微波碳热还原转炉干法除尘灰LT灰生产金属化球团
转炉煤气干法LT净化回收技术的应用及防爆措施

转炉煤气干法LT净化回收技术的应用及防爆措施概述炼钢厂在生产过程中会产生大量的转炉煤气,其中含有大量的有害物质,如一氧化碳、二氧化碳等,对环境造成威胁。
为了减少煤气对环境的影响,炼钢厂引入了转炉煤气干法LT净化回收技术。
技术原理转炉煤气干法LT净化回收技术是一种先将煤气进行除尘、水分脱除等处理后,采用催化剂进行低温净化,在净化完成后再进行回收利用的技术。
该技术的主要原理是:将煤气进行过滤处理,去除其中的杂质和水分,再通过特制的催化剂进行净化处理,使其中的有毒有害物质转化为无害化合物,最后再将净化后得到的煤气进行回收利用。
此种净化方式是比传统的高温净化的方式更加环保,且更加节能。
应用情况转炉煤气干法LT净化回收技术目前已经在国内多家炼钢厂得到了广泛应用,其净化效果得到了良好的验证。
它不仅可以降低污染排放,而且可以提高资源利用率,收益显著。
在使用过程中,需要做好相关的防爆措施,以确保工作安全。
防爆措施作为一种较为安全的净化方式,转炉煤气干法LT净化回收技术在实际使用过程中也需要做好相应的防爆措施。
具体可采取以下措施:1.操作人员必须接受专业的培训,熟练掌握操作技能及相关安全规范。
2.对设备进行定期检查维护,确保设备处于良好的工作状态,减少设备故障以及为防止事故的发生留下隐患。
3.在压力较高的部位加装爆炸防护装置,防止在操作过程中因煤气燃爆出现安全事故。
4.注意防火措施,在操作现场设立消防设施,在操作过程中严格控制火源,尽可能避免火花等潜在火源的出现。
通过加强设备维修保养,并加强操作人员的安全意识,可帮助工作人员避免由于设备故障或操作不当导致的事故发生。
结论转炉煤气干法LT净化回收技术是一种环保且高效的煤气净化方式,已经在国内多家炼钢厂得到了操纵和推广。
在此技术的应用过程中,我们需要加强设备维修保养,注重安全教育培训,在操作现场设立消防设备,注意防火措施等,可实现安全可靠的运转。
虽然转炉煤气干法LT技术已经得到了广泛应用,但我们还需要进行更深入的研究以优化该技术,并进一步推广和应用。
科技成果——转底炉煤基直接还原处理含铁尘泥生产金属化球团
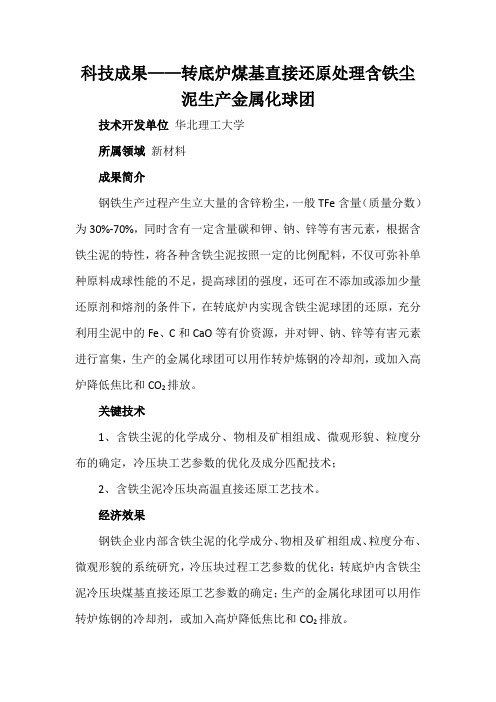
科技成果——转底炉煤基直接还原处理含铁尘
泥生产金属化球团
技术开发单位华北理工大学
所属领域新材料
成果简介
钢铁生产过程产生立大量的含锌粉尘,一般TFe含量(质量分数)为30%-70%,同时含有一定含量碳和钾、钠、锌等有害元素,根据含铁尘泥的特性,将各种含铁尘泥按照一定的比例配料,不仅可弥补单种原料成球性能的不足,提高球团的强度,还可在不添加或添加少量还原剂和熔剂的条件下,在转底炉内实现含铁尘泥球团的还原,充分利用尘泥中的Fe、C和CaO等有价资源,并对钾、钠、锌等有害元素进行富集,生产的金属化球团可以用作转炉炼钢的冷却剂,或加入高炉降低焦比和CO2排放。
关键技术
1、含铁尘泥的化学成分、物相及矿相组成、微观形貌、粒度分布的确定,冷压块工艺参数的优化及成分匹配技术;
2、含铁尘泥冷压块高温直接还原工艺技术。
经济效果
钢铁企业内部含铁尘泥的化学成分、物相及矿相组成、粒度分布、微观形貌的系统研究,冷压块过程工艺参数的优化;转底炉内含铁尘泥冷压块煤基直接还原工艺参数的确定;生产的金属化球团可以用作转炉炼钢的冷却剂,或加入高炉降低焦比和CO2排放。
