进行位置约束。 图示为装配刚刚开始时,导入起重棒。
PPT文档演模板
拉延类模具三维设计流程
从起重棒上 LINK过来的 补肉,可以与 模具本体进 行布尔运算
标准件的安装不可能一步到位,许多标准件如定位板,调
整垫块,导板等位置需要经常调整,而且这些标准件与铸件结 构有很多的关联。LINK过来的部分是与标准件有关联的,会 跟随标准件位置的变化而变化,因而无需另外调整。
PPT文档演模板
拉延类模具三维设计流程
LINK完成以后,可以将原标准件上的此部分移动到不可见的图 层中,此时LINK的部分就可以与模具本体进行布尔运算了。
w 将压边圈,上模和下模装配为一个文件。
w 出工程图。
拉延模的工作原理
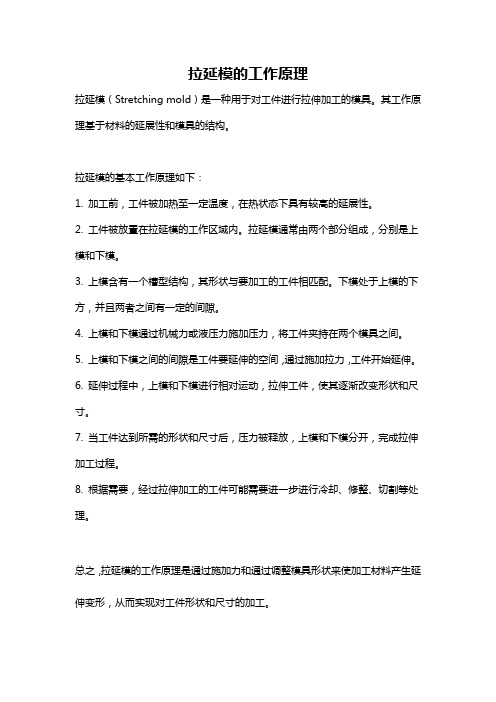
拉延模的工作原理
拉延模(Stretching mold)是一种用于对工件进行拉伸加工的模具。
其工作原理基于材料的延展性和模具的结构。
拉延模的基本工作原理如下:
1. 加工前,工件被加热至一定温度,在热状态下具有较高的延展性。
2. 工件被放置在拉延模的工作区域内。
拉延模通常由两个部分组成,分别是上模和下模。
3. 上模含有一个槽型结构,其形状与要加工的工件相匹配。
下模处于上模的下方,并且两者之间有一定的间隙。
4. 上模和下模通过机械力或液压力施加压力,将工件夹持在两个模具之间。
5. 上模和下模之间的间隙是工件要延伸的空间,通过施加拉力,工件开始延伸。
6. 延伸过程中,上模和下模进行相对运动,拉伸工件,使其逐渐改变形状和尺寸。
7. 当工件达到所需的形状和尺寸后,压力被释放,上模和下模分开,完成拉伸加工过程。
8. 根据需要,经过拉伸加工的工件可能需要进一步进行冷却、修整、切割等处理。
总之,拉延模的工作原理是通过施加力和通过调整模具形状来使加工材料产生延伸变形,从而实现对工件形状和尺寸的加工。
拉延模的设计过程

1.打开已建好的目录文件(即目录样本)
打开总装配
2.按“M”或者”ctrl+M”快捷键进入建模状 态
3.打开装配导航器即可对结构树进行操作
在这两种状态下均可进行图 形的设计;在“设为工作部件” 后,双击要操做的part,则其 他part将变暗,但仍可进行结 构间尺寸测量,曲线提取,等 功能的操作,从而使part之间 相结合设计
也可通过以下选项将凸直接拉伸至型面形状
在原有体上建模,选择布尔运算做出结果
草图的基本命令已讲过
附图:
在这两种状态下均可进行图 形的设计;在“设为显示部件” 后,则窗口只显示当前part其 他part将不显示
4 .画图前 DL 数据导入
4.1 将DL数据导入结构树中“DL”下
常见的数据导入 形式(即可直接 导入)
4.2 各part中所用到的片体及线体信息也按照以上步骤导入
5.在草图环境下设计,
画图前先建立基准平面
基准平面在UG中单独有此命令 ,各实体操作命令在进入草图后都有基 准平面此项选择,设计时可直接选用。 (基准平面的建立已讲)
注意:
按这种方法建立相 关联的基准平面,从 而使依附这些基准 平面建立的结构体 参数关联,可编辑
6. 片体缝合
7. 片体偏置
8. 结型面形状
拉延模

1. 什么是拉延将平板料,在拉延成型过程中,产生塑性变形,从而获得所需几何形状制件的冲模拉延在冲压件中的用途采用拉延工艺,能使板料拉延成为不规则的形状的制件;如:筒形,梯形,锥形,球形,盒形等拉延的基本过程拉延模是由凸模,凹模,压边圈三部分组成的,其凸模与凹模的结构和形状与冲裁模不同,他们的工作部分没有锋利的刃口,而是做成圆角(利于板料的流动)。
凸模与凹模的间隙大于板料的厚度。
在拉延开始时,凹(上)模首先形成往下至压边圈,将板料压紧在延边圈的压料面上,继续行程往下;此时拉延开始,板料通过凹模圆角经凸模拉入凹模,直至下死点,拉延成凸模形状,拉延完成。
拉延的过程是使板料的每一小单元体内产生内应力,在内应力的作用下,产生应变状态,使得板料产生塑性变形的过程;获得较好的刚度的制件。
2拉延模设计程序2.1依据冲压工艺的工序数型,冲压工艺的工序卡(参数,数据),涉及构思图(结构形式)。
2.2确定结构形式凹(上)模与凸(下)模导向A.上凹(上)模与凸(下)模的导腿(三面)导向。
B.上凹(上)模与凸(下)模得导板(长导板)导向。
