拉削
简述拉削的工艺特点
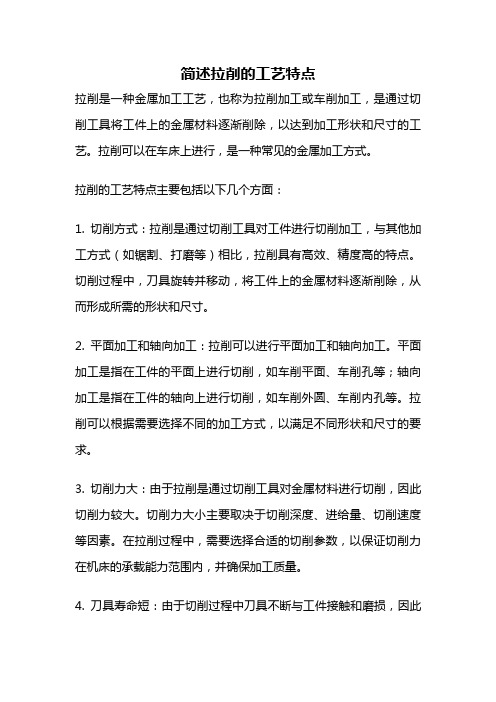
简述拉削的工艺特点拉削是一种金属加工工艺,也称为拉削加工或车削加工,是通过切削工具将工件上的金属材料逐渐削除,以达到加工形状和尺寸的工艺。
拉削可以在车床上进行,是一种常见的金属加工方式。
拉削的工艺特点主要包括以下几个方面:1. 切削方式:拉削是通过切削工具对工件进行切削加工,与其他加工方式(如锯割、打磨等)相比,拉削具有高效、精度高的特点。
切削过程中,刀具旋转并移动,将工件上的金属材料逐渐削除,从而形成所需的形状和尺寸。
2. 平面加工和轴向加工:拉削可以进行平面加工和轴向加工。
平面加工是指在工件的平面上进行切削,如车削平面、车削孔等;轴向加工是指在工件的轴向上进行切削,如车削外圆、车削内孔等。
拉削可以根据需要选择不同的加工方式,以满足不同形状和尺寸的要求。
3. 切削力大:由于拉削是通过切削工具对金属材料进行切削,因此切削力较大。
切削力大小主要取决于切削深度、进给量、切削速度等因素。
在拉削过程中,需要选择合适的切削参数,以保证切削力在机床的承载能力范围内,并确保加工质量。
4. 刀具寿命短:由于切削过程中刀具不断与工件接触和磨损,因此刀具寿命相对较短。
刀具寿命的长短主要取决于切削材料、切削速度、切削深度、切削方式等因素。
在拉削过程中,需要定期更换刀具,以保证加工质量和效率。
5. 加工精度高:拉削是一种高精度加工方式,可以获得较高的加工精度。
通过合理选择切削参数、采用精密的切削工具和机床,以及加工过程中的监控和调整,可以实现精度要求较高的工件加工。
6. 适用范围广:拉削可以加工各种金属材料,如铁、铜、铝、不锈钢等。
同时,拉削也可以加工不同形状和尺寸的工件,如外圆、内圆、平面、螺纹等。
因此,拉削是一种适用范围广、灵活性较高的金属加工方式。
总体来说,拉削是一种高效、精度高、适用范围广的金属加工工艺。
它通过切削工具对工件进行切削加工,可以获得较高的加工精度和表面质量。
然而,拉削也存在刀具寿命短、切削力大等问题,需要合理选择切削参数和刀具,以保证加工质量和效率。
刨削插削拉削工艺介绍及应用

刨削插削拉削工艺介绍及应用一、刨削工艺:刨削是利用刨床进行金属材料的加工工艺,通过切削刀具对工件进行旋转切削,实现加工的目的。
刨削适用于平面、曲面、槽、凸台等各种形状的工件加工。
其优点是加工精度高,表面质量好,但加工效率较低。
刨削工艺的应用:1.平面加工:刨床通过切削刀具对工件进行旋转切削,可以实现对平面的粗、中、精加工,广泛应用于制造各种平面结构的零件。
2.曲面加工:通过更换合适形状的切削刀具,可以实现对各种曲面的加工,如凹、凸面、曲线等,适用于制造车削机床主轴箱、引导轨道等曲线形状复杂的零部件。
3.细加工:刨削工艺可以使工件表面达到较高的光洁度和精度,适用于制造需要高精度和表面质量的工件,如刀模、测量工具、光学仪器等。
二、插削工艺:插削是利用插床进行金属材料的加工工艺,通过切削刃具对工件进行直线前进或旋进切削,实现加工的目的。
插削适用于薄壁管件、孔、凹槽等部位的加工,其优点是加工精度高、加工效率稍低。
插削工艺的应用:1.薄壁管件加工:插床通过切削刃具对薄壁管件进行加工,可以实现对管件内外径的加工,如加工钢管、铜管等,广泛应用于汽车、工程机械等行业。
2.孔加工:插削工艺可以实现对孔的精密加工,如毛细管、喷油嘴孔等,适用于制造小孔直径较精密的零件。
3.凹槽加工:插床通过切削刃具对工件表面进行切削,可以实现对各种形状、尺寸的凹槽和槽的加工,如齿轮、销槽等。
三、拉削工艺:拉削是利用拉床进行金属材料的加工工艺,通过钳爪夹持工件,通过切削刀具对工件进行旋转切削,实现加工的目的。
拉削适用于加工圆柱、圆锥、球面等各种形状的工件,其优点是加工精度高、加工效率较高。
拉削工艺的应用:1.圆柱加工:拉床可以实现对各种直径大小的圆柱形状的加工,如轴、轴套等。
2.锥面加工:拉床可以实现对各种锥面的加工,如锥孔、锥柱等,适用于制造锥形零件。
3.球面加工:通过更换合适形状的切削刀具,拉床可以实现对不同半径的球体的加工,如滚珠轴承、摩擦轮等。
拉削教案

讲座——拉削加工(一)拉削加工的特点及应用1.拉削和推削加工:⑴拉削加工:就是用各种不同的拉刀在相应的拉床上切削出各种内、外几何表面的一种加工方式。
