提高数控机床滚珠丝杠进给系统机械刚度的措施_许向荣
浅谈提高数控机床机械加工效率的有效措施

浅谈提高数控机床机械加工效率的有效措施随着科技的发展,数控机床作为现代机械加工的重要设备,其在各行业中的应用越来越广泛。
而如何提高数控机床的机械加工效率,成为了各行业工程师和技术人员所关注的焦点问题。
本文就浅谈提高数控机床机械加工效率的有效措施进行探讨。
一、合理规划生产流程合理规划生产流程是提高数控机床机械加工效率的关键。
首先需要通过工程师对产品的工艺要求和机床性能进行分析,确定加工方案和工序,以及具体的加工路径和工艺参数。
在确定加工路径和工艺参数后,需要对其进行综合考虑和优化,找到最佳的加工方案,尽量减少无效操作和机床停机时间,提高机床的稼动率和加工效率。
二、优化刀具选择和刀具路径刀具选择和刀具路径的优化对于提高数控机床机械加工效率起到举足轻重的作用。
正确选择刀具类型和规格,根据不同的加工物料和工艺要求,合理配置刀具参数,对加工效率具有直接的影响。
通过优化刀具路径,可以减少机床的空载时间和切削时间,提高机床的利用率和加工效率。
三、提高数控编程水平数控编程是数控机床加工过程中十分重要的一环,提高数控编程水平对于提高机械加工效率有着直接的促进作用。
工程师应通过不断学习和实践,提高自己的编程技术水平,熟练掌握数控编程软件和相关编程技巧,能够根据加工要求和机床性能,快速准确地编写加工程序,实现高效加工。
四、加强设备维护和保养设备维护和保养对于保持数控机床的良好工作状态和延长机床使用寿命是至关重要的。
及时的设备维护和保养能够有效地预防机床故障和损坏,减少机床故障停机时间和维修成本,从而保障机床的稳定运行和加工效率。
五、推广自动化装备和智能化管理随着工业自动化和智能化技术的不断发展和应用,自动化装备和智能化管理已成为提高机械加工效率的重要手段。
在生产现场,推广自动化加工设备和智能化管理系统,可以实现生产过程的自动化和数字化,提高生产效率和质量,降低人力成本和生产成本,从而提高机床的加工效率。
提高数控机床机械加工效率是一个系统工程,需要从多个方面进行综合考虑和改进。
提高数控机床机械加工效率的有效措施

提高数控机床机械加工效率的有效措施随着工业化的不断发展,数控机床在各种制造行业中发挥着重要的作用。
数控机床以其高精度、高效率、多功能等特点,越来越受到制造业的青睐。
要想发挥数控机床的最大作用,提高其机械加工效率,需要制定一系列有效的措施。
本文将重点介绍如何提高数控机床机械加工效率的有效措施。
一、合理规划生产工艺合理规划生产工艺是提高数控机床机械加工效率的基础。
在生产加工中,应该根据产品的材质、尺寸、形状和加工要求等因素,制定出科学合理的加工工艺流程。
这包括选择合适的刀具、切削参数、加工路线等。
通过合理规划生产工艺,可以有效地减少加工时间,提高数控机床的加工效率。
二、提高数控编程水平数控编程是数控机床加工的关键环节,直接影响到加工效率和加工质量。
提高数控编程水平,是提高数控机床机械加工效率的重要措施。
编程人员应该熟练掌握数控编程知识和技术,能够根据产品要求,合理编写加工程序,精准控制加工过程,提高加工效率和加工质量。
三、优化数控加工参数优化数控加工参数是提高数控机床机械加工效率的重要途径。
通过合理调整切削速度、进给速度、切削深度、切削宽度等参数,可以在保证加工质量的前提下,提高数控机床的加工效率。
在实际生产中,应该根据加工材料的性能特点和加工要求,不断优化数控加工参数,使之达到最佳状态,实现高效加工。
四、选择优质刀具和夹具刀具和夹具是数控机床加工过程中不可或缺的重要设备。
选择优质的刀具和夹具,对于提高数控机床机械加工效率具有至关重要的作用。
优质的刀具和夹具能够提高加工的稳定性和精度,降低刀具磨损,延长使用寿命,减少更换和调整时间,提高加工效率。
五、加强设备维护和保养设备维护和保养是保证数控机床长期稳定运行的关键。
合理的维护和保养措施可以有效地降低设备故障率,延长设备寿命,保证设备在高效运转。
定期对数控机床进行全面的保养,包括对润滑系统、冷却系统、传动系统、精密传感器等部件进行检查和调整,及时更换易损件,保持设备在最佳状态,以提高加工效率。
提高数控机床机械加工效率的有效措施

提高数控机床机械加工效率的有效措施【摘要】数控机床机械加工效率对生产企业的竞争力至关重要。
为了提高机床加工效率,可以通过优化加工工艺参数、提高数控编程技能、更新和维护设备、加强员工培训以及采用智能化管理系统等措施来实现。
优化加工工艺参数可以提高加工精度和效率,提高数控编程技能能够更快速地完成编程任务,更新和维护设备可以确保设备处于最佳状态,加强员工培训可以提升员工技能水平,采用智能化管理系统可以提高生产计划和资源调度的效率。
有效措施的实施对提高数控机床机械加工效率至关重要,可以帮助企业提升生产效率和竞争力。
【关键词】数控机床,机械加工效率,优化加工工艺参数,数控编程技能,更新设备,维护设备,员工培训,智能化管理系统,提高效率,实施有效措施。
1. 引言1.1 数控机床机械加工效率的重要性数控机床机械加工效率的重要性在现代制造业中是至关重要的。
随着市场竞争的加剧,企业需要不断提高生产效率,以降低成本、提高质量和提升竞争力。
而数控机床作为现代制造业中的重要设备,其机械加工效率直接影响着整个生产线的效率和产能。
提高数控机床机械加工效率可以带来诸多好处。
提高机械加工效率可以缩短生产周期,加快产品上市速度,满足市场需求的变化和客户需求的多样化。
提高机械加工效率可以降低生产成本,提高利润率,使企业更具竞争力。
高效率的机械加工还可以提高产品质量,减少次品率,增加客户满意度和信誉度。
作为企业管理者和生产运营者,必须重视提高数控机床机械加工效率的工作。
只有不断优化工艺参数、提高编程技能、更新设备、加强员工培训,并采用智能化管理系统,才能有效地提高机械加工效率,实现企业的可持续发展和盈利能力。
Efforts to improve the machining efficiency of CNC machine tools are crucial for modern manufacturing. With the intensification of market competition, companies need to continuously improve production efficiency to reduce costs, enhance quality, and increase competitiveness. As important equipment in modern manufacturing, the machining efficiency of CNC machine tools directly affects the efficiency and capacity of the entire production line.2. 正文2.1 优化加工工艺参数优化加工工艺参数是提高数控机床机械加工效率的重要措施之一。
提高数控机床刚度的措施

提高数控机床刚度的措施机床的刚度是指在切削力和其他力作用下,抵抗变形能力。
数控机床比普通机床要求具有更高的静刚度和动刚度,有标准规定数控机床的刚度系数应比类似的普通机床高50%。
机床在切削加工过程中,要承受各种外力的作用,承受的静态力有运动部件和被加工零件的自重,承受的动态力有:切削力、驱动力、加减速时引起的惯性力、摩擦阻力等。
机床的结构部件在这些力作用下,将产生变形,如固定连接表面或运动啮合表面的接触变形;各支承零件部的弯曲和扭转变形,以及某些支承件的局部变形等,这些变形都会直接或间接地引起刀具和工件之间的相对位移,从而导致工件的加工误差,或者影响机床切削过程的特性。
由于加工状态的瞬时多变情况复杂,通常很难对结构刚度进行精确的理论计算。
设计者只能对部分构件(如轴、丝杠等)用计算方法计算其刚度,而对床身、立柱、工作台和箱体等零件的弯曲和扭转变形,接合面的接触变形等,只能将其简化后进行近似计算,其计算结果往往与实际相差很大,故只能作为定性分析的参考。
近年来,虽然在机床结构设计中采用有限元法进行分析计算,但是一般来讲,在设计时仍需要对模型、实物或类似的样机进行试验、分析和对比以确定合理的结构方案,尽管如此,遵循下列原则和措施,仍可以合理地提高机床的结构刚度。
1.合理选择构件的结构形式(1)正确选择截面的形状和尺寸构件在承受弯曲和扭转载荷后,其变形大小取决于断面的抗弯和扭转惯性矩,抗弯和扭转惯性矩大的其刚度就高。
表7-1列出了在断面积相同(即重力相同)时各断面形状的惯性矩。
从表中的数据可知:形状相同的断面,当保持相同的截面积时,应减小壁厚、加大截面的轮廓尺寸,圆形截面的抗扭刚度比方形截面的大,抗弯刚度则比方形截面的小;封闭式截面的刚度比不封闭式截面的刚度大很多;壁上开孔将使刚度下降,在孔周加上凸缘可使抗弯刚度得到恢复。
(2)合理选择及布置隔板和筋条合理布置支承件的隔板和筋条,可提高构件的静、动刚度。
图7—1所示的几种立柱的结构,在内部布置有纵、横和对角筋板,对它们进行静、动刚度试验的结果列于表7—2中。
浅谈提高数控机床机械加工效率的有效措施