C.凹(上)模与压边圈导向:凹(上)模与压边圈(导腿)导向压边圈与凸(下)模导向:A. 压边圈与凸(下)模的内导向B. 压边圈与凸(下)模的外导向2.2.2凹模的作用凹模的主要作用:是通过凹模压料面和凹模圆角进行拉延压边圈的作用:主要是起压料作用。
板料被压边圈的压料面与凹模的压料面压紧。
在拉延过程中,拉延变形区的板料凸缘部分的料仅在压边圈的压料面与凹模压料面的间隙中通过3确定定位形式A.封闭定位(一周)B.三面定位4 确定定位装置导轮定位,挡料板,翻转定位等5 确定调压块的位置及数量依据压边力,且沿压边圈的压料面的轮廓,布置调压块的位置及数量。
6确定气顶孔的位置及数量根据客户提供的冲床(设备)参数,依据压边圈压料面的轮廓尺寸,确定气顶孔的位置及数量(尽量靠近压边圈的内轮廓)。
7确定限程装置的位置及数量A.依据结构的形式,限程装置的位置均布。
拉延模(DR)设计流程

拉延模(DR)设计流程一、工艺图分析01.板料线:指的就是拉延坯料(毛坯钣金)的尺寸大小02.分模线:指的就是压边圈和凸模的分界线(侧壁和法兰面的交线)03.到底标记:目的就是检测产品在拉延的时候,到底拉延到位了没,拉到底了没,根据产品拉延痕迹的深浅钳工很方便就可以判断出来,一套模具放2个到底标记(有些大模具放3~4,具体个数请看工艺图),到底标记我们安装在上模,到底标记超出上模型面0.3mm,直径一般是Φ16,有些客户用Φ13,具体看工艺图上给的是多大就用多大的,misimi型号DCBA16。
如下:工艺图04.左右标记:就是给产品打logo用的(产品有左右两个产品),在产品上刻一个标记以便于产品区分,左产品刻L,右产品刻R,一般刻在外表面,方便观察,具体刻字及大小尺寸看工艺图,左右标记超出型面0.3mm05.拉延收缩线:指坯料拉延后收缩的尺寸大小(板料最终的位置),如下:工艺图06.拉延筋:目的用来控制材料(坯料拉延时)的流动速度,常见的有起皱(流动速度太快),破裂(流动速度太慢)07.CH孔:后工程模具(比如:修边、冲孔)用来研模型面用的,保证拉延后(回弹)的钣金能够与后工程模具型面保持一致,内板件做φ10,外板件做φ6,CH做盲孔(没有打通的孔)还是通孔看客户的要求,工艺图有CH孔就做出来,没有就不用做(有的公司工艺图上有CH孔,也不做出来,因为后面有整形)08.排气孔:我们一般设置在凹模的凹处,内板件做φ6,外板件做φ4目的是为了能够把凹模凹处里面的气体及时排出去,保证拉延质量,把凹模打通就可以二、结构设计拉延模按导向可以分为3种:内导(压边圈与凸模导向)+外导(压边圈与下模座四角导向)+腔体导(压边圈四周与下模座导向),腔体导用的极少,所以这里不做讲解,我们重点是内导和外导拉延模(单动)结构分为:上模+下模+压边圈+凸模等四部分09.模具导向用内导还是外导?如何选择?〓〓〓内导结构〓〓〓a.内导结构:凸模导向精度比较高,模具结构比较小,省钱,压边圈受侧向力(不适合压边圈受侧向力比较大的结构)b.我们尽量选择内导(省钱凸模精度高)c.什么情况下用内导?凸模好放导板/压边圈受侧向力比较小的情况我们就用内导d.内导结构:是凸模(导板安装在凸模上)与压边圈导向〓〓〓外导结构〓〓〓a.外导结构:一般就是内导不好导向之后,考虑外导,外导结构比较大(相对于内导),所以成本比较高,压边圈受侧向力比较稳定,但凸模导向精度低点b.什么情况下用外导?内导用不了的情况下就用外导,比如:凸模导板放不下情况下就用外导比如:凸模型面落差比较大情况下就用外导(压边圈侧向力大)c.外导结构:是压边圈(导板安装在压边圈上)与下模座四角导向10.模具用整体式还是镶块式结构?如何选择?〓〓〓当料厚t<1.2a.压边圈(整体式MoCr)+凹模(整体式MoCr)+凸模(整体式MoCr)+下模座(HT300)〓〓〓料厚t>1.2或抗拉强度比较大的板a.压边圈(镶块式...)+凹模(镶块式...)+凸模(整体式MoCr)+下模座(HT300)整体式:一般指的板料比较薄,或者板料强度比较软的材质(压边圈+凹模)镶块式:一般指的板料比较厚,或者板料强度比较硬的材质(压边圈+凹模)凸模做镶块:一般是材质硬料厚比较厚型面比较复杂11.压边圈行程计算?保证板料放在压边圈(分模线外面的型面)上面不会碰到凸模(分模线里面的型面)且空有10左右mm余量,注意压边圈行程只能是5或0尾数模拟方式如下(用分模线外面片体整体往上移动超出凸模(不动)10mm左右,移动的行程就是压边圈行程,行程取0或5尾数,如10、15不要取11这样的行程数)12.