6sigma Project Report
SixSigmaProjectTemplate六西格玛报告模板

5. Control
4. Improve
Why? Why? Why?
Map information/ process flows
Repeatable Effective Efficient
Standard Work
Mistake Proof
Root Cause Analysis
Display Process Improvement Status
Benchmark as Needed Establish MFA data collection method Establish QCPC data collection method Establish SPC data collection method Gather Data
Analyze current costs / potential savings Perform Waste analysis on “As Is” process. Understand process variation Understand process performance
5 4
CONTROL
3
IMPROVE
2
ANALYZE
1
MEASURE DEFINE
Type PROJECT TITLE here
Type Date here
Put a picture of the part here (if applicable)
DMAIC Project Summary
Define, Measure, Analyze, Improve and Control
Perform Root Cause Analysis on problems. Develop / select alternative solutions Map “To Be” Process Develop Action Plan Management Review Pilot changes and validate improvement
6 sigma GB Project

Project name
6
2016/5/31
Project Schedule
Process Step
Schedule Step 1. D (Define) Define process to be improved Define customers & CTQs Define project scope and set goals Define project charter Step 2. M (Measure) Establish project Ys List prossible Xs Data collection Measurement system analysis Determine process capability 1 2 Jan 3 4 1 2 Feb 3 4 1 2 Mar 3
ALC planning, MH and MRB cost will be saved through this project.
Project name
10
2016/5/31
Define Measure Analyze Improve Control
Project name
11
2016/5/31
12
2016/5/31
Data Collection Plan
流挂类型 操作定义 数据来源 和位置 样本量 数据 采集人 数据采集 时间 数据采集 方法 应同时采集 的 其他数据
Y油漆流挂
流挂率=发生流挂车架数量/实际 生产的车架数量*100%
取正常生产产品, 在油漆下线区域进 行检验
2000套
2013年2月 ~9月
7
4 0.00%
注:流挂明显的分布于边梁与前板位置
六西格玛报告模板

USL
Within Ov erall
P otential (Within) Capability Cp CP U CP L Cpk Cpm Overall Capability Pp PPU PPL P pk * -0.67 * -0.67 * -0.70 * -0.70 * 0 500 1000 1500 2000
必经过程
DEFINE
项目背景 照片 目前水平(包括σ水平)
Y = SW set up times
Page 4
Shanghai Morgan Carbon Co.,ltd
可选工具
Current performance level
Morgan Six Sigma Project Report 你的项目名
Morgan Six Sigma Project Report 你的项目名
Project Title
: 你的全部项目名 : 你的姓名 : Shanghai Morgan Carbon : Shanghai. China : YYY :
PROJECT INFO
Green Belt Division Location Sponsor Champion
process capability study for SW set up times(one kanban) USL is our goal = 480 seconds
Process Capability Analysis for setup time
LB
P rocess Data US L Target Lower B ound Mean S ample N S tDev (Within) S tDev (Overall) 480.00 * 0.00 1038.55 40 267.472 277.981
优秀六西格玛报告模版
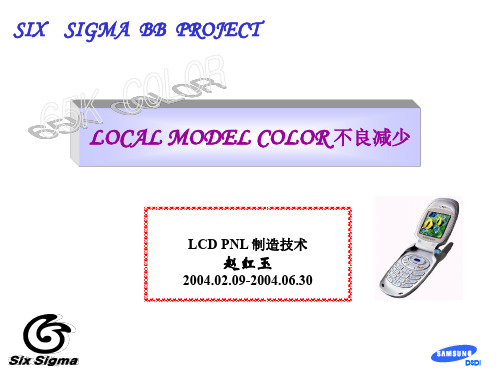
业务:
确保优秀原材料品 质
● Project Plan
MA I C
PHASE Define Measure Analyse Improve Control
DATE
3月3日 3月30日 4月30日 5月30日 6月30日
MEETING
推进内容
2月20日
1.课题计划、目标及方法 2.推进人员的责任及分配
R=0.09361 LCL=0
WE-12R09E1、 2月份 COLOR 散布比较大,需 要改善!
