煤直接和间接液化生产燃料油技术
煤炭加工中的煤液化与燃料油生产

02
清洁能源技术的发展将推动燃料油生产的技术进步和成本降低
燃料油生产的环保要求将越来越严格,需要不断改进生产工艺和设备
03
04
燃料油生产的市场竞争将更加激烈,需要不断提高产品质量和降低成本
煤液化和燃料油生产的水能等可再生能源,替代传统化石能源,降低对环境的影响。
01
02
煤液化可以生产化工原料,如乙烯、丙烯、苯等
煤液化可以生产清洁能源,如氢气、天然气等
03
04
煤液化可以减少对环境的污染,降低温室气体排放
燃料油的生产
原料:煤炭、水、氧气
产品:燃料油、化工原料、电力
应用:工业、交通、民用等领域
过程:煤的液化、裂解、精制
煤液化的优势和局限性
05
煤液化的优势
提高煤炭利用率:煤液化可以将煤炭转化为液体燃料,提高煤炭的利用率。
减少环境污染:煤液化过程中,可以减少硫、氮等有害物质的排放,降低环境污染。
提高能源安全性:煤液化可以减少对进口石油的依赖,提高国家的能源安全性。
促进煤炭产业发展:煤液化可以带动煤炭产业的发展,提高煤炭产业的附加值。
煤液化的局限性
设备投资大:煤液化需要大型设备,投资成本较高
提高能源利用效率:通过技术创新和优化工艺流程,提高能源利用效率,降低生产成本。
减少环境污染:采用环保技术和设备,减少废气、废水、废渣等污染物的排放,实现绿色生产。
提高产品质量:通过技术创新和严格质量控制,提高煤液化和燃料油产品的质量,满足市场需求。
感谢观看
汇报人:
添加标题
煤的液化:通过加压、加热等方式将煤转化为液态燃料
添加标题
液化产物的分离和净化:将液化产物中的有害物质去除,提高燃料油的质量
煤制油调研报告

煤制油调研报告一、背景介绍煤制油是指利用煤炭作为原料,通过化学反应将煤转化成油品的过程。
由于煤炭资源丰富,煤制油成为解决能源问题和碳排放问题的重要途径之一。
本调研报告旨在了解煤制油的发展现状、技术路线以及对环境和经济的影响。
二、煤制油技术路线煤制油的技术路线主要包括间接液化和直接液化两种方法。
1. 间接液化技术间接液化技术是指先将煤转化为合成气,再将合成气转化为液体燃料的过程。
这一技术路线采用多段反应器,包括气化、合成气制备、催化合成等步骤。
间接液化技术的优点是生产工艺成熟、设备稳定可靠,但是对煤质要求高,生产成本较高。
2. 直接液化技术直接液化技术是指将煤直接转化为液体燃料的过程。
这一技术路线主要包括溶剂解煤和兰斯曼气化两种方法。
直接液化技术的优点是对煤种适应性强,能够有效利用低质煤,但是生产工艺较复杂,设备投资较大。
三、煤制油发展现状目前,煤制油技术已经在中国取得了较大的发展。
我国拥有世界上最大的煤炭储量,因此发展煤制油具有优势。
中国采用的主要技术路线是间接液化技术,已经建设了多个煤制油基地,如山西阳煤化工公司的山西财团煤制油项目和内蒙古中国能源集团的内蒙古煤制油项目等。
这些项目不仅提高了能源供应的稳定性,还有利于优化煤炭结构,促进能源结构的升级。
四、煤制油的影响煤制油对环境和经济有着深远的影响。
1. 环境影响煤制油是一种高碳排放过程,会对大气环境造成污染。
煤制油过程中产生的二氧化碳等温室气体会加剧全球变暖的问题。
此外,煤制油会产生大量的固体废弃物和废水,对土壤和水源造成污染。
因此,在推进煤制油的发展过程中,必须加强环保措施,减少污染物排放,提高资源利用率。
2. 经济影响煤制油的发展对经济有着积极的影响。
煤制油能够提高我国的能源供应安全,减少对进口石油的依赖,降低能源价格波动对经济的冲击。
同时,煤制油也能够带动相关产业的发展,创造就业机会,促进经济增长。
五、发展煤制油的建议为了更好地发展煤制油,以下是一些建议:1. 加强环境保护意识,采取有效的污染治理措施,减少煤制油对环境的影响。
煤炭液化技术包括煤炭直接液化和煤炭间接液化

成绩中国矿业大学2011 级本科课程考试试卷考试科目学科前沿讲座考试时间2014年12月学生姓名彭玉斌学生学号06112931所在院系化工学院任课教师周敏教授等多名教师题目:煤炭液化技术煤炭液化技术摘要;煤炭液化技术包括煤炭直接液化和煤炭间接液化,是属于洁净煤技术的一种。
文章简要论述了煤炭直接接液化技术和煤炭间接液化技术的化学反应机理和化学反应过程;回顾了液化技术的发展历史,国外煤液化技术的发展状况;介绍了我国煤碳液化的现状;展望今后煤炭液化的发展方向。
关键字:煤炭;直接液化;间接液化所谓煤炭液化是指,固体煤炭通过化学加工过程,使其转化成为液体燃料、化工原料和产品的先进洁净煤技术。
根据不同的加工路线,煤炭液化可分为直接液化和间接液化两大类。
1煤炭直接液化概述煤与石油都是由碳、氢、氧为主的元素组成的天然有机矿物燃料。
只是煤中氢含量及H/C原子比,较石油相比要低很多。
要将煤转化为液体产物,必须在适当的温度、氢压、溶剂和催化剂的条件下,将煤中的大分子裂解为小分子,进而加氢稳定,降低H/C原子比,从而得到液体产物。
1.1煤直接液化的化学反应一般认为煤直接液化的过程是煤在溶剂、催化剂和高压氢气存在下,随着温度的升高,煤开始在溶剂中膨胀形成胶体体系。
煤进行局部溶解,并发生煤有机质的分裂、解聚,同时在煤有机质与溶剂间进行氢分配,于350~400℃左右生成沥青质含量较高的高分子物质。
在此过程中主要发生煤的热解、自由基加氢稳定、自由基缩合以及氮、氧、硫元素杂元素的脱除等一系列反应。
其主要反应是自由基的生成和加氢稳定。
自由基稳定后可生成分子量小的馏分油,分子量大的沥青烯,及分子量更大前沥青烯。
前沥青烯可进一步分解为分子量较小的沥青烯、馏分油和烃类气体。
同样沥青烯通过加氢可进一步生成馏分油和烃类气体。
如果煤的自由基得不到氢而它的浓度又很大时,这些自由基碎片就会互相结合而生成分子量更大的化合物甚至生成焦炭。
图1表示了煤热解产生自由基以及溶剂向自由基供氢、溶剂和前沥青烯、沥青烯加氢的过程:1.2煤直接液化技术的发展历程煤直接加氢液化一般是在较高温度,高压,氢气(或CO+H2, CO+H2O)、催化剂和溶剂作用下,将煤进行解聚、裂解加氢,直接转化为液体油的加工过程。
煤制油工艺

