雕刻机毕业设计外文文献翻译
机械毕业设计英文外文翻译496铣 削

附录A 英文原文MILLINGMilling is a machining process that is carried out by means of a multiedge tool known as a milling cutter .In this process,metal removal is achieved through combining the rotary motion of the milling cutter and linear motions of the workpiece ling operations are employed in producing flat ,contoured and helical surfaces as well as for thread-and gear-cutting operations.Each of the cutting edges of a milling cutter acts as an individualsingle-point cutter when it engages with the workpiece metal .Therefore ,each of those cutting edges has appropriate rake and relief angles .Since only a few of the cutting edges are engaged with the workpiece at a time ,heavy cuts can be taken without adversely affecting the tool life .In fact ,the permissible cutting speeds and feeds for milling are there to four times higher than those for turning or drilling .Moreover,the quality of the surfaces machined by turning ,shaping ,or drilling.A wide variety of milling cutters is available in industry with the fact that a milling machine is a very versatile machine milling machine the backbone of a machining workshop.As far as the direction of cutter rotation and workpiece feed are concerned ,milling is performed by either of a machining workshop.Up milling (conventional milling) .In up milling the workpiece is fed against the direction of cutter rotation ,as shown in Fig.5. l(a) .As we can see in that figure ,the depth of cut (and consequently the load ) gradually increases on the successively engaged cutting edges .Therefore ,the machining process involves no impact loading ,thus ensuring smoother operation of the machine tool and longer tool life .The quality of the machined surface obtained by up milling is not very high .Nevertheless ,upmilling is commonly used in inciustry ,especially for rough cuts.Down milling(climb milling) .As can be seen in Fig.5.1b ,in down milling the cutter rotation coincides with the direction of feed at the contact point between the tool and the workpiece .It can also be seen that the maximum depth of cut is achieved directly as the cutter engages with the workpiece .This result in a kind of impact ,or sudden loading .Therefore ,this method cannot be used the milling machine is equipped with a backlash eliminator on the feed screw. The advantages of this method include higher quality of the machined surface and easier clamping of workpieces,since the cutting forces act downward.Types of milling cuttersThere is wide variety of milling cutter shapes.Each of them is designed to perform effectively a specific.Generally,a milling cutter can be described as a multiedge cutting tool having the shape of a solid of revolution,with the cutting teeth arranged either on the periphery or on an end face or on both.following is a quick survery of the commonly used types of milling cutters.Plain milling cutter.A plain milling cutter is a disk-shaped cutting tool that may hace either straght or helical teeth,as shown in Fig.5.2a.This typeis always mounted on horizental milling machines and is used for machining flat surfaces.Face milling cutters.A face milling cutter is also used for machining flat surfaces,it is bothed at the end of a shot arbor,which is in turn mounted on a vertical milling machine.Fig.5.2b indicates a milling cutter of this type.Plain metal slitting saw.Fig.5.2c indicates a plain metal slitting saw cutter.We can see that it actually involves a very thin plain milling cutter.Side milling cutter.Aside milling cutter is used for cutting slots,grooves,and splines.As we can see in Fig.5.2d,it is quite sililar to the plain milling cutter,the difference between thebeing that this type has teeth on the side .As was the case with the plain cutter ,the cutting teeth can be straight or helical.Angle milling cutter .An angle milling cutter is employed in cutting dovetail grooves ,ratchet wheels ,and the like .Fig.5.2e) indicates a milling cutter of this type.T-slot cutter .As shown in Fig.5.2f) ,a T-slot cutter involves a plain milling cutter with an integral shaft normal to it .As the name suggests ,this type is used for milling T-slots.End mill cutters .End mill cutters find common application in cutting slots ,grooves ,flutes ,splines ,pocketing work ,and the like .Fig.5.2g indicates an end mill cutter .The latter is always mounted on a vertical milling machine and can have two or four times ,which may be either straight or helical.Form milling cutters Th:~ teeh of a form milling cuuter have a certain shape ,which is identical to the metal to be removed during the milling operation. Examples of this type include gear currer ,gear hobs, convex and concave cutters, and the like .Form milling cutters are mounted on horizontal milling machines,as is esplained later when we discuss gear cutting.Material of Milling CuttersThe commonly used milling cutters are made of high-speed steel, which is generally adequate for most jobs .Milling cutters tipped with sintered cabides nonferrous alloys as cutting teeth are usually employed for mass production,gh cutting speeds are requied.Cutting tool material may be classified in different ways main element. The main element may be carbon steel.high-speed steel meaJum-alloy steel .high-speed steel, acemented carbide. Of course, iron is the main constitutent .of the first three.Carbon steel toolsCarbon steel tools have a limited use, as they are characterized by. Low hot hardness and poor hardnability. Carbon contents range from o.s percent to 1.3 prcent. Tools of this type can be used for light work where temperatures produced do not exceed 204~C.Medium-alloy steelsThese steels are not satisfactory for operations finishing operations. They can be used successfully.High-speed steelsHigh-speed steel tools are characterized by superior wear resistance and hot hardness. High-speed steel tools contain Up to 18 percent tungsten and 51.5 percent chromium as the principal alloying element, Other alloying element such as molybdenum and cobalt give special qualities, These cutters will retain keen cutting edges at temperatures up to 593 ~C ( 1100~F ) .Also the proper cutting fluids can increase their life and improve use to a considerable extent.Cast AlloysA number of nonferrous alloys know as stellhes have developed for use asculting tools ,these alloys usually contain 2 to 4 percent carbon 14 to 29 percent tungsten 27 to 32 percent chromium 40 to 50 percent cobalt; the tools must be used as cast ;and cannot ;be near treated, they are not affected by heat up to 815~C (1500~F), high-speed steel tools are somewhat harder that Stellite up to 537 ~C(ll00~F).above this temperatures, stelite retails hardness much better ,highcutting speeds are possible with this type of tool than with high speed steel tools.Stelite, being cast ,has a tendency to shatter under shock ,thus ,it must be well supported in the toolhoider. It can be tip-brazed or weided to a shank steel. It may also be fashioned as a removable bit in a specialtoolhoider.Cemented CarbidesCemented carbide tools are know by trade named such as Carpoioy, Kennametal,Vascoioy-Ronet,and Firtnite. There are two genral grades of metal-cutting cemented in use:1. The "C" grace is made up of tung-sten carbide with cobait grace is used in machining cast ircn and nonterrous metals.2. The "S"grade is made up of tung-sten. Titanium,and tantalum carbides cobalt as a binder. This grade is used on steels withThe cobalt content may vary from 3 percent to 16 percent. The larger the amount of cobait. The tougher and more wear-resistant beccmes the tool. The"S"graces usually contain form 0 percent to 16 percent tianlum carbide and 0percent to 10 percent tantalum carbide. The mean grain size is important. Toolsof icential cnemical composition but of different grain size will have differentpropentes. Coarser grain materi tl is more snock resistant. Cemented carbices have the following cnaractenstics High naraness over a wide range of temperatures.High thermal concuctivity.Low thermal expansion.Stiffness.Cemented carbide shculd be used at much higher operating speeds than high speed steel tool.The depth of cut is the thickness of the meal layer that is to be removed in one cut o The maximum allowable depth of cue depends upon the material being machined and is commonly taken up to 5/16in. (or 8mm)in toughing operations and 1/16in(aboutl.5mm)in finishing operations .Another parameter that affects milling operations is the width of cut .The Latter is the width of the workpiece in contact with the cutter in a direction normal to the feed. We can easily see that the width of cut should decrease with increasingdepth of cut to keep the load and powerrequirement below by the cutter and the machine tool, respectively.Types of Milling MachinesThere are several types of milling machines in industry. They are generally classified based on their construction and design features .They vary from the common general-purpose types to duplicators and machining operation that involve a tool magazine and are capable of carrying out many machining operation with a single workpiece setup. For example Plain horizontal milling machine, Universal milling machine, Vertial milling machine, Duplicators,Machining centers.附录B 汉语翻译铣削铣削是用铣刀进行多刃旋转加工的工艺。
机械加工毕业论文中英文资料外文翻译文献
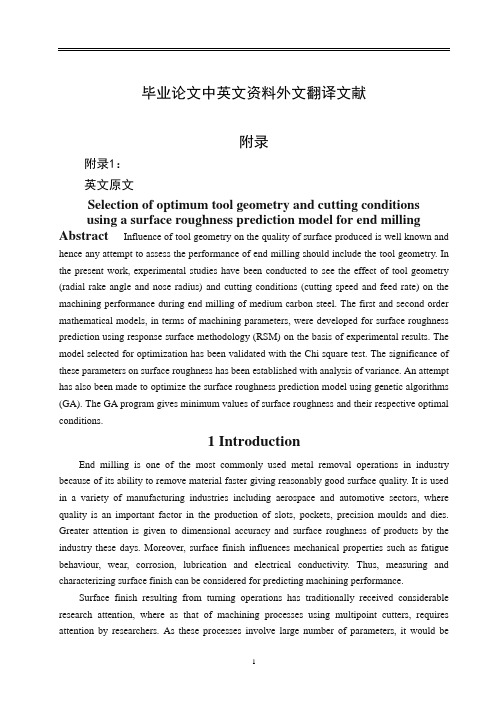
毕业论文中英文资料外文翻译文献附录附录1:英文原文Selection of optimum tool geometry and cutting conditionsusing a surface roughness prediction model for end milling Abstract Influence of tool geometry on the quality of surface produced is well known and hence any attempt to assess the performance of end milling should include the tool geometry. In the present work, experimental studies have been conducted to see the effect of tool geometry (radial rake angle and nose radius) and cutting conditions (cutting speed and feed rate) on the machining performance during end milling of medium carbon steel. The first and second order mathematical models, in terms of machining parameters, were developed for surface roughness prediction using response surface methodology (RSM) on the basis of experimental results. The model selected for optimization has been validated with the Chi square test. The significance of these parameters on surface roughness has been established with analysis of variance. An attempt has also been made to optimize the surface roughness prediction model using genetic algorithms (GA). The GA program gives minimum values of surface roughness and their respective optimal conditions.1 IntroductionEnd milling is one of the most commonly used metal removal operations in industry because of its ability to remove material faster giving reasonably good surface quality. It is used in a variety of manufacturing industries including aerospace and automotive sectors, where quality is an important factor in the production of slots, pockets, precision moulds and dies. Greater attention is given to dimensional accuracy and surface roughness of products by the industry these days. Moreover, surface finish influences mechanical properties such as fatigue behaviour, wear, corrosion, lubrication and electrical conductivity. Thus, measuring and characterizing surface finish can be considered for predicting machining performance.Surface finish resulting from turning operations has traditionally received considerable research attention, where as that of machining processes using multipoint cutters, requires attention by researchers. As these processes involve large number of parameters, it would bedifficult to correlate surface finish with other parameters just by conducting experiments. Modelling helps to understand this kind of process better. Though some amount of work has been carried out to develop surface finish prediction models in the past, the effect of tool geometry has received little attention. However, the radial rake angle has a major affect on the power consumption apart from tangential and radial forces. It also influences chip curling and modifies chip flow direction. In addition to this, researchers [1] have also observed that the nose radius plays a significant role in affecting the surface finish. Therefore the development of a good model should involve the radial rake angle and nose radius along with other relevant factors.Establishment of efficient machining parameters has been a problem that has confronted manufacturing industries for nearly a century, and is still the subject of many studies. Obtaining optimum machining parameters is of great concern in manufacturing industries, where the economy of machining operation plays a key role in the competitive market. In material removal processes, an improper selection of cutting conditions cause surfaces with high roughness and dimensional errors, and it is even possible that dynamic phenomena due to auto excited vibrations may set in [2]. In view of the significant role that the milling operation plays in today’s manufacturing world, there is a need to optimize the machining parameters for this operation. So, an effort has been made in this paper to see the influence of tool geometry(radial rake angle and nose radius) and cutting conditions(cutting speed and feed rate) on the surface finish produced during end milling of medium carbon steel. The experimental results of this work will be used to relate cutting speed, feed rate, radial rake angle and nose radius with the machining response i.e. surface roughness by modelling. The mathematical models thus developed are further utilized to find the optimum process parameters using genetic algorithms.2 ReviewProcess modelling and optimization are two important issues in manufacturing. The manufacturing processes are characterized by a multiplicity of dynamically interacting process variables. Surface finish has been an important factor of machining in predicting performance of any machining operation. In order to develop and optimize a surface roughness model, it is essential to understand the current status of work in this area.Davis et al. [3] have investigated the cutting performance of five end mills having various helix angles. Cutting tests were performed on aluminium alloy L 65 for three milling processes (face, slot and side), in which cutting force, surface roughness and concavity of a machined plane surface were measured. The central composite design was used to decide on the number of experiments to be conducted. The cutting performance of the end mills was assessed usingvariance analysis. The affects of spindle speed, depth of cut and feed rate on the cutting force and surface roughness were studied. The investigation showed that end mills with left hand helix angles are generally less cost effective than those with right hand helix angles. There is no significant difference between up milling and down milling with regard tothe cutting force, although the difference between them regarding the surface roughness was large. Bayoumi et al.[4] have studied the affect of the tool rotation angle, feed rate and cutting speed on the mechanistic process parameters (pressure, friction parameter) for end milling operation with three commercially available workpiece materials, 11 L 17 free machining steel, 62- 35-3 free machining brass and 2024 aluminium using a single fluted HSS milling cutter. It has been found that pressure and friction act on the chip – tool interface decrease with the increase of feed rate and with the decrease of the flow angle, while the cutting speed has a negligible effect on some of the material dependent parameters. Process parameters are summarized into empirical equations as functions of feed rate and tool rotation angle for each work material. However, researchers have not taken into account the effects of cutting conditions and tool geometry simultaneously; besides these studies have not considered the optimization of the cutting process.As end milling is a process which involves a large number f parameters, combined influence of the significant parameters an only be obtained by modelling. Mansour and Abdallaet al. [5] have developed a surface roughness model for the end milling of EN32M (a semi-free cutting carbon case hardening steel with improved merchantability). The mathematical model has been developed in terms of cutting speed, feed rate and axial depth of cut. The affect of these parameters on the surface roughness has been carried out using response surface methodology (RSM). A first order equation covering the speed range of 30–35 m/min and a second order equation covering the speed range of 24–38 m/min were developed under dry machining conditions. Alauddin et al. [6] developed a surface roughness model using RSM for the end milling of 190 BHN steel. First and second order models were constructed along with contour graphs for the selection of the proper combination of cutting speed and feed to increase the metal removal rate without sacrificing surface quality. Hasmi et al. [7] also used the RSM model for assessing the influence of the workpiece material on the surface roughness of the machined surfaces. The model was developed for milling operation by conducting experiments on steel specimens. The expression shows, the relationship between the surface roughness and the various parameters; namely, the cutting speed, feed and depth of cut. The above models have not considered the affect of tool geometry on surface roughness.Since the turn of the century quite a large number of attempts have been made to find optimum values of machining parameters. Uses of many methods have been reported in the literature to solve optimization problems for machining parameters. Jain and Jain [8] have usedneural networks for modeling and optimizing the machining conditions. The results have been validated by comparing the optimized machining conditions obtained using genetic algorithms. Suresh et al. [9] have developed a surface roughness prediction model for turning mild steel using a response surface methodology to produce the factor affects of the individual process parameters. They have also optimized the turning process using the surface roughness prediction model as the objective function. Considering the above, an attempt has been made in this work to develop a surface roughness model with tool geometry and cutting conditions on the basis of experimental results and then optimize it for the selection of these parameters within the given constraints in the end milling operation.3 MethodologyIn this work, mathematical models have been developed using experimental results with the help of response surface methodolog y. The purpose of developing mathematical models relating the machining responses and their factors is to facilitate the optimization of the machining process. This mathematical model has been used as an objective function and the optimization was carried out with the help of genetic algorithms.3.1 Mathematical formulationResponse surface methodology(RSM) is a combination of mathematical and statistical techniques useful for modelling and analyzing the problems in which several independent variables influence a dependent variable or response. The mathematical models commonly used are represented by:where Y is the machining response, ϕ is the response function and S, f , α, r are milling variables and ∈is the error which is normally distributed about the observed response Y with zero mean.The relationship between surface roughness and other independent variables can be represented as follows,where C is a constant and a, b, c and d are exponents.To facilitate the determination of constants and exponents, this mathematical model will have to be linearized by performing a logarithmic transformation as follows:The constants and exponents C, a, b, c and d can be determined by the method of least squares. The first order linear model, developed from the above functional relationship using least squares method, can be represented as follows:where Y1 is the estimated response based on the first-order equation, Y is the measured surface roughness on a logarithmic scale, x0 = 1 (dummy variable), x1, x2, x3 and x4 are logarithmic transformations of cutting speed, feed rate, radial rake angle and nose radiusrespectively, ∈is the experimental error and b values are the estimates of corresponding parameters.The general second order polynomial response is as given below:where Y2 is the estimated response based on the second order equation. The parameters, i.e. b0, b1, b2, b3, b4, b12, b23, b14, etc. are to be estimated by the method of least squares. Validity of the selected model used for optimizing the process parameters has been tested with the help of statistical tests, such as F-test, chi square test, etc. [10].3.2 Optimization using genetic algorithmsMost of the researchers have used traditional optimization techniques for solving machining problems. The traditional methods of optimization and search do not fare well over a broad spectrum of problem domains. Traditional techniques are not efficient when the practical search space is too large. These algorithms are not robust. They are inclined to obtain a local optimal solution. Numerous constraints and number of passes make the machining optimization problem more complicated. So, it was decided to employ genetic algorithms as an optimization technique. GA come under the class of non-traditional search and optimization techniques. GA are different from traditional optimization techniques in the following ways:1.GA work with a coding of the parameter set, not the parameter themselves.2.GA search from a population of points and not a single point.3.GA use information of fitness function, not derivatives or other auxiliary knowledge.4.GA use probabilistic transition rules not deterministic rules.5.It is very likely that the expected GA solution will be the global solution.Genetic algorithms (GA) form a class of adaptive heuristics based on principles derived from the dynamics of natural population genetics. The searching process simulates the natural evaluation of biological creatures and turns out to be an intelligent exploitation of a random search. The mechanics of a GA is simple, involving copying of binary strings. Simplicity of operation and computational efficiency are the two main attractions of the genetic algorithmic approach. The computations are carried out in three stages to get a result in one generation or iteration. The three stages are reproduction, crossover and mutation.In order to use GA to solve any problem, the variable is typically encoded into a string (binary coding) or chromosome structure which represents a possible solution to the given problem. GA begin with a population of strings (individuals) created at random. The fitness of each individual string is evaluated with respect to the given objective function. Then this initial population is operated on by three main operators – reproduction cross over and mutation– to create, hopefully, a better population. Highly fit individuals or solutions are given theopportunity to reproduce by exchanging pieces of their genetic information, in the crossover procedure, with other highly fit individuals. This produces new “offspring” solutions, which share some characteristics taken from both the parents. Mutation is often applied after crossover by altering some genes (i.e. bits) in the offspring. The offspring can either replace the whole population (generational approach) or replace less fit individuals (steady state approach). This new population is further evaluated and tested for some termination criteria. The reproduction-cross over