11
● Stability of Y
D
AIC
Normal Probability Plot
Normal Probability Plot .999
.99 .95
Probability Probability
1
● Project select
事业场经营方针
LCD经营方针
MY PROJECT
LOCAL MODEL COLOR 不良减少
确保世界最佳 LCD事业场
生产及品质 水准一流化
MA I C
全社经营方针
对应未来加速 “结构改革”
2
Count Percent
● Problem Statement 1
环境变化:COLOR 产量急剧增长(单位:KPC)
6000 5000 4000 3000 2000 1000
0
2278 2月
2661 3月
3444 4月
4537 5月
4944 6月
MODEL 别COLOR 不良率
Pareto Chart for MODEL名
4
3
2
1
0
6sigma五大阶段学习内容汇总

●对趋势图的 解释 ?
分析阶段-假设验证
Define
Measure
Analyze
Improve
Control
1. 假设验证概念
◎ 假设验证的概要 假设验证是 ? 把想要了解的内容(现象)建立成假设,通过收集的 Data进行分析,验证假设是否成立的步骤
▶ 回归假设 (Null Hypothesis : H0) - 在显著性水平α下,可以接受的假设 - “一样 ” , “无差异 “ 等的 Equal 概念.
分析阶段概述
Six Sigma技术与方法
分析阶段的目的是找到Y=F(x1,x2,x3……)中关键的x, 改善阶段目的是对x进行优化,以提升Y
Step 1 – Project选定(背景陈述) Project选定过程及必要技术 Project的目标和范围的设定 Project实施计划的承认 Project 满足CTQ的具体指标 测量把握现水准,确定改善目标 潜在原因变数 (X’s)的挖掘及优先化 Data 分析计划的树立及收集活动 为了确认Vital Few X’s的统计分析 分析结果 Review , 改善优先顺序 Vital Few X’s的特性区分 明确Y与 X’s的关系 决定最佳条件 决定方案的验证及改善效果的确认
Y
离散型 • 回归分析
• Run Chart
X
离散型
连续型
• Run Chart • Pareto Chart
X
• Proportion -Test
分析阶段-突出暂定因子 例-logic tree
Y Level 1 Level 2(x)
学历
能力
口才
气质 存款
找到几个关键的小x,并最优化小x, 来提升大Y的值,这个是六西格玛分析 改善阶段的任务
6sigma report final

D M A I C M
MSA for Dage4000
Accuracy: The test data shows Dage4000 accuracy is normal. For Dage4000 the accuracy +/-0.25% of full-scale. Using pull cartridge and special weight.
D M A I C
改善前後比 較
黃單數量Trend chart
100 80 60 40
40張
改善前
81張
改善後
20 0 avg'06
23張
29張 18張
Jan'07
Feb'07
Mar'07
Apr'07
改善后月均28張
D M A I C
改善前後比 較
改善前
Year of 06
改善後
Jan’07~Apr’07
調機
Process Flow Diagram
調機
Reject NVA NVA Pass Reject NVA Pass
VA Wire bonding
MNT 拉力
MNT 推球
WB L/A
佔黃單 總數 44.2%
佔黃單 總數 23.1%
由此可見拉力黃單佔黃單總數比重很大
D M A I C M
Fishbone
A.降低生産成本:
3 IDL cost/hour*40*12+ Saving WIP inventory cost + 1EA shelf =3*(3000÷21÷8)*40*12+3*9600*40 (WIP inventory)*2.26% (1 year interest)+2000 =25,714+26,035+2,000=53,749RMB=214,996NTD/year 預期目標Goal Statement 1. 黃單數量由81張/月→39張/月 Project Schedule
6Sigma 报告

标准测标不良改善 6sigma
Start Date:2010.06.25
上海欣洲电气有限公司
DMAI源自CMeasure Analysis
D
M
A
I
C AV:重复性
GR&R Analysis 检验 检验:
EV: 再现性
评估校验测量系统: 两名工作人员分别对10个产品进行2次测量,量测值如下:
