典型的制造工艺程序(精)
典型零件制造工艺

典型零件制造工艺一、前言典型零件制造工艺是机械制造领域中的重要内容,其涉及到材料的选择、加工方式的确定、设备的选择和加工精度等方面。
本文将详细介绍典型零件制造工艺,包括铸造、锻造、冲压、机加工等方面。
二、铸造铸造是指将金属或非金属熔化后倒入模具中,经过凝固后得到所需形状和尺寸的零件。
铸造分为砂型铸造、压力铸造和精密铸造等多种类型。
1. 砂型铸造砂型铸造是指用砂做模具,将熔化的金属倒入模具中,待冷却凝固后取出成型的一种方法。
其步骤包括:(1)设计模具:根据零件图纸设计好模具,并确定好每个部位所使用的材料。
(2)制作芯子:根据零件图纸制作好芯子,并在芯子表面涂上防粘剂。
(3)制作模板:根据设计好的模具尺寸和形状,在木板上切割出相应大小和形状的板块。
(4)制作模具:将制作好的模板放入砂箱中,把芯子放入模板内,再倒入一定数量的砂子,在表面压实。
(5)浇注铸件:在砂型上开孔,将熔化的金属倒入孔口中,待冷却后取出铸件。
2. 压力铸造压力铸造是指将金属液体通过高压喷射到模具中形成零件的一种方法。
其步骤包括:(1)设计模具:根据零件图纸设计好模具,并确定好每个部位所使用的材料。
(2)加热金属:将所需金属加热至液态状态。
(3)注射成型:将液态金属通过高压喷射到模具中,待冷却后取出铸件。
3. 精密铸造精密铸造是指采用特殊工艺,在高温下将金属液体注入陶瓷或合金型芯中进行凝固成型的一种方法。
其步骤包括:(1)设计模具:根据零件图纸设计好模具,并确定好每个部位所使用的材料。
(2)制作芯子:根据零件图纸制作好芯子,并在芯子表面涂上防粘剂。
(3)注射成型:将液态金属通过高压喷射到模具中,待冷却后取出铸件。
三、锻造锻造是指将金属材料加热至一定温度后,通过压力使其发生塑性变形的一种方法。
锻造分为自由锻造、模锻和冷锻等多种类型。
1. 自由锻造自由锻造是指在无模具的情况下,将金属材料加热至一定温度后,通过人工或机械压力进行塑性变形的一种方法。
详细说明过程设备制造的工艺流程
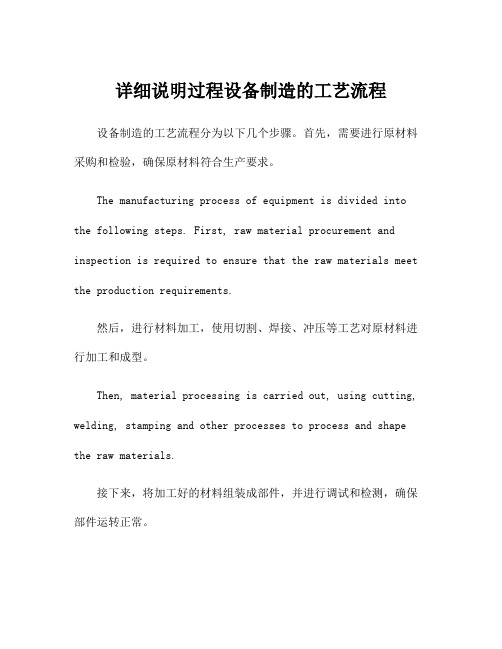
详细说明过程设备制造的工艺流程设备制造的工艺流程分为以下几个步骤。
首先,需要进行原材料采购和检验,确保原材料符合生产要求。
The manufacturing process of equipment is divided into the following steps. First, raw material procurement and inspection is required to ensure that the raw materials meet the production requirements.然后,进行材料加工,使用切割、焊接、冲压等工艺对原材料进行加工和成型。
Then, material processing is carried out, using cutting, welding, stamping and other processes to process and shape the raw materials.接下来,将加工好的材料组装成部件,并进行调试和检测,确保部件运转正常。
Next, the processed materials are assembled into components, and then tested to ensure that the components operate normally.随后,进行总装,将各个部件组装成整机,并进行全面检测和调试。
Subsequently, final assembly is carried out, assembling the various components into a complete machine, followed by comprehensive testing and debugging.最后,需要进行包装和运输,确保设备在运输过程中不受损坏。
Finally, packaging and transportation are carried out to ensure that the equipment is not damaged during transport.在整个制造工艺中,严格执行相关的质量管理标准和流程,保证设备的质量和性能达到要求。
汽车典型零件制造工艺

汽车典型零件制造工艺概述汽车是现代交通工具的重要组成部分,其制造过程涉及众多典型零件的制造工艺。
本文将重点介绍几个汽车典型零件的制造工艺,包括发动机缸体、座椅和刹车盘。
通过了解这些典型零件的制造工艺,我们可以更好地理解汽车的制造过程和技术要求。
发动机缸体制造工艺发动机缸体是汽车发动机的关键部件之一,承受着巨大的压力和高温。
典型的发动机缸体制造工艺通常包括以下几个步骤:1.材料选择:发动机缸体通常采用铸铁或铝合金材料制造。
铸铁具有良好的耐高温、耐磨和强度特性,而铝合金则具有较轻的重量和良好的导热性能。
2.模具制造:根据设计要求,制造专用的模具。
模具通常由两部分组成,上模和下模。
模具的制造需要考虑到零件的形状、尺寸和精度要求。
3.铸造工艺:将选定的材料熔化,然后倒入模具中,待材料凝固后可以得到初步成型的发动机缸体。
