混流拉动模式的生产实践
一汽混合动力汽车技术路线及研发实践

节油效果 1 00%
低 动力总成的电动化 高
EV RE-EV
FC-EV
PHEV
30%
HEV
2010
2015
2020
电池技术成熟度
2025
2030
以以满满足足电电池池成成熟熟度度为为导导向向,,逐逐步步开开发发相相应应新新能能源源汽汽车车车车型型。。
1.1 混合动力汽车发展驱动力 — 能源紧张
4
1.混合动力汽车技术发展背景
1.1 混合动力汽车发展驱动力 — 市场需求
g/km
191
176
127
130
car/1000 persons
606 496
2011, CO2 Emissions / Car / km
439
455
2020 预计170 48
2011,Car population 中中国国乘乘用用车车单单车车二二氧氧化化碳碳排排放放高高,,乘乘用用车车千千人人保保有有量量低低;; 22002200年年,,中中国国汽汽车车千千人人保保有有量量预预计计上上升升到到117700,,中中国国汽汽车车工工业业将将面面临临更更严严峻峻的的loloww--ccaarrbboonn cchhaalllelennggee。。
17
3.一汽混合动力汽车技术开发
3.1 整车性能仿真技术
整车建模/性能仿真分析
整车总成仿真模型搭建 HCU仿真模型搭建 整车性能仿真 整车控制策略离线优化
动力系统构型平台开发
动力系统构型评价
先进动力系统构型研究 动力系统功能模式分析 构型评价指标研究 构型评价模型搭建
动力系统集成开发
关于国有企业混合所有制改革的实践与思考
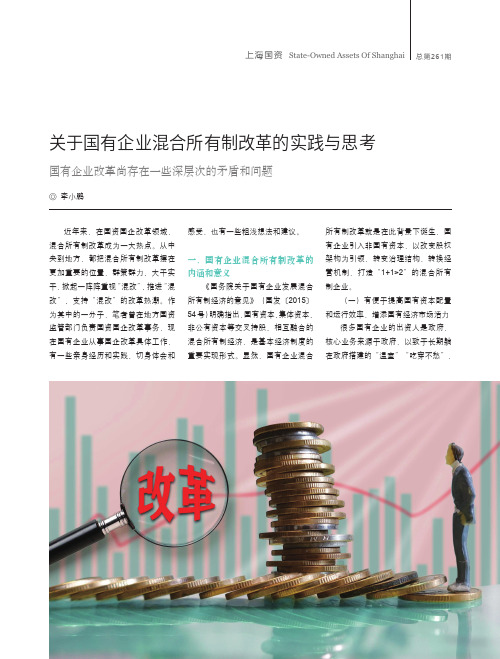
国有企业改革尚存在一些深层次的矛盾和问题◎ 李小鹏关于国有企业混合所有制改革的实践与思考近年来,在国资国企改革领域,混合所有制改革成为一大热点。
从中央到地方,都把混合所有制改革摆在更加重要的位置,群策群力、大干实干,掀起一阵阵重视“混改”、推进“混改”、支持“混改”的改革热潮。
作为其中的一分子,笔者曾在地方国资监管部门负责国资国企改革事务,现在国有企业从事国企改革具体工作,有一些亲身经历和实践、切身体会和感受,也有一些粗浅想法和建议。
一、国有企业混合所有制改革的内涵和意义《国务院关于国有企业发展混合所有制经济的意见》(国发〔2015〕54号)明确指出,国有资本、集体资本、非公有资本等交叉持股、相互融合的混合所有制经济,是基本经济制度的重要实现形式。
显然,国有企业混合所有制改革就是在此背景下诞生,国有企业引入非国有资本,以改变股权架构为引领,转变治理结构,转换经营机制,打造“1+1>2”的混合所有制企业。
(一)有便于提高国有资本配置和运行效率,增添国有经济市场活力很多国有企业的出资人是政府,核心业务来源于政府,以致于长期躺在政府搭建的“温室”“吃穿不愁”,慢慢成长为规模虽大但不经市场风浪考验的“巨婴”。
通过混合所有制改革,国有企业投身市场的汪洋大海,面对市场的竞争浪潮,倒逼自身适应市场变化,加强资本配置,提高运行效率,增强市场活力。
(二)有利于加强市场化资源整合和战略协同,增强国有企业竞争力受国有体制机制的影响,国有企业不可避免地带有较强的行政化特色,导致市场化程度不高、市场竞争力不强。
