合成氨双塔催化剂升温还原小结
A310QC型合成催化剂升温还原总结
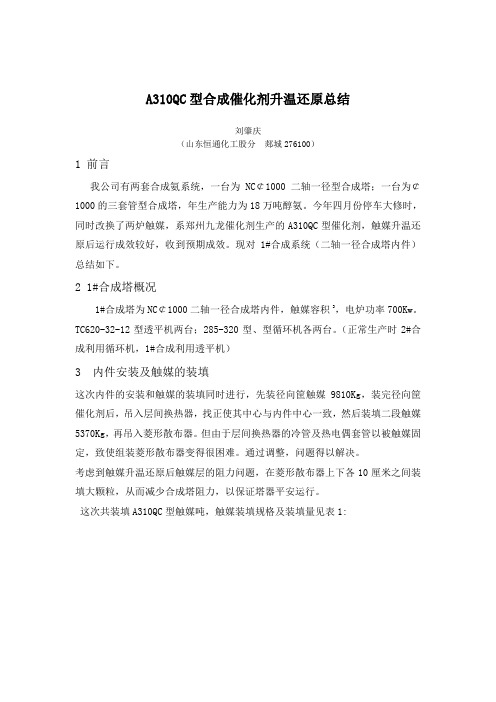
A310QC型合成催化剂升温还原总结刘肇庆(山东恒通化工股分郯城276100)1 前言我公司有两套合成氨系统,一台为NC¢1000二轴一径型合成塔;一台为¢1000的三套管型合成塔,年生产能力为18万吨醇氨。
今年四月份停车大修时,同时改换了两炉触媒,系郑州九龙催化剂生产的A310QC型催化剂,触媒升温还原后运行成效较好,收到预期成效。
现对1#合成系统(二轴一径合成塔内件)总结如下。
2 1#合成塔概况1#合成塔为NC¢1000二轴一径合成塔内件,触媒容积3,电炉功率700Kw。
TC620-32-12型透平机两台;285-320型、型循环机各两台。
(正常生产时2#合成利用循环机,1#合成利用透平机)3 内件安装及触媒的装填这次内件的安装和触媒的装填同时进行,先装径向筐触媒9810Kg,装完径向筐催化剂后,吊入层间换热器,找正使其中心与内件中心一致,然后装填二段触媒5370Kg,再吊入菱形散布器。
但由于层间换热器的冷管及热电偶套管以被触媒固定,致使组装菱形散布器变得很困难。
通过调整,问题得以解决。
考虑到触媒升温还原后触媒层的阻力问题,在菱形散布器上下各10厘米之间装填大颗粒,从而减少合成塔阻力,以保证塔器平安运行。
这次共装填A310QC型触媒吨,触媒装填规格及装填量见表1:表1 触媒装填规格及装填量一轴二轴径向合计:吨3 触媒的升温还原依照内件特点及A310QC型触媒的特点制定了升温还原方案(见表2),采纳分段还原的方式使热点慢慢往下移动。
在上层进行还原时用寒气操纵基层触媒在出水温度以下。
待上层还原完毕,加大空速,加大电炉功率,再利用氨反映热将基层触媒温度提起来,使底部触媒慢慢还原,并确保触媒还原完全。
还原轴向层时,第一把零米温度尽快提到490℃以上,把轴向层上段完全还原,然后慢慢关小冷激阀还原轴向层二段。
当轴向层触媒还原好后加大空速,并慢慢关小层冷阀,利用轴向层反映热将热点移到径向层。
还原径向层时,充分利用还原好的轴向层反映热,必要时提压降低循环氢,尽可能加大循环量,把大量还原水汽带到塔外。
氨合成催化剂升温还原经验总结
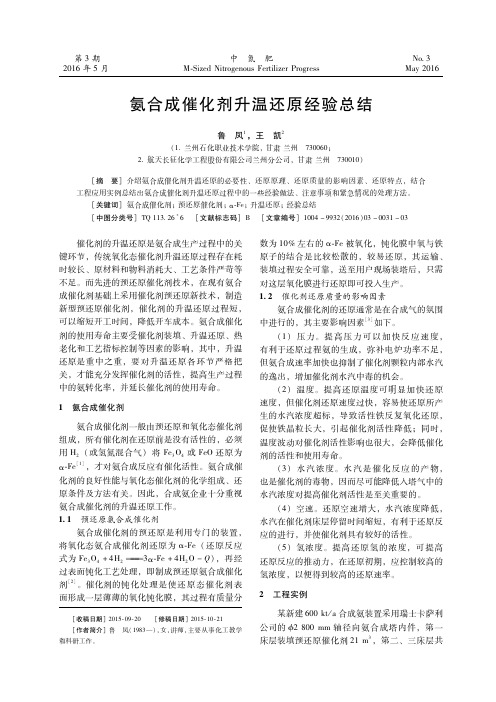
氨合成催化剂的还原通常是在合成气的氛围 中进行的,其主要影响因素[3]如下。
(1) 压 力。提 高 压 力 可 以 加 快 反 应 速 度, 有利于还原过程氨的生成,弥补电炉功率不足, 但氨合成速率加快也抑制了催化剂颗粒内部水汽 的逸出,增加催化剂水汽中毒的机会。
(2) 温度。提高还原温度可明显加快还原 速度,但催化剂还原速度过快,容易使还原所产 生的水汽浓度超标,导致活性铁反复氧化还原, 促使铁晶粒长大,引起催化剂活性降低;同时, 温度波动对催化剂活性影响也很大,会降低催化 剂的活性和使用寿命。
[摘 要] 介绍氨合成催化剂升温还原的必要性、还原原理、还原质量的影响因素、还原特点,结合 工程应用实例总结出氨合成催化剂升温还原过程中的一些经验做法、注意事项和紧急情况的处理方法。
[关键词] 氨合成催化剂;预还原催化剂;αFe;升温还原;经验总结 [中图分类号] TQ11326+6 [文献标志码] B [文章编号]1004-9932(2016)03-0031-03
1 氨合成催化剂
氨合成催化剂一般由预还原和氧化态催化剂 组成,所有催化剂在还原前是没有活性的,必须 用 H2 (或氢氮混合气) 将 Fe3O4 或 FeO还原为 αFe[1],才对氨合成反应有催化活性。氨合成催 化剂的良好性能与氧化态催化剂的化学组成、还 原条件及方法有关。因此,合成氨企业十分重视 氨合成催化剂的升温还原工作。 11 预还原氨合成催化剂
Amomax-10/10H型氨合成催化剂升温还原总结
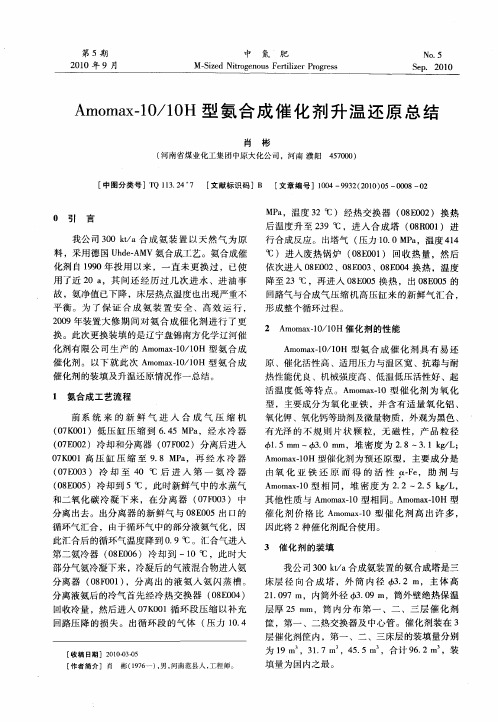
分 离 出去 。出分离 器 的新 鲜气 与 0 E 0 8 05出 口的
循 环气 汇合 ,由于循 环气 中的部分液 氨气化 ,因 此汇合后 的循 环气 温度 降到 0 9℃ 。汇合气 进入 . 第 二氨冷 器 ( 8 0 6 冷 却 到 一1 0E0 ) 0℃ ,此 时 大
催 化 剂 价 格 比 A o a一0型 催 化 剂 高 出 许 多 , m m x1
型 ,主要成 分 为 氧化 亚 铁 ,并 含有 适 量 氧 化 铝 、
催化 剂 。以 下 就 此 次 A o a一0 1H 型 氨 合 成 m m x1/0
催化剂 的装 填及 升温还 原情 况作一 总结 。
1 氨合成 工艺流 程
前 系 统 来 的 新 鲜 气 进 入 合 成 气 压 缩 机 ( 7 0 1 低压 缸 压 缩 到 6 4 P ,经 水 冷 器 0K0 ) .5 M a (7 02 0 E 0 )冷却 和分 离器 ( 7 0 2 分离后 进人 0 F0 ) 0K0 7 0 1高 压 缸 压 缩 至 9 8 M a . P ,再 经 水 冷 器
我 公 司 30k a 成氨装 置 的氨合成 塔是 三 0 t 合 /
床层 径 向合成 塔 ,外 筒 内径 4 . n , 2 i,主体 高 3
2.9 I 107I,内筒外 径 30 ,筒外壁 绝 热保 温 T .9i n
