螺旋铣程序
西门子宏程序铣螺纹教程
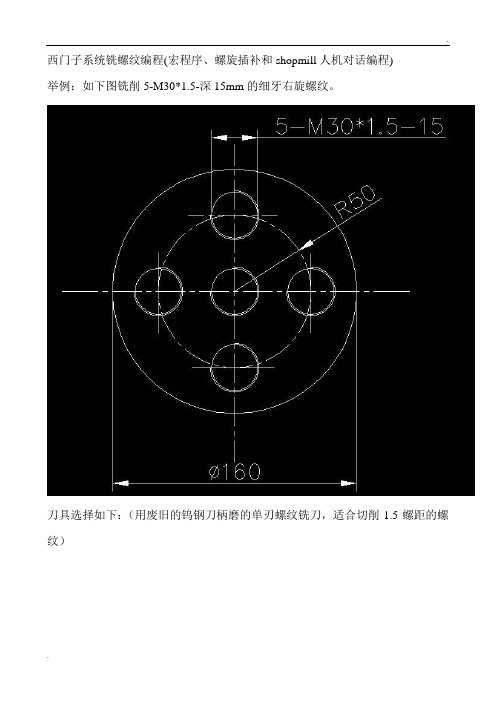
西门子系统铣螺纹编程(宏程序、螺旋插补和shopmill人机对话编程)举例:如下图铣削5-M30*1.5-深15mm的细牙右旋螺纹。
刀具选择如下:(用废旧的钨钢刀柄磨的单刃螺纹铣刀,适合切削1.5螺距的螺纹)工艺分析:三轴联动铣削螺纹,实质是XY平面加工整圆同时,Z轴每加工一个整圆下降一个螺纹,加工时是以螺纹孔的中心轴线作为编程参考点,所以铣削单个螺纹孔时,通常将坐标系原点建立在孔中心,若要铣削多个螺孔,就要试着将坐标系偏移至孔的中心。
这题要铣削5个孔,中间的孔直接可以铣削,R50圆周上的4个等分螺孔,可以借助坐标偏移(西门子系统用TRANS)实现。
M30*1.5的螺纹,事先将螺纹底孔加工到28.5mm,螺纹齿高H=0.974刀具直径经检测,直径为8mm,有效加工孔深为22mm,程序如下:1、宏程序铣削螺纹单个螺纹孔铣削程序G54 G90 G17 G64 坐标系原点建立在孔的中心,底孔事先加工好M03 S3500 (单刃切削,高转速,小吃刀,快进给)G00 Z50.G00 X0 Y0G00 Z3. (安全高度,定位值是螺距的整倍数)R1=0.3 齿高切深赋值NN1: R2=10.25 + R1 (单边14.25,刀半径4,刀具往内偏移到10.25定位)G02 X=R2 Y0 I =R2/2 J0 F300. 以半圆形式切入R3=1.5 螺距PNN2: G02 X=R2 Y0 Z=R3 I= - R2 J0 F3000. 插补螺纹,到Z1.5的高度R3 = R3 - 1.5IF R3 >= - 15.1 GOTOB NN2 螺纹切削孔深15mmG02 X0 Y0 I = - R2/2 J0 F300. 半圆形式切出,刀具到中心G00 Z3. 抬刀到安全高度,前后一致R1 = R1 + 0.2 切削齿高,往X方向增大IF R1 <= 0.91 GOTOB NN1 加工到齿高G01 X0 Y0 F300. 退刀G00 Z100. 抬刀M30本题5-M30*1.5-15的程序主程序:G54 G90 G17 G64 坐标系原点建立在孔的中心,底孔事先加工好M03 S3500 (单刃切削,高转速,小吃刀,快进给)G00 Z50.G00 X0 Y0L1000 P1 调用铣床螺纹的子程序R4 = 0 角度初始赋值NN3: R5 = 50 * COS ( R4 ) X坐标R6 = 50 * SIN ( R4) Y坐标TRANS X=R5 Y=R6 坐标偏移G00 X0 Y0 到偏移之后的原点定位L1000 P1 调用铣螺纹的子程序R4 = R4 + 90 角度增加IF R4 <= 271 GOTOB NN3 加工剩余3孔,要是写360,第一个孔要再加工一次G00 Z100.TRANS 后面不跟任何数值,单独占一段,取消偏移G54 G00 X100. Y100.M30子程序:L1000;G00 X0 Y0G00 Z3. (安全高度,定位值是螺距的整倍数)R1=0.3 齿高切深赋值NN1: R2 =10.25 + R1 (单边14.25,刀半径4,刀具往内偏移到10.25定位)G02 X=R2 Y0 I =R2/2 J0 F300. 以半圆形式切入R3=1.5 螺距PNN2: G02 X=R2 Y0 Z=R3 I= - R2 J0 F3000. 插补螺纹,到Z1.5的高度R3 = R3 - 1.5IF R3 >= - 15.1 GOTOB NN2 螺纹切削孔深15mmG02 X0 Y0 I = - R2/2 J0 F300. 半圆形式切出,刀具到中心G00 Z3. 