4.3.3普通浇注系统设计
注塑模普通浇注系统设计

优点:熔融态的塑料流流经浇口时以较低的速 度、平行均匀地流入型腔,降低了塑件的内应 力和带人空气的可能性,减少了因取向而产生 的翘曲变形。
缺点:成形后去除浇口的工作量大,增加了塑 件成本;沿塑件一侧壁有一比较长的剪切痕, 影响塑件外表的美观。
尺寸设计:
•浇口宽度等于或略大于型腔宽度 •浇口长度L≥1.3mm •浇口深度h≥0.25mm,其深度经 验公式为 h=0.7t
1.5mm。
浇口深度:
h = n ·t
式中 h—侧浇口深度,mm,中小型塑件常用h= 0.5~2mm.大约为制品最大壁厚的1/3~2/3; t—塑件壁厚(mm); n—塑料材料系数.
浇口宽度:
Wn A 30
式中 W—浇口宽度(mm); A—型腔表面积,即塑件外表面面积(mm2) n—塑料材料系数,
侧浇口的改进形式,开设在塑料件断面的边缘。 优点:避免熔体从浇口射出,产生喷射现象。 适用范围:低粘度塑料
④扇形浇口
应用范围:应用大面积薄壁塑件
优点:焙融状的塑料流经过浇口时,在横向得 到更为均匀的分配,可降低塑件的内应力和减 少带入空气的可能性.避免塑件产生变形和气 泡。
缺点:沿塑件一侧壁有比较长的剪切痕,影响 塑件外表的美观;成形后去除浇口的工作量大, 增加了塑件成本。
流动补缩; ④避免高压熔体对型芯和嵌件产生冲击,防止变形和位移, ⑤浇注系统凝料脱出方便可靠,易与塑料件分离或切除整修
容易,且外观无损伤 ⑥熔合缝位置须合理安排,必要时配以冷料井或溢料槽; ⑦尽量减少浇注系统的用料量; ⑧浇注系统应达到所需精度和粗糙度,其中浇口须有IT8级
以上精度。
3.3 普通流道浇注系统
多浇口
点浇口在成型大型薄壁塑件应用时,可采用多只点浇口
浇注系统设计
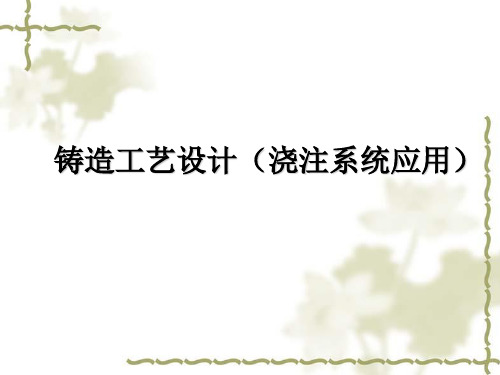
浇注系统设计
一、浇注系统构成 浇注系统由浇口杯(外浇口)、直浇道、横浇道和内浇道等构成。其构造见下图
1—浇口杯;2—直浇道;3—横浇道;4—内浇道
注意点:内浇道形状(提议使用Ⅰ型) ❖ Ⅰ型扁平内浇道易于清理,能提升横浇道旳挡渣效果。当使用宽度受限制时,可
用Ⅱ型。 ❖ Ⅲ型内浇道用于铸件垂直壁处或不宜冲刷处。 ❖ Ⅳ型和Ⅴ型内浇道用于需内浇道凝固较慢旳场合,其清理较困难。 ❖ Ⅵ型内浇道冷却较快、轻易清理。
老式浇系极难胜任三大功能旳两项:挡渣和降低紊流
浇注系统旳主要功能:1. 提供金属液进入型腔旳通道;2. 金属液尽量平稳;3.阻止渣/砂和其他反应产物进入型腔;
过滤器应用
带过滤器旳浇系
The controlling crosssection阻流截面
Downsprue : Runner Bar
:
Runner Bar : Ingate
带有过滤器旳浇注系统
❖ 内浇道和横浇道高度比
1. 内浇道形状扁平梯型;
2. H横=(5-6)H内—预防吸动作用产生杂质进型腔(针对放置在横浇道底部) ❖ 内浇道与横浇道连接方式
1. 放置在横浇道底部(在同一平面)---合用于封闭式浇注系统 2. 放置在横浇道顶部(不在同一平面)—封闭-开放式浇注系统
又称“缓流封闭式”。故充型旳平稳性及对型腔旳冲刷力都好于封闭式; ❖ 用于各类灰铸铁件及球铁件
浇注系统设计
(4) 封闭- 开放式---(推荐使用) ❖ F杯>F直<F横<F内 ❖ F杯>F直>F集渣包出口<F横后<F内 ❖ F直>F阻<F横后<F内 ❖ F直>F阻<F内<F横 ❖ 阻流截面设在直浇道下端,或在横浇道中,或在集渣包出口处,或在内浇道之