⑵推削加工:当刀具在切削时,不是受拉力而是受压力,这里刀具叫推刀,这种加工方法叫推削加工。
推削加工主要用于修光孔和校正孔的变形。
⑶拉削时的运动:拉削时,拉刀与工件的相对运动为主运动,一般为直线运动。
2.拉削加工的特点:生产率较高,被加工表面在一次走刀中成形。
拉削加工的精度可达IT8~IT7,表面粗糙度值可达Ra3.2~0.4μm。
3.拉削的适用范围:主要用于成批、大量生产的场合。
可以加工各种形状的通孔、平面及成形面等,但拉削只能加工贯通的等截面表面,特别适用于成形内表面的加工。
拉削的典型加工表面(二)拉床:拉床按其加工表面所处的位置,可分为内拉床和外拉床。
按拉床的结构和布局形式,又可分为立式拉床、卧式拉床、连续式(链条式)拉床等。
1.卧式拉床:如下图所示。
卧式拉床立式拉床2.立式拉床:见上图。
立式拉床根据用途可分为立式内拉床和立式外拉床两类。
立式内拉床可以用拉刀或推刀加工工件的内表面。
如下图所示。
3.连续式拉床(链条式拉床):如图所示。
连续式拉床可用于连续拉削零件,因而生产率较高,常用于大批大量生产中加工小型零件的外表面。
如汽车、拖拉机连杆的连接平面及半圆凹面等。
连续拉床工作原理(三)拉刀1.拉刀的种类:拉刀和种类很多,根据加工表面位置不同可分为内拉刀与外拉刀。
外拉刀用于加工工件的外表面,内拉刀用于加工工件的内表面。
拉刀是多齿类刀具,后一刀齿比前一刀齿高,其齿形与工件的加工表面形状吻合,进给运动靠后一刀齿的齿升量(前后刀齿的高度差)来实现。
拉刀的种类很多,根据加工表面的位置不同可分为内拉刀与外拉刀两种。
⑴常用内拉刀:常用的内拉刀有圆孔拉刀、方孔拉刀、花键拉刀、渐开线齿拉刀等。
如下图所示。
a 圆孔拉刀b 孔拉刀 C 花键拉刀 D 渐开线齿拉刀常用内拉刀⑵常用外拉刀:外拉刀用于加工工件的外表面。
拉削加工简介

1)齿升量: 齿升量af 是指前后两相邻刀齿的高度差。它影响加工质量、生产效
率和拉刀的制造成本。
af↑↑→
有利于拉刀的制造,生产效率高,表面粗糙度就大; 影响拉刀强度及拉床负荷;
af↓↓→
难以切下很薄的金属层,容易磨损刀齿,加工表面也 不光洁
一般,在拉刀强度许可条件下,粗切齿可尽量多切(约去除全部余量的 80%),精切齿为保证质量齿升量取小值(约总余量的10%),过渡齿在 10%余量范围内 逐渐减小齿升量,校准齿没有齿升量。
拉削加工
三、拉刀的组成及其加工方式
(3) 综合式拉削
特点: ① 粗切齿制成轮切式结构,分块拉削,精切齿采用成形式结构,分层拉削。 ② 缩短了拉刀长度。 ③ 提高了拉削生产率。 ④ 拉削后的表面质量较好。
EDUCATION PRACTICE SESSION PPT
感谢同学们观
看
胡林岚 老师 扬州市职业大学 机械工程学院
三、拉刀的组成及其加工方式
3. 拉削方法
(1) 分层拉削法
特点: ① 可获得较高的表面质量。 ② 刀齿上的分屑槽造成切屑上有一加强筋,切屑卷曲困难。 ③ 拉刀长度较长,降低了拉削生产率。 ④ 拉刀成本高。
拉削加工
三、拉刀的组成及其加工方式
(2) 分块拉削法
特点: ① 切削厚度大,在相同余量下,拉刀所需的刀齿总数较分层式少。 ② 切屑上无加强筋,切屑卷曲顺利。 ③ 拉刀长度短,提高了拉削生产率。 ④ 可拉削带硬皮的铸件、锻件。 ⑤ 拉削后的表面质量较差。
125mm,孔的深径比一般不超过5。但不能加工薄壁零件及轴向尺寸太大的零件
一、 拉削过程及特点
拉削加工
运动
主运动——拉刀的直线移动
拉削
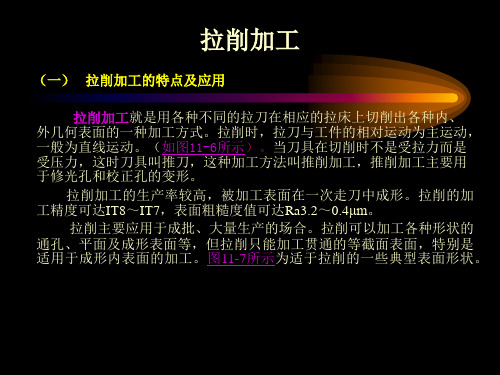
• 按同廓拉削方式设计的拉刀,每个刀齿的廓形与被加工表面 最终要求的形状相似,如图11-15所示,工件表面的形状与尺 寸由最后一个精切齿和校准齿形成,故可获得较高的工件表 面质量。
按此方式设计的拉 刀,刀齿廓形与被拉削 表面的形状不同,被加 工工件表面的形状和尺 寸由各刀齿的副切削刃 形成,如图11-16所示。这 对于加工复杂成形表面 的工件,拉刀的制造比 同廓式简单,但在工件 已加工表面上可能出现 副切削刃的交接痕迹, 故加工出的工件表面质 量较差。
• 拉刀是多齿刀具,后一刀齿比前一刀齿高,其齿形与工件的加工表 面形状吻合,进给运动靠后一刀齿的齿升量(前后刀齿高度差)来 实现(如图11-6所示)。
图11-7所示为适于拉削的一些典型表面形状。
