accu-lube喷油机英文版安装指导说明书
加油机安装方案及流程

加油机安装方案及流程英文回答:Installing a fuel dispenser involves several steps and requires careful planning and execution. Here is a step-by-step guide on how to install a fuel dispenser:1. Planning and Preparation:Determine the location for the fuel dispenser. It should be easily accessible for customers and comply with safety regulations.Obtain necessary permits and approvals from local authorities.Ensure proper electrical and plumbing connections are available at the installation site.Purchase the fuel dispenser and any additionalequipment required, such as filters and hoses.2. Site Preparation:Clear the installation site of any obstructions or debris.Level the ground and ensure a stable foundation for the fuel dispenser.Install any necessary underground piping for thefuel supply.3. Electrical and Plumbing Connections:Hire a licensed electrician to install the necessary electrical connections, including power supply and grounding.Connect the fuel dispenser to the electrical system, ensuring proper wiring and safety measures are in place.Hire a licensed plumber to install the necessary plumbing connections, including fuel supply lines and drainage.4. Fuel Dispenser Installation:Follow the manufacturer's instructions for assembling and installing the fuel dispenser.Secure the dispenser to the foundation, ensuring stability and safety.Connect the fuel supply lines to the dispenser, following proper procedures and safety guidelines.Install any additional equipment, such as filters and meters, as per the manufacturer's instructions.5. Testing and Inspection:Conduct thorough testing of the fuel dispenser, ensuring all functions are working properly.Perform leak tests to ensure there are no fuel or vapor leaks.Schedule an inspection by local authorities to ensure compliance with safety regulations.6. Training and Maintenance:Train staff on how to operate and maintain the fuel dispenser safely.Develop a maintenance schedule to regularly inspect and service the dispenser.Keep records of maintenance activities and monitor performance to ensure optimal operation.Installing a fuel dispenser requires attention todetail and compliance with safety regulations. By following the proper installation process and conducting regular maintenance, you can ensure the safe and efficientoperation of the fuel dispenser.中文回答:加油机的安装需要经过几个步骤,并且需要仔细的规划和执行。
ES4600_用户手册_V1.1.3

用户手册
版本:ES4600_UM_CN_V1.Байду номын сангаас.3
i
目录
注意事项 ...................................................................................................................................................................iv 1 参数 ........................................................................................................................................................................ 1
1-1 技术参数........................................................................................................................................................ 1 1-2 条码预设参数................................................................................................................................................ 2 2 开始使用 ...................................................
静电喷雾润滑液滴的荷电特性和摩擦磨损性能_胡志强

[研究·设计]DOI :10.3969/j.issn.1005-2895.2014.01.009收稿日期:2013-06-29;修回日期:2013-08-19基金项目:国家自然科学基金项目(No.51375454)专利项目:浙江工业大学,切削液气雾微量润滑装置(201320072042.7)作者简介:胡志强(1987),男,湖北咸宁人,硕士研究生,主要研究方向为静电喷雾润滑。
E-mail :huzhiqiang1110@163.com 静电喷雾润滑液滴的荷电特性和摩擦磨损性能胡志强,孔魁,姚伟强,李中亚,许雪峰(特种装备制造与先进加工技术教育部/浙江省重点实验室(浙江工业大学),浙江杭州310014)摘要:采用十二烷基苯磺酸钠表面活性剂对Accu-Lube LB-2000基础油进行改性处理来提高其电导率,获得了适用于静电喷雾润滑的润滑液。
通过目标网状法检测改性润滑液的荷电性能,利用四球摩擦磨损试验分析润滑液流量、时间和载荷对静电喷雾润滑摩擦磨损性能的影响。
结果表明,表面活性剂溶液体积含量为5%的润滑液具有较稳定的乳化状态,且电导率可达到6.5ˑ10-5S /m ,能满足静电喷雾润滑的荷电要求;与普通喷雾润滑相比,静电喷雾润滑在不同润滑液流量与载荷下均能获得更好的减摩抗磨性能,尤其是在润滑液流量为5mL /h 和载荷为147N 下作用效果更显著。
关键词:静电喷雾;电导率;荷质比;摩擦磨损中图分类号:TG501文献标志码:A文章编号:1005-2895(2014)01-0036-06Charged and Tribological Characteristics of Cutting Fluid Dropletsfor Electrostatic Spraying LubricationHU Zhiqiang ,KONG Kui ,YAO Weiqiang ,LI Zhongya ,XU Xuefeng(Key Laboratory of E&M (Zhejiang University of Technology ),Ministry of Education &Zhejiang Province ,Hangzhou 310014,China )Abstract :The Accu-Lube LB-2000base oil was modified by sodium dodecyl benzene sulfonate to obtain the lubricants suited for the electrostatic spraying lubrication ,which had a higher conductivity.The charged performance of conductivity-modified lubricants was detected by the method of target meshing ,based on which the effect of cutting fluids flow ,time and load on the properties of the friction and wear were evaluated by using the four-ball friction wear testing experiment.The result showed that the lubricants had a stable emulsified state and met the charged requirements because its conductivity could reach 6.5ˑ10-5S /m when the concentration of surfactant was at 5%,the better tribological characteristics can be obtained by electrostatic spraying lubrication compared with the normal spraying lubrication at different flows and loads ,especially getting more obvious at the flow of 5mL /h and the load of 147N.Key words :electrostatic atomization ;conductivity ;charge-to-mass ratio ;friction and wear 微量润滑(Minimal Quantity Lubrication ,MQL )技术是环境友好绿色切削技术的典型代表。
simalube 自动润滑油器产品说明书

