五金件检验规范
五金零件检验规范

目视
卡尺
3
生
锈
(1)
表面不允许生锈、氧化
√
目视
(2)
切断面生锈表面不作任何处理切割面在各制程不可超出切割面的20﹪
√
目视
(3)
表面有做防锈处理有效期为15天内不可有生锈
√
目视
4
毛
边
(1)
切断面不可有齿状毛边
√
目视
(2)
可允许毛边为其材料厚度的7%,上限不可超过0.06㎜
√
卡尺
(3)
放置时,毛边必须同方向
五金
品名
五金类产品
AQL
检
验
方
式
抽样计划
ANSI/ASQC Z1.4/ MIL-STD-105E(其它客户)单次正常抽样
CR
MAS
MIN
项目
项次
品质标准
0
0.40
065
一.
外
观
1
颜
色
(1)
颜色与确认颜色无明显差异
√
目视
(2)
电镀时处理不良,造成异常色之纹路、电镀层脱过薄变色不允许
√
目视
(3)
表面不可出现灼伤,黑色、白斑造成异色
√
卡尺
投影机
(2)
铁材厚度规格须与客户求一致,公差±0.05㎜
√
卡尺
(3)
下料模具用钢板,长度公差±0.5㎜,宽度公差±0.2㎜,对角线公差±0.5㎜
√
卡尺
(4)
切边模用钢板,长度公差+0(-0.5)㎜,宽度公差+0(-0.2)㎜,对角线公差+0(0.5)㎜
√
卡尺
(5)
冲压孔位,折边、折弯尺寸不符、偏差、角度不符
五金产品检验规范

4.14焊接疤痕:产品焊接后未经打磨刨光而残留的凸起疤痕。
4.15色差:产品表面颜色与标准样品颜色有差异。
4.16异色点:在产品表面出现颜色异于周围颜色的点。
4.17破裂:因机加工损伤而造成产品的裂纹或细小开裂。
4.18麻点:喷涂件表面上有附著的细小颗粒。
一.目的
为规范五金件的检验作业,明确检验内容和要求,有效管控材料品质,确保满足顾客和生产需要。
二.范围
适用于公司所有五金件的进料检验。
三.抽样方案
采用GB/T2828.1-2003单次抽样,检查水平(IL)和接收质量(AQL)遵循如下规定:
项目
检查水平(IL)
接收质量限(AQL)
外观
Ⅱ
0.65
尺寸
S-2
4.5毛边:由于机械冲压或切割后未处理好,导致加工件边缘或分型面处所产生的金属毛刺。
4.6划伤:由于在加工或包装、运输过程中防护不当导致产品表面出现的划痕、削伤。
4.7裁切不齐:由于产品在加工过程中定位或设备固定不当,导致产品边缘切割不齐。
4.8变形:因加工设备调校不当或材料因内应力而造成的产品平面形变。
2
3
5
4<L<8,0.2<W<0.3,DS>50
1
2
3
8<L<10,W<0.3,DS>50
0
1
2
4
堆漆
不允许
5
缩水
参照限度样品。
6
飞油
L<0.3或参照限度样品。
7
剥落
不允许
8
色差
△E<1.0或参照限度样品
9
光泽度
五金件检验规范
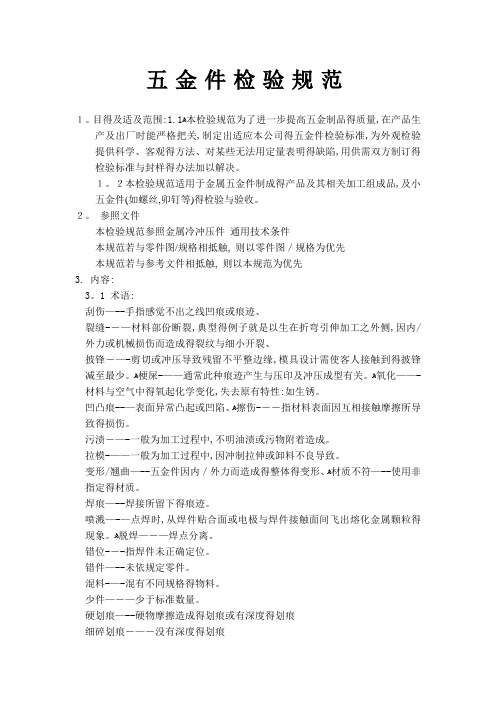
五金件检验规范1.1本检验规范为了进一步提高五金制品得质量,在产品生1。
目得及适及范围:ﻫ产及出厂时能严格把关,制定出适应本公司得五金件检验标准,为外观检验提供科学、客观得方法、对某些无法用定量表明得缺陷,用供需双方制订得检验标准与封样得办法加以解决。
1。
2本检验规范适用于金属五金件制成得产品及其相关加工组成品,及小五金件(如螺丝,卯钉等)得检验与验收。
2。
参照文件本检验规范参照金属冷冲压件通用技术条件本规范若与零件图/规格相抵触, 则以零件图/规格为优先本规范若与参考文件相抵触, 则以本规范为优先3. 内容:3。
1 术语:刮伤—--手指感觉不出之线凹痕或痕迹、裂缝--—材料部份断裂,典型得例子就是以生在折弯引伸加工之外侧,因内/外力或机械损伤而造成得裂纹与细小开裂、披锋-—-剪切或冲压导致残留不平整边缘,模具设计需使客人接触到得披锋减至最少。
ﻫ梗屎-——通常此种痕迹产生与压印及冲压成型有关。
ﻫ氧化——-材料与空气中得氧起化学变化,失去原有特性:如生锈。
凹凸痕--—表面异常凸起或凹陷、ﻫ擦伤---指材料表面因互相接触摩擦所导致得损伤。
污渍-—-一般为加工过程中,不明油渍或污物附着造成。
拉模-——一般为加工过程中,因冲制拉伸或卸料不良导致。
变形/翘曲—--五金件因内/外力而造成得整体得变形、ﻫ材质不符—--使用非指定得材质。
焊痕—--焊接所留下得痕迹。
喷溅—-—点焊时,从焊件贴合面或电极与焊件接触面间飞出熔化金属颗粒得现象。
ﻫ脱焊—-—焊点分离。
错位---指焊件未正确定位。
错件—--未依规定零件。
混料-—-混有不同规格得物料。
少件—-—少于标准数量。
硬划痕—--硬物摩擦造成得划痕或有深度得划痕细碎划痕-—-没有深度得划痕手印———在五金件表面或零件光亮面出现得手指印痕。
3。
2 检验方法3.2、1外观缺陷得检验方法及要求: 将待验品置于以下条件,作检验判定:A 、目测距离: 距离产品25c mﻫB、检验角度: 成45度目视检试之。
五金件检验规范
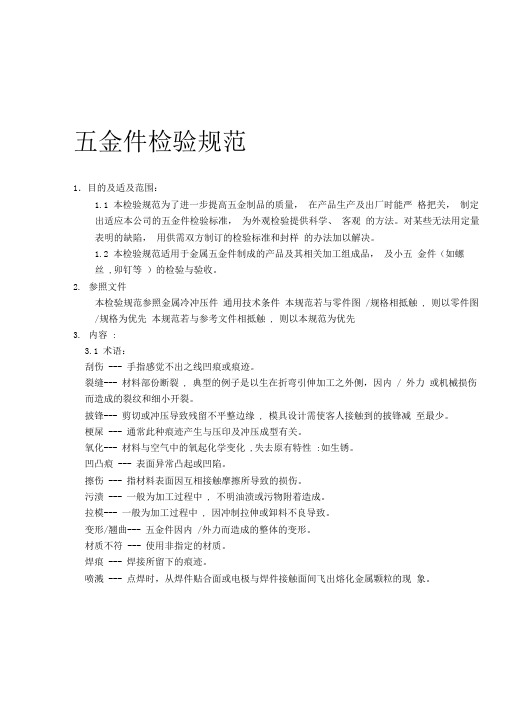
五金件检验规范1.目的及适及范围:1.1本检验规范为了进一步提高五金制品的质量,在产品生产及出厂时能严格把关,制定出适应本公司的五金件检验标准,为外观检验提供科学、客观的方法。