抬刀到安全高度,前后一致R1 = R1 + 0.2 切削齿高,往X方向增大IF R1 <= 0.91 GOTOB NN1 加工到齿高G01 X0 Y0 F300. 退刀G00 Z10. 抬刀TRANS 后面不跟任何数值,单独占一段,取消偏移M17 返回主程序2、利用螺旋插补加工螺纹单个螺纹孔铣削程序G54 G90 G17 坐标系原点建立在孔的中心,底孔事先加工好M03 S3500 (单刃切削,高转速,小吃刀,快进给)G00 Z50.G00 X0 Y0G00 Z3. (安全高度,定位值是螺距的整倍数)R1=0.3 齿高切深赋值NN1: R2= 10.25 + R1 (单边14.25,刀半径4,刀具往内偏移到10.25定位)G02 X=R2 Y0 I = R2/2 J0 F300. 以半圆形式切入G02 X0 Y0 Z-15 I = - R2 J0 TRUN=11 F3000. 每次1.5,重复11次G02 X0 Y0 I = - R2/2 J0 F300. 半圆形式切出,刀具到中心G00 Z3. 抬刀到安全高度,前后一致R1 = R1 + 0.2 切削齿高,往X方向增大IF R1 <= 0.91 GOTOB NN1 加工到齿高G01 X0 Y0 F300. 退刀G00 Z100. 抬刀M30本题5-M30*1.5-15的程序主程序:G54 G90 G17 坐标系原点建立在孔的中心,底孔事先加工好M03 S3500 (单刃切削,高转速,小吃刀,快进给)G00 Z50.G00 X0 Y0L1000 P1 调用铣床螺纹的子程序R4 = 0 角度初始赋值NN3: R5 = 50 * COS ( R4 ) X坐标R6 = 50 * SIN ( R4 ) Y坐标TRANS X=R5 Y=R6 坐标偏移G00 X0 Y0 到偏移之后的原点定位L1000 P1 调用铣螺纹的子程序R4 = R4 + 90 角度增加IF R4 <= 271 GOTOB NN3加工剩余3个孔,要是写360,第一个孔要再加工一次G00 Z100.TRANS 后面不跟任何数值,单独占一段,取消偏移G54 G00 X100. Y100.M30子程序:L1000;G00 X0 Y0G00 Z3. (安全高度,定位值是螺距的整倍数)R1=0.3 齿高切深赋值NN1: R2 = 10.25 + R1 (单边14.25,刀半径4,刀具往内偏移到10.25定位)G02 X=R2 Y0 I = R2/2 J0 F300. 以半圆形式切入G02 X0 Y0 Z-15 I = - R2 J0 TRUN=11 F3000. 每次1.5,重复11次G90 G02 X0 Y0 I = - R2/2 J0 F300. 半圆形式切出,刀具到中心G00 Z3. 抬刀到安全高度,前后一致R1 = R1 + 0.2 切削齿高,往X方向增大IF R1 <= 0.91 GOTOB NN1 加工到齿高G01 X0 Y0 F300. 退刀G00 Z10. 抬刀TRANS 后面不跟任何数值,单独占一段,取消偏移M17 返回主程序3、利用shopmill人机对话编程ShopMill ——内螺纹铣削说明:abs—绝对值inc—相对值select—选择/切换按“help”(帮助)可以切换视图。
螺旋铣削宏程序
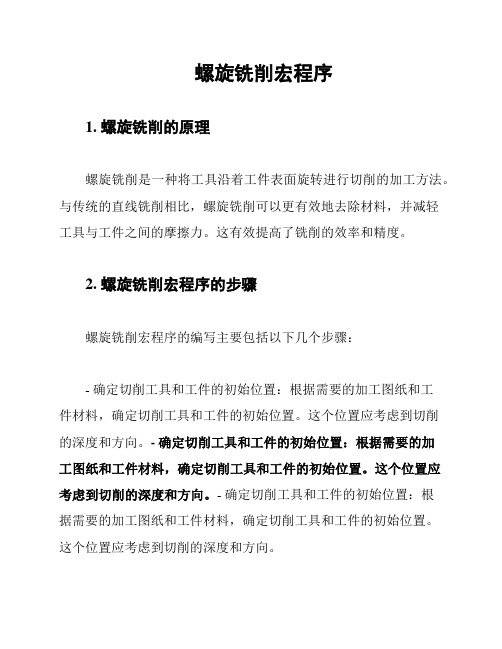
螺旋铣削宏程序1. 螺旋铣削的原理螺旋铣削是一种将工具沿着工件表面旋转进行切削的加工方法。
与传统的直线铣削相比,螺旋铣削可以更有效地去除材料,并减轻工具与工件之间的摩擦力。
这有效提高了铣削的效率和精度。