实施条件
钢铁企业,具备一定生产能力。
项目成熟度
产品级:批产合格、图纸完备、工艺成熟合作方式合作开发。
转炉煤气LT干法除尘工艺研究
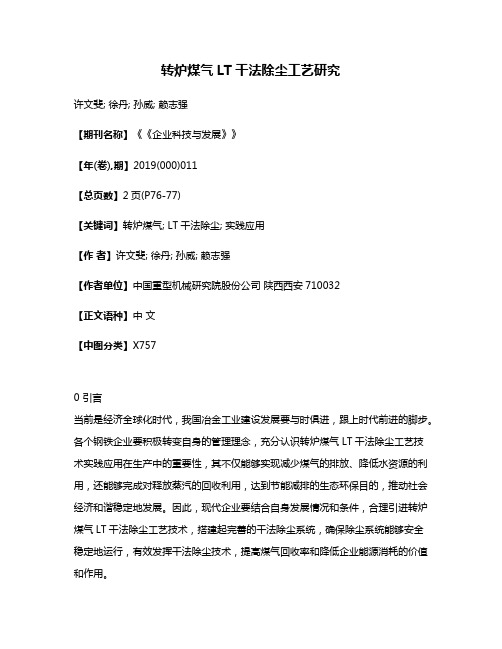
转炉煤气LT干法除尘工艺研究许文斐; 徐丹; 孙威; 赖志强【期刊名称】《《企业科技与发展》》【年(卷),期】2019(000)011【总页数】2页(P76-77)【关键词】转炉煤气; LT干法除尘; 实践应用【作者】许文斐; 徐丹; 孙威; 赖志强【作者单位】中国重型机械研究院股份公司陕西西安710032【正文语种】中文【中图分类】X7570 引言当前是经济全球化时代,我国冶金工业建设发展要与时俱进,跟上时代前进的脚步。
各个钢铁企业要积极转变自身的管理理念,充分认识转炉煤气LT干法除尘工艺技术实践应用在生产中的重要性,其不仅能够实现减少煤气的排放、降低水资源的利用,还能够完成对释放蒸汽的回收利用,达到节能减排的生态环保目的,推动社会经济和谐稳定地发展。
因此,现代企业要结合自身发展情况和条件,合理引进转炉煤气LT干法除尘工艺技术,搭建起完善的干法除尘系统,确保除尘系统能够安全稳定地运行,有效发挥干法除尘技术,提高煤气回收率和降低企业能源消耗的价值和作用。
1 转炉煤气除尘方式转炉煤气除尘方式被划分为两种:一种是湿法除尘工艺,另一种是干法除尘工艺。
前者发展至今已经有50 多年,从最早的IC 法到如今的OG法,它的工作原理是通过促使煤气中的尘粒与水进行相互碰撞凝聚,从而实现尘粒与气流的有效分离目标,该种除尘方式操作简单、系统安全可靠[1],但是在实际工作中容易产生二次污染,并且会消耗大量的水资源,因此,不利于生态环境与社会经济的协调发展。
后者最早由蒂森公司与西德鲁奇公司共同研发推出,干法除尘技术简称为LT法,该项除尘方法的工作原理是通过合理利用电极放电促使煤气中尘粒带电,然后在电场作用下将尘粒吸附在集尘电极上。
干法除尘工艺最大的优势在于除尘工作质量好、效率高,能够帮助企业节省更多能源,避免各项资源浪费。
经测算,干法除尘系统循环水量是湿法除尘的28%,是湿式除尘系统的1/5左右。
整个系统实现了污水零排放,避免了二次污染,节水效果显著。
转炉煤气LT法净化技术及在中国的应用

转炉煤⽓LT法净化技术及在中国的应⽤转炉煤⽓LT法净化技术及在中国的应⽤蔡富良(⼴东省韶钢设计院⼴东512123 )摘要: 转炉⼀次烟⽓静电除尘(LT法)是钢铁⾏业节能降耗的重要技术之⼀,钢铁协会贯彻《钢铁产业政策》时将其列为“三⼲三利⽤”等六⼤类先进技术加以重点推⼴。
本⽂介绍了转炉⼀次烟⽓静电除尘(LT法)技术的发展、应⽤,并对LT法及OG法进⾏⽐较,建议国内加快LT法的推⼴,尤其是现使⽤OG法的企业应在条件具备下加快改造,实现节能减排,以降低成本、保护环境。
LT法的采⽤将为钢铁⾏业年节约成本⼏⼗亿元,并可为国家提出的“⼗⼀五”期间单位GDP能耗降低20%做贡献。