对某些无法用定量表明的缺陷,用供需双方制订的检验标准和封样的办法加以解决。
1.2本检验规范适用于金属五金件制成的产品及其相关加工组成品,及小五金件(如螺丝,卯钉等)的检验与验收。
2.参照文件本检验规范参照金属冷冲压件通用技术条件本规范若与零件图/规格相抵触, 则以零件图/规格为优先本规范若与参考文件相抵触, 则以本规范为优先3.内容:3.1 术语:刮伤--- 手指感觉不出之线凹痕或痕迹。
裂缝--- 材料部份断裂, 典型的例子是以生在折弯引伸加工之外侧,因内/ 外力或机械损伤而造成的裂纹和细小开裂。
披锋--- 剪切或冲压导致残留不平整边缘, 模具设计需使客人接触到的披锋减至最少。
梗屎--- 通常此种痕迹产生与压印及冲压成型有关。
氧化--- 材料与空气中的氧起化学变化,失去原有特性:如生锈。
凹凸痕--- 表面异常凸起或凹陷。
擦伤--- 指材料表面因互相接触摩擦所导致的损伤。
污渍--- 一般为加工过程中, 不明油渍或污物附着造成。
拉模--- 一般为加工过程中, 因冲制拉伸或卸料不良导致。
变形/翘曲--- 五金件因内/外力而造成的整体的变形。
材质不符--- 使用非指定的材质。
焊痕--- 焊接所留下的痕迹。
喷溅--- 点焊时,从焊件贴合面或电极与焊件接触面间飞出熔化金属颗粒的现象。
脱焊---焊点分离。
错位---指焊件未正确定位。
错件---未依规定零件。
混料---混有不同规格的物料。
少件---少于标准数量.硬划痕---硬物摩擦造成的划痕或有深度的划痕 细碎划痕---没有深度的划痕手印---在五金件表面或零件光亮面出现的手指印痕。
3.2检验方法3.2.1外观缺陷的检验方法及要求: 将待验品置于以下条件,作检验判定:E 检查半成品、成品之前应核对相关检验资料。
五金质量检验标准

五金质量检验标准在制造业中,五金制品的质量检验标准是确保生产出优质产品的重要环节。
五金制品的质量不仅影响到产品的使用寿命和性能,还关系到用户的安全和满意度。
因此,制定一套科学、合理的五金质量检验标准至关重要。
一、材料检验1、五金制品的材料应符合相关国家和行业标准,如不锈钢、铝合金等。
检验人员应检查材料的质量证书、材质证明等文件,确保材料来源合法、质量合格。
2、材料表面应无裂纹、气泡、起皮等缺陷,色泽均匀,无明显划痕和压痕。
3、材料厚度应符合设计要求,厚薄均匀,不能有明显的薄厚不均现象。
二、尺寸检验1、五金制品的尺寸应符合设计图纸的要求,误差应在允许范围内。
检验人员应使用测量工具对制品的尺寸进行精确测量。
2、制品的各部分尺寸应符合相关标准和行业规范,如螺丝孔的大小和深度、铆钉的直径和长度等。
三、表面处理检验1、五金制品的表面处理应均匀、光滑,不能有明显的色差、气泡、划痕等缺陷。
2、电镀、喷涂等表面处理应符合相关工艺要求,如膜厚、附着力等。
四、力学性能检验1、五金制品的力学性能应符合相关国家和行业标准,如拉伸强度、屈服强度、硬度等。
检验人员应按照标准规定的试验方法进行检测。
2、对于需要进行疲劳试验的制品,应按照规定进行疲劳试验,以确定其使用寿命。
五、安全性能检验1、五金制品的安全性能应符合相关国家和行业标准,如防火性能、防腐蚀性能等。
检验人员应按照标准规定的试验方法进行检测。
2、对于涉及到使用者安全的制品,如门窗五金件、卫浴五金件等,应进行安全性评估,确保不会对使用者造成伤害。
六、环境适应性检验1、五金制品的环境适应性应符合相关国家和行业标准,如耐候性、耐腐蚀性等。
检验人员应按照标准规定的试验方法进行检测。
2、对于在特殊环境下使用的制品,如高温环境、低温环境、强腐蚀环境等,应进行环境适应性评估,确保制品能够在相应环境下正常工作。
五金质量检验标准涵盖了材料、尺寸、表面处理、力学性能、安全性能和环境适应性等多个方面。
五金件通用检验规范
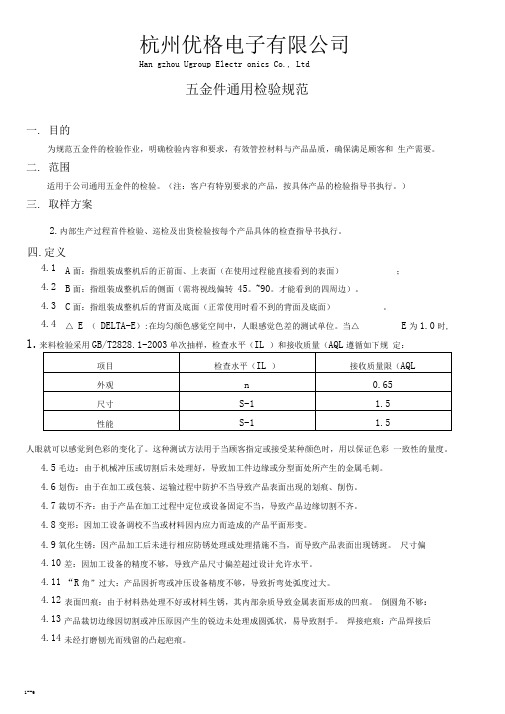
杭州优格电子有限公司Han gzhou Ugroup Electr onics Co., Ltd五金件通用检验规范一. 目的为规范五金件的检验作业,明确检验内容和要求,有效管控材料与产品品质,确保满足顾客和 生产需要。
二. 范围适用于公司通用五金件的检验。
(注:客户有特别要求的产品,按具体产品的检验指导书执行。
)三. 取样方案1.来料检验采用GB/T2828.1-2003单次抽样,检查水平(IL )和接收质量(AQL 遵循如下规 定:人眼就可以感觉到色彩的变化了。
这种测试方法用于当顾客指定或接受某种颜色时,用以保证色彩 一致性的量度。
2.内部生产过程首件检验、巡检及出货检验按每个产品具体的检查指导书执行。
四.定义A 面:指组装成整机后的正前面、上表面(在使用过程能直接看到的表面) ;B 面:指组装成整机后的侧面(需将视线偏转 45。
~90。
才能看到的四周边)。
C 面:指组装成整机后的背面及底面(正常使用时看不到的背面及底面)。
△ E ( DELTA-E ):在均匀颜色感觉空间中,人眼感觉色差的测试单位。
当△E 为1.0时,4.1 4.2 4.3 4.4 4.5毛边:由于机械冲压或切割后未处理好,导致加工件边缘或分型面处所产生的金属毛刺。
