铸造工具模具钢生产的品质控制
铸造生产过程的质量控制
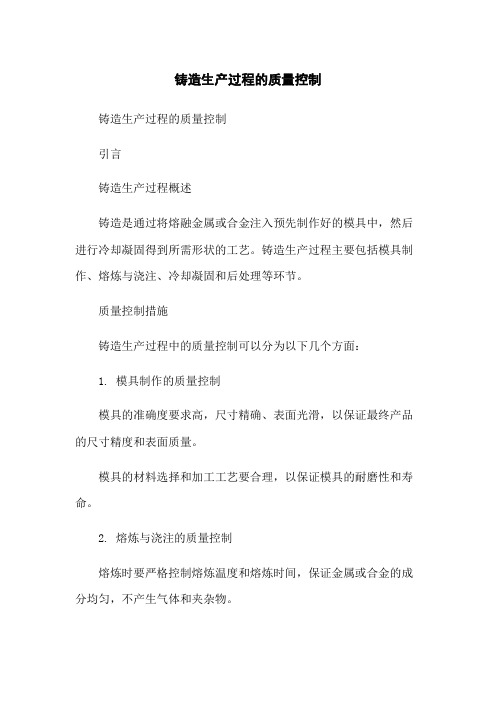
铸造生产过程的质量控制铸造生产过程的质量控制引言铸造生产过程概述铸造是通过将熔融金属或合金注入预先制作好的模具中,然后进行冷却凝固得到所需形状的工艺。
铸造生产过程主要包括模具制作、熔炼与浇注、冷却凝固和后处理等环节。
质量控制措施铸造生产过程中的质量控制可以分为以下几个方面:1. 模具制作的质量控制模具的准确度要求高,尺寸精确、表面光滑,以保证最终产品的尺寸精度和表面质量。
模具的材料选择和加工工艺要合理,以保证模具的耐磨性和寿命。
2. 熔炼与浇注的质量控制熔炼时要严格控制熔炼温度和熔炼时间,保证金属或合金的成分均匀,不产生气体和夹杂物。
浇注时要控制浇注温度和速度,避免产生气孔、夹渣和缩松等缺陷。
3. 冷却凝固的质量控制控制冷却速度和冷却方式,以避免产生组织缺陷,如晶粒过大、晶界不清晰等。
控制凝固过程中的温度变化,以避免产生应力和变形。
4. 后处理的质量控制清理杂质和缺陷,如夹渣、气孔等。
进行热处理、表面处理或机械加工,以改善产品的性能和表面质量。
质量控制方法为了有效控制铸造生产过程中的质量,可以采取以下几种方法:1. 设计质量控制在产品设计阶段,就应考虑产品的铸造性,合理设计产品的几何形状和壁厚,减少可能出现的缺陷和变形。
2. 工艺参数控制对每个工艺环节中的关键参数进行严格控制,如熔炼温度、浇注温度和速度等。
在铸造过程中,通过实时监测温度、压力和流速等参数,进行及时调整和控制。
3. 检测和检验使用各种检测设备和仪器,如X射线探伤仪、超声波检测仪等,对产品进行无损检测,以发现和排除可能存在的缺陷。
进行物理和化学性能的检验,如拉伸试验、硬度测试和成分分析等。
4. 信息化管理建立完善的质量管理体系,进行全过程的质量记录和数据分析,发现问题并采取措施进行改进。
运用信息化技术,实现数据的实时监控和追溯,提高生产过程的透明度和可控性。
结论铸造生产过程的质量控制是确保最终产品质量的重要环节。
通过合理的质量控制措施和方法,可以有效避免铸造过程中可能出现的缺陷和变形,提高产品的质量和性能。
铸钢件质量保证措施
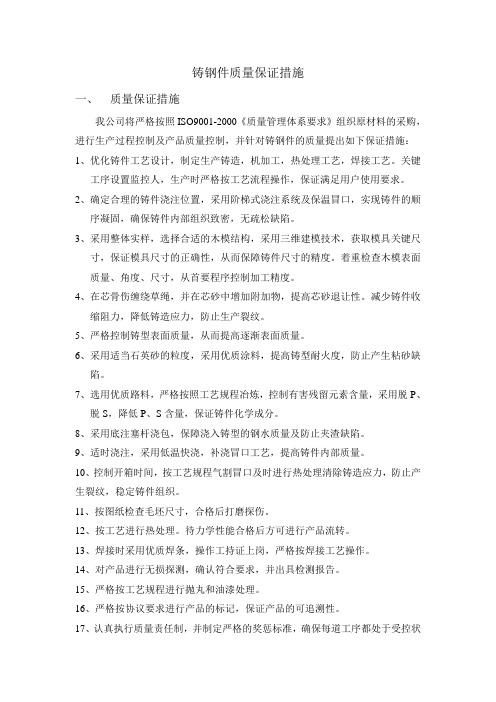
铸钢件质量保证措施一、质量保证措施我公司将严格按照ISO9001-2000《质量管理体系要求》组织原材料的采购,进行生产过程控制及产品质量控制,并针对铸钢件的质量提出如下保证措施:1、优化铸件工艺设计,制定生产铸造,机加工,热处理工艺,焊接工艺。
关键工序设置监控人,生产时严格按工艺流程操作,保证满足用户使用要求。
2、确定合理的铸件浇注位置,采用阶梯式浇注系统及保温冒口,实现铸件的顺序凝固,确保铸件内部组织致密,无疏松缺陷。
3、采用整体实样,选择合适的木模结构,采用三维建模技术,获取模具关键尺寸,保证模具尺寸的正确性,从而保障铸件尺寸的精度。
着重检查木模表面质量、角度、尺寸,从首要程序控制加工精度。
4、在芯骨伤缠绕草绳,并在芯砂中增加附加物,提高芯砂退让性。
减少铸件收缩阻力,降低铸造应力,防止生产裂纹。
5、严格控制铸型表面质量,从而提高逐渐表面质量。
6、采用适当石英砂的粒度,采用优质涂料,提高铸型耐火度,防止产生粘砂缺陷。
7、选用优质路料,严格按照工艺规程冶炼,控制有害残留元素含量,采用脱P、脱S,降低P、S含量,保证铸件化学成分。
8、采用底注塞杆浇包,保障浇入铸型的钢水质量及防止夹渣缺陷。
9、适时浇注,采用低温快浇,补浇冒口工艺,提高铸件内部质量。
10、控制开箱时间,按工艺规程气割冒口及时进行热处理清除铸造应力,防止产生裂纹,稳定铸件组织。
11、按图纸检查毛坯尺寸,合格后打磨探伤。
12、按工艺进行热处理。
待力学性能合格后方可进行产品流转。
13、焊接时采用优质焊条,操作工持证上岗,严格按焊接工艺操作。
14、对产品进行无损探测,确认符合要求,并出具检测报告。
15、严格按工艺规程进行抛丸和油漆处理。
16、严格按协议要求进行产品的标记,保证产品的可追溯性。
17、认真执行质量责任制,并制定严格的奖惩标准,确保每道工序都处于受控状态。
18、我公司派专人见证整个生产过程,必要时请专业监理工程师抽样旁站。
二、铸钢节点生产工艺2.1生产工艺流程:2.2主要工序工艺简述:大型钢结构建筑铸钢节点,属于钢结构建筑中的重要焊接结构件,在保证其正确优异的化学成分基础上,通过一定的热处理工艺来保证其良好的机械性能;同时亦需要有良好的焊接性能及结构外型的美观、精致等特征。
铸造工艺流程的质量控制方法
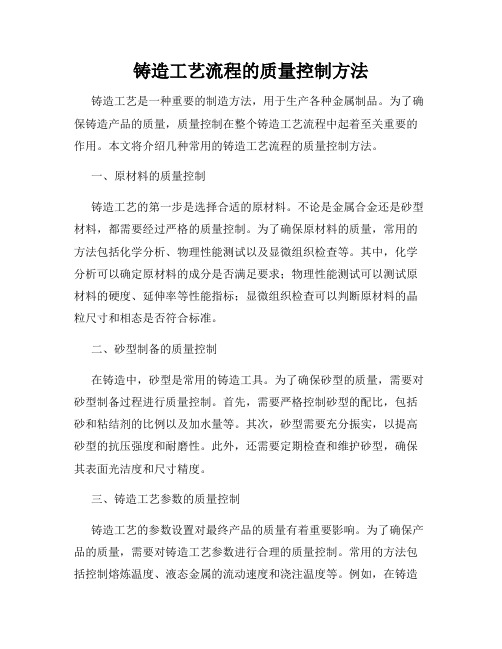
铸造工艺流程的质量控制方法铸造工艺是一种重要的制造方法,用于生产各种金属制品。
为了确保铸造产品的质量,质量控制在整个铸造工艺流程中起着至关重要的作用。
本文将介绍几种常用的铸造工艺流程的质量控制方法。
一、原材料的质量控制铸造工艺的第一步是选择合适的原材料。
不论是金属合金还是砂型材料,都需要经过严格的质量控制。
