浅谈旧加重钻杆耐磨带堆焊的必要性
耐磨材料堆焊

耐磨材料堆焊
耐磨材料堆焊是一种常用的表面修复和加固工艺,通过在金属基体表面堆积耐
磨合金材料,以提高金属零件的耐磨性能和使用寿命。
这种工艺适用于各种机械设备、矿山设备、冶金设备、建筑机械等领域,能够有效延长设备的使用寿命,降低维护成本,提高生产效率。
耐磨材料堆焊的工艺原理是利用焊接设备将耐磨合金材料焊接在金属基体表面,形成一层坚固的耐磨层。
这种耐磨层具有较高的硬度和耐磨性能,能够有效抵抗摩擦、磨损和冲击,提高设备的耐磨性能。
在进行耐磨材料堆焊时,首先需要对金属基体表面进行清理和预处理,以保证
焊接质量。
然后选择合适的焊接材料和焊接工艺参数,进行堆焊操作。
最后进行必要的后处理工艺,如热处理、抛光等,以提高耐磨层的性能和表面质量。
耐磨材料堆焊的优点是可以在原有金属基体上修复和加固,无需更换整个零件,节约了成本和时间。
同时,耐磨材料堆焊还可以根据实际工作条件选择不同的耐磨合金材料,以满足不同工作环境下的耐磨要求,具有较强的适应性和灵活性。
在实际应用中,耐磨材料堆焊需要根据设备的具体工作条件和要求进行合理的
选择和设计,以确保堆焊层的质量和性能。
同时,还需要注意堆焊工艺的控制和操作,确保焊接质量和安全生产。
总的来说,耐磨材料堆焊是一种重要的表面修复和加固工艺,能够有效提高设
备的耐磨性能和使用寿命,对于提高设备的可靠性和降低维护成本具有重要意义。
随着工业技术的不断发展和进步,耐磨材料堆焊技术也将不断完善和提高,为各行业的设备维护和维修提供更加可靠和有效的解决方案。
石油钻杆耐磨带磨损原因及耐磨解决方法

石油钻杆耐磨带磨损原因及耐磨解决方法在钻井过程中,钻柱在井眼中与套管内壁发生接触产生摩擦,使得扭矩和摩擦增加,而钻杆接头对套管的磨损影响最大,因为钻杆接头的直径比钻杆本体大20%~30%,很容易与套管内壁接触并磨损套管。
当接触力足够大时,润滑膜的润滑作用完全消失,钻杆接头与套管内壁直接接触产生了干摩擦。
在摩擦过程中,钻杆接头的磨损非常严重,偶然的碰撞就可能使钻杆接头产生断裂;同时,钻杆接头的磨损也使得套管壁厚减薄,抗挤能力随之降低。
若对此估计不足,有可能因此导致钻井事故或油气井的早期报废,给油田造成巨大的损失。
有研究结果表明,钻柱不居中使钻杆接头在钻井施工中与套管内壁相互摩擦是造成套管磨损的主要原因,而钻柱不居中又是钻探过程中不可避免的。
因此,可见如何降低钻杆与套管之间的摩擦接触或摩擦系数是防磨的关键与核心。
钻杆接头耐磨带是以凸起的形式熔合在钻杆接头表面,用以代替钻杆接头来和套管摩擦的材料,对钻杆接头起到了保护作用。
由于耐磨带的硬度低于钻杆本身,因此,对套管起到了一定的保护作用。
而耐磨带在磨损掉一部分之后,可以进行重复堆焊使用。
钻杆耐磨带主要是采用耐磨带焊丝通过CO2气体保护焊的方式堆焊到钻杆接头部位的一种高合金耐磨材料。
目前,国产耐磨带焊丝以北京固本KB150最具代表性。
KB150是北京固本公司第三代产品,是一种高级无裂纹、套管友好耐磨带,继承了KB100和KB300的优点,耐磨带能力介于KB100和KB300之间,摩擦因数低,减摩能力高于KB300和KB100,其焊接简单且焊接过程产生很少的火花和烟尘,且保持一定的韧性可承受在大位移井、深井和水平井的严苛钻井条件下产生的大转矩和高温;能在多种外界环境下补焊,而不会产生裂纹和脱落,同时抗硫化氢腐蚀。
钻杆接头耐磨带的使用性能及其堆焊材料

度磨 损 , 用 堆焊 方 式 ( 其 他方 法 ) 耐 磨 材料 沿 采 或 将
钻 杆接 头 圆周方 向堆 焊 ( 或熔 敷) 宽约 3 ~ 0mm、 0 5 厚 2 3m 的环形 带 。 - m 此环 形带 即称之为 钻杆接 头耐磨
带 技术 问世 以来 , 着 现场应 用 中 出现 问题 的逐 步 随
力 相 对增 大 , 时 无 论 是 耐 磨 带 还 是套 管 内壁 f 此 或 井壁)其磨损 现象 会加 剧 。 ) , ( 摩擦 系数 的影 响 。 钻 2 在 井过 程 中 , 是增 大 接头 与套 管 内壁 摩擦 系数 的因 凡 素 , 润滑 剂 品种 或加 入 量不 合适 、 盘 转速增 大 , 若 转 以及 温 度过 高 或 过低 时 , 其磨 损 现 象 也会 加 剧 。3 f1 钻杆接头 耐磨带 与套管( 或井 壁) 材料特 性 。 据摩擦 根 学 中的 “ 附膜 ” 论【, 于 钻杆 钢 与岩 石形 成 的 吸 理 l对 】 摩 擦 副 , 者 之 间很 难 形 成 吸 附膜 , 擦 系数 主要 两 摩
取 决于摩 擦 副材 料 的表 面 特性 , 而摩 擦 副其 表 面特
性是 稳定 的 , 摩擦 系数受 载荷 的影 响较小 。 对于钻 杆 与套 管 钢形 成 的摩 擦副 , 者之 间 比较 容易 形成 吸 两
附膜 , 当施加 正压 力பைடு நூலகம்时 , 随着 吸 附膜 逐渐 被破 坏 , 摩
克 服 , 型 耐磨 带 专 用 堆焊 材 料 不 断 被 推 出 , 磨 新 耐 带 的材料 品 种 已经发 生 了质 的变 化 , 耐磨 带 的使 用
带 。 机理上讲 , 从 钻杆接 头耐磨 带 的作 用是利用 自身 及 其 耐 磨性 , 钻 杆 外 壁 和套 管 内壁 隔 离 , 钻 杆 将 使 不 与套 管壁 或井 壁直 接 接触 , 以保 护 钻杆 接 头 和套 管 免遭 强烈 的磨损 。 然而 , 际情况 并 不简单 , 实 耐磨 带 的出现 , 将钻 杆接 头与套管 内壁 的接触摩 擦 , 换 转 为耐 磨带 与套 管 内壁 的接触 摩擦 。 它们 之 间的摩 擦 磨损 , 不仅 取 决于 两个 接 触体 材料 的特性 及其 匹 配 关系 , 同时还受 到钻井过 程中诸 多因素影响。 近年来 , 在多 种可供 选 用 的套管 防磨技 术 之 中 , 操作 方 便 和 效果最好 者首推 接头耐磨 带 。 研究表 明 , 头耐磨带 接 性 能 ( 与 套管 材 料 的 匹配 性 能) 含 的优化 与改 善 , 是 防止套管 强烈磨损 的关键技 术措施 。 事实上 , 自耐磨