simalubeAdvantages of automatic lubrication with simalube 3simalube – the lubrication expert 4/5simalube 15 ml 6simalube multipoint 7simalube IMPULSE 8/9Applications 10/11Standard lubricants 12Accessories 13/14/15simalube: continuouslubrication ensures low costsand high reliabilityMillions of simalube lubricators are used worldwide in everyindustry. They are the best and most economical solution forthe continuous supply of grease or oil for periods of up to oneyear.simalube – everywhere forces act, something spins orsomething moves.Because my bearingsare worth it!«Once installed, simalube lubricators lubricateevenly, accurately and reliably. This is not at allpossible with manual lubrication.»23Advantages of automatic lubrication with simalubeOptimized lubricant delivery Lower costs thanks to simalubesimalube lubricators replace costly manual lubrication. This not only saves time, but also prevents insufficient or over-lubrication. The costs can thus be reduced by up to 30 percent.No more manual lubrication ■ Saves time■Greater work safety■ Hard-to-reach lubrication points are permanently supplied ■ Lower lubricant consumptionNo under- or over-lubrication of components ■ Less wear■ Less machine downtime■ Increased machine performanceSealed, dustproof and waterproof system ■ No more confusion of lubricants ■ Reduced risk of contamination■ No contamination of lubrication pointsCompliance with international standards ■ TÜV-tested and Ex certified in all zones ■ Improved workplace safety■ No environmental impact thanks to recycling and disposal according to regulationsContinuous lubricant delivery with simalube effectively prevents insufficient or over-lubrication that often occurs with manual lubrication.Up to 30 percent lower costs:■ Time-saving and greater safety at work thanks to fewer maintenance intervals■ Longer machine service life and less unplanned down-timesimalube – the automatic single-point lubricatorAvailable in 5 sizes, simalube supplies various lubrication points with lubricant around the clock.Day in, day out – for up to one year.simalube –the lubrication expertMore technical information and user manual can be downloaded at /en/simalubeTOM'sTIPReliability■ Lubrication points are continuously supplied with lubricant ■ No lubrication point is missed■ Easy monitoring of the dispensing process thanks to the transparent housingEnvironmental sustainability■ simalube can be refilled up to 3 times ■ Easy disposal at end of dispensing cycle■ simalube lubricators do not contain toxic substancesFlexibility■ simalube is available in 5 sizes: 15, 30, 60, 125 and 250 ml ■ Freely selectable dispensing cycle of 1 to 12 months ■ Dispensing cycle can be modified anytime■ simalube is available filled or empty for self-fillingUnlimited range of uses (see pages 10/11)To determine the size and time setting, use our free«Calculation Pro» program at /en/calproProductAutomatic long-term grease and o il lubricator Power generation Hydrogen gas producing drycell Working pressure Max. 5 barAdjustment Stepless 1–12 months(for standard conditions)Operating temperature – 20 °C to +55 °C ambient temperature(Grease consistency changes with temperature)Storage temperatureRecommended at 20 °C ±5 °C Lubricator volume 30 ml 60 ml 125 ml 250 ml Weight full ~82 g ~115 g ~190 g ~335 g Weight empty ~55 g~60 g~75 g~111 gRefill The 15–250 ml simalubes are r efillable.CertificationsComponents Specifications43 m m (1.7 i n )sima lube 3062 m m (2.4 i n )sima lube 60100 m m (3.9 i n )sima lube 12514 m m (0.55 i n )14 m m (0.55 i n )14 m m (0.55 i n )14 m m (0.55 i n )193 m m (7.6 i n )sima lube 250DrivePistonØ 52 mm Ø 52 mmØ 52 mm Ø 52 mmG 1/4"G 1/4"G 1/4"G 1/4"6simalube 15 mlProduct Automatic, long-term grease andoil lubricatorPower generation Hydrogen gas producing drycellWorking pressure Max. 5 barAdjustment Stepless 1–12 months(for standard conditions)Operating temperature – 20 °C to +55 °C ambient temperature (Grease consistency changes with temperature)Storage temperature Recommended at 20 °C ±5 °C Lubricator volume 15 mlWeight full/empty ~36 g / ~22.5 gCertificationsDimensionsSpecificationsThe smallest automatic lubricatorIn confined spaces, the 15 ml simalube offers the perfect solution. With its compact size, it is unique on the global market as the smal-lest automatic lubricator. It functions the same as the larger simalube lubricators and offers the same advantages.Ø 22 mm75 m m (2.95 in)■ Space-saving thanks to compact size ■Robust aluminium enclosure■ Same refill, installation and function as other simalube lubricators■ Alternative to the simalube multipoint when less than 5 lubrication points are needed (see page 7)14 m m (0.55 i n )G 1/4"7simalube multipointProduct Automatic, multi-point, long-term lubricatorsfor grease and oilPower generation Hydrogen gas producing drycell Working pressure Max. 5 barAdjustment Stepless 1–12 months(for standard conditions)Operating temperature –20 °C to +55 °C ambient temperature (grease consistency changes with temperature)Storage temperature Recommended at 20 °C ±5 °C Lubricator volume 5×8 mlWeight full/empty ~147 g / ~120 gCertificationsDimensionsSpecificationsAutomatic multi-point lubricatorThe simalube multipoint simultanously supplies 5 lubrication points for up to one year in the same reliable way as the other proven sima-lube lubricators. Thanks to the snap-on connector, simalube multipoint can be replaced easily and quickly when empty.■ 5×8 ml lubricant volume■ Allows very low lubricant delivery over a long period of time■ Snap-on connector for multipoint ■ Quick couplings for connecting hoses ■ Ideally suited for lubrication of linear guidesØ 52 mm (2.05 in)16.5 m m (0.65 i n )105 m m (4.13 i n )simalube IMPULSEPressure booster up to 10 barThe simalube IMPULSE ensures reliable lubrication in situations with high counter-pressure and long lubrication lines. With the automatic simalube lubricators, this pressure booster pumps greases and oils at up to 10 bar and 0.5 ml per impulse to the targeted lubrication point.The LED display of the intelligent pressure booster provides information continuously about the current operating condition, and flashes green when the device is functio-ning correctly.More technical information and a video for simalube IMPULSE can be found at /en/impulseTOM'sTIPProcure new battery pack and yourself ...250125s i m a l u b e 6075 m m (2.95 i n )10simalube applicationsThe spindles of a lifting station for railway wagons and locomoti-ves are lubricated with 125 ml simalube over 12 months.Two 250 ml simalube lubricators with brushes lubricate and clean the chain drive of a drum washing machine.The drive chain of a transport belt, which allows rolls to cool, is cleaned with special blue brushes and lubricated with 2 simalube SL18 in 30 and 60 ml sizes.125 ml simalube lubricators lubricate the rotating assembly of acrane.LIFTING DEVICESFOOD INDUSTRYGRAVEL AND CONCRETE PLANTS CRANESA simalube multipoint can lubricate 5 linear guides of a cutting and paper stacking machine in a printing house.The simalube IMPULSE with a 125 ml lubricator is used in gravel plants. The IMPULSE pushes the lubricant with a pressure of 10bar through a 4-metre lubrication line.A 125 ml simalube lubricates the pedestal bearing of a conveyor 60 ml lubricators on the electric motor and the drive shaft ensurecontinuous lubrication of a centrifugal pump.The 125 ml simalube maintains the guide rails of elevators andprevents dry friction. The system is attached directly to the cabin roof.15 ml simalube lubricators with brushes constantly supply the rackMany other applications can be found at /en/simalube-applicationsTOM'sTIPGRAVEL AND CONCRETE PLANTS PRINTING INDUSTRY RECYCLING ELEVATORS AND ESCALATORSWATER TREATMENT/SEWAGE TREATMENT PLANTSMACHINERY AND PLANT ENGINEERING(EP)Datasheets are available for all greases and oils at /en/lubricantsTOM'sTIPsimalube standard lubricants and accessories13290.1045290.1046290.2037-S 290.2038-SMounting support with pro-tective cover for simalubeChain lubrication with round brush and two clampsChain lubrication with bra-cket, universally adjustableMounting bracketChain lubrication with clampLubrication of elevator gui-des or wire ropesRound brush with 90° connection + recommended • possible – not recommendedApplication examplesThe simalube can be easily installed anywhere and in any position with these accessories.290.2000290.2002290.2004290.2039290.2042290.2034290.2013290.2010290.2014290.2080290.2082290.2083290.2084290.1060290.2082290.2083290.2084290.2035290.2036290.2037290.2038290.2010290.2010290.2041290.1005290.2800290.2081290.2085290.2000290.2002290.2004290.2080290.1060290.2035290.2036290.2037290.2038290.1045290.1046Safety accessories 14Installation accessoriessimalube multipoint installation componentssimalube IMPULSE accessories15simatec agStadthof 2, CH-3380 Wangen a. Aare Tel.: +41 (0)32 636 50 00Fax: +41 (0)32 636 50 19*******************simatec – innovative solutions that deliver outstanding customer benefitsMaintenance products by simatec – industrial technologysimatec is an international, Swiss family enterprise. Since its founding in 1983, this motivated team has been developing, ma-nufacturing and marketing innovative pro-ducts for the maintenance of rolling bearings under the brand names of simalube, sima-therm and simatool.The direct customer benefits are always at the forefront. Using newly developed tech-nologies, simatec simplifies complex pro-cesses and reduces routine maintenance for tens of thousands of machines around the globe.Select trading partners sell simatec main-tenance products around the world. They provide professional service and individu-al, expert advice.LubricatorsThe simalube lubricator provides auto-matic lubrication over a period of one month to a year and can be adjusted in an infinitely variable manner. simalube supplies every lubricating point with the ideal amount of lubricant – be it oil or grease – so that subsequent manual lub-rication is no longer needed and mainte-nance costs are reduced in the long term.Induction Heaterssimatherm induction heaters heat circular metal parts, such as roller bearings, in a very short amount of time, so they can be installed quickly and efficiently. The inductive heating of metallic workpieces makes sense from both an economical and ecological perspective. simatec is the world’s leading manufacturer of these ty-pes of heaters.ToolsThe simatool toolkits enable the fast instal-lation and removal of roller bearings and seals. They are used all over the world in machine and maintenance workshops within all industries.simalube video1735/610.9201。
齿轮油泵的安装说明书(中英文)

SHANGHAI ELECTRIC GROUP CO. LTD PT. MAXIMA INFRASTRUKTURGear Oil Pump Assembly Instruction 齿轮油泵安装说明书四川高精净化设备有限公司SICHUAN FINE PURIFICATION EQUIPMENT CORP.LTD1.RIEF INTRODUCTIONWith history of more than 20 years in producing large separation equipment, our compary manufactures Model ZJA High Vacuum Oil Purifier, ZLY Vacuum Oil Filter, JYG Fine Filter,BMS, BAS Manual/Automatic Board Frame Press Oil Filter Which are designed for filtering turbine oil, transformer oil, aviation hydraulic oil, machine oils and Diesel fuel. Besides, We produce WCB,KCB,2CY Geared Oil Delivery Pumps suitable for delivering various medium oils.Model WCB, KCB,2CY Gear Oil Pumps are suitable for fertilizer factory, oil refinery, oil-pressing factory, power plant, transformer station, lubrication oil storehouse, capacitor plant, painting factory and grain departments for delivering oils, such as turbine oil ,transformer oil, aviation oil, mechanical oil, diesel oil and edible oil.WCB,KCB Geared Oil Pump features of good appearance, compact construction, stable performance, low pulsation impact value and low noise less than the specified of the national standard, safety and reliability as well as easy maintenance and service. We provide our customers with wear parts for a long term.Series of gear oil pumps produced by our company find their wide use in national defense, scientific research, Petroleum, light/chemical industry, metallurgy, textile, transportation, Pharmaceutical-making and food departments for delivering non-corrosion heavy oil, mid-viscosity oil, light oil, edible oil and other similes with viscosity below Engler 10°E at temperature below 60℃.However, they are not suitable for delivering dirty oils, lubricating/corrosive medium. Explosion-proof motors and special motors can be provided according to user's requirements.Model WCB Geared oil pump is of one with excellent performance and reasonable price. It can be used in grain sales department for delivering edible oil with illumination power.2.SPECIFICATION3. CONSTRUCTION AND OPERATION PRINCIPLE3.1StructureGeared pump is composed of body ,front/back end cover, driving gear, driven gear, bearings, bearing cap, oilseal coupling, motor, chassis, inlet/oulet oil pipe, flange and safety valve etc.Front/back end cover supports driving/driven gear by means of bearings. The body enables driving gear and driven gear to rotate, resulting in vacuum operation mode. Oilseal acts as sealing of driving shaft. Motor drives driving gear through coupling and shaft pin.2.Moving Sketch3.2 Operation PrincipleWhen driving shaft drives Gear1and Gear2 to rotate in direction shown by arrow and geared teeth disengage gradually in oil suction cavity, teeth disengage from teeth of another gear so that vacuum is formed. aˊ,bˊ…of a, b…between teeth carries oil from oil suction cavity to oil discharge cavity. Oil in geared space is pressed out when gear rotates continuously. Outer load action causes oil pressure. With continuous running of gear, oil pump sucks and discharges oil continuously.When resistance of oil circuit exceed safety Pressure, safety valve starts to make oil in discharge cavity go back suction cavity. In doing so, pressure is reduced and pump/piping is protected.4.INSTALATION AND CONISSIONINGGeared pump and motor is fixed on chassis. Shaft line between motor and geared pump has been adjusted. Geared pump rotates smoothly.During operation, keep an eye to suction height. Rated lift can be obtained. Specified oil inlet/outlet pipes should be chosen. Oil inlet should be through. Before starting, check to see whether fasteners are loose and whether geared pump moves freely. Idle running can't last more than 1 minute. If no oil is sucked in, check geared pump for correct rotation(Running in direction shown by arrow).Check to see whether oil suction pipe joint is loose, connections are leaky and oil groove bottom is blocked by oil suction pipe inserted as well as oil suction height and oil outlet height exceeds tolerance.No abnormal noise and vibration should occur when geared pump works.Safety valve was set in specified safe pressure scope at factory. Users can regulate it. But max regulation puessure can't exceed 40%.5.OPERATION5.1 Before operation, check to see whether geared pump moves freely(Turn by hand).5.2 Make sure power supply is OK and rotation direction of motor is correct.5.3 Check to see whether oil inlet/outlet diameter meets requirements and lift is within specified range.5.4Make sure that all fasteners are firm (Including connectors of inlet/outlet pipe)5.5Before starting, insert oil inlet pipe into oil groove properly. Oil pipe can't reach to groovebottom to prevent blocking intake.5.6Only everything is OK, you may start machine.6.MAINTENANCE AND SAFETY6.1 Connect grounding device6.2 Always keep an eye to loosening of fasteners and abnormal noise of geared pump.6.3 Corse filter should be mounted at oil inlet to prevent iron and impurities from entering pump. 6.4 Oil seal is wear part. In case that driving shaft leaks oil, change oil seal.6.5 Oil pump adopts ball bearings. If ball bearings are worn out, serious noise will occur. Replacement should be made.6.6 After service is completed, made sure that axial gap of the pump, and concentricity should be within tolerance. Otherwise, Pump will fail to work properly.6.7 Geared pump is not allowed to operate in environment and the open-air with high temperature.7.TROUBLESHOOTING AND REMEDYMAIN PARTS AND MATERIALS TABLEBEARING CATALOGUESPARE PART AND WEAR PART CATALGUESPARE PART AND WEAR PART CATALGUEOVERALL AND INSTALLATION DIMEMSIONS OF OIL PUMP一、简介我厂已有二十多年制造分离大型机械设备的历史,产品为各发电厂或从事电力事业的单位提供ZJA系列高真空净油机、ZLY系列真空滤油机、JYG系列精密过滤机、BMS、BAS系列手动和自动板框压滤机、LY系列板框滤油机过滤透平油、变压器油、航空液压油、机油、柴油,还为客户提供WCB、KCB、2CY系列齿轮输油泵,输送各类不同用途的介质油液。
accu-lube喷油装置(推荐油量使用范围)