为了确保原材料的质量,常用的方法包括化学分析、物理性能测试以及显微组织检查等。
其中,化学分析可以确定原材料的成分是否满足要求;物理性能测试可以测试原材料的硬度、延伸率等性能指标;显微组织检查可以判断原材料的晶粒尺寸和相态是否符合标准。
二、砂型制备的质量控制在铸造中,砂型是常用的铸造工具。
为了确保砂型的质量,需要对砂型制备过程进行质量控制。
首先,需要严格控制砂型的配比,包括砂和粘结剂的比例以及加水量等。
其次,砂型需要充分振实,以提高砂型的抗压强度和耐磨性。
此外,还需要定期检查和维护砂型,确保其表面光洁度和尺寸精度。
三、铸造工艺参数的质量控制铸造工艺的参数设置对最终产品的质量有着重要影响。
为了确保产品的质量,需要对铸造工艺参数进行合理的质量控制。
常用的方法包括控制熔炼温度、液态金属的流动速度和浇注温度等。
例如,在铸造过程中,如果熔炼温度过高,易导致铸件内部存在气孔和夹杂物;如果浇注温度过低,易导致铸件的收缩缺陷。
因此,合理控制这些参数可以有效提高铸件的质量。
四、铸造产品的检测与测试在铸造工艺流程中,对铸造产品进行质量检测和测试是不可或缺的环节。
常用的方法包括无损检测、机械性能测试以及尺寸测量等。
其中,无损检测可以通过X射线、超声波等方法检测产品是否存在缺陷;机械性能测试可以测试产品的抗拉强度、硬度等力学性能;尺寸测量则可以验证产品的尺寸精度是否符合要求。
五、质量记录与反馈为了总结经验并改进铸造工艺流程,需要对质量进行记录和反馈。
对于每个铸造批次,应该记录原材料、砂型、工艺参数以及产品质量等关键信息。
铸造质量控制
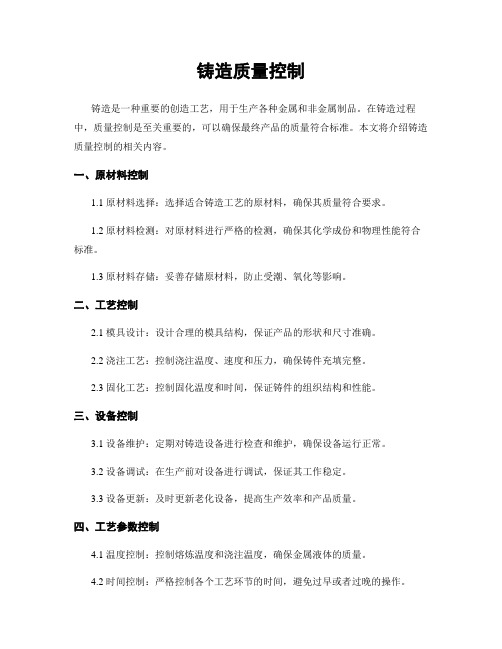
铸造质量控制铸造是一种重要的创造工艺,用于生产各种金属和非金属制品。
在铸造过程中,质量控制是至关重要的,可以确保最终产品的质量符合标准。
本文将介绍铸造质量控制的相关内容。
一、原材料控制1.1 原材料选择:选择适合铸造工艺的原材料,确保其质量符合要求。
1.2 原材料检测:对原材料进行严格的检测,确保其化学成份和物理性能符合标准。
1.3 原材料存储:妥善存储原材料,防止受潮、氧化等影响。
二、工艺控制2.1 模具设计:设计合理的模具结构,保证产品的形状和尺寸准确。
2.2 浇注工艺:控制浇注温度、速度和压力,确保铸件充填完整。
2.3 固化工艺:控制固化温度和时间,保证铸件的组织结构和性能。
三、设备控制3.1 设备维护:定期对铸造设备进行检查和维护,确保设备运行正常。
3.2 设备调试:在生产前对设备进行调试,保证其工作稳定。
3.3 设备更新:及时更新老化设备,提高生产效率和产品质量。
四、工艺参数控制4.1 温度控制:控制熔炼温度和浇注温度,确保金属液体的质量。
4.2 时间控制:严格控制各个工艺环节的时间,避免过早或者过晚的操作。
4.3 压力控制:根据产品要求控制浇注压力,确保铸件的密度和强度。
五、质量检验控制5.1 外观检验:对铸件的表面质量进行检查,包括气孔、裂纹等缺陷。
5.2 尺寸检验:测量铸件的尺寸和几何形状,确保符合设计要求。
5.3 化学成份检验:对铸件的化学成份进行分析,确保符合标准。
综上所述,铸造质量控制是确保铸件质量的关键环节,需要在原材料、工艺、设备、工艺参数和质量检验等方面进行全面控制。
惟独做好质量控制,才干生产出满足客户需求的优质铸件。
铸造质量控制

铸造质量控制铸造是一种常见的金属加工工艺,用于创造各种金属零件和构件。
在铸造过程中,质量控制是至关重要的,以确保最终产品的质量符合设计要求并满足客户的需求。
本文将详细介绍铸造质量控制的标准格式文本,包括质量控制的目的、方法和步骤等内容。
一、质量控制的目的铸造质量控制的目的是确保铸件的尺寸精度、力学性能和表面质量等符合设计要求,以满足客户的需求。
通过质量控制,可以减少次品率,提高生产效率,降低生产成本,并提升企业的竞争力。
二、质量控制的方法铸造质量控制主要采用以下几种方法:1.原材料检验:对铸造原材料进行检验,包括金属材料、砂型材料和熔炼剂等。
检验内容包括化学成份、机械性能、杂质含量等。
通过原材料检验,可以确保原材料的质量稳定和可靠。
2.工艺参数控制:铸造过程中的工艺参数对铸件质量有重要影响。
包括铸造温度、浇注速度、冷却时间等。
通过对工艺参数的控制,可以保证铸件的尺寸精度和力学性能。
3.成品检验:对铸件进行成品检验,包括尺寸检验、力学性能检验和表面质量检验等。
尺寸检验主要包括尺寸偏差、平面度和圆度等。
力学性能检验主要包括拉伸强度、屈服强度和延伸率等。
表面质量检验主要包括表面光洁度和表面缺陷等。
通过成品检验,可以确保铸件的质量符合设计要求。
4.过程控制:在铸造过程中,需要进行过程控制,包括浇注过程控制、冷却过程控制和清理过程控制等。
通过过程控制,可以避免铸件缩孔、气孔和夹杂等缺陷的产生。
三、质量控制的步骤铸造质量控制的步骤主要包括以下几个方面:1.制定质量控制计划:在铸造过程开始之前,需要制定质量控制计划。
质量控制计划包括原材料检验计划、工艺参数控制计划和成品检验计划等。
