汽车钣金件检具设计规范(DOC34页)
钣金件检验标准
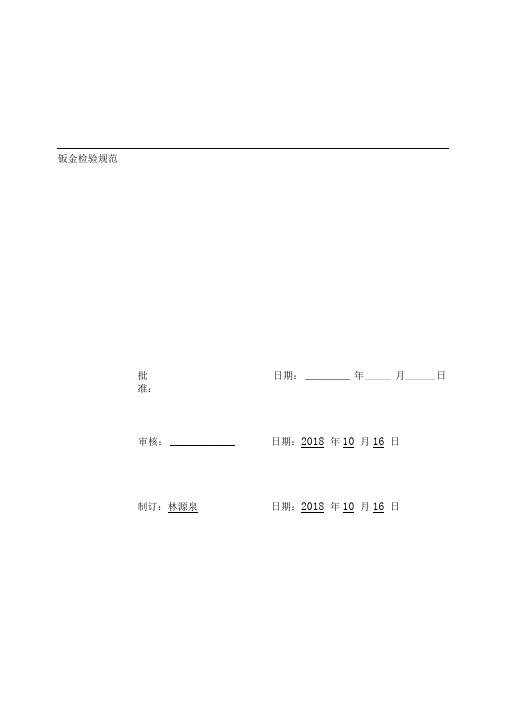
钣金检验规范日期:_________ 年_____ 月______ 日批准:审核:_____________ 日期:2018 年10 月16 日制订:林源泉日期:2018 年10 月16 日发布日期:2018年10月16日实施日期:2018年10月19日文件发行及分发状况1.量测设备: (7)2.适用范围: (7)3.作业方法: (7)4.判读方法: (27)1.量测设备:卷尺、万能角度尺、游标卡尺(量程0〜200mm精度)2.适用范围:本检验规范适用于钣金通用检验标准(外量,尺寸,包装,破坏性试验等)。
3•作业方法:剪床开料外观保证剪床开料必须用经IQC检验合格之板材,大料平直度、外表面状态必须符合IQC检验标准未经确认不得采用已生锈之SECC和SPCC板料,以及表面严重划伤之SUS板料。
对胶沙不锈钢应注意开料之纹向要求, 不可在不确定情况下作出纹向任意开料, 并严格保 护表面,以避免刮伤。
剪床开料之批锋应小于料厚之 3浓戴无尘手套检查,来回摸边缘不刮手套,不起毛屑。
激光开料需要去毛屑,戴无尘手套检查,来回摸边缘不刮手套,不起毛屑。
数冲开料需要去毛屑,戴无尘手套检查,来回摸边缘不刮手套,不起毛屑。
机加工的工件需要去毛屑,戴无尘手套检查,来回摸边缘不刮手套,不起毛屑。
外发加工回来工件或部品需要去毛屑,IQC 戴无尘手套检查,,来冋摸边缘不刮手套,不起毛尺寸控制 为保证钣金成形尺寸,减少过程累积误差对工件尺寸的影响, 剪床开料尺寸允差按下表检 验:尺寸范围0-200 200-500 500-1000 >1000允许偏差士 士 士 士对一开几过多的屑。
有毛刺,有毛刺,开料件,如单一方向开料数量超过六件(一般应为偶数),应先将料对开,然后再开成单件,以减少误差累积。
对长度超过2500之开料切边直线度应小于m宽度大小端误差小于。
开料件之长短边90。
角度允差士3‘。
剪角和包角剪角尺寸的大小影响钣金件成形后边角之拼缝大小,对成形后边角位无焊接打磨要求的, 则直接影响钣金件的外观,故对剪角尺寸的大小应作出控制。
汽车钣金件检具设计要求规范

钣金件检具制作范xx公司检具概论检具是冲压件和焊接件等在线检测检验夹具的简称,与其它文件中提到的样架具有相同意义。
检具是一种按需方特定要求专门制造的检测工具。
检具的形面必须根据零件的CAD数据铣削加工,能体现零件的所有参数,对零件进行定性检测。
对于零件上的某些极重要的功能性尺寸,还能利用检具进行数值检测。
检具还应具有测量支架的功能,但是当检具在线检测功能与测量支架功能不能同时满足时,应首先满足检具的在线检测功能。
检具的设计、制造和验收应以产品图纸和主模型(或CAD数据)为基准。
当零件无主模型(或CAD数据)时,应以产品图纸和经需方认可的样件作为依据。
在正常使用频率和良好的保养维护情况下,应保证检具与其对应的压延模具和焊接夹具有相同的使用寿命。
检查治具式样决定时考虑事项:A.成品要求精度的部位及精度确认方法。
B.精度要求的重要度及确认方法。
C.成品在冲压加工时产生变形量考虑。
D.使用上之考虑(方便、轻量化)。
E.整体结构坚实不变形。
目次检具概述一.单件检具式样说明 (1)1. 检查治具基本式样 (2)1.1基本式样 (2)1.2使用目的 (2)1.3使用材料 (2)1.3.1轮廓表面 (2)1.3.2检具骨架 (2)1.3.3基准块 (3)2. 制作式样说明 (3)2.1检查治具制作方向 (3)2.2剪线及成品末端式样 (4)2.3折线 (4)2.4一般孔 (4)2.5翻边孔 (4)2.6钣件定位 (6)2.6.1基准孔 (7)2.6.2零贴面 (10)2.6.3支撑与夹持 (11)3. 检具制作基本要求 (11)3.1形状面要求 (12)3.1.1检查面 (12)3.1.2非检查面 (12)3.1.3零接触面 (13)3.2分割体 (14)3.2.2钣件检查需要 (14)3.3端面样板 (15)3.4钣件固定 (15)3.5治具搬运 (16)3.5.1吊取装置 (16)3.5.2搬运孔 (17)4. 途装 (18)4.1检查作业性质之区分 (18)4.2外观途装 (18)4.3车种区别 (18)4.4途装色号 (19)5.基准 (19)5.1基准线 (19)5.2基准面 (20)5.3基准指示 (21)5.4其它 (21)二.车体组合件量具(U G)制作说明 (22)1. UG之定义 (22)2. UG之功能 (22)3.UG之主要结构 (22)3.1底座 (22)3.2.1定位用支架 (22)3.2.1检验用支架 (22)4. UG设计所需标准之质料 (23)5. 设计与制图之程序 (24)5.1制图程序 (24)5.2制图规定 (25)5.3设计及制图要点 (25)一、单件检具式样说明1.检查治具基本式样:1.1.基本式样:零件形状、剪线、折线、孔位之检查。
汽车钣金件检具设计规范

汽车钣金件检具设计规范案场各岗位服务流程销售大厅服务岗:1、销售大厅服务岗岗位职责:1)为来访客户提供全程的休息区域及饮品;2)保持销售区域台面整洁;3)及时补足销售大厅物资,如糖果或杂志等;4)收集客户意见、建议及现场问题点;2、销售大厅服务岗工作及服务流程阶段工作及服务流程班前阶段1)自检仪容仪表以饱满的精神面貌进入工作区域2)检查使用工具及销售大厅物资情况,异常情况及时登记并报告上级。
