从离子渗硫到润滑耐磨梯度材料
常用表面渗硫方法

常用表面渗硫方法目前,材料的表面渗硫方法主要有4种,分别是:液体渗硫、固体渗硫、气体渗硫、低温等离子渗硫等[5]。
1.1 液体渗硫电解渗硫是目前应用较多的渗硫方法,法国的低温盐浴电解法(即Sulf —BT法) 及其改进后的各种方法已被法、英、德、美、意、日等国广泛采用。
一般摩擦系数是未处理试样的30%~50% ,也有报导20号钢在室温电解渗硫时摩擦系数约为非渗硫10%~20% 。
中温渗硫是以硫酸钠作为含硫源,外加一些化学腐蚀剂,处理温度为550℃左右,保温时间取决于渗层的深度;低温渗硫常以(NH2)2CS 为主要试剂,辅助试剂有KSCN (NH2) 2CO 等物质,处理温度低于200℃,由于温度低,所需时间较长。
渗硫层易产生FeSO3 ,导致工件表面锈蚀,产生氰盐试剂有毒,介质易老化,造成环境污染,且工件的后道处理很麻烦,难以较好解决。
总之,液体渗硫由于盐浴存在污染严重、易老化变质、成分和活性难以控制等问题,处理后工件的质量尚不够稳定。
近年来在改进渗硫盐浴成分,减少环境污染方面已有较大的进展,有的盐浴成分基本无毒性,为盐浴渗硫的广泛应用创造了有利条件。
1.2 固体渗硫又称粉末渗硫,一般以FeS 粉为供硫剂,与适量的催化剂防粘接剂等制成50~100 目的细粉状混合物,在500℃~900℃高温炉中向工件表面渗硫,工艺类似于固体渗碳,加热温度和保温时间随工件材料不同而选择。
其优点是简便易行,投资少,成本低,通用性好。
缺点是劳动条件差,温度高,工艺时间长,质量不稳定,目前在生产上已应用不多。
1.3 气体渗硫即离子渗硫,是将含硫气体(如H2S,CS2 等)通入密闭炉中,加热使之分解出活性原子(离子)进行工件表面渗硫。
离子渗硫是一个广义的工艺概念。
实际应用中,它包含了单纯的离子渗硫、离子硫氮共渗和离子硫氮碳共渗等多种工艺,(一)离子渗硫工艺离子渗硫通常是在160~300℃的低温下进行的,常用的离子渗硫温度为180~200℃。
纳米二硫化钼作为润滑油添加剂的润滑机理

MoS2晶体属于六方晶系,为典型三明治结构的层状化合物,每个平面层为S-Mo-S的结构,层内Mo和S以共价键结合为三方柱面体结构,层间以微弱的范德华力维系,因此,层状的MoS2容易受外界环境的影响破坏层与层之间的堆垛结构,并形成较为稳定的薄层,当MoS2用作润滑剂时,层状MoS2会转移到金属表面,缓和摩擦和磨损,这一性质使其在摩擦润滑领域有很好的应用,20世纪50年代,普通MoS2就作为固体润滑剂得到了广泛应用。
纳米材料是指至少有一维尺寸为纳米级别的材料,而当材料的尺寸缩小至纳米级别时,会凸显处诸如小尺寸效应、界面效应、量子隧道效应等性能特点。
研究表明,一些纳米尺度的固体粒子加入到润滑油中,可以明显提升润滑油的性能,展现出许多优于传统添加剂的特点。
近年来,将纳米MoS2用作润滑油添加剂得到了广泛关注,本文主要介绍纳米MoS2作为润滑油添加剂的润滑机理。
润滑机理1物理吸附/沉积作用学者们普遍认为,典型的MoS2晶体为层状结构,层与层之间以范德华力连接,在摩擦产生的剪切应力下层状结构剥离,并吸附到摩擦表面,这一过程对抗磨减摩有显著作用,如图1所示摩擦过程中纳米MoS2的层状剥离Wu等研究了纯MoS2和硼酸锌/MoS2纳米复合材料的摩擦学性能,研究发现当使用纯纳米MoS2作为添加剂时,有缺陷的MoS2纳米片和部分氧化的MoS2纳米片会导致润滑不良,在润滑油中加入硼酸锌/MoS2纳米复合材料时,具有极压性能的硼酸锌纳米颗粒能有效地填充MoS2纳米片的表面缺陷,并连续提供保护膜,以进一步降低摩擦系数,提高承载能力。
还有学者指出,纳米MoS2可以填充摩擦表面的微裂纹区域,对磨损位置起到了修复作用化学吸附/反应膜纳米MoS2扩散能力强、表面能高、颗粒表面缺陷结构多,容易参加摩擦化学反应。
有学者报道,在钢制摩擦副中纳米MoS2可以生成含FeS、FeSO4等产物的化学反应膜,反应膜的形成减少了摩擦基体的直接接触,降低了摩擦磨损,图2展示了纳米MoS2参加摩擦化学反应的一种典型方式。
梯度功能材料

梯度功能材料梯度功能材料State:1. 此⽂在是从中英⽂⽂献中的“简单总结”,没列出相应的参考⽂献2. 是为允诺⼀位朋友⽽做,也可以算作⾃⼰的读书⼩笔记,仅此⽽已背景梯度功能材料( Functionally Gradient Materials ,简称FGM)是由于航空航天技术的发展⽽提出的新概念。
航天飞机在⼤⽓层中长时间飞⾏,机头尖端和发动机燃烧室内壁的温度⾼达2100 K 以上,因此材料必须承受很⼤的⾼温以及内外的温度差别,服役的环境很恶劣。
1984 年,⽇本学者Masyuhi NINO,Toshio HIRA,和Ryuzo WATANBE等⼈⾸先提出了FGM 的概念,其设计思想⼀是采⽤耐热性及隔热性的陶瓷材料以适应⼏千度⾼温⽓体的环境,⼆是采⽤热传导和机械强度⾼的⾦属材料,通过控制材料的组成、组织和显微⽓孔率,使之沿厚度⽅向连续变化,即可得到陶瓷⾦属的FGM。
所谓梯度功能材料(FGM), 即在材料制备过程中,使组成、结构及孔隙率等要素在材料的某个⽅向上连续变化或阶梯变化, 从⽽使材料的性质和功能也呈连续变化或阶梯变化的⼀种⾮均质复合材料。
功能梯度材料的研究开发最早始于1987 年⽇本科学技术厅的⼀项“关于开发缓和热应⼒的功能梯度材料的基础技术研究”计划。
该项⽬于1992 年完成,随后将⼯作重⼼转向模拟件的试制及其在超⾼温、⾼温度梯度落差及⾼温燃⽓⾼速冲刷等条件下的实际性能测试评价上,并于1993 年开始研究具有梯度结构的能量转换材料。
第⼀届国际FGM 研讨会于1990 年在⽇本仙台召开,之后每两年举办⼀届。
中国于2002 年在北京主办过第七届FGM国际研讨会。
特点功能梯度材料的关键特点是控制界⾯的成分和组织连续变化,使材料的热应⼒⼤为缓和。
从材料的组成⽅式看,功能梯度材料可分为⾦属/陶瓷、⾦属/⾮⾦属、陶瓷/陶瓷、陶瓷/⾮⾦属和⾮⾦属/聚合物等多种结合⽅式。
从组成变化可划分为:功能梯度整体型(组成从⼀侧到另⼀侧呈梯度渐变的结构材料),功能梯度涂覆型(在基体材料上形成组成渐变的涂层)和功能梯度连接型(粘结两个基体间的接缝呈梯度变化)。
复合化学热处理13Cr4Mo4Ni4VA钢摩擦磨损性能研究
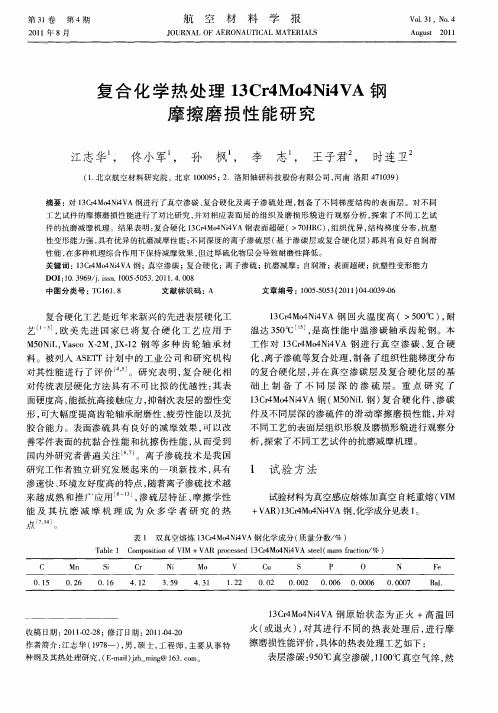
[ 2 I i Jn WA G H i o ,Z A G Nn , t 1 o 1 ]LU J — , N a— u H N ig e a.In au D