通过制定质量控制计划,可以明确质量控制的目标和方法。
2.执行质量控制计划:在铸造过程中,需要按照质量控制计划的要求进行操作。
包括原材料检验、工艺参数控制和成品检验等。
通过执行质量控制计划,可以确保铸件的质量符合设计要求。
3.记录质量控制数据:在质量控制过程中,需要记录相关的质量控制数据,包括原材料检验数据、工艺参数数据和成品检验数据等。
铸件质量控制计划
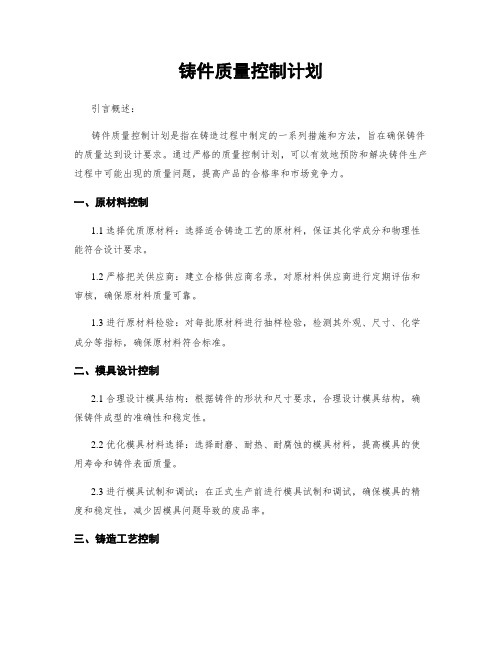
铸件质量控制计划引言概述:铸件质量控制计划是指在铸造过程中制定的一系列措施和方法,旨在确保铸件的质量达到设计要求。
通过严格的质量控制计划,可以有效地预防和解决铸件生产过程中可能出现的质量问题,提高产品的合格率和市场竞争力。
一、原材料控制1.1 选择优质原材料:选择适合铸造工艺的原材料,保证其化学成分和物理性能符合设计要求。
1.2 严格把关供应商:建立合格供应商名录,对原材料供应商进行定期评估和审核,确保原材料质量可靠。
1.3 进行原材料检验:对每批原材料进行抽样检验,检测其外观、尺寸、化学成分等指标,确保原材料符合标准。
二、模具设计控制2.1 合理设计模具结构:根据铸件的形状和尺寸要求,合理设计模具结构,确保铸件成型的准确性和稳定性。
2.2 优化模具材料选择:选择耐磨、耐热、耐腐蚀的模具材料,提高模具的使用寿命和铸件表面质量。
2.3 进行模具试制和调试:在正式生产前进行模具试制和调试,确保模具的精度和稳定性,减少因模具问题导致的废品率。
三、铸造工艺控制3.1 严格控制浇注温度:根据铸件材料和结构要求,控制浇注温度,避免因温度过高或过低导致铸件缺陷。
3.2 控制浇注速度和压力:合理控制浇注速度和压力,确保铸件充型充实,避免气孔和夹杂等缺陷。
3.3 采取适当的冷却措施:在铸造结束后,采取合适的冷却措施,避免因快速冷却或过慢冷却导致铸件内部应力过大。
四、热处理控制4.1 选择合适的热处理工艺:根据铸件的材料和使用要求,选择适合的热处理工艺,提高铸件的强度和硬度。
4.2 严格控制热处理参数:在热处理过程中,严格控制温度、时间和冷却速度等参数,确保热处理效果稳定可靠。
4.3 进行热处理质量检验:对热处理后的铸件进行硬度测试、金相分析等检验,确保热处理效果符合设计要求。
五、表面处理控制5.1 选择适合的表面处理方法:根据铸件的用途和要求,选择合适的表面处理方法,提高铸件的耐腐蚀性和美观度。
5.2 严格控制表面处理工艺:在表面处理过程中,严格控制处理时间、温度和液体浓度等参数,确保表面处理效果均匀一致。
铸造生产过程质量控制点
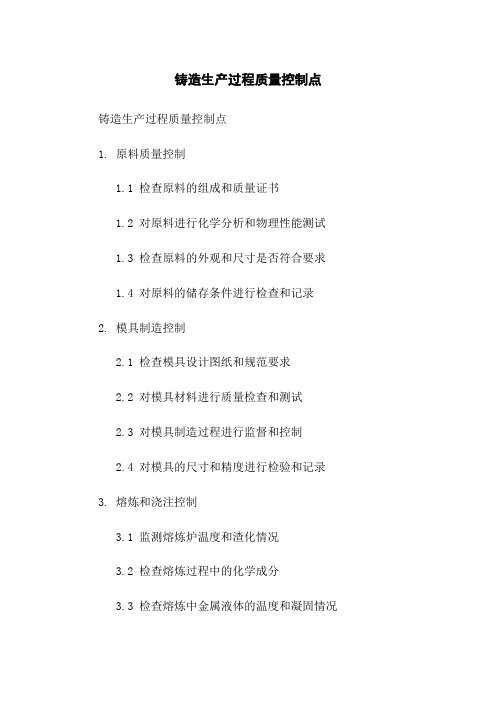
铸造生产过程质量控制点铸造生产过程质量控制点1. 原料质量控制1.1 检查原料的组成和质量证书1.2 对原料进行化学分析和物理性能测试 1.3 检查原料的外观和尺寸是否符合要求1.4 对原料的储存条件进行检查和记录2. 模具制造控制2.1 检查模具设计图纸和规范要求2.2 对模具材料进行质量检查和测试2.3 对模具制造过程进行监督和控制2.4 对模具的尺寸和精度进行检验和记录3. 熔炼和浇注控制3.1 监测熔炼炉温度和渣化情况3.2 检查熔炼过程中的化学成分3.3 检查熔炼中金属液体的温度和凝固情况3.4 对铸件的浇注过程进行监控和记录4. 铸造件外观和尺寸控制4.1 对铸件外观进行目测和检验4.2 使用光谱仪和显微镜对铸件进行化学成分和微观结构的分析4.3 使用激光扫描仪等设备对铸件的尺寸进行测量和记录4.4 对铸件进行外观和尺寸的合格判定5. 热处理控制5.1 对铸件进行退火、正火、淬火等热处理工艺的控制5.2 监测热处理过程中的温度和时间5.3 对热处理后的铸件进行硬度测试和金相分析5.4 对热处理后的铸件进行尺寸和外观的检验和记录6. 特殊工艺控制6.1 对特殊工艺参数进行监控和调整6.2 对特殊工艺工序进行质量检查和控制6.3 对特殊工艺产品的性能进行测试和验证附件:1. 铸造原料的质量证书样本2. 模具设计图纸和规范要求范本3. 铸造工艺流程图4. 铸造件外观和尺寸检验记录表5. 热处理工艺参数记录表6. 特殊工艺工序质量检查表法律名词及注释:1. 质量证书:指由生产厂商或供应商提供的证明原料质量合格的文件。
2. 模具设计图纸:指铸造过程中用于指导模具制造的图纸和规范要求。
3. 化学成分:指铸件材料中各元素的含量。
4. 光谱仪:用于分析金属材料化学成分和物理性能的仪器。
5. 显微镜:用于观察和分析铸件的微观结构和缺陷的仪器。
6. 激光扫描仪:用于测量和记录铸件尺寸的仪器。
7. 退火:指通过加热和冷却的方式改变金属材料的组织结构和性能的工艺。
铸造质量控制
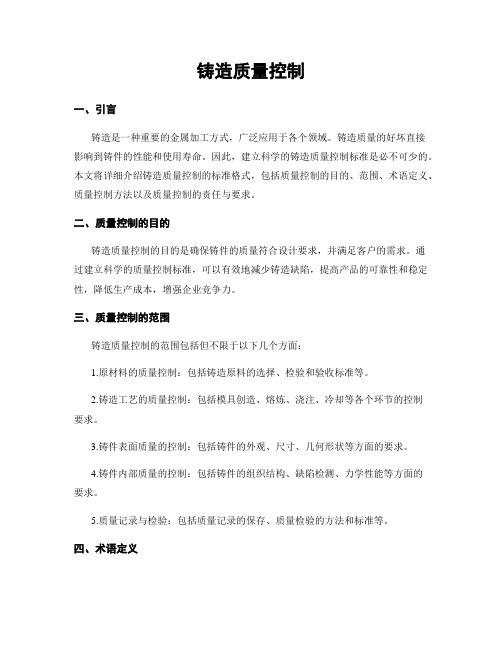
铸造质量控制一、引言铸造是一种重要的金属加工方式,广泛应用于各个领域。
铸造质量的好坏直接影响到铸件的性能和使用寿命。
因此,建立科学的铸造质量控制标准是必不可少的。
本文将详细介绍铸造质量控制的标准格式,包括质量控制的目的、范围、术语定义、质量控制方法以及质量控制的责任与要求。