铸造工艺中关键的参数包括熔化温度、铸造压力和冷却时间等。
4.补焊与修整:铸造得到的发动机缸体通常需要进行补焊和修整,以去除毛刺、气孔等不良缺陷。
这一步骤需要高水平的焊接和加工技术。
5.精加工:最后,通过加工工艺对发动机缸体进行精加工,包括钻孔、螺纹加工等。
这一步骤要求高精度的加工设备和工艺控制。
座椅制造工艺座椅是汽车舒适性的重要保证,其制造工艺通常包括以下几个步骤:1.骨架制造:座椅骨架是座椅的基础结构,通常由金属材料制成,如钢管或铝合金。
骨架制造需要考虑到座椅的结构强度和稳定性。
2.泡沫填充:在座椅骨架上填充合适的泡沫材料,以提供舒适的坐感和支撑。
泡沫填充需要掌握合适的材料选择和填充技术,以确保座椅的舒适性和耐久性。
3.皮革覆盖:在泡沫填充完成后,需要将皮革或其他合适的材料覆盖在座椅骨架上。
这一步骤需要高水平的缝纫和安装技术,以保证座椅的质量和外观。
4.装配与调试:最后,对座椅进行装配和调试,确保座椅的各项功能正常运作。
这一步骤涉及到座椅的调整机构、加热与通风系统等。
刹车盘制造工艺刹车盘是汽车刹车系统的关键部件之一,负责通过摩擦产生阻力,使车辆减速停止。
晶圆制造工艺流程
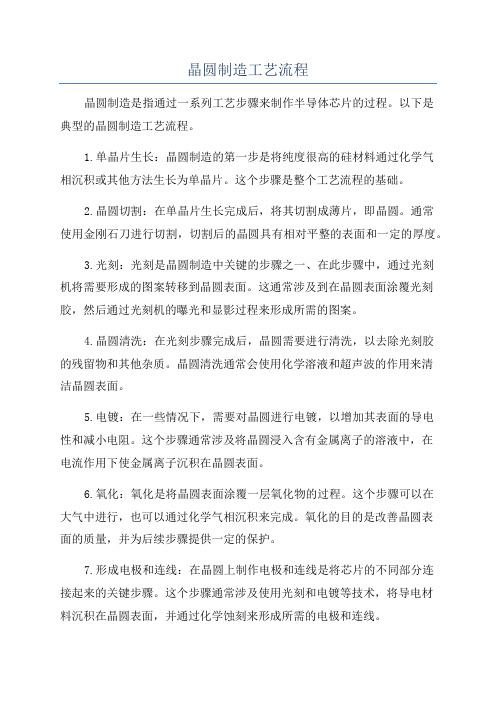
晶圆制造工艺流程晶圆制造是指通过一系列工艺步骤来制作半导体芯片的过程。
以下是典型的晶圆制造工艺流程。
1.单晶片生长:晶圆制造的第一步是将纯度很高的硅材料通过化学气相沉积或其他方法生长为单晶片。
这个步骤是整个工艺流程的基础。
2.晶圆切割:在单晶片生长完成后,将其切割成薄片,即晶圆。
通常使用金刚石刀进行切割,切割后的晶圆具有相对平整的表面和一定的厚度。
3.光刻:光刻是晶圆制造中关键的步骤之一、在此步骤中,通过光刻机将需要形成的图案转移到晶圆表面。
这通常涉及到在晶圆表面涂覆光刻胶,然后通过光刻机的曝光和显影过程来形成所需的图案。
4.晶圆清洗:在光刻步骤完成后,晶圆需要进行清洗,以去除光刻胶的残留物和其他杂质。
晶圆清洗通常会使用化学溶液和超声波的作用来清洁晶圆表面。
5.电镀:在一些情况下,需要对晶圆进行电镀,以增加其表面的导电性和减小电阻。
这个步骤通常涉及将晶圆浸入含有金属离子的溶液中,在电流作用下使金属离子沉积在晶圆表面。
6.氧化:氧化是将晶圆表面涂覆一层氧化物的过程。
这个步骤可以在大气中进行,也可以通过化学气相沉积来完成。
氧化的目的是改善晶圆表面的质量,并为后续步骤提供一定的保护。
7.形成电极和连线:在晶圆上制作电极和连线是将芯片的不同部分连接起来的关键步骤。
这个步骤通常涉及使用光刻和电镀等技术,将导电材料沉积在晶圆表面,并通过化学蚀刻来形成所需的电极和连线。
8.打磨和抛光:在制造晶圆过程中,由于一些原因,晶圆表面可能会有一些不平整和缺陷。
为了修复这些问题,晶圆需要经过打磨和抛光,使其表面更加平整和光滑。
9.测试和封装:在晶圆制造完毕后,需要对芯片进行测试,以确保其正常工作。
测试通常会使用特定的测试设备和测试程序来进行,包括电性能测试、可靠性测试等。
然后,芯片会进行封装,即将其放入塑料或金属封装中,以保护芯片并为其提供适当的引脚。
以上是晶圆制造的典型工艺流程。
当然,实际的晶圆制造可能会因不同应用领域和制造工艺的差异而略有不同。
铜材工艺流程范文
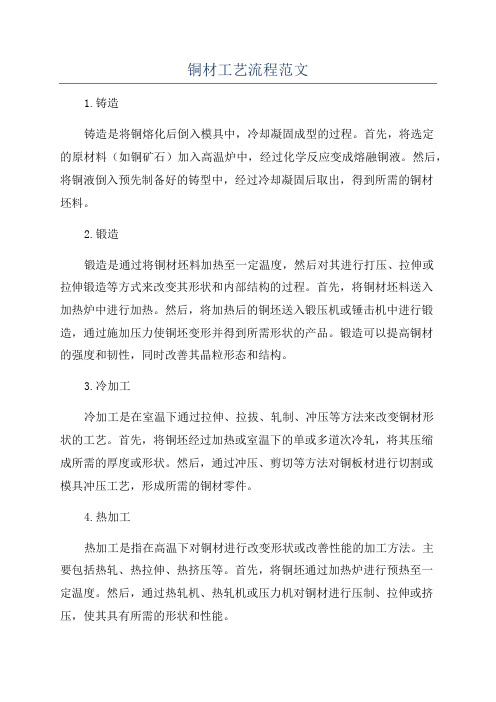
铜材工艺流程范文1.铸造铸造是将铜熔化后倒入模具中,冷却凝固成型的过程。
首先,将选定的原材料(如铜矿石)加入高温炉中,经过化学反应变成熔融铜液。
然后,将铜液倒入预先制备好的铸型中,经过冷却凝固后取出,得到所需的铜材坯料。
2.锻造锻造是通过将铜材坯料加热至一定温度,然后对其进行打压、拉伸或拉伸锻造等方式来改变其形状和内部结构的过程。
首先,将铜材坯料送入加热炉中进行加热。
然后,将加热后的铜坯送入锻压机或锤击机中进行锻造,通过施加压力使铜坯变形并得到所需形状的产品。
锻造可以提高铜材的强度和韧性,同时改善其晶粒形态和结构。
3.冷加工冷加工是在室温下通过拉伸、拉拔、轧制、冲压等方法来改变铜材形状的工艺。
首先,将铜坯经过加热或室温下的单或多道次冷轧,将其压缩成所需的厚度或形状。
然后,通过冲压、剪切等方法对铜板材进行切割或模具冲压工艺,形成所需的铜材零件。
4.热加工热加工是指在高温下对铜材进行改变形状或改善性能的加工方法。
主要包括热轧、热拉伸、热挤压等。
首先,将铜坯通过加热炉进行预热至一定温度。
然后,通过热轧机、热轧机或压力机对铜材进行压制、拉伸或挤压,使其具有所需的形状和性能。
5.精密加工精密加工是为了提高铜材的几何精度和表面质量,通过铣削、车削、钻孔、打磨、抛光等方法对铜材进行加工。
通过旋转工具在铜材表面进行切削或去除材料,使其达到所需的尺寸和形状要求。
精密加工可以进一步提高铜材的精度和表面质量。
6.表面处理表面处理是为了改善铜材的表面性能和外观效果,常用的方法包括电镀、喷漆、氧化和镀膜等。
通过在铜材表面加上一层保护性膜层或改变其颜色、光泽和外观,提高其抗腐蚀能力和装饰性。
7.检验和质量控制在铜材工艺流程中,对加工后的铜材进行检验和质量控制非常重要。
