冲压CAE分析技术在外板设计中的应用
9. 车门外覆盖件冲压与CAE分析关键技术

车门外覆盖件冲压与CAE 分析关键技术李玉强上海赛科利汽车模具技术应用有限公司,上海 201209摘要:车门外板在外板类覆盖件具有典型的代表性,从冲压工艺、工艺造型、CAE 分析及表面质量控制等方面都能代表外板类零件成型的工艺与分析技术,本文产品功能特点展开分析,从落料排样,冲压的工艺造型、冲压方向、CAE 分析关键技术等几个重点方面进行了深入分析。
关键词:车门;外覆盖件;工艺; CAE ;0前言车门外板是车身覆盖件中最重要的零部件之一,在车身的外观质量中,承前启后,前部和翼子板相连,中部和后部与侧围搭接,尺寸要求严格,表面质量要求高,其成形技术复杂,目前国内许多模具厂家都具备了车门外板的模具制作能力,但随着客户对产品精度和表面质量的要求越来越严格,其制作的难度也在逐渐增加。
本文将结合所完成的项目,从车门的功能性,冲压工艺,CAE 分析技术,造型技术,调试等关键技术方面展开论述。
1 车门外板功能特点门外板是汽车覆盖件中极为重要的部件之一,是车身上的活动部件,是典型的具有复杂型面的大型A 级曲面冲压件,门外板的要求外表面必须光顺平滑、棱线清晰、刚性良好,同时由于它与侧围、顶盖、后地板及后车灯等零件搭接,因此压合包边后的四周外轮廓精度要求较高,公差要求为±0.5mm 。
随着汽车设计质量以及安全性能的逐步升级,门外板的材料也在发生着变化,其对刚性的要求逐步加强,目前更多的门外板开始采用烘烤硬化板,以提高产品的抗凹陷性。
2 关键技术分析2.1落料工艺对于门外板,一般采用梯形料可以节省坯料大小。
不同产品由于形状不同,则梯形的尺寸和大小也不同,具体需要根据产品形状和工艺补充的大小确定。
梯形料通常采用摆剪落料,注意摆剪落料角度一般设备不能超过30度。
对于不能采用梯形料或摆剪超过30度的坯料形状,可以采用无缝排样的方式节省材料。
图1 波浪刀节省材料的原理 图2 门外板的定位板 矩形料 步距波浪刀料为了进一步节省材料,SGM已经开始应用和推广波浪刀,已经完成的某项目的后门外板落料模就是这种方式,在排布波浪刀的落料模时需要注意几个事项。
CAE在产品设计中的应用

CAE在产品设计中的应用作者:韦亮来源:《科技与企业》2013年第18期【摘要】CAE(计算机辅助工程)是采用虚拟分析方法对结构(场)的性能进行模拟预测结构(场)的性能,优化结构(场)的设计,为产品研发提供指南,为解决实际工程问题提供依据。
本文主要针对CAE在产品设计中的应用进行研究,通过对CAE在产品设计中应用现状的分析,结合具体的产品设计实践,提出进一步优化和增强CAE在设计中应用的对策。
【关键词】CAE;产品设计;有限元分析;应用1、引言随着世界经济全球化进程的不断加快以及市场竞争的激烈程度不断提高,生产制造企业迫切需要缩短产品研发的周期和成本投入,CAE技术的大规模普及正式满足了这样的要求。
CAE(计算机辅助工程)的实质就是为工程设计提供一种用于计算和仿真的平台。
目前的CAE应用领域覆盖了电子设计、飞机、汽车等大量的工程领域,CAE技术在这些领域的大规模应用大大的缩短了产品的设计周期,加快了产品研发的速度,而且通过CAE虚拟模拟技术的应用,大大降低了产品研发的成本,也为企业提高经济效益带来了条件。
2、CAE内涵及设计通常情况下的产品设计采取的是首先进行产品的设计,然后通过CAE(计算机辅助工程)技术对设计的产品进行后期的基于软件平台的分析,在这种意义来讲,CAE技术是CAD (计算机辅助设计)技术的后续过程。
然而,随着经济社会的快速发展以及市场竞争的不断激烈,同时也是为了满足公司降低产品开发成本、缩短产品开发周期的需要,将CAE技术在产品开发中的应用进行了新的调整,更加倾向于将CAE技术置于CAD技术的前一阶段,即首先通过基于计算机的软件仿真技术对产品就行仿真,可以大幅度的缩短产品的开发周期,同时对于降低产品开发成本也有着显著效果。
CAE技术本身就是一种典型的设计方法,它的应用对于产品设计的整个流程都有着重要影响。
一般情况下,传统的经验设计思路虽然能够取得一定的效果,但是如果加入CAE技术的理性元素,就会使得产品设计的周期更短、质量更好。
CAE技术在复杂冲压模具开发中的应用

0 引言
.