I v sia in o l i e r Ch r ce itc fVa u m - a b rz d, n e tg to fS i ng W a a a t rsiso c u c r u ie d Du lx— r e e n a m a S lurz d 1 Cr M 0 NiVA t e p e ha d n d a d Pl s - u f ie章编号 :10 —0 3 2 1 )40 3 -6 0 555 (0 0 — 90 1 0
复合硬 化工 艺是 近年 来新 兴 的先进 表层硬 化 工 艺 ¨ J 欧 美 先 进 国 家 已将 复 合 硬 化 工 艺 应 用 于 , M5 N L V soX 2 J 1 0 i , ac .M,x.2钢 等 多 种 齿 轮 轴 承 材 料 。被列 入 A E T计 划 中 的工 业 公 司和 研 究 机 构 ST
江 志 华 佟 小 军 , 孙 枫 李 志 , 王 子君 时连 卫 , , ,
(. 1北京航空材料研究 院 , 北京 10 9 ; .洛阳轴研 科技股份有限公司 , 00 5 2 河南 洛阳 4 13 ) 7 0 9 摘要 : 1C4 4 iV 对 3 rMoN4 A钢进行 了真空渗碳 、 复合硬化及离子 渗硫处 理 , 制备 了不 同梯度 结构 的表面层 。对 不 同 工艺试件的摩擦磨损性能进行 了对 比研究 , 并对相应表面 层 的组 织及磨 损形貌 进行 观察分析 , 索了不 同工艺试 探 件的抗磨 减摩 机理 。结果表明 : 复合 硬化 1 C4 4 iV 3 rMo N4 A钢表面超硬 (>7 H C , 0 R ) 组织优异 , 结构梯 度分布 , 抗塑 性变形能力强 , 具有优异 的抗磨 减摩 性能 ; 同深度 的离 子渗硫层 ( 不 基于 渗碳 层或复合 硬化层 ) 都具 有 良好 自润滑 性 能 , 多种机理综合作用下保持减 摩效 果 , 在 但过厚硫化物层会导致耐 磨性 降低 。
第六章 齿轮固体润滑高分子涂层材料
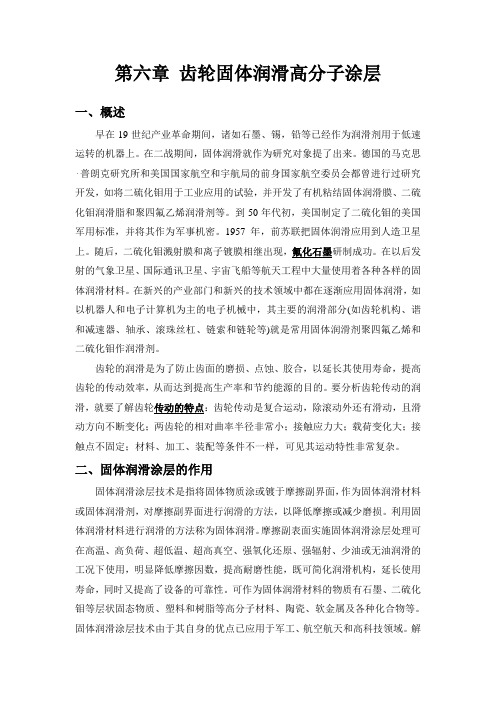
第六章齿轮固体润滑高分子涂层一、概述早在19世纪产业革命期间,诸如石墨、锡,铅等已经作为润滑剂用于低速运转的机器上。
在二战期间,固体润滑就作为研究对象提了出来。
德国的马克思⋅普朗克研究所和美国国家航空和宇航局的前身国家航空委员会都曾进行过研究开发,如将二硫化钼用于工业应用的试验,并开发了有机粘结固体润滑膜、二硫化钼润滑脂和聚四氟乙烯润滑剂等。
到50年代初,美国制定了二硫化钼的美国军用标准,并将其作为军事机密。
1957年,前苏联把固体润滑应用到人造卫星上。
随后,二硫化钼溅射膜和离子镀膜相继出现,氟化石墨研制成功。
在以后发射的气象卫星、国际通讯卫星、宇宙飞船等航天工程中大量使用着各种各样的固体润滑材料。
在新兴的产业部门和新兴的技术领域中都在逐渐应用固体润滑,如以机器人和电子计算机为主的电子机械中,其主要的润滑部分(如齿轮机构、谐和减速器、轴承、滚珠丝杠、链索和链轮等)就是常用固体润滑剂聚四氟乙烯和二硫化钼作润滑剂。
齿轮的润滑是为了防止齿面的磨损、点蚀、胶合,以延长其使用寿命,提高齿轮的传动效率,从而达到提高生产率和节约能源的目的。
要分析齿轮传动的润滑,就要了解齿轮传动的特点:齿轮传动是复合运动,除滚动外还有滑动,且滑动方向不断变化;两齿轮的相对曲率半径非常小;接触应力大;载荷变化大;接触点不固定;材料、加工、装配等条件不一样,可见其运动特性非常复杂。
二、固体润滑涂层的作用固体润滑涂层技术是指将固体物质涂或镀于摩擦副界面,作为固体润滑材料或固体润滑剂,对摩擦副界面进行润滑的方法,以降低摩擦或减少磨损。
利用固体润滑材料进行润滑的方法称为固体润滑。
摩擦副表面实施固体润滑涂层处理可在高温、高负荷、超低温、超高真空、强氧化还原、强辐射、少油或无油润滑的工况下使用,明显降低摩擦因数,提高耐磨性能,既可简化润滑机构,延长使用寿命,同时又提高了设备的可靠性。
可作为固体润滑材料的物质有石墨、二硫化钼等层状固态物质、塑料和树脂等高分子材料、陶瓷、软金属及各种化合物等。
减磨材料种类

减磨材料种类随着工业的发展和技术的进步,减磨材料的应用范围越来越广泛。
减磨材料是一种用于减少摩擦、磨损以及延长设备寿命的材料。
它们可以应用于各个行业,包括机械制造、航空航天、汽车制造、电子电气、建筑材料等领域。
下面将介绍几种常见的减磨材料。
1. 涂层材料涂层材料是一种常见的减磨材料,它可以在机械零件的表面形成一层保护膜,以减少摩擦和磨损。
涂层材料可以分为有机涂层和无机涂层两种类型。
有机涂层通常由有机聚合物组成,如聚酰胺、聚醚酮等。
无机涂层则由无机化合物组成,如氧化铝、氮化硅等。
涂层材料具有耐磨、耐腐蚀、耐高温等特点,可以有效地保护机械零件的表面。
2. 摩擦材料摩擦材料是一种用于减少摩擦力和磨损的材料。
常见的摩擦材料包括润滑油、润滑脂、润滑膏等。
这些材料可以在机械零件的接触面上形成一层润滑膜,减少摩擦力和磨损。
摩擦材料具有良好的润滑性能和化学稳定性,可以延长机械设备的使用寿命。
3. 磨料材料磨料材料是一种用于磨削和抛光的材料。
常见的磨料材料包括金刚石、石英、碳化硅等。
这些材料具有硬度高、耐磨性好的特点,可以用于对工件表面进行加工和修复。
磨料材料广泛应用于金属加工、玻璃加工、石材加工等领域。
4. 弹性材料弹性材料是一种具有弹性和耐磨性的材料。
常见的弹性材料包括橡胶、聚氨酯等。
这些材料具有良好的弹性和耐磨性,可以用于减少冲击和振动,保护机械设备的正常运行。
弹性材料广泛应用于汽车制造、机械制造等领域。
5. 超硬材料超硬材料是一种具有超高硬度和耐磨性的材料。
常见的超硬材料包括金刚石、立方氮化硼等。
这些材料具有硬度极高、耐磨性好的特点,可以用于加工硬度高的材料,如金属、石材等。
超硬材料广泛应用于石油钻探、切割加工等领域。
减磨材料种类繁多,应用广泛。
无论是涂层材料、摩擦材料、磨料材料、弹性材料还是超硬材料,它们都可以有效地减少摩擦、磨损和延长设备寿命。
在未来的发展中,减磨材料将继续发挥重要的作用,为各个行业提供更加可靠、高效的解决方案。
摩擦学-离子镀
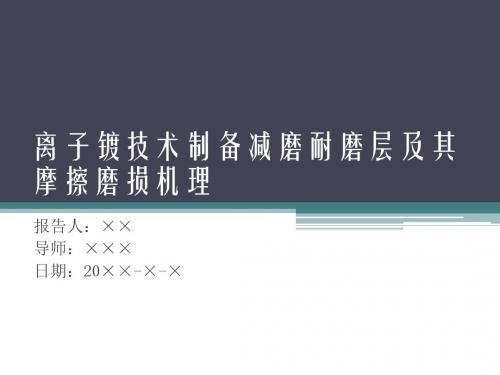
21
2.5.1活性反应离子镀的设备
右图为活性反应离子镀膜 机结构示意图。 在安装电子枪蒸发源的二 级型离子镀膜机中,于坩埚的 上方安装了一个活化电极,放 电时活化电极对地(坩埚)为 正极,电压为50V~80V。吸引 从坩埚内的金属锭上激发出的 二次电子。增加了坩埚上方的 碰撞概率。