4.6划伤:由于在加工或包装、运输过程中防护不当导致产品表面出现的划痕、削伤。
4.7裁切不齐:由于产品在加工过程中定位或设备固定不当,导致产品边缘切割不齐。
4.8变形:因加工设备调校不当或材料因内应力而造成的产品平面形变。
4.9氧化生锈:因产品加工后未进行相应防锈处理或处理措施不当,而导致产品表面出现锈斑。
尺寸偏差:因加工设备的精度不够,导致产品尺寸偏差超过设计允许水平。
“R 角”过大:产品因折弯或冲压设备精度不够,导致折弯处弧度过大。
表面凹痕:由于材料热处理不好或材料生锈,其内部杂质导致金属表面形成的凹痕。
倒圆角不够:产品裁切边缘因切割或冲压原因产生的锐边未处理成圆弧状,易导致割手。
五金产品检验规范

五金产品进料检查原则塑料件检查原则目旳: 由于塑料件产品在注塑、喷涂等一系列过程中存在诸多缺陷, 为了明确检查原则, 衡量产品缺陷限度, 同步, 为了让多数员工从主线上理解并掌握常见注塑产品旳缺陷名称和成因, 特制定本原则。
注塑件常见缺陷定义1.生产过程中, 常见旳产品缺陷如下:2.开裂: 塑料件局部受内应力, 外部冲击或环境条件等影响而在其表面或内部产生旳裂纹。
3.缩痕: 注塑件在模腔冷却凝固时, 由于注塑件壁厚不均, 凝固快慢不同, 在注塑件表面产生旳凹陷。
4.熔接痕:注塑件旳一种线状痕迹, 重要是由注塑成型中两股料流相遇时在其界面处未完全熔合而导致旳痕迹。
5.料流痕: 由于模具构造、成型工艺以及材料等因素, 使得塑料件在模腔内受注塑压力和料流速度旳影响在注塑表面上产生看得见旳料流痕迹, 一般采用喷涂解决。
6.银丝: 低分子挥发物、水分等气体在注塑件表面形成旳银白色条纹。
7.白印:注塑件局部受外力作用, 使材料内部部分分子构造重新排列或断裂, 引起注塑件表面发白旳印迹。
(又称顶白)。
8.飞边: 在注塑过程中溢入模具合模面以及嵌拼件旳间隙中, 冷却后留在注塑件上旳多余物。
9.拉毛: 注塑件表面因机械摩擦而产生旳无光泽、无深度感旳痕迹。
10.杂色、斑点:由于材料混入了异物, 成型后, 在其表面上浮现旳斑点。
11.翘曲:注塑件在注塑成型后, 由于内应力作用, 使注塑件局部或整体发生旳变形。
12.分层: 注塑件发生层间分离旳缺陷。
13.损伤: 塑料件表面旳机械划伤、碰伤或擦伤。
轻微可打磨喷涂。
14.剥离:受外界或加工旳影响, 油漆表面部分分离底材而导致旳缺陷。
15.附着力: 油漆和底材结合旳能力。
(油漆漆膜旳性能)16.针孔:喷涂时, 油漆漆膜表面上产生像针尖同样旳小孔。
17.漆点、漆丝: 油漆表面因杂质引起旳凹凸点。
18.气泡: 塑料件在加工时, 由于残留旳空气或其他气体在塑料件内部或表面上形成旳泡状缺陷。
五金件检验标准
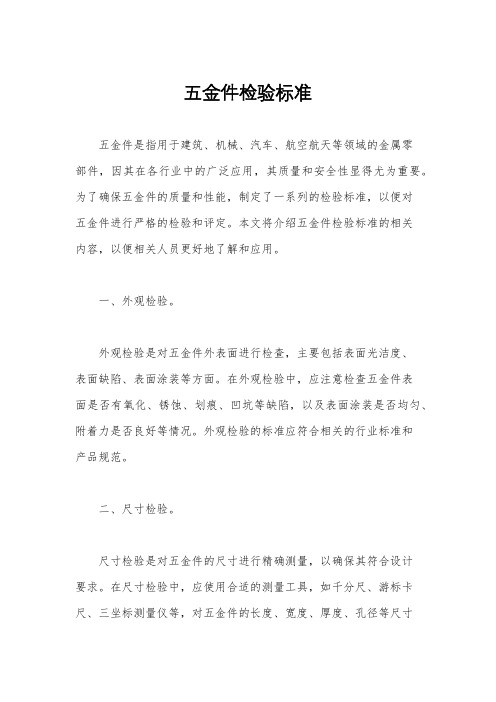
五金件检验标准五金件是指用于建筑、机械、汽车、航空航天等领域的金属零部件,因其在各行业中的广泛应用,其质量和安全性显得尤为重要。
为了确保五金件的质量和性能,制定了一系列的检验标准,以便对五金件进行严格的检验和评定。
本文将介绍五金件检验标准的相关内容,以便相关人员更好地了解和应用。
一、外观检验。
外观检验是对五金件外表面进行检查,主要包括表面光洁度、表面缺陷、表面涂装等方面。
在外观检验中,应注意检查五金件表面是否有氧化、锈蚀、划痕、凹坑等缺陷,以及表面涂装是否均匀、附着力是否良好等情况。
外观检验的标准应符合相关的行业标准和产品规范。
二、尺寸检验。
尺寸检验是对五金件的尺寸进行精确测量,以确保其符合设计要求。
在尺寸检验中,应使用合适的测量工具,如千分尺、游标卡尺、三坐标测量仪等,对五金件的长度、宽度、厚度、孔径等尺寸进行测量,并与设计图纸进行对比,判断其尺寸是否合格。
三、材质检验。
材质检验是对五金件所采用的材料进行检验,以确保其材质符合要求。
在材质检验中,应对五金件的材料进行化学成分分析、金相组织检验、硬度测试等,以确定其材质是否符合相关标准和要求。
四、功能性能检验。
功能性能检验是对五金件的功能和性能进行检验,以确保其能够正常使用。
在功能性能检验中,应对五金件的承载能力、耐磨性、耐腐蚀性等功能进行测试,以确保其能够满足设计要求和使用需求。
五、环境适应性检验。
环境适应性检验是对五金件在不同环境条件下的适应性进行检验,以确保其能够在各种环境条件下正常使用。
在环境适应性检验中,应对五金件进行高温、低温、湿热、盐雾等环境条件下的测试,以确定其在各种环境条件下的性能表现。
六、标识检验。
标识检验是对五金件的标识进行检验,以确保其标识清晰、准确、完整。
在标识检验中,应对五金件的标识内容、位置、方式等进行检查,以确保其符合相关标准和规定。
综上所述,五金件检验标准是确保五金件质量和性能的重要手段,通过严格的外观检验、尺寸检验、材质检验、功能性能检验、环境适应性检验和标识检验,可以有效地对五金件进行全面的检验和评定,以确保其质量和安全性。
五金类通用检验规范

5.5试装检验(5PCS/LOT)
5.5.1上下壳组装后检查是否能组装到位或缝隙≤0.3mm,正负段差≤0.2mm,配合不可有偏位或不顺畅.