非 线 性 、边 界 条 件 非 线 性 等 多重 非 线 性 的非 常 复 杂 的 力学 过 程 。 由于 影 响成 形 过 程 的 因素 很 多 , 因此 人 们 不 能 精 确 控 制 材 料 的流 动 。成 形 过 程 中 会 产 生 各 种 各 样 的缺 陷 ,影 响零 件 的 几 何 精 度 、 表 面 质 量 和 力学 性 能 。总 的来 说 ,覆 盖 件 成 形 的 主 要缺 陷有 起皱 、破 裂和 回弹 。 在 薄 板 冲压 成 形 过 程 中 , 当切 向 压 应 力 达 到
模拟来改进 模具设计。以Au o o m软件为例 ,介绍 了C E tf r A 技术在某轿 车前减振器架 前板 模具
开发中的应用 ,大大缩短 了模具的开发周期 ,降低 了制模成本 , 高了模具质量。 提
关键词 :O E;Auo o m;冲压 ;模具 A t fr 中图分类号 :T 3 6 G 8 文献标识码 :B 文章编号 :1 0 - 14 2 1 ) 下) 0 1 0 9 0 ( 0 o 1 ( -04 - 3 0 3 0
CAE 术 ,大 大缩 短 了模 具 的开 发 周期 ,降 低 了 技 成本 。
参l
匐 似
C E 术 在 复 杂 冲压 模具 开 发 中的 应 用 A 技
Applcaton of CA E echnol gy n co pl x am pi i i t o i m e st ng ( e dev o i f el pm ent
丁 友生 。 ,李志 军
工作。
CAE分析在板料成型冷冲压模具设计中的应用

CAE分析在板料成型冷冲压模具设计中的应用田乃东(上海电气集团上海电机厂有限公司,上海200240)摘要:目前,衡量国家加工业整体水平的主要指标是模具设计的发展,行业的进一步拓展,需要开发多功能、高效、复杂、大型、长寿、先进的设备。
在模具实际投入生产之前,它可以发现许多问题,然后技术人员可以对其进行分析,并根据CAE分析数据结果合理调整模具设计的实际方案,从而达到缩短模具生产周期的目的。
现主要研究CAE分析在板料成型冷冲压模具设计中的应用情况。
关键词:冷冲压模具;板料成型;CAE数值模拟0引言冲压工艺是金属(塑料)成型的基本手段,提供具有特定形状且可满足特定使用要求的零件。
其机制是:在压力机的作用下,金属(或非金属)板被推过冲模以使结构分离或变形。
通常,由于冲压过程在常温条件下进行,此类冲压也称为“冷冲压”。
冲压加工主要包括三个重要因素:冲压设备、原材料和冲压模具。
原材料通常由金属或非金属板制成;冲压模具涉及冲压操作中的约束,该工具能在冲压过程中限制板材的塑性变形过程,以根据所需部件结构特征加工板材;冲压设备通常是指压力机,其主要提供板变形所需的力。
所谓“数字设计”,即基于先进的理论和方法,使用数字技术作为工具来实现设计过程中对象的数字表达、处理、存储和控制。
随着计算机技术、虚拟仿真技术和数值理论等学科的迅速发展,数字化设计逐渐发展和成熟,其研究和开发已成为各个生产大国关注的热点。
通过计算机辅助设计(CAD)、计算机辅助分析(CAE)、计算机辅助工艺(CAPP)等先进技术实现数字化产品的设计和开发,能够降低生产成本,并最大限度地缩短开发周期,显著提高新产品商业开发的效率和市场适应性。
1板料冲压成型的缺陷板料冲压受到许多因素的影响和限制,需要解决的主要问题是材料是否可以根据预期的目标变形。
在实际生产中,形状设计的效果通常会受到很多因素影响,材料的起皱、回弹和破裂影响相对较大。
在冲压片材之后,将形成不同水平的材料缺陷,有些缺陷可以忽略,但如果是有特殊要求的组件,这将产生很大的影响。
冲压成形CAE技术在汽车冲压零件设计流程中的应用
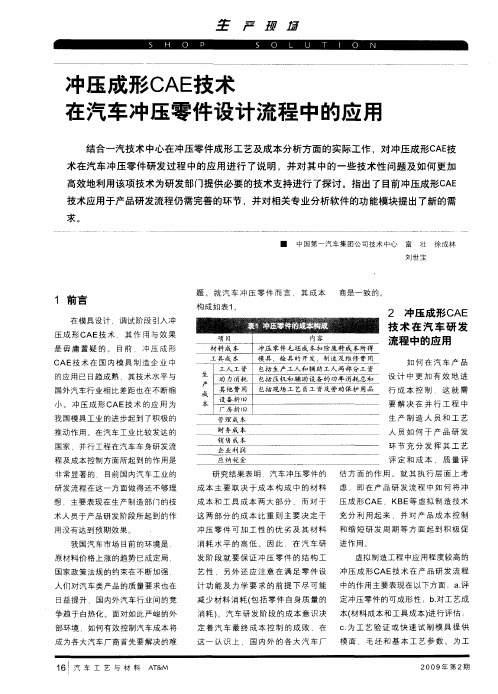
题 。 就 汽 车 冲 压 零 件 而 言 . 其 成 本 商 是 一 致 的 。 构 成 如 表 1 。
2 冲压成形C AE
内 容
项 目
材料成 本
工 具 成Байду номын сангаас本
冲压 零件 毛坯 成本扣除废 料成本所得
模 具、检具 的开发、制造 及维修 费用
技 术 在 汽 车 研 发 流 程 中的 应 用
日益提 升 ,国 内外汽 车行业 间的竞
争 趋 于 白 热 化 。面 对 如 此 严 峻 的 外
减 少材 料消 耗( 包括 零 件 自身质 量 的 定 ; 压 零 件 的 可 成 形 性 ,b对 工 艺 成 中 . 消 耗) 。汽 车研 发 阶段 的成 本意 识 决 本( 材料 成本和 工具 成本) 行评估 : 进
1 汽车 T艺- 6 l b材料 A& TM
2 0 年第2 09 期
生 产 琐 毯
艺 验 证 或 快 速 试 制 模 具 提 供 模 面 数 据 和 基 本 工 艺 参 数 不 仅 可 以 缩 短 研
发 周 期 、降低 试 制 成本 而且 试 验
反 馈 可 以 对 数 值 计 算 结 果 进 行 修 正 并 提 高 分 析 人 员 业 务 能 力 和 实 践 经
如 何 在 汽 车 产 品 设 计 中 更 加 有 效 地 进 行 成 本 控 制 这 就 需 要 解 决 在 并 行 工 程 中
生 产 制 造 人 员 和 工 艺
生 工人 工资 包括 生产工人和 辅助工人 两部分工 资
产 动 力 消 耗 包括 压 机 和 辅 助 设 备 的功 率 消耗 总 和 成 其 他 费 用
