7.63米焦炉上升管系统自动化系统及案例分析(内部工程师培训)
武钢7.63m焦炉推焦车走行控制系统的分析

武钢7.63m焦炉推焦车走行控制系统的分析杨光摘要:7.63m焦炉是德国伍德公司设计开发的,代表了世界大型焦炉炼焦技术的最高水平,它与国内焦炉的机车自动控制系统显著的区别就是自动控制精度最高,功能完善,网络功能最强大。
本文结合焦化炼焦三分厂7.63m焦炉的现场实际生产工作,对推焦车自动走行控制系统进行了分析。
关键词:7.63m焦炉,走行控制,自动定位1.概述7.63米焦炉是目前亚洲炭化室高度最高、单孔炭化室容积最大的焦炉。
武钢7.63米焦炉从德国Ude(伍德)公司引进,焦炉机车系统由德国Schalker 公司设计,该焦炉拥有先进的炼焦工艺技术,代表了当今世界炼焦工艺技术发展的方向,集中了炼焦工艺、焦炉机械、焦炉自动控制等方面的先进技术,具有国际领先水平。
2座焦炉分别于2008年3月和6月建成出焦,同年10月焦炭产量达到设计能力。
在高强度连续作业下,实现焦炉安全、稳定生产,减少乃至杜绝操作事故和设备事故,是炼焦生产和管理必须解决的问题。
推焦车的走行是在与炼焦炉平行的导轨上横向移动。
在我国,各大型炼焦生产厂大多是操作人员凭借视觉和经验确定推焦车是否到位和是否对中,往往会出现推焦车滞后或者超前指定的炉号,造成频繁操纵主令控制器、减速器频繁起停,液压抱闸频繁开启,使动力设备的安全性降低、使用寿命缩短。
所以利用PLC实现推焦车自动走行控制,对焦炉的安全生产和提高生产管理水平有着十分重要的意义。
2.武钢7.63m焦炉推焦车电气系统组成及工作模式2.1 武钢7.63m焦炉推焦车电气控制系统整个控制系统以西门子S7-400OLC为主站。
经过Profibus-DP工业现场总线把分布式I/O装置,如ET200M和ET200L、6ES70变频器、MTS线性位移传感器和EB342接口模块、推焦和平煤行程编码器以及称重模块等连接成Profibus-DP 主从网络。
由PLC程序完成设备的顺序控制、自动位置控制、速度控制及现场装置的数据采集等。
7.63米焦炉上升管气控箱结构说明(工程师培训)
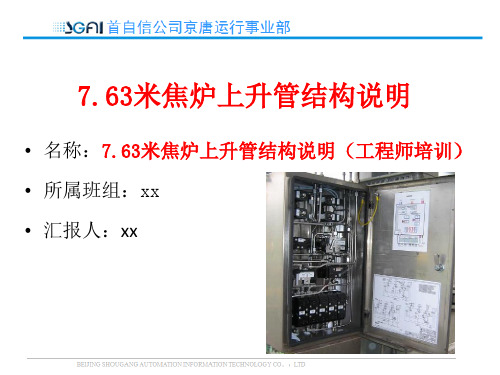
• 名称:7.63米焦炉上升管结构说明(工程师培训) • 所属班组:xx • 汇报人:xx
2*2*1.5 ZRDJYVP
11 +
12-
83 +
84-
2*1.5 ZR-
DJYVP
1+ 2-
设备自带 10米线
上升 上升 管盖 管盖
4*1.5 ZR-KFFP
AI
DI
DO
1 2 3 4 5 6 7 8 9 10 11 12 13 14 15 16 17 18 19 20 21 22 23 24 25 26 27 28 29 30
DCS压 力调节
AO
DCS活 塞杆位 置反馈
AI
10*1.5 ZR-KFFP
10*1.5 ZR-KFFP
10*1.5 ZR-KFFP
5OPห้องสมุดไป่ตู้21106
54-70#
48-70#
5OPR21107
注意:2AI和AO同用10X1.5的线缆,因AI部分点不在同一柜内,因此接线应注意 此线部分需分开接至不同柜内
201x年x月于xx班
10X1.5mm²
10X1.5mm² 10X1.5mm²
2AI
AO
4DO
4DI
柜子号
1-6#
1-23#
1-23#
5OPR21102
7-23#
1-23#
5OPR21103
24-29# 24-47#
24-47#
5OPR21104
30-47#
24-47#
5OPR21105
48-53# 48-70#
48-70#
设备已接好 设备已接好
马钢7.63m焦炉炭化室、上升管结石墨的原因分析及处理

马钢7.63m焦炉炭化室、上升管结石墨的原因分析及处理王明月1包向军1陈光1钱虎林2张峰1(1.安徽工业大学能源与环境学院,2.马鞍山钢铁股份有限公司煤焦化公司)摘要马钢煤焦化新区采用7.63m大型现代化焦炉,目前在生产过程中,炭化室炉墙、上升管根部等处结石墨严重,影响了焦炉的正常生产运行。
