无缺陷含Nb连铸坯的生产综述
连铸坯缺陷的产生与防止措施 Microsoft Word 文档1

连铸坯裂纹的产生与防止措施连铸坯裂纹的分类 :铸坯表面裂纹包括表面纵裂纹、表面横裂纹、网状裂纹(星裂)、发裂、角部纵裂纹、角部横裂纹等;铸坯内部裂纹包括中间裂纹、角部裂纹、中心线裂纹、三角区裂纹、皮下裂纹、矫直裂纹等。
1.1 铸坯表面裂纹部纵裂纹等几种主要的缺陷形式。
铸坯表面裂纹主要有表面纵裂纹、表面横裂纹、网状裂纹、角部横裂纹、边铸坯表面裂纹是在结晶器内产生的,在二冷段得到扩展。
它会导致轧制板材表面的微细裂纹,影响最终产品的表面质量。
图1为表面裂纹示意图图 1 铸坯表面裂纹示意图1-表面纵裂纹;2-表面横裂纹;3-网状裂纹;4-角部横裂纹;5-边部纵裂纹1.1.1 表面纵裂纹连铸坯表面纵裂纹是指沿着拉坯方向在铸坯表面上发生的裂纹。
它可由工艺因素或设备因素引起。
由工艺因素引起的纵裂,大多出现在铸坯宽面的中央部位,是表面裂纹中最常见的一种裂纹缺陷。
纵裂主要是由于初生坯壳在结晶器内冷却强度不均匀,造成应力的集中,在坯壳相对较薄的地方坯壳厚度不足以承受这种应力,致使坯壳裂开而产生裂纹,并在二冷区得到扩展,形成表面纵裂纹。
图2 图3 图4为表面纵裂纹示意图图2图3 图41.影响连铸坯表面纵裂纹因素:实际生产过程中,主要有以下因素影响连铸坯表面纵裂纹的产生:1) 成品成分及钢水质量(1) 成品钢中碳含量处在亚包晶和包晶反应区时,由于初生坯壳在结晶器弯月面内激冷时收缩较大,容易造成初生坯壳厚薄不均,从而使铸坯发生纵裂纹的倾向增加。
因此,在实际生产中各连铸厂家都尽量控制其成品钢中碳含量,使其避开亚包晶和包晶反应区,从而减少铸坯纵裂纹的发生机率。
(2) 成品钢中硫、磷含量也会影响铸坯纵裂纹的产生。
钢中硫、磷含量增加时,钢的高温强度和塑性明显降低,在应力作用下就容易产生裂纹,因此,在实际生产中各连铸厂家都尽量控制其成品钢中硫、磷含量,尽量控制在0.02%以内。
(3) 钢中微合金如铌、钒等对铸坯纵裂纹的产生也有重要影响,因为微合金而产生的铸坯纵裂纹在铸坯表面上分布不规则,缺陷较短、数量较多。
我国薄板坯连铸连轧技术成就综述
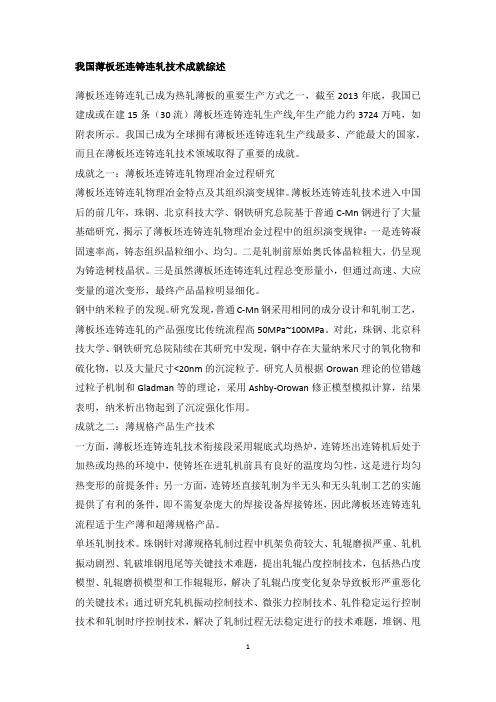
我国薄板坯连铸连轧技术成就综述薄板坯连铸连轧已成为热轧薄板的重要生产方式之一,截至2013年底,我国已建成或在建15条(30流)薄板坯连铸连轧生产线,年生产能力约3724万吨,如附表所示。
我国已成为全球拥有薄板坯连铸连轧生产线最多、产能最大的国家,而且在薄板坯连铸连轧技术领域取得了重要的成就。
成就之一:薄板坯连铸连轧物理冶金过程研究薄板坯连铸连轧物理冶金特点及其组织演变规律。
薄板坯连铸连轧技术进入中国后的前几年,珠钢、北京科技大学、钢铁研究总院基于普通C-Mn钢进行了大量基础研究,揭示了薄板坯连铸连轧物理冶金过程中的组织演变规律:一是连铸凝固速率高,铸态组织晶粒细小、均匀。
二是轧制前原始奥氏体晶粒粗大,仍呈现为铸造树枝晶状。
三是虽然薄板坯连铸连轧过程总变形量小,但通过高速、大应变量的道次变形,最终产品晶粒明显细化。
钢中纳米粒子的发现。
研究发现,普通C-Mn钢采用相同的成分设计和轧制工艺,薄板坯连铸连轧的产品强度比传统流程高50MPa~100MPa。
对此,珠钢、北京科技大学、钢铁研究总院陆续在其研究中发现,钢中存在大量纳米尺寸的氧化物和硫化物,以及大量尺寸<20nm的沉淀粒子。
研究人员根据Orowan理论的位错越过粒子机制和Gladman等的理论,采用Ashby-Orowan修正模型模拟计算,结果表明,纳米析出物起到了沉淀强化作用。
成就之二:薄规格产品生产技术一方面,薄板坯连铸连轧技术衔接段采用辊底式均热炉,连铸坯出连铸机后处于加热或均热的环境中,使铸坯在进轧机前具有良好的温度均匀性,这是进行均匀热变形的前提条件;另一方面,连铸坯直接轧制为半无头和无头轧制工艺的实施提供了有利的条件,即不需复杂庞大的焊接设备焊接铸坯,因此薄板坯连铸连轧流程适于生产薄和超薄规格产品。
单坯轧制技术。
珠钢针对薄规格轧制过程中机架负荷较大、轧辊磨损严重、轧机振动剧烈、轧破堆钢甩尾等关键技术难题,提出轧辊凸度控制技术,包括热凸度模型、轧辊磨损模型和工作辊辊形,解决了轧辊凸度变化复杂导致板形严重恶化的关键技术;通过研究轧机振动控制技术、微张力控制技术、轧件稳定运行控制技术和轧制时序控制技术,解决了轧制过程无法稳定进行的技术难题,堆钢、甩尾事故减少90%;通过轧辊长寿技术,包括低应力抗剥落支承辊辊形、新型工艺润滑技术、轧辊材质和辊径配置的研究,使前段、后段工作辊和支承辊的轧制周期分别延长了80%、33%和50%,实现了薄规格产品的批量生产。
无缺陷铸坯生产技术概述
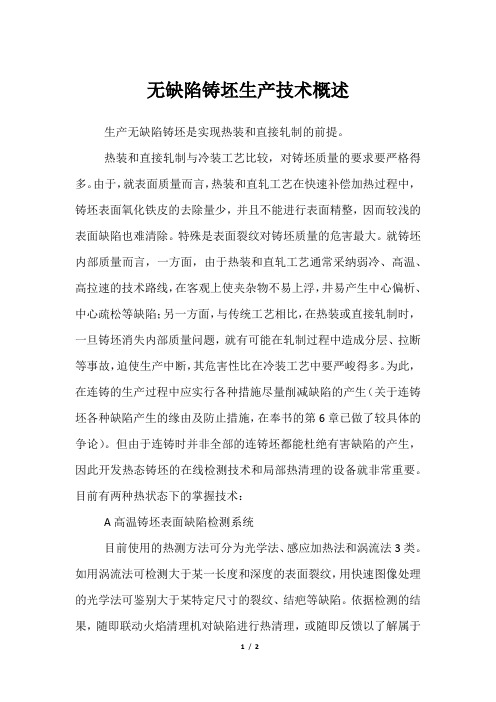
无缺陷铸坯生产技术概述生产无缺陷铸坯是实现热装和直接轧制的前提。
热装和直接轧制与冷装工艺比较,对铸坯质量的要求要严格得多。
由于,就表面质量而言,热装和直轧工艺在快速补偿加热过程中,铸坯表面氧化铁皮的去除量少,并且不能进行表面精整,因而较浅的表面缺陷也难清除。
特殊是表面裂纹对铸坯质量的危害最大。
就铸坯内部质量而言,一方面,由于热装和直轧工艺通常采纳弱冷、高温、高拉速的技术路线,在客观上使夹杂物不易上浮,井易产生中心偏析、中心疏松等缺陷;另一方面,与传统工艺相比,在热装或直接轧制时,一旦铸坯消失内部质量问题,就有可能在轧制过程中造成分层、拉断等事故,迫使生产中断,其危害性比在冷装工艺中要严峻得多。
为此,在连铸的生产过程中应实行各种措施尽量削减缺陷的产生(关于连铸坯各种缺陷产生的缘由及防止措施,在奉书的第6章已做了较具体的争论)。
但由于连铸时并非全部的连铸坯都能杜绝有害缺陷的产生,因此开发热态铸坯的在线检测技术和局部热清理的设备就非常重要。
目前有两种热状态下的掌握技术:A高温铸坯表面缺陷检测系统目前使用的热测方法可分为光学法、感应加热法和涡流法3类。
如用涡流法可检测大于某一长度和深度的表面裂纹,用快速图像处理的光学法可鉴别大于某特定尺寸的裂纹、结疤等缺陷。
依据检测的结果,随即联动火焰清理机对缺陷进行热清理,或随即反馈以了解属于何种不正常浇注操作所引起的这种缺陷,准时修正操作。
B铸坯在线质量推断系统实现铸坯质量的在线推断,以对铸坯质量做出评价,这是目前的进展趋势。
铸坯在线质量推断系统是以严格执行标准化浇注操作为基础的。
经过多年的生产实践,现已能定量的确定钢液成分、浇注工艺、设备状态和生产管理等因素对铸坯表面缺陷(裂纹、夹渣、气孔等)、内部缺陷(夹杂、偏析、裂纹等)和外形缺陷(如铸坯鼓肚、脱方等)的影响。
在浇注过程中,可将影响连铸坯质量的参数输入计算机,经分析后判定质量是否合格,井将不合格的铸坯剔出,进行清理。
连铸过程含Nb、V、Ti微合金化钢中碳、氮化物析出及钢的延塑.