(二)拉床 拉床按其加工表面所处的位置,可分为内拉床和外拉床。按拉床的结 构和布局形式,又可分为立式拉床、卧式拉床、连续式(链条式)拉床等。
综合拉削方式是前面两种拉削方式综合在一起的一种拉削方 式,如图11-18所示。
如图11-17所示,
分块拉削方式的优 点是切削刃的长度(切 削宽度)较短,允许的 切削厚度较大,这样, 拉刀的长度可大大缩短, 也大大提高了生产率, 并可直接拉削带硬皮的 工件。但是,这种拉刀 的结构复杂,制造麻烦。 拉削后工件的表面质量 较差
(四)拉削方式(拉削图形)
拉削方式可以分为三大类:分层拉削方式、分块拉削 方式和综合拉削方式。 ⒈ 分层(普通)拉削方式 分层拉削又可分为: (1)同廓拉削方式 按同廓拉削方式设计的拉刀,每个刀齿的廓形与被加 工表面最终要求的形状相似,如图11-15所示。 (2) 渐成拉削方式 按此方式设计的拉刀,刀齿廓形与被拉削表面的形状 不同,被加工工件表面的形状和尺寸由各刀齿的副切削刃形 成,如图11-16所示。
23讲91拉刀拉削方式

第一节 拉削特点及拉刀类型
一、拉削特点
拉刀是一种多齿刀
具,拉削时由于拉刀
的后一个(或一组)刀
齿高出前一个(或一组)
刀齿,从而能够一层
层地从工件上切下金
属(图9-1),以获得较
高精度和较好的表面
质量。
9-1拉削过程
1
拉削加工与其他切削加工方法相比较,具有以下特点:
(1)生产率高
由于拉刀是多齿刀具,同时参加工作的刀齿多(如图9-1所示为三 个),切削刃总长度大,一次行程能够完成粗—半精—精加工,因 此生产率很高,尤其是加工形状特殊的内、外表面工件时,效果 尤为显著。
拉削层尺寸有:拉削长L,切削厚度和切削宽度
9
图9-8 拉刀组成及拉削示意图
前柄——用于将拉刀装夹在拉床的夹头中以传送运动和拉力。 颈部——用于连接头部与刀体,一般在颈部上刻印拉刀的标记。 过渡锥——使前导部能顺利进入初孔(工件上予先加工的孔),起对准中 10 心的作用。
前导部——起引导作用,防止拉刀进入工件孔后发生歪斜,并可检查 拉削孔径是否符合要求。
拉削方式可分为分层式、分块式及综合式三大类。
1、分层式
分层式拉削又可分为同廓式和渐成式两种。
1)同廓式:它的特点是,刀齿的刃形与被加工表面形状相同,仅尺寸 不同,即刀齿直径(或高度)向后递增,加工余量被一层一层地切去。如 图9-9
这种拉削方式切削厚度小而切削宽度大,因此可获得较好的工件表面 质量。拉削力及功率较大,分屑槽转角处容易磨损而影响拉刀耐用度。 这种方式的拉刀除圆孔拉刀外,其他制造比较困难
采用综合式圆拉刀
14
图9-13 拉削方式
a)分层式 b)分块式 c)综合式
15
第三节 拉刀的合理使用
第九章拉削与拉刀

• 拉刀将工件加工余量一层一层顺序地切除。
• (1)成形式(同廓拉削):各刀齿形状与加工表面形状相同。 • 优点:表面质量↑ 。缺点:拉刀长度↑ 、刀具成本↑ 、效率↓
• 用途:精度高的中小型零件。
• (2)渐成拉削 • 刀齿切去的表面连接而成。刀具简单。表面质量差。 • 2.分块式(轮切式)拉削 • 加工表面的每一层金属是由一组尺寸基本相同但刀齿切削位置相 互交错的刀齿(通常每组由2-3个刀齿组成)切除的。 • 优点:工作刃宽度↓,切削厚度↑,效率↑ 。
• 一、工作部分设计
• 确定拉削方式
• 确定拉削余量A • 1.确定齿升量fz、齿数和刀齿直径
拉刀的齿升量fZ是指相邻两个刀齿(或者是两组刀齿)的半径差。
拉刀齿升量 fZ越大,切削齿数就越少,拉刀长度越短,拉削生产 率越高,刀齿成本相对较低。但齿升量af过大,则拉削力越大。齿
升量af也不能太小,造成滑行和挤压现象,加剧刀齿的磨损。
• 2.拉刀切削部分要素
• • • • • • 1.几何角度 2.结构参数 齿升量fz、齿距P、容屑槽深度h、齿厚g、齿背角θ、刃带宽度bα1 齿升量:齿升量↑齿数↓拉刀长度↓,最小量≥0.005mm; 齿距:齿距↓工作齿数↑工作平稳。 刃带宽度:起支承作用,保持重磨后齿高不变,便于测量。
• 二、拉削方式
齿升量af应根据工件材质和拉刀的类型确定。 粗切齿:齿升量fzⅠ最大,一般不可超过0.15mm,( 0.03~ 0.06mm)切去整个拉削余量的80%左右。 过渡齿:齿升量fzⅡ粗切齿逐渐递减至精切齿 精切齿:齿升量fzⅢ最小,一般取0.01~0.02mm 校准齿:齿升量fzⅣ为0.