通过检验手段如化学成分分析、物理性能测试、尺寸测量、外观检验等,对铜材进行质量检验,确保符合产品要求。
以上是一个典型的铜材工艺流程,根据具体产品的不同和生产需求,会有所差异。
产品生产工艺流程(3篇)
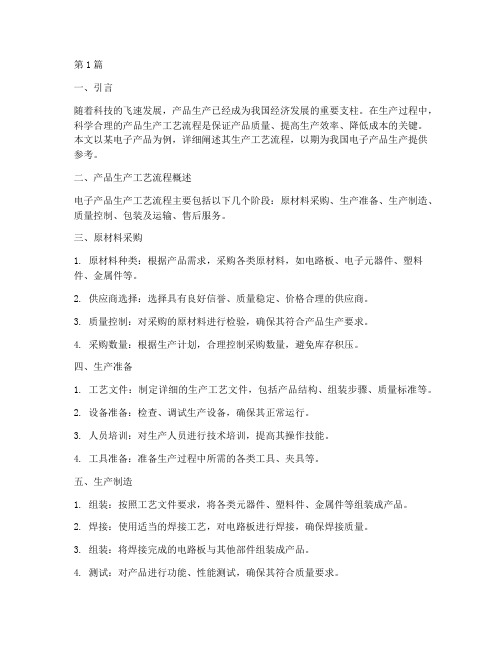
第1篇一、引言随着科技的飞速发展,产品生产已经成为我国经济发展的重要支柱。
在生产过程中,科学合理的产品生产工艺流程是保证产品质量、提高生产效率、降低成本的关键。
本文以某电子产品为例,详细阐述其生产工艺流程,以期为我国电子产品生产提供参考。
二、产品生产工艺流程概述电子产品生产工艺流程主要包括以下几个阶段:原材料采购、生产准备、生产制造、质量控制、包装及运输、售后服务。
三、原材料采购1. 原材料种类:根据产品需求,采购各类原材料,如电路板、电子元器件、塑料件、金属件等。
2. 供应商选择:选择具有良好信誉、质量稳定、价格合理的供应商。
3. 质量控制:对采购的原材料进行检验,确保其符合产品生产要求。
4. 采购数量:根据生产计划,合理控制采购数量,避免库存积压。
四、生产准备1. 工艺文件:制定详细的生产工艺文件,包括产品结构、组装步骤、质量标准等。
2. 设备准备:检查、调试生产设备,确保其正常运行。
3. 人员培训:对生产人员进行技术培训,提高其操作技能。
4. 工具准备:准备生产过程中所需的各类工具、夹具等。
五、生产制造1. 组装:按照工艺文件要求,将各类元器件、塑料件、金属件等组装成产品。
2. 焊接:使用适当的焊接工艺,对电路板进行焊接,确保焊接质量。
3. 组装:将焊接完成的电路板与其他部件组装成产品。
4. 测试:对产品进行功能、性能测试,确保其符合质量要求。
5. 后处理:对产品进行外观处理、防潮处理等。
六、质量控制1. 质量检验:在生产过程中,对每个环节的产品进行检验,确保其质量。
2. 质量控制点:设置关键质量控制点,如焊接、组装、测试等环节。
3. 不良品处理:对不合格产品进行返工、报废或修复。
4. 质量改进:根据质量反馈,对生产工艺进行改进,提高产品质量。
七、包装及运输1. 包装:按照产品特点,选用合适的包装材料,确保产品在运输过程中不受损坏。
2. 运输:选择可靠的物流公司,确保产品安全、及时送达客户。
典型零件机械加工工艺过程
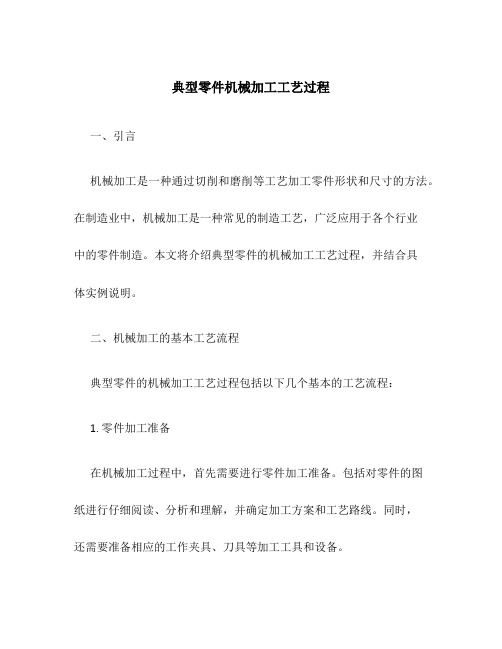
典型零件机械加工工艺过程一、引言机械加工是一种通过切削和磨削等工艺加工零件形状和尺寸的方法。
在制造业中,机械加工是一种常见的制造工艺,广泛应用于各个行业中的零件制造。
本文将介绍典型零件的机械加工工艺过程,并结合具体实例说明。
二、机械加工的基本工艺流程典型零件的机械加工工艺过程包括以下几个基本的工艺流程:1. 零件加工准备在机械加工过程中,首先需要进行零件加工准备。
包括对零件的图纸进行仔细阅读、分析和理解,并确定加工方案和工艺路线。
同时,还需要准备相应的工作夹具、刀具等加工工具和设备。
2. 零件装夹在机械加工过程中,零件装夹是一个非常关键的环节。
零件装夹的质量直接影响到加工的精度和效率。
根据零件的形状和结构,选择合适的夹具,并进行正确的装夹操作。
3. 加工工艺选择根据零件的特点和要求,选择合适的加工工艺,包括车削、铣削、钻削、刨削等。
针对不同的零件形状和材料特性,确定合适的刀具和切削参数,并进行加工工艺的选择。
4. 机床调试和加工在进行实际加工之前,需要进行机床的调试和测试。
确保机床的运转正常,并调整好各项加工参数。
然后,根据加工工艺选择,进行具体的加工操作,包括刀具路径的设定、加工速度的调整等。
5. 加工检测和调整在零件加工过程中,需要进行加工质量的检测和调整。
通过使用各种测量工具和设备,对加工后的零件进行尺寸和形状的检测。
如果不符合要求,需要及时进行调整和修正,以确保零件的加工质量。
6. 表面处理和组装完成零件的机械加工之后,还需要进行表面处理和组装。
包括去除零件表面的毛刺和氧化物,并进行必要的润滑和防护处理。
然后,根据具体的装配要求,对零件进行组装和调试。
三、案例分析为了更好地理解典型零件的机械加工工艺过程,我们以一款小型螺丝刀为例,进行具体的案例分析。
1.加工准备:仔细阅读零件图纸,了解零件的形状和加工要求。
根据图纸上的标注和尺寸要求,确定加工方案和工艺路线。
准备相应的夹具和刀具。
2.装夹:选择合适的夹具进行零件的装夹。
工艺流程短文
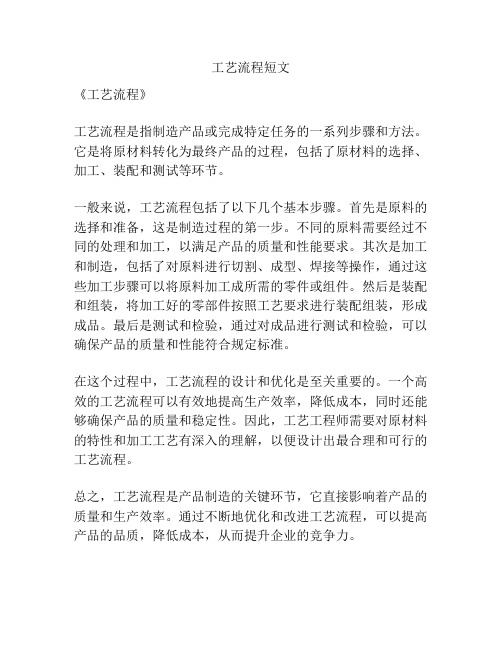
工艺流程短文
《工艺流程》
工艺流程是指制造产品或完成特定任务的一系列步骤和方法。
它是将原材料转化为最终产品的过程,包括了原材料的选择、加工、装配和测试等环节。
一般来说,工艺流程包括了以下几个基本步骤。
首先是原料的选择和准备,这是制造过程的第一步。
不同的原料需要经过不同的处理和加工,以满足产品的质量和性能要求。
其次是加工和制造,包括了对原料进行切割、成型、焊接等操作,通过这些加工步骤可以将原料加工成所需的零件或组件。
然后是装配和组装,将加工好的零部件按照工艺要求进行装配组装,形成成品。
最后是测试和检验,通过对成品进行测试和检验,可以确保产品的质量和性能符合规定标准。
在这个过程中,工艺流程的设计和优化是至关重要的。
