OP-XX-QC-001 Rev.01 来料质量控制程序
PLM系统文控中心登录指引-Rev01

5.特别提醒
各伙伴需查找哪份文件,或表单,不知存放哪个路径或部门时,可点击“体系及标准文档”菜单下的“各级体系文件清单”查看文件所属部门,以便及时准确查看。
文控中心
2015.07.15
PLM系统文控中心登录指引
1.首先输入密码进入http://192.168.1.3/PLM系统
(每台电脑都有个PLM账户,如无找部门文员或网管告知登录密码)
2.进入金蝶K/3 PLM系统后,选择文档管理—文档库—工作区
3.点击“体系及标准文档”,查看对应受控文件和表单
体系及标准文档”文件夹权限说明
文件夹名称
权限
可读取
仅浏览
01质量手册
管理者代表
品质经理
体系专员
公司全体
02程序文件
文件编制部门全体人员
其它兄弟部门
03三级文件
06审核
/
各部门全体人员
07外来文件
/
04记录文件
公司全体
/
09认证证书扫描档
/
各级体系文件清单
/
注:
1:PLM体系文件仅体系专员有导入,删除和打印权限
2: 如还无法进入“标准及体系文档”阅读权限的伙伴找谢工协助开通
质量控制程序文件

质量控制程序文件质量控制程序文件是指一个组织或企业为确保产品或服务质量达到一定标准而制定的一系列文件和程序。
这些文件和程序旨在规范和管理质量控制活动,确保产品或服务在生产和交付过程中的一致性和合规性。
以下是一个标准格式的质量控制程序文件的示例:1. 文件标题:质量控制程序文件2. 文件编号:QC-0013. 生效日期:2022年1月1日4. 目的:本文件旨在确保组织的产品或服务在生产和交付过程中达到一致的质量标准,以满足客户的需求和期望。
5. 适用范围:本质量控制程序文件适用于所有与产品或服务质量控制相关的部门和人员。
6. 定义和缩写词:- 质量控制(QC):指一系列活动和措施,以确保产品或服务符合预定的质量标准。
- 质量标准:指产品或服务应满足的规定要求和期望。
- 部门:指组织内负责特定职能的工作单元或团队。
7. 质量控制程序:7.1 质量计划制定- 质量计划应在产品或服务的开发或生产过程开始之前制定。
- 质量计划应明确列出产品或服务的质量目标、可接受的质量标准和质量控制活动的时间表。
- 质量计划应由相关部门经理和质量控制团队共同制定,并经批准后生效。
7.2 质量控制活动- 质量控制活动应根据质量计划进行执行。
- 质量控制活动包括但不限于原材料检验、生产过程监控、产品检测和测试、数据分析等。
- 质量控制活动应由经过培训和合格的质量控制人员执行,并记录相关数据和结果。
7.3 不合格品管理- 对于不符合质量标准的产品或服务,应立即进行不合格品处理。
- 不合格品应进行分类、标识和隔离,以防止误用或混淆。
- 不合格品的处理应根据相关的不合格品管理程序进行,包括原因分析、纠正措施和预防措施的制定。
7.4 数据分析和持续改进- 对质量控制活动的数据进行分析,并根据分析结果制定持续改进措施。
- 数据分析应包括但不限于质量指标的统计、趋势分析和问题识别。
- 持续改进措施应由质量控制团队和相关部门共同制定,并经批准后实施。
进货检验控制程序中英文版本

12.03.0setoCOP002COP014COP037COP038QCI002《纠正和预防措施控制程序》目的Purpose本程序规定了公司对原材料、辅助材料、设备零配件、委外加工件的进货检验/验证的控制方法,目的是为使供应商进厂交货的原材料、辅助材料、外购/外协件、加工品等验收工作能迅速、正确、有效地执行,确保未经检验或未经验证合格的产品不投入使用或加工(因生产急需来不及验证而放行的除外)。
This procedure stipulates con trol method for incoming goods in spect ion /validati on of raw / auxiliary material, equipme nt, parts ,subassembly and parts processed by other compa ny .Its purpc is to make checking and accepting of raw / auxiliary material , parts purchased from other company processed with the help of other compa ny and processed products can be carried out quickly ,correctly and effectively and en sure the products that have n?t bee n in spected or in spected be unsatisfactory will not be used or processed (except the ones we haven?t time to validate ) 范围Scope本程序适用于本公司所有原材料、辅助材料、设备零配件、委外加工件的进货检验/验证和试验。