ITW ROCOL North America Accu-Lube/Bluebe推荐油量使用范围(准干式植物金属加工润滑油)应用泵设定次/分钟(泵工作频率)消耗油量范围(ml)/8小时铣 2.0-2.6(圈)15-3030-75圆锯 3.3-3.6(圈)15-6030-85带锯 3.4-3.6(圈)15-12030-100冲孔0.6-0.7(圈)15-12035钻孔0.6-0.7(圈)15-12035磨0.2-0.3(圈)12-306-12拉削,扩孔 3.3-3.6(圈)15-12030-90消耗油量数据参考正常8小时工作制。
中铝集团洛阳铜业使用油量参考数值:(准干式锯切)材料:紫铜切削线速度:1318m/min(米/分钟)(圆锯片直径:1430毫米)进刀量:900mm/min毫米/分钟材料:铁白铜(BFe30-1-1)铝青铜(QA19-4)切削线速度:360m/min(米/分钟)(圆锯片直径:1430毫米)进刀量:180mm/min毫米/分钟60ml/一个喷嘴/8小时2升/一个喷嘴/月具体配置为5喷嘴,每天两班(16小时),每周5天,每个月耗油12升锯片寿命延长2倍以上断面和锯片温度基本保持室温中铝集团中色万基铝业使用油量参考数值:(准干式锯切)材料:铝锭(1100×400×180000)切削线速度:2000m/min(米/分钟)进刀量:250mm/min毫米/分钟配置三个喷嘴,每天耗油200ml铝材氧化热处理无需清洗、无油斑,铝屑干燥可直接回炉。
而他们原来使用乳化液单单烤屑机的电能消耗(热损耗)就远远超过此数据,还有许多节约的成本未算入:烤屑机投入,湿屑到烤屑机再到回熔炉的运输成本乳化液的取消刀具寿命延长2倍现场干净、环保工件质量提高等等一台CNC(数控加工中心)一般一桶油(3.785升)可以使用3个月以上。
自动注油器安装说明书

自动注油器安装说明书
Pulsarlube ML500型自动注油器安装说明书
在广大顾客朋友们够买注油器之时,让人疑惑的就是如何安装、如何使用自动注油器,下面三和波达公司为您解忧,呈现安装详情。
首先,在安装自动注油器装置前,清洗润滑点周边的污垢,并且确保所使用手动润滑枪清除润滑点的通道干净。
移开油脂嘴并且在轴承润滑点处检查硬化的润滑脂。
如果油脂出现硬化,在将自动注油器安装在轴承上之前清理润滑点。
然后,通过按住电源按钮2秒钟来打开自动注油器装置。
为了确认液晶显示屏是开着的,请确保当电源按钮被按住时红色的液晶显示屏闪烁。
于是,按住试验按钮两秒钟以运行试验循环。
装置将开始分配润滑脂并且持续处于净化、试验模式操作中。
该程序将会持续大概两分钟以确保润滑器的每个功能都正常运作。
接着,通过按住125/250试验按钮来选择合适的润滑脂袋体积。
按住模式按钮来安排调剂周期。
每次按住模式按钮,调剂周期按照以下递升序改变:1、2、3、6、12、H(H=半个月)
最后,使用合适的适配器以及配件(根据需要)将自动注油器装置安装在润滑点上,确保拧紧适配器以及配件。
应输入安装日期以及指定的润滑周期完成日期以便维护。
主机气缸油注油器说明书

ALPHA LUBRICATOR SYSTERM OPERATION MANUAL MC ENGINES国顺路80弄23号401室MAN B&W主机气缸油注油器说明书1 概况ALPHA润滑系统主要由泵站,注油单元,注油控制装置-ALCU,负荷变送器,触发系统,辅触发系统,控制面板等组成。
图:40C 01B主要部件:泵站单元泵站及启动屏(PUMPSTATIONANDSTARTERPANELS)泵站由2个独立的工作泵,加热盘管,滤器和吸入柜组成。
泵站电源由两路分别供电。
注油器单元每缸配有1个注油器单元,(98-70缸径的发动机注油器单元有2个注油器。
每个注油器单元在进出口侧配有蓄压器(进口侧的蓄压器氮气预充至30-50BAR,出口侧为1.5BAR)。
每个注油器右个注油柱塞,反馈检测元件和电磁阀组成。
注油器控制装置-ALCU(ALPHA LUBRICATORCONTROLUNIT)控制系统主要由三个电子元件组成。
称为ALCU装置MCU(主控单元)BCU(辅控单元)SBU(开关单元)所有电线通过接线终端至主机。
两路电源经USP 中的两个相互独立的断路器供给24V直流电。
负荷变送器(LOAD TRANSMITTER)负荷变送器连接在燃油齿条上,因此能连续地把检测到的负荷(百分比)传送给主控单元,主控单元根据此信号和主机转速信号计算主机的负荷。
图:40B05触发系统(TRIGGERSYSTERM)轴译码器安装在曲轴的前端,信号经接线盒传送至计算机。
由于转角译码器无法安装在主机曲轴的前端,所以一个触发环和转速检测装置安装在飞轮处图:40A 05控制面板HMI(HUMANMACHINEINTERFACEPANEL)在控制面板上,可进行单缸注油的调整,显示各种数据报警,手动进行预润滑,并附有泵站的控制按钮。
标准的HMI屏安装在集控室。
图:06A1-1 工作原理泵站供给注油器的压力为40-50BARMCU通过驱动注油器上的电磁阀实现注油控制注油后的反馈信号由该缸的指示单元上的发光二极管显示辅触发系统(BACKUP TRIGGER SYSTEM)辅触发系统由飞轮处盒子里的二个测速器组成,变送主机的转速信号至辅控单元。
ACCU-LUBE-安装操作使用指南

Accu-Lube
Environmentally Safe Lubricants and Micro-Lubrication Systems for Near-Dry Machining
Precision Lubricant Applicator
精密润滑喷油机
Installation and Operating Instructions 安装操作使用指南
4. 准备使用. . . . . . . . . . . . . . . . . . . . . . . . . . . . . . . . . . . . . . . . . . . . . . . . . . . . 4
5. 安装给油机. . . . . . . . . . . . . . . . . . . . . . . . . . . . . . . . . . . . . . . . . . . . . . . . . . .5
开箱检验
当您打开新的 Accu-Lube 供油润滑系统时请确认包括以下部件: 1. Accu-Lube 给机油 2.油罐 3.空气过滤器 4.样品油 5.喷头及紧固件 6.喷嘴 7.保修卡 8.调查表
客户服务
如果出现破损,建议立即联系承运商。如果缺少零部件,请联系 ITW ROCOL North America 的中国服务供应商。
ITW ROCOLTM North America 中国服务商 上海曼斯实业有限公司
上海市松江车墩松江工业区泖亭路 188 号 29-104 栋 电话:86-021-37620505/06/07 传真:86-021-37620508 邮箱:mansi@
但是使用ACCU-LUBE以外的油品或者非正常工艺及工况而出现的问题,由购买者自己 负责。
Altronic V 自动燃油系统安装说明书

SMALL ENGINES, 1-6 CYLINDERS FORM AV II 2-95 WARNING: DEVIATION FROM THESE INSTALLATION INSTRUCTIONS MAY LEAD TO IMPROPER ENGINE OPERATION WHICH COULD CAUSE PERSONAL INJURY TO OPERATORS OR OTHER NEARBY PERSONNEL.1.0 DESCRIPTION1.1The Altronic V self-powered ignition system consists of these basic components:1.Altronic V unit2.Wiring harness3.Ignition coils - 501 061, 501 061-S, 591 010, 591 010-S, 591 040(one per cylinder)2.0 ENGINE2.1Set the engine so that no. 1 cylinder is at the desired ignition firing point.3.0 DIRECTION OF ROTATION3.1Determine the rotation of the Altronic V unit (looking at the drive end of the Altronic V) for theengine being equipped.4.0 ALTRONIC V UNIT4.1Locate the timing mark on the housing for the proper rotation (see drawing 509 102). Rotatethe unit shaft until the red mark on the shaft lines up with the proper mark on the housing.4.2Mount the unit on the engine drive keeping the two red marks lined up as close as possible.Install and tighten finger-tight two 3/8"-16 mounting bolts. See drawing 509 101 for dimensions of the various Altronic V models.4.3Once the unit is mounted, rotate the entire unit to cause the two red timing lines to meet. Ifthe red lines cannot be made to meet in this manner, remove the four screws which fasten the back cover assembly to the unit. The entire back cover assembly should then be pulled away from the unit keeping the internal plug connected. Rotate the distributor gear until the two marks described above line up. Then reinstall the back cover to the unit, engaging the gears, and keeping the two red marks together. If necessary, the plastic cover can be removed to keep one finger on the timing decal to maintain the proper alignment of the two red timing marks. Securely tighten the four cover mounting screws.SMALL ENGINES, 1-6 CYLINDERS FORM AV II 2-95 4.4Final timing should be set using a timing light with the engine at operating speed. The entireunit is rotated to adjust ignition timing.4.5Tighten the two 3/8"-16 mounting bolts.5.0 IGNITION COILS5.1Use only the Altronic coils listed in section 1.1.5.2Mount the ignition coils as close to the spark plugs as possible keeping the high-tension leadlength to a minimum but also keeping termperature below 200°F. (95°C.) during operation.6.0 PRIMARY WIRING6.1The firing order of the Altronic V units is as follows:NO. OF CYLS.ALTRONIC VUNIT NO.FIRING ORDERCCWROTATIONFIRING ORDERCW ROTATIONWIRINGDIAGRAM1**1A18A A1A1*1A28H A A1B2**2A14A-B A-B2A2*2A25, 2A28A-B A-B2A2*2A28H A-B A-B2B3**3A14A-C-B A-B-C3A3*3A25, 3A35A-B-C A-C-B3B4**2A14, 2A64A-B-A-B A-B-A-B44*4A24, 4A34A-B-C-D A-D-C-B65*5A24A-B-C-D-E A-E-D-C-B66**3A14, 3A64A-B-C-A-B-C A-C-B-A-C-B56*6A24, 6A34A-B-C-D-E-F A-F-E-D-C-B6* Single firing unit - fires each cylinder individually on the compression stroke only. **Double firing unit - fires on exhaust stroke as well as compression stroke.SMALL ENGINES, 1-6 CYLINDERS FORM AV II 2-95 6.2Starting with lead "A" to the coil of no. 1 cylinder, the harness leads are connected inaccordance with the engine's firing order to the positive (+) terminals of the coils - see wiring diagrams. On exhaust stroke firing units (**), the coils for the cylinders with the same harness letter are connected in SERIES as shown in the wiring diagrams.6.3 A common ground lead connecting the negative (!) terminals of the coils must be connectedas shown in the wiring diagrams.6.4All connections should be made using ring type terminals specified for 16 gauge wire and#10 stud size. Terminals should either be soldered to the wire or attached with an appropriate staking tool. All primary wiring should be protected from physical damage, vibration and temperatures in excess of 200°F. (95°C.).6.5SHIELDED SYSTEM - Request Altronic drawing 509 013 for detail.7.0 SHUTDOWN WIRING7.1The shutdown harness lead must be grounded to shut-off the ignition. The shutdown leadis identified:- "E" for units with a 5-pin connector (models 1A, 2A, 3A);- "G" for units with a 7-pin connector (models 4A, 5A, 6A).7.2For proper operation of Murphy tattletale switches or fuel valve, use panel adapter 501 213as shown in the wiring diagrams.8.0 SECONDARY WIRING8.1The spark plug leads should be fabricated from 7 mm, silicone insulated, tinned copperconductor with suitable terminals and silicone spark plug boot. Keep spark plug leads as short as possible and in all cases not longer than 20 inches (500 mm). Spark plug leads should be kept at least 2 inches (50 mm) away from any grounded engine part. In deep spark plug wells, use rigid, insulated extenders projecting out of the well.8.2The use of a clear, silicone grease (such as Dow Corning DC-4, G.E. G-623 of GCElectronics Z5) is recommended for all high-tension connections and boots. This material helps seal out moisture and prevent corrosion from atmospheric sources.。
油浆器安装指南说明书