一个高效的工艺流程可以有效地提高生产效率,降低成本,同时还能够确保产品的质量和稳定性。
因此,工艺工程师需要对原材料的特性和加工工艺有深入的理解,以便设计出最合理和可行的工艺流程。
总之,工艺流程是产品制造的关键环节,它直接影响着产品的质量和生产效率。
通过不断地优化和改进工艺流程,可以提高产品的品质,降低成本,从而提升企业的竞争力。
工艺流程范本

工艺流程范本
《工艺流程范本》
工艺流程范本是指在特定的工业生产领域中,将生产过程中的各项技术、技巧和步骤进行统一规范和总结,形成标准化的生产流程文档,以供生产人员参考和执行的指南。
它在工业生产中发挥着重要的作用,不仅可以提高产品的生产效率和质量,还能够减少生产过程中的变动和浪费。
工艺流程范本的编制主要包括以下几个步骤:
首先,对生产工艺进行全面的调研和分析,包括原材料的选择、加工工艺、生产设备的使用等方面。
通过对生产过程的深入了解,可以确定最佳的生产流程,并且为制定工艺流程范本提供基础数据。
其次,根据调研结果,编制工艺流程图,详细描述生产过程中的每一个步骤和所需的技术参数,标示所需的工具、设备和原材料等关键要素。
工艺流程图应当简明直观,以便生产员工容易理解和执行。
接着,制定标准化的操作规程,包括各项生产技术要求、作业程序、安全注意事项等内容。
操作规程应当具体详细,既要求人员执行规范,又要求生产过程的可操作性。
最后,对工艺流程范本进行审核和修订。
在生产实践中,随着生产技术和工艺水平的不断提高,工艺流程范本也需要不断修
订和更新,以保证其与实际生产过程的匹配性。
通过以上步骤的编制,工艺流程范本能够成为生产过程中不可或缺的重要文档,它不仅可以指导生产员工进行规范化操作,更可以为企业提供标准化的生产管理手段,提高生产效率,降低生产成本,确保产品质量,为企业的持续发展提供可靠的保障。
最简易的半导体制造工艺流程

最简易的半导体制造⼯艺流程半导体制造⼯艺流程N型硅:掺⼊V族元素--磷P、砷As、锑SbP型硅:掺⼊III族元素—镓Ga、硼BPN结:半导体元件制造过程可分为前段(FrontEnd)制程晶圆处理制程(WaferFabrication;简称WaferFab)、晶圆针测制程(WaferProbe);後段(BackEnd)构装(Packaging)、测试制程(InitialTestandFinalTest)⼀、晶圆处理制程晶圆处理制程之主要⼯作为在矽晶圆上制作电路与电⼦元件(如电晶体、电容体、逻辑闸等),为上述各制程中所需技术最复杂且资⾦投⼊最多的过程,以微处理器(Microprocessor)为例,其所需处理步骤可达数百道,⽽其所需加⼯机台先进且昂贵,动辄数千万⼀台,其所需制造环境为为⼀温度、湿度与含尘(Particle)均需控制的⽆尘室(Clean-Room),虽然详细的处理程序是随著产品种类与所使⽤的技术有关;不过其基本处理步骤通常是晶圆先经过适当的清洗(Cleaning)之後,接著进⾏氧化(Oxidation)及沈积,最後进⾏微影、蚀刻及离⼦植⼊等反覆步骤,以完成晶圆上电路的加⼯与制作。
⼆、晶圆针测制程经过WaferFab之制程後,晶圆上即形成⼀格格的⼩格,我们称之为晶⽅或是晶粒(Die),在⼀般情形下,同⼀⽚晶圆上皆制作相同的晶⽚,但是也有可能在同⼀⽚晶圆上制作不同规格的产品;这些晶圆必须通过晶⽚允收测试,晶粒将会⼀⼀经过针测(Probe)仪器以测试其电⽓特性,⽽不合格的的晶粒将会被标上记号(InkDot),此程序即称之为晶圆针测制程(WaferProbe)。
然後晶圆将依晶粒为单位分割成⼀粒粒独⽴的晶粒三、IC构装制程IC構裝製程(Packaging):利⽤塑膠或陶瓷包裝晶粒與配線以成積體電路⽬的:是為了製造出所⽣產的電路的保護層,避免電路受到機械性刮傷或是⾼溫破壞。
半导体制造⼯艺分类半导体制造⼯艺分类⼀双极型IC的基本制造⼯艺:A在元器件间要做电隔离区(PN结隔离、全介质隔离及PN结介质混合隔离)ECL(不掺⾦)(⾮饱和型)、TTL/DTL(饱和型)、STTL(饱和型)B在元器件间⾃然隔离I2L(饱和型)半导体制造⼯艺分类⼆MOSIC的基本制造⼯艺:根据栅⼯艺分类A铝栅⼯艺B硅栅⼯艺其他分类1、(根据沟道)PMOS、NMOS、CMOS2、(根据负载元件)E/R、E/E、E/D半导体制造⼯艺分类三Bi-CMOS⼯艺:A以CMOS⼯艺为基础P阱N阱B以双极型⼯艺为基础双极型集成电路和MOS集成电路优缺点半导体制造环境要求主要污染源:微尘颗粒、中⾦属离⼦、有机物残留物和钠离⼦等轻⾦属例⼦。
中密度纤维板制造工艺曲线图(精)

中密度纤维板制造工艺曲线图如下:↗污水处理削片→热磨→干燥→铺装→热压→锯边→砂光→板胚分选→打包出库↑施胶为了使员工能够更好的对中纤板的生产要有足够的了解,在此对上面所讲的工艺制造作详细的介绍:一、1、削片:它是整个板生产中原料的制造车间,主要将松杂木材削成符合生产规格的木片,以备热为纤维分离提供更好的条件。
2、关键词:原料种类、木片规格、松杂木配比。
①原料种类:中纤板生产所用原料的植物纤维,其纤维素含量一般在30%以上,本公司所受用的是木质纤维,它主要包括采伐剩余物(如:小径材、板桠材、火烧材),造材剩余物(截头),加上剩余物(边皮、木芯、碎单板及其他下脚料),以及回收的废旧木材等,也可直接用林区或木材加工企业生产的木片。