. 定 着 汽 车 最 终 成 本 控 制 的 成 败 , 在 C 为 工 艺 验 证 或 快 速 试 制 模 具 提 供 这 一 认 识 上 国 内 外 的 各 大 汽 车 厂 模 面 毛 坯 和 基 本 工 艺 参 数 。 为 工
CAE技术在模具设计过程中的并行应用
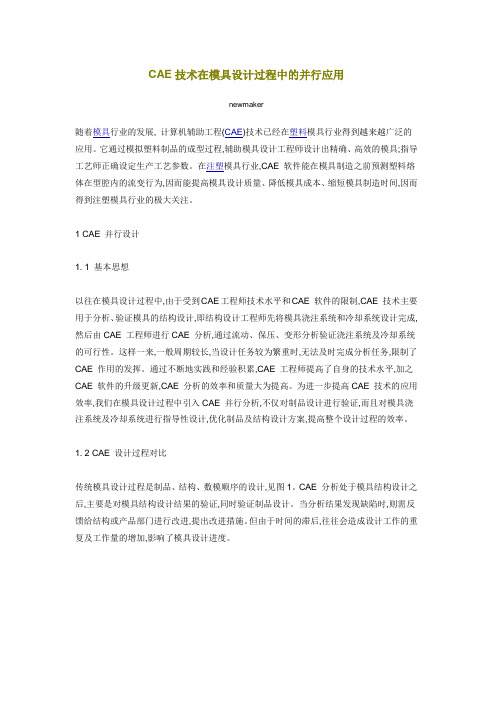
CAE技术在模具设计过程中的并行应用newmaker随着模具行业的发展, 计算机辅助工程(CAE)技术已经在塑料模具行业得到越来越广泛的应用。
它通过模拟塑料制品的成型过程,辅助模具设计工程师设计出精确、高效的模具;指导工艺师正确设定生产工艺参数。
在注塑模具行业,CAE 软件能在模具制造之前预测塑料熔体在型腔内的流变行为,因而能提高模具设计质量、降低模具成本、缩短模具制造时间,因而得到注塑模具行业的极大关注。
1 CAE 并行设计1. 1 基本思想以往在模具设计过程中,由于受到CAE工程师技术水平和CAE 软件的限制,CAE 技术主要用于分析、验证模具的结构设计,即结构设计工程师先将模具浇注系统和冷却系统设计完成,然后由CAE 工程师进行CAE 分析,通过流动、保压、变形分析验证浇注系统及冷却系统的可行性。
这样一来,一般周期较长,当设计任务较为繁重时,无法及时完成分析任务,限制了CAE 作用的发挥。
通过不断地实践和经验积累,CAE 工程师提高了自身的技术水平,加之CAE 软件的升级更新,CAE 分析的效率和质量大为提高。
为进一步提高CAE 技术的应用效率,我们在模具设计过程中引入CAE 并行分析,不仅对制品设计进行验证,而且对模具浇注系统及冷却系统进行指导性设计,优化制品及结构设计方案,提高整个设计过程的效率。
1. 2 CAE 设计过程对比传统模具设计过程是制品、结构、数模顺序的设计,见图1。
CAE 分析处于模具结构设计之后,主要是对模具结构设计结果的验证,同时验证制品设计。
当分析结果发现缺陷时,则需反馈给结构或产品部门进行改进,提出改进措施。
但由于时间的滞后,往往会造成设计工作的重复及工作量的增加,影响了模具设计进度。
随着计算机辅助设计技术的发展,以及工程数据库和参数设计的综合运用,并行工程被有效地应用到模具设计过程中,极大地提高了设计效率。
图2 为模具并行设计流程。
CAE 并行设计过程的主要思想是在制品设计中后期通过CAE 的简单分析,验证制品设计的合理性,同时根据制品性能要求优化选择制品材料,根据制品外观要求讨论制品进胶方式和可能出现的制品缺陷等。
应用CAE分析提高冲压工艺水平

序 工艺补充面的设计 。
11 冲压方 向的确定 .
传 统 冲 压 方 向 的确 定 有很 大 的
计算 时间越长 )。图3 为参 数设置 。
图4 为迭代结果 。
( 3)优化排 样 ,提 高
局 限性 ,对一 些 复 杂冲 压 件冲 压 方
向 的确 定显 得 束 手 无策 ( 传统 工 艺
传统 工 艺 方 法 对压 床 的选 用局 的预处理过程 中,好 的工艺辅 助面及
7 . 9 ,而 排样2 ( 图5 89 % 如 b)为经 备 前期提供有 力的保 证 过 C 软件优 化过 的排 样 .1 t 样 1 AE ;4 ; I ̄
R st e e :重 置 I o mp  ̄:导 入 Ep d x o :导 出
够 精 确 , 使 用 Au f m 优 化 t o o r
( t zt n Opi ai )模块 ,反复 求解得 mi o
出最 接近 结 果 的真 值 ( 代 的次 数 迭 越 多 ,其 结 果越 接 近真 值 ,但 所 需
( 2)使 凸 模 接 触 毛 坯 的 面 积
合适很容易 出现成形件破裂 、起皱或 大 。
其他成形缺陷。为 了避免这类情况 的
( 3)压料 面 各 部分 进 料 阻 力要 寸 ,使 用 不 同 的约 束条 件 将得 到 不 同的毛坯尺 寸 ( e tp On se )。
发 生 ,通 常需要修 改成形工序和工艺 均 匀 可 靠 。 参数或修 改模具 形状 。随着工业化的 而 运 用CAE分析 可 以根 据 冲压
瑞 士开 发 的专 业 薄板 成形 快 速 模拟 软 件 ,可 以用 于 薄板 、拼焊 板 的 冲 压 成形 、液压 胀形 等 过程 的模拟 , 配合 不 同 的功 能 模块 ,还 可 以进 行
CAE仿真技术在空调冲压件的模具设计和制造中的应用

导致成形时材料得不到及时补充而拉裂。因此 , 仅仅增加压 边力虽然可 以改善起皱 和拉深不足等成形缺陷, 但不能控制材料
图 2模具 、 压边圈 、 坯料的有限元模 型爆炸图
F g2 Ex l d d ve o i ie ee n d l o i s b n e n ln i . p o e i ws f r f t l me t mo e f d e , i d r a d b a k n
;mti e oe od gei b khl r oee ise ui wtdc eh la { ar at rs ni g n l -o eH wv , ivrc cln o i eo - eat h c rp n r o o a l f n d. rt y r ao h o ed t c } i ,e u br dh polot r —e s h h e ri s h hras tyo i ats{ tnt m e a e r e h d w ba , i tmn e es ia o fr n q l e o hn t f e a n i f d w c d e e w t t c r m g u i f i ;c b a i e t a d n u ec m li cnlyb k o i fr d r -e s a i 帆 e c e d r oBs m ras u o t ho g,a lno c a a ba h v on . e o n i i a ne o l h d g e d w d C l t n n n