mutation- evaluation cycle is repeated until the termination criteria are met.4 Experimental detailsFor developing models on the basis of experimental data, careful planning of experimentation is essential. The factors considered for experimentation and analysis were cutting speed, feed rate, radial rake angle and nose radius.4.1 Experimental designThe design of experimentation has a major affect on the number of experiments needed. Therefore it is essential to have a well designed set of experiments. The range of values of each factor was set at three different levels, namely low, medium and high as shown in Table 1. Based on this, a total number of 81 experiments (full factorial design), each having a combination of different levels of factors, as shown in Table 2, were carried out.The variables were coded by taking into account the capacity and limiting cutting conditions of the milling machine. The coded values of variables, to be used in Eqs. 3 and 4, were obtained from the following transforming equations:where x1 is the coded value of cutting speed (S), x2 is the coded value of the feed rate ( f ), x3 is the coded value of radial rake angle(α) and x4 is the coded value of nose radius (r).4.2 ExperimentationA high precision ‘Rambaudi Rammatic 500’ CNC milling machine, with a vertical milling head, was used for experimentation. The control system is a CNC FIDIA-12 compact. The cutting tools, used for the experimentation, were solid coated carbide end mill cutters of different radial rake angles and nose radii (WIDIA: DIA20 X FL38 X OAL 102 MM). The tools are coated with TiAlN coating. The hardness, density and transverse rupture strength are 1570 HV 30, 14.5 gm/cm3 and 3800 N/mm2 respectively.AISI 1045 steel specimens of 100×75 mm and 20 mm thickness were used in the present study. All the specimens were annealed, by holding them at 850 ◦C for one hour and then cooling them in a furnace. The chemical analysis of specimens is presented in Table 3. Thehardness of the workpiece material is 170 BHN. All the experiments were carried out at a constant axial depth of cut of 20 mm and a radial depth of cut of 1 mm. The surface roughness (response) was measured with Talysurf-6 at a 0.8 mm cut-off value. An average of four measurements was used as a response value.5 Results and discussionThe influences of cutting speed, feed rate, radial rake angle and nose radius have been assessed by conducting experiments. The variation of machining response with respect to the variables was shown graphically in Fig. 1. It is seen from these figures that of the four dependent parameters, radial rake angle has definite influence on the roughness of the surface machined using an end mill cutter. It is felt that the prominent influence of radial rake angle on the surface generation could be due to the fact that any change in the radial rake angle changes the sharpness of the cutting edge on the periphery, i.e changes the contact length between the chip and workpiece surface. Also it is evident from the plots that as the radial rake angle changes from 4◦to 16◦, the surface roughness decreases and then increases. Therefore, it may be concluded here that the radial rake angle in the range of 4◦to 10◦would give a better surface finish. Figure 1 also shows that the surface roughness decreases first and then increases with the increase in the nose radius. This shows that there is a scope for finding the optimum value of the radial rake angle and nose radius for obtaining the best possible quality of the surface. It was also found that the surface roughness decreases with an increase in cutting speed and increases as feed rate increases. It could also be observed that the surface roughness was a minimum at the 250 m/min speed, 200 mm/min feed rate, 10◦radial rake angle and 0.8 mm nose radius. In order to understand the process better, the experimental results can be used to develop mathematical models using RSM. In this work, a commercially available mathematical software package (MATLAB) was used for the computation of the regression of constants and exponents.5.1 The roughness modelUsing experimental results, empirical equations have been obtained to estimate surface roughness with the significant parameters considered for the experimentation i.e. cutting speed, feed rate, radial rake angle and nose radius. The first order model obtained from the above functional relationship using the RSM method is as follows:The transformed equation of surface roughness prediction is as follows:Equation 10 is derived from Eq. 9 by substituting the coded values of x1, x2, x3 and x4 in termsof ln s, ln f , lnαand ln r. The analysis of the variance (ANOV A) and the F-ratio test have been performed to justify the accuracy of the fit for the mathematical model. Since the calculated values of the F-ratio are less than the standard values of the F-ratio for surface roughness as shown in Table 4, the model is adequate at 99% confidence level to represent the relationship between the machining response and the considered machining parameters of the end milling process.The multiple regression coefficient of the first order model was found to be 0.5839. This shows that the first order model can explain the variation in surface roughness to the extent of 58.39%. As the first order model has low predictability, the second order model has been developed to see whether it can represent better or not.The second order surface roughness model thus developed is as given below:where Y2 is the estimated response of the surface roughness on a logarithmic scale, x1, x2, x3 and x4 are the logarithmic transformation of speed, feed, radial rake angle and nose radius. The data of analysis of variance for the second order surface roughness model is shown in Table 5.Since F cal is greater than F0.01, there is a definite relationship between the response variable and independent variable at 99% confidence level. The multiple regression coefficient of the second order model was found to be 0.9596. On the basis of the multiple regression coefficient (R2), it can be concluded that the second order model was adequate to represent this process. Hence the second order model was considered as an objective function for optimization using genetic algorithms. This second order model was also validated using the chi square test. The calculated chi square value of the model was 0.1493 and them tabulated value at χ2 0.005 is 52.34, as shown in Table 6, which indicates that 99.5% of the variability in surface roughness was explained by this model.Using the second order model, the surface roughness of the components produced by end milling can be estimated with reasonable accuracy. This model would be optimized using genetic algorithms (GA).5.2 The optimization of end millingOptimization of machining parameters not only increases the utility for machining economics, but also the product quality toa great extent. In this context an effort has been made to estimate the optimum tool geometry and machining conditions to produce the best possible surface quality within the constraints.The constrained optimization problem is stated as follows: Minimize Ra using the model given here:where xil and xiu are the upper and lower bounds of process variables xi and x1, x2, x3, x4 are logarithmic transformation of cutting speed, feed, radial rake angle and nose radius.The GA code was developed using MATLAB. This approach makes a binary coding system to represent the variables cutting speed (S), feed rate ( f ), radial rake angle (α) and nose radius (r), i.e. each of these variables is represented by a ten bit binary equivalent, limiting the total string length to 40. It is known as a chromosome. The variables are represented as genes (substrings) in the chromosome. The randomly generated 20 such chromosomes (population size is 20), fulfilling the constraints on the variables, are taken in each generation. The first generation is called the initial population. Once the coding of the variables has been done, then the actual decoded values for the variables are estimated using the following formula: where xi is the actual decoded value of the cutting speed, feed rate, radial rake angle and nose radius, x(L) i is the lower limit and x(U) i is the upper limit and li is the substring length, which is equal to ten in this case.Using the present generation of 20 chromosomes, fitness values are calculated by the following transformation:where f(x) is the fitness function and Ra is the objective function.Out of these 20 fitness values, four are chosen using the roulette-wheel selection scheme. The chromosomes corresponding to these four fitness values are taken as parents. Then the crossover and mutation reproduction methods are applied to generate 20 new chromosomes for the next generation. This processof generating the new population from the old population is called one generation. Many such generations are run till the maximum number of generations is met or the average of four selected fitness values in each generation becomes steady. This ensures that the optimization of all the variables (cutting speed, feed rate, radial rake angle and nose radius) is carried out simultaneously. The final statistics are displayed at the end of all iterations. In order to optimize the present problem using GA, the following parameters have been selected to obtain the best possible solution with the least computational effort: Table 7 shows some of the minimum values of the surface roughness predicted by the GA program with respect to input machining ranges, and Table 8 shows the optimum machining conditions for the corresponding minimum values of the surface roughness shown in Table 7. The MRR given in Table 8 was calculated bywhere f is the table feed (mm/min), aa is the axial depth of cut (20 mm) and ar is the radial depth of cut (1 mm).It can be concluded from the optimization results of the GA program that it is possible toselect a combination of cutting speed, feed rate, radial rake angle and nose radius for achieving the best possible surface finish giving a reasonably good material removal rate. This GA program provides optimum machining conditions for the corresponding given minimum values of the surface roughness. The application of the genetic algorithmic approach to obtain optimal machining conditions will be quite useful at the computer aided process planning (CAPP) stage in the production of high quality goods with tight tolerances by a variety of machining operations, and in the adaptive control of automated machine tools. With the known boundaries of surface roughness and machining conditions, machining could be performed with a relatively high rate of success with the selected machining conditions.6 ConclusionsThe investigations of this study indicate that the parameters cutting speed, feed, radial rake angle and nose radius are the primary actors influencing the surface roughness of medium carbon steel uring end milling. The approach presented in this paper provides n impetus to develop analytical models, based on experimental results for obtaining a surface roughness model using the response surface methodology. By incorporating the cutter geometry in the model, the validity of the model has been enhanced. The optimization of this model using genetic algorithms has resulted in a fairly useful method of obtaining machining parameters in order to obtain the best possible surface quality.中文翻译选择最佳工具,几何形状和切削条件利用表面粗糙度预测模型端铣摘要:刀具几何形状对工件表面质量产生的影响是人所共知的,因此,任何成型面端铣设计应包括刀具的几何形状。
机械类毕业设计外文文献翻译
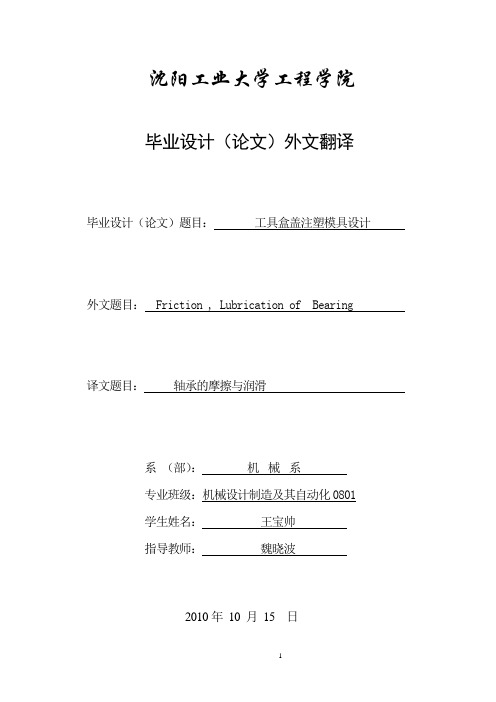
沈阳工业大学工程学院毕业设计(论文)外文翻译毕业设计(论文)题目:工具盒盖注塑模具设计外文题目:Friction , Lubrication of Bearing 译文题目:轴承的摩擦与润滑系(部):机械系专业班级:机械设计制造及其自动化0801学生姓名:王宝帅指导教师:魏晓波2010年10 月15 日外文文献原文:Friction , Lubrication of BearingIn many of the problem thus far , the student has been asked to disregard or neglect friction . Actually , friction is present to some degree whenever two parts are in contact and move on each other. The term friction refers to the resistance of two or more parts to movement.Friction is harmful or valuable depending upon where it occurs. friction is necessary for fastening devices such as screws and rivets which depend upon friction to hold the fastener and the parts together. Belt drivers, brakes, and tires are additional applications where friction is necessary.The friction of moving parts in a machine is harmful because it reduces the mechanical advantage of the device. The heat produced by friction is lost energy because no work takes place. Also , greater power is required to overcome the increased friction. Heat is destructive in that it causes expansion. Expansion may cause a bearing or sliding surface to fit tighter. If a great enough pressure builds up because made from low temperature materials may melt.There are three types of friction which must be overcome in moving parts: (1)starting, (2)sliding, and(3)rolling. Starting friction is the friction between two solids that tend to resist movement. When two parts are at a state of rest, the surface irregularities of both parts tend to interlock and form a wedging action. To produce motion in these parts, the wedge-shaped peaks and valleys of the stationary surfaces must be made to slide out and over each other. The rougher the two surfaces, the greater is starting friction resulting from their movement .Since there is usually no fixed pattern between the peaks and valleys of two mating parts, the irregularities do not interlock once the parts are in motion but slide over each other. The friction of the two surfaces is known as sliding friction. As shown in figure ,starting friction is always greater than sliding friction .Rolling friction occurs when roller devces are subjected to tremendous stress which cause the parts to change shape or deform. Under these conditions, the material in front of a roller tends to pile up and forces the object to roll slightly uphill. This changing of shape , known as deformation, causes a movement of molecules. As a result ,heat is produced from the added energy required to keep the parts turning and overcome friction.The friction caused by the wedging action of surface irregularities can be overcomepartly by the precision machining of the surfaces. However, even these smooth surfaces may require the use of a substance between them to reduce the friction still more. This substance is usually a lubricant which provides a fine, thin oil film. The film keeps the surfaces apart and prevents the cohesive forces of the surfaces from coming in close contact and producing heat .Another way to reduce friction is to use different materials for the bearing surfaces and rotating parts. This explains why bronze bearings, soft alloys, and copper and tin iolite bearings are used with both soft and hardened steel shaft. The iolite bearing is porous. Thus, when the bearing is dipped in oil, capillary action carries the oil through the spaces of the bearing. This type of bearing carries its own lubricant to the points where the pressures are the greatest.Moving parts are lubricated to reduce friction, wear, and heat. The most commonly used lubricants are oils, greases, and graphite compounds. Each lubricant serves a different purpose. The conditions under which two moving surfaces are to work determine the type of lubricant to be used and the system selected for distributing the lubricant.On slow moving parts with a minimum of pressure, an oil groove is usually sufficient to distribute the required quantity of lubricant to the surfaces moving on each other .A second common method of lubrication is the splash system in which parts moving in a reservoir of lubricant pick up sufficient oil which is then distributed to all moving parts during each cycle. This system is used in the crankcase of lawn-mower engines to lubricate the crankshaft, connecting rod ,and parts of the piston.A lubrication system commonly used in industrial plants is the pressure system. In this system, a pump on a machine carries the lubricant to all of the bearing surfaces at a constant rate and quantity.There are numerous other systems of lubrication and a considerable number of lubricants available for any given set of operating conditions. Modern industry pays greater attention to the use of the proper lubricants than at previous time because of the increased speeds, pressures, and operating demands placed on equipment and devices.Although one of the main purposes of lubrication is reduce friction, any substance-liquid , solid , or gaseous-capable of controlling friction and wear between sliding surfaces can be classed as a lubricant.Varieties of lubricationUnlubricated sliding. Metals that have been carefully treated to remove all foreign materials seize and weld to one another when slid together. In the absence of such a highdegree of cleanliness, adsorbed gases, water vapor ,oxides, and contaminants reduce frictio9n and the tendency to seize but usually result in severe wear; this is called “unlubricated ”or dry sliding.Fluid-film lubrication. Interposing a fluid film that completely separates the sliding surfaces results in fluid-film lubrication. The fluid may be introduced intentionally as the oil in the main bearing of an automobile, or unintentionally, as in the case of water between a smooth tuber tire and a wet pavement. Although the fluid is usually a liquid such as oil, water, and a wide range of other materials, it may also be a gas. The gas most commonly employed is air.Boundary lubrication. A condition that lies between unlubricated sliding and fluid-film lubrication is referred to as boundary lubrication, also defined as that condition of lubrication in which the friction between surfaces is determined by the properties of the surfaces and properties of the lubricant other than viscosity. Boundary lubrication encompasses a significant portion of lubrication phenomena and commonly occurs during the starting and stopping off machines.Solid lubrication. Solid such as graphite and molybdenum disulfide are widely used when normal lubricants do not possess sufficient resistance to load or temperature extremes. But lubricants need not take only such familiar forms as fats, powders, and gases; even some metals commonly serve as sliding surfaces in some sophisticated machines.Function of lubricantsAlthough a lubricant primarily controls friction and ordinarily does perform numerous other functions, which vary with the application and usually are interrelated .Friction control. The amount and character of the lubricant made available to sliding surfaces have a profound effect upon the friction that is encountered. For example, disregarding such related factors as heat and wear but considering friction alone between the same surfaces with on lubricant. Under fluid-film conditions, friction is encountered. In a great range of viscosities and thus can satisfy a broad spectrum of functional requirements. Under boundary lubrication conditions , the effect of viscosity on friction becomes less significant than the chemical nature of the lubricant.Wear control. wear occurs on lubricated surfaces by abrasion, corrosion ,and solid-to-solid contact wear by providing a film that increases the distance between the sliding surfaces ,thereby lessening the damage by abrasive contaminants and surfaceasperities.Temperature control. Lubricants assist in controlling corrosion of the surfaces themselves is twofold. When machinery is idle, the lubricant acts as a preservative. When machinery is in use, the lubricant controls corrosion by coating lubricated parts with a protective film that may contain additives to neutralize corrosive materials. The ability of a lubricant to control corrosion is directly relatly to the thickness of the lubricant film remaining on the metal surfaces and the chermical composition of the lubricant.Other functionsLubrication are frequently used for purposes other than the reduction of friction. Some of these applications are described below.Power transmission. Lubricants are widely employed as hydraulic fluids in fluid transmission devices.Insulation. In specialized applications such as transformers and switchgear , lubricants with high dielectric constants acts as electrical insulators. For maximum insulating properties, a lubricant must be kept free of contaminants and water.Shock dampening. Lubricants act as shock-dampening fluids in energy transferring devices such as shock absorbers and around machine parts such as gears that are subjected to high intermittent loads.Sealing. Lubricating grease frequently performs the special function of forming a seal to retain lubricants or to exclude contaminants.The object of lubrication is to reduce friction ,wear , and heating of machine pars which move relative to each other. A lubricant is any substance which, when inserted between the moving surfaces, accomplishes these purposes. Most lubricants areliquids(such as mineral oil, silicone fluids, and water),but they may be solid for use in dry bearings, greases for use in rolling element bearing, or gases(such as air) for use in gas bearings. The physical and chemical interaction between the lubricant and lubricating surfaces must be understood in order to provide the machine elements with satisfactory life.The understanding of boundary lubrication is normally attributed to hardy and doubleday , who found the extrememly thin films adhering to surfaces were often sufficient to assist relative sliding. They concluded that under such circumstances the chemical。
机械专业毕业设计外文翻译10
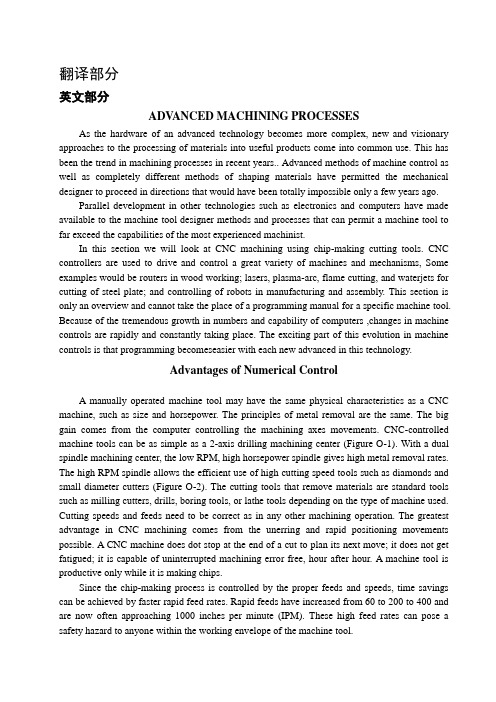