②木片规格:木片大小合格、均匀、平整、木片规格一般为:长16-30mm,宽15-25mm,厚3-5mm,我们所采用的削片机类型是鼓式削片机,为了使木片适合生产,以便防止进料螺旋堵,电耗高等,一方面要适时调整飞刀与底刀的间隙,一般调整的间隙为0.8-1.0mm。
另一方面要加强对原料含水率率的适时控制,尽量保证不低于40%,从而使木片整齐均匀,合格率高,碎悄少,也提高刀具使用寿命。
③松杂木配比:因为中纤板的强度取决于纤维的交织性能和结合时的工艺条件,关于纤维形态,在这简要介绍如下:a纤维:它一般分为纤维细胞(俗称纤维)和杂细胞,其中杂细胞的含量多与少决定了纤维质量的好与差,一般而言,针叶材杂细胞含量最低,而阔叶材次之,除了含量影响质量以外,纤维形态、化学组成以及原料的机械加工性能等,相对而言要考虑板材的强度要注意以下几点①长度大,长宽比大的纤维具有较好的结合性能,②细胞壁较薄,壁腔比较小的纤维在纤维分离和热压过程中易压扁,成为带状,柔软性较好,具有较大的接触面积,③长短、粗细纤维的合格搭配可以填补纤维之间的空隙,增大接触面,提高产品密度和结合强度,关于化学组成以及原料的机械加工性能这里不加多述,以下表针材材与阔叶材。
工艺流程我那

工艺流程我那
《工艺流程简介》
工艺流程是指完成一项工艺过程中所需要经历的步骤和技术操作。
在工艺生产过程中,工艺流程起着至关重要的作用,它的好坏直接关系到产品的质量和产量。
以下是一个典型的工艺流程简介:
1.原材料准备
首先,需要准备好所需的原材料,这些原材料可能是金属、塑料、玻璃或者其他物质。
原材料的选择和质量直接影响到产品的最终质量。
2.加工制造
一般来说,在工艺流程中最重要的一环是加工制造。
根据不同的产品和要求,可能需要进行钣金加工、机械加工、铸造等一系列工艺过程。
在这个阶段需要严格控制工艺参数,确保产品的精度和质量。
3.组装
对于一些复杂的产品,需要进行多部件的组装工艺。
在组装的过程中,需要严格按照图纸和工艺要求进行操作,确保所有部件的配合和功能。
4.检测与质量控制
为了确保产品的质量,检测与质量控制是不可缺少的一环。
通过各种检测手段和工艺控制手段,可以及时发现和解决工艺中
的问题,从而确保产品的质量和稳定性。
5.包装与出厂
最后,产品需要进行包装,并最终出厂。
包装需要保护产品不受损坏,并且要便于运输和存储。
总之,工艺流程是一个综合性的过程,需要各个环节的密切配合和严格控制,才能保证产品的质量和生产效率。
只有构建完善的工艺流程,才能满足市场对产品的质量和效率要求。
车间生产工艺流程图
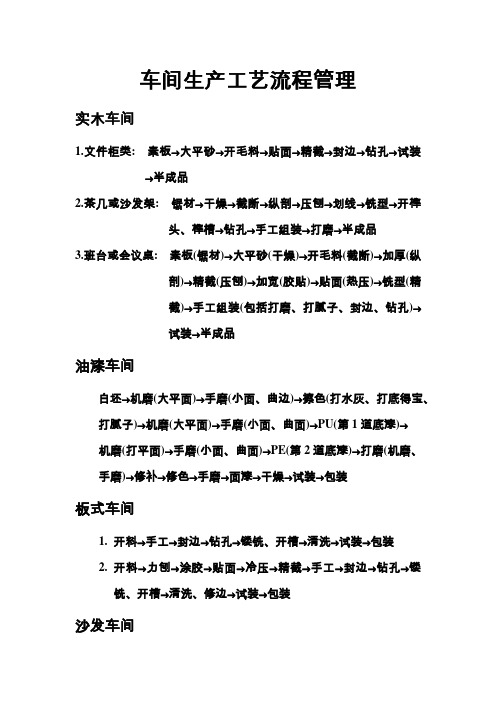
车间生产工艺流程管理实木车间1.文件柜类: 素板→大平砂→开毛料→贴面→精截→封边→钻孔→试装→半成品2.茶几或沙发架: 锯材→干燥→截断→纵剖→压刨→划线→铣型→开榫头、榫槽→钻孔→手工组装→打磨→半成品3.班台或会议桌: 素板(锯材)→大平砂(干燥)→开毛料(截断)→加厚(纵剖)→精截(压刨)→加宽(胶贴)→贴面(热压)→铣型(精截)→手工组装(包括打磨、打腻子、封边、钻孔)→试装→半成品油漆车间白坯→机磨(大平面)→手磨(小面、曲边)→擦色(打水灰、打底得宝、打腻子)→机磨(大平面)→手磨(小面、曲面)→PU(第1道底漆)→机磨(打平面)→手磨(小面、曲面)→PE(第2道底漆)→打磨(机磨、手磨)→修补→修色→手磨→面漆→干燥→试装→包装板式车间1.开料→手工→封边→钻孔→镂铣、开槽→清洗→试装→包装2.开料→力刨→涂胶→贴面→冷压→精截→手工→封边→钻孔→镂铣、开槽→清洗、修边→试装→包装沙发车间裁皮、开棉→打底(电车)→粘棉→扪皮(组装)→检验→包装转椅车间裁布(皮)、开棉→车位、粘绵→扪皮→组装→检验→包装屏风车间开料(铝材)→喷胶→贴绵→扪布(打钉)→组装→试装→包装五金车间1.椅架类: 开料→弯管→钻孔、攻牙→焊接→打磨→抛光→喷涂2.钢板类: 开料→冲板(圆孔、圆凸、方孔、方凸、小梅花、大梅花、网孔、菱凸)→折弯→焊接→打磨→喷涂3.台架类: 开料→冲弯→钻孔、攻牙→焊接→打磨→抛光→喷涂4.电镀类: 开料→开皮→冲弯→焊接→打磨→精抛→电镀总:开料(裁剪、剪板)→制造(冲床、弯管、钻孔、攻牙)→成型(焊接、打磨、抛光)→喷涂、电镀喷涂车间清洗→凉干→打磨→喷漆(喷粉)→电烤→包装。
产品加工工艺流程

产品加工工艺流程
《产品加工工艺流程》
产品加工工艺流程是指将原材料经过一系列加工工艺流程,最终制成具有一定形状、尺寸和功能的成品的过程。
在现代工业生产中,产品加工工艺流程扮演着至关重要的角色,它直接影响着产品的质量、成本和生产效率。
下面将以汽车发动机零部件的加工工艺流程为例,来说明产品加工的全过程。
首先,原材料准备。
将原材料按照设计要求进行采购,然后进行原材料的检验和筛选,确保其符合加工要求。
其次,加工工艺规划。
根据产品设计图纸和要求,制定相应的加工工艺流程,包括加工工序顺序、加工精度要求、工装夹具设计等。
然后,进行粗加工。
采用铣削、车削、钻孔等机械加工工艺,将原材料进行初步的成形。
接下来是精加工。
通过磨削、铣削、切割等高精度加工工艺,将零部件进行精细加工,保证其尺寸精度和表面光洁度。
之后,是热处理。
