在树脂砂生产中,如何消除铸件出现的脉纹现象
常见压铸件缺陷解决方法
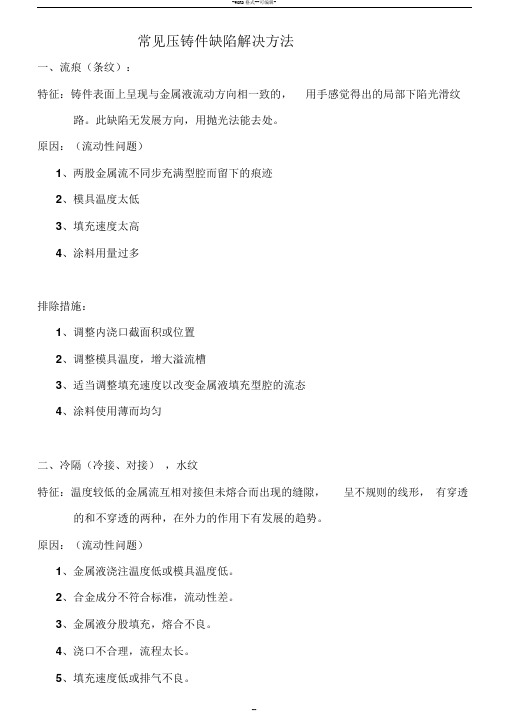
-WORD格式--可编辑-常见压铸件缺陷解决方法一、流痕(条纹):特征:铸件表面上呈现与金属液流动方向相一致的,用手感觉得出的局部下陷光滑纹路。
此缺陷无发展方向,用抛光法能去处。
原因:(流动性问题)1、两股金属流不同步充满型腔而留下的痕迹2、模具温度太低3、填充速度太高4、涂料用量过多排除措施:1、调整内浇口截面积或位置2、调整模具温度,增大溢流槽3、适当调整填充速度以改变金属液填充型腔的流态4、涂料使用薄而均匀二、冷隔(冷接、对接),水纹特征:温度较低的金属流互相对接但未熔合而出现的缝隙,呈不规则的线形,有穿透的和不穿透的两种,在外力的作用下有发展的趋势。
原因:(流动性问题)1、金属液浇注温度低或模具温度低。
2、合金成分不符合标准,流动性差。
3、金属液分股填充,熔合不良。
4、浇口不合理,流程太长。
5、填充速度低或排气不良。
6、比压偏低。
排除措施:1、适当提高浇注温度和模具温度。
2、改变合金成分,提高流动性。
3、改进浇注系统,加大内浇口速度,改善填充条件。
4、改善排溢条件,增大溢流量。
5、提高压射速度,改善排气条件。
6、提高比压三、擦伤(粘模伤痕)特征:顺着脱模方向,由于金属粘附,模具制造斜度太小而造成铸件表面的拉伤痕迹,严重时成为拉伤面。
产生原因:(粘着现象)1、型芯、型壁的铸造斜度太小或出现倒斜度。
2、型芯、型壁有压伤痕。
3、合金粘附模具。
4、铸件顶出偏斜,或型芯轴线偏斜。
5、型壁表面粗糙。
6、涂料常喷涂不到。
7、铝合金中含铁量低于0.6% 。
排除措施:1、修正模具,保证制造斜度。
2、打光压痕。
-WORD格式--可编辑-3、合理设计浇注系统,避免金属流对冲型芯、型壁,适当降低填充速度。
4、修正模具结构。
5、打光表面。
6、涂料用量薄而均匀,不能漏喷涂料。
7、适当增加含铁量至0.6~0.8%。
四、凹陷(缩陷、塌边)特征:铸件平滑表面上出现的凹瘪的部分,其表面呈自然冷却状态。
产生原因:(模具设计、环境问题)1、铸件结构设计不合理,有局部厚实部位,产生热节。
树脂砂使用中的常见缺陷及防止措施

树脂砂使用中的常见缺陷及防止措施树脂自硬砂铸造工艺和其它工艺一样,有自身的规律,如果在原材料选用、工艺设计、制型(芯)操作,生产管理等方面控制不当,将会出现一系列铸造缺陷,降低铸件质量。
本文将对呋喃树脂自硬砂使用过程中若干问题进行分析。
一、树脂砂使用中的常见缺陷及防止措施呋喃树脂自硬砂若使用不当,常出现气孔、机械粘砂、粘模等铸造缺陷。
1、气孔的产生及防止措施金属凝固过程中,陷入金属液中的气泡在铸件中形成孔洞,称之为气孔。
通过观察孔洞的形状、孔壁特征、表面形貌及产生部位等特征可区别于缩孔、缩松、砂眼、渣孔等铸造缺陷。
防止气孔产生的主要措施如下:a.选择合适的树脂种类,适当减少树脂加入量树脂或固化剂加入量过多,树脂含氮量过高,都要引起发气量增加,因此,要防止气孔产生应选用低氮树脂,尽量降低树脂和固化剂的加入量。
b.提高再生砂的质量,降低其灼烧减量和微粉含量若旧砂再生不良,使旧砂的灼烧减量失控,微粉尘含量过高,会造成型(芯)砂发气量增大,透气性降低,出现这种现象时应适当加大新砂比例,同时改进旧砂再生设备,使再生砂达到要求指标。
c.严格控制涂料的涂刷时间和烘干工艺砂型、砂芯硬化不良,涂刷涂料或烘干不当,涂料质量不好或干燥不充分,均使砂型(芯)中残留水分过多,发气量增大。
d.改进铸造工艺设计,合理设置砂型(芯)中的排气通道改进铸造工艺设计,适当提高压头,使砂芯排气通畅;砂型合理设置排气孔,合型时应将砂芯出气道与砂型气眼连通并引出,防止出气道被砂堵塞或浇注时铁液进入芯头出气道;控制浇注速度,避免浇注过慢,使浇注系统金属液充满。
e.调整原砂粒度适当调整原砂粒度,在保证铸件表面质量的前提下,原砂适当粗些可提高砂型的透气性。
f.适当控制浇注温度控制最佳的浇注温度范围,确保既不出气孔,又不至于引起粘砂。
2、机械粘砂的产生及防止措施机械粘砂是金属液在压力作用下渗入铸型型壁砂孔隙中产生金属和砂粒互相掺和、互相粘结的现象。