2. 螺旋铣削宏程序的步骤螺旋铣削宏程序的编写主要包括以下几个步骤:- 确定切削工具和工件的初始位置:根据需要的加工图纸和工件材料,确定切削工具和工件的初始位置。
这个位置应考虑到切削的深度和方向。
- 确定切削工具和工件的初始位置:根据需要的加工图纸和工件材料,确定切削工具和工件的初始位置。
这个位置应考虑到切削的深度和方向。
- 确定切削工具和工件的初始位置:根据需要的加工图纸和工件材料,确定切削工具和工件的初始位置。
这个位置应考虑到切削的深度和方向。
- 设置切削参数:根据需要的加工质量和效率,设置切削参数,如切削速度、进给速度和切削深度等。
这些参数应根据工具和工件的特性进行调整。
- 设置切削参数:根据需要的加工质量和效率,设置切削参数,如切削速度、进给速度和切削深度等。
这些参数应根据工具和工件的特性进行调整。
- 设置切削参数:根据需要的加工质量和效率,设置切削参数,如切削速度、进给速度和切削深度等。
这些参数应根据工具和工件的特性进行调整。
- 编写切削路径:根据加工图纸和要求,编写切削路径。
螺旋铣削的路径应沿着工件表面形成螺旋状的轨迹,以保证整个加工过程的稳定性和精度。
- 编写切削路径:根据加工图纸和要求,编写切削路径。
螺旋铣削的路径应沿着工件表面形成螺旋状的轨迹,以保证整个加工过程的稳定性和精度。
- 编写切削路径:根据加工图纸和要求,编写切削路径。
螺旋铣削的路径应沿着工件表面形成螺旋状的轨迹,以保证整个加工过程的稳定性和精度。
- 编写切削程序:根据切削路径,编写切削程序。
切削程序主要包括控制切削工具移动和设置相应的切削参数。
这些程序应根据具体的机床和控制系统进行编写。
- 编写切削程序:根据切削路径,编写切削程序。
螺纹铣刀的编程方法

(2)螺纹削程序(Fanuc系统) %
加工中心铣螺纹宏程序精华

加工中心铣螺纹宏程序精华-CAL-FENGHAI-(2020YEAR-YICAI)_JINGBIAN加工中心通用铣螺纹宏程序编程教程使用G03/G02三轴联动走螺旋线,刀具沿工件表面(孔壁或圆柱外表)切削。
螺旋插补一周,刀具Z向负方向走一个螺距量。
工作原理使用G03/G02三轴联动走螺旋线,刀具沿工件表面(孔壁或圆柱外表)切削。
螺旋插补一周,刀具Z向负方向走一个螺距量。
编程原理:G02 I3.等于螺距为2.5mm假设刀具半径为5mm则加工M16的右旋螺纹优势使用了三轴联动数控铣床或加工中心进行加工螺纹,相对于传统螺纹加工1、如螺距为2的螺纹铣刀可以加工各种公称直径,螺距为2mm的内外螺纹2、采用铣削方式加工螺纹,螺纹的质量比传统方式加工质量高3、采用机夹式刀片刀具,寿命长4、多齿螺纹铣刀加工时,加工速度远超攻丝5、首件通止规检测后,后面的零件加工质量稳定使用方法G65 P1999 X_ Y_ Z_ R_ A_ B_ C_ S_ F_XY 螺纹孔或外螺纹的中心位置X=#24 Y=#25Z 螺纹加工到底部,Z轴的位置(绝对坐标) Z=#26R快速定位(安全高度)开始切削螺纹的位置 R=#18A螺纹螺距A=#1B螺纹公称直径B=#2C螺纹铣刀的刀具半径C=#3 内螺纹为负数外螺纹加工为正数S主轴转速F进给速度,主要用于控制刀具的每齿吃刀量如: G65 p1999 X30 Y30 Z-10 R2 A2 B16 C-5 S2000 F150;在X30y30的位置加工 M16 螺距2 深10的右旋螺纹加工时主轴转速为2000转进给进度为150mm/min宏程序代码O1999;G90G94G17G40;G0X#24Y#25;快速定位至螺纹中心的X、Y坐标M3S#19;主轴以设定的速度正转#31=#2*+#3;计算出刀具偏移量#32=#18-#1;刀具走螺旋线时,第一次下刀的位置#33=#24-#31; 