浅谈旧加重钻杆耐磨带堆焊的必要性

加重钻杆耐磨带堆焊的必要性及其应用论文摘要:在深井超深井勘探过程中,由于径向力、涡动、横向振动等因素的存在,随着钻井时间的增长,钻柱作用于套管内壁的侧向力增大,导致套管和钻具接头磨损的问题越来越严重。
造成钻具耐磨带失效的主要原因有地层研磨性、钻杆的井下工况、耐磨材料选择与敷焊工艺的影响。
选择合理的耐磨材料与敷焊工艺对解决钻具耐磨带失效问题非常重要。
论文关键词:耐磨带钻具铁基合金粉焊丝一、加重钻杆的作用加重钻杆通常应用于水平井、定向井以及深井等难度较大的井位中,可以部分代替钻铤以提高钻机的钻深能力,由于它的弹性比普通钻铤高,在弯曲井眼中用它来代替钻铤时,可以降低旋转扭矩和提升负荷。
另外在弯曲井段用加重钻杆代替钻杆时,由于加重钻杆于井壁接触面积较小,能减少旋转扭矩和上提阻力以及压差卡钻的可能性。
更重要的是有利于保持定向井的方向。
二、钻井过程中的磨损种类在油气田勘探开发钻井中,尤其是在深井、大位移井、水平井、大斜度井中,钻杆和套管的磨损严重,给油气田带来重大损失。
因此,钻井过程中钻杆和套管的磨损及防磨问题,已引起钻井界的密切关注。
套管磨损———套管磨损的主要形式为偏磨,偏磨后的套管横截面呈月牙型。
一方面套管圆周上呈月牙型部位壁厚最薄,导致抗挤强度大大降低。
在高地层压力作用下,假如设计的套管安全系数没有足够大,轻易导致套管挤毁,造成钻井报废或局部井段报废。
另一方面,偏磨套管在抗挤强度降低的同时其抗内压强度也随着降低。
在井控及中途测试时,假如没有充分考虑到套管磨损的影响,可能造成严重后果,即气井完井井控和测试时,要么冒套管破裂地面窜气的风险,要么提前入套管或下套管后再测试。
这不仅造成重大经济损失,而且给加深钻井造成困难或钻不到设计深度。
钻杆磨损———由于钻杆接头的外径大于杆体的外径,因此钻杆的磨损主要表现在钻杆接头的磨损。
当井眼曲率较大时,钻杆杆体也会受到磨损。
在钻井过程中旋转的钻杆接头和井壁或套管壁不断地摩擦,造成接头的严重磨损,尤其在硬地层或研磨性地层,井段钻杆接头磨损加剧。
加重钻杆耐磨带焊接实例

加重钻杆耐磨带焊接实例(北京固本科技有限公司)随着石油钻探开采的发展,各类加重钻杆在石油钻探开采中的需求越来越大,用户对产品使用性能的要求也越来越高。
如何采取合理的焊接工艺方法,以实现低成本高效率且又能满足产品技术要求的耐磨带焊接研究成为需要解决的课题之一。
某石油公司研发的材料牌号为AISI4145H钢的114.3mm(4.5in)加重钻杆有4段工作面需要增加耐磨带,4段焊缝分别为币φ158.8mmx101mm、φ127mmx76mm、φ127mmx76mm、φ158.8mmx101mm,焊缝需堆焊3mm厚,加重钻杆内孔为币φ71.41mm,钻杆内螺纹接头与钻杆吊卡扣合处制成18°锥形台肩,焊前经过285~341HBW调质处理。
按石油天然气行业颁布的标准SY/5T146-1997规定:堆焊后,耐磨环外表面应平整过渡,基体不得有裂纹和焊层剥落等缺陷,表面硬度不低于50HRC,为使钻杆焊接后性能满足技术要求,需对原材料的焊接工艺、焊接质量进行分析和试验,以便制定合理可行的焊接工艺。
一、焊接性分析钻杆的材料牌号为AISI4145H,其化学成分符合表1的规定。
表1 AISI4145H的化学成分(质量分数)(%)按照国际焊接学会所推荐的碳当量计算公式,可计算出碳当量Ceq为0.725%~1%。
据大量试验得知:当碳当量Ceq大于等于0.60%时,属于高淬透性的钢,冷裂纹倾向较为严重,焊接性较差,这是因为材料中的含碳量较高,加人的合金元素也较多,在500℃以下的温度区间过冷奥氏体具有更大的稳定性所致其含碳量越高,淬硬倾向越大,冷裂纹倾向也越大,而且由于M点较低,在低温下形成的马氏体一般难以产生“自回火”效应,并且马氏体中的含碳量较高,有很大的过饱和度,点阵的畸变就更严重,因而硬度和脆性就更大,对冷裂纹的敏感性也就更大另外,由于原材料的含碳量及合金元素的含量都较高,因此液一固相区间较大,偏析也更严重,这就促使其具有较大的热裂纹倾向。
钢铁的磨损与堆焊

钢铁的磨损与堆焊【概述】众所周知,磨损是摩擦的必然结果,它导致材料和能源的消耗。
磨损是引起机械零件失效的主要原因之一,约75%的机器零件由于磨损而报废。
我国每年因磨损消耗的材料就有一佰万吨以上,加上停机和维修费用,造成了数十亿元的经济损失。
据有关统计,世界上大约有1/3~1/2的能源消耗在各种不同形式的摩擦上,因磨损造成的损失高达一千亿美元。
可见提高材料的耐磨性是一项具有重大的社会经济意义。
磨损分类的方法很多,按机理可分为粘着磨损、磨粒磨损、表面疲劳磨损、腐蚀磨损和微动磨损五个基本类型。
机械零件的磨损常常不是单一,往往函盖几种磨损形式,而且磨损形式随着工作条件的改变而改变。
由于磨损过程的复杂性,且涉及到材料学和摩擦学等多门学科,以至于至今尚无统一的理论和模式来描述磨损的本质与过程,在磨损机理上也存在着不同的认识。
在检测手段也不尽完善,故很难做到真正有效地控制。
提高机械零件耐磨性的办法很多,堆焊可以说是一种简单、有效而经济方法,堆焊的优势是:工艺简单、设备投资少、制造周期短,费用低,耐磨效果好等特点。
其用途主要有两个方面:修复旧零件。
机械零件(如轧辊、轴类、农机零件、采掘机件等易磨损件)在长时间使用后发生了磨损,被磨损部位尺寸变小而造成机械零件无法正常使用(或密封失效)。
若该零件价值低、又容易购到或制造,我们一般做法就是更换新零件;若该零件价值较高更换新零件在经济上不合算,或很难购到、制造周期又长,这时采用堆焊修复是个明智的选择,而且经堆焊修复零件的使用寿命往往又超过原零件。
可见堆焊修复再某些场合是不可缺少的。
制造新零件。
堆焊可制作双金属零件,这种零件包含基层和堆焊层,基层一般采用碳钢或低合金钢,保证零件的强度、韧性和基本尺寸的要求,具有造价低、材料易采购等特点;堆焊层可以根据零件不同的工作性质和需要,选择不同的堆焊焊条堆焊而成,以满足不同的技术要求。
