GB150-XXXX压力容器-制造、检验和验收
GB150

GB150-1998《钢制压力容器》一、前言1、简介本标准是原国家质量技术监督局98年3月20日批准,要求98年10月1日实施。
此为GB150-89颁布后第一次修改,GB150-98是我国目前压力容器标准体系中的基础标准,基础标准服务于量大面广的产品,采用共性技术,在行业中处于举足轻重的地位,GB150修改,其他相关标准均需做相应修改。
如:GB151、GB12337、JB4710《钢制塔式容器》、JB4731等。
2、中外有关标准、规范中国:JB/T4735-97《钢制焊接常压容器》GB150-98《钢制压力容器》JB4732-95《钢制压力容器-分析设计标准》美国:ASMEⅧ-1《锅炉压力容器规范》第八卷第1分篇《压力容器常规设计》ASMEⅧ-2《锅炉压力容器规范》第八卷第2分篇《压力容器分析设计》ASMEⅧ-3《锅炉压力容器规范》第八卷第3分篇《压力容器疲劳设计》日本:JIS B8270《压力容器》(基础标准)JIS B8271-8285《压力容器单项标准》英国:BS5500《非直接受火压力容器》德国:AD《压力容器规范》TRB《压力容器技术规程》法国:CODAP《非直接受火压力容器建造规范》3、基本原则GB150参照或等效采用了ASMEⅧ-1、JIS B8270,并体现中国特色,考虑我国的实际情况,如:等效采用——圆度概念附录B 爆轰1000M/S参照采用——焊接接头分类(原为对接、角接、纵缝、环缝)中国特色——焊缝返修次数,不宜超过二次。
二、适应范围1、GB150-1998《钢制压力容器》是钢制压力容器设计、制造、检验与验收的标准。
本标准适用范围如下:1)、设计压力大于等于0.1MPa,小于等于35MPa的钢制压力容器和真空度高于O的钢制压力容器;的设2000mmH22)、设计温度范围根据钢材允许的使用温度确定;3)、管辖范围为容器及与其连为整体的连通受压零部件,即开孔接管与外管道连接的第一道环向接头坡口端面;螺纹连接的第一个螺纹接头;螺栓紧固连接的第一个法兰密封面;管件连接的第一个密封面;接管、人孔、手孔等的承压封头、平盖及其紧固件;非受压元件与受压元件的焊接接头;直接连在容器上的超压泄放装置以及容器上的安全附件。
GB 150 钢制压力容器的制造检验与验收

一、总
则
根据GB/T19000—ISO9000族标准的理论、原则、方法,结 合压力容器安全法规、标准的要求建立一个文件化的质量 体系并有效实施。 压力容器
压力容器 压力容器 压力容器 压力容器 GB/T1900—ISO 9000 质量管理和 质量保证 安全法规 标 准 质量手册 程序文件 记录报告
(4)壳体直线度允差⊿l规定
除图样另有规定外,⊿l应符和下表
壳体长度 L(mm ) ≤30 >30 直度公差⊿l(mm ) 1‰l 按 JB4710 规定
检查方法:
壳体直线度检查按A向图示,即沿壳体0o 、
90o、180o、270o四个方位进行,用φ0.5mm的细
钢丝测量。当壳体厚度不同时,计算直线度时 应减去厚度差。
其 它 钢 材
清
施焊前
≥20 除
*当坡口无法作 MT 或 PT 检测 时,由切割工艺保证坡口质量。
≥20 围 范
应无氧化物、油污、 熔渣及其它有害物质
3.封头
(1)对拼接封头的规定
径向焊缝 由成形瓣片和顶圆板拼接封头 焊缝方向只允许是径向和环向
环向焊缝