(广 东美 的集 团 商用空调事 业部 , 山 5 80 ) 3 佛 2 30
Mo d d sg n p l a in o l e i n a d a pi t f c o CAE s mua in t c nqu n s a i lt e h i e i t mpn r c s o ig p o e s O i c dt n h e t I ar fa r On jO er e tme a t — j s p s
汽车产品设计制造中CAE技术的运用

汽车产品设计制造中CAE技术的运用1. 引言1.1 汽车产品设计制造中CAE技术的重要性在汽车产品设计制造过程中,CAE技术扮演着至关重要的角色。
CAE技术是计算机辅助工程的缩写,通过数值模拟方法和计算分析技术,可以对汽车产品进行多方面的设计、优化和验证,从而提高产品设计质量、缩短产品开发周期,降低产品研发成本。
CAE技术在汽车产品设计阶段的应用能够帮助工程师们进行结构强度、刚度、耐久性等方面的分析,预测产品在不同工况下的应力和变形情况,有效避免设计缺陷和隐患,提高产品的安全性和可靠性。
CAE技术在汽车产品制造阶段的应用可以帮助工程师优化且精准控制生产过程,减少废品率,提高生产效率并降低生产成本。
通过仿真模拟,可以提前发现潜在的生产问题,并及时调整生产方案。
CAE技术在汽车产品设计制造中的应用不仅提高了产品的设计质量和生产效率,还推动了汽车行业的技术创新和发展。
随着CAE技术的不断发展与进步,相信将为汽车行业带来更多的突破和发展机遇。
2. 正文2.1 CAE技术在汽车产品设计阶段的应用在汽车产品设计阶段,CAE技术的应用是非常关键的。
CAE技术可以帮助设计师快速准确地进行各种仿真分析,包括结构强度、热分析、流体动力学等,从而在设计阶段就能及时发现和解决问题,避免在后期制造和测试阶段造成成本和时间的浪费。
CAE技术可以通过虚拟原型的建立和测试,帮助设计师进行设计优化,提高产品设计的效率和质量。
通过CAE技术的应用,设计师可以在电脑上模拟各种复杂条件下的情况,快速评估各种设计方案的可行性和优劣,在实际制造之前就能够找出最佳的设计方案,从而提高产品的性能和可靠性。
CAE技术还可以帮助设计师进行多学科的优化设计,同时考虑结构、热功能、声学等多个方面的影响,从而实现产品的综合性能优化。
通过CAE技术的应用,设计师可以更加全面地了解产品的性能特点,并且在设计阶段就能够做出更加科学和合理的决策,从而提升产品的竞争力和市场表现。
冲压成形CAE技术在汽车冲压零件设计流程中的应用

一汽技术中心
R&D CENTER
培训
一汽技术中心
R&D CENTER
培训
一汽技术中心
R&D CENTER
培训
一汽技术中心
R&D CENTER
培训
一汽技术中心
R&D CENTER
培训
一汽技术中心
R&D CENTER
培训
一汽技术中心
第(3)部分工作介绍:
R&D CENTER
培训
冲压加工工艺基础知识的讲解及冲压零件相关标准的解释工作。
培训
本人在科室内主要负责冲压成形及金属塑性成形CAE分析方面的工作。
一汽技术中心
目前的工作内容:
R&D CENTER
培训
(1)冲压零件结构工艺性评估。这是产品设计人员需求最大的部分。 (2)冲压零件材料成本及制造成本的估算。
(3)冲压加工工艺基础知识的讲解及冲压零件相关标准的解释工作。
(4)冲压零件的试制及试制中的技术支持。
培训
冲压零件的结构无论多么复杂,都可以分解为若干个局部典型结构 如伸长类翻边、拉深变形区、胀形变形区、弯曲变形区等,而冲压零件 的成形极限一般是由其中的一个或多个局部典型结构来决定的。 对于这些局部典型结构,可以建立相应的参数化结构模型,通过不 同参变量及材料级别的组合并进行CAE计算可获得相应的成形极限、材 料厚度及强度变化的计算结果数据,该数据可以作为零件结构设计时的 参考数据以便对零件结构工艺性进行评估。 利用CAE方法获得基础数据的优势在于可以避免模型试验所必须的 高额费用,可以得到比生产实例范围更广、 更全面的基础数据。
一汽技术中心
R&D CENTER
冲压成形工艺中的CAE分析
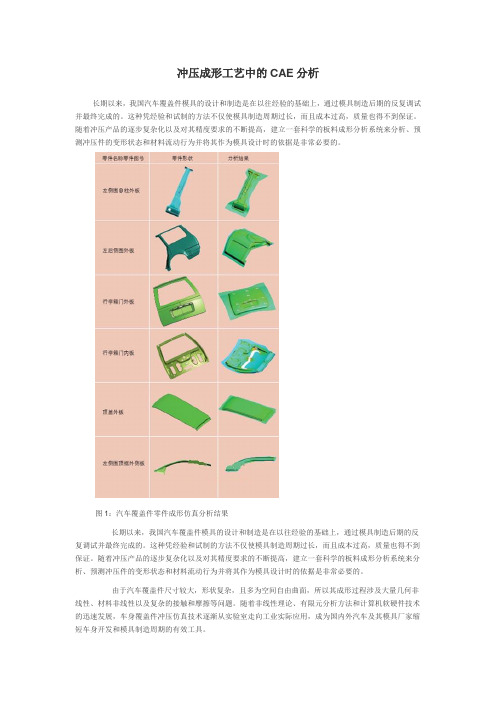
冲压成形工艺中的CAE分析长期以来,我国汽车覆盖件模具的设计和制造是在以往经验的基础上,通过模具制造后期的反复调试并最终完成的。
这种凭经验和试制的方法不仅使模具制造周期过长,而且成本过高,质量也得不到保证。
随着冲压产品的逐步复杂化以及对其精度要求的不断提高,建立一套科学的板料成形分析系统来分析、预测冲压件的变形状态和材料流动行为并将其作为模具设计时的依据是非常必要的。
图1:汽车覆盖件零件成形仿真分析结果长期以来,我国汽车覆盖件模具的设计和制造是在以往经验的基础上,通过模具制造后期的反复调试并最终完成的。
这种凭经验和试制的方法不仅使模具制造周期过长,而且成本过高,质量也得不到保证。
随着冲压产品的逐步复杂化以及对其精度要求的不断提高,建立一套科学的板料成形分析系统来分析、预测冲压件的变形状态和材料流动行为并将其作为模具设计时的依据是非常必要的。