计算出刀具移动到螺纹起点的位置G0Z#18;刀具快速定位至R点G1X#33F#9;刀具直线插补至螺旋线的起点,起点位于X的负方向N20 G02Z-#32I#31;以偏移量作为半径,以螺距作为螺旋线Z向下刀量(绝对坐标)IF[#32LE#26]GOTO30;当前Z向位置大于等于设定Z向底位时,进行跳转#32=#32-#1;Z向的下个螺旋深度目标位置(绝对坐标)GOTO20;N30;IF[#3GT0]THEN #6=#33-#1;外螺纹,退刀时刀具往X负方向退一个螺IF[#3LT0]]THEN #6=#24;内螺纹,退刀时刀具移动到螺纹中心位置G0X#6G90G0Z#18;提刀至安全高度M99;G0X#6;下面有误下面程序为单齿螺纹铣刀宏程序编法:内梯形螺纹(Tr40x7)的宏程序系统:FANUC-oimait编程思想:每一层分中、右、左三分,每一刀的Z轴方向的起刀点都不同1、内梯形螺纹加工程序:G54G99M3S100T0101G0Z3X33#101=; 每一刀的的深度(半径)#102=4 梯形螺纹的深度(半径)#103=1 分层切削的次数N90 G0U[2*#101*#103]G32Z-32F7G0X32Z[3+[#102-#101]*+A]; A是槽底宽-刀尖宽的一半X33U[2*#101*#103]G32Z-32F7G0X32Z[3-[#102-#101]*] 梯形螺纹的牙顶宽:螺距梯形螺纹的牙底宽:螺距-牙顶宽-2倍的(螺纹深度Xtg15°)X33U[2*#101*#103]G32Z-32F7G0X32G0Z3X33#102=##103=#103+1IF[#103LE20]GOTO90;G0Z100M5M30螺纹铣削编程现以M20×右旋内螺纹铣削加工实例说明螺纹加工的编程方法。
加工中心铣螺纹宏程序精华

加工中心铣螺纹宏程序精华-CAL-FENGHAI-(2020YEAR-YICAI)_JINGBIAN加工中心通用铣螺纹宏程序编程教程使用G03/G02三轴联动走螺旋线,刀具沿工件表面(孔壁或圆柱外表)切削。
螺旋插补一周,刀具Z向负方向走一个螺距量。
工作原理使用G03/G02三轴联动走螺旋线,刀具沿工件表面(孔壁或圆柱外表)切削。
螺旋插补一周,刀具Z向负方向走一个螺距量。
编程原理:G02 I3.等于螺距为2.5mm假设刀具半径为5mm则加工M16的右旋螺纹优势使用了三轴联动数控铣床或加工中心进行加工螺纹,相对于传统螺纹加工1、如螺距为2的螺纹铣刀可以加工各种公称直径,螺距为2mm的内外螺纹2、采用铣削方式加工螺纹,螺纹的质量比传统方式加工质量高3、采用机夹式刀片刀具,寿命长4、多齿螺纹铣刀加工时,加工速度远超攻丝5、首件通止规检测后,后面的零件加工质量稳定使用方法G65 P1999 X_ Y_ Z_ R_ A_ B_ C_ S_ F_XY 螺纹孔或外螺纹的中心位置X=#24 Y=#25Z 螺纹加工到底部,Z轴的位置(绝对坐标) Z=#26R快速定位(安全高度)开始切削螺纹的位置 R=#18A螺纹螺距A=#1B螺纹公称直径B=#2C螺纹铣刀的刀具半径C=#3 内螺纹为负数外螺纹加工为正数S主轴转速F进给速度,主要用于控制刀具的每齿吃刀量如: G65 p1999 X30 Y30 Z-10 R2 A2 B16 C-5 S2000 F150;在X30y30的位置加工 M16 螺距2 深10的右旋螺纹加工时主轴转速为2000转进给进度为150mm/min宏程序代码O1999;G90G94G17G40;G0X#24Y#25;快速定位至螺纹中心的X、Y坐标M3S#19;主轴以设定的速度正转#31=#2*+#3;计算出刀具偏移量#32=#18-#1;刀具走螺旋线时,第一次下刀的位置#33=#24-#31; 