铬铁3500KVA电弧炉袋除尘冷却器计算(冷却管按400mm计算)
硅 铁 炉 除 尘 方 案
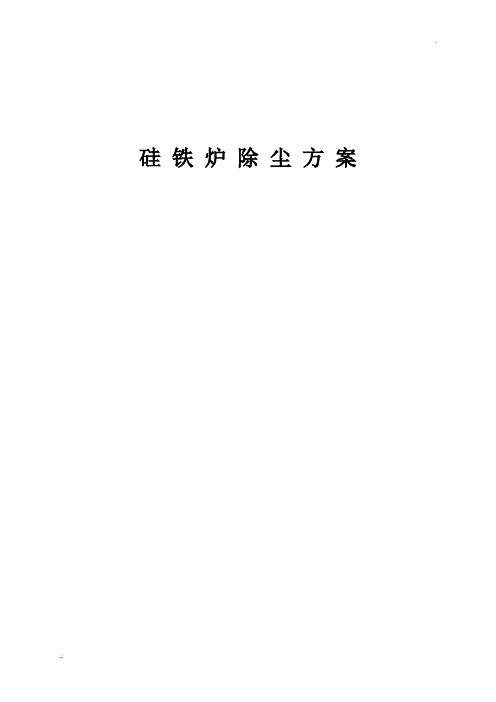
硅铁炉除尘方案前言大气污染是我国环境污染的首要问题之一,有地域的广阔性,污染的普遍性和排放物的多样性等特征。
在污染控制上难度大、技术复杂、投入多、运行困难。
我国的大气环境污染,特别是区流域性大气环境污染问题已经成为当前我国环境污染最具代表性的问题之一。
根据国家环保总局对我国大气环境污染现状统计调查表明:我国已普遍受到不同程度的污染,总体上呈现加重的趋势,造成污染加重的主要因素是工业废气和汽车尾气等。
我国工业废气污染主要以矿热炉烟尘污染为主,矿热炉烟尘是一种非常典型的工业废气,其特点是废气量大、温度高、烟尘浓度高、粒度非常小、部分有剧毒,直接排放对环境造成的危害非常大。
由于今年来一些发达国家对铁合金企业的限制,使得我国的铁合金企业如雨后春笋般的发展壮大,从而使得烟尘治理已成为现阶段国内大气环境保护技术领域垦待解决的一个问题。
一、硅铁电炉烟气的产生及性质硅铁冶炼过程中,电炉产生的废气主要包括:①电炉熔池在高温电热下,还原剂碳与氧发生反应生成CO和CO2;②熔池内碱性金属炉料在高温下气化、熔融金属被氧化或直接蒸发进人废气(随后冷却变成固态粒子);③未被完全燃烧的焦碳末、矿粉等被气化和蒸发的金属或热气流带出熔地进入废气;④在烟囱抽力的作用下,从烟罩敞口处进人的空气。
这些物质就构成了电炉烟气,也就是我们经常见到的浓浓的白色烟雾。
硅锰铁合金电炉在冶炼生产过程中排出大量的高温含尘烟气,烟尘主要成份是MnO和SiO2,烟尘粒径大部分小于5um,烟尘比重轻。
烟尘成分不是一成不变的,而是与炉料和炉况的变化密切相关。
二、贵公司两台硅铁炉工作排放情况1、目前硅铁炉在冶炼过程中,产生的废气除尘器不能有效捕集,超标排放严重。
除尘器负荷太重,效率低,滤袋破损率高,寿命短,两台炉同时生产时自由排放严重,工作环境十分恶劣。
2、粉尘性质:粉尘为金属类粉尘。
粒径较细,流动性差,堆集比重较轻,不易拔离,易造成循环负荷,水分较低。
三、除尘系统设计原则、依据A、根据炉废气粉尘的特点、工艺条件,选用先进的技术、可靠的设备、最优化的设计、高素质的专业施工人员,利用最短的时间保质保量、保证在最短工期内使除尘器安全、稳定、达标排放。
炼钢炼铁电炉除尘技术方案

化铁电炉除尘技术方案XXXX环保科技有限公司二0一二年五月化铁电炉除尘技术方案一、概况化铁电炉采用的原料是废旧钢铁,其中有一些是含有油漆的彩钢板,还有一些是含有机油、润滑油废钢铁,在进行投料的过程中产生大量的烟尘,现有的除尘系统采用布袋除尘器,不适合该场合使用,因此在工作一段时间后除尘装置失效,在车间内产生大量的扬尘,并通过车间门窗传出,这些烟尘不仅恶化作业化境,对工人的身体健康造成了很大的伤害,而且污染周围环境,造成不良影响。
选择合理的除尘装置不但能解决现有的环境污染问题,回收灰尘还还具有一定的利用价值,带来经济效益。
某公司化铁电炉,生产能力为每小时1吨,根据贵方的要求,现对其进行除尘处理.XXXX环保科技有限公司长期致力于锅炉烟气净化处理技术的研究,特别注重含尘含污气体的过滤除尘、吸附、化学治理、气体与液体介质的混合、碰撞、拦截、捕集的技术研究,在从气体中分离或还原气体污染物以及固体污染物上处于技术领先地位。
本公司为其设计除尘改造方案,并提供相关设备的制造和安装.二、化铁电炉除尘设计技术参数生产能力:1t/h设计处理烟气量:~12000 m3/ h处理烟尘浓度:~100 g/ m3(实际小于30g/ m3)烟气温度: 〈400℃三、执行标准GB9078—1996 工业炉窑大气污染物排放标准HJ462-2009 工业锅炉及炉窑湿法烟气脱硫工程技术规范四、烟气排放达到的要求按GB9078-1996 《工业炉窑大气污染物排放标准》熔化炉中的金属冶炼炉排放标准要求,本技术方案处理后的烟尘浓度达到小于100mg/m3,烟气黑度:格林曼一级。
在现有加料工艺情况下,不产生大量瞬时烟尘,允许有轻微烟尘漏出.五、除尘装置的技术参数处理烟气量~16000m3/h系统阻力<2500Pa液气比1:4每小时最小循环次数<2除尘效率〉99。
5%装置总功率25Kw六、除尘方案的选择1、常用的除尘方法对气体的除尘处理常用的方法有:机械除尘、湿法除尘、过滤除尘和静电除尘。
33000KVA硅铁炉除尘方案

33000KVA硅铁炉除尘方案一、除尘原理硅铁炉的除尘原理一般采用静电除尘、布袋除尘和湿式除尘三种方式的组合。
具体实施方案如下:1.静电除尘:通过高压电场产生静电,将粉尘带电,然后让带电粉尘在电场中偏转和沉积。
这种方式适用于小颗粒、高浓度的粉尘。
2.布袋除尘:通过布袋过滤材料,将烟气中的颗粒物截留在布袋上。
这种方式适用于中等颗粒、中等浓度的粉尘。
3.湿式除尘:将烟气通过喷雾装置,在烟气中添加湿润剂,使烟气中的粉尘湿润并沉降。
这种方式适用于大颗粒、低浓度的粉尘。
二、除尘设备的选择根据硅铁炉的特点和工况条件,可选用以下常用的除尘设备:1.静电除尘器:静电除尘器具有高除尘效率、低能耗、操作简单等优点。
可以采用带电极板或采用电子脉冲喷射清灰的方式,有效清除带电粉尘。