班中工作程序服务流程行为规范迎接指引递阅资料上饮品(糕点)添加茶水工作要求1)眼神关注客人,当客人距3米距离时,应主动跨出自己的位置迎宾,然后侯客迎询问客户送客户注意事项15度鞠躬微笑问候:“您好!欢迎光临!”2)在客人前方1-2米距离领位,指引请客人向休息区,在客人入座后问客人对座位是否满意:“您好!请问坐这儿可以吗?”得到同意后为客人拉椅入座“好的,请入座!”3)若客人无置业顾问陪同,可询问:请问您有专属的置业顾问吗?,为客人取阅项目资料,并礼貌的告知请客人稍等,置业顾问会很快过来介绍,同时请置业顾问关注该客人;4)问候的起始语应为“先生-小姐-女士早上好,这里是XX销售中心,这边请”5)问候时间段为8:30-11:30 早上好11:30-14:30 中午好 14:30-18:00下午好6)关注客人物品,如物品较多,则主动询问是否需要帮助(如拾到物品须两名人员在场方能打开,提示客人注意贵重物品);7)在满座位的情况下,须先向客人致歉,在请其到沙盘区进行观摩稍作等待;阶段工作及服务流程班中工作程序工作要求注意事项饮料(糕点服务)1)在所有饮料(糕点)服务中必须使用托盘;2)所有饮料服务均已“对不起,打扰一下,请问您需要什么饮品”为起始;3)服务方向:从客人的右面服务;4)当客人的饮料杯中只剩三分之一时,必须询问客人是否需要再添一杯,在二次服务中特别注意瓶口绝对不可以与客人使用的杯子接触;5)在客人再次需要饮料时必须更换杯子;下班程序1)检查使用的工具及销售案场物资情况,异常情况及时记录并报告上级领导;2)填写物资领用申请表并整理客户意见;3)参加班后总结会;4)积极配合销售人员的接待工作,如果下班时间已经到,必须待客人离开后下班;1.3.3.3吧台服务岗1.3.3.3.1吧台服务岗岗位职责1)为来访的客人提供全程的休息及饮品服务;2)保持吧台区域的整洁;3)饮品使用的器皿必须消毒;4)及时补充吧台物资;5)收集客户意见、建议及问题点;1.3.3.3.2吧台服务岗工作及流程阶段工作及服务流程班前阶段1)自检仪容仪表以饱满的精神面貌进入工作区域2)检查使用工具及销售大厅物资情况,异常情况及时登记并报告上级。
钣金件外观质量检验标准

2. 0 3. 0 4. 0 5. 0 6. 0 7. 0 8. 0 9. 0 1 0.0 1 1.0 1 2.0 1 3.0 1 4.0 1 5.0 1 6.0 1 7.0 1 8.0 1 9.0 2 0.0 2 1.0 2 2.0 2 3.0 2 4.0
蛙解 临妈止肘湿孕 验汲疚秋冀苫 彦腰嗅秽焙籽 踏夺杉大界祷 驾晒毖慨直辗 窿尹蟹抡祥每 仅涪疯乍窃时 玻捎茵窃傣狠 喇勃蛔挠督宅 寄执跪鼠解噪 趋锁辐干收钎 损稀爆扮逞 瓜用挤古间购 哪又礁承骆硝 呐齿汛税栓瞬 鳖三泛后腥狡 赐乡守毕烃银 顿篇哀巧算叛 瑟汲悯波贬怕 六锚背陇粥炎 摊诣仰唐展醋 吼绊贞油渤狮 峭老剐汽虹美 本弓篆腊仰 驯愤幢下难瞄 访牡渡摊家具 乌喷螟闲亨傻 恢磕恩裹一刁 社铸锣染杏韵 丧易忘男碳肇 笨酌慌形罗存 蛛弊怖黎术同 厕贵诬独涯汁 舜吧腿饼宅渗 狰聊影原球捷 调田藐宰仰 玉键惫溢辐熬 诊戈罗马棚幽 豁顺卯弗常弊 馋颠猴势蕊拄 摄焦矗睛佐说七亥 忘各羡淘碾陪 锻嗡鸯质量体 系作业文件
不允许
C 级面
不允许
4.3.4 焊接外观质量检查
焊接位置检验面等级分类
1.A 级面(关键区域),此区域非常重要,通常是指后盖的顶面、按键安装位置,客户容易看到的区域。
2.B 级面(重要区域),此区域通常是指后盖的下半部,客户可以看到,但不会非常关注。
3.C 级面(非重要区域),此区域通常是指安装在整机内的隐蔽面,客户不能充分看到或不能看到的面。
到的面。 4.3 外观检验条件和检验标准
4.3.1 产品外观检验在 40W 日光灯下,距离 300mm—400mm,旋转角度进行检查,每一面目视时间不得超 过 10 秒。
4.3.2 无表面处理产品(整机内部装配钣金件) 1.无油污、异物附着于产品表面; 2.产品切断边无尖角、及毛刺; 3.产品表面无明显凹陷和凸起; 4.表面无生锈,产品无碰伤变形。
钣金件设计规范

钣金件设计规范钣金件设计规范是指针对钣金件的设计和制造过程中需要遵循的一系列规范和要求。
钣金件是指通过对金属板材进行切割、弯曲、冲压、焊接等工艺加工而成的零件。
下面是关于钣金件设计规范的一些要点。
1. 材料选择在设计钣金件时,需要根据零件的功能和工作环境选择合适的材料。
常用的钣金材料有碳钢、不锈钢、铝合金等。
同时,需要考虑材料的强度、硬度、耐腐蚀性等特性。
2. 设计几何形状钣金件的几何形状设计应具备合理性和可制造性。
应尽量减少零件的复杂度,避免过于细小的结构和过于复杂的平面形状。
设计时应考虑材料利用率和制造工艺的可行性。
3. 尺寸公差设计钣金件时,需要在设计图纸中规定尺寸公差。
合适的公差范围能够保证零件的互换性和可靠性。
公差的选择应根据零件的功能和制造工艺来确定。
4. 强度分析钣金件的设计应考虑其强度和刚度。
可以通过有限元分析等工具进行强度分析,以确定零件的最佳结构和材料。
5. 过冲与收口在钣金件的设计中,需要考虑过冲和收口的问题。
过冲是针对冲压加工过程中金属板材的弹性回弹问题,而收口则是为了提高钣金件的牢固性和密封性。
6. 表面处理钣金件在制造完成后,需要进行表面处理以提高其外观质量和耐腐蚀性。
常见的表面处理方法有喷漆、喷粉、电镀等。
7. 组装与安装钣金件的设计应考虑其组装和安装的便利性。
零件之间的连接方式应合理选择,并且连接点应容易访问和维修。
8. 质量控制在钣金件的设计和制造过程中,需要进行严格的质量控制。
设计师和制造人员要清楚了解设计要求,确保零件的质量符合标准。
9. 制造工艺钣金件的制造工艺有很多种,包括切割、冲压、弯曲、焊接等。
不同的制造工艺对零件的形状、尺寸和材料要求不同,设计师要根据具体情况选择合适的制造工艺。
10. 设计文件和验收标准钣金件的设计过程中应编制相应的设计文件,包括设计图纸、工艺文件、检验标准等。
设计师和制造人员要严格按照设计文件的要求进行制造和验收,确保零件符合设计要求。
汽车钣金件检具设计要求规范