关键词:转炉煤⽓静电除尘(LT法)OG法节能降耗⼤⼒推⼴Application of Converter coal gas LT method of purifying technology in ChinaCAI Fu-Liang(Design Institute of Shaoguan Iron& Steel Company, guangdong 512100,China) Abstract: Converter haze electrostatic dust removal (LT method) is one of important techniques in the steel and iron industry to save energy and reduce consumes. It has been listed as it "three dyies, three uses" , one of six kind of advanced techniques, and has been mainly promoted., when the steel and iron association implements "Steel and iron Industry policy" .This article emphasizes on the development of the technology of Converter haze electrostatic dust removal (LT method) ,its application, and the comparison between LT and OG method. It suggests popularizing LT method at all attempts, especially the enterprises using OG method should quicken the speed of rebuilding on providedconditions in order to reduce cost and protect environment. The application of LT method will save the cost of scores of billions for steel and iron industry and reduce 20% energy consume on unit GDP in the period of “eleven-five” layout. Key words: Converter coal gas, electrostatic dust removal(LT method),OG method, energy-saving and consume-reducing, popularize at all attempts,1.前⾔转炉煤⽓⼲式除尘由于采⽤静电除尘器作为净化设施,在净化效果、能耗、占地⾯积、操作运⾏费等⽅⾯都⽐OG法更优越,⽽且没有OG法带来的⽔处理、污泥处理及对环境的⼆次污染,⾼含铁粉尘可直接回收利⽤,在国际上已被认定为今后的发展⽅向,世界各国都陆续采⽤。
转底炉生产金属化球团工业性试验
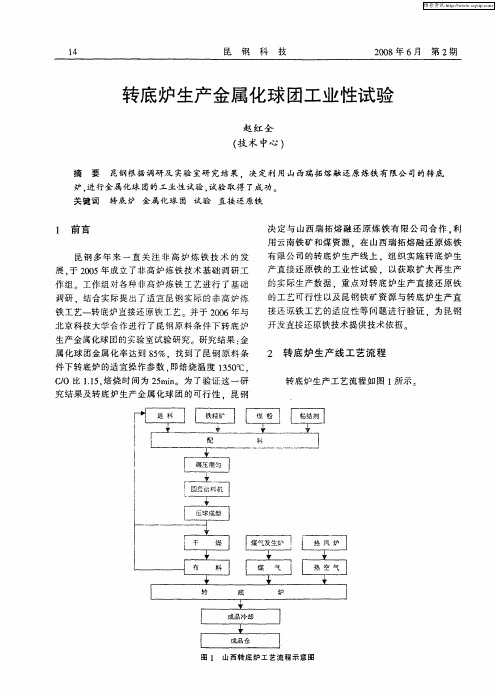
试 验用 转 底 炉 工 艺 采用 的是 两段 间接水 套 振
动冷却机 。 冷却效果不理想 。 且在第一段冷却机 内
适 当喷 水 加 强 冷却 , 果 仍 不理 想 。 多次 发生 因 效 曾 金属 化球 团 温度 过高 (3 o , 致堆 存后 “ > o℃)导 自燃 ” ( 二次 氧化 ) 的现象 。