翻译部分英文部分ADV ANCED MACHINING PROCESSESAs the hardware of an advanced technology becomes more complex, new and visionary approaches to the processing of materials into useful products come into common use. This has been the trend in machining processes in recent years.. Advanced methods of machine control as well as completely different methods of shaping materials have permitted the mechanical designer to proceed in directions that would have been totally impossible only a few years ago.Parallel development in other technologies such as electronics and computers have made available to the machine tool designer methods and processes that can permit a machine tool to far exceed the capabilities of the most experienced machinist.In this section we will look at CNC machining using chip-making cutting tools. CNC controllers are used to drive and control a great variety of machines and mechanisms, Some examples would be routers in wood working; lasers, plasma-arc, flame cutting, and waterjets for cutting of steel plate; and controlling of robots in manufacturing and assembly. This section is only an overview and cannot take the place of a programming manual for a specific machine tool. Because of the tremendous growth in numbers and capability of comp uters ,changes in machine controls are rapidly and constantly taking place. The exciting part of this evolution in machine controls is that programming becomeseasier with each new advanced in this technology.Advantages of Numerical ControlA manually operated machine tool may have the same physical characteristics as a CNC machine, such as size and horsepower. The principles of metal removal are the same. The big gain comes from the computer controlling the machining axes movements. CNC-controlled machine tools can be as simple as a 2-axis drilling machining center (Figure O-1). With a dual spindle machining center, the low RPM, high horsepower spindle gives high metal removal rates. The high RPM spindle allows the efficient use of high cutting speed tools such as diamonds and small diameter cutters (Figure O-2). The cutting tools that remove materials are standard tools such as milling cutters, drills, boring tools, or lathe tools depending on the type of machine used. Cutting speeds and feeds need to be correct as in any other machining operation. The greatest advantage in CNC machining comes from the unerring and rapid positioning movements possible. A CNC machine does dot stop at the end of a cut to plan its next move; it does not get fatigued; it is capable of uninterrupted machining error free, hour after hour. A machine tool is productive only while it is making chips.Since the chip-making process is controlled by the proper feeds and speeds, time savings can be achieved by faster rapid feed rates. Rapid feeds have increased from 60 to 200 to 400 and are now often approaching 1000 inches per minute (IPM). These high feed rates can pose a safety hazard to anyone within the working envelope of the machine tool.Complex contoured shapes were extremely difficult to product prior to CNC machining .CNC has made the machining of these shapes economically feasible. Design changes on a part are relatively easy to make by changing the program that directs the machine tool.A CNC machine produces parts with high dimensional accuracy and close tolerances without taking extra time or special precautions, CNC machines generally need less complex work-holding fixtures, which saves time by getting the parts machined sooner. Once a program is ready and production parts, each part will take exactly the same amount of time as the previous one. This repeatability allows for a very precise control of production costs. Another advantage of CNC machining is the elimination of large inventories; parts can be machined as needs .In conventional production often a great number of parts must be made at the same time to be cost effective. With CNC even one piece can be machined economically .In many instances, a CNC machine can perform in one setup the same operations that would require several conventional machines.With modern CNC machine tools a trained machinist can program and product even a single part economically .CNC machine tools are used in small and large machining facilities and range in size from tabletop models to huge machining centers. In a facility with many CNC tools, programming is usually done by CNC programmers away from the CNC tools. The machine control unit (MCU) on the machine is then used mostly for small program changes or corrections. Manufacturing with CNC tools usually requires three categories of persons. The first is the programmer, who is responsible for developing machine-ready code. The next person involved is the setup person, who loads the raw stork into the MCU, checks that the co rrect tools are loaded, and makes the first part. The third person is the machine and unloads the finished parts. In a small company, one person is expected to perform all three of these tasks.CNC controls are generally divided into two basic categories. One uses a ward address format with coded inputs such as G and M codes. The other users a conversational input; conversational input is also called user-friendly or prompted input. Later in this section examples of each of these programming formats in machining applications will be describes.CAM and CNCCAM systems have changed the job of the CNC programmer from one manually producing CNC code to one maximizing the output of CNC machines. Since CNC machine tools are made by a great number of manufacturers, many different CNC control units are in use. Control units from different manufacturers use a variety of program formats and codes. Many CNC code words are identical for different controllers, but a great number vary from one to another.To produce an identical part on CNC machine tools with different controllers such as one by FANCU, OKUMA or DYNAPATH, would require completely different CNC codes. Each manufacturer is constantly improving and updating its CNC controllers. These improvements often include additional code words plus changes in how the existing code works.A CAM systems allows the CNC programmer to concentrate on the creation of an efficient machining process, rather then relearning changed code formats. A CNC programmer looks atthe print of a part and then plans the sequence of machining operations necessary to make it (Figure O-3). This plan includes everything, from the selection of possible CNC machine tools, to which tooling to use, to how the part is held while machining takes place. The CNC programmer has to have a thorough understanding of all the capacities and limitations of the CNC machine tools that a program is to be made for. Machine specifications such as horsepower, maximum spindle speeds, workpiece weight and size limitations, and tool changer capacity are just some of the considerations that affect programming.Another area of major importance to the programmer is the knowledge of machining processes. An example would be the selection of the surface finish requirement specified in the part print. The sequence of machining processes is critical to obtain acceptable results. Cutting tool limitations have to be considered and this requires knowledge of cutting tool materials, tool types, and application recommendations.A good programmer will spend a considerable amount of time in researching the rapidly growing volume of new and improved tools and tool materials. Often the tool that was on the cutting edge of technology just two years ago is now obsolete. Information on new tools can come from catalogs or tool manufacturers' tooling engineers. Help in tool selection or optimum tool working conditions can also be obtained from tool manufacturer software. Examples would be Kennametal's "TOOLPRO", software designed to help select the best tool grade, speed, and feed rates for different work materials in turning application. Another very important feature of "TOOLPRO" is the display of the horsepower requirement for each machining selection. This allow the programmer to select a combination of cutting speed, feed rate, and depth of cut that equals the machine's maximum horsepower for roughing cuts. For a finishing cut, the smallest diameter of the part being machined is selected and then the cutting speed varied until the RPM is equal to the maximum RPM of the machine. This helps in maximizing machining efficiency. Knowing the horsepower requirement for a cut is critical if more than one tool is cutting at the same time.Software for a machining center application would be Ingersoll Tool Company's "Actual Chip Thickness", a program used to calculate the chip thickness in relation to feed-per-tooth for a milling cutter, especially during a shallow finishing cut. Ingersoll's "Rigidity Analysis" software ealculates tool deflection for end mills as a function of tool stiffness and tool force.To this point we looked at some general qualifications that a programmer should possess. Now we examine how a CAM system works. Point Control Company's SmartCam system uses the following approach. First, the programmer makes a mental model of the part to be machined. This includes the kind of machining to be performed-turning or milling. Then the part print is studied to develop a machining sequence, roughing and finishing cuts, drilling, tapping, and boring operations. What work-holding device is to be used, a vise or fixture or clamps? After these considerations, computer input can be started. First comes the creation of a JOBPLAN. This JOBPLAN consists of entries such as inch or metric units, machine type, part ID, type of workpiece material, setup notes, and a description of the required tools.This line of information describes the tool by number, type, and size and includes theappropriate cutting speed and feed rate. After all the selected tools are entered, the file is saved.The second programming step is the making of the part. This represents a graphic modeling of the projected machining operation. After selecting a tool from the prepared JOBPLAN, parameters for the cutting operation are entered. For a drill, once the coordinate location of the hole and the depth are given, a circle appears on that spot. If the location is incorrect, the UNDO command erases this entry and allows you to give new values for this operation. When an end mill is being used, cutting movements (toolpath) are usually defined as lines and arcs. As a line is programmed, the toolpath is graphically displayed and errors can be corrected instantly.At any time during programming, the command SHOWPATH will show the actual toolpath for each of the programmed tools. The tools will be displayed in the sequence in which they will be used during actual machining. If the sequence of a tool movement needs to be changed, a few keystrokes will to that.Sometimes in CAM the programming sequence is different from the actual machining order. An example would be the machining of a pocket in a part. With CAM, the finished pocket outline is programmed first, then this outline is used to define the ro ughing cuts to machine the pocket. The roughing cuts are computer generated from inputs such as depth and width of cut and how much material to leave for the finish cut. Different roughing patterns can be tried out to allow the programmer to select the most efllcient one for the actual machining cuts. Since each tool is represented by a different color, it is easy to observe the toolpath made by each one.A CAM system lets the programmer view the graphics model from varying angles, such as a top, front, side, or isometric view. A toolpath that looks correct from a top view, may show from a front view that the depth of the cutting tool is incorrect. Changes can easily be made and seen immediately.When the toolpath and the sequence of operations are satisfactory, machine ready code has to be made. This is as easy as specifying the CNC machine that is to be used to machine the part. The code generator for that specific CNC machin e during processing accesses four different files. The JOBPLAN file for the tool information and the GRAPHICE file for the toolpath and cutting sequence. It also uses the MACHINE DEFINE file which defines the CNC code words for that specific machine. This file also supplies data for maximum feed rates, RPM, toolchange times, and so on. The fourth file taking part in the code generating process is the TEMPLATE file. This file acts like a ruler that produces the CNC code with all of its parts in the right place and sequence. When the code generation is complete, a projected machining time is displayed. This time is calculated from values such as feed rates and distances traveled, noncutting movements at maximum feed rates between points, tool change times, and so on. The projected machining time can be revised by changing tooling to allow for higher metal removal rates or creating a more efficient toolpath. This display of total time required can also be used to estimate production costs. If more then one CNC machine tool is available to machine this part, making code and comparing the machining time may show that one machine is more efficient than the others.CAD/CAMAnother method of creating toolpath is with the use of a Computer-aided Drafting (CAD) file. Most machine drawings are created using computers with the description and part geometry stored in the computer database. SmartCAM, though its CAM CONNECTION, will read a CAD file and transfer its geometry represents the part profile, holes, and so on. The programmer still needs to prepare a JOBPLAN with all the necessary tools, but instead of programming a profile line by line, now only a tool has to be assigned to an existing profile. Again, using the SHOWPA TH function will display the toolpath for each tool and their sequence. Constant research and developments in CAD/CAM interaction will change how they work with each other. Some CAD and CAM programs, if loaded on the same computer, make it possible to switch between the two with a few keystrokes, designing and programming at the same time.The work area around the machine needs to be kept clean and clear of obstructions to prevent slipping or tripping. Machine surfaces should not be used as worktables. Use proper lifting methods to handle heavy workpieces, fixtures, or heavy cutting tools. Make measurements only when the spindle has come to a complete standstill. Chips should never be handled with bare hands.Before starting the machine make sure that the work-holding device and the workpiece are securely fastened. When changing cutting tools, protect the workpiece being machined from damage, and protect your hands from sharp cutting edges. Use only sharp cutting tools. Check that cutting tools are installed correctly and securely.Do not operate any machine controls unless you understand their function and what the y will do.The Early Development Of Numerically Controlled Machine ToolsThe highly sophisticated CNC machine tools of today, in the vast and diverse range found throughout the field of manufacturing processing, started from very humble beginnings in a number of the major industrialized countries. Some of the earliest research and development work in this field was completed in USA and a mention will be made of the UK's contribution to this numerical control development.A major problem occurred just after the Second World War, in that progress in all areas of military and commercial development had been so rapid that the levels of automation and accuracy required by the modern industrialized world could not be attained from the lab our intensive machines in use at that time. The question was how to overcome the disadvantages of conventional plant and current manning levels. It is generally ackonwledged that the earliest work into numerical control was the study commissioned in 1947 by the US governme nt. The study's conclusion was that the metal cutting industry throughout the entire country could not copy with the demands of the American Air Force, let alone the rest of industry! As a direct result of the survey, the US Air Force contracted the Persons Corporation to see if they could develop a flexible, dynamic, manufacturing system which would maximize productivity. TheMassachusetts Institute of Technology (MIT) was sub-contracted into this research and development by the Parsons Corporation, during the period 1949-1951,and jointly they developed the first control system which could be adapted to a wide range of machine tools. The Cincinnati Machine Tool Company converted one of their standard 28 inch "Hydro-Tel" milling machines or a three-axis automatic milling made use of a servo-mechanism for the drive system on the axes. This machine made use of a servomechanism for the drive system on the axes, which controlled the table positioning, cross-slide and spindle head. The machine cab be classified as the first truly three axis continuous path machine tool and it was able to generate a required shape, or curve, by simultaneous slide way motions, if necessary.At about the same times as these American advances in machine tool control were taking Place, Alfred Herbert Limited in the United Kingdom had their first Mutinous path control system which became available in 1956.Over the next few years in both the USA and Europe, further development work occurred. These early numerical control developments were principally for the aerospace industry, where it was necessary to cut complex geometric shapes such as airframe components and turbine blades. In parallel with this development of sophisticated control systems for aerospace requirements, a point-to-point controller was developed for more general machining applications. These less sophisticated point-to-point machines were considerably cheaper than their more complex continuous path cousins and were used when only positional accuracy was necessary. As an example of point-to-point motion on a machine tool for drilling operations, the typical movement might be fast traverse of the work piece under the drill's position-after drilling the hole, anther rapid move takes place to the next hole's position-after retraction of the drill. Of course, the rapid motion of the slideways could be achieved by each axis in a sequential and independent manner, or simultaneously. If a separate control was utilisec for each axis, the former method of table travel was less esse ntial to avoid any backlash in the system to obtain the required degree of positional accuracy and so it was necessary that the approach direction to the next point was always the same.The earliest examples of these cheaper point-to-point machines usually did not use recalculating ball screws; this meant that the motions would be sluggish, and sliderways would inevitably suffer from backlash, but more will be said about this topic later in the chapter.The early NC machines were, in the main, based upon a modified milling machine with this concept of control being utilized on turning, punching, grinding and a whole host of other machine tools later. Towards the end of the 1950s,hydrostatic slideways were often incorporated for machine tools of highly precision, which to sonic extent overcame the section problem associated with conventional slideway response, whiles averaging-out slideway inaccuracy brought about a much increased preasion in the machine tool and improved their control characteristics allows "concept of the machining center" was the product of this early work, as it allowed the machine to manufacture a range of components using a wide variety of machining processes at a single set-up, without transfer of workpieces to other variety machine tools. A machining center differed conceptually in its design from that of a milling machine, In that thecutting tools could be changed automatically by the transfer machanism, or selector, from the magazine to spindle, or vice versa.In this ductively and the automatic tool changing feature enabled the machining center to productively and efficiently machine a range of components, by replacing old tools for new, or reselecting the next cutter whilst the current machining process is in cycle.In the mid 1960s,a UK company, Molins, introduced their unique "System 24" which was meant represent the ability of a system to machine for 24 hours per day. It could be thought of as a "machining complex" which allowed a series of NC single purpose machine tools to be linked by a computerized conveyor system. This conveyor allowed the work pieces to be palletized and then directed to as machine tool as necessary. This was an early, but admirable, attempt at a form of Flexible manufacturing System concept, but was unfortunately doomed to failure. Its principal weakness was that only a small proportion of component varieties could be machine at any instant and that even fewer work pieces required the same operations to be performed on them. These factors meant that the utilization level was low, coupled to the fact that the machine tools were expensive and allowed frequent production bottlenecks of work-in-progress to arise, which further slowed down the whole operation.The early to mid-1970s was a time of revolutionary in the area of machine tool controller development, when the term computerized numerical control (CNC) became a reality. This new breed of controllers gave a company the ability to change work piece geometries, together with programs, easily with the minimum of development and lead time, allowing it to be economically viable to machine small batches, or even one-off successfully. The dream of allowing a computerized numerical controller the flexibility and ease of program editing in a production environment became a reality when two ralated factors occurred.These were:the development of integrated circuits, which reduces electronics circuit size, giving better maintenance and allowing more standardization of desing; that general purpose computers were reduced in size coupled to the fact that their cost of production had fallen considerably.The multipie benefits of cheaper electorics with greater reliability have result in the CNC fitted to the machine tools today, with the power and sophistication progtessing considerably in the last few years, allowing an almost artificial intelligence(AI) to the latest systems. Over the years, the machine tools builders have produced a large diversity in the range of applications of CNC and just some of those development will be reviewed in V olume Ⅲ。
毕业设计英文翻译
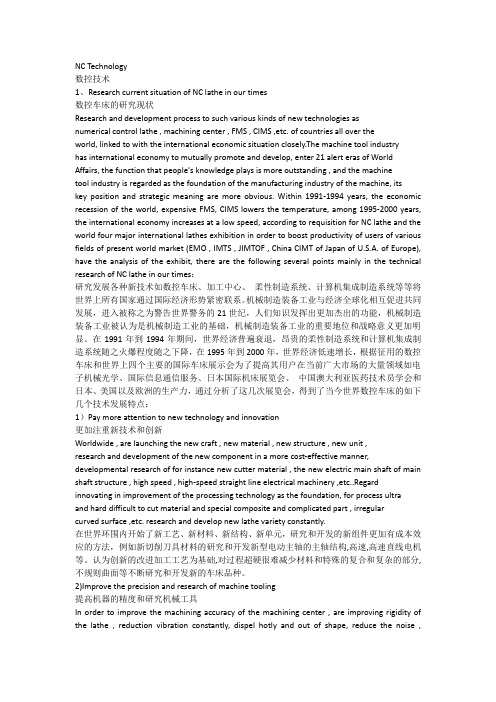
NC Technology数控技术1、Research current situation of NC lathe in our times数控车床的研究现状Research and development process to such various kinds of new technologies asnumerical control lathe , machining center , FMS , CIMS ,etc. of countries all over theworld, linked to with the international economic situation closely.The machine tool industryhas international economy to mutually promote and develop, enter 21 alert eras of World Affairs, the function that people's knowledge plays is more outstanding , and the machinetool industry is regarded as the foundation of the manufacturing industry of the machine, itskey position and strategic meaning are more obvious. Within 1991-1994 years, the economic recession of the world, expensive FMS, CIMS lowers the temperature, among 1995-2000 years, the international economy increases at a low speed, according to requisition for NC lathe and the world four major international lathes exhibition in order to boost productivity of users of various fields of present world market (EMO , IMTS , JIMTOF , China CIMT of Japan of U.S.A. of Europe), have the analysis of the exhibit, there are the following several points mainly in the technical research of NC lathe in our times:研究发展各种新技术如数控车床、加工中心、柔性制造系统、计算机集成制造系统等等将世界上所有国家通过国际经济形势紧密联系。
机械设计外文文献翻译、中英文翻译

机械设计外文文献翻译、中英文翻译unavailable。
The first step in the design process is to define the problem and XXX are defined。
the designer can begin toXXX evaluated。
and the best one is XXX。
XXX.Mechanical DesignA XXX machines include engines。
turbines。
vehicles。
hoists。
printing presses。
washing machines。
and XXX and methods of design that apply to XXXXXX。
cams。
valves。
vessels。
and mixers.Design ProcessThe design process begins with a real need。
Existing apparatus may require XXX。
efficiency。
weight。
speed。
or cost。
while new apparatus may be XXX。
To start。
the designer must define the problem and XXX。
ideas and concepts are generated。
evaluated。
and refined until the best one is XXX。
XXX.XXX。
assembly。
XXX.During the preliminary design stage。
it is important to allow design XXX if some ideas may seem impractical。
they can be corrected early on in the design process。
数控编程工艺类外文文献翻译、中英文翻译、外文翻译