过渡齿齿数: Z Ⅱ =4 ~ 8 ; 精切齿齿数: Z Ⅲ =3 ~ 7 校准齿齿数: Z V Ⅰ =5 ~ 1 0 粗切齿齿数: 计算
第15章 拉削与拉刀

2 分块式拉削 按分块式拉削图形设计的拉刀,其切削部分是由若
干齿组成。每个齿组中有2~3个刀齿,它们的直径相同, 共同切下加工余量中的一层金属,每个刀齿仅切去一层 中的一部分。图所示为它的主要优点是每 一个刀齿上参加工作的长度(即切削宽度)较小,因此 在保持相同的切削力的情况下,允许较大的切削厚度比 分层拉削要大得多。因此,虽然每层金属要用一组(2或 3个)刀齿去切除,但由于切削厚度比分层拉削方式大 2~3倍,所以在同一拉削量下,所用刀齿的总数减少了 许多,拉刀长度大大缩短,不仅节省了贵重的刀具村料, 生产率也大大提高。在刀齿上分屑槽的转角处,强度高, 散热良好,故刀齿的磨损量也较小。所以在同一拉削余 量下,轮切式拉刀所需的切削齿数目少,拉刀长度短, 不仅节省了贵重的刀具材料,生产率也大大提高。
.
第五节 圆孔拉刀设计
一、切削部 切削部是拉刀的主要部分,它与拉削质量、生产率以及拉
刀的制造成本有直接的关系。设计时必须充分考虑下列几个方 面。
.
1.拉削余量A 拉削余量是设计拉刀的重要的原始数据之一,它直接影响拉 削的效率和质量,所以选择的要适当,若拉削余量太小,则不 能全部切除前一道工序留下的加工误差,影响拉削质量;但拉 削余量太大,拉刀刀齿必然增多,拉刀较长,使拉刀制造困难 和浪费刀齿材料。加工不同形状和要求的表面,拉削余量也不 同。拉削余量可用经验公式计算,也可从相关中选取。圆孔拉 削余量如图所示。 当已知拉削前、后的孔径,则拉削余量为:
拉刀是一种加工精度和切削效率都比较高的多齿刀具。 拉削时拉刀作等速直线运动,于拉刀的后一个(或一组)刀 齿高出前一个(或一组)刀齿,从而能够一层层地从工件上 切下多余金属,如图所示。由于拉削速度较低,切削厚度很 小,可以获得较高精度和较好的表面质量。
第16章 拉削与拉刀

1)按经验公式计算 拉前孔为钻孔或扩孔时 按公式16.1。计算。 拉前孔为镗孔或铰孔时 按公式16.2。计算。 2)已知拉前孔直径和拉后孔直径时 可用拉前孔的最小值与拉后孔的最大值来计算拉 削余量。见公式16.3。 3)拉削余量也可以查表确定
3、确定齿升量 拉削余量确定后,齿升量越大,齿数就越小,拉 刀就越短,生产效率可以提高。但齿升量不能过 大,过大会拉断拉刀。 粗切齿、精切齿、过渡齿的齿升量各不相同,其 齿升量的确定见表16.1。P222。精切齿取小值, 粗切齿取大值,过渡齿的齿升量由粗切齿逐渐过 渡到精切齿。 最小齿升量的限制:由于刀刃钝圆半径的存在, 齿升量最小不能小过0.005mm。否则挤压严重。
容屑槽和切屑的纵向截面积之比来表示,见图 16.19。 设计拉刀时,许用容屑系数【K】必须认真选择 其大小与工件材料性质、切削层截形和拉刀磨损 有关。 加工一般钢件【K】=2.5—5.5。 加工铸铁、青铜【K】=2—2.5。 【K】值的最终确定应根据《复杂刀具设计手册》 《切削用量手册》来合理选取。如选择不当会造 成拉刀拉断。所以一定要非常慎重。
刃带用于在制造拉刀时控制刀齿直径,也为 了增加拉刀校准齿前刀面的可重磨次数,提 高拉刀使用寿命,有了刃带,还可提高拉削 过程稳定性。 第三节 拉削图形 拉削图形是指拉刀从工件上切除余量的顺序 和方式。拉削图形也叫拉削方式。拉削图形 可分为分层式、分块式和综合式三种。 一、分层式 分层式一层层地切去拉削余量。
重磨前刀面,如后角取得大,刀齿直径就会减 小的很快,拉刀使用寿命会显著缩短。因此, 内拉刀切削齿后角都选得很小,校准齿后角比 切削齿的更小,见表16.3。 特殊情况:当拉削弹性大的材料时,为减小切 削力,后角可取得较大些。 外拉刀的后角可取大些。 3)刃带宽度。拉刀各刀齿均留有刃带,以便于 制造拉刀时控制刀齿直径;校准齿的刃带还可 以保证沿前刀面重磨时刀齿直径不变。刃带齿数量可减 少,拉刀长度可缩短,效率较高,表面粗糙度较 大。 分块式又称为轮切式,可以用三个刀齿为一组, 交错排列,分别切去同一层金属的一部分,可以 加大切削厚度,提高刀具使用寿命。 另外,圆弧分屑槽也不会产生加强筋。 采用圆弧形分屑槽,容易磨出槽底后角和侧刃后 角,有利于减轻刀具磨损,提高刀具使用寿命。 分块式拉削的已加工表面质量不如成形式好。
机械制造与自动化专业《项目八、任务2 掌握拉削加工方法》
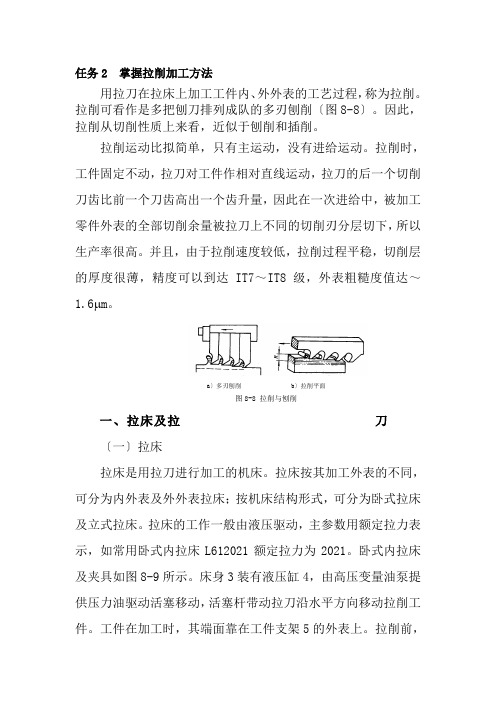