5.5.2螺纹类材料用相应牙/环规检验是否符合标准要求.
5.5.3螺牙型材料进行电批锁装,检验是否有滑牙、锁不到位现象;
版本
文件编号
制/修订内容
生效日期
制/修部门
拟 订
A/0
SW-IQC-028
初次发行
审核栏:
□
签名:
日期:
□
签名:
日期:
□
签名:
日期:
□
签名:
日期:
□
签名:
日期:
□
签名:
日期:
□
签名:
日期:
□
签名:
日期:
批准栏:
□
签名:
日期:
文件分发部门(需要则打√):
()总经办
()品质部
()开发部
()工程部
()生产部
5.3.5丝刷部分不可能模糊不清、缺划、粗细不均、脱落、颜色不符;
5.3.6电镀材料注意镀层不可有脱落、发白、发黑、发黄等现象;
5.3.7螺纹形材料不可有烂牙、光钉、偏位、牙纹不符承样要求.
5.4尺寸检验
5.4.1依样品承认书图示尺寸为准;
5.4.2使用游标卡尺或其它量测设备检验本体长宽高、脚间距和内外径是否符合要求;
√
17.油迹
√
18.熔接线D≤0.1 mm距离≥10 MM
√
19.桔纹
√
20.水口位高出
√
21.氧化,生绣
√
22.螺丝孔异常
五金件检验规范标准

五金件检验规1.目的及适及围:1.1本检验规为了进一步提高五金制品的质量,在产品生产及出厂时能严格把关,制定出适应本公司的五金件检验标准,为外观检验提供科学、客观的方法。
对某些无法用定量表明的缺陷,用供需双方制订的检验标准和封样的办法加以解决。
1.2本检验规适用于金属五金件制成的产品及其相关加工组成品,及小五金件(如螺丝,卯钉等)的检验与验收。
2. 参照文件本检验规参照金属冷冲压件通用技术条件本规若与零件图/规格相抵触, 则以零件图/规格为优先本规若与参考文件相抵触, 则以本规为优先3. 容:3.1 术语:刮伤---手指感觉不出之线凹痕或痕迹。
裂缝---材料部份断裂,典型的例子是以生在折弯引伸加工之外侧,因/外力或机械损伤而造成的裂纹和细小开裂。
披锋---剪切或冲压导致残留不平整边缘,模具设计需使客人接触到的披锋减至最少。
梗屎---通常此种痕迹产生与压印及冲压成型有关。
氧化---材料与空气中的氧起化学变化,失去原有特性:如生锈。
凹凸痕---表面异常凸起或凹陷。
擦伤---指材料表面因互相接触摩擦所导致的损伤。
污渍---一般为加工过程中,不明油渍或污物附着造成。
拉模---一般为加工过程中,因冲制拉伸或卸料不良导致。
变形/翘曲---五金件因/外力而造成的整体的变形。
材质不符---使用非指定的材质。
焊痕---焊接所留下的痕迹。
喷溅---点焊时,从焊件贴合面或电极与焊件接触面间飞出熔化金属颗粒的现象。
脱焊---焊点分离。
错位---指焊件未正确定位。
错件---未依规定零件。
混料---混有不同规格的物料。
少件---少于标准数量.硬划痕---硬物摩擦造成的划痕或有深度的划痕细碎划痕---没有深度的划痕手印---在五金件表面或零件光亮面出现的手指印痕。
3.2 检验方法3.2.1外观缺陷的检验方法及要求:将待验品置于以下条件,作检验判定:A、目测距离: 距离产品25cmB、检验角度: 成45度目视检试之。
C、检验光源: 正常日光灯,室无日光时用40W日光灯或60W普通灯泡的照度为标准。
五金件检验规范
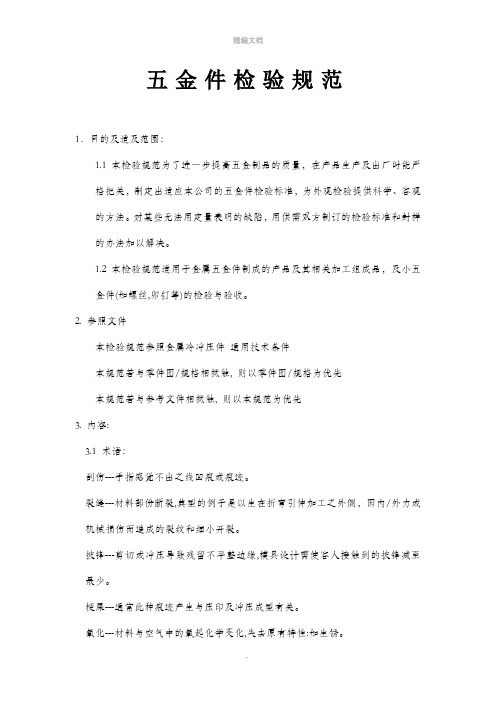
五金件检验规范1.目的及适及范围:1.1本检验规范为了进一步提高五金制品的质量,在产品生产及出厂时能严格把关,制定出适应本公司的五金件检验标准,为外观检验提供科学、客观的方法。
对某些无法用定量表明的缺陷,用供需双方制订的检验标准和封样的办法加以解决。
1.2本检验规范适用于金属五金件制成的产品及其相关加工组成品,及小五金件(如螺丝,卯钉等)的检验与验收。
2. 参照文件本检验规范参照金属冷冲压件通用技术条件本规范若与零件图/规格相抵触, 则以零件图/规格为优先本规范若与参考文件相抵触, 则以本规范为优先3. 内容:3.1 术语:刮伤---手指感觉不出之线凹痕或痕迹。
裂缝---材料部份断裂,典型的例子是以生在折弯引伸加工之外侧,因内/外力或机械损伤而造成的裂纹和细小开裂。
披锋---剪切或冲压导致残留不平整边缘,模具设计需使客人接触到的披锋减至最少。
梗屎---通常此种痕迹产生与压印及冲压成型有关。
氧化---材料与空气中的氧起化学变化,失去原有特性:如生锈。
凹凸痕---表面异常凸起或凹陷。
擦伤---指材料表面因互相接触摩擦所导致的损伤。
污渍---一般为加工过程中,不明油渍或污物附着造成。
拉模---一般为加工过程中,因冲制拉伸或卸料不良导致。
变形/翘曲---五金件因内/外力而造成的整体的变形。
材质不符---使用非指定的材质。