Numerical ControlOne of the most fundamental concepts in the area of advanced manufacturing technologies is numerical control (NC).Prior to the advent of NC, all machine tools were manual operated and controlled. Among the many limitations associated with manual control machine tools, perhaps none is more prominent than the limitation of operator skills. With manual control, the quality of the product is directly related to and limited to the skills of the operator . Numerical control represents the first major step away from human control of machine tools.Numerical control means the control of machine tools and other manufacturing systems though the use of prerecorded, written symbolic instructions. Rather than operating a machine tool, an NC technician writes a program that issues operational instructions to the machine tool, For a machine tool to be numerically controlled , it must be interfaced with a device for accepting and decoding the p2ogrammed instructions, known as a reader.Numerical control was developed to overcome the limitation of human operator , and it has done so . Numerical control machines are more accurate than manually operated machines , they can produce parts more uniformly , they are faster, and the long-run tooling costs are lower . The development of NC led to the development of several other innovations in manufacturing technology:1.Electrical discharge machining.ser cutting.3.Electron beam welding.Numerical control has also made machine tools more versatile than their manually operated predecessors. An NC machine tool can automatically produce a wide variety of par4s , each involving an assortment of undertake the production of products that would not have been feasible from an economic perspective using manually controlled machine tools and processes.Like so many advanced technologies , NC was born in the laboratories of the Massachusetts Institute of Technology . The concept of NC was developed in the early 1950s with funding provided by the U.S Air Force .In its earliest stages , NC machines were able to make straight cuts efficiently and effectively.However ,curved paths were a problem because the machine tool had to be programmed to undertake a series of horizontal and vertical steps to produce a curve. The shorter is the straight lines making up the step ,the smoother is 4he curve . Each line segmentin the steps had to be calculated.This problem led to the development in 1959 of the Automatically Programmed Tools (APT) language for NC that uses statements similar to English language to define the part geometry, describe the cutting tool configuration, and specify the necessary motions. The development of the APT language was a major step forward in the further development of NC technology. The original NC system were vastly different from those used punched paper , which was later to replaced by magnetic plastic tape .A tape reader was used to interpret the instructions written on the tape for the machine .Together, all /f this represented giant step forward in the control of machine tools . However ,there were a number of problems with NC at this point in its development.A major problem was the fragility of the punched paper tape medium . It was common for the paper containing the programmed instructions to break or tear during a machining process, This problem was exacerbated by the fact that each successive time a part was produced on a machine tool, the paper tape carrying the programmed instructions had to rerun thought the reader . If it was necessary to produce 100 copies of a given part , it was also necessary to run the paper tape thought the reader 100 separate times . Fragile paper tapes simply could not withstand the rigors of shop floor environment and this kind of repeated use.This led to the development of a special magnetic tape . Whereas the paper tape carried the programmed instructions as a series of holes punched in the tape , theThis most important of these was that it was difficult or impossible to change the instructions entered on the tape . To make even the most minor adjustments in a program of instructions, it was necessary to interrupt machining operations and make a new tape. It was also still necessary to run the tape thought the reader as many times as there were parts to be produced . Fortunately, computer technology become a reality and soon solved the problems of NC, associated with punched paper and plastic tape.The development of a concept known as numerical control (DNC) solve the paper and plastic tape problems associated with numerical control by simply eliminating tape as the medium for carrying the programmed instructions . In direct numerical control, machine tools are tied, via a data transmission link, to a host computer and fed to the machine tool as needed via the data transmission linkage. Direct numerical control represented a major step forward over punched tape and plastic tape. However ,it is subject to the same limitation as all technologies that depend on a host computer. When the host computer goes down , the machine tools also experience down time . This problem led to the development of computer numerical control.The development of the microprocessor allowed for the development of programmablelogic controllers (PLC) and microcomputers . These two technologies allowed for the development of computer numerical control (CNC).With CNC , each machine tool has a PLC or a microcomputer that serves the same purpose. This allows programs to be input and stored at each individual machine tool. CNC solved the problems associated downtime of the host computer , but it introduced another problem known as data management . The same program might be loaded on ten different microcomputers with no communication among them. This problem is in the process of being solved by local area networks that connectDigital Signal ProcessorsThere are numerous situations where analog signals to be processed in many ways, like filtering and spectral analysis , Designing analog hardware to perform these functions is possible but has become less and practical, due to increased performance requirements, flexibility needs , and the need to cut down on development/testing time .It is in other words difficult pm design analog hardware analysis of signals.The act of sampling an signal into thehat are specialised for embedded signal processing operations , and such a processor is called a DSP, which stands for Digital Signal Processor . Today there are hundreds of DSP families from as many manufacturers, each one designed for a particular price/performance/usage group. Many of the largest manufacturers, like Texas Instruments and Motorola, offer both specialised DSP‟s for certain fields like motor-control or modems ,and general high-performance DSP‟s that can perform broad ranges of processing tasks. Development kits an` software are also available , and there are companies making software development tools for DSP‟s that allows the programmer to implement complex processing algorithms using simple “drag …n‟ drop” methodologies.DSP‟s more or less fall into two categories depending on the underlying architecture-fixed-point and floating-point. The fixed-point devices generally operate on 16-bit words, while the floating-point devices operate on 32-40 bits floating-point words. Needless to say , the fixed-point devices are generally cheaper . Another important architectural difference is that fixed-point processors tend to have an accumulator architecture, with only one “general purpose” register , making them quite tricky to program and more importantly ,making C-compilers inherently inefficient. Floating-point DSP‟s behave more like common general-purpose CPU‟s ,with register-files.There are thousands of different DSP‟s on the market, and it is difficult task finding the most suitable DSP for a project. The best way is probably to set up a constraint and wishlist, and try to compare the processors from the biggest manufacturers against it.The “big four” manufacturers of DSPs: Texas Instruments, Motorola, AT&T and Analog Devices.Digital-to-analog conversionIn the case of MPEG-Audio decoding , digital compressed data is fed into the DSP which performs the decoding , then the decoded samples have to be converted back into the analog domain , and the resulting signal fed an amplifier or similar audio equipment . This digital to analog conversion (DCA) is performed by a circuit with the same name & Different DCA‟s provide different performance and quality , as measured by THD (Total harmonic distortion ), number of bits, linearity , speed, filter characteristics and other things.The TMS320 family DQP of Texas InstrumentsThe TLS320family consists of fixed-point, floating-point, multiprocessor digital signal processors (D[Ps) , and foxed-point DSP controllers. TMS320 DSP have an architecture designed specifically for real-time signal processing . The‟ F/C240 is a number of the‟C2000DSP platform , and is optimized for control applications. The‟C24x series of DSP controllers combines this real-time processing capability with controller peripherals to create an ideal solution for control system applications. The following characteristics make the TMS320 family the right choice for a wide range of processing applications:--- Very flexible instruction set--- Inherent operational flexibility---High-speed performance---Innovative parallel architecture---Cost effectivenessDevices within a generation of the TMS320 family have the same CPU structure but different on-chip memory and peripheral configurations. Spin-off devices use new combinations of On-chip memory and peripherals to satisfy a wide range of needs in the worldwide electronics market. By integrating memory and peripherals onto a single chip , TMS320 devices reduce system costs and save circuit board space.The 16-bit ,fixed-point DSP core of the …C24x device s provides analog designers a digital solution that does not sacrifice the precision and performance of their system performance can be enhanced through the use of advanced control algorithms for techniques such as adaptive control , Kalman filtering , and state control. The …C24x DSP controller offer reliability and programmability . Analog control systems, on the other hand ,are hardwired solutions and can experience performance degradation due to aging , component tolerance, and drift.The high-speed central processing unit (CPU) allows the digital designer to process algorithms in real time rather than approximate results with look-up tables. The instruction set of these DSP controllers, which incorporates both signal processing instructions andgeneral-purpose control functions, coupled with the extensive development time and provides the same ease of use as traditional 8-and 16-bit microcontrollers. The instruction set also allows you to retain your software investment when moving from other general-pur pose…C2xx generation ,source code compatible with the‟C2x generation , and upwardly source code compatible with the …C5x generation of DSPs from Texas Instruments.The …C24x architecture is also well-suited for processing control signals. It uses a 16-bit word length along with 32-bit registers for storing intermediate results, and has two hardware shifters available to scale numbers independently of the CPU . This combination minimizes quantization and truncation errors, and increases p2ocessing power for additional functions. Such functions might include a notch filter that could cancel mechanical resonances in a system or an estimation technique that could eliminate state sensors in a system.The …C24xDSP controllers take advantage of an set of peripheral functions that allow Texas Instruments to quickly configure various series members for different price/ performance points or for application optimization.This library of both digital and mixed-signal peripherals includes:---Timers---Serial communications ports (SCI,SPI)---Analog-to-digital converters(ADC)---Event manager---System protection, such as low-voltage and watchdog timerThe DSP controller peripheral library is continually growing and changing to suit the of tomorrow‟s embedded control mark etplace.The TMS320F/C240 is the first standard device introduced in the …24x series of DSP controllers. It sets the standard for a single-chip digital motor controller. The …240 can execute 20 MIPS. Almost all instructions are executed in a simple cycle of 50 ns . This high performance allows real-time execution of very comple8 control algorithms, such as adaptive control and Kalman filters. Very high sampling rates can also be used to minimize loop delays.The … 240 has the architectural features necessar y for high-speed signal processing and digital control functions, and it has the peripherals needed to provide a single-chip solution for motor control applications. The …240 is manufactured using submicron CMOS technology, achieving a log power dissipation rating . Also included are several power-down modes for further power savings. Some applications that benefit from the advanced processing power of the …240 include:---Industrial motor drives---Power inverters and controllers---Automotive systems, such as electronic power steering , antilock brakes, and climate control---Appliance and HV AC blower/ compressor motor controls---Printers, copiers, and other office products---Tape drives, magnetic optical drives, and other mass storage products---Robotic and CNC milling machinesTo function as a system manager, a DSP must have robust on-chip I/O and other peripherals. The event manager of the …240 is unlike any other available on a DSP . This application-optimized peripheral unit , coupled with the high performance DSP core, enables the use of advanced control techniques for high-precision and high-efficiency full variable-speed control of all motor types. Include in the event manager are special pulse-width modulation (PWM) generation functions, such as a programmable dead-band function and a space vector PWM state machine for 3-phase motors that provides state-of-the-art maximum efficiency in the switching of power transistors.There independent up down timers, each with it‟s own compare register, supp ort the generation of asymmetric (noncentered) as well as symmetric (centered) PWM waveforms.Open-Loop and Closed-Loop ControlOpen-loop Control SystemsThe word automatic implies that there is a certain amount of sophistication in the control system. By automatic, it generally means That the system is usually capable of adapting to a variety of operating conditions and is able to respond to a class of inputs satisfactorily . However , not any type of control system has the automatic feature. Usually , the automatic feature is achieved by feed.g the feedback structure, it is called an open-loop system , which is the simplest and most economical type of control system.inaccuracy lies in the fact that one may not know the exact characteristics of the further ,which has a definite bearing on the indoor temperature. This alco points to an important disadvantage of the performance of an open -loop control system, in that the system is not capable of adapting to variations in environmental conitions or to external disturbances. In the case of the furnace control, perhaps an experienced person can provide control for a certain desired temperature in the house; but id the doors or windows are opened or closed intermittently during the operating period, the final temperature inside the house will not be accurately regulated by the open-loop control.An electric washing machine is another typical example of an open-loop system , because the amount of wash time is entirely determined by the judgment and estimation of thehuman operator . A true automatic electric washing machine should have the means of checking the cleanliness of the clothes continuously and turn itsedt off when the desired degised of cleanliness is reached.Closed-Loop Control SystemsWhat is missing in the open-loop control system for more accurate and more adaptable control is a link or feedback from the output to the input of the system . In order to obtain more accurate bontrol, the controlled signal c(t) must be fed back and compared with the reference input , and an actuating signal proportional to the difference of the output and the input must be sent through the system to correct the error. A system with one or more feedback pat(s like that just described is called a closed-loop system. human being are probably the most complex and sophisticated feedback control system in existence. A human being may be considered to be a control system with many inputs and outputs, capable of carrying out highly complex operations.To illustrate the human being as a feedback control system , let us consider that the objective is to reach for an object on aperform the task. The eyes serve as a sensing device which feeds back continuously the position of the hand . The distance between the hand and the object is the error , which is eventually brought to zero as the hand reacher the object. This is a typical example of closed-loop control. However , if one is told to reach for the object and then is blindolded, one can only reach toward the object by estimating its exact position. It isAs anther illustrative example of a closed-loop control system, shows the block diagram of the rudder control system ofThe basic alements and the bloca diagram of a closed-loop control system are shown in fig. In general , the configuration of a feedback control system may not be constrained to that of fig & . In complex systems there may be multitude of feedback loops and element blocks.数控在先进制造技术领域最根本的观念之一是数控(NC)。
轴类毕业设计英文翻译、外文文献翻译
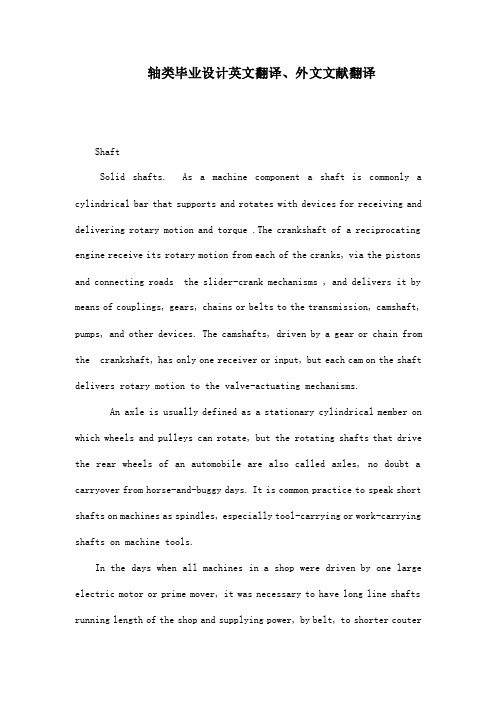
轴类毕业设计英文翻译、外文文献翻译ShaftSolid shafts. As a machine component a shaft is commonly a cylindrical bar that supports and rotates with devices for receiving and delivering rotary motion and torque .The crankshaft of a reciprocating engine receive its rotary motion from each of the cranks, via the pistons and connecting roads the slider-crank mechanisms , and delivers it by means of couplings, gears, chains or belts to the transmission, camshaft, pumps, and other devices. The camshafts, driven by a gear or chain from the crankshaft, has only one receiver or input, but each cam on the shaft delivers rotary motion to the valve-actuating mechanisms.An axle is usually defined as a stationary cylindrical member on which wheels and pulleys can rotate, but the rotating shafts that drive the rear wheels of an automobile are also called axles, no doubt a carryover from horse-and-buggy days. It is common practice to speak short shafts on machines as spindles, especially tool-carrying or work-carrying shafts on machine tools.In the days when all machines in a shop were driven by one large electric motor or prime mover, it was necessary to have long line shafts running length of the shop and supplying power, by belt, to shorter coutershafts, jack shafts, or head shafts. These lineshafts were assembled form separate lengths of shafting clampled together by rigid couplings. Although it is usually more convenient to drive each machine with a separate electric motor, and the present-day trend is in this direction, there are still some oil engine receives its rotary motion from each of the cranks, via the pistons and connecting roads the slider-crank mechanisms , and delivers it by means of couplings, gears, chains or belts to the transmission, camshaft, pumps, and other devices. The camshafts, driven by a gear or chain from the crankshaft, has only one receiver or input, but each cam on the shaft delivers rotary motion to the valve-actuating mechanisms.An axle is usually defined as a stationary cylindrical member on which wheels and pulleys can rotate, but the rotating shafts that drive the rear wheels of an automobile are also called axles, no doubt a carryover from horse-and-buggy days. It is common practice to speak short shafts on machines as spindles, especially tool-carrying or work-carrying shafts on machine tools.In the days when all machines in a shop were driven by one large electric motor or prime mover, it was necessary to have long line shafts running length of the shop and supplying power, by belt, to shorter coutershafts, jackshafts, or headshafts. These line shafts were assembled form separate lengths of shafting clampled together by rigid couplings.Although it is usually more convenient to drive each machine with a separate electric motor, and the present-day trend is in this direction, there are still some situation in which a group drive is more economical.A single-throw crankshaft that could be used in a single-cylinder reciprocating engine or pump is shown in Figure 21. The journals A andB rotate in the main bearings,C is the crankpin that fits in a bearing on the end of the connecting rod and moves on a circle of radius R about the main bearings, whileD andE are the cheeks or webs.The throw R is one half the stroks of the piston, which is connected, by the wrist pin, to the other end of the connecting rod and guided so as to move on a straight path passing throw the axis XX. On a multiple-cylinder engine the crankshaft has multiple throws---eight for a straight eight and for a V-8---arranged in a suitable angular relationship.Stress and strains. In operation, shafts are subjected to a shearing stress, whose magnitude depends on the torque and the dimensions of the cross section. This stress is a measure of resistance that the shaft material offers to the applied torque. All shafts that transmit a torque are subjected to torsional shearing stresses.In addition to the shearing stresses, twisted shafts are also subjected to shearing distortions. The distorted state is usually defined by the angle of tw。
机械加工专业毕业设计外文翻译
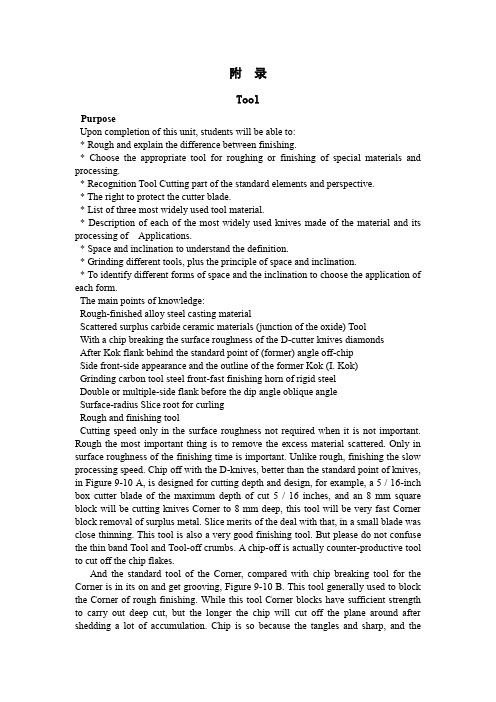