来料质量控制流程

来料质量控制流程一、背景介绍来料质量控制是指对供应商提供的原材料、零部件或者成品进行检验和评估,以确保其符合公司质量标准和客户要求。
来料质量控制流程的目的是确保所采购的物料质量稳定可靠,以减少不合格品的流入和对生产过程的影响,提高产品质量和客户满意度。
二、来料质量控制流程步骤1. 采购需求确认- 采购部门与相关部门沟通确认物料需求,并制定采购计划。
- 确定物料的技术要求、质量标准和特殊要求。
2. 供应商评估与选择- 采购部门根据公司的供应商管理制度,对潜在供应商进行评估。
- 评估内容包括供应商的质量管理体系、技术能力、交货能力、售后服务等。
- 选择合格的供应商,并与其签订合作协议。
3. 材料到货检验- 接收部门接收到货物后,进行外观检查,检查包括物料的数量、包装完整性等。
- 根据物料的特性,进行抽样检验或者全检。
- 根据公司的来料检验标准,对物料进行检验。
- 检验内容包括尺寸、外观、性能、化学成份等。
- 检验结果记录在来料检验报告中。
4. 不合格品处理- 如果发现不合格品,需要进行处理。
- 不合格品可以进行返工修复,或者退回供应商。
- 对于严重不合格的物料,需要进行隔离处理,以防止误用。
5. 供应商绩效评估- 根据供应商提供的物料质量情况,及时更新供应商绩效评估数据。
- 绩效评估内容包括物料的合格率、交货准时率、售后服务等。
- 根据绩效评估结果,对供应商进行分类管理,以便于后续采购决策。
6. 数据分析与持续改进- 对来料质量控制流程的数据进行分析,找出问题的根本原因。
- 制定改进措施,以减少不合格品的数量和提高物料质量。
- 定期召开质量改进会议,对改进措施进行评估和跟踪。
7. 定期审核- 对来料质量控制流程进行定期审核,确保其有效性和符合要求。
- 审核内容包括流程的执行情况、数据的准确性和合规性等。
- 根据审核结果,及时修订和更新来料质量控制流程。
三、流程的关键点和注意事项1. 与供应商的沟通合作至关重要,确保供应商理解和满足公司的质量要求。
QC01文件和资料控制程序

如此印章并非红色,代表此文件并非合法之版本,并不会受到控制及更新,请使用受控制之文件。
文件控制印章使用部门:□总经理 □管理者代表□财务课 □总务课 □营业课□资材课 □制造课 □品质课 □相关方1.目的为了规范质量环境管理体系文件和资料的制作、审批、分发、变更及报废等作业活动,使体系文件持续受控,确保各部使用正确、有效、最新的文件。
2.范围适用于公司内所有质量环境体系文件和资料的管制。
3.职责3.1总经理:负责质量环境手册及程序文件的承认。
3.2管理者代表:负责质量环境管理手册、程序文件的确认及三级文件的承认。
3.3品质课:负责文件之原稿存档、分类、标识、格式化、发行回收报废。
3.4职责部门:负责文件的制作及变更。
3.5相关部门:负责文件的接收、保存、标识、使用及变更的提出。
4.定义4.1正本文件:由文件发起人书写或制作的手稿及电子媒体或电子媒体输出件。
4.2管制副本:受品质课管制的有关正本文件的复印件。
4.3非管制副本:未受控的,也不作更新及回收的正本文件的复印件。
4.4作废文件:已失效的文件。
4.5参考文件:受品质课管理的,仅供参考的文件。
5.程序内容5.1文件和资料控制流程。
5.2文件制作5.2.1管理者代表组织全厂质量管理系统文件的编写,各职责部门负责根据质量管理系统运作实际编写相关文件。
5.2.2程序文件的构成与格式。
程序文件由封面、正文、附件三部分构成。
——文件封面由文件名称、制订部门、制定日期、修订日期、文件编号、版本、页数和制作者、审核者、批准者之签名栏构成。
——正文形式由文件编号、名称、版本、页次及文件内容组成。
各类文件因层次不同而内容不一。
A.质量环境管理手册各章、节描述文件化质量环境管理体系的构架及程序之概述,而且各过程描述包括目的、范围、权责、作业内容及参考文件、支持文件等。