型号 日期 单位:秒 零件号 1 2 3 4 5 6 7 8 9 10 量测值 第1次 19.1 19.3 19.0 18.8 20.0 19.1 19.8 19.4 18.7 19.2 第2次 20.4 18.9 19.0 18.6 17.8 17.7 19.3 19.1 17.7 19.5 平均 20 19 19 19 19 18 20 19 18 19 19 全距 1.3 0.4 0 0.2 2.2 1.4 0.5 0.3 1 0.3 1 MT 1PC10A 机台号 TTH012 型号 日期 单位:秒 量测值 第2次 19.2 18.1 18.7 18.0 18.7 18.7 19.7 18.9 18.0 18.9 平均 20 19 19 19 19 18 20 20 18 19 19 全距 1.4 1.6 0.6 1.1 0.1 1.4 0.1 1.3 0.2 0.3 1 MT 1PC10A 机台号 TTH012 2010.07.21 操作员:张秋芳 2010.07.21 操作员:吴晓霞
零件号 第1次 1 2 3 4 5 6 7 8 9 10 20.6 19.7 19.3 19.1 18.6 17.3 19.6 20.2 18.2 18.6
DMAIC六西格玛项目报告模板(共32张)

Action Taken
Cycle Time
30 20
10
0 0
5
10
15
Approval Time
Key Deliverables-交付项
▪ Data Analysis ▪ Hypothesis Test ▪ ANOVA ▪ Regression ▪ DOE
▪ 数据分析 ▪ 假设检验 ▪ 方差分析 ▪ 回归 ▪ DOE
第21页,共32页。
4.0 Improve Performance-改进(gǎijìn)业绩
DOE/RSM-响应曲面设计
Objective-目标
Main Activities-活动
Potential Tools and Techniques-工具和技术
Key Deliverables-交付项
• To identify critical measures to evaluate the success, meeting critical customer requirements
2.0 Measure Performance-绩效(jìxiào)测量
MSA-测量系统分析(Ys)
第11页,共32页。
2.0 Measure Performance-绩效(jìxiào)测量
Baseline and Objectives of Process –过程的基线和目标
第12页,共32页。
Potential Tools and Techniques-工具和技术
Gap Sigma Goal
Project Charter
Business Case Opportunity Statement Goal Statement Project Scope Project Plan Team Selection
六西格玛项目报告模版

18
M7
部分改善措施
经过2ndFMEA后,采取的主要改善措施有
D M A I C
改 善
前
改 善
后
图片
图片
改善前现象
改善内容
19
M7
部分改善措施
工程 名 改善项 目 对策实施 LIST(具体 内容)
D M A I C
改善前现况 负责 人 完成日 期
NO
20
M8
Trend Chart
经过部分改善措施后,Y的现况如下:
部 门: Green Belt: 开 始 日 期: 结 束 日 期:
1
D1 Project Selection
D M A I C
1.Project选定(Project selection) : 说明项目的来源,或选择该项目的背景是什么? 选择它是从公司和部门的目标出发? 还是从顾客的要求出发? 还是管理一线迫切需要解决的问题?
XXXXXXXX
XXXXXXXX XXXXXXXX XXXXXXXXXX
XXXXXXX XXXXXXX XXXXXXX XXXXXXXX XXXXXX XXXXXX XXXXXX
XXXXXXXXX XXXXXXXXXX XXXXXXXXXX XXXXXXXX XXXXXXX XXXXXXXX XXXXXXX XXXXXXX
内部 顾客
是谁?
D M A I C
外部顾客
是谁?
内部顾客VOC
外部顾客VOC
无异物 洁净 的产品
项目CTQ
4
D4
Problem Statement
D M A I C
2.问题陈述(Problem statement) : 选择该项目的理由的进一步说明,你为什么认为它是个 问题?它比其他问题严重吗? 说明该问题造成的后果有 多严重?该问题发生在何时?最近该问题如何? 最好用图表量化表示.
六西格玛项目报告模版41页PPT

22
A1 MSA for X
测量内容:XXXX ★[样本数量]:共X个 ★[测 量 者]:XXXXX ★[测量方法]:
0
12
0
13
0
14
0
15
我们从XX个输入因子中进行降序排列,从中筛选出了XX个影响顾客不良的输入因子,下一步0
合计 将对该XX个重要的输入因子再进行FMEA,进一步找出最关键的输入因子.
