精益生产基础(一)
精益生产系列之活动基础知识

增强员工技能:通过培训、实践、交流等方式,增强员工技能,提高员工素质。
改善工作环境:通过改善现场管理、减少噪音、保持清洁等方式,改善工作环境,提高员工 满意度。
实现可持续发展:通过采用环保材料、减少能源消耗、降低排放等方式,实现可持续发展, 提高企业形象。
目的:识别浪费,提高生产效率
步骤:价值流图绘制、价值流图分析、制定改进措施
工具:价值流图、生产过程流程图等
浪费的定义和类型 识别浪费的方法和技巧 消除浪费的步骤和措施 持续改进和优化
持续改进的定义和重要性 持续改进的步骤和方法 持续改进的实践案例 持续改进的未来展望
PART FOUR
确定改善项目:明确需要改进的生产环节或流程 设定目标:设定具体的、可衡量的、可实现的、有时限的目标 制定计划:制定详细的实施计划,包括时间表、责任人、所需资源等 实施改进:按照计划实施改进措施,持续跟进并调整计划
制定计划:根据分析结果,制定详细的实施计划,包括时间表、人员分工、资源分配 等。
审核与调整:对制定好的计划进行审核,确保其可行性和有效性,并根据实际情况进 行调整和优化。
明确改进目标:确定改进活动需要解决的问题和目标 制定改进计划:根据改进目标,制定详细的改进计划 实施改进措施:按照改进计划,采取具体的改进措施 监控和评估:对改进活动进行监控和评估,确保改进效果符合预期目标
鱼骨图:通过将问题分解成若干个因素,并对其进行分类和整理,找出关键因素,提出相应的解决方案。
价值流图:通过绘制产品从原材料到最终产品的整个流程图,找出浪费和不合理的环节,提出改进措施。
PART SIX
标准化操作:通过标准化操作, 提高生产线的稳定性和效率
JIT精益生产基础知识培训资料
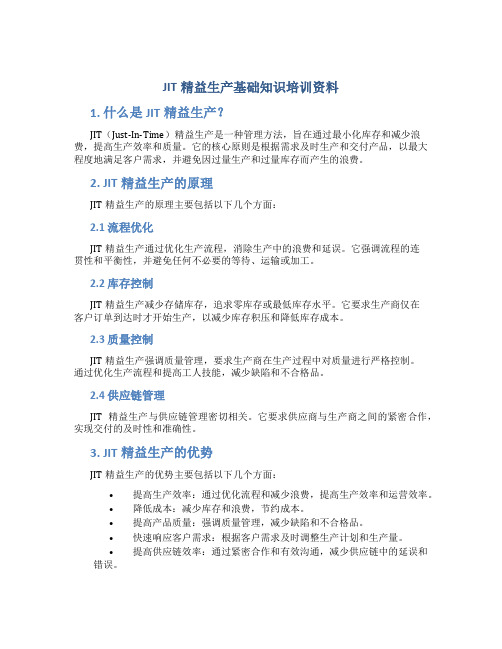
JIT精益生产基础知识培训资料1. 什么是JIT精益生产?JIT(Just-In-Time)精益生产是一种管理方法,旨在通过最小化库存和减少浪费,提高生产效率和质量。
它的核心原则是根据需求及时生产和交付产品,以最大程度地满足客户需求,并避免因过量生产和过量库存而产生的浪费。
2. JIT精益生产的原理JIT精益生产的原理主要包括以下几个方面:2.1 流程优化JIT精益生产通过优化生产流程,消除生产中的浪费和延误。
它强调流程的连贯性和平衡性,并避免任何不必要的等待、运输或加工。
2.2 库存控制JIT精益生产减少存储库存,追求零库存或最低库存水平。
它要求生产商仅在客户订单到达时才开始生产,以减少库存积压和降低库存成本。
2.3 质量控制JIT精益生产强调质量管理,要求生产商在生产过程中对质量进行严格控制。
通过优化生产流程和提高工人技能,减少缺陷和不合格品。
2.4 供应链管理JIT精益生产与供应链管理密切相关。
它要求供应商与生产商之间的紧密合作,实现交付的及时性和准确性。
3. JIT精益生产的优势JIT精益生产的优势主要包括以下几个方面:•提高生产效率:通过优化流程和减少浪费,提高生产效率和运营效率。
•降低成本:减少库存和浪费,节约成本。
•提高产品质量:强调质量管理,减少缺陷和不合格品。
•快速响应客户需求:根据客户需求及时调整生产计划和生产量。
•提高供应链效率:通过紧密合作和有效沟通,减少供应链中的延误和错误。
4. JIT精益生产的实施步骤JIT精益生产的实施步骤包括以下几个方面:4.1 识别和消除浪费首先,要对生产过程中的浪费进行识别和分类。
常见的浪费包括等待时间、废品、过程中的不必要移动等。
然后,制定相应的计划和策略,减少或消除这些浪费。
4.2 改善生产流程根据浪费的消除计划,对生产流程进行改善。
包括优化工作站布局、减少运输距离、改进工艺流程等。
确保生产流程的连贯性和平衡性。
4.3 建立稳定的供应链与供应商建立紧密的合作关系,确保供应链的稳定和可靠。
Lean精益生产基础知识-精选文档
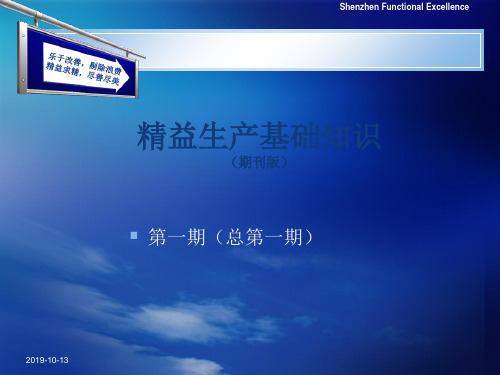
Creates a system which is intolerant of production abnormalities (不能容忍生产异常)
Eliminates waste in production processes (消除生产过程浪费)
Reduces lead times (缩短前置生产时间)
2019-10-13
Shenzhen Functional Excellence
Abnormality Response Process
(异常反应过程)
Q C D S
Measure impact (衡量影响)
React to problem (发现问题)
MAN MACHINE