文章重点分析了结构参数、操作参数对结石墨的影响,并通过上升管石墨样品分析得出上升管石墨主要是荒煤气中烃分解产物以及沉积在上升管耐火砖壁面的煤尘和焦油的结焦产物。
此外,从减少石墨生成、防止石墨粘结和定期清理石墨三个方面给出了石墨治理的献。
关键词石墨原因分析石墨治理Cause analysis and treatment of graphite bondingof 7. 63m coke oven chamber and ascension pipe in MasteelWang Mingyue1Bao Xiangjun1Chen Guang1Qian Hulin2Zhang Feng1(1 Anhui University of Technology,2 Maanshan Iron and Steel Co. ,Ltd.)Abstract L arge m od ern coke oven (7.63m high)w as used in th e n ew coal coking plant of M asteel.I n th e curren t p rod u ction process,th e adhesion of graph ite is very seriou s especially in th e coke o vencham ber wall,th e ro o t of th e ascension pipe,etc.This afects th e n orm al operation of coke oven.Hence,th e influence of stru ctu ral param eters an d operatin g p aram eters o n th e adhesion of graph itew ere analyzed em phatically.The analysis of graphite sam ples of th e ascension pipe sh o w s th at th egraph ite is m ainly t h e decom position of hyd rocarbon s in th e gas,also th e coking product of coal d u stan d tar d eposited on th e w all of th e ascension pipe refractory bricks.I n graph ite treatm en t fro m th e th ree aspects of reducing graph ite production,preventing an d regularly cleaning graph ite w ere p u t forw ard.Keywords graph ite causes analysis graph ite treatm en t马钢焦化新区采用从德国伍德公司引进的 7.63m焦炉设备工艺,配备P R O vn煤气冷却系 统。
焦炉上升管余热回收利用系统的应用及运行效果

焦炉上升管余热回收利用系统的应用及运行效果【摘要】焦炉上升管余热回收利用系统是一项重要的能源回收技术,可以有效地提高能源利用效率和降低生产成本。
本文介绍了焦炉上升管余热回收利用系统的工艺原理、系统组成、运行效果评价、应用案例和节能效果分析。
通过对该系统运行效果的评价和应用案例的分析,可以看出该技术在工业生产中具有重要的应用价值。
节能效果分析显示,焦炉上升管余热回收利用系统能够显著减少能源消耗并降低碳排放。
总结了该系统的重要性并展望了未来的发展前景。
焦炉上升管余热回收利用系统的不断完善和推广应用将为工业生产带来更多的节能效益,对于推动可持续发展具有重要意义。