煤制油工艺煤制油也称煤液化,是以煤炭为原料生产液体燃料和化工原料的煤化工技术的简称。
一、煤炭液化的研究背景:⑴中国是一个富煤贫油少气的国家,而煤炭液化技术也将成为新型煤化工产业的重要方向之一;⑵在应对当今石油供需矛盾和贯彻节能减排政策中,煤炭液化不仅具有重大的环保意义,而且具有保障能源安全的战略意义。
二、煤液化技术通常有两种技术路线,即直接液化和间接液化。
1、煤炭的直接液化技术:⑴反应机理:⑵煤质要求:①煤化程度:煤化程度越深,加氢液化越难;高等挥发烟煤(长焰煤、气煤)和年轻褐煤是最适宜的液化原料,中等变质程度以上的很难液化;②煤岩组成:镜质组和壳质组是活性组分,易加氢液化,而惰质组难液化或根本不能液化;③矿物质组成及含量:矿物质的含量越低越好,5%左右最好,最大不超过10%;⑶催化剂的选择:①钴(Co)、钼(Mo)、镍(Ni):这类催化剂的催化活性较高。
但是这类金属催化剂的价格比较昂贵而且丢弃对污染比较严重,因此用后要回收;②金属卤化物:如ZnCl2、SnCl2等,属酸性催化剂,裂解能力强,但是对煤液化装置设备有较强的腐蚀作用;③铁系催化剂:包括含铁的天然矿石、含铁的工业残渣和各种纯态铁的化合物(如铁的氧化物、硫化物和氢氧化物)。
⑷供氢溶剂的作用:①提供和传递转移活性氢作用;②溶胀分散作用;③对煤粒热裂解生成的自由基起稳定保护作用;④溶解作用;⑤稀释液化产物作用。
⑸直接液化工艺:①德国IGOR工艺:该工艺以炼铝赤泥为催化剂,催化剂加入量为4%,不进行催化剂回收。
反应压力为30MPa,反应温度为465C。
现已完成0.2t/d和200t/d规模的试验研究。
采用减压蒸馏(即闪蒸)方法进行固一液分离,液化粗油不经降温而直接进行提质加工,将难以加氢的沥青质留在残渣中用作气化制氢的原料。
②日本NEDOL工艺:该工艺以黄铁矿为催化剂,催化剂加人量为4%,也不进行催化剂回收。
反应压力为19 MPa,反应温度为460℃。
煤间接液化制油技术探讨
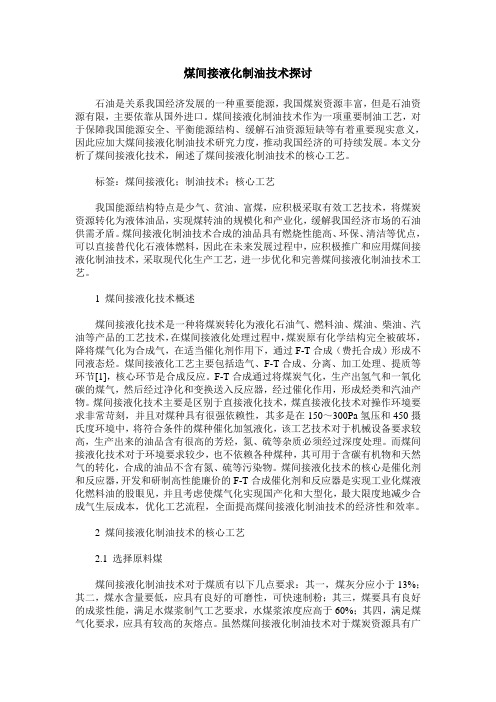
煤间接液化制油技术探讨石油是关系我国经济发展的一种重要能源,我国煤炭资源丰富,但是石油资源有限,主要依靠从国外进口。
煤间接液化制油技术作为一项重要制油工艺,对于保障我国能源安全、平衡能源结构、缓解石油资源短缺等有着重要现实意义,因此应加大煤间接液化制油技术研究力度,推动我国经济的可持续发展。
本文分析了煤间接液化技术,阐述了煤间接液化制油技术的核心工艺。
标签:煤间接液化;制油技术;核心工艺我国能源结构特点是少气、贫油、富煤,应积极采取有效工艺技术,将煤炭资源转化为液体油品,实现煤转油的规模化和产业化,缓解我国经济市场的石油供需矛盾。
煤间接液化制油技术合成的油品具有燃烧性能高、环保、清洁等优点,可以直接替代化石液体燃料,因此在未来发展过程中,应积极推广和应用煤间接液化制油技术,采取现代化生产工艺,进一步优化和完善煤间接液化制油技术工艺。
1 煤间接液化技术概述煤间接液化技术是一种将煤炭转化为液化石油气、燃料油、煤油、柴油、汽油等产品的工艺技术,在煤间接液化处理过程中,煤炭原有化学结构完全被破坏,降将煤气化为合成气,在适当催化剂作用下,通过F-T合成(费托合成)形成不同液态烃。
煤间接液化工艺主要包括造气、F-T合成、分离、加工处理、提质等环节[1],核心环节是合成反应。
F-T合成通过将煤炭气化,生产出氢气和一氧化碳的煤气,然后经过净化和变换送入反应器,经过催化作用,形成烃类和汽油产物。
煤间接液化技术主要是区别于直接液化技术,煤直接液化技术对操作环境要求非常苛刻,并且对煤种具有很强依赖性,其多是在150~300Pa氢压和450摄氏度环境中,将符合条件的煤种催化加氢液化,该工艺技术对于机械设备要求较高,生产出来的油品含有很高的芳烃,氮、硫等杂质必须经过深度处理。
而煤间接液化技术对于环境要求较少,也不依赖各种煤种,其可用于含碳有机物和天然气的转化,合成的油品不含有氮、硫等污染物。
煤间接液化技术的核心是催化剂和反应器,开发和研制高性能廉价的F-T合成催化剂和反应器是实现工业化煤液化燃料油的股眼见,并且考虑使煤气化实现国产化和大型化,最大限度地减少合成气生辰成本,优化工艺流程,全面提高煤间接液化制油技术的经济性和效率。
煤制油直接液化工艺技术剖析

