SPS –Kitting 拉动方案
SPS简介

底盘线 Chassis Line
• 底盘线主要负责给GA底盘生产线的零件配载工 作,底盘线共分为C1、C2 两条路径,共拣取 零件42余种,底盘线的零件装配质量直接影响 到汽车的安全及行驶性能。
• The chassis line in SPS mainly load 42 parts on carts for GA assembling, both C1&C2 branch routes composed of the whole chassis line. And the quality of chassis parts and its installation will directly result in the driving & safety capability.
NS2 SPS件选择及配载 * 除标准件、本地供应商排序直送零件和特殊大件外的零件
Parts except standard parts, local JIT parts and specific big parts. * SPS零件按单车用量配载上线
SPS parts will be kitted and supplied to line based on consumption per vehicle.
The pickers use the scanner at the first station of each SPS Kitting line to scan the bar code on the SPS Kitting Manifest, and the Banner lights for all the materials on the manifest will be turned on, giving the pickers guidance where to pick the parts.
厂内物流规划设计
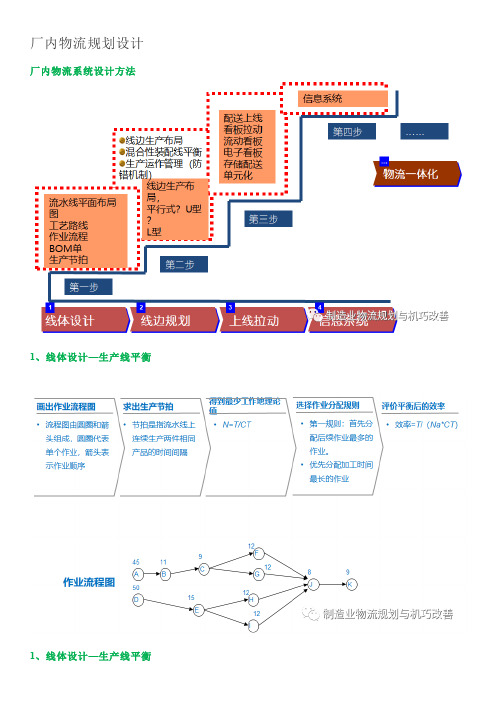
厂内物流规划设计厂内物流系统设计方法1、线体设计—生产线平衡1、线体设计—生产线平衡通过合理布置工作地,划分workstation,获得更高的生产线平衡.1、线体设计—平面布置SLP线体设计工具:E-FACTORY眼下很多工厂在进行规划时,都会做物流仿真,物流仿真的要点就是输入的数据需要系统,准确,不然不正确的输入,不会推导出一个合理的结果。
仿真可以大大减少未来运行的一些问题,可以说是预防性的演练与优化。
2、线边规划—线边库存每一种零部件在生产线边或仓库内的存放数量需最大程度保证生产的连续性并兼顾库存的最小化。
在设计线边库存和仓库库存时充分考虑以下因素:2、线边规划—物料存储区域规划线旁的面积是黄金,所以如何合理利用线边的空间是关键,既要保证线边作业美观,又要保证人员作业顺畅少步行,那就需要物料供应的手边化,结合工装设计来达到理想的线边物料供应模式,如今流行的是同步台车伴随供应的模式。
线边规划—存储区域规划作业步骤线边规划—物料存储规划方法线边规划是物流规划的起始原点,确定了物料上线的方式即可进行倒序推演。
如线边要求裸件上线,那么就需要供应商端包装也是为裸件包装,或者在RDC翻包成裸件上线的方式。
线边采用什么样的供应方式,是超市供货,是KITTING配送,还是SPS,JIS等方式都影响着物料的一系列属性。
3、上线拉动—工作流程3、上线拉动—物料供应基于供应商的两种上线拉动模式4、信息系统—MES功能规划设计4、信息系统—WMS功能规划设计WMS拥有以下四大核心优势:1、供应链系统集成思路通过观察,现如今制造业有几大趋势:1)国内市场群雄逐鹿,消费市场拓展方向转向个性化制造与中小城市;2)管理的数字化转型加快;3)线下模式的探索与复制加剧;4)阿x用投资,腾x用流量,京x用供应链基础设施服务能力布局市场;5)商业模式迭代方向:B2B/B2C/O2O→F2B2C→ODE→C2M,从制造—销售—需求转为需求预测—制造的计划性经济。
奇瑞捷豹路虎:树立汽车行业精益物流标杆
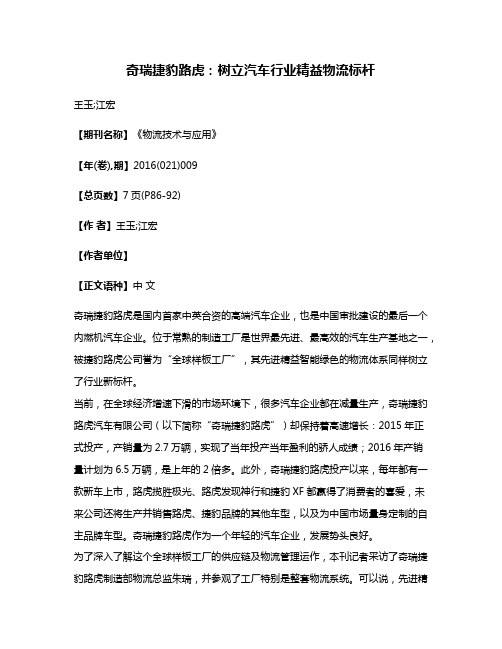
奇瑞捷豹路虎:树立汽车行业精益物流标杆王玉;江宏【期刊名称】《物流技术与应用》【年(卷),期】2016(021)009【总页数】7页(P86-92)【作者】王玉;江宏【作者单位】【正文语种】中文奇瑞捷豹路虎是国内首家中英合资的高端汽车企业,也是中国审批建设的最后一个内燃机汽车企业。
位于常熟的制造工厂是世界最先进、最高效的汽车生产基地之一,被捷豹路虎公司誉为“全球样板工厂”,其先进精益智能绿色的物流体系同样树立了行业新标杆。
当前,在全球经济增速下滑的市场环境下,很多汽车企业都在减量生产,奇瑞捷豹路虎汽车有限公司(以下简称“奇瑞捷豹路虎”)却保持着高速增长:2015年正式投产,产销量为2.7万辆,实现了当年投产当年盈利的骄人成绩;2016年产销量计划为6.5万辆,是上年的2倍多。
此外,奇瑞捷豹路虎投产以来,每年都有一款新车上市,路虎揽胜极光、路虎发现神行和捷豹XF都赢得了消费者的喜爱,未来公司还将生产并销售路虎、捷豹品牌的其他车型,以及为中国市场量身定制的自主品牌车型。
奇瑞捷豹路虎作为一个年轻的汽车企业,发展势头良好。
为了深入了解这个全球样板工厂的供应链及物流管理运作,本刊记者采访了奇瑞捷豹路虎制造部物流总监朱瑞,并参观了工厂特别是整套物流系统。
可以说,先进精益的供应链体系、高效智能的物流系统、持续改善的运营管理,为奇瑞捷豹路虎打造高度自动化、柔性化、智能化的汽车工厂奠定了坚实的基础。
奇瑞捷豹路虎汽车有限公司成立于2012年11月,由中国奇瑞汽车股份有限公司和英国捷豹路虎汽车公司共同出资组建,总投资额109亿元人民币,合资双方股比为50:50。
奇瑞捷豹路虎公司总部位于上海,生产基地位于常熟市沿江经济技术开发区,距离上海仅一个小时左右车程,占地面积约1平方公里。
1.工厂概况奇瑞捷豹路虎常熟工厂拟分两期建设,已投入运营的一期项目占地面积84.5公顷,规划整车年产能13万辆。
目前,常熟工厂拥有冲压、焊装、涂装、总装四大工艺车间,均按照全球最先进的汽车工厂建造标准建设。
随行配料系统(SPS)布局方案设计
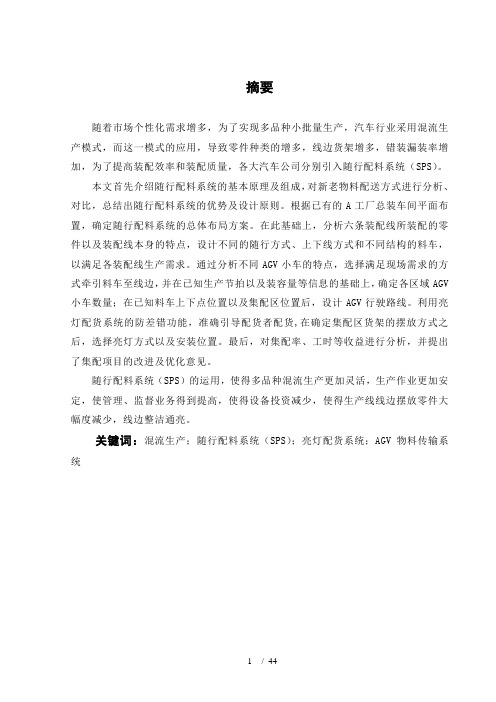
摘要随着市场个性化需求增多,为了实现多品种小批量生产,汽车行业采用混流生产模式,而这一模式的应用,导致零件种类的增多,线边货架增多,错装漏装率增加,为了提高装配效率和装配质量,各大汽车公司分别引入随行配料系统(SPS)。
本文首先介绍随行配料系统的基本原理及组成,对新老物料配送方式进行分析、对比,总结出随行配料系统的优势及设计原则。
根据已有的A工厂总装车间平面布置,确定随行配料系统的总体布局方案。
在此基础上,分析六条装配线所装配的零件以及装配线本身的特点,设计不同的随行方式、上下线方式和不同结构的料车,以满足各装配线生产需求。
通过分析不同AGV小车的特点,选择满足现场需求的方式牵引料车至线边,并在已知生产节拍以及装容量等信息的基础上,确定各区域AGV 小车数量;在已知料车上下点位置以及集配区位置后,设计AGV行驶路线。
利用亮灯配货系统的防差错功能,准确引导配货者配货,在确定集配区货架的摆放方式之后,选择亮灯方式以及安装位置。
最后,对集配率、工时等收益进行分析,并提出了集配项目的改进及优化意见。
随行配料系统(SPS)的运用,使得多品种混流生产更加灵活,生产作业更加安定,使管理、监督业务得到提高,使得设备投资减少,使得生产线线边摆放零件大幅度减少,线边整洁通亮。
