复合烧结剂对高铝质干式料烧结性能的影响
影响烧结矿强度的因素分析及改进措施

烧结强度攻关分析一、影响烧结矿强度的因素分析1、烧结矿中FeO含量:过高直接还原增加,过低强度不好;碳高时容易还原生成FeO,形成强度很好但还原性很差的铁橄榄石和钙铁橄榄石,因此生产时既要保证有一定的还原性,又要保证机械强度。
2、烧结矿化学成份:MgO、Al2O3的影响。
3、烧结混合料混匀程度:圆筒混合机中的三种运动状态——翻动、滚动、滑动,其中滑动对混料是没有效果的,需要控制;混合后碳粒的存在形式有三种——被矿粉包裹在中心形成的颗粒、与矿粉一起包裹在核表面形成的颗粒、单独存在的颗粒,因此要防止第一、三种状态,产生第二种混合颗粒。
4、烧结矿烧结工艺参数:点火温度1150~1250℃等;5、烧结矿的碱度:根据烧结矿强度分析,碱度在1.7~1.8时强度最好,加入的生石灰起粒化促进剂的作用。
6、固相反应有利于提高烧结矿的强度质量:在高碱度烧结条件下,主要是产生铁酸钙,甚至是铁酸二钙,铁酸三钙,都有较好的强度和还原性。
7、抽入的空气温度越低,抽风速度越快,则烧结矿气孔越薄,强度也就较差。
8、原料成分和矿相的影响:软熔温度的影响,结晶水的影响,粒度比例的影响。
二、【小知识】降低烧结矿FeO 对提高烧结矿产、质量和高炉生产有什么好处?烧结矿中FeO不是单独存在的,由于燃烧层高温的作用,使很大一部分FeO 与SiO2和CaO结合生成铁橄榄石和钙铁橄榄石。
此物质较多的烧结矿呈多孔蜂状,具有一定的强度但发脆,此种物质还原性很差。
该物质生成温度高,需配碳也多,也起烧结燃烧带变宽,阻力增大,影响烧结机台时产量提高。
同时由于生成温度高,因而燃料消耗也多,据日本试验和生产的经验数据统计,烧结矿FeO 增减1%,影响固体燃料消耗增减2~5kg/t。
对高炉的影响也是很大的,根据生产统计数据和经验数据表明,FeO 波动1%,影响高炉焦比1~1.5%,影响产1~1.5%。
因此在保证烧结矿强度的情况下,应尽量降低烧结矿FeO。
现在我国重点厂烧结矿FeO在10%左右,有个别厂达到7%。
干式料中间包
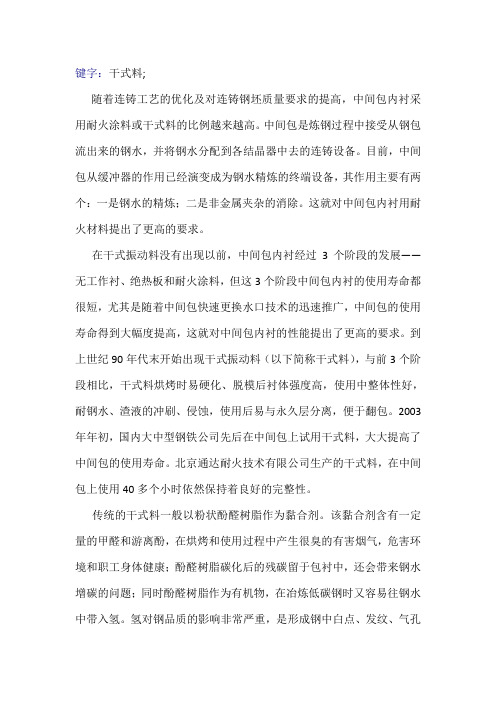
键字:干式料;随着连铸工艺的优化及对连铸钢坯质量要求的提高,中间包内衬采用耐火涂料或干式料的比例越来越高。
中间包是炼钢过程中接受从钢包流出来的钢水,并将钢水分配到各结晶器中去的连铸设备。
目前,中间包从缓冲器的作用已经演变成为钢水精炼的终端设备,其作用主要有两个:一是钢水的精炼;二是非金属夹杂的消除。
这就对中间包内衬用耐火材料提出了更高的要求。
在干式振动料没有出现以前,中间包内衬经过3个阶段的发展——无工作衬、绝热板和耐火涂料,但这3个阶段中间包内衬的使用寿命都很短,尤其是随着中间包快速更换水口技术的迅速推广,中间包的使用寿命得到大幅度提高,这就对中间包内衬的性能提出了更高的要求。
到上世纪90年代末开始出现干式振动料(以下简称干式料),与前3个阶段相比,干式料烘烤时易硬化、脱模后衬体强度高,使用中整体性好,耐钢水、渣液的冲刷、侵蚀,使用后易与永久层分离,便于翻包。
2003年年初,国内大中型钢铁公司先后在中间包上试用干式料,大大提高了中间包的使用寿命。
北京通达耐火技术有限公司生产的干式料,在中间包上使用40多个小时依然保持着良好的完整性。
传统的干式料一般以粉状酚醛树脂作为黏合剂。
该黏合剂含有一定量的甲醛和游离酚,在烘烤和使用过程中产生很臭的有害烟气,危害环境和职工身体健康;酚醛树脂碳化后的残碳留于包衬中,还会带来钢水增碳的问题;同时酚醛树脂作为有机物,在冶炼低碳钢时又容易往钢水中带入氢。
氢对钢品质的影响非常严重,是形成钢中白点、发纹、气孔等缺陷的主要原因。
由于传统干式料存在的缺陷,同时结合剂没有残留碳和氢,不会带来钢水增碳、增氢问题,符合目前材料应用领域向环保型发展的技术趋势,将有很好的应用前景。
2005年年初,上海、武汉生产干式料的厂家,先后研制出不含树脂的干式料,有效地弥补了第一代干式料在环保方面的不足。
但他们研制的黏合剂及其产品还存在泛潮、储放期短的问题。
2005年6月,攀钢冶金材料有限责任公司开始了环保型干式料的研制工作,经过3个月的探索,成功地解决了有害烟气危害环境和人身健康等问题,取得了试验室阶段的初步效果。
烧结矿质量对高炉冶炼的影响 精品

吉林电子信息职业技术学院毕业论文烧结矿质量对高炉冶炼的影响摘要烧结矿是高炉炼铁生产的主要原料之一,烧结矿的性能和质量直接影响高炉冶炼的顺行、操作制度和技术经济指标。
本论文通过对烧结矿的还原,滴落实验,验证不同粒度的半焦、无烟煤代替焦粉作燃料的铁矿烧结技术的比较优势。
以及改变其粒度等方面对烧结进行分析、研究。
本项研究内容包括:原、燃料的物理化学性质、燃料的性能及反应性、烧结矿质量指标的评价;在不同原料配比条件下改变燃料粒度的烧结实验;烧结矿的物理化学性能和冶金性能等检测;对燃料种类和配比对烧结矿生产指标、烧结矿化学成分、矿物组成、还原性能、还原粉化性能、软熔滴落性能的影响进行评价,实验结果及其分析。
实验结果证明:半焦在>5mm粒级控制在15%的粒度下是很好的烧结燃料。
无烟煤相对做烧结燃料效果不好;<3mm粒级控制在70%左右为宜。
关键词:烧结矿,无烟煤,焦粉,半焦,矿物组成,烧结矿冶金性能,改变粒度I吉林电子信息职业技术学院毕业论文目录第一章绪论·············································································································· - 6 -1.1烧结生产的目的·············································································································- 6 -1.2烧结用原料条件·············································································································- 7 -1.3燃料的粒度 ······················································································································- 7 -1.4燃料的基本性质·············································································································- 8 -1.4.1燃料的工业分析、元素分析 ......................................................................... - 8 -1.4.2燃料的灰成分和灰熔点·······························································································- 10 -第二章烧结的作用·································································································- 11 -2.1烧结矿的作用 ···············································································································- 11 -2.2烧结机的作用 ···············································································································- 12 -2.3烧结矿中MgO 作用机理 ····························································································- 12 -第三章烧结生成工艺及生产的工艺流程·························································- 13 -3.1烧结生成工艺 ···············································································································- 13 -3.2烧结生产的工艺流程··································································································- 13 -3.2.1烧结原料的准备 ..................................................................................... - 14 -3.2.2配料与混合............................................................................................... - 14 -3.2.3烧结生产 ................................................................................................... - 15 -第四章烧结矿对高炉冶炼的影响·····································································- 18 -4.1烧结矿指标对高炉冶炼过程的影响·······································································- 18 -4.2烧结矿指标和冶金性能的影响因素·······································································- 20 -第五章结论·········································································································- 24 -参考文献·················································································································- 25 -致谢·································································································错误!未定义书签。
氟化钙对高铝烧结矿矿相组成、冶金性能的影响
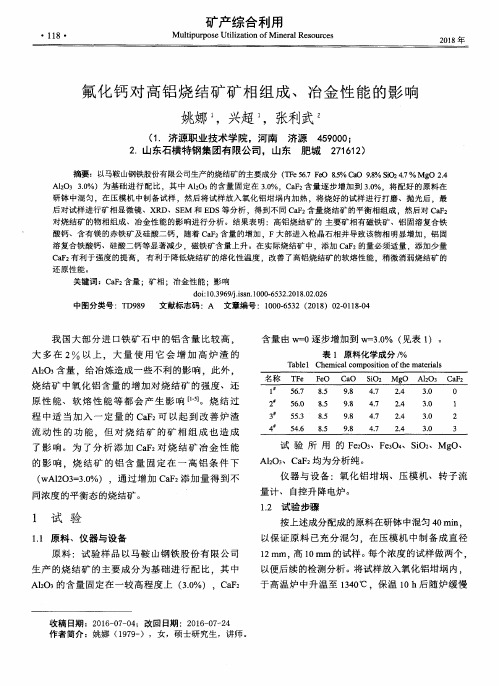
b
图 1 不 同 CaF2含 量的 X衍 射
Fig.1 XRD pattern of sinter in diferent content of CaF2
图 1中 a、b分 别为 在 A1203为 3.0% 的情 况下 , CaF2含 量 分 别 为 1.0% 和 3.0% 时烧 结 矿 的 x衍 射 分 析 结 果 。 结 合 不 含 CaF2时 的 结 果 ,在 CaF2含 量为 1.0% 时烧 结矿 的矿 相组 成 与不加 时 基本 相 同 , 主 要 有 磁 铁 矿 、铝 固溶 复合 铁 酸钙 、含 有 镁 的 赤 铁 矿 及 硅 酸 二 钙 :而 在 CaF2含 量 在 3.0% 时 烧 结
摘要 :以马鞍山钢铁股份有限公司生产 的烧结矿的主要成分 (TFe 56.7 F ̄O 8.5%CaO 9.8% Si02 4.7%MgO 2.4 A1203 3.0%)为基础 进行配 比 ,其 中 A1203的含 量固定在 3.O%,CaF2含 量逐步增 加到 3.0%,将配好 的原 料在 研钵 中混匀 ,在压模机 中制备试样 ,然 后将 试样放入氧化 铝坩埚 内加热 ,将烧好 的试样进行打磨 、抛 光后 ,最 后对 试样 进行矿相 显微镜、XRD、SEM 和 EDS等分析 ,得到不 同 CaF2含量烧 结矿 的平衡 相组成 ,然后对 CaF2 对烧 结矿 的物相组成 、冶金性 能的影 响进 行分析 。结果表 明:高铝烧结矿 的 主要矿相有 磁铁 矿、铝固溶复合铁 酸钙 、含有镁 的赤铁矿及硅酸二钙 ,随着 CaF2含量 的增 加 ,F大部进入枪 晶石相并 导致 该物相 明显增加 ,铝固 溶复合铁 酸钙 、硅 酸二钙等显著减少 ,磁铁矿含量上升 。在实 际烧结矿 中,添加 CaF2的量必须适量 ,添加少量 CaF2有利于强度 的提高 , 有利于 降低烧结矿 的熔化 性温度 ,改善了高铝烧 结矿 的软熔性能 ,稍微消弱烧结矿的 还 原 性 能 。