顶杆数量计算:11-01单个顶杆可以提供4T-5T的力,所以说顶杆数量=压料力/5T,然后考虑受力均匀(对称),力尽量比理论压料力大一点压料力计算:PB=SB(mm)×γn(kg/mm2)×T(mm)注:SB压边圈面积(mm2)γn系数T:板厚(mm)内容γn例以拉深为主体的零件0.15W/HOTR、FRPILLER OTR一般件0.22T/GOTR、DOOR INR etc 以拉延为主体的零件0.29DOOR OTR、HOOD OTR11-02氮气弹簧极限取氮气弹簧行程的80%(大部分是KALLER,其次DADCO) 13.凸模(长度):小模具<1000,1000<中<2000,大模具>2000【通过凸模长度确定好了模具是小模具后,我们可以度确定压边圈宽度】14.压边圈宽度确定(单边宽度):板料线+压料区域(15中小模具~20大模具)+平衡块(60小+70中+80大)+10(安装面)+20空面(退刀面)=========【到了这一步就可以开始压边圈和凸模设计】=============== 15.凸模设计(★★★★★)15-1.创建基准平面XY平面,距离-600左右,把分模线投影到XY平面上,然后把投影的曲线优化一下(编辑曲线参数)15-2.把刚才投影的曲线(15-1)拉伸出一个实体,超出型面(片体)即可15-3.通过修剪体(或者拆分体)把实体(15-2)修剪掉,保留下面部分15-4.把工艺片体大致偏置-50(向下),凸模做50型面肉厚,15-5.用偏置曲线(勾选大致偏置)把之前投影好的曲线(15-1),往里面偏置10(做空刀),15-6.用编辑曲线参数(原有),把刚才偏置的曲线(15-5)优化一下15-7.偏置好的曲线(15-5),拉伸出一个实体,往外偏置26(大于10就行)15-8.用修剪体修剪实体,保留下面,再跟凸模求差这样空刀面就做出来了(铸件空刀面做10)15-9.把曲线(15-5)往里大致偏置40,之后编辑曲线参数优化这条曲线,15-10.偏置40的曲线拉伸一个实体出来,用片体(15-4)修剪实体,保留下面部分,然后求差15-11.导板安装面比导板单边加大5(目的是为了防止铸件缩水导致导板后面悬空),安装面底部凸出10,底部高度3015-12.导滑面上面低于导板10,下面超出超出导板15,下面倒圆角R5,压边圈往上抬一个行程之后,导滑面与导板接触50左右15-13.导板安装面到凸模肉厚40-50左右,15-14.导滑面为什么要超出导板?为了后期钳工好调整导板间隙15-15.凸模大小确定:凸模长度<1000,就是小模具,<1000<凸模长度<2000,就是中模具,>2000就是大模具15-16.导板放在凸模的1/6处15-17.导板安装面超出分模线5左右,目的是为了刀具能够下去加工安装面15-18.凸模高度确定:导板安装面到凸模肉厚40~50+安装面高度+安装面底部30+15安装面底部到凸模底部距离15-19.副筋做30厚,主筋做4015-20.筋之间的距离做到300内最好15-21.起吊牙安装面:必须在分模线里面5mm左右即可目的是为了防止压边圈和凸模干涉,起吊牙大小起步M16及以上15-22.定位键(凸模下面一般放3个键):目的是用来干嘛的?一来:钳工能够快速找到装配基准,二来:键是可以防侧向力凸模定位件做明键,目的是为了钳工好装配凸模上需要加两个销钉孔,用来精定位,挤紧凸模,后期模具修模可以用来作为加工基准15-23.凸模锁付,小模具6个,中大型8个,锁付块单颗螺丝的50宽,超出分模线50左右,要打螺丝和销钉的宽度做80,超出分模线50左右,销钉做对角线上16.压边圈设计(★★★★★)=======宽度确定(单边)==========板料线+压料面(15mm小模具~20mm中大模具)+平衡块(60小+70中+80大)+10平衡块安装面+20退刀面16-1.板料线拉伸实体,超出片体即可16-2.16-1拉好的实体按16-1要求把压边圈宽度偏置出来(4个面都要偏置)16-3.把片体扩大,超出16-2实体,用工艺片体修剪实体,保留下面16-4.用板料线拉伸实体(记得超出上面实体16-3)+单边加大15(小模具压料型面)16-5.用16-4实体拆分16-3实体,然后删掉16-4实体,留下压边圈里外实体16-6.工艺片体往下大致偏置20,然后用大致偏置20的片体修剪16-5外面的实体(压边圈外面的实体),保留下面(就是平衡块安装部分),然后16-5两个(压边圈里外实体)实体求和16-7.