浅谈孔壁镀层空洞的成因及对策
缸套内孔镀铬层针孔产生的原因及预防措施
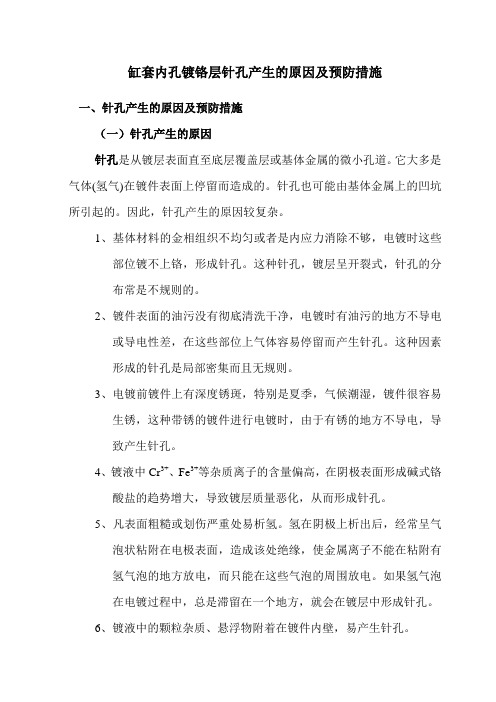
缸套内孔镀铬层针孔产生的原因及预防措施一、针孔产生的原因及预防措施(一)针孔产生的原因针孔是从镀层表面直至底层覆盖层或基体金属的微小孔道。
它大多是气体(氢气)在镀件表面上停留而造成的。
针孔也可能由基体金属上的凹坑所引起的。
因此,针孔产生的原因较复杂。
1、基体材料的金相组织不均匀或者是内应力消除不够,电镀时这些部位镀不上铬,形成针孔。
这种针孔,镀层呈开裂式,针孔的分布常是不规则的。
2、镀件表面的油污没有彻底清洗干净,电镀时有油污的地方不导电或导电性差,在这些部位上气体容易停留而产生针孔。
这种因素形成的针孔是局部密集而且无规则。
3、电镀前镀件上有深度锈斑,特别是夏季,气候潮湿,镀件很容易生锈,这种带锈的镀件进行电镀时,由于有锈的地方不导电,导致产生针孔。
4、镀液中Cr3+、Fe3+等杂质离子的含量偏高,在阴极表面形成碱式铬酸盐的趋势增大,导致镀层质量恶化,从而形成针孔。
5、凡表面粗糙或划伤严重处易析氢。
氢在阴极上析出后,经常呈气泡状粘附在电极表面,造成该处绝缘,使金属离子不能在粘附有氢气泡的地方放电,而只能在这些气泡的周围放电。
如果氢气泡在电镀过程中,总是滞留在一个地方,就会在镀层中形成针孔。
6、镀液中的颗粒杂质、悬浮物附着在镀件内壁,易产生针孔。
7、使用铬雾抑制剂后,气体不易逸出,氢气泡吸附在缸套表面上产生针孔。
(二)针孔的预防措施1、控制原材料质量。
对进入工序的原材料要保证金相组织均匀,消除应力。
2、保证镀前清洗工序的清洗质量,确保缸套清洁度达到标准要求。
保证做到当班清洗的工件全部电镀,减少清洗后存放产生锈蚀。
对入槽前的镀件严格执行酸洗、中和、漂洗步骤,确保内孔表面符合电镀前的要求。
3、锈蚀严重的镀件,退回前道工序,重新处理,合格后再施镀。
4、通常基体表面粗糙度越低,对镀层的沉积越有利,因此,应尽可能降低表面粗糙度。
5、采用镀铬液清理设备定期过滤溶液,降低Cr3+,过滤出Fe3+、Cu2+等有害离子,有利于氢气的逸出。
详谈pcb钻孔孔壁镀铜开裂问题及解决方案-豆丁
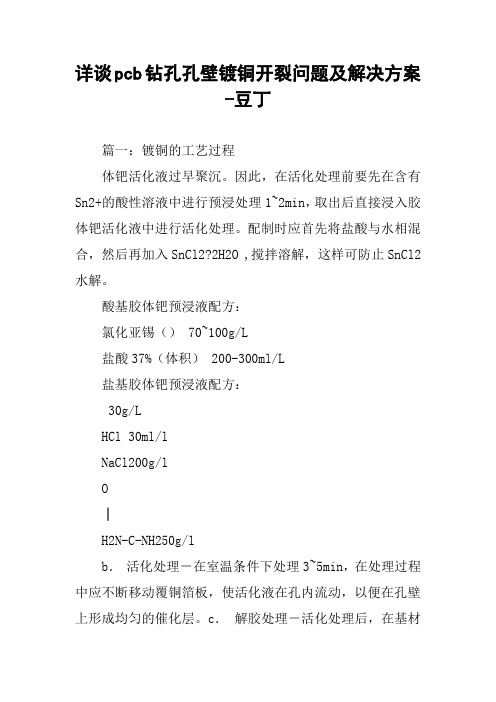
详谈pcb钻孔孔壁镀铜开裂问题及解决方案-豆丁篇一:镀铜的工艺过程体钯活化液过早聚沉。
因此,在活化处理前要先在含有Sn2+的酸性溶液中进行预浸处理1~2min,取出后直接浸入胶体钯活化液中进行活化处理。
配制时应首先将盐酸与水相混合,然后再加入SnCl2?2H2O ,搅拌溶解,这样可防止SnCl2水解。
酸基胶体钯预浸液配方:氯化亚锡() 70~100g/L盐酸37%(体积) 200-300ml/L盐基胶体钯预浸液配方:30g/LHCl 30ml/lNaCl200g/lO║H2N-C-NH250g/lb.活化处理-在室温条件下处理3~5min,在处理过程中应不断移动覆铜箔板,使活化液在孔内流动,以便在孔壁上形成均匀的催化层。
c.解胶处理-活化处理后,在基材表面吸附着以钯粒子为核心,在钯核的周围,具有碱式锡酸盐的胶体化合物。
在化学镀铜前,应将碱式锡酸盐去除,使活性的钯晶核充分暴露出来,从而使钯晶核具有非常强而均匀的活性。
经过解胶处理再进行化学镀铜,不但提高了胶体钯的活性,而且也显著提高化学镀铜层与基材间的结合强度。
常用的解胶处理液是5%的氢氧化钠水溶液或1%氟硼酸水溶液。
解胶处理在室温条件下处理1~2min,水洗后进行化学镀铜。
d.胶体铜活化液简介:明胶 2g/l/lDMAB(二甲胺基硼烷)5g/l水合肼 10 g/l钯20ppm配制过程:首先分别将明胶和硫酸铜用温水(40度C)溶解后将明胶加入至硫酸铜的溶液中,用25%H2SO4将PH值调至2..5当温度为45度C时,将溶解后DMAB在搅拌条件下缓慢加入上述的混合溶液中,并加入去离子稀释至1升,保温40~45度C,并搅拌至反应开始(约5~10分钟)溶液的颜色由蓝再变成绿色。
放置24小时颜色变成红黑色后加入水合肼。
篇二:PCB线路板镀铜表面粗糙问题原因分析PCB线路板镀銅表面粗糙问题原因分析可能原因如下:镀铜槽本身的问题1、阳极问题:成分含量不当导致产生杂质2、光泽剂问题(分解等)3、电流密度不当导致铜面不均匀4、槽液成分失调或杂质污染5、设备设计或组装不当导致电流分布太差…………当然作为镀铜本身来讲;以上问题导致粗糙的可能性不大前制程问题PTH制程带入其他杂质:1、活化成分失调钯浓度太高或者预浸盐残留板面2、速化失调板面镀铜是残有锡离子3、化学铜失调板面沉铜不均4、镀铜前酸洗不当导致板面残留杂质………………黑孔制程:微蚀不净导致残碳抗氧化不当导致板面不良烘干不良导致微蚀无法将板面碳剥除导致残碳电流输入输出不当导致板面不良…………篇三:化学镀铜常见故障和纠正方法-PCB工艺论文,SMT 技术文章-SMT专家网化学镀铜常见故障和纠正方法◎化学镀铜常见故障和纠正方法故障发生原因纠正方法化学镀铜空洞①钻孔粉尘,孔化后脱落①检查吸尘器,钻头质量,转速/进给等②加强去毛刺的高压水冲洗钻孔后孔壁裂缝或内层间分离检查钻头质量,转速/进给,以及层压板厚材料和层压工艺条件③除钻污过度,造成树脂变成海绵状,引起水洗不良和镀层脱落检查除钻污法工艺,适当降低去钻污强度④除钻污后中和处理不充分,残留Mn残渣检查中和处理工艺⑤清洁调整不足,影响Pd的吸附检查清洗调整处理工艺(如浓度、温度、时间)及副产物是否过量⑥活化液浓度偏低影响Pd吸附检查活化处理工艺补充活化剂⑦加速处理过度,在去除Sn的同时Pd也被除掉检查加速处理工艺条件(温度/时间/浓度)如降低加速剂浓度或浸板时间⑧水洗不充分,使各槽位的药水相互污染检查水洗能力,水量/水洗时间⑨孔内有气泡加设摇摆、震动等⑩化学镀铜液的活性差检查NaOH、HCHO、Cu2+的浓度以及溶液温度等⑾反应过程中产生气体无法及时逸出加强移动、振动和空气搅拌等。
深孔电镀孔无铜缺陷成因探讨及改善