高铝砖的性能与烧结温度的关系

高铝砖的性能与烧结温度的关系在理论上,Al2O3含量大于46%的硅酸铝质耐火材料称为高铝砖。
我国规定高铝砖Al2O3含量大于48%。
天然高铝矾土熟料+结合粘土细粉的细度越高,促进烧结作用越显著。
高铝砖的颗粒配比,一般采用3mm或5mm的临界颗粒,粗颗粒50-60%,中颗粒10-15%,细粉35-40%。
临界颗粒大些,对提高抗热震性、颗粒紧密堆积有利,但易出现颗粒偏析,表面结构粗糙,边角、棱松散。
(抗热震性——抵抗温度急剧变化和受热不均的能力。
)高铝砖的烧结温度有哪些:200℃以下,坯体内残余水分的排除;200-1250℃,结合粘土中的高岭石脱水分解,形成莫来石和游离SiO2;1250℃以上,熟料中的α-Al2O3与游离SiO2结合生成二次莫来石,并伴随体积膨胀。
(注:生成的物相密度不同。
)我们了解了高铝砖的烧结温度,再来了解一下高铝砖的性能优势有哪些?1、耐火度。
高铝砖制品是硅酸铝质耐火材料制品中的高级品种,它的耐火度随Al2O3,含量的增加而提高,一般不低于1750—1790℃。
如Al2O3含量大于95%的刚玉砖,耐火度可高达1900-2000℃。
2、荷重软化温度。
高铝砖制品的荷重软化温度随二氧化硅和碱金属氧化物含量的增加而降低,但比粘土砖制品高,约为1420—1530℃。
Al2O3。
含量大于95%的刚玉砖,其荷重软化温度可达1600℃以上。
3、抗渣性。
由于高铝砖制品中三氧化二铝呈中性而且含量高,所以此类材料制品对于酸碱性炉渣的侵蚀均有较强的抵抗能。
4、热震稳定性。
高铝砖制品中,有刚玉与莫来石两种晶体共存,因为刚玉的热膨胀系数比莫来石热膨胀系数大,在耐火砖温度变化时,由于膨胀差异导致应力集中。
所以,高铝砖制品比粘土砖制品的热震稳定性差,一般水冷次数只有3—5次。
5、重烧线变化。
如果高铝砖制品的烧成温度足够,烧成时间充足,则体积稳定,重烧线变化小;反之,则产生如粘土砖制品的残余收缩,原因也是发生再结晶所致。
烧结剂对耐火材料的影响

水玻璃结合剂(water glass binder)一种无机材料的胶结剂。
又称泡花碱。
在工业上呗广泛用作无机材料胶结剂,在耐火材料工业作为结合剂用相当广泛,也广泛用于造纸及纺织等工业。
添加剂对耐火材料烧结的影响在固相烧结时,少量的添加剂(烧结助剂)可与主晶相形成固溶体促进缺陷增加;在液相烧结时,添加剂能够改变液相的性质(如粘度、组成等),因而能起促进烧结的作用。
添加剂的作用可能在于以下几个方面。
形成固溶体。
当添加物与烧结物形成固溶体时,可以增加晶格缺陷,活化晶格,从而促进烧结。
一般来说,他们之间形成有限置换固溶体更有助于促进烧结。
添加剂离子的电价、半径与主晶格离子的电价、半径相差越大,晶格畸变程序也越大,促进烧结的作用也越明显。
如Al2O3烧结时,加入3%的Cr2O3形成连续固溶体可在1860℃烧结,而加入1%~2%只需在1600℃左右就能致密化。
阻止晶型转变。
有些氧化物在烧结时发生晶型转变并伴有较大的体积效应,这就难以实现烧结致密化,并容易引起坯体开裂。
这时若能选用适宜的添加剂加以抑制,即可促进烧结。
ZrO2烧结时添加一定量的CaO、MgO就属这一机理。
约在1200℃,m- ZrO2转变为t- ZrO2,并伴有约10%的体积收缩,使制品稳定性变坏。
引入电价比Zr4+低的Ca2+(或Mg2+),可形成稳定的立方萤石结构的固溶体。
这样,既防止了制品的开裂,又增加了晶体中缺陷浓度,使烧结加快。
抑制晶粒长大。
烧结后期晶粒长大,对促进烧结致密化有重要作用。
但若二次再结晶或间断性晶粒长大过快,会使晶粒变粗、晶界变宽而出现反致密化现象并影响制品的显微结构。
这时,可通过加入能抑制晶粒异常长大的添加剂来促进烧结。
在烧结透明Al2O3制品时,为抑制二次再结晶,消除晶界上的气孔,一般加入MgO或MgF2,高温下形成镁铝尖晶石包裹在Al2O3晶粒表面,抑制了晶界迁移的速度,并促使气孔的排出,对促进坯体的烧结具有显著的作用。
添加剂对中间包镁质干式料性能的影响
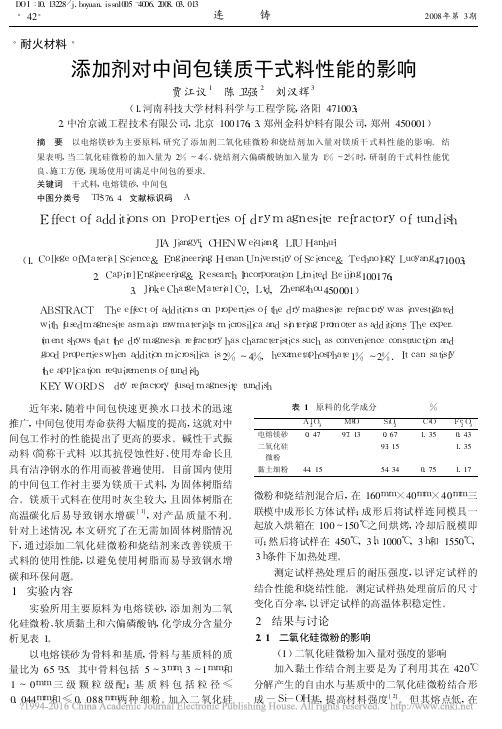
·耐火材料·添加剂对中间包镁质干式料性能的影响贾江议1 陈卫强2 刘汉辉3(1.河南科技大学材料科学与工程学院,洛阳471003;2.中冶京诚工程技术有限公司,北京100176;3.郑州金科炉料有限公司,郑州450001)摘 要 以电熔镁砂为主要原料,研究了添加剂二氧化硅微粉和烧结剂加入量对镁质干式料性能的影响。
结果表明,当二氧化硅微粉的加入量为2%~4%、烧结剂六偏磷酸钠加入量为1%~2%时,研制的干式料性能优良、施工方便,现场使用可满足中间包的要求。
关键词 干式料,电熔镁砂,中间包中图分类号 T F576.4 文献标识码 AE f f e c t o f a d d i t i o n s o np r o p e r t i e s o f d r y m a g n e s i t e r e f r a c t o r y o f t u n d i s hJ I AJ i a n g y i1,C H E NW e i q i a n g2,L I UH a n h u i3(1.C o l l e g e o f M a t e r i a l S c i e n c e&E n g i n e e r i n g,H e n a n U n i v e r s t i t y o f S c i e n c e&T e c h n o l o g y,L u o y a n g471003;2.C a p i t a l E n g i n e e r i n g&R e s e a r c h I n c o r p o r a t i o n L i m i t e d,B e i j i n g100176;3.J i n k e C h a r g e M a t e r i a l C o.,L t d.,Z h e n g z h o u450001)A B S T R A C T T h e e f f e c t o f a d d i t i o n s o np r o p e r t i e s o f t h e d r y m a g n e s i t e r e f r a c t o r y w a s