连铸过程含 Nb 、 V 、 Ti 微合金化钢中碳、氮化物析出及钢的延塑性能降低1采用控轧控冷工艺,轧制过程含铌、钒、钛微合金化钢中析出的微细 NbN 、Nb(C,N、 VN 、 V(C,N、 TiN 等能够细化钢的组织,并对钢起到沉淀强化的作用,得到较高强度、较好韧性的钢材。
因此,含铌、钒、钛微合金化钢在管线钢、大跨度重载桥梁、高压容器钢板、海洋设施用钢等方面得到了广泛的应用。
一、前言2析出物粒子大小、粒子间距与钢板废品率的关系4二、碳、氮化物析出热力学分析铌、钒、钛均为与氮或碳有较强亲和力的元素 , 在钢凝固冷却过程,铌、钒、钛与钢中的氮或碳反应生成相应的氮化物、碳化物。
因为生成氮化物和碳化物的反应经常同时进行 , 生成的二元氮化物、碳化物又均为 NaCl 型晶格结构 , 它们之间可以相互溶解 , 形成 Nb(C,N、 V(C,N等碳氮化物或更多元复合化合物。
1418假定钢中 [Al]、 [Nb]、 [V]含量均为 0.02%, [N] 含量为 0.005%,钢中析出物活度为 1, 则平衡条件下各析出物开始析出的温度分别为:AlN:1059℃ NbN:1029℃ NbC 0.7:1032℃ NbC 0.7N 0.2:1081℃ VN :882℃ VC 0.7:678℃三、静态析出、动态析出和形变诱导析出静态析出 :无形变、无应力作用条件下发生的析出, 静态析出一般需要较长的时间;动态析出 :在形变的同时发生的析出 ;形变诱导析出 :形变停止后立即开始的析出物的析出。
在有形变发生的情况下 , 晶格产生扭曲 , 为析出提供了成核的地点 ,因而大大加快了析出过程。
223539900℃保温 2分钟后拉伸试样中观察到的微细析出物 , 尺寸约为 10nm 左右 , 有球形和立方形两种。
由于尺寸太小 , 无法用 EDAX 打出成分 , 根据形貌判断其为以含铌为主的析出物。
40含铌、钒、钛微合金化钢根据高温延塑性能变化规律可分为以下类型 :1 低碳([C]≤0.10%含铌钢 ;2 高碳([C]≥0.12%含铌钢 ;3 低碳含较高铌、钒钢 ;4 低碳含钒钢。
2205双相不锈钢连铸坯连铸条件的研究
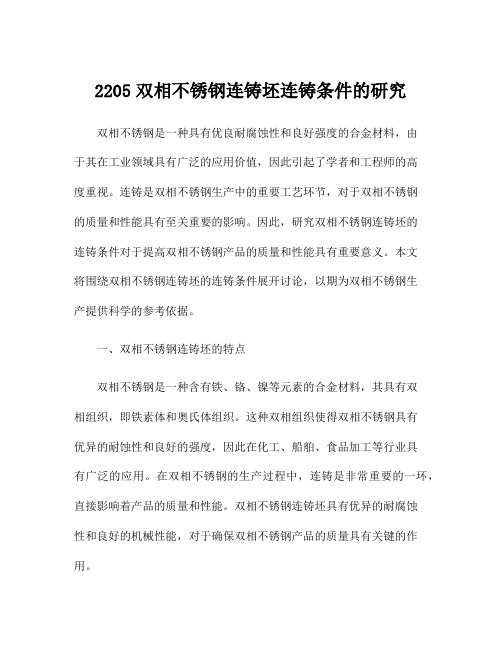
2205双相不锈钢连铸坯连铸条件的研究双相不锈钢是一种具有优良耐腐蚀性和良好强度的合金材料,由于其在工业领域具有广泛的应用价值,因此引起了学者和工程师的高度重视。
连铸是双相不锈钢生产中的重要工艺环节,对于双相不锈钢的质量和性能具有至关重要的影响。
因此,研究双相不锈钢连铸坯的连铸条件对于提高双相不锈钢产品的质量和性能具有重要意义。
本文将围绕双相不锈钢连铸坯的连铸条件展开讨论,以期为双相不锈钢生产提供科学的参考依据。
一、双相不锈钢连铸坯的特点双相不锈钢是一种含有铁、铬、镍等元素的合金材料,其具有双相组织,即铁素体和奥氏体组织。
这种双相组织使得双相不锈钢具有优异的耐蚀性和良好的强度,因此在化工、船舶、食品加工等行业具有广泛的应用。
在双相不锈钢的生产过程中,连铸是非常重要的一环,直接影响着产品的质量和性能。
双相不锈钢连铸坯具有优异的耐腐蚀性和良好的机械性能,对于确保双相不锈钢产品的质量具有关键的作用。
二、双相不锈钢连铸坯的连铸条件(一)浇注温度浇注温度是影响双相不锈钢连铸坯质量的重要因素之一。
过高或者过低的浇注温度都会影响双相不锈钢的组织形貌和化学成分,从而影响产品的性能。
因此,确定合理的浇注温度对于双相不锈钢的生产至关重要。
一般来说,双相不锈钢连铸坯的浇注温度应在合金的固相线以下100~150℃左右。
通过测定合金的凝固曲线和结晶温度,合理控制浇注温度,可以获得理想的双相不锈钢连铸坯。
(二)浇注速度浇注速度是影响双相不锈钢连铸坯凝固过程的重要因素。
合适的浇注速度可以促进均匀的凝固结构,从而获得优良的双相不锈钢连铸坯。
一般来说,较高的浇注速度可以促进块状铁素体的形成,提高产品的强度和硬度;而较低的浇注速度可以促进奥氏体的形成,提高产品的韧性和塑性。
因此,根据产品的要求,合理控制浇注速度对于获得理想的双相不锈钢连铸坯至关重要。
(三)结晶器参数结晶器在双相不锈钢连铸坯的凝固过程中具有非常重要的作用。
合理的结晶器参数可以有效地促进均匀的凝固结构,提高双相不锈钢连铸坯的质量。
连铸车间简介

连铸车间简介
一、概述
连铸车间是某钢铁公司的重要组成部分,负责生产高品质的钢铁产品。
该车间占地数百亩,拥有先进的连铸设备和技术,采用智能化的生产管理系统,为国内外客户提供优质的连铸钢坯。
二、设备和技术
连铸车间拥有多台先进的连铸设备,包括连续浇铸机、振动台、切割机等。
这些设备具有高精度、高效率、高可靠性等特点,能够生产不同规格和形状的连铸钢坯。
此外,车间还拥有多项核心技术,如结晶器电磁搅拌技术、二冷水技术等,确保了产品的质量。
三、生产流程
连铸车间的生产流程包括:将铁水注入钢包中,经过混铁炉、熔炼炉等环节,形成合格的钢水;通过连铸机将钢水凝固成钢坯,并通过振动台、切割机等设备对钢坯进行加工;最后将钢坯包装、储存,等待发货。
整个生产流程自动化程度高,操作简单,生产效率高。
四、产品质量
连铸车间生产的连铸钢坯具有高品质的特点,如表面光滑、尺寸精度高、内部组织均匀等。
此外,车间还采用多项核心技术,如结晶器电磁搅拌技术、二冷水技术等,确保了产品的质量。
因此,连铸车间生产的钢坯深受国内外客户的好评。
五、环保和安全
连铸车间注重环保和安全工作,采用先进的环保设施和安全措施,如废气处理设备、噪音控制设备、安全防护设备等。
同时,车间严格执行安全生产管理制度,确保员工的安全和健康。
六、未来发展
连铸车间将继续引进先进的连铸设备和技术,提高生产效率和产品质量。
同时,车间将加强与国内外同行的合作,引进先进的管理理念和方法,提高车间的智能化和信息化水平。
未来,连铸车间将为国内外客户提供更优质、更高品质的连铸钢坯,为公司的可持续发展做出更大的贡献。
连铸坯质量及其缺陷
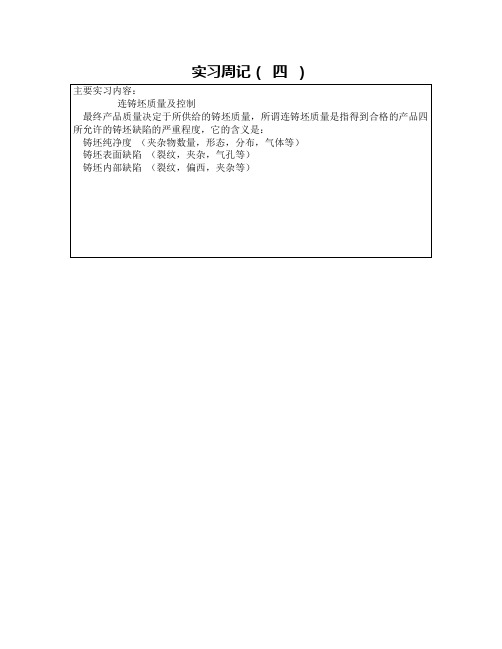
主要收获与心得体会: 铸坯纯净度主要取决于钢水进入结晶器之前处理过程。也就是说要把钢水搞“干 净”些,必须在钢水进入结晶器之前各工序下功夫如冶炼及合金化过程控制,选择 合适的炉外精炼,中间包冶金,保护渣浇注等。 铸坯表面缺陷主要决定于钢水在结晶器的凝固过程。它是与结晶器坯壳形成,结 晶器液面波动,侵入式水口设计,保护渣性能有关的,必须控制影响表面质量各参 数在目标值以内,以生产无缺陷铸坯,这是热传送和直接轧制的前提。 铸坯内部缺陷主要取决于二次冷却区,铸坯冷却过程和铸坯支撑系统。合理的二 次冷却水分布,支承辊的对中,防止铸坯鼓肚等是提高铸坯内部质量的前提。 因此,为了获得良好的铸坯质量,可以根据钢种和产品的不同要求,在连铸的不 同阶段如钢包,中间包,结晶器和二次冷却区采用不同的工艺技术,对铸坯质量进 行有效控制。 提高铸坯纯净度的措施 1.无渣出钢 2.钢包精炼 3.无氧化浇注 4.中间包冶金 5.侵入式水口加保护渣 提高铸坯表面缺陷的措施 1.结晶器液面的稳定性 2.结晶器震动 3.初生坯壳的均匀性 4.结晶器钢液流动 5.保护渣性能 提高铸坯内部缺陷的措施 1.控制铸坯结构 2.合理的二次冷却制度 3.控制二次冷却区铸坯的受力与变形 4.控制液相穴钢水流动,以促进夹杂物上浮和改善其分布