浅谈提高数控机床机械加工效率的有效措施数控机床是一种多功能、高精度的自动化机床,具有高效、稳定、精准等特点,被广泛应用于现代制造业中。
提高数控机床机械加工效率是现代制造业的重要课题,采用有效措施可以提高数控机床机械加工效率,降低生产成本,提高企业经济效益。
下面就是本文的内容。
一、加强机床维护保养数控机床机械加工效率是基于机床性能和设备状态的,因此解决机床问题可以提高机床的性能和设备状态,从而提高机床机械加工效率。
加强机床维护保养可以有效延长机床的寿命,提高机床的稳定性和生产效率。
具体措施包括及时更换磨损部件,保持机床清洁,适当润滑,及时维修等。
二、优化切削工艺切削工艺是数控机床机械加工的核心,优化切削工艺可以提高机床机械加工效率。
具体措施包括合理选择切削参数,选用合适的刀具和切削液,优化刀具路径,减小切削余量等。
合理的切削参数包括切削速度、进给量和切削深度等参数,合理选择这些参数可以最大限度地提高机床的机械加工效率和加工质量。
三、提高操作技术操作技术是影响数控机床机械加工效率的关键因素之一,提高操作技术可以有效提高机床机械加工效率。
具体措施包括加强操作培训,提高操作技术水平,严格遵守操作规程,充分利用机床功能等。
操作员必须了解切削参数、机床性能和刀具的选择等知识,实践中需要掌握切削参数优化、路径仿真和减小切削余量等技术。
四、应用模拟技术数字模拟技术可以模拟机床加工过程,优化切削参数和路径,从而提高数控机床机械加工效率。
具体措施包括采用仿真软件进行数字模拟,分析模拟结果,优化切削参数和路径,减小切削余量,提高机床机械加工效率。
利用模拟技术可以避免实际的试错过程,减少不良品数量,降低生产成本,提高经济效益。
总之,提高数控机床机械加工效率需要综合运用多种有效措施,包括加强机床维护保养,优化切削工艺,提高操作技术和应用模拟技术等。
只有采用正确的措施,加强管理,才能实现连续高效的生产,提高企业经济效益。
提高机床刚度的措施
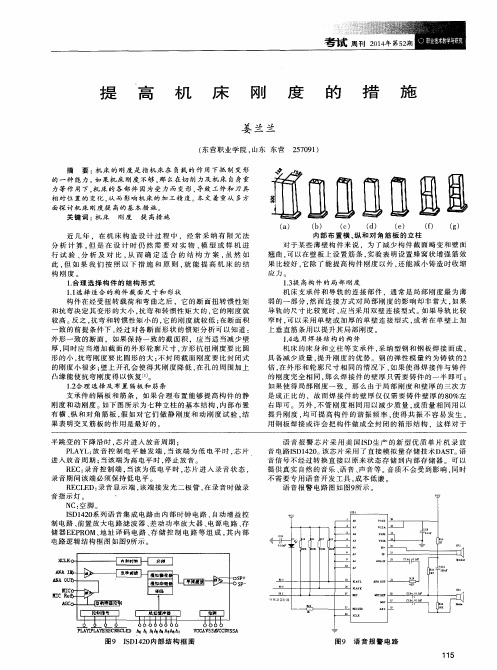
支 承件 的隔 板 和 筋 条 .如果 合 理 布 置 能 够 提 高 构 件 的 静 刚 度 和动 刚 度 。 如下 图所 示 为 七 种 立 柱 的 基 本 结 构 , 内部 布 置 有横、 纵和对角筋板 , 假 如 对 它 们 做 静 刚度 和 动 刚 度 试 验 。 结 果 表 明交 叉 筋 板 的作 用 是 最 好 的 。
弱 的一 部 分 , 然 而 连 接 方 式 对 局 部 刚度 的影 响却 非 常 大 , 如 果 导轨 的尺 寸 比较 宽 时 , 应 当 采用 双壁 连接 型式 。 如 果 导 轨 比 较 窄时 . 可 以 采 用 单 壁 或 加 厚 的单 壁 连 接 型式 , 或 者 在 单 壁 上 加 上垂 直筋 条用 以提 升 其 局 部 刚 度 。
的 刚度 小很 多 : 壁 上 开 孔 会 使 得 其 刚度 降低 . 在 孔 的周 围加 上 凸 缘 能使 抗 弯 刚度 得 以恢 复 …。
1 . 2 合 身 和 立 柱 等支 承件 , 采 纳 型钢 和钢 板 焊 接 而 成 , 具备减少质量 , 提 升 刚 度 的 优 势 。钢 的 弹性 模 量 约 为 铸 铁 的 2 倍, 在 外 形 和 轮 廓 尺 寸 相 同的 情 况 下 , 如 果 使 得 焊 接 件 与 铸 件 的 刚度 完 全 相 同 , 那 么 焊 接 件 的壁 厚 只需 要 铸件 的 一 半 即 可 : 如果 使 得 局 部 刚度 一 致 ,那 么 由于 局 部 刚 度 和 壁 厚 的 三 次 方 是 成 正 比 的 ,故 而 焊 接 件 的 壁 厚 仅 仅 需 要 铸 件 壁 厚 的 8 0 %左 右 即可 。另 外 , 不 管 刚 度 相 同 用 以减 少 质 量 , 或 质 量 相 同用 以 提升 刚度 , 均 可 提 高 构 件 的谐 振 频 率 。 使 得共振不 容易发 生 。 用 钢 板 焊 接 或 许 会 把 构 件 做 成 全 封 闭 的 箱 形 结 构 ,这 样 对 于
提高机床刚度的有效措施

提高机床刚度的有效措施
提高机床刚度是提高加工精度和工件表面质量的关键因素之一。
以下是一些有效的措施可
以提高机床的刚度:
1. 使用高刚性材料:选择高刚性的铸铁或钢材作为机床的结构材料,能够增加机床的整体刚度。
2. 加强机床结构设计:通过合理设计机床结构,增加机床的刚性。
例如,在承受力的部位增加
加强筋或支撑件,这样可以使机床更加坚固。
3. 增加机床的重量:增加机床的重量可以提高其刚度。
可采用增加床身或增加床身和工作台的
重量等方式。
4. 加强机床的支撑和固定:将机床牢固地固定在地面上,使用合适的支撑方式,避免机床在加
工过程中出现振动。
5. 提高导轨和传动系统的刚度:导轨是机床最关键的部件之一,选用高刚度的导轨和精密的传
动系统,可以有效提高整个机床的刚度。
6. 补偿机床变形:根据机床变形规律,采用合适的补偿方法,如预应力调整、补偿环技术等,
降低机床变形对刚度的影响。
7. 优化加工过程:通过合理的切削参数、工艺规程和工件夹持方式,减轻切削力对机床的影响,提高机床的稳定性和刚度。
总之,提高机床刚度需要多方面的措施综合应用,从材料、结构设计、支撑固定、导轨传动系
统和加工过程等方面入手,以达到提高机床刚度的目的。
双丝杠驱动进给单元轴向刚度模型及影响因素分析

双丝杠驱动进给单元轴向刚度模型及影响因素分析许向荣;鹿群鹏;宋现春;姜洪奎【摘要】双丝杠驱动进给单元在高性能数控机床中的应用较为广泛,研究其动态特性对于提高数控机床的加工性能具有重要的意义.文章基于关键滚动功能部件结合面刚度各个方向耦合的影响,围绕双丝杠驱动进给单元轴向刚度进行了研究分析,通过研究双丝杠驱动进给单元的轴向刚度模型,结合动力学和Hertz接触理论的相关知识,推导其各组成部分的刚度计算公式,探索其主要影响因素及关系曲线.结果表明:双丝杠驱动进给单元的轴向刚度主要受到滚珠丝杠副、支承轴承的结构参数,螺母位置以及两根丝杠跨距的影响;支承轴承结构参数的变化,会引起进给单元轴向刚度的明显变化;螺母位置是进给单元轴向刚度的主要影响因素,在两端固定的方式下其轴向刚度中间最小,在机床加工过程中,应尽量避免在丝杠的中间位置进行操作.【期刊名称】《山东建筑大学学报》【年(卷),期】2016(031)002【总页数】8页(P125-132)【关键词】结合面;双丝杠驱动;进给单元;轴向刚度【作者】许向荣;鹿群鹏;宋现春;姜洪奎【作者单位】山东建筑大学机电工程学院,山东济南250101;山东建筑大学机电工程学院,山东济南250101;山东建筑大学机电工程学院,山东济南250101;山东建筑大学机电工程学院,山东济南250101【正文语种】中文【中图分类】TH132.1与传统的单丝杠驱动进给系统相比,双丝杠驱动进给系统有很大的优势,如高精度、高刚度、低振动等,因此,双丝杠驱动进给系统日益成为高性能数控机床、加工中心研究领域的一个热点[1-3]。
目前,国内外学者纷纷围绕双丝杠驱动进给系统展开了理论和实验方面的研究。
Hiramoto等介绍了重心驱动原理,设计了工作台和主轴均采用重心驱动的机床模型和实际的双驱动进给系统的实验模型,通过实验发现重心驱动进给系统可以明显地减小机床的振动[1],但是缺乏理论支持。
Gomand等采用理论建模的方法,建立了龙门数控机床双驱动进给系统的数学模型,推导了丝杠轴向振动方程,并分析了丝杠变形对其静动态特性的影响[2]。
浅谈提高数控机床机械加工效率的有效措施