封头各种不相交的拼接焊缝中心线间 最小距离≥3δ s (弧长) ,且≥100(弧长) 先 拼 板后 成形 的封 头 拼接焊缝在成形 前应打磨 与母材齐平
Dmax
Dmin
Di–断面内径,mm di–开孔内径,mm
(11)承受外压及真空容器组装后,按
下图所示检查壳体的圆度
间隙 e 间隙 e
间隙 e 间隙 e
内弓形样板
内弓形样板
外弓形样板
外弓形样板
样板弦长 (查图)
样板弦长 (查图)
GB150[1]
![GB150[1]](https://img.taocdn.com/s3/m/3903797d31b765ce05081413.png)
10制造、检验与验收10.1总则10.1.1本章适用于单层焊接、多层包扎、热套及锻焊压力容器。
对于设计温度低于或等于—20℃的容器,还应符合附录C(标准的附录)的规定。
注:热套压力容器是指套合而经机械加工或不经机械加工,各层之间以过盈相互配合,其套合预应力须经热处理尽量消除的容器。
10.1.2容器的制造、检验与验收除应符合本章规定外,还应符合图样的要求。
10.1.3容器的制造单位应具有符合国家压力容器安全监察机构有关法规要求的质量体系或质量保证体系。
10.1.4容器的焊接应由持有相应类别的“锅炉压力容器焊工合格证书”的人员担任。
10.1.5容器的无损检测应由持有相应方法的“锅炉压力容器无损检测人员资格证书”的人员担任。
10.1.6容器主要受压部分的焊接分为A、B、C、D四类,如图10-1所示。
a)圆筒部分的纵向接头(多层包扎容器层板层纵向接头除外)、球形封头与圆筒连接的环向接头、各类凸形封头中的所有拼焊接头以及嵌入式接管与壳体对接连接的接头,均属A类焊接接头。
b)壳体部分的环向接头、锥形封头小端与接管连接的接头、长颈法兰与接管连接的接头,均属B类焊接接头,但已规定为A、C、D类的焊接接头除外。
c)平盖、管板与圆筒非对接连接的接头,法兰与壳体、接管连接的接头,内封头与圆筒的搭接接头以及多层包扎容器层板层纵向接头,均属C类焊接接头。
d)接管、人孔、凸缘、补强圈等与壳体连接的接头,均属D类焊接接头,但已规定为A、B 类的焊接接头除外。
D D D C CCB B B B BB A AA AA A AA A A图10-110.1.7凡制造受压组件的材料应有确认的标记。
在制造过程中,如原有确认标记被裁掉或材料分成几块,应于材料切割前完成标记的移植。
确认标记的表达方式由制造单位规定。
对于有防腐要求的不锈钢以及复合钢板制容器,不得在防腐蚀面采用硬印作为材料的确认标记。
10.2冷热加工成形10.2.1根据制造工艺确定加工裕量,以确保凸形封头和热卷筒节成形后的厚度不小于该部件的名义厚度减去钢板的负偏差。
GB150[1]制造检验与验收
![GB150[1]制造检验与验收](https://img.taocdn.com/s3/m/3aa6b2fa284ac850ad0242b8.png)
10制造、检验与验收10.1总则10.1.1本章适用于单层焊接、多层包扎、热套及锻焊压力容器。
对于设计温度低于或等于—20℃的容器,还应符合附录C(标准的附录)的规定。
注:热套压力容器是指套合而经机械加工或不经机械加工,各层之间以过盈相互配合,其套合预应力须经热处理尽量消除的容器。
10.1.2容器的制造、检验与验收除应符合本章规定外,还应符合图样的要求。
10.1.3容器的制造单位应具有符合国家压力容器安全监察机构有关法规要求的质量体系或质量保证体系。