由于汽车覆盖件尺寸较大,形状复杂,且多为空间自由曲面,所以其成形过程涉及大量几何非线性、材料非线性以及复杂的接触和摩擦等问题。
随着非线性理论、有限元分析方法和计算机软硬件技术的迅速发展,车身覆盖件冲压仿真技术逐渐从实验室走向工业实际应用,成为国内外汽车及其模具厂家缩短车身开发和模具制造周期的有效工具。
覆盖件成形仿真分析可以在多方面为企业的冲压生产提供有力的支持:在设计工作的早期阶段评价覆盖件及其模具设计、工艺设计的可行性;在试冲试模阶段,进行故障分析,解决实际问题;在批量生产阶段进行缺陷分析,以改善覆盖件生产质量,同时还可以被用来调整材料等级,降低生产成本。
以有限应变弹塑性有限元方法为基础的CAE技术通过对汽车覆盖件成形过程进行计算机模拟来预测某一工艺方案成形的可能性以及可能出现的问题,对提高覆盖件模具的加工精度,缩短模具制造周期起着非常重要的作用。
我公司汽模工程部对板料成形有限元模拟分析技术进行了深入研究,并将其用于指导模具设计和生产实践:1、板料成形过程模拟的基本流程。
CAE仿真技术在大型装备制造行业的应用
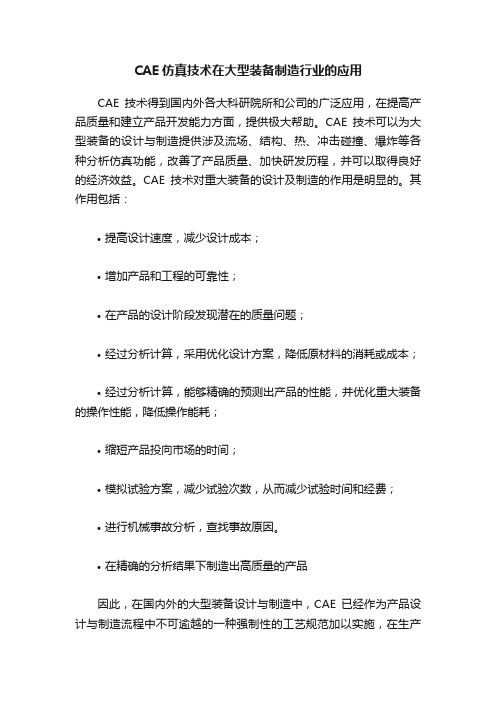
CAE仿真技术在大型装备制造行业的应用CAE技术得到国内外各大科研院所和公司的广泛应用,在提高产品质量和建立产品开发能力方面,提供极大帮助。
CAE技术可以为大型装备的设计与制造提供涉及流场、结构、热、冲击碰撞、爆炸等各种分析仿真功能,改善了产品质量、加快研发历程,并可以取得良好的经济效益。
CAE技术对重大装备的设计及制造的作用是明显的。
其作用包括:•提高设计速度,减少设计成本;•增加产品和工程的可靠性;•在产品的设计阶段发现潜在的质量问题;•经过分析计算,采用优化设计方案,降低原材料的消耗或成本;•经过分析计算,能够精确的预测出产品的性能,并优化重大装备的操作性能,降低操作能耗;•缩短产品投向市场的时间;•模拟试验方案,减少试验次数,从而减少试验时间和经费;•进行机械事故分析,查找事故原因。
•在精确的分析结果下制造出高质量的产品因此,在国内外的大型装备设计与制造中,CAE已经作为产品设计与制造流程中不可逾越的一种强制性的工艺规范加以实施,在生产实践作为必备工具普遍应用。
主要应用在如下几个方面:1、大型装备的刚度、强度分析刚度和强度分析作为装备设计和制造的基础,需要经常计算分析,包括各种零部件的刚度、强度分析,以及装备整体的刚度强度分析。
而随着大型装备的复杂性的提高,以及工作环境的多变,大量的计算不得不借助于CAE技术来辅助。
以ANSYS Mechanical为平台,分析各种大型装备总体结构及其零部件在自身重力载荷、恒定工作载荷等的(共同)作用下的变形特点和变形值、应力分布等,在此基础上进行改进,从而避免某些局部由于过大的应力集中而损坏。
某机床体的变形分析机床系统应力结果2、大型装备的结构抗震与振动性能分析大型装备在工作过程中通常会承受各种各样的动力载荷,比如,挖掘机挖掘过程中的瞬态冲击、工程机械在复杂施工条件下的运行等。
同时,大型装备由于体积和质量都较大,往往都是直接固定在地面上。
在装备运行的过程中,如果设计不好。
CAE分析在冲压成型中的应用

CAE分析在冲压成型中的应用
CAE分析在冲压成型中的应用
作者:于波;陈希娥
作者机构:辽宁曙光汽车集团有限公司;辽宁曙光汽车集团有限公司
来源:客车技术
ISSN:1006-6861
年:2008
卷:000
期:001
页码:24-26
页数:3
中图分类:U4
正文语种:chi
关键词:GAE;冲压成形;有限元;数值模拟;旋转拉深件
摘要:介绍了当前冲压数值模拟专用软件DYNAFORM的应用范围及概况,并以典型冲压件为例阐述了DYNAFORM在进行成形有限元模拟的一般步骤,即先由前处理器创建网格模型,再由求解器迭代计算出各个时间步的数据文件,最后由后处理器察看分析各处应力、应变等相关的参数分布.。
CAE分析在板料成型冷冲压模具设计中的应用

CAE分析在板料成型冷冲压模具设计中的应用摘要:现阶段,我国工业水平发展速度日渐加快。
衡量国家加工水平的重要指标之一就是模具设计。
在模具实际投入生产之前,通过CAE分析可以发现许多问题,然后技术人员可以根据CAE分析的数据结果合理调整模具设计的方案,从而达到缩短模具生产周期的目的。
本文主要研究CAE分析在板料成型冷冲压模具设计中的应用情祝。
关键词:CAE分析;板料成型冷冲压模具设计;应用引言冷冲压模具技术在当今社会有着广泛的应用,在整个模具行业内,占有近半数的比例。
但是由于模具本身的一些缺陷和技术水平的限制,使得在应用于实际生产中会存在一些困难,如某些零部件的排样不当,会使材料的利用率有所降低,导致成本偏高;部件外型的扭曲程度过大,会令连续的料带在连料和加工工艺上存在困难;对于某些孔的位置度以及精度有特殊要求的模具,会需要加入斜契冲孔;工件尖角处两侧余料过小,不易压料,需要加入氮气弹簧进行辅助压料,这些价格较高的特殊部件的加入,也会使成本上升等等。
由此可见,模具对技术的要求较高,而且必须要重视利润。
要想成功的为一件板料零部件设计级进模具,需要考虑多种因素,特别是在实际的生产中要想获得一件合格的零件,都需要进行反复的调试与实验,同时也需要一批经验丰富的模具设计师和模具钳工才能完成,在不断的修模和设变中,时间和金钱也在大量的流失。
而且随着金属材料的不断发展,汽车产业也在寻求大量的新型材料以满足和完善汽车的一些新的需求,因此按照过去传统的经验和对模具在实际生产中不断实验的方法,无法估测出新型材料的一些性能,使得模具在设计的过程中就会遇到很多困难,占用更多的时间,令实际的成本变得更高。