焊痕---焊接所留下的痕迹。
喷溅---点焊时,从焊件贴合面或电极与焊件接触面间飞出熔化金属颗粒的现象。
脱焊---焊点分离。
错位---指焊件未正确定位。
错件---未依规定零件。
混料---混有不同规格的物料。
少件---少于标准数量.硬划痕---硬物摩擦造成的划痕或有深度的划痕细碎划痕---没有深度的划痕手印---在五金件表面或零件光亮面出现的手指印痕。
3.2 检验方法3.2.1外观缺陷的检验方法及要求:将待验品置于以下条件,作检验判定:A、目测距离: 距离产品25cmB 、检验角度: 成45度目视检试之。
五金件检验规范

5.1 外观检验条件
5.1.1 光源:在朝背散射的自然光照下,或在物件距光源0.65~1.0m的40W日光灯下。
5.1.2 目视距离:300-500mm。
5.1.3 目视角度:检测面与人眼方向成45°~90°。
5.1.4 目视时间:5~10S。
5.2 尺寸检验条件
5.2.1 量测工具:精度为0.01mm的游标卡尺、精度为0.1mm的卷尺或钢板尺、精度为0.01mm的塞尺、精度为0.01mm的塞规、色差仪、精度为0.01mm的高度规、精度为0.002mm的横杆表。
8.2.2 判定标准
试验后五金件表面不允许生锈,锐边上的锈迹和任何能够擦掉的淡黄色膜可以忽略不计。
b) 判定标准
表7胶纸粘贴测试判定标准
测试结果/现象
缺陷类别
丝印轻微脱落(丝印内容无损)
MI
丝印脱落(丝印内容仍可清晰分辨)
MA
丝印脱落(丝印内容残缺)
CR(0/1)
8.2 防锈试验
8.2.1 可用5%的盐雾试验来测定,即在35℃温度1千克的压力下连续喷雾3小时,表面无锈为合格产品。当没有盐雾试验设备时,亦可延用3%的标准NaCl溶液做浸渍检验。
不允许
2
氧化、锈斑、电镀不良、气泡、烤漆脱落
不允许
3
混装、短装、缺附件
不允许
4
内部使用的五金件电镀前刮伤
L<30,W<2
不超过5条
L<60,W<5
不超过3条
L<30,W<10
不超过3条
5
电镀后刮伤
不允许
6
点焊、铆接不良
不允许
7
水纹面
S<0.1S
8
攻牙
不允许
五金件检验规范
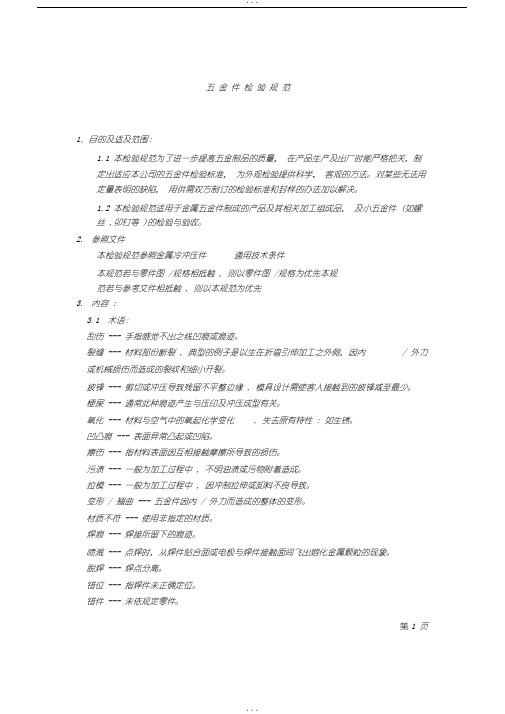
五金件检验规范1.目的及适及范围:1.1 本检验规范为了进一步提高五金制品的质量,在产品生产及出厂时能严格把关,制定出适应本公司的五金件检验标准,为外观检验提供科学、客观的方法。
对某些无法用定量表明的缺陷,用供需双方制订的检验标准和封样的办法加以解决。
1.2 本检验规范适用于金属五金件制成的产品及其相关加工组成品,及小五金件 (如螺丝 ,卯钉等 )的检验与验收。
2.参照文件本检验规范参照金属冷冲压件通用技术条件本规范若与零件图 /规格相抵触 , 则以零件图 /规格为优先本规范若与参考文件相抵触 , 则以本规范为优先3.内容 :3.1 术语:刮伤 --- 手指感觉不出之线凹痕或痕迹。
裂缝 --- 材料部份断裂 , 典型的例子是以生在折弯引伸加工之外侧,因内/ 外力或机械损伤而造成的裂纹和细小开裂。
披锋 --- 剪切或冲压导致残留不平整边缘 , 模具设计需使客人接触到的披锋减至最少。
梗屎 --- 通常此种痕迹产生与压印及冲压成型有关。
氧化 --- 材料与空气中的氧起化学变化, 失去原有特性 : 如生锈。
凹凸痕 --- 表面异常凸起或凹陷。
擦伤 --- 指材料表面因互相接触摩擦所导致的损伤。
污渍 --- 一般为加工过程中 , 不明油渍或污物附着造成。
拉模 --- 一般为加工过程中 , 因冲制拉伸或卸料不良导致。
变形 / 翘曲 --- 五金件因内 / 外力而造成的整体的变形。
材质不符 --- 使用非指定的材质。
焊痕 --- 焊接所留下的痕迹。
喷溅 --- 点焊时,从焊件贴合面或电极与焊件接触面间飞出熔化金属颗粒的现象。
脱焊 --- 焊点分离。
错位 --- 指焊件未正确定位。
错件 --- 未依规定零件。
第1 页混料 --- 混有不同规格的物料。
少件 --- 少于标准数量 .硬划痕 --- 硬物摩擦造成的划痕或有深度的划痕细碎划痕 --- 没有深度的划痕手印 --- 在五金件表面或零件光亮面出现的手指印痕。
五金件检验规范合格品质的基本要求
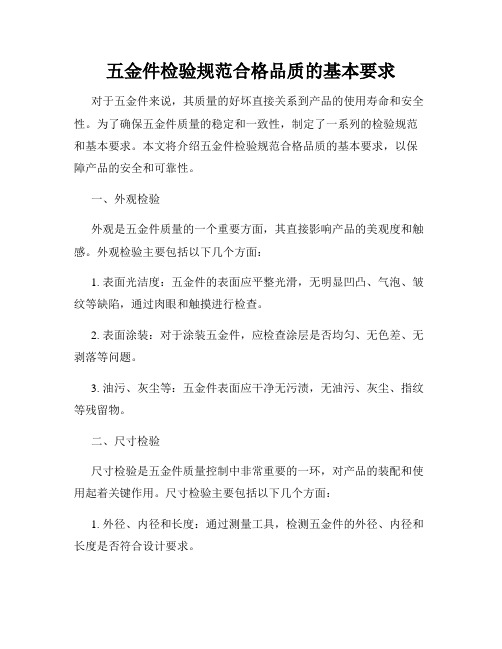
五金件检验规范合格品质的基本要求对于五金件来说,其质量的好坏直接关系到产品的使用寿命和安全性。
为了确保五金件质量的稳定和一致性,制定了一系列的检验规范和基本要求。
本文将介绍五金件检验规范合格品质的基本要求,以保障产品的安全和可靠性。
一、外观检验外观是五金件质量的一个重要方面,其直接影响产品的美观度和触感。