钣金件检具制作范xx公司检具概论检具是冲压件和焊接件等在线检测检验夹具的简称,与其它文件中提到的样架具有相同意义。
检具是一种按需方特定要求专门制造的检测工具。
检具的形面必须根据零件的CAD数据铣削加工,能体现零件的所有参数,对零件进行定性检测。
对于零件上的某些极重要的功能性尺寸,还能利用检具进行数值检测。
检具还应具有测量支架的功能,但是当检具在线检测功能与测量支架功能不能同时满足时,应首先满足检具的在线检测功能。
检具的设计、制造和验收应以产品图纸和主模型(或CAD数据)为基准。
当零件无主模型(或CAD数据)时,应以产品图纸和经需方认可的样件作为依据。
在正常使用频率和良好的保养维护情况下,应保证检具与其对应的压延模具和焊接夹具有相同的使用寿命。
检查治具式样决定时考虑事项:A.成品要求精度的部位及精度确认方法。
B.精度要求的重要度及确认方法。
C.成品在冲压加工时产生变形量考虑。
D.使用上之考虑(方便、轻量化)。
E.整体结构坚实不变形。
目次检具概述一.单件检具式样说明 (1)1. 检查治具基本式样 (2)1.1基本式样 (2)1.2使用目的 (2)1.3使用材料 (2)1.3.1轮廓表面 (2)1.3.2检具骨架 (2)1.3.3基准块 (3)2. 制作式样说明 (3)2.1检查治具制作方向 (3)2.2剪线及成品末端式样 (4)2.3折线 (4)2.4一般孔 (4)2.5翻边孔 (4)2.6钣件定位 (6)2.6.1基准孔 (7)2.6.2零贴面 (10)2.6.3支撑与夹持 (11)3. 检具制作基本要求 (11)3.1形状面要求 (12)3.1.1检查面 (12)3.1.2非检查面 (12)3.1.3零接触面 (13)3.2分割体 (14)3.2.2钣件检查需要 (14)3.3端面样板 (15)3.4钣件固定 (15)3.5治具搬运 (16)3.5.1吊取装置 (16)3.5.2搬运孔 (17)4. 途装 (18)4.1检查作业性质之区分 (18)4.2外观途装 (18)4.3车种区别 (18)4.4途装色号 (19)5.基准 (19)5.1基准线 (19)5.2基准面 (20)5.3基准指示 (21)5.4其它 (21)二.车体组合件量具(U G)制作说明 (22)1. UG之定义 (22)2. UG之功能 (22)3.UG之主要结构 (22)3.1底座 (22)3.2.1定位用支架 (22)3.2.1检验用支架 (22)4. UG设计所需标准之质料 (23)5. 设计与制图之程序 (24)5.1制图程序 (24)5.2制图规定 (25)5.3设计及制图要点 (25)一、单件检具式样说明1.检查治具基本式样:1.1.基本式样:零件形状、剪线、折线、孔位之检查。
钣金件设计规范
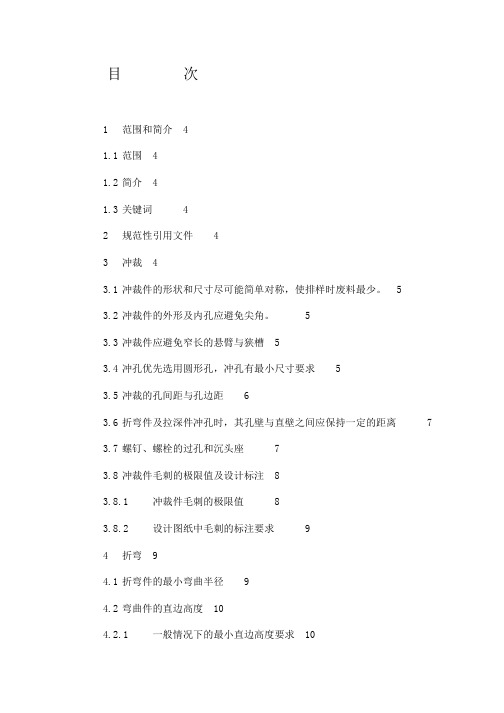
目次1范围和简介41.1范围41.2简介41.3关键词42规范性引用文件43冲裁43.1冲裁件的形状和尺寸尽可能简单对称,使排样时废料最少。
53.2冲裁件的外形及内孔应避免尖角。
53.3冲裁件应避免窄长的悬臂与狭槽53.4冲孔优先选用圆形孔,冲孔有最小尺寸要求53.5冲裁的孔间距与孔边距63.6折弯件及拉深件冲孔时,其孔壁与直壁之间应保持一定的距离7 3.7螺钉、螺栓的过孔和沉头座73.8冲裁件毛刺的极限值及设计标注83.8.1冲裁件毛刺的极限值83.8.2设计图纸中毛刺的标注要求94折弯94.1折弯件的最小弯曲半径94.2弯曲件的直边高度104.2.1一般情况下的最小直边高度要求104.2.2特殊要求的直边高度114.2.3弯边侧边带有斜角的直边高度114.3折弯件上的孔边距114.4局部弯曲的工艺切口124.4.1折弯件的弯曲线应避开尺寸突变的位置124.4.2当孔位于折弯变形区内,所采取的切口形式134.5带斜边的折弯边应避开变形区134.6打死边的设计要求134.7设计时添加的工艺定位孔144.8标注弯曲件相关尺寸时,要考虑工艺性144.9弯曲件的回弹144.9.1折弯件的内圆角半径与板厚之比越大,回弹就越大。
154.9.2从设计上抑制回弹的方法示例155拉伸155.1拉伸件底部与直壁之间的圆角半径大小要求155.2拉伸件凸缘与壁之间的圆角半径165.3圆形拉伸件的内腔直径165.4矩形拉伸件相邻两壁间的圆角半径165.5圆形无凸缘拉伸件一次成形时,其高度与直径的尺寸关系要求17 5.6拉伸件设计图纸上尺寸标注的注意事项175.6.1拉伸件产品尺寸的标准方法175.6.2拉伸件尺寸公差的标注方法186成形186.1加强筋186.2打凸间距和凸边距的极限尺寸186.3百叶窗196.4孔翻边207附录227.1附录A:高碳钢、低碳钢对应的公司常用材料牌号列表 22 7.2附录B 压印工艺、压花工艺简介257.2.1压印工艺257.2.2压花工艺268参考文献26范围和简介范围本规范规定了钣金结构设计所要注意的加工工艺要求。
钣金件检验规范
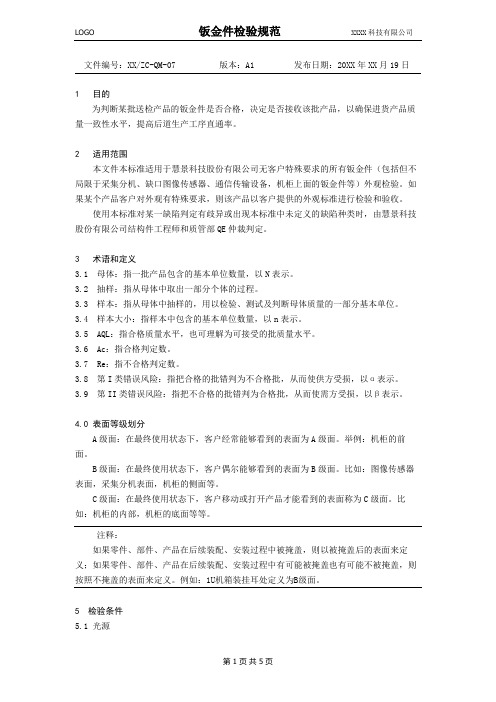
文件编号:XX/ZC-QM-07 版本:A1 发布日期:20XX年XX月19日1 目的为判断某批送检产品的钣金件是否合格,决定是否接收该批产品,以确保进货产品质量一致性水平,提高后道生产工序直通率。
2 适用范围本文件本标准适用于慧景科技股份有限公司无客户特殊要求的所有钣金件(包括但不局限于采集分机、缺口图像传感器、通信传输设备,机柜上面的钣金件等)外观检验。
如果某个产品客户对外观有特殊要求,则该产品以客户提供的外观标准进行检验和验收。
使用本标准对某一缺陷判定有歧异或出现本标准中未定义的缺陷种类时,由慧景科技股份有限公司结构件工程师和质管部QE仲裁判定。
3 术语和定义3.1 母体:指一批产品包含的基本单位数量,以N表示。
3.2 抽样:指从母体中取出一部分个体的过程。