2.布袋除尘器:布袋除尘器具有除尘效率高、压降低、适用于高温和高湿度等特点。
可以根据具体情况选择合适的布袋材料和滤袋结构。
3.湿式除尘器:湿式除尘器适用于处理高温、高湿度、粘稠度大的烟气。
可以采用旋流湿式除尘器或湿式静电除尘器等。
三、操作维护除尘设备的操作维护对于确保除尘效果和延长设备寿命至关重要1.定期清理除尘设备:定期清理静电极和布袋,及时清除粉尘和堵塞物,确保正常运行和除尘效果。
2.检修除尘设备:定期对除尘设备进行检查和维护,包括清理电极、更换滤袋、维修喷雾装置等,确保设备的正常运行。
3.监测除尘效果:定期监测除尘效果,测量排放浓度,确保符合国家排放标准。
4.健全运行管理制度:建立完善的运行管理制度,包括设备操作规程、维护记录、故障处理等,确保设备的安全和有效运行。
31500KVA硅铁电炉方案

2×31500KVA硅铁电炉设计初步方案目录1 概述 (1)2 建设规模及产品方案 (1)2.1 生产规模 (1)2.2 产品方案 (2)3 原料要求及工艺计算 (2)3.1 原料 (2)3.2 辅助材料 (4)3.3 产量计算 (4)3.4 主要技术经济指标 (5)4 生产工艺 (5)4.1 生产工艺原理 (5)4.2 工艺流程 (6)4.3 生产车间组成及工艺布置 (7)4.4 电炉工艺参数 (10)4.5 主要生产设备 (11)5 公用及辅助设施 (12)5.1 土建工程 (12)5.2 电气 (13)5.3 自动化仪表 (13)5.4 给排水 (13)5.5 烟气除尘及余热回收 (14)5.6 机修、电极壳制造及化验 (14)6 劳动定员 (15)7 节能降耗 (15)8 环境保护 (15)9 投资估算及建设进度 (16)1 概述本工程新建2台31500KVA硅铁电炉,并配套相应公辅设施。
设计年产75#硅铁41000吨。
工程主要组成为:原料上料系统、电炉冶炼主厂房(熔炼跨、浇注冷却跨、成品跨)、除尘及余热利用设施、变配电室、循环水池及泵房、备品备件库、机修间、材料库、电极糊库、微硅粉库、地磅房、门卫室、综合办公楼(含化验室、食堂、职工宿舍)等。
硅铁是在电炉中用硅石、还原剂(兰炭、冶金焦等)、含铁料(钢屑)为主要原料而生产的产品。
冶炼采用31500KVA矮烟罩半封闭式炉型。
每台电炉采用HKDSPZ-10500KVA/110KV型变压器3台(本设计中电炉变压器按110KV进线考虑)。
主要工艺为:原料按配比进行配料,由皮带运输机运至加料仓,混合均匀后加入炉内,炉内电极深而稳地插在炉料中,通过电弧加热化学反应制得硅铁。
硅铁在电炉内连续埋弧无渣冶炼,定时出铁、浇注、冷却、精整、破碎、包装、入库外销。
2 建设规模及产品方案2.1 生产规模本工程拟建2台变压器额定容量为31500KVA的硅铁电炉,及与其配套的原料系统、除尘系统和其它公辅设施。
6300KVA高碳铬铁炉粗炼炉操作、维护、检修规程

6300KVA高碳铬铁炉粗炼炉操作、维护、检修规程1.1、设备主要技术参数额定容量:6300KVA 烟道:Φ1200mm炉型:矮烟罩、固定式电极行程:1400mm冶炼品种:高碳硅铁电极速度:500mm/min常用电压:120V(105-140共9级) 卷扬起重量:6吨常用电流:18000A 卷扬电机:电极直径:中780mm 出铁口风机、电机:极心圆:Ф2050±75mm 出铁口:1个炉壳直径:Φ7000mm 调压方式:电动无载调压炉壳高度:5000mm1.2、设备操作规程1.2.1、电极压放:电极工作端消耗后,每班需要压放1--2次,保持料面至铜瓦300mm左右。
出铁后停电下插某相电极至底,先松开9米平台上抱箍并将抱箍相对把持简上法兰上移需压放的长度(小于200mm/次)再锁紧。
与此同时,4米平台做好松同相铜瓦夹紧环的准备,接到9米人员通知,松开夹紧环,提升把持简使上法兰靠住抱箍下平面,锁紧铜瓦。
三相电极依次进行,压放过程中,要专人指挥,冶炼工(4 米、9 米)操纵工要密切配合。
1.2.2、电极升降:升降电极控制电流和负荷,在送电生产过程中采用点动升降。
不得长动升降电极,注意电流变化,插电极时,要防止过流、卷扬钢丝绳松弛,升电极要防止上限位失灵,拉坏滑轮、钢绳等。
1.2.3、电极糊:当12m平台上电极壳离平台定位圈300mm左右时,须接长电极壳。
接电极壳要尽量对正筋片,将电极壳小端插入原电极壳(大端)约30mm,并使轴线垂直于楼面,接口处连续焊接,不得漏糊。
电极糊加入前要打断成150*150mm 以内,垂直匀称加入壳内,不得砸坏筋电、不得悬糊,根据电极消耗情况及时补充电极糊,保持糊柱高度约 2.5米,不得过高过低。
1.2.4、调压:根据冶炼工艺和炉况选择适当的二次电压。
调压应在无载(即停电后)进行,由当班冶炼班长指挥操纵工操作。
操作程序为:提升一点电极,按下分闸按钮,确认分闸灯亮,合闸灯灭,一次电压、电流指示为零后,再根据需要操作调压开关(上调或下调一级),在确认调压到位(电压级指示正确稳定显示)后,合闸送电。
12500kVA高碳铬铁炉技术文件

12500kVA高碳铬铁炉技术文件公司简介*****制造有限公司是专业从事冶金设备、环保设备、电力电子设备的研究、开发、设计、销售、安装、调试、铁合金工艺服务的高科技企业。