INSTALLATION1. Refer to warning above.2. Install as close as possible to the equipment requiring lubrication.3. Install the unit with the air flowing through the body in the direction indicated by the arrow.4. Install the same pipe-size unit as the pipeline in use. Avoid usingfittings, couplings, etc., that restrict the airflow or baffle the oil out of the air at the lubricator outlet.5. The lubricator may be filled under pressure by slowly removing the fill plug and pouring oil into the bowl through The tank may be taken off after the fill plug is removed. Do not replace the fill plug until the tank is secured in place.NOTE:As the fill plug is removed, the air pressure in the tank will be released.6. Use only clean non-detergent oil. SAE 10 or lighter is usually best.7. The rate of oil delivery can be controlled counterclockwise for more and clockwise for less delivery. This lubricator delivers all of the oil downstream that passes through the sight dome. The oil delivery rate will change auto-matically to deliver more oil during higher air flows and less oil for air flows lower than that at which the original setting was made.8. Maximum pressure and temperature ratings for metal tanks are 200 psig (14bar) and 175°F (79°C).MAINTENANCE1.Given clean operating conditions, this unit should be trouble-free. Drain off any contaminants which collect in the bottom of the bowl.2.IF THE OIL DELIVERY RATE DROPS, shut off the air supply to the lubricator and reduce the pressure in the unit to zero. Remove the adjusting screw and clean the needle and seat in the body. Inspect and clean the passage from the needle seat down into the siphon tube adapter. Remove the Flow-Guide ®variable orifice screw and clean air passage with a small wire. Check the bore that the screw fits into for contaminants and clean if necessary. Be sure the passageway from the sight dome cavity downward is open. Remove and clean the valve seat.3. Drain off any contaminants which collect in the bottom of the tank.REPAIR KITS AND REPLACEMENT PARTSBowl O-Ring Kit, Nitrile (10 per kit) (for L31, L32)..............................GRP-95-256Adjusting Screw O-Ring Kit (for L31, L32).........................................GRP-95-255Siphon Tube Assembly Kit (for L32)...................................................LRP-96-211Fill Plug Kit (for L31, L32)...................................................................LRP-95-253Flow-Guide ®, 1 NPT Models (for L31, L32).........................................LRP-95-190Sight Dome Kit (for L31, L32).............................................................LRP-95-249Sight Gauge Kit (for L31)....................................................................LRP-95-771Sight Gauge Kit (for L32)....................................................................LRP-95-716Tamper Resistant Kit (for L31, L32)...................................................LRP-95-587Force-Fill Adapter (for L31, L32)........................................................GRP-96-394O-Ring Repair Kit (for L31, L32).........................................................LRP-95-058Check Ball and O-Ring Kit..................................................................LRP-95-31083-297-000 REV REL 11/95Printed in U.S.A.INSTALLATION AND MAINTENANCE SHEETLubricator Model L31/L32with Variations and Accessories®OPERATIONSNNR = NOT NORMALLY REPLACED。
Pulsarlube 油漆器安装说明书
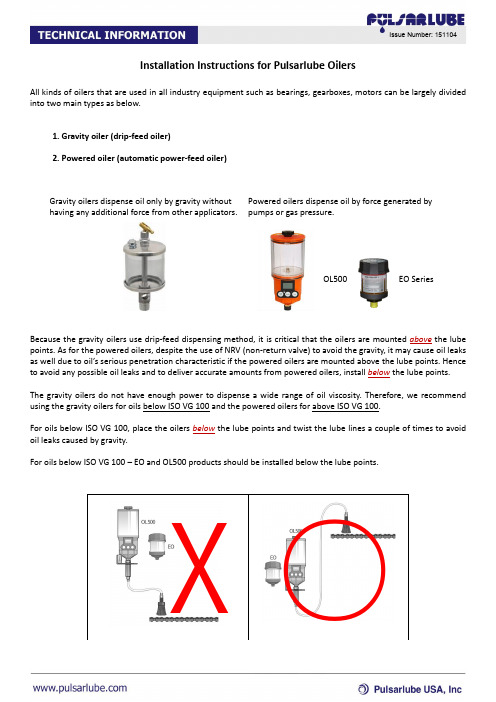
Issue Number: 151104Installation Instructions for Pulsarlube OilersAll kinds of oilers that are used in all industry equipment such as bearings, gearboxes, motors can be largely divided into two main types as below.1. Gravity oiler (drip-feed oiler)2. Powered oiler (automatic power-feed oiler)Gravity oilers dispense oil only by gravity without having any additional force from other applicators. Powered oilers dispense oil by force generated bypumps or gas pressure.OL500 EO SeriesBecause the gravity oilers use drip-feed dispensing method, it is critical that the oilers are mounted above the lube points. As for the powered oilers, despite the use of NRV (non-return valve) to avoid the gravity, it may cause oil leaks as well due to oil’s serious penetration chara cteristic if the powered oilers are mounted above the lube points. Hence to avoid any possible oil leaks and to deliver accurate amounts from powered oilers, install below the lube points.The gravity oilers do not have enough power to dispense a wide range of oil viscosity. Therefore, we recommend using the gravity oilers for oils below ISO VG 100 and the powered oilers for above ISO VG 100.For oils below ISO VG 100, place the oilers below the lube points and twist the lube lines a couple of times to avoid oil leaks caused by gravity.For oils below ISO VG 100 – EO and OL500 products should be installed below the lube points.X ○。
汽油气设备安装与运行指南(英语)说明书