这样既充分发挥材料的工作潜力,又节省了大量贵重合金材料的消耗。
钻杆耐磨带敷焊技术的应用
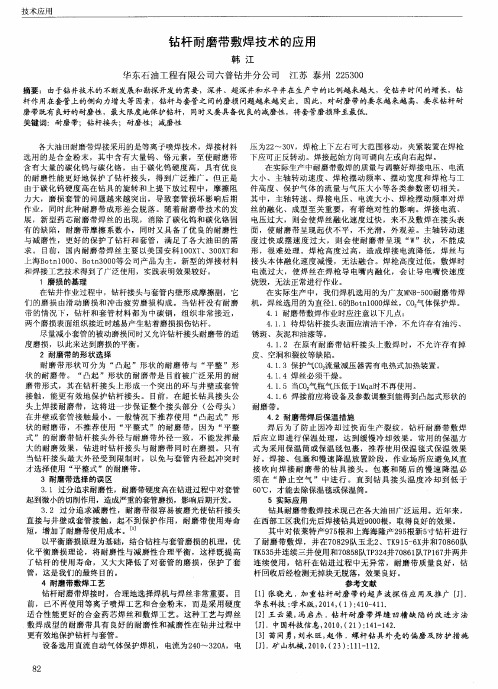
钻杆耐磨带敷焊 技术 的应用
韩 江
华 东石 油工程 有 限公司六 普钻 井分 公 司 江 苏 泰 州 2 2 5 3 0 0
摘要 :由于钻井技术 的不 断发展和勘探开发 的需要 ,深井 、超 深井和水平井在生产 中的比例越 来越大 ,受钻井时间的增长 ,钻 杆作用在套管上 的侧 向力增 大等 因素 ,钻杆 与套 管之 间的磨损 问题越 来越 突 出。因此,对 耐磨带的要求越来越 高,要求钻杆耐 磨带既有 良好的耐磨 性,最大限度地保护钻杆 ,同时又要 具备优 良的减磨性 ,将套管磨损 降至最低 。 关键词 :耐磨带;钻杆接 头;耐磨性 ;减磨性
各 大 油 田耐 磨 带 焊 接 采 用 的是 等 离 子 喷 焊 技 术 , 焊接 材 料 选 用 的是 合金粉末 ,其 中含有大量 钨、铬元 素 ,至 使耐磨 带 含 有大量 的碳化钨 与碳化 铬 ,由于碳化钨硬 度高 ,具有优 良 的 耐 磨 性 能 更 好 地 保 护 了 钻 杆 接 头 ,得 到 广 泛 推 广 。但 正 是 由于碳 化钨硬 度高在钻 具 的旋转 和上提 下放过程 中 ,摩擦 阻 力大 ,磨损套 管 的问题 越来越 突 出,导致套管损 坏影 响后期 作业 , 同时此 种耐磨 带成形差 会脱落 。随着 耐磨带技术 的发 展 ,新型药 芯耐磨 带焊丝 的出现 ,消除 了碳 化钨和碳化 铬 固 有 的 缺 陷 , 耐 磨 带 摩 擦 系 数 小 , 同 时 又 具 备 了 优 良 的 耐 磨 性 与减 磨性 ,更好 的保护 了钻 杆和套 管 ,满足 了各大 油 田的需 求 。 目前 ,国 内耐磨 带焊丝主要 以美 国安科 1 0 0 X T 、3 0 0 X T S H 上海 B o t n l 0 0 0 、B o t n 3 0 0 0 等公司产 品为主 。新 型的焊接材料 和 焊 接 工 艺技 术 得 到 了广 泛 使 用 ,实 践 表 明 效 果较 好 。 1磨损 的基理 在钻井作业 过程 中,钻杆接头 与套管 内壁形成摩擦副 ,它 们 的磨损 由滑 动磨损和 冲击疲 劳磨损构 成 。当钻 杆没有 耐磨 带 的情 况 卜,钻杆和 套管材料 都为 中碳 钢 ,组 织非常接 近 , 两 个 磨 损 表 面 组 织 接近 时越 易产 生粘 着 磨 损 损 伤 钻 杆 。 尽 量 减 小 套 管 的 被 动 磨 损 同 时 又 允 许钻 杆接 头耐 磨带 的适 度 磨 损 , 以此 来 达 到 磨 损 的 平衡 。 2 耐 磨 带 的形 状 选 择 耐 磨带形 状可 分为 “ 凸起 ”形状 的耐磨带 与 “ 平 整 ” 形 状 的耐磨 带 。 “ 凸 起 ”形 状 的 耐 磨 带 是 目前 被 广 泛 采 用 的 耐 磨带形 式,其在 钻杆接头 上形成 一个突 出的环与井 壁或 套管 接触 ,能更有效 地保护钻 杆接头 。 目前 ,在超长钻 具接 头公 头上焊接 耐磨带 ,这将进 一步保 证整个接 头部分 ( 公母 头 ) 在井壁 或套管接 触最 小。一般情 况下推 荐使用 “ 凸起式 ”形 状 的耐磨带 ,不推荐 使用 “ 平 整式 ”的耐磨带 ,因 为 “ 平 整 式 ”的耐磨 带钻杆接 头外径 与耐磨带 外径一致 ,不 能发挥最 大 的耐磨效 果 ,钻进 时钻杆接 头与耐 磨带 同时在磨损 。只有 当钻 杆接头 最大外径 受到 限制时 ,以免与套 管 内径起 冲突 时 才选择使用 “ 平整式 ”的耐磨带 。 3 耐 磨 带 选 择 的误 区 3 . 1 过分追求耐磨性 ,耐磨带硬度 高在钻进过程中对套管 起到 微 小 的切 削 作用 ,造 成严 重 的套 管 磨损 ,影 响 后期 开 发 。 3 . 2 过 分 追 求 减 磨 性 ,耐 磨 带 很 容 易 被 磨 光 使 钻 杆 接 头 直接与 井壁或套 管接触 ,起不到 保护作用 ,耐 磨带使用 寿命 短,增加了耐磨带使用成本 。… 压为2 2  ̄3 0 V ,焊 枪 上 下 左 右 可 大 范 围 移 动 ,夹 紧 装 置 在 焊 枪 下应可正反转动 。焊接起始方 向可调 向左或 向右起 焊。 在 实 际 生 产 中 耐磨 带敷 焊 的质 量 与 调 整 好 焊 接 电压 、 电流 大小 、主轴转动 速度 、焊枪摆动 频率 、摆动 宽度 和焊枪 与工 件高度 、保护气 体 的流量与气 压大小等 各类参 数密切相 关 。 其 中,主轴 转速 、焊 接 电压 、 电流大 小、焊枪 摆动频 率对焊 丝 的融化 、成型至 关重要 ,有着绝对 性 的影响 。焊接 电流 、 电压过大 ,则会使 焊丝融化 速度过快 ,来 不及敷焊在 接头表 面 ,使耐 磨带呈现起 伏不平 ,不 光滑 ,外 观差 。主轴 转动速 度 过快 或摆 速度 过大 ,则 会使 耐磨 带呈现 “ W ” 状 , 不 能 成 形 ,很难 处理 。焊枪高度 过高 ,造成焊接 电流 降低 ,焊丝 与 接 头本 体融化速 度减慢 ,无法融 合 。焊枪 高度过 低 ,敷焊 时 电流过 大 ,使焊 丝在焊 枪导 电嘴 内融化 ,会让 导 电嘴快速 度 烧毁,无法正常进行 作业 。 在实际 生产 中,我们焊机选用 的为广友M N B 一 5 0 0 耐磨带焊 机 ,焊丝选用的为直径1 . 6 的B o t n l 0 0 0 焊丝 ,c O , 气体保护焊 。 4 . 1耐 磨 带 敷 焊 作 业 时 应注 意 以 下几 点 : 4 . 1 . 1待 焊 钻 杆 接 头 表 面 应 清 洁 干 净 , 不 允 许 存 有 油 污 、 锈斑 、灰泥和油漆等 。 4 . 1 . 2 在 原有 耐磨带钻 杆接头上敷 焊时 ,不允许存 有掉 皮 、 空洞 和 裂 纹 等 缺 陷 。 4 . 1 . 3保护气c O , 流量减压器需有 电热须 干 燥 。 4 . 1 _ 5 当C O , 气瓶气压低于1 M q a 时不再使用。