层厚 2 5 mm,筒 内分 布 第 一 、二 、三 层 催 化 剂 筐 ,第 一 、二热 交换器 及 中心 管 。催 化剂 装 在 3
第 5期
21 0 0年 9 月
中 氮
肥
No 5 . Sp 2 0 e . 01
M ie to e o sFe t ie r g e s S z d Ni g n u ri z r P o r s r l
卧式合成塔催化剂的升温还原总结
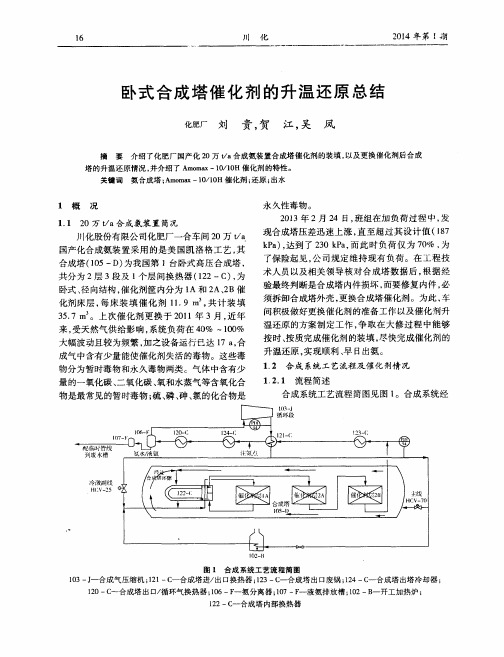
1 . 2 . 1 流程 简述
合成系统工艺流程简图见图 l 。合成系统经
图 1 合成系统工艺流程简图 1 0 3一 J 一合 成气压缩机 ; 1 2 1一c 一合成塔进/ 出口换热器 ; 1 2 3一c 一合成塔 出 口废锅 ; 1 2 4一 c 一合成塔 出塔 冷却 器 ; 1 2 0一c ~合 成塔 出 E l / 循环气换热器 ; 1 0 6一F 一 氨分 离器 ; 1 0 7一 F 一液 氨排 放槽 : 1 0 2一B 一开工加热炉 ; 1 2 2一C 一合 成塔内部换热器
塔 进 出 口热 交换 器 ( 1 2 1一C ) 被加热到 2 7 0 c c, 然
度( T I 一 1 0 4 8 ) 为一 2 6℃, 如果氨冷器 1 、 2级初期 不建液位 , 这时的冷冻温度也大大低于水的冰点 温度 , 会导致水结成冰堵 塞工艺 劁同心导管或损 坏压缩机 , 因此在这个阶段必须启动氨注射泵 向 工艺侧 注 氨 , 从 而达 到提高 冰 点 的 目的。 2 . 2 催 化 剂装 填情 况
l 6
川 I 化
2 0 1 4年 第 i 期
卧式 合成 塔催 化 剂 的升 温 还 原 总结
化 肥 厂 刘 贵, 贺 江, 吴 凤
摘 要 介绍 了化肥厂 国产化 2 0万 t / a 合成氨装 置合 成塔催化剂 的装 填 , 以及 更换催化剂后合成
氨合成塔 ; A m o m a x一1 0 / 1 0 H催化剂 ; 还原 ; 出水
后 的新 鲜 合成 气在 1 0 3一J二段高 压 缸压 缩 后 , 流
合 成塔升 温 还原 时 相 当关 键 , 因 为合 成 塔 催 化剂 在 升温还 原初 期 没 有 氨 生成, 而本 装 置 四级 组合 式 氨冷器 的合 成 气 工 艺 侧 有 8 0 0根 同心 套 管 , 最 低温 度换 热到 一3 3 . 3℃ , 进 氨分 离器 ( 1 0 6一 F ) 温
合成氨触媒双塔还原技术

合成氨触媒双塔还原技术
合成氨系统由于存在两塔操作,双塔还原时带来较大的困难,特别是如果两个塔同时更换触媒,会存在以下几个问题1、循环量不足2、还原速率不一样,温度较难控制3、水汽浓度控制困难4、还原时间长,这也是重点问题,影响经济效益。
为解决这项问题,合成两塔还原过程中,采用一项合理的还原方法,因为该系统使用的是主副塔操作,双塔同时升温,根据电炉能量的最高值,控制最大循环量。
当双塔升至中期大量出水时,对副塔采用恒温操作在400℃-430℃左右,严格控制水汽浓度在 2.0%左右,主塔继续升温并严格控制出水浓度,当进入末期495℃以后,主塔水汽出完,副塔再缓慢提温,在这个过程中,压力继续控制在7.0MP左右,当副塔也升至与主塔同样温度495℃后,水汽全部出完,再提升压力,最大循环量操作至还原结束。
轻负荷后,合成触媒活性效果较好,甲烷达到20%,合成驰放气量大幅降低,大修时间明显缩短,能够做到提前几天加满量,具有较好的经济效益。
TA201―2型含钴合成氨催化剂还原小结-3页word资料

TA201―2型含钴合成氨催化剂还原小结一、合成塔及触媒情况简介合成塔的耐高温高压外筒由南化机制作,高约26.38m、直径2.4m,合成塔内件为从瑞士卡萨利成套进口,该内件采用三床层、两中间换热器的设计,换热器分别位于第一床和第二床之后,最大限度地提高了反应热回收率。
合成塔内件的设计采用了卡萨利专利的“轴径向”催化剂床,保证100%利用催化剂,每一催化剂床层均达到最高效率。
轴径向技术降低了氨合成塔和合成回路阻力,节省了合成气压缩机功耗。
合成触媒采用的是山东临朐泰丰催化剂厂的TA201-2型铁系含钴合成氨触媒,具有如下技术特点:1、堆密度约为 2.7~2.9kg/L。
2、加入氧化钴和其它活性助剂,导致催化剂的晶体结构、表面结构、孔结构的明显变化。
尤其是还原后晶体粒度明显变小,有利于催化剂活性的提高。
3、催化剂的粒度:1.5~3.0mm ,规格均匀,比表面积大。
合成塔第一床层采用预还原型的TA201-2-H型触媒,表面镀上了氧化膜,预还原型触媒可以较快的完成还原,缩短三个床层的总还原时间。
合成塔第二、第三床层装填型号TA201-2的催化剂为氧化态触媒。
具体的装填量,见下表。
合成塔触媒的装填质量密切关系到装置的生产能力,在装填的几个重点环节,我们采用了几个如下的办法,确保了装填的质量:1.设置布制触媒装填斜面,氧化型触媒在高处平台滑下装填斜面过程中,触媒灰由斜面底端的鼓风机吹除,减少了采用振动筛可能造成的触媒被氧化的可能。
2.装填过程中,采用内面光滑的塑胶软管、专门制作的触媒分布器和带有活插板的装填槽机构,在降低装填过程中触媒摩擦的同时,在工具设计上最大限度的保证了触媒能够装填均匀。
3.人工不间断摇动装填圆环和不断测量调整,进一步保证了装填的质量。