实习周记( 实习周记( 四 )
主要实习内容: 连铸坯质量及控制 最终产品质量决定于所供给的铸坯质量,所谓连铸坯质量是指得到合格的产品四 所允许的铸坯缺陷的严重程度,它的含义是: 铸坯纯净度 (夹杂物数量,形态,分布,气体等) 铸坯表面缺陷 (裂纹,夹杂,气孔等) 铸坯内部缺陷 (裂纹,偏西,夹杂等)
薄板坯连铸连轧技术综述
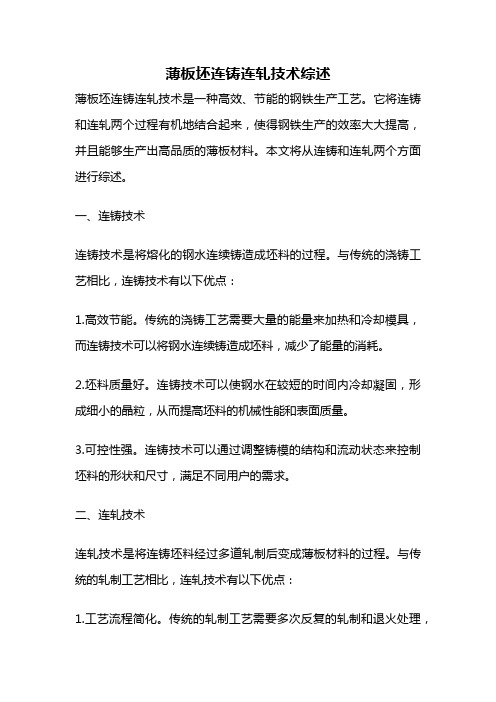
薄板坯连铸连轧技术综述薄板坯连铸连轧技术是一种高效、节能的钢铁生产工艺。
它将连铸和连轧两个过程有机地结合起来,使得钢铁生产的效率大大提高,并且能够生产出高品质的薄板材料。
本文将从连铸和连轧两个方面进行综述。
一、连铸技术连铸技术是将熔化的钢水连续铸造成坯料的过程。
与传统的浇铸工艺相比,连铸技术有以下优点:1.高效节能。
传统的浇铸工艺需要大量的能量来加热和冷却模具,而连铸技术可以将钢水连续铸造成坯料,减少了能量的消耗。
2.坯料质量好。
连铸技术可以使钢水在较短的时间内冷却凝固,形成细小的晶粒,从而提高坯料的机械性能和表面质量。
3.可控性强。
连铸技术可以通过调整铸模的结构和流动状态来控制坯料的形状和尺寸,满足不同用户的需求。
二、连轧技术连轧技术是将连铸坯料经过多道轧制后变成薄板材料的过程。
与传统的轧制工艺相比,连轧技术有以下优点:1.工艺流程简化。
传统的轧制工艺需要多次反复的轧制和退火处理,而连轧技术可以将这些过程有机地结合起来,减少了生产环节和能源消耗。
2.产品质量稳定。
连轧技术可以通过调整轧制工艺参数来控制薄板材料的厚度和表面质量,保证了产品质量的稳定性。
3.生产效率高。
连轧技术可以实现高速轧制,大大提高了生产效率和产量。
三、薄板坯连铸连轧技术的应用薄板坯连铸连轧技术已经广泛应用于钢铁生产领域。
它不仅可以生产高品质的薄板材料,而且还可以有效地节约能源和减少环境污染。
目前,国内外很多大型钢铁企业都采用了薄板坯连铸连轧技术,如宝钢、鞍钢、武钢等。
同时,随着技术的不断进步和创新,薄板坯连铸连轧技术将会有更广阔的应用前景。
薄板坯连铸连轧技术是一种高效、节能、高质量的钢铁生产工艺。
它在钢铁生产中发挥着越来越重要的作用,是推动钢铁产业可持续发展的重要手段之一。
连铸板坯缺陷特征和缺陷图谱

连铸板坯缺陷特征和缺陷图谱首钢京唐板坯质检编制2010年8月8日一.连铸坯质量特征综述1.1连铸坯质量定义和特征所谓连铸坯质量是指的到合格产品所允许的铸坯缺陷的严重程度。
对铸坯质量要求而言,主要有四项指标,即连铸坯几何形状、表面质量、内部组织致密性和钢的洁净性;而这些质量要求与连铸机本身设计,采取的工艺以及凝固特点密切相关。
1.2铸坯的检查和清理的意义提高钢的质量,降低成本,加强产品市场的竞争力是企业追求的目标,生产无缺陷连铸坯以保证高附加值产品优良的性能是永恒的主题,连铸坯的裂纹和夹杂物所产生的缺陷可以说是影响产品质量的两大障碍,生产无缺陷或缺陷不足以影响产品质量的连铸坯,这是要努力达到的目标,而连铸坯裂纹和夹杂物所产生的缺陷是受设备、工艺、管理等多种因素制约的。
因此设备、工艺和管理的现代化加上人的质量意识是提高产品质量的关键。
,但是在连铸生产中,铸坯的各种缺陷总是无法避免的,铸坯清理对钢厂保障铸坯质量、降低废品比例具有重要意义。
(1)火焰铸坯清理的注意事项1)一般对表面质量要求较高的钢种,铸坯清理的目的以检查铸坯表面和皮下质量为主,包括夹杂物、气泡、裂纹等分布情况,在清理检查的基础上提供铸坯的进一步处理(清除缺陷、决定铸坯表面质量级别、是否送机器去皮、决定钢种是否达到热送条件等)的意见。
2)微合金钢如Nb、V微合金钢和包晶钢等容易产生角部横裂纹,往往位于铸坯振痕谷底,也需要用火焰清理才能发现。
这方面也应引起足够重视。
3)对于包晶钢、中碳钢等钢种,则以人工清理肉眼可见缺陷为主,包括铸坯常见的表面缺陷,如纵裂、角横裂、重接、凹陷、夹渣、毛刺等,以便尽量降低铸坯判废损失。
(2)不良的火焰清理的危害虽然火焰清理是检查和去除连铸坯表面缺陷的一个极好的方法。
但是,这项操作的确需要掌握一定的技巧,一旦能够正确地操作可确保最终产品不产生额外的表面缺陷。
连铸坯表面上的深槽、凸脊和界面必须平滑以确保清理操作本身不造成额外表面缺陷。
薄板坯连铸连轧技术综述

薄板坯连铸连轧技术综述薄板坯连铸连轧技术是一种先进的钢铁生产技术,它将连铸和连轧两个工序有机地结合在一起,实现了钢铁生产的高效、节能、环保和高质量。
本文将从薄板坯连铸连轧技术的原理、特点、应用和发展趋势等方面进行综述。
一、薄板坯连铸连轧技术的原理薄板坯连铸连轧技术是将连铸和连轧两个工序有机地结合在一起,实现了钢铁生产的高效、节能、环保和高质量。
其原理是:将熔融的钢水通过连铸机连续铸造成薄板坯,然后将薄板坯直接送入轧机进行连续轧制,最终得到所需的薄板产品。
这种技术不仅可以减少钢铁生产的能耗和环境污染,还可以提高钢铁产品的质量和生产效率。
二、薄板坯连铸连轧技术的特点1.高效节能:薄板坯连铸连轧技术将连铸和连轧两个工序有机地结合在一起,避免了传统钢铁生产中的多次加热和冷却过程,大大降低了能耗和生产成本。
2.环保节能:薄板坯连铸连轧技术可以减少钢铁生产中的二氧化碳、氮氧化物等有害气体的排放,降低了环境污染和对大气的负荷。
3.高质量:薄板坯连铸连轧技术可以实现钢铁产品的高质量生产,因为它可以避免传统钢铁生产中的多次加热和冷却过程,减少了钢铁产品的氧化和变形。
4.生产效率高:薄板坯连铸连轧技术可以实现钢铁产品的高效生产,因为它可以将连铸和连轧两个工序有机地结合在一起,减少了生产周期和生产成本。
三、薄板坯连铸连轧技术的应用薄板坯连铸连轧技术已经广泛应用于钢铁生产中,特别是在高端钢铁产品的生产中。
例如,汽车、航空航天、电子、建筑等领域的高端钢铁产品都可以采用薄板坯连铸连轧技术进行生产。
此外,薄板坯连铸连轧技术还可以用于生产高强度、高韧性、高耐磨性等特殊钢铁产品。
四、薄板坯连铸连轧技术的发展趋势随着钢铁生产技术的不断发展和进步,薄板坯连铸连轧技术也在不断地改进和完善。
未来,薄板坯连铸连轧技术将更加注重环保、节能和高效,同时还将更加注重钢铁产品的高质量和高附加值。
此外,薄板坯连铸连轧技术还将更加注重智能化和自动化,以提高生产效率和生产质量。
世界薄板坯连铸连轧技术设备发展综述

世界薄板坯连铸连轧技术设备发展综述世界薄板坯连铸连轧技术设备发展综述1989年美国纽柯公司采用德国西马克公司开发的紧凑型带钢生产(CSP)作业线,在全球率先开展了工业化生产,之后德国、中国、日本、意大利、俄罗斯、加拿大、埃及、印度、奥地利等国的钢铁公司也相继安装,并对其工艺进行进一步设计和开发,获得了一批颇具影响、独具特色的科研成果,使CSP发展成为20年来全球钢铁业一项具有重要意义的创新技术。
西马克的紧凑型带钢生产技术1985年,德国西马克公司在实验工厂成功地铸造出来第一块50毫米的薄板坯后,又创造设计了紧凑型带钢生产技术。
在生产实践中,CSP工艺不仅降低了能量需求,而且,由于其独特的工艺条件,还提高了带钢质量。
与厚板坯相比,薄板坯凝固速度更快,对生产高质量的钢种如微合金钢和硅钢十分有利。
与传统工艺相比,CSP生产的非取向电工钢的变形损失显著减少。