10.1.4容器的焊接应由持有相应类别的“锅炉压力容器焊工合格证书”的人员担任。
10.1.5容器的无损检测应由持有相应方法的“锅炉压力容器无损检测人员资格证书”的人员担任。
10.1.6容器主要受压部分的焊接分为A、B、C、D四类,如图10-1所示。
a)圆筒部分的纵向接头(多层包扎容器层板层纵向接头除外)、球形封头与圆筒连接的环向接头、各类凸形封头中的所有拼焊接头以及嵌入式接管与壳体对接连接的接头,均属A类焊接接头。
b)壳体部分的环向接头、锥形封头小端与接管连接的接头、长颈法兰与接管连接的接头,均属B类焊接接头,但已规定为A、C、D类的焊接接头除外。
c)平盖、管板与圆筒非对接连接的接头,法兰与壳体、接管连接的接头,内封头与圆筒的搭接接头以及多层包扎容器层板层纵向接头,均属C类焊接接头。
d)接管、人孔、凸缘、补强圈等与壳体连接的接头,均属D类焊接接头,但已规定为A、B 类的焊接接头除外。
D D D C CCB B B B BB A AA AA A AA A A图10-110.1.7凡制造受压组件的材料应有确认的标记。
在制造过程中,如原有确认标记被裁掉或材料分成几块,应于材料切割前完成标记的移植。
确认标记的表达方式由制造单位规定。
对于有防腐要求的不锈钢以及复合钢板制容器,不得在防腐蚀面采用硬印作为材料的确认标记。
10.2冷热加工成形10.2.1根据制造工艺确定加工裕量,以确保凸形封头和热卷筒节成形后的厚度不小于该部件的名义厚度减去钢板的负偏差。
GB1502011压力容器制造检验和验收

▲7、删去了对质保体系,人员资格的 要求。
◆1、修改了受压元件成 形后实际厚度的规定;
●2、修改了封头形状偏 差检查方法及合格要求;
●3、修改了简体直线度 检查方法;
●4、修改了筒节长度的 规定;
★5、提高了M36~M48的 螺栓、螺柱和螺母的要求。
GB150.4 《压力容器-制造、检验和验收》
五、GB 150.4修订的主要变化
▪ ——材料新能提升:减少材料的复验。
GB150.4 《压力容器-制造、检验和验收》
——“基于风险(失效模式)的压力容器设计、制造与检 验”技术的应用:制造过程中的失效预防与控制。 ▪ ——封头成形技术提升:限制褶皱,采用全尺寸样板检 查形状。 ▪ ——焊接技术与装备提高:提高焊接工艺评定要求,减 少产品焊接试件数量。 ▪ ——检验技术开发:壳体直线度检查、TOFD检测技术、 气液组合压力试验…… ▪ ——相关标准修订与进步:NB/T 47014《承压设备焊接 工艺评定》等
GB150.4 《压力容器-制造、检验和验收》
▪ GB150.4-2011 ▪
压力容器 ▪
第4部分:制造、检验和验收 ▪ 2012.03.11
GB150.4 《压力容器-制造、检验和验收》
▪ 二、修订过程
▪ — 2010年1月6日海口会议
▪
增列钢带错绕容器
▪ — 2010年3月合肥会议
▪
并入低温容器
PED的安全基本要求,全面提出了基于失效模式设计的理 念,在设计准则、计算方法、制造检验要求等方面引入了 现代技术研究的成果。对促进贸易和提高竞争力起到了重 要的作用。 ▪ 在美国、澳大利亚和其他国家也相继修订了原有的技术 标准体系。 ▪ 相应降低了安全系数,使我国面临国外压力容器产品的 冲击,需合理修订标准(如容器分类,设计与制造阶段的 风险评估与控制,材料复验,产品焊接试件要求等),提 高中国压力容器产品的质量和国际竞争力。
GB150.4制造与检验部分