石油钻杆接头耐磨带焊接研究

石油钻杆接头耐磨带焊接研究内螺纹接头外圆的一段长度内,再堆焊一层耐磨带使之呈“凸起”状态。
通常,建议在内螺纹接头的外圆上堆焊76mm宽、3mm厚的耐磨带。
于是耐磨带自己形成一个接触面,而不是使钻杆内螺纹接头的全部长度管或裸眼井的内壁表面相接触。
这样就减少了套管和钻杆接头双方的磨损。
例如φ168mm钻杆内螺纹接头外圆上堆焊“口起”状态耐磨带示意1所示。
图1 “凸”状态的耐磨带用这种方法堆焊的耐磨带可以吸收载荷的冲击。
一旦发生了最恶劣的情况,比如说耐磨带被破坏了,那就需要剔除损坏的耐磨带,然后重把整个钻杆从意外的灾难中抢救恢复出来,以便今后继续使用。
钻杆和套管的接触力主要分布在较小的耐磨带区域,而耐磨带的摩擦系数比钻小,当耐磨带与套管的内表面接触吋,由于摩擦系数的减小,同时也降低了钻具在延伸区作业或大角度钻井时产生的较大扭矩和拉力。
这样,拉力的减小又可以减少燃料的消耗。
(2)“平坦”焊接状态的耐磨带只有当钻杆接头的最大外径被限制,以免与套管内径相干涉时,才建议使普通平坦耐磨带的类型。
所谓平焊指耐磨带高度与接头本体直径钻杆接头本体的外径与耐磨带同时都在受到摩擦。
钻杆和套管的接触力或多或少地沿整个钻杆接头的长度方向分布,降低了耐磨带的支撑,同了钻杆接头本体与套管的接触,增大了钻杆接头和套管的磨损。
用这种方法堆焊的任何一种耐磨带,包括KB150,都不能产生最大的耐磨效果对于平坦焊接类型的耐磨带的应用,需要在整个接头的耐磨带区域加工凹槽,然后填充磨带,使之与钻杆接头的外径齐平。
耐磨带区域一18°的吊卡台肩。
例如φ168mm钻杆内螺纹接头外圆上堆焊“平坦”状态耐磨带示意图见图2所示。
图2 “平坦”状态的耐磨带三、钻杆接头表而耐磨带堆焊工艺措施根据钻杆接头化学成分表1和国际焊接学会碳当量公式,求得钻杆接头碳当量Ceq约为0.8%。
表1 AISI4137H钢的化学成分(质量分数,%)对于钻杆接头,分别等离子弧堆焊铁基合金粉末、80%Ar+20%CO2气体保护焊KB150焊丝和98%Ar+2%O2气体保护焊ER70S-2焊丝外加碳化按甘油法,测定的扩散[H]含量约为0.2ml/100g。
浅析堆焊的应用现状及方法

浅析堆焊的应用现状及方法作者:丁英冬来源:《山东工业技术》2016年第10期摘要:堆焊是用焊接的方法将具有一定性能(耐磨、耐蚀或特殊性能)的材料堆敷在焊件表面上的一种工艺过程,或修复外形不合格的金属旧零件的工艺方法。
堆焊的应用范围极广,如为了增加耐磨性在汽车转动轴上加锰加硅的堆焊挖掘机铲齿表面堆焊是为了增加耐磨性以提高使用寿命。
常用的工程零件,容易磨损,因此采用恰当的堆焊,能提高零部件的使用寿命、节省制造及维修费用外,还可以缩短修理和更换零件的时间,减少停机、停产的损失,从而提高生产率,降低生产成本。
因此,堆焊是机械工业中的一种重要制造和维修方法,广泛应用于各行各业的制造和修理工作中关键词:现状;堆焊方法;展望DOI:10.16640/ki.37-1222/t.2016.10.0041 现状金属堆焊过程中,关键是获得实际所需的产品的性能。
堆焊技术应用范围很广,在船舶、车辆、航空、锅炉、电机、冶炼设备、石油化工机械、矿上机械、起重机械、建筑及国防等行业。
堆焊修复旧的金属零件,关键能降低企业成本,提高产品的使用寿命。
不完全统计,堆焊合金总量的72.2%主要用于修复旧零件。
比如,修复一根普通旧轧辊的费用约为新轧辊成本的25%左右,修补后使用时间能提高一倍。
.制造机械零件采用堆焊后,不仅可发挥金属材料的工作潜力和零件的综合技术性能,又能节省大量的贵重金属。
例如,热锻模采用8CrMnMo或6CrNiMo等合金钢整体模制造,与45Mn2铸钢作为热锻模基体来制造的性能是一样的,节约了成本提高了生产效率。
2 几种常用的堆焊方法堆焊是一种重要的焊接方法和工艺措施,也是表面热处理的一种手段。
堆焊的方法有熔焊、钎焊、压焊、喷熔等工艺方法。
目前常用的主要有气体保护电弧焊堆焊、气焊焊接堆焊和焊条电弧焊的堆焊。
(1)气体保护电弧堆焊。
气体保护电弧堆焊分为钨极氩弧焊堆焊和熔化极气体保护电弧堆焊两种:1)钨极氩弧焊堆焊采用TIG设备,包括焊机、焊枪、供气系统、冷却系统、控制系统等。
石油钻杆接头耐磨带堆焊材料的发展及应用

0 引 言
料 控 制 接头 耐 磨带 性 能 的机 理 又是 怎样 的 ? 为此 , 本 文特 意 将典 型堆 焊材 料 与接头 耐磨 带磨 损 特性 相 联 系 ,综合 评 述耐 磨 带 堆 焊 材料 的发 展 及 其应 用 。
能对 于 耐磨带 焊 接材料 性 能 的重大 突破 具有 重 要参
考价 值 。 12 耐磨 带性 能影 响 因素 . 接 头耐磨 带性 能 影响 因素 较 多 ,总体 上有 三大
因素 : 121 栽荷 力的 影响 ..
在 钻井 过程 中 ,凡是 增大 钻杆 接头 与套 管 内壁
维普资讯
钻 杆 接 头 耐 磨 带 实 质 上 是 一 个 沿 接 头 圆 周 方
向 ,具有 一定 宽 度和一 定 厚度 的 隔离带 。通 过 这个
隔 离带 ,使钻 杆 接头外 壁 和套 管壁 或井 壁 隔离 ,避
免钻 杆 接头 与套 管壁 或井 壁直 接接 触 ,以保 护 钻杆 接 头和套 管免 遭 强烈磨 损 。耐磨 带 的工 况条 件 比较
一பைடு நூலகம்
该 项 工 作 对 推 动 钻杆 接 头 耐 磨 带 技 术 的 进 一 步 完
善 ,提 高 钻 具 使 用 寿 命 ,具 有 积 极 意 义 和 参 考 价
值。
。
从 机 理上讲 ,钻杆 接头 耐磨带 的作用 是利 用 自
1 石 油 钻杆 接头 耐磨 带工 作原 理 与性 能影 响 因素 11 耐磨 带 工作原理 .