二、质量控制的目的铸造质量控制的目的是确保铸件的质量符合设计要求,并满足客户的需求。
通过建立科学的质量控制标准,可以有效地减少铸造缺陷,提高产品的可靠性和稳定性,降低生产成本,增强企业竞争力。
三、质量控制的范围铸造质量控制的范围包括但不限于以下几个方面:1.原材料的质量控制:包括铸造原料的选择、检验和验收标准等。
2.铸造工艺的质量控制:包括模具创造、熔炼、浇注、冷却等各个环节的控制要求。
3.铸件表面质量的控制:包括铸件的外观、尺寸、几何形状等方面的要求。
4.铸件内部质量的控制:包括铸件的组织结构、缺陷检测、力学性能等方面的要求。
5.质量记录与检验:包括质量记录的保存、质量检验的方法和标准等。
四、术语定义1.铸造缺陷:指在铸造过程中产生的不符合设计要求的缺陷,如气孔、夹杂、砂眼等。
2.模具:用于创造铸件形状的工具,可以是金属模具、砂型、蜡模等。
3.熔炼:将金属原料加热至液态,并进行铸造准备的过程。
4.浇注:将熔融金属倒入模具中,使其冷却凝固成型的过程。
5.冷却:铸件在浇注后,通过自然冷却或者其他冷却方式使其降温凝固的过程。
五、质量控制方法1.原材料的质量控制方法:(1)选择合适的原材料供应商,并建立长期稳定的合作关系。
(2)对原材料进行严格的检验,包括外观、化学成份、物理性能等指标。
(3)制定原材料验收标准,明确合格和不合格的判定标准。
2.铸造工艺的质量控制方法:(1)制定详细的工艺流程和作业指导书,明确每一个环节的工艺参数和操作要求。
(2)对模具进行定期检查和维护,确保其精度和使用寿命。
(3)严格控制熔炼过程中的温度、时间、搅拌等参数,确保金属液的质量。
铸造生产过程质量控制点

铸造生产过程质量控制点铸造生产过程质量控制点1. 概述铸造是一种常用的金属加工方法,广泛应用于制造各种零部件和工件。
在铸造生产过程中,质量控制是非常重要的,直接影响产品的质量和性能。
本文将介绍铸造生产过程中的质量控制点,以确保产品符合设计要求和质量标准。
2. 材料选择与检验铸造中最关键的环节之一是材料的选择和检验。
合适的材料选择可以保证产品具有所需的机械性能和化学成分。
在进行铸造前,应对材料进行严格的检验,包括外观检查、成分测试、力学性能测试等。
只有合格的材料才能进入下一步的生产工艺。
3. 模具制造与维护模具的质量直接关系到铸件的成型质量。
模具应具备足够的强度和硬度,能够承受铸造过程中的温度和压力。
铸造生产过程中,应定期检查和维护模具,确保其几何尺寸的准确性,防止模具磨损或变形,导致铸件尺寸偏差或表面缺陷。
4. 液态金属处理在铸造过程中,金属通常以液态形式存在,因此对液态金属的处理十分重要。
首先,需要控制金属的准确浇注温度,以确保其流动性和润湿性。
其次,应对液态金属进行除杂处理,以去除杂质和气泡。
最后,在金属浇注前,需要进行温度和成分的检测,以保证金属液在合适的条件下进行铸造。
5. 铸造工艺控制铸造工艺是决定铸件质量的关键因素之一。
在铸造过程中,需要控制浇注速度、温度、浇注压力等参数,以确保铸件形状的准确性和表面的质量。
此外,还需要对铸件冷却速度进行控制,以防止产生缩孔、夹杂等缺陷。
6. 后续处理与热处理铸件在铸造完成后,通常还需要经过一系列的后续处理和热处理过程。
后续处理包括去除毛刺、修整表面、修复缺陷等操作,以提高铸件的外观质量。
热处理则可以改善铸件的机械性能和材料结构,通过控制热处理参数,如温度、时间等,可以获得所需的性能指标。
7. 检测与检验为了确保铸件质量符合要求,需要对铸件进行严格的检测和检验。
常用的检测方法包括尺寸检测、外观检查、材料成分分析、力学性能测试等。
这些检测可以通过非破坏性检测方法,如超声波检测、X射线检测等,或者通过破坏性检测方法,如拉伸试验、冲击试验等进行。
铸造质量控制
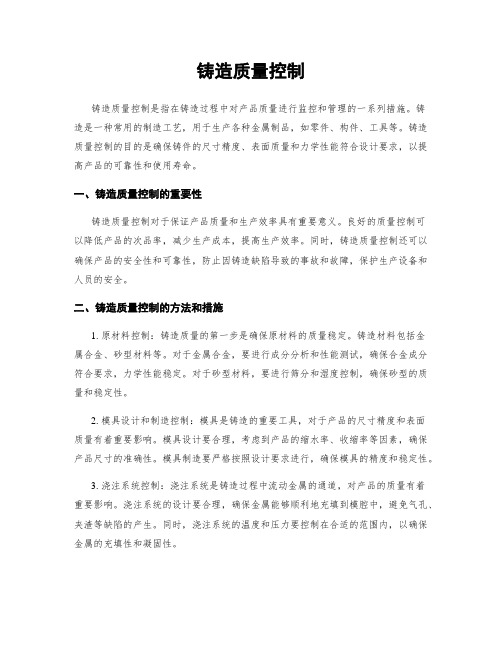
铸造质量控制铸造质量控制是指在铸造过程中对产品质量进行监控和管理的一系列措施。
铸造是一种常用的制造工艺,用于生产各种金属制品,如零件、构件、工具等。
铸造质量控制的目的是确保铸件的尺寸精度、表面质量和力学性能符合设计要求,以提高产品的可靠性和使用寿命。
一、铸造质量控制的重要性铸造质量控制对于保证产品质量和生产效率具有重要意义。
良好的质量控制可以降低产品的次品率,减少生产成本,提高生产效率。
同时,铸造质量控制还可以确保产品的安全性和可靠性,防止因铸造缺陷导致的事故和故障,保护生产设备和人员的安全。
二、铸造质量控制的方法和措施1. 原材料控制:铸造质量的第一步是确保原材料的质量稳定。
铸造材料包括金属合金、砂型材料等。
对于金属合金,要进行成分分析和性能测试,确保合金成分符合要求,力学性能稳定。
对于砂型材料,要进行筛分和湿度控制,确保砂型的质量和稳定性。
2. 模具设计和制造控制:模具是铸造的重要工具,对于产品的尺寸精度和表面质量有着重要影响。
模具设计要合理,考虑到产品的缩水率、收缩率等因素,确保产品尺寸的准确性。
模具制造要严格按照设计要求进行,确保模具的精度和稳定性。