另外,由于温度均匀,薄板坯在宽度、厚度和长度上都达到了严格的标准,“冷边”问题不再出现,粗大晶粒的现象也消失了。
CSP生产线保证了轧制工艺的高效稳定,确保了带钢的宽度、厚度都被控制在理想的公差范围内。
紧凑型带钢生产技术的优势引起了中国珠钢、邯钢、马钢、唐钢、涟钢、酒钢的高度关注。
邯钢、马钢通过从西马克公司引入传统生产线,提高了他们的热轧生产能力,并开发了一批特色产品。
涟钢利用半无头轧制技术,铸造出270米超长扁坯和0.78毫米超薄产品。
武钢于2009年2月建成新的CSP生产线,专门生产非取向电工钢。
达涅利加强表面质量控制意大利达涅利研制开发了独特的薄板坯连铸技术,目的是克服第一代连铸机在产品质量和设备生产能力方面受到的限制。
这项新技术已借助于灵活的薄板坯连铸机概念而变为现实,到目前为止,达涅利薄板坯连铸机已经能够浇铸用于板带生产的所有钢种。
达涅利开发的新一代薄板坯连铸机,充分利用了漏斗形结晶器设计的优点,使最早凝固的初生坯壳沿出坯方向从漏斗形逐渐过渡到较为平坦的形状,从而解决了铸坯表面质量问题。
薄板坯含Nb微合金钢氮含量控制工艺实践
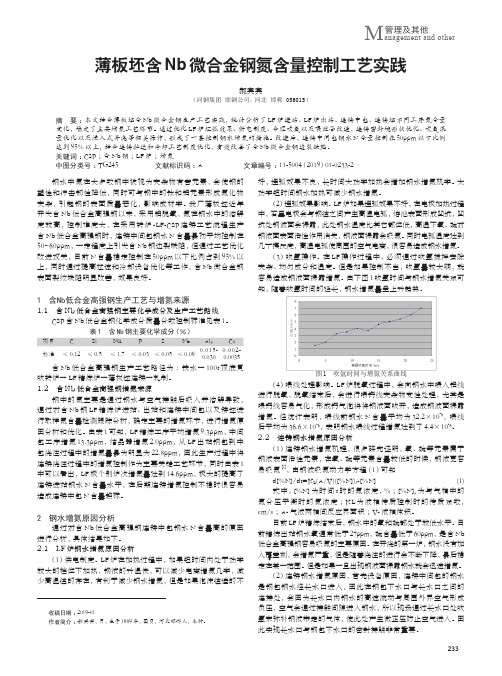
进行脱氧,脱氧结束后,会进行喂钙线夹杂物变性处理,尤其是
喂钙线容易气化,形成钙气泡将将钢液面吹开,造成钢液面裸露 增氮。经统计表明,喂线前钢水 N 含量平均为 32.2×10-6,喂线 后平均为 36.6×10-6,表明钢水喂线过程增氮达到了 4.4×10-6。
2.2 连铸钢水增氮原因分析
(1)连铸钢水增氮机理,很多研究证明,氧、硫等元素属于
此实现长水口与钢包下水口的密封接触非常重要。
233
M 管理及其他 anagement and other
钢液表面活性元素,在氧、硫等元素含量较低的时候,钢液更容 易吸氮 [1],由钢液吸氮动力学方程(1)可知
d[%N]/dt=KL(A/V)([%N])e-[%N]
(1)
式中,[%N] 为时间 t 时的氮浓度,% ;[%N]e 为与气相中的
氮分压平衡时的氮浓度 ;KL 为液相传质控制时的传质系数,
cm/s ;A- 气液两相间反应界面积 ;V- 液相体积。
目前 LF 炉精炼结束后,钢水中的氧和硫都处于较低水平。目
前精炼出站钢水氧通常低于 27ppm,硫含量低于 60ppm,是含 Nb
低合金高强钢容易吸氮的主要原因。在开浇的第一炉,钢水没有加
入覆盖剂,会增氮严重,但是随着浇注的进行会不断下降,最后稳
M 管理及其他 anagement and other
薄板坯含 Nb 微合金钢氮含量控制工艺实践
郝宾宾
(河钢集团 邯钢公司,河北 邯郸 056015)
摘 要 :本文结合薄板坯含 Nb 微合金钢生产工艺实践,统计分析了 LF 炉进站、LF 炉出站、连铸中包、连铸坯不同工序氮含量
变化,确定了主要增氮工艺环节。通过优化 LF 炉埋弧效果、供电制度、合理吹氩以及喂丝管改造,连铸密封碗形状优化、吹氩流
连铸年度总结范文
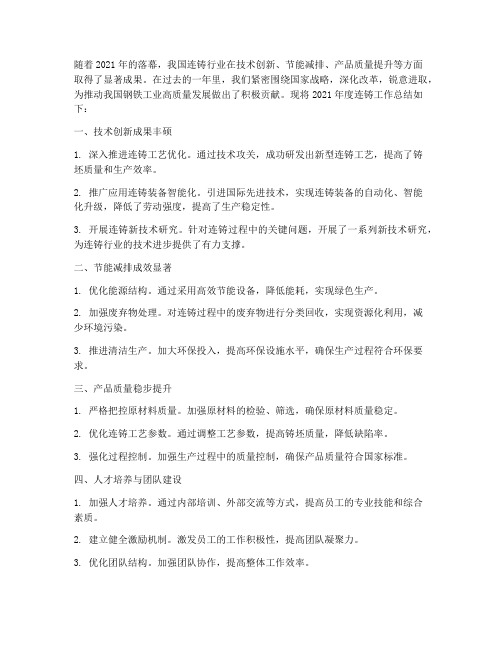
随着2021年的落幕,我国连铸行业在技术创新、节能减排、产品质量提升等方面取得了显著成果。
在过去的一年里,我们紧密围绕国家战略,深化改革,锐意进取,为推动我国钢铁工业高质量发展做出了积极贡献。
现将2021年度连铸工作总结如下:一、技术创新成果丰硕1. 深入推进连铸工艺优化。
通过技术攻关,成功研发出新型连铸工艺,提高了铸坯质量和生产效率。
2. 推广应用连铸装备智能化。
引进国际先进技术,实现连铸装备的自动化、智能化升级,降低了劳动强度,提高了生产稳定性。
3. 开展连铸新技术研究。
针对连铸过程中的关键问题,开展了一系列新技术研究,为连铸行业的技术进步提供了有力支撑。
二、节能减排成效显著1. 优化能源结构。
通过采用高效节能设备,降低能耗,实现绿色生产。
2. 加强废弃物处理。
对连铸过程中的废弃物进行分类回收,实现资源化利用,减少环境污染。
3. 推进清洁生产。
加大环保投入,提高环保设施水平,确保生产过程符合环保要求。
三、产品质量稳步提升1. 严格把控原材料质量。
加强原材料的检验、筛选,确保原材料质量稳定。
2. 优化连铸工艺参数。
通过调整工艺参数,提高铸坯质量,降低缺陷率。
3. 强化过程控制。
加强生产过程中的质量控制,确保产品质量符合国家标准。
四、人才培养与团队建设1. 加强人才培养。
通过内部培训、外部交流等方式,提高员工的专业技能和综合素质。
2. 建立健全激励机制。
激发员工的工作积极性,提高团队凝聚力。
3. 优化团队结构。
加强团队协作,提高整体工作效率。
五、展望未来2022年,我们将继续深化改革,创新发展,努力实现以下目标:1. 深化连铸工艺优化,提高铸坯质量和生产效率。
2. 加大节能减排力度,实现绿色生产。
3. 提升产品质量,满足市场需求。
4. 加强人才培养,打造高素质团队。
总之,2021年是我国连铸行业取得丰硕成果的一年。
在新的一年里,我们将继续努力,为实现我国钢铁工业高质量发展贡献力量。
王新华-鞍钢6.21无缺陷板坯连铸技术

组成 CaO SiO2 Al2O3 MgO Na2O K2O CaF2 MnO B2O3 ZrO2 结晶温度
粘度
22
增加结晶相比率的作用
增加晶界热阻; 晶界产生裂纹增加热
阻; 减弱玻璃相的辐射传
热。
23
NKK福山厂浇铸中碳钢采用的保护渣
纵裂纹总是发生在厚 薄不均匀坯壳中较薄 坯壳表面;
初生坯壳如厚薄不均 匀,在较薄的坯壳处 便形成应力集中;
应力超过坯壳强度时, 即导致纵裂纹的产生。
佐伯毅,铁と钢,68(1982),1773
11
凝固迟缓 k S平均 Sk / S平均 100
凝固迟缓程度超过10%,纵裂纹显著增加。 12
高温变形过程钢的再结晶:
静态再结晶; 动态再结晶。
在达到最大应力p后,钢出 现软化,在应力不再增加的 情况下可以继续变形。 一般认为,在略低于与最大 应力相对应的应变p处,动 态再结晶开始发生,在s处形成较完全的再结晶组织。动态 再结晶与变形温度和应变速率有关,高的变形温度和低的应 变速率有利于动态再结晶的进行。
27
流入不足的原因
保护渣粘度偏高; 钢水表面液渣层
过薄; 拉速偏高; 钢水表面供热不
足。
28
减少结晶器钢水液面波动
T. Ueda, et al., 铁と钢, 67(1981), P1236
29
浸入式水口尺寸、夹角、埋入深度
浸入式水口流出的钢 水如向上分流过强, 会造成表面波动过大, 引起的卷渣等。
保护渣
化学成分
CaO/ Si O2 Al 2O3 MgO
Li 2O 粘度,Pa. s ( 1300℃)
无缺陷含Nb连铸坯的生产

无缺陷含Nb连铸坯的生产在利用钢坯轧制板材时,连铸坯中有害的缺陷有表面裂纹、中心偏析和宏观夹杂,除此之外,连铸坯还易于产生某些连铸工艺本身特有的缺陷,如振痕以及连铸结晶器保护渣引发的缺陷,以及由鼓肚和弯曲应变引发的内部裂纹等。
这些缺陷在轧制产品上引发了诸如条形或线形表面缺陷,对材料的拉伸性能、塑性、韧性、疲劳强度有不利的影响;也会降低钢产品用户制作过程中的成形性和焊接性。
为了防止这些缺陷产生,连铸技术不仅从操作条件的角度得到了改善,而且连铸机本身也改进了很多。
然而,为了生产无缺陷含Nb连铸坯,还要研究[Nb]对上述缺陷的影响。