【关键词】焦炉,上升管,余热回收利用系统,应用,运行效果,工艺原理,系统组成,评价,应用案例,节能效果分析,重要性,未来发展前景,总结1. 引言1.1 焦炉上升管余热回收利用系统的应用及运行效果焦炉上升管余热回收利用系统被广泛应用于焦化行业,其运行效果备受关注。
通过对余热的回收利用,可以有效提高能源利用效率,减少能源消耗,降低生产成本,实现节能减排的目标。
焦炉上升管余热回收利用系统还能改善环境质量,减少对大气环境的污染,符合可持续发展的要求。
在实际应用中,焦炉上升管余热回收利用系统能够有效提高热能的利用率,延长设备的使用寿命,提高生产效率。
通过科学设计和优化操作,系统可以实现较高的热效率,达到节能减排的效果。
系统运行稳定可靠,保障了工业生产的正常进行,为企业创造了经济效益和环境效益。
焦炉上升管余热回收利用系统在实际应用中取得了显著效果,有利于提高工业生产的可持续发展水平,实现经济效益和环境效益的双赢。
未来,随着技术的不断进步和应用经验的积累,焦炉上升管余热回收利用系统的应用前景将更加广阔,为推动工业节能减排、实现可持续发展作出更大贡献。
2. 正文2.1 工艺原理焦炉上升管余热回收利用系统的工艺原理主要是通过将焦炉排放的高温废热经过余热回收系统进行回收利用。
7_63m焦炉建设调试过程中的技术分析
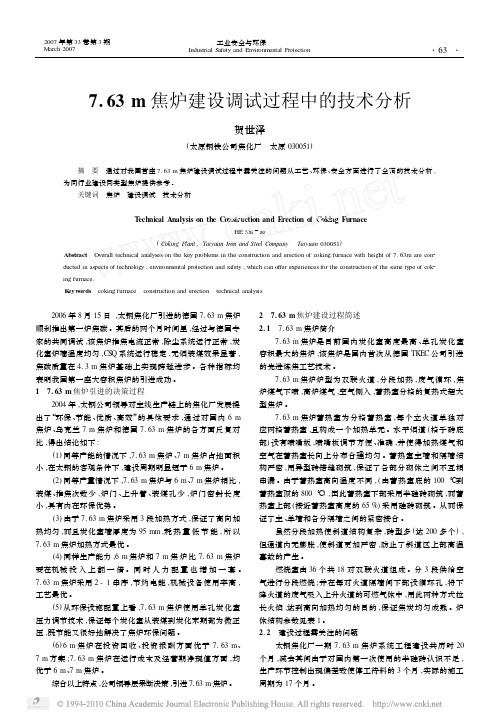
7.63m焦炉建设调试过程中的技术分析贺世泽(太原钢铁公司焦化厂 太原030051) 摘 要 通过对我国首座7.63m焦炉建设调试过程中需关注的问题从工艺、环保、安全方面进行了全面的技术分析,为同行业建设同类型焦炉提供参考。
关键词 焦炉 建设调试 技术分析T echnical Analysis on the Construction and E rection of Coking FurnaceHE Shi ze(Coking Plant,Taiyuan Iron and Steel Company Taiyuan030051)Abstract Overall technical analyses on the key problems in the construction and erection of coking furnace with height of7.63m are con2 ducted in aspects of technology,environmental protection and safety,which can offer experiences for the construction of the same type of cok2 ing furnace.K eyw ords coking furnace construction and erection technical analysis 2006年8月15日,太钢焦化厂引进的德国7.63m焦炉顺利推出第一炉焦碳。
其后的两个月时间里,经过与德国专家的共同调试,该焦炉推焦电流正常,除尘系统运行正常,炭化室炉墙温度均匀,CS Q系统运行稳定,无烟装煤效果显著,焦碳质量在4.3m焦炉基础上实现跨越进步。
各种指标均表明我国第一座大容积焦炉的引进成功。
1 7.63m焦炉引进的决策过程2004年,太钢公司领导对主线生产链上的焦化厂发展提出了“环保、节能、优质、高效”的具体要求,通过对国内6m 焦炉、乌克兰7m焦炉和德国7.63m焦炉的各方面反复对比,得出结论如下:(1)同等产能的情况下,7.63m焦炉、7m焦炉占地面积小,在太钢的客观条件下,建设周期明显短于6m焦炉。
7.63米大型焦炉工艺设备及维护知识讲解和分析(内部工程师培训资料)

7.63米大型焦炉工艺设备及维护知
识讲解和分析
编写:王XX
审核:X志X
校对:XX伟
2011.8.8
一、交换机系统(R ESEVERING SYSTEM) (5)
1、交换机系统概述 (5)