3. 浇注系统控制:浇注系统是铸造过程中流动金属的通道,对产品的质量有着重要影响。
浇注系统的设计要合理,确保金属能够顺利地充填到模腔中,避免气孔、夹渣等缺陷的产生。
同时,浇注系统的温度和压力要控制在合适的范围内,以确保金属的充填性和凝固性。
4. 浇注工艺参数控制:浇注工艺参数包括浇注温度、浇注速度、浇注压力等。
这些参数对于产品的质量和性能有着重要影响。
浇注温度要控制在合适的范围内,以确保金属的流动性和凝固性。
浇注速度要适当,避免金属的冷却不均匀和产生缩孔、夹渣等缺陷。
浇注压力要控制在合适的范围内,以确保金属的充填性和凝固性。
5. 铸件检测和分析:铸件的质量检测是铸造质量控制的重要环节。
常用的检测方法包括尺寸检测、表面质量检测、力学性能检测等。
铸造生产过程质量控制点
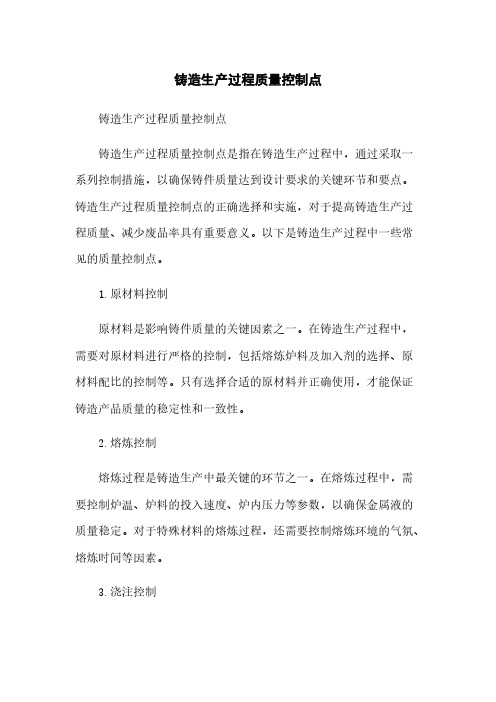
铸造生产过程质量控制点铸造生产过程质量控制点铸造生产过程质量控制点是指在铸造生产过程中,通过采取一系列控制措施,以确保铸件质量达到设计要求的关键环节和要点。
铸造生产过程质量控制点的正确选择和实施,对于提高铸造生产过程质量、减少废品率具有重要意义。
以下是铸造生产过程中一些常见的质量控制点。
1.原材料控制原材料是影响铸件质量的关键因素之一。
在铸造生产过程中,需要对原材料进行严格的控制,包括熔炼炉料及加入剂的选择、原材料配比的控制等。
只有选择合适的原材料并正确使用,才能保证铸造产品质量的稳定性和一致性。
2.熔炼控制熔炼过程是铸造生产中最关键的环节之一。
在熔炼过程中,需要控制炉温、炉料的投入速度、炉内压力等参数,以确保金属液的质量稳定。
对于特殊材料的熔炼过程,还需要控制熔炼环境的气氛、熔炼时间等因素。
3.浇注控制浇注过程是将熔融金属注入到型腔中的过程。
在浇注过程中,需要控制浇注速度、浇注温度、浇注方式等因素,以保证浇注质量和铸件的致密性。
还需要控制浇注过程中金属液的气体排出情况,避免气孔的产生。
4.型腔控制型腔是铸造中形成铸件形状和尺寸的关键部位,对铸件质量有着重要影响。
型腔控制包括型腔设计、制造和维护等环节。
必须确保型腔的准确尺寸和光洁度,避免型腔表面的破损和变形,以确保铸件的形状精度和表面质量。
5.冷却控制冷却过程是铸件从熔融状态到固态过程中的一个关键环节。
在冷却过程中,需要控制冷却速度、冷却介质、冷却时间等因素,以保证铸件组织的均匀性和致密性。
还需要控制冷却过程中的温度梯度,避免铸件产生应力和变形。
6.热处理控制对于某些特殊材料或要求较高的铸件,还需要进行热处理过程。
热处理过程包括加热、保温和冷却等环节。
在热处理过程中,需要控制温度、保温时间、冷却速度等参数,以确保铸件组织的改善和性能的提升。
7.表面处理控制铸件的表面处理是为了提高铸件的表面质量和耐腐蚀性。
表面处理包括喷砂、抛光、电镀等工艺。
在表面处理过程中,需要控制处理剂的使用和浸溶时间,以保证铸件表面的光洁度和处理效果。
铸造生产过程的质量控制

铸造生产过程的质量控制铸造生产过程的质量控制1. 原材料的质量控制铸造过程中使用的原材料主要包括金属合金和砂型材料。
为了保证产品的质量,必须对原材料进行质量控制。
具体控制措施包括:选择高质量的原材料供应商,并建立稳定的供应链。
对原材料进行严格的检验和筛选,确保其符合产品的要求。
对原材料进行化学成分分析和物理性能测试,以确保其质量符合标准。
2. 模具制造过程的质量控制模具是铸造过程中的重要工具,其质量直接影响到产品的精度和表面质量。
为了保证模具的质量,必须对模具制造过程进行质量控制。
具体控制措施包括:制定模具制造工艺和工作指导书,确保每个环节都符合标准要求。
对模具材料进行质量检查和测试,以确保其质量达到要求。
对模具零部件进行尺寸检验和装配检验,确保模具的准确性和稳定性。
3. 铸造工艺参数的质量控制铸造工艺参数是影响产品质量的重要因素,必须进行严格的质量控制。
具体控制措施包括:确定合理的铸造温度和压力,以确保产品的致密性和机械性能。
控制铸造过程中的冷却速率和凝固时间,以确保产品的表面质量和内部组织结构。
对铸造过程中的熔炼和浇注过程进行监控和调整,以确保产品的成分和收缩率符合要求。
4. 产品质量的检验和测试铸造产品的质量必须进行全面的检验和测试,以确保其质量达到要求。
具体控制措施包括:对产品外观进行目测和尺寸测量,以检查产品的表面质量和尺寸精度。
对产品进行物理性能测试,包括硬度、拉伸强度等指标。
对产品进行化学成分分析,以确保其成分符合标准要求。
对产品进行无损检测,如X射线检测、超声波检测等,以检查产品的内部质量。
5. 不良品的处理和纠正措施在质量控制过程中,可能会出现一些不合格的产品或过程。
为了保证产品质量,必须及时进行处理和纠正措施。
具体控制措施包括:对不良品进行分类和评估,确定其影响范围和原因。
采取相应的纠正措施,如返工、修复、补救等。
对纠正措施进行跟踪和评估,以确保问题得到彻底解决。
以上就是铸造生产过程中常用的质量控制方法和措施。
铸造生产过程质量控制点