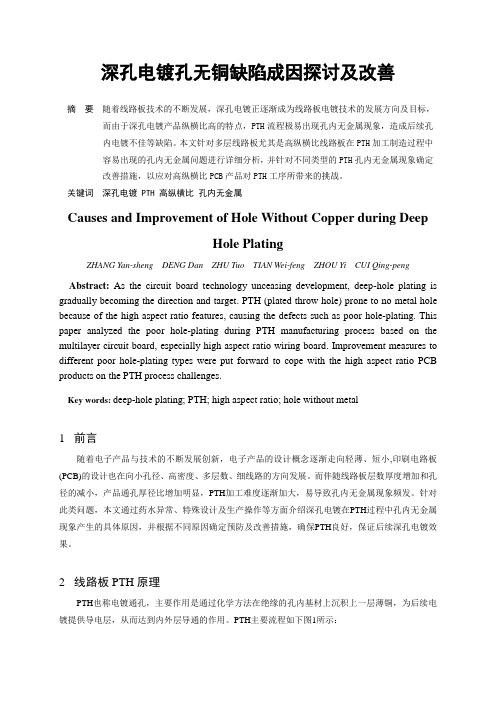
深孔电镀孔无铜缺陷成因探讨及改善摘要随着线路板技术的不断发展,深孔电镀正逐渐成为线路板电镀技术的发展方向及目标,而由于深孔电镀产品纵横比高的特点,PTH流程极易出现孔内无金属现象,造成后续孔内电镀不佳等缺陷。
本文针对多层线路板尤其是高纵横比线路板在PTH加工制造过程中容易出现的孔内无金属问题进行详细分析,并针对不同类型的PTH孔内无金属现象确定改善措施,以应对高纵横比PCB产品对PTH工序所带来的挑战。
关键词深孔电镀 PTH 高纵横比孔内无金属Causes and Improvement of Hole Without Copper during DeepHole PlatingZHANG Yan-sheng DENG Dan ZHU Tuo TIAN Wei-feng ZHOU Yi CUI Qing-pengAbstract: As the circuit board technology unceasing development, deep-hole plating is gradually becoming the direction and target. PTH (plated throw hole) prone to no metal hole because of the high aspect ratio features, causing the defects such as poor hole-plating. This paper analyzed the poor hole-plating during PTH manufacturing process based on the multilayer circuit board, especially high aspect ratio wiring board. Improvement measures to different poor hole-plating types were put forward to cope with the high aspect ratio PCB products on the PTH process challenges.Key words: deep-hole plating; PTH; high aspect ratio; hole without metal1前言随着电子产品与技术的不断发展创新,电子产品的设计概念逐渐走向轻薄、短小,印刷电路板(PCB)的设计也在向小孔径、高密度、多层数、细线路的方向发展。
印制电路板镀层缺陷成因分析及其对策

印制电路板镀层缺陷成因分析及其对策1前言金属化孔质量与多层板质量及可靠性息息相关。
金属化孔起着多层印制线路电气互连的作用。
孔壁镀铜层质量是印制板质量的核心,不仅要求镀层有合适的厚度、均匀性和延展性,而且要求镀层在288℃热冲击10秒不能产生断裂。
因为孔壁镀铜层热冲击断裂是一种致命的缺陷,它将造成内层线路间和内层与外层线路之间断路;轻者影响线路断续导电,重者引起多层板报废。
目前,印制板生产中经常出现的金属化孔镀层缺陷主要有:金属化孔内镀铜层空洞、瘤状物、孔内镀层薄、粉红圈以及多层板孔壁与内层铜环连接不良等。
这些缺陷的绝大多数将导致产品报废,造成严重的经济损失,影响交货期。
2金属化孔镀层主要缺陷的产生原因及相应对策我们首先简单回顾一下多层印制板的制造工艺过程。
下料→制板→蚀刻→黑化→层压→钻孔→去沾污及凹蚀处理→孔金属化→全板电镀→制板→图形电镀→脱膜→蚀刻→丝印阻焊→热风整平→丝印字符本文将从钻孔工序、孔壁去树脂沾污及凹蚀处理工序、电镀及多层板层压工序等几个方面,分析金属化孔镀层的主要缺陷及产生原因,阐述如何优化工艺参数,进行严格的工艺及生产管理,以保证孔化质量。
2.1钻孔工序大多数镀层空洞部位都伴随出现钻孔质量差引起的孔壁缺陷,如孔口毛刺、孔壁粗糙、基材凹坑及环氧树脂腻污等。
由此造成孔壁镀铜层空洞,孔壁基材与镀层分离或镀层不平整。
下面,将对孔壁缺陷的成因及所采取的措施进行阐述:2.1.1孔口毛刺的产生及去除无论是采用手工钻还是数控钻,也无论是采用何种钻头和钻孔工艺参数,覆铜箔板在其钻孔过程中,产生毛刺总是不可避免的。
孔口毛刺对于金属化孔质量的影响历来不被人们所重视,但对于高可靠性印制板的金属化孔质量来讲,它却是一个不可忽视的因素。
首先,孔口毛刺会改变孔径尺寸,导致孔径入口处尺寸变小,影响元器件的插入。
其次,凸起或凹陷进入孔内的铜箔毛刺,将影响孔金属化过程中电镀时的电力线分布,导致孔口镀层厚度偏薄和应力集中,从而使成品印制板的孔口镀铜层在受到热冲击时,极易因基板热膨胀所引起的轴向拉伸应力造成断裂现象。
电镀层孔隙类型和起因

电镀层孔隙类型和起因电镀层是一种通过电化学方法在金属表面形成保护层的工艺。
然而,在实际应用中,电镀层常常会出现孔隙问题,降低了其保护性能和美观度。
本文将从孔隙的类型和起因两个方面,对电镀层孔隙问题进行探讨。
一、孔隙的类型电镀层的孔隙主要分为两大类:气孔和溶解孔。
1.气孔:气孔是由于电镀液中存在气体而引起的,其形成原因多种多样。
首先,电镀液中的气体可能是由于操作不当,未能彻底排除气体导致的。
其次,电解质中的水分可能会在电解过程中释放出气体。
另外,电极上的气体也是产生气孔的原因之一。
2.溶解孔:溶解孔是由于金属表面存在缺陷或不均匀的镀层导致的。
金属表面的不均匀性可能是由于腐蚀、疲劳、划伤等原因造成的。
此外,电镀液中的杂质也可能在电镀过程中影响镀层的均匀性,导致溶解孔的产生。
二、孔隙的起因电镀层孔隙的产生与多种因素相关,主要包括以下几个方面:1.电镀液的成分:电镀液的成分对孔隙的形成起着重要作用。
电镀液中的气体、杂质、电解质浓度等都会对电镀层的均匀性产生影响。
如果电镀液中存在过多的气体或杂质,并且电解质浓度不均匀,就会导致电镀层产生孔隙。
2.电镀工艺参数:电镀工艺参数的选择和控制也是影响电镀层孔隙的重要因素。