i n v e s t i g a t e dw i t h f u s e d m a g n e s i t e a s m a i n r a w m a t e r i a l s,m i c r o s i l i c a a n d s i n t e r i n g p r o m o t e r a s a d d i t i o n s.T h e e x p e r-i m e n t s h o w s t h a t t h e d r y m a g n e s i a r e f r a c t o r y h a s c h a r a c t e r i s t i c s s u c h a s c o n v e n i e n c e c o n s t r u c t i o n a n dg o o d p r o p e r t i e s w h e na d d i t i o nm i c r o s i l i c a i s2%~4%,h e x a m e t a p h o s p h a t e1%~2%.I t c a n s a t i s f yt h e a p p l i c a t i o n r e q u i r e m e n t s o f t u n d i s h.K E Y WO R D S d r y r e f r a c t o r y,f u s e d m a g n e s i t e,t u n d i s h 近年来,随着中间包快速更换水口技术的迅速推广,中间包使用寿命获得大幅度的提高,这就对中间包工作衬的性能提出了更高的要求。
高铝对高炉炼铁的影响及优化
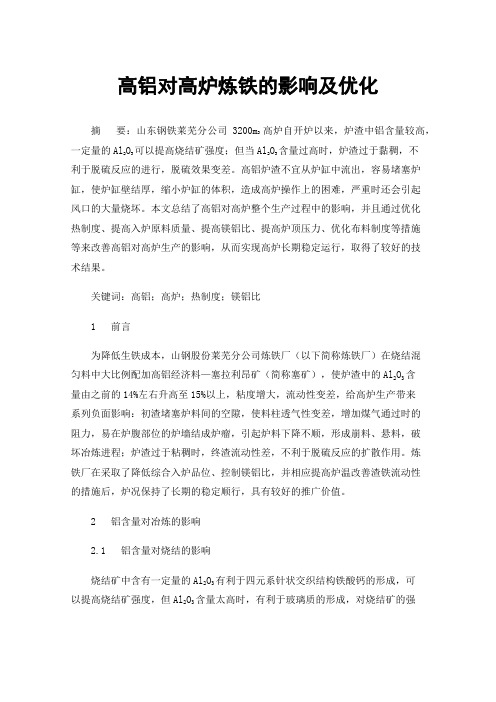
高铝对高炉炼铁的影响及优化摘要:山东钢铁莱芜分公司3200m3高炉自开炉以来,炉渣中铝含量较高,一定量的Al2O3可以提高烧结矿强度;但当Al2O3含量过高时,炉渣过于黏稠,不利于脱硫反应的进行,脱硫效果变差。
高铝炉渣不宜从炉缸中流出,容易堵塞炉缸,使炉缸壁结厚,缩小炉缸的体积,造成高炉操作上的困难,严重时还会引起风口的大量烧坏。
本文总结了高铝对高炉整个生产过程中的影响,并且通过优化热制度、提高入炉原料质量、提高镁铝比、提高炉顶压力、优化布料制度等措施等来改善高铝对高炉生产的影响,从而实现高炉长期稳定运行,取得了较好的技术结果。
关键词:高铝;高炉;热制度;镁铝比1 前言为降低生铁成本,山钢股份莱芜分公司炼铁厂(以下简称炼铁厂)在烧结混匀料中大比例配加高铝经济料—塞拉利昂矿(简称塞矿),使炉渣中的Al2O3含量由之前的14%左右升高至15%以上,粘度增大,流动性变差,给高炉生产带来系列负面影响:初渣堵塞炉料间的空隙,使料柱透气性变差,增加煤气通过时的阻力,易在炉腹部位的炉墙结成炉瘤,引起炉料下降不顺,形成崩料、悬料,破坏冶炼进程;炉渣过于粘稠时,终渣流动性差,不利于脱硫反应的扩散作用。
炼铁厂在采取了降低综合入炉品位、控制镁铝比,并相应提高炉温改善渣铁流动性的措施后,炉况保持了长期的稳定顺行,具有较好的推广价值。
2 铝含量对冶炼的影响2.1 铝含量对烧结的影响烧结矿中含有一定量的Al2O3有利于四元系针状交织结构铁酸钙的形成,可以提高烧结矿强度,但Al2O3含量太高时,有利于玻璃质的形成,对烧结矿的强度和低温还原粉化性能不利[1]。
实践证明,当烧结矿中铝含量>2.5%,对烧结矿强度和低温还原粉化性能影响较大。
2.2 铝含量对高炉生产的影响Al2O3在炉渣中有一定的脱硫效果,但弱于CaO和MgO。
对高炉生产的影响具体表现为:在炉内,压差升高,上部容易悬料,炉缸容易粘结堆积;在炉外,主沟内渣铁不易分离,渣中带铁,渣沟内炉渣流动性很差,容易结壳。
烧结矿质量及其对高炉冶炼主要操作指标的影响

烧结矿质量及其对高炉冶炼主要操作指标的影响摘要:烧结矿质量对高炉炼铁产量、能耗、生铁质量、高炉寿命起着决定性的作用。
基于此,本文重点分析了烧结矿质量及其对高炉冶炼主要操作指标的影响。
关键词:烧结矿质量;高炉冶炼;操作指标;影响目前,在高炉炼铁过程中,烧结矿的质量作为影响炼铁燃料消耗的重要因素之一,应进行有效的优化完善,以有效提高烧结矿的性能,为高炉炼铁过程奠定坚实的物质基础,从而在一定程度上促进炼铁工艺节能降耗的发展。
一、烧结矿产量与质量的影响因素1、燃料粒度影响。
合适的固体燃料粒度等级和粒度分布能提烧结机利用系数,使烧结矿成品率、转鼓指数、平均粒径等指标明显改善,同时也能降低固体燃料消耗和高炉返矿率。
2、烧结熔剂结构影响。
自熔性烧结矿要满足高炉所需各项理化指标,必须在混合料中配加一定量生石灰、石灰石和白云石等熔剂。
配加熔剂结构的不同会对烧结矿强度、碱度、还原性、低温还原粉化率和混匀料粒级分布等各项理化指标产生影响,这些指标会直接关系到高炉冶炼的稳定顺行,从而对生铁产量及炼铁成本产生影响。
二、烧结矿质量对高炉冶炼主要操作指标的影响1、烧结矿主要化学成分的影响①品位及SiO2含量影响。
在正常情况下,入炉矿品位1%变动将导致高炉燃料比1~1.5%变动,产量2~2.5%变动,一旦确定了烧结矿在炉料结构中比例,就可计算出烧结矿品位变动1%对高炉燃料比及产量的影响。
入炉矿SiO2含量1%变动将影响30~35kg/t渣铁比,100kg渣量将影响3.0~3.5%燃料、产量。
有了烧结矿入炉比例,乘以该比例将决定烧结矿SiO2含量变动对高炉主操作指标的影响。
②烧结矿碱度的影响。
生产实践表明,烧结矿最佳碱度范围为1.9~2.3,当低于1.85时,碱度每降低0.1,燃料比与产量将分别影响3.0~3.5%。
据了解,实际生产中,降低碱度对高炉燃料比影响远高于3.5%的比例。
近年来,一些生产企业的烧结矿碱度低于1.80甚至低于1.70,应该认识到,碱度对烧结矿质量和高炉主要操作指标都有影响。
影响复合材料性能的因素

影响复合材料性能的因素复合材料是由两种或两种以上的材料组合而成的材料,其性能受到多种因素的影响。
首先,材料的成分对复合材料的性能有着重要的影响。
不同的成分会影响复合材料的密度、强度、硬度、耐磨性等性能指标。
例如,玻璃纤维和碳纤维是常用的增强材料,它们的强度和刚度很高,可以有效提高复合材料的强度和刚度;而树脂是常用的基体材料,不同种类的树脂会影响复合材料的耐腐蚀性、耐热性等性能。
其次,复合材料的制备工艺也会影响其性能。
不同的制备工艺会影响复合材料的成型质量、成型效率、成型成本等方面。
例如,手工层叠工艺和自动化预浸料工艺是常用的制备工艺,它们会影响复合材料的纤维含量、树脂含量、纤维排列方式等方面,进而影响复合材料的性能。