通过混合所有制改革,国有企业根据自身实际,引入产业链互补、价值观相近的战略投资者,吸收非公有制企业的资源、资金、技术、管理等方面的优势资源,取长补短、整合融合,进一步增强企业的核心竞争力。
(三)有助于加快国有经济布局优化和结构调整,扩大国有资本影响力国有企业在经济社会发展中具有中流砥柱的作用,但也存在行业分散、结构老化、存量资产多、沉淀资金多等问题。
精益管理如何实现拉动式生产
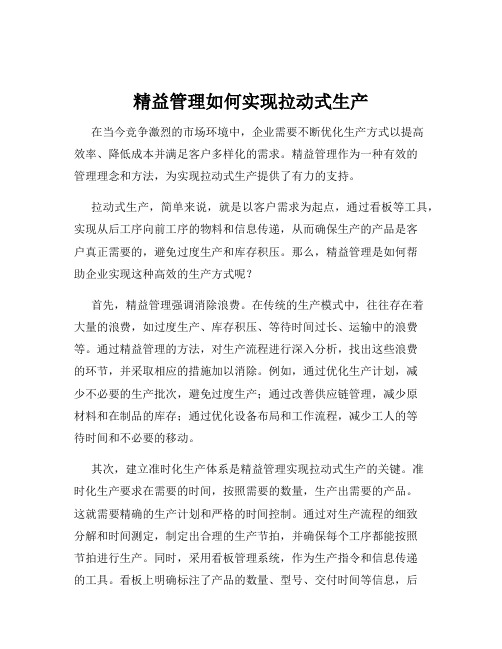
精益管理如何实现拉动式生产在当今竞争激烈的市场环境中,企业需要不断优化生产方式以提高效率、降低成本并满足客户多样化的需求。
精益管理作为一种有效的管理理念和方法,为实现拉动式生产提供了有力的支持。
拉动式生产,简单来说,就是以客户需求为起点,通过看板等工具,实现从后工序向前工序的物料和信息传递,从而确保生产的产品是客户真正需要的,避免过度生产和库存积压。
那么,精益管理是如何帮助企业实现这种高效的生产方式呢?首先,精益管理强调消除浪费。
在传统的生产模式中,往往存在着大量的浪费,如过度生产、库存积压、等待时间过长、运输中的浪费等。
通过精益管理的方法,对生产流程进行深入分析,找出这些浪费的环节,并采取相应的措施加以消除。
例如,通过优化生产计划,减少不必要的生产批次,避免过度生产;通过改善供应链管理,减少原材料和在制品的库存;通过优化设备布局和工作流程,减少工人的等待时间和不必要的移动。
其次,建立准时化生产体系是精益管理实现拉动式生产的关键。
准时化生产要求在需要的时间,按照需要的数量,生产出需要的产品。
这就需要精确的生产计划和严格的时间控制。
通过对生产流程的细致分解和时间测定,制定出合理的生产节拍,并确保每个工序都能按照节拍进行生产。
同时,采用看板管理系统,作为生产指令和信息传递的工具。
看板上明确标注了产品的数量、型号、交付时间等信息,后工序根据看板向前工序领取所需的零部件或产品,前工序则根据看板的需求进行生产补充。
再者,精益管理注重员工的参与和持续改进。
员工是生产过程的直接执行者,他们最了解生产中的问题和改进的机会。
因此,鼓励员工积极参与生产流程的优化和改进,提出合理化建议,并给予相应的奖励和认可。
通过建立小组活动、质量圈等形式,让员工共同探讨解决生产中的问题,不断优化生产流程和方法。
持续改进是精益管理的核心思想之一,只有不断地发现问题、解决问题,才能使生产系统更加高效、灵活地适应市场的变化和客户的需求。
具有无序工序生产特征的混合柔性流水车间在线调度
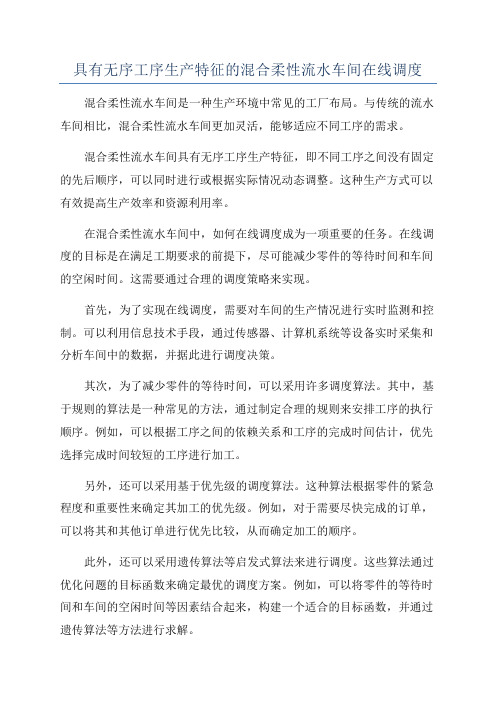
具有无序工序生产特征的混合柔性流水车间在线调度混合柔性流水车间是一种生产环境中常见的工厂布局。
与传统的流水车间相比,混合柔性流水车间更加灵活,能够适应不同工序的需求。
混合柔性流水车间具有无序工序生产特征,即不同工序之间没有固定的先后顺序,可以同时进行或根据实际情况动态调整。
这种生产方式可以有效提高生产效率和资源利用率。
在混合柔性流水车间中,如何在线调度成为一项重要的任务。