煤制油直接液化工艺技术剖析摘要:煤制油主要以煤炭为原材料,通过化学加工处理之后而产生油品或石油化工类产品的一项技术。
煤制油包括两种工艺技术门类,一是煤制油直接液化工艺技术,二是煤制油间接液化工艺技术。
本文就煤制油直接液化工艺技术的形式及生产工艺过程作以论述,剖析在该项技术作用下的煤制油的工业化流程。
关键词:煤制油液化工艺技术剖析前言:煤制油直接液化技术与间接液化技术是两种不同风格的工艺技术路线,前者是将煤炭磨粉后经高温高压反应,而形成汽油、柴油燃料,该技术的工艺过程较为复杂;后者是将煤炭气体转化成为一种合成气体(一般为一氧化碳与氢气的混合气体),在经过合成技术将这些混合气体制作成为汽油、柴油燃料或化工原料等,该技术的发展及应用在上个世纪50年代就在南非发展起来,适合于多煤缺油的国家制造油类燃料时使用。
相比之下,煤制油直接液化工艺技术的发展潜力巨大。
一、煤制油直接液化工艺技术概述煤制油直接液化工艺技术的运作流程较为简单,首先,将质地良好的煤炭原料研磨成粉末状,再经过高温高压的技术处理,再加上催化加氢直接液化合成液态烃类物质燃料,通过一系列化学反应而除去硫离子、氧离子等活性物质,生产出汽油、柴油等燃料。
煤制油直接化工技术的操作限制内容较多,煤制油的环境对于煤炭种类的选择较严格,只有符合条件的煤炭才能生产出较低杂质的燃油[1]。
从实践中观察,煤制油直接液化工艺技术的特点及工艺制造的形式都较为复杂,而且煤制油工业化的技术还在不断的摸索中,距离技术成熟阶段还有很大一部分发展空间。
1.煤制油直接液化工艺技术的特点煤制油直接液化技术最早由德国引入国内,并逐步实现该技术的工业化。
煤制油直接液化工艺具有高温高压的技术特点,并且对于煤炭原料的种类要求极为苛刻。
只有将高质量的煤炭原料进行加工处理,才能制造出低杂质的汽油、柴油燃料。
可见,煤制油直接液化工艺技术的特点与一般的工业生产技术略有不同,需要在实践过程中不断摸索。
煤制油技术

谢谢指导
风险挑战
技术风险 资源问题 投资风险
煤制油有直接液化和 间接液化两种技术路 线,在全球范围内, 大规模工业化生产的 只有南非萨索尔公司 的间接液化技术,美 国、德国、日本均号 称拥有成熟的直接液 化技术,但均未有大 批量工业化生产的例 子。
资源要素主要包括煤 炭资源和水资源。煤 直接液化法生产一吨 油品需要煤炭3~4吨, 煤间接液化法生产一 吨油品需要煤炭5~7 吨。煤制油工艺需要 消耗大量的水,煤直 接液化法生产一吨油 品需要消耗8吨至9吨 水,Sasol公司所采 用的间接液化方式, 耗水量更是直接液化 法的1.5倍。
资源储备
中国2003-2012能源消费结构
中国各种一次能源消费的百分率 (%)
中国总的能源特征是“富煤、少油、有气”,与之对应的是煤炭在能源消费结 构中占主导,然而煤炭的燃烧引起了严重的环境污染,对煤炭的进一步加工处理使 用已迫在眉睫。
中国能源 元化消费的最佳选择。2
神华鄂尔多斯百万吨煤制油项目工艺流程
技术发展
国内发展
中国中科院山西煤化所从20世纪80年代开始进行铁基、 钴基两大类催化剂费-托合成油煤炭间接液化技术研究及 工程开发,完成了2000吨/年规模的煤基合成油工业实验, 5吨煤炭可合成1吨成品油。目前世界上可以通过”煤制 油”技术合成高品质柴油的只有南非等少数国家。山西 煤化所优质清洁柴油的问世,标志着我国已具备了开发 和提供先进成套产业化自主技术的能力,并成为世界上 少数几个拥有可将煤变为高清洁柴油全套技术的国家之 一。
无论是Sasol公司或 者Shell公司技术, 最大优点是成熟可靠, 而缺点是引进费用高, 使项目总体造价可能 大幅度上升(估计 ﹥15%);相反,采用 国内自主研发技术最 大缺点是,工程放大 存在一定风险,放大 倍数越大,风险也越 大,好处是项目总体 造价可以大幅降低。
煤直接和间接液化生产燃料油技术