另外,环境因素也会对复合材料的性能产生影响。
复合材料在不同的环境条件下,其性能表现也会有所不同。
例如,在高温环境下,复合材料的热膨胀系数会增大,导致尺寸稳定性变差;在潮湿环境下,复合材料容易受潮变软,失去原有的强度和刚度。
此外,复合材料的表面处理也会对其性能产生影响。
表面处理可以改善复合材料的表面粗糙度、耐磨性、耐腐蚀性等性能。
常见的表面处理方法包括喷砂、化学处理、涂层等,这些方法可以有效提高复合材料的表面质量和使用性能。
最后,复合材料的使用条件也会对其性能产生影响。
不同的使用条件会对复合材料的力学性能、热学性能、耐久性能等方面提出不同的要求。
因此,在实际应用中,需要根据具体的使用条件选择合适的复合材料,并且进行必要的设计和改进,以保证其性能满足使用要求。
综上所述,影响复合材料性能的因素包括材料的成分、制备工艺、环境因素、表面处理和使用条件等多个方面。
在实际应用中,需要综合考虑这些因素,合理选择材料和工艺,以确保复合材料具有良好的性能和稳定的品质。
烧结助剂对高铝陶瓷烧成温度及磨损性能的影响
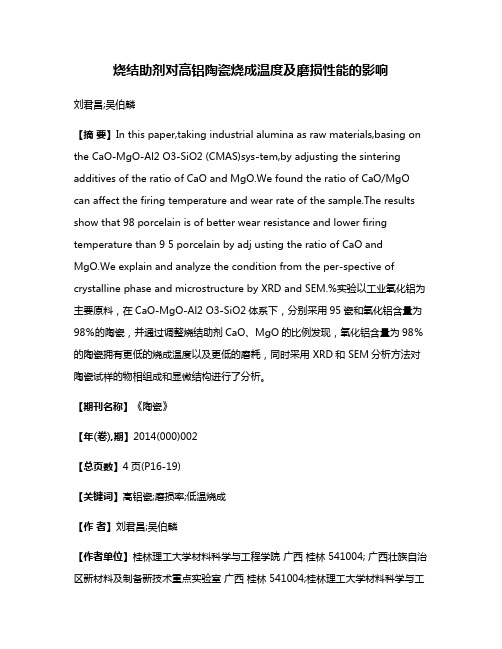
烧结助剂对高铝陶瓷烧成温度及磨损性能的影响刘君昌;吴伯麟【摘要】In this paper,taking industrial alumina as raw materials,basing on the CaO-MgO-Al2 O3-SiO2 (CMAS)sys-tem,by adjusting the sintering additives of the ratio of CaO and MgO.We found the ratio of CaO/MgO can affect the firing temperature and wear rate of the sample.The results show that 98 porcelain is of better wear resistance and lower firing temperature than 9 5 porcelain by adj usting the ratio of CaO and MgO.We explain and analyze the condition from the per-spective of crystalline phase and microstructure by XRD and SEM.%实验以工业氧化铝为主要原料,在CaO-MgO-Al2 O3-SiO2体系下,分别采用95瓷和氧化铝含量为98%的陶瓷,并通过调整烧结助剂CaO、MgO的比例发现,氧化铝含量为98%的陶瓷拥有更低的烧成温度以及更低的磨耗,同时采用 XRD和 SEM分析方法对陶瓷试样的物相组成和显微结构进行了分析。
【期刊名称】《陶瓷》【年(卷),期】2014(000)002【总页数】4页(P16-19)【关键词】高铝瓷;磨损率;低温烧成【作者】刘君昌;吴伯麟【作者单位】桂林理工大学材料科学与工程学院广西桂林 541004; 广西壮族自治区新材料及制备新技术重点实验室广西桂林 541004;桂林理工大学材料科学与工程学院广西桂林 541004; 广西壮族自治区新材料及制备新技术重点实验室广西桂林 541004【正文语种】中文【中图分类】TB332前言氧化铝陶瓷具有高熔点、高硬度、优良的加工性能和稳定的化学性能,同时还兼具价格低廉等优点,成为一种使用量最大的工业陶瓷。
ZHS
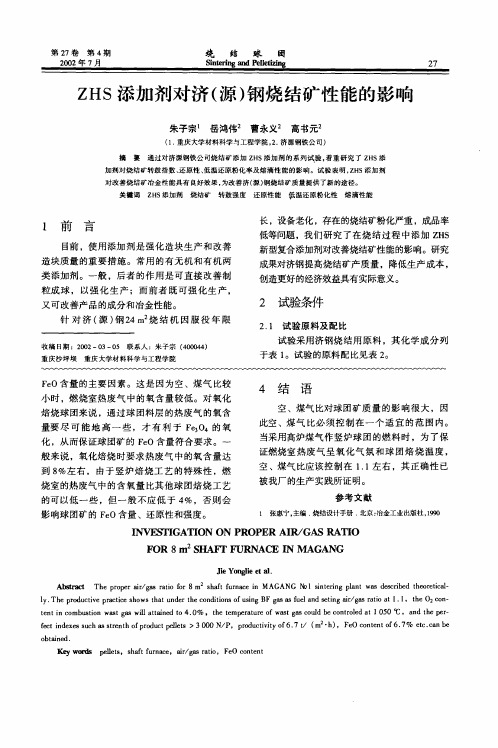
D , : I 】 rGA oN I Ⅱ oN PRoPER I GAS RA o AI Ⅱ
F lS F U N E I MA A G OR 8n2 HA T F R AC N G N
JeYo gi ta . i n l e 1 e
Ab ta t Th r p ra r g s r t o s a tf r a e i AGANG N sn e i g p a t W e c i e h o e ia- src e p o e i a a i f r8 m / o h f u n c n M o i trn l n a d s rb d t e r t l l s c l Th r d c ie p a t e s o h tu d rt e c n i o so s g BF g u la d s t g ar g ai t1 1 t e 0 o ’ y. e p o u t rc i h wst a n e h o d t n fu i a a f e n e i / a rtoa . , h 2c n v c i n s s n i s
otn . ba e i d
Ke I y WO' t t  ̄ e l s h rae i / a rt p l t , s a t u n c , ar g a i , F O o t n e f f s o e c ne t
创造更好的经济效益具有实际意义。
2 试验条件
2 1 试 验原料 及 配 比 .
针 对 济 ( ) 4I 烧 结机 因服役 年 限 源 钢2 l l
收 稿 日期 :20 0 2—0 0 联 系 人 :朱 子 宗 (0 0 4 3— 5 404 )
试验 采用济 钢 烧 结用 原 料 ,其化 学 成 分 列 于表 1 。试 验 的原 料 配 比见 表 2 。
配加落地烧结矿对高炉冶炼影响

矿入炉增加了多次倒运过程,必然影响落地烧结 矿的含粉率和粒度组成结构。
截取同一筛网直送烧结矿与落地烧结矿粒度 组成分析如表]所示。落地烧结矿与直送烧结矿 在筛上物粒度组成上存在较大差别:落地烧结矿 平均粒度较直送烧结矿偏小1 ~2mm。粒度组成 上,10 - 16mm小粒级比例增多约3% -6%, 25 ~40mm大粒级比例降低约2% -3%, 40mm以 上大粒级比例降低约2% ~3%
<5mm/% 2. 52 2. 49 2. 46 2. 39 2. 39 2. 38
平均粒度/ mm 17. 95 17. 73 17. 68 19. 35 19. 17 19. 08
12.0 10.0 &0进 6.0§
4.0蚁 2.0 0.0
图1 2月份落地烧结矿占比与矿筛返粉率关系
1.2低温还原粉化率分析 在高炉上部低温区(约500〜600兀),烧结
Vol. 40 No. 3
冶金能源
May. 2021
ENERGY FOR METALLURGICAL INDUSTRY
33
矿种 落地烧结矿
直送烧结矿
表1落地烧结矿与直送烧结矿筛上粒度组成对比