2、交换机动作流程简介 (6)
3、导致交换机停止的因素 (7)
3.1、温度开关信号 (8)
3.2、液位开关信号 (9)
3.3、煤气加热时,板前后压力因素 (9)
3.4、废气压力因素 (9)
3.5、手动切断阀信号 (9)
3.6、油压信号 (10)
3.7、加热时间监控 (10)
3.8、油缸移动超时,及链条断裂 (10)
3.9、压力表故障 (13)
4、交换停机后如何启动及典型故障分析 (13)
4.1、什么是交换机停机 (13)
4.2、交换机停机如何复位启动 (14)
4.3、典型故障分析 (14)
4.3.1故障现象1 (14)
4.3.2、故障现象2 (21)
4.3.3、故障现象3 (24)
5、对于安全DO模块A3.5的几点说明 (27)
6、液压部分的连锁 (32)
6.1、交换机液压部分概述 (32)
6.2、C8液压缸溜缸典型故障分析 (33)
6.3、液压缸内部是否有窜油现象 (36)
7、交换机典型故障汇总 (37)
7.1、2009年4月日22日A炉交换机停机 (37)
7.2、2009年5月22日A炉夜间停机 (40)。
7.65米焦炉主工艺介绍(内部工程师培训)
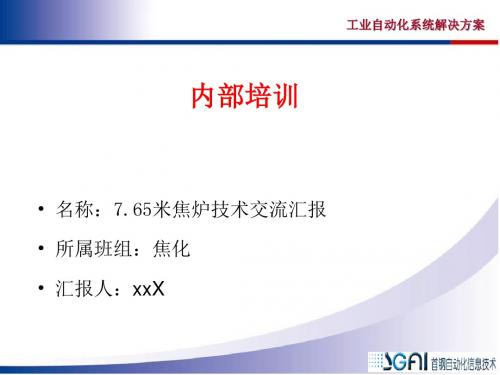
液压交换机系统
工业自动化系统解决方案
上升管系统
工业自动化系统解决方案
上升管系统概述
工业自动化系统解决方案
• 京唐钢铁公司焦化作业部的焦炉采用炉压调节技术( 针对焦炉各阶段对炭化室压力的不同要求提出的一套 完整的解决方案。在炼焦过程中,使炭化室压力维持 在一定范围内,可以有效抑制由炼焦过程中生成的荒 煤气而引起的炉压变化对炉体的损害;在炼焦结束进 行推焦过程时,为避免空气进入集气管产生爆炸危险 ,必须将炭化室与集气管隔离;在装煤时,为防止烟 尘外溢对环境造成污染,要实现负压装煤,即使炭化 室压力小于大气压力。
焦炉煤气加热
工业自动化系统解决方案
双联火道下喷式
焦炉煤气加热
斜道
分格蓄热室
混合煤气加热
工业自动化系统解决方案
液压交换机系统
工业自动化系统解决方案
工业自动化系统解决方案
工业自动化系统解决方案
交换机系统不管是用焦炉煤气加热还是用混合煤气加热,都是每20分钟红管/绿 管换向一次。 ①、焦炉煤气加热红向换绿向加热时液压缸动作顺序: C1红向液压缸关闭→除碳空气吹扫30s→C2红向空气小盖关闭→C3绿向空气小 盖打开→C4由红向换到绿向→加热暂停时间→C5绿向液压缸打开 ②、焦炉煤气加热绿向换红向时液压缸动作顺序: C5绿向液压缸关闭→除碳空气吹扫30s→C3绿向空气小盖关闭→C2红向空气小 盖打开→C4由绿向换到红向→加热暂停时间→C1红向液压缸打开 ③、混合煤气加热红向换绿向加热时液压缸动作顺序: C6红向液压缸关闭→除碳空气吹扫30s→C4由红向换到绿向→加热暂停时间 →C7绿向液压缸打开。 ④、混合煤气加热绿向换红向加热时液压缸动作顺序: C7绿向液压缸关闭→除碳空气吹扫30s→C4由绿向换到红向→加热暂停时间 →C6红向液压缸打开
焦炉上升管余热回收利用系统的应用及运行效果

焦炉上升管余热回收利用系统的应用及运行效果【摘要】焦炉上升管余热回收利用系统是一种重要的能源利用设备,可以有效地利用焦炉生产过程中产生的余热,实现能源的循环利用。
本文首先介绍了此系统的构成和工作原理,接着通过实际案例分析展示了系统在工业生产中的应用效果。
运行效果评价和能源节约效益分析显示,该系统具有显著的节能效益,并有助于降低生产成本。
进一步的系统改进和优化也被提出,以进一步提高系统的运行效率和节能性能。
结论部分展望了焦炉上升管余热回收利用系统在未来的发展前景,总结了系统的优势和不足,并提出了未来可能的改进方向。
通过本文的介绍和分析,可以更好地了解焦炉上升管余热回收利用系统的应用及运行效果,为相关领域的研究和实践提供参考。
【关键词】焦炉上升管、余热回收利用系统、系统组成、原理、应用案例分析、运行效果评价、能源节约效益分析、系统改进、优化、前景展望、总结、展望。