用分模线拉实体出来,超出16-6实体,往外偏置3mm(凸模与压边圈间隙),然后求差(16-6实体与16-7实体)16-8.用分模线拉实体出来,超出16-7实体,往外偏置13mm(压边圈10mm 空刀),然后用工艺片体往下大致偏置50,用偏置出来的片体修剪刚刚拉伸出来的实体,保留下面,然后再与实体(压边圈)求差,压边圈10mm的空刀面就出来了16-9.压边圈底面替换到导滑面底面16-10.把顶杆位置数量确定好(拉实体方便观察),16-11.顶杆位置确定好了,就可以挖压边圈导滑面避位(导滑面左右35,靠近压边圈里面两边倒R30角,上面留35),再与压边圈实体求差16-12.凸模导板安装面可以与凸模求和,起吊牙安装面也可以与凸模求和16-13.工艺片体往下大致偏置60(做压边圈面板40厚),然后用偏置出来的片体拆分实体压边圈16-14.压边圈底部里面一圈线连接起来,往外面偏置曲线40(做40厚主筋),编辑曲线参数优化曲线,然后拉伸片体(实体)拆分实体压边圈(下面部分),然后压边圈下面外面部分从底部拆分40厚的主筋,上下里3个实体求和(压边圈求和)16-15.平衡块:小模具平衡块60+10安装面,厚度10mm,平衡块安装面比型面要低5-10mm,平衡块安装面离型面20mm距离,目的是为了刀具在加工平衡块安装面的时候方便退刀,平衡块可以保证压边圈受力均匀,提高拉延的稳定性,同时试模钳工可以用来调整进料阻力,16-16.平衡块之间的距离做到300左右(不是死的可以根据模具适当调整距离),平衡块要考虑受力均匀16-17.平衡块下面必须有筋支撑,顶杆位置也要有筋支撑,筋做30厚16-18.平衡块下面是蹲死块,蹲死块是安装在下模,位置大小和平衡块一样,底部要有筋支撑16-19.顶杆垫块:我们一般用两颗螺丝的型号,防止垫块转动,上面有筋支撑17.凸模锁付,对角要做两个销钉,用来精定位的,挤紧凸模,修模找基准定位键一来是给钳工用来找装配基准的,二来可以防侧向力18.压边圈卸料螺钉计算:80(不变的)+行程(变的)+20(不变的)安全余量19.安装面我们一般直径做0或5的尾数20.压边圈卸料螺钉放4个(在四个角落)21.卸料螺钉过孔单边加大1mm22.端头导板之间的距离取压边圈宽度的1/2~2/3之间23.端头要做防呆设计,宽度单边缩小10mm,目的是防止钳工(现场人员)装反模具(旋转180)24.外定位定位面与板料线对齐,外定位直线部分做到10-15mm,并且外定位直面底面在压料面下面,防止板料卡在里面,拉断外定位板25.起吊棒(4个)能够承受2套模具重量,四面补强50mm厚,里面补强30厚26.铸件与铸件做15避位间隙(凸模与压边圈),铸件与钢件做10避位间隙,钢件与钢件做5避位间隙27.下模设计(★★★★★)27-01.压板宽度做到120mm,厚度50mm27-02.压板槽宽度40,深度40,台阶面10,单边25,27-03.T型槽尽量选择距离比较远的,受力面积比较大,27-04.副筋30,主筋40(受力的地方),模座外面一圈都是主筋40副筋之间的距离一般在300内(300不是固定的)27-05.副筋到压板槽之间的距离做到100左右,如果空间不够做到80左右27-06.凸模受力筋(主筋最外面一圈就是)支撑到底,下模座要做出来,上模座也要做出来27-07.平衡块下面就是蹲死块,蹲死块下面必须有筋(30厚副筋)支撑,局部加强区域做到受力面2/3就可以28.上模设计(★★★★★)28-01.上模设计:用压边圈外形(宽度一致,长度和端头对其,简单理解为平衡块的安装区域面)创建实体出来(创建方块命令),28-02.把工艺片体打开,扩大面(修剪延伸),保证工艺片体超出01实体,然后进行修剪,保留上部分28-03.再用压料型面区域创建实体,拉伸实体超出02实体(创建方块),然后把02实体进行拆分,拆分完厚删除刚刚拉伸的实体28-04.再用工艺片体往上大致偏置20,用大致偏置20的片体修剪上模外面部分,保留上部分,然后两个实体求和28-05.再用工艺片体往上大致偏置60然后修剪上模实体,保留下面28-06.上模主筋(最外面一圈)、副筋做出来,替换到机床上台面28-07.压板宽度120,厚度5029.外定位板:定位直面做到10-15MM(拉延模),修边模做到15-20MM(回弹)、定位板直面处底面要低于压料面5mm左右,目的为了防止板料跑到里面,拉延时候拉断外定位板30.