浇注系统的设计

浇注系统的设计(总8页)--本页仅作为文档封面,使用时请直接删除即可----内页可以根据需求调整合适字体及大小--浇注系统设计1 浇注系统的设计要求浇注系统是指在模具中,从注射机喷嘴进人模具处开始到型腔为止的塑料熔体流动通道,分为普通浇注系统和无流道浇注系统。
浇注系统的作用是使塑料熔体平稳有序地填充到型腔中,并在塑料填充和凝固的过程中,把注射压力充分传递到型腔的各个部位,以获得组织致密、外形清晰的塑件。
普通浇注系统(下称浇注系统)一般由主流道、分流道、浇口、冷料井4 部分组成。
单型腔模具有时可省去分流道和冷料井,只有圆锥形的主流道通过浇口和塑件相连。
浇注系统的设计非常重要,设计合理与否对塑件的内在性能质量、尺寸精度、外观质量以及模具结构、成型效率、塑料利用率等都有较大影响。
浇注系统进行设计时,一般应遵循以下基本原则。
( l )适应塑料的成型工艺性能。
了解塑料的成型工艺性能,如塑料熔体的流动特性,温度、剪切速度对猫度的影响,型腔内的压力周期等,使浇注系统适应于所用塑料的成型特性要求,以保证塑件质量。
( 2 )结合型腔布局考虑。
尽可能保证在同一时间内塑料熔体充满各型腔,为此,尽最采用平衡式布局.以便设置平衡式分流道;型腔布t 和浇口开设部位力求沿模具轴线对称,避免在模具的单面开设浇口,以防止模具承受偏载而产生溢料现象;使型腔及浇注系统在分型面上投影的中心与注射机锁模机构的锁模力作用中心相重合.以使锁模可靠、锁模机构受力均匀;型腔排列尽可能紧凑,以减小模具外形尺寸。
( 3 )热量及压力损失要小。
应该尽量缩短浇注系统的流程,特别是对于较大的模具型腔,增加断面尺寸,尽量减少弯折,控制表面粗糙度。
( 4 )有利于型腔中气体的排出。
浇注系统应能顺利地引导塑料熔体充满型腔的各个角落,使型腔及浇注系统中的气体有序排出,保证在充填过程中不产生紊流,避免因气体积存而引起凹陷、气泡、烧焦等塑件成型缺陷。
( 5 )防止型芯变形和嵌件位移。
浇注系统设计方案

流道设计的优化与改进
减少流道阻力
采用大截面、短流程的流道
防止金属液氧化
采用密封式或保护气氛浇注系 统
提高充型能力
采用多浇口、分流道设计
降低能耗
采用热平衡设计,减少热量损 失
04 模具设计
模具材料的选用
01
02
03
耐热性
选择耐热性好的材料,如 钢材、铝合金等,以确保 模具在高温下件结构、生产批量、合金种类、浇注条件
适用场合
直浇道适用于中小型铸件的大批量生产;横浇道适用于大型铸件的 单件、小批量生产;内浇道适用于各种铸件
流道尺寸与形状的确定
流道截面积
满足金属液的流量要求,保证充 型能力
流道长度与宽度
根据铸件大小、浇注温度和速度确 定
流道高度
根据金属液的静压力头和浮力确定
调整工艺参数
调整浇注温度、注射压力和注射速度等工艺 参数,提高浇注质量和效率。
改进模具结构
优化模具冷却、排气和顶出机构,提高模具 使用寿命。
采用先进的浇注技术
如应用热流道技术、顺序阀控制等,提高生 产效率和浇注质量。
浇注系统方案的经济性分析
模具成本
生产成本
评估不同浇注系统方案对模具材料、加工 和装配成本的影响。
排溢系统设计
设计有效的排溢系统,以 排除模具内的气体和溢出 的金属液,防止产品产生 气孔和浇不足等缺陷。
模具冷却系统的设计
冷却水道设计