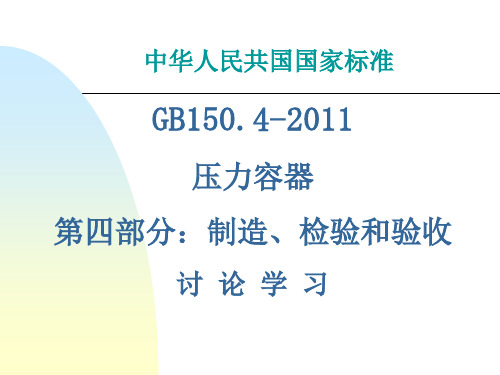
6.冷热加工成形与组装
6.1 成形 6.1.1 制造单位应根据制造工艺确定加工余量,以确 保受压元件成形后的实际厚度不小于设计图样标注 的最小成形厚度。 6.1.2 采用经过正火、正火加回火或调质处理的钢材 制造的受压元件,宜采用冷成形或温成形;采用温 成形时,须避开钢材的回火脆性温度区。
回火脆性 :是指淬火钢回火后出现韧性下降的现象。淬火 钢在回火时,随着回火温度的升高,硬度降低,韧性升高, 但是在许多钢的回火温度与冲击韧性的关系曲线中出现了两 个低谷,一个在 200~400℃之间,另一个在450~650℃之间。 回火脆性可分为第一类回火脆性和第二类回火脆性。
6.冷热加工成形与组装
第一类回火脆性又称不可逆回火脆性,低温回火脆性,主 要发生在回火温度为 250~400℃时, 1.特征 (1)具有不可逆性; (2)与回火后的冷却速度无关; (3)断口为沿晶脆性断口。 2.防止方法 避免这个温度范围内回火,没有能够有效抑制产生这种回 火脆性的合金元素。
6.冷热加工成形与组装
6.冷热加工成形与组装
6.5.2 在焊接接头环向、轴向形成的棱角E,宜分别 用弦长等于Di/6,且不小于300mm的内样板(或 外样板)和直尺检查(见图5、图6),其E值不得 大于(δs/10+2)mm,且不大于5mm。
GB150钢制压力容器是压力容器行业标准体系中的核心标准

GB150钢制压力容器是压力容器行业标准体系中的核心标准,本标准规定了钢制压力容器的设计、制造、检验和验收要求。
该标准第10条中对制造检验与验收进行了原则性规定。
壳体直径是压力容器的一个重要性能参数,在设计图纸上给出了理论(公称)数值,其公差要求由GB150中相应条款给以限定。
在GB150中,第10.2.7款规定了非机加面的尺寸公差,第10.2.4.10款规定了圆度公差,第10.2.4.2款规定了壳体上焊缝形成的棱角E的允差值。
用公差原理对这几款进行分析后,笔者认为GB150中对壳体直径的规定是清楚和确定的。
但这一规定是不尽合理的。
它既不符合公差原理中尺寸公差应大于形状偏差的包容原则,又必使制造、检验与验收中出现不必要的争议。
为此,笔者就这一问题进行分析,提出改进建议。
2公差原理零件在图样上表达的所有要素都有一定的公差要求,无功能要求的要素是不存在的。
通常对于线性尺寸的公差有的标注于图纸,而图纸未标注的(未注公差)也均在技术条件中给定。
给出的尺寸公差是该尺寸要素的极限值,即所谓的包络线,也就是最大尺寸与最小尺寸的界线。
而该尺寸要素的形状偏差应在该要素的尺寸公差范围内,这是公差理论中的一个基本原理和准则,即是说要素的形状偏差不能超出要素的尺寸公差。
要素为圆的尺寸公差,是指以理论圆心为中心的两个以圆的直径上下公差为数值的两个同心理论圆。
而圆的形状偏差不规则,应在两个同心圆的中间。
如果图纸和技术要求给出的形状偏差超出尺寸公差,那就违背了公差原理。
3GB150相关条款及其分析对于压力容器壳体直径(一般指壳体内径Di)是一个重要参数,在实际图纸中只给出理论值,而不标注公差,其公差要求在GB150中进行了规定。
3.1尺寸公差第10.2.7中规定,非机械加工表面的线性尺寸的极限偏差,按GBT1804中C级的规定。