导板窥视孔:基本上导板都要挖出来窥视孔,目的是为了钳工方便测量或者观察导板与倒滑面之间的间隙(导板间隙0.05mm)31.模具结构:上模小,下模大可以,上模大下模小不可以!!!32.贴字:F(前)+(→)送料方向+产品号+零件号+模具号+(OP10-DR)工序号+材质(HT300国产灰口铸铁FC300日本材质)(凸模材质MoCr国产=GM241M日本)修边模(铸件刀块材质是7CrSiMnMoV=空冷钢=日本ICD5)钢件刀块国产材质Cr12日本SKD11(DC53整形TD处理)美国D2 33.拉延模材质(整体式模具=凸模+凹模+压边圈材质MoCr+下模座TH300)(镶块式模具=凸模(MoCr85%+Cr12)+凹模(Cr12)+压边圈(Cr12)+下模座HT300)MoCr(铸件)Cr12(钢件)=SKD11(钢件)34.粗加工基准面:做L型加工基准面,目的是用来开粗加工用的35.三销孔:用来精加工模具或者后期模具修模找基准用的(铰出来盲孔+线割通孔(钢件))三销孔长度方向2个,宽度方向1个,三销孔尽量设置在高处,但是要考虑翻转损坏三销孔(我们就设置在低处)36.键槽:键槽大小28或32,具体大小看公司要求,目的是用来模具放在加工机台上时能够快速定位找到装配基准(机加工公用模板)37.百位线:上下模都要做,主要是用来加工底面时,控制加工量的,直径40,半圆形式表示,距离底面10038.V型槽:放在模具中心,加工时用来快速取中39.运输连接板:连接上下模,搬运(移模)的时候保证模具不会晃动,40.安全区域:100*100小模具,120*120中模具,150*150大模具有条件的情况下我们做10的凸台,没有条件就5凸台,目的是:就是试模工作人员使用的41.起吊棒处倒圆角(起吊处),倒R20,目的就是为了保护我们钢丝绳不会被直角面损坏42.到底标记:(misimi型号DCBA16)43.汽车四大工艺:冲压工艺+焊装工艺+涂装工艺+总装工艺44.英文简称:DR(拉延)+TR(修边)+PI(冲孔)+FL(翻边)+RST(整形)+CTR(侧修边)+CPI(侧冲孔)+CFL(侧翻边)+CRST(侧整形)+CAM(斜楔)+BEND(折弯)+SEP(分离)+BUR(翻孔)+BL(落料)45.销钉植入深度2直径46.快速定位孔:就用顶杆孔作为快速定位孔47.排水孔:直径φ40,开口向上的铸件就要做出来,一来清洗模具时水能够及时排出来,二来冲压的时候机床上流下的油液能够及时排出48.拉延模板料定位用外定位板来定位,到了修边模就可以用型面和外定位板来定位,翻遍整形模可以用型面和定位孔以及外定位板来定位。
拉延模的工作原理

拉延模的工作原理
拉延模是一种用来模拟材料在受力作用下的延伸或收缩过程的装置。
其工作原理可以简单描述如下:
1. 材料加油:首先,拉延模中的材料被夹持在两个夹具之间,夹具可以施加外力来实现拉伸或压缩。
这些夹具可通过螺杆或液压系统等机械装置来调节距离和施加的力。
2. 施加外力:接下来,外力被施加到材料上,使其开始产生应力。
外力的大小和方向会影响材料的延伸或收缩。
3. 监测变形:在施加外力的过程中,可以使用传感器来监测材料的变形情况。
这些传感器可以测量材料的形变、应力或应变等参数。
4. 记录数据:材料的变形数据可以通过数据记录器或计算机程序进行收集和记录。
这些数据可以分析材料的力学性质、强度和可靠性等。
总结起来,拉延模的工作原理是通过施加外力到材料上,并监测材料的变形来模拟材料在实际应用中的行为。
通过分析变形数据,可以得出材料的力学性质和行为规律。
拉延模工作原理

拉延模工作原理
拉延模是一种在注塑成型中常用的成型方法,其工作原理是通过拉伸成型来改变材料的分子结构,从而使得最终产品的性能得到优化。
具体工作流程如下:
1. 注塑:首先,在注塑机中加热并熔化塑料原料,然后将熔化后的塑料通过注射喷嘴注入到模具的腔体中。
2. 完全填充:随后,以一定的压力将塑料完全填充到腔体内,在填充过程中,塑料流动受到注射速度、熔体温度、模具温度等参数的控制,确保塑料充满模具腔体。
3. 冷却:注塑过程完成后,开始对注塑件进行冷却。
通常采用的方法是通过冷却剂(如水)通过模具的水路进行循环,吸取塑料的热量,使其迅速冷却和凝固。
4. 拉伸模:当注塑件达到一定的硬度后,开始进行拉伸模。