EFFECT
Alert team (提醒 同事)
Raw materials (原料) Equipment (设备)
Labor (人力)
2019-10-13
Space (场地)
Shenzhen Functional Excellence
JIT Principles (及时生产三原理)
及时生产 JIT
Takt time (节拍生产)
METHOD
MATERIAL
Find root cause (找出原因)
(提出改善, 进行试 验)
Develop and test improvement
Ensures on-time delivery (保证准时交货)
Quality…Cost…Delivery…Safety…
2019-10-13
Shenzhen Functional Excellence
Jidoka is (自働化是)…
精益生产方式思想基础
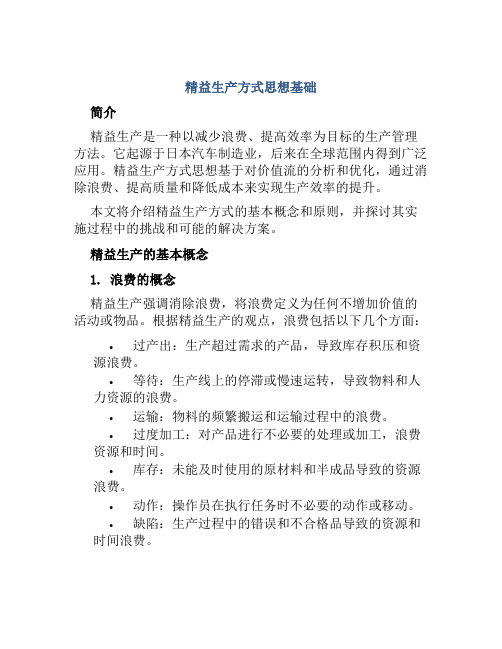
精益生产方式思想基础简介精益生产是一种以减少浪费、提高效率为目标的生产管理方法。
它起源于日本汽车制造业,后来在全球范围内得到广泛应用。
精益生产方式思想基于对价值流的分析和优化,通过消除浪费、提高质量和降低成本来实现生产效率的提升。
本文将介绍精益生产方式的基本概念和原则,并探讨其实施过程中的挑战和可能的解决方案。
精益生产的基本概念1. 浪费的概念精益生产强调消除浪费,将浪费定义为任何不增加价值的活动或物品。
根据精益生产的观点,浪费包括以下几个方面:•过产出:生产超过需求的产品,导致库存积压和资源浪费。
•等待:生产线上的停滞或慢速运转,导致物料和人力资源的浪费。
•运输:物料的频繁搬运和运输过程中的浪费。
•过度加工:对产品进行不必要的处理或加工,浪费资源和时间。
•库存:未能及时使用的原材料和半成品导致的资源浪费。
•动作:操作员在执行任务时不必要的动作或移动。
•缺陷:生产过程中的错误和不合格品导致的资源和时间浪费。
2. 价值流图精益生产使用价值流图来分析生产过程中的价值流和浪费。
价值流图是一种图形化工具,用于可视化生产过程中的各个环节和流程,并标识出其中的浪费点。
价值流图的绘制需要考虑以下几个要素:•价值流:从原材料到最终产品的所有流程。
•价值流中的价值增加环节:实际为产品添加价值的环节。
•流程时间:完成每个环节所需的时间。
•库存:每个环节中存储的物料数量。
•流程中的浪费:包括等待时间、运输时间、过度加工等。
3. 在精益生产中消除浪费的方式精益生产通过量化和深入分析浪费的根源,提出了一系列消除浪费的方式,包括:•质量管理:通过强调质量的重要性和培养质量意识,减少产品缺陷,避免浪费。
•5S方法:通过整理、整顿、清扫、清洁和纪律的执行,改善工作环境,提高工作效率。
•供应链优化:与供应商和合作伙伴合作,通过减少物料运输时间和库存,降低整体生产成本。
•作业标准化:定义明确的工作标准和流程,减少错误和重复工作。
•连续改进:通过监测和分析生产过程中的绩效指标,持续改进生产效率和质量。
精益生产基础知识

①.利用夹具或轨道限定动作路径; ②.抓握部的形状要便于抓握; ③.在可见的位置通过夹具轻松定位; ④.用轻便操作工具。
基本原则
要点
要素
动作经济原则
三、精益屋
课后作业: ECRS:发现一个可改善问题点; 动作经济原则:做一个工序的动作分析,并给出改善方案。
Thank You
*
三、精益屋
2.合并(combine)
合并就是将两个或两个以上的对象变成一个。如工序或工作的合并、工具的合并等。合并后可以有效地消除重复现象,能取得较大的效果。当工序之间的生产能力不平衡,出现人浮于事和忙闲不均时,就需要对这些工序进行调整和合并。有些相同的工作完全可以分散在不同的部门去进行,也可以考虑能否都合并在一道工序内。 例如,合并一些工序或动作,或将由多人于不同地点从事的不同操作,改为由一个人或一台设备来完成。
三、精益屋
1.减少动作数
2.双手同时进行
3.缩短动作距离
4.轻快动作
是否进行多余的搜索、选择、思考和预制
某只手是否处于空闲等待或拿住状态
是否用过大的动作进行作业
能否减少动素数
1.作业动作
①.取消不必要的动作; ②.减少眼的活动; ③.合并两个以上的动作。
①.双手同时开始,同时结束; ②双手反向、对称同时动作。
“简化”具体操作
简化包括将复杂的流程加以简化,也包括简化每道工序的内容: 减少各种繁琐的程序,减少各种复杂性。 使用最简单的动作来完成工作。 简化不必要的设计结构,使工艺更合理, 力求作业方法的简化。 运送路线、信息传递路线力求缩短。
三、精益屋
ECRS分析原则的适用性
Lean基础知识培训教材(1)