采用火焰淬火、渗碳、回火等热处理工艺,提高零部件的硬度、耐磨性和强度。
最后,进行表面处理。
包括喷涂、镀层、抛光等工艺,提高零部件的外观质量和防腐蚀能力。
通过以上工艺流程,原材料逐步转化为成品零部件,最终用于汽车发动机的装配。
产品加工工艺流程不仅需要精湛的技术和经验,还需要不断创新,以提高生产效率和产品质量,从而满足市场需求。
典型工艺流程
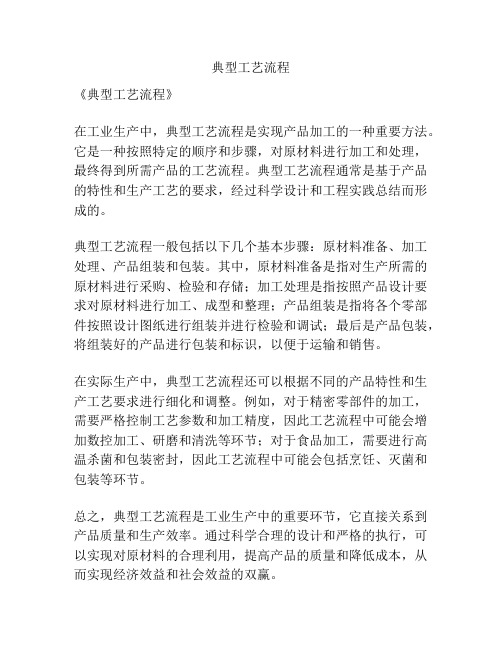
典型工艺流程
《典型工艺流程》
在工业生产中,典型工艺流程是实现产品加工的一种重要方法。
它是一种按照特定的顺序和步骤,对原材料进行加工和处理,最终得到所需产品的工艺流程。
典型工艺流程通常是基于产品的特性和生产工艺的要求,经过科学设计和工程实践总结而形成的。
典型工艺流程一般包括以下几个基本步骤:原材料准备、加工处理、产品组装和包装。
其中,原材料准备是指对生产所需的原材料进行采购、检验和存储;加工处理是指按照产品设计要求对原材料进行加工、成型和整理;产品组装是指将各个零部件按照设计图纸进行组装并进行检验和调试;最后是产品包装,将组装好的产品进行包装和标识,以便于运输和销售。
在实际生产中,典型工艺流程还可以根据不同的产品特性和生产工艺要求进行细化和调整。
例如,对于精密零部件的加工,需要严格控制工艺参数和加工精度,因此工艺流程中可能会增加数控加工、研磨和清洗等环节;对于食品加工,需要进行高温杀菌和包装密封,因此工艺流程中可能会包括烹饪、灭菌和包装等环节。
总之,典型工艺流程是工业生产中的重要环节,它直接关系到产品质量和生产效率。
通过科学合理的设计和严格的执行,可以实现对原材料的合理利用,提高产品的质量和降低成本,从而实现经济效益和社会效益的双赢。
圆钢生产工艺流程

圆钢生产工艺流程
圆钢的生产工艺流程主要包括以下步骤:
1. 原料准备:原料是指未加工的钢材坯料,一般为连铸坯或钢锭。
原料经过检验合格后,进行预处理,包括除锈、去氧化皮、压坯等。
2. 加热:将原料送入预热炉进行加热,提高钢材的塑性和可塑变形能力,以便后续的轧制工艺。
3. 热轧工艺:将预热后的原料经过一系列的轧制过程,使其成为需要的规格和形状。
热轧过程一般包括粗轧、精轧、整形轧制等,通过调整轧制压力和温度,使圆钢在连续的轧制机组上通过变形实现形状和尺寸的准确控制。
4. 探伤工艺:热轧完成后,进行探伤工艺,检测圆钢的内部缺陷和表面质量,以确保产品的合格率。
常用的探伤方法包括超声波探伤、磁粉探伤、涡流探伤等。
5. 修边处理:修边是为了去除圆钢表面的不均匀和缺陷,以提高圆钢的表面质量。
修边主要通过修边机进行。
这些步骤完成后,即得到成品圆钢。
更多具体操作可咨询专业生产人员获取帮助。
金工车间工艺流程

金工车间工艺流程引言概述金工车间是生产金属制品的重要环节,其工艺流程直接影响产品质量和生产效率。
本文将详细介绍金工车间的工艺流程,包括原材料准备、加工工艺、表面处理、装配和质量检验等内容。
一、原材料准备1.1 选择合适的金属材料:根据产品要求和客户需求,选择适合的金属材料,如不锈钢、铝合金等。
1.2 切割和预处理:将原材料按照设计要求进行切割和预处理,确保尺寸和形状符合要求。
1.3 清洗和除锈:对原材料进行清洗和除锈处理,确保表面光洁度和质量。
二、加工工艺2.1 冲压加工:使用冲床或冲压机对原材料进行冲压加工,制作出产品的基本形状。
2.2 弯曲和成型:通过弯曲机或成型机对原材料进行弯曲和成型,使其符合设计要求。
2.3 焊接和组装:将各个部件进行焊接和组装,形成成品。
三、表面处理3.1 打磨和抛光:对产品表面进行打磨和抛光处理,提高表面光洁度和质感。
3.2 喷涂和镀层:根据客户要求,对产品进行喷涂或镀层处理,增加产品的耐腐蚀性和美观度。
3.3 氧化和阳极处理:对铝合金产品进行氧化或阳极处理,增强产品的硬度和耐磨性。
四、装配4.1 零部件装配:将各个部件按照设计要求进行装配,确保产品结构完整和功能正常。
4.2 调试和检测:对装配好的产品进行调试和检测,确保产品质量和性能达标。
4.3 包装和出厂:对合格的产品进行包装和出厂,保护产品不受损坏。
五、质量检验5.1 外观检查:对产品外观进行检查,确保表面光洁度和无明显缺陷。
5.2 尺寸检验:对产品尺寸进行检验,确保尺寸精度符合设计要求。
5.3 功能测试:对产品功能进行测试,确保产品性能正常。
结论金工车间的工艺流程包括原材料准备、加工工艺、表面处理、装配和质量检验等环节,每个环节都至关重要。
只有严格按照工艺流程操作,才能保证产品质量和生产效率。
希望本文的介绍能帮助读者更好地了解金工车间的工艺流程。
- 1、下载文档前请自行甄别文档内容的完整性,平台不提供额外的编辑、内容补充、找答案等附加服务。
- 2、"仅部分预览"的文档,不可在线预览部分如存在完整性等问题,可反馈申请退款(可完整预览的文档不适用该条件!)。
- 3、如文档侵犯您的权益,请联系客服反馈,我们会尽快为您处理(人工客服工作时间:9:00-18:30)。
典型的制造工艺程序一、序言压力容器根据其用途和结构分类是多种多样、五花八门的,难以制定一个统一的普通适用的制造工艺规程,但是根据常用的压力容器,从制造角度仍可分为下列几大类:1、容器类,包括贮槽、贮罐、快开容器等2、反应器类3、塔器类4、换热器类,包括余热锅炉、空气冷却器、制冷设备等;5、超高压容器类,包括超高反应器、临界箤取器、深海探测容器等。