关键词:混流生产;随行配料系统(SPS);亮灯配货系统;AGV物料传输系统AbstractWith the increasing market demand for personalized, in order to achieve more varieties of small batch production, the automotive industry using mixed production mode, and the application of this model, leading to an increase in types of parts, wire shelf edge increases, the wrong equipment installed leak rate increase, in order to improve assembly efficiency and assembly quality, the major car companies were introducing set part supply (SPS).This article introduces the basic principles of the set part supply (SPS) and its composition, comparing and analyzing the new and old material distribution methods, summarizing as well the advantages and design principles of the system (SPS). The overall layout of the set part supply (SPS) program is determined on the basis of the existing a factory assembly shop layout. Six assembly lines and their characteristics are analyzed with the aim of designing different patterns and structures to meet the demand of production lines. The characteristics of different AGV cars are analyzed, the AGV car with the pattern top traction is selected, sending the materials to the line by using the mode of tape navigation.Based on the known production rhythm and assembly capacity, the number of AGV cars is fixed. The AGV route is designed after confirming the position of the points on the material cars and the assembly location. The workers can accurately distribute the parts by making use of the light picking system. After fixing the mode of arrangement, the light-on pattern and installation position can be selected. Finally, the earnings such as assembly rates, working hours are calculated, and then some ideas and suggestions are proposed towards the assembly project.With the use of the set part supply (SPS), the multi-species mixed production becomes more flexible, the operation more stable, and the management and supervision business is improved. Meanwhile, reduce greatly the equipment investment and the number of the parts on the line side, which make the line side more clean and tidy.Keywords:mixed production; set part supply (SPS); the lights picking system; AGV cars目录第一章概论................................................... - 1 -1.1 论文研究的意义............................................. - 1 -1.2 随行配料系统(SPS)国内外现状.............................. - 1 -1.3 论文的主要内容............................................. - 2 - 第二章随行配料系统(SPS)介绍................................ - 3 -2.1 随行配料系统(SPS)组成.................................... - 4 -2.2 随行配料系统(SPS)原理.................................... - 4 -2.3 随行配料系统(SPS)优势分析................................ - 5 -2.4 随行配料系统(SPS)设计要求................................ - 5 -2.5 本章小结................................................... - 6 - 第三章随行配料系统(SPS)布局方案设计........................ - 6 -3.1 A工厂总装车间平面布置图.................................... - 7 -3.2 随行配料系统(SPS)布局设计方案............................ - 7 -3.3 本章小结................................................... - 8 - 第四章料车设计............................................... - 9 -4.1 料车的设计原则............................................. - 9 -4.2 六个区域料车设计........................................... - 9 -4.2.1 HC1料车.............................................. - 9 -4.2.2 HC2料车............................................. - 11 -4.2.3 PDB料车............................................. - 12 -4.2.4 POR料车............................................. - 13 -4.2.5 MV1料车............................................. - 15 -4.2.6 MV2料车............................................. - 16 -4.3 本章小结.................................................. - 17 - 第五章 AGV物料传输系统....................................... - 17 -5.1 AGV物料传输系统设计原则................................... - 17 -5.2 AGV小车设计............................................... - 18 -5.2.1 AGV小车选择......................................... - 18 -5.2.2 AGV数量确定......................................... - 18 -5.3 AGV行驶路线确定........................................... - 20 -5.4 本章小结.................................................. - 21 - 第六章亮灯配货系统.......................................... - 22 -6.1 亮灯配货系统应用背景及原理................................ - 22 -6.2 集配区零件布置............................................ - 23 -6.2.1 布置原则............................................. - 23 -6.2.2 布置信息............................................. - 23 -6.2.3 平面布置图确定....................................... - 24 -6.3 亮灯方式及安装位置........................................ - 26 -6.4 本章小结.................................................. - 28 - 第七章随行配料系统(SPS)成效............................... - 29 -7.1 XX公司A工厂总装车间集配信息.............................. - 29 -7.2 总体收益.................................................. - 30 - 第八章结论.................................................. - 31 -结束语....................................................... - 32 -致谢......................................................... - 33 -参考文献..................................................... - 34 -附录1 ....................................................... - 34 -第一章概论在现今汽车生产中,如何利用并不宽裕的物料存储区域,提高装配线的柔性和工作效率,这是现如今每一个汽车公司未来发展的方向。
总装车间SPS运行方式分析

总装车间SPS运行方式分析图1 总装车间平面布置随着丰田生产方式在汽车行业的引入,总装车间物流的SPS(Set Parts System)配货方式也在中国得到了极大关注,无论是丰田合资、大众合资还是通用合资都在大力推广应用。
SPS配货方式就是按每车装配辆份配送货物的方式。
本文将重点分析SPS配货方式的优势、适用条件以及如何合理有效地应用。
SPS运行方式现以总装车间为例,说明SPS运行方式。
图1是年生产单班5000辆整车的总装车间平面布置图。
整车装配在一环形线上完成一次内饰、底盘装配和二次内饰装配,全线有26个装配工位(图1中蓝线所示区域)。
SPS 区域分三块(图1中粉色线所示区域),即仪表板分装零件配货区、底盘零件配货区和一次内饰及二次内饰零件配货区。
总装车间厂房内仅为中小零件的配货区,大件零部件配货、零部件的拆箱、开捆及大件零部件的分装均在另一厂房内,即物流仓库(见图2)。
图2 物流仓库平面布置1.配货顺序总装车间的物流系统在信息控制系统指导下,有条不紊地从仓库货架取出所需零件,按SPS配货方式送到指定工位,配货顺序如下:(1)中央控制室(CCR)根据市场分析及订单情况安排生产计划,并将生产计划的车辆顺序信息向总装车间情报中心传递。
(2)车辆顺序信息传到总装车间情报中心,由情报信息员根据实际工位查找相应信息指示卡。
(3)情报信息员将信息指示卡投递到SPS供应管理板处。
(4)物流配货人员从SPS供给管理板处获取信息选取配货指示票,配货指示票上标有某个车型在某个工程装配零件的种类和数量。
(5)物流人员按照配货指示票到SPS区配货(KITTTING),放在相应的台车上,物流人员将部品放到运输台车上。
(6)配完后放在供给待发区,物流人员将零件供给到生产线的起始位置。
(更先进的方式是AGV 自动输送至相应工位。
(7)物流人员将空台车返回到零件供给待发区,通过SPS方式配货完成。
2. 物料配送的四个步骤在图3的SPS物料及信息流程图中我们可以看到,所有的物料都是经过四个步骤完成运送的:接收物料需求信息(图3中①);按需求信息进行配货(图3中②);将配货送到装配线的接收端(图3中③);随装配线完成装配工序(图3中④)。
21-缩短制造周期之拉动系统流程与实施方法(试行)

21
二、拉动系统流程介绍
4、JIT拉动方式(排序物料拉动方式)
示意图
网上发布 排序供应商整车厂 22二、拉动系 Nhomakorabea流程介绍
5、SPS按台套拉动
释义:物料在SPS分拣区内针对车型及颜色进行排序拣取并排序上线。 流程:通过SAP系统、人工巡检等形式将生产零件拉动至SPS配载操作区,操作人员根据系统输出的配料 信息,将一台车份的零件配载到相应的料车上,按需求时间送至生产线指定工位投入,料车在线随对应生产 车辆同步行进,配料车内零件全部装配完毕后,在指定工位撤出。物料集中放置在SPS区域,线旁只有少量 JIT物料及部分大件,节省线旁空间。
车身
EPS拉动
焊装
VSS
涂装
107
FLEX/SFE
无线暗灯 2
GA 总装
VQ 车检
PLC
实时车辆位移信息
PPS
4
2
无线EPS终端
DD拉动
3 JIT
排序拉动
JIT/DD
普通供应商
RDC供应商
1
看板扫描
PPS拉动
5
SPS
台套拉动
分拣区
8
二、拉动系统流程介绍
1、看板拉动方式