合理布置冷却水道,以提高模具的冷 却效果,减少冷却时间,提高生产效 率。
冷却介质选择
冷却水道密封
确保冷却水道的密封性,防止冷却液 泄漏,以保证生产安全和产品质量。
根据模具材料和使用条件,选择合适 的冷却介质,如水、油等。
浇注系统设计
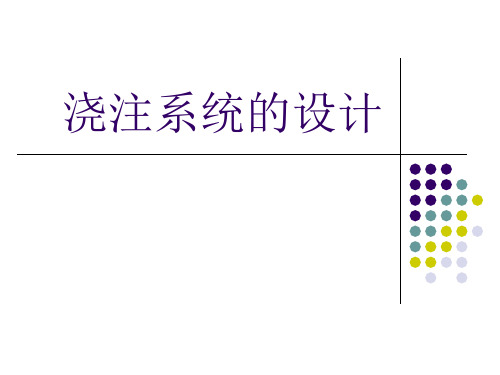
结构形状:
圆形热损失最小、流动平稳,但工艺复杂; 一般采用:高/宽=1.2-1.5的梯形。
扩张式浇注系统(横浇道并不立即被充满)
内 浇 道 流 速 V内
与h有关
(横浇道中的液面高度)
横浇道未充满前
与H有关
(浇口杯中液面算起的压力头)
横浇道充满后
[由于h远小于H,所以可把合金液进入型腔的初速度控制在较小的范围内] 避免喷溅或冲击型壁 避免氧化杂质和气孔缺陷
雷诺数Re
vL Re
ρ、μ为流体密度和粘度;v、L为流场的 特征速度和特征长度,内流问题则取通道 内平均流速和通道直径。
轻合金优质铸件:当Re<20000时,液流表面的氧化膜不会破 碎,如果将Re控制在4000-10000范围内时,就可符合生产 铝合金和镁合金优质铸件的要求; 铝合金铸件:允许的最大雷诺数,在直浇道内应不超过 10000,横浇道内不超过7000,内浇道内不超过1100,型腔 内不超过280。
内浇道
主要作用: 控制充型速度和方向 分配液态金属 调节局部温度场和凝固顺序 提供部分补缩金属液来源
内浇道流量分配
一般条件下,远离直浇道流量大。
浇不足,冷隔,过热 破坏凝固次序 氧化,缩松和裂纹
措 施
尽可能将内浇道设置在横浇道的对称位置; 将横浇道断面设计成顺着液流方向逐渐缩小的形式; 设置浇口窝。
内浇道的吸动作用
吸动作用越大,横浇道越难挡渣。
采用较高的横浇道和较低的内浇道
1.第一个内浇道不要离直浇道太近;最后一个内浇道 与横浇道末端要有一定的距离。 2.内浇道一般应置于横浇道的中部(中置式);轻合 金金属型铸造中,上置式的比较多用。 3.液态金属的导入位置是控制铸件凝固顺序的一个重 要措施。
浇注系统设计

例三:圆形塑料薄片变形
如厚1.5mm,直径100mm的PP圆薄片,采用中心浇口 时,出现翘曲。
一般用扇形浇口或多点浇口。
.
43
例四:对有金属嵌件的制品
利用取向、收缩包紧塑件,注意收缩引起开裂
.
44
4. 防止型芯变形
.
45
4.4 浇口平衡
4.4.1 非平衡布置的相同多型腔的浇口平衡 使熔体向各型腔充模工艺条件一致是致关重要的问题。 基本要求:
点浇口
1×105s-1
2. 根据剪切速率的计算体积流率Q
圆形流道和浇口
矩形流道和浇口
Q
R3
.
4
Q
Wh
2
.
6
.
52
3. 由适当的γ和Q查γ-Q-Rn曲线求得当量半径
.
53
4.流道截面当量半径计算
Rn
3
2 A2 L
Rn——假想的圆形流道的当量半径,cm L——实际流道截面的周边长,cm
c直锥孔 d球形底锥孔
.
27
基本尺寸
浇口圆柱孔长度: L=0.5~0.75mm
浇口直径常见为0.5~1.8mm,经验公式:
dnc4 A
.
3 d2Q 3 105s1
式 c——壁厚系数,随塑件壁厚增加而增加,由表(3.3-2) 查得
A——塑料件的表面积
点浇口引导部分长度
一般15~25mm
浇注系统——是熔体从注塑机喷嘴到模具型腔 所经过的一个完整输送通道。
浇注系统作用: 输送熔体,传质、传压和传热。 1. 组成和作用
主流道 分流道 冷料井 浇口
.