决 定 与 山西瑞 拓 熔 融 还原 炼 铁 有 限公 司 合作ห้องสมุดไป่ตู้. 利 用 云南 铁 矿 和煤资 源 .在 山西 瑞 拓熔 融还 原 炼铁
有 限公 司 的转 底炉 生产 线上 .组 织实 施转 底 炉 生
产 直接 还原 铁 的工业 性 试验 .以 获取 扩大 再 生产
作 组 工作 组对 各种 非高 炉炼 铁 工 艺进行 了基 础
维普资讯
1 4
昆
钢
科
技
20 0 8年 6月 第 2期
转底炉 生产 金属化球 团工业性试 验
赵 红 全
( 术 中心 ) 技
摘 要 昆钢根 据调 研及 实验 室研 究 结 果 .决 定利 用 山西瑞 拓 熔融 还原 炼铁 有 限公 司的转底
的实 际生产 数据 .重 点对 转 底 炉 生产 直接 还 原铁
的工 艺可行 性 以及 昆钢 铁矿 资 源 与转 底炉 生 产直 接 还 原铁工 艺 的适应 性 等 问题 进行 验证 .为 昆钢
调研 .结合 实际 提 出了适 宜 昆钢 实 际的 非 高炉 炼
铁工艺 一转底炉 直接还原 铁工 艺 。并 于 2 0 0 6年与 北 京科 技 大学合 作进行 了昆 钢原料 条 件 下转 底 炉
一种转炉干法除尘灰冷固球团生产工艺[发明专利]
![一种转炉干法除尘灰冷固球团生产工艺[发明专利]](https://img.taocdn.com/s3/m/3c7794b8312b3169a551a48c.png)
专利名称:一种转炉干法除尘灰冷固球团生产工艺
专利类型:发明专利
发明人:王欣,李长兴,向海升,崔乾民,王纪英,杨晓明,张全申申请号:CN201110258059.7
申请日:20110902
公开号:CN102367499A
公开日:
20120307
专利内容由知识产权出版社提供
摘要:一种转炉干法除尘灰冷固球团生产工艺,属于资源综合利用和环境保护技术领域。
实现该工艺的设备包括原料系统、消化系统、混碾系统、造球系统、成品系统及输送系统,主要用于转炉干法除尘灰中金属铁元素的回收。
转炉干法除尘灰冷固球团生产工艺使转炉干法除尘灰通过“配料-消化-混碾-压球-表面固化”等环节,最终生产出符合转炉使用要求的冷固球团。
冷固球团可替代铁矿石或球团矿作为转炉炼钢的冷却剂、造渣剂回用转炉,从而大大降低外购含铁资源的费用,经济效益和社会效益显著,符合循环经济模式。
申请人:北京首钢国际工程技术有限公司
地址:100043 北京市石景山区石景山路60号
国籍:CN
代理机构:北京华谊知识产权代理有限公司
代理人:刘月娥
更多信息请下载全文后查看。
- 1、下载文档前请自行甄别文档内容的完整性,平台不提供额外的编辑、内容补充、找答案等附加服务。
- 2、"仅部分预览"的文档,不可在线预览部分如存在完整性等问题,可反馈申请退款(可完整预览的文档不适用该条件!)。
- 3、如文档侵犯您的权益,请联系客服反馈,我们会尽快为您处理(人工客服工作时间:9:00-18:30)。
钢铁冶金含铁粉尘综合利用项目简介重庆连横冶金技术有限公司重庆科健冶金材料有限公司重庆大学材料科学与工程学院二〇一四年十二月钢铁冶金含铁粉尘综合利用项目简介一、前言在钢铁冶炼过程中,需要经过选矿、烧结、炼铁、炼钢、轧钢等生产工序,各工序都会产生一些不同的工业固体废弃物。
根据生产流程不同,吨钢固体废弃物产生量约300~500 kg。