释义:主要针对小件物料,使用看板卡进行物料需求、供货信息传递,根据拉动请求发布需求。 流程:每箱零件都放有一个看板卡,该看板卡上印有条码,条码内容为看板卡号、看板数量、序号等信息, 装配工人在用到该零件时,取出看板卡,放到看板收集箱中,表示该箱零件已经开始使用。看板收集人员定期 收集看板卡,对看板卡进行整理,看板扫描人员集中扫描整理后的看板卡,经过系统即时处理后,发布看板物 料拉动单,供应商按照物料单上的信息进行配料,物料工把配好的物料送至生产线旁。
SPS项目实施方案

06
项目实施效果评估与总结
项目实施效果评估
评估方法
采用定量和定性评估方法,收集 和分析项目实施过程中的数据和 信息,以客观地评估项目的实施
效果。
评估指标
建立包括项目进度、质量、成本 、安全等方面的评估指标体系,
以全面衡量项目的实施效果。
评估流程
按照事前、事中和事后的流程, 对项目实施过程进行全程监控和 评估,及时发现问题并采取措施
系统维护与优化
01
02
03
04
故障处理
及时响应和处理系统运行 中出现的故障和异常情况 ,确保系统的稳定性和可 用性。
性能监控与优化
定期对系统进行性能监控 和分析,发现并解决性能 瓶颈,提高系统的响应速 度和吞吐量。
功能优化
根据用户反馈和使用情况 ,对系统功能进行优化和 改进,提高用户体验和满 意度。
对测试通过的代码进行审查和优化,提高 系统的性能和稳定性。
系统上线与部署
环境准备
搭建服务器、网络等基础设 施,确保系统能够稳定运行
。
1
数据迁移
将旧系统中的数据迁移到新 系统中,确保数据的完整性和准确Fra bibliotek。系统部署
将开发完成的系统部署到服 务器上,进行系统配置和安 装。
上线发布
完成系统的上线发布,通知 用户和相关人员使用新系统 。
予以解决。
项目实施经验总结与分享
经验总结
对项目实施过程中的成功经验和存在问 题进行总结,分析原因并提出改进措施 。
VS
经验分享
将项目实施的成功经验和做法进行分享, 为其他类似项目的实施提供参考和借鉴。
项目实施不足与改进方向
不足分析
对项目实施过程中的不足之处进行分析,找出原因和症结所在。
浅析丰田SPS物料供应模式
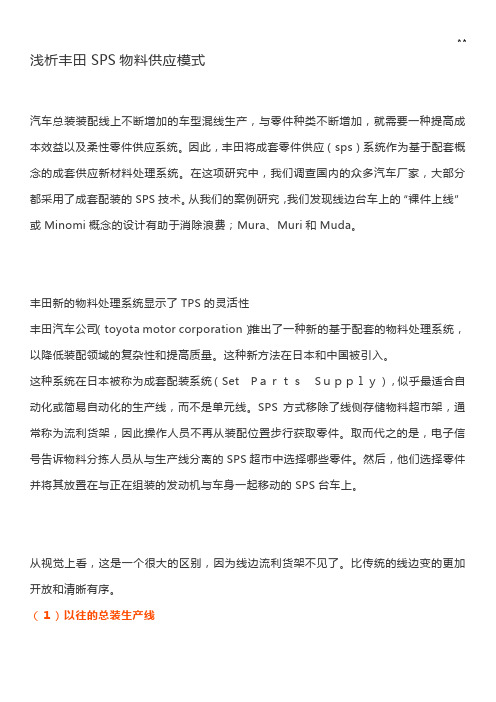
浅析丰田SPS物料供应模式汽车总装装配线上不断增加的车型混线生产,与零件种类不断增加,就需要一种提高成本效益以及柔性零件供应系统。
因此,丰田将成套零件供应(sps)系统作为基于配套概念的成套供应新材料处理系统。
在这项研究中,我们调查国内的众多汽车厂家,大部分都采用了成套配装的SPS技术。
从我们的案例研究,我们发现线边台车上的“裸件上线”或Minomi概念的设计有助于消除浪费;Mura、Muri和Muda。
丰田新的物料处理系统显示了TPS的灵活性丰田汽车公司(toyota motor corporation)推出了一种新的基于配套的物料处理系统,以降低装配领域的复杂性和提高质量。
这种新方法在日本和中国被引入。
这种系统在日本被称为成套配装系统(Set PartsSupply),似乎最适合自动化或简易自动化的生产线,而不是单元线。
SPS方式移除了线侧存储物料超市架,通常称为流利货架,因此操作人员不再从装配位置步行获取零件。
取而代之的是,电子信号告诉物料分拣人员从与生产线分离的SPS超市中选择哪些零件。
然后,他们选择零件并将其放置在与正在组装的发动机与车身一起移动的SPS台车上。
从视觉上看,这是一个很大的区别,因为线边流利货架不见了。
比传统的线边变的更加开放和清晰有序。
(1)以往的总装生产线(2)实施SPS的总装生产线由于零部件选择是在上游进行的,因此装配工可以“关注安装质量”。
随着向客户提供越来越多的功能,多样性和由此产生的复杂性不断增加。
例如,在新系统为当前一代凯美瑞和Avalon引入之前,物流拣货人员必须在24种遮阳板中进行选择。
这一变化意味着,装配作业人员现在将近100%的时间集中在安装部件的增值工作上,因为他们不再需要执行非增值任务,即走几步从流利货架上取回部件。
”装配作业人员保持在一个非常高效的作业步率,几乎100%的增值时间。
”该方式还消除了装配操作员对零件的步行、拉伸容器和搜索零件的浪费。
汽车行业SPS简述
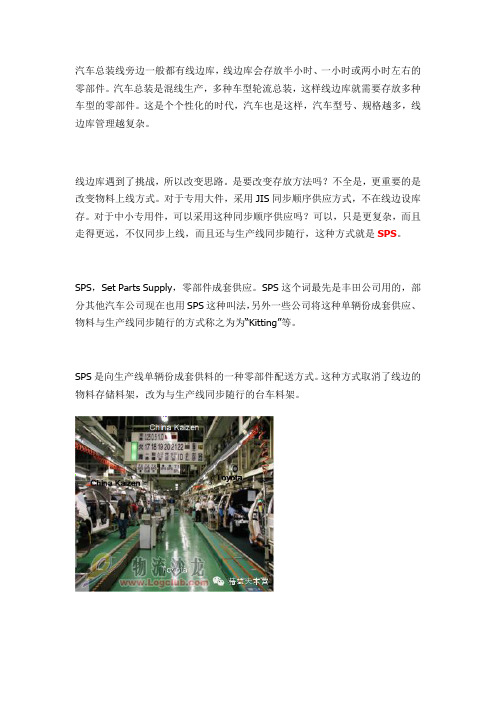
汽车总装线旁边一般都有线边库,线边库会存放半小时、一小时或两小时左右的零部件。
汽车总装是混线生产,多种车型轮流总装,这样线边库就需要存放多种车型的零部件。
这是个个性化的时代,汽车也是这样,汽车型号、规格越多,线边库管理越复杂。
线边库遇到了挑战,所以改变思路。
是要改变存放方法吗?不全是,更重要的是改变物料上线方式。
对于专用大件,采用JIS同步顺序供应方式,不在线边设库存。
对于中小专用件,可以采用这种同步顺序供应吗?可以,只是更复杂,而且走得更远,不仅同步上线,而且还与生产线同步随行,这种方式就是SPS。
SPS,Set Parts Supply,零部件成套供应。
SPS这个词最先是丰田公司用的,部分其他汽车公司现在也用SPS这种叫法,另外一些公司将这种单辆份成套供应、物料与生产线同步随行的方式称之为为“Kitting”等。
SPS是向生产线单辆份成套供料的一种零部件配送方式。
这种方式取消了线边的物料存储料架,改为与生产线同步随行的台车料架。
刚开始,SPS成套供应主要应用在在内饰线和车门线等,因为这两条线的零部件具有体积大、重量轻、配置多、颜色件多等特点,线边存放占用面积较大,操作人员拣选麻烦。
随着对SPS的应用越来越熟悉,慢慢就扩展到底盘线、发动机装配线等。
为什么SPS这种方式越来越多地被汽车企业采用呢?首先,由于SPS是单辆份成套供应,所以,降低了取料错误的可能性,提高了装配质量和装配效率。
中国汽车行业增长较快,车间新手较多,这种降低拣料、装配复杂度的方法能有效减少新手的学习时间。
其次,SPS单辆份成套供应还降低了生产线操作人员拣选物料的时间。
同时,由于零部件是与生产线同步随行,物料箱可以放在操作人员身边,不需要走出装配区域去取物料,这同样提升了装配效率。
装配效率的提升会导致装配节拍的降低,这对生产线资源紧缺的汽车总装来讲非常重要,因为同样的生产线在不扩产的情况下可以生产出更多的车辆了。
再次,由于SPS采用同步顺序上线和物料随行方式,所以节省了线边库的占用。
拉动生产课件
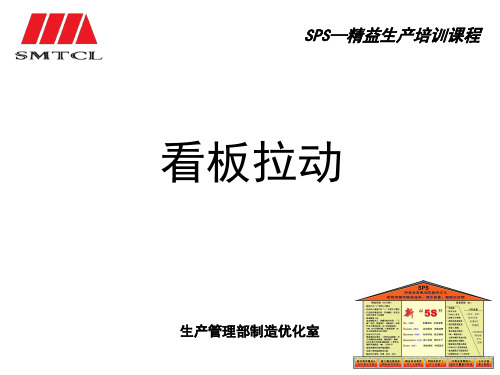
投产卡使用规则
1.箱体部装车间:每天下午17:00点将空盒运送到轴杂车间库房由轴杂车间库房管理员 将其填满并取回。
2.轴杂车间:库房管理员将箱体部装车间运来的空盒填满后取出相应数量的投产卡片 并将其插在拉动看板上;当到达投产点后将消耗的个零件数量用电话+电子邮件的形 式告知轴杂车间主计划员;轴杂车间主计划员收到信息后将其分解并填写零件投产 信息卡并交给各线线长由线长进行排产并插到排产视板上组织生产。
13478382579
此卡片仅用于轴杂车间内部流通
轴杂车间库房布局规划图
拉动看板存放处
轴杂车间投产板设计
轴杂车间内部拉动卡片流程
轴杂车间库房
空盒
满盒
轴杂车间库房 管理员为其将 空盒填满,并 在物料架上取 出将相应数量 的投产卡插在 拉动看板上
轴杂车间库房
零件名称
缺欠数量
HTC1650L//HL1602110L//挡油环
推动式生产与拉动式生产
拉动式生产的对客户的响应时间是:
对客户的交货期 生产交货期 运输交货期
工厂
客户
缩短交货期
挑战!
如何实施拉动式生产?
实施拉动式生产分为5个阶段:
第一阶段:识别现状 第二阶段:按照流程重新布局 第三阶段:设计单元制造的方式 第四阶段:引入看板系统 第五阶段:转为单件流
实施拉动式生产的好处?