铸造生产过程质量控制点一、原料检验原料检验是确保产品质量的第一步,主要包括铸造用沙、金属材料和添加剂等的检验。
1.铸造用沙的检验:包括沙粒度检测、含水率检测、化学成分和矿物组成检测等。
沙粒度应符合设计要求,含水率应控制在一定范围内,化学成分和矿物组成应符合标准。
2.金属材料的检验:包括铁水、铝水、铜液等金属的化学成分检测、包括有害杂质的检测等。
金属的化学成分应符合设计要求,有害杂质应控制在合理范围内。
3.添加剂的检验:包括炭素稳定剂、铁矿粉、红土等添加剂的化学成分检测、水分检测等。
添加剂的化学成分应符合标准要求,水分应控制在合理范围内。
二、铸型制备铸型制备是铸造过程中至关重要的环节,主要包括模具制备和芯制备两个方面。
1.模具制备:模具制备的关键是模具材料的选择和加工工艺的控制。
模具材料应具有足够的强度和韧性,并且耐用性好。
加工工艺应控制模具尺寸的精度和表面质量,以及模腔的几何形状和位置精度。
2.芯制备:芯的制备需要控制芯盒尺寸的精度、芯材的化学成分和物理性能、芯粘结剂的配比和固化工艺等。
芯盒尺寸的精度直接影响最终铸件的尺寸精度,芯材的物理性能与化学成分直接关系到芯的强度和稳定性,芯粘结剂的配比和固化工艺决定芯的强度和表面质量。
三、铸造操作铸造操作是铸造生产中最关键的环节,主要包括浇注、冒口设置、冷却措施和除渣等。
1.浇注:控制浇注的速度、浇注的位置和浇注的角度等,以防止铸件内部出现夹渣、气孔等缺陷。
2.冒口设置:合理设置冒口位置和数量,以利于铸件内部的气体和夹渣排除,防止缩孔、砂眼等缺陷的产生。
3.冷却措施:采取适当的冷却措施,控制最终铸件的显微组织和性能。
包括调整浇注温度、铸件的冷却速率和冷却时间等。
4.除渣:及时清除铸件上的渣滓,防止渣滓对铸件品质的影响。
四、冷却处理冷却处理是铸件的重要环节,主要包括冷却速率、冷却时间和冷却介质等控制。
1.冷却速率:控制铸件的冷却速率,会影响到铸件的显微组织和力学性能。
铸造质量控制

铸造质量控制在现代工业生产中,铸造是一种常见的创造工艺,涉及到各种金属和合金的加工,其质量控制对产品的性能和可靠性至关重要。
本文将从不同角度探讨铸造质量控制的重要性和方法。
一、原材料质量控制1.1 选择合适的原材料:铸造过程中所使用的原材料对最终产品的质量有着决定性影响。
因此,必须选择符合标准要求的原材料,包括金属、砂型、石膏等。
1.2 原材料检测:在使用原材料之前,需要进行严格的检测,确保其符合生产要求。
例如,金属原料需要进行化学成份、机械性能等多方面的检测。
1.3 原材料存储管理:正确的原材料存储管理可以有效避免原材料受潮、氧化等问题,影响产品质量。
因此,需要建立严格的存储管理制度。
二、工艺参数控制2.1 控制铸造温度:铸造温度的控制对产品的组织结构和性能有着重要影响。
需要根据不同金属材料的特性,合理控制铸造温度。
2.2 控制浇注速度:浇注速度直接影响产品的凝固过程和内部缺陷情况。
需要根据产品的形状和尺寸,合理控制浇注速度。
2.3 控制冷却时间:冷却时间的长短会影响产品的晶粒大小和组织致密度。
因此,需要合理控制冷却时间,确保产品质量。
三、模具设计和创造控制3.1 合理设计模具结构:模具设计的合理性直接影响产品的尺寸精度和表面质量。
需要根据产品要求,设计出合适的模具结构。
3.2 选择优质模具材料:模具材料的质量对模具的使用寿命和稳定性有着重要影响。
需要选择高强度、高耐磨的模具材料。
3.3 严格控制模具加工精度:模具加工精度直接决定了产品的尺寸精度和表面质量。
因此,需要严格控制模具的加工精度,确保产品质量。
四、工艺流程控制4.1 制定详细的工艺流程:在铸造过程中,需要制定详细的工艺流程,包括浇注、冷却、清理等各个环节,确保每一个环节都符合标准要求。
4.2 实施严格的工艺控制:在生产过程中,需要严格按照工艺流程执行,确保每一个步骤都得到正确执行,避免产生质量问题。
4.3 定期进行工艺检测:定期对工艺流程进行检测和评估,及时发现问题并进行调整,以确保产品质量稳定。
铸造生产过程的质量控制
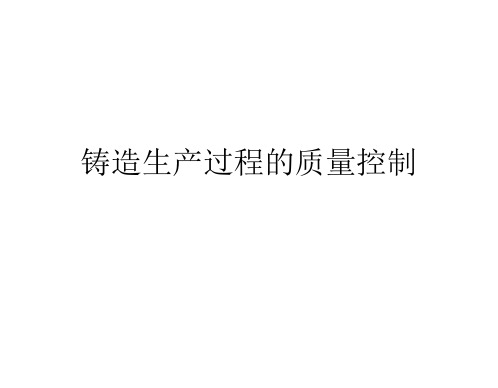
口不平,银白色,细晶粒,有时在中心有些缩松,三角试片尖角部位的白口 消失或仅有1-2mm,说明球化孕育正常。
铸件材质检测
金相显微镜
直读光谱仪
通过辅助试块、光谱试样来验证生产铸件材质
6.铸件的漆膜质量检验
用涂-4检验油漆的浓度16-18S,画格仪来检测漆膜的附着 力大于I ,漆膜测厚仪测量漆膜厚度30-40UM
• 2.4 球化处理反应时间大于50秒。用取样勺从铁水表面200㎜以下取适量铁 水浇注三角试样和光谱试块,待三角试块冷却至暗红色放入水中冷却,打断 观察球化效果
• 2.5 球化后的铁水加除渣剂,迅速扒渣,扒渣完成后,加覆盖剂。 • 2.5 球化孕育之后,球化质量判断:球化后三角试片两侧及顶部有凹陷,断
案例2(内部质量)
解决方案:
1.提高铁水的纯净度(球 化包、炉内、球化扒渣)
2.使用陶瓷泡沫过滤片
该铸件为制动缸体,浇 注重量84kg,浇注时间 13-16S.