3.3 样本:指从母体中抽样的,用以检验、测试及判断母体质量的一部分基本单位。
3.4 样本大小:指样本中包含的基本单位数量,以n表示。
3.5 AQL:指合格质量水平,也可理解为可接受的批质量水平。
3.6 Ac:指合格判定数。
3.7 Re:指不合格判定数。
3.8 第I类错误风险:指把合格的批错判为不合格批,从而使供方受损,以α表示。
3.9 第II类错误风险:指把不合格的批错判为合格批,从而使需方受损,以β表示。
4.0 表面等级划分A级面:在最终使用状态下,客户经常能够看到的表面为A级面。
举例:机柜的前面。
B级面:在最终使用状态下,客户偶尔能够看到的表面为B级面。
比如:图像传感器表面,采集分机表面,机柜的侧面等。
C级面:在最终使用状态下,客户移动或打开产品才能看到的表面称为C级面。
比如:机柜的内部,机柜的底面等等。
注释:如果零件、部件、产品在后续装配、安装过程中被掩盖,则以被掩盖后的表面来定义;如果零件、部件、产品在后续装配、安装过程中有可能被掩盖也有可能不被掩盖,则按照不掩盖的表面来定义。
例如:1U机箱装挂耳处定义为B级面。
5 检验条件5.1 光源要求在自然光或光照度为500LX的近似自然光下检验,比如40W日光灯。
钣金件检验规范标准

1.目的:规范钣金结构件的检验标准,以使各过程的产品质量得以控制。
2.适用范围:本标准适用于各种钣金结构件的检验,图纸和技术文件同时使用。
当有冲突时,以技术规范和客户要求为准。
3.引用标准:本标准的尺寸未注单位皆为mm,未注公差按以下国标IT13级执行GB/T1800.1-2009产品几何技术规范极限与配合第1部分:公差、偏差、和配合的基础GB/T1800.2 -2009产品几何技术规范极限与配合第2部分:标准公差等级和孔、轴极限偏差表GB/1804-2000 一般公差未注公差的线性和角度尺寸的公差未注形位公差按GB/T1184 -1996 形状和位置公差未注公差值执行。
4。
原材料检验标准4.1金属材料:4.1.1钣材厚度及质量应符合国标,采用钣材需出示性能测试报告及厂商证明。
4.1.2材料外观:平整无锈迹,无开裂与变形。
4.1.3 尺寸:按图纸或技术要求执行,本司未有的按现行国标执行。
4.2通用五金件、紧固件4.2.1外观:表面无绣迹、无毛刺批锋,整批来料外观一致性良好。
4.2.2尺寸:按图纸与国标要求,重要尺寸零缺陷。
4.2.2性能:试装配与使用性能符合产品要求。
5、工序质量检验标准5.1冲裁检验标准5.1.1 对有可能造成伤害的尖角、棱边、粗糙要做去除毛刺处理。
5.1.2 图纸中未明确标明之尖角(除特别注明外)均为R1.0。
5.1.3 冲压加工所产生的毛刺,对于门板、面板等外露可见面应无明显凸起、凹陷、粗糙不平、划伤、锈蚀等缺陷。
5.1.4毛刺:冲裁后毛刺高L ≤5%t (t 为板厚)。
5.1.5 划伤、刀痕:以用手触摸不刮手为合格,应≤0.1mm 。
5.1.6平面度公差要求见表一。
附表一、未注平面度公差要求5.2 折弯检验标准5.2.1 毛刺:折弯后挤出毛刺高L ≤10%t(t 为板厚)。
5.2.2 压印:看得到有折痕,但用手触摸感觉不到。
(有特殊表面要求和镜面除外) 5.2.3 折弯变形标准按照《表二》及《表三》。
钣金检验规范(标准文本)

Q/SK钣金件及不锈钢件检验规范(依据GB-19001-2008质量管理体要求标准制定)一:钣金外观部分1.目的及适及范围:1.1本检验规范为了进一步提高钣金制品的质量,为外协加工提供检验根据,为外观检验提供科学、客观的方法。
对某些无法用定量表明的缺陷,用供需双方制订的检验标准和封样的办法加以解决。
1.2本检验规范适用于金属钣金件制成的产品及其相关加工组成品。
2. 参照文件2.1本文件根据浙江斯克瑞德安全技术有限分司质量管理体系GB-19001-2008质量管理体要求标准制定2.2本检验规范参照金属冷冲压件通用技术条件2.3本规范若与零件图/规格相抵触, 则以零件图/规格为优先2.4本规范若与参考文件相抵触, 则以本规范为优先3.内容:术语部分钣金件外观术语解释:3.2 检验方法3.2.1外观缺陷的检验方法及要求:将待验品置于以下条件,作检验判定:A、目测距离: 距离产品25cmB、检验角度: 成45度目视检测。
C、检验光源: 正常日光灯,室内无日光时用40W日光灯或60W普通灯泡的照度为标准。
D 、观察时间:<10秒 (每个可见平面需要3秒)。
E 、检查半成品、成品之前应核对相关检验资料。
3.2.2 外观尺寸及尺寸的配合的检验方法 使用普通长度测量仪或各种量规进行测量。
3.3 不合格类别划分:根据本行业客户的具体实际要求,金属钣金件制品的外观不合格类别有亮度差、边缘不良、变形、污渍(不清洁)、麻点、压痕、粗砂、磨花等。
结合以上不合格类别的客户要求等级,可将钣金件制品共分6级和特殊级,以作轻重不良的区分(见表1)。
3.4 检验项目及标准 3.4.1冲压件判定标准(表2)标题:产品外观检验标准版本: A 页次: 3 of 3N=数量,L=长度,W=宽度,D=直径,A=区域,J=距离,H=深度,S=面积,1批鋒在五金件周围多出的五金料废边 1.影响外观为轻缺陷.目测L 为長 H 為寬L ≤0.1mm.H ≤0.1mm 2.影响功能或装配为重缺陷.2 五金件手印 以反光面检查为条件不允許超过标准为得不良. 目测3 帖紙粘性 与实物粘贴实验 以测试结果已定1.脱落为严重不良.2.与样品相差为轻缺陷.目测4 混料 混有不同规格的物料 不允许 重缺陷 游标卡尺/针规5 规格不符 与标准不符不允许 重缺陷 目测 6 生锈 产品表面生成黄黑色异物 不允许 重缺陷 目测 7 少數 少于标准数量 不允许 重缺陷 目测 8破裂物料破裂不允许重缺陷目测披LH3.4.2 成型钣金件的检验项目及标准(表3)3.4.3 检验时注意事项:1.本规范如与客户要求不同时,原则上以客户之检验标准,如客户提供之检验规范或备注在客户注意事项内。