3
2. 设计原则
(1)浇注系统的分流道一 般在分型面上;
浇注系统设计

浇注系统设计随着制造业的不断发展,越来越多的工厂需要使用浇注系统来制造产品。
浇注系统是将液体材料注入模具中,然后在模具中凝固成形的一种生产工艺。
浇注系统设计的好坏直接影响到产品质量和生产效率。
浇注系统的组成浇注系统由喷枪、管道、泵、控制器、储液罐等组成。
其中,喷枪是将液体材料喷入模具中的关键部件,而泵和控制器则是控制喷枪运作的核心部件。
浇注系统的设计要点1. 选择合适的材料在进行浇注系统设计之前,需要根据生产需求选择合适的浇注材料。
不同的浇注材料具有不同的流动性和凝固性,因此需要根据具体情况选择合适的材料。
2. 设计合适的喷嘴喷嘴是浇注系统中最重要的部件之一。
它的质量直接影响到产品的质量和生产效率。
合适的喷嘴应该具有以下特点:1)耐磨性强,能够经受长时间的使用和摩擦。
2)喷嘴的通径应该与浇注材料的流动性相适应,既不能过大也不能过小。
3)喷嘴的位置应设计在模具的合适位置,能够充分覆盖到整个模具。
3. 优化管道设计在进行浇注系统设计时,合理的管道布局能够有效地减小材料的阻力和浪费,提高浇注系统的效率。
合适的管道布局还可以减少对材料的污染和损坏,延长浇注系统的使用寿命。
4. 选择合适的控制器浇注系统控制器是控制浇注系统的核心部件。
合适的控制器能够确保浇注系统的正常运作,避免材料浪费和设备故障。
在进行控制器选择时,需要考虑以下因素:1)控制器的输出功率适应所需的浇注速度和压力。
2)控制器的控制方式能够满足生产需求。
3)控制器的调整范围适应材料的不同流动性和凝固性。
5. 设计适当的储液罐储液罐是存储浇注材料的容器。
合适的储液罐设计能够保证材料的质量和数量。
在进行储液罐设计时,需要考虑以下因素:1)储液罐的大小应根据生产需求确定。
2)储液罐的材质应能够耐受浇注材料的腐蚀和压力。
3)储液罐的密封性应优良,能够避免材料泄漏和污染。
浇注系统的优点浇注系统具有以下优点:1. 生产效率高浇注系统可以实现大规模、连续、高速的生产,提高生产效率。
3.3 浇注系统设计(3.3.1分类)

中总截面积最小的是内 浇道,即内浇道成为系统
中的阻流断面。
F直>F 横> F内
3.3 浇注系统设计
3.3.1 浇注系统的基本类型及选择
横浇道充满是挡渣的必要条件 封闭式浇注系统优点: (1)挡渣效果好 1 (2)金属液的消耗量少 缺点: 金属液进入型腔的线速度高,易冲坏铸型,并易产生 飞溅,使金属液氧化。 适用:中小型铸铁件。对易氧化的有色件、压头大的 铸件、柱塞包浇注的铸钢件一般不宜采用。
3.3.1 浇注系统的基本类型及选择
二、按内浇道在铸件上相对位置高低分类 4. 阶梯式浇注系统 实现分层引注结构设计: 1)在金属液进入分配直浇道以前设置阻流断面 2)加大分配直浇道尺寸或改变其结构形状
3.3.1 浇注系统的基本类型及选择
二、按内浇道在铸件上相对位置高低分类 4. 阶梯式浇注系统
3.3.1 浇注系统的基本类型及选择
二、按内浇道在铸件上相对位置高低分类 4. 阶梯式浇注系统 保证阶梯式浇注系统发挥良好效果的关键:各层 内浇道自下而上逐层地接替使用。 保证内浇道分层引入金属液的条件:分配直浇道在 其最上层内浇道工作以前不应充满,其中 金属液的有效压头h有效<两层内浇道之间的距离H0。 或者 内浇道中线以上的分配直浇道中的自由液面h自由< H0。 ——这也是阶梯式浇注系统设计的关键所在。
图3.42 阶梯式浇注系统
3.3.1 浇注系统的基本类型及选择
适用: 中大型较高的厚壁铸件;结构复杂件;易氧化 有色件;铸钢件。
3.3.1 浇注系统的基本类型及选择
二、按内浇道在铸件上相对位置高低分类 2. 底注式浇注系统
牛角浇口:避免旋转,铸齿齿轮和有砂 芯的盘形件、有色小件;反牛角避免“喷泉”
浇注系统设计.