问题描述:
铸件在加工时,渣 眼废品太多
铸件质量的稳定,取决于每个生产过程质量的可控
备注:由于铸造过程的特殊性(如原材料、造型设备、操作方式的差 异),下面出现的技术参数仅供参考。
离合器壳体 玉米机箱体
HT250
差(制)动器壳 HT250
1.9--2.3 3.1-3.3 1.7-2.0 3.3-3.5 1.9-2.2
≤0.20 ≤0.030 ≤0.015 0.8-1.0 ≤0.12 ≤0.12 0.4-0.6 ≤0.12 ≤0.12
Ti ≤ 0.030
5.2铁水的球化及浇注
FBO造型
3.砂芯的制作
冷芯盒射芯机
射芯机大林砂50-100目芯 砂,芯子在保证合适的强 度时,要尽量降低芯子的 发气量;注意铸件飞翅的 发生(浇注时芯子出现裂 缝)
铸造生产过程的质量控制

铸造生产过程的质量控制质量控制是铸造生产过程中非常重要的一环,能够确保产品符合质量标准和客户要求。
本文档将详细介绍铸造生产过程中的质量控制措施和标准,以供参考。
1.质量控制概述1.1 目的和范围本章节介绍质量控制的目的和范围,明确质量控制对产品质量的重要性,以及在整个铸造生产过程中需要实施的质量控制措施。
1.2 质量控制流程本章节详细描述铸造生产过程中的质量控制流程,包括材料准备、模具制备、熔炼浇注、冷却和清理等环节中的质量控制措施和标准。
2.材料准备质量控制2.1 材料选择本章节介绍材料选择的原则和标准,包括原材料的物理性质和化学成分等要求。
2.2 材料检验本章节详述材料检验的方法和标准,包括外观检验、尺寸检验、化学成分分析等。
3.模具制备质量控制3.1 模具设计本章节介绍模具设计的原则和要求,包括模具结构、内腔形状等方面的质量控制。
3.2 模具加工本章节详细描述模具加工的质量控制要求,包括模具尺寸精度、表面光洁度等方面。
4.熔炼浇注质量控制4.1 熔炼操作本章节介绍熔炼操作的要求,包括熔炼温度、保持时间、熔炼材料配比等方面的质量控制。
4.2 浇注操作本章节详述浇注操作的质量控制措施,包括铸型预热、浇注速度、浇注温度等方面的要求。
5.冷却和清理质量控制5.1 冷却过程质量控制本章节介绍冷却过程中的质量控制措施,包括冷却时间、冷却速率等方面的要求。
5.2 清理过程质量控制本章节详细描述清理过程中的质量控制要求,包括清理方法、清理剂的选择等方面。
附件:法律名词及注释:1.法律名词:的解释说明。
2.YYY法律名词:YYY的解释说明。
铸造质量控制

铸造质量控制引言概述:铸造是一种重要的创造工艺,广泛应用于各个行业。
而铸造质量的好坏直接影响产品的性能和可靠性。
因此,铸造质量控制成为了铸造过程中不可忽视的关键环节。
本文将从五个方面详细阐述铸造质量控制的重要性和方法。
一、原材料控制1.1 合理选择原材料:根据产品的要求和铸造工艺的特点,选择适当的原材料,确保其化学成份和物理性能符合要求。
1.2 严格检测原材料:通过化学分析、物理性能测试等手段,对原材料进行全面检测,确保其质量稳定可靠。
1.3 做好原材料的储存和保管工作:采取适当的储存条件,避免原材料受潮、变质等问题,确保其在使用过程中的质量不受影响。
二、模具设计与创造控制2.1 合理设计模具结构:根据产品的形状和尺寸要求,合理设计模具的结构,确保铸件的准确成型。
2.2 严格控制模具创造工艺:采用先进的数控加工设备,确保模具的精度和质量。
2.3 定期维护和保养模具:定期检查和维护模具,及时修复损坏和磨损部位,保证模具的使用寿命和创造质量。
三、铸造工艺控制3.1 控制熔炼工艺参数:合理控制熔炼温度、保温时间等参数,确保熔炼过程中金属液的化学成份和温度稳定。
3.2 严格控制浇注工艺:采取合适的浇注方式和速度,避免金属液中的气体和杂质进入铸件,确保铸件的内部质量。
3.3 控制冷却过程:合理控制冷却速度和冷却介质,确保铸件的组织结构和物理性能符合要求。
四、铸件检测与评估4.1 采用先进的无损检测技术:如X射线检测、超声波检测等,对铸件进行全面、准确的检测,发现和排除缺陷。
4.2 进行物理性能测试:对铸件进行拉伸、硬度等物理性能测试,评估其力学性能和耐久性。
4.3 进行化学成份分析:通过化学成份分析,检测铸件中的杂质含量和化学成份是否符合要求。
五、质量管理与改进5.1 建立完善的质量管理体系:制定质量管理制度和操作规程,确保每一个环节都有明确的责任和要求。
5.2 进行持续改进:通过定期召开质量改进会议、开展质量培训等方式,不断提高员工的质量意识和技术水平。
铸造质量控制

铸造质量控制一、引言铸造是一种常见的制造工艺,用于生产各种金属制品。
铸造质量控制是确保铸造产品达到预期质量标准的关键步骤。
本文将详细介绍铸造质量控制的标准格式文本,包括质量控制的目的、过程和方法。
二、质量控制目的铸造质量控制的目的是确保铸造产品的质量符合设计要求和客户需求,以提供高质量、可靠的铸造产品。
通过质量控制,可以降低产品缺陷率,减少生产成本,提高客户满意度,增强企业竞争力。
三、质量控制过程1. 材料选择铸造材料的选择对产品质量至关重要。
根据产品的要求和使用环境,选择合适的铸造材料,包括金属合金、砂型材料等。
材料选择应考虑其力学性能、耐腐蚀性、热处理性能等因素。
2. 设计评审在铸造产品设计阶段,进行设计评审是必要的。
评审团队应包括设计师、工艺工程师、质量工程师等相关人员。
评审内容包括产品设计的可行性、材料选择的合理性、工艺流程的优化等。
3. 工艺规范制定详细的工艺规范是保证铸造产品质量的重要环节。
工艺规范应包括铸造设备的选择和调试、砂型制备、熔炼和浇注工艺、冷却和固化过程等。
规范应具体明确每个工艺环节的要求和操作方法。
4. 检验和测试在铸造过程中,进行检验和测试是必要的,以确保产品符合质量要求。
常用的检验和测试方法包括尺寸测量、外观检查、金相分析、力学性能测试等。
检验和测试结果应记录并进行分析,以便及时调整工艺参数。
5. 缺陷分析与改进如果在铸造过程中出现缺陷,应进行缺陷分析并采取相应的改进措施。
缺陷分析可以通过金相显微镜观察、断口分析、化学成分分析等方法进行。
改进措施可以包括调整工艺参数、改变材料配比、优化工艺流程等。
四、质量控制方法1. 统计质量控制统计质量控制是常用的铸造质量控制方法之一。
通过对铸造产品的抽样检验和统计分析,评估产品的质量水平和生产过程的稳定性。
常用的统计质量控制方法包括控制图、过程能力指数等。
2. 全员参与铸造质量控制需要全员参与,每个员工都应对产品质量负责。
通过培训和教育,提高员工对质量的认识和责任感。
铸造质量控制

铸造质量控制一、引言铸造是一种重要的创造工艺,用于生产各种金属零件和构件。
在铸造过程中,质量控制是确保最终产品符合规格和要求的关键因素。
本文将详细介绍铸造质量控制的标准格式文本,包括质量控制的目的、方法和流程等。
二、质量控制目的铸造质量控制的目的是确保生产的铸件符合设计要求,并具有良好的机械性能和表面质量。
通过质量控制,可以减少缺陷率和废品率,提高生产效率和产品质量,降低成本和风险。
三、质量控制方法1. 工艺控制铸造工艺控制是铸造质量控制的基础。
包括合理的铸造工艺参数设置、选用合适的铸造材料、控制熔炼和浇注温度、控制浇注速度和压力等。
通过优化工艺参数,可以减少缺陷的产生,提高铸件的质量。