15
HTC2050L//HL1602111L//挡油环
15
HTC1650L//HL1602112L//调整垫
15
HTC2050L//HL1602115L//法兰盘
15
HTC1650L//HL1602114L//调整垫
15
HTC2050L//HL1603014L//活塞
浅谈SPS在微车制造企业中的应用
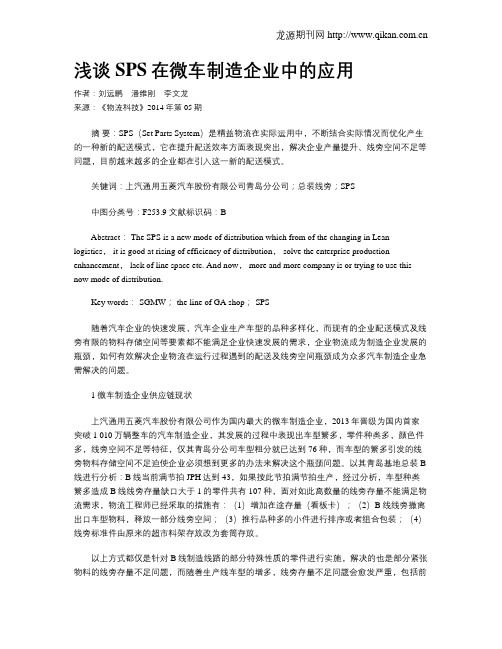
浅谈SPS在微车制造企业中的应用作者:刘远鹏潘维刚李文龙来源:《物流科技》2014年第05期摘要:SPS(Set Parts System)是精益物流在实际运用中,不断结合实际情况而优化产生的一种新的配送模式,它在提升配送效率方面表现突出,解决企业产量提升、线旁空间不足等问题,目前越来越多的企业都在引入这一新的配送模式。
关键词:上汽通用五菱汽车股份有限公司青岛分公司;总装线旁;SPS中图分类号:F253.9 文献标识码:BAbstract: The SPS is a new mode of distribution which from of the changing in Lean logistics, it is good at rising of efficiency of distribution, solve the enterprise production enhancement, lack of line space etc. And now, more and more company is or trying to use this now mode of distribution.Key words: SGMW; the line of GA shop; SPS随着汽车企业的快速发展,汽车企业生产车型的品种多样化,而现有的企业配送模式及线旁有限的物料存储空间等要素都不能满足企业快速发展的需求,企业物流成为制造企业发展的瓶颈,如何有效解决企业物流在运行过程遇到的配送及线旁空间瓶颈成为众多汽车制造企业急需解决的问题。
1 微车制造企业供应链现状上汽通用五菱汽车股份有限公司作为国内最大的微车制造企业,2013年晋级为国内首家突破1 010万辆整车的汽车制造企业,其发展的过程中表现出车型繁多,零件种类多,颜色件多,线旁空间不足等特征,仅其青岛分公司车型粗分就已达到76种,而车型的繁多引发的线旁物料存储空间不足迫使企业必须想到更多的办法来解决这个瓶颈问题。
SPS实施方案
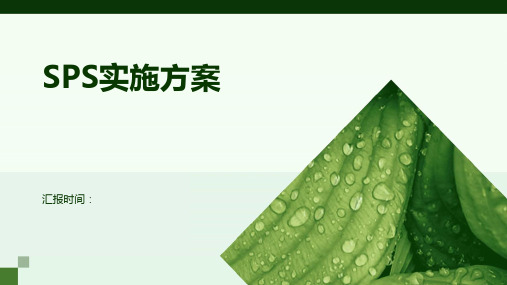
案例三
03
某电信运营商实施SPS项目,通过对网络资源进行精
细管理和优化配置,提高了网络质量和客户满意度。
失败案例分析
案例一
某服装品牌在实施SPS项目时 ,未充分考虑到供应链的复 杂性,导致项目实施过程中 出现物流配送不及时、库存 积压等问题。
案例二
某电子产品制造商实施SPS项 目时,过分追求技术的先进 性,忽略了实际应用场景的 需求,导致项目效果不佳。
方案设计
基于需求分析的结果,进行方案设计,明确 技术路线、系统架构、功能模块等。
系统开发
按照方案设计的要求,进行系统开发和测试 。
项目实施流程设计
数据迁移
如果需要,进行数据迁移,保 证数据的完整性和准确性。
系统测试
完成系统的测试和调试,确保 系统的稳定性和性能。
上线部署
完成系统的部署和上线,进行 上线前的最后调试和测试,确 保系统的顺利运行。
数据迁移和接口对接
如果需要,进行数据迁移和接口对接,保证数据的完整 性和系统的正常运行。
系统上线与部署
完成系统的部署和上线,进行上线前的最后调试和测试 ,确保系统的顺利运行。
用户培训和服务支持
为用户提供培训服务,解决用户使用中的问题,提供持 续的技术支持。
项目实施流程设计
需求分析
对业务需求进行详细了解和分析,确定系统 升级或替换的具体目标和要求。
用户培训
为用户提供培训服务,解决用 户使用中的问题,提供持续的
技术支持。
项目时间表与里程碑
01
第一阶段(1-3 个月)
初步调查和评估现有系统 ,进行需求分析和方案设 计。
02
汽车物流SPS运作细节设计
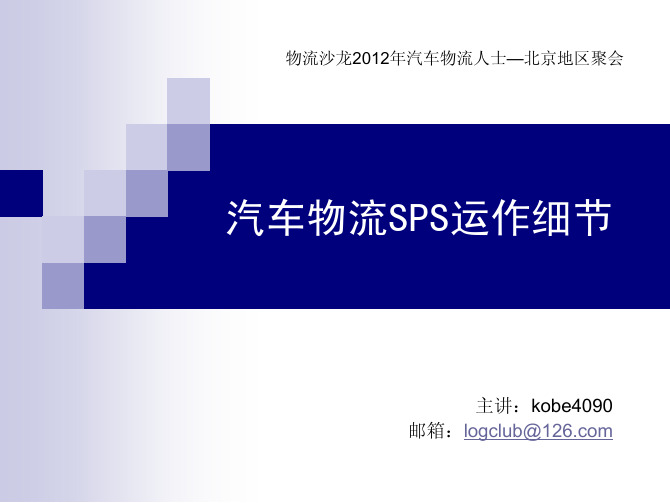
一些轨道及随行案例:
七、内饰台车的设计
内饰台车的设计比较复杂,一般来说内饰分为两条线,所以SPS件的选择应根据工艺 来定。同时如果是双随行小车时。零件装配的位置也不一样。要分为发舱、前舱、后 舱与行李箱等。 下面几个图分别是随行台车的参考图例:
八、 单元生产模式
会后思考:
流水生产线的缺点: 1. 组装复杂的车与简单的车所用的工时是一样的,是以最复杂的车来设计生产 线的。而沃尔沃生产方式则可以将两种车的工时分开,简单的车所用工时 少,成本更低。 2. 当某工位因各种原因停线时,会影响整条生产线或该条线都停止,造成了较 大的浪费,而单元生产方式则对其它操作不会有影响。 讨论:但为什么单元生产方式(沃尔沃生产方式)没有在汽车行业中 大量使用起来?
2.
台车设计细节:
3.