企业为了实现利润最大化,都在缩短生产周期,提高模具质量上下工夫,CAE技术也自然而然的被引用到了实际的生产之中。
1.板料冲压成型过程中存在的缺陷板料冲压成型过程中受到多方面因素影响和限制,其中主要需要面对的问题是,是否能够依据预期规定的轨道来对材料进行变形。
汽车产品设计制造中CAE技术的运用

汽车产品设计制造中CAE技术的运用随着现代科技的不断发展,汽车产业也在不断进行创新和改革。
在汽车产品设计和制造过程中,计算机辅助工程(CAE)技术的应用已经成为了不可或缺的一部分。
CAE技术是指将计算机技术应用于工程领域,通过数值模拟、分析和优化来辅助产品的设计和制造。
本文将对汽车产品设计制造中CAE技术的运用进行探讨。
CAE技术在汽车产品设计中的应用是非常广泛的。
在汽车产品设计的初期阶段,工程师可以利用CAE软件进行各种仿真分析,提前预测产品性能和行为,从而提前发现潜在的问题并进行改进。
在汽车车身结构设计中,CAE技术可以帮助工程师进行强度、刚度、疲劳寿命等方面的分析,从而确保车身结构的安全性和稳定性。
CAE技术还可以应用于汽车动力系统设计、悬挂系统设计、乘坐舒适性分析等方面,为汽车设计提供全面的技术支持。
CAE技术在汽车产品制造中的应用也是十分重要的。
在汽车产品的制造过程中,工程师可以利用CAE技术进行制造工艺的仿真模拟,帮助优化制造过程并提高生产效率。
在汽车车身冲压工艺中,CAE技术可以模拟车身冲压过程,分析变形情况并优化冲压模具设计,以降低成本并提高冲压质量。
CAE技术还可以用于汽车焊接工艺、涂装工艺、装配工艺等方面的仿真分析,为汽车制造提供科学的技术支持。
CAE技术还可以在汽车产品的性能优化和节能环保方面发挥重要作用。
通过CAE技术的辅助,工程师可以对汽车产品进行全面的性能分析和优化设计,以提高产品的性能和可靠性。
在汽车发动机设计中,CAE技术可以进行燃烧过程模拟、流场分析等,帮助工程师优化燃烧室结构和气缸排列方式,从而提高发动机的燃烧效率和动力性能。
CAE技术还可以应用于汽车空气动力学优化、轮胎滚动阻力优化、混合动力系统优化等方面,帮助汽车产品实现节能环保的目标。
CAE技术在示波器外壳注塑模具设计中的应用

文 章 编号 : 1 0 0 1 — 4 9 3 4 ( 2 0 1 3 ) 0 4 — 0 0 4 5 — 0 5
4 5
C A E技 术 在 示 波器 外 壳 注塑 模 具 设 计 中的应 用
赵 建 平 ,蔡 隆 玉 ,王 力
( 南 京 理 工 大 学 紫 金 学 院 , 江苏 南京 2 1 0 0 4 6 )
ZHAO J i a n - p i n g ,CAI L o n g - y u,W ANG L i Ab s t r a c t :I n o r d e r t o i mpr o v e o s c i l l o s c o p e s h e l l ’ S p r o d u c t i o n e f f i c i e n c y a n d q u a l i t y a s we l l a s r e d u c i ng t h e ma n u f a c t u r i n g c o s t , mo u l d f l o w a n a l y s i s o n t h e o s c i l l o s c o p e s h e l l wi t h CAE Mo l d f l o w s o f t wa r e wa s c a r r i e d o u t .Ba s e d o n g r i d d i v i s i o n o f 3 D mo d e l o f t he o s c i l l o s c o p e s h e l l ,t h e o p t i ma l g a t e l o c a t i o n wa s c a l c u l a t e d, a n d t h e f i l l t i m e, p r e s s u r e d i s t r i b u t i o n, c o o l i n g p r o c e s s a n d wa r p a g e d e f o r ma t i o n we r e a n a l y z e d.Co mb i n e d wi t h s i mu l a t i o n a n a l y s i s r e s u l t s ,r e a s o n a b l e mo u l d d e s i g n a n d p r o c e s s p a r a me t e r s we r e o b t a i n e d.A f t e r o s c i l l o s c o p e
模具CAE技术在轿车发动机罩外板模具调试中的应用

模具CAE技术在轿车发动机罩外板模具调试中的应用阐述了基于汽车覆盖件板成形的有限元模型分析软件AutoForm的模具CAE技术,对其特点和功能作了阐述。
以风神Bluebird发动机罩外板的模具调试为例阐述了其实际应用,对拉延模的模面设计方案进行了分析,对其拉延成形过程进行了模拟分析,并依此对拉延模的调试方案进行分析和判断,优化了改进方案,和现场取得了完全一致的结果。
一、前言当代汽车和现代模具设计制造技术都表明。
汽车覆盖件模具的设计制造离不开有效的板成形模拟软件。