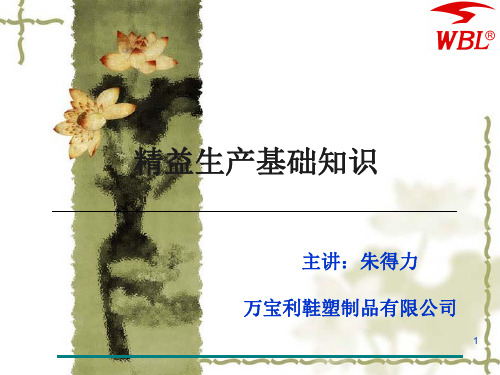
(四)后拉式生产
定义﹕也称看板生产方式
是由下游发向上游单位生产和交期指令的系统,上游供应商 在下游客戶尚未发出信号以前不会制造出任何东西。
在制造部分,代表只制造出客戶需求(下游單位)的产量即可。 若考虑到物料的控制,它代表存货的提领是由正在进行的作
业所要求,物料不会主动流向下游除非得到客戶的信号。
38
后拉式看板举例
39
持续改善﹐不断精进﹗
THE END!
40
材料损失
能源消耗
18
三﹑效率的认识
表面效率与实质效率:
表面效率:亦称为假效率,其意义是效率虽然提高,但公司利润并沒 有提高。 实质效率:亦称为真效率,依市场订单的需求数量生产,不多做出库 存品,而又能提升效率。
个別效率与全体效率:
个別效率:指仅考虑单一个人的效率,或仅考虑单一因素的效率, 个別作业人员的效率提高,只是表象而已,对于全公司整体的效率, 有时不升反降。 全体效率:必须考虑诸多因素,整体性利益考量, 全面配合来达 成整条线全体作业员的目标产量,评估大家的共同绩效,而非仅衡量 个別工程或个別作业员的效率。
占用生产空间,产生不必要的仓库建设費用以及搬运设备的投资; 库存会积压资金,不但损失了利息、增加资金的需求,还影响企业扩充
成长的机会; 为了保管库存,衍生许多不必要的额外工作,如搬运、堆集、取放、
防护、找寻、文书作业等; 库存产品有时因放置过久,使品质变异成为次品、呆滞品,甚至成为
报废品,产品价值因此降低;
机器设备需能满足TT;
人员的技能水平符合要求。
31
32
(二)安定化生产
人员的安定
人员安定取决于 “标准作业”﹔ 标准作业三要素﹕产距时间﹑标准在制品﹑作业顺序﹔
精益生产基础知识

动 4. Involve and Empower employees.
全员参于并充分授权。
5. Continuously improve in pursuit of
perfection. 不断改进,追求完美。
价值 价值流
拉动 全员参于 不断改进
4、精益实践方法
不良品都是连1元钱的收益也无法得到的产品、但生产不良品所花费的劳动者的 时间、购买的原材料也都成为了浪费,同时会产生顾客的信赖度降低这一看不 见的浪费,生产规模越大,影响也就越大。但是,不良品的发生几率越小的话, 就越能实现利益的飞跃。
谢谢!
进入20世纪顾客需求量增大对品质要求高
2、十九世纪~二十世纪:大批量生产 市场特点: 供需两旺 生产特点: 以流水线为主体的大规模生产,产量大、品质提高
20世纪后期,顾客需求个性化突出
3、二十一世纪:精益生产 市场特点:多品种,小批量,变化快。 生产方式: 一种适应顾客定制的“多品种”“小批量”生产 生产特点:产量和品种能快速对应市场变化柔性生产
合理布局
5S、可视化管理
IE改善
线体平衡
快速换型
标准化作业
5、精益生产与传统生产比较
1. 人力资源--与批量生产方式相比,均能减1/2; 2. 新产品开发周期--可减至l/2或2/3; 3. 生产过程在制品库存(WIP)--可减至批量生产的1/10; 4. 占用空间--可减至采用大量生产方式工厂的1/2; 5. 成品库存--可减至大量生产方式工厂平均库存水平的1/4; 6. 产品质量--可提高3倍;
搬运是浪费。消除不能产生 附加价值的浪费
④加工的浪费
针对采取什么样的方 式才能够使现在的加 工方式更为简易、怎 样才能够使加工效率 得到提升等问题下功 夫进行改善,包括操 作工所掩饰掉了一些 机械・装置・夹具等的 缺陷,以及生产过剩 的质量问题及提前生 产所产生的浪费。
JIT精益生产基础知识

JIT精益生产基础知识引言JIT(Just-in-Time)精益生产是一种以最大限度减少库存的生产方法。
它的目标是通过减少库存和减少生产过程中的浪费来提高生产效率和产品质量。
JIT生产方法最早由日本汽车制造商丰田公司引入,并在全球范围内广泛应用。
JIT的原理和核心概念JIT生产方法的核心原理是按需生产,即在需要产品时才进行生产,以避免库存积压和浪费。
为了实现按需生产,JIT方法依靠以下核心概念:1.Takt时间: Takt时间是指完成一个产品所需的时间,它是按照顾客需求进行计算的。
JIT生产中,所有生产环节的时间都要受到Takt时间的限制。
2.流水线制造: JIT生产方法通常采用流水线制造方式,以实现高效的生产流程。
每个环节都必须在规定的时间内完成任务,以便产品能够按时交付。
3.零库存: JIT生产目标是把库存降到最低。
通过精确计算需求量和生产速度,并及时交付零部件,可以避免库存积压。
4.物理层面整理: JIT生产方法强调工作环境整洁和物品摆放合理。
通过整理和排序,可以减少生产过程中的浪费,并提高效率。