二、催化剂的升温还原还原思路:催化剂采用分层还原的办法使热点逐步下移,气量由压缩机和塔后放空阀等控制,热负荷由开工加热炉提供,在满足升温速率的情况下,尽量提高空速。
合成氨催化剂升温还原水汽浓度分析小结
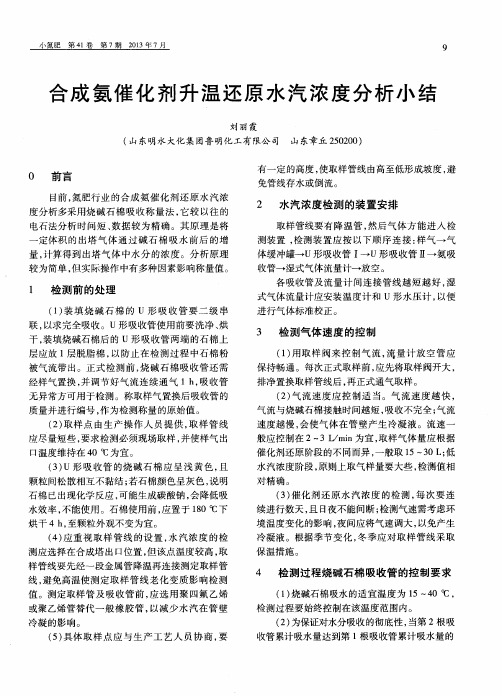
0 前言
为代 替无 烟块 煤 , 太 原 理 工 大 成工 程 有 限公 司和 山西 中元 煤洁 净技术 有 限公 司联合 研究 开发 了 1种 以粉煤 为 原料 的碳 化 型 煤 , 山西晋 煤 天 源 化 工有 限公 司 ( 以下 简称 天 源公 司 ) 承 担 了该 碳 化 型煤 的试 烧 工 作 。试烧 结 果 表 明 : 碳 化 型煤 可 完 全替代 无 烟块 煤 作 为 固定 层 间 歇 气化 的原 料 ,
气流与烧碱石棉接触时间越短 , 吸收不完全 ; 气流 速度 越慢 , 会使 气 体 在 管 壁 产 生冷 凝 液 。 流速 一
般 应控 制在 2~ 3 L / a r i n为 宜 , 取 样气 体 量应 根 据 催 化剂 还原 阶段 的不 同而 异 , 一 般取 1 5~ 3 0 L ; 低 水 汽浓 度 阶段 , 原则上 取气 样量 要 大些 , 检 测值 相 对 精确 。 ( 3 ) 催 化 剂 还 原 水 汽 浓 度 的检 测 , 每 次要 连 续 进行 数天 , 且E t 夜不 能 间断 ; 检 测气 速需 考虑 环 境 温度 变化 的影 响 , 夜 间应将 气 速调 大 , 以免产 生 冷 凝液 。根据 季 节 变 化 , 冬 季 应对 取 样 管 线 采 取
或聚 乙烯 管替 代 一般 橡 胶 管 , 以减 少 水 汽 在 管 壁
冷凝 的影 响 。
4 检测过程烧碱石棉 吸收 管的控 制要求
( 1 ) 烧碱石棉吸水的适宜温度为 1 5— 4 0℃,
合成氨催化剂卸装及升温还原总结

该公司采用卡萨利装填技术 ,利用催化剂高
度 落差 ,用专 用 的催化 剂装 填喷 头装 填 。此方 法 不需 振动 就能 达到所 需 的装 填密 度 ,有效 地提 高 了催 化剂 的装 填速 度 和质 量 ,而且 避 免 了振荡 装 填过 程 中振 动 棒 损 坏 催 化 剂 筐 和 引 起 催 化 剂 粉 碎 。塔顶 固定一 放料 斗 ,料 斗下部 接 有 4根带 钢 丝橡胶 管 ,每根 管 的下端 接 有 1 锥 型喷 头 ( 个 喷
剂筐损 坏 事故 的发生 。 2 催 化剂 的装填
化。在煤气量 7 0 ~7 0 3h时 ,即使将 50 O 80 0m / 合 成氨 系 统 弛放 气量 加 到最 大 ( 0 O 20 0 儿 0 ~1 0
m3h ,合 成 系统 仍 经 常超 压 放空 ,合 成 氨 产 量 /) 偏 低 。鉴 于此 ,决 定更 换催 化剂 。
环系统、供给人体呼 吸的空气 系统 ) ,我公 司只 提供 焊 接 各种 支 架所 需 的材 料 和 60m3h的氮 0 /
气 。将合 成 塔 与 系 统 隔离 ,氮气 从 塔 底 向 上 反 吹 ,用来 补充循 环 氮气 的损 失 。 该公 司采 用干 法卸还 原态 催化 剂技术 。大盖 打开 后 ,拆 除合 成 塔 内件 ,用 棉 白布保 护好 密封 面及 塔 内外壁 环隙 ,用球 胆塞 实冷 激人 口,用 苫 布将 塔顶 盖好 ,确保 塔 内为 氮气正 压 ,氧含量 < 05 ( 4h分 析 1次 ) .% 每 ,防止 还 原态催 化 剂遇 氧气发 生燃 烧 。启动 真空 抽 吸系统 ,将真 空抽 吸 管插入 催 化 剂 床 层 ,保 持 真 空 度 在 0 0 a .4MP , 抽出 的催 化 剂 储 存在 1个 45m3的 储 存 罐 中 , . 储 存罐 架高 41。当储存 罐 中的催 化 剂积 累 到一 I T
氨合成催化剂还原小结

第 5期
杨
瑾 :氨合 成催 化 剂还原 小 结
・ 9・ 2
部 又装 填 了 大 颗 粒 预 还 原 态 催 化 剂 ,装 填 量 0 1 ,装填 高 度 02m。 氧化 态 催 化 剂 是 河 南 .5t .
使水 汽浓度 不致 过高 。上 床层 温度 在 20 时水 2
汽浓 度 已达到 29 2×1 一,3 0~4 0℃ 开始 出 4 0 8 0
骏化催化剂厂生产 的 A 1- 302型氨合成催 化剂 , 粒 径在 1 5— . m;预还原 态催 化剂 是南 京南 . 3 0m 化公 司生 产 的 A 1 —H 型 氨 合 成 催 化 剂 ,小 颗 10 1
[ 中图分 类号]T 1.4 7 [ Q 132 文献标识码 ]B [ 文章编号] 10 9 3 (0 2 0 0 2 0 0 4— 92 2 1 )5— 0 8— 2
我产 能 力 为
6 ta 0k/ ,氨 合 成 塔 内件 原 采 用 瑞 士 卡 萨 利 公 司
第 5期 21 0 2年 9月
中 氮
肥
No 5 .
M— i d N t g n u e t ie r g e s S z i o e o sF ri z r P o r s e r l
S p. 2 2 e t 01
氨 合 成 催 化 剂 还 原 小 结
杨 瑾
1 14 ) 6 0 1 ( 黑龙江黑化集 团有 限公 司 ,黑龙江 齐齐 哈尔