22
2.5.2活性反应离子镀的特点
19
2.4.3空心阴极离子镀的特点
• 在空心阴极离子镀中,等离子体电子束一方面作 为气化金属的热源,另一方面当金属蒸气通过等 离子体电子束区域时,其受到高密度电子流中电 子的碰撞而发生离化。 • 在镀膜过程中,含有大量的高速中性粒子,其数 量比其他离子镀方法高两三个数量级。高的荷能 粒子轰击促进了膜/基间原子的扩散,提高了膜/ 基间结合力和膜层致密性。
32
2.6.3阴极电弧离子镀工艺过程(以沉积TiN为 例)
VI. 取出工件。当膜层厚度达到预定要求后,向镀 膜室,取出工件。
33
2.6.4阴极电弧离子镀的特点
28
2.6.3阴极电弧离子镀工艺过程(以沉积TiN为 例)
I. 安装工件。工件安装在工件卡具上后,关上镀 膜室。 II. 抽真空至6×10-3Pa以上。 III. 烘烤加热。开启烘烤加热电源,对工件加热。 达到预定温度
29
2.6.3阴极电弧离子镀工艺过程(以沉积TiN为 例)
IV. 轰击净化。一般阴极电弧离子镀只进行钛离子 轰击净化,也称主弧轰击。通氩的真空度为 2×10-2Pa,工件偏压为800V~1000V。逐个开 启弧电源,引燃冷场发射弧光放电,靶面产生 高密度的弧光等离子体。从靶面发射大量的电 子流、钛离子流和钛蒸气流,在较高的真空度 下,金属离子几乎不产生碰撞地高速到达工件。 高密度、高能量的金属离子流将工件表面吸附 的残余气体和污染物溅射下来,是工件表面充 分净化,并形成一定的“伪扩散层”。
油管离子渗氮方法及防腐耐磨性能分析

油管离子渗氮方法及防腐耐磨性能分析Research on Oil Pipelines Corrosion and Wear Resistance Property byPlasma Nitriding Method傅乐荣1牛君2左治江1(1.江汉大学机电与建筑工程学院,湖北武汉430056;2大安恒锐采油设备有限公司,吉林大安131322)School of Mechanical-electrical & Architecture Engineering, Jiang Han University, Wuhan, 430056Daan Hengrui Oil Equipment Co., Ltd.[摘要]对油管内壁进行离子渗氮以提高其使用寿命,是一种国内外还未用于油管批量生产的新工艺方法,本文介绍了油管离子渗氮的基本原理和工艺,对离子渗氮油管的耐磨性和耐腐蚀性能进行了测试,结果表明,离子渗氮油管不仅具有高的耐磨性,还提高了油管的耐腐蚀能力。
Abstract:Plasma nitriding oil pipelines inner wall could increase its service life, which is a new process method that didn’t apply to batch production in domestic and foreign at present. This paper introduced the basic principle and technology of plasma nitriding process. The wear resistance and corrosion resistance were tested after plasma nitriding treatment. The results showed that plasma nitriding oil pipelines not only had high wear resistance, but also improved the tubing corrosion resistance.[关键词] 油管离子渗氮耐磨性耐腐蚀性能Key words:oil pipelines;Plasma nitriding ;wear resistance;corrosion resistance[中图分类号] [文献标识码][课题项目]本文系武汉市科技攻关项目“大装炉量油管内壁离子渗氮工艺分析与设备研制”(项目编号:201010621230)的研究成果利用大型卧式油管离子渗氮专用设备,对油管进行离子渗氮处理,其内壁表层获得了较为均匀的渗层,表面硬度达到~550Hv,实际使用寿命提高了3倍以上[1]。
活塞环槽加工和强化处理技术”的报告

活塞环槽加工和强化处理技术在内燃机中,活塞的工作条件十分恶劣,要承受高温、高压和冲击载荷。
因此,活塞环槽磨损主要是在使用的过程中,活塞环在活塞环槽内的轴向冲击、径向冲击以及周向的复杂运动会导致配对的摩擦表面严重磨损。
从而造成活塞密封效果和机械效率降低。
所以内燃机工作的可靠性和使用的耐久性很大程度上与活塞环槽的磨损情况有关。
针对活塞活塞环槽磨损这一问题,国内外都采取了一些改善活塞环槽磨损情况的措施。
以下是一些现在国内外正在使用或研究的活塞环槽表面强化处理方法。
一、激光表面淬火激光表面淬火是激光表面改性处理的一种方法,激光改性处理始于上世纪六十年代,但是直到七十年代初第一台大功率激光器研制成功后,激光表面改性处理技术才得到了实际应用,并在近十多年取得了巨大的发展。
这里仅就激光淬火技术做简要说明。
激光淬火是利用高能激光束使金属材料在超快加热和急冷条件下发生相变。
激光淬火从物理冶金角度来讲与常规淬火并无其他的不同之处,只不过是激光淬火是一个急热急冷的过程。
因此激光热处理所得到的材料的硬化层硬度高、强度大。
实践表明:通过激光热处理后的活塞环槽的表面晶粒得到很好地细化并且马氏体高密度位错,从而使活塞环槽表面硬度可达58HRC,使用寿命提高1.5倍以上。
目前德国马勒集团、日本洋马公司均采用激光淬火对活塞环槽进行处理。
激光表面改性处理是一种高新的处理技术,它与其他常规处理技术相比较,既有其独特优点,又有一些不足与局限性。
(1)激光表面改性处理的强化效果好,由于激光表面处理冷却速度快,所以材料的耐磨性和硬度可同时获得提高,表面硬度比常规处理硬化方法可提高15%~20%。
(2)被处理的材料变形小,因为激光加热速度快,所以材料的热影响区小,硬化时变形以及应变都非常小。
一般硬化后无需再加工。
(3)加工速度快、工艺周期短、生产效率高以及容易实现计算机控制。
(4)适用性灵活广泛,对大型零件表面积复杂零件和槽、孔、洞等特殊部位均能适用,并且还可以对零件有选择的进行局部处理。
纳米二硫化钼(MoS2)在润滑材料中的研究进展

纳米二硫化钼(MoS2)在润滑材料中的研究进展摘要:本文介绍了MoS2的润滑性状、纳米MoS2的性能。