B.程序文件正文内容含目的、范围、职责、定义、程序内容及相关表单、参考资料等,标准规范文件形式由制定部门、文件编号、页次、制定日期、修订日期、版本及制订者、审核者、批准者签名和正文组成,正文内容可以直接按需要列出文件内容。
QP1001进料检验控制程序

1. 目的验证分承包方提供的产品是否满足规定的产品质量要求.确保不合格原材料和外购外协件不投入使用.2. 适用范围本程序适用于本公司产品用原材料、外购外协件及包装箱(品)进厂的检验或试验控制.(包括新产品开发、样件、小批量试制、批量生产)3. 职责3.1 质保部负责进货检验控制和归档管理,有关检验人员负责分别按进货检验作业指导书对原材料、外购外协件的进厂检验,正确作出合格与否的符合性结论,并作好相关原始记录.作好检验状态标识.3.2 技术课负责有关原材料标准的制订及进货检验作业指导书的审核,并及时作好有关技术更改的通知.3.3 副总经理负责进货检验作业指导书和技术更改的批准.3.4 采购课负责原材料、外购外协件的采购事宜和签订《采购合同》,原材料和外购外协件到厂后向质保部及时提出检验申请,并负责不合格原材料及外购外协件的退货及所造成损失的索赔等工作.3.5 仓库保管人员必须及时做好相关产品标识,作好原材料、外购外协件的入库手续控制.3.6 所有员工应确保和维护检验和试验状态的标识.4. 工作程序4.1 检验和试验策划4.1.1在产品先期质量策划阶段,由技术课负责根据产品的过程流程图、PFMEA、顾客指定特性值,相似产品/工艺的资料以及QFD/DOE分析结果制订检验流程计划(该计划须包括产品形成过程中的所有检验包括委外检验),并将检验流程计划供现场使用,其内容包括:a.注明零件名称、零件号;b.各过程阶段的产品质量;c.简述工序名称;d.注明使用检验指导书名称/编号;e.说明决策可能性(如认可、返工、返修、隔离等).该检验流程计划每年由质保部进行审核,计划须与各项质量计划(控制计划)相符.4.1.2由质保部根据检验流程计划编制检验指导书,对每项重要检验项目的方式和方法作出规定,其内容必须包括:检验方法、检验工具以及精度、抽样方法(接收准则C=0)、评定(统计)方法、记录方式,注明可需要提供质保书/自检报告,要求和验证方式,目检项目根据材料名称/编号等.对于复杂的检验和试验以及复检(如返工后检验)须制订检验和试验操作规程和返工指导书,对于目检项目的极限样件顾客要求时须经认可.4.2 对进厂的原材料,外购外协件等物资进行检验,试验和验证,确保不合格的原材料、外购外协件不入库,不投产,不使用.4.2.1对于A类和B类物资进货检验控制流程:a. 原材料(含主要辅料),外购外协件进厂应分类分批存放在仓库指定的地点,并以标识牌示“待检”,作好待检工作.b.原材料和外购外协件进厂后由采购课填写《产品检验申请单》,并附分承包方提交的质量证明文件和试样提交质保部复检,如不符合手续,质保部可拒绝接收.对没有试样的厂家应由采购课负责联系尽快解决,或由制造部及时安排有关车间制出试样.c.质保部根据进货检验作业指导书进行复检和试验,填写《检验报告单》和《试验报告单》,作出合格或不合格的结论.如果本公司无复检手段时,可由本公司检验员赴分承包方现场或定期委外复检.d.质保部可采用以下一种或多种方式对进货产品进行验证:------针对分承包方提供的重要特性值的控制图和过程能力测定报告;------根据检验指导书进行全数或抽样检验和试验;------由认可的测试机构出具检验/试验报告并核对报告;------根据事先在质量协议中规定的检验项目,由分承包方对所供产品的质保书或自检报告进行确认;------所供产品经检验合格或已提供了质保书情况下,对分承包方进行第二方/第三方现场审核.e.检验或试验合格的原材料和外购外协件,由检验人员开具《检验合格单》交采购课及仓库保管员.由仓库保管员办理入帐手续。
QCP模板 来料检查Incoming inspection

N
参考OIQA-001 《来料检查工作指引》 Refer to "Incoming Inspection Instruction"
参考OIQA-001 参考OIQA-001 《来料检查工 《来料检查工作 作指引》 指引》 Refer to Refer to "Incoming "Incoming Inspection Inspection Instruction" Instruction"
每批 Per Lot
OIQA-001 FM001进料 检查报告 "Incoming Inspection Report"
IPQCBiblioteka Form Number:OIQA-032 FM001 Rev.02 Effective date:2018.01.15