16
M5 失效模式分析(FMEA)
DMAIC
工序
输入
潜在的失 败模式
潜在失败 影响
严重 度
潜在要因
发生 率
当前控制 方法
5
D5 Project Scope
Process 宏观流程图
微观流程图
Production Production是什么?
6
DMAIC
D6 Y Defining and Defect
Y定义
是什么?
DEFECT
Y1.是什么? Y2.是什么? Y3.是什么?
DMAIC
7
D7 Goal Statement
部
门:
Green Belt:
开 始 日 期:
结 束 日 期:
1
D1 Project Selection
DMAIC
1.Project选定(Project selection) :
说明项目的来源,或选择该项目的背景是什么? 选择它是从公司和部门的目标出发? 还是从顾客的要求出发? 还是管理一线迫切需要解决的问题?
DMAIC
结论:
13
M3 Process Mapping
输入
类型 过程 输出
XXXXXXXX XXX
六西格玛黑带项目报告

某汽车线束有限公司六西格玛黑带项目报告降低开线工序质量损失2005年6月整理公司简介某汽车线束有限公司是生产中高档汽车线束之中外合资企业,主要客户有上海大众、上海通用、延峰江森、科世达- 华阳、日本丰田、日本铃木等。
公司已通过QS9000、质量管理体系、ISO14001环境管理体系、OHSAS1800职1 业健康安全管理体认证,目前正在推行ISO/TS16949 质量体系认证。
团队名称: 潜海队(潜入海底,寻找隐藏的冰山)项目背景:客户反映(最初是延峰江森),电线长短不一致现象较普遍,装配极不方便,尤其当一束电线中粗线偏长而细线偏短时,很难安装也容易出现其它意想不到的隐患,如拉断、脱钉等。
但因电线有柔性,还勉强可以安装,虽然没有造成客户正式投诉,但影响了客户对公司的满意程度。
项目选择:汽车行业零部件价格每年都以一定比例下降,降低生产成本是汽车零部件企业必须面对的客观现实。
在公司领导大方向的指引下,我提出了降低开线工序质量损失的项目,经过咨询公司和金亭公司领导的论证与评价之后,正式批准立项。
线束制造主要过程包括前工程开线打钉、后工程装配、QC检查及包装,前工程所用材料金额占总用料的70%以上,设备占全过程80%以上。
开线工序包括手工开线(C351开平线)、自动开线(KOMA、XC451、K333、C551 等自动开线打钉机)。
降低劣质成本首先想到的是降低内部损失,比如不良率、返工、返修。
后来统计03年1-6 月份各种不良率包括工序内不良、批量不良、零星不良累加一起,外销平均286ppm,相当于σ水平,内销平均900ppm,相当于σ水平,改进空间不大。
而工序质量损失还包括计量设备费用、检定周期、电线浪费、端子损耗、电线尾和端子尾等等。
也就是要在整个开线工序中寻找并设法降低劣质成本。
第一阶段:项目界定2) 项目“股东”分析(Project Stakeholder Analysis)3) 确定项目范围:为了在无边无际大海寻找质量损失,我们必须确定项目范围,于是小组对开线工序进行了详细的流程分析:图1 开线工序工艺详细流程图人员准备设备点检项目小组成员,采用头脑风暴,分析每一步工艺流程可能的质量损失环节:工序1:接收排期1.1 生产调配不合理;1.2 排期变动太多造成材料浪费;1.3 排期变更太多,造成人员加班1.4 排产不准确,造成半成品呆滞或报废损失工序2:分工艺卡(线卡、压着卡)2.1 工艺不完善2.2 开发变更错误工序3:领料端子盘脱落电线来料错误(标识、线色)端子方向绕反欠料物料来料不良/ 