5.质量保证: JIT生产方法注重质量,并通过不断改进和反馈机制来提高产品质量。
减少库存和浪费可以更容易地发现问题,并及时解决。
JIT的优势和应用领域JIT生产方法具有以下优势:1.降低库存成本: JIT生产方法帮助企业降低原材料和成品的库存。
通过减少库存积压,企业可以节省资金,并降低仓储成本。
2.提高生产效率: JIT生产方法通过流水线制造和按需生产,可以大幅提高生产效率。
减少等待时间和浪费,提高生产线利用率。
3.增强产品质量: JIT生产方法通过持续改进和严格质量控制,可以提高产品质量。
减少库存和浪费可以更容易地检测和解决质量问题。
4.加强供应链管理: JIT生产方法要求与供应商建立紧密的合作关系,以确保按时交付零部件。
这有助于提高供应链的效率和可靠性。
JIT生产方法适用于各种制造行业,特别是批量生产和定制生产领域。
现代工业工程精益生产的基础

现代工业工程精益生产的基础1. 引言现代工业工程是一种以提高生产效率和降低成本为目标的管理方法。
而精益生产则是现代工业工程的一种重要理念和方法论,旨在通过消除浪费、提高价值流程效率来实现企业的持续改进和竞争优势。
本文将介绍现代工业工程精益生产的基础知识,包括其背景、核心原则和关键实践。
2. 现代工业工程的背景现代工业工程起源于20世纪初的美国,最早应用于制造业。
随着工业化的深入和全球竞争的加剧,企业面临着越来越大的压力,需要提高生产效率、降低生产成本和提升产品质量。
传统的生产方式存在许多浪费,例如过多的库存、不必要的运输、繁琐的工艺流程和低效的生产线配置等。
因此,人们开始寻求一种创新的管理方法,以解决这些问题并实现持续改进。
3. 精益生产的核心原则精益生产基于以下几个核心原则:3.1 顾客价值导向精益生产将满足顾客需求视为最重要的目标。
它强调通过消除非价值增加的活动和流程,从而提高产品和服务的价值。
只有为顾客创造价值的工作才是有意义的,并能够带来持续的业务增长。
3.2 浪费的消除精益生产鼓励企业通过不断消除各种形式的浪费来提高效率。
浪费包括过多的库存、等待时间、不必要的运输、瑕疵品和生产设备故障等。
通过减少浪费,企业能够提高生产效率、降低成本,并增强对市场的竞争力。
3.3 价值流分析价值流分析是精益生产的关键方法之一。
它通过对生产流程的详细分析,识别出各个环节中的浪费和瓶颈,并提出改进措施。
价值流图是一个直观且有效的工具,可以帮助企业了解整个生产过程,并找到改进的空间和机会。
3.4 持续改进持续改进是精益生产的核心理念之一。
企业应当不断追求卓越,不断改进生产流程和管理方法,以实现更高的效率、质量和灵活性。
持续改进需要全员参与,通过团队合作和员工培训,促进创新和学习。
4. 精益生产的关键实践精益生产的实践包括以下几个关键步骤:4.1 设置目标企业应当明确自己的目标和期望,例如提高生产效率、降低成本、提升产品质量等。
JIT精益生产基础知识

JIT精益生产基础知识Just-in-Time(JIT)精益生产是一种通过减少库存和实现高效运作来提高生产效率的方法。
它的核心理念是在所需时间、所需数量和所需质量的基础上,按需生产,及时交付产品,避免库存积压和浪费,提高生产效率和产品质量。
JIT精益生产的起源JIT精益生产起源于日本丰田汽车公司,是丰田汽车制造体系的核心。
20世纪60年代,丰田汽车公司面临着生产效率低下的困境,为解决这一问题,丰田引入了JIT生产模式。
JIT精益生产的原则JIT精益生产的原则包括:1.在需时生产:根据客户订单的需求及时生产,避免过多积压库存。
2.减少浪费:避免不必要的库存、运输、等待和翻修等浪费,最大化价值创造。
3.持续改进:不断寻求改善生产流程和质量控制,提高生产效率和产品质量。
4.建立稳定的供应链:与供应商建立稳定的合作关系,实现原材料的及时供应。
JIT精益生产的关键技术JIT精益生产的核心技术包括:1.Kanban系统:通过设立看板系统,使生产线与上下游环节之间实现信息流畅通,达到材料从上游到下游的精确控制和协调,实现生产的拉动式管理。
2.单片流生产:以最小的生产批量进行生产,减少库存积压,提高生产效率。
3.精益生产工具:如5S整顿、标准作业流程(SOP)、持续改进(Kaizen)等工具的应用,帮助企业实现生产过程的优化和改善。
4.设备保养:通过定期保养和维护设备,确保设备正常运转,减少生产线停机时间,提高生产效率。
JIT精益生产的优势JIT精益生产具有以下优势:1.降低生产成本:减少库存积压和生产浪费,降低生产成本,提高利润率。
2.提高生产效率:精细化的生产计划和及时交付机制,提高生产效率,缩短生产周期。
3.优化生产流程:通过持续改进和优化生产流程,提高产品质量和生产效率。