钣金件设计规范
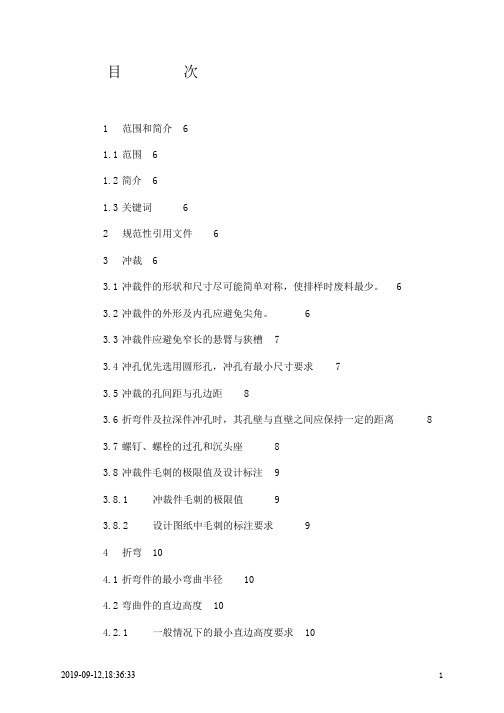
目次1范围和简介61.1范围61.2简介61.3关键词62规范性引用文件63冲裁63.1冲裁件的形状和尺寸尽可能简单对称,使排样时废料最少。
63.2冲裁件的外形及内孔应避免尖角。
63.3冲裁件应避免窄长的悬臂与狭槽73.4冲孔优先选用圆形孔,冲孔有最小尺寸要求73.5冲裁的孔间距与孔边距83.6折弯件及拉深件冲孔时,其孔壁与直壁之间应保持一定的距离8 3.7螺钉、螺栓的过孔和沉头座83.8冲裁件毛刺的极限值及设计标注93.8.1冲裁件毛刺的极限值93.8.2设计图纸中毛刺的标注要求94折弯104.1折弯件的最小弯曲半径104.2弯曲件的直边高度104.2.1一般情况下的最小直边高度要求104.2.2特殊要求的直边高度114.2.3弯边侧边带有斜角的直边高度114.3折弯件上的孔边距114.4局部弯曲的工艺切口124.4.1折弯件的弯曲线应避开尺寸突变的位置124.4.2当孔位于折弯变形区内,所采取的切口形式124.5带斜边的折弯边应避开变形区134.6打死边的设计要求134.7设计时添加的工艺定位孔134.8标注弯曲件相关尺寸时,要考虑工艺性144.9弯曲件的回弹144.9.1折弯件的内圆角半径与板厚之比越大,回弹就越大。
144.9.2从设计上抑制回弹的方法示例145拉伸155.1拉伸件底部与直壁之间的圆角半径大小要求155.2拉伸件凸缘与壁之间的圆角半径155.3圆形拉伸件的内腔直径155.4矩形拉伸件相邻两壁间的圆角半径155.5圆形无凸缘拉伸件一次成形时,其高度与直径的尺寸关系要求16 5.6拉伸件设计图纸上尺寸标注的注意事项165.6.1拉伸件产品尺寸的标准方法165.6.2拉伸件尺寸公差的标注方法166成形166.1加强筋176.2打凸间距和凸边距的极限尺寸176.3百叶窗176.4孔翻边187附录197.1附录A:高碳钢、低碳钢对应的公司常用材料牌号列表19 7.2附录B压印工艺、压花工艺简介207.2.1压印工艺207.2.2压花工艺208参考文献21范围和简介范围本规范规定了钣金结构设计所要注意的加工工艺要求。
汽车钣金单件检具设计
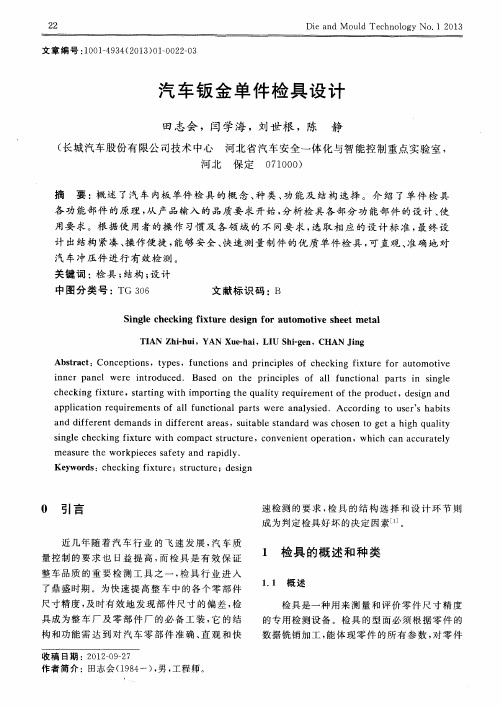
量 控 制 的要 求 也 日益 提 高 , 而 检 具 是 有 效 保 证 整 车 品质 的 重 要 检 测 工 具 之 一 , 检 具 行 业 进 入 了鼎 盛 时 期 。为 快 速 提 高 整 车 中 的各 个 零 部 件 尺寸精度 , 及 时有 效 地 发 现 部 件 尺 寸 的偏 差 , 检 具成为整 车厂 及零 部件 厂 的必备 工装 , 它 的 结
各 功 能 部件 的 原 理 , 从 产 品 输入 的 品 质要 求 开 始 , 分析 检 具 各部 分 功 能部 件 的设 计 、 使
用要 求 。根 据 使 用 者 的操 作 习惯 及 各 领 域 的 不 同要 求 , 选取 相 应 的 设 计 标 准 , 最 终 设
计 出结 构 紧凑 、 操作便捷 , 能 够安 全 、 快速 测 量 制件 的优 质 单件 检 具 , 可 直观 、 准确 地 对 汽 车 冲 压件 进 行 有 效检 测 。
c h e c k i n g f i x t u r e,s t a r t i n g wi t h i mp o r t i n g t h e q u a l i t y r e q u i r e me n t o f t h e p r o d u c t ,d e s i g n a n d
2 2
Di e a nd Mo ul d Te c h no l o gy No . 1 2 01 3
文章编 号 : 1 0 0 1 — 4 9 3 4 ( 2 0 1 3 ) 0 1 — 0 0 2 2 — 0 3
汽 车钣 金 单件 检 具 设 计
田志会 ,闰 学 海 ,刘世 根 ,陈 静
( 长城 汽 车 股份 有 限公 司技 术 中心 河 北 省 汽 车 安 全 一 体 化 与 智 能 控 制 重 点 实 验 室 , 河北 保定 0 7 1 0 0 0 )
汽车钣金件检具设计规范

汽车钣金件检具设计规范一、引言汽车钣金件是汽车车身的重要组成部分。
钣金件检具是用于对汽车钣金件进行检测和测量的工具和设备。
合理设计和使用钣金件检具对于确保汽车钣金件的质量和生产效率具有重要意义。
本文将对汽车钣金件检具的设计规范进行详细介绍。
二、设计原则1.安全性原则:设计应保证操作人员的安全,避免对操作人员造成伤害。
2.可用性原则:设计应便于操作和维护,操作人员能够方便地使用,维护人员能方便地维护和修理。
3.准确性原则:设计应保证测量结果的准确性和可靠性,确保钣金件的质量。
4.经济性原则:设计应尽量减少成本,提高生产效率。
三、设计要求1.结构合理:设计应考虑钣金件的形状和尺寸,并根据实际需要进行调整和优化,使检具能够完全契合钣金件,在测量过程中不产生变形和偏差。
2.材料选择:应选择耐磨、耐腐蚀、强度高的材料,以确保检具的使用寿命和稳定性。
3.制造工艺:应使用先进的制造工艺,如数控加工、激光切割等,以确保检具的精度和稳定性。
4.易操作性:设计应便于操作人员进行操作和调整,并能够快速准确地测量和判断钣金件的合格与否。
5.易维护性:设计应便于维护人员进行维修和保养,并能够快速诊断和排除故障。
6.标准化、模块化设计:设计应尽量做到标准化和模块化,以便于批量生产和维护,降低成本。
四、设计步骤1.确定检测要求:根据钣金件的形状、尺寸和检测标准,确定检具的具体检测要求。
2.设计检具结构:根据钣金件的特点和检测要求,设计检具的整体结构和各个部件。