(料箱前行轨道)无动力滚道。
如右图:(如北京现代三厂) (双层滚道传送带)随行料箱在滚 道上靠车门吊架推动前进。料箱在 使用完毕后可通过底部动力滚道返 回。(左右料箱各一条轨道)。
如左图:(如东风裕隆) 无动力单轨道,随行料箱在滚道 上靠车门吊架推动前进。料箱随 行至线尾,料箱自身重力,从两 侧带坡度的滚道滑下来。
SPS台车 纵 向 移 动 车 门 吊 架
六、内饰SPS
双料车近距随行模式(内侧取料) 双料车近距随行模式(外侧取料) 单料车远距随行模式 单料车两车中间随行模式
内侧取料
外侧取料
单车远距
线间取料定因素:大平板的宽度
大平板较窄:可参考一汽轿车、上海通用北厂、北京长安的模式。 大平板较宽:可参考上海通用南厂、通用北盛、一汽轿车内饰 大平板很宽:可参考广汽丰田(直接推至平板上,并做好限位) 两车间距很宽:可参考一汽大众
精益时代的汽车线边物流规划与发展

少搬运、缩短距离、减少浪费、降低负 荷、提高效率为基础,以各种各样的形 式展开。张芸指出,精益线边物流规划 需要从以下几个方面顺序进行:
1. 分析并确定产线物流需求。 首先要确认物流需求和配送流程。 客户/下游需求决定了产线的生产流程、 物料、节拍、工位构造、制造工艺等基 础信息及初步物流需求,精益的线边物流 须对应精益的产线来进行设计(人员、设 备、物料分布、均衡化生产节拍)。 2. 线边物料展开设计。 结合产线对于物料的需求,规划工 作者需要将该物料需求分解到产线的具 体工位上。在此过程中,同时需要考虑 线边物料的存放方式、库存设置、使用 方式、空间设置等等。 展开来说,线边存放方式需要采 用人机工程的料架和包装,便于操作人
分段式 SPS 上线
设计应当考虑线边整体库存设置标准, Kitting零件的包装设计应当充分考虑到 配比关系和线边存量。另外,也要考虑 匹配运输设备和线边料架的设计,以及 物流整体包装尺寸链要求。
二、精益思想下的线边物流模式 精益供应链与物流规划与改善专
家李波表示,汽车物流规划始于装配线 边,什么样的装配工艺决定了什么样的 线边物流模式。随着生产模式变化及精 益理念的深入,线边物流模式也不断地 创新发展。
92 物流技术与应用 2019.10
善、成本节省等等。她告诉记者:“很 多汽车企业都从精益管理中获益。举例来 说,我们的客户A在进行精益化的线边物 料包装改善后,库存数量降低了53.4%, 总装车间用于二次排序的面积大大减 少,操作流程简化,物流作业人员实现 精简。这一系列的改变使客户A的成本大 幅度降低,对应的利润率也大大增加。
F
FOCUS REPORT
焦点
精益时代的汽车线边物流规划与发展
TPS之拉动式生产课件

搬运
售出信息
货 架
收银
看 前工序
板 后工序拿取信息
搬运 工位零部件
生产线
看板的流动
物料的流动 看板架
[8]按照产品的售出方式组织生产的3种形式
1)A型・・・后补充生产
aa b c d e TPS之拉动式生产 工序
均衡化的成 品集中方式
出货场
2)B型……顺序生产
生产顺序计划
前 工序
总量控制看板
TPS之拉动式生产
25%
增值时间
四方有限各种产品的流程效率是?
流程的效率=
总提前时间(产品实际制造周期)
精益是什么
精益五
原则
价值:精确地确定特定产品的价值
价值流:识别出每种产品T的PS之价拉动值式生流产
流动:使价值不间断的流动
拉动:让用户从生产者方面拉动价值
尽善尽美:永远追求尽善尽美
【美】詹姆斯.沃麦克 【英】丹尼尔.琼斯 《精益思想》1996年
增加工位
标准作业
T/T
操作者工作负荷不均,通过 工作量的调整,使工序平衡 。
TPS之拉动式生产
标准作业
T/T
操作者负荷均可满足生产节 拍,但个别工位负荷不足。
TPS之拉动式生产
通过工作量的调整, 达到少人化的目的。
减少 一人
标准作业
T/T
考虑作业改善,不增加工位 操作者负荷较大,个别工位 保证节拍因难----增加工位。
工序
出货场
①按照后工序拉动进行生产。 ②生产的数量保持统一。
3)C型……后补充和顺序的混合生产
前 工序
ab d e
工程
TPS之拉动式生产
均衡化的成品 集中方式
sps配送实施方案

sps配送实施方案SPS配送实施方案。
一、背景介绍。
随着电商行业的快速发展,用户对配送服务的要求也越来越高,配送速度、配送准时性、配送安全性等方面都成为用户选择电商平台的重要考量因素。
因此,建立高效、稳定的配送体系成为电商企业提升竞争力的关键之一。
本文档将详细介绍SPS配送实施方案,旨在提高配送效率,保障配送质量,满足用户需求。
二、配送范围。
SPS配送实施方案将覆盖全国范围内的配送服务,包括城市、乡村甚至偏远地区。
通过建立完善的配送网络和合作伙伴关系,实现全国范围内的快速配送。
三、配送流程。
1. 订单接收,用户下单后,系统自动分配最近的配送中心进行订单接收。
2. 配送派单,配送中心根据订单信息和目的地,选择最优配送路线和配送员,进行派单。
3. 配送取件,配送员按照派单信息前往取件,确保货物准时到达配送中心。
4. 配送途中,配送员根据路线规划,及时将货物送达目的地,确保配送准时性。
5. 签收确认,用户签收货物后,配送员进行签收确认,并及时反馈系统。
四、配送优势。
1. 高效快速,通过智能化路线规划和派单系统,实现最短路径配送,提高配送效率。
2. 稳定可靠,建立完善的配送网络和合作伙伴关系,确保配送服务的稳定性和可靠性。
3. 安全保障,配送员经过专业培训,严格遵守配送规范,保障货物的安全送达。
4. 用户体验,提供实时的配送信息查询和客服支持,提升用户对配送服务的满意度。
五、配送管理。
1. 实时监控,建立配送监控中心,实时监控配送过程,及时发现和解决问题。
2. 数据分析,对配送数据进行分析,优化配送路线和派单策略,提高配送效率。
3. 问题处理,建立配送问题反馈机制,及时处理配送过程中出现的问题,确保配送质量。
六、总结。
通过SPS配送实施方案的落地实施,电商企业将能够提升配送效率,保障配送质量,提升用户满意度,从而增强竞争力,实现可持续发展。
希望本文档能够为电商企业的配送管理工作提供一定的参考和帮助。
SPS –Kitting 拉动方案
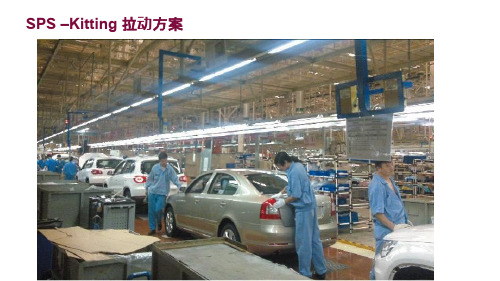
SPS –Kitting 拉动方案SPS-Kitting系统操作流程SPS物料拉动模式为物料车生产线随行供料。
SPS每天定时从MES(或SAP)获取车辆零件BOM信息。
当车辆进入总装车间时,MES系统下传该车单车所需零件,SPS进行拆分工段,拆分料车后下发到分拣系统,并打印配料单。
捡料工在Kitting操作区域扫描配料单,Kitting系统点亮需配载零件对应的灯,用以辅助零件配载。
MES 系统SPS 系统打印捡料单Kitting 区域SPSWMS 系统PTLWMS零件仓库DEMATIC项目范围SPS work flow V1.0 by Sudors.ShiSPS ServerMESPick StationWMSPTL ControllerPrinterP c k F n s h e dS e n dR e c e v eP r o c e s sP c k P a r t sStartPrint pick listEnter BarCodeCheck shift codePick partsvalidHandle the messageAlertNon-consecutive SNSend pick finished message to WMSFinishinvalid barcodePress zone finishbuttonUpdate picked partsbatch infoUpdate pick listpickingSend order toSPSIs order ’s format valid?Alertinvalid validIs pick list ’s data