4.增强企业竞争力:JIT精益生产可以有效提高企业响应市场需求的能力,增强企业在市场中的竞争力。
JIT精益生产的应用案例日本丰田汽车公司是JIT精益生产的典范。
精益生产基础篇---课后测试及答案

精益生产基础篇课后测试单选题1、传统生产方式的第三次转折是( )(10 分)A批量生产B单件生产C流水线生产D自动化生产正确答案:D2、精益生产的核心理念是( ),通过持续改进来提高生产效率和质量。
(10 分)A精益求精B减少产品变差C提升客户满意度D消除一切形式的浪费正确答案:D多选题1、精益生产的影响和意义有哪些( )(10 分)A提高了生产效率B降低了成本C推动了生产方式和管理方式的革新D对全球制造业产生了深远影响正确答案:A B C D2、精益生产的基本原则包括( )(10 分)A价值B价值流C流动D拉动E持续改进正确答案:A B C D E3、实施精益生产可以通过哪些方式来提高生产效率,从而实现更高效的生产和更高的利润。
(10 分)A减少浪费B增加库存C优化供应链D引入自动化技术正确答案:A C D4、实现成本无限下降需要企业不断进行改善和创新,措施包括( )(10 分) A优化生产流程B提高生产效率C增加运营投入D减少浪费正确答案:A B D判断题1、精益生产通过消除浪费和提高效率,实现生产成本的降低,从而提升企业的竞争力。
(10 分)A正确B错误正确答案:正确2、精益思想强调成本取决于制造的方法,通过持续改善,企业可以实现成本的无限下降,从而提升竞争力。
(10 分)A正确B错误正确答案:正确3、精益生产通过优化制造方法,消除浪费,提高生产效率,从而实现成本的降低。
(10 分)A正确B错误正确答案:正确4、拉动生产通过正确的价值观念和压缩提前期,保证用户在要求的时间得到需要的产品。
(10分)A正确B错误正确答案:正确。
精益生产基础知识概述
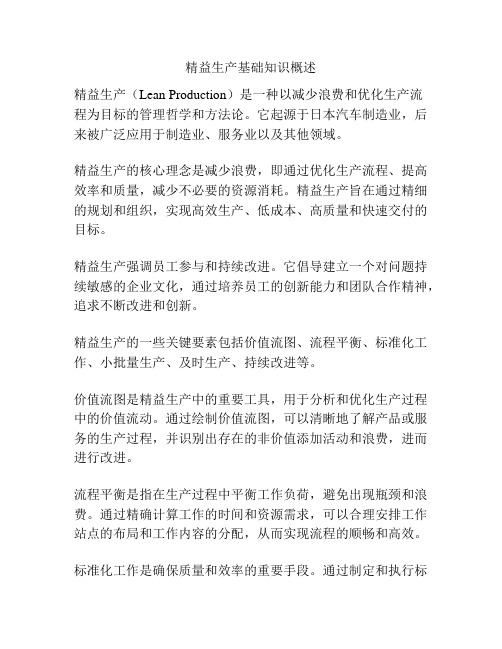
精益生产基础知识概述精益生产(Lean Production)是一种以减少浪费和优化生产流程为目标的管理哲学和方法论。
它起源于日本汽车制造业,后来被广泛应用于制造业、服务业以及其他领域。
精益生产的核心理念是减少浪费,即通过优化生产流程、提高效率和质量,减少不必要的资源消耗。
精益生产旨在通过精细的规划和组织,实现高效生产、低成本、高质量和快速交付的目标。
精益生产强调员工参与和持续改进。
它倡导建立一个对问题持续敏感的企业文化,通过培养员工的创新能力和团队合作精神,追求不断改进和创新。
精益生产的一些关键要素包括价值流图、流程平衡、标准化工作、小批量生产、及时生产、持续改进等。
价值流图是精益生产中的重要工具,用于分析和优化生产过程中的价值流动。
通过绘制价值流图,可以清晰地了解产品或服务的生产过程,并识别出存在的非价值添加活动和浪费,进而进行改进。
流程平衡是指在生产过程中平衡工作负荷,避免出现瓶颈和浪费。
通过精确计算工作的时间和资源需求,可以合理安排工作站点的布局和工作内容的分配,从而实现流程的顺畅和高效。
标准化工作是确保质量和效率的重要手段。
通过制定和执行标准化工作程序,可以减少变异和错误,提高产品和服务的一致性和可靠性。
小批量生产和及时生产是精益生产中的两个重要原则。
小批量生产可以减少库存和等待时间,降低成本和资源消耗。
及时生产则强调按需生产和按时交付,避免过产和库存积压。
持续改进是精益生产的核心精神。
它强调通过持续地观察、分析和改进,不断优化生产过程和提升绩效。
持续改进需要建立一个鼓励员工提出问题和改进建议的文化,同时提供必要的培训和支持。
总之,精益生产是一种在全球范围内被广泛应用的管理方法,它通过减少浪费和优化生产流程,实现高效生产、低成本、高质量和快速交付的目标。
它不断追求改进和创新,强调员工参与和持续学习,是现代企业管理中的重要理念和工具。
精益生产(Lean Production)是一种在制造业和服务业等领域中被广泛应用的管理哲学和方法论。
培训课件JIT精益生产实务1JIT基础知识课件

安定化生产
平稳化生产
适时化生产
10、你要做多大的事情,就该承受多大的压力。11、自己要先看得起自己,别人才会看得起你。12、这一秒不放弃,下一秒就会有希望。13、无论才能知识多么卓著,如果缺乏热情,则无异纸上画饼充饥,无补于事。14、我只是自己不放过自己而已,现在我不会再逼自己眷恋了。
谢谢大家
工厂常见的
等待浪费
搬运浪费
不良浪费
动作浪费
加工浪费
库存浪费
制造过多(过早)浪费
7大浪费
企业每生产一件产品就在制造一份浪费。伴随企业运营中各业务环节不被察觉或不被重视的浪费,日本企业管理界将之形象地比喻为“地下工厂”。
地下工厂
你知道发现下面的都是那些浪费吗?