拉延模的过程是通过施加张力,将注塑件沿着拉伸方向发生变形。
这使得塑料分子链在拉伸过程中进行排列和重组,从而使得最终产品具有更好的力学性能以及更高的材料密度。
5. 保持时间:在拉伸过程完成后,注塑件需要保持一段时间以使其保持形状。
这个时间一般取决于塑料的特性和产品的要求。
6. 退模:最后,通过开模装置将拉伸模后的成品从模具中取出。
总之,拉延模通过拉伸力的作用,改变塑料分子链的排列方式和结晶状态,从而使得产品的性能得到优化,同时也能改善产品的尺寸稳定性和表面质量。
拉延模制造流程
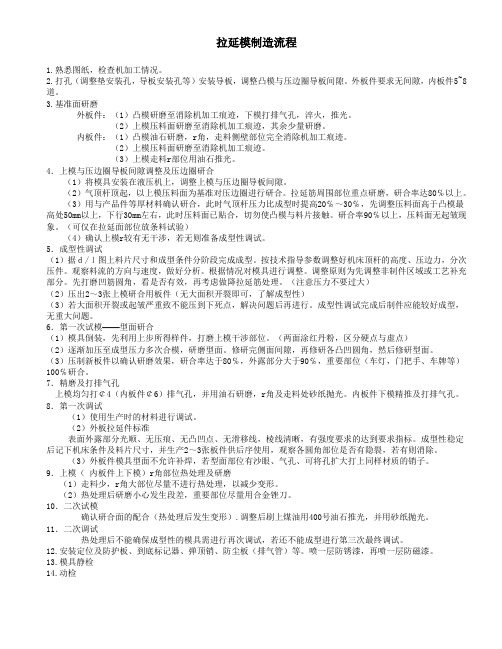
拉延模制造流程1.熟悉图纸,检查机加工情况。
2.打孔(调整垫安装孔,导板安装孔等)安装导板,调整凸模与压边圈导板间隙。
外板件要求无间隙,内板件5~8道。
3.基准面研磨外板件:(1)凸模研磨至消除机加工痕迹,下模打排气孔,淬火,推光。
(2)上模压料面研磨至消除机加工痕迹,其余少量研磨。
内板件:(1)凸模油石研磨,r角,走料侧壁部位完全消除机加工痕迹。
(2)上模压料面研磨至消除机加工痕迹。
(3)上模走料r部位用油石推光。
4.上模与压边圈导板间隙调整及压边圈研合(1)将模具安装在液压机上,调整上模与压边圈导板间隙。
(2)气顶杆顶起,以上模压料面为基准对压边圈进行研合。
拉延筋周围部位重点研磨,研合率达80℅以上。
(3)用与产品件等厚材料确认研合,此时气顶杆压力比成型时提高20℅~30℅,先调整压料面高于凸模最高处50mm以上,下行30mm左右,此时压料面已贴合,切勿使凸模与料片接触。
研合率90℅以上,压料面无起皱现象。
(可仅在拉延面部位放条料试验)(4)确认上模r较有无干涉,若无则准备成型性调试。
5.成型性调试(1)据d/l图上料片尺寸和成型条件分阶段完成成型。
按技术指导参数调整好机床顶杆的高度、压边力,分次压件。
观察料流的方向与速度,做好分析。
根据情况对模具进行调整。
调整原则为先调整非制件区域或工艺补充部分。
先打磨凹筋圆角,看是否有效,再考虑做降拉延筋处理。
(注意压力不要过大)(2)压出2~3张上模研合用板件(无大面积开裂即可,了解成型性)(3)若大面积开裂或起皱严重致不能压到下死点,解决问题后再进行。
成型性调试完成后制件应能较好成型,无重大问题。
6.第一次试模——型面研合(1)模具倒装,先利用上步所得样件,打磨上模干涉部位。
(两面涂红丹粉,区分硬点与虚点)(2)逐渐加压至成型压力多次合模,研磨型面。
修研完侧面间隙,再修研各凸凹圆角,然后修研型面。
(3)压制新板件以确认研磨效果,研合率达于80℅,外露部分大于90℅,重要部位(车灯,门把手、车牌等)100℅研合。
拉延模标准加工工艺(0912)

具工程有限公司
件号 序号 5 工序 名称 钳 零件名称 工
拉延模 标准工艺卡
装配 序 数量 内 容
制造令号 模具图号
材料 定位 热处理 加工 加工 加工 转 步 进 数 理论 刀具 尺寸1 尺寸2 尺寸3 速 距 给 量 工时 实际 工时
组装定位;组装存放器; 组装防护板; 组装托料架; 组装连接板; 10 15 热处理 表面淬火 型面R角、棱线热处理;检查硬度(硬度表) 钳 型面R角、棱线推顺抛光;凸模型面做好作为基准 型面研配;(见操作标准)以凸模为基准研配凹模型面 凸模、凹模型面推顺抛光 试冲件 油漆 检验 按技术要求油漆; 全面检查;(动、静检表) 开具合格证;
20 25
工艺编制:
校:
审核:
拉延模制造流程
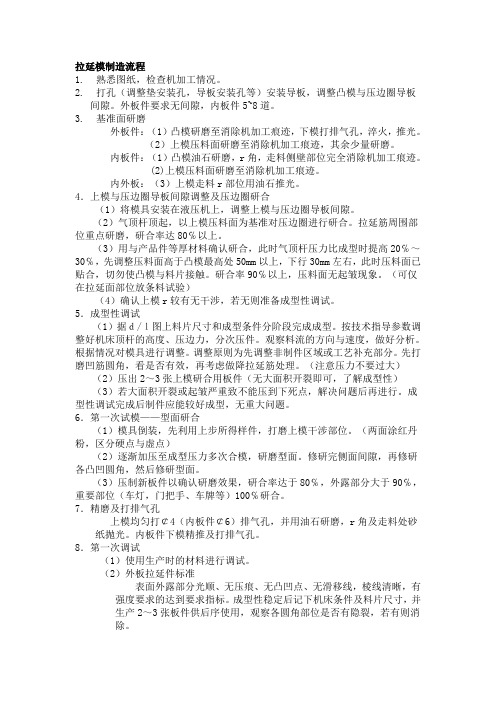
拉延模制造流程1.熟悉图纸,检查机加工情况。
2.打孔(调整垫安装孔,导板安装孔等)安装导板,调整凸模与压边圈导板间隙。
外板件要求无间隙,内板件5~8道。
3.基准面研磨外板件:(1)凸模研磨至消除机加工痕迹,下模打排气孔,淬火,推光。
(2)上模压料面研磨至消除机加工痕迹,其余少量研磨。
内板件:(1)凸模油石研磨,r角,走料侧壁部位完全消除机加工痕迹。
(2)上模压料面研磨至消除机加工痕迹。
内外板:(3)上模走料r部位用油石推光。
4.上模与压边圈导板间隙调整及压边圈研合(1)将模具安装在液压机上,调整上模与压边圈导板间隙。
(2)气顶杆顶起,以上模压料面为基准对压边圈进行研合。
拉延筋周围部位重点研磨,研合率达80℅以上。