1.1 连铸坯表面裂纹连铸坯裂纹是按照形状(包括星形裂纹、纵向裂纹和横向裂纹)和产生的位置(面裂、角裂、边裂和内部裂纹)分类的,以便针对相关的凝固现象提出对策。
一般讲,当作用到凝固壳上的应变大于通过模拟试验得到的临界应变时,就会产生裂纹。
表1-9给出了裂纹形成的条件,包括与应变有关的工艺因素。
通过适当的连铸机的设计,可以将鼓肚和弯曲应变减至最小。
也就是说,通过采用气雾冷却使热应变、相变应变和凝固应变减至最小,从而使连铸坯表面温度均匀且维持高温。
所以,为防止裂纹的形成,重要的是从冶金学角度通过控制化学成分来提高临界应变。
凝固坯壳的热塑性(脆性)示意性显示如图1-25[21]所示。
凝固坯壳的塑性在接近1100℃温度区(第2区)、900℃以下50℃温度区(第3区)、接近为零塑性的温度区(第1区)都很差。
从冶金学的角度来看,在这些区域中对脆性的影响是由于[Nb]造成的。
表1-9 与连铸坯上裂纹有关的操作因素1.1.1 零塑性温度区脆性(第1区):纵向裂纹,内部裂纹基于试验结果,零塑性温度等于计算的凝固温度-100℃(熔点-100℃)或更少些。
可以通过减少[S]、[P]和其他偏析元素的含量降低第1区脆性,这样就减小了糊状区的长度(降低液线温度和实际凝固温度之差)。
然而,由于钢液凝固时不可避免存在糊状区,对结晶器施加均匀、轻微的冷却,减小热应变是更有效的防止纵向裂纹的方法。
改进工艺操作生产无缺陷钢材产品—含铌钢铸坯的冶炼和连铸
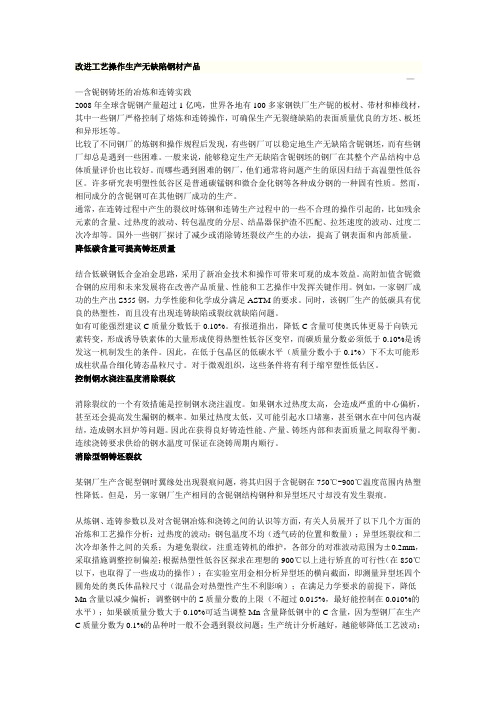
改进工艺操作生产无缺陷钢材产品——含铌钢铸坯的冶炼和连铸实践2008年全球含铌钢产量超过1亿吨,世界各地有100多家钢铁厂生产铌的板材、带材和棒线材,其中一些钢厂严格控制了熔炼和连铸操作,可确保生产无裂缝缺陷的表面质量优良的方坯、板坯和异形坯等。
比较了不同钢厂的炼钢和操作规程后发现,有些钢厂可以稳定地生产无缺陷含铌钢坯,而有些钢厂却总是遇到一些困难。
一般来说,能够稳定生产无缺陷含铌钢坯的钢厂在其整个产品结构中总体质量评价也比较好。
而哪些遇到困难的钢厂,他们通常将问题产生的原因归结于高温塑性低谷区。
许多研究表明塑性低谷区是普通碳锰钢和微合金化钢等各种成分钢的一种固有性质。
然而,相同成分的含铌钢可在其他钢厂成功的生产。
通常,在连铸过程中产生的裂纹时炼钢和连铸生产过程中的一些不合理的操作引起的,比如残余元素的含量、过热度的波动、转包温度的分层、结晶器保护渣不匹配、拉坯速度的波动、过度二次冷却等。
国外一些钢厂探讨了减少或消除铸坯裂纹产生的办法,提高了钢表面和内部质量。
降低碳含量可提高铸坯质量结合低碳钢低合金冶金思路,采用了新冶金技术和操作可带来可观的成本效益。
高附加值含铌微合钢的应用和未来发展将在改善产品质量、性能和工艺操作中发挥关键作用。
例如,一家钢厂成功的生产出S355钢,力学性能和化学成分满足ASTM的要求。
同时,该钢厂生产的低碳具有优良的热塑性,而且没有出现连铸缺陷或裂纹就缺陷问题。
如有可能强烈建议C质量分数低于0.10%。
有报道指出,降低C含量可使奥氏体更易于向铁元素转变,形成诱导铁素体的大量形成使得热塑性低谷区变窄,而碳质量分数必须低于0.10%是诱发这一机制发生的条件。
因此,在低于包晶区的低碳水平(质量分数小于0.1%)下不太可能形成柱状晶合细化铸态晶粒尺寸。
对于微观组织,这些条件将有利于缩窄塑性低估区。
控制钢水浇注温度消除裂纹消除裂纹的一个有效措施是控制钢水浇注温度。
如果钢水过热度太高,会造成严重的中心偏析,甚至还会提高发生漏钢的概率。
冷镦不锈钢综述

冷镦不锈钢综述l^7钢/歇/冷镦不锈钢综述冶金部钢铁研究总院易邦旺郎文运沈阳标准件研究所程从志,,,林松祯本溪特钢试验厂关秀阳—兰一,,刖商在合金钢领域内不锈钢作为后起之秀,近十多年来迅速发展.据不完全统计916全世界不锈钢年总产量已突破1000万吨以上.随着汽车,建筑,机械,石油化工,电子,食品,运输,航空等工业的发展,对紧固件的不锈性,耐蚀性,无磁性,热强性,高硬度化等的特殊需求量越来越大.随之,冷镦不锈钢也逐步形成系列化,标准化.标准件,紧固件作为机电行业基础件产品是机电产品重要支柱之一.我国标准件,紧固件行业年消耗钢材量约为657i吨,其中不锈钢紧固件用材量约占7%左右.预测西方世界到2000年不锈钢紧固件年进口量约为28万吨.随着不锈钢紧固件在各行业中广泛当用,加速发展我国冷镦不锈钢材的市场供应,利用不锈钢紧固件的生产属劳动密集型行业的特点,开拓国际,国内代'表钢市场是我国冶金,陈淑芬-1鲫cl机械行业的共同任务.二,冷镦不锈钢的发展,应用与系列紧固件行业随着技术的进步几乎涉及整个不锈钢系列.利用铁索体不锈钢的经济性广泛地应用于建筑行业;利用奥氏体不锈钢的不锈,耐蚀性应?嗣'于机械,石油,化工行业;利用双相不锈钢,沉淀硬化不锈钢的强度,耐应力腐蚀的特点应用于海洋机械,航空,发电设备;利用马氏体不锈钢具有高硬度特点,主要用于自攻螺丝,作为功能材料利用奥氏体不锈钢的无磁性,利用马氏体,铁索体高导磁的特点,应用于家用电器,核聚变,加速器等高技术领域.1.冷镦不锈钢的主要应用范围冷镦不锈钢涉及不锈钢三大类,目前主要使用有1o个钢种,其冷镦不锈钢主要应用范围见表1.种与用途表1分类代表钢种加工特点螺钉种类木螺钉,机螺钉马氏体SUS41013cr系列中代表钢种,可淬火硬化,耐蚀性差自攻螺钉铁索体,,43O木螺钉,机螺钉18cr系列中代表钢种,成形性优良,冷加工硬化小,适用家庭装饰用.A一.体系列代表钢种,加工硬化显着,成形困难,只有良好tt304铆钉,埋头螺钉的耐蚀性,耐热性.,,305在3O3钢的基础上加3NNi,改善303钢的冷镦性,耐蚀性.小螺钉,六角螺奥氏体母,自攻螺钉小螺钉,,305Jl305改良钢种,适用强加工用自攻螺钉,,XM7在304钢中加入3.S%Cu,~305JI钢更具优越的冷镦性.木螺钉,机螺钉,特殊螺钉"316A一体不锈钢中耐蚀性最为优良钢种之一,冷加工硬化性小,化工装置铆钉,机但强度低螺钉●l.▲●...,...,-l■常用冷镦不锈钢的可冷镦性由低到商按钢种排列顺序排列如下:互304--~31"---6圈一t~305J11f—i384H410;,-~}s从上述排列中可以看出在奥氏体不锈钢中304可冷镦性最差,384冷镦效果最好,而马氏体410钢,铁索体430钢冷镦变能远远高于奥氏体钢,可承受重度冷镦变形.在冷镦不锈钢标准系列钢种中,依照冷加工硬化程度,冷镦螺栓,螺钉,螺母等产品可分重度加工,强加工,轻度加工j大类钢可供选择,详见表2.,2.冷镦不锈钢钢种的发展动向为提高不锈钢的冷镦性能,提高钢材利用率,提高紧固件的合格率,降低模具消耗,减少18—8类型不锈钢的加工硬化螺钉种类与使用钢种及可加工性表2钢种适用作螺丝种类可加工IT?SUS头部磁性毹形状种类深度,41.04100e自攻螺钉,螺栓重度加工强磁性43O430,,-机螺钉,木螺钉,螺栓,铆钉,螺母304M304,,螺钉,螺母,木螺钉,螺母轻度加工弱磁性3053O5"螺钉,自攻螺钉,螺栓,木螺钉,螺母强加工无磁性305Ji3o5Ji,,机螺钉,自攻螺钉木螺钉,螺母,特殊铆钉, ",,XM,XM,,机螺钉,特殊螺钉,木螺钉,螺栓,螺母",,306A,,306AM,,,————.