库存的浪费
过量制造的浪费
专业化作业有利于提高个别效率,不少企业因此实行计件工资。 但是,效率追求的重点应该是关注【整体效率】,这对企业才有创造利润的实际意义。
7、可动率与运转率
可动率
运转率
生产时间
%设备可以有效运转(有效产出)的时间
设备有效运转(有效产出)时间
%设备必要的有效运转(有效产出)时间
精益企业
构筑精益企业之屋
Just In Time
适品 · 适量 · 适时
自主管理活动
流线化生产
安定化生产
平稳化生产
适时化生产
你能发现那些浪费吗?
浪费的两层含义:1、在生产活动过程中,不产生附加价值的活动,是浪费。2、尽管增加附加价值,但是所用资源超出了“绝对最小”界限的活动,也是浪费。
库存
库存的危害: ☆ 额外的搬运储存成本 ☆ 造成空间浪费 ☆ 资金占用(利息及回报损失) ☆ 物料价值衰减 ☆ 造成呆料废料 ☆ 造成先进先出作业困难☆ 掩盖问题,造成假象
精益生产基础知识普及

精益生产基础知识普及一、精益生产1、什么是精益生产•精益生产是通过消除浪费提高周转和降低所有流程(不管是制造流程还是服务流程)成本的方法•一套被证明是很好的工具和解决方案•以最快的速度➢降低所有商业流程中的成本➢通过消除浪费➢客户来定义价值,所有的改善是最大限度的为客户提供增值服务精益生产的方法告诉我们,不要做不能为客户增加价值的流程2、为什么要推行精益生产?•为客户增加价值•价值流动速度越快=成本越低•授权所有员工–每个人都要参与•通过精益改善,员工的工作氛围更好•大的改善比较容易做到,持续改善文化却比较难培养•推行精益生产将会取得持续渐进的业绩改善➢20%—40%的生产力提升➢20%—70%库存减少➢通过减少批量,降低5%—20%的生产不良➢对于按预测生产的库存品达到95%的可用率,对于按订单生产的产品95%—99%可以按时交货3、精益生产需满足的条件:人、机、物、料、法•人,要稳定➢员工离职率小于3%较好➢执行率,如计划完成率越高越好➢标准工时等•机,生产所试用的设备、工具等辅助生产设备➢设备综合效率(OEE)=设备产出时间/设备计划可用时间•物,指物料,半成品、配件、原料等产品用料➢准时交货率=准时交货的次数/总交货次数•料,➢合格的物料➢恰当的时间到达➢库存合理•法,法则,生产过程中所遵循的规章制度4、精益流程的特征•流动:流程按照一定的速度尽可能的持续流动,没有浪费•标准作业: 准确的描述每个动作的周期时间,客户需求时间,每个细节的工作顺序,手上零件的最低库存•通过消除浪费建立流动,建立作业标准。
➢浪费是不增加价值的活动–例如:任何消耗资源但是在客户的角度来看不增加价值的活动。
5、精益生产的衡量指标速度和浪费被认为是衡量精益项目的最主要的指标…•速度➢订货至交货时间—前置时间➢前置时间= 库存总量/平均的客户需求量•浪费➢周期流程效率等于增值时间和非增值时间的相比➢效率(%) = 增值时间/ 增值时间+非增值时间•节拍时间节拍时间=可用时间(秒)/客户需求量➢可用时间= 生产时间中可用于生产产品的时间➢客户需求量= 平均每天的需求二、识别八大浪费•过量生产–生产比需要数更多的产品•搬运–过多的搬运物料或者是产品•多余动作–没有产生附加价值的动作•等待–人员利用率不高•库存–里有很多物料,占用很多空间(通常象征另外一种浪费)•过渡加工–生产的产品质量超出客户期望的标准•返工–浪费很多资源,生产出来的不良,包括报废的不良和返修的不良。
精益生产及精益工具大纲(1)
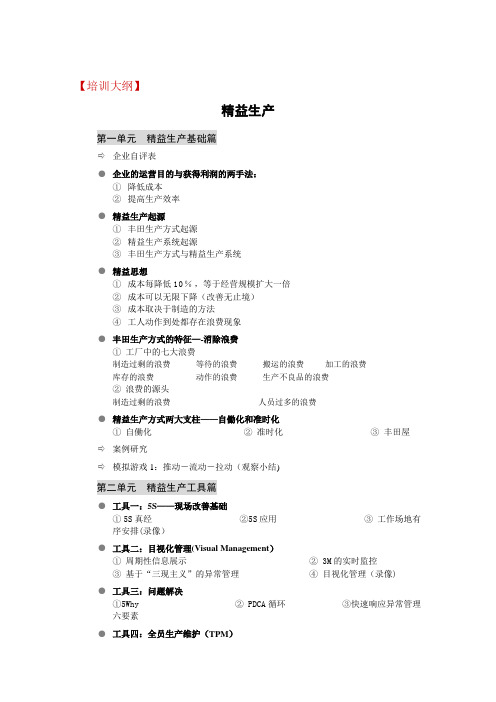
【培训大纲】精益生产第一单元精益生产基础篇⇨企业自评表●企业的运营目的与获得利润的两手法:①降低成本②提高生产效率●精益生产起源①丰田生产方式起源②精益生产系统起源③丰田生产方式与精益生产系统●精益思想①成本每降低10%,等于经营规模扩大一倍②成本可以无限下降(改善无止境)③成本取决于制造的方法④工人动作到处都存在浪费现象●丰田生产方式的特征—-消除浪费①工厂中的七大浪费制造过剩的浪费等待的浪费搬运的浪费加工的浪费库存的浪费动作的浪费生产不良品的浪费②浪费的源头制造过剩的浪费人员过多的浪费●精益生产方式两大支柱——自働化和准时化①自働化②准时化③丰田屋⇨案例研究⇨模拟游戏1:推动-流动-拉动(观察小结)第二单元精益生产工具篇●工具一:5S——现场改善基础①5S真经②5S应用③工作场地有序安排(录像)●工具二:目视化管理(Visual