国外大的汽车集团,其车身开发与模具制造都要借助于一种或几种板成形模拟软件来提高其成功率和确保模具制造周期。
作者从2001年5月开始探讨AutoForm在解决汽车覆盖件模具制造中的应用,经过各个阶段的重点攻关,实现了:对汽车冲压零件产品的可冲压成形性进行分析,判定成形的难点和关键区域;对汽车冲压零件产品实现毛坯展开计算;对模具和工艺方案的确认进行有选择性和针对性的模拟分析,给模具调试提供量化的分析判断数据,对可进行的模具调试方案进行判别,并对可行的调试方案提供具体技术参数;对模具和工艺方案进行反复优化的多次模拟,用先于现场模具调试的模具CAE技术,对拉延模具设计的可行性和可靠性进行量化的分析和判断,对有欠缺的设计提出优化改进方案: 二、AutoForm的功能和特点AutoForm提供了从产品的概念设计直至最后的模具设计的一个完整的解决方案,特别适合于复杂的深拉延和拉伸成形模的设计、冲压工艺和模面设计的验证、成形参数的优化、材料与润滑剂消耗的最小化、新板料(如拼焊板、复合板)的评估和优化。
从数据输人到后处理结果的输出,AutoForm融合了一个有效开发环境所需的所有模块,从前处理到后处理的全过程与CAD数据的自动集成,网格的自适应划分,所有的技术工艺参数设置的过程易于理解且符合工程实际。
AutoForm使用了许多现代模拟技术:应用新的隐式有限元算法保证求解的迭代收敛;采用自适应网格、时阶控制、复杂工具描述的强有力接触算法、数值控制参数的自动决定和使用精确的全量拉格朗日理论等保证求解快而且准确。
冲压磨具结构设计的最新技术应用

冲压磨具结构设计的最新技术应用近年来,随着制造业的快速发展和工业技术的不断创新,冲压磨具结构设计也得到了新的突破和应用。
本文将详细介绍冲压磨具结构设计的最新技术应用,旨在为制造业提供更好的解决方案和技术支持。
一、CAD/CAE技术在冲压磨具结构设计中的应用CAD(Computer-Aided Design)和CAE(Computer-Aided Engineering)技术的广泛应用,为冲压磨具结构设计带来了革命性的变化。
通过CAD技术,设计师可以利用计算机辅助设计软件,快速绘制冲压磨具的三维模型,准确地模拟和预测磨具的性能和工艺参数。
同时,CAE技术可以将模型导入分析软件,对磨具的刚度、强度、疲劳寿命等进行仿真分析,帮助设计师在设计过程中及时发现和解决问题,提高设计的准确性和效率。
二、材料技术在冲压磨具结构设计中的应用在冲压磨具结构设计中,材料选择起着至关重要的作用。
近年来,新型材料的应用使得磨具更加耐磨、耐腐蚀、高温抗性等方面得到了显著提升。
例如,钨钢、硬质合金、高速钢等高强度、高硬度的材料广泛用于磨具的工作部位,大大增加了磨具的使用寿命。
此外,复合材料、陶瓷等新型材料的应用,也为冲压磨具的轻量化提供了新的思路和可能性。
三、CNC加工技术在冲压磨具结构设计中的应用CNC(Computer Numerical Control)加工技术的广泛应用,使得冲压磨具的加工制造变得更加精确、高效。
CNC加工技术通过计算机程序控制加工设备,实现对冲压磨具的自动化、高精度加工。
相对于传统的手工操作,CNC加工具有更高的生产效率和加工精度,减少了人为因素对产品质量的影响,并提高了磨具的一致性和稳定性。
四、模具设计软件在冲压磨具结构设计中的应用随着模具设计软件的不断完善,模具设计过程变得更加简洁快捷。
模具设计软件通过模型的参数化设计,实现了模具设计的自动化、智能化。
设计师只需输入所需规格参数,软件便可以自动生成相应的模具设计,并进行优化和校验。
- 1、下载文档前请自行甄别文档内容的完整性,平台不提供额外的编辑、内容补充、找答案等附加服务。
- 2、"仅部分预览"的文档,不可在线预览部分如存在完整性等问题,可反馈申请退款(可完整预览的文档不适用该条件!)。
- 3、如文档侵犯您的权益,请联系客服反馈,我们会尽快为您处理(人工客服工作时间:9:00-18:30)。
收稿日期226
作者简介吕淑艳(6),女,讲师。
文章编号:100124934(2010)022*******
冲压CAE 分析技术在外板设计中的应用
吕淑艳1,孙朝晖2,王永飞2
(1.包头职业技术学院 材料工程系,内蒙古 包头 014030;2.包头北奔重型汽车有限公司,内蒙古 包头 014032)
摘 要:介绍了冲压CA E 分析技术,并以外板说明冲压CA E 分析技术在零件设计中
的应用。
对冲压成形过程进行模拟分析,尽早发现成形缺陷,从而缩短了模具制造周期,提高了模具质量。
关键词:冲压;CA E ;设计;优化;应用中图分类号:TP391.7 文献标识码:B
Abstract :The s t ampi ng CA E a nalys is t echnology was i nt roduced ,a nd i ts appli cat i on i n pa rts
desi gni ng was ill ust rat ed by t a ki ng t he outsi de pla te as a n exa mpl e.Through si m ulat i ng t he st a mpi ng p rocess ,t he f or mi ng def ects coul d be ea rly det ect ed s o as t o s hort e n t he ma nuf ac 2t uri ng cycl e and i mp rove t he qualit y of t he di e.