磨 带堆焊 材料 的发 展 ,介 绍 了石 油钻杆接 头耐 磨 带堆 焊材 料 的 应 用 。材料 特 性是 影 响 耐磨 带性 能 的核 心影 响 因素 。 “ 材料 控 制性 能”理 论 ,在 钻杆 接 头 耐磨 带技 术发展 过 程 中起 到 积 极 的推 动 作 用 。AR C N O耐 磨 带 的优越 性 被 应 用 所验 证 , 国产 P 10耐磨 带的 主要 技 术指 标 超 过碳 化 钨 耐 磨 T0 带 。必须加 快 步伐 开发 价格合 理 、性 能优 良的新 型耐磨 带 堆焊材 料 。 关 键 词 :堆焊 材料 ;钻 杆接 头 ;耐磨 带 ;发展 ;应 用
堆焊技术在采掘设备修旧利废中的应用
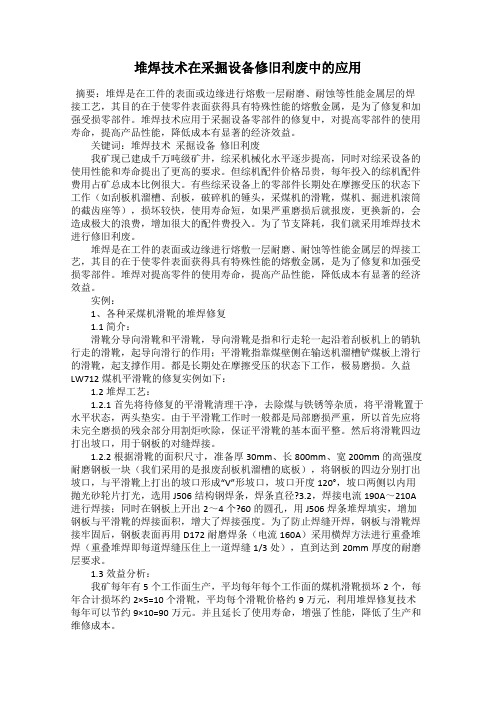
堆焊技术在采掘设备修旧利废中的应用摘要:堆焊是在工件的表面或边缘进行熔敷一层耐磨、耐蚀等性能金属层的焊接工艺,其目的在于使零件表面获得具有特殊性能的熔敷金属,是为了修复和加强受损零部件。
堆焊技术应用于采掘设备零部件的修复中,对提高零部件的使用寿命,提高产品性能,降低成本有显著的经济效益。
关键词:堆焊技术采掘设备修旧利废我矿现已建成千万吨级矿井,综采机械化水平逐步提高,同时对综采设备的使用性能和寿命提出了更高的要求。
但综机配件价格昂贵,每年投入的综机配件费用占矿总成本比例很大。
有些综采设备上的零部件长期处在摩擦受压的状态下工作(如刮板机溜槽、刮板,破碎机的锤头,采煤机的滑靴,煤机、掘进机滚筒的截齿座等),损坏较快,使用寿命短,如果严重磨损后就报废,更换新的,会造成极大的浪费,增加很大的配件费投入。
为了节支降耗,我们就采用堆焊技术进行修旧利废。
堆焊是在工件的表面或边缘进行熔敷一层耐磨、耐蚀等性能金属层的焊接工艺,其目的在于使零件表面获得具有特殊性能的熔敷金属,是为了修复和加强受损零部件。
堆焊对提高零件的使用寿命,提高产品性能,降低成本有显著的经济效益。
实例:1、各种采煤机滑靴的堆焊修复1.1简介:滑靴分导向滑靴和平滑靴,导向滑靴是指和行走轮一起沿着刮板机上的销轨行走的滑靴,起导向滑行的作用;平滑靴指靠煤壁侧在输送机溜槽铲煤板上滑行的滑靴,起支撑作用。
都是长期处在摩擦受压的状态下工作,极易磨损。
久益LW712煤机平滑靴的修复实例如下:1.2堆焊工艺:1.2.1首先将待修复的平滑靴清理干净,去除煤与铁锈等杂质,将平滑靴置于水平状态,两头垫实。
由于平滑靴工作时一般都是局部磨损严重,所以首先应将未完全磨损的残余部分用割炬吹除,保证平滑靴的基本面平整。
然后将滑靴四边打出坡口,用于钢板的对缝焊接。
1.2.2根据滑靴的面积尺寸,准备厚30mm、长800mm、宽200mm的高强度耐磨钢板一块(我们采用的是报废刮板机溜槽的底板),将钢板的四边分别打出坡口,与平滑靴上打出的坡口形成“V”形坡口,坡口开度120°,坡口两侧以内用抛光砂轮片打光,选用J506结构钢焊条,焊条直径?3.2,焊接电流190A~210A 进行焊接;同时在钢板上开出2~4个?60的圆孔,用J506焊条堆焊填实,增加钢板与平滑靴的焊接面积,增大了焊接强度。
钻杆接头耐磨带堆焊药芯焊丝的研究

1 试 验 材料 及 方法
向力的不断增高 , 导致钻杆 与套管 的磨损 问题更 为突 出 卜 。钻 杆接 头耐 磨带 因其 具 有优 于钻 杆 接 头 本 身 的耐磨性能 , 同时能够降低对套管 的磨损 的优点 , 从而 对解决钻杆与 套管 的磨损 这一 问题起 到关 键性 的作 用 J 。耐磨带技术 已经成为 了现代钻井过程 中必不
堆焊专题 r 蜉 掳
钻 杆 接 头 耐 磨 带 堆 焊 药 芯 焊 丝 的 研 究
北京 工 业 大 学 材 料 科 学 与 工 程 学 院( 1 0 0 1 2 4 ) 北京 工业 大 学 机 械 工程 博士 后 流动站 ( 1 0 0 1 2 4 )
摘要
刘希 学 贺定 勇 蒋 建敏
周 正 王 智慧 崔
丽
赵秋 颖
研 制一种 F e ・ B — N b - N i 系钻杆耐磨带堆焊药芯焊丝 , 采用 C O 气体保护 堆焊方法 , 制备 F e . B . N b 。 N i 耐磨
堆焊合金 , 利用 O M, S E M, X R D等方法对堆焊合金 的显 微组织进行 了观察分析 , 对堆焊层 的硬度及 耐磨性 能进行 了 测试 分析。结 果表明 , F e - B . N b - N j 堆焊 合金 耐磨 性 能 比国外 某进 口药芯 焊丝 提 高 了约 3 7 %, 其 宏观 硬度 值 达到 H R C 6 0 . 5—6 2 . 2 。F e - B — N b — N i 堆 焊 合 金 的显 微 组 织 为 马 氏体 +铁 素 体 +少 量 渗 碳 体 +颗 粒 状 N b C+包 晶 F e , ( B, c)+ 共晶F e , ( B, C ) 6 、 F e , ( B , C )+少量共晶 F e B相 , 其中 N b C硬质颗 粒弥散 的分 布于基 体 中, 基体 中 的 马氏体组 织具 有优异的强度和耐磨性 , 起 到了很 好的耐磨骨架 的作 用 。F e - B — N b - N i 堆焊 合金 的磨 损机理 主要是犁
降低钻杆耐磨带过度磨损 提高钻杆使用寿命

2791 概述钻杆是钻柱的基本组成部分,主要用于传递扭矩、输送钻井液,以及在钻井过程中不断连接钻杆,以达到不断加深井眼的目的。
钻杆使用寿命的长短,与钻杆失效数量成正比。
某管具服务站使用量最大、最频繁的是5"G105钻杆。