1. 引言1.1 焦炉上升管余热回收利用系统的概述焦炉上升管余热回收利用系统是指利用焦炉上升管在高温高压条件下产生的余热,通过相应的设备和技术手段进行回收利用,以达到节能减排的目的。
焦炉上升管是焦炉的重要部件,是焦炉热能的主要来源之一,能够提供大量的工业余热。
焦炉上升管余热回收利用系统主要包括余热回收设备、余热转换装置、余热回收管道等组成部分。
通过余热回收设备将焦炉上升管产生的余热转化为其他形式的能量,如电能或热能,从而实现能源的有效利用。
这不仅可以降低企业的能源消耗,减少环境污染,还可以降低生产成本,提高企业竞争力。
在当前国家对节能减排的政策和要求下,焦炉上升管余热回收利用系统已经得到广泛应用,并取得了显著的经济和环境效益。
通过系统的应用,不仅可以实现能源的高效利用,还可以提升企业的可持续发展能力。
焦炉上升管余热回收利用系统具有重要的意义和发展前景。
2. 正文2.1 系统组成及原理焦炉上升管余热回收利利用系统,主要由余热回收装置、余热转换装置、余热利用设备以及控制系统组成。
7.63米焦炉荒煤气放散点火系统工艺设备及维护知识讲解和分析(工程师培训)

7.63米大型荒煤气放散点火系统工艺设备及维护知识讲解和分析(内部工程师培训资料)编写:王XX审核:X志X校对:XX伟2011.8.87.63米大型荒煤气放散点火系统工艺设备及维护知识讲解和分析(内部工程师培训资料) (1)三、BLEEDER放散系统 (2)1、荒煤气点火放散系统的工艺原理 (2)2工艺流程 (2)3、案例分析 (3)3.12010.9.4A炉的西段放散管在下过雨后不正常放散 (3)3.22010.9.4C炉的西部放散管测试没有电火花 (4)三、BLEEDER放散系统1、荒煤气点火放散系统的工艺原理XX企业焦化作业部的7.63米大型焦炉的上升管通过鹅型管与集气管相连,集气管则通过三段吸气管连接到鼓风机,由鼓风机产生吸力将炼焦时产生的荒煤气吸到煤气净化区域进行相应处理。
每段吸气管上装有一个电液执行器,其对应的集气管上的装有三块压力表,每段集气管上配有两套Bleeder 放散系统,每套系统包括现场控制面板、声光报警器、点火电极、气缸、热电偶、气动阀、电磁阀等设备构成2工艺流程吸气管上的电液执行器,与其对应的集气管上的三块压力表(量程-600Pa~600Pa)进行PID调节,用来控制该段集气的总压力。
该段集气管的最终压力算法为:三块压力表示数两两作差,取差值最小的两个示数,于其中示数最小的作为最后集气管的压力。
这样取压力值的好处是避免由于单个压力表故障或波动过大而造成信号不准确。
当焦炉压力保持在-300 Pa~-200Pa之间时(推焦时整段集气管保持-300Pa左右,整段集气管装煤完毕后结焦压力保持-200Pa左右),焦炉集气管压力在正常生产的范围之内,此时放散塔和集气管联接的翻板受气缸趋动处于关闭状态,氨水管道由气动阀控制打开形成水封液面,防止荒煤气逸出,蒸气管道关闭。
当整段集气管压力不在正常调节压力范围内时,Bleeder放散系统就会根据现场压力值的变化而依次进行的放散动作:当集气管压力达到放散报警值时,现场的声光报警器开始报警,当压力达到放散警戒值时,氨水管道由气动阀控制执行关闭命令,放散塔和集气管联接的翻板受气缸趋动执行打开动作,此时高压电弧点火装置启动,在放散塔顶部形成高压电弧,引燃荒煤气,8秒后气动切断阀控制蒸汽通入塔内,此为一个放散塔放散过程,如果该段集气管打开一个放散塔进行荒煤气放散,仍不恢复正常的集气管压力值,就要启动第二个放散塔一同执行放散动作,直到达到正常生产的压力值为止。
7.63米焦炉调火汇编(一)

7.63米焦炉调火汇编(一)1.7.3炭化室压力调节各炭化室压力的调节是通过一个PROven装置实现的。
如上图,在集气管内对应每孔炭化室桥管末端安装一个形状象皇冠的管,皇冠管上开有多条沟槽,同时桥管下端设有一个“固定杯”,杯内设有由执行机构控制的活塞杆及与其相连的杯口塞,同时在桥管设有压力检测与控制装置。