浅谈提高数控机床机械加工效率的有效措施【摘要】现代制造业中,数控机床机械加工效率的提升已成为企业发展的关键之一。
本文主要探讨了几项有效措施,包括优化工艺流程、提高设备稼动率、精细化管理、加强人员培训和引入先进技术。
通过优化工艺流程和提高设备稼动率,可以有效提高加工效率。
精细化管理可以提升生产效率和质量,加强人员培训则能更好地发挥员工的潜力。
引入先进技术可以进一步提高机械加工效率。
在总结了提高效率的措施并展望了未来发展方向。
通过以上措施的实施,企业可以有效提升数控机床机械加工效率,提高竞争力并实现更好的发展。
【关键词】数控机床,机械加工效率,优化工艺流程,设备稼动率,精细化管理,人员培训,先进技术,提高效率,未来发展方向。
1. 引言1.1 背景介绍数统计等。
: 数控机床机械加工是现代制造业中非常重要的一环,其效率直接影响到整个生产线的效率和质量。
随着市场需求的不断增长和竞争的日益激烈,提高数控机床机械加工效率已成为制造企业迫切需要解决的问题。
传统的机床加工方式存在着人工操作不精准、效率低下、不稳定等问题,迫使企业不得不寻求新的解决方案。
探讨如何提高数控机床机械加工效率,已成为当前制造业中的热门话题。
在这样一个背景下,本文将从优化工艺流程、提高设备稼动率、精细化管理、加强人员培训和引入先进技术等方面探讨有效提高数控机床机械加工效率的措施,以期为制造企业提供一些建设性的建议。
1.2 问题意识在数控机床机械加工领域,提高生产效率是企业追求的目标之一。
随着市场竞争的加剧和客户需求的不断变化,机床加工效率的提升面临着一些问题。
传统的工艺流程可能存在一些繁琐和低效的环节,造成加工周期较长,影响生产效率。
设备稼动率不高也是制约机床加工效率的重要因素之一,如果设备长时间处于空闲状态,就无法实现充分利用。
精细化管理不到位、人员培训不足、技术水平不够等问题也会影响机床加工效率的提高。
在面对这些问题时,企业需要采取一系列有效措施来提高数控机床机械加工效率。
浅谈提高数控机床机械加工效率的有效措施

浅谈提高数控机床机械加工效率的有效措施随着科技的不断发展,数控机床已经逐渐成为现代工业生产中不可或缺的重要设备。
数控机床可以有效提高机械加工的精度和效率,提高产品质量,降低生产成本,从而使生产过程更加安全和可靠。
要想实现数控机床的最大化效率,需要实施一系列的有效措施来提高数控机床机械加工效率。
一、合理选用数控机床提高数控机床机械加工效率的有效措施是合理选择适合自己生产需求的数控机床。
如果生产批量较大,建议选择高速数控机床;如果生产批量较小,可以选择多功能数控机床。
还需要考虑加工的材料,对于硬度较大的材料,需要选择适合的加工中心。
合理选用数控机床可以提高生产效率,降低生产成本,提高产品质量。
二、优化数控编程优化数控编程也是提高数控机床机械加工效率的重要措施。
数控编程是数控机床的“大脑”,编程的优劣直接影响到加工的效率和质量。
在编程时,需要根据加工工件的几何形状、尺寸和工艺要求,合理选择加工路径和刀具轨迹,减少刀具的空走时间,提高加工效率。
还需要根据不同的加工任务,合理设置切削参数和进给速度,进行合理的切削。
优化数控编程可以提高机床的利用率,降低加工成本。
三、加强设备维护设备的维护保养对于提高数控机床的机械加工效率同样十分重要。
定期对数控机床进行维护保养,保证设备的稳定性和可靠性。
及时更换磨损严重的零配件,保证设备的精度和加工质量。
在日常使用过程中,做好设备的清洁和润滑工作,减少设备的故障率,提高生产效率和设备利用率。
四、提高操作技术水平提高操作技术水平也是提高数控机床机械加工效率的重要措施。
操作人员需要熟练掌握数控机床的操作技术,了解各种加工工艺和操作规程。
熟练掌握数控机床的编程和调试技术,提高生产效率和产品质量。
还需要加强对数控机床加工工艺和设备的学习和培训,不断提高操作技术水平,保持良好的工作状态。
提高操作技术水平可以有效减少加工错误,提高加工效率。
五、采用先进的刀具和工装。
浅谈提高数控机床机械加工效率的有效措施

浅谈提高数控机床机械加工效率的有效措施数控机床机械加工是现代制造业中较为常见的一种加工方式,随着制造业的发展,数控机床机械加工效率也需要不断的提高。
下面将从多个方面介绍如何提高数控机床机械加工效率的有效措施。
一、优化数控机床加工程序优化加工程序,将机床的加工轨迹进行优化,可以减少加工时间、提高效率。
优化程序需要注意以下几点:1. 合理选择刀具:根据工件材料、形状等选择适当的刀具,可以有效避免多余的切削和刀具损耗。
2. 合理选用加工参数:根据工件材料、精度要求等,选用合适的切削参数和进给速度,可以尽可能地提高加工效率。
3. 合理布局机床:把相同工序的工件集中安排在同一区域,合理配置加工顺序,可以减少机床的空转时间,提高加工效率。
二、适当升级数控设备现代数控机床的控制系统较为复杂、精细,因此在适当的情况下升级设备并可以提高机床的加工效率。
例如:1. 更换控制系统:更换更高配置的控制系统可以提高机床运行的稳定性、精确度和响应速度,从而提高加工效率。
2. 升级电机实现高速加工:对于那些需要高精度、高速度的机床,可以考虑升级电机,实现高速加工。
三、合理选择刀具不同材料、不同性质的工件需要不同的刀具去加工。
选择合适的刀具,可以减少切削阻力,降低切削力,从而提高加工效率。
四、加强刀具管理切削刀具是数控机床加工过程中的重要组成部分,合理的刀具管理可以延长刀具寿命、提高加工效率。
刀具管理需要注意以下几点:1. 做好刀具保养:及时清洗、润滑以及检查刀具的磨损情况,延长刀具寿命,提高加工效率。
2. 合理选择刀具库存:选择一定大小的刀具库存,减少刀具换装时间,提高加工效率。
五、确保机床运转稳定机床的稳定运转和机床系统的结构特性密切相关,不良的机床结构会导致加工偏差,影响机床的稳定性。
因此,需要确保机床的运转稳定性,进而优化加工效率。
以上就是提高数控机床机械加工效率的有效措施,只有在不断的优化和改进中,才能够让机床的生产力得到全面提升。
提高数控加工效率的途径与措施