xxx
来料检查 Incoming inspection
参考OIQA-001 《来 料检查工作指引》 Refer to "Incoming Inspection Instruction"
X.1
参考OIQA-001 《来 料检查工作指引》 Refer to "Incoming Inspection Instruction"
Process No
Proc. Name
Machine, device, jig, tools for Mfg 机器&设备&工具
No. 检验序号
Characteristics 特征
序号
工序名称
CTQ 是否为 重点检 查项 目?
Method/方法 Inspection items 检查项目 Inspection tools 检查工具 Sample/样品 Size 抽样数 Freq. 检查频率 Control method 控制方法 Responsible Person 责任人 Remedial Action Plan 计划对策 标识、隔离、参考 《不良品处理程序 》 Labelling,quaranti ne,refer to "NonConformance Control Procedure"
来料品质控制程序
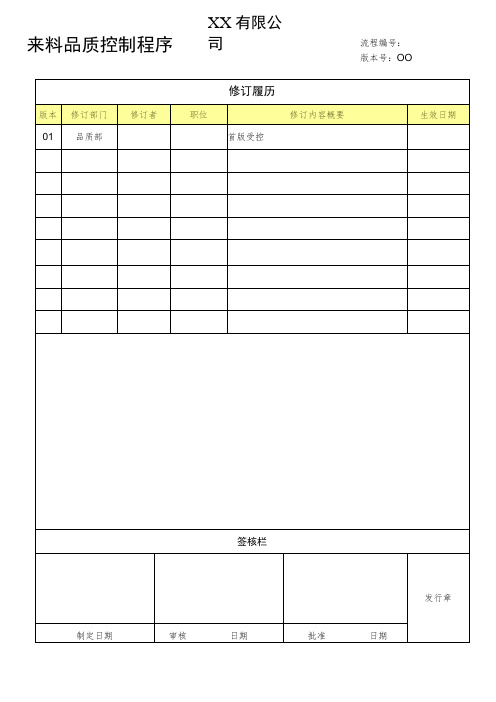
来料品质控制程序
XX 有限公
司
流程编号: 版本号:OO
1.0目的:
明确来料品质控制流程,防止来料不合格品的非预期使用。
2.0范围:
适用于本公司所有生产物料(包括客供物料)的来料品质控制。
4.0流程图:
1、状态未经标识或可疑的产品,应归类为不合格品并须提交QC再次确认。
2、无需经IQC检验的物料,若有不合格时由货仓组织相关部门处理即可,无需召开MRB会议。
4.3紧急物料放行流程图:
附表1非BOM物料检验:
6.0参考文件和资料
6.1 《环境物质管理手册》
6.2 《新物料认可流程》
6.3 《不合格品控制流程》
7.0本文件自20XX年XX月XX日起生效。
8.0本文件主管部门:品质部。
9.0本文件解释权归属品质部经理。
QA-RG-001 rev 01医疗器械质量方针和质量目标管理程序

更改历史1.0目的为建立符合《医疗器械监督管理条例》、《医疗器械生产质量管理规范》等规范性文件,明确本公司质量管理的总体质量方针和质量目标,特制定本制度。
2.0依据《医疗器械生产质量管理规范》及其附录3.0范围适用于公司质量方针的确定和年度质量目标的制定,以及对质量方针和目标的管理、实施。
4.0规定内容:4.1质量方针是由企业负责人正式发布的本企业总的质量宗旨和方向。
4.2质量目标是企业一定时期在质量方面所追求的目的,应与质量方针保持一致。
4.3质量目标是可测量的。
公司必须在各个相关部门将质量目标逐级分解和展开,以确保最终能得以落实和实现。
4.4企业负责人每年年底组织管理者代表和各部门负责人,重新审核质量方针、修订公司的质量总目标,并由企业负责人批准发布。
4.5质量方针和目标的管理程序分为计划、执行、检查、总结改进四个阶段:4.6计划阶段4.6.1每年度末,根据企业外部形势,结合本企业的质量工作实际情况,由企业负责人、管理者代表和各部门负责人召开企业质量方针研讨会,提出下年度的质量工作方针和目标4.6.2将方针目标的草案进行广泛讨论征求意见,经各部门负责人讨论通过后确定,并予以发布。
4.6.3根据企业的方针目标,各部门再进行分解,确定自己的工作目标,并落实实施目标的措施。
4.7执行阶段4.7.1公司规定各项目标措施开始与完成时间。
4.7.2各部门围绕公司下达的目标,制定相应的工作计划和方案。
4.7.3每年末,各部门将目标执行情况上报质量部,对实施过程中的困难和问题采取有效措施,确保各项目标措施按规定完成。
4.8检查阶段4.8.1质量部负责企业质量方针目标实施情况的日常检查和督促。
4.8.2每年年底,质量部按照《医疗器械监督管理条例》及公司内审制度要求对质量目标和方针内容进行审核4.9总结改进阶段4.9.1公司质量部负责对本年度质量方针目标的实施情况进行总结,认真分析执行过程中存在的问题,对未完成的项目进行分析,找出主观、客观原因。
品质控制流程

来料 Reject 客服特殊 来料 Reject 检验 Reject OQC让步 出货抽检生产 Reject IPQC 检验 获 工程师主导和提供物料首 检 RejectReject Reject RejectIPQC 巡检 全检 PE 工程师主导 PMC 和生产部负责, ECN 生效目的:为更好的保障旭峰威视产品质量制作一个流程《品质控制流程》, <应用本公司各部门>是一个特殊的团体每一个人身兼数职。