在线调度的目标是在满足工期要求的前提下,尽可能减少零件的等待时间和车间的空闲时间。
这需要通过合理的调度策略来实现。
首先,为了实现在线调度,需要对车间的生产情况进行实时监测和控制。
可以利用信息技术手段,通过传感器、计算机系统等设备实时采集和分析车间中的数据,并据此进行调度决策。
其次,为了减少零件的等待时间,可以采用许多调度算法。
其中,基于规则的算法是一种常见的方法,通过制定合理的规则来安排工序的执行顺序。
例如,可以根据工序之间的依赖关系和工序的完成时间估计,优先选择完成时间较短的工序进行加工。
另外,还可以采用基于优先级的调度算法。
这种算法根据零件的紧急程度和重要性来确定其加工的优先级。
例如,对于需要尽快完成的订单,可以将其和其他订单进行优先比较,从而确定加工的顺序。
此外,还可以采用遗传算法等启发式算法来进行调度。
这些算法通过优化问题的目标函数来确定最优的调度方案。
例如,可以将零件的等待时间和车间的空闲时间等因素结合起来,构建一个适合的目标函数,并通过遗传算法等方法进行求解。
总之,具有无序工序生产特征的混合柔性流水车间的在线调度是一项复杂而重要的任务。
通过合理的调度策略和算法,可以有效提高车间的生产效率和资源利用率,从而实现优化的生产调度。
推行混流拉动式生产方式大幅提高生产能力
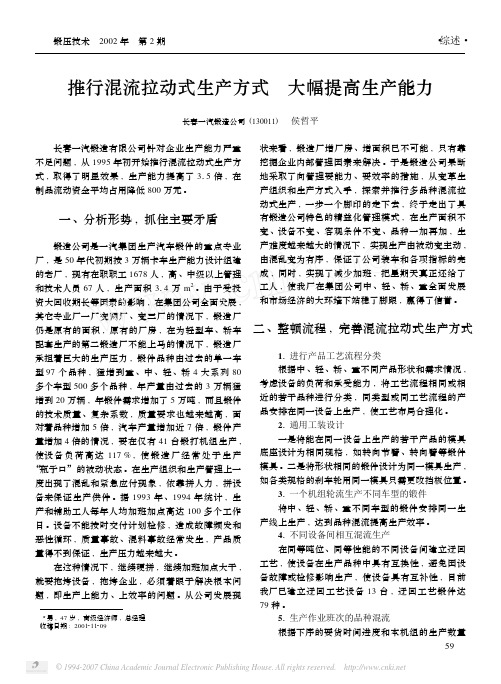
锻压技术 2002年 第2期・综述・推行混流拉动式生产方式 大幅提高生产能力长春一汽锻造公司(130011) 侯哲平3男,47岁,高级经济师,总经理收稿日期:2001211209 长春一汽锻造有限公司针对企业生产能力严重不足问题,从1995年初开始推行混流拉动式生产方式,取得了明显效果,生产能力提高了315倍,在制品流动资金平均占用降低800万元。
一、分析形势,抓住主要矛盾锻造公司是一汽集团生产汽车锻件的重点专业厂,是50年代初期按3万辆卡车生产能力设计组建的老厂,现有在职职工1678人,高、中级以上管理和技术人员67人,生产面积314万m 2。
由于受投资大回收期长等因素的影响,在集团公司全面发展,其它专业厂一厂变两厂、变三厂的情况下,锻造厂仍是原有的面积,原有的厂房,在为轻型车、轿车配套生产的第二锻造厂不能上马的情况下,锻造厂承担着巨大的生产压力,锻件品种由过去的单一车型97个品种,猛增到重、中、轻、轿4大系列80多个车型500多个品种,年产量由过去的3万辆猛增到20万辆,年锻件需求增加了5万吨,而且锻件的技术质量、复杂系数,质量要求也越来越高,面对着品种增加5倍,汽车产量增加近7倍,锻件产量增加4倍的情况,要在仅有41台锻打机组生产,使设备负荷高达117%,使锻造厂经常处于生产“瓶子口”的被动状态。
在生产组织和生产管理上一度出现了混乱和紧急应付现象,依靠拼人力,拼设备来保证生产供件。
据1993年、1994年统计,生产和辅助工人每年人均加班加点高达100多个工作日。
设备不能按时交付计划检修,造成故障频发和恶性循环,质量事故、混料事故经常发生,产品质量得不到保证,生产压力越来越大。
在这种情况下,继续硬拼,继续加班加点大干,就要拖垮设备,拖垮企业,必须着眼于解决根本问题,即生产上能力、上效率的问题。