查GBT1804-92的,C级的各尺寸段(括号内)的偏差数值分别为:(>120-400mm)?1.2mm,(>400-1000mm)?2.0mm,(>1000-2000mm)?3.0mm,(>2000-4000mm)?4.0mm;换言之,公差相对尺寸的百分比分别为2.0-0.6,1.0-0.4,0.6-0.3,0.4-0.2;由上看出,直径尺寸大于240mm时,其直径尺寸公差与直径尺寸数值之比均小于1.3.2圆度在第10.2.4.10中规定,内压容器(针对锅炉压力容器制造质量体系的分析)组装后的壳体圆度,同一截面上最大内径与最小内径之差e,应不大于该截面内径Di的1,且不大于25mm.壳体圆度是直径的形状偏差,本条是说圆度允差为壳体直径的1,与3.1条对比,明显看出,当直径尺寸大于240mm时,直径的圆度偏差超出了直径的尺寸公差。
GB150-2011宣贯

GB150-2011宣贯主讲:杨建平(一)GB150.1~GB150.4-2011《压力容器》作为我国压力容器建造的基础标准替代了原GB150-1998《钢制压力容器》,于2011年11月21日发布,2012年3月1日实施。
标准的结构:第1部分:通用要求;第2部分:材料;第3部分:设计;第4部分:制造、检验和验收。
种编排方式在组合使用(包括GB150以外的)时对设计人员提出了更高的要求。
如:(1)、GB150.1的1.3.2钢制容器不得超过按GB150.2中列入材料的允许使用温度范围;2、GB150.1的1.4.1本标准适用钢制容器的结构形式按本部分以及GB150.2-GB150.4的相应规定;(2)、GB150.1的4.1.4《固定式压力容器安全技术监察规程》管辖范围内的压力容器设计应接受特种设备安全监察机构的监察;(3)、GB150.1的4.1.6对不能按GB150.3确定结构尺寸的容器或受压元件,可以采用以下方法进行设计:附录C、D、E(而这些都要按《容规》1.9不符合本规程时的特殊处理规定——报国家质量监督检疫总局(简称国家质检总局),由国家质检总局委托有关的技术组织或者技术机构进行技术评审)(二)标准的内容1、GB150.1《压力容器》第1部分:通用要求本标准的第1部分由四章正文和六个规范性附录构成。
四章正文的内容分别是:范围、规范性引用文件、名词术语与符号和通用要求:六个规范性附录分别是:附录A——标准的符合性声明及修订、附录B——超压泄放装置、附录C——以验证性爆破试验确定容器设计压力、附录D——对比经验设计方法、附录E——局部结构应力分析和评定和附录F ——风险评估报告。
GB150.1《压力容器-通用要求》代替GB150-1998《钢制压力容器》中的部分内容(第1章-第3章、附录B、附录C),主要技术变化如下:(1)扩大了标准的使用范围,使用各种金属材料制压力容器;(2)修订了确定许用应力的安全系数;(3)增加了满足特种设备安全技术规范所规定的基本安全要求的符合性声明;(4)增加了采用标准规定之外的设计方法的实施细则;(5)增加了进行容器设计阶段风险评估的要求和实施细则。
GB150钢制压力容器是压力容器行业标准体系中的核心标准

GB150钢制压力容器是压力容器行业标准体系中的核心标准,本标准规定了钢制压力容器的设计、制造、检验和验收要求。
该标准第10条中对制造检验与验收进行了原则性规定。
壳体直径是压力容器的一个重要性能参数,在设计图纸上给出了理论(公称)数值,其公差要求由GB150中相应条款给以限定。
在GB150中,第10.2.7款规定了非机加面的尺寸公差,第10.2.4.10款规定了圆度公差,第10.2.4.2款规定了壳体上焊缝形成的棱角E的允差值。