电镀过程中的电流密度、温度、电解质浓度、搅拌速度等参数的不合理选择都可能导致孔隙的产生。
过高或过低的电流密度、温度过高或过低、电解质浓度过低等都会影响电镀层的均匀性,从而产生孔隙。
3.基材的表面处理:基材的表面处理对电镀层的质量也有重要影响。
如果基材表面存在油污、氧化物、锈蚀等污染物,会导致电镀层与基材之间附着力不佳,从而产生孔隙。
因此,在进行电镀前,必须对基材进行适当的清洗和处理,确保其表面光洁度和纯净度。
4.设备和操作:设备和操作也是孔隙产生的重要因素。
设备的性能和状态直接影响到电镀层的质量。
操作人员的技术水平和操作规范也会对电镀层的均匀性产生影响。
不合理的设备选择、设备故障、操作不当等都可能导致孔隙的产生。
钻孔电镀基本问题以及处理方案
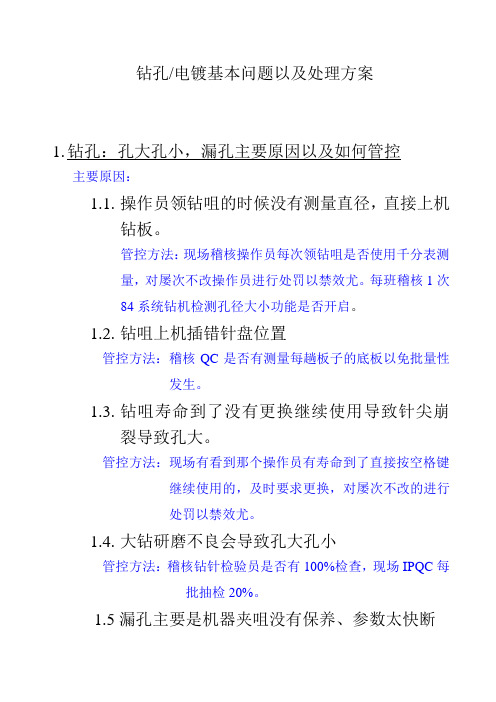
钻孔/电镀基本问题以及处理方案1.钻孔:孔大孔小,漏孔主要原因以及如何管控主要原因:操作员领钻咀的时候没有测量直径,直接上机钻板。
管控方法:现场稽核操作员每次领钻咀是否使用千分表测量,对屡次不改操作员进行处罚以禁效尤。
每班稽核1次84系统钻机检测孔径大小功能是否开启。
钻咀上机插错针盘位置管控方法:稽核QC是否有测量每趟板子的底板以免批量性发生。
钻咀寿命到了没有更换继续使用导致针尖崩裂导致孔大。
管控方法:现场有看到那个操作员有寿命到了直接按空格键继续使用的,及时要求更换,对屡次不改的进行处罚以禁效尤。
大钻研磨不良会导致孔大孔小管控方法:稽核钻针检验员是否有100%检查,现场IPQC每批抽检20%。
1.5漏孔主要是机器夹咀没有保养、参数太快断针、钻咀研磨不良。
管控方法:1.每班生产前稽核是否有保养夹咀。
2.针对断针多的机台查看参数是否按照SOP设定。
3.稽核钻针检验员是否有100%检查,现场IPQC每批抽检20%。
2.电镀孔无铜主要原因以及如何管控。
主要原因:钻孔----1、钻咀蹦缺(孔壁粗糙度):孔壁粗糙度需要控制≤25.4um,钻孔前以及钻孔后都需要检查钻咀的实际状况,每台设备每天需要抽测其钻孔的粗糙度;另钻咀每使用2000次后需要进行一次研磨,并用颜色胶颗粒标示,使用次数到期的钻咀需要昨报废处理;2、粉尘对于≤0.8mm的孔,钻孔后需要用气枪吹孔,防止有粉尘3、断钻咀如有出现断钻咀的现象,生产需要第一时间标示短针的位置,并由IPQC检查孔内是否残留钻咀头。
沉铜-----1、背光不良每2小时打一次背光,确认背光状况,背光需要≥9级2、孔内气泡每班稽核摇摆和振动马达是否正常在运行。
电镀-----1、镀电前氧化严重沉铜电镀前放置时间不超过4H。
若超过4H未板电,需返工沉铜处理;———XX负责监督2、电镀时掉电流操作员每2时点检电流,有异常及时检修3、药水成分失控化验分析后,及时调整药水;4、光剂延展性能差每季度做延展性测试,了解药水现况,小于15做出原因查找包志国2009-04-01。
空洞的来因
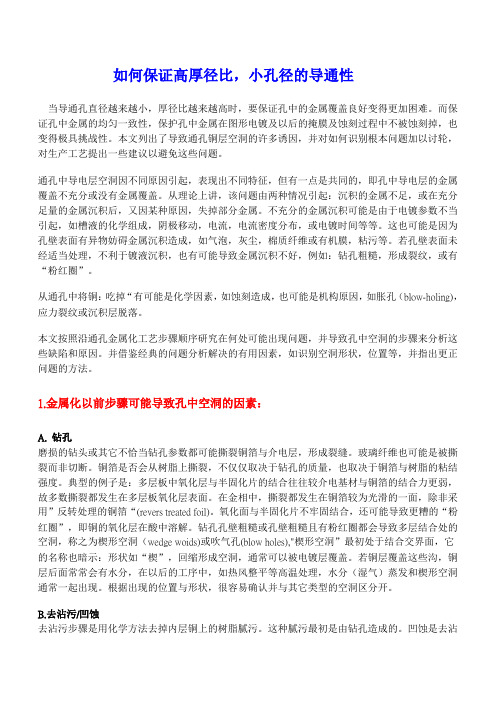
如何保证高厚径比,小孔径的导通性当导通孔直径越来越小,厚径比越来越高时,要保证孔中的金属覆盖良好变得更加困难。
而保证孔中金属的均匀一致性,保护孔中金属在图形电镀及以后的掩膜及蚀刻过程中不被蚀刻掉,也变得极具挑战性。
本文列出了导致通孔铜层空洞的许多诱因,并对如何识别根本问题加以讨轮,对生产工艺提出一些建议以避免这些问题。
通孔中导电层空洞因不同原因引起,表现出不同特征,但有一点是共同的,即孔中导电层的金属覆盖不充分或没有金属覆盖。
从理论上讲,该问题由两种情况引起:沉积的金属不足,或在充分足量的金属沉积后,又因某种原因,失掉部分金属。
不充分的金属沉积可能是由于电镀参数不当引起,如槽液的化学组成,阴极移动,电流,电流密度分布,或电镀时间等等。
这也可能是因为孔壁表面有异物妨碍金属沉积造成,如气泡,灰尘,棉质纤维或有机膜,粘污等。
若孔壁表面未经适当处理,不利于镀液沉积,也有可能导致金属沉积不好,例如:钻孔粗糙,形成裂纹,或有“粉红圈”。
从通孔中将铜:吃掉“有可能是化学因素,如蚀刻造成,也可能是机构原因,如胀孔(blow-holing),应力裂纹或沉积层脱落。
本文按照沿通孔金属化工艺步骤顺序研究在何处可能出现问题,并导致孔中空洞的步骤来分析这些缺陷和原因。
并借鉴经典的问题分析解决的有用因素,如识别空洞形状,位置等,并指出更正问题的方法。
1.金属化以前步骤可能导致孔中空洞的因素:A. 钻孔磨损的钻头或其它不恰当钻孔参数都可能撕裂铜箔与介电层,形成裂缝。
玻璃纤维也可能是被撕裂而非切断。
铜箔是否会从树脂上撕裂,不仅仅取决于钻孔的质量,也取决于铜箔与树脂的粘结强度。
典型的例子是:多层板中氧化层与半固化片的结合往往较介电基材与铜箔的结合力更弱,故多数撕裂都发生在多层板氧化层表面。
在金相中,撕裂都发生在铜箔较为光滑的一面,除非采用”反转处理的铜箔“(revers treated foil)。
氧化面与半固化片不牢固结合,还可能导致更糟的“粉红圈”,即铜的氧化层在酸中溶解。
关于深孔缺陷的原因与防治措施

选用合适钻头
根据加工需求选择合适类 型和规格的钻头,以减小 钻底应力。
控制钻深
合理控制钻孔深度,避免 因钻头过长或过短导致钻 底应力过大或过小。
调整机床参数
根据实际情况调整机床转 速、进给速度等参数,以 减小钻头在钻底时的振动 和冲击。
孔身缺陷的防治措施
保持钻头锋利
定期检查和修磨钻头,确保其锋利度 和切削性能良好。
关于深孔缺陷的原因与防治 措施
汇报人: 2024-01-01
目录
• 深孔缺陷的种类与特征 • 深孔缺陷产生的原因 • 深孔缺陷的防治措施 • 深孔缺陷的检测与评估 • 深孔缺陷的案例分析 • 未来研究方向与展望
01
深孔缺陷的种类与特征
孔口缺陷
总结词
孔口缺陷通常表现为孔口边缘不整齐 、出现缺口或毛刺,有时还伴有裂纹 。
新型防治措施的开发与推广
总结词
针对深孔缺陷的防治,新型防治措施的 开发和推广是未来的重要研究方向。这 些措施能够有效地减少或避免深孔缺陷 的产生,提高产品质量和可靠性。
VS