Management)①周期性信息展示②3M的实时监控③基于“三现主义”的异常管理④目视化管理(录像)●工具三:问题解决①5Why ② PDCA循环③快速响应异常管理六要素●工具四:全员生产维护(TPM)①TPM的概念和目的②五大对策和八大策略③自主维护保养的七个层次④TPM实施的十大步骤●工具五:标准化作业①准作业条件②标准作业三要素(TT, WS,SWIP)●工具六:现场改善-Kaizen①改善步骤②改善ECRS手法③改善突破法—现场改善的利器(录像)●工具七:防错(Pokayoke)①追求零缺陷②品质三不政策③自働化三原则●工具八:看板(Kanban)①看板的种类与工作原理②看板的实施前提③看板六原则●工具九:快速换模(SMED原理)①明确划分内外部因素②将内部因素转化成外部因素③理顺留下的内部因素④理顺所有外部因素⑤使用工件更换器(快速夹紧装置或完全去除夹紧装置)⑥进行平行作业⑦去除调整/校准过程●工具十:价值流图析(Value Stream Mapping)①确定产品系列②现状图绘制③未来状态图绘制④计划与实施⇨案例研究⇨模拟游戏2:推动-流动-拉动(观察小结)第三单元精益生产总结篇●精益改善失败原因●精益改善-终身之旅①精益改善路线图②精益改善的顺序③精益改善的合理化建议④精益改善实施绩效指标⑤精益企业4项基本标准⑥精益企业5项基本特征⇨案例研究⇨模拟游戏3:推动-流动-拉动(观察小结)精益工具一:5S-工作场地有序安排第一部分 5S基础篇一、现场5S改善科学推行二、现场管理与市场意识三、5S推行关系与成效四、5S活动原则与误区五、生产经理心智修炼六、建立最优素质模型七、专业能力与管理提升八、5S管理技巧分享第二部分 5S推进篇一、整理推进快刀斩乱麻二、倡导提领法则三、整理不良的对策与分析四、整顿的推进重点五、目视化定置管理六、动作经济原则七、彻底杜绝污染源八、点检与点检通道优化九、清洁的最有效推进十、制度与标准化模型建立十一、修养的推进重点十二、标杆推进十三、团队作战十四、责任重于泰山十五、常见不安全现状与行为分析第三部分 5S方法篇一、现场可视化管理要点二、3级标准管理方法三、可视化的合理分类四、颜色管理与视觉原理五、企业文化与基础设施六、看板管理三大要素七、识别管理大全八、识别与形迹管理第四部分 5S督导篇一、建立5S推行组织二、拟定推进方针和目标三、拟定计划和实施方法四、5S推行过程五、样板区的选择与总结推广六、5S绩效考核七、确定评比方法八、5S纠正与预防第五部分持续改进篇一、5S推进中易存在问题二、问题意识与五现手法三、PDCA与SDCA递进四、改善与创新五、日常管理与改善六、激发创新思维七、标准化八、防错法九、提案改善活动第六部分 5S延伸篇一、5S与制造业精益生产LP模式二、5S与设备维护管理TPM的推行三、办公室5S四、文件5S五、会议5S六、5S问与答精益工具二:目视化管理第一部分目视化管理1.什么是目视控制2.目视化管理的定义和作用3.目视化Vs。
- 1、下载文档前请自行甄别文档内容的完整性,平台不提供额外的编辑、内容补充、找答案等附加服务。
- 2、"仅部分预览"的文档,不可在线预览部分如存在完整性等问题,可反馈申请退款(可完整预览的文档不适用该条件!)。
- 3、如文档侵犯您的权益,请联系客服反馈,我们会尽快为您处理(人工客服工作时间:9:00-18:30)。
仅供个人参考、提升知识,不得作为商业 产品 产品! 仅供个人参考、提升知识,不得作为商业.产品!
Table of Contents 目录
Contents Slide(s)
Overview & Scope 概述与范围 Objectives 目的 A Brief History of Lean 精益历史简介
Lean Thinking 精益思想
It’s a people issue. That’s why it’s so hard. Getting people to change – to do things differently than they have done them – is really, really hard.