valid?Create pick listvalidAlertinvalid Receive orderSend print messageto Printer(Auto)SPS-Kitting系统带来的效率提升(1)加快捡料速度(30%-50%)(2)降低捡料错误率(99.98%的正确率)(3)免除表单作业(提高工作效率50%以上)(4)人员训练容易且标准化(培训只需5分钟)(5)促进管理升级观致总装装配零件数对比(basic data from 2014.07.11 BOM)CF11/CF14/CF14K 三种车型总装共装配1680种零件(其中包括选装件)SPS-Kitting 实施零件777种,实施率为46%0100200300400500600700800kitting kanban EXTJIS INTJIS FASTEN ERS CF 零件数77756355873996总装装配零件数kitting 46%kanban 3%EXTJIS 21%INTJIS 5%FASTENERS 24%CF 0.36%总装装配零件百分比GA kitting layout 总装Kitting 总图EDU CH A1FIN CHA2TR1-FLTR1-RLBUFFERTR1-RRTR2-RLTR2-FLIPT R 2-F RTR2-RRDOORCHA2装配零件数对比CHA2线kitting 实施率为21%0102030405060708090100kitting kanban EXTJIS FASTENERS零件数43109257CHA2装配零件数kitting 21%kanban 5%EXTJIS 46%FASTENERS 28%CHA2装配零件百分比CHA2 delivery route 底盘2线线边补货路径满车Full kitting 空车Empty kitting trolleyC H A 2CHA2 补货路径CHA2CHA2 SPS Status 底盘2线SPS 情况CHA1 CHA2CHA2kitting实施工位15~24CHA2 Kitting Area底盘2线KITTING区域Kitting area manpower calculation Kitting区域人员规划1.36JPH----生产节拍2.10s/part based on experienced data----10S拣选一个零件3.5s for mistake or emergency---------------预留5S应急cycle time/zone=(3600s/36JPH)-5=95s/zonepicker ability=roundDown(95/10,0)=9 parts/cycle拣选人工数Picker=roundup(SKU of each line/9,0)CHA2 Kitting Area底盘2线KITTING区域Picking list 捡料单配载线代码配载单号内容:CHAS-2:配载线代码141021:捡料指示单打印日期0206859:车辆订单号,来自MES系统02786:SPS为每份捡料单分配的识别代码,按单连续一维码包含信息同配载单号VIN:来自MES系统Shift NO.:来自MES系统捡料单上显示零件在kitting区库位地址,零件号,需拣货数量,Kitting料车地址,PTL灯地址以及零件名称供捡料人员识别捡料PTL 界面及操作零件标签,四位数码显示Task monitor Finish button 区域完成标签C3:零件在Kitting 车放置的位置;1:需拣选数量当完成某区域时操作在规定时间内完成该区域零件的拣选操作指示灯为绿色;超过规定时间完成作业,指示灯为黄色; 当前区域有故障时,指示灯为红显示正在等待的任务;显示各区域拣选进度。
物流--“SPS推进”步骤
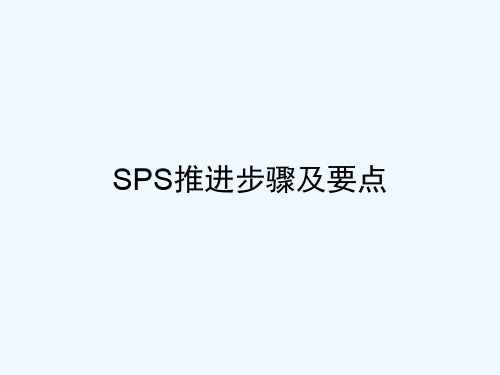
日
1 3 km/h
5 km/h
+ (A × 2F) 秒+ (A × D× M
到连接台车中
3 月央6 日时间 * 2
1
7 6秒
项目计划、启动
2项5目启秒动、实施阶
⑦ 水槽分装时间1.69节拍244种车 秒型混流生产;轿车公司物
⑧ 较大10零件台 拿取 车 流 份( 模 配分式 送6种 由 。开原 一)来 次时 批 内间 量 饰全 SP品 S物种2流配 4管送秒 理改基为础SP由S量 2个 ⑨ 条形12零件叉 整理 车 班时 长作,间2业 个 (在4一库 种管 次 )理员,28个流秒动工组成。
四、SPS推进步骤三:基础数据的建立(SPS前提)
1.部品明细 ① 技术数据:部品编号、名称、单台用量 ② 采购数据:供应商名称、代码、供货比例 ③ 路径数据:仓库地址、存放地址、工位 ④ 包装数据:包装类别、尺寸、收容数、重量
2.后期维护相关流程的建立 ① 设变管理流程(保证部品明细准确率) ② 包装确认流程 ③ 工位调整流程
五、SPS推进步骤四:周转箱、台车设计(SPS基础)
1.周转箱 适用于部品体积较小的,置于车身内
• 1.生产线侧流动架
安顺序投 件
空箱推 出
实空交 换
• 2.生产线侧转台
空实交 换
五、SPS推进步骤四:周转箱、台车设计(SPS基础)
2.随行台车 用于体积较大、外形特异、随手化困难的零件
六、SPS推进步骤五:信息指示设计(SPS中枢)
61
品种 10 秒
S取 5P出 S准 部割备 品捆 发指 的区示 绑 通 基台过票 本 车 带 一取 整 步 次(理出 内 行3饰 每 时 人 时S/P间 条 间 S班配次) 送;人线员侧的子算母出台,车已切确替定22及SPSSP配S箱货整人 M秒 理员 /4部 /2人0回人 品 /班/班次次.1物; .流供 5管给理 秒 人及员异3人常/对班应次人;员信:息 班长 指1示人及、待在
推荐 Kitting物料配送在发动机生产线的应用 精品

在物流管理中,生产线的配送物流,是供方配送物流、配送中心配送和制造物流的交集,有承上启下的作用。
产能及节拍的需求决定了物料配送上线的方式。
要做到在极短的时间内完成拣选、配送任务,只有不断提高物流装备的运行速度和处理能力。
Kitting配送方式正是通过提高物流装备的运行速度和改善配送方法而实现在短时间内完成配送。
发动机装配线采用Kitting物料配送方案,可减少取料及步行等非增值时间,为发动机的制造系统提供了良好的产能提升效益。
Kitting的基本概念Kitting有两种意思:·生产配件。
·打包备料的一个过程。
在物流配送管理中应取第二种意思。
Kit原意为工具包,采用Kit的这种理念,将物料配成“工具包”,就是根据工作站物料的需求,打包配送,目的使该工作站物料齐全配套、利于识别和使用,降低供应链成本,同时达到柔性化生产线装错物料的防错效果。
Kitting的优点在各种制造系统中,Kitting配送方式已经得到广泛的应用。
其优势主要体现在生产系统柔性化、良好的质量控制及生产能力的提高。
1.实现精益、柔性的装配系统的设计使用相同的设备,建造多种不同型号的产品;减少由于产品种类增加所带来的影响;减少装配系统现场空间的需求;所有物料都在操作工触手可及的范围;重新进行生产线工时平衡时,工作站改造花费更少的成本;降低系统复杂性,提高设备开动率;降低购买及维护物料防错装置的成本。
2.改善装配系统的质量避免操作工选错物料;在正确的时间提供正确数量、正确型号、正确方向排列的物料给操作工;消除与物料缺失相关的风险;KIT上线点:能够目视出是否所有的物料都包含在料盘中;KIT下线点:能够目视出是否所有的物料都被装配在发动机上;Kitting流程增加了一层检查,能够在Kitting 过程中发现供应商错误;物料混放、物料质量问题。
3.提高装配系统的生产力将NVA(Non Valuable Added)工作由在线装配工转换为离线操作工;通过消除物料隔衬相关操作节约操作时间;减少操作工周期时间的变化;促进生产量的提高;将人机工程问题(弯身、伸展、扭曲)最小化;工具和物料在操作工前方;消除过多的移动;所有的物料都在操作工触手可及的范围内;消除由于抓取物料、寻找物料、零件掉落所导致的不必要的动作。