任务2 掌握拉削加工方法用拉刀在拉床上加工工件内、外外表的工艺过程,称为拉削。
拉削可看作是多把刨刀排列成队的多刃刨削〔图8-8〕。
因此,拉削从切削性质上来看,近似于刨削和插削。
拉削运动比拟简单,只有主运动,没有进给运动。
拉削时,工件固定不动,拉刀对工件作相对直线运动,拉刀的后一个切削刀齿比前一个刀齿高出一个齿升量,因此在一次进给中,被加工零件外表的全部切削余量被拉刀上不同的切削刃分层切下,所以生产率很高。
并且,由于拉削速度较低,拉削过程平稳,切削层的厚度很薄,精度可以到达IT7~IT8级,外表粗糙度值达~1.6 m。
a〕多刃刨削 b〕拉削平面图8-8 拉削与刨削一、拉床及拉刀〔一〕拉床拉床是用拉刀进行加工的机床。
拉床按其加工外表的不同,可分为内外表及外外表拉床;按机床结构形式,可分为卧式拉床及立式拉床。
拉床的工作一般由液压驱动,主参数用额定拉力表示,如常用卧式内拉床L612021额定拉力为2021。
卧式内拉床及夹具如图8-9所示。
床身3装有液压缸4,由高压变量油泵提供压力油驱动活塞移动,活塞杆带动拉刀沿水平方向移动拉削工件。
工件在加工时,其端面靠在工件支架5的外表上。
拉削前,护送夹头和滚柱向左移动,将拉刀穿过工件预制孔,并将拉刀柄部插入拉刀夹头。
〔a〕〔b〕a卧式内拉床1-拉刀 2-工件 3-床身 4-液压缸 5-工件支架 6-后托架〕b拉床夹具〔1-支承体 2-球座 3-套筒 4-弹簧〕图8-9 卧式内拉床及夹具〔二〕拉刀根据被加工外表及孔断面形状的不同,拉刀有各种形式。
图8-10为圆孔拉刀的结构图。
l1为拉刀的柄部,用以夹持拉刀,并带动拉刀运动。
l2为颈部。
l3为导向局部,用以引导拉刀正确的加工位置,防止拉刀歪斜。
l4为切削局部,有切削齿,用于切削金属。
切削齿上有切屑槽用以容纳切屑。
切屑槽应有足够的空间,否那么切屑容纳不下,会破坏已加工外表,甚至使拉刀折断。
切削齿刃上沿轴向有交错的断屑槽。
l5为校正局部,用作最后的修正加工。
拉削加工

拉床
拉削方式 拉削方式是指拉削过程中,加工余量在各刀齿上的分配方式,拉削方式直接 关系到刀齿切除金属层的图形(即拉削图形)。不同的拉削方式对拉刀的结构形 式、拉削力的大小、拉刀耐用度、拉削表而质量和生产效率有很大的影响。 拉削方式主要分为:分层拉削方式、轮切拉削方式和综合拉削方式三大类。
(一)、分层拉削方式 分层拉削是将加工余量一层一层地切去。其中根据已加工表两的形 成过程不同,又可分为: ⒈同廓拉削 各刀齿形状与加工表面最终形状一样。最后一个 刀齿的刀刃形状和尺寸决定了已加工表面的形状和尺寸。采用这种 拉削方式可获得较高的工件表面质量。但这种拉刀齿数较多,长度 较长,刀具成本高,效率低。它主要用于加工余量较少和较均匀的 中小尺寸零件,也用于加精度要求高的成形表面。 ⒉渐成拉削 被加工表面最终形状和尺寸是由各刀齿切去的表 面连接而成。因此,各齿刀刃形状不同于被加工表面最终形状。达 种拉刀制造较简单,但拉削表面质量较差。
(二)、分块拉削方式 ⒈轮切拉削是将加工余量分为若干层,每层被刀齿分段切除。 按这种拉削方式设计的拉刀上有几组刀齿,每组刀齿中包含两个或 三个刀齿。同一组刀齿的直径相同或基本相同,每个刀齿的切削位 置是相互错开的,各切除一层金属中的一部分。全部余量由几组刀 齿按顺序切除。
轮切式与分层拉削方式比较,它的优点是每一个刀齿上参加工作的切削刃的宽度较 小,但切削厚度较分层拉削方式要大得多。因此虽然每层金属要有一组(2或3个)刀齿去切 除,但由于切削厚度要比分层拉削方式大二倍以上,所以在同一拉削余量下,所需刀齿 的总数减少了很多,拉刀长度大大缩短,不仅节省了贵重的刀具材料,生产效率也有提 高。这种拉削方式可用来加工带有硬皮的铸件和锻件。但是,轮切式拉刀的结构较复杂, 制造困难,拉削后的工件表面也较粗糙。 2、综合轮切式 综合轮切式集中了同廓式和轮切式的优点,即粗切齿及过渡齿制成轮切式结构,精 切齿则采用同廓式结构。这样即缩短了拉刀长度,提高生产效率,又能获得较高的工件 表面质量是利用特制的拉刀在拉床上进行的。
拉削工艺特点和应用

拉削工艺的特点和应用1. 应用背景拉削工艺是一种常见的金属加工方法,通过将金属材料置于拉削机床上,利用刀具对材料进行切削和塑性变形,从而得到所需形状和尺寸的零件。
拉削工艺在制造业中广泛应用,涉及到诸多行业,如汽车制造、航空航天、机械制造等。