科技创新与应用 I 2 0 1 4 年 第1 6 期
工 业 技 术
提 高数控 加工效率 的途径 与措施
廖 昌荣
( 湖 南衡阳技 师学院, 湖南 衡 阳 4 2 1 1 0 1 )
摘 要: 数控 机床 在 机械 制 造 领域 中 占有 着 非 常重要 的地位 , 充分 改善 数 控 机床 在 实 际操 作 中 的工作 效 率 能够 确保 生 产量 增 多、 投入资金 少、 加强企业竞争力的作用。文章主要是根据平时积 累的操作经验, 并且从 中找 出问题存在的主要原因以及解决方法
的 。第 三 , 在 实 际 实施 操 作 中 , 一 定 要 遵循 设 定 好 的程 序 来 进 行 加 工, 尽 量 避免 出 现机 床切 削 刃没 有 进行 切 削 的现 象 。 产 品设计 的标 准化 、 系列 化 是 多 品种企 业 生 产 和新 产 品 开发 有 序、 高 效 的基 础 。 新产 品在设 计 上往 往 对 老产 品有 一定 继 承 性 。 根据 数 控 编 程 阶段 来 说 ,当 然也 希 望 能 够 尽 量 利用 成 熟 产 品 的加 工 程 序, 从 而不来回的重复劳动, 提高编程效率。具体实现过程如下: 针 对 结 构相 似 、 技 术要 求 相 对 固定 , 工 艺 安排 规 范 的零 件 族 , 在 深 入分 析、 总 结成 员 的结 构 要 素 、 加 工 工 艺 的基 础 上 , 划分数控特征单元 , 并 用 参 数 描 述其 几何 属 性 和 工艺 特性 , 编制 标 准 的程 序 模 块 , 形 成 企 业 内部 标 准库 , 以便 编 程调 用 。一 般 说 来 , 参数 程 序 模块 中 , 参数 设 置 的越 细 , 其 通用 性 越强 。 实 际 应用 中 , 若用 高 级语 言 自行 开 发小 的应 用 程 序 ,实 现 数 据 文件 的 自动 读 人 和 数 控 加 工代 码 的 自动输 出, 这 样 就 可 以把参 数 编程 所 带来 的 的优 点 发挥 出应 有 的 效果 。 4改 善供 气 质量 , 提高 数控 机 床 的工 作效 率 现代数控机床随着其 自动化程度的不断改革 , 对辅助保障系统 的依 赖性 也 明 显增 加 了许 多 。 数控 机 床是 集 机 、 电、 光、 液、 气 于一 体 的综 合 系统 , 它 的许 多 功 能 和动 作最 终 是 南液 、 气 系统 来 执 行 的 , 如 果 工 厂 的供 气 系 统压 力 不 足 、 压 力 稳 定 性较 差 , 或 是 气 源 的 洁 净 度 不高 , 都 容易 造 成机 床 l T作 不 良。 一般 来说 , 如果 供气 压 力 不足 可 能 造 成 数控 机 床报 警 停 机 ,但 一般 不 会 对 机床 本 身 的 系统 造 成损 坏 。 但 如 果气 源 的 洁净 度较 差 , 混有 油 水 、 灰 尘等 杂 质 时 , 会很 容 易 对 机 床 本 身造 成 一些 损 坏 。虽 然 数控 机 床 的气 路 系 统本 身 有 滤 清装 置 , 但 这 种 过滤 作 用是 非 常有 限 的 , 不 能 够长 时 间 的进 行 过 滤 。 当气 源 过 脏 时 可 造 成机 床 气 路 管 道 堵 塞 , 供气不畅, 压 力 不 稳 等 毛 病 。所 以, 提 高 供气 质 量 可 以提 高数 控机 床 的工 作 效率 。 5加强管理 , 提高数控机床的工作效率 数控 机 床 跟别 的机 床 有 着很 大 的 区 别 , 它本 身 包 含着 一 定 的差 异性 。 所 以, 在 实 际操作 生 产 过程 中 , 要尽 量 发挥 机 床所 具 有 的 的优 点, 减 轻设 备带 来 的缺 点 , 要 有效 的使 生 产效 率 达 到要 求 , 这 也 是 所 有工 业 企业 发 展 中不 可忽 视 的重 中之重 。 再加 上 很 多 因素 致使 那 些 中小 企 业 的利 益都 得不 到理 想状 态 , 也 根 本 体 现不 出数 控机 床 在 工 作中所带来 的好处 。假如, 有一个缸体零件 , 在加工中心上加工 , 应 该 在 完 成一 次 装卡 之 后 完成 五 面 体 的所 有加 工 , 这 样 可 以使 零 件 加 工更 加 的准 确 性 , 还使 加 工 效率 有 着 明显 的提 高 。而 如果 只是 在 加 工 中心 里做 好 部分 划 线 和 打孔 的 工作 之 后 ,再 转 移 到别 的铣 床 、 钻 床 和镗 床 上 去 完 成铣 削 、 钻孑 L 和镗 孔 工 序 的做 法 是 完 全 不 对 , 因 为 这样 会 使企 业 的发 展 逐 渐退 化 。由于 影 响企 业 运 营 , 我 们一 定 要 对 其有 着 足够 的重视 。通 过调 查研 究表 明 , 大 多 都是 工 作 人 员工 艺 知 识水 平 不 足 , 所 以也 不能 忽 视人 为 的原 因 。 因此 , 科 学 管理 、 合 理 调 度, 是 为 了能 够提 升 数控 机 床加 工效 率 的 一个 相 当重 要 的环 节 。
数控机床滚珠丝杠副的改进方法

摘 要 分析了滚珠丝杠副的原理及结构形式。详细 阐述了适合高速化数控机床的滚珠丝杠副形 式。提出了一种新的滚珠丝杠副的调隙和预 紧方式—连续可调预紧装置。运用压电陶瓷 传感器与压电驱动器结合的方法。通过此种 方法可以直接测量预紧力, 随时精确地补偿因 磨损而增大的间隙。提高了数控机床的轴向 刚度和定位精度。 关键词 数控机床;滚珠丝杠副;调隙;预紧方式; 压电陶瓷传感器;驱动器;定位精度 Abstract The rule and the composition of the ball screws were analyzed. The shape of the ball screws were detailed elaborated which was fit for the NC machine for high speed. A new coordination gap and a new firmly beforehand means of the ball screws which was said a continued coordination gap unit were proposed. That was used piezoelectric ceramics which was in combine with piezoelectric ceramics driver. By this means, we can directly survey the firmly beforehand means. We also can accurately compensate the increscent coordination gap that aroused by abrasion. The positioning accuracy and axial stiffness of the NC machine had been improved. Key words The NC machine;Ball screws;Coordination gap; Firmly beforehand means;Piezoelectric ceramics sensor;Driver;Positioning accuracy
提升数控机床性能的具体措施

提升数控机床性能的具体措施摘要:数控机床是一种高精度、高效率的自动化机床。
主传动装置应具有很宽的变速范围,并能无级变速;进给传动装置应具有很高的传动精度、灵敏性和稳定性。
本文结合数控机床传动系统的特点特点,对其误差控制进行分析探讨。
关键词:数控机床传动中图分类号:{o311.3}一、传动系统概述数控机床的传动系统,包括主轴运动和进给传动,与普通机床相比,省去了复杂的齿轮变速机构。
数控机床的主传动由主轴电动机、传动系统和主轴部件组成。
数控机床的进给运动由主轴电动机、传动系统、滚珠丝杠螺母机构和导轨组成。
数控机床需要根据数控系统的指令,自动完成对进给速度、主轴转速、刀具运动轨迹以及其他机床辅助技能(如自动换刀,自动冷却)的控制。
它必须利用伺服进给系统代替普通机床的进给系统,并可以通过主轴调速系统实现主轴自动变速。
因此,在机械结构上,数控机床的主轴箱、进给变速箱结构一般非常简单;齿轮、轴类零件、轴承的数量大为减少;电动机可以直接连接主轴和滚珠丝杠,不用齿轮;在使用直线电动机,电主轴的场合,甚至可以不用丝杠、主轴箱。
在操作上,它不像普通机床那样,需要操作者通过手柄进行调整和变速,操作机构比普通机床要简单多,许多机床甚至没有手动机械操作系统。
此外,由于数控机床的大部分辅助动作都可以通过数控系统的辅助技能(m技能)进行控制,因此,常用的操作按钮也较普通机床少。
二、数控机床对机械的基本要求(一)具有较高的静、动刚度和良好抗震性机床的刚度反映了机床机构抵抗变形的能力。
机床变形产生的误差,通常很难通过调整和补偿的方法予以彻底的解决。
为了满足数控机床高效、高精度、高可靠性以及自动化的要求,与普通机床相比,数控机床应具有更高的精刚度。
此外,为了充分发挥机床的效率,加大切削用量,还必须提高机床的抗震性,避免切削时产生的共振和颤振。
而提高机构的动刚度是提高机床抗震性的基本途径。
(二)具有较好的热稳定性机床的热变性是影响机床加工精度的主要因素之一。
提高数控机床系统的刚度的措施

提高数控机床系统的刚度,可以采取以下措施:
1.合理选择材料和结构:选择高强度、高刚性的材料和结构,如采用更坚固和稳定的材料,增加结构件的截面尺寸或厚度,增加连接件的数量和质
量等,以增强机床的刚性。
2.优化机床组件设计:对机床组件进行优化设计,包括减轻运动部件的重量、优化润滑和冷却系统、提高传动系统的精度和刚性等,以减小运动过
程中的惯性和阻力,提高机床的动态刚度。
3.加强部件之间的接触刚度:改善部件之间的接触条件,如增加接触面积、提高接触表面的粗糙度和平整度、采用预应力等措施,以增加部件之间
的接触刚度。
4.提高控制系统性能:优化控制系统的算法和参数,提高控制系统的响应速度和精度,以减小运动过程中的动态误差,从而提高机床的加工精度和
刚度。
5.加强维护和保养:定期对机床进行检查和维护,保持机床的清洁和润滑,及时更换磨损严重的部件,以保持机床的良好状态,提高其刚度和使用
寿命。
6.采用先进的加工技术和工艺:采用先进的加工技术和工艺,如高速切削、超精密切削、激光加工等,可以减小切削力和热变形对机床刚度的影响,
提高机床的加工质量和效率。
7.加强机床地基和安装基础:确保机床地基和安装基础的稳定性和刚性,采用合适的隔震和减震措施,以减小外部振动对机床的影响,提高机床的
稳定性和刚度。
总之,提高数控机床系统的刚度需要从多个方面入手,综合考虑材料、结构、控制系统、维护保养等多个方面的因素,采取综合性的措施来实现。
提高数控机床机械加工效率的有效措施