(3)用与产品件等厚材料确认研合,此时气顶杆压力比成型时提高20℅~30℅,先调整压料面高于凸模最高处50mm以上,下行30mm左右,此时压料面已贴合,切勿使凸模与料片接触。
研合率90℅以上,压料面无起皱现象。
(可仅在拉延面部位放条料试验)(4)确认上模r较有无干涉,若无则准备成型性调试。
5.成型性调试(1)据d/l图上料片尺寸和成型条件分阶段完成成型。
按技术指导参数调整好机床顶杆的高度、压边力,分次压件。
观察料流的方向与速度,做好分析。
根据情况对模具进行调整。
调整原则为先调整非制件区域或工艺补充部分。
先打磨凹筋圆角,看是否有效,再考虑做降拉延筋处理。
(注意压力不要过大)(2)压出2~3张上模研合用板件(无大面积开裂即可,了解成型性)(3)若大面积开裂或起皱严重致不能压到下死点,解决问题后再进行。
成型性调试完成后制件应能较好成型,无重大问题。
6.第一次试模——型面研合(1)模具倒装,先利用上步所得样件,打磨上模干涉部位。
(两面涂红丹粉,区分硬点与虚点)(2)逐渐加压至成型压力多次合模,研磨型面。
修研完侧面间隙,再修研各凸凹圆角,然后修研型面。
(3)压制新板件以确认研磨效果,研合率达于80℅,外露部分大于90℅,重要部位(车灯,门把手、车牌等)100℅研合。
凸凹模以及拉延模做法
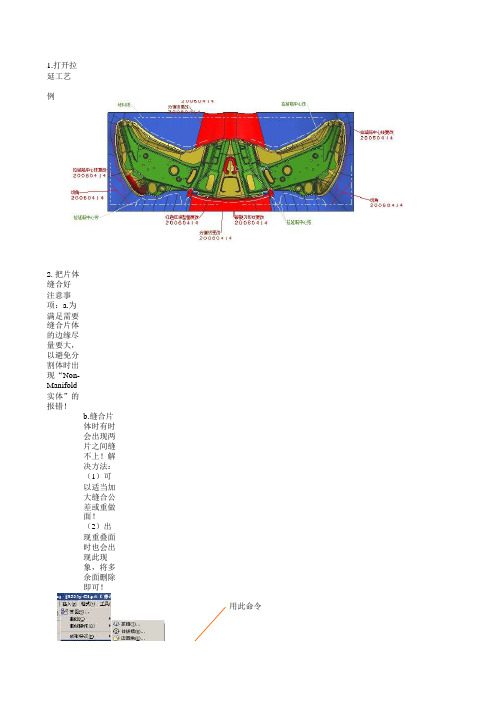
1.打开拉延工艺例2.把片体缝合好注意事项:a.为满足需要缝合片体的边缘尽量要大,以避免分割体时出现“Non-Manifold实体”的报错!b.缝合片体时有时会出现两片之间缝不上!解决方法:(1)可以适当加大缝合公差或重做面!(2)出现重叠面时也会出现此现象,将多余面删除即可!用此命令3.做一块体,在符合要求的情况下尽量做大以方便做模具时裁剪4.用‘分割体’命令将实体裁开5.用分模线‘拉伸’出片体,把实体分割。
凸模压边圈凹模绿色线为分模A.凸模的作法1.把缝好的片体‘大致偏置’50mm,把凸模裁开注意:最好先把坐标系沿Z轴转45度2.做凸模刃口。
把此面‘偏置面’向里偏10mm。
(如果偏不进去,可以适当休整一下复杂再偏。
)3.把大致偏置好的面向Z轴负方向移动10mm 用‘变换’命令做。
4.用移动好的片体把紫颜色的实体裁开。
5.将紫色实体裁开后,使型面壁厚为60mm。
裁开红色区域为刃口,高50mm 6.把型面部分和10mm厚的体‘并’在一起。
并7.把分模线沿Z轴投影到XY平面上。
8.用偏置曲线命令把投好的曲线向里偏置60(如果不给偏可以适当休整曲线)9.用拉伸命令拉出体10.用刚做出的实体面把紫色实体分割开。
多余部分去掉。
(选择裁剪面时,选做出的实体表面即可)11.把两块实体并起来。
12.四周做法兰螺钉一般为M16的12.做加强筋,挖减重孔。
(加强筋40厚)注意凸模下挖空的立筋上的减重孔必须是圆孔(孔径不要过大,最大不要超过100,最小40),不要方孔。
B.凹模的作法注:上面用过的命令在下面做图中就不讲了。
1.把坯料线沿Z轴投到XY平面上绿线为投好的线红线为坯料线2.用‘偏置曲线’把投好的线向外偏10mm3.用偏好的线拉伸出实体。
4.用作好实体四周的面将兰色体裁剪开。
5.把缝好的片体向下‘大致偏置’25,然后将兰色体裁剪开。
去6将兰色体去掉,把大致偏好的面向下复制35(用变换里的平移功能)7.用移好的面将绿色体和橘黄体裁剪开。
《拉延模结构设计》PPT课件
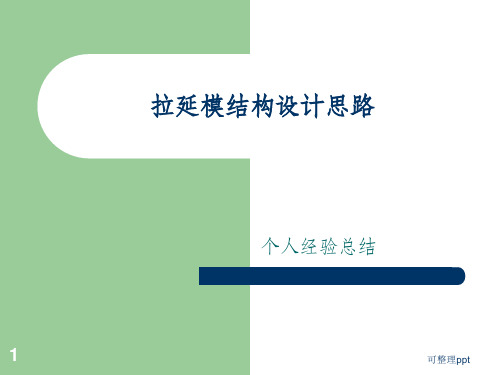
(2)还要考虑下模的整体强度及
起重装置(吊耳,起重棒等)
18
的空间
可整理ppt
气顶接柱接触面积〉 3/4(接柱整园面积)即可
19
可整理ppt
6.确定压料芯限程及坯料送料定位装置
确定压料芯限程 (1)一般采用退料螺钉限程, 外导向盒式导向模具多用限程板。 (2)限程距离=压料芯行程 +(10mm-20mm) (3)一般选用4个布在受力平衡的四角
流水孔一般为直径40的圆孔,设在模具型腔底部,并要保证 液体能流到模具外侧。
检查干涉,做出躲空。
25
可整理ppt
实体设计完成
26
可整理ppt
工艺更改可能对拉延模结构造成的影响
分模线更改 影响气顶的布置,凸模及压边圈支撑筋的位置,镦死垫的位置, 凸模及压边圈导板的大小及位置等
坯料线更改 影响压边圈及凹模压料面的大小,制件定位位置,调压垫的位置