详细描述
目前,新型防治措施如改进加工工艺、优 化切削参数、使用新型刀具和材料等正在 被积极研究。这些措施能够显著减少深孔 缺陷的产生,提高深孔加工的质量和效率 。未来,这些措施将进一步得到开发和推 广,为深孔加工行业的发展提供有力支持 。
可能对飞机的性能和安全性造成潜在威胁。
06
未来研究方向与展望
新型检测技术的研究与应用
总结词
随着科技的发展,新型检测技术的研究和应用对于深孔缺陷的检测和预防具有重要意义。这些技术能 够更精确、快速地检测出深孔缺陷,提高产品质量和生产效率。
详细描述
目前,新型检测技术如超声波检测、射线检测、涡流检测等正在被深入研究。这些技术能够检测出微 小的缺陷,甚至在产品制造过程中实时监测,有效避免了产品的不合格率。未来,这些技术将进一步 应用于实际生产中,为深孔缺陷的防治提供有力支持。
PCB镀通孔发生_空洞_的根本原因和对策

PCB镀通孔发生“空洞”的根本原因和对策林金堵 吴梅珠摘 要 文章概述了多层板镀通孔发生“空洞”的根本原因与对策。
基材、钻孔、孔壁粗糙度、孔尺寸、化学镀铜和电镀铜等都会影响PTH的“空洞”问题。
关键词 镀通孔;镀层“空洞”;镀层附着力;高性能基材;孔壁表面状态;化学镀铜中图分类号:TN41 文献标识码:A 文章编号:1009-0096(2010)4-0031-06The Basic and Countermeasureof the Plated Through Hole Voiding in PCBLIN Jin-du WU Mei-zhuAbstract The paper describes the basic and countermeasure of the plated through hole voiding in PCB. The substrate material, drilling hole, hole-wall topography, hole size, electroless copper, and plated copper can signi fi cantly impact the hole-wall voids, adhesion, and reliability of the PTH.Key words PTH(Plated Through-Hole); hole-wall voids; hole-wall adhesion; high-performance substrate; hole-wall topography; electroless copper目前,多层板随着高密度化发展和无铅化焊接要求等条件下,层间连接的导通孔面临着产生“空洞”等缺陷,其可靠性方面面临着严厉而复杂的挑战。
这些挑战:(1)是导通孔高厚径比(孔微小化和高多层化)化和盲孔化等带来孔金属化与电镀的复杂困难度;(2)是无铅化要采用更高的T d 、T g 温度的CCL (高性能)材料所带来“导通孔”的加工新问题;(3)由于无铅化焊接要求有耐更高的焊接温度、更长的高温焊接时间和快速的冷却速度,因此,导通孔内的铜镀层,不仅要有更好的延展性,而且更重要地是要与孔壁有更好的结合力,才能经得起更高的焊接条件的考验;(4)是所制造的成品要经得起更高幅度的多次“热循环”、“热冲击”(更高温度和更长的高温停留时间)等的“老化(可靠性)”考验。
孔无铜
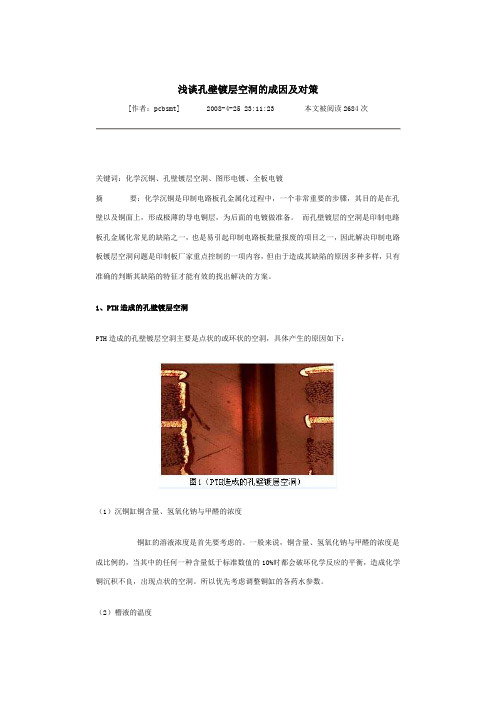
浅谈孔壁镀层空洞的成因及对策[作者:pcbsmt] 2008-4-25 23:11:23 本文被阅读2684次关键词:化学沉铜、孔壁镀层空洞、图形电镀、全板电镀摘要:化学沉铜是印制电路板孔金属化过程中,一个非常重要的步骤,其目的是在孔壁以及铜面上,形成极薄的导电铜层,为后面的电镀做准备。
而孔壁镀层的空洞是印制电路板孔金属化常见的缺陷之一,也是易引起印制电路板批量报废的项目之一,因此解决印制电路板镀层空洞问题是印制板厂家重点控制的一项内容,但由于造成其缺陷的原因多种多样,只有准确的判断其缺陷的特征才能有效的找出解决的方案。
1、PTH造成的孔壁镀层空洞PTH造成的孔壁镀层空洞主要是点状的或环状的空洞,具体产生的原因如下:(1)沉铜缸铜含量、氢氧化钠与甲醛的浓度铜缸的溶液浓度是首先要考虑的。
一般来说,铜含量、氢氧化钠与甲醛的浓度是成比例的,当其中的任何一种含量低于标准数值的10%时都会破坏化学反应的平衡,造成化学铜沉积不良,出现点状的空洞。
所以优先考虑调整铜缸的各药水参数。
(2)槽液的温度槽液的温度对溶液的活性也存在着重要的影响。
在各溶液中一般都会有温度的要求,其中有些是要严格控制的。
所以对槽液的温度也要随时关注。
(3)活化液的控制二价锡离子偏低会造成胶体钯的分解,影响钯的吸附,但只要对活化液定时的进行添加补充,不会造成大的问题。
活化液控制的重点是不能用空气搅拌,空气中的氧会氧化二价锡离子,同时也不能有水进入,会造成SnCl2的水解。
(4)清洗的温度清洗的温度常常被人忽视,清洗的最佳温度是在20℃以上,若低于15℃就会影响清洗的效果。
在冬季的时候,水温会变的很低,尤其是在北方。
由于水洗的温度低,板子在清洗后的温度也会变的很低,在进入铜缸后板子的温度不能立刻升上来,会因为错过了铜沉积的黄金时间而影响沉积的效果。
所以在环境温度较低的地方,也要注意清洗水的温度。
(5)整孔剂的使用温度、浓度与时间药液的温度有着较严格的要求,过高的温度会造成整孔剂的分解,使整孔剂的浓度变低,影响整孔的效果,其明显的特征是在孔内的玻璃纤维布处出现点状空洞。
通孔铜层空洞的原因和解决方法

通孔铜层空洞的原因和解决方法通孔中导电层空洞的原因大概有两种:沉积的金属不足,或在充分足量的金属沉积后,又因某种原因,失掉部分金属。
不充分的金属沉积可能是由于电镀参数不当引起,如槽液的化学组成,阴极移动,电流,电流密度分布,或电镀时间等等。
本文按照导通孔金属化工艺步骤顺序研究在何处可能出现问题,并导致孔中空洞的步骤来分析这些缺陷和原因。