是一家专门从事冶金和化学工业电炉设备节能新技术、新产品开发的技术型企业。
我公司结合国内外技术开发研制的新型铁合金矿热炉,采用压力环代替锥形环技术、新型水冷电缆技术及锻造铜瓦,采用变压器出线端与铜瓦一对一的新型短网结构,使设备更先进、作业率更高。
采用液压和气动技术相结合的气囊抱闸技术,PLC控制,实现带电压放,使电极装置更加安全可靠,提高了电极系统的作业率。
大水套采用无磁不锈钢后,可大幅度降低电能损耗。
采用上述新型技术与装备的矿热炉目前在国内居领先水平。
我公司开发生产的矿热炉除尘装置,主风机上采用高温耐磨技术,并采用柔性启动方式开启风机。
整套装置采用PLC控制使装置的技术性能达到国内领先水平。
公司采用国际先进的管理模式,追求科学灵活的经营方式;奉行“用户至上、服务第一”的经营宗旨和“团结进取、诚信敬业”的企业精神,不断研究开发新一代冶金电炉和环保产品,全心全意地服务于冶金和化工企业。
公司拥有一批知识层次高、业务精通、经验丰富的工程技术人员和管理人才;尊重科学、尊重人才,注重引进国际先进技术的消化吸收和科技成果的转化以及售前、售后服务;为用户提供高效可靠、节能降耗的设备。
我公司的产品已被国内多家企业采用,以其先进的技术水平、精良的制造质量和完善的售后服务,创造了良好的经济效益和社会效益,受到用户的好评和信赖。
概 述12500kVA 高碳铬铁炉是我公司近几年吸收了国外设备的经验结合我国的产业政策具体情况推出的新型矿热炉,是我国矿热炉的优化产品,在国内处于领先水平。
我公司投标本项目的优势。
1、我公司多年来从事矿热炉、短网技术的研制、开发出同相逆并联的短网,修正平面布置短网,倒三角形短网,由于其具有短网阻抗低、三相不平衡系数低、功率因数高、节电效果显著。
(仅供参考)冷却器的计算公式
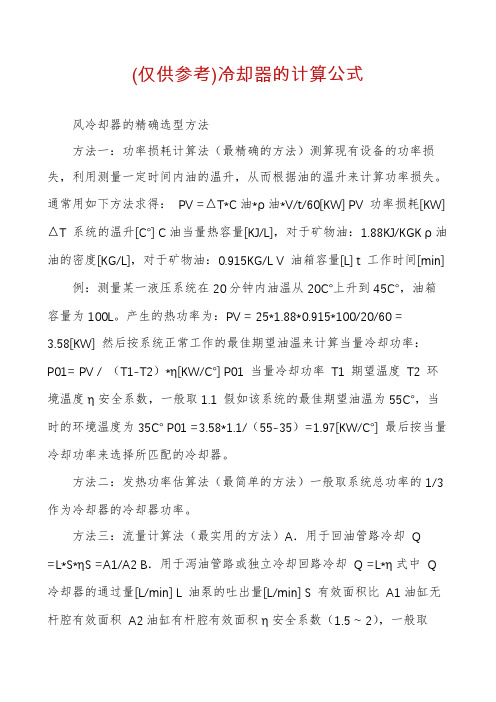
(仅供参考)冷却器的计算公式风冷却器的精确选型方法方法一:功率损耗计算法(最精确的方法)测算现有设备的功率损失,利用测量一定时间内油的温升,从而根据油的温升来计算功率损失。
通常用如下方法求得:PV =△T*C油*ρ油*V/t/60[KW] PV 功率损耗[KW] △T 系统的温升[℃] C油当量热容量[KJ/L],对于矿物油:1.88KJ/KGK ρ油油的密度[KG/L],对于矿物油:0.915KG/L V 油箱容量[L] t 工作时间[min] 例:测量某一液压系统在20分钟内油温从20℃上升到45℃,油箱容量为100L。
产生的热功率为:PV = 25*1.88*0.915*100/20/60 =3.58[KW] 然后按系统正常工作的最佳期望油温来计算当量冷却功率:P01= PV / (T1-T2)*η[KW/℃] P01 当量冷却功率T1 期望温度T2 环境温度η安全系数,一般取1.1 假如该系统的最佳期望油温为55℃,当时的环境温度为35℃ P01 =3.58*1.1/(55-35)=1.97[KW/℃] 最后按当量冷却功率来选择所匹配的冷却器。
方法二:发热功率估算法(最简单的方法)一般取系统总功率的1/3作为冷却器的冷却器功率。
方法三:流量计算法(最实用的方法)A.用于回油管路冷却Q=L*S*ηS =A1/A2 B.用于泻油管路或独立冷却回路冷却Q =L*η式中Q 冷却器的通过量[L/min] L 油泵的吐出量[L/min] S 有效面积比A1油缸无杆腔有效面积A2油缸有杆腔有效面积η安全系数(1.5 ~ 2),一般取1.8,液压油黏度越大则安全系数越大。
对于需要配置或改装液压冷却系统的机动车辆,计算出液压系统单位时间内的热损耗,即系统的发热功率Pv,然后结合你需要的油温期望值T1,对照风冷却器的当量冷却功率P1曲线图,选择与之匹与的型号。
这是普遍使用的计算方法。
必须注意,在测定系统单位时间内油的温升时,要区分是否有冷却器在工作,该文所指的工况是系统没有冷却器时油的温升。
12500KVA碳素铬铁电炉有关内容及参数

电压等级
容量(KVA)
一次电压10KV
二次电压V
一次电流A
二次电流A
1
12226
721.7
52678
2
12500
137
721.7
52678
3
12500
140
721.7
51549
4
12500
143
721.7
50468
5
12500
146
721.7
mm
7600
3
炉壳高度
mm
4050
4
炉膛直径
mm
6100
5
炉膛深度
mm
2200
6
电极直径
mm
Φ1060
7
极心圆直径
mm
Φ2500
8
电极工作行程
mm
1200
9
最大行程
mm
1200
10
极心圆功率密度
KW/m2
2150
11
极墙距
Mm
1270
12
电极电流密度
A/cm
5.5
13
出铁口数
个
2
14
附加料管
个
1
三、变压器参数:
1、额定容量:12500KVA
2、额定电压:10KV-134-160V
3、额定电流:721.7A/45105A-53859A
4、相数:3相
5、频率:50HZ
6、调压方式:有载电动调压
7、连接组别:D, do或△/△-12
8、使用条件:户内
在5 MVA矿热炉中以300系列不锈钢除尘灰球为原料生产低镍铬生铁工业试验