(2)用坯料线外偏10-20MM确定压边圈 工作部分的轮廓(同凹模做法)
(3)确定刃口高度
刃口高度
50
压料面为二维曲面是高度一般为50MM
压料面为三维曲面是高度一般为60MM
(4)做出受力筋
11
可整理ppt
压边圈工作 部分
12
可整理ppt
3.布置调整垫块及镦死垫块
调整垫块布置(压边圈) (1)300MM-400MM均布 (2)调整垫块安装台的位置 距离压料面至少30MM (3)手动线时尽量保证垫块 的上表面在坯料面以下
拉延模压边圈行程〉制件拉延后最大落差+10mm
气顶数量=压边力/单个气顶所受力(3T-4T)+安全个数(0-4)
气顶位置的布置 (1)保证气顶均布在分模线外侧并尽量接近分模线 (2)尽量保证300MM均布 (3)尽量保证受力平衡
- 1、下载文档前请自行甄别文档内容的完整性,平台不提供额外的编辑、内容补充、找答案等附加服务。
- 2、"仅部分预览"的文档,不可在线预览部分如存在完整性等问题,可反馈申请退款(可完整预览的文档不适用该条件!)。
- 3、如文档侵犯您的权益,请联系客服反馈,我们会尽快为您处理(人工客服工作时间:9:00-18:30)。
1. 熟悉图纸,检查机加工情况。
2. 打孔(调整垫安装孔,导板安装孔等)安装导板,调整凸模与压边圈导板间隙。
外板件要求无间隙,内板件5~8道。
3. 基准面研磨
外板件:(1)凸模研磨至消除机加工痕迹,下模打排气孔,淬火,推光。
(2)上模压料面研磨至消除机加工痕迹,其余少量研磨。
内板件:(1)凸模油石研磨,r角,走料侧壁部位完全消除机加工痕迹。
(2)上模压料面研磨至消除机加工痕迹。
内外板:(3)上模走料r部位用油石推光。
4.上模与压边圈导板间隙调整及压边圈研合
(1)将模具安装在液压机上,调整上模与压边圈导板间隙。
(2)气顶杆顶起,以上模压料面为基准对压边圈进行研合。
拉延筋周围部位重点研磨,研合率达80℅以上。
(3)用与产品件等厚材料确认研合,此时气顶杆压力比成型时提高20℅~30℅,先调整压料面高于凸模最高处50mm以上,下行30mm左右,此时压料面已贴合,切勿使凸模与料片接触。
研合率90℅以上,压料面无起皱现象。
(可仅在拉延面部位放条料试验)
(4)确认上模r较有无干涉,若无则准备成型性调试。
5.成型性调试
(1)据d/l图上料片尺寸和成型条件分阶段完成成型。
按技术指导参数调整好机床顶杆的高度、压边力,分次压件。
观察料流的方向与速度,做好分析。
根据情况对模具进行调整。
调整原则为先调整非制件区域或工艺补充部分。
先打磨凹筋圆角,看是否有效,再考虑做降拉延筋处理。
(注意压力不要过大)
(2)压出2~3张上模研合用板件(无大面积开裂即可,了解成型性)
(3)若大面积开裂或起皱严重致不能压到下死点,解决问题后再进行。
成型性调试完成后制件应能较好成型,无重大问题。
6.第一次试模——型面研合
(1)模具倒装,先利用上步所得样件,打磨上模干涉部位。
(两面涂红丹粉,区分硬点与虚点)
(2)逐渐加压至成型压力多次合模,研磨型面。
修研完侧面间隙,再修研各凸凹圆角,然后修研型面。
(3)压制新板件以确认研磨效果,研合率达于80℅,外露部分大于90℅,重要部位(车灯,门把手、车牌等)100℅研合。
7.精磨及打排气孔
上模均匀打¢4(内板件¢6)排气孔,并用油石研磨,r角及走料处砂纸抛光。
内板件下模精推及打排气孔。
8.第一次调试
(1)使用生产时的材料进行调试。
(2)外板拉延件标准
表面外露部分光顺、无压痕、无凸凹点、无滑移线,棱线清晰,有强度要求的达到要求指标。
成型性稳定后记下机床条件及料片尺寸,并生产2~3张板件供后序使用,观察各圆角部位是否有隐裂,若有则消除。
(3)外板件模具型面不允许补焊,若型面部位有沙眼、气孔、可将孔扩大打上同样材质的销子。
9.上模(内板件上下模)r角部位热处理及研磨
(1)走料少,r角大部位尽量不进行热处理,以减少变形。
(2)热处理后研磨小心发生段差,重要部位尽量用合金锉刀。
10.二次试模
确认研合面的配合(热处理后发生变形).调整后刷上煤油用400号油石推光,并用砂纸抛光。
11.二次调试
热处理后不能确保成型性的模具需进行再次调试,若还不能成型进行第三次最终调试。
12.安装定位及防护板、到底标记器、弹顶销、防尘板(排气管)等。
喷一层防锈漆,再喷一层防磁漆。
13.模具静检
14动检。