要认真研究各类压力容器的制造过程和检验程序,必须掌握各类设备的具体结构、材料和制造厂的工艺装备、传统习惯等资料进行具体的分析,在此无法详细一一描述。
本教材仅通过几个具有代表性的压力容器实例,较原则地叙述整个制造过程和检验内容,以期对压力容器的制造和检验的一般的了解,并通过其学习而举一反三,逐步牚握各类受压设备基本制造工艺过程和检验程序。
二、压力容器一般的制造工作程序设计→图纸审查→编制材料采购说明书→编制制造工艺文件(包括焊接工艺评定说明书和热处理及特殊工艺评定说明书、焊工或特种工艺操作工技能考试文件→编制生产计划和检验、试验、发运计划→工装准备→材料采购和验收→焊接工艺评定和特种工艺评定→编制焊接工艺指导书→焊工和特种工艺操作工技能考试→下料→成型→零部件加工→检验→零部件组对、焊接→检测→热处理(如果需要的话→检测检验(包括无损检测→总装→检验→压力试验→气密试验或泄漏检测→清洗、吹干→总检→油柒包装→发运→售后服务。
三、加氢反应器的制造和检验(以板焊式为例1、加氢反应器是一种典型的受压反应器,它的制造过程和检验方法几乎包括了所有受压容器的全部内容。
通过了解其制造过程和检验方法基本上就掌握了所有压力容器的制造工艺和检验方法。
2、制造过程及检验内容见图1。
3、制造和检验的详细说明3.1容器封头通常采用4片碟瓣并以子午线(经线焊缝组焊在一起,每一片球瓣都是采用水压机高温热压成型的。
然后进行正火和回火热处理。
坯料通常是由热轧装态供货的。
每一片坯料都应留有足够的余量,允许热压以后,正火后的取样,以及修复拼焊坡口。
每一个封头都有一件用锻件制成的具有自身开孔补强的大接管。
接管与封头采用双面焊缝连接,而封头的中心位置即顶部为一球罐。
球罐与球瓣组成的“桔皮”部分直接焊在一起。
考虑到封头切线处的厚度与筒节之间的厚度有差别,因此必须按规范的要求进行削边。
(详见GB150、附录D或ASMEⅧ.div.1 Fig UW-13.1 Heads Attached to Shells(cont’d (see Table UW-12 for limitationsP120要求封头的中心线与筒节的中心线之差≤1/2(tn-ts,tn为较厚厚度,ts为较薄厚度。
削边长度≥3Y。
Y为较厚者与较薄都连接的单面厚度差(取较大者。
3.2 上、下封头的制造和检验程序(假设材料21/2Cr-1Mo(1)板材验证和钢厂试验报告审查(轧制状态板,检查钢厂试板经受最大温度和最小温度下的模拟热处理后的机械性能,包括冲击韧性;如果需要,制造厂要进行复验;(2)球片坯料划线。
应留有适当裕量,以便切取热压后正火热处理的机械性能试料;(3)预热≥200℃,手工或数控自动切割机上氢气切割下料;(4)进炉加热到920~940℃,保温时间按每25mm(寸)30分钟计算;(5)-(6)在水压机上热压成形,并在空气中冷却到200℃左右,再送进炉子内进行正火热处理920±20℃、保温30分钟×每英寸(25mm),然后在静止空气中冷却;(7)用球壳样板检查成形后的球瓣曲率半径;(8)送沪进行回火热处理。
加热到630~650℃,保温时间按每英寸(25mm)30分钟计算。
如果需要的话,为了获得正确的形状,可在压力下保温。
加热速率应在56℃/小量,地静止的空气中冷却;(9)最后尺寸检查;(10)-(11)划出多余的尺寸线,并在预热200℃切割;将一块试板送到试样加工车间,按标准要求进行加工;另一块作为拼焊试板;(12)材料试样送到实验室进行检查。
材料试板将要经受模拟热处理(热处理数按容器制造厂的要求),机械性能试验结果必须符合球瓣进炉消除应力前的性能;(13)准备封头拼焊试板。
由封头压制瓜片经热处理后留下的另一块试板制成;(14)装配球形封头瓜片+焊接产品试板(上、下封头同样焊接工艺和焊接材料可作一块);(15)预热所有装配焊接用的挡块点,加热温度250℃(如果采用普通碳钢挡块,则必须采用预堆焊);(16)检查焊接工艺和产品冲击试验;(17)预热250℃并在外坡口焊接;焊接可以在变位器上采用自动多道埋弧焊工艺,或取决于工艺过程,采用手工焊(SMAW);(18)-(19)背面用风铲机挑焊根或盘到砂轮打磨焊根。
进行根部磁粉检测(MT),最好采用150℃以下的热态干粉检测,(见JB4730.4—xxxx. 4.5干法);(20)预热250℃并进行反面焊接。
重复按(15)-(19)的操作完成封头的所有瓜片的组焊工作;(21)中间热处理。
温度在620~600℃,保温时间T/50h(尺寸检查和可能校正在200℃);(22)超声波检测(UT)和修补(如果需要的话)。
修补后仍应预热250~300℃,保温8小时,再冷却到室温。
在重要的修补(可某些修补长度超过总长的10%,应进行中间热处理600~620℃×T/50h;超声波检测应在正反两面进行。
(JB4730.3—xxxx).(23)x-射线检测(RT),可采有电子回旋加速器或Co60并带特殊屏蔽物;(24)-(25)内表面的喷砂和打磨(如需要的话),宏观检查(VT);(26)加热150℃,内表面进行自动埋弧带极堆焊。