2. 应用过程拉削工艺主要包括以下几个步骤:2.1 材料准备在进行拉削之前,需要对材料进行准备。
选择适合的金属材料,并根据零件的要求进行切割或锯断。
对材料进行表面处理,如去除氧化层、清洁表面等。
2.2 夹紧固定将材料夹紧固定在拉削机床上。
通常使用夹具来固定材料,确保其稳定性和准确性。
2.3 选择刀具和加工参数根据零件的要求和材料的特性,选择合适的刀具,并确定合适的加工参数,如切削速度、进给速度、切削深度等。
2.4 进行拉削加工根据所选的刀具和加工参数,进行拉削加工。
刀具通过旋转和移动的方式对材料进行切削,同时产生塑性变形,最终得到所需形状和尺寸的零件。
2.5 检测和修整完成拉削后,对零件进行检测,检查其尺寸、表面质量等是否符合要求。
如有需要,可以进行修整操作,以确保零件的质量。
3. 应用效果拉削工艺具有以下几个特点和应用效果:3.1 高精度加工由于拉削工艺使用专门的拉削机床和刀具,能够实现高精度的加工。
通过合理选择刀具和控制加工参数,可以达到较高的尺寸精度和表面质量要求。
3.2 多种形状加工拉削工艺适用于多种形状的零件加工。
无论是简单的直线、曲线还是复杂的曲面,都可以通过合适的刀具路径实现精确加工。
3.3 高效率生产拉削工艺具有高效率的特点。
一台拉削机床可以同时进行多个工序的加工,提高生产效率。
另外,由于切削速度较快,加工时间相对较短。
3.4 适应性强拉削工艺适应性强,适用于多种金属材料的加工。
无论是钢、铝、铜还是合金等材料,都可以通过拉削工艺进行加工。
3.5 可靠性高由于拉削工艺在加工过程中刀具和材料之间有直接接触,因此能够更好地控制加工质量。
拉削过程中切削力和切削温度较低,减少了零件表面的热变形和刀具磨损。
拉削生产率高的原因
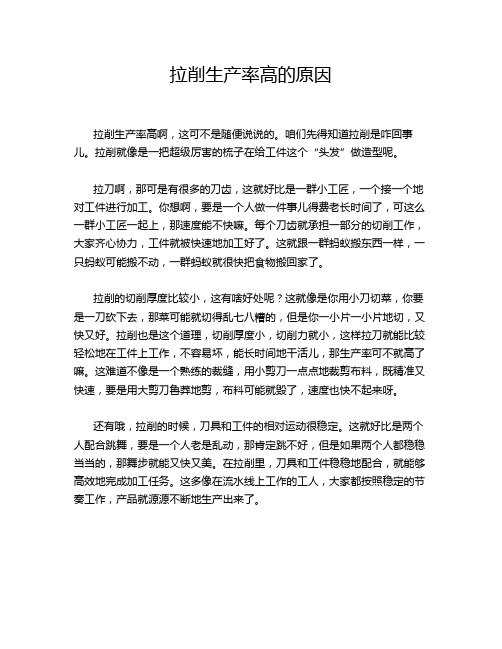
拉削生产率高的原因拉削生产率高啊,这可不是随便说说的。
咱们先得知道拉削是咋回事儿。
拉削就像是一把超级厉害的梳子在给工件这个“头发”做造型呢。
拉刀啊,那可是有很多的刀齿,这就好比是一群小工匠,一个接一个地对工件进行加工。
你想啊,要是一个人做一件事儿得费老长时间了,可这么一群小工匠一起上,那速度能不快嘛。
每个刀齿就承担一部分的切削工作,大家齐心协力,工件就被快速地加工好了。
这就跟一群蚂蚁搬东西一样,一只蚂蚁可能搬不动,一群蚂蚁就很快把食物搬回家了。
拉削的切削厚度比较小,这有啥好处呢?这就像是你用小刀切菜,你要是一刀砍下去,那菜可能就切得乱七八糟的,但是你一小片一小片地切,又快又好。
拉削也是这个道理,切削厚度小,切削力就小,这样拉刀就能比较轻松地在工件上工作,不容易坏,能长时间地干活儿,那生产率可不就高了嘛。
这难道不像是一个熟练的裁缝,用小剪刀一点点地裁剪布料,既精准又快速,要是用大剪刀鲁莽地剪,布料可能就毁了,速度也快不起来呀。
还有哦,拉削的时候,刀具和工件的相对运动很稳定。
这就好比是两个人配合跳舞,要是一个人老是乱动,那肯定跳不好,但是如果两个人都稳稳当当的,那舞步就能又快又美。
在拉削里,刀具和工件稳稳地配合,就能够高效地完成加工任务。
这多像在流水线上工作的工人,大家都按照稳定的节奏工作,产品就源源不断地生产出来了。
拉削的加工精度还高呢。
这就意味着一次加工就能让工件达到比较理想的状态,不需要返工。
你想想,要是做一件东西,做完了发现不合格,还得重新做,那多浪费时间啊。
拉削就像是一个神射手,一箭就射中靶心,不需要补射。
这也为提高生产率做出了很大的贡献啊。
拉刀的使用寿命也比较长。
这就像是一个耐用的工具,不需要老是更换。
要是一个工具用一会儿就坏了,你得花时间去换,这期间就不能干活儿了。
拉刀呢,就可以长时间地为我们服务,一直高效地进行拉削工作。
这就像一头老黄牛,任劳任怨地耕地,不需要经常换牛,地就能很快地耕完。
GW77_拉削基础知识专题讲座

第二部分
拉削的结构要素
第二部分 拉削的结构要素
一、拉刀的组成部分(以圆孔拉刀为例)
1-前柄 5-切削部
圆孔拉刀的组成部分
2-颈部 6-校准部
3-过渡锥 7-后导部
4-前导部 8-后托部
1.运动简单 2.生产效率高 3.加工精度和表面质量高 4.加工成本低
拉削过程只需要一个主运动,而进
给运动则是依靠拉刀刀齿的齿升量来完