被 冷却至 5 8℃ ,然后 去水 冷 器进 一 步冷 却 到 3 5 ℃ 以下 ,经 氨 分 离 器 分 离 掉 液 氨 后 进 5 2循 环 1 机 ,补充 压力 后开 始下一 个循 环 。
情 况作一 介 绍 。
氨合成催化剂升温还原方案

JR型合成塔A202氨合成催化剂升温还原方案
1、氨合成岗位试压和置换结束后,向高压系统充氨50~100Kg(3~5g/Nm3)。
锅炉应在氨合成升温前开始通蒸汽煮废锅,并在升温还原期间,控制好温度,充分利用余热,减轻电炉负荷。
2、温度升到120℃排水一次,200℃时开启水冷器上水阀,250℃时氨冷器开始加液氨,并控制气氨压力,380℃以上每小时排水一次,380℃开始做水汽浓度,430℃以上每半个小时排一次水。
3、进入还原主期时,补气阀保持常开,用塔后放空阀控制系统压力,CH4≥4%时开大塔后放空阀,同时开大补气阀确保系统压力稳定。
4、水汽浓度尽可能控制在2.5~3.0mg/L,并参考出水量控制升温速度,出水量大、水汽浓度较高时应恒温。
是否提温以水汽浓度和出水量为准。
5、当循环机跳闸急停时,立即紧急切断电炉,开大塔后放空阀,关闭补气阀;循环机开车恢复送气后,即可开电炉,缓慢提升电炉电流、电压,恢复升温还原前的工况。
6、当电炉跳闸时,立即开大系统近路和循环机近路阀,关补气阀和塔后放空阀;电炉恢复送电后缓慢提升电流、电压,视温升趋势关小系统近路和循环机近路阀,直至恢复停电前的原工况。
7、催化剂还原结束条件:(1) 水汽浓度连续2小时≤0.2mg/L。
(2) 底部温度提到460℃以上,恒温6~10小时即可降温转低负荷生产。
8、在还原过程中,以高空速、高氢、高电炉功率和低氨冷温度、低压、低水汽浓度的“三高三低”原则执行。
9、由于此次还原循环量不够,在进入还原主后期时,要根据情况及时、逐渐增压。
附:A202型触媒ø1000内冷绝热型氨合成塔升温还原计划表
生产部
2012.11.17。
贵州宜化2#合成塔内件修复总结

贵州宜化2#氨合成塔检修经验总结贵州宜化公司:唐祥、徐黔贵州宜化“8.29”事故后,公司进行了大修工作,大修期间更换了2#合成塔(φ1200)的触媒。
检修结束后进行升温还原工作,当此步骤结束在加量生产时发现塔壁超温严重,最高温度达到了220℃,随即进行了单系统停车检修合成塔内件。
在检修过程中发现合成塔内部保温材料有局部脱落,出现空洞现象。
更为严重的是发现塔内件筒体局部变形严重,最高达20mm。
随后经开会讨论进行了一系列的校直、校圆、校正检修工作。
现把经验总结如下:一、对使用5年以上合成塔内件在更换触媒时,无条件进行保温材料及塔内件是否变形的检查工作。
二、物资准备1、保温不锈钢薄板,δ=1.5mm,材质为304,价格:30元/kg,数量根据需更换数量而定,但要考虑修理过程中的部分损坏,还要考虑一定余量。
2、保温石棉布,δ=3mm,价格:12元/kg,耐温800~1000℃,面积数量为2倍不锈钢薄板(要包两层)。
3、铁丝,规格为14#;铁丝网,普通保温铁丝网,价格2.1元/平方米。
4、紧绳器,数量:4套,最大作用力为4吨,价格为260元/套。
5、千斤顶,数量:4台,最大作用力为100吨,价格为2360元/台。
三、检修过程1、用卷扬机或吊车吊出合成塔内件保证直立铅锤于地平面,并保证随时可上下移动。
在内件上部以法兰处为基准,在东南西北各点焊一根钢筋,然后进行悬挂铅锤线检查凹陷或变形处,并详细记录所得尺寸。
2、制作校正工具,材料选择普通钢板,厚度为50mm,外径为φ1900,内径为φ1400。
把内件套入此工具内,然后对变形处用千斤顶、大锤进行校直校正。
3、校直校正完成后再用铅锤线进行检查核实无误后进行保温恢复,保温石板布包2层,先用铁丝进行固定,再用铁丝网进行再一步加固,下一步进行包扎不锈钢保温薄板(薄板先用卷板机卷好,并把周长尺寸定准),用紧绳器配合小钢丝绳箍紧贴实保温不锈钢薄板,并采用氩弧焊进行满焊。
氨合成塔催化剂升温还原方案

氨合成塔催化剂升温还原方案氨合成铁触媒通常均以氧化态形式存在(FeO、Fe2O3),而其只有在α-Fe状态下才具有活性,起到催化作用,因此在利用前必需将氧化铁还原成α-Fe,且还原质量的好坏将直接阻碍其利用寿命及企业的经济效益,必需严格依照还原方案进行操作,确保催化剂还原质量。
一、还原方程式及理论出水量一、方程式:FeO+H2=Fe+H2O+QFe2O3+H2=2Fe+3H2O-Q二、理论出水量:3、气体流程循环机出口的气体经油分分离油水后,分成三股:第一股10%的环隙气从下部沿内外筒环隙进入塔上部,从塔顶引出,与热交的热气体汇合后约30-35%再进入冷管制。
第二股5%左右零米冷激气从上部进入合成塔上部,用来调剂合成塔上部温度。
第三股,被塔外热互换器加热到170-200℃、约65-70%的主线气体进入合成塔下部的换热器管内,气体加热到360-410℃,经中心管进入触媒层表面。
通过第一绝热层反映后,气体温度达到460-470℃,与段间冷却器出来的气体在混合散布器内混合,温度降到400-430℃,进入径向框与内筒的环隙向下,从圆周方向径向流向径向筐Ⅰ中部的换热器。
气体通过换热器外壳进入管间,气体从换热器管间上部折流向下,温度降至310-340℃出塔。