提高数控机床机械加工效率的有效措施数控机床是现代机械加工领域中的重要设备,其高效率和高精度的加工特性使其在工业生产中得到广泛应用。
为了提高数控机床的机械加工效率,可以采取以下有效措施:1. 优化刀具选择:选择合适的刀具材料和刀具类型并合理配置刀具数量,以提高切削力和加工速度,提高加工效率。
根据加工材料的不同选择适当的刀具涂层和刀具形状,以提高切削效果。
2. 优化切削参数:根据不同加工材料的特性和加工要求,合理选择切削速度、进给速度和切削深度等切削参数,以最大限度地提高切削效率。
3. 优化工艺路线:在设计加工工艺时,应尽量减少切削次数和换刀次数,合理安排切削路径和切削方法,以减少无效运动和切削时间,提高加工效率。
4. 提高机床刚性:加强机床的刚性设计和加工精度控制,以提高机床的稳定性和抗振能力,减少振动对加工质量的影响,提高加工效率。
5. 优化工件夹持方式:选择合适的夹具和夹具方式,以提高工件的定位精度和刚性,减少因工件变形而导致的加工误差和重复定位误差,提高加工效率。
6. 加强机床维护保养:定期对数控机床进行维护保养,保持机床的良好状态和稳定性,及时更换磨损零部件,减少故障发生,提高机床的可靠性和加工效率。
7. 加强操作人员培训:对操作人员进行专业培训,提高他们的操作技能和加工理论知识,使其熟练掌握数控机床的操作方法和各项功能,以提高加工效率。
8. 应用智能化技术:利用智能化技术,如人工智能和大数据分析等,对数控机床进行优化配置和智能化管理,提高加工过程的自动化水平,提高加工效率。
9. 采用高效的切削液和冷却系统:选择高效的切削液和冷却系统,有效降低切削温度,减少切削热对刀具和工件的影响,提高切削效率和加工质量。
10. 优化加工方案和工艺改进:通过不断的研究和实践,对加工方案进行优化和改进,采用新的加工方法和工艺,以提高加工效率和质量。
提高数控机床机械加工效率需要综合考虑刀具选择、切削参数、工艺路线、机床刚性、工件夹持、机床维护、操作人员培训、智能化技术、切削液和冷却系统等因素,通过适当的优化和改进措施,可以提高数控机床的机械加工效率。
提高数控机床滚珠丝杠进给系统机械刚度的措施_许向荣
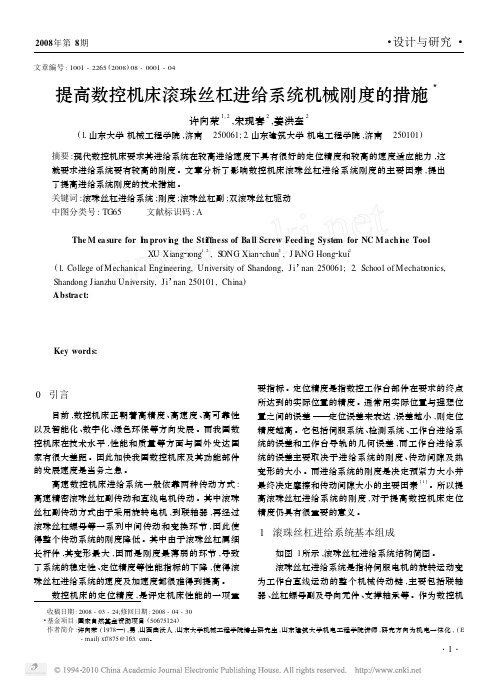
文章编号:1001-2265(2008)08-0001-04收稿日期:2008-03-24;修回日期:2008-04-30 3基金项目:国家自然基金资助项目(50675124)作者简介:许向荣(1978—),男,山西曲沃人,山东大学机械工程学院博士研究生,山东建筑大学机电工程学院讲师,研究方向为机电一体化,(E-mail )xt7875@ 。
提高数控机床滚珠丝杠进给系统机械刚度的措施3许向荣1,2,宋现春2,姜洪奎2(1.山东大学机械工程学院,济南 250061;2.山东建筑大学机电工程学院,济南 250101)摘要:现代数控机床要求其进给系统在较高进给速度下具有很好的定位精度和较高的速度适应能力,这就要求进给系统要有较高的刚度。
文章分析了影响数控机床滚珠丝杠进给系统刚度的主要因素,提出了提高进给系统刚度的技术措施。
关键词:滚珠丝杠进给系统;刚度;滚珠丝杠副;双滚珠丝杠驱动中图分类号:TG65 文献标识码:AThe M ea sure for I m prov i n g the Sti ffness of Ba ll Screw Feed i n g Syste m for NC M ach i n e ToolXU Xiang 2r ong 1,2,S ONG Xian 2chun 2,J I A NG Hong 2kui2(1.College of Mechanical Engineering,University of Shandong,J i ’nan 250061;2.School of Mechatr onics,Shandong J ianzhu University,J i ’nan 250101,China )Abstract:Key words:0 引言目前,数控机床正朝着高精度、高速度、高可靠性以及智能化、数字化、绿色环保等方向发展。
而我国数控机床在技术水平,性能和质量等方面与国外发达国家有很大差距。
数控机床滚珠丝杠可靠性优化设计
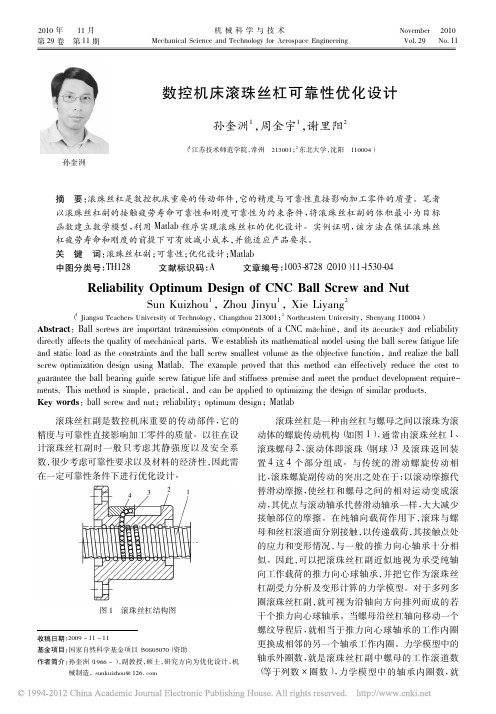
塑性接触变形。 压疲劳破坏、 ( 2 ) 滚珠丝杠的工作表面的接触疲劳破坏 。 ( 3 ) 滚珠体的工作表面的接触疲劳破坏、 剪切 疲劳断裂、 磨损、 过量塑性接触变形。 按照最弱强度原则确定滚珠丝杠副的可靠性设 计指标为: 滚珠丝杠传动的疲劳寿命、 滚珠或滚道面 的塑性接触变形( 刚度) 。 1. 2 设计变量的选取 所有影响滚珠丝杠副传动质量的独立 一般地, 如滚珠丝杠的公称直径、 滚珠体的直径、 设计参数, 螺旋升角、 滚珠丝杠导程、 工作滚珠数、 工作滚珠圈 数与列数、 滚珠螺母外径、 滚珠螺母螺纹底径、 滚珠 滚珠螺母长度、 滚珠丝杠长度等结构 丝杠螺纹外径、 尺寸都应作为设计变量。 但过多的设计变量, 会增 加计算的工作量和难度, 通常将那些对优化目标影 响比较明显的、 易于控制的设计参数作为设计变量 。 对于滚珠丝杠传动, 主要的参数有: 滚珠丝杠公 称直径 d0 、 滚珠直径 d b 、 滚珠丝杠导程 P 、 工作滚珠 圈数 × 列数 i、 螺旋升角 φ 等。 公称直径直接影响滚 珠丝杠的大小和强度; 滚珠直径影响滚珠丝杠承受 静载荷和动载荷的大小与丝杠寿命的长短 ; 滚珠丝 杠导程和螺旋升角也是选择滚珠丝杠副的重要参 数。 所以选择滚珠丝杠公称直径 d0 、 滚珠直径 d b 、 滚 珠丝杠导程 P 、 螺旋升角 φ 作为独立设计变量, 即 T T X =[ x1 , x2 , x3 , x4] =[ d0 , db , P, φ] 1. 3 目标函数的建立 根据具体工作要求, 可对滚珠丝杠提出不同的 目标函数。 如: 要求疲劳寿命最长、 磨损寿命最长、 摩擦力矩最低、 额定静负荷最大、 多目标函数优化 等。笔者根据设计要求, 为使滚珠丝杠副机构紧凑, 经济性最佳, 取滚珠丝杠副的体积和 ( 包括螺母、 丝 杠、 滚珠体 ) 最小为优化目标。 根据滚珠丝杠副体 积的近似计算公式, 相应的目标函数为 2 2 ( π D2 πx1 1 - πx1 ) f( X) = L1 + L + 4 4 2
浅谈提高数控机床刚度的措施