多技能工-五星班组建设方案-咨询公司出版

特色产品:四步法
成立精益小组
定 期 小 组 会 议
-13-
五星班组星级介绍
“三星”班组介绍
阶段主题:降本增效
持续四步法改善,对日常管理的进行标准化,异常情况自主改善, 员工多能工训练体制建立,岗位作业中防呆改善
班后交接
QCD日报输出
教育训练 26Hr
持续改善
班组长交接
对应工位交接
班组长交接
实施重点 晋级率20% 晋级率30% 晋级率30%
二星 班组运营
精益部 制造部
6个月↑
循环 1.优秀班组活动基金一次性2000 300元 元
晋级率50%
一星 团队改善
精益部 制造部
3个月↑
一次性 500元
1.优秀班组长旅游
班组改善训练
-9-
五星班组星级介绍
“一星”班组介绍
阶段主题:团队改善
组建班组团队,明确团队工作分工,对现场的基本环境维持管理改善, 通过3S实战提升环境,班前会议管理等组建改善型团队
精益文化 + 革新行动 + “0”浪费
■一星级班组 ■二星级班组 ■三星级班组 ■四星级班组 ■五星级班组
-7-
推进步骤
五星班组平台推进步骤
目 实践精益经营理念,创造企业核心竞争力,
培育精益人才,实现客户、员工、企业三赢
的 目标。
目 实现自主管理,消除浪费,提高利润率人均
产值提升30%,库存压缩30%,质量成本下
团队改善 挑战自我 革新激情
五星班组简介
Lowest costal ways win
目录Contents
一 推进背景及目标 二 五星班组的定义 三 推进方向 四 推进步骤 五 五星晋级流程 六 五星班组星级介绍
- 1、下载文档前请自行甄别文档内容的完整性,平台不提供额外的编辑、内容补充、找答案等附加服务。
- 2、"仅部分预览"的文档,不可在线预览部分如存在完整性等问题,可反馈申请退款(可完整预览的文档不适用该条件!)。
- 3、如文档侵犯您的权益,请联系客服反馈,我们会尽快为您处理(人工客服工作时间:9:00-18:30)。
SPS –Kitting 拉动方案
SPS-Kitting系统操作流程
SPS物料拉动模式为物料车生产线随行供料。
SPS每天定时从MES(或SAP)获取车辆零件BOM信息。
当车辆进入总装车间时,MES系统下传该车单车所需零件,SPS进行拆分工段,拆分料车后下发到分拣系统,并打印配料单。
捡料工在Kitting操作区域扫描配料单,Kitting系统点亮需配载零件对应的灯,用以辅助零件配载。
MES 系统SPS 系统打印捡料单Kitting 区域
SPS
WMS 系统
PTL
WMS
零件仓库
DEMATIC项目范围
SPS work flow V1.0 by Sudors.Shi
SPS Server
MES
Pick Station
WMS
PTL Controller
Printer
P c k F n s h e d
S e n d
R e c e v e
P r o c e s s
P c k P a r t s
Start
Print pick list
Enter BarCode
Check shift code
Pick parts
valid
Handle the message
Alert
Non-consecutive SN
Send pick finished message to WMS
Finish
invalid barcode
Press zone finish
button
Update picked parts
batch info
Update pick list
picking
Send order to
SPS
Is order ’s format valid?
Alert
invalid valid
Is pick list ’s data valid?
Create pick list
valid
Alert
invalid Receive order
Send print message
to Printer(Auto)
SPS-Kitting系统带来的效率提升
(1)加快捡料速度(30%-50%)
(2)降低捡料错误率(99.98%的正确率)
(3)免除表单作业(提高工作效率50%以上)
(4)人员训练容易且标准化(培训只需5分钟)
(5)促进管理升级
观致总装装配零件数对比(basic data from 2014.07.11 BOM)
CF11/CF14/CF14K 三种车型总装共装配1680种零件(其中包括选装件)SPS-Kitting 实施零件777种,实施率为46%
0100200
300400500600700800kitting kanban EXTJIS INTJIS FASTEN ERS CF 零件数
777
56
355
87
399
6
总装装配零件数
kitting 46%
kanban 3%
EXTJIS 21%
INTJIS 5%
FASTENERS 24%
CF 0.36%
总装装配零件百分比
GA kitting layout 总装Kitting 总图
EDU CH A1
FIN CHA2
TR1-FL
TR1-RL
BUFFER
TR1-RR
TR2-RL
TR2-FL
IP
T R 2-F R
TR2-RR
DOOR
CHA2装配零件数对比
CHA2线kitting 实施率为21%
0102030405060
708090100kitting kanban EXTJIS FASTENERS
零件数
43
10
92
57
CHA2装配零件数
kitting 21%
kanban 5%
EXTJIS 46%
FASTENERS 28%
CHA2装配零件百分比
CHA2 delivery route 底盘2线线边补货路径
满车Full kitting 空车Empty kitting trolley
C H A 2
CHA2 补货路径CHA2
CHA2 SPS Status 底盘2线SPS 情况
CHA1 CHA2
CHA2
kitting实施工位15~24
CHA2 Kitting Area底盘2线KITTING区域
Kitting area manpower calculation Kitting区域人员规划
1.36JPH----生产节拍
2.10s/part based on experienced data----10S拣选一个零件
3.5s for mistake or emergency---------------预留5S应急
cycle time/zone=(3600s/36JPH)-5=95s/zone
picker ability=roundDown(95/10,0)=9 parts/cycle
拣选人工数Picker=roundup(SKU of each line/9,0)
CHA2 Kitting Area底盘2线KITTING区域
Picking list 捡料单
配载线代码
配载单号内容:
CHAS-2:配载线代码
141021:捡料指示单打印日期
0206859:车辆订单号,来自MES系统
02786:SPS为每份捡料单分配的识别代码,按单连续
一维码包含信息同配载单号
VIN:来自MES系统
Shift NO.:来自MES系统
捡料单上显示零件在kitting区库位地址,零件号,
需拣货数量,Kitting料车地址,PTL灯地址以及零
件名称供捡料人员识别捡料
PTL 界面及操作零件标签,四位数码显示Task monitor Finish button 区域完成标签
C3:零件在Kitting 车放置的位置;1:需拣选数量当完成某区域时操作在规定时间内完成该区域零件的拣选操作指示灯为绿色;超过规定时间完成作业,指示灯为黄色; 当前区域有故障时,指示灯为红显示正在等待的任务;显示各区域拣选进度。