炭化室压力调节是由调节杯内的水位也就是荒煤气流经该装置的阻力变化实现的。
其操作原理如下:两个喷嘴喷洒的氨水流入杯内,测压压力传感器将检测到上升管部位的压力信号及时传到执行机构的控制器,控制器发出指令执行机构控制活塞杆带动杯口塞升降,调节固定杯出口大小来调节杯内的水位,使炭化室压力永远保持在微正压状态。
水位越高,沟槽开度越小,荒煤气导出所受阻力越大;水位越低,沟槽开度越大,荒煤气导出所受阻力越小。
在装煤和结焦初期,炭化室产生大量荒煤气使压力增高,此时压力控制装置通过执行机构,活塞杆将杯口塞提升,使固定杯下口全开。
桥管内喷洒的氨水全流入集气管,在杯内不形成任何水封,使大量荒煤气以最小阻力导入集气管,炭化室内压力不致过大。
而在结焦末期,压力控制装置通过执行机构,活塞杆使杯口关闭,大量氨水迅速充满固定杯,形成阻断桥管与集气管的水封,以维持炭化室的正压。
在结焦过程中则可通过压力控制装置自动调节固定杯内的水封高度,从而实现对炭化室内煤气压力的自动调节,防止因超压而造成的炉门泄漏。
推焦时,炭化室需要与集气管隔绝,以免将空气吸入集气管,这时活塞达到最低位置,大量氨水迅速将固定杯充满,同时关闭皇冠管的沟槽,切断了荒煤气的通道。
为了减少冲满固定杯的时间,或在风、电中断时达到完全隔绝的目的,应快速打开注水阀,与此同时,上升管打开装置自动打开上升管盖,将多余荒煤气放散。
要求用冲洗液冲洗固定杯,以关闭“皇冠”管中的沟槽,活塞达到最低位置即可完成此项任务,为减少冲入固定杯时间,也为防止停风、停电,需要打开快速注水阀。
人工操作:使用气动控制操作面板,把气缸停止在最低极限位置,打开快速注水管,将固定杯注满,可使集气管与炭化室隔绝。
7.63米焦炉上升管系统自动化系统及案例分析(内部工程师培训)
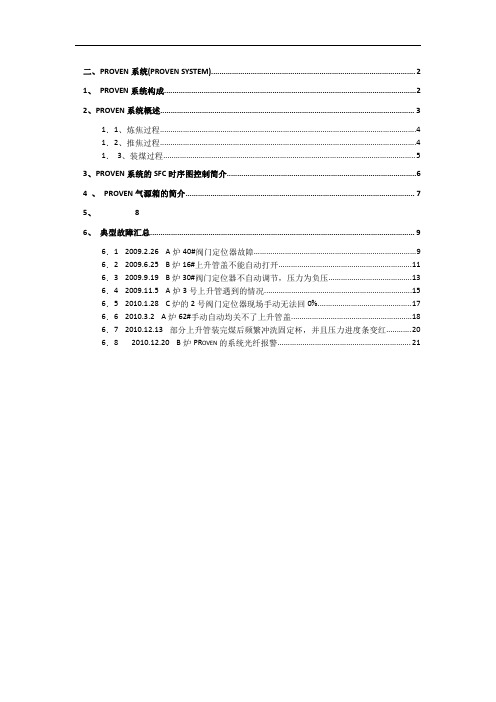
二、PROVEN系统(PROVEN SYSTEM) (2)1、PROVEN系统构成 (2)2、PROVEN系统概述 (3)1.1、炼焦过程 (4)1.2、推焦过程 (4)1.3、装煤过程 (5)3、PROVEN系统的SFC时序图控制简介 (6)4、PROVEN气源箱的简介 (7)5、86、典型故障汇总 (9)6.12009.2.26A炉40#阀门定位器故障 (9)6.22009.6.25B炉16#上升管盖不能自动打开 (11)6.32009.9.19B炉30#阀门定位器不自动调节,压力为负压 (13)6.42009.11.5A炉3号上升管遇到的情况 (15)6.52010.1.28C炉的2号阀门定位器现场手动无法回0% (17)6.62010.3.2A炉62#手动自动均关不了上升管盖 (18)6.72010.12.13部分上升管装完煤后频繁冲洗固定杯,并且压力进度条变红 (20)6.82010.12.20B炉PR OVEN的系统光纤报警 (21)二、PROVEN系统(PROVEN SYSTEM)1、Proven系统构成单炭化室压力调节系统(简称Proven系统)用于对单个炭化室的压力进行精确调节。
该系统在集气管内,对应每孔炭化室的桥管末端安装一个形状像皇冠的管,上面开有多条沟槽,皇冠管下端设有一个“固定杯”,固定杯由三点悬挂,保持水平。
杯内设有执行机构控制的活塞杆及其相连的杯口塞,同时在桥管设有压力检测与控制装置。
炭化室压力调节是由调节杯内的水位也就是荒煤气流经该装置的阻力变化实现的。
在桥管上部有两个喷嘴喷洒的氨水流入杯内,测压压力传感器将检测到上升管部位的压力信号及时传到执行机构的控制器,控制器发出指令使执行机构控制活塞杆带动杯口塞升降,调节固定杯出口大小来调节杯内的水位,使炭化室压力保持在微正压力状态.水位越高,沟槽出口越小,荒煤气导出所受阻越大;水位越低,沟槽出口越大,荒煤气导出所受阻力越小,如图1-1。
7.63米焦炉液压交换机系统典型故障分析及处理(工程师培训)