本文就5"G105钻杆失效数量及原因进行统计分析,找出影响5"G105钻杆使用寿命的主要原因,从而提出相应对策,提高钻杆使用寿命。
本文中的使用寿命指正常使用周期内的使用寿命,即钻杆正常使用寿命周期内因失效而影响的使用寿命。
2 5"G105钻杆使用情况分析某管具服务站近三年5"G105钻杆周转总量116286根次,停用总量为1995根,其中报废总量493根(报废指因使用后损坏而无法修复的钻杆,不包括技术淘汰)。
从量上的分析来看,因接头损坏导致停用的钻杆占74.02%,是影响钻杆使用寿命的主要因素。
以上的分析图表表明,非正常停用的钻杆中,接头外径过小、管体腐蚀严重、管体刺穿是影响钻杆使用寿命的三大主要因素。
在诸多因素中,直接引发钻杆报废的因素包括管体的腐蚀、刺穿、咬扁、过度弯曲等,与钻杆的使用、泥浆性能等相关,从该服务站层来看,视为不可抗因素,本文不做分析。
引发钻杆停用的因素主要是接头的损坏,包括偏磨、长度不够、外径过小、耐磨带掉块等。
分析表明,接头外径过小是接头损坏的主要原因。
接头外径过度磨损、偏磨这二项之和超过总数的98%。
而钻杆的结构形式决定了此二项均发生在接头耐磨带过度磨损之后。
所以,应该把预防耐磨带过度磨损作为提高钻杆使用寿命的主要手段。
3 耐磨带过度磨损原因分析下面结合该管具服务站管理现状以及所服务站的井队的实现情况,对耐磨带过度磨损的原因进行分析。
3.1 修复不及时造成耐磨带磨损后修复不及时的主要原因有:3.1.1 服务站巡井原因该服务站主要负责47支钻井队的管具保障服务。
井队数量多、分布广、距离远、用车量大等因素直接导致巡井力度不够。
目前大部分巡检工作主要依靠服务站上井作业人员上井查看后反馈信息。
无磁钻铤耐磨材料和堆焊工艺研究与应用
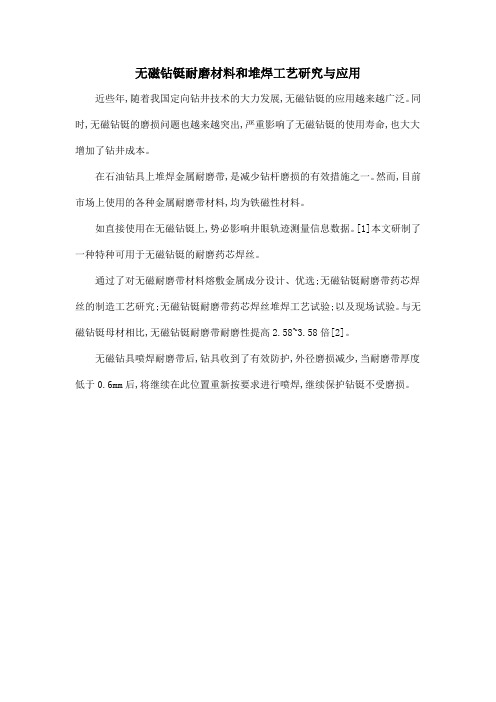
无磁钻铤耐磨材料和堆焊工艺研究与应用近些年,随着我国定向钻井技术的大力发展,无磁钻铤的应用越来越广泛。
同时,无磁钻铤的磨损问题也越来越突出,严重影响了无磁钻铤的使用寿命,也大大增加了钻井成本。
在石油钻具上堆焊金属耐磨带,是减少钻杆磨损的有效措施之一。
然而,目前市场上使用的各种金属耐磨带材料,均为铁磁性材料。
如直接使用在无磁钻铤上,势必影响井眼轨迹测量信息数据。
[1]本文研制了一种特种可用于无磁钻铤的耐磨药芯焊丝。
通过了对无磁耐磨带材料熔敷金属成分设计、优选;无磁钻铤耐磨带药芯焊丝的制造工艺研究;无磁钻铤耐磨带药芯焊丝堆焊工艺试验;以及现场试验。
与无磁钻铤母材相比,无磁钻铤耐磨带耐磨性提高2.58~3.58倍[2]。
无磁钻具喷焊耐磨带后,钻具收到了有效防护,外径磨损减少,当耐磨带厚度低于0.6mm后,将继续在此位置重新按要求进行喷焊,继续保护钻铤不受磨损。
焊接加重钻杆BoTn3000耐磨带堆焊工艺研究
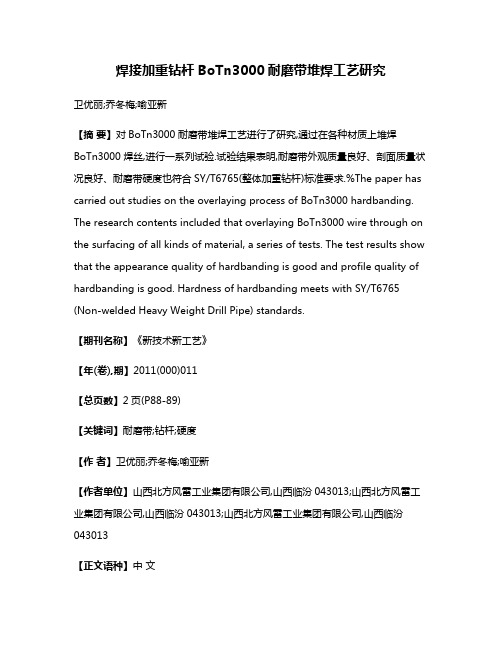
焊接加重钻杆BoTn3000耐磨带堆焊工艺研究卫优丽;乔冬梅;喻亚新【摘要】对BoTn3000耐磨带堆焊工艺进行了研究,通过在各种材质上堆焊BoTn3000焊丝,进行一系列试验.试验结果表明,耐磨带外观质量良好、剖面质量状况良好、耐磨带硬度也符合SY/T6765(整体加重钻杆)标准要求.%The paper has carried out studies on the overlaying process of BoTn3000 hardbanding. The research contents included that overlaying BoTn3000 wire through on the surfacing of all kinds of material, a series of tests. The test results show that the appearance quality of hardbanding is good and profile quality of hardbanding is good. Hardness of hardbanding meets with SY/T6765 (Non-welded Heavy Weight Drill Pipe) standards.【期刊名称】《新技术新工艺》【年(卷),期】2011(000)011【总页数】2页(P88-89)【关键词】耐磨带;钻杆;硬度【作者】卫优丽;乔冬梅;喻亚新【作者单位】山西北方风雷工业集团有限公司,山西临汾043013;山西北方风雷工业集团有限公司,山西临汾043013;山西北方风雷工业集团有限公司,山西临汾043013【正文语种】中文【中图分类】TG44BoTn3000焊丝属于无铬材料,焊接工艺性良好、飞溅小,可以堆焊在各种钻杆接头、整体加重钻杆、摩擦焊加重钻杆、钻铤及各种井下工具表面,代替其磨损,延长寿命。
石油钻杆耐磨带的实际应用
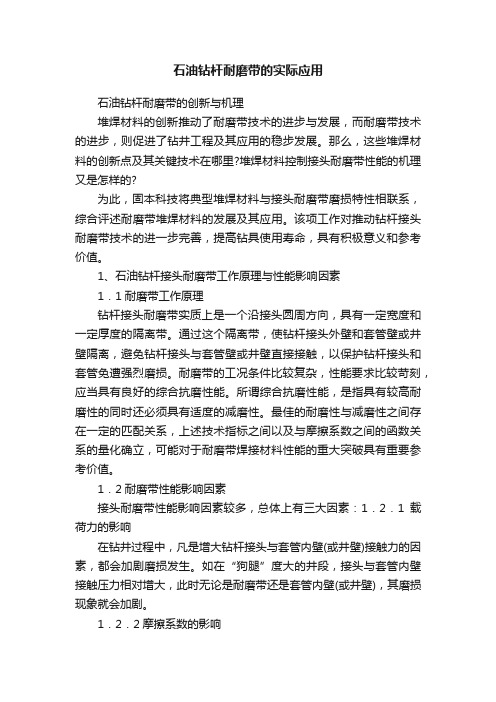
石油钻杆耐磨带的实际应用石油钻杆耐磨带的创新与机理堆焊材料的创新推动了耐磨带技术的进步与发展,而耐磨带技术的进步,则促进了钻井工程及其应用的稳步发展。
那么,这些堆焊材料的创新点及其关键技术在哪里?堆焊材料控制接头耐磨带性能的机理又是怎样的?为此,固本科技将典型堆焊材料与接头耐磨带磨损特性相联系,综合评述耐磨带堆焊材料的发展及其应用。
该项工作对推动钻杆接头耐磨带技术的进一步完善,提高钻具使用寿命,具有积极意义和参考价值。
1、石油钻杆接头耐磨带工作原理与性能影响因素1.1耐磨带工作原理钻杆接头耐磨带实质上是一个沿接头圆周方向,具有一定宽度和一定厚度的隔离带。