附录ToolPurposeUpon completion of this unit, students will be able to:* Rough and explain the difference between finishing.* Choose the appropriate tool for roughing or finishing of special materials and processing.* Recognition Tool Cutting part of the standard elements and perspective.* The right to protect the cutter blade.* List of three most widely used tool material.* Description of each of the most widely used knives made of the material and its processing of Applications.* Space and inclination to understand the definition.* Grinding different tools, plus the principle of space and inclination.* To identify different forms of space and the inclination to choose the application of each form.The main points of knowledge:Rough-finished alloy steel casting materialScattered surplus carbide ceramic materials (junction of the oxide) ToolWith a chip breaking the surface roughness of the D-cutter knives diamondsAfter Kok flank behind the standard point of (former) angle off-chipSide front-side appearance and the outline of the former Kok (I. Kok)Grinding carbon tool steel front-fast finishing horn of rigid steelDouble or multiple-side flank before the dip angle oblique angleSurface-radius Slice root for curlingRough and finishing toolCutting speed only in the surface roughness not required when it is not important. Rough the most important thing is to remove the excess material scattered. Only in surface roughness of the finishing time is important. Unlike rough, finishing the slow processing speed. Chip off with the D-knives, better than the standard point of knives, in Figure 9-10 A, is designed for cutting depth and design, for example, a 5 / 16-inch box cutter blade of the maximum depth of cut 5 / 16 inches, and an 8 mm square block will be cutting knives Corner to 8 mm deep, this tool will be very fast Corner block removal of surplus metal. Slice merits of the deal with that, in a small blade was close thinning. This tool is also a very good finishing tool. But please do not confuse the thin band Tool and Tool-off crumbs. A chip-off is actually counter-productive tool to cut off the chip flakes.And the standard tool of the Corner, compared with chip breaking tool for the Corner is in its on and get grooving, Figure 9-10 B. This tool generally used to block the Corner of rough finishing. While this tool Corner blocks have sufficient strength to carry out deep cut, but the longer the chip will cut off the plane around after shedding a lot of accumulation. Chip is so because the tangles and sharp, and theoperator is a dangerous, so this is a chip from the need to address the problem. Double, or triple the speed of the feed will help to resolve, but this will require greater horsepower and still easily chip very long. Because of the slow processing, however, this action will be a good tool but also because of the small root radius of the processing will be a smooth surface. Especially when processing grey cast iron especially.Cutting Tools appearanceAppearance, sometimes called the contour of the floor plan is where you see the vision or the top down or look at the surface. Figure 9-11 illustrate some of the most common form, those who could be on the cutting tools and grinding out successfully be used. National Standards in its thread-cutting tool on a tiny plane can be as GB thread, the Anglo-American unity and international standards screw threads. A special tool to outline the thread of the plane is to be ground into the correct size.Tools Corner fixedCorner to a number of knives around the 15 degree angle while the other knives and cutting of the straight. When the mill in Figure 9-12 A and 9-12 B, for example by the space and the inclination, these must factor into consideration in the review. Figure 9-12 B Tool Corner block the angle is zero, compared with 9-12 A map is a heavier cutting tools, and the 9-12 A map will take more heat. The same amount of space in front of the two cases are the same.Tool Corner block component and the angleFigure 9-13 Tool Corner block an integral part of the name, and plans 9-14 point of the name, is the machinery industry standards.Grinding Wheel Tool Corner BlockWhen the cutter is fixed in the middle of Dao, Tool Corner block can not be the grinding. Can not do so for the reasons: because of the large number of Dao and extra weight, making Corner together with the grinding is a clumsy and inefficient way. Too much pressure could be added to round on the sand. This can cause the wheel Benglie wheel or because of overheating and the rift on the Corner Tool damage. There are grinding to the possibility of Dao.GrindingA craftsman in his toolbox, should always be a small pocket lining grinding tool. Alumina lining a grinding tool as carbon tool steel and high speed steel tool tool. The silicon carbide lining grinding tool grinding carbide cutting tools. Cutting Tools should always maintain smooth and sharp edge, so that the life expectancy of long knives and processing the surface smooth.Cutting tool materialsCarbon tool steel cutter Corner block usually contains 1.3 percent to 0.9 percent of carbon. These make use of the cutting tool in their tempering temperature higher than about 400 degrees Fahrenheit (205 degrees Celsius) to 500 degrees Fahrenheit (260 degrees Celsius) remained hardness, depending on the content of carbon. These temperature higher than that of carbon tool steel cutter will be changed soft, and it will be the cutting edge. Damaged. Grinding blades or cutting speed faster when using carbon tool steel cutter will be made of the blue, this will be in the imagination. Toolwill be re-hardening and tempering again. So in a modern processing almost no carbon as a tool steel blade.Low-alloy steel cutting tool in the carbon steel tools added tungsten, cobalt, vanadium alloying elements such as the consequences. These elements and the hardness of high-carbon carbide. Increased tool wear resistance. Alloy tool steel that is to say there will be no hard and fast with hot red when the knife's edge can still continue to use it. Low-alloy steel cutting tool is relatively small for a modern processing.High-speed steel with tungsten of 14 percent to 22 percent, or Containing 1.5% to 6% of the W-Mo (molybdenum which accounted for 6 percent to 91 percent). From high-speed steel tool made of a rigid heat, some high-speed steel also contains cobalt, which is formed of rigid factor. Cobalt containing high-speed steel tool can maintain hardness, more than 1,000 degrees Fahrenheit (or 540 degrees Celsius) blade will become soft and easily damaged. After cooling, the tool will harden. When grinding, you must be careful because of overheating and cold at first, so that profile Benglie Zhucheng a variety of metal alloy materials have a special name called Carbide, such as containing tungsten carbide cobalt chrome. In little or iron carbide. However, its high-speed steel cutting speed than the maximum cutting speed is higher 25 percent to 80 percent. Carbide Tool General for cutting force and the intermittent cutting processing, such as processing Chilled Iron.The past, Carbide Tool is mainly used for processing iron, but now carburizing tool for processing all the metal.Carbide Tool into the body than to the high-speed steel tool or casting - lighter alloy cutting tools, because tend to be used as a tool carbide cutting tools. Pure tungsten, carbon carburizing agent or as a dipping formation of the tungsten carbide, suitable for the cast iron, aluminum, non-iron alloy, plastic material and fiber of the machining. Add tantalum, titanium, molybdenum led to the carbon steel The hardness of higher tool, this tool suitable for processing all types of steel. In manufacturing, or tungsten steel alloy containing two or more of a bonding agent and the mixture is hard carbon steel tool, is now generally containing cobalt, cobalt was inquiry into powder and thoroughly mixed, under pressure Formation of Carbide.These cutting tools in the temperature is higher than 1,660 degrees F (870 degrees C) can also be efficiently used. Carbide Tool hardware than high-speed steel tool, used as a tool for better wear resistance. Carbide Tool in a high-speed Gangdao nearly three times the maximum cutting speed of the cutting rate cutting.Made from diamonds to the cutting tool on the surface finish and dimensional accuracy of the high demand and carbide cutting tools can be competitive, but these tools processing the material was more difficult, and difficult to control. Metal, hard rubber and plastic substances can be effective tool together with diamonds and annoyance to the final processing.Ceramic tool (or mixed oxide) is mixed oxide. With 0-30 grade alumina mixture to do, for example, contains about 89 percent to 90 percent of alumina and 10 percent to 11 percent of titanium dioxide. Other ceramic tool is used with the tiny amount of the second oxides Mixed together the cause of pure alumina.Ceramic tools in more than 2,000 degrees F (1095 degrees C) temperature of the work is to maintain strength and hardness. Cutting rates than high-carbon steel knives to 50 percent or even hundreds of percentage. In addition to diamonds and titanium carbide, ceramic tool in the industry is now all the materials of the most hard cutting tool, especially at high temperatures.Tao structure easily broken in a specific situation, broken only carbon intensity of the half to two-thirds. Therefore, in cut, according to the proportion of cutting and milling would normally not be recommended. Ceramics cutting machine breakdown of failure is not usually wear failure, as compared with other materials, their lack of ductility and lower tensile strength.In short, the most widely used by the cutting tool material is cut high-speed steel, low alloy materials and carbide.Gap and dipSpace and inclination of the principle is the most easily to the truck bed lathe tool bladed knives to illustrate. Shape, size of the gap, and dip the type and size will change because of machining. Similarly a grinding tool Corner block is just like brushing your teeth.Gap tool to stop the edge of friction with the workpiece. If there is no gap in Figure 9-15A in the small blades, knives and the side will wear will not be cutting. If there are gaps in Figure 9-15 B, will be a cutting tool. This basic fact apply to any type of tool.Clearance was cutting the size depends on material and the cutting of the material deformation. For example, aluminum is soft and easy to slightly deformed or uplift, when the cutter Corner into space within the perspective and the perspective of the space under, the equivalent in steel mill and will very quickly broken. Table 9-1 (No. 340) that different materials grinding space and perspective.The correct amount of space will be properly protected edge. Too much space will cause the blade vibration (fibrillation), and may edge of total collapse. Tool Corner for the slab block must have a backlash, behind (in front) gap, knife and cut-corner. The main cutting edge is almost as all the cutting work at the cutting edge of the cutting tool on the edge, on the left or right-lateral knives, or cutting tool in the end, cut off on a cutter.Backlash angle for example, the role of a lathe tool Corner to the left block when it mobile. If there is no backlash Kok, Fig 9-16 A, with the only tool will be part of friction rather than cutting. If a suitable backlash Kok, Fig 9-16 B, will be cutting edge and will be well supported. If I have too many gaps, Fig 9-16 C, the edge will not support leading tool vibration (fibrillation) and may be completely broken.Tool gap to the front or rear of the role when it fixed to zero, as shown in Figure 9-17. If not in front of the Gap. Figure 9-17 A, the tool will not only friction and cutting. If a suitable space in front, Fig 9-17 B, but also a good tool will be cutting edge will be well supported. If a big gap in front of Ms, Fig 9-17 C, the tool will lack support, will have a vibrate, and cutting edge may be pressure ulcer.Figure 9-18 illustrate the gap in front of a lathe tool, when it with a 15 degree angle when fixed. The same amount of space on the front fixed to zero, and around thecutter, but the tool is the relatively thin. So the heat away from the blade less. Typically, front-side or front-not too big in Figure 9-19. It is usually from zero degrees to 20 degrees change, an average of about 15 degrees. There are clear advantages, according to the following: good cutting angle so that the cutting edge of the work was well, but relatively thin chips. Cutting Tools is the weakest part. By the former angle, the blade In the form of points around the workpiece. Cutting Edge shock will cause the entire tool vibration. When cutting the work nearly completed, the final section of metal was to ring, packing iron sheet or tangles in the form of the metal ball away gradually replaced by direct removal. Pressure tends to stay away from the workpiece cutting tool rather than narrow the gap between its parts. 9-19 A in the plan was an example of the use of a 30-degree lateral Cutting Angle tool processing thin slice example. A mathematical proof of the plan 9-19 B in the right-angle triangle trip is to expand the use of a map 9-19 A right triangle in the same way, that is, in the direction of upward mobility to feed a 0.010 inch. Right triangle adjacent to the edge (b) and feed 0.010 feet equivalent.The following formula using triangulation to explain:Kok cosine A = right-angle-B / C XiebianOr cosine of 30 degrees = b / c0.886 = b/0.010b = 0.866 * 0.010b = 0.00866 (bladed too thin)When the mobile tool, the purpose of front-to be processed to eliminate from the surface of the cut-cutting tools. This angle is usually from 8 degrees to 15 degrees, but in exceptional circumstances it as much as 20 degrees to 30 degrees. If there is no gap in Figure 9-20 A, cutting tools will be tied up, sharp beep, and the rivets may be the first to die away. The appropriate space, in Figure 9-20 B, cutting tool will be cutting well.A manufacturing plant or cut off the fast-cutter blade with three space, in a root-surface or surface and the other in bilateral level, in Figure 9-21. If a tool Corner block from the date of the face, It can have up to five space, in Figure 9-22. Grooving tool sometimes known as area reduction tool used to cut a groove in the shallow end of the thread.Inclination is the top tool inclination or, in the Tool Corner block on the surface. Changes depending on the angle of the cutting material. Improvement of the cutting angle, the blade shape, and guidelines from the chip from the edge of the direction. Chip dip under the direction named. For example, if a chip from the edge cutter outflow, it is called anterior horn. If the chip to the back of the outflow, that is, to the Dao, which is known as the horn. Some mechanical error and the staff horn as a front-or knife corner.Single tool like Tool Corner block may be the only edge of the blade side oblique angle, or in the back, only to end on the edge of the horn, or they may have roots in the face or front surface of the main Cutting edge of the blade and cutting edge of the horn and a roll angle of the portfolio. In the latter case, cut off most of the surface with a cutter and a chip to the point of view in the tool horn and roll angle in bothdirections has been moved out.Two different roll angle in Figure 9-23 A and 9-23 B was an example. Angle depends on the size and type of material was processed.9-24 A map in Figure 9-24 B and gives examples of zero to a fixed cutter after the two different angle. In Figure 9-25 B and 9-25 A Tool to the regular 15-degree angle. Figure 9-26 tool to display a 15 degree angle fixed, but in this case a tool to roll angle after angle and the combination of form close to the workpiece. Double or multiple chips to lead the inclination angle of a mobile or two away from the edge of the back and side to stay away from the cutter.Comparison of various horn, shown in Figure 9-27, Corner of the horn of a negative point of view, and zero is the point of view. These dip in the Corner cutter on the manifestation of a decision in the hands of the processing needs of the pieces. After Kok was the size of the type of materials processing, and knives in Dao fixed on the way.The type of lateral oblique angleFigure 9-28 examples of tools Corner blocks and four different types of lateral oblique angle of the cross-sectional. Figure 9-28 A, is zero lateral oblique angle, like some of the brass materials, some bronze and some brittle plastic material is particularly necessary. Standard side oblique angle, in Figure 9-28 B, is the most common one of the bevel side. In the ductile material on the deep cut, easy to chip in the tool around the accumulation of many, and this will cause danger to the operator. The chip will become a deal with the problem. Such a tool to cut off the grey cast iron is the most appropriate.Chip laps volumes, Figure 9-28 C, is one of the best types of inclination, especially in the ductile material on the special deep cutting. Chip small crimp in close formation against the Dao of bladed knives against the will of the rupture. The chip rolled up to maintain a narrow trough of the chip will guarantee that the width of closely Lane V ol. The chip is very easy to handle. V olume circle with a chip is not a cut-chip.Chip cut off, in Figure 9-28 D, leading to chip in the corner was cut off, and then to small chips fell after the chip. The need to cut off a chip provides up to 25 percent of the force. This inclination of the stickiness of the steel is good.Gap KokWhen cutting any material time, the gap should always be the smallest size, but the gap should never angle than the required minimum angle small space. The gap is too small knives Kok will lead to friction with the workpiece. Choice of space at the corner to observe the following points:1. When processing hardness, stickiness of the material, the use of high-speed steel tool cutting angle should be in the space of 6 to 8 degrees, and the use of carbon tool steel cutter at the corner of the gap in size should be 5 degrees to 7 degrees.2. When the processing of carbon steel, low carbon steel, cast iron when the gap angle should be the size of high-speed steel tool 8 degrees to 12 degrees, and carbon tool steel cutter 5 degrees to 10 degrees.3. Scalability when processing materials such as copper, brass, bronze, aluminum,iron, etc. Zhanxing materials, space Kok should be the size of high-speed steel tool 12 degrees to 16 degrees, carbon steel knives 8 degrees to 14 , Mainly because of the plastic deformation of these metals. This means that, when the cutter and around them, the soft metal to some minor deformation or protruding, and this tool will be friction. At this time, we must have a tool on the additional space.刀具目的在完成这一个单元之后,学生将会能够:* 解释粗加工和精加工之间的差别。
(完整版)机械毕业设计外文翻译7243268

Introduciton of MachiningHave a shape as a processing method, all machining process for the production of the most commonly used and most important method. Machining process is a process generated shape, in this process, Drivers device on the workpiece material to be in the form of chip removal. Although in some occasions, the workpiece under no circumstances, the use of mobile equipment to the processing, However, the majority of the machining is not only supporting the workpiece also supporting tools and equipment to complete.Machining know the process . For casting, forging and machining pressure, every production of a specific shape of the workpiece, even a spare parts, almost the shape of the structure, to a large extent, depend on effective in the form of raw materials. In general, through the use of expensive equipment and without special processing conditions, can be almost any type of raw materials, mechanical processing to convert the raw materials processed into the arbitrary shape of the structure, as long as the external dimensions large enough, it is possible. Because of a production of spare parts, even when the parts and structure of the production batch sizes are suitable for the original casting, Forging or pressure processing to produce, but usually prefer machining.Strict precision and good surface finish, Machining the second purpose is the establishment of the and surface finish possible on the basis of. Many parts, if any other means of production belonging to the large-scale production, Well Machining is a low-tolerance and can meet the requirements of small batch production. Besides, many parts on the production and processing of coarse process to improve its generalshape of the surface. It is only necessary precision and choose only the surface machining. For instance, thread, in addition to mechanical processing, almost no other processing method for processing. Another example is the blacksmith pieces keyhole processing, as well as training to be conducted immediately after the mechanical completion of the processing.Primary Cutting ParametersCutting the work piece and tool based on the basic relationship between the following four elements to fully describe : the tool geometry, cutting speed, feed rate, depth and penetration of a cutting tool.Cutting Tools must be of a suitable material to manufacture, it must be strong, tough, order to effectively processing, and cutting speed must adapt to the level of specific parts -- with knives. Generally, the more the work piece or tool for reciprocating movement and feed rate on each trip through the measurement of inches. Generally, in other conditions, feed rate and cutting speed is inversely proportional to。
(完整)雕刻机毕业设计外文文献翻译

附录1外文翻译—原文部分DXF File Identification with C# for CNC Engraving Machine System Huibin Yang, Juan YanAbstractThis paper researches the main technology of open CNC engraving machine,the DXF identification technology. Agraphic information extraction method is proposed。
By this method,the graphic information in DXF file can be identified and transformed into bottom motion controller’s code。
So the engraving machine can achieve trajectory tracking。
Then the open CNC engraving machine system is developed with C#。
At last, the method is validated on a three axes motion experiment platform. The result shows that this method can efficiently identify the graphic information including line, circle, arc etc。
in DXF file and the CNC engraving machine can be controlled well。
KeywordsDXF, CNC Engraving Machine , GALIL,C#1.IntroductionWith the development of pattern recognition techniques, modern CNC engraving machine needn’t be programmed manually。
数控专业毕业设计外文翻译
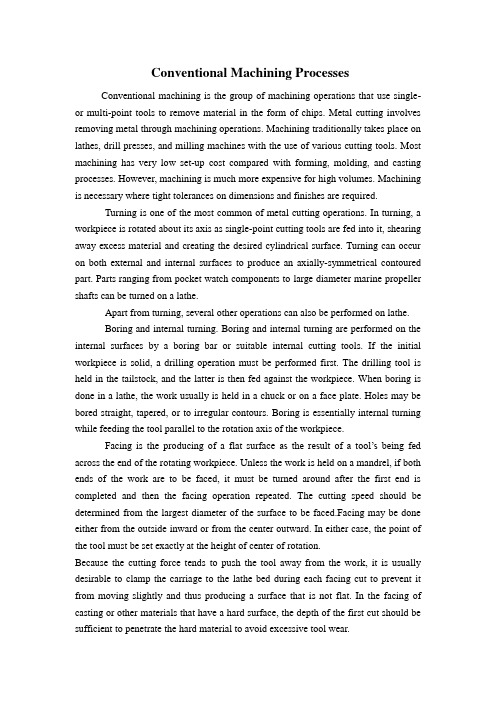
Conventional Machining ProcessesConventional machining is the group of machining operations that use single- or multi-point tools to remove material in the form of chips. Metal cutting involves removing metal through machining operations. Machining traditionally takes place on lathes, drill presses, and milling machines with the use of various cutting tools. Most machining has very low set-up cost compared with forming, molding, and casting processes. However, machining is much more expensive for high volumes. Machining is necessary where tight tolerances on dimensions and finishes are required.Turning is one of the most common of metal cutting operations. In turning, a workpiece is rotated about its axis as single-point cutting tools are fed into it, shearing away excess material and creating the desired cylindrical surface. Turning can occur on both external and internal surfaces to produce an axially-symmetrical contoured part. Parts ranging from pocket watch components to large diameter marine propeller shafts can be turned on a lathe.Apart from turning, several other operations can also be performed on lathe.Boring and internal turning. Boring and internal turning are performed on the internal surfaces by a boring bar or suitable internal cutting tools. If the initial workpiece is solid, a drilling operation must be performed first. The drilling tool is held in the tailstock, and the latter is then fed against the workpiece. When boring is done in a lathe, the work usually is held in a chuck or on a face plate. Holes may be bored straight, tapered, or to irregular contours. Boring is essentially internal turning while feeding the tool parallel to the rotation axis of the workpiece.Facing is the producing of a flat surface as the result of a tool’s being fed across the end of the rotating workpiece. Unless the work is held on a mandrel, if both ends of the work are to be faced, it must be turned around after the first end is completed and then the facing operation repeated. The cutting speed should be determined from the largest diameter of the surface to be faced.Facing may be done either from the outside inward or from the center outward. In either case, the point of the tool must be set exactly at the height of center of rotation.Because the cutting force tends to push the tool away from the work, it is usually desirable to clamp the carriage to the lathe bed during each facing cut to prevent it from moving slightly and thus producing a surface that is not flat. In the facing of casting or other materials that have a hard surface, the depth of the first cut should be sufficient to penetrate the hard material to avoid excessive tool wear.Parting is the operation by which one section of a workpiece is severed from the remainder by means of cutoff tool. Because cutting tools are quite thin and must have considerable overhang, this process is less accurate and more difficult. The tool should be set exactly at the height of axis of rotation, be kept sharp, have proper clearance angles, and be fed into the workpiece at a proper and uniform feed rate.Threading can be considered as turning since the path to be travelled by the cutting tool is helical. However, there are some major differences between turning and threading. While in turning, the interest is in generating a smooth cylindrical surface, in threading the interest is in cutting a helical thread of a given form and depth which can be calculated from the formulae. There are two basic requirements for thread cutting. An accurately shaped and properly mounted tool is needed because thread cutting is a form-cutting operation. The resulting thread profile is determined by the shape of the tool and its position relative to the workpiece.The second by requirement is that the tool must move longitudinally in a specific relationship to the rotation of workpiece, because this determines the lead of the thread. This requirement is met through the use of the lead screw and the split unit, which provide positive motion of carriage relative to the rotation of spindleLathe bed is foundation of the engine lathe, which heavy, rugged casting is made to support the working parts of the lathe. The size and mass of the bed gives the rigidity necessary for accurate engineering tolerances required in manufacturing. On top of the bed are machined slideways that guide and align the carriage and tailstock, as they are move from one end of the lathe to the other.Headstock is clamped atop the bed at left-hand end of the lathe and contains the motor that drives the spindle whose axis is parallel to the guideways through a series of gears housed within the gearbox. The function of gearbox is to generate a number of different spindle speeds. A spindle gear is mounted on the rear of the spindle to transmit power through the change gears to the feeding box that distributes the power to the lead screw for threading or to the feed rod for turning.The spindle has a through hole extending lengthwise through which bar stocks can be fed if continuous production is used. The hole can hold a plain lathe center by its tapered inner surface and mount a chuck, a face plate or collet by its threaded outer surface.Carriage assembly is actually an H-shaped block that sits across the guideways and in front of lathe bed. The function of the carriage is to carry and move the cuttingtool longitudinally. It can be moved by hand or by power and can be clamped into position with a locking nut. The carriage is composed of the cross slide, compound rest, tool saddle, and apron.The cross slide is mounted on the dovetail guideways on the top of the saddle and it moved back and forth at 90°to the axis of the lathe by the cross slide lead screw. The lead screw can be hand or power activated.The compound rest is mounted on the cross slide and can be swiveled and clamped at any angle in a horizontal plane. The compound is typically used for cutting chamfers or tapers, but must also be used when cutting thread. The compound rest can only be fed by hand. There is no power to compound rest. The cutting tool and tool holder are secured in the tool post which is mounted directly to the compound rest.The tool saddle is an H shaped casting mounted on the top of the guideways and houses the cross slide and compound rest. It makes possible longitudinal, cross and angular feeding of the tool bit.The apron is attached to the front of the carriage and contains the gears and feed clutches which transmit motion from the feed rod or lead screw to carriage and cross slide. When cutting screw threads, power is provided to the gearbox of the apron by the lead screw. In all other turning operations, it is the feed rod that drives the carriage.Tailstock is composed of a low base and the movable part of the tail-stock proper, the transverse adjustments being made with a cross screw furnished with a square head. The two parts are hold together by the holding-down bolts which secure the tailstock to the bed.。