计算出刀具移动到螺纹起点的位置G0Z#18;刀具快速定位至R点G1X#33F#9;刀具直线插补至螺旋线的起点,起点位于X的负方向N20 G02Z-#32I#31;以偏移量作为半径,以螺距作为螺旋线Z向下刀量(绝对坐标)IF[#32LE#26]GOTO30;当前Z向位置大于等于设定Z向底位时,进行跳转#32=#32-#1;Z向的下个螺旋深度目标位置(绝对坐标)GOTO20;N30;IF[#3GT0]THEN #6=#33-#1;外螺纹,退刀时刀具往X负方向退一个螺IF[#3LT0]]THEN #6=#24;内螺纹,退刀时刀具移动到螺纹中心位置G0X#6G90G0Z#18;提刀至安全高度M99;G0X#6;下面有误下面程序为单齿螺纹铣刀宏程序编法:内梯形螺纹(Tr40x7)的宏程序系统:FANUC-oimait编程思想:每一层分中、右、左三分,每一刀的Z轴方向的起刀点都不同1、内梯形螺纹加工程序:G54G99M3S100T0101G0Z3X33#101=; 每一刀的的深度(半径)#102=4 梯形螺纹的深度(半径)#103=1 分层切削的次数N90 G0U[2*#101*#103]G32Z-32F7G0X32Z[3+[#102-#101]*+A]; A是槽底宽-刀尖宽的一半X33U[2*#101*#103]G32Z-32F7G0X32Z[3-[#102-#101]*] 梯形螺纹的牙顶宽:螺距梯形螺纹的牙底宽:螺距-牙顶宽-2倍的(螺纹深度Xtg15°)X33U[2*#101*#103]G32Z-32F7G0X32G0Z3X33#102=##103=#103+1IF[#103LE20]GOTO90;G0Z100M5M30螺纹铣削编程现以M20×右旋内螺纹铣削加工实例说明螺纹加工的编程方法。
加工中心铣螺纹编程【详细版】
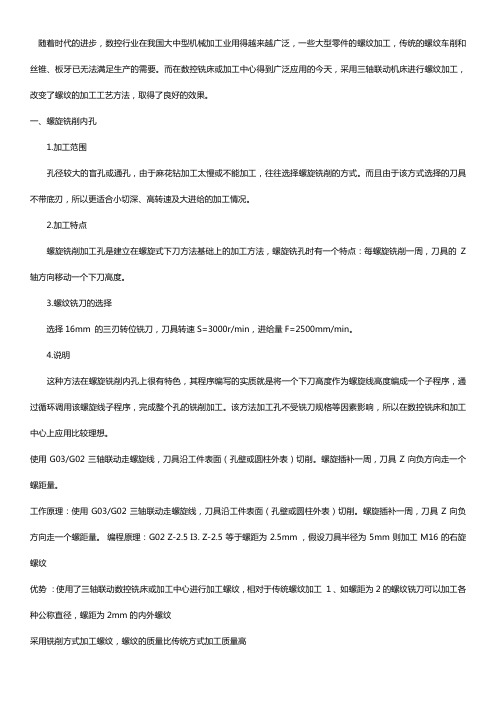
随着时代的进步,数控行业在我国大中型机械加工业用得越来越广泛,一些大型零件的螺纹加工,传统的螺纹车削和丝锥、板牙已无法满足生产的需要。
而在数控铣床或加工中心得到广泛应用的今天,采用三轴联动机床进行螺纹加工,改变了螺纹的加工工艺方法,取得了良好的效果。
一、螺旋铣削内孔1.加工范围孔径较大的盲孔或通孔,由于麻花钻加工太慢或不能加工,往往选择螺旋铣削的方式。
而且由于该方式选择的刀具不带底刃,所以更适合小切深、高转速及大进给的加工情况。
2.加工特点螺旋铣削加工孔是建立在螺旋式下刀方法基础上的加工方法,螺旋铣孔时有一个特点:每螺旋铣削一周,刀具的Z 轴方向移动一个下刀高度。
3.螺纹铣刀的选择选择16mm 的三刃转位铣刀,刀具转速S=3000r/min,进给量F=2500mm/min。
4.说明这种方法在螺旋铣削内孔上很有特色,其程序编写的实质就是将一个下刀高度作为螺旋线高度编成一个子程序,通过循环调用该螺旋线子程序,完成整个孔的铣削加工。
该方法加工孔不受铣刀规格等因素影响,所以在数控铣床和加工中心上应用比较理想。
使用G03/G02三轴联动走螺旋线,刀具沿工件表面(孔壁或圆柱外表)切削。
螺旋插补一周,刀具Z向负方向走一个螺距量。
工作原理:使用G03/G02三轴联动走螺旋线,刀具沿工件表面(孔壁或圆柱外表)切削。
螺旋插补一周,刀具Z向负方向走一个螺距量。