> 40 mm/ % 4. 02 3.27 4. 02 6. 08 6.44 6. 03
25 ~ 40mm/% 14. 82 14. 93 14. 38 1& 29 16. 74 17. 14
唐钢3号高炉1998年开炉,设计炉容为 2560m3, 2007年推移大修扩容至3200m30自 2019年以后,采暖季环保响应进入常态化,烧 结工艺长期限产甚至停产。高炉大量配吃自产和 外购落地烧结矿,配加比例长期在50%左右, 最高短期配加100%落地烧结矿。长期大量配吃 落地烧结矿对炉况长期稳定顺行带来较大压力, 通过采取一系列针对性措施,维持了高炉的长期 稳定顺行,取得了较好的经济技术指标。
提高铝含量对烧结矿质量的影响研究
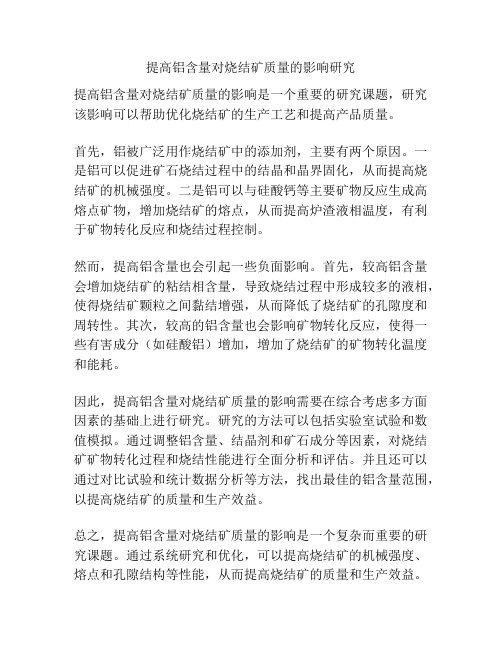
提高铝含量对烧结矿质量的影响研究
提高铝含量对烧结矿质量的影响是一个重要的研究课题,研究该影响可以帮助优化烧结矿的生产工艺和提高产品质量。
首先,铝被广泛用作烧结矿中的添加剂,主要有两个原因。
一是铝可以促进矿石烧结过程中的结晶和晶界固化,从而提高烧结矿的机械强度。
二是铝可以与硅酸钙等主要矿物反应生成高熔点矿物,增加烧结矿的熔点,从而提高炉渣液相温度,有利于矿物转化反应和烧结过程控制。
然而,提高铝含量也会引起一些负面影响。
首先,较高铝含量会增加烧结矿的粘结相含量,导致烧结过程中形成较多的液相,使得烧结矿颗粒之间黏结增强,从而降低了烧结矿的孔隙度和周转性。
其次,较高的铝含量也会影响矿物转化反应,使得一些有害成分(如硅酸铝)增加,增加了烧结矿的矿物转化温度和能耗。
因此,提高铝含量对烧结矿质量的影响需要在综合考虑多方面因素的基础上进行研究。
研究的方法可以包括实验室试验和数值模拟。
通过调整铝含量、结晶剂和矿石成分等因素,对烧结矿矿物转化过程和烧结性能进行全面分析和评估。
并且还可以通过对比试验和统计数据分析等方法,找出最佳的铝含量范围,以提高烧结矿的质量和生产效益。
总之,提高铝含量对烧结矿质量的影响是一个复杂而重要的研究课题。
通过系统研究和优化,可以提高烧结矿的机械强度、熔点和孔隙结构等性能,从而提高烧结矿的质量和生产效益。
【技术文摘】烧结矿质量及其对高炉冶炼主要操作指标的影响

【技术文摘】烧结矿质量及其对高炉冶炼主要操作指标的影响许满兴(北京科技大学)摘要:本文阐述了烧结矿在高炉炼铁中的地位和作用,阐明了烧结矿质量的内涵,分析了烧结矿的化学成分、物理性能和冶金性能对高炉冶炼主要操作指标的影响,提出了烧结生产改善烧结矿质量的几点结论性意见。
关键词:烧结矿质量、主要化学成分、强度和粒度、冶金性能、高炉冶炼主要操作指标1 烧结矿在高炉炼铁中的地位和作用自上世纪八十年代以来,高碱度烧结矿一直是我国高炉炼铁的主要原料,近几十年来,含铁原料占高炉炼铁成本接近70%,烧结矿占高炉炼铁炉料的70%以上,占吨钢能耗指标的10%以上,是钢铁生产能耗的第二大户,也是废气物排放的大户,因此不论从炉料组成比例、生铁成本、还是废弃物排放及环境保护,烧结矿生产对高炉炼铁有着举足轻重的影响。
烧结矿的质量对高炉炼铁的产量、能耗、生铁质量和高炉寿命均起着决定性的作用。
例如,烧结矿的品位变动1%,将会影响高炉燃料比1.0%~1.5%,影响产量2.0~2.5%;烧结矿的SiO2含量变动1%,影响吨铁渣比30~35kg;烧结矿的碱金属和锌超标,其化合物在高炉下部高温区还原后形成K、Na、Zn蒸汽,随煤气上升在炉身中、下部循环富集、冷凝破坏炉料的强度,影响料柱的透气性,还会造成高炉结瘤、腐蚀耐火材料和金属结构。
烧结矿的低温还原粉化和熔滴性能是高炉上部和下部透气性的限制性环境,凡此种种,烧结矿的质量对高炉炼铁的作用和影响是不能忽视的,故讨论和探索烧结矿质量对改善高炉炼铁技术经济指标,实现低成本、低燃料比高效炼铁有着重大的经济价值和实际意义。
2 烧结矿质量的内涵和价值烧结矿的质量由化学成分、物理性能和冶金性能三部分组成,它们三者间的关系是:化学成分是基础,物理性能是保证,冶金性能是关键。
2.1 烧结矿的主要化学成分及其价值烧结矿的主要化学成分包括品位和SiO2、碱度、MgO和Al2O3、FeO,S、P、Ka2O、Zn和Cl等有害元素。
MgO对烧结工艺及烧结矿冶金性能的影响 杜瑞臣
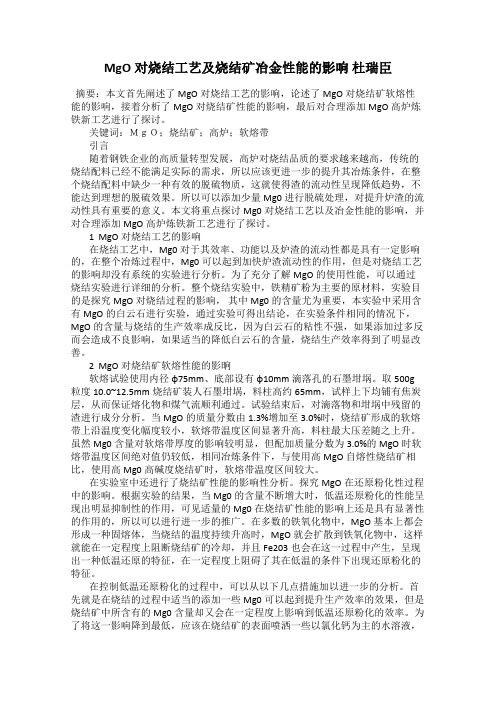
MgO对烧结工艺及烧结矿冶金性能的影响杜瑞臣摘要:本文首先阐述了MgO对烧结工艺的影响,论述了MgO对烧结矿软熔性能的影响,接着分析了MgO对烧结矿性能的影响,最后对合理添加MgO高炉炼铁新工艺进行了探讨。
关键词:MgO;烧结矿;高炉;软熔带引言随着钢铁企业的高质量转型发展,高炉对烧结品质的要求越来越高,传统的烧结配料已经不能满足实际的需求,所以应该更进一步的提升其冶炼条件,在整个烧结配料中缺少一种有效的脱硫物质,这就使得渣的流动性呈现降低趋势,不能达到理想的脱硫效果。
所以可以添加少量Mg0进行脱硫处理,对提升炉渣的流动性具有重要的意义。
本文将重点探讨Mg0对烧结工艺以及冶金性能的影响,并对合理添加MgO高炉炼铁新工艺进行了探讨。
1 MgO对烧结工艺的影响在烧结工艺中,Mg0对于其效率、功能以及炉渣的流动性都是具有一定影响的,在整个冶炼过程中,Mg0可以起到加快炉渣流动性的作用,但是对烧结工艺的影响却没有系统的实验进行分析。
为了充分了解MgO的使用性能,可以通过烧结实验进行详细的分析。
整个烧结实验中,铁精矿粉为主要的原材料,实验目的是探究MgO对烧结过程的影响,其中Mg0的含量尤为重要,本实验中采用含有MgO的白云石进行实验,通过实验可得出结论,在实验条件相同的情况下,MgO的含量与烧结的生产效率成反比,因为白云石的粘性不强,如果添加过多反而会造成不良影响,如果适当的降低白云石的含量,烧结生产效率得到了明显改善。
2 MgO对烧结矿软熔性能的影晌软熔试验使用内径φ75mm、底部设有φ10mm滴落孔的石墨坩埚。
取500g 粒度10.0~12.5mm烧结矿装人石墨坩埚,料柱高约65mm,试样上下均铺有焦炭层,从而保证熔化物和煤气流顺利通过。
试验结束后,对滴落物和坩埚中残留的渣进行成分分析。
当MgO的质量分数由1.3%增加至3.0%时,烧结矿形成的软熔带上沿温度变化幅度较小,软熔带温度区间显著升高,料柱最大压差随之上升。
烧结矿对高炉的影响
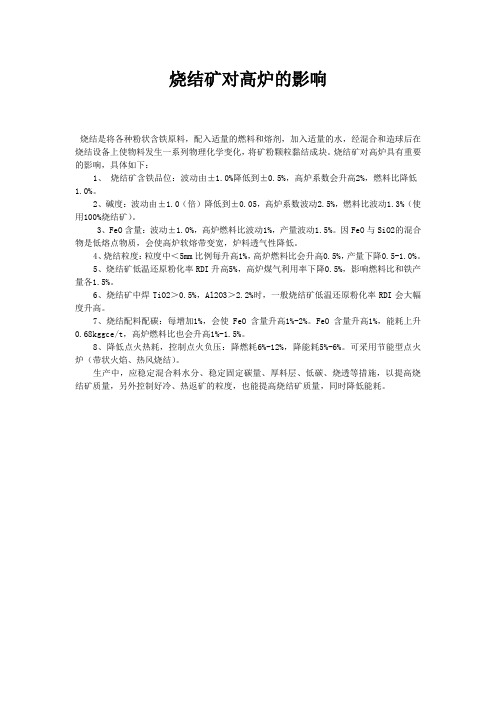
烧结矿对高炉的影响
烧结是将各种粉状含铁原料,配入适量的燃料和熔剂,加入适量的水,经混合和造球后在烧结设备上使物料发生一系列物理化学变化,将矿粉颗粒黏结成块。