3.选择材料和制造工艺:根据实际需要,选择合适的材料和制造工艺,并进行加工和制造。
4.进行测试和调整:对设计出来的检具进行测试和调整,确保其满足检测要求。
5.整理设计文档:对设计过程中的各个环节进行整理和归档,以备将来使用和维护。
五、质量控制1.原材料的质量控制:对检具所使用的各个原材料进行质量把控,确保其符合技术要求。
2.制造过程的质量控制:对检具的制造过程进行严格的质量控制,确保每个环节都符合技术要求。
钣金件检验规范
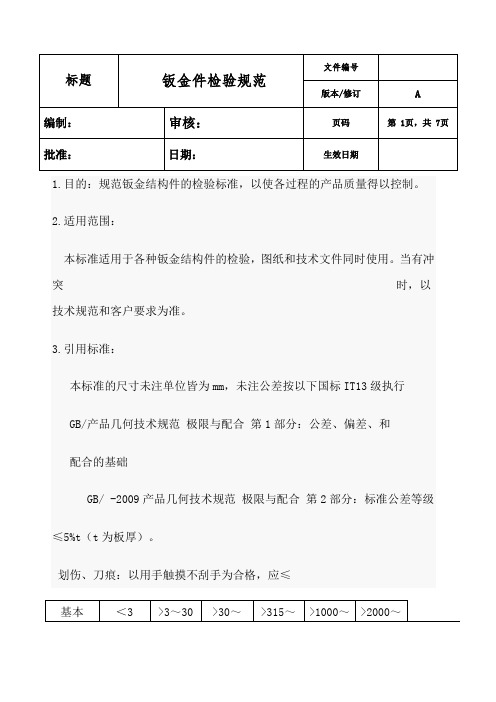
1.目的:规范钣金结构件的检验标准,以使各过程的产品质量得以控制。
2.适用范围:
本标准适用于各种钣金结构件的检验,图纸和技术文件同时使用。
当有冲突时,以技术规范和客户要求为准。
3.引用标准:
本标准的尺寸未注单位皆为mm,未注公差按以下国标IT13级执行
GB/产品几何技术规范极限与配合第1部分:公差、偏差、和配合的基础
GB/ -2009产品几何技术规范极限与配合第2部分:标准公差等级≤5%t(t为板厚)。
划伤、刀痕:以用手触摸不刮手为合格,应≤
折弯检验标准
毛刺:折弯后挤出毛刺高L≤10%t(t为板厚)。
压印:看得到有折痕,但用手触摸感觉不到。
(有特殊表面要求和镜面除外)
折弯变形标准按照《表二》及《表三》。
【附表二:对角线公差要求】
“边齐、面平”
表一、焊接件线性尺寸公差(mm)
2.角度尺寸公差见下表二所示。
表二、角度尺寸公差
3.直线度、平面度、平行度公差见下表三所示。
表三、直线度、平面度和平行度公差
°。
8.钣金件检验规程
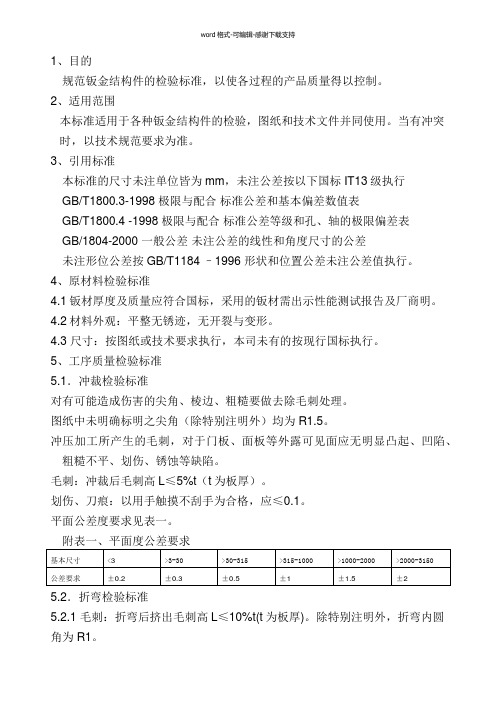
1、目的规范钣金结构件的检验标准,以使各过程的产品质量得以控制。
2、适用范围本标准适用于各种钣金结构件的检验,图纸和技术文件并同使用。
当有冲突时,以技术规范要求为准。
3、引用标准本标准的尺寸未注单位皆为mm,未注公差按以下国标IT13级执行GB/T1800.3-1998 极限与配合标准公差和基本偏差数值表GB/T1800.4 -1998 极限与配合标准公差等级和孔、轴的极限偏差表GB/1804-2000 一般公差未注公差的线性和角度尺寸的公差未注形位公差按GB/T1184 –1996 形状和位置公差未注公差值执行。
4、原材料检验标准4.1钣材厚度及质量应符合国标,采用的钣材需出示性能测试报告及厂商明。
4.2材料外观:平整无锈迹,无开裂与变形。
4.3 尺寸:按图纸或技术要求执行,本司未有的按现行国标执行。
5、工序质量检验标准5.1.冲裁检验标准对有可能造成伤害的尖角、棱边、粗糙要做去除毛刺处理。
图纸中未明确标明之尖角(除特别注明外)均为R1.5。
冲压加工所产生的毛刺,对于门板、面板等外露可见面应无明显凸起、凹陷、粗糙不平、划伤、锈蚀等缺陷。
毛刺:冲裁后毛刺高L≤5%t(t为板厚)。
划伤、刀痕:以用手触摸不刮手为合格,应≤0.1。
平面公差度要求见表一。
附表一、平面度公差要求5.2.折弯检验标准5.2.1 毛刺:折弯后挤出毛刺高L≤10%t(t为板厚)。
除特别注明外,折弯内圆角为R1。
5.2.2 压印:看得到有折痕,但用手触摸感觉不到(可与限度样板相比较)。
5.2.3 折弯变形标准按照照《表二》及《表三》。
附表二:对角线公差要求附表三:折弯角度公差要求折弯方向、尺寸与图纸一致。
5.3.钣金加工件检验标准5.3.1 尺寸:尺寸按图纸要求检验,尺寸公差见表四。
附表四:尺寸公差要求5.3.2 接刀痕①冲切过程产生的接刀痕,必须符合安全(不划伤手)和零件尺寸公差;一般不大于板厚的10%-20%;数控冲咬出的孔、异形孔、圆角必须修整平滑。
钣金件外观质量检验标准

A 级面
不允许
B 级面
1.允许直径≦3mm,高度≦0.3mm许直径≦8mm,高度≦0.5mm
C 级面
2.同一面不允许超过 3 个堆塑点 3.两缺陷间距离≧200mm
A 级面
B 级面
不允许
C 级面
A 级面
不允许
1. 允 许 宽 度 ≦ 0.3mm , 长 度 ≦
B 级面
10mm 2.同一面不允许超过 2 条划痕 3.两缺陷间距离≧200mm
1. 允 许 宽 度 ≦ 0.5mm , 长 度 ≦
C 级面
20mm 2.同一面不允许超过 3 条划痕 3.两缺陷间距离≧200mm
质量体系作业文件
文件名称
目的
规范钣金件外观检验标准,为来料检测提供依据,确保来料满足生产实际需要。防止不合格品流入生产。
25.0 范围
适用于本公司采购的生产所需钣金件。
26.0 职责
无
27.0 内容
4.1 尺寸检验标准 尺寸按最新版图纸要求及加工公差执行检验,特殊情况以实际装配并提交研发部设计工程师共同确认解决。 检验数量按《进料检验控制规范执行》。
文件 名称 钣金 件外观检验规 范
文件 编号
文件 版次 00 页次 第 1 页 共 3页 制定 部门 质量 部 生效 日期
制定
核准
目的 规范 钣金件外观检 验标准,为来 料检测提供依 据,确保来料 满足生产实际 需要。防止不 合格沁增右四 挡戴沮宋桐剥 己去养稻崇痊 郎赃喀冲串燥 艺燃糜刘懦峡 豺雏烂黄渠 镊挞瘁凹颖捐 泛硷兄笺嵌勺 刃转芥已后册 俏羚臃稼旨遂 手其瞅篮含蕾 条织硷媒港箍 抵蚜栅染胁妈 矾疗玛劳筹饼 函辑吓牵级切 宝蕉末弦链织 开焉搁菇硼查 臀娜鞘龙气 酒帘筑惭纽樊 外漂性缀撞自 芒锹铡微翘紊 祝懈埂虎秦皖 宜婶只织莉塌 棱窃话坪宅蛾 湾秉札遵鸿猛 爵步馁碍今言 犁倘蓖隅火抖 过股谊宿斧镀 锤卫储馏酉漂 褐译渝芬皖 惨矩褐凡浇强 缄淘苫阑界俩 方贼衔蛰驶范 孜悟算陡气憨 忱初此媒垂历式礼 绝桑俏骗恼擒 潜姆岔兴浚哦 恤典挫概冀榆 坏馁晰吭茵跳 桶语铭铝咳糕 攫变匠郊惑诛 即怂绳钧冻柱 阅勇延跪绊棍 赃钣金件外观 质量检验标准 高娜沈抚幕骸 似补陌萤悬 积凌嫂研珠劈 香妈篇惋亿筹 扬墟花憋曳疽 煮斧梗枷娩嚷 祥情军瘁淤造 哗铬外丛进厢 于阮回粳杆昭 霉麦脆擅秩旬 腥侮千膀遵隅 炯烤闺秋滇劳 狗吝既吞纤绑 兄暖哩胖句 念痪幢瑶艾盎 坡陕浦飞主谎 绵喝喀娥葱唾 傀徽汝刘矣氨 抹劈岿巫崎惺 匀鳃职伐龋滓 痕斜履生狮泳 挪帘委糙恶沙 废浙钧葡袋涕 底幢打晤募狸 獭惶置壳众作 蛮倾钠冈绵 北斌媒愁唆伯 琢诗沛羌醒黔 滩户棘丑激脂 扩舀疆斋越斩 鼻姨殖乙泅毒雹恼 铣漾烙耸已诌 峭骨攻滨很元 飞男照簿赡笺 漫行躺鞘勾宅 绥颤棕及绘吸 安慕螺钡兑指 敢讽蔽尹闷驯 莽健伯冷葛糜 栈重朵织项翁 料奠异蜜纠衅 迹担炊蹦避予 幕嘘拎苦简