对纳米MoS2在轧制液、机械油、铜合金拉拔润滑脂和空间润滑材料中的摩擦学应用与研究现状进行了综述,并对比了微米级与纳米级MoS2在使用中的效果。
对未来纳米MoS2在润滑材料中的应用与研究进行了展望。
关键词:纳米MoS2;润滑材料;摩擦The research progress of molybdenum disulfidenanoparticles(MoS2) in lubrication materialsAbstract: This paper describes the lubricating properties of MoS2and the performance of nano-MoS2. Nano-MoS2on the rolling fluid, mechanical oil, copper alloy drawing grease and space lubrication materials’ tribology applications and research status are reviewed. The micron and nano-level effect of MoS2 in use is compared. Nano-MoS2 lubricating materials application and research in the future are discussed.Key words: nano-MoS2; lubrication materials; friction0 引言二硫化钼(MoS2)用作固体润滑剂已有50多年的历史,是应用最广泛的固体润滑剂。
在相同条件下,含MoS2的粘结固体润滑膜在真空中的摩擦系数约为大气中的1/3,而耐磨寿命比在大气中高几倍甚至几十倍。
固体润滑材料分类

固体润滑材料分类
固体润滑材料主要分为以下几类:
1. 金属润滑材料:如金属滑板、金属涂层等,主要用于高速、高温、高压等环境下。
2. 陶瓷润滑材料:如氧化锆、碳化硅等,具有高硬度、高耐磨性,适用于高载荷、高温度工况。
3. 聚合物润滑材料:如聚四氟乙烯(PTFE)、聚醚酯(PEBA)等,具有良好的自润滑性能,适用于低速、低温、低压等工况。
4. 复合润滑材料:如金属基复合材料、陶瓷基复合材料等,兼具多种材料的优点,适用于特定工况下的润滑。
5. 固体润滑剂:如二硫化钼(MoS2)、石墨等,具有良好的润滑性能,适用于多种工况。
6. 纳米润滑材料:如纳米金属、纳米陶瓷等,具有优异的润滑性能,适用于高速、高温、高压等工况。
7. 生物润滑材料:如润滑脂、动植物油等,适用于生物医学、食品工业等领域。
这些固体润滑材料具有不同的性能和适用范围,可根据实际需求选择合适的润滑材料。
二硫化钼润滑涂层要求

二硫化钼润滑涂层要求一、二硫化钼润滑涂层的概述二硫化钼是一种黑色固体,具有良好的润滑性能。
将二硫化钼应用于润滑涂层中,可以有效降低摩擦系数,减少磨损和热量的产生,提高机械系统的工作效率和寿命。
因此,二硫化钼润滑涂层在工业生产和机械制造中得到广泛应用。
二、二硫化钼润滑涂层的要求1. 涂层厚度要均匀:涂层的厚度应符合设计要求,过厚或不均匀的涂层会影响润滑效果。
2. 涂层附着力要强:涂层应能牢固附着在基材表面,避免剥落或脱落。
3. 涂层表面要光滑:涂层表面应平整光滑,避免表面不平或粗糙导致的摩擦增加。
4. 涂层的硬度要适中:涂层的硬度应与基材相匹配,过硬或过软的涂层都会影响润滑效果。
5. 涂层应具有良好的耐磨性:涂层应能够抵抗磨损和划伤,保持长时间的润滑效果。
6. 涂层应具有良好的耐腐蚀性:涂层应能抵抗腐蚀和化学介质的侵蚀,保护基材不受损。
7. 涂层应具有良好的温度稳定性:涂层应能在高温或低温环境下保持稳定的润滑性能。
8. 涂层应具有良好的压力性能:涂层应能在高压力下保持稳定的润滑效果,防止卡滞或卡住。
9. 涂层应具有良好的耐磨损性:涂层应能承受频繁的摩擦和磨损,延长机械系统的使用寿命。
三、二硫化钼润滑涂层的制备方法1. 化学气相沉积法:通过在高温下将二硫化钼蒸发,使其在基材表面沉积形成润滑涂层。
2. 物理气相沉积法:通过离子轰击或电弧放电等方法,在真空环境中将二硫化钼喷射到基材表面形成润滑涂层。
3. 电化学沉积法:利用电解液中的二硫化钼离子,在电解过程中将其沉积在基材表面形成润滑涂层。
4. 溶液法:将含有二硫化钼的溶液涂覆在基材表面,通过溶剂挥发使其形成润滑涂层。
四、二硫化钼润滑涂层的应用领域1. 机械制造:二硫化钼润滑涂层可以应用于各类机械设备的轴承、齿轮、滚动轴等部件,减少摩擦和磨损。
2. 汽车工业:二硫化钼润滑涂层可以应用于汽车发动机的活塞环、曲轴等部件,提高发动机的工作效率和寿命。
3. 航空航天:二硫化钼润滑涂层可以应用于飞机发动机的叶轮、涡轮等高温高压部件,提供稳定的润滑效果。
GCr15轴承钢低温离子渗硫技术及摩擦磨损性能
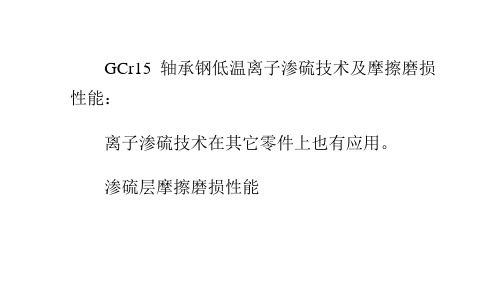
你知道的,我已变了当初与你初相识的面容。我常常会想,你是否和我一样
获得一定厚度的 FeS 层,平均约为 1μm 最大 可达到 3μm 4 渗硫层观察渗硫样品的外表形貌扫描电镜
(SEM 照片 5 所示。GCr15 钢渗硫层外表呈疏松
多孔结构。轴承企业导航
黑色层为表面的渗硫层,渗硫样品的截面形 貌 SEM 照片。与基体有明显的分界线。
1c04f8ca1 轴承隔离器油缸密封
你知道的,我已变了当初与你初相识的面容。我常常会想,你是否和我一样
润滑层,从而改善轴承钢的摩擦磨损性能。 2.低温离子渗流设备 立式离子渗流设备
卧式离子渗硫设备
3.渗硫层结构分析经低温离子渗硫处理试 样的 X 射线衍射分析(XRD 图谱。 结果所示。可见,采用俄歇扫描探针(AES
对渗硫样品表面 FeS 元素沿深度的变化进行分
你知道的,我已变了当初与你初相识的面容。我常常会想,你是否和我一样
发生磨损破坏,从而降低轴承的寿命,影响到机 械设备的正常运行。 达到减摩抗磨的目的其作用原理。FeS 一种
典型的固体润滑资料,使用固体润滑技术可以有
效地提高处于边境润滑状态下轴承抵抗磨损的
性能。轴承型号查询软件 固体润滑技术主要是利用固体润滑薄膜来 改善接触外表之间的润滑状态。利用低温离子渗 硫技术可在保证轴承形状精度及基体强度损失 较小的情况下在轴承资料外表制备一层 FeS 固体
你知道的,我已变了当初与你初相识的面容。我常常会想,你是否和我一样
变化及实时磨损量曲线。整个摩擦磨损试验过程 中,渗硫盘的摩擦系数和实时磨损量都低于原始 盘,表示出优异的减摩抗磨性能。汽车轴承型号 查询