怎样做到文件程序化,目前还没有正规的企业管理软件,那么需要我们共同配合和监督来完成所需要的文件,每一个文件都需供应商评审 采购材料 入库存储发料生产 顾客满意度调查出 货 顾客抱怨顾客满意业务受理 退货供应商要求改善,提供分析报告和改善方案采取纠正/预防措施各工序检测 调查分析/落实责任 包装 不合格供应商 开 始产品试产 入 库 首次定单生产 记录归档 结束返工或返修 直接报废 降级生产过程分析与改进 下工单生产要列入清单。
根据实际情况陆续完善清单内容.没有完成的监督完成,没有完善的陆续完善。
一,来料品质控制1、原材料采购;采购员看到工程部发放的《物料评估报告》才可以下定单(封面电子档即可)《物料评估报告》a,需要附样板3-5PCS,特殊包装物料需要按要求包装附样板A、测试报告,特殊零件需要有QA《可靠性测试报告》B、SGS认证原材料采购只是针对目前没有完善的文件作出要求,IQC运作由品质部门控制2、半成品外购;采购员看到工程部发放的《物料评估报告》才可以下定单(封面电子档即可)《物料评估报告》a,需要附有样板至少1PCS,包装方式可以以图纸说明A、PCB板《作业指引书》,工艺要求,工艺图B、机箱部件--《作业指引书》外观要求,尺寸,材料要求说明,可以参考供应商检测报告半成品检查:PCB板抽检,外观/性能需要记录每检测的产品外观只需记录有损坏的。
《来料检验报告》发放给QA和PE负责人。
SOP-011 QF-05 REV.A 来料检查报告记录表Data Sheet

外观
尺寸
插\拔力
镀层厚度及附着力
审核(Checked By): 日期(Date):
盐雾实验
其它:______
SOP-011 QF-05 REV.A
2.尺寸及功能检验续(Dimensional & Functional Inspection-continued) No. (编号) Specification/T Evaluation/MeasuSample Size rement Method olerance (规格/公差) (检验工具/方法) (检验数量) No.1 Actual Inspection Results(实际检验结果) No.2 No.3 No.4 No.5 REJ QTY
八达光电科技有限公司
Page of
Incoming Inspection Data Sheet 来 料 检 验 记 录 表
Part No. (零件编号) Part Des(供应商) Drawing Rev. (图纸版本) Inspection Date (检验日期)
测量仪器代码(Mearsurement Instrument Code):目视Naked Eyes(A) 5X放大镜 5XMagnifier(B) 显微镜Microscope (C) 卡尺Caliper(D) 普通千分尺 Standard Micrometer (E) 刀口千分尺 Blade Micrometer (F)工具显微镜DTM(G) 投影仪Shadow Graph(H) 三次元OGP(I) 高度规Depth Gage(J) 针规Pin Gage(K) 牙规Thread gage(L) 螺纹千分尺Thread Micrometer (M) 推拉力计Push/Pull Force Tester(N) 电涡流测厚仪Coating Thickness Gage(O) X光 测量仪X-Ray fluorescence Measuring System(P) 万用表Multimeter(Q) 盐雾试验机Salt Spray Tester(R) 粗糙度对比块Surface Finish Comparator(S) 已根据WI-QA-001对以下项目进行检验: QC检验员(Inspected By): 日期(Date):
来料质量控制流程
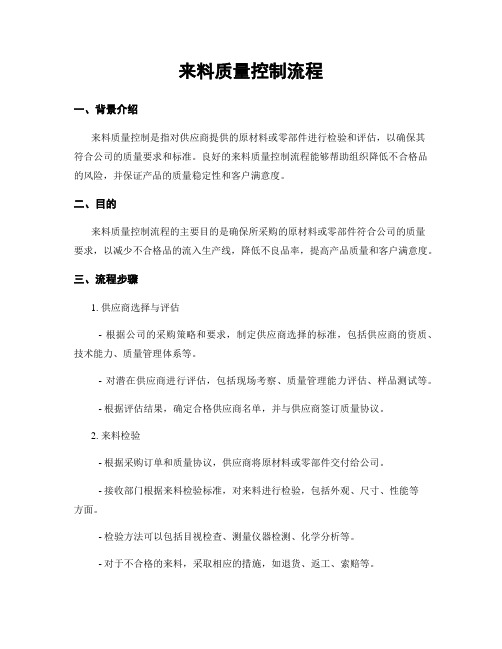
来料质量控制流程一、背景介绍来料质量控制是指对供应商提供的原材料或零部件进行检验和评估,以确保其符合公司的质量要求和标准。
良好的来料质量控制流程能够帮助组织降低不合格品的风险,并保证产品的质量稳定性和客户满意度。
二、目的来料质量控制流程的主要目的是确保所采购的原材料或零部件符合公司的质量要求,以减少不合格品的流入生产线,降低不良品率,提高产品质量和客户满意度。
三、流程步骤1. 供应商选择与评估- 根据公司的采购策略和要求,制定供应商选择的标准,包括供应商的资质、技术能力、质量管理体系等。