sb egdac u c ,nod ror oe rc u e liecrmim, i e e . n es i ess e dd sn s u m re t mae i re e vr ei sm t k ho u nc l t a dt t n s t l eut g h f t c p o al k c h a l e i a
摘 要
中国
750 ) 3 10
为 开 发利 用 不 锈 钢 除 尘 灰 , 回收 铬 、 等 贵 重 金 属元 素 , 矿 热 炉 生产 低镍 铬 生 铁 进 行 了 工业 生产 试 验 。 镍 对 结
果 表 明 , 热 炉 冶 炼 30系 列 不锈 钢 除 尘 灰 球 , 但 解 决 了对 环 境 的影 响 , 矿 0 不 而且 还 能 够 通 过 回收 利 用 生 产 出 符 合 不 锈 钢 标 准 的 低 镍铬 生铁 , 有一 定 的社 会 和 经 济 效 益 , 行 工 业 生 产 是 可行 的 。 具 进 关 键词 除 尘 灰 球 矿 热炉 低 镍 铬 生 铁
常重 要 的环保 和社会 意 义 。
电炉 法冶 炼 中采用 中频 炉 居 多 ,冶 炼方 法也 只在专 利技 术 中略见 一斑 , 要 配加 红土 镍矿 , 直接 用压 且 而
球 进行 矿热 炉 冶炼 的工艺 技: 内尚未见 报道 。 术国
低镍 铬铁 生铁 简称 低镍 铬铁 , 主要 用 于不 锈钢 、 耐热 钢 、 工具 钢 的生产 。镍 、 铬元 素具 有 良好 的耐 热 性, 速发 展 的汽车 工业 也需 要大 量 的含镍 铬 铸件 。 高
前 言
酒钢 不锈 钢厂 日产 除尘灰 10t 右 , 0 左 自不 锈钢 投产 至 今一 直没 有得 到有 效 的处理 , 因其含 有 铬 、 镍 等物 质 , 对酒 钢及 嘉 峪关 市环 境造 成很 大 的危 害 , 随 着 不锈 钢 产 能 的增 加 ,除尘 灰 处 理 问题 1 严 重 。 3趋 铬 、 等 贵重元 素 , 镍 价格 昂贵 , 回收利用 具有重 要 的经 济 意义 。因此 不锈 钢 除尘灰 的循 环 再生 利 用具 有 非
提锌回转窑冷却面积计算

绝对温度
℃
298
V烟
实际排烟量
m3/h
120000
t1
冷却器入口温度
℃
250
t2
除尘器入口温度
℃
150
t3
环境温度
℃
20
V0
标准状态计算风量
m3/h
160268.5
VQ
设计选用风量
m3/h
174692.6
r1
烟气含尘量
g/m3
100
r
容量
kg/m3
0.425
c1
冷却器入口烟气比热 W/(h*kg*℃) 0.396
m2
80.07
冷却管至除尘器主管直径
m
1.385641 取
1.7
冷却管至除尘器主管长度
m
15
冷却管至除尘器主管冷却面积
m2
80.07
冷却管高 冷却管边缘间距 冷却管中心间距
冷却管组数
m
6
Hale Waihona Puke m0.8m
1.6
组
7.659606 取
10
c2
除尘器入口烟气比热 W/(h*kg*℃) 0.388
Q1 冷却器入口烟气产生的热流量
W
7350192
Q2 除尘器入口烟气产生的热流量
W
4321022
Q散
冷却器散发的热流量
W
3029170
d0
管道外径
m
0.82
d1
管道内径
m
0.8
n
冷却器排数
3
v
管道内气体流速
m/s
22.11607
v0
空气流速
真空自耗电弧炉铜坩埚的受热与冷却计算

真空自耗电弧炉铜坩埚的受热与冷却计算自耗电弧炉是一种使用电能将电能转化为热能的设备,其主要应用于熔化金属材料。
在电弧炉的操作过程中,铜坩埚在高温环境下进行受热和冷却,因此需要进行相应的计算。
首先,需要计算铜坩埚的受热过程。
在电弧炉工作时,电能将通过电弧传导到铜坩埚上,使其达到高温。
可以通过下述公式计算铜坩埚的受热速率:Q=m*Cp*(T2-T1)其中,Q为受热速率,m为铜坩埚的质量,Cp为铜的比热容,T2为铜坩埚的最终温度,T1为铜坩埚的初始温度。
接下来,需要计算铜坩埚的冷却过程。
在停止供电后,铜坩埚会通过自然冷却失去热能。
一般情况下,可以使用牛顿冷却定律计算铜坩埚的冷却速率:Q=-h*A*(T2-T1)其中,Q为冷却速率,h为热传导系数,A为铜坩埚的表面积,T2为初始温度,T1为环境温度。
以上是计算铜坩埚的受热和冷却的基本原理,下面将对具体计算过程进行详细说明。
1.计算铜坩埚的质量:铜坩埚的质量可以通过称重或从产品规格中获取。
2.计算铜的比热容:铜的比热容为0.386J/(g·℃)。
3.计算受热过程的能量:根据上述公式,计算铜坩埚的受热速率。
需要输入初始温度和最终温度,以及铜坩埚的质量。
4.计算冷却过程的能量:根据上述公式,计算铜坩埚的冷却速率。
需要输入初始温度、环境温度,以及铜坩埚的表面积和热传导系数。
5.根据受热速率和冷却速率的差值,可以得到铜坩埚在操作过程中的热能损失。
需要注意的是,以上计算仅为基本的理论计算,实际计算过程需要考虑其他因素的影响,例如电弧炉的具体工作情况、炉温的稳定性等。
此外,铜坩埚的材料和结构也会对受热和冷却过程产生影响,因此在实际运行中需要进行更为详细的计算和试验。
总之,铜坩埚的受热和冷却计算是电弧炉操作过程中的重要环节,可以通过理论计算和实验验证相结合的方法来得到更准确的结果。