并借鉴经典的问题分析解决的有用因素,如识别空洞形状,位置等,并指出更正问题的方法。
1、金属化以前步骤可能导致孔中空洞的因素:A、钻孔磨损的钻头或其它不恰当钻孔参数都可能撕裂铜箔与介电层,形成裂缝。
玻璃纤维也可能是被撕裂而非切断。
铜箔是否会从树脂上撕裂,不仅仅取决于钻孔的质量,也取决于铜箔与树脂的粘结强度。
典型的例子是:多层板中氧化层与半固化片的结合往往较介电基材与铜箔的结合力更弱,故多数撕裂都发生在多层板氧化层表面。
在金板中,撕裂都发生在铜箔较为光滑的一面,除非采用”反转处理的铜箔“(revers treated foil)。
氧化面与半固化片不牢固结合,还可能导致更糟的“粉红圈”,即铜的氧化层在酸中溶解。
钻孔孔壁粗糙或孔壁粗糙且有粉红圈都会导致多层结合处的空洞,称之为楔形空洞(wedge woids)或吹气孔(blow holes),"楔形空洞”最初处于结合交界面,它的名称也暗示:形状如“楔”,回缩形成空洞,通常可以被电镀层覆盖。
若铜层覆盖这些沟,铜层后面常常会有水分,在以后的工序中,如热风整平等高温处理,水分(湿气)蒸发和楔形空洞通常一起出现。
根据出现的位置与形状,很容易确认并与其它类型的空洞区分开。
B、去沾污/凹蚀去沾污步骤是用化学方法去掉内层铜上的树脂腻污。
这种腻污最初是由钻孔造成的。
凹蚀是去沾污的进一步深化,即将去掉更多的树脂,使铜从树脂中“突出”,与镀铜层形成“三点结合”或“三面结合”,提高互联可靠性。
高锰酸盐用于氧化树脂,并“蚀刻”之。
首先需要将树脂溶胀,以便于高锰酸盐处理,中和步骤可以去掉锰酸盐残渣,玻璃纤维蚀刻采用不同的化学方法,通常是氢氟酸。
化孔镀层缺陷成因分析及对策
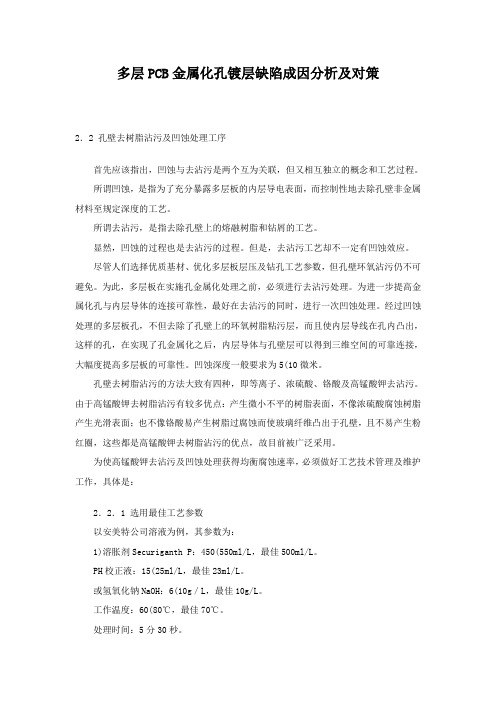
多层PCB金属化孔镀层缺陷成因分析及对策2.2 孔壁去树脂沾污及凹蚀处理工序首先应该指出,凹蚀与去沾污是两个互为关联,但又相互独立的概念和工艺过程。
所谓凹蚀,是指为了充分暴露多层板的内层导电表面,而控制性地去除孔壁非金属材料至规定深度的工艺。
所谓去沾污,是指去除孔壁上的熔融树脂和钻屑的工艺。
显然,凹蚀的过程也是去沾污的过程。
但是,去沾污工艺却不一定有凹蚀效应。
尽管人们选择优质基材、优化多层板层压及钻孔工艺参数,但孔壁环氧沾污仍不可避免。
为此,多层板在实施孔金属化处理之前,必须进行去沾污处理。
为进一步提高金属化孔与内层导体的连接可靠性,最好在去沾污的同时,进行一次凹蚀处理。
经过凹蚀处理的多层板孔,不但去除了孔壁上的环氧树脂粘污层,而且使内层导线在孔内凸出,这样的孔,在实现了孔金属化之后,内层导体与孔壁层可以得到三维空间的可靠连接,大幅度提高多层板的可靠性。
凹蚀深度一般要求为5(10微米。
孔壁去树脂沾污的方法大致有四种,即等离子、浓硫酸、铬酸及高锰酸钾去沾污。
由于高锰酸钾去树脂沾污有较多优点:产生微小不平的树脂表面,不像浓硫酸腐蚀树脂产生光滑表面;也不像铬酸易产生树脂过腐蚀而使玻璃纤维凸出于孔壁,且不易产生粉红圈,这些都是高锰酸钾去树脂沾污的优点,故目前被广泛采用。
为使高锰酸钾去沾污及凹蚀处理获得均衡腐蚀速率,必须做好工艺技术管理及维护工作,具体是:2.2.1 选用最佳工艺参数以安美特公司溶液为例,其参数为:1)溶胀剂Securiganth P:450(550ml/L,最佳500ml/L。
PH校正液:15(25ml/L,最佳23ml/L。
或氢氧化钠NaOH:6(10g/L,最佳10g/L。
工作温度:60(80℃,最佳70℃。
处理时间:5分30秒。
2)高锰酸钾KMnO4:50(60g/L,最佳60g/L。
氢氧化钠NaOH: 30(50g/L,最佳40g/L。
工作温度:60(80℃,最佳70℃。
处理时间:12分。
浅谈电路板维修孔壁镀层空洞的成因及对策

浅谈电路板维修孔壁镀层空洞的成因及对策1、电路板PTH造成的孔壁镀层空洞PTH造成的孔壁镀层空洞主要是点状的或环状的空洞,具体产生的原因如下:浅谈电路板孔壁镀层空洞的成因及对策- 飛隆侠客- 飛隆侠客欢迎您的到来!其筋骨苦其心智诚(1)电路板沉铜缸铜含量、氢氧化钠与甲醛的浓度铜缸的溶液浓度是首先要考虑的。
一般来说,铜含量、氢氧化钠与甲醛的浓度是成比例的,当其中的任何一种含量低于标准数值的10%时都会破坏化学反应的平衡,造成化学铜沉积不良,出现点状的空洞。
所以优先考虑调整铜缸的各药水参数。
(2)电路板槽液的温度槽液的温度对溶液的活性也存在着重要的影响。
在各溶液中一般都会有温度的要求,其中有些是要严格控制的。
所以对槽液的温度也要随时关注。
(3)电路板活化液的控制二价锡离子偏低会造成胶体钯的分解,影响钯的吸附,但只要对活化液定时的进行添加补充,不会造成大的问题。
活化液控制的重点是不能用空气搅拌,空气中的氧会氧化二价锡离子,同时也不能有水进入,会造成SnCl2的水解。
(4)电路板清洗的温度清洗的温度常常被人忽视,清洗的最佳温度是在20℃以上,若低于15℃就会影响清洗的效果。
在冬季的时候,水温会变的很低,尤其是在北方。
由于水洗的温度低,板子在清洗后的温度也会变的很低,在进入铜缸后板子的温度不能立刻升上来,会因为错过了铜沉积的黄金时间而影响沉积的效果。
所以在环境温度较低的地方,也要注意清洗水的温度。
(5)电路板整孔剂的使用温度、浓度与时间药液的温度有着较严格的要求,过高的温度会造成整孔剂的分解,使整孔剂的浓度变低,影响整孔的效果,其明显的特征是在孔内的玻璃纤维布处出现点状空洞。
只有药液的温度、浓度与时间妥善的配合,才能得到良好的整孔效果,同时又能节约成本。
药液中不断累积的铜离子浓度,也必须严格控制。
(6)电路板还原剂的使用温度、浓度与时间还原的作用是去除去钻污后残留的锰酸钾和高锰酸钾,药液相关参数的失控都会影响其作用,其明显的特征是在孔内的树脂处出现点状空洞。
PCB制程中金属化孔镀层空洞的成因及改善_程骄

PCB制程中金属化孔镀层空洞的成因及改善程 骄 李卫明 刘敏然(广东东硕科技有限公司,广东 广州 510288)摘 要 文章从印制线路板的生产流程和工艺参数等方面,结合切片观察的手段,浅析了金属化孔镀层空洞的形成原因。