编程原理:G02 Z-2.5 I3. Z-2.5等于螺距为2.5mm ,假设刀具半径为5mm则加工M16的右旋螺纹优势:使用了三轴联动数控铣床或加工中心进行加工螺纹,相对于传统螺纹加工1、如螺距为2的螺纹铣刀可以加工各种公称直径,螺距为2mm的内外螺纹采用铣削方式加工螺纹,螺纹的质量比传统方式加工质量高采用机夹式刀片刀具,寿命长多齿螺纹铣刀加工时,加工速度远超攻丝首件通止规检测后,后面的零件加工质量稳定使用方法:G65 P1999 X_ Y_ Z_ R_ A_ B_ C_ S_ F_XY 螺纹孔或外螺纹的中心位置 X=#24 Y=#25Z 螺纹加工到底部,Z轴的位置(绝对坐标) Z=#26 R 快速定位(安全高度)开始切削螺纹的位置 R=#18 A 螺纹螺距 A=#1 B 螺纹公称直径 B=#2C 螺纹铣刀的刀具半径 C=#3 内螺纹为负数外螺纹加工为正数 S 主轴转速F 进给速度,主要用于控制刀具的每齿吃刀量如: G65 p1999 X30 Y30 Z-10 R2 A2 B16 C-5 S2000 F150;在X30y30的位置加工 M16 螺距2 深10的右旋螺纹加工时主轴转速为2000转进给进度为150mm/min 宏程序代码 O1999;G90G94G17G40;G0X#24Y#25; 快速定位至螺纹中心的X、Y坐标 M3S#19; 主轴以设定的速度正转 #31=#2*0.5+#3; 计算出刀具偏移量#32=#18-#1; 刀具走螺旋线时,第一次下刀的位置 #33=#24-#31; 计算出刀具移动到螺纹起点的位置 G0Z#18;刀具快速定位至R点G1X#33F#9; 刀具直线插补至螺旋线的起点,起点位于X的负方向N20 G02Z-#32I#31;以偏移量作为半径,以螺距作为螺旋线Z向下刀量(绝对坐标) IF[#32LE#26]GOTO30; 当前Z向位置大于等于设定Z向底位时,进行跳转 #32=#32-#1; Z向的下个螺旋深度目标位置(绝对坐标) GOTO20; N30; IF[#3GT0]THEN #6=#33-#1; 外螺纹,退刀时刀具往X负方向退一个螺距量 IF[#3LT0]]THEN #6=#24; 内螺纹,退刀时刀具移动到螺纹中心位置 G0X#6G90G0Z#18; 提刀至安全高度加工M75螺距1.5的内螺纹 %O0001(Tool cutting diameter = 63 mm - Fanuc 11M Controller.) G90 G00 G57 X0 Y0 G43 H10 Z0 M3 S353 G9 1 G00 X0 Y0 Z-10.352 G41 D60 X3.313 Y-34.241 Z0G91 G03 X34.241 Y34.241 Z0.352 R34.241 F5 G91 G03 X0 Y0 Z1.500 I-37.554 J0 F17 G91 G03 X-34.241 Y34.2 41 Z0.352 R34.241 G00 G40 X-3.313 Y-34.241 Z0 G90 G00 Z200.000G49M5 M301 攻丝加工1.1 攻丝加工的方法攻丝加工是利用丝锥进行螺纹加工,其加工过程和传统方法相同,在加工进给和退出时要保证丝锥转一转在进给方向进给一个螺距,属于成型刀具加工,刚性攻丝,其加工过程都是由数控铣床自动控制,生产效率和质量得到了提高,程序编制简单方便。
螺旋铣床安全操作规程

螺旋铣床安全操作规程Q/SZ J08.0491 目的为贯彻公司环境、职业健康安全方针,有效的进行安全生产并控制污染物的产生和排放,保护环境、保护员工的身体健康,特制定本作业指导书。
2 适用范围本作业指导书适用于减速机厂所有机械加工设备及其辅助动力动能设备设施,以及手工操作等各类人员。
3 总则3.1本总则规定了我厂生产用机械设备作业安全的规定和操作要求。
3.2本总则适用于各类生产机械设备的安全作业。
4 操作规程4.1.1.装卡工件前,必须检查好工装(内套胎棒,工件内孔试装一下),合适后再使用。