只有部分成分及物理性能稳定的粉尘和副产品在工艺流程中得到了有效的回收利用,但仍有相当部分排放堆积,既浪费了资源,又污染了环境。
含铁固体废弃物的典型化学成分见表1。
表1 含铁固体废弃物的典型化学成分 %转炉炼钢过程中,由于点火区高温蒸发和一氧化碳气泡带走部分铁产生粉尘,每冶炼1t钢将产生10~25kg粉尘(主要成分为FeO和Fe2O3)。
粉尘造成的铁损已成为炼钢过程较大的金属吹损。
按国内年产8亿t转炉钢计算,不计其它元素损失量,每年仅粉尘排放造成的金属铁损达400万t以上。
人类社会与现代工业发展至今,发展循环经济已得到世界的普遍认同,并成为人类文明进步的时代要求。
当今,我国钢铁工业持续迅猛发展,在产能极度膨胀的同时,也受到了资源、能源和环境三大因素的严峻考验。
只有走发展循环经济之路、环保健康之路,才能真正解决制约钢铁工业发展的瓶颈问题,使自己的企业在节能减排、淘汰落后的大环境中持续健康发展。
转炉炼钢过程采用干法或湿法除尘,形成的除尘灰和污泥粒径较细,为5~15μm,铁品位约50%左右,并含有一定的金属铁,二次利用价值较高。
目前大多数钢铁企业采用直接配入烧结系统回用的方式处理。
该方式在一定程度上实现了除尘灰资源的回收利用,但是对烧结透气性影响较大,锌等金属蒸汽随烧结矿进入高炉,并在高炉内循环富集,致使高炉结瘤,影响高炉正常生产。
为此,国内部分钢铁企业已经开始考虑将除尘灰等含铁资源加工为冷固球团直接用于转炉炼钢过程短循环使用,既可促进化渣和回收铁等有价资源,又可代替铁矿石作为调温、调渣剂,这无疑是一个最经济,并对炼钢成本有重大贡献的有效回收利用方法。
但是,目前国内生产冷固球团工艺较落后,生产成本高、周期长,并且强度低、水分高,制约了冷固球在转炉炼钢环节大量推广使用。
为此,我公司联合重庆大学材料科学与工程学院自2006年开始了对转炉除尘灰在转炉短流程使用的研究。
经过近年来的努力,利用研发的高效复合粘接剂及对应的工艺技术,解决了上述问题,使用此技术,可根据炼钢的钢种与渣系要求,以转炉除尘灰等含铁粉尘为基料,与其它辅料一块混合,用复合粘结工艺技术,制成系列造渣材料,送高位料仓供转炉直接使用。
使用此技术,我们遵循“追求资源高效循环利用、不影响炼钢主流程生产、实现短流程直接使用”的原则,将可用于炼钢生产的元素(铁、碳、钙等)尽可能回收循环利用,真正实现“变废为宝”和资源高效利用。
经过对首钢、宝钢等国内大型钢厂同类材料的处理工艺对比,该工艺生产的冷固球团无论是强度还是残余水分指标都远远优于国内同行,处于国内领先水平。
目前该冷固球团产品已经正常在重钢转炉炼钢厂大量使用,代替传统化渣剂作为炼钢化渣熔剂,代替铁矿石作为炼钢冷却剂,实现了炼钢副产品资源的有效利用,为重钢炼钢厂含铁资源综合利用实现降本降耗发挥了积极作用。
该工艺方案设计先进、自动化程度高,过程控制便捷,由于采用高效复合粘接剂成型技术,产品强度高。
冷固球半成品自然固结反应存放3~5天后即可自然干燥达到入炉水分要求。
另外根据成品球团水分具体要求,可适当延长自然固结反应时间或增设成品球烘干装置,使得成品球水分达到入炉要求,通常成品冷固球水分控制在5%以内。
该工艺技术已申请国家发明专利并受理。
二、转炉除尘灰生产冷固球品种工艺技术及其应用转炉除尘灰的主要成分为转炉冶炼过程中产生的铁氧化、以及废钢铁锈产生的氧化铁粉尘,同时还存在散状料(石灰等)在冶炼过程中加入时其细粉被烟气带出的粉尘。