研究表明:半固化片的型号、含胶量及填料的比例与芯板质量有很大关联,影响着层压和钻孔工序的板件质量;沉铜和电镀工序的工艺参数、周边辅助设施的工作状况及加工过程中的时效是影响镀层空洞的主要因素。
针对每一个异常点,找到缺陷的形成原因,对工艺流程进行有效的改进,有的放矢的起到预防措施,最终达到改善镀层质量,提高产品的合格率,对提高线路板可靠性具有重要的意义。
关键词 空洞;化学沉铜;电镀;钻孔中图分类号:TN41 文献标识码:A 文章编号:1009-0096(2013)08-0021-03Research on the causes & control of through-holevoids for PCB processCHENG Jiao LI Wei-Ming LIU Min-RanAbstract Voids in plated through-holes are caused by many different processing problems. This paper will show how to identify rim voids by PCB production process & parameter with micro section observation. The results indicate that stronger correlation existed in core board between the proportion of rubber polymer to fi ller and type of PP, which could infl uence the quality of lamination and drill. The primary reason of VPTH formed was by process parameter, the condition of assisting machine and processing time for electroless and electroplate process. The reason of defect was found for every abnormal board. Effective improvement measures not only had a defi nite object in view of prevention measures, but also improved quality and percent of certifi ed products, this measure had the vital signifi cance to improve reliability of printed circuit board.Key words Void PTH; Electroless Copper Plating; Electroplating; Drill现代印制电路板设计要求向高密度、细线条、微孔径的多层板发展,因此金属化孔质量将直接关系到线路板的质量及可靠性,而过孔不通会直接导致成品板的电气互连失败,从而使成品板件由于镀层空洞缺陷而报废。
孔壁分离的原因
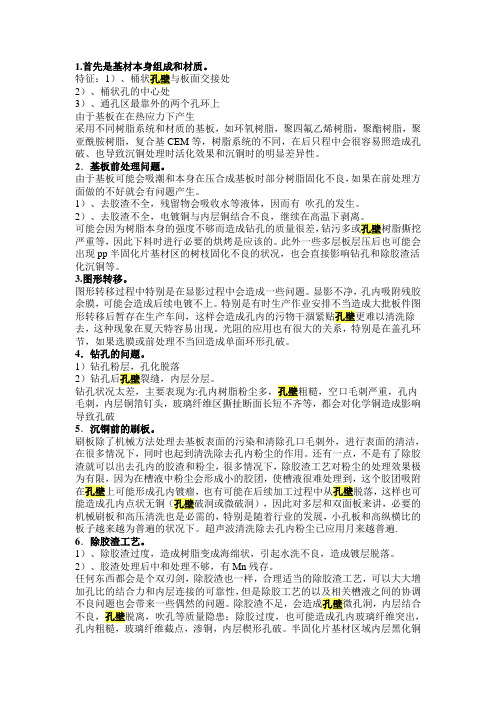
1.首先是基材本身组成和材质。
特征:1)、桶状孔壁与板面交接处2)、桶状孔的中心处3)、通孔区最靠外的两个孔环上由于基板在在热应力下产生采用不同树脂系统和材质的基板,如环氧树脂,聚四氟乙烯树脂,聚酯树脂,聚亚酰胺树脂,复合基CEM等,树脂系统的不同,在后只程中会很容易照造成孔破、也导致沉铜处理时活化效果和沉铜时的明显差异性。
2.基板前处理问题。
由于基板可能会吸潮和本身在压合成基板时部分树脂固化不良,如果在前处理方面做的不好就会有问题产生。
1)、去胶渣不全,残留物会吸收水等液体,因而有吹孔的发生。
2)、去胶渣不全,电镀铜与内层铜结合不良,继续在高温下剥离。
可能会因为树脂本身的强度不够而造成钻孔的质量很差,钻污多或孔壁树脂撕挖严重等,因此下料时进行必要的烘烤是应该的。
此外一些多层板层压后也可能会出现pp半固化片基材区的树枝固化不良的状况,也会直接影响钻孔和除胶渣活化沉铜等。
3.图形转移。
图形转移过程中特别是在显影过程中会造成一些问题。
显影不净,孔内吸附残胶余膜,可能会造成后续电镀不上。
特别是有时生产作业安排不当造成大批板件图形转移后暂存在生产车间,这样会造成孔内的污物干涸紧贴孔壁更难以清洗除去,这种现象在夏天特容易出现。
光阻的应用也有很大的关系,特别是在盖孔环节,如果选膜或前处理不当回造成单面环形孔破。
4.钻孔的问题。
1)钻孔粉层,孔化脱落2)钻孔后孔壁裂缝,内层分层。
钻孔状况太差,主要表现为:孔内树脂粉尘多,孔壁粗糙,空口毛刺严重,孔内毛刺,内层铜箔钉头,玻璃纤维区撕扯断面长短不齐等,都会对化学铜造成影响导致孔破5.沉铜前的刷板。
刷板除了机械方法处理去基板表面的污染和清除孔口毛刺外,进行表面的清洁,在很多情况下,同时也起到清洗除去孔内粉尘的作用。
还有一点,不是有了除胶渣就可以出去孔内的胶渣和粉尘,很多情况下,除胶渣工艺对粉尘的处理效果极为有限,因为在槽液中粉尘会形成小的胶团,使槽液很难处理到,这个胶团吸附在孔壁上可能形成孔内镀瘤,也有可能在后续加工过程中从孔壁脱落,这样也可能造成孔内点状无铜(孔壁破洞或微破洞),因此对多层和双面板来讲,必要的机械刷板和高压清洗也是必需的,特别是随着行业的发展,小孔板和高纵横比的板子越来越为普遍的状况下。
建筑施工漏浆、孔洞、连接缺陷的常用处理措施

建筑施工漏浆、孔洞、连接缺陷的常用处理措施一、建筑外观质量缺陷的原因混凝土本身是一种多相(体积比气相2~5%、液相13~18%、固相77~85%),多孔(凝胶孔、层间孔、毛细孔、气泡粗孔和裂缝等)存在内部原生缺陷的不均匀不连续体,另外,由于所用原材料质量的波动、计量的误差,搅拌不充分而易使新拌砼出现分层离析、泌水、干涩、板结等和易性不良的特征;又由于施工过程中模板和钢筋制作的偏差,以及浇注、振捣、成型、养护等施工操作的不当,都可以引起现浇结构的外观质量缺陷。