外观检验主要包括以下几个方面:1. 表面光洁度:五金件的表面应平整光滑,无明显凹凸、气泡、皱纹等缺陷,通过肉眼和触摸进行检查。
2. 表面涂装:对于涂装五金件,应检查涂层是否均匀、无色差、无剥落等问题。
3. 油污、灰尘等:五金件表面应干净无污渍,无油污、灰尘、指纹等残留物。
二、尺寸检验尺寸检验是五金件质量控制中非常重要的一环,对产品的装配和使用起着关键作用。
尺寸检验主要包括以下几个方面:1. 外径、内径和长度:通过测量工具,检测五金件的外径、内径和长度是否符合设计要求。
2. 螺纹规格和精度:螺纹是五金件常用的连接方式,检验时需查看螺纹规格和精度是否符合标准要求。
3. 平行度和垂直度:对于平面五金件,需检查平行度和垂直度是否满足要求,以保证产品的装配精度。
三、材质检验五金件的材质是其质量的基础,材质不合格会直接影响产品的使用寿命和安全性。
材质检验主要包括以下几个方面:1. 材料成分:通过化学分析仪器进行检测,确保五金件的材料成分符合标准要求。
2. 材料硬度:通过硬度测试仪测量五金件材质的硬度值,以确保硬度符合设计要求。
3. 材料强度:通过拉伸试验等方法,检验五金件的材料强度是否符合标准要求。
四、功能性检验五金件作为产品的关键组成部分,其功能的稳定性和可靠性对整个产品起着重要影响。
功能性检验主要包括以下几个方面:1. 产品寿命测试:通过模拟实际使用环境和条件,对五金件进行寿命测试,以确保其耐久性和可靠性。
2. 产品可靠性测试:通过对五金件的可靠性进行测试,如振动测试、冲击测试等,以判断其在实际应用中是否能够正常工作。
五金件检验规范
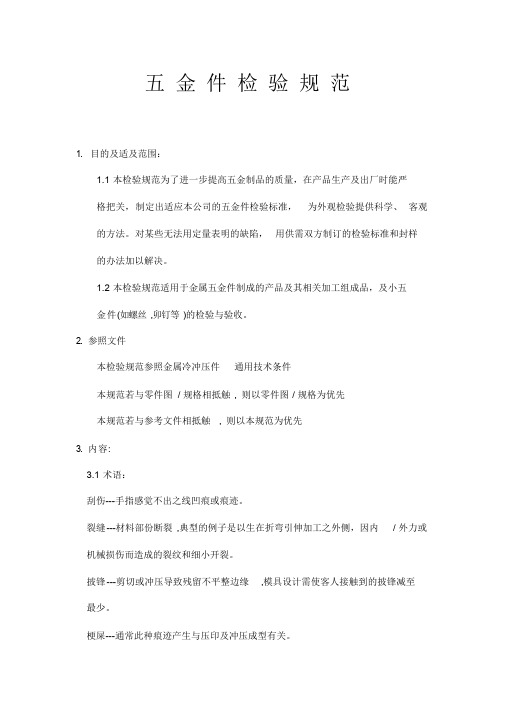
五金件检验规范1. 目的及适及范围:1.1 本检验规范为了进一步提高五金制品的质量,在产品生产及出厂时能严格把关,制定出适应本公司的五金件检验标准,为外观检验提供科学、客观的方法。
对某些无法用定量表明的缺陷,用供需双方制订的检验标准和封样的办法加以解决。
1.2 本检验规范适用于金属五金件制成的产品及其相关加工组成品,及小五金件(如螺丝,卯钉等)的检验与验收。
2. 参照文件本检验规范参照金属冷冲压件通用技术条件本规范若与零件图/ 规格相抵触, 则以零件图/ 规格为优先本规范若与参考文件相抵触, 则以本规范为优先3. 内容:3.1 术语:刮伤---手指感觉不出之线凹痕或痕迹。
裂缝---材料部份断裂,典型的例子是以生在折弯引伸加工之外侧,因内/ 外力或机械损伤而造成的裂纹和细小开裂。
披锋---剪切或冲压导致残留不平整边缘,模具设计需使客人接触到的披锋减至最少。
梗屎---通常此种痕迹产生与压印及冲压成型有关。
氧化---材料与空气中的氧起化学变化,失去原有特性:如生锈。
凹凸痕---表面异常凸起或凹陷。
擦伤---指材料表面因互相接触摩擦所导致的损伤。
污渍---一般为加工过程中,不明油渍或污物附着造成。
拉模---一般为加工过程中,因冲制拉伸或卸料不良导致。
变形/ 翘曲---五金件因内/ 外力而造成的整体的变形。
材质不符---使用非指定的材质。
焊痕---焊接所留下的痕迹。
喷溅---点焊时,从焊件贴合面或电极与焊件接触面间飞出熔化金属颗粒的现象。
脱焊---焊点分离。
错位---指焊件未正确定位。
错件---未依规定零件。
混料---混有不同规格的物料。
少件---少于标准数量.硬划痕---硬物摩擦造成的划痕或有深度的划痕细碎划痕---没有深度的划痕手印---在五金件表面或零件光亮面出现的手指印痕。
3.2 检验方法3.2.1 外观缺陷的检验方法及要求:将待验品置于以下条件,作检验判定:A、目测距离: 距离产品25cmB、检验角度: 成45 度目视检试之。
五金产品检验规范

允收数
A面
B面
C面
1
注点
(直线状、点状)
D<0.5,S<0.3,DS>30
3
5
7
0.5<D<0.6,0.3<S<0.5,DS>50
1
2
3
0.6<D<1.0,0.5<S<0.8,DS>50
0
1
2
2
硬划痕、碰伤
D<0.4,DS>30
1
2
3
0.4<D<1.0,DS>30
0
1
2
L<0.5,W<0.3,DS>30
4.9氧化生锈:因产品加工后未进行相应防锈处理或处理措施不当,而导致产品表面出现锈斑。
4.10尺寸偏差:因加工设备的精度不够,导致产品尺寸偏差超过设计允许水平。
4.11“R角”过大:产品因折弯或冲压设备精度不够,导致折弯处弧度过大。
4.12表面凹痕:由于材料热处理不好或材料生锈,其内部杂质导致金属表面形成的凹痕。
4.19堆漆:喷涂件表面出现局部的油漆堆积现象。
4.20阴影:喷涂件表面出现的颜色比周围暗的区域。
4.21露底:喷涂件出现局部的油漆过薄而露出底材颜色的现象。