烧结矿对高炉具有重要的影响,具体如下:
1、烧结矿含铁品位:波动由±1.0%降低到±0.5%,高炉系数会升高2%,燃料比降低
1.0%。
2、碱度:波动由±1.0(倍)降低到±0.05,高炉系数波动2.5%,燃料比波动1.3%(使用100%烧结矿)。
3、FeO含量:波动±1.0%,高炉燃料比波动1%,产量波动1.5%。
因FeO与SiO2的混合物是低熔点物质,会使高炉软熔带变宽,炉料透气性降低。
4、烧结粒度:粒度中<5mm比例每升高1%,高炉燃料比会升高0.5%,产量下降0.5-1.0%。
5、烧结矿低温还原粉化率RDI升高5%,高炉煤气利用率下降0.5%,影响燃料比和铁产量各1.5%。
6、烧结矿中焊TiO2>0.5%,Al2O3>2.2%时,一般烧结矿低温还原粉化率RDI会大幅度升高。
7、烧结配料配碳:每增加1%,会使FeO含量升高1%-2%。
FeO含量升高1%,能耗上升0.68kggce/t,高炉燃料比也会升高1%-1.5%。
8、降低点火热耗,控制点火负压:降燃耗6%-12%,降能耗5%-6%。
可采用节能型点火炉(带状火焰、热风烧结)。
生产中,应稳定混合料水分、稳定固定碳量、厚料层、低碳、烧透等措施,以提高烧结矿质量,另外控制好冷、热返矿的粒度,也能提高烧结矿质量,同时降低能耗。
烧结助剂

几种常用的低温烧结复合助剂在实际生产中,单一助剂往往不能同时满足其烧结和机电性能的要求,一般情况下单一助剂在降低烧结温度的同时会导致陶瓷性能的降低,因此,采用多种不同助剂组成的复合添加剂要比单独使用其中一种助剂更为常见。
在选配复合助剂时一般要遵循以下原则:(1) 不同助剂之间应具有协同促进烧结的作用,多种助剂复合添加与单一助剂相比可以更好的降低烧成温度;(2) 不同助剂之间最好不发生反应,否则会减弱或抵消其促烧作用;(3) 不同助剂之间可以起到相互补充的作用,一种助烧剂在促进烧结的同时对材料性能产生的不利影响可以由另一种助剂进行弥补,故一般根据烧结助剂的作用往往选择将可以降低烧结温度的助剂与可以改善烧结体显微组织结构和烧结性能的其他助剂搭配使用。
在具体选用不同助剂组成复合助剂的时候,一般形成低共熔体系的添加剂主要以玻璃形成体如SiO2为主,辅以玻璃中间体Al2O3、BeO、ZnO 等和玻璃调整体MgO、Li2O、BaO、CaO、Sr2O 等形成MgO-Al2O3-SiO2( MAS) ,CaO-Al2O3-SiO2( CAS) ,Li2O-Al2O3-SiO2( LAS) 等系统。
对于高纯氧化铝陶瓷,通常都选用MgO 作为基本的烧结助剂进行添加,但是MgO 的高温挥发性会使陶瓷表面产生大的晶粒。
由于稀土元素添加剂可以在添加量极低的情况下很大程度地减小氧化铝的晶界长大速率,现在多采用MgO 和La2O3或Y2O3等复合的形式加入到氧化铝陶瓷中。
目前,比较常用的复合助剂主要有CaO-MgO-SiO2体系、MnO2-TiO2-MgO 体系以及CuO-SiO2体系。
1 CaO-MgO-SiO2体系采用这一体系的烧结助剂,可在1500 ~ 1550 ℃左右合成氧化铝基陶瓷。
薄占满等的研究表明体系中MgO 对氧化铝陶瓷的细晶显微结构起了重要作用,MgO 在烧结中能维持CaO/SiO2比,即维持烧结系统中的液相量,并有尖晶石、镁铝硅酸盐、铝硅酸盐、铝酸盐等多种第二相晶体生成,对晶界移动具有钉扎作用,它们有效地抑制了晶粒的生长; 同时引入了少量的La2O3、Sm2O3等稀土氧化物,使Al2O3陶瓷的烧结温度下降大约30 ℃,其表面显微结构也有所改善,这主要是由于La2O3和Sm2O3为网络变性离子,能够分解熔体网络而促进烧结。
- 1、下载文档前请自行甄别文档内容的完整性,平台不提供额外的编辑、内容补充、找答案等附加服务。
- 2、"仅部分预览"的文档,不可在线预览部分如存在完整性等问题,可反馈申请退款(可完整预览的文档不适用该条件!)。
- 3、如文档侵犯您的权益,请联系客服反馈,我们会尽快为您处理(人工客服工作时间:9:00-18:30)。
原料 A l2O3 Fe2O3 N a2O CaO MgO TiO2 SiO2 K2O
铝矾土
85 2. 0 0. 5 0. 25 0. 25 -
-
-
粘土
34 1. 04 0. 075 0. 3 0. 36 2. 05 47 0. 125
钾长石
18 0. 5 0. 3 -
-
- 65 15. 24
表 2 高铝矾土干式料的配比 (w ) Ta b le 2 Fo rm u la s o f ba uxite d ry ramm ing m ixe s %
图 6为含有钾长石的试样 K于 1 000 ℃热处理 后的 XRD 图谱 。从图中可以看出 :钾长石转变成微 斜长石 ( KA lSi3O8 ) ,该物质能提高干式料的中温烧结
图 3 粘土含量对烧结性能的影响 F ig. 3 Effe c t o f c la y co n te n t o n s in te ring p rop e rtie s
2. 3 钾长石对试样烧结性能的影响 图 4 ( a)为烧结剂中钾长石含量与干式料耐压强
度的关系曲线 。图 4 ( b)为钾长石含量对干式料显气 孔率的影响 。从图 4可以看出 :低温下钾长石对于干
编号
A B CD E F GH I J KL
骨料
65 65 65 65 65 65 65 65 65 65 65 65
粉料
35 35 35 35 35 35 35 35 35 35 35 35
硼酸 (外加 ) 0. 5 1 1. 5 2 1 1 1 1 1 1 1 1
粘土 (外加 ) 1 1 1 1 0. 5 1 1. 5 2 1 1 1 1
3
1 试验
1. 1 原料 试验的主要原料采用山西孝义的高铝矾土 ,其中
骨料粒度为 3 ~5 mm , 1 ~3 mm , ≤1 mm ,粉料粒度 ≤0. 088 mm; m (骨料 ) ∶ m (细粉 ) = 65 ∶35。烧结 剂硼酸 (w (H3 BO3 ) > 99. 6% )的粒度 ≤0. 1 mm ,粘土 粒度 ≤0. 05 mm , 钾长石粒度 ≤0. 1 mm , 硅灰粒度 ≤0. 1μm。原料的化学组成见表 1。 1. 2 试样制备与性能的测试
3 岳建设 :男 , 1980年生 ,硕士研究生 。
E2mail: yjs109@ gmail. com 收稿日期 : 2006 - 10 - 18
2007 /3 耐火材料 /NAIHUO CAILIAO 213
© 1994-2010 China Academic Journal Electronic Publishing House. All rights reserved.