一——.384,,机螺钉,自攻螺钉,,补316,,螺钉,螺栓,铆钉,木螺钉,螺母轻度加工"压擀Iho/h图1不同钢种压缩率一.一圈2不同钢种可切削性●t●,●●I■}■而引起马氏体转变,一般在l8—8钢中加入2—4%Cu,来稳定奥氏体,利用铜的自润滑作用,减少模具消耗,并适应地控制钢中碳含量.典型钢种为美国302HQ,日本nS标准为XM,其主要成分为17cr一1O Ni一3.5cu.为获得好的冷镦后无磁r性,,钢_中增加Ni含量,降低钢巾P,S含量,如18cr--12Ni(305J1)钢,18cr一16Ni(384)钢.最近日本又发展了既可冷镦又可切削的冷镦易切不锈钢l8cr—l0Ni一3cu—Se (Lak7),其冷镦性能见图1,切削性能见图2.三器L.AK~Ss1Os纠s珥图3同钢种耐点蚀性能比较为了降低成本,提高铁索体不锈钢的耐点蚀性能,新型极低C,N铁素体不锈钢2Ocr一1Mo(Lak52)它具有与304奥氏体不锈钢相当的耐热腐蚀性能,其耐蚀性能见图3.为克服奥氏体不锈钢强度低的缺点,在18cr一1ONi一3.5cu钢的基础上加入Nb,Ni元素,经冷加工后,采用400—600.C时效处理,可获得oo.达90kg/ mm,ob可达105kg/m~的高强冷镦奥氏体不锈钢,即DSK.U钢.双相不锈钢具有高强度,良好的耐蚀性,良好的抗应力腐蚀性能,双相不锈钢用作紧同件通采JIj25cr一4Ni一2M0 (SU532931)及24cr—GNi…Io—N (SUS329J:L)二个牌号.双相不锈钢主要用于海洋装备,环保设备,油气田开采紧固件.当今双相不锈钢正向高N,高Mo方向发展.析出强化型不锈钢紧固件主要用于航空,航天部件.通常用手要求ob>~20kg/ mm紧固件,代表钢种为17—7PH,17—4PH,PH15—7Mo,15—5PH,PH13—8Mo等牌号.作为耐热用紧固件,在550.C以下常采用12cr系列马氏体钢作为紧固件材料, 代表钢种为SUS403,SUH600,SUH616.使用温度超过600.C,在700.C左右使用,通常选用304,SUH31,SUH37,SU310等奥氏体不锈钢.更高温度则采用铁, 镍基合金作为紧固件材料,如R26,A286, 37Ni一18cr一2.6Ti—O.6等.为适应汽车排气阀需要,最新开发了』一种较低镍RS3O7L2ONi—llcr一2.7Ti—O.2Al新型冷镦耐热钢.若在恶劣环境中使用的紧固件,当使用温度大于600.C时,需采用Ni基合金材料.此外纯钛及钛合金紧固件也广泛使肘予飞机和海洋装备上.作为功能材料紧固件,无磁冷镦不锈钢,常用305,XM7,316,317,384等高奥氏体不锈钢'.软磁冷镦不锈钢常用430,403,13cr一2/4Ni,25cr一5Ni—Mo等铁素体,低碳马氏体不锈钢作为紧固件材料;值得注意的是记忆合金,记忆不锈钢是近来世界大力开发的新型紧固件,标准件新材料.3.冷镦不锈钢常用钢种标准以JlSG4315(日本)为例,其化学成分,力学性能见表3,4.4.JIS标准冷镦不锈钢代表钢种的力学性能从表3中可以看出在JIS标准,没有SUS,~21即Icr18NigTi这个钢号作为冷镦不锈钢紧固件材料.——3——J1S标准冷镦不锈钢代表钢种化学成分表3成分种类钢种CSiMnPSNiCrCUSUS304<0.08<1.0<2.0<0.045<0.0308.O/lO.518/20JA一体305<0.12<1.0<2.O∥,,10.s/13.017.0/19.0|305JI<0.08,,}}}}11/13.516.5/19.0i.384<0.08,,撑}},,17.0/19.015.o/17.0|XM7<O.O8.,,挣挣,,8.5/10.5a7/193.0/4.0430<0.12<07.5<1.0<0.04<O.03|16.0/18.0|中一体434<0.12<1.0<1.0<0.04<0.03|16.o/I8.0MoO.75/i.25 M一体41O<0.15<1.0<1.0<0.04<0.03|11.s/is.5|表4钢种退火状态WSA.冷拔状态WSB-ob6ob6ITSUSkgf/mm%%kgf/mm%一%410'41O47N651O以上65以上43043047~65lO以上,,304M30d55~654O以上70以上52~7O25以上,,13O530550~65∥∥52,v70∥,,S0SJI305n5O~6S∥∥52N70,,,,XM7XM745~60∥}}47~654O以上7O以上306A4子~60,,,,,,,,,,306,AM45—,6O,/∥,,,,,,—●38438445N60,,,,,,}},,31631655~65,,,/52~7025以上65以上特点三,冷镦不锈钢的生产工艺1.冷变形对主要性能影响冷镦不锈钢主要用途是九j来制作紧固件,紧固件生产特点是局部剧烈冷变形(包括温镦).在三大类不锈钢中,奥氏体钢应用范围最广泛,而奥氏体钢在冷加工时,极易加工硬化.从图4,5中可以看到所有不锈钢随着冷加工变形量的增加与钢的强度增加呈直线关系,钢的延伸率也在激剧下降,其中以不稳定奥氏体钢301,302,304强度增加最为显着.——4——£,一I3Dk一,蕊2,./',●._—一:;04/.6一,J^/二/r,===二一/,1)一r叮,,,/===一')图4不锈钢的加工硬化性.彬工事,㈦图5冷拔加工率与强度延伸关系..(AISI304)冷拔丝径变化为:,4.8O÷3.963.46÷2.98÷2.7O÷2.48 -->-2.1O专?2,02(ram)/卜8/,一I9一口/'/,,Y/.,-f/.嫡'….//.,,/_/'.,,训?J,|,列/f,,厂/J|..广'●,lII,.,B//,/|I|I|嚣//}I/.'////,M,L一●6/—簟三孑I6弓;一1日【一a.一删u磁-蝮6bPsKlooo)罔6不同不锈钢在磁场强度5O高斯下的导磁率变化2'rje/m#)图7不锈钢不同强度与耐蚀性的关系(在5%沸腾HzSO'中6小时)由于冷加工变形量的增加,不锈钢的强度在直线上升.导至不稳定奥氏体不锈钢产生组织转变,即由r向体转变,使钢的导磁上升.详见图6.冷镦不锈钢的不锈性,耐蚀性也随着冷加工深度大小在发生变化,冷加工深度越大,则不锈钢的耐蚀性就越降低.从图7中我们可以看到在不同强度下,不同钢种在5%沸腾HSO.中腐蚀6小时的耐蚀性能变化.冷镦紧固件冷冲时,不但受到材料本身性能变化的影响,而且受到冲压速度的影响,图8比较了奥氏体不锈钢与炭素钢在不同冲压速度下临介冷镦极限的关系. 从图中可以看出奥氏体不锈钢适合较低的冲压速度来产紧同件."一b一-=壤—SAE?"8A^II|$:磊一J.●D,\\\,\\.,',\加工逮毫LiPJ图8加工速度的影响2.冷镦不锈钢对生产工艺要求(1)高纯净度冷镦不锈钢的冷镦性能的改善,除受钢神本身成分约束外,影响冷镦性最大的内在因素是钢的纯净度.作为冷镦紧固件用钢必须尽力减少钢中夹杂物.依结构钢~CH45K,CH35K,CK15K~],从图9可以看出钢中夹杂物对冷镦裂纹影响很大.因而各国冷镦不锈钢标准中都没有9夹杂与冷锻裂纹的关系1crl8Ni19Ti这个牌号.bklcr18Ni9钢低倍上看,一般存在2.5级以上皮下钛疏松. 从高倍上看,Icrl8Ni9,1cr18NigTit~界周围含有大量的TiO,TiN夹杂,无法保证冷镦性能.