煤直接和间接液化生产燃料油技术摘要:我国是煤资源丰富而石油资源相对短缺的国家。
随着国民经济的快速发展,我国对油品的需求持续增长,导致了原油进口量的逐年递增,2001年进口原油已占我国原油加工总量的近三分之一,这不仅消耗了大量外汇,也使得国民经济对进口原油的依赖性增加,对我国的国家能源安全构成了威胁。
关键词:煤;直接;间接;液化生产;燃料油1 发展历程1.1 煤直接液化技术煤直接液化技术始于二十世纪初,1913年德国科学家首先研究了煤高压加氢,并获得了世界上第一个煤液化专利,在此基础上开发了著名的1GFarben工艺。
该工艺反应条件较为苛刻,反应温度为470℃,反应压力为70MPa。
1927年德国在建立了世界上第一个规模为0.1Mt/a的煤直接液化厂,到第二次世界大战结束时,德国的18个煤直接液化工厂总油品生产能力已达约4.23Mt/a,其汽油产量占当时德国汽油消耗量的50%。
第二次世界大战前后,英国、美国、日本、法国、意大利、苏联等国也相继进行了煤直接液化技术的研究。
以后由于廉价石油的大量发现,从煤生产燃料油变得无利可图,煤直接液化工厂停工,煤直接液化技术的研究处于停顿状态。
20世纪70年代,石油危机发生后,各发达国家投入大量人力物力进行煤直接液化技术的研发,相继开发出多种煤直接液化工艺,但由于从20世纪80年代后期起原油价格在高位维持的时间不长,从煤生产燃料油获利的可能性较低,这些工艺都没有实现工业化。
1.2 煤间接液化技术1923年德国科学家FanrsiFseher和HansTorp-csh发明了将合成气经催化转化为液态烃的方法,简称F一T合成。
1936年德国建成世界上第一座煤间接液化工厂,到二战结束时,在德国、法国、日本、中国和美国等共建了16套以煤基合成气为原料的合成油装置。
二战以后由于廉价石油的大量发现,从煤生产液体燃料成本变得过高,这些装置先后停产。
20世纪50年代,南非联邦受到国际制裁,无法进口石油,为满足对燃料油的需求,根据本国煤的特点,发展了煤间接液化生产燃料油的技术。
煤炭液化的工艺

煤炭液化的工艺煤的液化是先进的洁净煤技术和煤转化技术之一,是用煤为原料以制取液体烃类为主要产品的技术。
煤掖化分为“煤的直接液化”和“煤的间接液化”两大类。
煤直接液化煤在氢气和催化剂作用下,通过加氢裂化转变为液体燃料的过程称为直接液化。
裂化是一种使烃类分子分裂为几个较小分子的反应过程。
因煤直接液化过程主要采用加氢手段,故又称煤的加氢液化法。
煤的间接液化是以煤基合成气(CO+ 2H )为原料,在一定的温度和压力下,定向催化合成烃类燃料油和化工原料的工艺,包括煤气化制取合成气及其净化、变换、催化合成以及产品分离和改质加工等过程。
通过煤炭液化,不仅可以生产汽油、柴油、LPG(液化石油气)、喷气燃料,还可以提取BTX(苯、甲苯、二甲苯),也可以生产制造各种烯烃及含氧有机化合物。
煤炭液化可以加工高硫煤,硫是煤直接液化的助催化剂,煤中硫在气化和液化过程中转化成硫化氢再经分解可以得到元素硫产品。
2.1直接液化的基本原理2.1.1 反应机理大量研究证明,煤在一定温度、压力下的加氢液化过程基本分为三大步骤,首先,当温度升至300℃以上时,煤受热分解,即煤的大分子结构中较弱的桥键开始断裂,打碎了煤的分子结构,从而产生大量的以结构单元分子为基体的自由基碎片,自由基的相对分子质量在数百范围。
第二步,在具有供氢能力的溶剂环境和较高氢气压力的条件下,自由基被加氢得到稳定,成为沥青烯及液化油的分子。
能与自由基结合的氢并非是分子氢,而应是氢自由基,即氢原子,或者是活化氢分子,氢原子或活化氢分子的来源有:①煤分子中碳氢键断裂产生的氢自由基;②供氢溶剂碳氢键断裂产生的氢自由基;③氢气中的氢分子被催化剂活化;④化学反应放出的氢,如系统中供给(2CO+H O ),可发生变换反应(222CO+H O CO +H )放出氢。
当外界提供的活性氢不足时,自由基碎片可发生缩聚反应和高温下的脱氢反应,最后生成固半焦或焦炭。
第三步,沥青烯及液化油分子被继续加氢裂化生成更小的分子。
煤制油

煤制油煤制油包括直接液化和间接液化两种工艺技术路线。
1.煤炭直接液化技术煤在高压和一定温度下直接与氢气反应生成液体燃料油的工艺技术称为直接液化。
煤炭直接液化主要产品为汽油、柴油、航空煤油、石脑油、LPG(液化石油气),另外还可以提取BTX(苯、甲苯、二甲苯),副产品有硫磺、氨或尿素等。
直接液化工艺的产品中,柴油的比例在60~70%,汽油和LPG占40~30%左右。
直接液化的工艺主要有Exxon供氢溶剂法(EDS)。
氢-煤法等。
EDS法是煤浆在循环的供氢溶剂中与氢混合,溶剂首先通过催化器,拾取氢原子,然后通过液化反应器,释放出氢原子,使煤分解。
氢-煤法是采用沸腾床反应器,直接加氢将煤转化成液体燃料。
直接液化过程流程现代煤炭直接液化技术提高了产品质量,特别是通过液化后的提质加工工艺,使液化油通过加氢精制、重整、加氢裂化,可得到合格的汽油、柴油或航空煤油。
尤其是柴油的凝点很低,可以在高寒地区使用,所得航空煤油的比重较大,同样容积的油箱可使飞机的续航距离增加。
2. 煤炭间接液化技术间接液化是把煤炭先气化再合成,煤在高温下与氧气和水蒸气反应生成合成反应气(CO+H2),合成反应气再经F-T合成催化反应合成液体燃料及其化学品。
煤炭间接液化主要产品为汽油、柴油、航空煤油、石脑油、LPG、以及乙烯、丙稀等重要化工原料,副产品有α烯烃、硬蜡、氨、醇、酮、焦油、硫磺、煤气等。
间接液化的产品品种是可以变通的,即可以生产油品,又可以根据市场需要加以调节,生产高附加值、价格高、市场紧缺的化工产品。
对中国的石油产品市场而言,以优质石脑油和高质量柴油、烯烃、LPG 和石蜡等产品为好。
另外烯烃的价值较高,LPG也是市场紧俏物资。
此外我国石蜡生产和销售市场上,高熔点微晶蜡缺口较大,高品位润滑油也是国内比较紧缺的。
因此,汽油、柴油与高附加值的润滑油、微晶蜡等市场紧缺的产品并举,可以作为合成油产品的主攻方向。
间接液化在可控制的条件下进行合成,获得的柴油的十六烷值达70,且低硫、无芳烃,既可直接供给环保要求高的地区使用,也可作为优质油与其它油品调配。
现代煤化工新技术