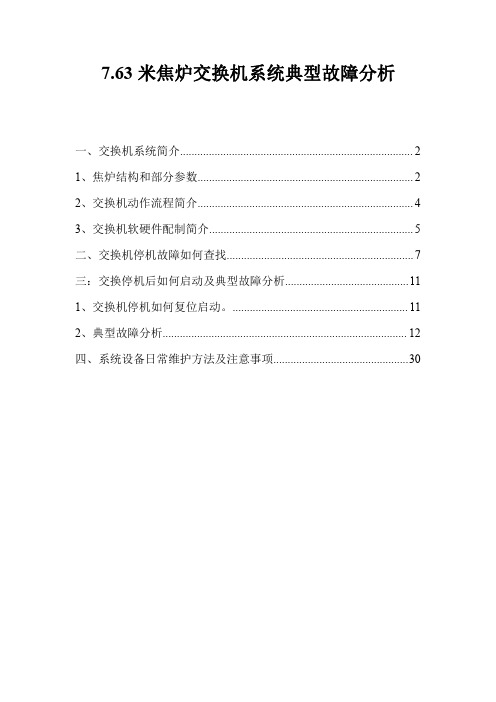
7.63米焦炉交换机系统典型故障分析一、交换机系统简介 (2)1、焦炉结构和部分参数 (2)2、交换机动作流程简介 (4)3、交换机软硬件配制简介 (5)二、交换机停机故障如何查找 (7)三:交换停机后如何启动及典型故障分析 (11)1、交换机停机如何复位启动。
(11)2、典型故障分析 (12)四、系统设备日常维护方法及注意事项 (30)一、交换机系统简介1、焦炉结构和部分参数7.63米焦炉为双联火道,分段加热,废气循环,焦炉煤气、混合煤气、空气均下喷,蓄热室分格的复热式超大型焦炉。
焦炉采用单侧烟道结构,仅在焦侧设有废气瓣和交换设施。
焦炉蓄热室分为煤气蓄热室和空气蓄热室,均为分格蓄热室,在分格蓄热室中,每个立火道单独对应1格蓄热室构成1个加热单元。
用焦炉煤气加热时,在地下室用设有孔板的喷嘴调节煤气,孔板调节方便,准确;空气是通过小烟道顶部的金属调节板调节。
用低热值混合煤气加热时,煤气和空气均用小烟道顶部的金属调节板调节,使得加热煤气和空气在蓄热室长向上分布合理,均匀。
燃烧室由36个共18对双联火道组成。
当焦炉单用焦炉煤气加热时,混合煤气通道也和空气通道一样走空气,空气通过燃烧室底部两个斜道出口,距燃烧室底部1/3处的立火道隔墙出口,2/3处的立火道隔墙出口分别喷出。
焦炉煤气由燃烧室底部煤气喷嘴喷出,形成3点燃烧加热。
由于3段燃烧加热和废气循环,炉体高向加热均匀,废气中的氮氧化物含量低,可以达到先进国家的环保标准。
部分炼焦基本工艺参数:炭化室孔数70孔炭化室有效容积76.25m3每孔炭化室装煤量(干)57.1875t焦炉周转时间25.7h焦炉年工作日数365d焦炉紧张操作系数 1.07交换机系统是整个焦炉的心脏,她负责整个焦炉的供热。
7.63米焦炉为复热式超大型焦炉,她既可以用焦炉煤气加热,又可以用混合煤气加热。
整套设备都由德国UHDE公司供货,并提供技术支持。
这套系统由液压缸、液压泵、蓄能器、油箱、油路控制台、限位开关等设备构成,主要动力源是液压油。
7.63m焦炉存在的问题及解决办法

7.63m焦炉存在的问题及解决办法1 提高单孔炭化室装煤量7.63m焦炉投产初期,装煤量不足,炉顶空间高度达800mm,导致炉顶空间温度高达987℃,由此引发下列问题。
(1) 装煤孔和上升管内的石墨生长速度很快,影响装煤操作,延误了出焦。
(2) 上升管因长石墨而造成内径缩小,导致炭化室内的压力增加,使机焦侧炉门和装煤孔冒烟。
(3) 3号装煤孔堵死,4个装煤孔的煤线高度不均匀,没有达到设计要求。
(4) 装煤车的装煤螺旋加料机产生大电流,甚至堵死螺旋加料出口,无法正常生产。
1.1 提高单孔炭化室装煤量的措施为解决装煤量不足带来的一系列问题,我们采取以下措施:(1) 装煤称重仓单斗装煤量调试优化;(2) 装煤车称重系统校正、提高稳定性,保证装煤量的稳定;(3) 培训提高工人的作业水平,稳定装煤操作环节;(4) 修改不同炉号、不同炉孔的加煤控制时间及装煤各导套的延迟时间,测试出较准确的配置方案。
原设计的加煤总时间为82s,因煤的粒度、水分、配煤等差异,加煤后期,会因炉顶空间压力过大而造成装煤孔冒烟着火现象,环保方面达不到要求。
由于加煤速度在短时间内变化过快,会影响装煤螺旋机构的正常运转,经常发生螺旋电流大、螺旋拧死、堵塞装煤孔等问题。
针对以上情况,连续测量了加煤过程中4个装煤孔的压力变化,从加煤总时间和4个煤斗分别延迟加煤等方面进行试验,最终测算出加煤时间为85s比较合理,且4个煤斗加煤部分采用延迟时间控制在5s、3s、 1s和0s。
有利于炉顶空间压力的流畅,确保了装煤过程中不冒烟,达到了环保要求。
(5) 为解决装煤末期炉顶空间压力波动大,装煤孔冒烟,环保不达标的难题,测试出装煤车二次加煤及推焦机二次平煤的协调控制方式。
原设计的不足之处是平煤时炉顶空间压力过大,焦侧炉门冒烟情况居多,平煤杆带出的余煤大。