出塔气经废热回收器进热互换器管内(下进上出)温度90℃,进入水冷却器,水冷出来的气体降温到40℃,进入冷凝蒸发分离器(1)气体进冷凝器管内,再进氨蒸发器管内,进分离器,分离氨后的气体经导气管从分离器底部引来,再进冷凝蒸发分离器(2),气体进冷凝器关键,再进氨蒸发器管内,出氨蒸发器的气体,与补气油分来的新鲜气汇合,经分离器分离氨后,通过氨蒸发器的中心管进入上部冷凝器的管内,从冷凝蒸发器(2)的冷凝器管内出来的气体在进入冷凝蒸发分离器(1)的冷凝器的管间,冷却进入管内的水冷后的热气体,本身温度提高到25℃以上进入循环机,开始新的一轮循环。
二、还原前的预备工作一、各分析仪器齐全,水汽浓度取样管,出水掏出点接管畅通。
合成氨催化剂升温还原技术在化工中的应用

合成氨催化剂升温还原技术在化工中的应用我们知道,合成氨是化学工业中的一种重要反应,而这个过程的核心就是催化剂。
今天,我们要聊的就是合成氨催化剂升温还原技术在化工中的应用。
我们要明白,催化剂在合成氨的过程中起到的是什么作用。
合成氨的反应式是N2+3H2→2NH3,这是一个需要能量的反应,而催化剂就是帮助这个反应快速进行,降低反应所需的能量。
那么,催化剂的还原是什么意思呢?还原,就是指物质失去氧原子或者获得电子。
在合成氨的过程中,催化剂需要通过还原,才能发挥出最大的效果。
而这个还原的过程,就是升温还原技术。
升温还原技术,简单来说,就是通过升温,让催化剂中的金属离子失去氧原子,恢复其活性。
这个技术在合成氨的工业生产中,起到了至关重要的作用。
升温还原技术可以提高催化剂的活性。
催化剂的活性,是指催化剂在单位时间内催化反应的能力。
催化剂经过升温还原后,其活性会得到显著提高,从而提高了合成氨的反应速度。
升温还原技术可以延长催化剂的使用寿命。
催化剂在反应过程中,会逐渐失去活性,而升温还原技术可以恢复催化剂的活性,使其重新焕发活力。
这样,催化剂的使用寿命就会得到延长。
升温还原技术可以提高合成氨的产率。
催化剂的活性提高了,合成氨的反应速度就会加快,从而提高了产率。
总的来说,合成氨催化剂升温还原技术在化工中的应用,不仅可以提高催化剂的活性,延长使用寿命,还可以提高合成氨的产率,对于化工产业的发展,具有重要的意义。
然而,升温还原技术并不是没有缺点。
比如,升温还原过程需要消耗大量的能源,而且升温过程中,催化剂可能会发生结构变化,影响其活性。
因此,如何在保证催化剂活性的同时,降低能源消耗,就是合成氨工业中需要解决的问题。
总的来说,合成氨催化剂升温还原技术在化工中的应用,是一种重要的技术手段。
虽然存在一些问题,但随着科技的发展,我们相信这些问题都会得到解决。
合成氨催化剂升温还原技术在化工中的应用,将会越来越广泛。
合成氨催化剂升温还原技术在化工中的应用,是一项关键的技术。
氨合成塔内件和催化剂更新及运行总结

成 塔 ,具有 催化 剂床 层 温度分 布较 能接 近最 佳操 作 温度 线和 操 作 稳 定 的 特 点 ,故 决 定 采 用 ⅢJ D -
2. 2 0 0 0型 4 ,1 6 0 0 m m 氨 合 成 塔 内件 由 1 套 直形 异径 径 向冷管束 、2台 气体 混 合 分 布器 和
[ 收 稿 日期 ]2 0 1 6 — 0 9 — 1 4
另外 2股约 8 % 的冷气 作 为 调节 床 层 温度 用 气直 接 人 塔 。其 中 ,零 米 冷 激 气 进 入 第 一 轴 向 层 ,层 间冷激气 进 入第一 径 向层 。
[ 作者简介 ]郭金森 ( 1 9 7 2 一) , 男, 工程师 , 福建三钢 ( 集团) 三 明化工有限责任公司技术科副科长。
役 已超 过 1 0 a 。2 0 1 6年 3月 系统 大 修 期 间 ,对
透平 机来 的 循 环 气 分 为 4股 进 塔 。 一 股 约
3 0 %的气体直接进入段间冷却器 ( 冷管柬) 。这 股气 体 由两部 分组 成 :一部 分冷气 通 过冷 副 阀 由
塔 下部进 入 氨合成 塔外 筒 与 内件 间 的环 隙 ,由下
第 2期 2 0 1 7年 3月
中 氮
肥
No . 2
M— S i z e d Ni t r o g e n o us Fe r t i l i z e r P r o g r e s s
Ma r .201 7
氨 合 成 塔 内件 和 催 化 剂 更 新 及 运 行 总 结
而上 ,在塔顶 部 引 出 ;另一 部分是 塔 外热交 换 器 加热 的 未反应 冷气 ,该 冷气 通过 热副 阀后 与环 隙
4 4 , 1 6 0 0 m m 氨合成 塔 系统 进行 改 造 ,更 换 了氨
B206型低变催化剂还原总结

B206型低变催化剂还原总结童刚刘志四川美丰化肥分公司我公司现有合成氨生产能力为450kt/a,变换系统由100kt/a、200kt/a等多套组成,本文主要介绍年产20万吨合成氨系统低变催化剂的升温还原情况,供同行参考。
年产20万吨合成氨系统是由成达化学工程公司设计,属该档规模的第一套完全国产化装置,即以天然气为原料,采用两段蒸汽转化法造气,高低温变换、低热耗的改良热钾碱法脱碳、甲烷化工艺、14.0MPa(G)压力下合成氨。
该系统于2005年7月24日点火开车,8月1日即产出合成氨,创下了该装置本阶段的最好成绩。
为稳妥起见,本系统仍选用南化催化剂厂(现安格公司)生产的B206型低变催化剂。
为缩短全系统的开车时间,杜绝传统的以中变气作为升温介质的弊端,采用氮气作为载气单独对低变催化剂进行循环升温还原(以老系统甲烷化气作为H2源)的办法,并取得了圆满成功。