K eyw or ds :p unchi ng ;CA E ;desi gn;opti mi zat ion ;applic ati on
0 引言
CA E 是采用计算机辅助求解复杂工程和产
品结构强度、刚度、屈曲稳定性、动力响应、热传导、三维多体接触、弹塑性等力学性能的分析计算以及结构性能的优化设计等问题的1种近似数值分析方法。
目前在世界上主流的冲压CA E 软件[123]主要有:ES I 公司的PA M 2S TAM P 、E TA 公司的D YNA FO RM 和AU TO FORM 公司的A U TO FORM 。
这3款软件各有特色,本文采用的是操作性及易用性较好的PA M 2S TA MP 软件。
1 零件工艺分析
外板是汽车覆盖件中的重要零件(见图1),
与其他零件多处有搭接关系,因此对零件法兰部分的精度要求较高,不允许存在翻边起皱现
象,
否则影响零件间搭接。
图1 外板三维零件图
经过工艺分析,外板左右完全对称,所以模具采用一模二件的拉深方式。
零件的工艺流程为:拉深―修边、冲孔―修边、剖切、冲孔、整
形―翻边、整形。
外板拉深工艺图见图2。
图 外板拉深工艺图
84Die and Mo uld Technology No.22010
:2009070:197-2
2 各参数设定及有限元模型
2.1 材料
板料为DC06普通材料,屈服函数[4]为:
σ2x +σ2y -2r r +1σx σy +22r +1r +1
σ2
xy =σ
-2(1)
式中:σ-
———沿轧制方向的等效应力
x ———板材的轧制方向
y ———垂直于板材的轧制方向
r
———板材的厚向异性系数n ———应变强化指数
板料厚度为1.5mm ,材料参数为n =0.22,
r =2.0,σs =140M Pa ,σb =250MPa 。
2.2 其他参数
毛坯与模具间摩擦因数取0.12;压边速度v 1=2000mm/s ;成形速度v 2=5000mm/s ;单元类型:BT 单元;厚向积分点个数:5;初始网格最小尺寸:12mm ;模具间隙:1.05t (t 为板料厚度)。
2.3 有限元模型
由于该零件一模二件,为了节省计算时间,只对1/2有限元网格进行分析。
有限元模型如图3所示,模具采用倒装式结构,模型中凸模、
凹模、压边圈选为刚性材料。
分析中网格进行自适应划分,为减少计算时间,拉深筋简化为等效模型。
板料采用等向指数强化模型,应力应变关系数学表达式[4]为:
σy =K (εy p +εp )n
(2)
式中:n ———硬化指数
K ———材料常数,K >
图3 外板模具及毛坯的有限元模型
3 分析
3.1 初始分析
通过CA E 分析,调整材料、板料形状、拉深
筋力等工艺参数后得到如下分析结果。
经分析零件上各处都不会破裂。
但由图4
可以看出,外板在翻边成形过程中A 、B 、C 三处
均存在翻边起皱缺陷。
A 、B 两处翻边处于零件的转角或过渡位置,翻边模与翻边面无法同时接触,造成翻边起皱。
可将起皱位置的翻边高度局部降低,由20mm 改为10mm ,从而避免翻边起皱,如图5(a )和(b )所示。
C 处起皱位置处于零件直边部分,但是此处零件翻边高度太高(平均翻边高度32mm )。
针对C 处翻边起皱问
题,对C 处翻边位置的拉深工艺进行了补充优化,将图5(c )中线框所示位置的拉深深度增加,降低翻边高度。
3.2 优化分析
保持所有工艺参数不变,按上述更改方案
修改零件数学模型后重新进行了CA E 分析(见图6和7)。
由图6可以看出,D 、E 两处的变薄量分别为22%和25%,均小于DC06材料的破裂判断标准(变薄量不大于25%)。
说明此零件不破裂。
由图7可以看出,A 、B 、C 三处翻边起皱已
解决。
图 初始分析外板局部翻边过程示意图
9
4模具技术2010.No.2CAE 4
4
结论
图7 优化分析外板局部翻边过程示意图
通过对外板的CA E 分析,修改了原产品
局部结构,不但不会引起设计及制造成本的增加,反而缩短了模具制造周期,提高了模具质量。
上述模拟结果经实际生产验证,零件质量非常好,说明该零件的材料、结构等均满足要求。
参考文献:
[1]罗亚军,杨曦,何丹农,等.板料成形中的有限元
数值模拟技术[J ].金属成形工艺.2000,18(6):
123.
[2]钟志华,李光耀.薄板冲压成型过程的计算机仿
真与应用[M ].北京:机械工业出版社,1998.
[3]林忠钦,李淑慧,于忠奇.车身覆盖件冲压成形仿
真[M ].北京:机械工业出版社,2005.
本刊加入“万方数据———数字化期刊群”的声明
为了实现科技期刊编辑、出版发行工作的电子化,推进科技信息交流的网络化进程,我刊
现已入网“万方数据———数字化期刊群”,所以,向本刊投稿并录用的稿件文章,将一律由编辑部统一纳入“万方数据———数字化期刊群”,进入因特网提供信息服务。
凡有不同意者,请另投它刊。
本刊所付稿酬包含刊物内容上网服务报酬,不再另付。
“万方数据———数字化期刊群”是国家“九五”重点科技攻关项目。
本刊全文内容按照统一格式制作,读者可上网查询浏览本刊内容,并征订本刊。
《模具技术》编辑部
05Die and Mo uld Technology No.22010。