式料烧结有阻碍作用 。试样 800 ℃热处理后 ,钾长石 的烧结作用才表现出来 ,试样显气孔率开始大幅升 高 。从 K2 O - A l2 O3 - SiO2 三元相图 [ 3 ]可以看出 : 钾 长石与鳞石英最低共熔点为 990 ℃,莫来石 、鳞石英 和钾长石的最低共熔点为 985 ℃。所以 ,钾长石作为 烧结剂 ,在 1 000 ℃热处理后的干式料强度随钾长石 含量的增加而逐渐提高 。此时粘土分解产物 SiO2 也 同钾长石发生固相反应 ,粘土在该温度下对耐压强度 的负面影响也被消除了 。从试验数据可以看出 :添加 钾长石的干式料在 800 ℃热处理后强度开始提高 ,这 可能是钾长石与基料中细粉及硅灰反应的结果 。硅 灰中的石英颗粒细小 ,比表面积大 ,活性很强 ,可以显 著地降低与钾长石的共熔温度 。
本试 验中 , 硼 酸的 最大 添加 量 确 定 为 2%。从 A l2O3 - B2O3 二元相图 (见图 2)判断 ,此时可形成熔点 为 1 952 ℃的高熔点矿物 。但是 ,在耐火材料的实际生 产中 ,由于混料不均匀 ,导致硼酸颗粒的分布并不均 匀。当温度升高到硼酸的熔点 ( 450 ℃)时 ,硼酸开始 熔化并局部浸润高铝颗粒 ,与颗粒中的 A l2O3 发生固 - 液反应 。B2O3 熔融微区处 A l2O3 含量相对较少 ,形 成不一致熔融化合物 2A l2 O3 ·B2 O3 [2 ] ,对干式料起初 始烧结作用。随着温度的升高 , B2O3 完全熔化并附着 于骨料颗粒表面 , B2O3 对于骨料颗粒的浸润面积增大 , 接触面积增大使得固 - 液反应增强。当 B2O3 熔融物 在颗粒表面完全铺开后 , A l2O3 的相对含量增多 ,形成 熔点为 1 952 ℃的一致熔融化合物 9A l2O3 ·2B2O3 ,填 充在骨料颗粒之间 ,形成颗粒间的联结物质。
2 结果与讨论
2. 1 硼酸对试样烧结性能的影响 图 1 ( a)为不同温度热处理后试样的耐压强度。
可以看出 : 600 ℃处理后试样的耐压强度随烧结剂中 硼酸含量的增加而增加 ,但强度增幅不大 。700 ℃热 处理后 ,试样耐压强度变化规律与 600 ℃相似 ,硼酸 含量 > 1. 5%的 试 样 耐 压 强 度 显 著 增 加 。 800 ℃、 900 ℃和 1000℃热处理后试样的耐压强度增加趋势 相同 。随着热处理温度的提高 ,全部试样耐压强度逐 步增加 ,在 600~800 ℃之间 ,每增加 100 ℃,试样的 耐压强度增幅在 40% ~150%之间 ;在 700 ~800 ℃ 之间耐压强度增加最为显著 。图 1 ( b)为试样的显气 孔率与温度的关系图 。可以看出 :硼酸含量 < 1. 5% 时 ,试样在各个温度下热处理后显气孔率变化不大 ; 当硼酸含量为 2%时 ,试样在 800 ~1 000 ℃内烧结 , 显气孔率变化很大 。
NA IHUO CA IL IAO /耐火材料 2007 , 41 (3 ) 213 ~216
开发应用
复合烧结剂对高铝质干式料烧结性能的影响
岳建设 赵敬忠 常金晶
西安理工大学材料学院 西安 710048
摘 要 以粒度 3~5 mm , 1~3 mm , ≤1 mm , ≤0. 088 mm 的高铝矾土为主要原料 ,以粒度 ≤0. 1 mm 的硼酸 (H3 BO3 > 99. 6% ) 、粒度 ≤0. 05 mm 的粘土 、粒度 ≤0. 1 mm 的钾长石和粒度 ≤0. 1 μm 的硅灰 ( SiO2 > 90% )为 复合烧结剂 ,按 m (骨料 ) ∶ m (细粉 ) = 65∶35的配比配料 。将混合料在陶瓷模具中手工捣打成型 ,将成型好 的试样分别在 600 ℃、700 ℃、800 ℃、900 ℃和 1 000 ℃下均保温 2 h后脱模 。测量热处理后各试样的耐压强度 和显气孔率 ;采用 XRD 分析了试样的物相组成 。结果表明 :复合烧结剂中钾长石和硼酸在中温 、低温下具有良 好的烧结作用 ,在 700~800 ℃热处理后 ,试样耐压强度和显气孔率明显增加 。硼酸含量为 2%的试样 ,在 800~ 1 000 ℃热处理后 ,显气孔率增幅较大 。添加硅灰可以降低钾长石烧结温度 ;而复合烧结剂中的粘土在中温 、低 温下不利于干式料的烧结 ,低于 800 ℃热处理后的试样 ,耐压强度和显气孔率没有随粘土含量增加而变化 ; 900 ~1 000 ℃热处理后的试样 ,耐压强度随粘土含量的增加而降低 ,显气孔率增加不大 。 关键词 烧结性能 ,干式料 ,复合烧结剂
图 2 A l2O3 - B2O3 二元相图 F ig. 2 A l2O 3 - B2O 3 p ha se d ia g ram
2. 2 粘土对试样烧结性能的影响 图 3 ( aLeabharlann 为烧结剂中粘土含量与干式料耐压强度
的关系曲线 。图 3 ( b)为粘土含量与干式料显气孔率 的关系图 。可以看出 :随着温度的增加 ,材料的耐压 强度和显气孔率都逐渐升高 。600 ℃、700 ℃下烧后 试样的耐压强度没有随着粘土含量的增加而增加 ,材 料的气孔率也变化不大 。这说明粘土在低温下没有 起烧结作用 ,试样总的耐压强度随温度增加而增加的 主要原因是复合烧结剂中硼酸的作用结果 。试样在 900 ℃和 1 000 ℃热处理后 ,耐压强度随粘土含量的 增加呈下降趋势 。这是因为粘土的主要成分是高岭 石 (A l2 O3 ·2SiO2 ·2H2 O ) ,高岭石在低于 1 000 ℃条 件下脱水生成偏高岭石 (A l2 O3 ·2SiO2 ) 。偏高岭石 在 1 000 ℃开始发生如下分解 :
高铝质干式料的配料组成见表 2。按表 2的配比
称料 ,干混均匀后倒入 <34 mm ×50 mm 的陶瓷模具中
手工捣打成型 ,每种配料制备 3个试样 。将成型好的
试样分别在 600 ℃、700 ℃、800 ℃、900 ℃和 1 000 ℃下
均保温 2 h后脱模。
表 1 原料的化学组成 (w ) Ta b le 1 C hem ica l com po s itio n o f s ta rting m a te ria ls %
钾长石 (外加 ) 0. 5 0. 5 0. 5 0. 5 1 1 1 1 0. 5 1 1. 5 2
硅灰 (外加 ) 2 2 2 2 2 2 2 2 2 2 2 2
用排水法测试试样的显气孔率 。将不同温度下 热处 理 的 试 样 置 于 W E - 100 万 能 试 验 机 上 , 以 1 mm ·m in- 1的速度加压 ,进行耐压强度测试 。采用 XRD 对试样进行物相分析 。
A l2 O3 ·2SiO2 →A l2 O3 + 2SiO2 此时没有液相生成 ,分解产物也没有和其他物质反 应 ,添加的微量硼酸已经与粉料中的 A l2 O3 和 SiO2 形 成化合物而无剩余 。高岭石的分解产物孤立存在 ,当 粘土含量增大后 ,分解产物 A l2 O3 和 SiO2 增多 ,将已