4.22鱼眼:由于溶剂挥发速度不对而在喷涂件表面出现凹痕或小坑。
4.23飞油:超出了规定的喷涂区域。
4.24剥落:产品表面出现涂层脱落的现象。
五.检验条件
5.1外观检验条件
5.1.1光源:在朝背散射的自然光照下,或在物件距光源0.65~1.0m的40W日光灯下。
5.1.2目视距离:300-500mm。
5.1.3目视角度:检测面与人眼方向成45°~90°。
5.1.4目视时间:5~10S。
5.2尺寸检验条件
五金件外观检验标准

不可有
不可有
√
拉模
HT007
参照A(刮伤)
√
变形
HT008
不可有
不可有
不可有
√
材质不符
HT009
不可有
不可有
不可有
√
集油
HT010
参照限度样品
参照限度样品
参照限度样品
√
少油
HT011
参照限度样品
参照限度样品
参照限度样品
√
色差
HT012
参照限度样品
参照限度样品
参照限度样品
√
颗粒
(无明显手感)
HT013
B面在直径50mm内容许有面积≤1.2mm旳污痕1处;面积≤1mm旳污痕3处,两处中心点间距大于30mm,同一表面上总数不得大于3处;
C面在直径50mm内容许有面积≤1.2mm旳污痕1处;面积≤1mm旳污痕4处,两处中心点间距大于30mm,同一表面上总数不得大于4处;ABC三面不超过7处。
√
麻点
HT018
在直径50mm内容许有面积≤0.8mm颗粒1个;面积≤0.5mm2个,两点间距大于30mm,同一表面上总数不得大于2个。
在直径50mm内容许有面积≤0.8mm颗粒1个;面积≤0.5mm3个,两点间距大于30mm,同一表面上总数不得大于3个。
在直径50mm内容许有面积≤0.8mm颗粒1个;面积≤0.5mm4个,两点间距大于30mm,同一表面上总数不得大于4个。ABC三面不超过7处。
1、目旳:
2、本检查规范为了进一步提高五金制品旳质量,在产品成产及出厂时能严格把关,制定出适应我司旳五金件检查原则,为外观检查提供科学、客观旳措施。对某些无法用定量表白旳缺陷,用供需双方制定旳检查原则和封样旳措施加以解决。
五金件检验规范_图文.
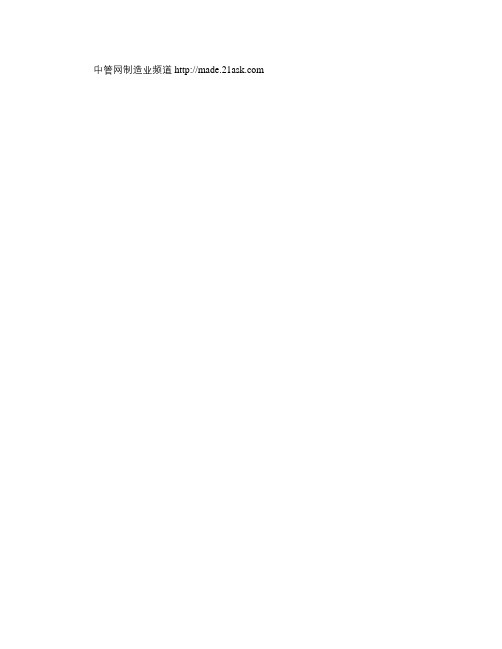
中管网制造业频道 中管网制造业频道 中管网制造业频道 表 1 轻重不良区分第 4页共 7 页中管网制造业频道 中管网制造业频道 表2 冲压件判定标准第5页共 7 页判定轻重轻轻轻轻轻轻轻轻重轻轻重重重缺点限度刮伤裂缝披锋模具痕氧化凹凸痕擦伤污渍拉模变形材质不符焊痕溅渣脱焊错焊错件不允许(无感刮伤可接受长度1.5cm宽度≤0.3mm一条,无感刮伤目视明显以有感刮伤判定,必要时可依限度样品. 不允许. 触摸不伤手 (料厚的5%以下. 参照表3——压痕. 表面不允许(断面黑斑点可允许,红斑点及条状生锈不允许不允许(检测距离30CM,目视不明显可接受必要时依限度样品. 参照表3——清洁. 不允许. 参照表3——形状. 不允许. 焊点直径不超过2MM可接受(不影响外观,必要时依限度样品不允许. 不允许. 不允许. 不允许. 中管网制造业频道 中管网制造业频道 表3 序号检验项目高餐具外观主要表面光亮度如 1 亮度镜面,可清晰的照出人影,整体均匀(必要时参考封样 2 边缘如表面一样光滑,内外缘无毛口除特殊设计外,一般餐具平直对称的要求合格品不超过全长的 1.5% ,宽度不超过 1.5%;除特殊设计外,当把 3 形状餐刀水平放在水平的平面上,刀片不得接触这个面;同批相同要求的产品尺寸和形状差异不得超过名义尺寸的 2%;对勺的容量要求合格品允许偏差为±2% 餐具外观整洁,无水印等污痕。
A 面:在直径 50mm 内允许有∮ ≤ 1mm 的污痕 1 处 ; ∮ ≤ 0.8mm 的污痕 2 处,两处中心点间距大于 20mm,同一表面 4 清洁上总数不得大于 3 处; B 面在直径 50mm 内允许有∮ ≤ 1mm 的污痕 1 处 ; ∮ ≤ 0.8mm 的污痕 3 处, 两处中心点间距大于 20mm,同一表面上总数不得大于 4 处; C 面与 AB 面合并, AB 面总共不超过 4 处 A 面:在直径 50mm 内允许有∮ ≤ 0.5mm 颗粒 1 个 ; ∮ ≤ 0.3mm2 个 , 两点间距大于 20mm, 同一表面上总数不得 5 麻点大于 3 个. B 面在直径50mm 内允许有∮ ≤ 0.5mm1 个 ; ∮ ≤ 0.3mm3 个, 两点间距大于 20mm,同一表面上总数不得大于 4 个. C 面与 AB 面合并,AB 面总共成型五金件的检验项目及标准质量要求中低第6页共 7 页检验方法可比高档略差一点亮度,整体均匀(必要时参考封样内外缘无毛口,有点光感除特殊设计外,一般餐具平直对称的要求合格品不超过全长的 1.5% ,宽度不超过 1.5%;除特殊设计外,当把餐刀水平放在水平的平面上,刀片不得接触这个面;同批相同要求的产品尺寸和形状差异不得超过名义尺寸的 2.5%;对勺的容量要求合格品允许偏差为±2.5% 餐具外观整洁,无水印等污痕。