砌体和二次构件是在一结构施工完成验收后进行的下一道工序内容,表面污染是各工种穿插施工过程中的接触产生的污染。
构造柱跑浆是模板加固不到位以及胶带漏贴等。
尺寸偏差是构件加固过紧和定位措施不足等原因造成。
墙体顶部塞缝高度不统一是施工过程工人对墙体高度皮数杆排列不合理造成的。
二、建筑外观质量缺陷处理方法根据国家标准GB50204-2015《混凝土结构工程施工质量验收规范》第八章第一节之规定,混凝土现浇结构外观质量缺陷划分为九种情况(见下表)。
(一)、建筑混凝土峰窝(含麻面)混凝土拆模之后,表面局部漏浆、粗糙、存在许多小凹坑的现象,称之为麻面;若麻面现象严重,混凝土局部酥松、砂浆少、大小石子分层堆积,石子之间出现状如蜜峰窝的窟窿,称之为蜂窝缺陷。
从工程实践中总结出麻面蜂窝与混凝土强度的下降级别如下:A级,混凝土表面有轻微麻面,浇注层间存在少量间断空隙,敲击时粗骨料不下落,此时相当于强度比率为80%;B级,混凝土表面有粗骨料,凸凹不平,粗骨料之间存在空隙,但内部没有大的空隙,粗骨料之间相互结合较牢,敲击时没有连续下落的现象,此时相当于强度比率为60%~80%;C级,混凝土内部有很多空隙,粗骨料多外露,粗骨料周围及粗骨之间灰浆黏结很少,敲击时卵石连续下落,存在空洞,有少量钢筋直接与大气接触,此时相当于强度比率在30%以下。
1、原因分析(1)模板安装不密实,局部漏浆严重。
孔壁镀层空洞

孔壁镀层空洞
孙亚林
【期刊名称】《印制电路信息》
【年(卷),期】2001(000)007
【摘要】@@ 孔壁镀层空洞是印刷电路板(双面、多层和盲孔板)金属化孔最常见的问题之一,也是印刷电路板报废项目之一,因此解决和控制印刷电路板孔壁镀层空洞是多数印刷电路板厂家重点控制的内容之一,但是造成印刷电路板孔壁镀层空洞的原因很多,只有正确地判断孔壁镀层空洞的类型才能更及时有效地找出解决方案.【总页数】3页(P45-47)
【作者】孙亚林
【作者单位】西安631所
【正文语种】中文
【中图分类】TN41
【相关文献】
1.浅谈孔壁镀层空洞的成因及对策 [J], 高勇
2.多层印制板金属化孔镀层空洞研究 [J], 迟海蓉
3.PCB制程中金属化孔镀层空洞的成因及改善 [J], 程骄;李卫明;刘敏然
4.印制板孔内镀层空洞原因分析 [J], 卢大伟
5.论孔化电镀后孔壁出现空洞的原因 [J], 徐自金
因版权原因,仅展示原文概要,查看原文内容请购买。
镀层的针孔、麻点与孔隙率
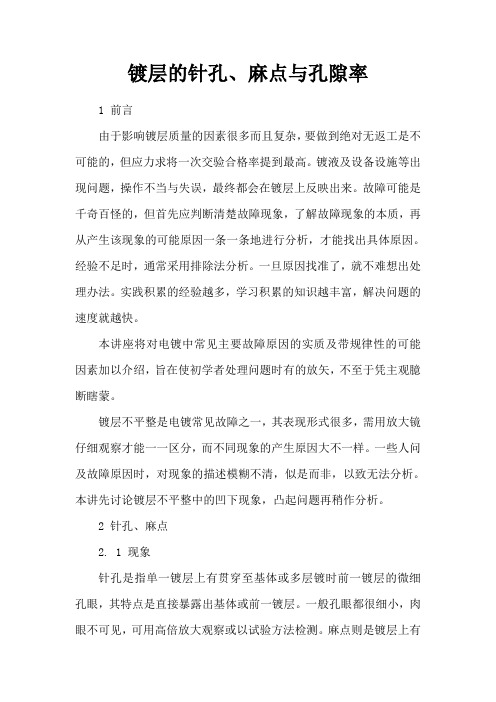
镀层的针孔、麻点与孔隙率1 前言由于影响镀层质量的因素很多而且复杂,要做到绝对无返工是不可能的,但应力求将一次交验合格率提到最高。
镀液及设备设施等出现问题,操作不当与失误,最终都会在镀层上反映出来。
故障可能是千奇百怪的,但首先应判断清楚故障现象,了解故障现象的本质,再从产生该现象的可能原因一条一条地进行分析,才能找出具体原因。
经验不足时,通常采用排除法分析。
一旦原因找准了,就不难想出处理办法。
实践积累的经验越多,学习积累的知识越丰富,解决问题的速度就越快。
本讲座将对电镀中常见主要故障原因的实质及带规律性的可能因素加以介绍,旨在使初学者处理问题时有的放矢,不至于凭主观臆断瞎蒙。
镀层不平整是电镀常见故障之一,其表现形式很多,需用放大镜仔细观察才能一一区分,而不同现象的产生原因大不一样。
一些人问及故障原因时,对现象的描述模糊不清,似是而非,以致无法分析。
本讲先讨论镀层不平整中的凹下现象,凸起问题再稍作分析。
2 针孔、麻点2. 1 现象针孔是指单一镀层上有贯穿至基体或多层镀时前一镀层的微细孔眼,其特点是直接暴露出基体或前一镀层。
一般孔眼都很细小,肉眼不可见,可用高倍放大观察或以试验方法检测。
麻点则是镀层上有未贯穿至基体或前一镀层的凹下坑点。
其特点是凹下部分也有镀层,但比其他部分的镀层薄而形成凹坑。
大的麻点肉眼即可见,细小麻点则要放大后才能察觉。
2. 2 主要成因2. 2. 1 气体针孔麻点当镀液阴极电流效率较低,易发生析氢副反应,且镀液润湿性不足,镀件上产生的氢气小泡不能及时逸出而滞留在工件表面时,会出现两种情况:(1)氢气泡一直滞留。
电沉积之初,若有一个小的氢气泡滞留于工件某一点上,且一直滞留于该点,直至电沉积结束,因氢气小泡为电的绝缘体,主盐金属离子无法穿透气泡放电还原,则该处始终无金属沉积,形成一个小孔眼,成为针孔。
(2)氢气泡间歇滞留。
当工件上产生的氢气小泡只间歇性地滞留于工件上某一点上,即一会儿滞留于该点,一会儿又逸出,如此反复,则滞留期间该点上无电沉积发生,而逸出后一段时间内又发生电沉积。
孔壁粗糙度解决处理方案
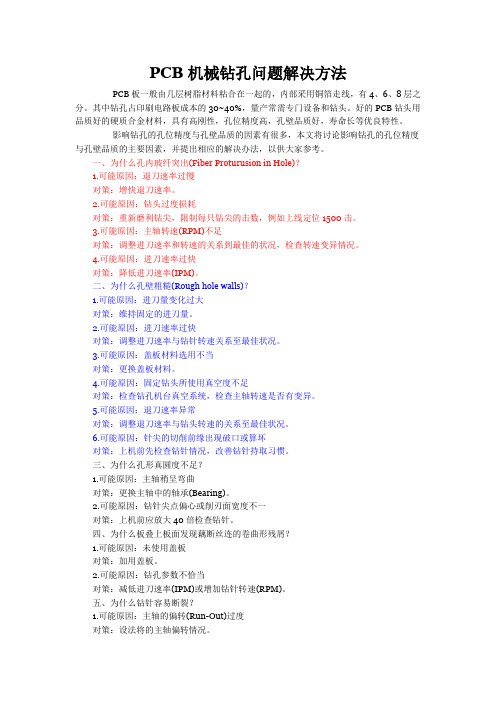
PCB机械钻孔问题解决方法PCB板一般由几层树脂材料粘合在一起的,内部采用铜箔走线,有4、6、8层之分。
其中钻孔占印刷电路板成本的30~40%,量产常需专门设备和钻头。
好的PCB钻头用品质好的硬质合金材料,具有高刚性,孔位精度高,孔壁品质好,寿命长等优良特性。
影响钻孔的孔位精度与孔壁品质的因素有很多,本文将讨论影响钻孔的孔位精度与孔壁品质的主要因素,并提出相应的解决办法,以供大家参考。
一、为什么孔内玻纤突出(Fiber Proturusion in Hole)?1.可能原因:退刀速率过慢对策:增快退刀速率。
2.可能原因:钻头过度损耗对策:重新磨利钻尖,限制每只钻尖的击数,例如上线定位1500击。
3.可能原因:主轴转速(RPM)不足对策:调整进刀速率和转速的关系到最佳的状况,检查转速变异情况。
4.可能原因:进刀速率过快对策:降低进刀速率(IPM)。
二、为什么孔壁粗糙(Rough hole walls)?1.可能原因:进刀量变化过大对策:维持固定的进刀量。
2.可能原因:进刀速率过快对策:调整进刀速率与钻针转速关系至最佳状况。