树脂砂轮制造中常见问题解决方案.doc
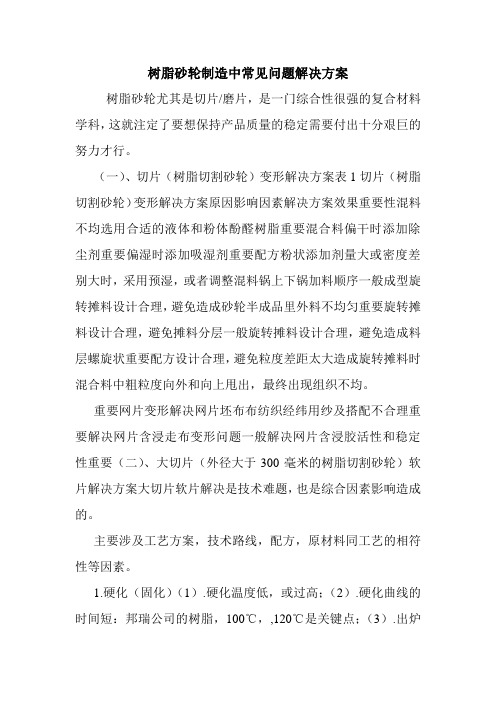
树脂砂轮制造中常见问题解决方案树脂砂轮尤其是切片/磨片,是一门综合性很强的复合材料学科,这就注定了要想保持产品质量的稳定需要付出十分艰巨的努力才行。
(一)、切片(树脂切割砂轮)变形解决方案表1切片(树脂切割砂轮)变形解决方案原因影响因素解决方案效果重要性混料不均选用合适的液体和粉体酚醛树脂重要混合料偏干时添加除尘剂重要偏湿时添加吸湿剂重要配方粉状添加剂量大或密度差别大时,采用预湿,或者调整混料锅上下锅加料顺序一般成型旋转摊料设计合理,避免造成砂轮半成品里外料不均匀重要旋转摊料设计合理,避免摊料分层一般旋转摊料设计合理,避免造成料层螺旋状重要配方设计合理,避免粒度差距太大造成旋转摊料时混合料中粗粒度向外和向上甩出,最终出现组织不均。
重要网片变形解决网片坯布布纺织经纬用纱及搭配不合理重要解决网片含浸走布变形问题一般解决网片含浸胶活性和稳定性重要(二)、大切片(外径大于300毫米的树脂切割砂轮)软片解决方案大切片软片解决是技术难题,也是综合因素影响造成的。
主要涉及工艺方案,技术路线,配方,原材料同工艺的相符性等因素。
1.硬化(固化)(1).硬化温度低,或过高;(2).硬化曲线的时间短:邦瑞公司的树脂,100℃,,120℃是关键点;(3).出炉或出窑太急,温差太大;(4).硬化炉窑的排除硬化潮湿气氛问题。
解决方案:(a).调整科学合理的硬化曲线;(b).在温差变化大或者湿度变化大的季节交叉时期,及时调整硬化低温干燥时间和最高硬化温度;(c).如果上述两项调整难度大,可以寻求酚醛树脂供应商调整部分技术指标,使之适应硬化条件。
2.天气及环境(1).生产现场的环境问题,海拔高度、是否在河边、山凹等;(2).如果工厂现场确实存在这些问题,就要认真面对来改善。
众所周知,夏天或春夏/秋冬交替季节是最容易出现软片的。
主要原因是潮气太大,或者温差太大,造成炉窑排潮不畅。
解决方案:(a).工厂环境不适宜制造砂轮的情况下,安排空调系统,确保室温不高于20℃.(b).如果不能安装空调系统,可以寻求酚醛树脂供应商调整部分技术指标,使之适应硬化条件。
常见压铸件缺陷解决方法
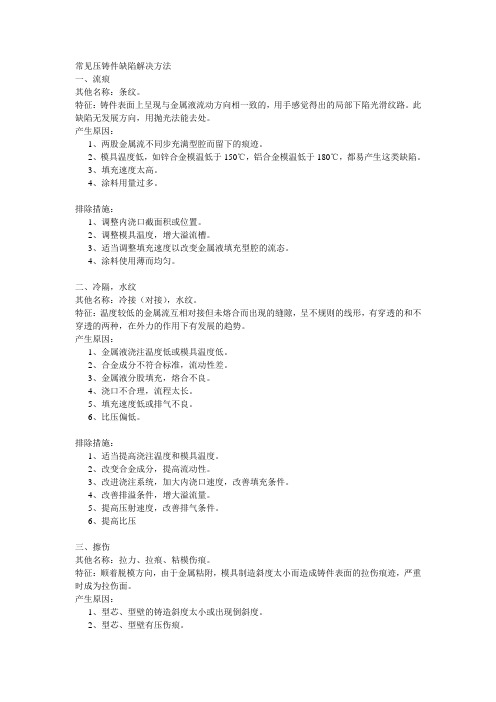
1、改善合金的流动性:
(1)、采用正确的熔炼工艺,排除气体及非金属夹杂物。
(2)、适当提高合金浇注温度和模具温度。
(3)、提高压射速度。
(4)、补充氮气,提高有效压力。
(5)、采用定量浇注。
(6)、改进铸件结构,适当调整壁厚。
2、改进浇注系统:
(1)、正确选择浇口位置和导流方式,对非良形状铸件及大铸件采用多股内浇口为有利。
排除措施:
1、正确选用模具材料及合理的热处理工艺。
2、模具在压铸前必须预热到工作温度范围。
3、尽可能降低合金浇注温度。
4、提高模具型腔表面质量,降低Ra数值。
5、镶块定期退火,消除应力。
6、正确设计浇注系统,在满足成型良好的条件下,尽可能用较小的压射速度。
十三、有色斑点
其他名称:油斑、黑色斑点。
特征:铸件表面上呈现的不同于基体金属的斑点,一般由涂料碳化物形成。
其他名称:错缝。
特征:铸件的一部分与另一部分在分型面上错开,发生相对位移(对螺纹称错扣)。
产生原因:
1、模具镶块位移。
2、模具导向件磨损。
3、两半模的镶块制造误差。
排除措施:
1、调整镶块,加以紧固。
2、更换导柱导套。
3、进行修整,消除误差。
十九、变形
其他名称:扭曲、翘曲。
特征:铸件的几何形状与设计要求不符的整体变形。
产生原因:
1、模具型腔表面龟裂造成的痕迹,内浇口区域附近的热传导最集中,摩擦阻力最大,经受熔融金属的冲蚀最强,冷热交变最剧,最易产生热裂,形成龟裂。
2、模具材料不当或热处理工艺不正确。
3、模具冷热温差变化大。
4、合金液浇注温度过高,模具预热不够。
5、模具型腔表面粗糙度Ra太大。
防肪纹添加剂在汽车铸件上的应用
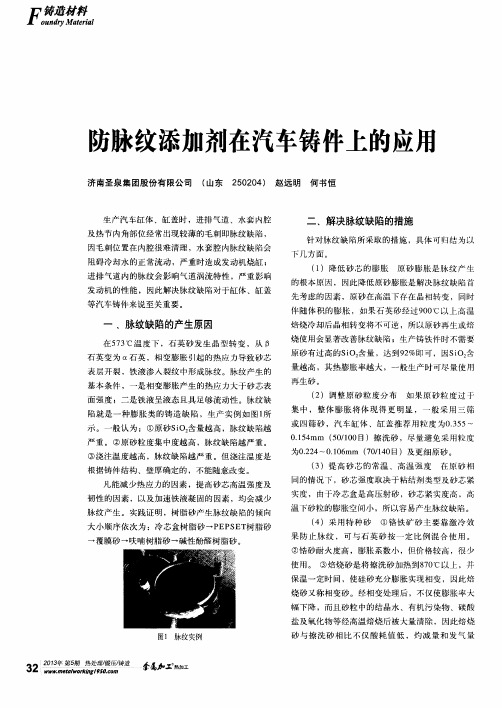
( 2 ) 调 整 原 砂粒 度分 布
如 果 原 砂 粒 度过 于