线色不符多芯线剥皮不好剥,造成作业速度慢,报废来料不良,错料换料,时间耗费,领料不准确,物料积压,占用资金待料材料损失工序4:确认物料来料烂线工序5:人员准备人员培训不到位出现不良后,人员再次培训技术人员、操作人员经验不足人员流失再次培训人员流失大员工睡眠不足,影响正常作业宿舍太热,同一宿舍也有三班翻班排期变更太多,造成人员加班工培训不到位,无法判定不良品人员流失人员流失(新员工上岗能率降低,不良品增多,增加检查人员)工序6:设备点检设备故障员工缺勤机器空缺测量端子电线时停机(要求每50PCS测量一次)设备故障工序7:机器参数设定违反作业手册电线长度偏长造成浪费工序8:首件加工违反作业手册未作好“三对照”导致用错端子(客户投诉)工序9:首件确认变更错误计量器具损坏作业过程中识别不良时待确认等来料不良增加作业员检查时间由于各种原因造成员工疏忽,看错线卡,开错线作业员未作好“三对照”工作,造成批量不良检验员对特许使用的产品判断不熟练检具的鉴定用期自动侦察出的电线损失较大工序10:模具设备调整模具调试模具不良引起的调机浪费,工时等待模具不稳定,造成检查端子时间加长模具、设备不稳定模具、设备不稳定造成端子变形,烂线等的批量不良每一批产品增加检查频率调试模具时,电线、端子的损耗工序11:批量加工批量不良作业工具不保养,损坏(开线钳、剪刀等)批量不良造成的浪费批量不良流入后工程零星不良,造成后工程停机未作好“三对照”导致用错端子(客户投诉)工序12:中间检查批量不良来料不良增加作业员检查时间不良在不影响功能的情况下,不需要报废。
6 Sigma report

牧田产品227719-8加工工艺流程图 1 12 2 3 4 5 6
备注: 正常工序:
11
10
9
8
7
延迟:
检验:
13
14
15
16
存储:
返工:
运输:
矩阵图
过程输入 重要影响 1 2 3 4 5 6 7 8 9 10 11 12 13 14 15 16 原料进料检验 下料 正火 车夹位钻孔 车外形A 车外形B 平端面 滚齿 去毛刺 中间检验 渗碳淬火 抛光 珩孔 综合检验 最终检验 包装入库 珩孔废品率高 10 2 0 3 1 5 0 1 0 3 0 2 2 10 0 0 0 珩孔效率低 8 2 0 3 0 2 0 0 0 0 0 4 3 8 0 0 0 36 0 54 10 66 0 10 0 30 0 52 44 164 0 0 0 合计
227719-8产品总共节约金额 产品总共节约金额=81504元/年 产品总共节约金额 元 年 珩孔效率提升46% 珩孔效率提升
Team Member
序号 1 2 3 4 5 6 7 组员 项目组长 设备维修 过程指导 数据收集 车间班长 品质 采购 姓名 喻春金 张久元 喻春金 喻春金 曹晓书 汪先冬 杨启林 项目过程中负责的内容 项目组织,跟进,数据分析等. 设备功能回复,易损件的维修、更换、保养等. 对相关责任基层管理者进行操作及基本保养的培训. 定义过程中的数据收集及改善过程中的各种数据收集. 对相关操作员工进行操作及基本保养的培训. 对改善后的品质进行长期跟踪统计、通报改善后的废品情况. 设备配件的采购.
6 Sigma project report
解决齿轮类产品珩孔效率低、 解决齿轮类产品珩孔效率低、废品率高的问题
6sigma改善活动报告-新版.ppt

人
标准不明确
作业不熟练
X1 X2
SHORT漏焊 /假焊/
作业不良
机器 材料 方法
波峰焊高度 波峰焊温度/预热温度
FLUX的密度 S/MC的速度 焊锡的质量
PAD氧化 部品氧化
TEAM 长 XXX
D
指导 LG XXX
M A IC
PCB主管 XXX
生产部经理 XXX
工程主管 XXX
生产部锡炉技术员 XXX
资料收集 及
对策实施
资料收集 及
对策实施
资料收集 及
对策实施
4/33
对锡炉SPEC参数 调整和资料收集及
对策实施
彩 煌
CH
Technology
现水准把握/目标设定
D
Converting into Z value
Technology
03 Theme 登录书(6σ 活动)
BIG Y:外驻管理强化
Theme名 XX科技基板PCBA锡点不良改善
活动Team名 XXTEAM 活动 时间 2012.5.20-7.20
主要 改善 对象
PCBA锡点不良率降低
为什么 要做(背景)? 内/外部 环境
Theme 定量性 目标
b)AUTO SOLDER每日检则
4、2#锡更换使用“云南锡” 5、生产异常管理流程化 6、根本对策立即实施,IPQC/PE跟踪确认
- 基板工程不良率高及LOT合格率低, 且变化不稳定,造成总装反馈不良 率高.