2. 材料控制铸造材料的选择和控制对铸件质量至关重要。
包括选用合适的铸造合金、控制原材料的化学成份和物理性能、控制熔炼过程中的杂质含量等。
通过严格的材料控制,可以提高铸件的强度、硬度和耐腐蚀性能。
3. 设备控制铸造设备的选择和控制对铸件质量也有重要影响。
包括选用合适的铸造设备、控制设备的精度和稳定性、定期维护和保养设备等。
通过优化设备控制,可以提高铸件的尺寸精度和表面质量。
4. 检测控制铸造质量控制中的检测控制是确保铸件质量的重要环节。
包括非破坏性检测和破坏性检测两种方式。
非破坏性检测包括超声波检测、射线检测和磁粉检测等,用于检测铸件的内部缺陷;破坏性检测包括拉伸试验、冲击试验和硬度试验等,用于检测铸件的机械性能。
通过合理的检测控制,可以及时发现和排除铸件的缺陷,确保产品的质量。
四、质量控制流程1. 铸造前准备在铸造前,需要进行充分的准备工作。
包括准备合适的模具和芯子、准备合适的铸造材料、准备合适的铸造设备等。
同时,需要对模具和设备进行检查和维护,确保其正常工作。
2. 铸造过程控制在铸造过程中,需要严格控制各项工艺参数。
包括控制熔炼和浇注温度、控制浇注速度和压力、控制铸造时间等。
同时,需要对铸件进行实时监测和记录,确保铸件的质量。
- 1、下载文档前请自行甄别文档内容的完整性,平台不提供额外的编辑、内容补充、找答案等附加服务。
- 2、"仅部分预览"的文档,不可在线预览部分如存在完整性等问题,可反馈申请退款(可完整预览的文档不适用该条件!)。
- 3、如文档侵犯您的权益,请联系客服反馈,我们会尽快为您处理(人工客服工作时间:9:00-18:30)。
nn 直 径 为 1 3tr 圆球 形 , 掉 此类 铸 件 的 冒 u, ~ n的 u 打 口, 冒 口根 部气 孔 呈径 向分 布 , 浇 注 位 置看 , 则 从 铸件
的底 部及 内圆角 处更 甚 。
由于 A、 B型 气 孔 可 直 观 , 检 验 时很 容 易 被 发 在
现 而 C型孔 处 于皮 下 , 难 发 现 , 很 具有 较 大 的 潜在
摘要: 通过对采 用白云石砂 生产 工具模 具钢 产生气孔特征 的分析 , 有针对性地对 冶炼和铸造工 艺进行 改进 , 生产 出优质 铸件 : 关 键词 : 具 模 具 镪 ; 云 石砂 ; 工 白 气孔
中 圈分 类 号 : G2 5 T 4 文 献标 识 码 : B 文 章 编 号 :018 6 t0 2 0 .150 10 3 5 2 0 }20 0 2 3
8 % ,G8 r 0 Z C 3的产 品 又 占整 个 铸 钢 件 产 量 的 1 % 0
左 右 。因此 , 决 气孔 问题 成为生产 的关键 。 解
维普资讯
16 0
经验 交流
《 铸造技 术)/02 220
1 气 孔 特征及 生产 条件 下 出现 气孔 几率 的观 察与 分析 17 年 以前 , 用 硅砂 干 型 铸 造 , 要 缺 陷是 牯 97 采 主 砂和夹 砂 , 很少 有 气 孔 。 而 采 用 白云 石 砂 后 , 好 相 恰 反 , 孔 缺 陷为主 , 少 有 粘砂 和夹砂 现象 观察 这些 气 很
气孔 的形 状和 分布 , 表现 出一 定 的规律 性 , 基本 可分 成 3种类 型 : A 型 多裸 露 在铸 件 表面 , 弥散 度 较 高 的 敞 口 呈 细针孔 及针孔 麻 点 , 直径 为 1 1I ~2I1 1 T
c型
多出现在薄 壁件 上, 于铸件 皮下 2 8 处 ~
维普资讯
《 铸造技术》 / 0 2 22 0 分型 面 处 疏 松 较 为 明显 , 压废 品 率 为 3 % 试 2 左右 , 进后 基本 无疏 松 , 压废 品率为 5 以下 。 改 试 %
降为 3 %以下 。 ( )直径 7 . m 和 1 16Ⅱ 三通在改进前型板 3 62Ⅱ 0. m
Qu U yC nr l f a t o l i t l rd cin a t o to o s T o c e o u t C D s eP o
Z HOU ln YE Jwx Ja i ( Lc ie e a t l l _ H l n b i ig m t h ol g ,H l y n 2 0 8 hn ;2 Maei r e t ol eo Hu a i :t 1 N ahn p rr Z I I ul n a e n a e e e g a g 4 1 0 ,C i d l lf m e d r] l t a tr dP o c c lg t n n Unv s v e j e  ̄ l Ch n s a4 0 0 Chn ) a g h 1 0 0, ia
图 3 改 进 前 工 艺
图 4 改 进 后 工 艺
( )直径 3 . T /和 3 . 11 通 在 改 进 前 型 2 】 7I 1 W 8 1nf 三 1 板布置 , 图 3 两工 件 间 的大 冒 口基 本 对 内侧 转 角 见
改进 , 因疏 松 造 成 的 漏 气 废 品率 从 6 %左 右 下 降 到 3
的漏 气废 品超出 2 %。改成如 图 8的型 板 后 . 艺 出 2 工
品率 提 高 2 % , 6 漏气 废 品率能保 证在 3 %以下 。
∞3 7mm 1 08 3 1㈨ _ 三通
( )直径 3 . 5ri 、8 1rl 和 5 . n 1 头 5 1 7 a n 3 . l l 0 8TI 弯 l T T 改进前 型板 布 置 , 图 9 见 。改 进 后 型 板见 图 1 。通 过 0
7 改进 前 1艺 和 改进 后工 艺 =
收稿 日期 :0 I1一2 2 0 一 I1 ;
修订 日期 :0 11 4 2 0 —2 1
铸 造 工 具 模 具 钢 生 产 的 品质 控制
周 健 叶 久 新 . (. 1湖南建 树 高等专科 学 院机 械系 , 湖南 衡 阳 4 10 ; 湖南大 学材 料工程 学 院 ,湖南 长 沙 40 0 ) 20 8 2 100
布置 , 图 5 见 。此 工 艺 内侧转 角 处很 容 易产 生 疏 松 、 缩 孔 , 类废 品率 在 5 % 以上。按 图 6型板工 艺 改进 后 , 此 6 疏松 、 缩孔造成 的漏气废 品率 为 1%以下 , 0 效果明显。 ( ) 径 1 . i 1 .5rn 2 . i 头在 4 直 2 7rn、90 i、5 4r n弯 a a a 改进 前 型板 布置 , 图 7 见 。工 艺 出 品率低 , 因疏 松产 生
8 以 下 %
∞7 6 2一 0 0 6 nH 通 【 I li
o 1 7一 2
ol 0 n 9 5 r m
图 5 改进 前 工 艺
图 6 改 进后 工 艺
图 8 改 进 前 工 艺 和 改 进后 工 艺
o 7 rrl 口 9 1 f霄 击 l lf和 】 1 m_ 2 l 5 l
在 汽 车生产 中 , 些 承受 复杂 应 力 和 大 负荷 的零 一
气 孔缺 陷 占整个 废 品率 的 3 %-5 % , 的高达 7 % 0 - 0 有 0
-
件, 如前 梁 、 曲轴 及各 种齿 轮 , 一般 采用 模 锻 成形 。 自
17 9 7年 以来 , 崩 白云 石 砂铸 造 生产 工 具 模 具钢 件 , 采