集 中,整体 膨胀将体现得 更 明显 ,一般采用三筛
或 四 筛 砂 ,汽 车 缸 体 、 缸 盖 推 荐 用粒 度 为0 . 3 5 5 ~ 0 . 1 5 4 mm ( 5 0 / 1 0 0 目)擦 洗砂 ,尽量 避 免 采 用粒 度
防脉纹添加剂在汽车铸件上的应用
济南圣泉集 团股 份有 限公 司 ( 山东 2 5 0 2 0 4 ) 赵 远明 何 书恒
生 产汽 车 缸 体 、缸 盖 时 ,进排 气 道 、水 套 内腔
二、解决脉纹缺陷的措施
针 对脉 纹 缺 陷所 采 取 的措 施 ,具 体 可 归 结 为以
下 几方 面 。
石英 变 为 石 英 ,相 变 膨胀 引起 的热 应 力导 致 砂 芯
表 层开 裂 ,铁 液 渗 入裂 纹 中形 高 ,其热 膨 胀率 越 大 ,一 般 生产 时 可尽 量 使 用
再 生砂 。
基本条件 ,一是相变膨胀产生的热应 力大于砂芯表
面 强度 ;二是 铁 液 呈液 态 且具 足 够流 动 性 。脉 纹 缺 陷就 是 一种 膨 胀 类 的铸 造 缺 陷 ,生 产 实 例 如 图1 所 示 。一 般认 为 :①原 砂 S i O : 含 量 越高 ,脉纹 缺 陷越 严重 。②原 砂 粒 度集 中度越 高 ,脉 纹 缺 陷越 严 重 。 ③浇 注 温 度越 高 ,脉 纹 缺 陷越 严 重 。但 浇注 温 度 是 根据 铸 件结 构 、壁 厚 确定 的 ,不能 随意 改 变 。 几 能减 少热 应 力 的 因素 ,提高 砂 芯 高温 强度 及
及热节内角部位经常出现较薄的毛 ̄ J H I J 脉纹缺陷 , 因毛刺位置在 内腔很难清理,水套腔 内脉纹缺陷会
铸造常见的缺陷及解决办法

铸造常见的缺陷及解决办法铸造是一种常见的加工方法,用于制造大量金属和非金属产品。
然而,铸造过程中常常会出现一些缺陷,这些缺陷会影响铸件的质量和性能。
本文将介绍几种常见的铸造缺陷及解决办法。
气孔气孔是指在铸件内部或表面上出现的气泡。
这些气泡会影响铸件的强度和密封性能。
气孔的出现原因可能是铸造温度或压力不足,或是砂模中的水分蒸发不充分。
解决气孔的问题,需要改变铸造过程中的温度、压力或砂模中的水分含量。
另外,选择合适的金属合金也是避免气孔出现的重要因素,例如在铸造铝合金时,可以使用特殊的铝合金材料来降低气孔的出现。
毛刺毛刺是指在铸件表面上出现的细小凸起物。
这些毛刺会影响铸件的表面光滑度和密封性能。
毛刺的出现原因可能是砂模中的杂质、铸件表面的耗损或金属液体的流动不充分。
解决毛刺的问题,需要在铸造过程中施加足够的压力和控制金属液体的流动速度。
另外,使用高品质的砂模和特殊的涂料或添加剂也可以有效地减少毛刺的出现。
缩孔缩孔是指在铸件内部或表面上出现的缺陷。
这些缺陷会影响铸件的强度和密封性能。
缩孔的出现原因可能是铸造温度不足、金属合金不均匀、砂模中的气包或铸造中的氧化物等。
解决缩孔的问题需要改变铸造温度、金属合金中元素的成分、砂模的密度和金属液体中的氧化物含量。
此外,在铸造过程中添加特殊的合金和增量剂也可以有效地减少缩孔的出现。
内孔内孔是指在铸件内部出现的缺陷,这些缺陷会影响铸件的强度和密封性能。
内孔的出现原因可能是砂模泥中的气孔或金属液体中的气泡。
解决内孔的问题需要改变铸造过程中的气压和金属液体的流动速度。
此外,在铸造过程中添加特殊的漏铸剂和降泡剂也可以有效地减少内孔的出现。
总之,铸造过程中出现的缺陷会严重影响铸件的质量和性能。
通过改变铸造过程中的温度、压力和砂模的含水量,以及添加特殊的金属合金、涂料、合金和漏铸剂等,可以有效地减少这些缺陷的出现。
因此,在铸造过程中应该尽可能地避免出现这些问题,并采取合适的方法来解决这些问题。
脉纹缺陷的防止及抗脉纹齐在树脂砂芯上的试用
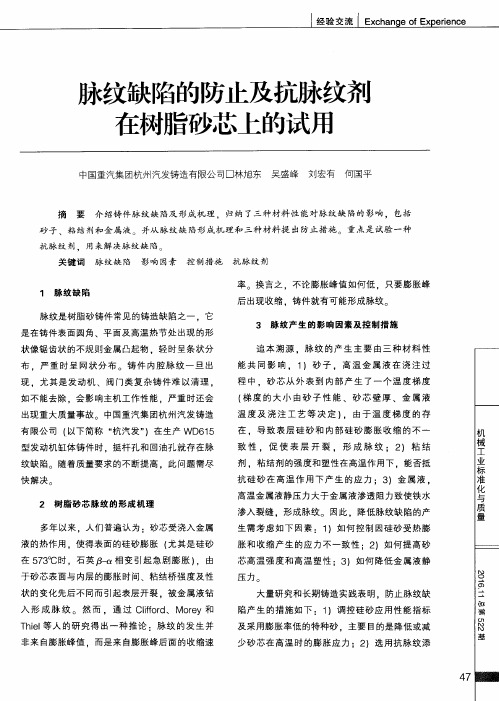
及 采用膨胀率低 的特种砂 .主要 目的是降低或 减
少砂芯 在 高温 时的膨 胀应 力 ;2 )选 用抗脉 纹 添
47
E x c h a n a e o f Ex D e i f e n c e I 经 验 交 流
机 械
工