机械毕业设计英文外文翻译446数控机床 (2)
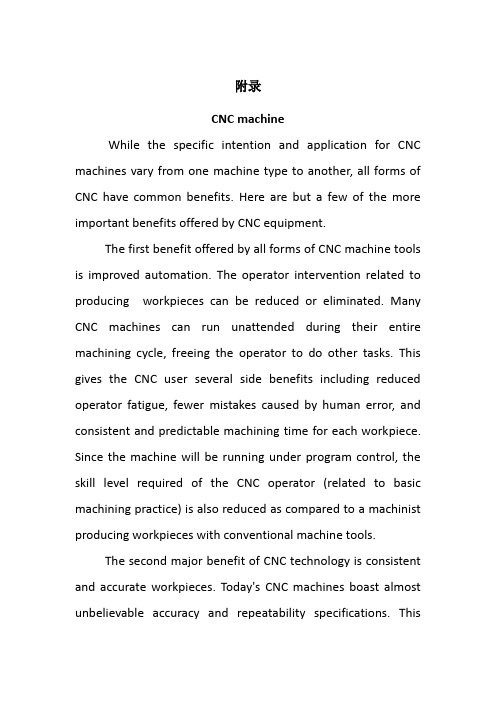
附录CNC machineWhile the specific intention and application for CNC machines vary from one machine type to another, all forms of CNC have common benefits. Here are but a few of the more important benefits offered by CNC equipment.The first benefit offered by all forms of CNC machine tools is improved automation. The operator intervention related to producing workpieces can be reduced or eliminated. Many CNC machines can run unattended during their entire machining cycle, freeing the operator to do other tasks. This gives the CNC user several side benefits including reduced operator fatigue, fewer mistakes caused by human error, and consistent and predictable machining time for each workpiece. Since the machine will be running under program control, the skill level required of the CNC operator (related to basic machining practice) is also reduced as compared to a machinist producing workpieces with conventional machine tools.The second major benefit of CNC technology is consistent and accurate workpieces. Today's CNC machines boast almost unbelievable accuracy and repeatability specifications. Thismeans that once a program is verified, two, ten, or one thousand identical workpieces can be easily produced with precision and consistency.A third benefit offered by most forms of CNC machine tools is flexibility. Since these machines are run from programs, running a different workpiece is almost as easy as loading a different program. Once a program has been verified and executed for one production run, it can be easily recalled the next time the workpiece is to be run. This leads to yet another benefit, fast change over. Since these machines are very easy to set up and run, and since programs can be easily loaded, they allow very short setup time. This is imperative with today's just-in-time (JIT) product requirements.Motion control - the heart of CNCThe most basic function of any CNC machine is automatic, precise, and consistent motion control. Rather than applying completely mechanical devices to cause motion as is required on most conventional machine tools, CNC machines allow motion control in a revolutionary manner2. All forms of CNC equipment have two or more directions of motion, called axes. These axes can be precisely and automatically positioned along their lengths of travel. The two most common axis types arelinear (driven along a straight path)and rotary (driven along a circular path).Instead of causing motion by turning cranks and handwheels as is required on conventional machine tools, CNC machines allow motions to be commanded through programmed commands. Generally speaking, the motion type (rapid, linear, and circular), the axes to move, the amount of motion and the motion rate (feedrate) are programmable with almost all CNC machine tools.A CNC command executed within the control tells the drive motor to rotate a precise number of times. The rotation of the drive motor in turn rotates the ball screw. And the ball screw drives the linear axis (slide). A feedback device (linear scale) on the slide allows the control to confirm that the commanded number of rotations has taken place3. Refer to fig.1.Fig.1Though a rather crude analogy, the same basic linear motion can be found on a common table vise. As you rotate thevise crank, you rotate a lead screw that, in turn, drives the movable jaw on the vise. By comparison, a linear axis on a CNC machine tool is extremely precise. The number of revolutions of the axis drive motor precisely controls the amount of linear motion along the axis.How axis motion is commanded - understanding coordinate systemsIt would be infeasible for the CNC user to cause axis motion by trying to tell each axis drive motor how many times to rotate in order to command a given linear motion amount4. (This would be like having to figure out how many turns of the handle on a table vise will cause the movable jaw to move exactly one inch!) Instead, all CNC controls allow axis motion to be commanded in a much simpler and more logical way by utilizing some form of coordinate system. The two most popular coordinate systems used with CNC machines are the rectangular coordinate system and the polar coordinate system. By far, the more popular of these two is the rectangular coordinate system.The program zero point establishes the point of reference for motion commands in a CNC program. This allows the programmer to specify movements from a common location. Ifprogram zero is chosen wisely, usually coordinates needed for the program can be taken directly from the print.With this technique, if the programmer wishes the tool to be sent to a position one inch to the right of the program zero point, X1.0 is commanded. If the programmer wishes the tool to move to a position one inch above the program zero point, Y1.0 is commanded. The control will automatically determine how many times to rotate each axis drive motor and ball screw to make the axis reach the commanded destination point . This lets the programmer command axis motion in a very logical manner. Refer to fig.2, 3.Fig.2Fig.3All discussions to this point assume that the absolute mode of programming is used6. The most common CNC word used to designate the absolute mode is G90. In the absolute mode, the end points for all motions will be specified from the program zero point. For beginners, this is usually the best and easiest method of specifying end points for motion commands. However, there is another way of specifying end points for axis motion.In the incremental mode (commonly specified by G91), end points for motions are specified from the tool's current position, not from program zero. With this method of commanding motion, the programmer must always be asking "How far should I move the tool?" While there are times when the incremental mode can be very helpful, generally speaking, this is the more cumbersome and difficult method of specifyingmotion and beginners should concentrate on using the absolute mode.Be careful when making motion commands. Beginners have the tendency to think incrementally. If working in the absolute mode (as beginners should), the programmer should always be asking "To what position should the tool be moved?" This position is relative to program zero, NOT from the tools current position.Aside from making it very easy to determine the current position for any command, another benefit of working in the absolute mode has to do with mistakes made during motion commands. In the absolute mode, if a motion mistake is made in one command of the program, only one movement will be incorrect. On the other hand, if a mistake is made during incremental movements, all motions from the point of the mistake will also be incorrect.Assigning program zeroKeep in mind that the CNC control must be told the location of the program zero point by one means or another. How this is done varies dramatically from one CNC machine and control to another8. One (older) method is to assign program zero in the program. With this method, the programmer tellsthe control how far it is from the program zero point to the starting position of the machine. This is commonly done with a G92 (or G50) command at least at the beginning of the program and possibly at the beginning of each tool.Another, newer and better way to assign program zero is through some form of offset. Refer to fig.4. Commonly machining center control manufacturers call offsets used to assign program zero fixture offsets. Turning center manufacturers commonly call offsets used to assign program zero for each tool geometry offsets.Fig. 4Flexible manufacturing cellsA flexible manufacturing cell (FMC) can be considered as a flexible manufacturing subsystem. The following differences exist between the FMC and the FMS:1.A n FMC is not under the direct control of thecentral computer. Instead, instructions from the central computer are passed to the cell controller.2.The cell is limited in the number of part families itcan manufacture.The following elements are normally found in an FMC:•Cell controller•Programmable logic controller (PLC)•More than one machine tool•A materials handling device (robot or pallet)The FMC executes fixed machining operations with parts flowing sequentially between operations.High speed machiningThe term High Speed Machining (HSM) commonly refers to end milling at high rotational speeds and high surface feeds. For instance, the routing of pockets in aluminum airframe sections with a very high material removal rate1. Over the past 60 years, HSM has been applied to a wide range of metallic and non-metallic workpiece materials, including the production of components with specific surface topography requirements and machining of materials with hardness of 50 HRC and above. With most steel components hardened to approximately 32-42HRC, machining options currently include: Rough machining and semi-finishing of the material in its soft (annealed) condition heat treatment to achieve the final required hardness = 63 HRC machining of electrodes and Electrical Discharge Machining (EDM) of specific parts of dies and moulds (specifically small radii and deep cavities with limited accessibility for metal cutting tools) finishing and super-finishing of cylindrical/flat/cavity surfaces with appropriate cemented carbide, cermet, solid carbide, mixed ceramic or polycrystalline cubic boron nitride (PCBN)For many components, the production process involves a combination of these options and in the case of dies and moulds it also includes time consuming hand finishing. Consequently, production costs can be high and lead times excessive.It is typical in the die and mould industry to produce one or just a few tools of the same design. The process involves constant changes to the design, and because of these changes there is also a corresponding need for measuring and reverse engineering .The main criteria is the quality level of the die or mould regarding dimensional, geometric and surface accuracy. If thequality level after machining is poor and if it cannot meet the requirements, there will be a varying need of manual finishing work. This work produces satisfactory surface accuracy, but it always has a negative impact on the dimensional and geometric accuracy.One of the main aims for the die and mould industry has been, and still is, to reduce or eliminate the need for manual polishing and thus improve the quality and shorten the production costs and lead times.Main economical and technical factors for the development of HSMSurvivalThe ever increasing competition in the marketplace is continually setting new standards. The demands on time and cost efficiency is getting higher and higher. This has forced the development of new processes and production techniques to take place. HSM provides hope and solutions...MaterialsThe development of new, more difficult to machine materials has underlined the necessity to find new machining solutions. The aerospace industry has its heat resistant and stainless steel alloys. The automotive industry has differentbimetal compositions, Compact Graphite Iron and an ever increasing volume of aluminum3. The die and mould industry mainly has to face the problem of machining high hardened tool steels, from roughing to finishing.QualityThe demand for higher component or product quality is the result of ever increasing competition. HSM, if applied correctly, offers a number of solutions in this area. Substitution of manual finishing is one example, which is especially important on dies and moulds or components with a complex 3D geometry.ProcessesThe demands on shorter throughput times via fewer setups and simplified flows (logistics) can in most cases, be solved by HSM. A typical target within the die and mould industry is to completely machine fully hardened small sized tools in one setup. Costly and time consuming EDM processes can also be reduced or eliminated with HSM.Design & developmentOne of the main tools in today's competition is to sell products on the value of novelty. The average product life cycle on cars today is 4 years, computers and accessories 1.5 years, handphones 3 months... One of the prerequisites of this development of fast design changes and rapid product development time is the HSM technique.Complex productsThere is an increase of multi-functional surfaces on components, such as new design of turbine blades giving new and optimized functions and features. Earlier designs allowed polishing by hand or with robots (manipulators). Turbine blades with new, more sophisticated designs have to be finished via machining and preferably by HSM . There are also more and more examples of thin walled workpieces that have to be machined (medical equipment, electronics, products for defence, computer parts)Production equipmentThe strong development of cutting materials, holding tools, machine tools, controls and especially CAD/CAM features and equipment, has opened possibilities that must be met with new production methods and techniques5.Definition of HSMSalomon's theory, "Machining with high cutting speeds..." on which, in 1931, took out a German patent, assumes that "at a certain cutting speed (5-10 times higher than in conventionalmachining), the chip removal temperature at the cutting edge will start to decrease..."Given the conclusion:" ... seems to give a chance to improve productivity in machining with conventional tools at high cutting speeds..."Modern research, unfortunately, has not been able to verify this theory totally. There is a relative decrease of the temperature at the cutting edge that starts at certain cutting speeds for different materials.The decrease is small for steel and cast iron. But larger for aluminum and other non-ferrous metals. The definition of HSM must be based on other factors.Given today's technology, "high speed" is generally accepted to mean surface speeds between 1 and 10 kilometers per minute or roughly 3 300 to 33 000 feet per minute. Speeds above 10 km/min are in the ultra-high speed category, and are largely the realm of experimental metal cutting. Obviously, the spindle rotations required to achieve these surface cutting speeds are directly related to the diameter of the tools being used. One trend which is very evident today is the use of very large cutter diameters for these applications - and this has important implications for tool design.There are many opinions, many myths and many different ways to define HSM.数控机床虽然各种数控机床的功能和应用各不相同,但它们有着共同的优点。
机械专业毕业设计外文翻译相关外文文献

A new driver based on dual-mode frequency and phase control for traveling-wave type ultrasonic motorTien-Chi Chen a,*,Chih-Hsien Yu a ,Mi-Ching Tsai ba Department of Engineering Science,National Cheng Kung University,Tainan,Taiwan bDepartment of Mechanical Engineering,National Cheng Kung University,Tainan,Taiwana r t i c l e i n f o Article history:Received 6August 2007Accepted 24March 2008Available online 12May 2008Keywords:Ultrasonic motorFrequency and phase modulation controla b s t r a c tA mode conversion rotary traveling-wave ultrasonic motor (TWUSM)has potential applications in min-iature robotics.However,its electrical drive circuit presents unique challenges,particularly in producing a high frequency (about 40kHz),high voltage (400V peak-to-peak)signal input to a low impedance capacitive motor,while achieving high efficiency.A novel driving circuit is proposed to provide two-phase balance voltage for a TWUSM.This paper describes the design of TWUSM drive circuit,intended for simultaneously employs both the driving frequency and phase modulation control scheme.The oper-ating principles and a detailed analysis of the proposed driving circuit,consisting of voltage-controlled oscillator (VCO),voltage-controlled phase-shifter circuit and power amplifier circuit,are introduced.To drive the USM effectively a two-phase power amplifier converter using non-resonant technique was designed to provide a balanced two-phase voltage source,and the two-phase output driving voltages could be maintained at the same peak voltage value at the driving frequency under varying phase-mod-ulation processes.Detailed experimental results are provided to demonstrate the effectiveness of the pro-posed driving circuit.Crown Copyright Ó2008Published by Elsevier Ltd.All rights reserved.1.IntroductionThe ultrasonic motor (USM)has many excellent performance features,including high-retention torque,high torque at low speed,silence,compactness in size,and no electromagnetic inter-ference.The USM has been used in a number of industrial,medical,space,robotic,and automotive applications.The driving principles of the USM are high-frequency mechani-cal vibrations and frictional force and its mathematical model is thus difficult to derive.As a result,a lumped motor model of the USM is presently unavailable [1].Moreover,the control character-istics of the USM are complicated and highly nonlinear,as motor parameters are time-varying,owing to increases in temperature and changes in motor-drive operating conditions,such as driving frequency,source voltage and load.Basically,the speed of the TWUSM can be manipulated by con-trolling the frequency,phase difference and the voltage amplitude of the two sinusoidal voltage waveforms which input to the TWUSM.Many researchers have opted for the frequency of the sinusoidal voltage waveforms as the control variable [2–5].It can easily be controlled digitally and spans the entire allowable speed range of the TWUSM.Most TWUSMs contain a two-phase half-bridge series-resonant inverter with an approximated unityswitching frequency (f s )to resonant frequency (f o )ratio.According to the description in the previous paragraph,the quality factors of the two phases are different and time varying.Moreover,when the frequency ratio (f s /f o )of a series-resonant inverter approaches unity,the voltage gain varies severely with the variation of the quality factor [6].Thus,the two-phase sinusoid output voltages are unbalanced under the same switching frequency.Conse-quently,good dynamic performance of the USM is difficult to ob-tain due to the variation in the unbalanced peak values of the two-phase voltages.By contrast,a voltage amplitude control strat-egy using additional boost choppers was employed in [7].Each chopper–inverter driving circuit is composed of one boost chopper cascading with one half-bridge series-resonant parasitic load impedance inverter.Since the two phase constructions of the USM are coupled mechanically and the reaction from the electrical to the mechanical part is unbalanced for both phases,the equiva-lent two-phase loads of the rotor are unbalanced and varied for dif-ferent rotating directions,rotor speeds,load torque,applied voltages and static pressure force between stator and rotor.In addition,the internal two-phase blocking capacitors of the USM are unbalanced and will vary in value under different rotational directions.As a result,it is difficult maintain the two-phase sinu-soid output voltages at the same constant peak value at the same switching frequency.However,a driving circuit proposed by Lin and Kuo [8]operates within working limits where the inverter voltage gain is greatly affected by the variation of the quality0196-8904/$-see front matter Crown Copyright Ó2008Published by Elsevier Ltd.All rights reserved.doi:10.1016/j.enconman.2008.03.023*Corresponding author.E-mail address:tchichen@.tw (T.