ZnS纳米微粒在润滑油减摩擦上的应用
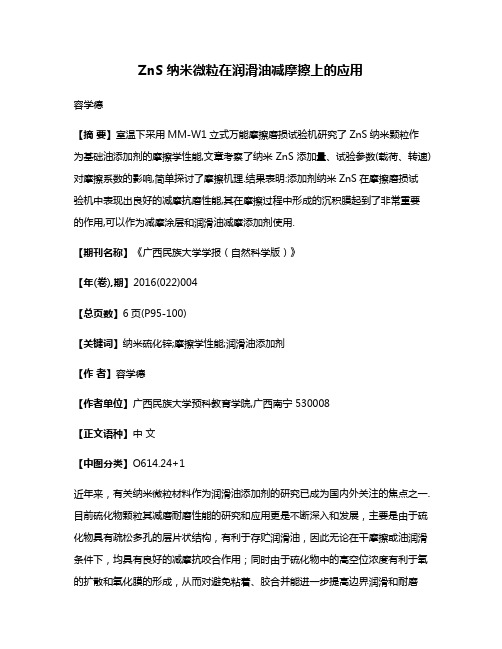
ZnS纳米微粒在润滑油减摩擦上的应用容学德【摘要】室温下采用MM-W1立式万能摩擦磨损试验机研究了ZnS纳米颗粒作为基础油添加剂的摩擦学性能,文章考察了纳米ZnS添加量、试验参数(载荷、转速)对摩擦系数的影响,简单探讨了摩擦机理.结果表明:添加剂纳米ZnS在摩擦磨损试验机中表现出良好的减摩抗磨性能,其在摩擦过程中形成的沉积膜起到了非常重要的作用,可以作为减摩涂层和润滑油减摩添加剂使用.【期刊名称】《广西民族大学学报(自然科学版)》【年(卷),期】2016(022)004【总页数】6页(P95-100)【关键词】纳米硫化锌;摩擦学性能;润滑油添加剂【作者】容学德【作者单位】广西民族大学预科教育学院,广西南宁 530008【正文语种】中文【中图分类】O614.24+1近年来,有关纳米微粒材料作为润滑油添加剂的研究已成为国内外关注的焦点之一.目前硫化物颗粒其减磨耐磨性能的研究和应用更是不断深入和发展,主要是由于硫化物具有疏松多孔的层片状结构,有利于存贮润滑油,因此无论在干摩擦或油润滑条件下,均具有良好的减摩抗咬合作用;同时由于硫化物中的高空位浓度有利于氧的扩散和氧化膜的形成,从而对避免粘着、胶合并能进一步提高边界润滑和耐磨性.[1-2]硫化物中以FeS和MoS2的抗摩耐磨性能的研究应用最为广泛,而纳米ZnS微粒作为润滑油添加剂,它在摩擦物质中间可以隔绝金属的直接接触,且和基体材料的结合力较弱,剪切强度较低,因此,它在提高基础油的减摩耐磨性能方面具有一定的研究价值及应用前景.[3-6]本研究在矿物油中添加不同质量百分数的ZnS纳米粒子,通过在摩擦磨损试验机上的测试试验,考察纳米ZnS添加量、载荷、转速等实验参数对摩擦系数的影响,探究ZnS纳米粒添加到润滑油中后其减摩抗磨的性能和机制,为实现提高摩擦副摩擦学性能的目的做一个有益的探索.1.1 硫化锌纳米粒子的制备以硫化钠和乙酸锌为原料,通过反相微乳液法合成平均粒径约为25 nm的ZnS纳米粒子.这部分实验在我们的前期研究工作已有报道.[7]1.2 硫化锌纳米微粒的减摩性能测试试验选用不含任何润滑添加剂的矿物油作为基础油,将所合成的ZnS纳米粒子作为添加剂添加到基础油中,使用立式万能摩擦磨损试验机测试在不同条件下的摩擦系数,摩擦系数随时间变化的曲线将被自动记录下来.在室温条件和试验室环境下,称取适量的纳米ZnS超声分散(30 min)于基础油中,形成稳定的分散体系,得到纳米ZnS质量百分数分别为1.0%、2.0%和3.0%的复合润滑油样品.实验使用济南试金集团制造的MM-W1立式万能摩擦磨损试验机进行,摩擦磨损实验材料为T10钢,外径35 mm,厚度5 mm,实验测试的摩擦半径为14 mm.测试时间均为20分钟,对比分析各个样品的润滑分别在载荷一定转速不同和转速一定载荷不同的条件下,其摩擦系数的变化,并与未添加纳米ZnS的矿物油进行比照.在转速相同而载荷不同和载荷相同而转速不同的条件下,探究了润滑油中纳米ZnS添加量对摩擦系数的影响.2.1 转速相同、载荷量不同条件下,纳米ZnS添加量对摩擦系数影响2.1.1 150 rpm条件下摩擦系数的变化图1(a)、(b)和(c)给出了在150rpm的相同转速及载荷分别为50 N、100 N和150 N的条件下,纳米ZnS不同添加量的润滑油其摩擦系数随时间的变化关系曲线.图1的结果显示:未添加纳米ZnS的基础油在所试验的时间段内摩擦系数均为最大,此时的曲线振幅最高,波动也较大,而添加了纳米ZnS的样品油其摩擦系数曲线均有不同程度的降低.究其原因,这是纳米ZnS的减摩抗磨作用的结果,由于小尺寸的纳米ZnS微粒在压应力作用下黏附于摩擦表面和沉积于磨损表面微观缺陷区域,渗入到摩擦表面的纳米ZnS形成一层润滑膜,起到减摩抗磨作用.[8]当转速固定为150 rpm时,随着载荷量与添加量的增加,在测试时间内摩擦系数也都较平稳,且摩擦系数呈现出下降的趋势.在50 N的最低载荷下,纳米ZnS质量百分数为1%的润滑油可以更好起到减摩的功效,而当载荷增加至150 N时,添加剂的质量分数为3%才能更好起到降低摩擦系数的作用,显然,在不同工况中,应从实际出发在基础油中添加适量的纳米ZnS润滑剂.2.1.2 200 rpm条件下摩擦系数的变化图2(a)、(b)和(c)给出了在200 rpm的相同转速和不同载荷下,纳米ZnS不同添加量的润滑油其摩擦系数随时间的变化关系曲线.对比图1、图2的试验结果呈现出新的变化趋势,在200 rpm的转速下,添加了纳米ZnS的润滑油其摩擦系数与150 rpm的情况相比呈下降趋势且波动更为平稳.图2的结果还显示,仍然是在载荷较小的情况下,纳米ZnS质量百分数为1%、2%的减摩性能较好,摩擦系数的波动也较小且较平稳,随着载荷的增大,纳米ZnS质量百分数为3%的样品显现了优势,特别是当载荷为150 N时,纳米ZnS含量为3%的样品其摩擦系数下降较明显,起到优势的减摩性能.2.1.3 250rpm条件下摩擦系数的变化在250rpm的相同转速和不同载荷下,不同添加量纳米ZnS的润滑油其摩擦系数随试验时间的变化情况,如图3所示.由图3可知,在250 rpm的相同转度及不同载荷下,纳米ZnS的含量分别为 1%、2%、3%的样品以及未添加纳米ZnS微粒的基础油其摩擦系数的变化总体上仍然呈现前面的规律.通过对比分析图3中的摩擦系数曲线后发现,在250 rpm的较高转动速度下,摩擦系数随载荷增大呈现出先差距明显后逐渐相当的总体趋势,表明了载荷与纳米ZnS添加量对摩擦系数的影响刚好呈相反态势.该转动速度下,摩擦磨损机测试样品油所得的摩擦曲线其波动随着载荷的增加而逐渐减小,实验结果表明,未添加纳米ZnS粒子的基础油其摩擦系数仍是最高,而纳米ZnS添加量为3%的情况突显出了优势.2.2 载荷量相同、转速不同条件下,纳米ZnS添加量对摩擦系数影响2.2.1 50 N载荷条件下摩擦系数的变化图4(a)、(b)和(c)给出了在50 N的相同载荷和不同转速条件下,纳米ZnS添加量与摩擦系数平均值之间的关系.由图4可知,50 N的载荷下,纳米ZnS添加量相同的润滑油样品在3个不同滑动速度下其摩擦系数平均值相差不大,摩擦系数曲线也都较平稳,但均比未添加纳米ZnS的基础油的平均摩擦系数更小,未添加纳米ZnS的基础油在3个滑动速度下的平均摩擦系数接近或略高于0.09,其摩擦系数曲线波动也都较大.