因此,其主要成分应为氧化铁及氧化钙等物质。
由上述表1可见,除尘灰中主要成分氧化铁、氧化钙、氧化镁,其都是转炉炼钢氧化精炼所须物质,并且酸性物质SiO2低,这无凝对回收利用于炼钢过程的造渣材料是有益的。
粉尘中由于存在硫的挥发富集,硫含量较高,如果入炉原料硫控制得当,可望将粉尘中硫控制在,转炉入炉散状料对硫要求小于0.2%的基本要求范围。
由此,可根据其成分特点,以除尘灰为基础原料,根据炼钢的钢种与渣系要求,配加相应添加剂,采用复合粘结工艺技术,制成具有较高强度的系列造渣材料。
该系列材料可制成球状,具有较高强度,可以满足从高位料仓进料的要求,属于循环综合利用产品,社会效益显著。
具体材料可分以下三类:1、配镁造渣剂配镁造渣剂用于转炉吹炼初期,其主要作用是造早期高氧化铁、碱性含氧化镁渣。
造渣剂主要成份是FeO、Fe2O3和MgO。
冶金热力学表明,在碱性氧化渣中,如果MgO含量在<8%时,MgO的存在将对石灰起助熔作用,并且在初期渣中配入一定量的MgO,可防止初期低碱度渣对炉衬的浸蚀。
因此,转炉炼钢过程须在初期渣中配入一定量的MgO,一般控制在6~8%范围。
现常采用的配镁方式为,向初期渣中配入一定量的轻烧白云石。
但轻烧白云石吸热量大,这影响废钢的加入量。
因此,直接向转炉初期渣中配加一定量的MgO,实现初期高效低吸热的配镁方式是需要的。
该研究以转炉除尘粉为基料,配入一定量的氧化镁,利用其中的氧化铁,使其形成熔点在1580~1610℃,熔点低于MgO的MgO.Fe2O3,实现对初期渣的高效低吸热的配镁。
配镁造渣剂成分及性能指标由表2所示。
加入时间:配镁造渣剂用于转炉冶炼初期,其主要作用为对炉渣配镁,以实现炉渣快速熔化和保护炉衬为目的。
因此,它将随转炉吹炼时,第一批渣料加入。
加入量:配镁造渣剂加入量按初期渣中MgO含量为6~8%,白云石加入量、渣量确定。
一般为6~10Kg/t钢。
表2 配镁造渣剂成分及性能指标2、转炉炼钢脱磷促进剂转炉炼钢过程是一个速度快、周期短的高效氧化精炼过程。
其中脱磷反应是其主要任务之一。
它是利用炼钢过程的高氧化性、高碱性炉渣来实现。
由于该反应为放热反应,因此冶炼前期的低温条件是脱磷的有利时期,而在冶炼后期的高温下,如果控制不当会出现高温回磷现象。
因此为实现炼钢过程的高效脱磷,须实现在冶炼前期快速成渣,利用前期低温好的热力学条件高效脱磷,将磷降到目标要求,而在冶炼后期高温下,须控制好熔渣的碱度及氧化性,防止冶炼中后期因渣中氧化铁的过分消耗,使熔渣氧化性低,并且温度又高的条件,而出现脱磷热力学条件被破坏,发生回磷的现象。
因此,常用的方法为,在冶炼的中后期,及冶炼的过程中须适时向熔池中补充因脱碳消耗的 (FeO),保证高氧化性、高碱性脱磷热力学条件,来防止回磷,以保证转炉炼钢的脱磷效率。
根据上述机理,该研究将以除尘灰为基料,利用其高的氧化铁组元,及活性的氧化钙成分,同时引入了活性BaO材料,组成了一种由Fe2O3、CaO、BaO物质组成的高氧化性、高碱性低熔点的脱磷促进剂,实现对转炉炼钢过程补充(FeO),加强脱磷效率,实现高效脱磷的作用。
脱磷促进剂成分由表3所示。
该产品中引入的BaO可实现强化脱磷的作用。
因BaO渣系比CaO渣系有更强的脱磷能力,在高温下生成的脱磷产物更为稳定。
研究表明:1500℃时,CaO渣系的磷酸根容量是1025.7,而20%BaO渣系磷酸根容量是1027.7,大了2个数量级。