现代煤化工新技术随着世界能源消费量的不断增加,煤炭作为一种重要的化石能源,一直扮演着重要的角色。
然而,传统的煤炭化工过程还存在着许多问题,如排放量大、能源利用率低、资源浪费等。
为此,煤炭化工领域的科学家和工程师一直在探索和研究新的技术和方法,降低煤炭化工过程的成本和环境影响,提高能源利用效率。
以下将介绍几种现代煤化工新技术。
1.煤间接液化技术煤间接液化技术是一种将煤转化为液体燃料的方法,通过间接液化将煤转化为燃油、柴油等燃料。
这种技术可以大幅度降低煤的排放量,使得煤成为一种十分可持续的能源形式。
目前,美国、日本等国家的研究机构都在推动这一技术的发展。
2.煤直接液化技术煤直接液化技术是一种将煤转化为液态燃料的方法。
这种技术可以在较低温度和压力下将煤转化为液态燃料,比传统方法更为高效。
但是,这种技术需要大量的煤来转化为液态燃料,同时还需要大量的水和氢气。
因此,这种技术在现阶段还需要更多的研究和改进。
3.煤气化技术煤气化技术是一种将煤转化为气体燃料的方法。
它可以将煤中的碳转化为一种气体,称为合成气。
可以通过合成气来生产燃料、化学品和电力。
许多国家已经开始使用煤气化技术,因为它的产出比石油更为经济。
4.超临界水气化技术超临界水气化技术是一种将煤转化为液体燃料的方法。
超临界水是指在高温和高压下,水的状态不再是液态或气态。
这种技术可以在较短的时间内将煤转化为液体燃料,同时还可以降低污染物的排放。
目前,中国等国家的科学家正在探索和发展这种技术。
总结现代煤化工新技术的出现,不仅可以提高煤炭化工的环保性、效率,还可以促进能源行业的可持续发展。
虽然这些技术还存在一些问题和挑战,但是相信会有更多的煤化工科学家和实践者不断地探索和改进这些技术。
煤的液化和气化

煤的液化和气化煤的液化是先进的煤炭转化技术之一, 是以煤为原料制取液体烃类为主要产品的技术。
煤液化分为煤的直接液化和煤的间接液化两大类.一.煤炭直接液化是把煤直接转化成液体燃料,煤直接液化的操作条件苛刻,对煤种的依赖性强。
典型的煤直接液化技术是在400摄氏度、150个大气压左右将合适的煤催化加氢液化,产出的油品芳烃含量高,硫氮等杂质需要经过后续深度加氢精制才能达到目前石油产品的等级。
一般情况下,一吨无水无灰煤能转化成半吨以上的液化油。
煤直接液化油可生产洁净优质汽油、柴油和航空燃料。
但是适合于大吨位生产的直接液化工艺目前尚没有商业化,主要的原因是由于煤种要求特殊,反应条件较苛刻,大型化设备生产难度较大,使产品成本偏高。
煤直接液化煤在氢气和催化剂作用下,通过加氢裂化转变为液体燃料的过程称为直接液化。
裂化是一种使烃类分子分裂为几个较小分子的反应过程。
因煤直接液化过程主要采用加氢手段,故又称煤的加氢液化法。
二.煤间接液化是先把煤炭在高温下与氧气和水蒸气反应,使煤炭全部气化、转化成合成气(一氧化碳和氢气的混合物),然后再在催化剂的作用下合成为液体燃料的工艺技术。
间接液化首先将原料煤与氧气、水蒸汽反应将煤全部气化,制得的粗煤气经变换、脱硫、脱碳制成洁净的合成气(CO+H2),合成气在催化剂作用下发生合成反应生成烃类,烃类经进一步加工可以生产汽油、柴油和LPG等产品。
特点在煤炭液化的加工过程中,煤炭中含有的硫等有害元素以及无机矿物质(燃烧后转化成灰分)均可脱除,硫还可以硫磺的形态得到回收,而液体产品品质较一般石油产品更优质。
编辑本段煤间接液化技术的发展70 年代以后, 德国、美国、日本等主要工业发达国家, 为提高效率、降低生成成本, 相继开发了许多我国煤炭直接液化技术的开发研究为了解决我国石油短缺的问题, 寻求廉价生产人造石油的有效途径, 我国自1980 年重新开展煤炭直接液化技术研究。
在煤炭科学研究总院北京煤化学研究所建成具有先进水平的煤炭直接液化、油品提质加工、催化剂开发和分析检验实验室, 开展了基础和技术研究, 取得了一批科研成果, 培养了一支技术队伍, 为深入进行工艺开发和筹建大型煤炭直接液化生产厂奠定了基础。
煤间接液化与直接液化技术的比较及缺点