加剂 。市场 上有多种添加 剂 ,这些 添加剂 一般具 有低熔点 。可使砂芯在高 温下变形 能力较 好 ,从 而释放 由于 硅砂 膨胀 引起 的热 应 力 ;3 )合 理控
踩
纹 ,防止脉 纹缺 陷 :5 )优 化 制芯 、熔炼 和 浇注
工艺 ,原砂 水份 应 ≤0 I 2 % ,砂温 应 控制 在 1 5 ℃
~
J 1 气 缸 怵 挺 杆 孔 脉 纹 缺 陷 罔
驽 I I }
r
度超过 3 mm 的脉 纹 。 原 因可 能 是 在 浇 注 过 程 中,挺 杆芯处于型腔 底部 .长期 处于高温 金属液 烘烤 ,并且处于高金 属静压力下 ,所 以更容 易使 得挺杆 孔圆柱砂芯表 面开裂 .形成脉纹 。
能共 同影 响 ,1 )砂 子 ,高 温 金 属 液 在 浇 注 过
现 .尤 其是 发动机 、阀 门类 复杂铸 件难 以清 理 ,
如不能去 除 。会 影响主机工作 性能 ,严 重时还会
程 中 .砂芯 从 外 表 到 内部 产 生 了一 个温 度 梯 度 ( 梯 度 的大 小 由砂 子 性 能 、砂 芯 壁 厚 、金 属 液 温度及 浇注工艺等决定 ) ,由 于 温 度 梯 度 的 存 在 .导 致表 层 硅 砂 和 内部 硅砂 膨 胀 收 缩 的不 一 致 性 ,促 使 表 层 开 裂 ,形 成 脉 纹 ;2 ) 粘 结 剂 。粘结剂 的强度和塑性 在高温作用下 。能否抵 抗 硅 砂在 高 温 作 用 下产 生 的应 力 ;3 )金属 液 ,
铸件的常见不良现象及对策
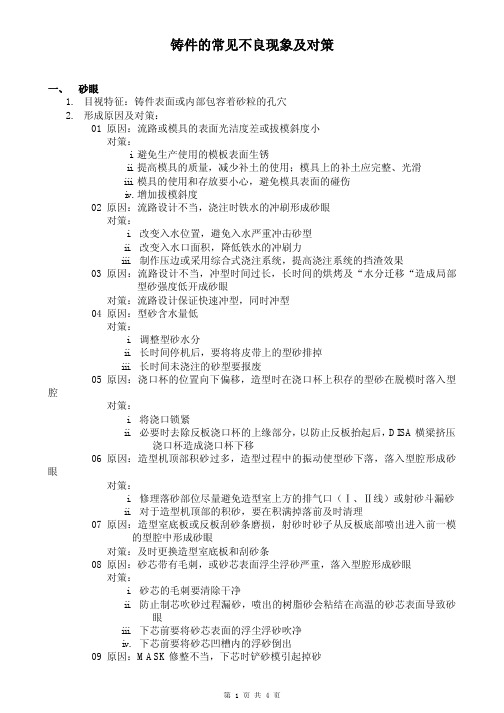
一、砂眼1.目视特征:铸件表面或内部包容着砂粒的孔穴2.形成原因及对策:01 原因:流路或模具的表面光洁度差或拔模斜度小对策:i.避免生产使用的模板表面生锈ii.提高模具的质量,减少补土的使用;模具上的补土应完整、光滑iii.模具的使用和存放要小心,避免模具表面的碰伤iv.增加拔模斜度02 原因:流路设计不当,浇注时铁水的冲刷形成砂眼对策:i.改变入水位置,避免入水严重冲击砂型ii.改变入水口面积,降低铁水的冲刷力iii.制作压边或采用综合式浇注系统,提高浇注系统的挡渣效果03 原因:流路设计不当,冲型时间过长,长时间的烘烤及“水分迁移“造成局部型砂强度低开成砂眼对策:流路设计保证快速冲型,同时冲型04 原因:型砂含水量低对策:i.调整型砂水分ii.长时间停机后,要将将皮带上的型砂排掉iii.长时间未浇注的砂型要报废05 原因:浇口杯的位置向下偏移,造型时在浇口杯上积存的型砂在脱模时落入型腔对策:i.将浇口锁紧ii.必要时去除反板浇口杯的上缘部分,以防止反板抬起后,DISA横梁挤压浇口杯造成浇口杯下移06 原因:造型机顶部积砂过多,造型过程中的振动使型砂下落,落入型腔形成砂眼对策:i.修理落砂部位尽量避免造型室上方的排气口(Ⅰ、Ⅱ线)或射砂斗漏砂ii.对于造型机顶部的积砂,要在积满掉落前及时清理07 原因:造型室底板或反板刮砂条磨损,射砂时砂子从反板底部喷出进入前一模的型腔中形成砂眼对策:及时更换造型室底板和刮砂条08 原因:砂芯带有毛刺,或砂芯表面浮尘浮砂严重,落入型腔形成砂眼对策:i.砂芯的毛刺要清除干净ii.防止制芯吹砂过程漏砂,喷出的树脂砂会粘结在高温的砂芯表面导致砂眼iii.下芯前要将砂芯表面的浮尘浮砂吹净iv.下芯前要将砂芯凹槽内的浮砂倒出09 原因:MASK修整不当,下芯时铲砂模引起掉砂对策:修整MASK或模具消除下芯铲砂现象10 原因:型腔位置偏上时,压型器将砂型压裂,掉砂形成砂眼对策:造型时注意排版状况,适当调整压型器位置11 原因:夹板或底板挂职铁将型腔挤裂造成砂眼对策:生产中及时清模二、气孔A、侵入性气孔1、目视特征01形状:气孔尺寸一般较大,呈圆球形、团球形或梨形;梨形的小头指向外部气源方向02孔壁面貌:孔壁平滑——侵入气体成分主要为CO时孔壁呈蓝色,侵入气体成分主要为氢气时孔壁呈金属本色且发亮,侵入气体成分主要为水蒸气时孔壁呈氧化色且发暗。
铸造工艺缺陷及解决措施
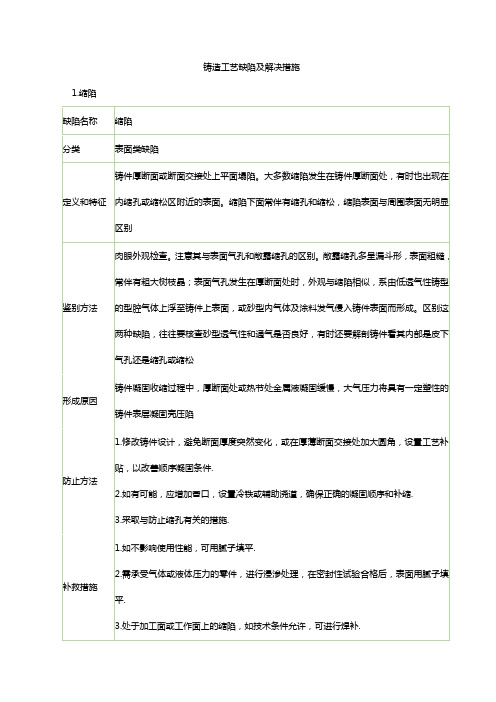
概率因子
0.3
缺陷名称
脉纹
分类
多肉类缺陷
定义和特征
鉴别方法
形成原因
浇温高,浇注时间长,树脂砂膨胀厉害,型芯易产生裂纹.