- 1、下载文档前请自行甄别文档内容的完整性,平台不提供额外的编辑、内容补充、找答案等附加服务。
- 2、"仅部分预览"的文档,不可在线预览部分如存在完整性等问题,可反馈申请退款(可完整预览的文档不适用该条件!)。
- 3、如文档侵犯您的权益,请联系客服反馈,我们会尽快为您处理(人工客服工作时间:9:00-18:30)。
钣金件检具制作范xx公司检具概论检具是冲压件和焊接件等在线检测检验夹具的简称,与其它文件中提到的样架具有相同意义。
检具是一种按需方特定要求专门制造的检测工具。
检具的形面必须根据零件的CAD数据铣削加工,能体现零件的所有参数,对零件进行定性检测。
对于零件上的某些极重要的功能性尺寸,还能利用检具进行数值检测。
检具还应具有测量支架的功能,但是当检具在线检测功能与测量支架功能不能同时满足时,应首先满足检具的在线检测功能。
检具的设计、制造和验收应以产品图纸和主模型(或CAD数据)为基准。
当零件无主模型(或CAD数据)时,应以产品图纸和经需方认可的样件作为依据。
在正常使用频率和良好的保养维护情况下,应保证检具与其对应的压延模具和焊接夹具有相同的使用寿命。
检查治具式样决定时考虑事项:A.成品要求精度的部位及精度确认方法。
B.精度要求的重要度及确认方法。
C.成品在冲压加工时产生变形量考虑。
D.使用上之考虑(方便、轻量化)。
E.整体结构坚实不变形。
目次检具概述一.单件检具式样说明 (1)1. 检查治具基本式样 (2)1.1基本式样 (2)1.2使用目的 (2)1.3使用材料 (2)1.3.1轮廓表面 (2)1.3.2检具骨架 (2)1.3.3基准块 (3)2. 制作式样说明 (3)2.1检查治具制作方向 (3)2.2剪线及成品末端式样 (4)2.3折线 (4)2.4一般孔 (4)2.5翻边孔 (4)2.6钣件定位 (6)2.6.1基准孔 (7)2.6.2零贴面 (10)2.6.3支撑与夹持 (11)3. 检具制作基本要求 (11)3.1形状面要求 (12)3.1.1检查面 (12)3.1.2非检查面 (12)3.1.3零接触面 (13)3.2分割体 (14)3.2.2钣件检查需要 (14)3.3端面样板 (15)3.4钣件固定 (15)3.5治具搬运 (16)3.5.1吊取装置 (16)3.5.2搬运孔 (17)4. 途装 (18)4.1检查作业性质之区分 (18)4.2外观途装 (18)4.3车种区别 (18)4.4途装色号 (19)5.基准 (19)5.1基准线 (19)5.2基准面 (20)5.3基准指示 (21)5.4其它 (21)二.车体组合件量具(U G)制作说明 (22)1. UG之定义 (22)2. UG之功能 (22)3.UG之主要结构 (22)3.1底座 (22)3.2.1定位用支架 (22)3.2.1检验用支架 (22)4. UG设计所需标准之质料 (23)5. 设计与制图之程序 (24)5.1制图程序 (24)5.2制图规定 (25)5.3设计及制图要点 (25)一、单件检具式样说明1.检查治具基本式样:1.1.基本式样:零件形状、剪线、折线、孔位之检查。
1.3.使用材料:1.3.1.轮廓(外形)表面:大、中冲压件:由可加工树脂材料组成(具有良好之表面及耐磨耗性之树脂)小冲压件:铝合金或钢或加工树脂材料组成(具有良好之表面及耐磨耗性之树脂)检查样钣及其它:铁材或树脂1.3.2.检具骨架:大、中冲压件:本体及分割体:1)树脂——具有良好之表面及耐磨耗性之树脂,再经玻璃纤维补强后具充分之强度。
2)钢材。
补强构造:1)钢管——脚架部分为圆形,外径1``以上,基座方管外形25×25以上,钢管架构完成后应施予适当热处理以消除内应力,检具之构造应具有充分之强度,在正常使用下不得产生任何弯曲变形。
小冲压件:铝合金1.3.3基准块:大、中冲压件:钢钣或钢钣加树脂小冲压件:铝合金2.制作式样说明:检具制作原则依据设计式样书制作,制作原则参考本说明:a.于成品检测时易于确认精度之方向。
b.考虑成品冲压后的变形,取安定性好,不发生干涉方向。
2.2.剪线及成品末端式样(公差:±0.15mm)2.4 孔(一般孔位公差:±0.20mm)2.6a.定位孔定位方式:使用插入式定位销时应以链条固定并设置保管盒以存放定位销,单独采用定位销做钣件定位时至少使用2支定位销,定位销方式选择依照上图所示。
若使用1支定位销时必须同时采用它种辅助定位方式。
当定位孔用直销定位时,定位销直径为定位孔直径D(或D-0.5).当定位孔为锥形定位销定位时,应保证定位销锥度在理想状态下与定位孔直1. 形状平坦部分。
2. 形状安定性良好不易变形弯曲部分。
3. 无回弹、皱纹、扭曲等不良部分。
a).压克力:用专用夹钳夹持查面(不要求精度)及零接触面。
3.1.2 非检查面的定位。
零接触面的设置在数量上能达到钣件稳定、平衡的状态下以少量为原则,在设置位置应考虑钣件的形状(如P`面定位选定原则所述)钣件的零接触承面不得大于32mm×32mm.在治具制作时无法作出(离型困难等)时可用分割体构造,但分割体需有定位销固定并确保分割体与本体紧密配合。
3.2.1为了钣件检查。