从公司发展现状来看,锻造厂增厂房、增面积已不可能,只有靠挖掘企业内部管理因素来解决。
于是锻造公司果断地采取了向管理要能力、要效率的措施,从变革生产组织和生产方式入手,探索并推行多品种混流拉动式生产,一步一个脚印的走下去,终于走出了具有锻造公司特色的精益化管理模式,在生产面积不变、设备不变、客观条件不变、品种一加再加,生产难度越来越大的情况下,实现生产由被动变主动,由混乱变为有序,保证了公司装车和各项指标的完成,同时,实现了减少加班,把星期天真正还给了工人,使我厂在集团公司中、轻、轿、重全面发展和市场经济的大环境下站稳了脚跟,赢得了信誉。
混流生产线物料索取系统的设计及实现

键技 术进 行 了详 细 的 阐 述 。该 物 料 索 取 系统 已应 用 于某 企 业 装 配 生 产 线 . 试 运行 结果 表 明 物料 配送 效 率 得 到 显 著提 高 关键 词 : 物 料 索取 系统 ; 电子 看板 ; B / S ; C / S ; . N E T 框架 中 图分 类 号 : T P 3 1 1 文献 标 志 码 : A
ቤተ መጻሕፍቲ ባይዱ
ma t e i r a l r e q u i r e me n t i n s t r u c t i o n s d i r e c t l Y .I t wa s d e s i g n e d a n d i mp l e me n t e d a ma t e r i a l c l a i m s y s t e m b a s e d o n B / S a n d C / S mi x e d mo d e, a n d t h e s y s t e m’ S mo d e l i n g , f u n c t i o n s a s w e l l a s t h e k e y t e c h n o l o g i e s we r e d e s c i r b e d i n d e t a i l . T h e s y s t e m h a s b e e n p u t i n t o p r a c t i c e i n o n e a s s e mb l i n g i n d u s t r y, a n d t r i a l i u n r e s u l t s s h o w t h a t t h e e ic f i e n c y o f ma t e r i a l d i s t ib r u t i o n h a s b e e n s i g n i i f c a n t l y i mp r o v e d . Ke y wo r d s : ma t e r i a l c l a i m s y s t e m; e - Ka n b a n ; B / S; C / S; NE T f r a me w o r k
拉动式生产实施方案

拉动式生产实施方案拉动式生产是一种以顾客需求为导向的生产方式,它强调的是按需生产,避免库存浪费,提高生产效率和产品质量。
在当前市场竞争激烈的环境下,企业需要不断优化生产方式,提高生产效率,以满足客户需求。
因此,制定一套科学的拉动式生产实施方案对于企业的发展至关重要。