4.1.2.选择适当的压板和螺丝,紧螺帽时,要使用合乎标准规格的套板子。
站好适当位置,不要用力过猛,且防摔伤,卡紧工件。
4.1.3.卡托架的位置要适当,以免影响工作台旋转或碰到刀架,人未下工作台不准开车。
4.1.4.应从工作台走梯上下,禁止在工作台上下。
4.1.5.装滚刀时必须离开工件,防止碰手。
4.1.6.对刀或上刀时,刀具接近工件30mm时应严格要求手动进给,禁止机动点车。
4.1.7吊运轴齿轮时应使用吊索吊具,或用等长对绳捆牢,垂直。
4.1.8.铣刀重量超过25Kg时应用适当的钢丝绳用天车吊,人工扶正,并将刀杆与铣刀槽配好,防止滑落。
4.1.9.开车前,应检查闸托上插销是否放在要求的位置上,并取下摇把,以防甩出伤人。
4.1.10.在挂轮和卸轮时,必须停车,并做好相互联系工作,以免绞手。
4.1.11.下地沟时,防止地面油滑,手扶梯子,手里不准拿东西。
4.1.12.加工完的工件将残油擦洗干净放在有胶皮的适当位置,防止渗油污染环境。
附加说明:本作业指导书由XXX有限责任公司安技环保处提出本作业指导书由XXX有限责任公司安技环保处负责起草本作业指导书起草人:本作业指导书审核:本作业指导书批准:45。
螺旋伞齿铣安全操作规程

螺旋伞齿铣安全操作规程一、操作规程1、螺旋伞齿铣使用时,首先对机电传动系统、操作手柄、防护装置以及当班需用工、夹、量具进行全面检查,确认良好,才可开始工作。
2、对加工的工件,应吃透技术文件,按图纸要求,正确计算挂轮齿数,并准确地选用。
装配挂轮应实现啮合间隙适中。
3、挂换分齿齿轮时,必须关闭总电门。
放介轮时,不准把手指垫到啮合的两个齿轮中间,以免夹伤。
4、挂换齿轮,拧紧螺帽,关锁齿轮箱护罩和开关电门要由一个去完成,防止误开电门而发生事故。
5、投入切削前要把摇柄、扳手等各种工具从工作台上取下,防护挡板要好,冷却系统要经常检查并保持畅通。
6、换工件时,工作台要退出一定距离,防止铣刀划伤手,要检查好芯轴、套垫,下工件时两手要端平,不得把手伸到齿轮下面去穿套,以免压伤手指。
7、夹紧工件时不准用与螺帽规格不符的扳手,也不准在扳手上加套管,以免脱开时伤人。
8、清理铁屑时,要用专用工具,加工好的工件不可堆放过高,以防倾倒砸伤手脚。
9、观察切削面精度或测量尺寸时,不准用手去擦拭油沫,以免造成手指扎刺划伤。
10、工作结束或下班时,切断电源,清理现场。
二、日常保养1、擦净设备外表和外露导轨面,并润滑导轨。
2、按润滑图表规定检查润滑。
3、开空车试验,检查运转部件运转时的润滑情况。
4、清扫尘屑,擦拭设备外表及导轨、工作台、铣刀盘,并及时润滑导轨。
5、擦拭各部件并必要润滑后归位。
6、将本班使用的附件擦拭并必要润滑后,按定置管理要求摆放。
7、将本班使用的工、夹、量具擦拭后归位。
8、认真检查、填写设备的日常点检卡和交接班记录。
9、将铣削好的工件剃去毛刺,按定置管理要求,整齐稳妥地摆放在工件架上或油盘内。
- 1、下载文档前请自行甄别文档内容的完整性,平台不提供额外的编辑、内容补充、找答案等附加服务。
- 2、"仅部分预览"的文档,不可在线预览部分如存在完整性等问题,可反馈申请退款(可完整预览的文档不适用该条件!)。
- 3、如文档侵犯您的权益,请联系客服反馈,我们会尽快为您处理(人工客服工作时间:9:00-18:30)。
螺旋铣
O0001
:
G01X20Y50 预设G52坐标点
G65P2014B20C16J0K20F300 宏程序调用子程序号2014,B附值为孔直径,C附值为刀具径,
J附值为Z轴增量基数,K附值为铣孔深度,F附值为进给量。
%
O2014 子程序号为2014