成的。齿升量是指后面的刀齿高于前面 刀齿拉拉的刀削高齿时度数的。很切拉多削削,层加又很工是薄操几、作个拉相刀削对齿速较同度简时较单参。 加低切,削所,以切易削获刃得工较作小的的总表长面度粗很糙大度,值一。 次由拉于削被行加程工中表可面以尺完寸成、粗形、状半主精要和决精定加于 工拉工刀序精,切因齿此和生较产准效齿率,很而高拉。刀由于在低 速下拉工刀作虽,然磨制损造较复慢杂,、所价以格只高要,保但证寿了命 很多拉件长,刀的,加的尺一工精寸把效度一(率,致套又就性)高可好拉,以、刀所保互加以证换工拉工性的削件较工加精高件工度。数成,很本工 较低。
外拉刀可加工平面、键槽、台阶面、成型表面、直齿和螺旋齿外齿轮以及盘上的榫槽 和叶片的榫头等。从形状上分拉刀大体可分为方拉刀和圆拉刀。加工键槽、榫槽等外表 面,拉削工件一般采用方形拉刀,拉削内孔、特形孔及内花键一般都采用圆拉刀。
2、拉刀按结构分,可分为整体式和组合式(装配式)两大类,中 小规格的内拉刀大都做成整体式,即由高速钢制成刀齿与刀体为一体的 结构。大规格内拉刀和大部分外拉刀则多做成组合式结构,即刀齿或刀 块由高速钢制造,刀体则由结构钢制造,这样既可节约贵重的高速钢, 也较容易制造。硬质合金拉刀也多做成组合式。
拉削工作原理

拉削工作原理
"拉削"通常是指拉削加工,也称拉切、拉伸削减,是一种金属加工方法。
拉削工作原理主要包括拉伸材料并将其通过刀具的形成,从而实现切削加工。
以下是拉削的一般工作原理:
1.工件准备:被加工的工件通常是金属材料,如钢、铝等。
首先,工件被准备好,可能包括切割、磨削或其他预处理工序。
2.夹紧工件:工件被夹在拉削机床上,以确保在加工过程中保持稳定。
3.拉伸工件:工件在机床上被拉伸,通常是沿着其长度方向。
这有助于在拉伸过程中使工件保持稳定的几何形状。
4.切削刀具:切削刀具通常是带有刃口的刀片,这些刃口在拉伸过程中贴近工件表面,从而将工件削除一部分。
5.切削操作:切削刀具在拉伸的工件表面上切削,形成切屑。
切削的深度和速度可以通过调整机床的参数进行控制。
6.拉屑:切削操作会生成切屑,这是从工件上切削下来的薄片状材料。
拉屑的形状和类型取决于刀具的几何形状和工件材料的特性。
7.完成工件:切削过程继续,直到整个工件的加工完成。
最终的形状和尺寸受切削刀具、机床参数和工件材料的影响。
拉削是一种高效的切削加工方法,特别适用于长丝、线材或管材等工件的加工。
拉削的工作原理使其适用于对材料进行细长形状的精密切削。
简述拉削的工艺特点
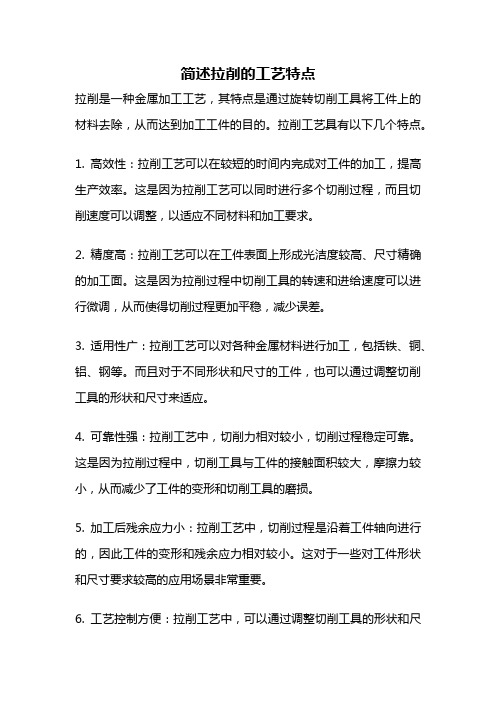
简述拉削的工艺特点
拉削是一种金属加工工艺,其特点是通过旋转切削工具将工件上的材料去除,从而达到加工工件的目的。
拉削工艺具有以下几个特点。
1. 高效性:拉削工艺可以在较短的时间内完成对工件的加工,提高生产效率。
这是因为拉削工艺可以同时进行多个切削过程,而且切削速度可以调整,以适应不同材料和加工要求。
2. 精度高:拉削工艺可以在工件表面上形成光洁度较高、尺寸精确的加工面。
这是因为拉削过程中切削工具的转速和进给速度可以进行微调,从而使得切削过程更加平稳,减少误差。
3. 适用性广:拉削工艺可以对各种金属材料进行加工,包括铁、铜、铝、钢等。
而且对于不同形状和尺寸的工件,也可以通过调整切削工具的形状和尺寸来适应。
4. 可靠性强:拉削工艺中,切削力相对较小,切削过程稳定可靠。
这是因为拉削过程中,切削工具与工件的接触面积较大,摩擦力较小,从而减少了工件的变形和切削工具的磨损。
5. 加工后残余应力小:拉削工艺中,切削过程是沿着工件轴向进行的,因此工件的变形和残余应力相对较小。
这对于一些对工件形状和尺寸要求较高的应用场景非常重要。
6. 工艺控制方便:拉削工艺中,可以通过调整切削工具的形状和尺
寸,切削速度和进给速度,来达到不同的加工要求。
这使得拉削工艺在实际应用中具有较好的可控性。
拉削工艺是一种高效、精确、可靠的金属加工工艺,适用于各种金属材料和工件形状。
它可以满足对工件尺寸、形状和表面粗糙度要求较高的加工需求。
在实际应用中,我们可以根据具体的加工要求选择合适的拉削工艺参数,从而获得最佳的加工效果。
试述拉削工艺特点和应用

试述拉削工艺特点和应用
拉削工艺是一种通过拉拽金属材料来改变其形状和尺寸的加工方法。
其特点如下:
1. 高精度:拉削工艺能够实现较高的精度要求,可以制造出精密的工件。
因为拉削过程中,金属材料受到箔带的拉伸和压力,使其在侧向扩展和纵向延伸,从而改变了其形状。
2. 高效率:相比于其他加工方法,拉削工艺具有较高的生产效率。
一次性可将金属材料加工成所需形状和尺寸。
3. 省材料:拉削工艺能够最大限度地利用原料,减少浪费和剩余材料。