INSTALLATION & OPERATIONAL MANUALIMPORTANT FOR YOUR SAFETYTHIS MANUAL HAS BEEN PREPARED FOR PERSONNEL QUALIFIED TO INSTALL GAS EQUIPMENT, WHO SHOULD PERFORM THE INITIAL FIELD START-UP AND ADJUSTMENTS OF THE EQUIPMENT COVERED BY THIS MANUAL.POST IN A PROMINENT LOCATION THE INSTRUCTIONS TO BE FOLLOWED IN THE EVENT THE SMELL OF GAS IS DETECTED. THIS INFORMATION CAN BE OBTAINED FROM THE LOCAL GAS SUPPLIER. IMPORTANTIN THE EVENT A GAS ORDOR IS DETECTED, SHUT DOWN UNITS AT THE MAIN SHUTOFF VALVE AND CONTACT THE LOCAL GAS COMPANY OR GAS SUPPLIER FOR SERVICE.FOR YOUR SAFETYDO NOT STORE OR USE GASOLINE OR OTHER FLAMMABLE VAPORS OR LIQUIDS IN THE VICINITY OF THIS OR ANY OTHER APPLIANCE.Improper installation, adjustment, alteration, service or maintenance can cause property damage, injury or death. Read the installation, operating and maintenance instructions thoroughly before installing or servicing this equipment.Using the appliance safelyBeing an appliance designed only for professional use, it should be operated by qualified personnel exclusively.Never leave the appliance unattended while it is on.Do not move the appliance while hot.Do not replenish the tank while the oil is hot. Please pay attention to the oil level mark when filling the tank. If it is below the minimum line, the oil might catch fire. If it is over the maximum line, the oil might overspill. It must be somewhere between min and Max line.Please make sure the food is not wet. If food is wet or water drops inside the oil or fat, oil would burstand it is extremely dangerous.Do not use flammable solvents or cleaning aids to clean this fryer. Corrosion might occur. Safety instructions in case of malfunctionIf the appliance will remain idle for some time or in the event of a failure, abnormal operation, etc., turn off the shutoff valve upstream of the appliance. Call the service. Additional prohibitions (hazardous procedures)Never tamper with the seals of the adjusting screws located on the gas valves. Disposing of the applianceThis appliance has been manufactured using recyclable raw materials and does not contain any hazardous or toxic substances. To dispose of the appliance and all its packaging materials, strictly follow the local regulations in force in the place where it is installed. Packaging materials should be divided according to the type and delivered to a specific collection site. Ensure compliance with environmental protection regulations.TABLE OF CONTENTS Important for your safety IntroductionGeneralSpecifications InstallationClearancesLocationASSEMBLYFlue connectionGas connectionGas pressureTest gas supplyLeveling the fryerOperationOver temperature shutdown Before first useCleaningFilling the tank with shortening Lighting the pilotTurning on the fryerTurning off the fryer Extended shutdownBasic frying instructionsFry Basket GuidelinesExtended shortening life Daily filteringCLEANING DailyBolt out procedure MaintenanceFlue vent inspection TroubleshootingINTRODUCTIONGENERALThis type of Fryer is produced with quality workmanship and material. Proper installation, usage and maintenance will result in years of satisfactory performance.Before installing the fryer, thoroughly read this manual and carefully follow all instruction.This manual is applicable to model listed on the cover page. Procedures in this manual will apply toall models unless specified. Pictures and illustrations can be of any model unless the picture or illustration needs to be model specific.SpecificationMODEL Burner Qty Type of gas Heat Input Ignition Width Inch Shortening lbs.GF90 3 G20,G30,G3126.40.5kW (NG),0.6kW(LPG) 15.5" 35-40GF120 4 G20,G30,G31 35.2 15.5" 45-50 GF120T 4 G20,G30,G31 35.2 15.5" 25+25 GF150 5 G20,G30,G31 44 21.0" 65-70 GF85 5 G20,G30,G31 44 21.0" 85-90SpecificationMODEL Burner Qty Type of gas Heat Input Ignition Width Inch Shortening lbs.GF90 3 G25.3 25.50.5kW 15.5" 35-40GF120 4 G25.3 34 15.5" 45-50 GF120T 4 G25.3 34 15.5" 25+25 GF150 5 G25.3 42 21.0" 65-70 GF85 5 G25.3 42 21.0" 85-90INSTALLATIONBefore installing the fryer, verify that the type of gas (natural or propane) agrees with the specifications on the fryer naming plate which is located at the rear part of the unit. Make sure the fryer is configured for the proper elevation.Record your fryer model, device, and serial numbers for future reference in the space provided below. This information can be found on the fryer data plate.Model No: ___________________Device: ______________________Serial No: ____________________Clearances☆Minimum clearance from combustible construction:6” (15 cm) from the sides of the fryer 6” (15 cm) from the back of the fryer The fryer may be installed on combustible floors☆Minimum clearance from noncombustible construction:0” from the sides of the fryer 0” from the back of the fryer☆Between the fryer and any open-top flame units:16” (41 cm)Location☆ Install fryer in an area with sufficient air supply for gas combustion at fryer burners.☆ Do not obstruct the flow of combustion and ventilation air.☆ Provide adequate clearance for air openings into the combustion chamber.☆ Do not permit fans to blow directly onto fryer.☆ Avoid wall-type fans, which create cross-currents within a room. Avoid open windows next to sides or back.ASSEMBLYThe fryer must be restrained to prevent tipping and the splashing of hot liquid. The means of restraint may be the manner of installation, such as connection to a battery of appliances, installing the fryer in an alcove, or by separate means such as adequate ties.FLUE CONNECTIONMake the flue connection as follows:☆ Locate the fryer under a hood with adequate connection to an exhaust duct. The hood must extend 6” (15 cm) beyond fryer on both sides.☆ Clearance above the fryer should be adequate for combustion by-products to be removed efficiently.☆ An 18” (46 cm) minimum clearance should be maintained between the flue ventand the filters of the hood venting system.☆ Never make flue connections directly to the fryer.☆ Do not obstruct the flow of the gases from the appliance. Proper air balance should be maintained in the room.GAS CONNECTIONAll gas supply connections and any pipe joint compound must be resistant to the action of propane gases.The gas inlet is located on the lower rear of the fryer. Codes require that a gas shutoff valve be installed in the gas line ahead of the fryer.The gas supply line must be at least the equivalent of ½” (12.7 mm) iron pipe for single units and 1-1/4” (31.75 mm) for batteries. If using the optional quick-disconnect flex hose, ¾” (19 mm) iron pipe for single units and 1-1/4” (31.75 cm) iron pipe for batteries.Make sure the pipes are clean and free of obstructions, dirt, and piping compound. A battery requires one or two connections of appropriate size for the gas requirement.Prior to lighting, check all joints in the gas supply line for leaks. Use soap and water solution. Do not use an open flame.After piping has been checked for leaks, fully purge gas pipes to remove air.GAS PRESSURES (ALL MODELS):The available gas pressure should be the same as that indicated on naming plate. If incoming pressure exceeds 5 kPa, an additional pressure regulator must be installed.TESTING THE GAS SUPPLY PIPING SYSTEM:When test pressures exceed 5 kPa, the fryer and its individual shutoff valve must be disconnected from the gas supply piping system.LEVELING THE FRYERCheck the level of the fryer by placing a level on top of the fryer after gas connections have been made. Ensure that the fryer is level front-to-back and side-to-side in the final installed position. If using casters, lock the wheels after unit is level.Air adjustmentUnscrew the locking screw of the burner air shutter and adjust the air shutter to desired height. In the above picture you can find the suggested height for different types of gases. The height is the distance between burner base and air shutter.OPERATIONOVER-TEMPERATURE SHUTDOWNIf the shortening becomes overheated, a high-temperature shutoff device will turn the gas valve off and extinguish the pilot.If the fryer shuts down due to overheating, DO NOT re-light the pilot until the shortening℃℉temperature is below 149 (300 )If an overheating situation persists, contact qualified technician for help.BEFORE FIRST USECleaningNew units are wiped down at the factory to remove any visible signs of dirt, oil, grease, etc. remaining from the manufacturing process.Before any food preparation, thoroughly wipe protective oil from all surface parts and the tank interior with hot soapy water to remove any film residue and dust or debris.Do not use chlorine or sulfate/sulfide cleaners.☆ Wash any accessories shipped with unit.☆ Rinse fryer and accessories thoroughly and drain the fryer. Š Wipe tank completely dry with a soft, clean cloth.FILLING TANK WITH SHORTENINGSolid shortening should NOT be used with this type of fryer. Melting solid shortening will damage the tank.☆Close the drain valve.☆Fill the fryer tank with liquid shortening.☆Shortening level should be between the min and max lines in the fryer tank. ☆Shortening will expand when heated. Do not ill the fryer tank past the☆MAX line.☆Add fresh shortening as needed to maintain oil level.LIGHTING THE PILOT1. Open the door.2.Turn the thermostat OFF (see figure above). The thermostat is located behind the door.3.Push the gas control valve knob and turn to “O” (see figure below, view A). Wait 5 minutes forunburned gas to vent.4.5.While still holding the knob in, light the pilot with a lit flame. Continue to depress the knobuntil pilot remains lit when knob is released. If the pilot does not remain lit, repeat step 3 through 5.6.Depress and turn gas control knob to “” (See figure below, view C).7.If gas supply is interrupted, repeat steps 2 through 6.TURNING ON THE FRYER1. Set the temperature knob to desired temperature.2. After the set temperature has been reached, the thermostat shuts off the gas flow to burners.3. The pilot remains lit. The burners will cycle on and off, maintaining the set temperature. TURNING OFF THE FRYER1. Turn the thermostat OFF.3. To shut off all gas to the system, including the pilot, turn the gas valve knob to “O”. EXTENDED SHUTDOWN1. Turn the thermostat knob to OFF.2. Push in the pilot knob and turn to “O”.3. Thoroughly drain the fryer. Refer to DRAINING THE FRYER.4. Clean the fryer according to CLEANING.5. Turn off the main gas shutoff valve.BASIC FRYING INSTRUCTIONSet the desired temperature and allow shortening to heat up to that temperature.Fry items that are about the same size together to ensure equal doneness.Drain or wipe dry raw or wet foods to minimize splatter when lowering into hot shortening. Add fresh shortening as needed.Fry Basket GuidelinesDo not overfill baskets. Carefully lower basket into oil.When frying doughnuts and fritters, turn product only once during frying.When cooking French fries or onion rings, shake the basket several times in a way that does not splatter the shortening.Batter-covered foods should be dropped carefully, one by one, into shortening or basket. If you use the basket, first dip the basket into the shortening to reduce batter-build up on basket surfaces. When frying is completed, remove basket or product. Hang basket on rear hanger.EXTENDING SHORTENING LIFEShortening life can be extended by the following guidelines:☆ Do not salt foods over the fryer.☆ Use good-quality shortening.☆ Filter shortening daily (at a minimum).☆ Replace shortening if it becomes poorly flavored.☆ Keep equipment and surrounding clean.☆ Set thermostat correctly.☆ Remove excess moisture and particles from food products before placing on fryer. DRAINING THE TANK1. Turn the thermostat to OFF.3. Direct the drain spout into the container that you want to drain the shortening into.4. Open the drain valve. The oil will drain into the container. When the container is full or the fryer tank is empty, close the drain valve. Repeat this step until the fryer is empty.5. If desired, perform the weekly clean-out as described under CLEANING.6. Once tank is completely empty, add new shortening and set thermostat to desired temperature. DAILY FILTERING☆ Filter shortening at least once a day. Refer to the instructions provided with your filtering equipment.☆ A cold fryer will not drain properly. Always filter shortening between 250F and 350F. The shortening in the cold zone area will remain hard if the heat is only on for a few minutes. If necessary, use the clean-out rod to carefully stir the hard shortening to an area above the cold zone where it will melt. Use the tank brush to help clear sides and tubes of debris.CLEANINGDailyClean your fryer regularly with the tank brush along with a damp cloth, and polish with a soft dry cloth. If regular cleaning is neglected, grease will be burned on and discolorations may form. Fingerprints are sometimes a problem on highly polished surfaces of stainless steel. They can be minimized by applying a cleaner that will leave a thin oily or waxy film.☆ Clean all exterior surfaces of your fryer at least once daily.☆ Use a damp cloth with warm water and a mild soap or detergent.Do not use chlorine or sulfate/sulfide cleaners.☆ Rinse thoroughly, and then polish with a soft dry cloth.☆ Keep the fryer exterior clean and free of accumulated grease to prevent stubborn stains from forming. If regular cleaning is neglected, grease will be burned on and discolorations may form. ☆ Remove discolorations by washing with any detergent or soap and water.☆ Use a self-soaping, non-metallic scouring pad for particularly stubborn discolorations.☆ Always rub with the grain of the stainless steel. Š Do not use a metallic scoring pad or harsh cleaners.BOIL OUT PROCEDUREWeekly or as required:1.Drain the tank as described under DRAINING THE TANK.2.Once the shortening has been drained, flush out scraps and sediment with a small amount ofwarm shortening, using tank brush. Allow the tank to drain thoroughly.3.Close the drain valve and fill tank with non-corrosive, grease-dissolving commercial cleaner.Follow the manufacture’s instructions.Do not use chlorine or sulfate/sulfide cleaners.4.Add commercial boil-out solution. Solution level must be between the MIN and MAX levelson the fryer tank.5.Set thermostat to the temperature recommended for the solution being used. Allow solutionto simmer for about 15 to 20 minutes.6.Drain the cleaning solution from the tank.7.Close the drain valve and refill the tank with water. Add 1 cup (1/4 L) of vinegar to neutralizealkaline left by the cleaner. Solution level must be between the MIN and MAX level on the fryer tank.8.Bring the solution to a simmer only, turn the thermostat off. Allow to stand for a fewminutes.9.Drain the tank according to DRAINING THE TANK. Rinse thoroughly with clear, hotwater. All traces of cleaner must be removed. Dry the tank thoroughly.10.Close the drain valve and add shortening. Follow the FILLING TANK WITHSHORTENING procedure in this manual. The fryer is now ready for use. MAINTENANCEFLUE VENT INSPECTIONWhen the fryer is cool, inspect annually. Check the flue and clear any obstructions. TroubleshootingTroubleshooting Chart:Problem: Probable Cause:No Heat: Thermostat dial not turned on.Pilot not lit.Gas supply not turned on.Wire connections loose (call service)Wires connections need cleaning (call service)Thermopile (call service)Insufficient or too much heat: Thermostat dial not set to desired temperature.High limit tripped (call service)Temperature probe (call service)Tank will not drain: Shortening too cold.Drain pipe clogged with debris.Parts listKey Qty Description1 1 Screen, crumb, 3 and 4 tube fryercock2 1 Drain3 1 Tank(excluding flue)4 1 Drain, extension5 1 Flue, top, removable6 1 Flue, wrap, top, removable Wiring diagramADEXA DIRECT LIMITEDGROUND FLOOR UNIT 1 214 PURLEY WAY CROYDON CR0 4XG LONDON UNITED KINGDOM T: +44 1483 931040 ****************.uk EC Declaration of ConformityAdexa Direct Limited declares that:Equipment Type: Gas fryerModel: GF120, GF120T, GF150, GF85, GF90Imported By: ADEXA DIRECT LIMITEDGROUND FLOOR UNIT 1 214 PURLEY WAY CROYDON CR0 4XGLONDON, UNITED KINGDOMSerial Number:Year of Manufacture:Brand: ADEXAApplication of Council Directive(s): (EU) 2016/426 (9 March 2016)Standards:EN 203‐1:2014, EN 203‐2‐4:2005EN 203‐3:2009I, the undersigned, hereby declare that the equipment specified above conforms to the above Directive(s) and Standard(s).Date: 01.09.2017Signature:Full Name: Hakan BaykalPosition: Purchase Manager。
Buckeye厨房油烟净化器安装手册说明书