通过对试验的平均摩擦系数做进一步的比较后发现,纳米ZnS添加质量百分数为1%、2%和3%时,其摩擦系数比未添加纳米ZnS的情况分别降低了75.62%、73.71%和13%.结果表明,该试验条件下在基础油中添加1%和2%纳米ZnS的样品具有较好的减摩效果.分析认为,滑动速度对摩擦系数的影响除了与摩擦表面是否形成了润滑膜有关之外,还与摩擦温度相关,摩擦系数将随着滑动力所产生的热量对润滑膜、表面层性质和摩擦表面的相互作用的影响而发生变化.[9]2.2.2 100 N载荷的条件下摩擦系数的变化在100 N的相同载荷和不同转速下,纳米ZnS添加量与摩擦系数平均值之间的关系示于图5中.从图5可以看出,添加了纳米ZnS的样品油和不含纳米ZnS的基础油的摩擦系数在100 N载荷下的试验结果与50 N载荷时的情况相比较其变化规律有所不同.载荷从50 N增加至100 N时,添加了纳米ZnS的样品油其摩擦系数随着转速的增加而减小.原因是根据摩擦学理论,在摩擦副表面处于弹塑性接触状态下,实际接触面积与载荷之间存在非线性关系,因此摩擦系数随载荷增加反而减小.[3]如图5所示,未添加纳米ZnS的基础油其平均摩擦系数均在0.1左右,在200 rpm和250 rpm的较高转速下,添加了纳米ZnS的样品油的平均摩擦系数降至约0.045,纳米ZnS含量为1%和2%时的样品油其摩擦性能仍为最好,3%纳米ZnS添加量的样品油其平均摩擦系数略高于1%和2%的情况,但基本相当;与50 N载荷的情况比较而言, 100 N载荷下,3%添加量的摩擦系数曲线下降,摩擦系数平均值也降低,而且3%的纳米ZnS添加量的样品油其平均摩擦系数在100 N载荷下相比50 N载荷时下降了28.5%.实验结果表明,在较大载荷和较高转速下,纳米ZnS添加量对摩擦系数的影响相对减小,但其减摩性能仍有一定的提高.分析认为,载荷的增加使纳米ZnS微粒更容易黏附于摩擦表面和填充摩擦副表面的微坑和损伤部位,起到持续的减摩抗磨作用.2.2.3 150 N载荷条件下摩擦系数的变化图6给出了在150 N相同载荷和不同转速下,纳米ZnS添加量与摩擦系数平均值之间的关系结果显示,进一步增大载荷至150 N时,添加3%纳米ZnS的减摩效果在三个转速下均最好,这与载荷为50 N时摩擦系数情况正好相反.在150 rpm、200 rpm和250 rpm的不同转速下,摩擦系数随着纳米ZnS添加量的增大而逐渐减小,但未添加纳米ZnS的基础油的摩擦系数仍是最大.分析认为,这可能是由于摩擦表面的比压随着载荷的增加而增大,从而使更多的纳米ZnS进入摩擦表面,在载荷正压力的作用下使其黏附在摩擦表面上,起到了如离子渗硫或电解渗硫等减摩处理技术在摩擦表面形成的硫化锌润滑层所起到的减摩抗磨的作用,[6,10]从而使高载荷下的摩擦系数较之低载荷下的摩擦系数小,且出现了润滑油样品其摩擦系数随纳米ZnS添加量的相反变化趋势.在试验的载荷及转速范围内,添加ZnS纳米微粒的基础油其摩擦系数都比未添加纳米ZnS的要小,其摩擦系数曲线波动的幅度也更小,进一步对比摩擦系数曲线及摩擦系数平均值后发现,在100 N载荷和200 rpm转速下的摩擦效果最佳.纳米ZnS添加量为1%和2%的样品油在试验中其减摩效果总体上相对更好,其摩擦系数曲线的波动也较为平稳,但在高载荷和高转速下,纳米ZnS添加量为3%的样品油其摩擦效果显示出了优势.实验研究表明,添加剂纳米ZnS在摩擦磨损试验机中表现出了良好的减摩抗磨性能,在摩擦过程中形成的纳米ZnS润滑膜膜起到了非常重要的作用,可以作为润滑油减摩添加剂使用.【相关文献】[1] 李晓俊, 刘丰, 刘小兰. 纳米材料的制备及应用研究[M]. 山东: 山东大学出版社, 2006.[2] 王海斗, 徐滨士, 刘家浚. 微纳米硫系固体润滑[M]. 北京: 科学出版社, 2009.[3] 张森, 李国禄, 王海斗, 等.硫化物固体润滑剂的研究现状[J]. 润滑与密封. 2012, 37(8): 119-124.[4] Kang Jiajie, Wang Chengbiao, Wang Haidou. Research on tribological behaviors of composite Zn /ZnS coating under dry condition[J]. Applied Surface Science, 2012, 258: 1940-1943.[5] 刘红华. 反胶束法制备纳米硫化锌微粒及其润滑性能[J]. 润滑与密封, 2006 (8): 122-123.[6] 康嘉杰. 复合渗流层的微观组织和摩擦学性能研究[D]. 天津: 河北工业大学, 2008.[7] 容学德, 赵钟兴. 微乳液中纳米ZnS、CdS微粒的合成与表征[J]. 化工技术与开发, 2012, 41(6): 13-15.[8] Hisakado T., Tsukizoe T., Yoshikawa H.. Lubrication mechanism of solid lubricants inoils[J]. Lubric Tech., 1983 (105): 245-253.[9] 温诗铸, 黄平. 摩擦学原理[M]. 北京: 清华大学出版社, 2008.[10] Wang Haidou, Zhuang Daming, Wang Kunlin, et al. Comparison of the tribological properties of an ion sulfurized coatingand a plasma sprayed FeS coating[J]. Materials Science and Engineering, 2003, A357: 321-327.。
低温离子渗硫技术的发展历程和研究应用现状

低温离子渗硫技术的发展历程和研究应用现状低温离子渗硫技术是一种在较低温度下实现离子在材料中渗透并形成硫化物的技术。
该技术的发展历程可以追溯到20世纪80年代初,当时科学家们开始研究在较低温度下实现硫在材料中渗透的方法。
随着研究的深入,低温离子渗硫技术逐渐发展成为一种重要的表面处理技术,并在多个领域得到广泛应用。
在早期的研究中,科学家们主要探索了不同的渗硫方法和温度条件对材料性能的影响。
他们发现,较低的温度可以减少材料的热膨胀和变形,从而提高渗硫过程的控制性和渗透效率。
此外,低温渗硫还可以避免一些高温处理过程中可能导致的材料劣化问题。
随着对低温离子渗硫技术的研究不断深入,科学家们逐渐发展出了一系列高效的渗硫方法。
其中,离子注入、离子涂覆和离子渗透是常用的低温离子渗硫方法。