首先,实施拉动式生产需要建立一个完善的信息系统。
信息系统是拉动式生产的核心,它能够实时掌握市场需求,及时调整生产计划,避免过剩生产和库存积压。
企业可以利用先进的信息技术,建立起供应链管理系统,实现从供应商到生产线再到客户的信息共享和协同,实现生产的精细化管理。
其次,拉动式生产需要优化供应链管理。
供应链管理是拉动式生产的重要保障,它能够确保原材料和零部件的及时供应,减少生产过程中的等待时间和浪费,提高生产效率。
企业可以与供应商建立长期稳定的合作关系,共同制定供应计划,减少因供应不稳定而导致的生产中断和延误。
另外,拉动式生产需要加强生产过程的标准化和稳定性。
通过对生产流程的优化和改进,企业可以实现生产过程的标准化,减少因操作失误和变动而导致的生产质量问题,提高产品的一致性和稳定性。
同时,企业还可以采用先进的生产设备和技术,提高生产效率和产品质量,降低生产成本。
最后,拉动式生产需要建立一套科学的绩效考核体系。
绩效考核是推动拉动式生产持续改进和优化的重要手段,它能够激励员工积极参与生产过程,并对生产效率和产品质量进行监控和评估。
企业可以建立基于绩效的薪酬体系,激励员工提高生产效率和质量,同时还可以通过绩效考核结果对生产过程进行持续改进和优化。
总之,实施拉动式生产需要全面考虑生产过程中的各个环节,建立起完善的信息系统,优化供应链管理,加强生产过程的标准化和稳定性,建立科学的绩效考核体系。
只有这样,企业才能实现按需生产,提高生产效率和产品质量,保持竞争优势,实现可持续发展。
精益生产管理实践之四

– 在产品基本型的基础上,改动少量零部件,形成各 种变型产品,用以满足不同需求。
– 由于基型与各种变型之间存在大量通用件,生产过 程相对可以简化。
• (二)模块化设计 • (三)设计时应考虑易实现生产自动化
– 使装配过程由一系列挑选——放置操作来完成,以 便实现装配自动化。
• “一个流”生产是同步化生产的高级形式,它 是指在生产线内任何两道工序间流的在制品数 不得超过紧前工序的装夹数。一般流动的在制 品为一件,简称“一个流”。实现“一个流” 生产,要求生产必须按节拍进行,按标准操作 规程操作。
二、看板管理
(一)看板及其在生产现场控制中 的应用
• 看板管理是一种生产现场物流控制系统,它是 通过看板的传递或运动来控制物流的一种方法。
• (四)新设计的产品尽量采用通用件、标准件 或采用通用设备、通用工具生产的零部件
二、均衡化生产
• 达到准时生产,其基础为均衡化生产
– 物流在各作业之间、生产线之间,工序之间,工厂 之间平稳、均衡地流动。
• 关键是缩短作业准备时间,减少加工批量整个 生产过程就越接近于流水状态。
• 而多品种、成批轮番生产
• 车、磨。。。 • 装配 • 喷漆
• 费增值:
– 如何花费时间、材料或空间,但不改变材 料的活动
• 分拣、堆放 • 盘点 • 检验
Value-Adding / Non-Value传统的批A量d生d产ing
增值
95 % NVA
5%
订单
发运
Total Lead Time to Customer
Order
5% VA
大多数流程改造关注于 Teams Attack this . . .