Buckeye kitchen mister insd flames, hot cooking surfaces and a busy environment combine to make the modern commercial kitchen a potentially dangerous fire hazard. Fires in restaurant kitchens have expanded rapidly, and it has been shown that it is very difficult to determine the cause of damage caused by structural fires in the United States. Protecting the modern commercial kitchen from the ever-present threat of oil and grease fires is why we developed a restaurant diet for restaurants: Buckeye Kitchen Mister™. Using advanced mist technology, the Mister kitchen system has proven to be the most effective kitchen fire extinguishment system, capable of extinguishing dead kitchen fires before they spread. System rolls are referred to as BFR-5, BFR-10, BFR-15 and BFR-20 rolls according to their flow capacity as the amount of reagent they contain. Recharging is available in 5 and 10 stream containers to reduce errors. The interface is used to connect the Buckye dummy cable with any standard 1/2-in tube pipe. Using Buckey's armored cable instead of pipes and angles to connect gas valve, remote cartoon station and connect fuse to unlock system shortens installation time to 50%. Five noise number of the kitchen Mister Kitchen has a color ID for easy identification of nozzles even when installed in difficult places: red, blue, green, white or yellow. On the Subscriber List Laboratories, Inc. (Standard UL-300) Listed by Underwriters Laboratories of Canada, Inc. Approved by New York Co #5550 Fire Service in accordance with NFPA-96 and NFPA-17A standards. The Mister Kitchen system is approved for use with the Buckey armored cable instead of traditional pipes and corner pulleys for all inputs and system outputs. Buckeye armored cable is used for gas valve, detection control and sampling station. My kitchenAn open flame, red stains on kitchen surfaces and a greasy environment combine to make today's commercial kitchen a potential fire hazard. Restaurant kitchen fires spread quickly and are extremely difficult to extinguish, making them the leading cause of structural fire damage in the United States. To protect the modern commercial kitchen from the constant threat of cooking oil and grease fires, we developed a fire extinguishing system for restaurants: the Buckeye Kitchen Mister\xe2\x84\xa2 system. The Küchenmister system has proven to be the most effective stationary kitchen fire extinguishing system ever developed, extinguishing deadly kitchen fires before they spread. System Cylinders Model BFR-5, BFR-10, BFR-15 and BFR-20 cylinders are designated by their pour point, not the amount of active ingredient they contain. To reduce the number of errors, the filling is in 5 and 10 point containers. The interface is used to connect the Buckeye Shield cable to a device with a standard 1/2-inch connector. By using Buckeye cable instead of lines and angle washers to connect the gas valve, remote station, and fusible link line to the system shutdown module, installation time is reduced by up to 50%. All five Kitchen Mister model number accessories have a color identification strip that makes it easy to identify the accessory, even when installing in hard-to-reach places: red, blue, green, white or yellow. Underwriters Laboratories, Inc. is listed. (UL-300 standard) Listed Underwriters Laboratories of Canada, Inc. Approved New York City Fire Department CoA no. 5550, conforms to NFPA-96 and NFPA-17A. Use Buckeye shielded cable. instead of the usual cables and corner plates for all system inputs and outputs. Shielded Buckeye cable for gas valve, detection line and pull station.Fire protection company | 110 Kings Road, Kings Mountain, NC 28086 Postfach 428 | Telephone: 704-739-7415 | All rights reserved
3L100P 1 2 PL10 雾油润滑器安装与维护指南说明书