煤间接液化与直接液化技术的比较及缺点一.煤间接液化介绍煤的间接液化技术是先将煤全部气化成合成气,然后以合成气为原料,在一定温度、压力和催化剂存在下,通过F-T合成为烃类燃料油及化工原料和产品的工艺。
包括煤气化制取合成气、催化合成烃类产品以及产品分离和改制加工等过程。
煤炭间接液化技术主要有南非的萨索尔(Sasol)费托合成法、美国的Mobil(甲醇制汽油法)和荷兰SHELL的中质馏分合成(SMDS)间接液化工艺。
F-T合成的特点是:合成条件较温和,无论是固定床、流化床还是浆态床,反应温度均低于350℃,反应压力2.0-3.0MPa;转化率高,如SASOL 公司SAS工艺采用熔铁催化剂,合成气的一次通过转化率达到60%以上,循环比为2.0时,总转化率即达90%左右。
二.煤直接液化介绍煤的直接液化是煤在适当的温度和压力下,催化加氢裂化生成液体烃类及少量气体烃,脱除煤中氮、氧和硫等杂原子的转化过程。
煤化工监理目前国内外的主要工艺有:1.美国HTI工艺该工艺是在两段催化液化法和H-COAL工艺基础上发展起来的,采用近十年来开发的悬浮床反应器和HTI拥有专利的铁基催化剂(GelCatTM)。
反应温度420~450℃,反应压力17MPa;采用特殊的液体循环沸腾床反应器,达到全返混反应器模式;催化剂是采用HTI专利技术制备的铁系胶状高活性催化剂。
在高温分离器后面串联一台加氢固定床反应器,对液化油进行在线加氢精制。
2.日本NEDOL工艺该工艺由煤前处理单元、液化反应单元、液化油蒸馏单元及溶剂加氢单元等4个主要单元组成。
反应压力17M~19MPa,反应温度为430~465℃;催化剂采用合成硫化铁或天然硫铁矿。
离线加氢方式3.德国煤液化新工艺(IGOR工艺)1981年,德国鲁尔煤矿公司和费巴石油公司对最早开发的煤加氢裂解为液体燃料的柏吉斯法进行了改进,建成日处理煤200吨的半工业试验装置,操作压力由原来的70MPa降至30MPa,反应温度450~480℃,固液分离改过滤、离心为真空闪蒸方法,将难以加氢的沥青烯留在残渣中气化制氢,轻油和中油产率可达50%。
煤炭加工中的煤炭液化技术及应用

政策支持与推动煤炭液化技术发展的建议
柴油等。
煤炭液化与生物 质能技术的结合: 利用煤炭液化技 术生产生物质能 产品,如生物柴 油、生物乙醇等。
煤炭液化与氢能 技术的结合:利 用煤炭液化技术 生产氢能产品, 如氢气、氢燃料
电池等。
煤炭液化与碳捕 获与封存技术的 结合:利用煤炭 液化技术生产低 碳产品,如二氧 化碳、甲烷等。
添加标题
添加标题
航空燃料:煤炭液化技术可以生产出高热值、低挥发性的航空燃料,提高飞行安全性。
船舶燃料:煤炭液化技术可以生产出低硫、低灰分的船舶燃料,降低船舶排放对环境的影响。
工业燃料:煤炭液化技术可以生产出高热值、低挥发性的工业燃料,提高工业生产效率。
间接液化燃料的应用
燃料电池:将煤炭液化燃 料转化为电能,用于电动 汽车、便携式电子设备等
领域。
航空燃料:将煤炭液化燃 料转化为航空燃料,用于 飞机燃料,降低对石油的
依赖。
化工原料:将煤炭液化 燃料转化为化工原料, 用于生产塑料、橡胶、
纤维等化工产品。
供热燃料:将煤炭液化燃 料转化为供热燃料,用于 家庭、商业和工业供热,
减少对天然气的依赖。
煤炭液化与其他技术的结合应用
煤炭液化与石油 化工技术的结合: 利用煤炭液化技 术生产石油化工 产品,如汽油、
法。
生物质液化法:通过生物质 气化、合成气净化、合成油 等步骤将生物质转化为液体 燃 料 , 如 瑞 典 Va t t e n f a l l
煤炭液化技术包括煤炭直接液化和煤炭间接液化

成绩中国矿业大学2011 级本科课程考试试卷考试科目学科前沿讲座考试时间2014年12月学生姓名彭玉斌学生学号06112931所在院系化工学院任课教师周敏教授等多名教师题目:煤炭液化技术煤炭液化技术摘要;煤炭液化技术包括煤炭直接液化和煤炭间接液化,是属于洁净煤技术的一种。
文章简要论述了煤炭直接接液化技术和煤炭间接液化技术的化学反应机理和化学反应过程;回顾了液化技术的发展历史,国外煤液化技术的发展状况;介绍了我国煤碳液化的现状;展望今后煤炭液化的发展方向。
关键字:煤炭;直接液化;间接液化所谓煤炭液化是指,固体煤炭通过化学加工过程,使其转化成为液体燃料、化工原料和产品的先进洁净煤技术。
根据不同的加工路线,煤炭液化可分为直接液化和间接液化两大类。
1煤炭直接液化概述煤与石油都是由碳、氢、氧为主的元素组成的天然有机矿物燃料。
只是煤中氢含量及H/C原子比,较石油相比要低很多。
要将煤转化为液体产物,必须在适当的温度、氢压、溶剂和催化剂的条件下,将煤中的大分子裂解为小分子,进而加氢稳定,降低H/C原子比,从而得到液体产物。
1.1煤直接液化的化学反应一般认为煤直接液化的过程是煤在溶剂、催化剂和高压氢气存在下,随着温度的升高,煤开始在溶剂中膨胀形成胶体体系。
煤进行局部溶解,并发生煤有机质的分裂、解聚,同时在煤有机质与溶剂间进行氢分配,于350~400℃左右生成沥青质含量较高的高分子物质。
在此过程中主要发生煤的热解、自由基加氢稳定、自由基缩合以及氮、氧、硫元素杂元素的脱除等一系列反应。
其主要反应是自由基的生成和加氢稳定。
自由基稳定后可生成分子量小的馏分油,分子量大的沥青烯,及分子量更大前沥青烯。
前沥青烯可进一步分解为分子量较小的沥青烯、馏分油和烃类气体。
同样沥青烯通过加氢可进一步生成馏分油和烃类气体。
如果煤的自由基得不到氢而它的浓度又很大时,这些自由基碎片就会互相结合而生成分子量更大的化合物甚至生成焦炭。
图1表示了煤热解产生自由基以及溶剂向自由基供氢、溶剂和前沥青烯、沥青烯加氢的过程:1.2煤直接液化技术的发展历程煤直接加氢液化一般是在较高温度,高压,氢气(或CO+H2, CO+H2O)、催化剂和溶剂作用下,将煤进行解聚、裂解加氢,直接转化为液体油的加工过程。
煤的直接液化与间接液化技术进展