- 1、下载文档前请自行甄别文档内容的完整性,平台不提供额外的编辑、内容补充、找答案等附加服务。
- 2、"仅部分预览"的文档,不可在线预览部分如存在完整性等问题,可反馈申请退款(可完整预览的文档不适用该条件!)。
- 3、如文档侵犯您的权益,请联系客服反馈,我们会尽快为您处理(人工客服工作时间:9:00-18:30)。
混流拉动模式的生产实践
原创:张齐文
“纸上得来终觉浅,绝知此事要躬行”。
对于知识,学说和技能而言,听闻,了解,理解,掌握和应用分别代表着不同的认知等级,并且不同等级之间的鸿沟远比字面上的差别难以逾越。
在精益生产或TPS中,拉动生产无疑是其最为核心的生产形式,所以可以相当肯定的说,掌握拉动生产的内核并进行恰如其分的应用是精益生产进击过程中的必修课。
所以,也就不难理解很多公司在初步了解过拉动生产,看板管理后就在精益生产的大门前急不可耐,跃跃欲试。
但事实上,了解拉动生产一点也不高大上,对拉式和推式的长短优劣如数家珍也并不能证明就已取得真经。
对于所有的应用性科学来说,恰如其分,妙到毫巅的应用才是真正的王道。
比如,核裂变,核聚变的原理现在只要你肯上网并且恰巧还识字,小学生也能了解到其真正的原理,但要做到无毒无风险的恰当应用却几乎需要一个国家的科技和工业实力来担当。
对于拉动式生产来说,其理念是普适的,洞彻其原理及基本原则也不会太难(只要沉下心去学习和思考)。
但是,要做到在该应用的地方恰如其分的应用,却是需要千锤百炼的真功夫和取舍得当的大智慧。
所谓”知易行难”,这话不是没有道理的。
比如,你捣鼓半天,非要在年采购额不过30-50元的手工针上较劲,这又有什么现实的经济意义呢?
我不反对内部的物料流转采用拉动方式,但不建议为这点金额去跟供应商谈什么拉动。
有这闲功夫,还不如直接改善内部拉动的批量来得直接和有效果。
1、拉动模式的简单模型
所谓简单模型,通常指一个连续流同一个时间段只生产一种产品。
这通常意味着某单一产品的产量还比较客观,同时因为产品或(和)过程特性的原因,制造过程有一定针对性甚至一定程度的定制化。
有一种情况是,同一条生产线稍作调整的情况下就可以适用多种产品。
在这种情况下,具有一定水准的公司会实行混合生产,但对于一些从未实施过精益生产或TPS
的工厂和组织来说,大部分在起始阶段还是先按照同一时间段只生产一种产品,完成后再切换生产线去生产另一种产品的模式比较妥当。
在这种简单模式下,连续流是首选。
如下图,工艺顺序上是A供货给B,B然后供货给C,C最后制成成品。
ABC工序在物理的空间上形成一个不间断的连续流,并在每个工序间相互保有一定数量的在制品。
在这种模式下,拉动生产时如何实现的呢?
假定ABC之间是单件流(如果在制品是以小批量流转,也没有关系,将小批量看做一个单件即可),那么基本的套路是这样的:
——均衡生产计划下发到作业C。
——作业C从BC之间的指定地点取走零部件,进行生产作业。
——零部件取走后,BC之间出现空白,这个空白就是传递给B的一个作业信号(看板),提醒B需要按协议规定组织生产,进行补货。
——作业B从AB之间的指定地点取走零部件,进行生产作业。
——零部件取走后,AB之间出现空白,这个空白就是传递给A的一个作业信号(看板),提醒A需要按协议规定组织生产,进行补货。
——作业A取走原材料,进行生产作业。
如果水准足够高,而且供应商也愿意,那么A取走的原材料所传递的信息也可以用来拉动相关供应商的生产。
这也是拉动式生产应用的普世哲学。
2、复杂生产中的拉动模式
当然,上述简单模型其实是建立在重复生产的基础上,因此许多人会认为多品种小批量的制造行业中,拉动式生产是不可能实现的。
诚然,在任何一个行业中应用拉动式生产都不是一件容易的事情,在多种少量的生产中要实现拉动式生产,确实是难上加难,但说不可能肯定是不对的。
事实上,不但多品种少批量的生产模式可以完美的应用拉动模式,甚至在定制化的行业里应用拉动生产也不会有什么问题。