用公差原理对这几款进行分析后,笔者认为GB150中对壳体直径的规定是清楚和确定的。
但这一规定是不尽合理的。
它既不符合公差原理中尺寸公差应大于形状偏差的包容原则,又必使制造、检验与验收中出现不必要的争议。
为此,笔者就这一问题进行分析,提出改进建议。
2公差原理零件在图样上表达的所有要素都有一定的公差要求,无功能要求的要素是不存在的。
通常对于线性尺寸的公差有的标注于图纸,而图纸未标注的(未注公差)也均在技术条件中给定。
给出的尺寸公差是该尺寸要素的极限值,即所谓的包络线,也就是最大尺寸与最小尺寸的界线。
而该尺寸要素的形状偏差应在该要素的尺寸公差范围内,这是公差理论中的一个基本原理和准则,即是说要素的形状偏差不能超出要素的尺寸公差。
要素为圆的尺寸公差,是指以理论圆心为中心的两个以圆的直径上下公差为数值的两个同心理论圆。
而圆的形状偏差不规则,应在两个同心圆的中间。
如果图纸和技术要求给出的形状偏差超出尺寸公差,那就违背了公差原理。
3GB150相关条款及其分析对于压力容器壳体直径(一般指壳体内径Di)是一个重要参数,在实际图纸中只给出理论值,而不标注公差,其公差要求在GB150中进行了规定。
3.1尺寸公差第10.2.7中规定,非机械加工表面的线性尺寸的极限偏差,按GBT1804中C级的规定。
查GBT1804-92的,C级的各尺寸段(括号内)的偏差数值分别为:(>120-400mm)?1.2mm,(>400-1000mm)?2.0mm,(>1000-2000mm)?3.0mm,(>2000-4000mm)?4.0mm;换言之,公差相对尺寸的百分比分别为2.0-0.6,1.0-0.4,0.6-0.3,0.4-0.2;由上看出,直径尺寸大于240mm时,其直径尺寸公差与直径尺寸数值之比均小于1.3.2圆度在第10.2.4.10中规定,内压容器(针对锅炉压力容器制造质量体系的分析)组装后的壳体圆度,同一截面上最大内径与最小内径之差e,应不大于该截面内径Di的1,且不大于25mm.壳体圆度是直径的形状偏差,本条是说圆度允差为壳体直径的1,与3.1条对比,明显看出,当直径尺寸大于240mm时,直径的圆度偏差超出了直径的尺寸公差。
GB150-98(容器制造、检验、验收)-文档资料

(1)弧 长 = 0.030D0 (2)弧 长 =0.035D0
(3)弧 长 =0.040D0 (4)弧 长 =0.045D0 (5)弧 长 =0.055D0 (6)弧 长 =0.065D0
2 0 0 (7)弧 长 =0.075D0
(8)弧 长 =0.085D0
100 80 60
(9)弧 长 =0.100D0 (10)弧 长 =0.125D0 (11)弧 长 =0.150D0
上 表A类 焊 接 接 头 不 包 括 此 类 焊 接 接 头
上 表B类 焊 接 接 头 包 括 此 类 焊 接 接 头
b.复合钢板对口错边量b
基层
δs δ复
δs
δs
δ复
b≥50%δ复且≦2
(2)焊接接头棱角规定
a.焊接在环向形成的棱角规定
外棱角
1/6Di 且≥300
E≤0.1δs+2 且≤5
1/6Di 且≥300 样板
D:法兰外径 当D<100mm时按100mm计算。
B C
A A向
C B向
不允许 C-C
A
A
不允许
A -A
允许
图样注明特殊要求 法兰的螺栓通孔应与壳 体主轴线或铅垂线跨中 布 置 ,有 特 殊 要 求 时 ,应 在图样上注明.