这些计算结果对于保证电弧炉的正常运行和提高生产效率具有重要意义。
16500KVA高碳铬铁矿热炉粉尘收集系统-除尘设计方案

16500KVA铬铁矿热炉粉尘收集系统文件编号:XXX-XXXX-XXX技术方案目录公司简介 (2)单位基本信息.......................................................... 错误!未定义书签。
公司资质.. (3)工程质量保证 (4)售后服务及备品备件承诺 (5)第一章、16500KV A高碳铬铁炉除尘设计方案(正压) (6)一、概述: (6)二、设计依据 (7)三、除尘器设计选型 (10)四、除尘器结构简介 (15)五.操作简介 (22)第二章、施工组织设计 (23)一、施工内容 (23)二、施工组织结构 (23)三、施工组织措施 (25)四、非标设备制作及设备安装方案 (36)五、单机调试和系统整体联动调试方案 (39)第三章、工程报价: (41)附件:公司以往铁合金工程实列 (46)略略工程质量保证工程质量保修范围及质保期质量保修范围包括乙方提供的设备及备品备件。
质量保修期从工程实际竣工之日算起。
单项竣工验收的项目,按单项分别计算质量保修期,质保期一年。
质量措施乙方保证按照合同及相关附件约定精心组织施工,设备质量达到双方约定的要求。
合同签订后,指定专人负责本工程的项目,负责协调工程全过程的各项协调配合工作,如工程进度、制造设计、图纸文件、设备配套、包装运输、技术交底、人员培训,现场安装、调试验收等。
设备到货时业主及时到现场参加设备的清点和交接工作。
负责人安装全过程在现场,负责处理安装过程中的各种问题,接受甲方的监督,并对甲方提出的改正意见及时响应。
负责人处理现场出现的一切技术和商务问题,如现场出现质量问题,负责人员在规定时间内解决。
交接验收及性能测试工作结束后,双方签署会议纪要及工程验收合格等签证。
质量保证烟气排放长年达到<100mg/Nm3的国家标准,除尘器长期稳定可靠运行,随主机运转率达99%以上。
质量保修金的支付本工程约定的工程质量保修金为施工合同价款的 5 %。
33000KVA硅铁炉除尘方案

.XXXXXXX硅业有限公司33000KVA硅铁矿热炉除尘器设计方案中国·江苏江苏XXXXX制造有限公司二0一0年八月目录第一部分:技改方案第二部分:设备配置第三部分:项目报价第四部分:生产制造计划第五部分:质量控制计划第六部分:技术服务措施第一部分方案设计我公司根据贵公司计划的33000KVA硅矿热炉烟气除尘的有关数据及要求,结合当前铁合金行业矿热炉烟气治理技术发展状况和硅铁炉对微硅粉回收的特殊工艺内容,本着安全、高效、经济、合理、切实、可行的原则,确保投入的设备能长期、稳定运行, 现对该项目的设备选型及参数等方面提供如下方案。
一、预期达到的目标:1、烟气经综合除尘后达到环保要求即:50mg/m3以下。
二、设计依据1.本设计依据冶金工业部《钢铁工业烟气净化技术政策规定》第七章“铁合金电炉烟烟气净化”中有关规定。
2.废气排放执行GB9078-1996《工业炉窑大气污染物排放标准》中一级排放标准。
3.产生的噪声执行GB12348-90《工业企业厂界噪声标准》之规定,即厂界噪声白天≤65db,夜间≤55db。
4.《钢铁工业污染物排放标准》(有关工业炉窑部分)GB4911;5.《工业炉窑大气污染物排放标准》GB9078;6.《除尘设计手册》;7.《XXXXXXX有限公司产品说明书》;8.33000KVA矿热炉,矮烟罩、半封闭式排烟方式,通常情况下的烟气排放生产工艺参数:1、工况烟气量:480000m3/h.2、烟气温度:800-950 ℃ ;3、烟气含尘浓度:2-6g/Nm34、岗位粉尘浓度15mg/Nm3。
根据以上选择我公司的大型反吸风袋式除尘器LSF-20×800三、除尘器选择:(一)、正压反吸风除尘系统一、概述:由于采用矮烟罩硅铁电炉烟气出口温度较高,因此需采用U型空冷器对烟气进行降温。
电炉排放的烟气通过风管、U 型空冷器降温,同时,U型空冷器对粉尘起二沉降分级作用。
此时温度从800℃(极端9500C)降至250℃左右,再进入予处理器,进一步对烟气中所含粉尘进行沉降分级及降低烟气温度。
回转窑滚筒冷却器冷却风量计算方法
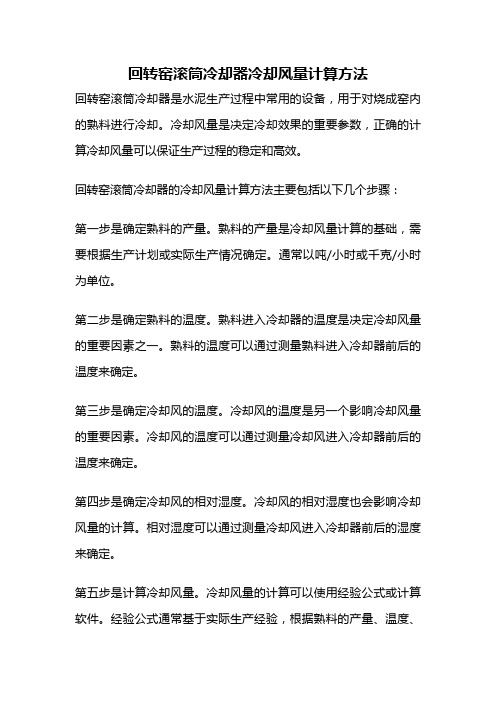
回转窑滚筒冷却器冷却风量计算方法回转窑滚筒冷却器是水泥生产过程中常用的设备,用于对烧成窑内的熟料进行冷却。
冷却风量是决定冷却效果的重要参数,正确的计算冷却风量可以保证生产过程的稳定和高效。
回转窑滚筒冷却器的冷却风量计算方法主要包括以下几个步骤:第一步是确定熟料的产量。
熟料的产量是冷却风量计算的基础,需要根据生产计划或实际生产情况确定。
通常以吨/小时或千克/小时为单位。
第二步是确定熟料的温度。
熟料进入冷却器的温度是决定冷却风量的重要因素之一。
熟料的温度可以通过测量熟料进入冷却器前后的温度来确定。
第三步是确定冷却风的温度。
冷却风的温度是另一个影响冷却风量的重要因素。
冷却风的温度可以通过测量冷却风进入冷却器前后的温度来确定。
第四步是确定冷却风的相对湿度。
冷却风的相对湿度也会影响冷却风量的计算。
相对湿度可以通过测量冷却风进入冷却器前后的湿度来确定。