煤的直接液化与间接液化技术进展郭新乐(合肥学院,化学与材料工程系,安徽合肥230022)摘要:分析了煤液化技术在我国经济发展中的战略性意义,介绍了煤液化技术,包括直接液化技术,间接液化技术,展望了我国煤液化技术的发展方向并提出了建议。
关键词:煤液化技术;直接液化;间接液化Prospect of Direct Coal Liquefaction and Indirect Coal LiquefactionGUO Xin-Le(Department of Chemical and Mater ials Engineering, Hefei University, Anhui Hefei 230022,China)Abstract: This paper introduced the significance of the coal liquefaction technology in the development of economy. The coal liquefaction technology was then reviewed, including direct coal liquefaction and indirect coal liquefaction. Prospects were done, and the development direction of the coal liquefaction technology in China was suggested.Key words: coal liquefaction technology of; direct coal liquefaction; indirect coal liquefaction众所周知石油作为能源储备资源较煤炭少,且分布不均匀,石油供需矛盾日益突出。
我国富煤,贫油这一资源特点,决定了能源发展必然以煤为主,长期以来,煤炭在我国的能源消费结构中一直占70%以上。
- 1、下载文档前请自行甄别文档内容的完整性,平台不提供额外的编辑、内容补充、找答案等附加服务。
- 2、"仅部分预览"的文档,不可在线预览部分如存在完整性等问题,可反馈申请退款(可完整预览的文档不适用该条件!)。
- 3、如文档侵犯您的权益,请联系客服反馈,我们会尽快为您处理(人工客服工作时间:9:00-18:30)。
煤直接和间接液化生产燃料油技术
发表时间:2018-09-27T16:43:45.137Z 来源:《建筑模拟》2018年第18期作者:杨晓飞刘亚玲
[导读] 随着国民经济的快速发展,我国对油品的需求持续增长,导致了原油进口量的逐年递增,2001年进口原油已占我国原油加工总量的近三分之一,这不仅消耗了大量外汇,也使得国民经济对进口原油的依赖性增加,对我国的国家能源安全构成了威胁。
油煤新技术开发公司陕西榆林 718500
摘要:我国是煤资源丰富而石油资源相对短缺的国家。
随着国民经济的快速发展,我国对油品的需求持续增长,导致了原油进口量的逐年递增,2001年进口原油已占我国原油加工总量的近三分之一,这不仅消耗了大量外汇,也使得国民经济对进口原油的依赖性增加,对我国的国家能源安全构成了威胁。
关键词:煤;直接;间接;液化生产;燃料油
1 发展历程
1.1 煤直接液化技术
煤直接液化技术始于二十世纪初,1913年德国科学家首先研究了煤高压加氢,并获得了世界上第一个煤液化专利,在此基础上开发了著名的1GFarben工艺。
该工艺反应条件较为苛刻,反应温度为470℃,反应压力为70MPa。
1927年德国在建立了世界上第一个规模为0.1Mt/a 的煤直接液化厂,到第二次世界大战结束时,德国的18个煤直接液化工厂总油品生产能力已达约4.23Mt/a,其汽油产量占当时德国汽油消耗量的50%。
第二次世界大战前后,英国、美国、日本、法国、意大利、苏联等国也相继进行了煤直接液化技术的研究。
以后由于廉价石油的大量发现,从煤生产燃料油变得无利可图,煤直接液化工厂停工,煤直接液化技术的研究处于停顿状态。
20世纪70年代,石油危机发生后,各发达国家投入大量人力物力进行煤直接液化技术的研发,相继开发出多种煤直接液化工艺,但由于从20世纪80年代后期起原油价格在高位维持的时间不长,从煤生产燃料油获利的可能性较低,这些工艺都没有实现工业化。
1.2 煤间接液化技术
1923年德国科学家FanrsiFseher和HansTorp-csh发明了将合成气经催化转化为液态烃的方法,简称F一T合成。
1936年德国建成世界上第一座煤间接液化工厂,到二战结束时,在德国、法国、日本、中国和美国等共建了16套以煤基合成气为原料的合成油装置。
二战以后由于廉价石油的大量发现,从煤生产液体燃料成本变得过高,这些装置先后停产。
20世纪50年代,南非联邦受到国际制裁,无法进口石油,为满足对燃料油的需求,根据本国煤的特点,发展了煤间接液化生产燃料油的技术。
自1955年以来,陆续建立了3座大型煤间接液化厂,分别是Sasol工,assolll,aSsolm,产品包括发动机燃料、聚烯烃等。
目前Sasol公司的煤间接液化工厂仍在运行,并获得可观利润。
2 煤液化技术的工艺特征对比分析
2.1 煤液化工艺原理对比分析
2.1.1F-T合成
典型煤基F-T合成工艺包括:煤的气化及煤气净化、变换和脱碳:F-T合成反应;油品加工等3个纯“串联”步骤。
气体装置产出的粗煤气经除尘、冷却得到净煤气,净煤气经CO2宽温耐硫变换和酸性气体(包括H2S和CO2等)脱除,得到成分合格的合成气。
合成气进入合成反应器,在一定温度、压力及催化剂作用下,H2和CO2转化为直链烃类、水以及少量的含氧有机化合物。