1.工艺概况1.1工艺简介制氮机生产的纯度达99.8%以上的氮气,压力0.65MPa,送入联压机空气二段入口,二段出口气进入开工加热炉管程,经与锅炉送来的2.5MPa蒸汽间接换热,达到低变炉升温还原所需温度后进入低变炉,再经甲烷化水冷器及分离器返回到联压机空气二段入口,进行循环升温。
还原介质为甲烷化气,压力为2.2MPa,从低变炉进口补入。
低变炉入口温度控制有两种方法:一是载气部分不走加热器,直接进入低变炉,用副线控制;一是在蒸汽压力稳定的前提下,调节蒸汽的温度以控制载气温度。
工艺流程如下:1.2低变炉概况本系统的高低温变换炉设计为上下两个重叠而成,上部为高变炉,下部为低变炉,公称直径均为DN3200,低变炉筒体高度为6150mm,设备进气口设有气体分布器,出气口设有集气器,触媒框未分层,沿径向约45°的角线方向上设有5只测温热电偶(TI211~TI215)。
2.催化剂的装填及还原2.1催化剂装填先在底部装Φ50耐火球,装至离标线100处,然后再装入Φ25耐火球至标线并在其上放二层筛网(GF2W16.0/1.6和GF2W2.0/0.63各一层)。
合成氨双塔催化剂升温还原小结

合成氨双塔催化剂升温还原小结
刘海成
【期刊名称】《河南化工》
【年(卷),期】2006(23)4
【摘要】在合成氨生产中,分别采用分层升温还原法、整体升温还原法对Φ1 000和Φ 800氨合成塔同时进行升温还原,详述了其升温还原控制过程.
【总页数】3页(P33-34,46)
【作者】刘海成
【作者单位】洛阳骏马化工有限公司,河南,宜阳,471600
【正文语种】中文
【中图分类】TQ113.266
【相关文献】
1.五万吨/年合成氨装置低变催化剂升温还原总结 [J], 张超博
2.合成氨催化剂升温还原水汽浓度分析小结 [J], 刘丽霞
3.合成氨催化剂卸装及升温还原总结 [J], 李桂颖
4.合成氨催化剂高压升温还原及评价 [J], 侯树文;窦文清
5.Kt51-9型甲醇合成催化剂升温还原小结 [J], 任庆伟;徐广才;姚剑锋
因版权原因,仅展示原文概要,查看原文内容请购买。
氨合成双塔串并联技术应用总结

氨合成双塔串并联技术应用总结(河北东光化工有限责任公司徐希江、黄志宏)摘要:河北东光化工有限公司对700t/d氨合成系统进行增产节能改造,采用南京国昌化工科技有限公司“氨合成双塔串并联工艺技术”,改造后装置产能增加以及节能降耗效果明显。
本文介绍了该项目改造概况、工艺改造流程和运行情况。
关键词:氨合成技术改造串并联应用1概况我国国民经济的发展表明,化肥在农业中所占的地位越来越重要,需求量也逐渐增加,很多化肥企业正在扩大或准备扩大生产能力,以满足市场需求和提高企业市场竞争力。
河北东光化工有限责任公司(以下简称东光化工)目前一套2009年7月投产的φ2000氨合成系统生产能力为日产700吨,2012年初开始筹备对该系统挖掘生产潜力、通过增产进一步实现节能降耗,最终形成年产24万吨合成氨能力。
2012年4月,东光化工经充分调研,选择采用南京国昌化工科技有限公司(以下简称国昌公司)开发的“氨合成双塔串并联工艺技术”(以下简称“串并联工艺”),对原有φ2000氨合成系统进行增产节能改造,即在原有氨合成塔后,合成废锅前串入一台GC型φ2000轴径向氨合成塔,原来各设备的工艺条件基本不变。
改造仅增加一台氨合成塔和一台循环机,其它设备均利用原有合成系统的设备,体现了投资省、建设周期短、见效快、占地面积少的特点。
并委托国昌公司进行改造部分的工程设计和GC 型轴径向氨合成塔内件的设计制造。
2串并联工艺流程串并联工艺流程如图1所示:改造后整个系统中需要增加10个阀门V1-10,2个8字盲板。
(1)串联运行合成塔部分流程简述循环机油分(S1001)出口管线分三路,分别进入1#合成塔环隙冷却塔壁、2#合成塔环隙冷却塔壁(新增PG1101)、塔前换热器与出塔气换热。
塔前换热器冷气出口进入1#合成塔反应出口~300℃进入2#合成塔继续反应,~350℃出口进入废锅副产蒸汽。
串联流程阀门的控制:阀门V1、V2、V3、V5打开,V4、V6-10关闭,盲板1关闭,盲板2打开。
A310QC型合成触媒升温还原总结

A310QC型合成触媒升温还原总结刘肇庆(山东恒通化工股份有限公司郯城276100)1 前言我公司有两套合成氨系统,一台为NC¢1000二轴一径型合成塔;一台为¢1000的三套管型合成塔,年生产能力为18万吨醇氨。
今年四月份停车大修时,同时更换了两炉触媒,系郑州九龙催化剂有限公司生产的A310QC型催化剂,触媒升温还原后运行效果较好,收到预期效果。
现对2#合成系统(三套管合成塔内件)总结如下。
2 2#合成塔概况2#合成塔为并流三套管式合成塔内件,触媒容积 5.0m3,电炉功率700Kw。
DZW-3.5/285-320型、ZDZ-5.5-1.6/285-320型循环机各两台。
3 触媒的选用及装填3.1 本次选用郑州九龙催化剂公司生产的A310QC型触媒。
触媒颗粒以¢4.0~¢6.7为主,共装填触媒15360Kg。
3.2 触媒的装填根据¢1000塔内件的结构特点,我厂在选择装填触媒时,主要遵循以下几条原则:一是考虑到应尽可能减小阻力,选择了颗粒相对较大的球型触媒,二是考虑到触媒层的高低温区及不同位置触媒还原的难易。