通过这个隔离带,使钻杆接头外壁和套管壁或井壁隔离,避免钻杆接头与套管壁或井壁直接接触,以保护钻杆接头和套管免遭强烈磨损。
耐磨带的工况条件比较复杂,性能要求比较苛刻,应当具有良好的综合抗磨性能。
所谓综合抗磨性能,是指具有较高耐磨性的同时还必须具有适度的减磨性。
最佳的耐磨性与减磨性之间存在一定的匹配关系,上述技术指标之间以及与摩擦系数之间的函数关系的量化确立,可能对于耐磨带焊接材料性能的重大突破具有重要参考价值。
1.2耐磨带性能影响因素接头耐磨带性能影响因素较多,总体上有三大因素:1.2.1载荷力的影响在钻井过程中,凡是增大钻杆接头与套管内壁(或井壁)接触力的因素,都会加剧磨损发生。
如在“狗腿”度大的井段,接头与套管内壁接触压力相对增大,此时无论是耐磨带还是套管内壁(或井壁),其磨损现象就会加剧。
1.2.2摩擦系数的影响在钻井过程中,凡是增大接头与套管内壁摩擦系数的因素,都会加剧磨损发生。
如润滑剂品种或加入量不合适、转盘转速增大以及温度过高或过低时,其磨损现象也会加剧。
1.2.3耐磨带与套管(或井壁)材料特性的影响根据摩擦学中的“吸附膜”理论,对于钻杆钢与岩石形成的摩擦副,两者之间很难形成吸附膜,摩擦系数主要取决于摩擦副材料的表面特性,而摩擦副其表面特性是稳定的,摩擦系数受载荷的影响较小。
浅谈报废无磁钻铤的改进技术r——无磁钻铤的敷焊修复

浅谈报废无磁钻铤的改进技术r——无磁钻铤的敷焊修复赵晶;刘战锋;郑锡坤【摘要】钻井行业生产经营中,无磁钻铤发挥着重要的作用.但是,在无磁钻铤的实际应用中,人们发现其外径的磨损量较为严重,且很快无磁钻铤便会报废.为提高无磁钻铤的应用价值,提高钻井行业的经济收益,技术人员通过实际操作和参考技术资料等,对报废的无磁钻铤进行改进,将其运用在钻井行业,减少无磁钻铤的采购成本,并为无磁钻铤技术的发展提供新的方向.【期刊名称】《信息记录材料》【年(卷),期】2018(019)004【总页数】2页(P31-32)【关键词】无磁钻铤;改进技术;敷焊修复【作者】赵晶;刘战锋;郑锡坤【作者单位】西安石油大学机械工程学院陕西西安 710065;山西北方风雷工业集团有限公司山西侯马 043013;西安石油大学机械工程学院陕西西安 710065;山西北方风雷工业集团有限公司山西侯马 043013【正文语种】中文【中图分类】TE921.21 引言无磁钻铤在使用中损耗较为严重,技术人员为节省采购成本、研发新技术以及改善无磁钻铤的浪费现象,通过敷焊修复技术改进报废无磁钻铤,使其可以重新使用,投入石油钻井的使用中。
本文从石油钻井实际工作的角度出发,对无磁钻铤进行简要介绍,而后分析无磁钻铤的敷焊修复技术,最后分析修复报废无磁钻铤的实际意义,推动敷焊修复技术的发展。
2 无磁钻铤简介低碳高铬锰合金钢是制作无磁钻铤的原材料,需要经过严格的化学配比,并利用精炼以及锻造等技术,使其具有强度较高的机械性能、低磁导率良好,且耐磨性以及耐腐蚀开裂等性能非常优异,达到石油钻井的工作需求。
石油钻井工作中,需要利用磁性测量仪器确定井眼的方向,而磁性测量仪器工作中需要感应大地磁场,故而,磁性测量仪器需要在无磁环境下工作[1]。
但是,钻井工作适应的钻具绝大多数具有磁性,进而产生磁场,对磁性测量仪器产生影响,影响井眼方向测量数据的准确性。
无磁钻铤可以在钻进工作中营造无磁环境,为磁性测量仪器提供工作条件,保证感应大地磁场数据信息的准确性,且满足钻井工作对钻铤的需求。
耐磨堆焊技术

耐磨堆焊技术
耐磨堆焊技术是一种被用于金属制造领域的特殊焊接方法,它可以让机械零部件集成到机床或其他类似装置中,从而增强零部件的强度和结构稳定性。
耐磨堆焊技术主要用于铰链、轴和其他高度精确的零部件,能够极大地提高机械零部件的耐磨性。
耐磨堆焊技术的基本原理是用高温的激光或等离子等离子来分
解特定部位的金属,使它变得较软并分散在其他金属表面。
激光分解金属时不会产生任何金属熔核,因此可以保证结构安全,组件之间也不会有任何错位。
耐磨堆焊技术主要包括:设计焊锡图、制作焊接夹具、选择正确的焊接材料和清洁焊点。
设计焊锡图时,应根据机械零部件和焊接材料的性能,选择适当的焊接形状,如痕迹折弯、焊点面积大小、锡头的形状等,确保焊接的质量和稳定性。
制作焊接夹具时,应根据机械零部件的形状,重点做好夹具的精度要求,以便在焊接过程中,机械零部件的延伸质量及焊接精度能达到预期要求。
选择正确的焊接材料也是耐磨堆焊技术的重要环节,一般来说,金属零件应该使用高抗磨性、低熔点和低收缩率的焊接材料。
清洁焊点时,应使用漂洗和酸洗、高压水洗等方法清除金属表面的附着物,加强金属表面的附着力。
耐磨堆焊技术具有良好的耐磨性和耐久性,能够保证更好的机械特性,更长的使用寿命。
它可以实现高精度零部件的针脚焊接,相对于传统的焊接方法,具有更高的稳定性,能够满足高性能机床的高要
求。
耐磨堆焊技术在机械加工领域有广泛的应用,可以极大地提高机械零部件的耐磨性,为制造业提供高性能的解决方案。
钻具耐磨带磨损情况说明

钻具耐磨带磨损情况说明
无磁钻具耐磨性差,价格昂贵。
随着水平井、大位移井、超深井等复杂结构井越来越多,无磁钻具的磨损问题日益突出,因此开展无
磁钻具的磨损机理及防护措施的研究具有十分重要的工程应用价值。
无磁钻具具有导磁率低的特性,它能够使井下磁性测量仪器处于不受钻具磁性干扰的无磁环境中,从而确保测得的数据真实。
影响无磁钻具破坏的因素有疲劳破坏、腐蚀、氢脆、纯强度破坏和刺穿等。
本文以无磁钻具防护技术措施为研究目标,分析无磁钻具磨损机理,对比
无磁钻具抗磨材料特点,对无磁钻具等离子喷焊技术的应用进行了深入研究。