(7)直立容器底座圈、底板上的地脚螺栓 通孔分布、尺寸及中心圆直径允差规定
Emax≤1.25Di/100 Emax—最大间隙
球形封头
Emax≤1.25Di/100
直边纵向折皱深度 ≤1.5 直边纵向折皱深度 ≤1.5
Di ≥3/4Di 转角半径
样板
碟形封头
Emax≤1.25Di/100
Di 转角半径
- 1、下载文档前请自行甄别文档内容的完整性,平台不提供额外的编辑、内容补充、找答案等附加服务。
- 2、"仅部分预览"的文档,不可在线预览部分如存在完整性等问题,可反馈申请退款(可完整预览的文档不适用该条件!)。
- 3、如文档侵犯您的权益,请联系客服反馈,我们会尽快为您处理(人工客服工作时间:9:00-18:30)。
▪ (2) 与国际接轨和国际贸易的需要 ▪ 1997年欧盟颁布了PED,同时实施了以技术法规为基本
安全要求、协调标准为技术支撑的安全保障体系。 ▪ 后续发布的欧洲统一压力容器标准在技术上全面满足
PED的安全基本要求,全面提出了基于失效模式设计的理 念,在设计准则、计算方法、制造检验要求等方面引入了 现代技术研究的成果。对促进贸易和提高竞争力起到了重 要的作用。 ▪ 在美国、澳大利亚和其他国家也相继修订了原有的技术 标准体系。 ▪ 相应降低了安全系数,使我国面临国外压力容器产品的 冲击,需合理修订标准(如容器分类,设计与制造阶段的 风险评估与控制,材料复验,产品焊接试件要求等),提 高中国压力容器产品的质量和国际竞争力。
(3) 解决行业关注的突出问题的需要
▪
如给予失效模式的制造、检验,成型受压
▪ 元件的性能恢复,无损检测的时间与方法等……
(4) 技术发展的需要
▪
GB 150-1998《钢制压力容器》实施以来,
我国压力容器材料、设计、制造。检验水平大幅
度提高。
▪ ——新材料开发:增加新材料制造、检验、与验 收要求。
▪ 五、GB 150.4修订的主要变化
▪ GB 150.4主要变化的原因:
▪
1、为完善我国压力容器法规、技术标准体系,与
修订后的《固定式压力容器安全技术监察规程》相适应所
做的修订(该部分变化在下表中以★标识,共23处)。
▪
2、为适应技术发展,采用先进技术所作的修订
(该部分在下表中以●标识,共12处)。
▪ — 2011年7月征求WTO成员国意见并修改定稿
▪ 三98颁布13年来中国发生的技术和管理变化
▪ ——压力容器的大型化、高参数、长周期趋势(失效模式发 生变化)
▪
千吨级的加氢反应器,二千吨级的煤液化反应器,一
万立方米的球罐,高温、高压强腐蚀、深冷等极端工况容器。
第5章
●增加材 料复验的 规定。
第6章
◆1、修改了受压元件成形 后实际厚度的规定; ●2、修改了封头形状偏差 检查方法及合格要求; ●3、修改了简体直线度检 查方法; ●4、修改了筒节长度的规 定; ★5、提高了M36~M48的 螺栓、螺柱和螺母的要求。
五、GB 150.4修订的主要变化
第7章
第8章
★1、修改了需进行焊接工艺 评定的范围; ★2、修改了焊接工艺评定试 样、技术档案保存期; ●3、增加了取样、试验方法 、合格指标的规定; ★4、修改了焊接返修后再次 热处理的规定。
◆1、增加了成形受压元件进 行恢复性能热处理规定; ●2、增加了改善材料力学性 能热处理及其他热处理的规 定; ★3、增加了对热处理炉、热 处理工艺和记录的要求; ◆4、修改了容器及受压元件 需进行焊后热处理范围; ◆5、修改了容器及其受压元 件焊后热处理操作要求。
●修改了
GB150.4适用范 围。
▲增加了规范性 ▲增加了名
引用文件
词术语
五、GB 150.4修订的主要变化