由于拉削是通过拉伸材料来改变其形状,不需要额外的材料添加或切削,因此材料的利用率较高。
4. 简便易行:拉削工艺设备简单,操作方便。
通过合适的机械结构和设备设置,可以实现自动化拉削,提高效率和一致性。
5. 应用广泛:拉削工艺可以应用于各种金属材料的加工,包括铜、铝、钢等。
它可以用于制造各种形状和尺寸的零件和产品,如管道、轴承、钉子等。
拉削工艺的应用领域包括机械制造、汽车工业、航空航天、电子设备等。
例如,在汽车制造中,拉削工艺可以用来制造发动机零件、变速箱零件等。
在电子设备制造中,拉削工艺可以用来制造散热片、机箱等。
在航空航天领域,拉削工艺可以用来
制造飞机发动机零件等。
由于拉削工艺的高精度和高效率,它在制造行业中扮演着重要的角色。
拉削力计算公式

拉削力计算公式拉削力的计算公式可以通过以下公式表示:拉削力 = 切削力系数× 主轴功率× 切削速度÷ 进给速度其中,切削力系数是一个与切削材料、刀具和切削参数等因素相关的参数,一般通过实验或经验确定。
主轴功率是指切削过程中主轴所消耗的功率,可以通过主轴电机的额定功率来估算。
切削速度是指切削刀具表面上一点在单位时间内相对于工件表面的移动速度,通常用米/分钟或英尺/分钟表示。
进给速度是指切削过程中工件相对于刀具沿进给方向的移动速度,通常用毫米/转或英寸/转表示。
拉削力的计算公式可以帮助工程师根据切削参数和工件材料来合理选择刀具和切削参数,从而提高切削加工的效率和质量。
例如,在铣削加工中,工程师可以通过计算拉削力来选择合适的铣刀和切削参数,以确保工件表面质量和刀具寿命。
在实际应用中,拉削力的计算公式可以根据不同的加工情况进行修正和调整。
例如,在高速切削加工中,由于切削速度较高,切削力会受到空气动力学效应的影响,因此需要考虑空气动力学因素对拉削力的影响。
此外,工件材料的硬度、强度以及切削液的使用等因素也会对拉削力产生影响,因此在具体应用中需要根据实际情况进行修正。
除了切削力,对于拉削过程中的切削温度也是需要考虑的重要因素。
切削温度过高会导致刀具磨损加剧、工件表面质量下降甚至工件变形等问题。
因此,工程师在进行拉削力计算时,还需要综合考虑切削温度的影响,以确保切削加工的稳定性和质量。
拉削力的计算公式是切削加工中的重要工具,它可以帮助工程师选择合适的切削参数和刀具,提高切削加工的效率和质量。
在实际应用中,还需要根据具体情况进行修正和调整,以确保计算结果的准确性和可靠性。
通过合理使用拉削力计算公式,工程师可以更好地控制切削过程,提高切削加工的效果,实现工件的精确加工。
- 1、下载文档前请自行甄别文档内容的完整性,平台不提供额外的编辑、内容补充、找答案等附加服务。
- 2、"仅部分预览"的文档,不可在线预览部分如存在完整性等问题,可反馈申请退款(可完整预览的文档不适用该条件!)。
- 3、如文档侵犯您的权益,请联系客服反馈,我们会尽快为您处理(人工客服工作时间:9:00-18:30)。
(2)拉刀的结构 )
圆孔拉刀由头部、颈部、过渡锥部、前导部、 切削部、校准部、后导部及尾部组成。
平面的拉削
平面的拉削
孔的拉削
三、拉削工艺特点
1、生产率高 3、适于批量生产 拉刀多齿,粗、精加工可在一次行程中 拉刀结构复杂,制造困难,拉削每一种 完成,生产率较高。 表面都需要用专门的拉刀,制造成本高, 仅适用于大批量生产的孔加工。 2、加工质量高 4、不能拉台阶孔和盲孔。 拉削加工切屑薄,切削运动平稳,加工 精度较高,表面粗糙度较低。
§6.4 拉削加工
拉削:利用各种形状的拉刀在拉床上拉 拉削 出各种孔或平面的方法。
一、拉削加工范围
当拉刀相对工件作直线移动时﹐工件 的加工余量由拉刀上逐齿递增尺寸的 刀齿依次切除。
拉削孔的形状
图6-16 拉削孔的形状
拉 削 加 工 的 典 型 表 面 形 状
二、拉床与拉刀
1、拉 床 、 按结构分为立式拉床和卧式拉床(图6.17)。 电动机通过驱动液压泵使活塞拉杆作水平直 线运动,实现拉刀相对于工件的直线运动。 拉杆一端带刀夹,用来夹持拉刀。拉刀随拉 杆移动通过工件而拉削出所需孔形 拉刀
托架 床身 液压部件 图6-17 拉床外形
2、拉 刀
(1) 拉刀的类型 拉刀的类型
按加工工件的表面不同 加工工件的表面不同可分为: 加工工件的表面不同 内拉刀:圆孔拉刀、键槽拉刀 及花键拉刀等; 内拉刀 外拉刀:如平面拉刀、成形表面拉刀及齿轮拉刀 外拉刀 等 。 按受力不同 受力不同可分为拉刀和推刀。 受力不同 按拉刀构造 拉刀构造不同,可分为整体式与组合式 。 拉刀构造