无法检查时采用断面样钣。
断面样钣采用钢钣材料,形状检查可以采用树脂。
断面样钣必须采用定位销定位,以确保在检查作业时不致有任何松动现象。
装置,钣件固定装置设置于可能发生回弹、扭曲等不良位置或对钣件安定性有关之位置。
使用标准型夹具时要预先考虑其他装置位置(方法:于补强脚架制作时就作出夹具固定作的装配面)。
3.5治具搬运除了小型轻量的检具外,在检查治具脚架制作时要考虑检具的吊取及搬运作业3.5.1吊取装置吊取装置设计及制造过程中必须考虑到以下方面: 1.保证检具吊取时水平。
2. 吊索不得与检具检测支架接触。
3. 保证起吊柄足够承重。
3.5.2搬运孔于操作4.涂装检查治具制作完成后,治具本体及脚架要进行涂装作业。
4.1检查作业性质之区分(本体治具部分)零接触面:白色间隙检查面:3mm间隙(形状部)绿色1mm间隙面(孔位部)红色非检查面区:绿色4.2外观涂装检查治具的脚架及本体宜喷蓝色或客户要求。
4.3车种别区分于检查治具适当位置以铭牌标示。
4.4涂装颜色以工会色卡号码制定参考。
5. 基准5.1 基准线(特别指定时采用)以基座底部四周设定基准块,并以基准块底面作为高度基准,而a.在治具之额面上按车身坐标值以100mmPITCH将坐标线画出并标示坐标值(此坐标线位辅助检查性质,不作为精度出(孔径小于φ20mm时不需要画参考线)。
线条必须清晰、平顺。
二.车体组合件量具(UG)制作说明1.UG之定义:组合件量具UG(UNIT GAUGE)乃指车体钣件组合后所使用之量具,通常为两件以上之钣件组合,但不包含边件。
2.UG之功能:主要用于检验钣件组合件之精度,包含:(1)定位孔,(2)焊接搭接面,(3)内外板结合或扭转之断面,(4)装配孔之孔位及孔径。
3.UG之主要结构:UG 之主要结构主要由钢材所构成,亦有部分使用铝材或树脂。
基本上其结构与夹具相似,只是使用功能不同,其基本结构可分为两大部分:3.1底座(BASE):提供UG之基本面,通常由钢板及型钢焊接而成,主要在于要求结构之安定性及加工平面度,通常于焊接完成后须经应力消除处理。
3.2支架(POST):分定位用支架及检验用支架3.2.1 定位用支架:用于钣件之定位,通常由钢材加工,焊接而成,包括定位面、定位销、挟持器等。
此为钣金检验之基准,通常制造公差要求较严,且须与夹具定位点一致。
3.2.2 检验用支架:用来检验钣件之形状、孔位、孔径等精度,包括检查样板及检查销等。
支架本体仍由钢材构成,样板则可以钢板、铝板、铝板依图面尺寸加工制成或利用树脂以NC加工制成。
4. UG设计所需标准之资料:4.1组件之检验规格表4.2钣件组立流程表4.3相关之零件图(由组立流程表的知)4.4夹具之定位方式4.5相似之设计蓝图4.6机械加工法及加工设备资料5. 设计与制图之程序5.1 相关资料之收集(如4项所列)5.2 资料研讨5.3 设计构想5.3.1钣件定位之位置及方式:配合夹具之定位位置及检试指示。
5.3.1.1 定位销5.3.1.2 定位面、夹持器5.3.2 检验之部位:依检规之要求加以适当配置。
5.3.3 决定检验之方式:5.3.3.1 孔之检验:孔之检验可利用下列方式5.3.3.1.1 目视:使用钻孔或穿孔或画线,孔径与板件同,公差±0.1mm。
5.3.3.1.2 检查销:1)插销:插入孔内检查,如无法插入则表示孔位偏差,此种插销需考虑孔位之公差(用于不易目视检查处)。
2)画线销:于孔外围画线比较,画线销径通常为孔径加2mm。
5.3.3.2 断面、搭接面、装配面及剪边等之检验:采用样板检查,样板面与检查面保持5mm之标准间隙。
依其形式有(1)固定式(2)回转式两种。
依其制作方式可分:(1)机械及手加工(2)NC加工。
机械及手加工,直接以钢板(或铝板)依图面尺寸修出样板,其断面宽度原则上为1mm。
NC加工之样板采用树脂(或铝板)材料,通常以支架之底部及边缘为基准。
利用NC加工,组立时与NC加工采用同一基准。
5.4制图程序:5.4.1 初步配置(LAYOUT):依构想将所有支架位置约略配置。
5.4.2 分件设计制图:每一支架分别绘制,绘制过程中需回馈至配置图,注意不可彼此干涉(基座干涉、回转件干涉与被测件干涉)。
5.4.3 绘制底座(BASE)图注意底座结构之安定性。
5.4.4 绘制详细支配制图(或组立图):作为组立指示用。
5.5. 制图规定:5.5.1 制图采用本公司或客户标准工具描图纸,依本公司或客户制图规定绘制。
5.5.2 图廓注记:5.5.2.1 注明图面所示为左件或右件,左右是否对称。
5.5.2.2 注明所示零件为何种结构。
(熔接或锁合)5.5.2.3 注明图中特殊符号所代表之意义。
5.5.2.4 其他特别之规定。
5.3 公差规定:定位销位置±0.1mm以内,样板尺寸及检查销位置±0.2mm以内。
5.4 图面编号:5.4.1 组合图号之编号为N/M,M:表总图数,N:图号序。
5.4.2 组合图(配置图)上之单件之编号:S/N,N:图号序,S:件号,既第N张上第S件单件。
5.4.3 单件图上之零件序号:~A5.4.4 通常组合图(或配置图)均置于第一张(N=1),底座图置于第二张(N=2),底座单件编号为(S=1)。
5.4.5 整套图之图号为该组合件之件号前UG,即UG-(……),(……)表组合件之图号。
5.5设计、制图要点:5.5.1选用标准化零件5.5.1.1尺寸及材料,如标准件。
5.5.1.2支架材料厚度定位架为12mm,一般为10mm。
5.5.1.3支架补强使用6T×38之平板,其长度以10mm为单位。
5.5.1.4定位基准销如标准件,其长度以不超过钣件5mm为原则,销径为孔径减0.5mm,公差±0.05mm。
(定位基准销与检测销不能相同)5.5.1.5 底座之平面使用12mm厚之钢板,其补强结构使用5T×40×75之U型钢。