G52X#24Y#25 设置刀轴当前点为局部坐标系X0Y0点(以下移动使用局部坐标系)G0X0.Y0. 快速移动至坐标系零点
#4=[#2-#3]/2 孔直径减刀具直径后除以2(做为起点在X向偏置)
Z3. 快速移动至Z3
G01Z0.5F500 直线插补Z轴以500MM/分钟进给至Z0.5
X#4Z0.F200 直线插补至X轴偏置,Z0 进给200MM/分钟
WHILE[#5LT#6]DO1 如果#5小于#6时执行DO到END之间的程序,如果#5大于#6时
执行END后的程序。
DO为条件执行符号
#5=#5+0.5 Z轴每次增量为0.5
G03X#4Y0Z-[#5]I-[#4]F#9 逆时针圆弧插补至上一个坐标Z轴增量点(X.Y不变)
END1 END为条件执行符号
G03X#4Y0.I-[#4]F#9 指定螺旋铣终点
G01X[#4-0.5] 在停止点向圆心方向偏置0.5(准备抬刀)
G0Z50. 抬刀至Z50
G52X0.Y0. 回局部坐标零点
M99 子程序结束
%
自变量指定:
自变量中不允许出现地址:G、L、N、O、P 。
不需要的地址省略,对应变量为空。
除I、J、K有字母顺序要求外其余为顺序要求。
坐标系旋转
%
O0001
G40 G17 G90
G91 G28 Z0.0
T01 M06
G54G0 G90 X-50 Y50 S3500 M03
Z50
G43 Z50. H01
M98P2014 子程序调用号2014
G68X0Y0R45 坐标旋转45度(角度第一象限至第四象限渐增)M98P2014 调用子程序号2014
G68X0Y0R90 坐标旋转90度
M98P2014 调用子程序号2014
G49Z50 取消刀具长度补偿
G69M05 取消坐标系旋转
M30
%
%
O2014
G41G01X20Y5D02F300
:
G40X0Y0
:M99
铣螺纹
Ф100圆心及圆周均分M30*1.5,底孔Ф28.5 牙高0.974 刀径8
%
O0001 主程序号
G54G90G17 提取坐标,绝对编程,选择XY平面
M03S3500 主轴正转,转速3500转/分钟
G0Z50 安全平面高50
G0X0Y0 定位
M98P1000 调用子程序号O1000
#4=0 附值
N30#5=50*COS[#4] 计算X轴坐标
#6=50*SIN[#4] 计算Y轴坐标
G52X#5Y#6 临时坐标零点
G0X0Y0 零点
M98P1000 调用子程序号O1000
#4=#4+90 附值
IF[#4LE271]GOTO30 如果#4小于271,则由N30开始,如大于271,则执行下行。
G0Z100 Z轴提升
G52X0Y0 回到临时坐标零点
G54G0X0Y0 使用G54坐标,移动
M30 结束,回到程序头
%
%
O1000 子程序号
G0X0Y0 孔中心
G0Z3 接近
#1=0.3 附值,第一刀单边加工量
N10#2=10.25+#1 偏置(-底孔-刀径)/2
G02X#2Y0I[#2/2]J0F300 顺时针走正圆,Z轴下降一个螺距接近工件
#3=1.5 Z轴附值
N20G02X#2Y0Z#3I-[#2]J0F300 顺时针走正圆,Z轴下降一个螺距切入工件
#3=#3-1.5 Z轴附值
IF[#3GE-15.1]GOTO20 如果#3大于-15.1则由N20开始,如果#3下于-15.1则执行下行G02X0Y0I-[#2/2] J0F300 圆弧切出
G0Z3 Z轴提升
#1=#1+0.2 附值
IF[#1LE0.91]GOTO10 如果#1小于0.91则由N10开始,如果#1大于0.91则执行下行G1X0Y0F300 回到孔中心
G0Z100 Z轴提升
M30 结束,回到程序头。