防止方法
控制浇注温度,浇注速度适中.
补救措施
概率因子
0.3
缺陷名称
脉纹
分类
多肉类缺陷
定义和特征
鉴别方法
形成原因
型芯中的局部过热处,易膨胀开裂
防止方法
在局部过热的地方采用特种砂或增厚涂层的厚度
形成原因
铸件凝固收缩过程中,厚断面处或热节处金属液凝固缓慢,大气压力将具有一定塑性的铸件表层凝固壳压陷
防止方法
1.修改铸件设计,避免断面厚度突然变化,或在厚薄断面交接处加大圆角,设置工艺补贴,以改善顺序凝固条件.
2.如有可能,应增加冒口,设置冷铁或辅助浇道,确保正确的凝固顺序和补缩.
3.采取与防止缩孔有关的措施.
3.易氧化合金钢在还原性或中性气氛中浇注.
4.调整合金成分以提高其流动性,适当提高浇注温度和浇注速度,防止金属液在浇注过程中氧化,改进型砂和涂料成分以防止型壁与金属液发生化学反应,包内静置足够时间并加强挡渣,金属型铸造时适当提高型温 5.在浇注系统中设置过滤网和集渣包
补救措施
有皱皮缺陷的铸件通常不会报废,不加工表面的皱皮可用砂轮打磨掉,加工表面的皱皮一般可机械加工掉
鉴别方法
肉眼外观检查。易于同其他表面缺陷相区别。象皮状皱皮有较深的网状沟槽,是球墨铸铁件和镁合金铸件特有的缺陷,根据合金种类易与一般皱皮相区别
形成原因
1.镁球墨铸铁在加镁处理时形成的化合物(氧化物、硫化物、硅酸盐等),通常以薄膜形式分散在金属液中,在浇包中上浮缓慢,浇注时随金属液进入铸型,并上浮至铸件上表面,离心铸造时则聚集在铸件内壁,
自硬树脂砂型的开裂原因及防止措施
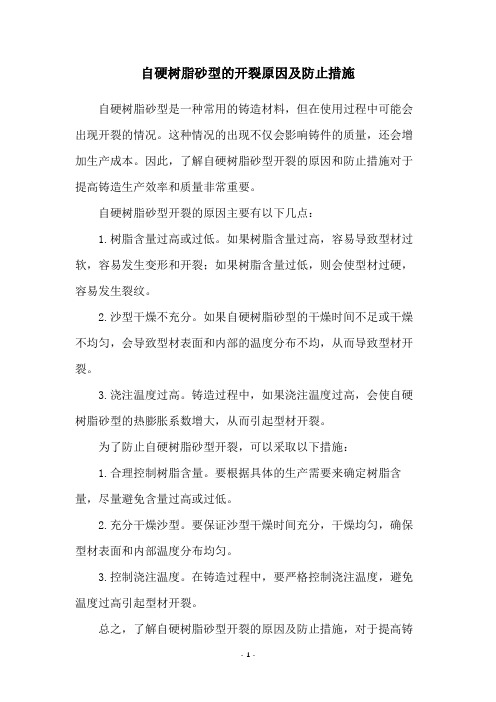
自硬树脂砂型的开裂原因及防止措施自硬树脂砂型是一种常用的铸造材料,但在使用过程中可能会出现开裂的情况。
这种情况的出现不仅会影响铸件的质量,还会增加生产成本。
因此,了解自硬树脂砂型开裂的原因和防止措施对于提高铸造生产效率和质量非常重要。
自硬树脂砂型开裂的原因主要有以下几点:
1.树脂含量过高或过低。
如果树脂含量过高,容易导致型材过软,容易发生变形和开裂;如果树脂含量过低,则会使型材过硬,容易发生裂纹。
2.沙型干燥不充分。
如果自硬树脂砂型的干燥时间不足或干燥不均匀,会导致型材表面和内部的温度分布不均,从而导致型材开裂。
3.浇注温度过高。
铸造过程中,如果浇注温度过高,会使自硬树脂砂型的热膨胀系数增大,从而引起型材开裂。
为了防止自硬树脂砂型开裂,可以采取以下措施:
1.合理控制树脂含量。
要根据具体的生产需要来确定树脂含量,尽量避免含量过高或过低。
2.充分干燥沙型。
要保证沙型干燥时间充分,干燥均匀,确保型材表面和内部温度分布均匀。
3.控制浇注温度。
在铸造过程中,要严格控制浇注温度,避免温度过高引起型材开裂。
总之,了解自硬树脂砂型开裂的原因及防止措施,对于提高铸
造生产效率和质量非常重要。
只有通过科学的生产管理和技术手段,才能更好地保证自硬树脂砂型的质量和生产效率。
缸体缸盖铸件内腔脉纹缺陷成因分析及防止对策
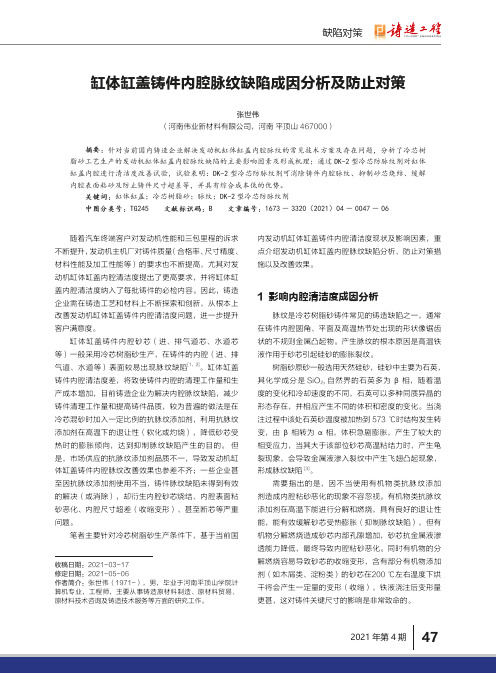
理论值 铸件 1 铸件 2 铸件 3 铸件 4 铸件 5
尺寸 1 120
119.512 119.517 119.545 119.587 119.511
表 1 浇注后铸件尺寸变化(单位:mm) Tab.1 Dimensions change of poured casting(unit:mm)
累计值 600
598.103 598.142 597.957 598.098 597.946
偏差 0-1.897 Fra bibliotek1.858 -2.043 -1.902 -2.054
2021 年第 4 期 49
缺陷对策
经过分析,进气道收缩主要发生在砂芯烘干和浇注 两个阶段。将有机防脉纹剂加入量调整为 0.5% 和 1.0% 进行试验,均出现不同比例的脉纹缺陷,且铸件进气道 尺寸收缩值均大于 1.5 mm,无法满足客户对产品尺寸 公差 1.0 mm 的精度要求。
图 2 缸盖进气道脉纹 Fig.2 Veining defect in air inlet of cylinder head