- 对潜在供应商进行评估,包括现场考察、质量管理能力评估、样品测试等。
- 根据评估结果,确定合格供应商名单,并与供应商签订质量协议。
2. 来料检验- 根据采购订单和质量协议,供应商将原材料或零部件交付给公司。
- 接收部门根据来料检验标准,对来料进行检验,包括外观、尺寸、性能等方面。
- 检验方法可以包括目视检查、测量仪器检测、化学分析等。
- 对于不合格的来料,采取相应的措施,如退货、返工、索赔等。
3. 来料评估- 对合格的来料进行评估,包括质量记录的完整性、供应商的交货准时率等。
- 根据评估结果,对供应商进行绩效评价,并提供反馈意见,以便供应商改进质量管理。
4. 数据分析和持续改进- 对来料质量数据进行分析,包括不合格率、供应商绩效等指标。
- 根据数据分析结果,制定改进措施,如加强供应商培训、改进来料检验标准等。
- 定期进行来料质量控制流程的审核,确保其有效性和适应性。
四、相关角色和责任1. 采购部门- 负责制定供应商选择和评估的标准,并与供应商签订质量协议。
- 监督供应商的质量管理能力和交货准时率。
- 协调供应商和接收部门之间的沟通和合作。
2. 接收部门- 负责来料检验和评估,确保来料符合质量要求。
- 及时反馈不合格品情况,并与供应商协商解决措施。
- 维护来料检验记录和质量数据的完整性和准确性。
3. 质量部门- 提供来料检验标准和方法,并对接收部门进行培训和指导。
来料质量控制流程

来料质量控制流程一、引言来料质量控制是指对供应商提供的原材料、零部件等来料进行质量检验和控制的过程。
良好的来料质量控制流程能够确保生产过程中所使用的原材料和零部件的质量符合要求,从而提高产品质量和客户满意度。
本文将详细介绍来料质量控制流程的各个环节和相关要求。
二、来料质量控制流程1. 来料接收来料接收是来料质量控制流程的第一步,负责接收供应商送来的原材料和零部件。
在接收过程中,需要进行以下操作:- 核对送货单和物料清单,确保所接收的物料与订单一致。
- 检查包装完好性,防止物料在运输过程中受损。
- 对物料进行数量检验,确保数量与订单一致。
2. 外观检验外观检验是对来料外观质量进行评估的环节。
在外观检验过程中,需要进行以下操作:- 检查外包装是否完好,有无破损或变形。
- 对物料的表面进行检查,确保无划痕、凹陷、变色等问题。
- 检查物料的颜色、纹理等外观特征是否符合要求。
3. 尺寸检验尺寸检验是对来料尺寸精度进行评估的环节。
在尺寸检验过程中,需要进行以下操作:- 使用合适的测量工具(如卡尺、量规等)对物料的尺寸进行测量。
- 将测量结果与设计图纸或规格书进行对比,确保尺寸符合要求。
- 对于关键尺寸或特殊要求的物料,可以进行更加精细的测量和评估。
4. 功能性检验功能性检验是对来料功能性能进行评估的环节。
在功能性检验过程中,需要进行以下操作:- 根据产品要求和测试方法,对物料的功能进行测试。
- 测试结果应与产品要求进行对比,确保功能性能符合要求。
- 对于特殊要求的物料,可以进行更加严格的功能性能测试。
5. 化学成分检验化学成分检验是对来料化学成分进行评估的环节。
在化学成分检验过程中,需要进行以下操作:- 根据产品要求和测试方法,对物料的化学成分进行测试。
- 测试结果应与产品要求进行对比,确保化学成分符合要求。
- 对于特殊要求的物料,可以进行更加精确的化学成分分析。
6. 抽样检验抽样检验是对来料进行抽样检测的环节。
来料质量控制流程
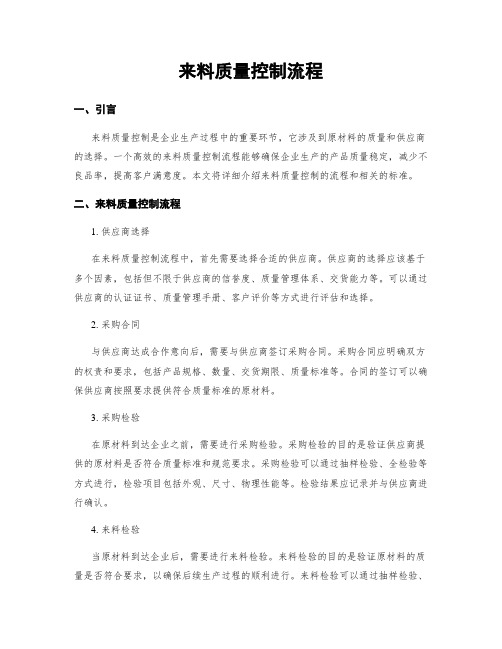
来料质量控制流程一、引言来料质量控制是企业生产过程中的重要环节,它涉及到原材料的质量和供应商的选择。
一个高效的来料质量控制流程能够确保企业生产的产品质量稳定,减少不良品率,提高客户满意度。
本文将详细介绍来料质量控制的流程和相关的标准。
二、来料质量控制流程1. 供应商选择在来料质量控制流程中,首先需要选择合适的供应商。
供应商的选择应该基于多个因素,包括但不限于供应商的信誉度、质量管理体系、交货能力等。
可以通过供应商的认证证书、质量管理手册、客户评价等方式进行评估和选择。
2. 采购合同与供应商达成合作意向后,需要与供应商签订采购合同。
采购合同应明确双方的权责和要求,包括产品规格、数量、交货期限、质量标准等。
合同的签订可以确保供应商按照要求提供符合质量标准的原材料。
3. 采购检验在原材料到达企业之前,需要进行采购检验。
采购检验的目的是验证供应商提供的原材料是否符合质量标准和规范要求。
采购检验可以通过抽样检验、全检验等方式进行,检验项目包括外观、尺寸、物理性能等。