浅谈提高数控机床刚度的措施摘要:现代机械制造业对加工精度要求很高,特别是随着国防、电子、汽车等现代工业的飞速发展,对制造业提出了更高的要求。
在制造业中金属切削加工占很大比重,因此对机床的要求越来越高,提高机床的精度是该领域研究的一个重点方向。
刚度是影响机数控机床加工床精度的重要参数,提高机床的刚度就能有效的提高零件的加工精度。
目前数控机床以其加工精度高,误差稳定,效率高等特点得以广泛使用,而机床的刚度关系到机床的性能,所以研究机床的刚度是非常有价值的。
本文主要通过分析数控机床的刚度和影响数控机床刚度方法,得出提高数控机床刚度的可行方法。
关键词:数控机床;刚度;结构布局1 前言现代机械制造业对加工精度要求很高,特别是随着国防、电子、汽车等现代工业的飞速发展,对制造业提出了更高的要求。
在制造业中金属切削加工占很大比重,因此对机床的要求越来越高,提高机床的精度是该领域研究的一个重点方向。
刚度是影响机数控机床加工床精度的重要参数,提高机床的刚度就能有效的提高零件的加工精度。
目前数控机床以其加工精度高,误差稳定,效率高等特点得以广泛使用,而机床的刚度关系到机床的性能,所以研究机床的刚度是非常有价值的。
2 数控机床刚度分析刚度主要是指在材料在外力作用下,抵抗变形的一种能力。
数控机床的刚度就是数控机床在加工过程中切削力和其他力的作用下不发生部件变形的能力。
机床的刚度通常可以分为动态刚度和静态刚度,数控机床要普通机床具有更高的动、静刚度。
静态刚度是数控机床承受自重和加工工件重量时,机床抵抗变形的情况,而机床在切削加工过程中,还要承受切削力、惯性力、机床部件发热变形、摩擦阻力等,这时机床的刚度就是动态刚度。
数控机床刚度分析主要考察机床组件本身刚度和部件之间的接触刚度与硬度。
机床元件本身的刚度,取决于部件本身的横截面形状和尺寸大小,还有材料性质。
部件之间的接触刚度不仅与接触几何形状和表面硬度有关,而且在接触表面上,几何精度,加工方法,接触面介质,预压力和其他的接触表面表面粗糙度等因素有关。
提高进给系统传动精度的新措施