堆焊两层,正常厚度应为6.4mm,并且在距离表面3.2mm的堆焊层内的化学成份分析必须满足要求;第一层堆焊材料为309L,第二层为347L;(27)-(28)内表面喷砂或用不锈钢丝刷刷并进行表面100%渗透检测(PT);(见JB4730.5—xxxx)(29)超声波检测堆焊层厚度和抽查10%-30%堆焊层交界处的接合状况;(30)采用机械的和电子的两种方法检测堆焊层厚度,并进行堆焊焊层化学成份分析;(31)按照Delong图进行铁素体含量检查(最小4%,最大10%);(32)中心接管焊接坡口机械加工,在搪床或立车上进行;(33)-(34)侧向开孔划线并氢气切割(应预热),开孔位置检验;(35)打磨或机械加工侧向坡口;(36)沿开孔周围160mm范围内进行超声波检测(UT)(JB4730.3—xxxx);(37)焊接坡口表面进行磁粉检测,采用直流磁化圆棒电极(MT)(见JB4730.4—xxxx);(38)装配接管(注意按(15)的要求);(39)检查接管的位置;(40)检查焊接工艺(手工焊或自动焊);(41)预热到250℃,焊接外坡口焊缝。
采用手工焊,但也可以采用自动氩弧焊或埋弧焊工艺;(42)-(43)焊缝背后用风铲铲焊根或打磨焊根,并进行热法磁粉检测;(44)预热到250℃进行反面焊接;(45)中间热处理600~620℃,保温T/50h;(46)超声波检测和修补(如果需要的话);(47)x射线检测。
采用直线回旋加速器或Co60;(48)接管与封头之间堆焊层的“连接”。
采用手工堆焊,最少两道,第一道309L,第二道或以后各道采用347L;(49)“连接”堆焊层化学成份分析;(50)铁素体检测(最低4%,最高10%);(51)采有机械的和电子的两种方法测定“连接”堆焊层厚度;(52)渗透检测“连接”堆焊层表面;(53)重复操作(48)-(52)完成所有接管堆焊层与封头堆焊层的“连接”堆焊层工作;(54)在立车上加工封头与筒节组焊的环缝坡口;(55)采用直流磁化圆棒电极对环缝坡口进行磁粉检测(MT)(JB4730-xxxx);(56)综合检验。
汇总所有检验和试验报告。
将上、下封头部件送交下道工序,与筒节组合。
3.3筒节一台加氢反应器将由许多筒节组成。
每一个筒节都有一条纵向焊缝。
每一块板料应有超出所需周长预卷直边余量,各长250mm。
这些附加的直边长度可以作为材料试板、焊接工艺评定试板和焊工考试试板,以及产品焊接试板等。
冷卷筒节可用正火状态供货板,热卷筒节则需热轧状态供货板。
每台反应器(在正火和回火之后)将从一个筒节中抽取一个焊接试板作母材和焊缝金属的机械性能试验。
这件试样应与筒体一样经受机似的热处理,以预测容器的制造效果。
制造过程如下:3.3.1单件壳体筒节的制作(1)板材验证+钢板试验报告审查。
必要时应进行复验;(2)在热态下预压头(在卷板机或水压机下进行)。
如果卷板机或水压机能力足够,则可冷预弯头(如有可冷弯160mm卷板机时);(3)-(4)划线,氢气切割机和机械加工去除直边;(5)纵向焊缝坡口表面磁粉检测(JB4730.4-xxxx);(6)-(7)温卷(600℃)、热卷(920℃)或冷卷成形,用样板检查曲率半径;(8)装配产品焊接试板。
在纵焊缝延长部位,数量按技术规范;(9)装配用焊接挡块的所有焊点应预热到250℃。
(如果用碳钢挡块,必须采取过度堆焊,堆焊金属应为2 1/2Cr-1Mo);(10)检查焊接工艺。
检查焊丝和焊剂,检查焊接参数;(11)纵缝预热达到250℃后焊接。
采用自动多层埋弧焊工艺(最好采用窄间隙焊);(12)用风铲挑焊根或打磨焊根,并采用直流磁化圆棒电极进行磁粉检测,采用红色或黑色磁粉;(13)背面焊接(预热到250℃);(14)进炉加热到920℃进行正火热处理。
加热速率从250℃开始为56℃/W;保温时间为30分钟/25mm(寸,出炉后浸入水中急速冷却到300℃;(15)进炉中加热到630~650℃进行回火热处理。
保温时间30分钟/25mm(寸),加热速率56℃/h。
在静止空气中冷却;(16)温热状态下在卷板机上进行圆度校正(本操作类似于(15))(17)尺寸检查、圆度检查。
按ASME规范、GB150或工程标准要求;(18)超声波检测和修补(如果需要的话)UT*每台设备至少有一个筒节带有正火状态下的试板。
(19)射线检测(RT),采用直线回旋加速器或直线加速器,(底片采用Kodak AA或天津N-Ⅲ、Ⅳ-C型T3-JB4730.2)(20)送试板到物理试验室检查。
试板应是进行过消除应力的。
热处理次数按热处理循环所预期的最大要求数。
检验结果应符合筒节进入下一操作程序之前的要求;(21)-(22)去除临时附件,打磨和进行磁粉检测焊接处的周围边域;(23)-(24)筒节表面打砂;如果需要的话进行打磨,宏观检查;(25)内壁带极堆焊。
二层堆焊,第一层堆焊后要进行中间消除应力热处理;两层堆焊的正常厚度应是6.4mm(1/4”,第一层309L,第二层347L,应确保表面以下3.2mm的化学成份满足要求;(26)-(27)表面用不锈钢钢刷刷,并进行渗透检测(JB4730.5-xxxx);(28)堆焊层的抽查化学分析(在靠近筒节端部,用于手提钻钻孔);(29)铁素体食量检测和堆焊层厚度检验;(30)堆焊层表面交界处(带极道与道之间)10%超声波检测;(31)划线。