B 铸造厂采用围场砂(SiO2 含量为 92%),冷芯 盒工艺生产 6 缸柴油机缸盖进、排气道砂芯,混砂时不 加抗脉纹添加剂,分别试验了 3 种国外品牌的防脉纹涂 料,涂料比重控制在 1.36~1.38 g/cm3,涂层湿态厚度 控制在 350~400 μm。经过多轮对比试验,3 种防脉纹 涂料对缸盖进、排气道内腔脉纹缺陷均无根本的改善, 仅使缺陷形态有减轻趋势 ( 如图 3)。同时使用防脉纹涂 料后缸盖内腔(水道、气道)出现淡黄色的涂料皮(如 图 4),清理难度大,在缸盖加工清洗过程中及发动机 使用过程中存在涂料皮脱落的风险,不能满足客户对内 腔清洁度及内腔色差的要求。
呋喃树脂铸件脉纹问题(与“脉纹”相关文档)共2张PPT

渗入砂层,在铸件上形成 “脉纹” 采呋用喃热 树膨脂胀自小硬或砂粒铸度件较脉分纹散问的题原砂
在采膨用胀 热、膨收胀缩小应或力粒作度用较下分表散层的龟原裂砂,金属液从裂缝渗入砂层,在铸件上形成 “脉纹” 在膨胀、收缩应力作用下表层龟裂,金属液从裂缝渗入砂层,在铸件上形成 “脉纹” 2.脉纹(脉状凸起、飞刺、飞翘)
采用热膨胀小或粒下散表的层原龟砂裂,金属液从裂缝渗入砂层,在铸件上形成 “脉纹” 在膨胀、收缩应力作用下表层龟裂,金属液从裂缝渗入砂层,在铸件上形成 “脉纹” 2采.用脉热纹膨(胀脉小状或凸粒起度、较飞分刺散、的飞原翘砂)
在膨胀、收缩应力作用下表层龟裂,金属液从裂缝 在砂膨型胀 (、芯收)缩表应层力在作液用态下金表属层激龟热裂下,金由属表液及从里裂产缝生渗很入大砂的层温,度在梯铸度件,上石形英成受热“脉相纹变”膨胀,粘结桥会突然收缩而脆化破裂
呋喃树脂自硬砂铸 件脉纹问题
第1页,共2页。
2.脉纹(脉状凸起、飞刺、飞翘)
原因:
砂型(芯)表层在液态金属激热下,由表及里产生很 2.脉纹(脉状凸起、飞刺、大飞翘的) 温度梯度,石英受热相变膨胀,粘结桥会突然收 缩而脆化破裂 2在.膨脉胀纹、(收脉缩状应凸力起作、用飞下刺表、层飞龟翘裂),金属液从裂缝渗入砂层,在铸件上形成 “脉纹”
预防措施 呋喃树脂自硬砂铸件脉纹问题
在膨胀、收缩应力作用下表层龟裂,金属液从裂缝渗入砂层,在铸件上形成 “脉纹” 采用热膨胀小或粒度较分散的原砂
采用热膨胀小或粒度较分散的原砂
在型(芯)砂中加入氧化铁粉
降低浇注温度
刷涂料
第2页,共2页。
铸件脉纹形成机理及其防治
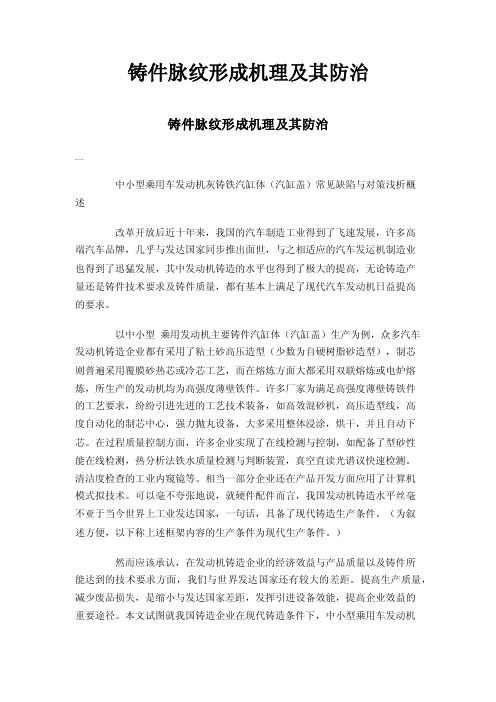
铸件脉纹形成机理及其防治铸件脉纹形成机理及其防治00中小型乘用车发动机灰铸铁汽缸体(汽缸盖)常见缺陷与对策浅析概述改革开放后近十年来,我国的汽车制造工业得到了飞速发展,许多高端汽车品牌,几乎与发达国家同步推出面世,与之相适应的汽车发运机制造业也得到了迅猛发展,其中发动机铸造的水平也得到了极大的提高,无论铸造产量还是铸件技术要求及铸件质量,都有基本上满足了现代汽车发动机日益提高的要求。
以中小型乘用发动机主要铸件汽缸体(汽缸盖)生产为例,众多汽车发动机铸造企业都有采用了粘土砂高压造型(少数为自硬树脂砂造型),制芯则普遍采用覆膜砂热芯或冷芯工艺,而在熔炼方面大都采用双联熔炼或电炉熔炼,所生产的发动机均为高强度薄壁铁件。
许多厂家为满足高强度薄壁铸铁件的工艺要求,纷纷引进先进的工艺技术装备,如高效混砂机,高压造型线,高度自动化的制芯中心,强力抛丸设备,大多采用整体浸涂,烘干,并且自动下芯。
在过程质量控制方面,许多企业实现了在线检测与控制,如配备了型砂性能在线检测,热分析法铁水质量检测与判断装置,真空直读光谱议快速检测。
清洁度检查的工业内窥镜等。
相当一部分企业还在产品开发方面应用了计算机模式拟技术。
可以毫不夸张地说,就硬件配件而言,我国发动机铸造水平丝毫不亚于当今世界上工业发达国家,一句话,具备了现代铸造生产条件。
(为叙述方便,以下称上述框架内容的生产条件为现代生产条件。
)然而应该承认,在发动机铸造企业的经济效益与产品质量以及铸件所能达到的技术要求方面,我们与世界发达国家还有较大的差距。
提高生产质量,减少废品损失,是缩小与发达国家差距,发挥引进设备效能,提高企业效益的重要途径。
本文试图就我国铸造企业在现代铸造条件下,中小型乘用车发动机灰铸铁汽缸体(汽缸盖)铸件生产中常见的铸造缺陷与对策,与广大业界同仁作一交流。
1气孔气孔通常是汽缸体铸件最常见缺陷,往往占铸件废品的首位。
如何防止气孔,是铸造工作者一个永久的课题。
注塑产品流痕怎么办?