随着冶金工业的进步,铁水预处理技术,炉外精炼技术枉不锈钢生产中应用,使钢获得极低P,S,u,N,控制非金碾夹杂含量已不是困难的问题.尤其氩氧精炼炉VOD炉,AOD炉的开发,给不锈钢生产带来一次革命,提高了钢水纯净度,降低不锈钢中的碳含量成了轻而易举的事.(2)高尺寸精度冷镦不锈钢要求高的尺寸精度,钢材表面无缺陷.为保证轧制尺寸精度,一股采用高精度轧制.为确保钢材表面质量, 对冷镦不锈钢钢锭(连铸坯)表面全面警修清理外,在热轧过程中进行在线热探,以保证全线质量.冷加工时进箜通工程的强化管理,严格控制钢材表圃量.对产品冷拔丝材还须表面镀铜或用草酸盐处理交货.冷镦不锈钢生产工艺如下电炉WAO.D.炉外精炼一铸清理一电炉A0D炉外精炼(连铸坯)猜埋一:羹酸洗一冷拔一成品光免处埋衣叫一冷镦紧固件.四,我国冷镦不锈钢近况1.钢种使用落后我国不锈钢生产起步较晚,总产量还不刘日本总产聚l/l0.钢种主要是lc¨i9.此钢号美国AIsI标准,f=j本¨s标:——6一中已经废除,但在我'国不锈钢生产中1Cr 18Ni9Ti仍占主导地位,并选用不能作冷镦材料的1Cr18Ni9Ti作紧固件材料,造成冷镦紧固件合格率低,成本增加,无国际市场竞争力.至于含铜,高镍不锈冷镦紧固件材料还处于初步开发阶段.众所周知,至所以引起不锈钢晶问腐蚀,主要原因是钢中碳含量偏高.在电弧炉直接冶炼不锈钢,降碳是非常困难的事.为克服这一矛盾,通常在18—8不锈钢中加入Ti75(c—o.02)m0.7的Ti元素.其日的形成TiC,防止18—8不锈钢品界贫铬,改善腐蚀性能.随着AOD炉,AOD炉的生产应用,可以用高炭铬铁冶炼超低碳不锈钢,使不锈钢生产成本大大降降,钢中再加入Ti显得无多大意义.电弧炉直接冶炼钢时在炼4Cr18Ni9Ti钢过程中Ti的回收率不到60%.使钢中形成大量的TiO TiN夹杂.我国某厂曾经组织大量人员来攻关1Cr18Ni9Ti的裂纹及表面问题,由予钢种本身问题,收效甚微.大量不变形TiO,TiN的存在,造成1Cr18Ni9Ti低倍结果坯料皮下1—2mm处存在针孔状Ti疏松,按皮下气泡评级标准,一般在2.5级以上,高倍下TiO,TiN夹杂密集.1cr18Ni9Ti中Ti夹杂是冷镦裂纹纹源,同时由2.生产装备不完善近年来我国特钢生产引进和自行研制了不少炉外精炼装置,如VOD炉,AOD 炉,SKF炉.由于生产主产品为板材,棒材,管材,热轧高精度不锈钢生产线不完善,冷镦不锈钢冷加工处于小批量生产阶段.国内紧固件生产用冷镦不锈钢线材,丝材主要依赖从日本,德国,南韩,台湾进口.随着上钢五厂现代化热轧机的投产,充分发挥抚顺钢厂引进4o吨OD炉的作用,以及本溪特钢试验厂年产2000吨级冷镦不锈钢冷拔棒材,丝材生产线的建成,将为我国冷镦不锈钢生产带来生机.五,结语1.冷镦不锈钢紧固件,国内外市场广阔,是值得我国开发的产品.2.我国具备开发冷镦不锈钢冶炼,热轧,冷拔,冷镦紧固件生产能力,但必须加强合作,在国际市场上争得一席之地.3.开发含铜及其它冷镦不锈钢新钢种,适应汽车,电子,石化建筑等行业的需要,以势在必行.于Ti夹杂的萄荐,无法获得表面光洁的紧4.淘汰1cr18Ni9Ti作冷镦不锈钢酣.固件/.赫躺麴枰..]『~检测状态对紧固件扭矩值影响与控制沈阳汽车发动机厂7H131(摘要]通过SY492Q一1I型机大瓦螺栓不同检测方法与状态所测扭矩值变化表明,施加同一扭矩值,因检测方法与状态的差异,其检测结果必然不同.指fIIr变化规律与结果.定tl1.给出适合机的扭矩值与控制方法.一,前言随着汽乍业的发展,汽车榆测技术。
- 1、下载文档前请自行甄别文档内容的完整性,平台不提供额外的编辑、内容补充、找答案等附加服务。
- 2、"仅部分预览"的文档,不可在线预览部分如存在完整性等问题,可反馈申请退款(可完整预览的文档不适用该条件!)。
- 3、如文档侵犯您的权益,请联系客服反馈,我们会尽快为您处理(人工客服工作时间:9:00-18:30)。
无缺陷含Nb连铸坯的生产摘自《如何用铌改善钢的性能——含铌钢生产技术》在利用钢坯轧制板材时,连铸坯中有害的缺陷有表面裂纹、中心偏析和宏观夹杂,除此之外,连铸坯还易于产生某些连铸工艺本身特有的缺陷,如振痕以及连铸结晶器保护渣引发的缺陷,以及由鼓肚和弯曲应变引发的内部裂纹等。
这些缺陷在轧制产品上引发了诸如条形或线形表面缺陷,对材料的拉伸性能、塑性、韧性、疲劳强度有不利的影响;也会降低钢产品用户制作过程中的成形性和焊接性。
为了防止这些缺陷产生,连铸技术不仅从操作条件的角度得到了改善,而且连铸机本身也改进了很多。
然而,为了生产无缺陷含Nb连铸坯,还要研究[Nb]对上述缺陷的影响。
1.1 连铸坯表面裂纹连铸坯裂纹是按照形状(包括星形裂纹、纵向裂纹和横向裂纹)和产生的位置(面裂、角裂、边裂和内部裂纹)分类的,以便针对相关的凝固现象提出对策。
一般讲,当作用到凝固壳上的应变大于通过模拟试验得到的临界应变时,就会产生裂纹。
表1-9给出了裂纹形成的条件,包括与应变有关的工艺因素。
通过适当的连铸机的设计,可以将鼓肚和弯曲应变减至最小。
也就是说,通过采用气雾冷却使热应变、相变应变和凝固应变减至最小,从而使连铸坯表面温度均匀且维持高温。
所以,为防止裂纹的形成,重要的是从冶金学角度通过控制化学成分来提高临界应变。
凝固坯壳的热塑性(脆性)示意性显示如图1-25[21]所示。
凝固坯壳的塑性在接近1100℃温度区(第2区)、900℃以下50℃温度区(第3区)、接近为零塑性的温度区(第1区)都很差。
从冶金学的角度来看,在这些区域中对脆性的影响是由于[Nb]造成的。
表1-9 与连铸坯上裂纹有关的操作因素1.1.1 零塑性温度区脆性(第1区):纵向裂纹,内部裂纹基于试验结果,零塑性温度等于计算的凝固温度-100℃(熔点-100℃)或更少些。
可以通过减少[S]、[P]和其他偏析元素的含量降低第1区脆性,这样就减小了糊状区的长度(降低液线温度和实际凝固温度之差)。
然而,由于钢液凝固时不可避免存在糊状区,对结晶器施加均匀、轻微的冷却,减小热应变是更有效的防止纵向裂纹的方法。
而且均匀轻微的冷却还有其他优点,如:凝固过程均匀一致,凝固坯壳均匀应变,凝固坯壳在结晶器里不发生局部变形,这样就可阻止纵向裂纹的萌发。
钢液中的[Nb ]并不影响凝固温度或糊状区的长度。
因此,钢液中的[Nb ]对零塑性温度脆性没有影响,对纵向裂纹或内部裂纹的产生不起作用。
1.1.2 1100℃温度区脆性(第2区):横向裂纹,边部裂纹,星形裂纹1100℃温度区脆性是由枝晶间显微偏析引发的。
固态钢中低溶解度的元素如[S ]、[P ]、[B ]、[Cu ]、[Sn ]、[Pb ]和[Zn ]在枝晶间隔中形成严重的显微偏析。
热塑性随着这些元素含量的增加而降低。
可以通过降低这些元素的含量阻止与第2区脆性有关裂纹的形成。
图1-26[22]给出了一个典型示例,表明了[S ]和[P ]含量对热塑性的影响。
为了防止第2区脆性,[P ]或[S ]含量应当按照[C ]含量(或是钢凝固类型)的要求在钢包中加以控制。
在w [C ]>0.2%时(钢液凝固成奥氏体时的C 含量),[P ]含量应当小于等于0.02%,在w [C ]>0.6%时,[P ]含量应当是小于等于0.01%。