第五步是计算冷却风量。
冷却风量的计算可以使用经验公式或计算软件。
经验公式通常基于实际生产经验,根据熟料的产量、温度、冷却风的温度和相对湿度进行计算。
计算软件则可以根据更为复杂的模型和算法进行计算,并考虑更多的影响因素。
在计算冷却风量时,还需要考虑一些其他因素。
例如,冷却器的结构和尺寸、冷却风的流速等。
这些因素都会对冷却风量的计算结果产生影响。
除了计算冷却风量,还需要对冷却器进行调整和优化。
例如,可以通过调整冷却风的流速和温度,改变冷却器的结构和尺寸等方式,来提高冷却效果和降低能耗。
回转窑滚筒冷却器的冷却风量计算是水泥生产过程中重要的环节。
通过合理计算和调整冷却风量,可以保证生产过程的稳定和高效,提高水泥生产的质量和产量。
同时,也可以降低能耗,减少对环境的影响。
因此,对冷却风量的计算和优化应引起足够的重视。
高碳铬铁物料平衡计算

一、物料平衡计算1、基本原始数据:直接还原铁成分、燃料成分见表一、表二(1)直接还原铁(2)焦炭成分(3)白云石白云石化学成分入炉白云石粒度20"80mnio(4)硅石入炉硅石的化学成分应符合表4. 2-10的规定。
表4.2-10 硅石化学成分入炉硅石粒度20^80mn)o2、直接还原铁耗碳量计算(以100kg计算)假设Cr以C G O J、Cr形态存在,Fe以Fe?()3 ,Fe形态存在,其中Cr2O;5 全部还原,Fe? 03 98%还原为Fe, 45%还原为FeO, Si022%还原,成品中含C 量为2%,加入焦炭全部用于还原氧化物,则耗碳量为:冶炼100kg铁矿消耗焦炭量为Me二耗 C 量/(Wc 固* (1-W 水))=11. 25/(84%*(1-8%))* (1 + 10%) =16kg 冶炼1吨髙碳絡铁合金需要直接还原铁量为M矿=1枫(Cr高碳貉铁水中质量比)/W (Cr矿中质量比)*还原率=1*62%/ (40. 18%) *98%=1.575 吨3、冶炼1吨髙碳鎔铁合金需要焦炭量为M 焦炭=16kg*l. 575*10=252kg4、渣铁比计算以100kg直接还原铁配16kg焦炭,假设元素分配按下表所示物料平衡中未计算P和S的平衡量,按高碳辂铁合金生产状况设定P和S的含量。
直接还原铁成渣量和成合金量见下表由于Cr /Fe=64/27 =2. 37,符合髙碳鎔铁生产的鎔铁比大于2. 2的要求,MgO/ Al203=(5 . 6+13 . 79)/13. 18=1. 47,符合高弹鎔铁生产的镁铝比大于1. 2 的要求。
铁水成分符合髙碳鎔铁FeCr67C6的标准。
表1高碳镒铁牌号的化学成分(GB/T 5683-2008)5、炉气生成量计算假设冶炼过程产生的炉气含CO量为100%,则100kg直接还原铁生成的co量见下表,即100kg的直接还原铁产生740. lmol的炉气。
12500KVA电炉高炭铬铁工艺

高炭铬铁工艺流程1选矿工艺简介本项目设计的铬矿原料主要原材料成分(业主保证):●Cr2O3含量:39~40%●Fe2O3含量:27~28%●砂矿粒度: 0.4mm(占砂矿总量92%以上)●湿度:6~8 %本项目中,一台12.5MVA矿热炉日产高碳铬铁61t,日消耗精矿量为140 t左右。
因为原矿品位很低,Cr2O3含量在39%左右,而达到生产需要的Cr2O3必须在45%以上。
故1.3t 以上原矿才能选出1t左右合格矿。
所以日处理原矿在190t 以上。
工艺流程见图一。
2造球工艺简介日产高碳铬铁61t,日消耗精矿量为140t左右。
即每天需造球140t以上。
每小时生产量在6t以上。
本设计采用三套造球设备,设备小时产量为4t,三套设备小时产量为12t,两套设备日产量为192t,三套设备日产量为288t,考虑到实际需要,可两套使用,一套备用。
工艺流程见图二。
3高碳铬铁生产工艺高炭铬铁以铬矿为主要原料,焦炭、兰炭作还原剂,硅石和镁质材料作熔剂,在镁砖内衬矿热炉内进行冶炼生产。
12500kVA矿热炉设一套配料仓,经造球处理的合格原料由装载机送至配料仓,然后经自动称量系统按批次配料,再由皮带机送至+15m平台炉顶料仓内,需要时炉料经料管靠自重下降和人工辅助推动布料。
为补充不断消耗的电极,电极壳和电极糊由3t 悬挂起重机从±0.0m提升至+20.5m平台上进行电极接长和添加电极糊。
矿热炉设两个出铁口,交替使用,12500kVA矿热炉每2h出一次铁。
熔渣和铁水同时从铁口流入铁包车上的铁水包内,熔渣再流入渣盘内,铁包车牵引至浇注跨,经20/5t起重机将铁水浇注成锭,经冷却后,由电动平车送精整跨,破碎加工,称量,包装,然后送成品跨存放。
熔渣经高压水冲渣系统水淬处理后,外销综合利用。
工艺流程见下图三。
图一选矿工艺流程图二造球工艺流程图三生产工艺流程图5.横幅有标明赞助商备注:赞助费达2000元的,商家可参与颁奖四、活动经费预算场地租用费 500元宣传展板 300元后勤、志愿者服务队、礼仪队 400元保安工作人员、秩序维护员, 0.00元宣传人员 200元设备:运动会所用器材使用费。
- 1、下载文档前请自行甄别文档内容的完整性,平台不提供额外的编辑、内容补充、找答案等附加服务。
- 2、"仅部分预览"的文档,不可在线预览部分如存在完整性等问题,可反馈申请退款(可完整预览的文档不适用该条件!)。