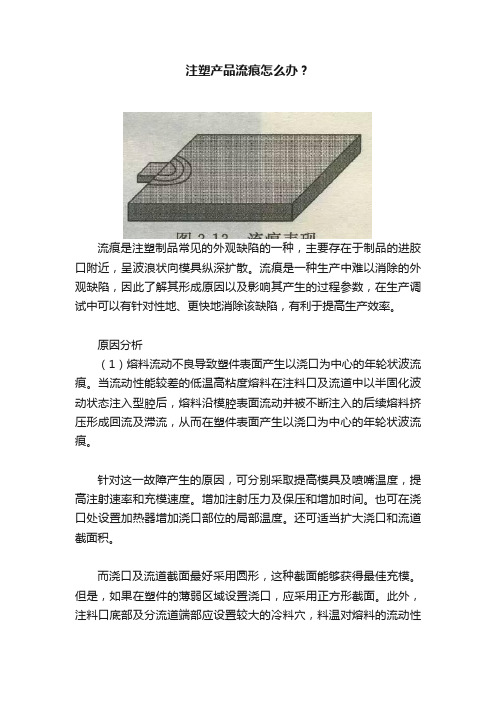
注塑产品流痕怎么办?流痕是注塑制品常见的外观缺陷的一种,主要存在于制品的进胶口附近,呈波浪状向模具纵深扩散。
流痕是一种生产中难以消除的外观缺陷,因此了解其形成原因以及影响其产生的过程参数,在生产调试中可以有针对性地、更快地消除该缺陷,有利于提高生产效率。
原因分析(1)熔料流动不良导致塑件表面产生以浇口为中心的年轮状波流痕。
当流动性能较差的低温高粘度熔料在注料口及流道中以半固化波动状态注入型腔后,熔料沿模腔表面流动并被不断注入的后续熔料挤压形成回流及滞流,从而在塑件表面产生以浇口为中心的年轮状波流痕。
针对这一故障产生的原因,可分别采取提高模具及喷嘴温度,提高注射速率和充模速度。
增加注射压力及保压和增加时间。
也可在浇口处设置加热器增加浇口部位的局部温度。
还可适当扩大浇口和流道截面积。
而浇口及流道截面最好采用圆形,这种截面能够获得最佳充模。
但是,如果在塑件的薄弱区域设置浇口,应采用正方形截面。
此外,注料口底部及分流道端部应设置较大的冷料穴,料温对熔料的流动性能影响较大,越要注意冷料穴尺寸的大小,冷料穴的位置必须设置在熔料沿注料口流动方向的端部。
如果产生年轮状波流痕的主要原因是树脂性能较差时,可在条件充许的情况下,选用低粘度的树脂。
(2)熔料在流道中流动不畅导致塑件表面产生螺旋状波流痕。
当熔料从流道狭小的截面流入较大截面的型腔或模具流道狭窄,光洁度很差时,流料很容易形成湍流,导致塑件表面形成螺旋状波流痕。
对此,可适当降低注射速度或对注射速度采取慢,快,慢分级控制。
模具的浇口应设置在厚壁部位或直接在壁侧设置浇口,浇口形式最好采用柄式,扇形或膜片式。
也可适当扩大流道及浇口截面,减少流料的流动阻力。
此外,应节制模具内冷却水的流量,使模具保持较高的温度。
若在工艺操作温度范围内适当提高料筒及喷嘴温度,有利于改善熔料的流动性能。
(3)挥发性气体导致塑件表面产生云雾状波流痕。
当采用ABS或其他共聚树脂原料时,若加工温度较高,树脂及润滑剂产生的挥发性气体会使塑件表面产生云雾状波流痕。
铸件缺陷及解决方法
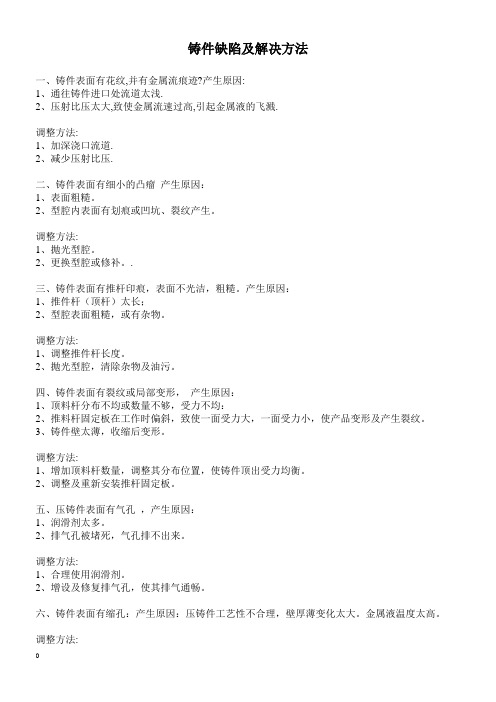
铸件缺陷及解决方法一、铸件表面有花纹,并有金属流痕迹?产生原因:1、通往铸件进口处流道太浅.2、压射比压太大,致使金属流速过高,引起金属液的飞溅.调整方法:1、加深浇口流道.2、减少压射比压.二、铸件表面有细小的凸瘤产生原因:1、表面粗糙。
2、型腔内表面有划痕或凹坑、裂纹产生。
调整方法:1、抛光型腔。
2、更换型腔或修补。
.三、铸件表面有推杆印痕,表面不光洁,粗糙。
产生原因:1、推件杆(顶杆)太长;2、型腔表面粗糙,或有杂物。
调整方法:1、调整推件杆长度。
2、抛光型腔,清除杂物及油污。
四、铸件表面有裂纹或局部变形,产生原因:1、顶料杆分布不均或数量不够,受力不均:2、推料杆固定板在工作时偏斜,致使一面受力大,一面受力小,使产品变形及产生裂纹。
3、铸件壁太薄,收缩后变形。
调整方法:1、增加顶料杆数量,调整其分布位置,使铸件顶出受力均衡。
2、调整及重新安装推杆固定板。
五、压铸件表面有气孔,产生原因:1、润滑剂太多。
2、排气孔被堵死,气孔排不出来。
调整方法:1、合理使用润滑剂。
2、增设及修复排气孔,使其排气通畅。
六、铸件表面有缩孔:产生原因:压铸件工艺性不合理,壁厚薄变化太大。
金属液温度太高。
调整方法:1、在壁厚的地方,增加工艺孔,使之薄厚均匀。
2、降低金属液温度。
七、铸件外轮廓不清晰,成不了形,局部欠料,产生原因:1、压铸机压力不够,压射比压太低。
2、进料口厚度太大;3、浇口位置不正确,使金属发生正面冲击。
调整方法:1、更换压铸比压大的压铸机;2、减小进料口流道厚度;3、改变浇口位置,防止对铸件正面冲击。
八、铸件部分未成形,型腔充不满,产生原因:1、压铸模温度太低;2、金属液温度低;3、压机压力太小,4、金属液不足,压射速度太高;5、空气排不出来。
调整方法:1、2、提高压铸模,金属液温度;3、更换大压力压铸机。
4、加足够的金属液,减小压射速度,加大进料口厚度。
九、压铸件锐角处充填不满。
产生原因:1、内浇口进口太大;2、压铸机压力过小;3、锐角处通气不好,有空气排不出来。
- 1、下载文档前请自行甄别文档内容的完整性,平台不提供额外的编辑、内容补充、找答案等附加服务。
- 2、"仅部分预览"的文档,不可在线预览部分如存在完整性等问题,可反馈申请退款(可完整预览的文档不适用该条件!)。
- 3、如文档侵犯您的权益,请联系客服反馈,我们会尽快为您处理(人工客服工作时间:9:00-18:30)。
在树脂砂生产中,如何消除铸件出现的脉纹现象?