具体装填方案见下表1:型号粒度(mm)数量(kg)桶数(桶)A310QC 6.7-9.4 90 3A310QC 4.0-4.74350145A310QC 4.7-5.55970199A310QC 5.5-6.7 3330 111A310QC 6.7-9.4 1410 47A310QC 9.4-13210 7钢球φ16200合计:15360kg4 触媒的升温还原4.1 升温还原方案根据内件特征及A310QC型触媒的特点制定了升温还原方案(见表2)。
说明:490℃恒温结束前热点温度均指零米温度。
4.2触媒的升温还原过程2007年5月7日0:30开电炉加电开始升温还原,升温至120℃时试放物理水,5月7日16:00升温至345℃试放化学水,5月7日16:25升温到353℃,分析合成塔出口水汽浓度为0.55g/m3,以后每30分钟分析一次水汽浓度。
- 1、下载文档前请自行甄别文档内容的完整性,平台不提供额外的编辑、内容补充、找答案等附加服务。
- 2、"仅部分预览"的文档,不可在线预览部分如存在完整性等问题,可反馈申请退款(可完整预览的文档不适用该条件!)。
- 3、如文档侵犯您的权益,请联系客服反馈,我们会尽快为您处理(人工客服工作时间:9:00-18:30)。
%
pH 值 mo l/L mo l/L mo l/L
10. 26
0. 0984 0. 0855 - 0. 0089
碘 10. 27 标 10. 29 液 10. 09 1 10. 27
10. 28
碘 10. 28
标 液
10. 28
2 10. 28
0. 2
0. 04 0 0. 2
0. 04 0
11. 25
温度在 340 e 时, 触媒已开始还原, 并有水明显 出现, 视出塔水汽浓度调整循环量, 以 5 e / h的速 率升温至 400 e , 如水汽浓度高可放慢速度或恒温, 升温时间 12 h。当热点温度升至 400 e 后, 触媒已 明显出水, 调整循环量, 以 3~ 4 e / h的速 率升至 420 e , 升温时间 6 h。调整循环量以 2~ 3 e / h的 速率升至 450 e , 当温度在 430 e 时, 已有大量出水 现象, 出塔水汽浓度极易超标, 在此期间, 应绝对避 免温度有较大幅度的波动, 温度的调节幅度及波动
升温期间, 应保持同平面温差在 10 e 以内, 轴 向温差在 100 e 以内, 若有超标, 采取恒温措施, 待 达到指标后再继续升温。
2. 2. 2 还原初期 调整循环量, 以 20 e /h的速率升温至 340 e ,
升温时间 2 h。控制指 标: 氨冷 温度: - 10~ 0 e , H 2: \ 75% , 压力 6. 0 MP a, 出塔 水汽 浓度 [ 2 g / Nm 3, 同时冷凝塔、分离器要定期错开排水。 2. 2. 3 还原主期
由于双塔内件塔型不同, 所采用的还原方法也 不 同 , 5 10 0 0氨 合 成 塔 采 用 分 层 升 温 还 原 法 , 5 800氨合成塔采用整体升温还原法。 2. 1 5 1 000氨合成塔升温还原控制过程
采用高氢、低压、高空速的快速升温还原法。第 一层升温还原时, 二、三、四层分别用 1# 、2# 、3# 冷激 阀控制其温度不高于 250 e , 一层还原后, 二、三、四 层按顺序逐层进行, 整个还原时间约 110 h。 2. 1. 1 升温期
注: 以不加 N a2 CO3 的 N a2 S2O3 溶 液标定 出的 碘溶液 的 浓度为基准, 计算绝对差值。
在配制 N a2 S2 O3 溶液时加入少量 N a2 CO3, 虽然 抑制了 N a2 S2 O3 的分解, 但却影响了碘量法的反应 条件, 使计算碘溶液的浓度偏离了真实值。而采用 碘量法的分析项目均需要以碘标液的准确浓度参与 计算, 因此 N a2 S2 O3 溶液中加入少量 N a2 CO3, 使标
要控制指标: 压力 8. 0~ 12. 0 M Pa, H 2: 70% ~ 75% , 连续三次分析水汽浓度不大于 0. 1 g /Nm3 时, 可视 为升温还原结束。
2. 1. 5 降温和轻负荷生产 还原结束后, 缓慢减掉电炉, 通过副阀、三个冷
激阀和循环量调节使一、二、三、四层温度分别以 5 e / h的速率降温到 465 e ? 5 e , 转入轻负荷生产。
收稿日期: 2006- 02- 21 作者简介: 刘海成 ( 1975- ) , 男, 助理工程师, 从事合成氨技术开发和管理工作, 电话: ( 0379) 68856265。
# 34#
河南化工 H ENAN CHEM ICA L INDUSTRY
2006年 第 23卷
于 35 e 时, 冷排通水。 2. 1. 2 还原初期
e , 10 h, 2 e / h; 460~ 470 e , 10 h, 1 e / h; 470 e 恒温。还原 54 h, 调 节 2# 冷 激阀使 第三层 触媒由 250 e 开始升温, 升温速率 50 e / h, 升温 2 h至 350 e 后, 各升温速率、所需时间同上, 升至 470 e 恒温。 还原 65 h, 调节 3#冷激阀使第四层触媒由 250 e 开 始升温, 以 50 e / h的速率升温 2 h升至 350 e 后, 各升温速率、所需时间同上。温度升至 460 e 时恒 温。
1 主要设备规格配置