我们将4.3m焦炉采用过的2次加煤及2次平煤的操作经验应用到7.63m焦炉上。
装煤车第1次加煤后暂时停止装煤,推焦机进行第1次平煤,使炭化室内的煤峰得到初步拉平,然后装煤车再继续加煤,推焦机进行2次平煤。
- 1、下载文档前请自行甄别文档内容的完整性,平台不提供额外的编辑、内容补充、找答案等附加服务。
- 2、"仅部分预览"的文档,不可在线预览部分如存在完整性等问题,可反馈申请退款(可完整预览的文档不适用该条件!)。
- 3、如文档侵犯您的权益,请联系客服反馈,我们会尽快为您处理(人工客服工作时间:9:00-18:30)。
二、PROVEN系统(PROVEN SYSTEM) (2)
1、PROVEN系统构成 (2)
2、PROVEN系统概述 (3)
1.1、炼焦过程 (4)
1.2、推焦过程 (4)
1.3、装煤过程 (5)
3、PROVEN系统的SFC时序图控制简介 (6)
4、PROVEN气源箱的简介 (7)
5、8
6、典型故障汇总 (9)
6.12009.2.26A炉40#阀门定位器故障 (9)
6.22009.6.25B炉16#上升管盖不能自动打开 (11)
6.32009.9.19B炉30#阀门定位器不自动调节,压力为负压 (13)
6.42009.11.5A炉3号上升管遇到的情况 (15)
6.52010.1.28C炉的2号阀门定位器现场手动无法回0% (17)
6.62010.3.2A炉62#手动自动均关不了上升管盖 (18)
6.72010.12.13部分上升管装完煤后频繁冲洗固定杯,并且压力进度条变红 (20)
6.82010.12.20B炉PR OVEN的系统光纤报警 (21)
二、PROVEN系统(PROVEN SYSTEM)
1、Proven系统构成
单炭化室压力调节系统(简称Proven系统)用于对单个炭化室的压力进行精确调节。
该系统在集气管内,对应每孔炭化室的桥管末端安装一个形状像皇冠的管,上面开有多条沟槽,皇冠管下端设有一个“固定杯”,固定杯由三点悬挂,保持水平。
杯内设有执行机构控制的活塞杆及其相连的杯口塞,同时在桥管设有压力检测与控制装置。
炭化室压力调节是由调节杯内的水位也就是荒煤气流经该装置的阻力变化实现的。
在桥管上部有两个喷嘴喷洒的氨水流入杯内,测压压力传感器将检测到上升管部位的压力信号及时传到执行机构的控制器,控制器发出指令使执行机构控制活塞杆带动杯口塞升降,调节固定杯出口大小来调节杯内的水位,使炭化室压力保持在微正压力状态.水位越高,沟槽出口越小,荒煤气导出所受阻越大;水位越低,沟槽出口越大,荒煤气导出所受阻力越小,如图
1-1。
图1-1
而未使用PROVEN系统的焦炉,集气管压力一般控制在120Pa左右,炉门底部的压力在结焦周期内变化幅度很大。
刚开始装煤时,炉门底部压力可以达到300Pa以上,很容易造成从炉体的不严密处逸出荒煤气;而在推焦前,炉门底部压力已经降到0Pa附近,考虑到压力的波动,焦炉在结焦末期经常出现负压,会抽入空气。
使用PROVEN系统后,焦炉集气管压力保持在-300Pa左右,炉门底部的压力始终可控制在40~60Pa范围内变化。
因此焦炉逸出的荒煤气大大减少,改善了作业环境。
实验显示,使用PROVEN系统后焦炉荒煤气的逸出量和未使用前相比可降低近70%。
2、PROVEN系统概述
炭化室作为炼焦最主要的设备,其压力调节担负着十分重要的作用。
在炼焦过程中,使炭化室压力维持在一定范围内,可以有效抑制由炼焦过程中生成的荒煤气而引起的炉压变化对炉体的损害;在炼焦结束进行推焦过程时,为避免空气进入集气管产生爆炸危险,必须将炭化室与集气管隔离;在装煤时,为防止烟尘外溢对环境造成污染,要实现负压装煤,即使炭化室压力小于大气压力。
京唐钢铁公司焦化作业部的焦炉采用的德国Uhde公司的炉压调节技术(Pressure Regulation Oven,简称PROven),正是针对焦炉各阶段对炭化室压力的不同要求提出的一套完整的解决方案,下图为现场的固定杯和皇冠杯的样图和实体图1-1-1。