检验结果应记录并与供应商进行确认。
4. 来料检验当原材料到达企业后,需要进行来料检验。
来料检验的目的是验证原材料的质量是否符合要求,以确保后续生产过程的顺利进行。
来料检验可以通过抽样检验、全检验等方式进行,检验项目包括外观、尺寸、化学成分、机械性能等。
检验结果应记录并与供应商进行确认。
5. 不合格品处理如果原材料经过来料检验发现不合格,需要进行不合格品处理。
不合格品可以进行退货、返修、报废等处理方式。
不合格品的处理应符合相关的质量管理制度和流程,确保不合格品不会影响到后续的生产过程。
6. 数据分析与改进来料质量控制流程的最后一步是数据分析与改进。
通过对来料质量的数据进行分析,可以发现问题的根源和改进的方向。
可以使用统计工具和方法,如控制图、因果分析等,进行数据分析和问题解决。
同时,企业还应与供应商进行沟通和合作,共同改进来料质量。
三、来料质量控制的标准1. 供应商评估标准供应商评估标准应包括以下方面:- 供应商的信誉度和声誉- 供应商的质量管理体系和认证情况- 供应商的交货能力和供货稳定性- 供应商的售后服务能力和响应速度- 供应商的价格和成本控制能力2. 采购合同标准采购合同应包括以下内容:- 产品的规格和要求- 产品的数量和交货期限- 产品的质量标准和检验要求- 价格和支付方式- 违约责任和索赔条款3. 采购检验标准采购检验标准应包括以下方面:- 抽样检验和全检验的比例和方法- 检验项目和检验标准- 检验结果的判定标准和处理方式- 检验记录和报告的要求4. 来料检验标准来料检验标准应包括以下内容:- 抽样检验和全检验的比例和方法- 检验项目和检验标准- 检验结果的判定标准和处理方式- 检验记录和报告的要求5. 不合格品处理标准不合格品处理标准应包括以下方面:- 不合格品的分类和处理方式- 不合格品的追溯和责任追究- 不合格品的记录和报告要求- 不合格品处理的监督和审核机制四、总结来料质量控制是企业生产过程中的重要环节,一个高效的来料质量控制流程能够确保企业生产的产品质量稳定。
产品质量控制程序
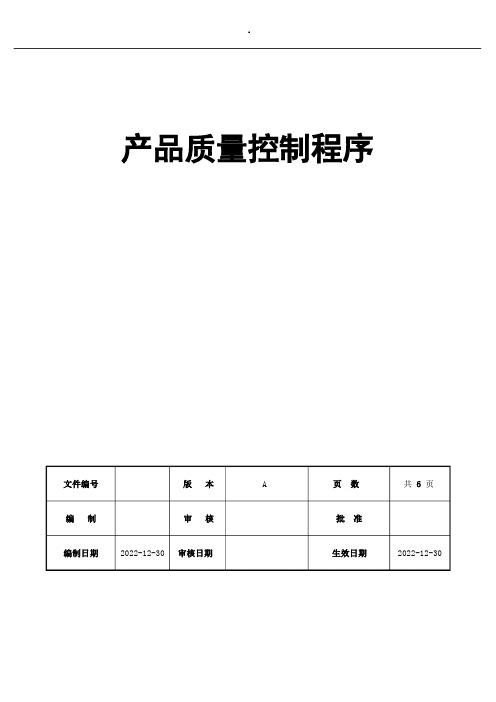
共页样品采购送样批量采购供应商来料通知采购入库送检不合格来料检验合格领料成品/半成品生产不合格样品承认合格采购申请单供应商样品承认报告1.采购申请单2.请款单来料检验报告供应商品质异常处理单1.入库单2.物料控制卡1.领料单2.退补料单制程检验合格成品合格入库确认合格不合格不合格不合格返工返工返工1.不合格品处理单2.巡检记录表3.成品检验记录1.生产流程卡2.入库单3.巡检记录表成品入库出货确认不合格出货检验报告返工成品包装1.出库单2.发货单出库/发货TEC-QM-8241退货对原材料、成品及半成品进行检验,为生产出合格优质的产品提供保证;对产品特性进行监视和测量,验证产品要求得到满足,以确保满足顾客的要求。
合用于公司所有的来料检验、制程检验、入库检验、出货检验。
3.1 :仓管员负责对来料的接收、数量核对。
3.2 :负责将来料品质不良的信息传达给供应商,并跟踪其处理进度。
3.3 :3.3.1 来料检验(IQC)职责:依照检验规范对来料进行检验,识别和记录来料品质问题。
3.3.2 制程检验(IPQC)职责:3.3.2.1 对公司生产线进行巡检,识别和记录产品品质问题,制程中问题点的研究与分析。
3.3.2.2 对成品/半成品按照检验标准进行检验,对于检验不合格的产品告知生产进行修复和调试,并对不合格事项进行记录。
3.3.3 成品检验职责:3.3.3.1 依照成品检验标准对生产完的产品进行检验,识别和记录成品品质问题。
3.3.3.2 拒收不合格的成品。
3.3.4 入库和出库检验职责:对于原材料、外协件、成品的入库或者出库,品质工程师需要先确定相关的信息并在入库单和出库单上签字后才干进行入库和出库。
3.4 :负责对评定后的新物料/新供应商物料进行测试、评估,提供样品的评估结果。
4.1 来料检验(IQC):指对供应商提交的原材料、外购件、外协件的检验。
4.2 制程检验(IPQC):指产品开始生产到产品入库前这一过程的检验。
品质控制流程—QC工作流程—检验控制流程

□总经办 □生产制造 □财务 □工程部 □品管部 □客服部 □人力资源部 □资材部 □合金部 □仓务 □五金冲压□五金加工 □手动抛光 □自动抛光 □装配 □首饰 □工模 □生产技术 □样品 □设备维护 □仓储 □采购 □PMC