Lean Manufacturing has its’ root in the Toyota Production System (TPS). Several individuals at Toyota were instrumental in developing and systematizing TPS. Among the most important were:精益生产来自于丰田制造 精益生产来自于丰田制造 几位丰田人对其进行了发展和系统化, 系统 (TPS).几位丰田人对其进行了发展和系统化,其中贡献最大的 : 几位丰田人对其进行了发展和系统化 Sakichi Toyoda丰田佐吉(1867~1930) • Japan’s “King of Inventors.”日本“发明家之父” • His concept of Jidoka (autonomation) is one of the foundational principles of TPS. 他的概念jidoka (自动化) 是TPS的几项基础原则之一 • First applied to Toyoda Power Loom equipped with a new weft-breakage automatic stopping device (developed in 1896).最初应用在自动织布机上,只要有断线就自动 停机(发明于1896年) • World‘s first automatic loom with a non-stop shuttle-change motion, the Type-G Toyoda Automatic Loom (developed in 1924). 发明了世界上第一台不停线换梭自动 织布机,G型自动织机(发明于1924年) • Founded Toyota Motor Co. in 1937. 1937年创立丰田汽车公司
* Info Source: /wiki/Lean_manufacturing
仅供个人参考、提升知识,不得作为商业 产品 产品! 仅供个人参考、提升知识,不得作为商业.产品!
3
Objective目的 Objective目的 Introduce Lean Manufacturing and its elements 介绍精益生产及基本原理
4 5 7 14 30 38 56
Waste Elimination 消除浪费 Value Stream Mapping (VSM) 价值流程图 5S & Visual Management 5S及可视化管理 及可视化管理 Super Market 超市
仅供个人参考、提升知识,不得作为商业 产品 产品! 仅供个人参考、提升知识,不得作为商业.产品!
“The Machine That Changed The World” 改变世界的机器 “Lean Thinking” 精益思想
仅供个人参考、提升知识,不得作为商业 产品 产品! 仅供个人参考、提升知识,不得作为商业.产品!
7
The Origins of Lean Manufacturing精益生产的起源 精益生产的起源
Waste Elimination消除浪费 消除浪费 Value Stream Mapping价值流程图 价值流程图 5S & Visual Management 5S 及可视化管理 Super Market超市 超市
仅供个人参考、提升知识,不得作为商业 产品 产品! 仅供个人参考、提升知识,不得作为商业.产品!
Mark DeLuzio, architect of the Danaher Business System, Danaher 如果一家公司已经真正开始推行Lean,那要花上2,3年的时间才能达到初级阶段。 那是多么的困难!
Excerpts from the book “Lean Machines”
For more info: /wiki/Sakichi_Toyoda
Type G Automatic Loom
Toyota Sedan Model AA Info Source: http://www.toyota.co.jp/en/vision/production_system/origin.html
2
Overview & Scope 概述 范围 概述&范围
Lean Manufacturing is a generic process management philosophy derived mostly from the Toyota Production System (TPS) but also from other sources. It is renowned for its focus on reduction of ‘Seven Wastes’ in order to improve overall customer value. * 精益生产是一门流程管理哲学,主要来自于丰田制造系统( )。其焦点在如何减少 精益生产是一门流程管理哲学,主要来自于丰田制造系统(TPS)。其焦点在如何减少 )。 大浪费” “7大浪费”以增加客户价值。 大浪费 以增加客户价值。 Toyota's achievement made "Lean" a hot topic in management science in the first decade of the 21st century. 丰田的成功使Lean成为 世纪前10年管理科学的热点。 丰田的成功使 成为21世纪前 年管理科学的热点。 成为 世纪前 年管理科学的热点 Lean Manufacturing can be defined as: "A systematic approach to identifying and eliminating waste (non-value-added activities) through continuous improvement by flowing the product at the pull of the customer in pursuit of perfection." Lean可以如此定义:“从客户拉货到产品源头的整个流程不断改善,识别并消除浪费(无 可以如此定义: 从客户拉货到产品源头的整个流程不断改善 识别并消除浪费( 从客户拉货到产品源头的整个流程不断改善, 可以如此定义 价值活动),使之日臻完善的一种系统方法” 价值活动),使之日臻完善的一种系统方法” ),使之日臻完善的一种系统方法
仅供个人参考、提升知识,不得作为商业 产品 产品! 仅供个人参考、提升知识,不得作为商业.产品!
8
The Origins of Lean Manufacturing精益生产的起源 精益生产的起源
Kiichiro Toyoda丰田喜一郎(1894~1952)
• Sakichi’s son.丰田佐吉之子. • The TPS has evolved through may years of trial and error to improve efficiency based on the Just–in–Time (JIT) concepts developed by Kiichiro Toyoda, the founder (and second president) of Toyota Motor Corporation. TPS一直在准时制生产的基础上不断试验去提升效率, 而准时制生产就是由丰田喜一郎发明的,丰田汽车的创始人。 • Inherited Sakichi Toyoda philosophy, set out to realize his belief that “the ideal conditions for making things are created when machine, facilities and people work together to add value without generating any waste“.继承了佐吉的丰田思想,他坚信”最理想的状态就是人,机, 设备最佳配合增加价值,不产生任何浪费” • Conceived methodologies and techniques for eliminating waste between operations, between lines, between processes. The result was the so called JIT method. 他一直思考在操作,线体 和流程之间消除浪费最佳的方法,即“准时制生产“ • Drawing on his experience of introducing a flow production method using a chain conveyor into the assembly line of a textile plant (completed in 1927) with a monthly production capacity of 300 units. 他将流水线生产的经验应用于纺织厂,链条式传送带使月产量达到300 • Introduced this method into the body production line at Toyota Motor Co., Ltd.‘s Koromo Plant (present day Honsha Plant), completed in 1938. 将这种方法引入到丰田汽车公司车身生产 线,1938年完成 • He studied Ford’s production system and adapted it to the smaller, more diverse Japanese market.他研究了福特生产系统并把它应用于更小,更多变的日本汽车市场