生成物经三相分离,水相去提取醇、酮、醛等化学品;油相采用常规石油炼制手段(如常、减压蒸馏),根据需要切割出产品馏份,经进一步加工(如加氢精制、临氢降凝、催化重整、加氢裂化等工艺)得到合格的油品或中间的产品;气相经冷冻分离及烯烃转化处理得到LPG、聚合级丙烯、聚合级乙烯及中热值燃料气。
F-T合成的特点是:合成条件较温和,无论是固定床、流化床还是浆态床,反应温度均低于350℃,反应压力2.0-3.0MPa;转化率高,如SASOL公司SAS工艺采用熔铁催化剂,合成气的一次通过转化率达到60%以上,循环比为2.0时,总转化率即达90%左右。
2.1.2加氢液化
典型的煤直接加氢液化工艺包括:氢气制备、煤糊相(油煤浆)制备、加氢液化反应、油品加工“先串后并”4个步骤。
氢气制备是加氢液化的重要环节,可以采用煤气化、天然气转化及水电解等手段,但大规模制氢通常采用煤气化及天然气转化。
液化过程中,将煤、催化剂和循环油制成的煤浆,与制得的氢气混合送入反应器。
在液化反应器内,煤首先发生热解反应,生成自由基“碎片”,不稳定的自由基“碎片”再与氢在催化剂存在条件下结合,形成分子量比煤低得多的初级加氢产物。
出反应器的产物构成十分复杂,包括气、液、固三相。
气相的主要成分是氢气,分离后循环返回反应器重新参加反应;固相为未反应的煤、矿物质及催化剂;活这个相则为轻油(粗气油)、中油等馏份油及重油。
液相馏份油经提质加工(如加氢精制、加氢形裂化和重整)得到合格的汽油、柴油和航空煤油等产品。
重质的液固淤浆经进一步分离得到循环重油和残渣。
加氢液化的特点是:液化油收率高,例如采用HTI工艺,我国神华煤的油收率可高达63%-68%;煤消耗量小;馏份油以汽、柴油为主,目标产品的选择性相对较高;油煤浆进料,设备体积小,投资低,运行费用低;制氢方法有多种选择,无需完全信赖于煤的气化;反应条件相对较苛刻,现代工艺如IGOR、HTI、NEDOL等液化压力也达到17-30MPa,液化温度430-470℃;液化反应器的产物组成较复杂,液、固两相混合物由于粘度较高,分离相对困难,氢耗量大,一般在6%-10%,工艺过程中不仅要补充大量新氢,还需要循环油作供氢深剂,使装置的生产能力降低。
2.2 液化工艺对煤种的选择性对比
分析煤基间接液化工艺对煤种的选择性也就是与之相适应的气化工艺对煤种的选择性。
气化的目的是尽可能获取以合成气(CO+H2)为主要成分的煤气。
目前得到公认的最先进煤气化工艺是干煤粉气流床加压气化工艺,已实现商业化的典型工艺是荷兰Shell公司的SCGP工艺。
干煤粉气流床加压气化从理论上讲对原料有广泛的适应性,几乎可以气化从无烟煤到褐煤的各种煤及石油焦等固体燃料,对煤的活性没有要求,对煤的灰精密仪器融性适应范围可以很宽,对于高灰分、高水分、高硫分的煤种也同样适应。
2.3 液化产品的市场适应性对比分析
煤基间接液化产物分布较宽,如SASOL固定流化床工艺,C4以下产物约占总合成产物的44.1%;C5以上产物约占总合成产物的49.7%。
C4以下的气态烃类产物经分离及烯烃岐化转化得到LPG、聚合级丙烯、聚合级乙烯等终端产品。
C5以上液态产物经馏份切割得到石脑油、a-烯烃、C14-C18烷及粗蜡等中间产品。
石脑油经进一步加氢精制,得到高级乙烯料,也可以重整得到汽油a-烯烃不经提质处理就是高级洗涤剂原料,经提质处理得到航空煤油;C14-C18烷不经提质处理也是高品质的洗涤剂原料,通过加氢精制和异构降凝处理即成为高级调和柴
油(十六烷值高达75);粗蜡经加氢精制得到高品质软蜡。
加氢液化工艺的柴油收率在70%左右,LPG和汽油约占20%其余为以多环芳烃为主的中间产品。
由于加氢液化产物具有富含环烷烃的特点,因此,经提质处理及馏份切割得到的汽油及航空煤油均属于高质量终端产品。
另外,加氢液化产物也是生产芳烃化合物的重要原料。
实践证明,不少芳烃化合物通过非煤加氢液化途径获取往往较为困难,甚至不可能。
国内外的相关研究结果同样已经表明,基于不可逆转的石油资源形势和并不乐观的国际政治形势,在我国发展直接液化工艺,适宜定位在生产燃料油品及特殊中间化学品。
3 产品分布比较
根据煤质选择液化工艺是第一条必须遵守的原则,只有这样才能获得好的经济效益。
根据市场需求确定煤液化目标产品,根据目标产品选择煤液化工艺是第二条必须遵守的原则。
直接液化和间接液化的产品分布是不同的。
间接液化时,不同温度、催化剂的F-T工艺如低温浆态床、高温固定床、高温流化床,所得产品分布也是不同的。
相对来讲,高温流化床,可生产出附加值较高的石油化工产品群。
煤直接液化的目标产品主要是柴油、汽油或石脑油。
煤间接液化:(1)固定床液化工艺主要产品是汽油和重质柴油;(2)循环流化床液化工艺主要产品是汽油、烯烃(乙烯、丙烯、丁烯),乙烯、丙烯是最有价值的基本有机化工原料,可以综合加工利用;(3)浆态床液化工艺主要产品是柴油、石脑油、蜡;(4)SMDS中间馏分固定床工艺主要为汽油、石脑油,粗油不裂解可得到柴油和蜡。
总结:煤直接液化中NEDOL法和氢煤法对工艺条件要求差别不大,但NEDOL法的产品油未进行提质加工,导致产品质量低;而氢煤法采用沸腾床催化反应器,可以使催化剂更新和再生,从而使产品质量和产率分布保持恒定不变,操作得以简化。
参考文献:
[1]徐会军,刘治中.煤炭直接液化技术的发展[J].煤炭加工与综合利用,2003(4).
[2]郭树才.煤化学工程[M].北京:冶金工业出版社,1991.
[3]庞刚生.煤炭液化技术及其发展意义[J].科技情报开发与经济,2006(9).。