- 适应LG客户品质的要求,通过6σ活
- Brain storming - LOGIC TREE - Gage R&R - Hypothesis TEST - MELT IN
六西格玛绿带培训教材(英文版)

DAY 5 (Analyze Phase分析階段):
- What is a binomial distribution ?什么是二次項分配 - Conditions for the use of the Bernoulli trials (流程) - Graphical illustration of a binomial distribution二項次分配繪制的說明 - Measures of central tendency and dispersion for binomial distribution 二項次分配的集中趨勢和離散趨勢的測量 - Probability calculation with binomial distribution用二項次分配計算概率 - Binomial distribution case studies二項次分配的案例學習 - Characteristics of the Poisson distribution泊松分配的特點 - Probability calculation using Poisson distribution用泊松分配的概率計算 - Poisson distribution as an approximation of binomial distribution 泊松分配是一個比較接近二次項分配的 ------------------------------------Break---------------------------------------------- Poisson distribution case studies泊松分配案例的學習 - Introduction to normal distribution介紹正態分配 - Characteristics of normal distribution典型的正態分配 - Areas under the normal curve正態曲線內部的區域面積的理解 - The use of normal probability distribution table使用概率分配表 - Probability calculation using normal distribution利用正態分配計算概率 - Normal distribution case studies正態分配案例的學習 - Using computer to calculate probability of different distribution 利用電腦計算不同性質的概率分配 ------------------------------------Lunch---------------------------------------------6
6σ简介
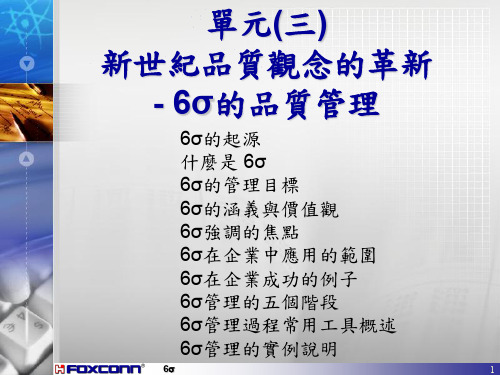
35%
30%
劣質成本 (%銷售額)
25%
20%
15%
10% 5%
DPMO 3.4 233 6210 66,807 308,537 691,462
σ
6
5
4
3
2
1
6s
10
6σ的涵義與價值觀
6σ —實際的涵義
99%好(3.8σ)
99.99966% 好 (6σ)
• 每小時丟失20,000個郵件
• 每小時丟失7個郵件
品質工程分為線上(On-line)及線外( Off-line)兩部分。
線上品質工程,主要應用的手法有新品管七大手法,統計過 程控制等常用在制程之改善
線外品質工程,系針對產品設計開發及制程設計開發而發展 出来的系統方法,對產品的品質影響較大。
6s
17
6σ在企業中應用的範圍
那些業務功能需要 6σ?
服務
6s
28
鑑別CTQ(Critical To Quality)
從顧客的角度定義對顧客最重要的 產品和服務特性
CTQ必須可以測量.必須要能夠透過測量 CTQ,來決定一個6σ專案開始時的當前績 效水準,以及專案結束時用CTQ來驗證顧 客滿意是否有所改善,都是很重要的.
6s
29
甚麼甚對麼顧對客最顧重客要最?重要?