Installation & Service Instructions:3L100P1/2" PL10 Mist LubricatorsISSUED: January, 2003Supersedes: April, 2001Doc.# 3L100, ECN# 020674, Rev. 2 IntroductionFollow these instructions when installing, operating, or servicingthe product.Application LimitsThese products are intended for use in general purposecompressed air systems only.Operating Pressure Maximum kPa PSIG barBowl w/ Twist Drain / No Sight Gauge206830021.0Bowl w/ Twist Drain and Sight Gauge170025017.0Operating Temperature Range:4°C to 82°C (40°F to 180°F)SymbolsLubricatorw/Manual DrainInstallation1.The lubricator should be installed with reasonableaccessibility for service whenever possible. Keep pipe ortubing lengths to a minimum with inside clean and free ofdirt and chips. Pipe joint compound should be usedsparingly and applied only to the male pipe – never intothe female port. Do not use PTFE tape to seal pipe joints –pieces have a tendency to break off and lodge inside theunit, possibly causing malfunction.2.Install lubricator so air flows in the direction of arrow onbody.3.Installation should be upstream of the device it is to lubricate(valve, cylinders, tool, etc.) as possible.Pneumatic Division North AmericaRichland, Michigan 49083!!WARNINGTo avoid unpredictable system behavior that can cause personalinjury and property damage:•Disconnect electrical supply (when necessary) before installation,servicing, or conversion.•Disconnect air supply and depressurize all air lines connected tothis product before installation, servicing, or conversion.•Operate within the manufacturer’s specified pressure, temperature,and other conditions listed in these instructions.•Medium must be moisture-free if ambient temperature is belowfreezing.•Service according to procedures listed in these instructions.•Installation, service, and conversion of these products must beperformed by knowledgeable personnel who understand howpneumatic products are to be applied.•After installation, servicing, or conversion, air and electricalsupplies (when necessary) should be connected and the producttested for proper function and leakage. If audible leakage is present,or the product does not operate properly, do not put into use.•Warnings and specifications on the product should not be coveredby paint, etc. If masking is not possible, contact your localrepresentative for replacement labels.WARNINGFAILURE OR IMPROPER SELECTION OR IMPROPER USE OFTHE PRODUCTS AND/OR SYSTEMS DESCRIBED HEREIN ORRELATED ITEMS CAN CAUSE DEATH, PERSONAL INJURY ANDPROPERTY DAMAGE.This document and other information from Parker Hannifin Corporation,its subsidiaries and authorized distributors provide product and/orsystem options for further investigation by users having technicalexpertise. It is important that you analyze all aspects of yourapplication, including consequences of any failure and review theinformation concerning the product or systems in the current productcatalog. Due to the variety of operating conditions and applicationsfor these products or systems, the user, through its own analysis andtesting, is solely responsible for making the final selection of theproducts and systems and assuring that all performance, safety andwarning requirements of the application are met.The products described herein, including without limitation, productfeatures, specifications, designs, availability and pricing, are subjectto change by Parker Hannifin Corporation and its subsidiaries at anytime without notice.EXTRA COPIES OF THESE INSTRUCTIONS ARE AVAILABLE FORINCLUSION IN EQUIPMENT / MAINTENANCE MANUALS THAT UTILIZETHESE PRODUCTS. CONTACT YOUR LOCAL REPRESENTATIVE.Service Kits AvailableDescription PL10 (1/2")Drip Control and Fill Plug Kit PRKL10SS1/2" PL10 Mist Lubricators 3L100POperation and ServiceCaution: Shut off air supply and exhaust the pressuretrapped within the lubricator before filling unit.1.Remove the fill plug and fill the lubricator with thesuggested lubricant.Suggested lubricant: F442Petroleum based oil of 100 to 200 SSU viscosity at 100°F and an aniline point greater than 200°F . (Mobil DTE24and Sun Company Sunvis 932 are good examples). Do not use oils with adhesives, compound oils containing solvents, graphite, detergents or synthetic oils.2.Replace the fill plug (by turning clockwise) and seat firmly.Excessive torque is not required. If leakage occurs, DO NOT OPERATE — check to make sure the fill plug is installed properly. The lubricator is now ready for setting.3.O il delivery adjustment — T o adjust oil delivery, turnadjustment knob on top of the lubricator.Leaner — Clockwise Richer — CounterclockwiseBy counting the number of drops per minute in the sight dome, you can adjust to your requirements.Every drop visible in the sight dome goes downstream.Generally, one drop per minute downstream for every 10 - 15 SCFM flow is satisfactory.25 drops per minute equals one (1) ounce per hour -volume of oil passing through the sight dome.NO TE: This is a constant density type lubricator which delivers a constant ratio of oil to air flow. Therefore, if air flow increases or decreases, oil delivery will be adjusted proportionately. O NLY IF A DIFFERENT RATIO IS DESIRED SHO ULD YO UR ADJUSTMENT KNO B SETTING BE CHANGED AFTER YO UR INITIAL SETTING.4.To replace fill plug, drip control, & service lubricator:A.T urn off air supply and depressurize the unit.B.Refer to pictorial for servicing and torque values.C.T urn on air supply and check lubricator for leakage.If leakage occurs, DO NOT OPERATE — conduct repairs again.Inspect for nicks, scratches, and surface imperfections.If present, reduced service life is probable and future replacement should be planned.Clean with lint-free cloth.(Finger Tighten)Lubricator BodyDrip Control Fill Plug Torque:1.2 to 1.7 Nm(11 to 15 in. lb.)}PL10 Metal Bowl With Sight Gauge!。
ACCU-LUBE(BLUBE)阿库路巴
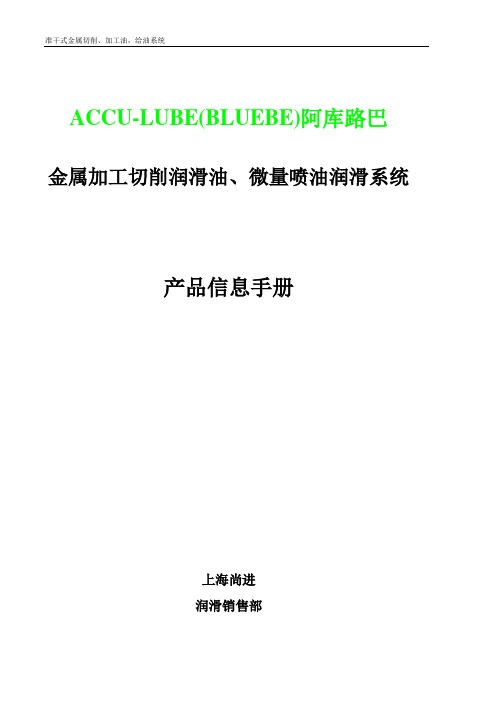
ACCU-LUBE(BLUEBE)阿库路巴金属加工切削润滑油、微量喷油润滑系统产品信息手册上海尚进润滑销售部阿库路巴(ACCU-LUBE/BlueBe)金属加工液是冶金制造行业的自然选择当你调查市场利益的时候,阿库路巴金属加工切削产品是你的第一选择……ITW ROCOL North America是为金属加工产业提供科学、先进的润滑产品的先驱者。
与传统的水溶性冷却剂、乳化液和切削油相比,纯天然的阿库路巴油为具有高效、经济、安全环保等特点。
标准型号的阿库路巴给油机可广泛应用于绝大多数的金属加工行业、我们的工程师还能针对各种特殊的情况具体设计、定做微量给油润滑系统。
一点点润滑油的准干式切削润滑有以下优点:●替代传统乳化液、切削油●极少耗用量●节约成本●延长工具使用寿命●提供安全工作环境●操作干净●工件不变色、不污染●无毒●无处理成本●减少机器维护费●无需后处理在许多行业中得到证明:●钻深孔●铣●研磨●车螺纹、攻丝●圆锯●带锯●铰孔●切削●折弯、剪边●扩孔●拉丝●成型、冷轧成卷●去毛边●拉削●冲压成型、冲孔●磨刀具●链条润滑应用ACCU-LUBE方便、安全、益处多ACCLUBE为您提供一系列完善的服务,包括纯天然的润滑剂,还有专业、成熟的获有专利的精密润滑系统。
这些产品无毒、保护环境,被广泛应用于多种行业,不会造成污染。
它们可以提高工作效率,增加作业安全,以下可以证明。
ITW ROCOL North America作为ACCU-LUBE产品的生产商,是向金属加工行业提供科学、先进的金属加工液体的工业先驱。
它推动了该产品在金属制造行业中的应用。
我们的母公司,美国伊诺斯工具有限公司,是财富200强之一,是世界上技术革新最快的公司之一。
环境安全ACCU-LUBE无毒、不会过敏。
ACCU-LUBE喷油器将润滑液喷向切割口边缘,不会产生油雾粒子。
ACCU-LUBE可生物分解,对环境起保护作用。
它不会对水、空气和土壤的质量产生损害,在你使用它的时候它自然地消耗。
AccuProbe IR 泄漏侦测器使用与维护说明书 型号 69320

AccuProbe™ IR Leak DetectorOperation and MaintenanceManualModel: 69320Made in the USAwith Globally Sourced PartsPOWER ON: Turn on or off by long press-ing the ON/OFF button. The power LED will illuminate green unless battery is low.WARM-UP: During warm-up, the unit will beep slowly and the signal LEDs will continuously scroll from left to right until warm-up is complete. Warm-up time is 45 to 90 seconds.SEARCH: Detector is ready for use when signal LEDs stop scrolling from left to right and a different beep rate can be heard.If a leak is detected, the signal LEDs will illuminate from left to right and the beep rate will increase. The number of LEDs illuminated indicates the strength of the leak.The default mode is Standard mode. In Standard mode, the detector automati-cally zeros to the background refrigerant. Once it zeros, the alarm will stop and it will only alarm to a higher concentration of refrigerant. To reset the zero point, hold the probe in clean air for a few seconds to allow the detector to re-zero.ADJUSTING THE SENSITIVITY LEVELS: Short press the ON/OFF button to toggle sensitivity from high to low. The HIGH or LOW LED will illuminate to indicate the current sensitivity setting. High is the default setting during power on.MANUAL MODE: Short pressing the MODE button toggles between Standard mode and Manual mode. Manual mode is indicated by the 1st signal LED slow blinking and both HIGH and LOW LEDs being off.In manual mode, if a leak is detected, the detector will alarm until the MODE button is long pressed. The HIGH and LOW LEDs will blink for 1 second to indicate theOPERATING INSTRUCTIONS2detector is zeroing. At this point, the detector will only alarm if a high concen-tration of refrigerant is detected.You can also reset the zero point in clean air by holding the detector in clean air and long pressing the MODE button again.BATTERY AND CHARGING: The power LED will slow blink red when the battery is 10% or less. If the battery is depleted completely, the power LED will illuminate solid red and the unit will not operate.To charge the unit, plug the supplied micro USB cable into an appropriate USB charging port per the input specifications (see specifications).When charging, the power LED will slow blink green until fully charged, then remain solid green.ERRORS: If the battery is above or below charge temperature, the unit will not charge and the power LED will alter-nate red and green. In this case, let the battery cool or warm up. The unit will charge once the battery is within the safe operating temperature.Other faults or internal errors are indicat-ed when all LEDs blink. Contact Ritchie Engineering Company, Inc. for service in this case.FILTER REPLACEMENT: Accuprobe ™ IR has an integrated filter and probe tip. To replace the filter/probe tip assembly, simply unscrew the probe tip and screw on the new filter/probe tip assembly. Do not attempt to clean the filter.SENSOR/BATTERY REPLACEMENT: The sensor and battery in Accuprobe ™ IR are not field replaceable. For instru-ment service, contact Ritchie Engineering Company, Inc.3• Sensor Type: Infrared • Battery Type: Lithium Ion• Charging Input Type: Micro USB• Charging Time (starting at 0%): Approx 3 hours • Battery Life: 8 hours• Input Voltage: 5 V (dc) ±5%• Input Current: 1 A ±5%•Temperature Ranges and Humidity:▪Storage: -20–60°C (-4–140°F) ▪Operating*: -20–50°C (-4–122°F) ▪Charging: 0–45°C (32–113°F) ▪Humidity: 95% RH NC maximumSPECIFICATIONS• Only use a certified charger/cord with an output of 5 V (dc) ±5%, 1 A ±5%• Keep the device out of extremely high or low temperature locations • Do not expose the battery to liquid• Do not use the device if you notice any damage to the battery • Do not disassemble or modify the battery• Handle and dispose of the battery per local regulations• If the recharging operation fails to complete, even when the specified recharging time has elapsed, immediately stop further recharging • Do not leave the battery unattended while charging • Unplug the charger when the battery is fully charged• Improper use or disposal of lithium ion batteries can cause a fire • This instrument is not intended for use in flammable environmentsCAUTIONSButtonLEDsPower LED Sensitivity LEDsON/OFF ButtonProbe Tip• Altitude: 2000 m (6500 ft.)• Pollution Degree: 2• Overvoltage Category: 2• Weight: 0.84 lb. (0.38 kg)* Use below 0°C (32°F) should be limited24 MONTH LIMITED WARRANTY Ritchie Engineering Company, Inc. guarantees YELLOW JACKET® Accu-Probe™ IR Leak Detectors to be free of defective material and workmanship that would affect the life of the product under normal use for the purpose for whichit was designed. This warranty doesnot cover items that have been altered, abused, misused, improperly maintainedor returned solely in need of field service maintenance. This warranty excludes the sensor, which has a one year warranty.If found defective, we will upon compliance with the following instruc-tions, credit, replace or repair at our option, the defective leak detector provided it is returned within 24 monthsof the date of sale. AccuProbe™ IR Leak Detectors have a date of manufacture serial number located on the label on the bottom of the unit.Correction in the manner provided above shall constitute a fulfillment of allMost returned AccuProbe™ IR Leak Detec-tors are merely in need of normal field service maintenance, such as making minor adjustments. In many instances, the information in this manual can save you the time and effort of returning your AccuProbe™ IR Leak Detector. If the infor-mation contained in this manual does not solve the problem, please call for service.Ritchie Engineering Company, Inc. YELLOW JACKET® Products Division 10950 Hampshire Avenue South Bloomington, MN 55438-2623 USAE-mail:************************* Website: Phone: (800) 769-8370(952) 943-1333 INTLFax: (800) 322-8684(952) 943-1605 INTL©1/20Ritchie Engineering Company,Inc. liabilities with respect to the quality, material and workmanship of the product. THE FOREGOING WARRANTY IS EXCLUSIVE AND IN LIEU OF ALL OTHER WARRANTIES OF QUALITY, WHETHER WRITTEN, ORAL OR IMPLIED.See to register your product or contact Customer Service for full warranty details.Contact the Ritchie Engineering Customer Service Department:Phone: (952) 943-1300 or(800) 769-8370Fax: (952) 943-1605 or(800) 322-8684E-mail:************************* You will receive personal help to determine if the problem can be solved without sending your leak detector to the factory and taking it out of service.HOW TO OBTAIN SERVICE4。
兰爱尔产品4109 Capital Circle 215 Gallon 汽油废油罐及燃烧器安装说明书