在w [C ]<0.1%时(凝固成铁素体),[S ]含量应当小于70×10-4%或更少些。
[S ]含量对热塑性的负面作用随w [Mn ]/w [S ]的增加而减少。
第2区的热塑性随着应变率的增加而降低,见图1-27[22]1。
一种有效的避免过度应变的方法是使用多重平整铸机,它可通过增加平整点(或弯曲点)的区域和次数将应变速率降低到0.01/s 以下。
在第2区,钢液中的Nb 对枝晶间显微偏析影响不大且对脆性没有直接的影响。
然而,假定大颗粒Nb 碳氮化物在显微偏析区析出的话,也会降低第2区的热塑性。
Nb 碳氮化物的大小和数量与析出温度和显微偏析区的凝固温度之差有关。
其数量取决于显微偏析区w [Nb ]×(w [C ]+w [N ])的产物,其大小取决于显微偏析区的[S ]和[P ]含量。
为了防止含Nb 钢第2区脆性引发的裂纹,应当根据[C ]或[Nb ]的含量将[S ]和[P ]含量控制到低水平。
在高碳钢中,Nb 碳氮化物可能在枝晶间析出(如前面1.2.2节中谈到的)所以要将[S ]和[P ]含量减至最小。
在电炉钢中,含有90×10-4%的[N ],不仅应当小心控制[S ]和[P ]含量,还要尽可能保持低的[Nb ]含量。
1.1.3 750℃温度区脆性(第3区):边部裂纹,短横裂纹 在先共析钢中(w [C ]<0.7%)尤其是在低合金钢中已观察到第3区脆性。
图1-28[21]表明了应变速率对Al 镇静和低合金钢第3区脆性的影响。
较低应变速率导致的第3区脆性与第1和第2区脆性是不同的,第1和第2区脆性是随着应变速率的提高而加大(如图1-27所示)。
1在连铸工艺中第2区脆性(称之为“热脆”)问题热轧时比连铸矫直时更为严重,因为热轧时的应变速率达到10/s 数量级,比连铸矫直时高得多。
值得指出的是,连铸前就应当控制与第2区脆性有关的元素以便防止热轧时产生热裂纹。
A 接近750℃温度区(第3区)脆性机制考虑到应变速率对脆性的影响,第3区脆性机制通常有如下解释:(1)在第3区中由于凝固组织晶粒度较大,在奥氏体晶界上有薄片状铁素体析出;(2)由于析出铁素体的强度很高,晶界在较低的应变速率下不发生变形;(3)应变集中在晶界或析出物的三叉交点并且形成显微空洞;(4)这些显微空洞在平整(弯曲)时长大并最终形成裂纹;(5)在Al 镇静钢中,Al 氮化物在晶界上析出,强化了析出的铁素体,也增加了显微空洞生成点。
因此在Al 镇静钢中脆性更为严重。
图1-29[21]表明了裂纹形成机制。
B 防止第3区形成裂纹的措施考虑到第3区形成裂纹的机制,下面是一些有效的应对措施:(1)通过减少平整点和次数来提高应变速率。
但是,提高了应变速率,第1区(内部裂纹)和第2区(横向裂纹)的脆性就会变得更严重。
因此[S ]或[P ]含量两者都应保持较低的水平,例如,w [S ]<0.01%,w [P ]<0.02%。
(2)连铸坯在较高温度(高于第3区温度)变形,见图1-30[22,23]。
很明显,在矫直之前应当开启通常的强化喷淋,降低表面温度以避免第2区脆性。
之后,维持其表面温度在较高水平,在矫直前应减小喷淋强度。
C Nb 对第3区脆性的影响在这个温度范围Nb 碳氮化物析出并且如Al 氮化物一样对第3区脆性有影响。
图1-28b [21]表明了应变速率对含Nb (0.05%)钢第3区脆性的影响。
含Nb 钢的第3区脆性温度范围有所增加,扩展到了800~900℃[24]。
这是由Nb 碳氮化物在奥氏体晶界析出引起的。
当温度降至低于1000℃时,Nb 碳氮化物静态析出占优。
除了前面提到的措施之外(应变速率控制,表面温度控制),下面方法能防止在此温度范围内Nb 碳氮化物析出,可能改善含Nb 钢热塑性。
(1)降低[N ]含量或者加入少量的Ti 作为N 净化剂[24](形成TiN )以便减少在第3区析出的Nb 碳氮化物的数量。
(2)降低冷却速率或者在大约1100℃等温[25]。
在这种情况下,由于Nb 碳氮化物的粗化而极大减少了在第3区析出的Nb 碳氮化物的数量。
然而,Nb碳氮化物的粗化因其费时太多,对常规的连铸工艺来说不切实际[25,26]。
(3)在1050℃左右施加预变形,加速Nb 碳氮化物析出(Nb 碳氮化物粗化)[25,26]。
有报道说对于应变速率大于0.01/s 的情况,预应变大于5%是最佳的连铸工艺。
无论如何,上述方法只能稍微降低第3区的脆性。
将弯曲温度控制在第3区之上(如图1-30[22~24]所示),才是更有效的办法。
在钢的生产过程中由于热轧具有高应变速率的特点,几乎达到10/s ,显著地改善了第3区的热塑性,即便是含Nb 钢也是如此,由于第3区脆性而导致的热轧期间的热裂纹也得到改善。
1.1.4 热轧时由于大颗粒Nb 碳氮化物引发的热裂纹当含Nb 连铸坯在650~900℃入炉温度下热装时,热轧时会发生热裂纹。
这是由于在连铸和入炉加热过程的间隙中,粗大Nb 碳氮化物颗粒在从凝固遗传下来的奥氏体晶界上析出[27]。
热轧时如此大的奥氏体晶界上Nb 碳氮化物引起应变集中,使协变性能很差的晶界在变形过程中与基体分离产生空洞等缺陷。
为了避免含Nb 钢热装时产生热裂纹,应选择上述温度范围之外的热装温度。
即便在上述温度范围将连铸坯装进加热炉,应通过提高加热温度到Nb 碳氮化物的溶解温度之上(大于1200℃),这样也能在含Nb 钢中避免产生热裂纹,见图1-31[27]。
1.2 夹杂缺陷钢液中各种脱氧剂(或合金元素)的相对脱氧能力如下所示:Al >Ti >Si-Mn >Si >Nb >Mn 。
当生产含Nb 钢时,用Al (或Si-Mn ,或Ti )脱氧后,再将Nb 加入到钢包的钢液中。
因而,在含Nb 钢液中含有大颗粒悬浮的Al 2O 3氧化物夹杂(或硅酸盐夹杂物)。
如果钢液中悬浮的夹杂物保留在连铸坯中,将会在成品中产生表面缺陷,如条型或线型缺陷和内部缺陷(如钢产品中的UT 缺陷)。
钢液中的[Nb ]并不直接引起夹杂缺陷,因为Nb 氧化物(或Nb 夹杂)并不悬浮于钢液中。
而且,它们仅在凝固期间析出而且其尺寸小于几个微米。
这意味着用Nb 脱氧是解决Al 2O 3夹杂问题的一种可能的冶金方法。
1.2.1 生产Al 镇静含Nb 钢时结晶器中的夹杂钢液浇注中悬浮的氧化物以及[Al]与钢液弯月面处吸附的连铸结晶器保护渣反应形成的二次氧化物都是连铸坯中氧化物夹杂的来源。
前者的类型是早期脱氧产物(Al2O3夹杂)以及[Al]与空气(Al2O3夹杂)或是与渣中或耐火材料中的(FeO)和(SiO2)(Al2O3-CaO-MgO 夹杂)反应形成的二次氧化产物。
后者是Al2O3-CaO-MgO夹杂,它与将在下面1.3.3节中讨论的渣中形成的二次氧化产物是一样的。
理想的结果是悬浮在浇注钢液中的Al2O3夹杂漂浮在结晶器上面(或在未凝固的钢液上面)并被去除掉。
但是在上浮期间有些会陷在凝固坯壳中并以大颗粒夹杂的形式(夹杂缺陷)保留在连铸坯中。
图1-32[28]表明了连铸坯中氧化物夹杂的分布。
其夹杂指数(数量和尺寸)表明在坯子上部尤其是上表面夹杂指数最大[28,29]。
图1-33表明了根据模拟试验结果计算出的在凝固坯壳中夹杂的捕获率。
尽管它并不很高,也就是4%或更少些,但即使大颗粒夹杂(大于100μm)也在凝固的早期阶段(接近连铸坯表面)被捕获,尤其是在由弯曲铸机生产的板坯的上表面(自由边)。