{ Average Company
Best Companies
{ Airline Safety
6s
8
6σ—績效目標
σ
長期合格率
標準
3σ
93.32 %
歷史的
4σ
99.379 %
現行的
5σ
99.9767 %
6 sigma 2ndQtr report
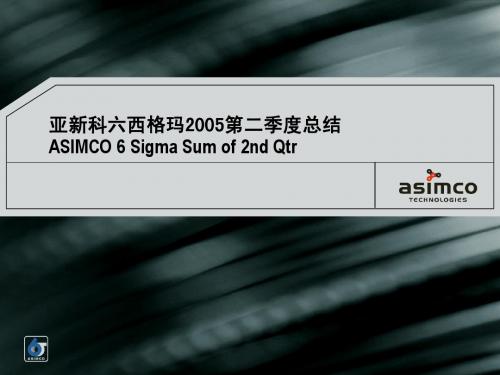
在2005年总部在运营公司举行了一系列的六西 格玛认知和绿带培训. 上半年参加认知培训: 489人 参加绿带第一阶段培训学员: 381人 参加绿带第二阶段培训学员: 309人 己培训绿带学员比例从2004年占公司总人数的 0.75%增加到目前的 3.6%,占非生产一线员工的12%
Abstract of Six Sigma implementation in 1st Qtr 6西格玛实施摘要 西格玛实施摘要
Six Sigma implementation Sum in 1st half year 上半年六西格玛推行总结
Negative aspect
– Only Tianwei and Meilian have full time BB and some BBs in low administrant position, which make it difficult to coordinate in different departments of OC. org should be more powerful even the org is stronger than it in 2004. – Projects on time close rate is not good, too busy or some unexpected things happed are normal excess. – Six Sigma awareness level still is not high and need more training by OP themselves – Guan and Camshaft still have not project kick off. – Saving calculation is a complicated case, because some meaningful projects can not get direct cost or can not get payback in short period of time
客户维修服务部6SIGMA项目立项报告书

客户维修服务部6SIGMA项目立项报告书客户维修服务部6SIGMA项目立项报告书一.项目名称:缩短联想显示器维修周期二.项目描述(一)将联想显示器维修周期从现在的7天缩短至3天(二)利用SIX SIGMA方法建立客户维修服务部持续改进机制与队伍。
改进维修服务工作质量,促进联想“大服务”。
三.项目来源:来源分析(一)联想显示器维修周期长是维修服务不满的重要原因一层不满指标分布图:结论:各类产品维修时间长是导致客户不满的最主要原因,不满比例最高,均在40%以上。
解决维修时间长是我们当前维修服务解决问题的当务之急。
维修时间长造成用户不满的比例图结论:显示器维修周期长是造成维修时间长的主要原因。
维修时间与用户不满程度分析图:维修时间与用户不满程度趋势图:结论:用户在显示器维修达到7天时,还可以忍受;如果维修周期达到14天,就是用户忍耐的极限。
我们应该按维修周期严格控制在7天之内。
但目前我们只能达到平均7天。
最大值与用户的差距过大。
(二)显示器维修周期明显长于主机问题的维修周期 主机维修周期与显示器维修周期对比图:结论:显示器维修周期明显长于主机维修周期。
两者之间存在巨大的差距。
我们在维修中与用户对显示器维修的认识有差距:我们认为主机是我们生产的,是联想的产品,显示器是供应商生产的不是联想产品;用户的想法是无论主机还是显示器都是联想的产品。
(以上数据来源于客户维修服务部客户调查处2001年第一季度情况分析)四.推广策略:策略及策略分析不满程度周期分布0.0430.3930.2050.3160.0430.10.20.30.40.57天14天21天30天30天以上不满程度2468主机显示器系列1(一)策略一.推广显示器本地自主维修模式结论:本地自主维修比重占整体维修数量还是较小,应扩大到60%以上。
返京维修的周期过长,比重应该最大限度的降低。
(二)策略二.制定显示器维修SOP,控制、缩短显示器返京维修、区域维修、本地维修的周期各种维修模式的维修周期不稳定当地维修周期分布图:返京维修周期分布图:结论:一种维修模式的每一次的维修时间差异过大,说明我们的维修过程不受控。
- 1、下载文档前请自行甄别文档内容的完整性,平台不提供额外的编辑、内容补充、找答案等附加服务。
- 2、"仅部分预览"的文档,不可在线预览部分如存在完整性等问题,可反馈申请退款(可完整预览的文档不适用该条件!)。
- 3、如文档侵犯您的权益,请联系客服反馈,我们会尽快为您处理(人工客服工作时间:9:00-18:30)。
IMPROVE- Improvement Plan
Improvement plan:
Root Cause
Lack of usual component statistics document Cable selection depend on experience Lack of crimping list model Lack of DVP model
16
D M
A
I
C
P-MAP
After improvement, we added some critical inputs to steps, which will help reduce the overall lead time.