沖擊型澆口將進澆的熔膠導向一金屬面,以釋除應力, 可穩定塑流,避免噴流。 重疊式澆口(overlap gate) 和潛伏式澆口(submarine gate)可設計成沖擊型澆口。
使用沖擊型澆口以避免噴流
差的 Poor
好的 Good
使用沖擊型澆口以避免噴流
差的 Poor
好的 Good
material constant 0.6 for PE, PS 0.7 for POM, PP 0.75 for ABS 0.8 for CA, PMMA, PA , PC 0.9 for PVC
澆口井 Dimple
d : 4~10 h : 0.75 (t<0.75)
t (0.75≤t≤1.5) 0 (t>1.5)
加工、鉗工和品管的責任是按圖施工和品管,並且反馈設計合 理化的意見。
這樣經年累月下來,一競爭力不斷增強的模具/注塑廠將脫穎而 出,並且繼續領袖群倫。
模具設計圖
徐昌煜: 製圖標準要及早訂定,並且不斷的合理化,這一標準 是相關專業人員的官方語言(official language),工程語言以簡 明為要,這要靠大家不斷的探討更新,才能夠不斷精進,當精 益求精成為模具廠的文化時,此一模具廠的脫穎而出,進而登 峰造極,必然是指日可待的了!
澆注系統設計流程
(徐昌煜)
產品(制件)設計 (Part Design) 模穴(型腔)設計 (Cavity Design) 澆口設計 (Gate Design) 流道設計 (Runner Design) 噴嘴設計 (Nozzle Design)
澆注系統檢查點
(邱明正提供)
1. 定位環尺寸大小是否合理 2. 注口襯套選取是否合理 3. 進澆位置是否合理 4. 流道直徑設計是否合理 5. 澆口尺寸大小及形式是否合理
- 1、下载文档前请自行甄别文档内容的完整性,平台不提供额外的编辑、内容补充、找答案等附加服务。
- 2、"仅部分预览"的文档,不可在线预览部分如存在完整性等问题,可反馈申请退款(可完整预览的文档不适用该条件!)。
- 3、如文档侵犯您的权益,请联系客服反馈,我们会尽快为您处理(人工客服工作时间:9:00-18:30)。
拉料杆尺寸及公差可参考表5-11和表5-12
第四章 塑料注射模的设计和制造
§4.3 普通浇注系统的设计及制造
八、排气系统设计
1.排气系统的设计
问题 目的与要求
2015年9月8日
排气不良所产生的问题
重点和难点
浇口的设计制造 排气系统设计
烧焦
填充不足
阴影
色差
流紋
不熔合
思考与练习
排气不良
短射
脱模不良
气泡
七、冷料穴与拉料杆设计
5.拉料杆的技术要求
问题 目的与要求
2015年9月8日
拉料杆材料:T8A或T10A 热处理:头部HRC50~55 配合:
重点和难点
浇口的设计制造 排气系统设计
拉料杆与推件板:H9/f9(间隙应小于塑料的溢料值) 拉料杆固定部分:H7/m6 表面粗糙度: 配合部分:Ra0.8
思考与练习
重点和难点
浇口的设计制造 排气系统设计
思考与练习
第四章 塑料注射模的设计和制造
§4.3普通浇注系统的设计七、冷料Biblioteka 与拉料杆设计4.无拉料杆冷料穴
问题 目的与要求
2015年9月8日
在主浇道对面的模板上开一锥行凹坑
重点和难点
浇口的设计制造 排气系统设计
思考与练习
第四章 塑料注射模的设计和制造
§4.3普通浇注系统的设计
2015年9月8日
(3)排气槽排气:适用于较大塑件或成型过程 中有大量气体产生的情况。 排气槽应开在型腔最后填 充部位 排气槽不应正对操作工人
重点和难点
浇口的设计制造 排气系统设计
思考与练习
第四章 塑料注射模的设计和制造
§4.3 普通浇注系统的设计及制造
八、排气系统设计
2.引气系统的设计
问题 目的与要求
§4.3 普通浇注系统的设计及制造
八、排气系统设计
1.排气系统的设计
问题 目的与要求
2015年9月8日
(2)顶针排气和模具零件间的配合间隙
重点和难点
浇口的设计制造 排气系统设计
思考与练习
0.04mm
第四章 塑料注射模的设计和制造
§4.3 普通浇注系统的设计及制造
八、排气系统设计
1.排气系统的设计
问题 目的与要求
拉料杆固定在推杆固定板上。
重点和难点
浇口的设计制造 排气系统设计
缺点:凝料推出后不能
自动脱落
思考与练习
第四章 塑料注射模的设计和制造
§4.3普通浇注系统的设计
七、冷料穴与拉料杆设计
问题 目的与要求
2015年9月8日
1.钩形(Z形)拉料杆 不能使用钩形拉杆的例子
重点和难点
浇口的设计制造 排气系统设计
第四章 塑料注射模的设计和制造
2015年9月8日
读书不是为了雄辩和驳斥,
问题 目的与要求
也不是为了轻信和盲从, 而是为了思考和权衡。
——培 根
重点和难点
浇口的设计制造 排气系统设计
思考与练习
第四章 塑料注射模的设计和制造
问题:
问题 目的与要求
2015年9月8日
1.浇口的作用是什么?