前提是真正把握拉动生产的基本要点。
这些要点就是:
1. 拉动信号由谁发出,又由谁接收。
2. 发出和接收之间是否有明确的协议。
3. 是否有明确的,一目了然的控制。
假设生产流程如下。
该流程每天要生产多种产品。
粗看之下,要对所有产品实现从C到A的拉动是有点勉为其难。
因为拉动即意味着保有一定的库存。
在定制化行业中,产品几无定式,如果保有库存,既无可能,也不实用。
哪怕有这可能,如果品种类型成百上千,那库存金额也将是个天文数字。
这就是为什么大家追逐按单生产(manufacturing by order)的原因。
但如果深刻的理解拉动式生产的要点,那么从理论上来说,无论你生产何种产品,只要坚守住拉动生产的要点,你就会发现这些作业步骤仍然遵守拉动制度的规则。
在这种按单生产的模式下,虽然生产是从A工序发起,但生产计划单的生产顺序就是末道工序C需求的顺序,也就是C对B对A拉动的顺序。
只不过这个拉动的信号是通过生产计划单的形式传递,而不是我们一向以为的看板。
单除此之外,还有另外一个拉动信号。
这个拉动信号也是逐步由C向A传递。
那就是何时向后道工序补货的信号。
如果C的生产没有完成,B也就不能讲生产完的产品向C传递,也就不能进行下一个产品的生产,而只能等候作业C发出补给的信号。
B与A之间也是同样的道理。
在这种模式下,拉动的方式与我们通常理解的看板拉动略有不同,传统意义上工序之间的拉动一张看板就够了,这里的看板信息实际上是由两部分组成(生产计划单和工序之间的需求供给信息)。
但无论如何,实际上作业C仍然决定作业B的作业,而作业B也决定作业A的作业(生产计划单上的下一个生产项目)。
而这个补给的信号也从根本上解释了跟传统的按单生产中的推动模式的区别。
在产品组合高度变化的情况下,成功实施拉动生产的关键点:
1. 每一位作业员都要有能力在任何时候生产所需要的任何款式;
2. 不同产品之间的生产节拍要尽可能接近(这就需要前期大量的观察,分析和改善);
3. 尽可能确保每个工序的生产节拍低于顾客的需求节拍(就是比出货速度要快,以保证不影响满足客户需求的能力);
4. 谨慎实施单件流,适当的在工序之间保有合适的缓冲库存(当然这些缓冲库存是协议的一部分,并可以目视管理)。
所以,对于拉动式生产来说,只要始终把握拉动生产的基本要素,再仔细规划制程中的细节,建立明确的连接,在大部分的生产形式中都是可以应用的。
展示道具应该是一个定制化程度很高的行业,但事实上,通过结合基本理念的灵活运用,当年也是做到过拉动式生产的。
虽然当时短期的效果确实不如需求稳定的产品,为工作平衡和过程兼容的所做的努力也大大超出常态,但总体上还是实现了拉动式的生产。
3、拉动式生产的忠告
在精益生产模式中,拉动方式的最终成功实施源自于其基本的2个保证条件得到满足。
这2个基本条件之一是建立了稳定的连续流。
划重点记住,是稳定的连续流,而不仅仅只是所谓的连续流。
基本条件之二是均衡生产模式。
需要强调的是,均衡生产也是连续流保持稳定的基本要素之一(其他要素还有稳定的零部件质量,可靠的机器,稳定的,统一的作业方法,合格的人员等)。
均衡生产即意味着你的需求端的稳定,如果需求端波动极大,天皇老子也救不了你。
在需求不稳定的情况下,一意孤行,强行实现拉动,那就是逆天命,批龙鳞,拉动式生产就会变成一个难以收拾的烂摊子,并最终沦为人们茶余饭后的笑柄。
丰田生产模式中的基本理念就是平时对可能出现的坏情况尽可能多的做出预演和应对,但也接受随机性,并通过应急计划来进行处理。
对于必然发生的做出选择而不是去控制,去控制自己可以控制的。
就像供应中的缺货,细究起来原因真是五花八门,甚至员工上个厕所都能让你缺货,难道你不让员工上厕所么?所以用统计标准差留出余量不去管它。
但是供应的频次是我可以控制的,为什么不控呢?这样创造出了灵活性,反倒有了持续改善的可能。
经验打败理论还是理论打败经验取决于你对自己家产品的运营方式知道多少。