Security Classification
17
IMPROVE- IMR Chart (Before/After)
Failure Effects
SEV
OCC
DET
RPN
Cause
Controls
Actions
Component selection
Cost increase
9
Cable selection depend on experience Lack of usual component statistics document
Security Classification
12
D M A
I
C
Improve Design Process
※ Crimping List
Security Classification
13
D M A
I
C
Improve Design Process
※ Design Validation Plan
Security Classification
8
Design cable selection tool
7
504
According to cable selection tool, select suitable cable diameter Select component from BOD,and update BOD regularly
Component selection
8
Lack of crimping list model
8
Build Crimping list model
7
448
According to crimping list model complete crimping list.
Design Valiadtion Plan
9
Lack of DVP model
7
Build DVP model
7
441
Write DVP refer to DVP model and then get customer approval Take unique input document format other engineer check 2 times request customer double check input data.
45
5
SE drawing error
Modify Drawing
3D harness arrange
3
Customer arround date unfullness
4
Duble check data with customer
4
48
Security Classification
8
MEASURE-PARETO
Compare Current Status and Improved Status
Improved level is 7.08 days.
Conclusion: Generally, HV harness design lead time reduced 7 days, which is 11.6% reduction.
Security Classification
2
D
M A
I
C
Contract Sheet
Security Classification
3
D
M A
I
C
Problem Description and Background
Background:
– HV Harness conceptual design includes Electrical Schematic Design, Components Selection, 3D & 2D Harness Drawing Design, BOM & Chart, Crimping list, and Design Validation Plan. When a certain business opportunity comes, all above need to be prepared and sent to SAL, PUR, IE, etc. for quotation and prototype.
Security Classification
4
D
M A
I
C
Initial Lead Time
Current level is 60.75 days.
Security Classification
5
D
M A
I
C
SIPOC
Y
Security Classification
6
D
M
A
I
C
P-MAP
These 3 steps greatly impact the total HV harness design lead time, which will be our focus.
Security Classification 18
D M A
I
C
Control Plan
Security Classification
19
SAVING
The improved process of save cost is as below:
Hybrid average salary:1000 $/month Work time:176h/month Hybrid engineer quantity:11 Each step save time as follow: Technical Proposal:2day BOM:0.5day Chart:0.5day Crimping list:0.5day Drawing&3D:2day DVP:1.5day Total:7days Save cost: $ 318.2 Hybrid average salary:$1000 /month Work time:176h Hybrid Project number:33
Draw schematic
Schematic error
Customer input error 2D drawing error Harness interfere with other component
4
3
Double check customer input
Double check
4
3
80
Securit- Auto Program Introduction
Auto Test Program Measurement Program Interface – one setup , four test items
Conclusion: Using this auto test program, we can do USB RF four test items simultaneously, and achieve auto measure and saving test data.
Security Classification
7
ANALYZE-FMEA
Failure Modes and Effects Analysis ( FMEA )
Process Stephe Failure Mode
Cable design diameter bigger than ausual requried Component unusual
14
D M A
I
C
Improve Design Process
※ Bill of design --- Cable
Security Classification
15
D M A
I
C
Improve Design Process
※ Fuse & Cable Selection Tool
Security Classification
Problem Statement:
– Now many documents and drawings need to be prepared for quotation, and more and more business opportunity will be come in future, so it is urgent to optimize the conceptual design process and shorten lead time.
purchase difficultly
8
7
Build BOD
8
448
Select crimping requirement
Crimping requirement Lead time to and test long mothod various DVP can't satisfy to customer DV test standard and parameter various