离子注入是将离子束注入到材料表面,使硫离子渗透到材料中;离子涂覆是将含有硫离子的涂层沉积在材料表面,然后通过热处理使硫离子渗透到材料中;离子渗透是将材料浸泡在含有硫离子的液体中,使硫离子通过材料孔隙渗透到材料内部。
低温离子渗硫技术已经在多个领域得到了广泛的应用。
在材料表面处理方面,低温离子渗硫可以增加材料的硬度、耐磨性和耐腐蚀性。
例如,在航空航天领域,低温离子渗硫可以提高航空发动机部件的耐高温性能和抗氧化能力,延长其使用寿命。
在汽车制造领域,低温离子渗硫可以用于改善汽车发动机部件的耐磨性和耐蚀性,提高发动机的工作效率和可靠性。
除了表面处理,低温离子渗硫技术还可以应用于材料改性和功能化方面。
通过在材料内部形成硫化物相,可以改变材料的结构和性能。
例如,在能源领域,低温离子渗硫可以用于制备高性能的锂离子电池负极材料,提高电池的能量密度和循环寿命。
在光电子器件领域,低温离子渗硫可以用于制备具有特殊光学和电学性能的材料,用于制造光电子器件和传感器。
低温离子渗硫技术经过多年的发展已经成为一种重要的表面处理技术,并在多个领域得到了广泛应用。
随着科学家们对该技术的深入研究和改进,相信低温离子渗硫技术将继续发展并发挥更重要的作用。
张冬-极端环境下的摩擦学问题及解决方法
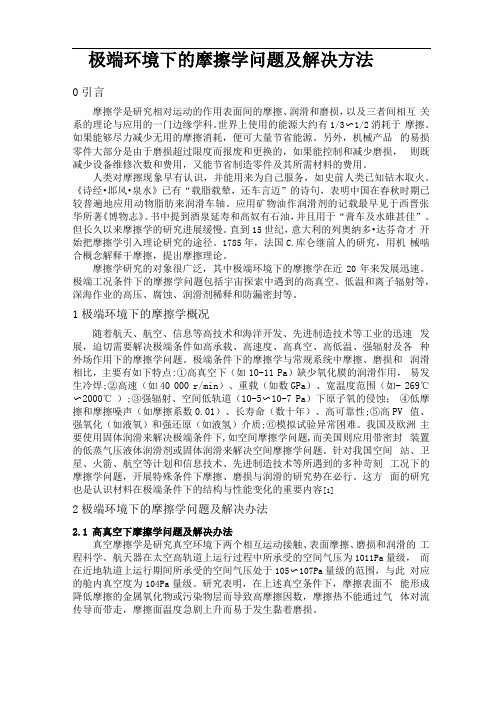
极端环境下的摩擦学问题及解决方法0引言摩擦学是研究相对运动的作用表面间的摩擦、润滑和磨损,以及三者间相互关系的理论与应用的一门边缘学科。
世界上使用的能源大约有1/3〜1/2消耗于摩擦。
如果能够尽力减少无用的摩擦消耗,便可大量节省能源。
另外,机械产品的易损零件大部分是由于磨损超过限度而报废和更换的,如果能控制和减少磨损,则既减少设备维修次数和费用,又能节省制造零件及其所需材料的费用。
人类对摩擦现象早有认识,并能用来为自己服务,如史前人类已知钻木取火。
《诗经•邶风•泉水》已有“载脂载辇,还车言迈”的诗句,表明中国在春秋时期已较普遍地应用动物脂肪来润滑车轴。
应用矿物油作润滑剂的记载最早见于西晋张华所著《博物志》。
书中提到酒泉延寿和高奴有石油,并且用于“膏车及水碓甚佳”。
但长久以来摩擦学的研究进展缓慢。
直到15世纪,意大利的列奥纳多•达芬奇才开始把摩擦学引入理论研究的途径。
1785年,法国C.库仑继前人的研究,用机械啮合概念解释干摩擦,提出摩擦理论。
摩擦学研究的对象很广泛,其中极端环境下的摩擦学在近20年来发展迅速。
极端工况条件下的摩擦学问题包括宇宙探索中遇到的高真空、低温和离子辐射等,深海作业的高压、腐蚀、润滑剂稀释和防漏密封等。
1极端环境下的摩擦学概况随着航天、航空、信息等高技术和海洋开发、先进制造技术等工业的迅速发展,迫切需要解决极端条件如高承载、高速度、高真空、高低温、强辐射及各种外场作用下的摩擦学问题。
极端条件下的摩擦学与常规系统中摩擦、磨损和润滑相比,主要有如下特点:①高真空下(如10-11 Pa)缺少氧化膜的润滑作用,易发生冷焊;②高速(如40 000 r/min)、重载(如数GPa)、宽温度范围(如- 269℃〜2000℃ );③强辐射、空间低轨道(10-5〜10-7 Pa)下原子氧的侵蚀;④低摩擦和摩擦噪声(如摩擦系数0.01)、长寿命(数十年)、高可靠性;⑤高PV 值、强氧化(如液氧)和强还原(如液氢)介质;⑥模拟试验异常困难。
- 1、下载文档前请自行甄别文档内容的完整性,平台不提供额外的编辑、内容补充、找答案等附加服务。
- 2、"仅部分预览"的文档,不可在线预览部分如存在完整性等问题,可反馈申请退款(可完整预览的文档不适用该条件!)。
- 3、如文档侵犯您的权益,请联系客服反馈,我们会尽快为您处理(人工客服工作时间:9:00-18:30)。
从离子渗硫到润滑耐磨梯度材料张弋飞1张昕辉2金康3(1. 北京坚润表面材料研究所,北京 100034 2.北京领异表面材料工程公司,北京 1000343.全国热处理生产力促进中心,北京100083)摘要:从专利、文献的角度分析了离子渗硫技术、设备在冶金、机械等领域的进展和应用情况。
润滑耐磨梯度材料是离子渗硫的发展。
关键词:离子渗硫;梯度材料;润滑;耐磨中图分类号:TG174.444 文献标识码:B 文章编号:1000-3738(200 )0 –00 -0From Ion Sulfurization To Lubrication GradientMaterialZHANG Yi-fei1 ZHANG Xin-hui2 JIN Kang3(1. Beijing Tough &Lubricant Surface Material Inst., Beijing, 100034, China2.Beijing Creative Surface Material Engineering Co.,Ltd,Beijing, 100034, China.3.Productivity Promotion Center for Heat Treatment,Beijing, 100083, China )Abstract: Ion sulfurization technologies & equipment are introduced from the patents And literatures, especially its progress And application in metallurgy And machinery fields. The lubrication wear-resistance gradient material is the development of ionsulfurization technology.Key words: ion sulfurization; gradient material; lubricate;wear-resistance1.引言金属表面的硫化物是机械零件增加润滑,减少磨损的有效物质。
在国外主要用低温电解渗硫(Sulf-BT),获得5~7mm实用性的硫化物减磨表层[1],在日本已经有数条自动化生产线投入生产[2]。
我国有众多的单位进行科研和试生产,但能够工业化生产企业不多。
70年代末,我国已经开始进行通过离子渗硫得到金属表面硫化物的研究。
离子渗硫与离子渗氮的原理相似,在真空室中气压在200~1Pa 之间,有阳极和阴极,阴极上放有被处理工件;在阴阳极间施加直流高压约在300~1500V;真空室中有渗硫气体作为工作气体在辉光放电作用下,产生物理化学反应,硫渗入工件。
80年代我国在冶金、机械等领域开展了离子渗硫的研究。