□总经办 □生产制造 □财务 □工程部 □品管部 □客服部 □人力资源部 □资材部 □合金部 □仓务 □五金冲压□五金加工 □手动抛光 □自动抛光 □装配 □首饰 □工模 □生产技术 □样品 □设备维护 □仓储 □采购 □PMC
□总经办 □生产制造 □财务 □工程部 □品管部 □客服部 □人力资源部 □资材部 □合金部 □仓务 □五金冲压□五金加工 □手动抛光 □自动抛光 □装配 □首饰 □工模 □生产技术 □样品 □设备维护 □仓储 □采购 □PMC
□五金加工 □手动抛光 □自动抛光 □装配 □首饰 □工模 □生产技术 □样品 □设备维护 □仓储 □采购 □PMC
□五金加工 □手动抛光 □自动抛光 □装配 □首饰 □工模 □生产技术 □样品 □设备维护 □仓储 □采购 □PMC
□总经办 □生产制造 □财务 □工程部 □品管部 □客服部 □人力资源部 □资材部 □合金部 □仓务 □五金冲压□五金加工 □手动抛光 □自动抛光 □装配 □首饰 □工模 □生产技术 □样品 □设备维护 □仓储 □采购 □PMC。
- 1、下载文档前请自行甄别文档内容的完整性,平台不提供额外的编辑、内容补充、找答案等附加服务。
- 2、"仅部分预览"的文档,不可在线预览部分如存在完整性等问题,可反馈申请退款(可完整预览的文档不适用该条件!)。
- 3、如文档侵犯您的权益,请联系客服反馈,我们会尽快为您处理(人工客服工作时间:9:00-18:30)。
1.目的:
规范XX公司的来料质量控制。
2.范围:
该程序适用于XXXXXXXXX科技有限公司所有采购物料,包括原材料、设备、器件等。
3.定义:
3.1 收货单---收货单据。
3.2 检查验收报告—来料检测验收记录
3.3 供应商纠正预防措施报告---供应商对质检发现的问题进行的原因分析和提出的解决措施
3.4 物料评审报告---对不合格物料处理方式的报告
4.参考文件:
4.1 采购程序(OP-XX-PUR-001 Rev.02)
5.职责:
5.1 仓库负责收货并通知质检组验货。
5.2 质检组负责根据检验标准和规范对来料进行检查验收并完成检查验收报告。
5.3 质检组负责就不合格来料召集相关部门讨论处理方案、完成《物料评审报告》。
5.4 技术部和工程部负责提供来料的验收标准和规范,并对质检组的检查工作提供协助。
5.5 项目部负责组织相关部门对采购的大型工程设备或复杂的设备系统的联合验收。
6. 过程描述:
6.1 物料的接收:
6.1.1 当仓库收到物料后,填写收货单,并通知质检组验货。
6.2 检查验收:
6.2.1 确认到货的包装是否符合合同要求。
6.2.2 确认到货的数量是否符合合同要求。
6.2.3 产品质量性能检查:
6.2.3.1 根据物料的种类数量不同,确定抽样的数量或是否全检。
6.2.3.2 如果抽样检查,则随机抽取样品。
6.2.3.3 根据技术部和工程部给出的验收标准和规范,对样品进行检查或全检。
6.3 检查验收结果记录于《检查验收报告》。
6.4 处理:
6.4.1 若检查验收合格,则通知仓库办理入仓手续。
6.4.2 若检查验收不合格,则通知仓库拒收并反馈给采购部。
6.5 物料评审:
6.5.1 对检查验收质量性能不合格的物料,质检组应及时召开物料评审会议以决定如何处理。
6.5.2 物料评审会议的代表应包括技术部、工程部、生产部、项目部、采购部的代表。
6.5.3 最终的处理决定由主管副总经理或其授权的代表签署。
6.5.3.1 特采。
6.5.3.2 挑选。
6.5.3.3 退货。
6.5.3.4 报废。
6.5.3.5 返修。
6.5.4 若最后的处理结果为返修,则返修后的物料需质检组重新按正常的程序检查验收合格后才能入仓。
6.5.5 对来料有问题的供应商,质检组需发给其《供应商纠正预防措施报告》并要求改善。
6.6 来料质量监控:
6.6.1 质检组应每三个月对所有来料的质量情况作一次总结并抄送采购部。
6.7 施工现场的应急性采购质量控制:
6.7.1 由施工现场的质检组人员对所有应急性采购物料进行检查验收;如现场无质检组人员,则由项目部负责人
代为组织工程部、技术部人员进行三方共同验收,完成检查验收报告,并将验收结果及时反馈给质检组和采
购部。
6.8 对于从外采购的大型工程设备或复杂的设备系统则由项目部组织工程技术质检等相关部门的人员联合进行检查验
收,质检组协同做好相关验收记录。
7.记录:
7.1检查验收报告【F-XX-QC-001 Rev.01】
7.2供应商纠正预防措施报告【F-XX-QC-002 Rev.01】
7.3 物料评审报告【F-XX-QC-003 Rev.01】
8.过程流程图:
8.1来料检查流程
来料检查流程图。