这对保证脱磷效率,防止后期高温回磷很有意义。
该产品主要成分为Fe2O3、CaO、BaO,熔化后形成的产物为:铁酸钙、铁酸钡。
其熔点分别为1200~1300℃、1300~1400℃。
因此,该脱磷促进剂熔点低,不仅具有强的脱磷促进能力,并且还具有强的化渣助熔作用。
使用方法如下:加入时间:脱碳反应开始后,随第二批料分批加入,在氧化铁消耗到最低前(返干前)加完。
加入量:10~15Kg/t钢。
表3 转炉炼钢脱磷促进剂理化指标3、转炉炼钢调温剂转炉炼钢是通过铁水的物理热及化学反应热来保证造渣材料的熔化及出钢温度。
一般铁水的物理热及化学反应热都大于转炉炼钢所需要的热量,这须加一定量的冷却剂进行调整,使之保证出钢终点温度的要求。
常用冷却剂为:废钢、铁矿石、氧化铁皮球。
由于加入方法的限制,常将铁矿石及氧化铁皮球作为过程调温用冷却剂,同时加入的氧化铁既作了氧化剂,其还原后其中铁又得到回收,无凝是好的调温剂。
但铁矿石中SiO2含量高,为保证一定的脱磷碱度,会增加渣量。
而氧化铁皮来源又受限,其中所含的水和油清除难度大。
表1所示的转炉除尘粉,不仅有高的氧化铁含量,而且SiO2含量低,其中所含的CaO活性高,也是炼钢精炼所须材料,因此用其添加一定量的氧化铁皮,回收利用为转炉炼钢过程的调温剂,将克服铁矿石及氧化铁皮球调温剂的缺点。
由此,利用转炉除尘粉开发了环保型转炉炼钢调温剂,成分及性能指标见表4所示。
表4 转炉炼钢调温剂成分及性能指标加入量将根据熔池温度确定。
加入时间为:转炉冶炼的中后期加入为宜,也可在废钢料斗中加入。
三、除尘灰冷固球在炼钢过程中的冶金作用及应用效果3.1加快成渣速度。
冷固球团加入,在转炉炼钢过程中增加了前期渣中FeO 的含量,加快成渣速度,改善了冶炼过程中的脱P 、脱S 效果。
脱磷反应的反应式2[P]+5[O]=(P 2O 5) (1)2[P]+5(FeO)+3(CaO)=(3CaO P 2O 5)+5[Fe] (2)2[P]+5(FeO)+4(CaO)=(4CaO P 2O 5)+5[Fe] (3)按照炉渣离子模型2[P]+5(Fe 2+)+8(O 2-)=2(PO 43-)+5[Fe] (4)2[P]+5[O]+8(O 2-)=2(PO 43-) (5)∑+⨯+-=)log(%5.2)(%08.00.1623350][)(log Fe CaO T P P 3.2改善渣料结构,提高冷却效果。
随着冷固球团的加入,石灰的熔化速率提高,同时由于冷固球团含有一定量的CaO ,可以减少石灰消耗。
图一 氧化物含量对炼钢炉渣熔化温度及石灰熔化速度的影响3.3简化炉前操作。
由于冷固球团加入带来的良好化渣效果,可以减少萤石甚至不加,代替铁矿石、烧结返矿等材料,大大简化了炉前操作。
传统工艺——向熔池中加铁矿石、烧结返矿、氧化铁皮球进行化渣、控温,但铁矿石、烧结返矿中SiO2含量高,为保证一定的脱磷碱度,会增加渣量。
而氧化铁皮来源又受限,其中所含的水和油清除难度大。
3.4提高金属收得率,冷固球中Tfe含量在55%以上,在炼钢过程中加入,可以有效提高金属收得率。
如图中所示,由于供氧为脱碳限制性环节,在此前加入的除尘灰球,都可使除尘灰中的氧化铁被碳还原,实现回收除尘灰中金属铁的目的。
而该加入时期也是脱磷化渣、控温的要求时期。
3.5有利于提高转炉炉衬寿命。