3.可能原因:盖板材料选用不当对策:更换盖板材料。
4.可能原因:固定钻头所使用真空度不足对策:检查钻孔机台真空系统,检查主轴转速是否有变异。
5.可能原因:退刀速率异常对策:调整退刀速率与钻头转速的关系至最佳状况。
6.可能原因:针尖的切削前缘出现破口或算坏对策:上机前先检查钻针情况,改善钻针持取习惯。
三、为什么孔形真圆度不足?1.可能原因:主轴稍呈弯曲对策:更换主轴中的轴承(Bearing)。
2.可能原因:钻针尖点偏心或削刃面宽度不一对策:上机前应放大40倍检查钻针。
四、为什么板叠上板面发现藕断丝连的卷曲形残屑?1.可能原因:未使用盖板对策:加用盖板。
2.可能原因:钻孔参数不恰当对策:减低进刀速率(IPM)或增加钻针转速(RPM)。
五、为什么钻针容易断裂?1.可能原因:主轴的偏转(Run-Out)过度对策:设法将的主轴偏转情况。
- 1、下载文档前请自行甄别文档内容的完整性,平台不提供额外的编辑、内容补充、找答案等附加服务。
- 2、"仅部分预览"的文档,不可在线预览部分如存在完整性等问题,可反馈申请退款(可完整预览的文档不适用该条件!)。
- 3、如文档侵犯您的权益,请联系客服反馈,我们会尽快为您处理(人工客服工作时间:9:00-18:30)。
浅谈孔壁镀层空洞的成因及对策
关键词:化学沉铜、孔壁镀层空洞、图形电镀、全板电镀
摘要:化学沉铜是印制电路板孔金属化过程中,一个非常重要的步骤,其目的是在孔壁以及铜面上,形成极薄的导电铜层,为后面的电镀做准备。
而孔壁镀层的空洞是印制电路板孔金属化常见的缺陷之一,也是易引起印制电路板批量报废的项目之一,因此解决印制电路板镀层空洞问题是印制板厂家重点控制的一项内容,但由于造成其缺陷的原因多种多样,只有准确的判断其缺陷的特征才能有效的找出解决的方案。
1、PTH造成的孔壁镀层空洞
PTH造成的孔壁镀层空洞主要是点状的或环状的空洞,具体产生的原因如下:
(1)沉铜缸铜含量、氢氧化钠与甲醛的浓度
铜缸的溶液浓度是首先要考虑的。
一般来说,铜含量、氢氧化钠与甲醛的浓度是成比例的,当其中的任何一种含量低于标准数值的10%时都会破坏化学反应的平衡,造成化学铜沉积不良,出现点状的空洞。
所以优先考虑调整铜缸的各药水参数。
(2)槽液的温度
槽液的温度对溶液的活性也存在着重要的影响。
在各溶液中一般都会有温度的要求,其中有些是要严格控制的。
所以对槽液的温度也要随时关注。
(3)活化液的控制
二价锡离子偏低会造成胶体钯的分解,影响钯的吸附,但只要对活化液定时的进行添加补充,不会造成大的问题。
活化液控制的重点是不能用空气搅拌,空气中的氧会氧化二价锡离子,同时也不能有水进入,会造成SnCl2的水解。
(4)清洗的温度
清洗的温度常常被人忽视,清洗的最佳温度是在20℃以上,若低于15℃就会影响清洗的效果。
在冬季的时候,水温会变的很低,尤其是在北方。
由于水洗的温度低,板子在清洗后的温度也会变的很低,在进入铜缸后板子的温度不能立刻升上来,会因为错过了铜沉积的黄金时间而影响沉积的效果。
所以在环境温度较低的地方,也要注意清洗水的温度。
(5)整孔剂的使用温度、浓度与时间
药液的温度有着较严格的要求,过高的温度会造成整孔剂的分解,使整孔剂的浓度变低,影响整孔的效果,其明显的特征是在孔内的玻璃纤维布处出现点状空洞。
只有药液的温度、浓度与时间妥善的配合,才能得到良好的整孔效果,同时又能节约成本。
药液中不断累积的铜离子浓度,也必须严格控制。
(6)还原剂的使用温度、浓度与时间
还原的作用是去除去钻污后残留的锰酸钾和高锰酸钾,药液相关参数的失控都会影响其作用,其明显的特征是在孔内的树脂处出现点状空洞。
(7)震荡器和摇摆
震荡器和摇摆的失控会造成环状的空洞,这主要是由于孔内的气泡未能排除,以高厚径比的小孔板最为明显。
其明显的特征是孔内的空洞对称,而孔内有铜的部分铜厚正常,图形电镀层(二次铜)包裹全板镀层(一次铜)。
2、图形转移造成的孔壁镀层空洞
图形转移造成的孔壁镀层空洞主要是孔口环状和孔中环状的空洞,具体产生的原因如下:
(1)前处理刷板
刷板的压力过大,将全板铜和PTH孔口处的铜层被刷磨掉,使后面的图形电镀无法镀上铜,从而产生孔口环状空洞。
其明显的特征是孔口的铜层渐渐变薄,图形电镀层包裹全板镀层。
所以要通过做磨痕测试,控制刷板压力。
(2)孔口残胶
在图形转移工序对工艺参数的控制非常重要,因为前处理烘干不良、贴膜的温度、压力的不当都会造成孔口的边缘部位出现残胶而导致孔口的环状空洞。
其明显的特征是在孔内的铜层厚度正常,单面或双面孔口处呈现环状空洞,一直延伸到焊盘,断层边缘有明显被蚀刻的痕迹,图形电镀层没有包裹全板(参见图3)。
(3)前处理微蚀
前处理的微蚀量要严格控制,尤其要控制干膜板的返工次数。
主要是孔中部因电镀均匀性的问题镀层厚度偏薄,返工过多会造成全板孔内的铜层减薄,而最终产生孔内中部的环状无铜。
其明显的特征是孔内全板镀层渐渐变薄,图形电镀层包裹全板镀层(参见图4)。
3、图形电镀造成的孔壁镀层空洞
(1)图形电镀微蚀
图形电镀的微蚀量也要严格的控制,其产生的缺陷与干膜前处理微蚀基本相同。
严重时孔壁会大面积无铜,板面上的全板层厚度明显偏薄。
所以要定时测微蚀速率,最好通过进行DOE实验优化工艺参数。
(2)镀锡(铅锡)分散性差
由于溶液性能差或摇摆不足等因素使镀锡的镀层厚度不足,在后面的去膜和碱性蚀刻时把孔中部的锡层和铜层蚀掉,产生环状空洞。
其明显的特征是孔内的铜层厚度正常,断层边缘有明显被蚀刻的痕迹,图形电镀层没有包裹全板(参见图5)。
针对这种情况,可以在镀锡前的浸酸内加一些镀锡光剂,能够增加板子的润湿性,同时加大摇摆的幅度。
4、结论
造成镀层空洞的因素很多,最常见的是PTH镀层空洞,通过控制药水的相关工艺参数能有效的减少PTH镀层空洞的产生。
但其它因素也不能忽视,只有通过细致的观察,了解到产生镀层空洞的原因及缺陷的特点,才能及时有效的解决问题,维护产品的品质。
由于本人的水平经验有限,在此列举了一些平时生产中遇到的实际问题,与同行共享和交流。