第4章
●1、增加了对容器元件、焊材的要求 ; ●2、增加了容器制造过程中风险预防 与控制的规定; ★3、增加了对新技术、新工艺和新方 法的使用规定; ★4、增加了容器制造过程中设计修改 、材料代用的规定; ★5、增加信息化管理规定; ▲6、将容器焊接接头分类的规定至 GB150.1,并增加E类接头; ▲7、删去了对质保体系,人员资格的 要求。
▪ ①随着国内企业高含硫原油的加工,介质腐蚀性愈加严重。压 力容器面临着防止应力腐蚀、腐蚀疲劳、氢损伤等多种失效模 式的亲课题;
▪ ②装置与单位设备的大型化导致低合金高强钢的广泛应用,同 时引起裂纹敏感性增强。目前高强钢承压设备占国内承压设备 的2%左右,其中10%发现有各种原因造成的裂纹。
▪ ③大型石化装置运行周期大幅度提高,对选材、设计、制造提 出新要求。
▪
3、为与国际接轨和提升我压力容器产品竞争力所
做的修订(该部分在下表中以◆标识,共6处)。
▪
4、调整表述方法,使文字简洁,结构更合理。
(该部分在下表中以▲标识,共7处)。
五、GB 150.4修订的主要变化
总体结构
第1章
第2章
第3章
▲1、修订为分标准 ,共13章; ▲2、将GB 1501998附录C融入正 文; ▲3、多层容器相关 要求成章
▪ ——材料新能提升:减少材料的复验。
——“基于风险(失效模式)的压力容器设计、制造与 检验”技术的应用:制造过程中的失效预防与控制。
▪ ——封头成形技术提升:限制褶皱,采用全尺寸样板检 查形状。
▪ ——焊接技术与装备提高:提高焊接工艺评定要求,减 少产品焊接试件数量。
▪ ——检验技术开发:壳体直线度检查、TOFD检测技术、 气液组合压力试验……
五、GB 150.4修订的主要变化
第9章
◆1、修改了制备产品焊 接试件范围; ★2、修改了制备母材热 处理试件及其他试件范 围; ●3、增加了取样、检验 与评定要求; ★4、增加了合并制备产 品焊接试件与母材热处 理试件的规定。
第10章
★1、增加了无损检测方法选择的规定; ★2、增加了无损检测实施时间的规定; ★3、修改了全部(100%)涉嫌或超声检测 的范围; ★4、修改了局部射线或超声检测范围; ◆5、修改了表面检测的范围; ★6、增加了射线和超声技术等级要求; ★7、增加了衍射时差法超声检测方法 (TOFD)并规定了合格级别 ★8、增加了组合检测要求; ★9、增加了无损检测档案保存要求。
▪ 四、主要修订依据及参考资料
▪ 主要参考资料:
▪ 1、 ASME规范等
▪ 2、 公开发表的论文及相关技术资料
▪ 3、 行业专家提供的技术资料和修订意见
▪ 4、 GB 150-1998实施过程收集的36份提案
▪
——采纳29条,如:风头直边部分不得存在纵向
褶皱等;
▪
——未采纳7条,如:提高气密性试验压力等。
▪ ——相关标准修订与进步:NB/T 47014《承压设备焊接 工艺评定》等
▪ 主要修订依据: ▪ 4.1、 TSG R0004-2009《固定式压力容器安
全技术监察规程》
▪ 4.2、 GB 150-1998《钢制压力容器》 ▪ 4.3、 HG 3129-1998《整体多层夹紧式高压
容器》
▪ 4.4、 钢带错绕压力容器相关资料
▪ GB150.4-2011
▪ 压力容器
▪ 第4部分:制造、检验和验收
▪ 二、修订过程
▪ — 2010年1月6日海口会议
▪
增列钢带错绕容器
▪ — 2010年3月合肥会议
▪
并入低温容器
▪ — 2010年6月北京会议
▪
处理网评意见211条,初步形成送审稿
▪ — 2010年11月
▪
处理送审意见78条,形成报批稿草稿