脉纹是树脂砂铸件常见的铸造缺陷之一,它是在铸件表面园角、平面及高温热节处出现的形状像锯齿状的不规则金属凸起物,轻时呈条状分布,严重时呈网状分布。
铸件内腔脉纹一旦出现,尤其是发动机、阀门类复杂铸件难以清理,如不能去除,会影响母机工作性能,严重时还会出现重大质量事故。
生产实残证明,树脂砂产生脉纹倾向大小的先后顺序是冷芯盒、酚醛尿烷自硬、热芯盒、覆膜砂、自硬呋喃工艺等。
大家知道:脉纹的产生必须有两个条件,一是石英砂在573℃发生相变体积膨胀致使砂型表面开裂成缝,二是高温金属液静压力大于金属液渗透阻力致使铁水渗入裂缝。
即高温金属液在加热砂型的过程中,砂型从外表到内部产生了一个很大的温度梯度,其表面产生了热应力,当砂型的高温粘结强度小于此热应力时,砂型就会出现裂纹。
而高温金属液能否进入砂型裂纹主要取决于裂纹的大小,金属液对砂型表面的润湿能力、表面张力和静压力。
由此可见,如果能提升砂型的热强度和热塑性,克服因硅砂的膨胀和树脂的燃烧分解而产生的热应力和热变形,克服砂型表面开裂,或抑制金属液渗入裂缝,就可避免或减轻脉纹缺陷的产生。
其主要方法与措施如下:
1)调控硅砂应用性能指标:硅砂的热膨胀和相变膨胀是砂型开裂的主要原因之一,但不同类别的硅砂因其SiO2、碱性氧化物(FeO、CaO、K0、NaO等) 含量、粒形、粒度及其分布、砂粒表面显微结构、砂粒与树脂亲和力等的不同,其热膨胀性呈现出很大的差异。
大林砂其因SiO2含量适中,粒形园整,单位面积上树脂膜较厚,它的热膨胀应力较小;粒度分布相对分散的原砂,例如将三筛法变为四筛或五筛法,此时原砂粒径差异较大,它们发生热膨胀的时间有先有后,可减少砂型的“宏观膨胀”,减缓热开裂倾向;经过900℃左右焙烧的相变砂已发生了部分不可逆相变,热膨胀率降低,砂粒表面出现晶格畸变和晶格缺陷,活性增大,使树脂与砂粒间粘附强度提高,有显著的抗脉纹能力。
2)选用抗脉纹添加剂:抗脉纹剂是一种硅酸盐、金属氧化物经特别处理的多元复合化合物。
在常温条件下,它既不影响混合料可使用时间、流动性、固化速度、仓储时向等常规使用性能,又不增加砂型的发气量。
在高温条件下,它能和二氧化硅发生物理化学作用,形成低熔点的多元玻璃态物质,增加砂型的热强度和热塑性,吸收石英砂在573℃发生相变时的体积膨胀,减少砂型(型)热开裂的趋势,封堵
裂纹,增加金属液渗透阻力,防止砂型气体向铸件内扩散,加入原砂重量的5~10%可有效解决脉纹缺陷。
3)选用膨胀率低的特种砂:锆英砂、铬矿砂、莫来石砂等非石英质原砂与石英砂相比具有热膨胀系数小,热导率和蓄热系数大,耐火度高,与铁及其氧化物的润湿性低等优点。
可按不同砂型脉纹缺陷的严重程度,用25~5O%的特种砂,大多数使用铬铁矿砂来解决脉纹缺陷。
但在实际应用时,要注意特种砂与石英砂存在着密度和粒形差异,因此必须考虑到密度和比表面积不同而调整树脂的实际加入量,一般按下式折算特种砂与石英砂的质量关系:m特=m石英×(p石英/p特)×(s特/s石英) 其中:m一质量p一密度s一比表面积
4)选用热塑性好的树脂:树脂是影响砂型常温及热强度、热塑性的关键重要因素。
由于各种牌号树脂性能的差异,势必造成砂粒与树脂膜之间不同的界面现象,不同的树脂膜强度,不同的影响因素和实现条件。
为量化不同树脂的热塑性,通常是用砂型在一定载荷和温度条件下保持不溃散的持续时间和变形量来表示,正变形量表明砂型抵抗变形能力,负变形量表示砂型在热作用下的膨胀应力,从变形量可以很方便地判断出不同树脂在同等工艺条件下的热强度和热塑性,这种试验可在树脂砂高温性能试验机上进行测定。
5)选用激冷和烧结型涂料:采用激冷涂料加快金属液冷却,使金属液在硅砂尚未完成“宏观膨胀”前就已凝固,或用绝热涂料,降低砂型加热速度,减小硅砂的热膨胀量,使砂型不再产生裂纹,都可以达到防止铸件产生脉纹的目的。
常用的激冷涂料有锑涂料,在实际应用时,宜在激冷涂料上面再涂一层常规涂料,以避免铸件表面产生麻口组织,但这种激冷涂料仅对小型铸件的脉纹有效。
对其中大型铸件而言,宜选用使用强度、韧性优良,导热性能好的烧结型涂料,这种涂料的膨胀系数应接近砂型热膨胀系数,增强砂型表面抗膨胀裂纹的能力。
6)优化造型、熔炼浇注工艺:在造型制芯工艺方面,控制优化好水份、温度、压力和时间等工艺参数,例如原砂水份要≤0.2%,砂温不能小于15℃大于40℃,混合料要在可使用时间内使用等,保证砂型有较高的强度、表面光洁、紧实度,无疏松;在金属熔炼方面,尽量降低磷(P)的含量;在浇注时,在保证能得到健全铸件而不产生气孔等缺陷的铁液充型温度下,尽可能采取较低的浇注温度和压头,以
减轻砂型受热膨胀的程度和金属液的渗透压力,同时采用较快的浇注速度,以避免砂型长时间受到高温烘烤可能产生膨胀裂纹。