-C.Chen).Energy Conversion and Management 49(2008)2767–2775Contents lists available at ScienceDirectEnergy Conversion and Managementj ou r na l h om e pa ge :w w w.e lse vi e r.c om /lo c at e /en c on manfactor.Moreover,to resolve the difficulty of the amplitude varia-tion in the output voltages of the parallel-resonant inverter,an ex-tra energy feedback circuit is added to reduce the quality factors in the parallel-resonant circuit.However,the energy feedback circuit increases the complexity of the driving circuit.In addition to the use of a boost converter,a voltage amplitude control strategy may also be implemented using pulse-width mod-ulation(PWM).In[9],the voltage amplitude was adjusted by the forward and backward PWM method for position control of the TWUM.In[10],the voltage amplitude was adjusted by the ON–OFF PWM method for speed control.Both methods essentially adopted the same principle in which the modulation was used to control the ratio of the number of ultrasonic cycles within the for-ward-direction or on-time duration to the total number of ultra-sonic cycles,including the backward-direction or off-time duration.Such control methods cause intermittent operation of the TWUM,leading to the creation of severe audible noise.In order to suppress this audible noise,the PWM should be applied to each ultrasonic cycle[11].Given these limitations,a specific drive circuit control tech-nique is required.Hence,it is desirable to develop a novel drive system that solves these issues while supplying the necessary power with high efficiency.Compared to work on drive circuit design for TWUSM based on the phase difference between the two-phase voltages,less research has been done in other areas of drive circuit design for TWUSM. Only the phase difference control strategy offers the advantage of bidirectional rotation,while the other two parameters of the con-trol scheme,frequency and voltage amplitude,need the assistance of phase-shift change between p/2toÀp/2.In the design of modern drive circuits with adjustable phase dif-ferences,a low-cost and simple phase shifter circuit providing two-phase signals of two-phase voltage source is a critical design issue. The motivation of this study is to design a novel driving scheme that simultaneously employs both the driving frequency and phase difference as dual-mode control variables to handle system nonlin-earities and parameter variations.In order to reduce the system hardware size and cost,the proposed phase shifter circuit is imple-mented by using a voltage-controlled resistance(VCR)and all-pass filter circuit that can provide piecewise-linear phase control over the entire speed range.In the conventional series and parallel resonant converter archi-tecture,two inductances must be inserted in parallel or series with the load for each phase,respectively,in order to become resonant with the inherent two-phase parasitic capacitances of the USM. Moreover,the motor parameters of the USM are dependent on the operating temperature,the running time,and the load.In addi-tion,the equivalent two-phase loads of the rotor are also unbal-anced and the equivalent resistor values vary for different operating conditions.Therefore the quality factors of the resonant inverters in two-phase are unequal and time-varying,resulting in the consumption of time to determine suitable RLC tank compo-nents.In contrast with conventional series and parallel resonant converters with two reactive components,the power amplifier circuit in this study is implemented to build high-frequency two-phase high drive voltages for USM(e.g.400V peak to peak) and is not in need of additional reactive components or a compli-cated energy feedback circuit.Although the quality factors of the two RLC tanks vary at different rotating speeds and are not equal, the output driving voltage of the proposed power amplifier circuit in two-phase can be maintained at the same peak voltage value when the driving frequency is operated close to the resonant frequency.In this paper,the design of a novel phase shifter circuit for applying TWUSM driving is presented.For a USM prototype,the operating principles and characteristics at the operating conditions will be also briefly described.Next,the novel driving circuit for the TWUSM,which contains VCO,VCR,voltage-controlled phase shif-ter,and power amplifier driving circuit,is introduced.The results of experiments investigating the effectiveness of the proposed dri-ver are given in Section4.Finally,a discussion and conclusions are provided in Section5.2.Operating principle and characteristicIn the operation of the TWUSM,a two-stage energy conversion is formed.Thefirst stage consists of the electro-mechanical energy conversion where the electrical energy is converted into mechani-cal energy.This is achieved by excitation of the piezoelectric cera-mic by ultrasonic range frequency.The second stage comprises mechanical energy conversion where the mechanical vibrations are converted to linear or rotary motion by the friction force gen-erated in the stator–rotor interface.Fig.1illustrates the operating principles of the TWUSM.The stator,designed with comb-tooth surface,is attached above the sectors of piezoelectric elements. The piezoelectric elements are divided into sectors instead of form-ing a complete ring so that they can be applied with different voltages.The rotor is pressed against the stator by means of a pressure spring disc.It should be noted that the spring as shown is for illus-tration only,since in reality it is not a normal spring,but a pressure disc.The operating principle of the TWUSM is based on the mechanical vibrations of the piezoelectric elements.As a result of voltages applied to them,they produce a traveling wave in the sta-tor.The surface interaction between the stator and the rotor cre-ates a driving torque in the rotor.As shown in Fig.1, piezoelectric elements are positioned at an appropriate distance from one another.One is produces a mechanical vibration by being fed by the phase-A voltage source V m sin x t,while the other is fed by the phase-B voltage source V m sin(x t+U),generating another vibration,where V m is the amplitude,x=2p f is the angular version of frequency f,and U is the phase difference of the two driving volt-age sources.Each voltage source generates a mode of vibration throughout the stator,and the superposition of them forms a trav-eling wave that propagates along the stator.Depending on which phase of the voltage leads the other,the traveling wave will travel in either a right or left direction.Elliptical motion can be observed at the wave peak of the surface of the stator.Such motion produces a tangential force at the contact surface between the stator and the rotor.With a spring disc to keep the rotor in pressure contact with the stator,the rotor can be driven to travel in the opposite direc-tion from the traveling wave by this tangential force at the contactsurface.Fig.1.TWUSM operating principle[1].2768T.-C.Chen et al./Energy Conversion and Management49(2008)2767–2775The speed of the USM is controlled by:Frequency of two-phase voltages.Amplitude of two-phase voltages.Phase difference between two-phase voltages.3.Drive circuit designFig.2shows actual configuration view of a typical USR-60circu-lar traveling wave type motor(from Shinsei of Japan),in which the specification is a40kHz,0.32Nm,3W,120rev/min type motor. The operation of a mode conversion USM is based on the torque generated by piezoelectric ultrasonic vibrations.An optimal supply voltage for the USM is a sinusoidal voltage with frequency near the mechanical resonance frequency of the stator–rotor assembly. Since this USM presents a large capacitive load and requires a high operating frequency(40kHz),its equivalent impedance could be extremely low.This USM also requires a high drive voltage (400V peak-to-peak),which leads to a large drive current.The goals for drive circuit design are to satisfy these require-ments,as well as achieve high power efficiency and reduce the sys-tem hardware size and cost.In the design of modern drive circuit with adjustable phase difference,the key technology is a low-cost and simple phase shifter circuit,provided two-phase signals from a two-phase voltage source.The purpose of this study is to design a novel driving scheme that simultaneously employs both the driv-ing frequency and phase difference as the dual-mode control vari-ables to handle system nonlinearities and parameter variations. The block diagram of the driving circuit is shown in Fig.3.This cir-cuit is composed of voltage-controlled oscillator(VCO),voltage-controlled phase shifter,power amplifier,and transformer.The design procedures of the proposed drive system are described in detail below.3.1.Voltage-controlled oscillatorThe ICL8038waveform generator is a monolithic integrated cir-cuit capable of producing high accuracy sine,square,triangular, sawtooth,and pulse waveforms with a minimum of external com-ponents[12].The frequency(or repetition rate)can be selected externally from0.001Hz to more than300kHz using either resis-tors or capacitors,and frequency modulation and sweeping can be accomplished with an external frequency-modulated voltage(V f). The frequency of the waveform generator is a direct function of the DC voltage at Terminal8,shown in Fig.4.By altering this volt-age,frequency modulation is performed by means of a voltage-controlled oscillator(VCO).To clarify the relation between the frequency-modulated voltage and the magnitude of the single fre-quency,experimental measurements were made at different volt-age values in Fig.5.Fig.5shows that this characteristic is quite linear.In this study,motor speed is controlled at40–44kHz,which may be considered the linear frequency range.3.2.Voltage-controlled phase shifterFig.6shows afirst-order all-passfilter with a junctionfield-effect transistor(JFET)used as a variable resistor to control the pole and zero time constants in thefilter transfer function.Let VCR R eq be the resistance of the JFET.If we assume that this is a linear resis-tor,the transfer function isTðsÞ¼V oi¼s sÀ1ð1Þwhere the time constant s is given by s=R eq C.By varying the gate-source voltage of JFET(V GS),i.e.the phase-modulated voltage(V p)in Fig.3,the resistance of the JFET can be varied,which in turn changes the time constant s.For s=j x,the phase difference of the transfer function is therefore\Tðj xÞ¼À2tanÀ1x R eq Cð2ÞFig.2.The photograph of experimentalsetup.The magnitude of the transfer function (j T (j x )j )is 1for all fre-quency x .The phase displacement not only depends on the oper-ating frequency of the TWUSM but is also affected by the timeconstant (s ).At different frequencies,between 41and 44kHz,the voltage signal (V i )applied to the USM,the VCR (R eq )drifting through the control voltage (V GS ),and the relationship between them were measured (Table 1).At a specific resonant frequency (f o =41kHz),the goals for phase shifter circuit designed to adjust the phase differential from Àp /2to Àp rad.Fig.6shows a general all-pass filter circuit.The circuit is composed of a resistor,a capac-itor,and an operational amplifier.The frequency of the input signalfor the circuit has to be near the resonant frequency of the TWUSM.We inset the VCR instead of the resistor,and adjusted the proper-ties of the circuit components (R =10k X ,C =0.01l F).As a result,when the operating frequency equal the resonant frequency (f o )and the control voltage minimizes as zero (V GS =0),the phase dis-placement reaches Àp /2rad,i.e.x R eq C =1.Conversely,if the R eq is increased in small increments,the phase difference gradually diminishes.3.3.Voltage-controlled resistanceVoltage-controlled filter,voltage-controlled oscillators,and voltage-to-time period/frequency converters have been applied in many instrumentation and measurement situations.A simple way to realize such circuits is to start from known circuits and then replace resistors by voltage-controlled resistances (VCR).Schemes to construct such VCR using FET’s are known in literature [13].Fig.4.A voltage-controlled oscillatorcircuit.Fig. 5.The measured relation between controlled voltage and output single frequency.Table 1Measurement results of V GS versus R eq V GS (V)0À0.2À0.4À0.6À0.8À1.0R eq (X )357.1416.7471.7531.9617.3746.3V GS (V)À1.2À1.4À1.6À1.8À2.0À2.2R eq (X )943.4128219233846291661Fig.8.FET output characteristics (K30A).2770T.-C.Chen et al./Energy Conversion and Management 49(2008)2767–2775The VCR configuration is shown in Fig.7.A routine analysis of the circuit shows that when the FET is confined to operate in a non-saturated region under the same constraints as in [13,14],the output characteristic of the FET may be represented by a qua-dratic function given by I DS ¼I DSS V p½2ðV GS ÀV p ÞV DS ÀV 2DSð3Þwhere I DSS and V p are saturation current and pinch-off voltage,respectively.The implementation of the voltage-tunable resistance can be simplified by neglecting the V 2DS term of Eq.(3),in which case R eq would be R eq¼V DS DS %V 2pDSS GS p ;providedV DS <j 0:5jð4ÞA typical set of characteristics obtained experimentally for an n-channel JFET (K30A)is shown in Fig.8.The range of values includes those prescribed in [14]as well as larger values,to show the nonlinear nature of these curves.Clearly if thisfield-effectFig.9.Phase displacement against controlvoltage.Fig.10.Measured results of the divergent index coefficient under difference ope-rating control voltage.Fig.12.Generated signals of phase-shifted circuit.(a)Phase difference set at p /2rad (b)p /3(c)p /6(d)0(e)Àp /6(f)Àp /3(g)Àp /2.Fig.13.Measured results of the phase shifter circuit under difference operating driving frequency.T.-C.Chen et al./Energy Conversion and Management 49(2008)2767–27752771transistor(FET)is to be used as a bidirectional linear resistor,j V DS j should be kept low,at least less than500mV,particularly for prac-tical circuit applications.For the relationship between the phase displacement angle(U) and the control voltage(V GS),the analysis of the phase shifter cir-cuit should yield the following results by observing the phase dis-placement versus control voltage curve in Fig.9x R eq C%tanðaV GSþbÞð5ÞUsing Eq.(5)to simplify Eq.(2),the following relationship results:\T¼À2ðaVGSþbÞð6Þwhere the constants a and b are calculated to define as a=À0.3865, b=p/4,and were used in the verifications below.Note that,as ex-pected,even nonlinearities do not appear in Eq.(6),as they are can-celed out.In the following,we test the divergence between the theoretical formula and experimental data and also define the divergent index coefficient D(the ratio of the phase value according to Eq.(6)di-vided by the actual phase displacement relating to Eq.(2)of exper-imental data)asD¼À2ðaV GSþbÞÀ2tanÀ1ðx R eq CÞð7ÞTo illustrate the difference between(2)and(6),actual and esti-mated UÀV GS curves using both schemes are presented in Fig.9. The measured index coefficient(D)of the divergence as the input control voltage swing during different operating values is shown in Fig.10.As thisfigure shows,a reasonably good correspondence is observed between the two sets of data,confirming the validity of the above supposition property regarding Eq.(6).A phase shifter circuit was designed to provide two-phase sig-nals of two-phase driving voltage sources with a phase difference ranging from p/2toÀp/2.To design a low-cost,simple phase shifter circuit for a TWUSM,we constructed a phase-regulating driving circuit for the USM by utilizing the VCR and all-passfilter circuit.The proposed phase shifter circuit,shown in Fig.11, has dual complementary channels,in which the sinusoid output signals have angles complementary to each other (\A+\B=90°).The driving voltage signals with the phase difference from the phase shifter circuit for the resonance frequency of TWUSMsetFig.14.A Push–pull class-B amplifier with Darlingtonpairs.Fig.15.Rotational speed versus driving frequency under freeloading.Fig.16.Two-phase output voltages of phase-modulation driving circuit for drivingfrequency set at41kHz:the phase regulated as equal value.2772T.-C.Chen et al./Energy Conversion and Management49(2008)2767–2775at 40kHz are shown in Fig.12.Even if the phase in the phase shifter circuit was slightly affected by the operating driving frequency,the output signals in phase A and B can still maintain symmetrical amplitude and the range of phase difference reaches ±p /2rad.By observing the characteristics of the measured phase difference angle versus the phase-modulated voltage (V p ),shown in Fig.13,we found that the relationship between the phase difference angle (U )and phase-modulated voltage (V p )is highly linear over a wide operating range under different driving frequencies.3.4.Power amplifiers and transformerA practical circuit using ClassB elements is a complementary pair or push–pull arrangement.Here,complementary devices are used to each amplify the opposite halves of the input signal,which is then recombined at the output.This arrangement gives excellent efficiency,but can suffer from the drawback of a small glitch at the joins between the two halves of the signal,a problem known as crossover distortion.A solution to this is to bias the devices just on,rather than off altogether,when they are not in use.One way to greatly boost the current gain (A I )of a Class B push–pull ampli-fier is to use Darlington pairs instead of single transistors,shown in Fig.14.Since this USM presents a large capacitive load and requires a high operating frequency,its equivalent impedance could be extre-mely low.This USM also requires a high drive voltage,which leads to a large drive current.Hence,a ferrite-core transformer which features high efficiency,small size,and light weight,was chosen to isolate and boost the high frequency AC voltage.The non-reso-nant power amplifier circuits are designed in order to provide two-phase,phase A and B,sinusoid output voltages V A and V B with the same amplitude under the variable frequency and phase con-trol.According to experiment test in Section 4,the amplitude of the output voltage will not be affected by the variation of the qual-ity when the driving frequency is operated closely to the resonant frequency of the TWUSM.The phase B power amplifier circuit is designed using the same method as for phase A.4.Experimental resultsA prototype of power driver for a TWUSM was built and tested.Based on the circuit design of TWUSM driver discussed above,mo-tor performance was measured by experimental results.There are three basic input signals for the TWUSM:frequency,independence amplitude,and phase.It is important to confirm the driving char-acteristics for eachparameter.Fig.17.Experimental results of phase-modulation driving circuit for driving frequency set at 41kHz,10l s/div.(a)Two-phase output voltages with phase difference p /6for CW rotation.(b)Two-phase output voltages with phase difference p /6for CCWrotation.Fig.18.Experimental results of phase-modulation driving circuit for driving frequency set at 41kHz,10l s/div.(a)Two-phase output voltages with phase difference p /3for CW rotation.(b)Two-phase output voltages with phase difference p /3for CCW rotation.T.-C.Chen et al./Energy Conversion and Management 49(2008)2767–27752773First,we measured the rotational speed in relation to the driv-ing frequency in Fig.15.The mechanical resonant frequency of the USM (USR-60)ranges from 39to 40kHz in the ultrasonic fre-quency range.The switching frequency of the voltage-controlled oscillator,which is designed to vary between 40.5and 44kHz,should be higher than the resonant frequency of the mechanical vibration.The highest rotational speeds around the phase differ-ence p /2were roughly 229and 221rpm in the direction of CW and CCW,respectively.The frequency,at around 40.5kHz,is nearly the same as the natural resonance frequency of TWUSM as de-scribed above.This characteristic is the same as that of a conven-tional single-frequency-mode control ultrasonic motor.The vibration velocity becomes high near the resonant frequency of the stator,which means the rotational velocity of the rotor reaches its maximum value.Subsequently,we tested the rotational speed in relation to the phase difference.The phase shifter circuit worked as mentioned above.The control input to the drive circuit (V p )is calculated by the control algorithm.According to the control input,the phase dif-ference (U )is regulated by means of the designed phase shifter cir-cuit.The phase shifter circuit is designed for the two-phase power amplifier to provide two-phase output voltages V A and V B with var-iable phase difference,where the rotational direction (CW or CCW)can be controlled by allowing either V A or V B to lead.In order to as-sess the performance and stability of the proposed phase-mode driver for TWUSM,the phase differences of two-phase AC outputvoltage has been regulated from 0to ±p /2rad,shown in Figs.16–19,respectively.The two-phase sinusoid output V A and V B can thus be maintained at the same constant peak value at the switching frequency under varying phase-modulation processes.The driving phase difference of the designed phase-shifter circuit is the major control variable,and balanced two-phase sinusoid output voltages with the same amplitudes and variable-phase control results in satisfactory control performance of the TWUSM servo drive.Fig.20shows the experimental results of the Speed versus phase difference curves under variable operating driving frequencies.Experimental results confirm that the rotor could be rotated using the design driving circuit.By comparison,the phase-mode driving can offer a much wider controllable range,which verifies that the proposed driver circuit can successfully adapt the change of com-mand signals.In addition to these advantages,only the phase shift parameter can control the rotational direction of a rotor,which the phase-shift varies between p /2and Àp /2.5.ConclusionsUSMs are potentially interesting for a number of industry appli-cations,such as miniature robotics.Their electrical drive circuits present unique challenges,particularly in producing signals of several hundred volts and tens of kilohertz with variable phase dif-ferences,inputted to a low impedance capacitive motor,whileFig.20.Rotational speed versus phase difference under difference operating drivingfrequency.Fig.19.Experimental results of phase-modulation driving circuit for driving frequency set at 41kHz,10l s/div.(a)Two-phase output voltages with phase difference p /2for CW rotation.(b)Two-phase output voltages with phase difference p /2for CCW rotation.2774T.-C.Chen et al./Energy Conversion and Management 49(2008)2767–2775。
雕刻机毕业设计外文文献翻译
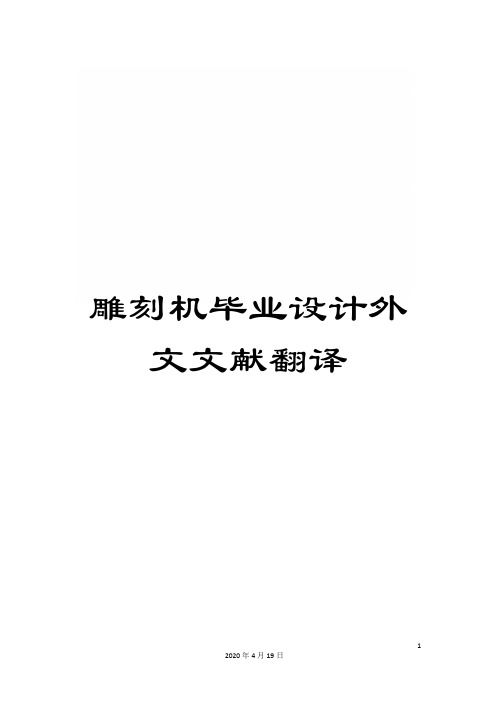