1. 1 5 1 000氨合成塔系统 氨合成塔: 5 1 000 , YD型内件, 催化剂管容积
为 6. 5 m3, 列管式换 热器, 电炉功率 750 kW; 冷凝 塔: 5 800, 高 10 314 mm; 氨冷器: 5 1 500, 高 8 746 mm, 换热面积 220 m2; 后置锅炉: 5 1 800, 长 5 955 mm, 换热面积 70 m2; 水冷器: 套管式冷排管, 换热面 积, 309 m2; 分离 器: 5 800, 高 5 147 mm; 循环机: TC450 /320- 13Ò型透平机一台, 512循环机一台。 1. 2 5 800 氨合成塔系统
氨合成塔 : 5 800, 均温型内 件, 催化剂管容积 3. 2m3, 列管式 换热器, 电炉功率 550kW; 冷凝塔 : 5 800, 高 10 314 mm; 氨 冷器: 5 2 148, 高 4 870 mm, 换 热面积 110 m2; 氨分离 器: 5 700, 高 4 800 mm; 水冷器: 套管式冷排管, 换热面积 337 m2; 循环 机: 两台 N3. 6循环机。
电炉预热干燥后, 缓慢给电炉加负荷, 逐渐加大 循环量, 调整循 环量, 升 温速 率 50 e / h 升 至 300 e , 升温时间 6 h。加足电炉负荷, 关死系统近路, 加 大循环量, 循环量用 2# 小车近路调节, 在调整过程 中应注意电炉安全打气量。
当触媒层温度升至 100 e 时, 应密切注意各测 温点的变化情况, 如有异常, 迅速联系仪表人员进行 处理, 同时视 仪表 情况 升温 速率 应稍慢。升温 至 200 e 时, 冷凝塔、分离塔开始试放水, 热点温度在 250 e 时, 定期分析出塔和入塔水汽浓度, 在此期间 氨冷器开始缓慢加氨, 塔出口温度 \ 35 e 时, 冷排 通水。
10. 88 7. 33 11. 25 10. 88 7. 33
0. 0985 0. 0857 - 0. 0087 0. 0988 0. 0860 - 0. 0084 0. 1035 0. 0921 - 0. 0023 0. 1142 0. 0944
0* 0. 1144 0. 0943 0. 09875 0. 0951 - 0. 0094 0. 1035 0. 1029 - 0. 0016 0. 1144 0. 1045 0*
第一层进入还原主期, 调节循环量, 升温速率不 大于 2 e /h, 升温 13 h至 470 e , 恒温 15 h, 调整循 环量, 以 1 e /h的速率升温 10 h至 480 e 恒温。
还原 38 h后, 通过调节 1#冷激阀使第二层触媒 以 50 e /h升温至 350 e , 然后按以下所需时间及 升温速率进行: 350~ 400 e , 5 h, 10 e /h; 400~ 450
(下转第 46页 )
# 46#
河南化工 H ENAN CHEM ICA L INDUSTRY
2006年 第 23卷
N a2 CO 3 含量的实验数据得以证实, 结果详见表 1。
表 1 同一碘标液由 0. 1 m o l/L 的 N a2 S2 O3 溶液标定结果
日期 c( N a2CO3 ) 溶液 c( N a2 S2O3 ) c( I2 ) 绝对差
第 4期
刘海成: 合成氨双塔催化剂升温还原小结
# 33#
适
合成氨双塔催化剂升温还原小结
用
技
术
刘海成
( 洛阳骏马化工有限公司 , 河南 宜阳 471600)
摘 要: 在合成氨生产中, 分别采 用分层升温还原法、整体 升温还原 法对 5 1 000和 5 800 氨合成塔 同时进 行升温
还原, 详述了其升温还原控制过程。
两个氨合成塔系统共用精练气总管, 通过精练 气分配阀向双系统导入精练气进行合成氨反应。循 环机可通过联通阀相互切换配置, 实现双系统可分 和可合性, 保证了生产的连续稳定。
2 催化剂的升温还原
5 1 000氨合成塔装填郑州九龙催化技术有限
公司生产的 A310型球 状氨合成催化 剂 18. 7 ;t 5 800氨合成塔装填驻马店催化剂厂生产的 A110无 定型氨合成催化剂 9. 3 t。 2005年 3月 27日 11时 准备工作就绪后, 开启透平循环机、电炉, 对 5 1 000 氨合成塔催化剂升温还原; 4 h后开启 N3. 6循环机 及 550 kW 电炉, 对 5 800氨合成 塔催化剂升温还 原 。5 1 00 0氨合 成 塔 预 计 总 还 原 时 间 需 1 10 h, 5 800氨合成塔预计还原时间为 85 h。
电炉经预热干燥后, 缓慢加负荷, 同时逐渐调整 循环量, 使触媒温度以 50 e / h的速率升到 250 e , 计 5 h。升温期间副线阀、三个冷激阀、系统近路阀 均应关死, 升温开始后, 根据需要和要求逐渐加大电 炉负荷和循环量调节温度, 当温度升至 100 e 时, 注 意检查各测温点温度有无异常, 若有异常应联系仪 表人员进行处理, 当温度升至 200 e 时, 冷凝塔、分 离器试放水。当温度升到 250 e 时, 通知中心化验 室定期分析入塔、出塔水汽浓度。入塔水汽浓度每 小时测定 1次, 出塔水汽浓度每半小时测定 1次, 同 时氨冷器加氨使氨冷温度在 0~ 5 e , 当合成塔出口 温度为 150 e 时, 后锅加软水, 当后锅出口温度不低