第22卷第5期周口师范学院学报2005年9月Vo l.22 No. 5 Jou r na l of Zhoukou No r m a l U n i ve rsity Sep. 2005 提高进给系统传动精度的新措施李大庆,邓效忠1 ,张明柱1 ,李1 ,2 峰1( 1. 河南科技大学机电学院,河南洛阳471000; 2. 濮阳职业技术学院机电系,河南濮阳457000 )摘要:在机床数控改造中,如何提高进给系统传动精度是一项重要改造内容.文章讨论了一些常见的方法并针对具体型号铣齿机提出了新措施.关键词:传动精度;液力阻尼;双导程蜗杆中图分类号: TH13 文献标识码: A 文章编号: 1671 - 9476 ( 2005 )05 - 0054 - 03在数控机床改造中,提高传动精度是一项重要内容.在采用齿轮来传递动力和运动的数控机床的传动中,由于进给系统经常处于自动变向状态,齿侧间隙会造成进给反向时丢失指令脉冲,并产生反向死区,从而影响加工精度,因此,必须采取措施消除齿轮传动的间隙.作者在对某机床数控改造的过程中,通过一些特殊的消除齿轮间隙的方法,使得该机床的传动精度有较大改善,完全满足了用户需求.1 常见提高进给系统传动精度的方法在用齿轮副来传递运动和动力的进给系统中,消除齿侧间隙的方法目前有两种应用较多:一种是刚性调整法,另一种是柔性调整法.刚性调整法的结构比较简单,具有较好的传动刚度,但是这种调整方法调整后齿侧间隙不能自动补偿,而且调整时齿轮的周节公差及齿厚要严格控制. 因此,这种调整法对于要求精度较高的数控机床来说, 往往需要经常调整,非常不方便.常见的刚性调整法有两种:一种是通过转动偏心套就可调节两啮合齿轮的中心距,从而消除齿侧间隙,此方法称为偏心套调整法. 另外一种是两个啮合着的齿轮的节圆直径沿齿宽方向制成稍有锥度,使其齿厚在轴向稍做线性变化. 通过改变调整垫片的厚度来调节两个齿轮在轴线方向的相对位置而消除间隙, 通常这种方法称为轴向垫片调整法.柔性调整法是调整后齿侧间隙仍可自动补偿的调整法,它一般都采用调整压力弹簧的压力来消除齿侧间隙. 这种调整法能在齿轮的齿厚和周节有变动的情况下,也能保持无间隙啮合. 但结构较复杂,轴向尺寸大,传动刚度低,同时传动平稳性也差. 常见的柔性调整法有两种: 轴向弹簧调整法和周向弹簧调整法[ 1 ] .图1为周向弹簧调整法剖面图,两个齿数相同的薄片齿轮 3和 4 与另一个宽齿轮相啮合,齿轮 3 空套在齿轮 4 上,可相对回转. 每个齿轮端面分别均匀装有 4 个螺纹凸耳 1 和 2 ,齿轮 3 的端面上有4个通孔,凸耳 1 可以从中穿过,弹簧8 分别勾在调节螺钉5和凸耳 2 上. 旋转螺母 6 和7 可以调整弹簧8 的拉力,弹簧的拉力可以使薄片齿轮错位, 即两片薄齿轮的左右齿面分别与宽齿轮齿槽的左右贴紧,从而消除齿侧间隙.除此以外,近年来同步齿形传动也被广泛应用. 当传动力矩不大时,也可利用钢制齿轮与尼龙齿轮齿侧过盈啮合来消除间隙.图1 周向弹簧调整法结构图收稿日期: 2005 - 04 - 30作者简介:李大庆( 1970 - ) ,男,山东莘县人,讲师,河南科技大学在读研究生,主要从事机械制造研究.第22卷第5期李大庆,等:提高进给系统传动精度的新措施55 2 铣齿机切齿受力分析2. 1 铣齿机工作时运动分析机床铣削锥齿轮的方法属于展成法,采用了近似平面齿轮的原理,即用双铣刀盘代替平面齿轮的一个齿,铣刀和齿轮毛坯做无间隙的啮合. 两个刀盘只做位置不变的简单旋转运动,而齿轮毛坯则绕自身轴线转动,同时在平面齿轮的节平面上作纯滚动,慢慢进入切削.当被加工齿轮的节锥面垂直于双刀盘时,即切至全齿高.然后又逐渐切出,完成一个齿轮的加工.如图2所示,在整个加工过程中,齿轮毛坯装在工件头上,绕着工件头心轴轴线作旋转运动n1 ,同时, 整个工件头随着摇台绕着摇台主轴轴线做旋转n2 . 即齿轮毛坯除了自转, 还有公转, 所有的进给运动有工件头和摇台完成. 双刀盘只做简单的旋转运动n3 .2. 2 机床受力分析在铣削进给过程中, 由于切削进给力 f ( t) 是一随时间变化的变量,推导非常复杂,这里只做定性分析. 由图2, 假想平面齿轮的一个齿的两侧面是由双铣刀盘旋转时主切削刃形成的表面所代表的. 切削过程近似为两齿轮的啮合过程,由于刀盘上的刀片交错布置,刚切入时,是刀具的右侧刀片承受切削力, 左侧刀片承受范成力. 切出时, 刀具的左侧刀片既承受切图2 铣齿机工作时运动分析指示图削力,又承受范成力,此范成力即为切削进给力.并且由于刀盘上均匀分布着刀片, 在切削中, 切削进给力是断续的. 对被加工齿轮来说, 切削进给阻力不但是变化的,而且还是断断续续的.也就是说工件头传动链中的蜗轮副同样受到大小变化的、断断续续的阻力.对于摇台来讲, 受的阻力是通过工件头来传递的, 由于本机床为锥齿轮铣齿机, 铣削时, 齿轮毛坯受到的力可分解为两个方向的分力,一分力的作用为向下压被加工件,另一分力表现为沿轴线方向推毛坯. 力的大小也是变化的. 同样道理,这种阻力通过摇台转盘、摇台主轴传递到摇台的蜗轮副上.无论是工件头还是摇台上的蜗轮副, 受到大小变化的断续切削力时, 齿间侧隙就会发生变化. 这种变化使传动中的冲击和磨损更加严重,从而加强了切削颤振,影响加工精度.齿侧间隙的消除措施在本文的第一部分列举了一些常见的消除间隙的方法, 但这些方法都有不同程度的缺陷.在原机床上, 在工件头的传动中采用了图1 所示的周向弹簧调整法. 由前面分析可知, 当传动齿轮受到的力为变化的断续切削力时,此结构中的弹簧力也会发生变化,那么也就表现出传动平稳性差的特点. 为消除前面这些方法的不足, 在机床改造中提出了一些新的方法, 并取得了良好的效果.3. 1 工件头部分在工件头上,采取了液力阻尼,如图3所示,在此传动中,蜗轮 2 随蜗轮轴6在轴承1和5的支撑下转动,压力油进入后盖7和摩擦盘3之间的缝隙,对摩擦盘产生一个向右的推力, 使摩擦盘的右端紧靠在蜗轮的左端.零件4起导向作用, 蜗轮副之间的传动间隙靠蜗轮左侧和摩擦盘产生的摩擦力来消除. 优点是在整个切削过程中,无论何时,蜗轮受到的摩擦阻力都为一恒3图3 液力阻尼工件头结构图传动时一直保持压紧状态,消除了传动间隙,解决了原机床方案中弹簧力刚度不足,传动平稳性差的缺点,减小了切削颤振和传动误差,大大提高了加工精度.3. 2 摇台部分3. 2. 1 双导程蜗杆结构在摇台的传动链中,采用了一种双导程蜗杆来调整间隙,如图4所示,其左、右齿面具有不等的轴向节距. 图4中,实线表示变导程渐厚齿形,点线表示标准齿形. 若t d1 为右侧轴向节距, t x1 为左侧轴向节距, t0为公称轴向节距, V t 为左、右侧节距与公称节距的差值, 则:t d1 t x1 = t+ Vt; = t0 - V t.56 周口师范学院学报 2005年 5月πm 0 由此看出 , 以中间的某一个齿厚度 为标准值 , 则向一侧2 的螺牙厚度依次递减 , 而向另一侧的螺牙厚度依次递增 , 形成了一种渐变的齿厚 .3. 2. 2 调整间隙原理 由于蜗杆齿顶与齿根尺寸分别为公称齿顶与齿根尺寸 ,因此 , 若设备上采用了这种蜗杆结构后 , 只需轴向左 、右移动蜗杆 , 就能方便地调整蜗杆与蜗轮的齿侧间隙 , 以保证正确的侧隙. 其原理如下 :由于蜗杆左 、右侧节距不等 , 左 、右侧模数也不等 .图 4 双导程蜗杆传动链说明图 t d 1 t 0 +Δt = m 0即 m d 1 = π 但与之相啮合的蜗轮齿厚相等 . 左 、右侧模数相等 . 取 d 2 , D e 2 分别为蜗轮公称分度圆和齿顶圆直径 齿顶圆直径 ; d x 2 , D e x 2 为蜗轮左侧齿面的分度圆和齿顶圆直径则= m 0 ( Z 2 + 2 f ’= m d ( Z 2 + 2 f ’ ) > D e 2 ,= m x ( Z 2 + 2 f ’ ) < D e 2 .d 2 = m 0 z 2 ,= m d ×z 2 > d 2 ,= m x ×z 2 < d 2 , D e 2 D e d 2 D e x 2 d d 2 d x 2 蜗轮轮齿两侧的齿顶圆和齿根圆直径必须分别相同 ,都应等于公称齿顶圆和齿根圆直径 . 因此 ,把小模数侧进行正变位 ,把大模数侧进行负变位 . 这样 ,蜗杆与蜗轮不仅能正常相互啮合传动 ,且还能调整相互啮合的侧隙. 当蜗轮副摩损传动间隙过大时 ,通过增减蜗杆两端的垫片使蜗杆轴向移动 ,从而达到调整间隙的作用. 4 结束语图 5 传动间隙数据示意图 以上列举了常用的一些在机床改造中提高传动精度的措施 ,分析了它们的优点和不足之处 ,又针对具 体某型号铣齿机的数控改造 ,提出了新的消除传动间隙的办法 ,可为其他类型机床的改造提供参考. 参考文献 :[ 1 ] 李 佳 . 数控机床及应用 [M ]. 北京 :清华大学出版社 , 2001.[ 2 ] 载 曙 . 金属切削机床设计 [M ]. 北京 :机械工业出版社 , 1985.[ 3 ] 吴大任 ,骆家舜 . 齿轮啮合原理 [M ]. 北京 :科学出版社 , 1985.[ 4 ] 余梦生 . 吴宗泽 . 机械零部件手册 [M ]. 北京 :机械工业出版社 , 1996.[ 5 ] 王立勇 . 双导程蜗杆副在设备维修中的应用 [ J ]. 制造技术与机床 , 1998, ( 7 ) : 13 - 14.The n e w m ea sure s to i m prove tran s m iss i on prec is i on of feed sy s temL I D a Οq i ng 1 , 2 , D E N G X i ao Οz hong 1 , ZHAN G M i ng Οz hu 1 , L I Feng 1( 1. H e nan U n i ve r sity of S c i ence and Techno l o g y , L u oyang 471039, Ch i na;2. Puyang Voca t ion Techno l og y Co l leg e, Puyang , 457000 , Ch i na )A b s tra c t : How to i m p r ove tran s m ission p rec i si o n of feed d r ive gea r ing is an i m po r tan t item when the m a ch i ne too l is rebu l t .Th i s p a p e r ana l yse s s om e o r d i na r y way s and p u t s fo r wa r d a few new m e a su r e s fo r a typ e of g ea r Οm a k i ng m a ch i ne too l . Key word s : tran s m issi o n p ric i si o n hyd r au l ic damp e r d o ub l e p itch wo r m。