雕刻机毕业设计外文文献翻译附录1 外文翻译-原文部分DXF File Identification with C# for CNC Engraving Machine System Huibin Yang, Juan YanAbstractThis paper researches the main technology of open CNC engraving machine,the DXF identification technology. Agraphic information extraction method is proposed. By this method,the graphic information in DXF file can be identified and transformed into bottom motion controller’s code. So the engraving machine can achieve trajectory tracking. Then the open CNC engraving machine system is developed with C#. At last, the method is validated on a three axes motion experiment platform. The result shows that this method can efficiently identify the graphic information including line, circle, arc etc. in DXF file and the CNC engraving machine can be controlled well. KeywordsDXF, CNC Engraving Machine , GALIL,C#1.IntroductionWith the development of pattern recognition techniques, modern CNC engraving machine needn’t be programmed manually. By importing graphics file, the corresponding shape will be engraved by the machine immediately. The operating process of the machine is simplified enormously, and the rich programming knowledge is no longer need for operators. Among them, DXFidentification is a key technology of CNC engraving machine. By reading and recognition of the DXF file, the machining track can be directly generated, so the motion control of the CNC engraving machine can be achieved.2. Research StatusResearchers have done a lot of researches on how to contact CAD software to NC code. Omirou and Barouniproposed a series of machine codes, with which the advanced programming ability is integrated into the control of modern CNC milling machine system [1]. Kovacic and Brezocnik proposed the concept of which using the genetic algorithm to program the CNC machine based on the CAD model under manufacturing environment [2].But some problems are still existed in this kind of CNC programming (such as the artificial participation degree is higher and the efficiency is lower).The research direction of Chinese researchers mainly includes two aspects. One is the theoretical study of DXF file and NC machining, the other is the application of DXF file reading. ZhaiRui and Zhang Liang proposed a program structure, which is used to read data information of DXF file and do some preprocess based on the cross platform open source library DXF Lib by the analysis of DXF file structure characteristic [3]. Huang Jieqiong and Yuan Qun wrote the interface program to read the stored parts graphic information in DXF file by use of the object-oriented secondary development tools, Object ARX and C++, in the research of stamping parts machining. The stamping parts geometric model is automatically created by the automatic generationalgorithm of closed contour [4].3. DXF File and Graphic Information Extraction3.1. DXF FileDXF (Drawing Exchange File) is a representation of all information labeled data contained in the AutoCAD graphics file, and the ASCII or binary file format of AutoCAD file. It can be used as input/output interface and graphics file exchange between AutoCAD and other graphics applications [5].A complete DXF file is composed of six segments called SECTION. These segments were HEADER,CLASSES, TABLES, BLOCKS, ENTITIES and file ending character (group code is 0,group value is EOF)3.2. Graphic Information Extraction MethodIn order to extract useful information of the graphic, many parts in the file can be ignored. The corresponding geometric description can be completed as long as the sections of TABLES,BLOCK, ENTITIES are obtained. Each graphic element in the DXF file are stored with a fixed format, so it is convenient for data exchange, and also called its readability. The characteristics of each individual graphic element in DXF file is described by the parameter (group) consisted by paired group code and group value. Therefore, according to the target of open CNC engraving machine, it is enough to describe the target geometry contour by reading the ENTITIES section in DXF files only. The particular identification process is: First search the DXF file until the “ENTITLES” is found, then build a graphic element object. Then search the graphic element type (LINE, CIRCLE, ARC),and search the corresponding value followed by the group code. For example, if the program has found the ENTITLES section and confirm the first graphic element is LINE (The program found “LINE” after “ENTITLES”). Then it will search the group code which represents the。
机械毕业设计外文翻译---数控机床

What Is CNCCNC stands for Computer Numerical Control and has been around since the early 1970''s. Prior to this, it was called NC, for Numerical Control. (In the early 1970''s, computers were introduced in these controls, hence the name changed)While people in most walks of life have never heard of this term, CNC has touched almost every form of manufacturing process in one way or another. If you''ll be working in manufacturing, it''s likely that you''ll be dealing with CNC on a regular basis.Before CNCWhile there are exceptions to this statement, CNC machines typically replace (or work in conjunction with) some existing manufacturing process/es. Take one of the simplest manufacturing processes, drilling holes, for example.A drill press can of course be used to machine holes. (It''s likely that almost everyone has seen some form of drill press, even if you don''t work in manufacturing.) A person can place a drill in the drill chuck that is secured in the spindle of the drill press. They can then (manually) select the desired speed for rotation (commonly by switching belt pulleys), and activate the spindle. Then they manually pull on the quill lever to drive the drill into the workpiece being machined.As you can easily see, there is a lot of manual intervention required to use a drill press to drill holes. A person is required to do something almost every step along the way! While this manual intervention may be acceptable for manufacturing companies if but a small number of holes or workpieces must be machined, as quantities grow, so does the likelihood for fatigue due to the tediousness of the operation. And do note that we''ve used one of the simplest machining operations (drilling) for our example. There are more complicated machining operations that would require a much higher skill level (and increase the potential for mistakes resulting in scrap workpieces) of the person running the conventional machine tool. (We commonly refer to the style of machine that CNC is replacing as the conventional machine.)By comparison, the CNC equivalent for a drill press (possibly a CNC machining center or CNC drilling & tapping center) can be programmed to perform this operation in a much more automatic fashion. Everything that the drill press operator was doing manually will now be done by the CNC machine, including: placing the drill in the spindle, activating the spindle, positioning the workpiece under the drill, machining the hole, and turning off the spindle.How CNC worksThere is another article included in this web site called The Basics of CNC that explains how to program, setup, and operate CNC machines in greater detail. Additionally, we offer a series of products aimed at helping you learn how to use CNC machines. Here we''re relating how CNC works in very general terms.As you might already have guessed, everything that an operator would be required to do with conventional machine tools is programmable with CNC machines. Once the machine is setup and running, a CNC machine is quite simple to keep running. In fact CNC operators tend to get quite bored during lengthy production runs because there is so little to do. With some CNC machines, even the workpiece loading process has been automated. (We don''t mean toover-simplify here. CNC operators are commonly required to do other things related to the CNC operation like measuring workpieces and making adjustments to keep the CNC machine running good workpieces.)Let''s look at some of the specific programmable functions.Motion controlAll CNC machine types share this commonality: They all have two or more programmable directions of motion called axes. An axis of motion can be linear (along a straight line) or rotary (along a circular path). One of the first specifications that implies a CNC machine''s complexity is how many axes it has. Generally speaking, the more axes, the more complex the machine.The axes of any CNC machine are required for the purpose of causing the motions needed for the manufacturing process. In the drilling example, these (3) axis would position the tool over the hole to be machined (in two axes) and machine the hole (with the third axis). Axes are named with letters. Common linear axis names are X, Y, and Z. Common rotary axis names are A, B, and C.Programmable accessoriesA CNC machine wouldn''t be very helpful if all it could only move the workpiece in two or more axes. Almost all CNC machines are programmable in several other ways. The specific CNC machine type has a lot to do with its appropriate programmable accessories. Again, any required function will be programmable on full-blown CNC machine tools. Here are some examples for one machine type.Machining centersAutomatic tool changerMost machining centers can hold many tools in a tool magazine. When required, the required tool can be automatically placed in the spindle for machining.Spindle speed and activationThe spindle speed (in revolutions per minute) can be easily specified and the spindle can be turned on in a forward or reverse direction. It can also, of course, be turned off.CoolantMany machining operations require coolant for lubrication and cooling purposes. Coolant can be turned on and off from within the machine cycle.The CNC programThink of giving any series of step-by-step instructions. A CNC program is nothing more than another kind of instruction set. It''s written in sentence-like format and the control will execute it in sequential order, step by step.A special series of CNC words are used to communicate what the machine is intended to do. CNC words begin with letter addresses (like F for feedrate(馈送率), S for spindle speed, and X, Y & Z for axis motion). When placed together in a logical method, a group of CNC words make up a command that resemble a sentence.For any given CNC machine type, there will only be about 40-50 words used on a regular basis. So if you compare learning to write CNC programs to learning a foreign language having only50 words, it shouldn''t seem overly difficult to learn CNC programming.The CNC controlThe CNC control will interpret a CNC program and activate the series of commands in sequential order. As it reads the program, the CNC control will activate the appropriate machine functions, cause axis motion, and in general, follow the instructions given in the program.Along with interpreting the CNC program, the CNC control has several other purposes. All current model CNC controls allow programs to be modified (edited) if mistakes are found. The CNC control allows special verification functions (like dry run) to confirm the correctness of the CNC program. The CNC control allows certain important operator inputs to be specified separate from the program, like tool length values. In general, the CNC control allows all functions of the machine to be manipulated.What is a CAM system?For simple application (like drilling holes), the CNC program can be developed manually. That is, a programmer will sit down to write the program armed only with pencil, paper, and calculator. Again, for simple applications, this may be the very best way to develop CNC programs.As applications get more complicated, and especially when new programs are required on a regular basis, writing programs manually becomes much more difficult. To simplify the programming process, a computer aided manufacturing (CAM) system can be used. A CAM system is a software program that runs on a computer (commonly a PC) that helps the CNC programmer with the programming process. Generally speaking, a CAM system will take the tediousness and drudgery out of programming.What is a DNC system?Once the program is developed(either manually or with a CAM system), it must be loaded into the CNC control. Though the setup person could type the program right into the control, this would be like using the CNC machine as a very expensive typewriter. If the CNC program is developed with the help of a CAM system, then it is already in the form of a text file . If the program is written manually, it can be typed into any computer using a common word processor (though most companies use a special CNC text editor for this purpose). Either way, the program is in the form of a text file that can be transferred right into the CNC machine. A distributive numerical control (DNC) system is used for this purpose.A DNC system is nothing more than a computer that is networked with one or more CNC machines. Until only recently, rather crude serial communications protocol (RS-232c) had to be used for transferring programs. Newer controls have more current communications capabilities and can be networked in more conventional ways (Ethernet, etc.). Regardless of methods, the CNC program must of course be loaded into the CNC machine before it can be run.中文翻译:什么数控机床数控机床代表计算机数字控制机床,并且从20世纪70年代以来一直受到人们的关注。
- 1、下载文档前请自行甄别文档内容的完整性,平台不提供额外的编辑、内容补充、找答案等附加服务。
- 2、"仅部分预览"的文档,不可在线预览部分如存在完整性等问题,可反馈申请退款(可完整预览的文档不适用该条件!)。
- 3、如文档侵犯您的权益,请联系客服反馈,我们会尽快为您处理(人工客服工作时间:9:00-18:30)。
附录1外文翻译-原文部分DXF File Identification with C# for CNC Engraving Machine System Huibin Yang, Juan YanAbstractThis paper researches the main technology of open CNC engraving machine,the DXF identification technology. Agraphic information extraction method is proposed. By this method,the graphic information in DXF file can be identified and transformed into bottom motion controller’s code. So the engraving machine can achieve trajectory tracking. Then the open CNC engraving machine system is developed with C#. At last, the method is validated on a three axes motion experiment platform. The result shows that this method can efficiently identify the graphic information including line, circle, arc etc. in DXF file and the CNC engraving machine can be controlled well.KeywordsDXF, CNC Engraving Machine , GALIL,C#1.IntroductionWith the development of pattern recognition techniques, modern CNC engraving machine needn’t be programmed manually. By importing graphics file, the corresponding shape will be engraved by the machine immediately. The operating process of the machine is simplified enormously, and the rich programming knowledge is no longer need for operators. Among them, DXF identification is a key technology of CNC engraving machine. By reading and recognition of the DXF file, the machining track can be directly generated, so the motion control of the CNC engraving machine can be achieved.2. Research StatusResearchers have done a lot of researches on how to contact CAD software to NC code. Omirou and Barouniproposed a series of machine codes, with which the advanced programming ability is integrated into the control of modern CNC milling machine system [1]. Kovacic and Brezocnik proposed the concept of which using the genetic algorithm to program the CNC machine based on the CAD model under manufacturing environment [2].But some problems are still existed in this kind of CNC programming (such as the artificial participation degree is higher and the efficiency is lower).The research direction of Chinese researchers mainly includes two aspects. One is the theoretical study of DXF file and NC machining, the other is the application of DXF file reading. ZhaiRui and Zhang Liang proposed a program structure, which is used to read data information of DXF file and do some preprocess based on the cross platform open source library DXF Lib by the analysis of DXF file structure characteristic [3]. Huang Jieqiong and Yuan Qun wrote the interface program to read the stored parts graphic information in DXF file by use of the object-oriented secondary development tools, Object ARX and C++, in the research of stamping parts machining. The stamping parts geometric model is automatically created by the automatic generation algorithm of closed contour [4].3. DXF File and Graphic Information Extraction3.1. DXF FileDXF (Drawing Exchange File) is a representation of all information labeled data contained in the AutoCAD graphics file, and the ASCII or binary file format of AutoCAD file. It can be used as input/output interface and graphics file exchange between AutoCAD and other graphics applications [5].A complete DXF file is composed of six segments called SECTION. These segments were HEADER,CLASSES, TABLES, BLOCKS, ENTITIES and file ending character (group code is 0,group value is EOF)3.2. Graphic Information Extraction MethodIn order to extract useful information of the graphic, many parts in the file can be ignored. The corresponding geometric description can be completed as long as the sections of TABLES,BLOCK, ENTITIES are obtained. Each graphic element in the DXF file are stored with a fixed format, so it is convenient for data exchange, and also called its readability. The characteristics of each individual graphic element in DXF file is described by the parameter (group) consisted by paired group code and group value. Therefore, according to the target of open CNC engraving machine, it is enough to describe the target geometry contour by reading the ENTITIES section in DXF files only. The particular identification process is: First search the DXF file until the “ENTITLES” is found, then build a graphic element object. Then search the graphic element type (LINE, CIRCLE, ARC),and search the corresponding value followed bythe group code. For example, if the program has found the ENTITLES section and confirm the first graphic element is LINE (The program found “LINE” after “ENTITLES”). Then it will search the group code which represents the parameters of the line. The number at the next line after the group code is the value of the parameter.(e.g. The number at the next line after “10” represent the X value of start point of this line, and “20” for Y value of start point,“11” for X value of end point,“21” for Y value of end point, etc.). Table 1 shows an example of an ENTITIES section. Table 1 shows an example of an ENTITIES section.By getting these parameters and values, system then “sees” the graph and “knows” the specific parameters of the graph which is drew by AutoCAD. Figure 1 is the flow diagram of extraction of graphic information. Table 1 shows an example of an ENTITIES section.3.3. C# Realization of Graphic Information ExtractionIn order to store the graph data, the convenient method is to store numeric variables by using array, and it is also very convenient for call and assignment operation. First define a 2D array:s[i,j] (i <= 100,j <= 20),define a 100 lines and 20 lows array at initialization, in which, every line i stores a graphic element, every element j in a line stands for the value after the group code. The format and meaning are shown in Table 2Then, the graphic element storage state is s[i,0],s[i,1],⋅⋅⋅,s[i,15] (I = 0,1,2,⋅⋅⋅).The advantage of this design is: For each graphic element, all the geometric elements associated with the trajectory can be stored in an array variable space which has a fixed serial number. It is convenient and not easy to make mistakes in the calculation or logical judgment. But to any entire graphics trajectory, the number of lines or curves is not consistent, so it is important to apply for enough variable memory space to adapt to different requirements of graphics trajectory. Part of the C# program of reading arc graphic element in DXF are as follows:do{Line = mysr. ReadLine ();if (Line == “ENTITIES”){……if (Line == “10”){Line = mysr.ReadLine();string m;m = Line;double n;n = Convert.ToDouble(m);s[i,j] = n;j++;}……} while (Line! = null)4. Graphics Trajectory GenerationTo open CNC engraving machine,the key point is how to convert the graphic element information in DXF file into motion controller code, so as to control the machine’s motion according to the machining trajectory.4.1. DXF Analysis PrincipleThe so-called DXF analysis is the standardization of each graphic element which has been read in order to according with the standard instructions of motion controller. Considering the basic type of graphic element is line, circle or arc, the standardization requirements of different graphic element type are different. The specific principles are as follows:1) LINELine has only start and end point coordinate. the actual useful memory space is s[i,0],s[i,1],…,s[i,6],other parts are all zero.2) ARCAs the format of arc in the DXF is include the center coordinates value, radius, start angle andend angle. So the center coordinates value, radius, start angle and end angle can be recognized and stored in s[i,7],s[i,8],…,s[i,12] .But for the GALIL DMC2143 motion controller which is used in the open CNC engraving machine,the arc instruction requires start and end point coordinate and rotation angle of the arc. So, the analysis of arc includes two aspects: a) Calculate the start and end point coordinate. b) Calculate the rotation angle and store in s [i,15].3) CIRCLEBecause the rotation angle of circle is 360˚,it can be set as a fixed value. For the sake of convenience, the starting position of circle is set to the left or right quadrantal points.4.2. DXF Analysis MethodAccording to 3.1, the difficulty of graphic element analysis is arc. Although the information in DXF file can confirm geometry feature, for the track sequencing, the start and end point coordinates are needed; and for the motion controller programs, it also need to change the format for direct connection. By four elements of center, radius, start angle and end angle as well as simple trigonometric function calculation, the start and end point position as well as the rotation angle of the arc can be determined. For example, if center of the arc is o(x0,y0),radius is r, start angle is θ (0 < θ < 90˚) and end angle is δ (0 < θ < 90˚),according to the parametric equation of the circle, the start point a(x1,y1),end point b(x2,y2),and rotation angle ε can be calculated using Equation (1) to Equation (3):5. Development of Open CNC Engraving Machine SystemThe hardware of the open CNC engraving machine system includes a motion controller and an upper computer (PC). The real-time control of the CNC engraving machine body is done by the motion controller. The main task of the motion controller is servo motor control and IO logic control. The PC runs The DXF analysis algorithm, Human-Machine Interface (HMI) and sends the motion control instructions got from the DXF analysis algorithm to the motion controller, so the engraving machine can be controlled. The software of the system includes PC program and motion controller program.5.1. PC ProgramThe PC program includes HMI and DXF analysis program running in the background. DXF analysis program are mainly programmed based on DXF analysis principles and methods on 3.5.2. Program Design of Motion ControllerIn this design, the subprograms of linear and circular interpolation are programmed in GALIL motion controller. According to the results of DXF analysis in PC, call different subprogram in proper order and assign variable, the continuous tracking trajectory can be realized. The linear interpolation program of GALIL motion controller is as follows:#LINEARMT 2,2VMABVS 5000V A 100000VD 100000VP X,YVEBGSEN6. Test Running ResultBy C#, the authors first finished the DXF file identification as well as the extraction and storage of graphic element information. The graphic element ordering operations were also achieved. At last,the graphics trajectories were generated by calling the bottom GALIL software instructions and achieved motion tacking. The test was carried out on a three axes motion experiment platform, the carving cutter was replaced with pen. Pen was fixed on the experiment platform. The test used a trajectory graph drawn by AutoCAD. The final result shows that the developed open CNC engraving machine system can accurately complete the identification of DXF file, and the walk path is consistent with the CAD file.References[1] Omirou Sotiris,L. and Barouni Antigoni,K. (2005) Integration of New Programming Capabilities into a CNC MillingSystem. Robotics and Computer-Integrated Manufacturing,21,518-527. /10.1016/j.rcim.2004.10.002[2] Kovacic,M.,Brezocnik,M.,Pahole,I.,Balic,J. and Kecelj,B. (2005) Evolutionary Programming of CNC Machines.Journal of Materials Processing Technology,164-165,1379-1387. /10.1016/j.jmatprotec.2005.02.047[3] Zhai,R. and Zhang,L. (2011) Reading Frame Design Based on the DXF File Format. Fujian Computer,4,107-109.[4] Huang,J.Q. and Yuan,Q. (2012) Automatic Input and Identification for Stamping Graph Based on AutoCAD. Machinery Design & Manufacture,2,82-84.[5] Bai,X.C. and Chen,Y.M. (2010) Automatic Programming of Bridge Cutting Machine Based on the DXF File. Equipment Manufacturing Technology,2,110-112.附录2外文翻译-中文部分利用C#识别DXF文件的数控雕刻机系统Huibin Yang, Juan Yan摘要本文研究开放式数控雕刻机的关键技术,即DXF识别技术。