- 3、如文档侵犯您的权益,请联系客服反馈,我们会尽快为您处理(人工客服工作时间:9:00-18:30)。
铬铁3500KV A电弧炉袋除尘冷却器计算详细计算一基本情况1铬铁厂3500KV A电弧炉冶炼时产生大量高温烟气,目前由于风管长度短、散热面积小,散热能力不足,高温烟气经风管自然冷却降温后到达袋除尘进口时烟气温度不能降到滤袋正常使用温度范围,容易造成袋除尘滤袋在长期高温下烧毁或缩短使用寿命,若使用高温滤袋,滤袋成本会大幅度上升。
经实际检测,袋除尘进口烟气温度在120~263℃之间(按电弧炉功率计算,263℃的高温属于电弧炉炉口引风罩吸入冷风量较少时的非正常情况,此时风管内风量较小),尤其在引风机50Hz全速运行时袋除尘进口温度普遍高于130℃,超出袋除尘滤袋正常运行温度。
虽然风管上安装有冷风阀,高温时自动打开混入冷风可以起到一定的降温作用,但必然增加除尘系统的阻力,降小电弧炉引风罩口负压,使电弧炉产生的烟气不能全部进入袋除尘净化,造成烟气外冒污染操作环境。
另外,冷风的混入也加大了袋除尘滤袋的过滤风速、降低袋除尘的除尘效率和滤袋的使用寿命。
2 电弧炉冶炼时高温烟气的含尘量大,经检测袋除尘进口含尘量在1000~3000mg/m3(甚至有高达到13186mg/m3的含尘量),含尘浓度远高于袋除尘正常处理含尘量1000mg/m3的上限,造成袋除尘滤袋负荷过大、早期磨损破裂和过滤效率下降------从检测的袋除尘出口气体含尘量在132~260mg/m3范围结果也说明袋除尘负荷过大,排放不能达到50mg/Nm3的标准准要求。
(附品管部烟气检测表)3 为降低袋除尘进口烟气温度,达到现用常温滤袋的正常工作温度范围,降低袋除尘运长期运行的滤袋更换成本,极有必要在袋除尘前增加蛇形管风冷器降低袋除尘进口烟气温度,并增加旋风除尘降低烟气含尘量,以降低袋除尘滤袋寿命和提高除尘效率。
二电弧炉烟气放热量计算1基本参数电弧炉满载功率:3500kw,其一小时发热量3500 kwh,换算为1h的发热量为Q=1.26*107KJ;工况平均烟气量:83487 m3/h;(按烟气检查报告数据,剔除可能异常的最大值和最小值的平均值)折算为标况平均烟气量:53880 m3/h(用于根据其比热容计算烟气的放热量);工况平均烟气温度:150℃;(按烟气检查报告数据,剔除可能异常的最大值和最小值的平均值)工况烟气含尘浓度:1650/2495mg/m3;(分子为按烟气检查报告数据,剔除可能异常的最大值和最小值的平均值,分母为根据袋除尘灰斗卸灰量5t/24h的推算值,两者相差较大)烟气平均初温T1=172℃;(按电弧炉满载功率时1h放出的热量把通过引风管标况下的烟气计算,假设此时精炼时电极放出的热量量不参与冶炼的化学反应,只考虑炉体及铁水辐射、对流散失总热量的15%,可加热标况下53880 m3/h烟气最高升温152℃,检测期间气温20℃。
电弧炉出口引风管处冷风阀设置200℃没有打开过,说明烟气初温不超过200℃,也符合能量守恒定律,引风管中部冷风阀设定温度150℃,多次打开,说明引风管内烟气温度高于150℃,与理论计算及实测情况基本相符,实际计算时考虑预留一定的安全系数及异常情况,计算温度考虑异常情况按180℃取值);烟气终温(降低到袋除尘进口的要求温度)T2=120℃;烟气的平均含尘浓度μ=1650mg/m3=0.00165kg/m3;灰尘的比热(灰尘的比热随温度变化值较小,差值忽略)C h=0.58kJ/(kg·℃);灰尘的质量流量M h=V2*μ=83487*0.0025=208kg;由于烟气中含尘量很高,所以烟气中粉尘的热焓量也较高,需要计算。
烟气总放热量为Q总=Q气+ Q尘查流体热力学资料,得知烟气的平均比热C1=1.3kJ/(m3·℃);2 放热量计算(注:为每小时烟气平均放热量)(1)烟气放热量Q气;高温烟气从180℃降温到120℃时放出的总热量Q气= C1V1ΔT1=1.3*53880*(180-120)=4202640KJ;(2)灰尘放热量Q尘= C h M hΔT h=0.58*208*(180-120)=7238KJ;(3)烟气总放热量为Q总=Q气+ Q尘=4202640+7238=4209878KJ 三冷却器计算1采用具有占地面积小,运行费用低优点的自然风冷蛇形管冷却器。
蛇形管冷却器的散热冷却能力和冷却器管壁温度与环境气温之差成正比,夏季环境气温高时,两者温差变小,冷却器散热冷却能力下降。
所以,冷却器冷却面积按3500KV A 电弧炉正常冶炼生产并在夏季环境气温30℃时为基本条件设计。
2 设计计算根据能量平衡原理,高温烟气从180℃降温到120℃放出的热量(Q 总)通过引风管散失一部分(即Q 管),其余需要蛇形管冷却器散热(Q 蛇)。
所以,要准确计算出高温烟气经过风管和蛇形管散热器把温度从200℃降低到120℃需要的蛇形管散热面积,首先必须计算出已知引风管的散热量,然后得到需要蛇形管散热的热量,根据蛇形管散热单位面积的热流量即可计算出蛇形管的散热面积。
风管和蛇形管冷却器的散热过程包含风管内高温尘和管内壁、管内壁与管外壁、管外壁与周围空气的三部分热交换过程。
即烟气管内壁管外壁 要计算通过引风管和蛇形管冷却器的散热量,首先必须计算出上述高温烟气分别通过引风管和蛇形管时单位管道面积的散热能力。