重点和难点
浇口的设计制造 排气系统设计
§4.3普通浇注系统的设计
七、冷料穴与拉料杆设计
作用:贮存冷料,拉出凝料。
问题 目的与要求
2015年9月8日
重点和难点
浇口的设计制造 排气系统设计
思考与练习
第四章 塑料注射模的设计和制造
§4.3普通浇注系统的设计
七、冷料穴与拉料杆设计
问题 目的与要求
2015年9月8日
1.钩形(Z形)拉料杆 开模时钩住主浇道凝料并从主浇道中拉出。
问题 目的与要求
2015年9月8日
重点和难点
浇口的设计制造 排气系统设计
思考与练习
拉料杆固定端装在型心固定板上。
常用于弹性较好的塑料件并采用推件板脱模的情况。
第四章 塑料注射模的设计和制造
§4.3普通浇注系统的设计
2015年9月8日
七、冷料穴与拉料杆设计
问题 目的与要求
3
分流锥形拉料杆 拉料杆头部做成锥形
2015年9月8日
大型深壳形塑件包紧型芯形成真空,难以脱 模,需要引气装置。 镶拼式侧隙引气 气阀引气
重点和难点
浇口的设计制造 排气系统设计
思考与练习
第四章 塑料注射模的设计和制造
浇口位置选择
问题 目的与要求
2015年9月8日
重点和难点
浇口的设计制造 排气系统设计
思考与练习
第四章 塑料注射模的设计和制造
浇口位置选择
问题 目的与要求
2015年9月8日
重点和难点
浇口的设计制造 排气系统设计
思考与练习
第四章 塑料注射模的设计和制造
思考与练习:
问题 目的与要求
2015年9月8日
1.什么是浇口,它有什么作用?
重点和难点
浇口的设计制造 排气系统设计
思考与练习
第四章 塑料注射模的设计和制造
浇口位置选择
问题 目的与要求
2015年9月8日
重点和难点
浇口的设计制造 排气系统设计
思考与练习
缩水
表面凹陷
第四章 塑料注射模的设计和制造
§4.3 普通浇注系统的设计及制造
八、排气系统设计
1.排气系统的设计
问题 目的与要求
2015年9月8日
⑴利用模具分型面自然排气 排气间隙以不产生溢料为限,通常为0.03~0.05mm。
重点和难点
浇口的设计制造 排气系统设计
思考与练习
第四章 塑料注射模的设计和制造
思考与练习
第四章 塑料注射模的设计和制造
§4.3普通浇注系统的设计
七、冷料穴与拉料杆设计
2.锥形或沟槽拉料穴
问题 目的与要求
2015年9月8日
适用于弹性较好的塑件成型
重点和难点
浇口的设计制造 排气系统设计
思考与练习
第四章 塑料注射模的设计和制造
§4.3普通浇注系统的设计
七、冷料穴与拉料杆设计
2.带球头拉料杆的冷料穴
2.浇注系统有哪几部分组成?
思考与练习
第四章 塑料注射模的设计和制造
目的与要求:
问题 目的与要求
2015年9月8日
1.要求掌握冷料穴设计原则,并会选择冷料穴 在工件上的位置。
重点和难点
浇口的设计制造 排气系统设计
2.会设计冷料穴,拉料杆。
思考与练习
重点和难点:
实例分析
第四章 塑料注射模的设计和制造