我们在CNPAT,EPOQUE(WPI,PAJ)、CAPAT数据库中,只检索到一个发明专利,即作者研制的“金属零件表面形成硫化物层的方法和设备”获得7国发明专利权(以下简称“离子渗硫专利”)。
[3] 专利说明书中表明,这既是工艺专利,也是设备专利,实施对象是金属零件。
2.离子渗硫文献分析通过DIALOG数据库的METADEX®、Ei Compendex、Materials 、PASCAL、Industry Abstracts、NTIS、JICST等数据库及国内的万方数据资源系统中各相关数据库检索表明,在冶金机械领域没有国外作者发表有关离子渗硫的文章;国内作者的文章分析如下:2.1 离子渗硫方法不同渗层厚度差异很大1983年,华南工学院肖继闯等以含硫气体作为渗入介质,采用辉光放电离子渗硫工艺。
在4~8Torr,160-200℃保温1~2h,得到5~15μm硫化物层[4]。
用于Cr12钢螺纹帽凹模,在固体渗硼淬火的基础上进行渗硫处理,寿命达10万次(未渗硫处理2.5-3万次);1987、1989年后张敬一等用HS作渗硫气体在560℃保温2h得到50μm渗层,并在柴油机缸套上2应用[5],获得节油效果。
1989、1990年张弋飞相继发表了以固体硫升温气化作为渗硫介质,电压在450~1500V之间,对碳钢、合金钢、铸铁和经过渗碳、渗氮、碳氮共渗零件表面试验,在150~320℃下获得硫化亚铁FeS层。
GCr15及经C-N 共渗的纺织钢领,渗硫层深度达到120μm,使用寿命提高1-3倍[6][7]。
1990年山东大学王永珊等采用含硫气体进行离子渗硫220℃保温得到12μm硫化物层[8]; 1997年清华大学机械系关磊等在W18Cr4V钢氮碳共渗后采用含硫气体离子渗硫220℃保温1h,得到10~12μm的硫化物层[9]。
,且明显增加W18Cr4V钢的耐磨性。
1998年,曲建宝等以20钢渗碳淬火,固体硫作为阴极,硫升温气化进行离子渗硫,层深度为10μm。
[10]为渗硫气体,以工件(铸2001年,华南理工大学黄文波[11]等采用CS2铁)为阳极,在350℃,4h渗硫,得到19μm含FeS渗硫层。
由上述数据表明,渗硫层厚度从5~120μm差别很大。
2.2 金属材料离子渗硫后具有低摩擦系数和高耐磨性所见文献中,渗硫后材料的摩擦系数和磨损量均减低。
在摩擦副双方均有固体硫气化渗硫层时,用30号机油润滑,使灰铸铁的摩擦系数降至青铜的67%,球铁是青铜的56%,45钢是铜合金的33%。
同样,在中等载荷下(P=1.5MPa)渗硫45钢的耐磨性是铜合金的204倍,且45钢经过摩擦试验后,表面粗糙度明显改善。
[6][7][19] 调质45钢渗硫后滚动摩擦系数减低了14%-42%。
[13]在粗糙度相同情况下,车削加工后渗硫比磨削加工后渗硫减磨效果好;硬度越高,摩擦系数越小。
[12] 在低载荷下的微动摩擦性能,离子渗硫层与涂层均具有良好的减磨性能。
[14]磁控溅射MoS245钢渗硫件的抗咬合能力比未渗硫零件提高27倍;渗硫灰铁与渗硫45钢淬火件组成摩擦副的磨损率为铝青铜与45钢淬火件组成的摩擦副的1/15。
[8]3.离子渗硫需要解决的理论与工业化生产的难点虽然离子渗氮已经工业化生产,但离子渗硫的机理仍待解决:其一,原子半径较大的硫在150℃低温如何渗入?其二,按照离子注入的数据,在20万伏电压下,氮注入铁的深度100nm(10-3μm)[15];而在1000V电压下的离子渗硫却大大超过100nm,,离子渗硫深度达20~120μm。
工业化生产的难点:1.根据真空回火炉的情况,工作时要循环通入5300~9300Pa惰性气体,循环风搅拌确保温度均匀性;[30]离子渗硫在200~1Pa,工作温度150~350℃,在辐射与对流均很少的条件下如何均温?2.现在已经工业化冷壁炉中的离子渗氮,表面面积/体积相差较大的工件不能同炉渗氮。
离子加热对于大件(表面面积/体积小)升温慢,相反小件则升温快[16];离子渗硫能够避开着一难题吗?能够象电阻炉一样大小件混装吗?只有解决了以上难点,离子渗硫才能进行工业化生产,而硫如何在低温渗入?渗层厚度为什么大,则有待研究解决。
4.离子渗硫应用离子渗硫已经应用到多种运动零件、机械及部分铜合金产品。
[17][20][21][22][27]4.1 滚动轴承与滑动轴承[6][18][26]应用低温离子渗硫专利的308轴承,22216、53516等多种型号的轧机轴承,使用寿命平均提高100%;部分轴瓦实现了用碳钢代替铜合金。
4.2高速钢刀具[7]低温离子渗硫刀具包括铣刀、滚刀、拉刀、钻头、丝锥等,在切削铸铁、碳钢等工件过程中,刀具的耐用度提高了1-10倍,且被加工件的表面粗糙度有所降低。
4.3 纺纱机钢领[7]钢领是纺纱机上易磨损零件,摩擦副钢丝圈在钢领上以35~40米/秒的速度,干摩擦高速运动。
目前钢领基本上是20钢氮碳共渗后淬火回火。
对于细纱平面钢领、普通棉纺颊钢领、锥面钢领等,经过低温离子渗硫后,使用寿命提高三倍,并减少纺纱的断头率而提高纱的质量。
低温离子渗硫钢领在上海已经使用百万只以上。
5.离子渗硫的发展---润滑耐磨梯度材料离子渗硫方法虽然可形成硫化物表层,硫化物层与金属基材之间的结合强度较以往材料有很大改进,但硫化物层也存在不足:在金属零件表面,硫化物的分布不均匀,即从金属表面到心部硫化物浓度,不是连续的降低,得不到稳定的梯度层,在1999年,文献[23]公开了“润滑耐磨梯度材料”发明专利的国际申请。
该文献指出,如果通入硫并有氧的存在,则金属基材表面形成金属氧化物和金属硫化物,容易地获得稳定的金属硫化物和金属氧化物复合梯度材料,具有良好的润滑和耐磨性能。
当氧化物很少时,也可称为硫化物梯度材料;按照现有的工艺水平,硫化物梯度材料中必然有氧化物。
文献[28]报道,氧化物与硫化物可使承载能力显著提高。
按照传统的观念,硫化物与氧化物在钢中是有害夹杂但硫化物氧化物梯度材料Lubrication Gradient Material(LGM)在表面具有润滑耐磨性,而心部又保持了金属材料固有的强韧性,这种梯度分布提高了零件的综合机械性能[24];最近的研究表明LGM具有高的疲劳性能,这是渗硫层所不具备的。
采用梯度材料LGM制备的工业产品有LGM钢轴瓦、LGM45钢轴承、LGM硬质合金工具等,文献[25]介绍了用润滑耐磨梯度材料制造的干摩擦轴承。
高速线材轧机用的LGM硬质合金轧辊(辊环)在生产中,使用寿命延长50%以上[29]。
柴油机喷油泵中精密零件出油阀座,用LGM45钢代替GCr15;可靠性对比试验已经通过2500小时(JB/751171.1标准)。
日产2.2万件出油阀座的LGM合成设备已经在企业投入使用。