215 GallonWaste Oil TankWith Metering PumpInstallation InstructionsLanair Products LLC4109 Capital CircleJanesville,Wisconsin 53546®BEFORE YOU BEGIN INSTALLATION...IMPORTANTRead and understand this manual completely before beginning installation.•This tank is for commercial and industrial use only.This unit is not intended for residential use.•Install Heater/Tank combination in an area that is protected from fork lift and motor vehicle traffic.•Bolt tank to floor before you fill the tank or install the heater.• Secure the heater to a permanent structure after installation.•Install the heater according to the printed information in your owners manual.• Installation of this unit must be made in accordance with state and local codes orauthorities having jurisdiction over environmental control,fuel,fire and electrical safety.•Read and familiarize yourself with these instructions and associated photos,diagrams and illus-trations before beginning installation or operation.These instructions should be followed closely,to achieve the best possible results.If you have questions or concerns at any time during the installation,stop the installation and contact a Lanair Service Representative.•Check to make sure you have all the required components needed for proper installation and operation.• Check each component for visible damage.If you find a damaged component,contact a Lanair Service Representative for a replacement.Do not install broken or damaged parts.•Read and understand the warranty.Fill out the enclosed warranty card and return within 10days of purchase.•Clean and de-burr all pipe connections prior to use.Loose filings and burrs can clog the nozzle.• Install Heater/Tank combination in an area that is protected from fork lift and motor vehicle traffic.• Bolt tank to floor before you fill the tank or install the heater.• Secure the heater to a permanent structure after installation.• Install the heater according to the printed information in your owners manual.!Part # 8909Tee1/4” x 1/4” x 1/4”QTY: 1Part # 8915Nipple1/8” x 2”QTY: 1Part # 8908Bushing1/8” x 1/4”QTY: 1Part # 8462Check Valve1/4” NPT x 1/4” FNPTQTY: 1Part # 8917Brass Elbow3/8” Comp x 1/4” NPTQTY: 1Part # 8939Brass Fitting3/8” Comp x 1/4” NPTQTY: 1Part # 8902Elbow Street1/2”QTY: 2Part # 8904Bushing1/2” x 1”QTY: 2Part # 8917Brass Elbow3/8” Comp x 1/4” NPTQTY: 2Part # 8602Elbow1/2”QTY: 1Part # 9412Tee1/2” x 1/4” x 1/2”QTY: 1Part # 8919Tee1/2” x 1/2” x 1/2”QTY: 1Part # 8186Nipple Close1/2”QTY: 5Part # 8647Nipple Close1/4”QTY: 1Part # 8558Coupling Reducing1/2” x 1/4”QTY: 2Part # 8185Pipe Plug1/2”QTY: 2Part # 8556Union1/2”QTY: 1Part # 7101Screw#10 x 1”QTY: 4Part # 8557Nipple1/2” x 5-1/2”QTY: 2Part # 8924Cap1/2”QTY: 1®Part # 9030Pick-up Tube Qty: 1Part # 89213/8” Copper Tube 180”Qty: 1Section 2 - Installation Instructions TANK INSTALLATION1.Unwrap the tank and parts.2.Choose tank location.Locate the tank in anarea that is protected from lift truck and motorvehicle traffic.NOTE:Make sure you haveenough room to install and service your heater.3.Anchor all four legs of the tank to the floor asindicated In Fig.1.NOTE:This method ofanchoring is a suggestion only.Anchoringmethods may vary per individual applicationsand environments.Check state and local codes for clarification.4.Install the four tank legs included with the tankon top of the bottom legs (see Fig.2).ing a forklift,lift and center the heater on topof the platform.NOTE:The front of each unit is indicated on the top of the tank platforming a forklift,carefully raise the platform andheater assembly and place on top of the previ-ously installed legs (see Fig.2).7.Locate the four holes on the bottom side ofthe heater platform.Attach the heater to theplatform using four #10 x 1" screws provided.Concrete Anchor(not included)FIGURE 1FIGURE 2 Top Tank LegHeaterAssemblyBurneron RightBottom TankLegPlatformPumpPlatformLabel®2.Locate the pick-up tube assembly (P/N 9030).This tube will have a 2" bushing welded onto it.3.Attach the brass check valve (P/N 8662 - included in the heater accessory kit) to the bottom of the pick-up tube assembly (P/N 9030).NOTE:The arrow on the check valve must point in the direction of the oil flow (up) or the check valve will not work properly (see Fig.4).4.Attach the 1/2" elbow (P/N 8902) to the check valve.Attach the suction line strainer (P/N 8748 -included in the heater accessory kit) to the 1/2" elbow (P/N 8902) as indicated in Fig.4.5.Insert the pick-up tube assembly into the 2" bung (hole) and tighten (see Fig.3 for bung location).4.Install a 1/2" x 1" bushing (P/N 8904), 1/2" elbow street (P/N 8902), 1/2" close nipple (P/N 8186), 1/2" x 1/4" x 1/2" tee (P/N 9412), 1/2" close nipple (P/N 8186) and Union (P/N 8556) to the primary strainer assembly (P/N 9807) as indicated in Fig. 5 above. NOTE: When making plumbing connections, use the thread seal compound (P/N 5277) included in the plumbing kit on all joints.DO NOT USE TEFLON TAPE.®PLUMBING INSTALLATION - Pick-Up Tube to Pump Plumbing (cont.)5.Install a 1/4" close nipple (P/N 8647) to the pump head (see Fig.5,page 7).6.Install a 1/4" x 1/2" reducing coupling (P/N 8558),elbow (P/N 8902) and 1/2" x 5" nipple to the previously installed 1/4" close nipple (see Fig.5,page 7).7.Separate the 1/2" union (P/N 8556) as indicated in Fig.5.8.Re-assemble the union and tighten.9.Check to make sure all joints are tight.NOTE:1/4" x 1/2" tee (P/N 9412) as indicated in Fig.6.®©2013 Lanair Products LLC Lanair is a registered trademark of Lanair Products LLC Part # 5300Rev. 16REV. 04-18-2013Lanair Products LLC 4109 Capital CircleJanesville, Wisconsin 535461-888-370-6531。
- 1、下载文档前请自行甄别文档内容的完整性,平台不提供额外的编辑、内容补充、找答案等附加服务。
- 2、"仅部分预览"的文档,不可在线预览部分如存在完整性等问题,可反馈申请退款(可完整预览的文档不适用该条件!)。
- 3、如文档侵犯您的权益,请联系客服反馈,我们会尽快为您处理(人工客服工作时间:9:00-18:30)。
1. Liquid Reservoir: Lightweight, durable polycarbonate reservoir (several sizes and designs are available, see page 12 for information).
2. Reservoir Extension: Connects the liquid reservoir (#1) to the applicator. 3. Braided Air Hose: Carries compressed air to the nozzle.* 4. Lubricant Line: Capillary tube that runs inside the braided air hose.*
An Accu-Lube precision pump uses positive displacement and air pressure to power the pump cycle. The back stroke of the cycle draws a precise, measured amount of lubricant into a chamber like a syringe. Instantly the forward stroke forces the lubricant down a capillary tube inside an air hose up to 60 ft. (18 m) long. Since the pump cycle is automatically regulated by a frequency generator it is not affected by lubricant viscosity, which changes with temperature. This is crucial for any application operating in an environment without climate control since lubricants thicken in the cold. Accu-Lube precision pumps deliver instant performance, with every type of Accu-Lube lubricant, in all conditions.
unPAckIng & InsPectIng
Before beginning set-up make sure that you have the following items: 1. Accu-Lube precision pump applicator (Box, Junior, or Custom Applicator) 2. Liquid reservoir 3. Nozzles and mounting clamps (if applicable) 4. 8 oz. LB-2000 sample 5. Warranty card, fill out and return within 10 days of purchase If one of these items is missing do not continue with set-up. Contact Customer Service at 800-452-5823 ext. 2 regarding missing/damaged items.
*Hose Assembly: braided air hose (#3) & lubricant line (#4). 5. Airflow Valve: Controls the amount of continuous air supplied to the nozzle. 6. Security-Box (Box & Custom Applicators only): Durable steel box with lock.
ITW ROCOL North America
ITW ROCOL North America, manufacturer of Accu-Lube products, is an industry leader in the development and production of scientifically advanced fluid products for the metalworking industry.
IntroducIng Accu-Lube
History of Excellence
Since 1979 Accu-Lube has been the industry leader in manufacturing lubricants and equipment for Minimum Quantity Lubrication (MQL). Today Accu-Lube continues to be at the forefront of MQL and near-dry machining through a dedication to innovation, safety, and service.
Quality over Quantity
Accu-Lube MQL precision pump applicators use advanced technology to focus droplets of lubricant directly onto the tool’s cutting edge, providing lubrication and protection precisely where it is needed. This minimum quantity approach allows manufacturers to conserve fluid and cut down on waste. By eliminating unneeded flood coolant shops remain clean and fluid maintenance is no longer necessary. This process is called Near-Dry Machining.
Accu-Lube precision pumps are designed to accurately deliver a constant and consistent amount of lubricant from the instant the applicator is turned on until the moment it is turned off. Unlike cheap siphon-type imitators, which are negatively affected by small variances in air pressure, room temperature, air hose length, and lubricant viscosity, Accu-Lube precision pumps operate with accuracy and precision year after year to deliver lubricant to the cutting edge each time, every time.
Precision Pump Applicator
2
tAbLe of contents Components .............................................................4 Preparing ..................................................................5 Installing ..................................................................6 Nozzle Positioning ............................................... 6-7 Operating ..................................................................7 Setting the Lubricant Control............................... 8-9 Setting the Frequency Generator ...........................10 Re-Priming the Pump.............................................10 Replacing the Hose Assembly ...............................11 Replacement Parts............................................ 12-13 Warranty .................................................................13 Troubleshooting .....................................................14 Technical Support ..................................................14
3
Precision Pump Applicator
comPonents
1 7
2
8
+AIRFLOW– +AIRFLOW–
– OIL+ –来自OILI IIIIII5I0I