而要计算其散热能力,必须分别求出高温尘和管内壁、管内壁与管外壁、管外壁的散热系数,再根据公式求出其总换热系数。
要准确计算通过引风管和蛇形管冷却器的散热量,首先必须计算出上述高温烟气分别通过引风管和蛇形管时单位面积管道的散热能力。
而要计算其散热能力,必须分别求出高温尘和管内壁、管内壁与管外壁、管外壁的散热系数,然后由公式Q=kL ΔT 计算出散热量和散热面积。
引风管和蛇形管冷却器截面均为园,管内因引风机负压作用高温烟气流速较高,高温烟气与管内壁的换热可看做为强制对流换热,管外壁与空气之间的换热为自然对流换热,因此查热学资料得知其平均换热系数分别为h 1=50[w/(m 2·k)],h 2=5[w/(m 2·k)],钢的导热系数λ=49.8 w/(m ·k)。
根据圆管单位管长传热系数计算公式可分别求出风管散热量和蛇形管长度。
(1)引风管散热计算已知参数引风管内径d n1=0.95m ,引风管外径d w2=0.96m (引风管壁厚t w =5mm );钢的导热系数λ=49.8[w/(m ·k)];因此引风管的单位管长传热系数为K =221)12ln(211111d h d d d h ππλπ++ =96.0*10*1)952.096.0ln(8.49*21952.0*100*11πππ++=28[w/(m ·k)];L=55m (引风管从电弧炉到袋除尘长度)根据公式Q=kL ΔT 可计算出引风管的总散热量为Q 管=kL ΔT=28*3.6*55*(180-30)=831600(kJ)(1) 蛇形管降温需要散失的热量根据能量守恒定律列出热平衡方程,Q 总= Q 管+ Q 蛇Q 蛇= Q 总- Q 管=4209878-831600=3378278KJ(2) 蛇形管散热面积和管长计算取蛇形管内径d n1=0.4m ,外径d w2=0.405m (引风管壁厚t w =2.5mm );钢的导热系数λ=49.8[w/(m ·k)];因此蛇形管的单位管长传热系数为K =221)12ln(211111d h d d d h ππλπ++ =405.0*10*1)4.0405.0ln(8.49*214.0*100*11πππ++=11.5[w/(m ·k)]根据公式Q=kL ΔT 可计算出蛇形管的总长度为 L= Q 蛇/K ΔT=3378278÷[11.5*3.6*(180-30)]=545m蛇形管总散热面积S=683m 2,简单推算电弧炉放出的全部热量在精炼时铬铁还原的化学反应吸收的热量已经很小,假设全部用于加热铬铁铁水,并假设此时除电弧炉和铁水本身散失的热量外,其余热量全部被烟气吸收。
由于没有相关数据可参考,假设最多85%的热量被空气吸收,此时可把标况下53880 m3/h的烟气加热最高升温150℃,考虑烟气初温,烟气最高温度170℃。
把53880 m3/h的170℃高温烟气冷却到120℃,需要放出热量Q= CVΔT=1.3*53880*(170-120)=3502200KJ;根据钢的换热系数,可求出总冷却面积S=3502200÷[10*3.6*(170-30)]=695(m2)已知引风管的冷却面积为S1=55*3=165(m2)所以加设冷却器的冷却面积应为S2=S-S1=695-165=530(m2)考虑到原设计中旋风除尘器(若不加设旋风除尘器,蛇形管也具有沉降除尘作用,按530m2的计算值设置蛇形管冷却器即可)也具有冷却降温作用和蛇形管冷却器的进出风箱体的100m2冷却面积,实际需要增加的冷却面积为530-100=430m2,为原设计1078m2(不包括进出风箱体的100m2)的40%左右即可达到降温冷却到袋除尘进口要求温度。
综合选型根据两种计算方法的结果看,冷却面积相差150m2,差别较大,为可靠期间取两种方法计算值的平均值作为最终冷却面积,即S=600 m2去除冷却器的进出风箱体的100 m2的固定冷却面积,蛇形管的冷却面积按S蛇=500 m2计算,根据单位长度管子的面积,可求出蛇形管的总长为398m,根据计算结果绘制蛇形管排列布置图(见附件)。
原袋除尘厂家提供的冷却器冷却管道长度和面积对比(1)原设计蛇形管直径D=400mm;原设计蛇形管总长度L=858m;原设计蛇形管总散热面积S=1078 m2;(2)参考原设计基本结构参数现设计蛇形管直径D=400mm;现设计蛇形管总长度L=398m;现设计蛇形管总散热面积S=500m2考虑到原设计中旋风除尘器(若不加设旋风除尘器,蛇形管也具有沉降除尘作用,按683m2的计算值设置蛇形管冷却器即可)也具有冷却降温作用和蛇形管冷却器的进出风箱体的100 m2冷却面积,实际需要增加的冷却面积为680-100=580 m2,为原设计1078 m2(不包括进出风箱体的100 m2)的54%左右即可达到降温冷却到袋除尘进口要求温度。
说明1 为最大限度发挥蛇形管冷却器的冷却散热能力,蛇形管散热器安装时应尽可能靠近引风管的高温端,此时蛇形管冷却器的进口烟气温度较高,与管外空气的温差较大,蛇形管的对流、传导、辐射散热效率最高;2 为确保因异常情况下高温烟气不进入袋除尘滤袋,袋除尘进口风管仍然加装自动控制的冷风阀;3 现在增加蛇形管冷却器和旋风除尘器后,必然增加系统总阻力,在现有管道阻力本身较大的情况下,可能存在引风机全压不足的情况。