通过大量试验对比,提出了一套可行的等离子喷焊技术的工艺参数配合,以此工艺参数所进行敷焊的无磁钻具的耐磨性在现场实际使用中得到验证。
本文的研究成果可以应用于无磁钻具的防护,延长无磁钻具使用寿命,对科学使用和防护无磁钻具磨损具有一定的指导意义。
- 1、下载文档前请自行甄别文档内容的完整性,平台不提供额外的编辑、内容补充、找答案等附加服务。
- 2、"仅部分预览"的文档,不可在线预览部分如存在完整性等问题,可反馈申请退款(可完整预览的文档不适用该条件!)。
- 3、如文档侵犯您的权益,请联系客服反馈,我们会尽快为您处理(人工客服工作时间:9:00-18:30)。
加重钻杆耐磨带堆焊的必要性及其应用
论文摘要:在深井超深井勘探过程中,由于径向力、涡动、横向振动等因素的存在,随着钻井时间的增长,钻柱作用于套管内壁的侧向力增大,导致套管和钻具接头磨损的问题越来越严重。
造成钻具耐磨带失效的主要原因有地层研磨性、钻杆的井下工况、耐磨材料选择与敷焊工艺的影响。
选择合理的耐磨材料与敷焊工艺对解决钻具耐磨带失效问题非常重要。
论文关键词:耐磨带钻具铁基合金粉焊丝
一、加重钻杆的作用
加重钻杆通常应用于水平井、定向井以及深井等难度较大的井位中,可以部分代替钻铤以提高钻机的钻深能力,由于它的弹性比普通钻铤高,在弯曲井眼中用它来代替钻铤时,可以降低旋转扭矩和提升负荷。
另外在弯曲井段用加重钻杆代替钻杆时,由于加重钻杆于井壁接触面积较小,能减少旋转扭矩和上提阻力以及压差卡钻的可能性。
更重要的是有利于保持定向井的方向。
二、钻井过程中的磨损种类
在油气田勘探开发钻井中,尤其是在深井、大位移井、水平井、大斜度井中,钻杆和套管的磨损严重,给油气田带来重大损失。
因此,钻井过程中钻杆和套管的磨损及防磨问题,已引起钻井界的密切关注。
套管磨损———套管磨损的主要形式为偏磨,偏磨后的套管横截面呈月牙型。
一方面套管圆周上呈月牙型部位壁厚最薄,导致抗挤强度大大降低。
在高地层压力作用下,假如设计的套管安全系数没有足够大,轻易导致套管挤毁,造成钻井报废或局部井段报废。
另一方面,偏磨套管在抗挤强度降低的同时其抗内压强度也随着降低。
在井控及中途测试时,假如没有充分考虑到套管磨损的影响,可能造成严重后果,即气井完井井控和测试时,要么冒套管破裂地面窜气的风险,要么提前入套管或下套管后再测试。
这不仅造成重大经济损失,而且给加深钻井造成困难或钻不到设计深度。
钻杆磨损———由于钻杆接头的外径大于杆体的外径,因此钻杆的磨损主要表现在钻杆接头的磨损。
当井眼曲率较大时,钻杆杆体也会受到磨损。
在钻井过程中旋转的钻杆接头和井壁或套管壁不断地摩擦,造成接头的严重磨损,尤其在硬地层或研磨性地层,井段钻杆接头磨损加剧。
钻杆接头磨损后其接头壁厚变小,加快了钻杆的降级和报废速度。
同时由于接头外径磨损变小,钻杆丝扣强度降低,在钻井过程中轻易导致钻杆胀扣、脱扣或钻柱掉入井内,造成井下事故。
所有这些都将带来严重的经济损失,从而增加了钻井成本。
三、加重钻杆磨损分析
由于加重钻杆自身的重量,在斜井段工作时,在重力的作用下,不可避免的于井壁进行偏磨,由于接头直径大于管体直径,首先接头进行偏磨,因此加重钻杆生产厂家在加重钻杆出厂前,都要对接头及加厚部位进行耐磨带敷焊,来保护加重钻杆的接头,从而延长其使用寿命。
旧加重钻杆由于多次在井下工作,接头不断地与井壁摩擦,随着在井下使用次数的增多,原有的耐磨带不断的偏磨,导致接头出现椭圆,无法进行连接,只能重新对焊新接头或报废。
四、钻杆耐磨带技术及其作用
防止钻杆和套管磨损的一个最基本的原理是避免钻杆和套管的直接接触,在钻杆接头上加焊耐磨带也是一项有效的防磨技术。
通过耐磨带堆焊把钻杆与套管隔离,从而有效地保护套管和钻杆。
钻杆耐磨带的作用:
1.在钻杆接头上敷焊耐磨带,耐磨带代替钻杆接头与套管和井壁直接接触,保护
的钻杆接头。
2.在钻杆接头敷焊耐磨带,可以有效的防止接头表面直接与井壁或套管接触,显
著的减少摩擦热,从而有效降低钻杆街头热裂纹产生的几率。
3.没有敷焊耐磨带的光钻杆接头,或敷焊碳化硅等不具有保护套管类型得耐磨带
得钻杆街头,将会对套管产生严重的磨损,选择具有优良减磨性能的耐磨带,可以降低与套管壁或地层井壁之间的摩擦,实现及保护钻杆又保护套管得目
的。
五、耐磨材料的选择及敷焊工艺
钻具接头外表面的磨损机理以显微切削为主同时兼有腐蚀作用。
对于这种磨损其基本对策是大幅度提高钻具接头工作面的硬度。
一般接头寿命约为管体寿命的几分之一,如果在接头外径部分敷焊耐磨带,可大幅度提高钻具接头的耐磨性,延长使用寿命。
为了提高钻具接头的使用寿命,其外表面喷涂耐磨合金带的方法在国内外已被广泛采用。
目前我国的钻具耐磨带敷焊材料主要以美国安科公司的100XT、300XT和国产金达陵的2-55、3-60焊丝以及铁基自熔性合金粉Fe14、Fe90为主。
六、综合社会、经济、技术效益分析
对一根旧加重钻杆进行耐磨带的敷焊,成本价约400元,而对焊修复成本为7000元,其中接头费用3000元、加工费用4000元。
接头出现偏磨的加重钻杆,随着偏磨量的不断加大,与井壁的间隙就越大,钻具偏摆量增加,离心力加大,偏磨量也加大,导致井径不规则,钻头磨损加大,从而影响井深质量,增加钻井成本。
对旧加重钻杆进行耐磨带敷焊可延长使用寿命,即为公司节约成本。
又节约钻井成本,还可以提高井身质量,减少井下事故的发生。
因此对加重钻杆进行耐磨带敷焊具有重大经济和社会效益。
目前加重钻杆的市场价格调查。
目前市场加重钻杆的需求量
目前加重钻杆生产量
磨损情况,速度,什么情况报废。
堆焊后的效果。