- 1、下载文档前请自行甄别文档内容的完整性,平台不提供额外的编辑、内容补充、找答案等附加服务。
- 2、"仅部分预览"的文档,不可在线预览部分如存在完整性等问题,可反馈申请退款(可完整预览的文档不适用该条件!)。
- 3、如文档侵犯您的权益,请联系客服反馈,我们会尽快为您处理(人工客服工作时间:9:00-18:30)。
文章编号:1001-2265(2008)08-0001-04收稿日期:2008-03-24;修回日期:2008-04-30 3基金项目:国家自然基金资助项目(50675124)作者简介:许向荣(1978—),男,山西曲沃人,山东大学机械工程学院博士研究生,山东建筑大学机电工程学院讲师,研究方向为机电一体化,(E-mail )xt7875@ 。
提高数控机床滚珠丝杠进给系统机械刚度的措施3许向荣1,2,宋现春2,姜洪奎2(1.山东大学机械工程学院,济南 250061;2.山东建筑大学机电工程学院,济南 250101)摘要:现代数控机床要求其进给系统在较高进给速度下具有很好的定位精度和较高的速度适应能力,这就要求进给系统要有较高的刚度。
文章分析了影响数控机床滚珠丝杠进给系统刚度的主要因素,提出了提高进给系统刚度的技术措施。
关键词:滚珠丝杠进给系统;刚度;滚珠丝杠副;双滚珠丝杠驱动中图分类号:TG65 文献标识码:AThe M ea sure for I m prov i n g the Sti ffness of Ba ll Screw Feed i n g Syste m for NC M ach i n e ToolXU Xiang 2r ong 1,2,S ONG Xian 2chun 2,J I A NG Hong 2kui2(1.College of Mechanical Engineering,University of Shandong,J i ’nan 250061;2.School of Mechatr onics,Shandong J ianzhu University,J i ’nan 250101,China )Abstract:Key words:0 引言目前,数控机床正朝着高精度、高速度、高可靠性以及智能化、数字化、绿色环保等方向发展。
而我国数控机床在技术水平,性能和质量等方面与国外发达国家有很大差距。
因此加快我国数控机床及其功能部件的发展速度是当务之急。
高速数控机床进给系统一般依靠两种传动方式:高速精密滚珠丝杠副传动和直线电机传动。
其中滚珠丝杠副传动方式由于采用旋转电机,到联轴器,再经过滚珠丝杠螺母等一系列中间传动和变换环节,因此使得整个传动系统的刚度降低。
其中由于滚珠丝杠属细长杆件,其变形最大,因而是刚度最薄弱的环节,导致了系统的稳定性、定位精度等性能指标的下降,使得滚珠丝杠进给系统的速度及加速度都很难得到提高。
数控机床的定位精度,是评定机床性能的一项重要指标。
定位精度是指数控工作台部件在要求的终点所达到的实际位置的精度。
通常用实际位置与理想位置之间的误差———定位误差来表达,误差越小,则定位精度越高。
它包括伺服系统、检测系统、工作台进给系统的误差和工作台导轨的几何误差,而工作台进给系统的误差主要取决于进给系统的刚度、传动间隙及热变形的大小。
而进给系统的刚度是决定预紧力大小并最终决定摩擦和传动间隙大小的主要因素[1]。
所以提高滚珠丝杠进给系统的刚度,对于提高数控机床定位精度仍具有很重要的意义。
1 滚珠丝杠进给系统基本组成如图1所示,滚珠丝杠进给系统结构简图。
滚珠丝杠进给系统是指将伺服电机的旋转运动变为工作台直线运动的整个机械传动链,主要包括联轴器、丝杠螺母副及导向元件、支撑轴承等。
作为数控机・1・床的重要部分,它主要完成刀具相对工作位置的自动控制和机床各坐标进给速度的控制,是影响数控机床各项性能的主要因素。
图1 滚珠丝杠进给系统结构简图2 滚珠丝杠进给系统刚度滚珠丝杠进给系统刚度来自于进给系统机械传动链中各弹性元件的弹性变形。
它表示系统抵抗变形的能力。
一般以在加载方向上使某一零件产生变形量ΔL 为1μm 时所需要的力F (N )来表示,即:K =F /ΔL 滚珠丝杠进给系统刚度包括:(1)滚珠丝杠进给系统的轴向刚度滚珠丝杠进给系统的轴向刚度主要是指滚珠丝杠副的传动刚度。
包括滚珠丝杠副的轴向刚度和扭转刚度折合成的轴向刚度。
滚珠丝杠副的轴向刚度(N /μm )一般指滚珠丝杠副和支撑丝杠的轴承在内的传动系统的综合拉压刚度,它表示滚珠丝杠副及其支承部件抵抗轴向变形的能力。
丝杠的扭转刚度主要是指丝杠抵抗扭转变形的能力。
扭转变形可以折算成轴向变形,并入轴向刚度计算。
(2)滚珠丝杠进给系统的径向刚度滚珠丝杠进给系统的径向变形主要包括工作台和丝杠自重引起的弯曲变形,滚珠丝杠支承座的径向变形,以及进给系统直线滚动导轨的径向变形。
工作台和丝杠自重引起的弯曲变形量较小,或直接或间接地与滚珠丝杠副的支承方式有关[2];滚珠丝杠支承座的径向变形,一般情况下,可以忽略不计,通过采用高刚度支撑部件来解决;直线滚动导轨的径向变形对于丝杠的弯曲变形相当于一个约束力,这部分变形一般情况下,也可以忽略不计。
这里主要讨论滚珠丝杠进给系统的轴向刚度。
3 滚珠丝杠进给系统轴向刚度的影响因素(1)滚珠丝杠副的轴向刚度实际工作中,滚珠丝杠主要承受轴向载荷,除丝杠本身的自重以外,一般不承受径向外载荷,因而进给系统的轴向传动刚度K 就可视为与滚珠丝杠相关联的零部件刚度的串联总和。
用弹簧常数K 1表示,按下式计算。
K 1=F /δ11K 1=1K S+1K N+1K B+1K H式中:K 1———进给滚珠丝杠副传动系统轴向刚度,N /μm ;F ———施加于进给丝杠的轴向负载,N ;δ1———进给滚珠丝杠副轴向弹性位移,μm ;K S ———丝杠轴向刚度,N /μm ;K N ———螺母组件轴向刚度,N /μm ;K B ———支承轴承轴向刚度,N /μm ;K H ———螺母支架及轴承支架轴向刚度,N /μm 。
①滚珠丝杠轴向刚度K S通常丝杠受轴向载荷作用而产生的轴向拉压变形约占整个进给传动系统误差的30%~50%,因而要特别重视提高丝杠的轴向拉压刚度Ks [3]。
K s =πd 2c ・E4l s ×103N /μm 其中,l s ———螺母到丝杠轴向固定处距离,mm ;E ———丝杠材料弹性模量,对于钢材:E =2107×105MPa ;d c ———滚珠丝杠受载点直径,mm 。
d c =D p w -D W ×cosα式中:D p w ———滚珠丝杠公称直径,mm ;D w ———滚珠直径,mm ;α———接触角,(°)。
从上式可以看出螺母至丝杠轴向固定处的距离越近,接触角越大,公称直径越大,滚珠直径越小,丝杠的轴向刚度越高。
②螺母组件轴向刚度K N螺母组件的变形量包括螺母和螺母座的变形量,螺母的固定螺栓所产生的轴向变形量和滚珠与滚道面弹性接触变形所引起的轴向变形量。
由于尽量使螺母和螺母座的刚性好,故其变形甚微。
当采用预紧螺母时,对固定螺栓的变形量可略去不计。
故对螺母组件・2・的变形只需考虑滚珠和滚道面弹性接触变形。
所以螺母组件的刚度,包括滚珠和丝杠、螺母螺纹滚道的轴向刚度。
根据赫兹接触理论,滚珠和螺纹滚道间的轴向弹性变形量δN按下式计算:δN =214sinαF2×10-2Z2d0sin2α1/3式中:α———滚珠的接触角,(°);F———轴向载荷,N;d0———滚珠直径,mm;Z———每圈有效载荷滚珠数,Z=πD m/d0cosφ;D m———螺母公称直径,mm;<———螺旋升角(°)。
滚珠/滚道区的弹性接触刚度与下列因素有关:轴向载荷,滚珠直径,丝杠公称直径,承受载荷滚珠的个数,接触角和螺旋升角。
且轴向载荷越小,滚珠直径越小,螺旋升角越大,螺母公称直径越大,接触角越大,滚珠/滚道区的弹性接触刚度越高。
螺母组件的刚度一般根据产品样本中给出的刚度值来计算。
尤其是双螺母预紧情况下还与预紧力有关。
具体计算公式见参考文献[4]。
③支承轴承轴向刚度KB按赫兹弹性接触理论计算。
轴承类别[5]不同,刚度计算公式也不同。
不加预压载荷时,轴承轴向刚度按下式计算K B=F/δB式中:F———轴向载荷,N;δB———轴承轴向弹性位移量,μm。
施加预压载荷时,轴承轴向刚度计算公式为K B =3Fao/δao式中:Fao———轴向预压载荷,N;δao———在预压载荷作用下,轴向弹性位移。
支承轴承轴向刚度与轴向载荷、预紧力及轴承本身的结构有关。
④螺母支架及轴承支架轴向刚度KH螺母支架的刚度或忽略不计,或在计算螺母刚度是乘以系数018记入。
轴承支架的刚度可通过采用高刚度支承部件解决。
(2)滚珠丝杠副的扭转刚度引起的轴向变形滚珠丝杠副的扭转刚度引起的轴向变形量为:δ2=MKT×P h2π×103=FKT×P h2π2×103(μm)式中:KT———丝杠扭转刚度,N・mm/rad;M———扭矩,N・mm;P H———滚珠丝杠导程,mm。
(3)滚珠丝杠进给系统的传动刚度设滚珠丝杠副轴向变形为δ1,则滚珠丝杠进给系统的轴向变形为应为δ1+δ2。
其传动刚度K应为K=Fδ1+δ2可见,滚珠丝杠副的扭转刚度引起的轴向变形与扭矩、导程的大小有关,而且导程越大,扭矩越大,滚珠丝杠进给系统的传动刚度越低。
而扭矩的大小又与传动系统中各传动件的速度有关,速度越大,扭矩越大。
所以提高各传动件的转速和丝杠的导程,反而会降低滚珠丝杠进给系统的传动刚度。
4 提高滚珠丝杠进给系统机械刚度的措施从前面的分析可以知道,滚珠丝杠副的传动刚度与滚珠丝杠副的结构(丝杠螺母公称直径,滚珠直径、接触角、螺旋升角、导程等)、支承形式[6]和轴承的结构及布置、预紧力大小有关。
因此,要提高滚珠丝杠进给系统的刚度主要从以下方面着手:(1)适当减小滚珠直径滚珠直径越小,丝杠和滚珠螺母组件的刚度就越高。
而且随着数控机床进给系统的高速化,滚珠丝杠中滚珠的自旋速度、公转速度很大,会产生很大的离心力和陀螺力矩,这是丝杠滚珠直径小,有利于减小离心力和陀螺力矩。
而且滚珠直径减小,滚珠的承载能力也减弱,因此,现在已有些高速丝杠采用小直径氮化硅Si3O4陶瓷球[7],其具有硬度高,密度小,弹性模量大,热膨胀系数小,磨损小等优点。
(2)适当加大螺旋升角加大螺旋升角可以提高滚珠丝杠螺母组件接触刚度。
增大螺旋升角,导程亦增大,虽然可以实现高速进给,但是加大导程会增大滚珠丝杠的扭转变形,降低进给系统的传动刚度。
(3)施加合适的预紧力,使滚珠与滚道面接触点处产生一定量的预变形。
滚珠螺旋副承受轴向工作载荷后,在滚珠与螺纹滚道面的接触点处将产生一定量的弹性接触变形,并将直接影响到它的轴向刚度,从而降低其传动的质量。
从前文中可以知道,适当加大预紧力,有利于提高滚珠・3・丝杠螺母组件和支承轴承的刚度。
但是过大的预紧力会使滚珠螺旋副在工作中产生过大的接触应力和变形,增加摩擦力,降低传动效率,从而缩短其工作寿命。