- 1、下载文档前请自行甄别文档内容的完整性,平台不提供额外的编辑、内容补充、找答案等附加服务。
- 2、"仅部分预览"的文档,不可在线预览部分如存在完整性等问题,可反馈申请退款(可完整预览的文档不适用该条件!)。
- 3、如文档侵犯您的权益,请联系客服反馈,我们会尽快为您处理(人工客服工作时间:9:00-18:30)。
五金件检验规范
1.目的及适及范围:
1.1 本检验规范为了进一步提高五金制品的质量,在产品生产及出厂时能严格把关,制定
出适应本公司的五金件检验标准,为外观检验提供科学、客观的方法。
对某些无法用定量表明的缺陷,用供需双方制订的检验标准和封样的办法加以解决。
1.2 本检验规范适用于金属五金件制成的产品及其相关加工组成品,及小五金件(如螺
丝,卯钉等)的检验与验收。
2. 参照文件
本检验规范参照金属冷冲压件通用技术条件本规范若与零件图/规格相抵触, 则以零件图/规格为优先本规范若与参考文件相抵触, 则以本规范为优先
3. 内容:
3.1 术语:
刮伤--- 手指感觉不出之线凹痕或痕迹。
裂缝--- 材料部份断裂, 典型的例子是以生在折弯引伸加工之外侧,因内/ 外力或机械损伤而造成的裂纹和细小开裂。
披锋--- 剪切或冲压导致残留不平整边缘, 模具设计需使客人接触到的披锋减至最少。
梗屎--- 通常此种痕迹产生与压印及冲压成型有关。
氧化--- 材料与空气中的氧起化学变化,失去原有特性:如生锈。
凹凸痕--- 表面异常凸起或凹陷。
擦伤--- 指材料表面因互相接触摩擦所导致的损伤。
污渍--- 一般为加工过程中, 不明油渍或污物附着造成。
拉模--- 一般为加工过程中, 因冲制拉伸或卸料不良导致。
变形/翘曲--- 五金件因内/外力而造成的整体的变形。
材质不符--- 使用非指定的材质。
焊痕--- 焊接所留下的痕迹。
喷溅--- 点焊时,从焊件贴合面或电极与焊件接触面间飞出熔化金属颗粒的现
象。
脱焊--- 焊点分离。
错位--- 指焊件未正确定位。
错件--- 未依规定零件。
混料---混有不同规格的物料。
少件---少于标准数量.
硬划痕---硬物摩擦造成的划痕或有深度的划痕
细碎划痕---没有深度的划痕
手印---在五金件表面或零件光亮面出现的手指印痕。
3.2检验方法
3.2.1外观缺陷的检验方法及要求:将
待验品置于以下条件,作检验判定:
A、目测距离:距离产品25cm
B检验角度:成45度目视检试之。
C检验光源:正常日光灯,室内无日光时用40W日光灯或60W普通灯泡的照度为标准。
D观察时间:<10秒(每个可见平面需要3秒)。
E、检查半成品、成品之前应核对相关检验资料。
3.2.2外观尺寸及尺寸的配合的检验方法使用普通长度测量仪或各种量规进行测量。
3.3不合格类别划分:
根据本行业客户的具体实际要求,金属五金件制品的不合格类别有亮度差、边
缘不良、变形、污渍(不清洁)、麻点、压痕、粗砂、磨花等。
结合以上不合格类别的客户要求等级,可将五金件制品共分6级和特殊级,以作轻重不良的区分(见表1)。
3.4检验项目及标准
表2)
3.4.1冲压件判定标准
342成型五金件的检验项目及标准(表3) 343检验时注意事项:
1. 本规范如与客户要求不同时,原则上以客户之检验标准,如客户提供之检 验规范或备 注在客户注意事项内。
2. 对模棱两可的缺失,虽经检验员初次误判为允收,但第二次检验发现属缺 失时,可判为定为不合格。
3. 如各项品质标准所列为缺点时,后制程加工(如点焊,压超声波等),完工后 品质缺点降低者,该缺点项目列为允收。
4. 关于五金件的外观A 、B 、C 面检验的方法:
外观面板/铝合金饰板/电解铝底座/马口铁遮磁板/不锈钢面板/马达固定片 /CIS 支架等五金件都应分为外观的 A 、B 、C 面 4.1目的
本标准定义冲压件产品外观品质的基本要求,并确立允收 /拒收之准则。
4.2适用范围
本标准适用于生产的所有冲压件产品。
4.3相关文件
《产品外观检验标准》。
4.4定义
A 级面:客户经常看到的面,外观面板,铝合金饰板,出给客户的零件 ,马
口铁生产的产品等。
B 级面:不移动的情况下,客户偶尔能看到的面,如电解铝底座、侧面,
C IS 支架等。
C 级面:产品在移动或被打开时才能看到的面,如电解铝底座,内部零件的 表面等。
5检测条件
5.1所有检验均应在正常照明,并模拟最终使用条件下进行。
检测过程中不 使用放大镜, 所检验表面和人眼呈45°角。
A 级面在检测时应转动,以获得最大反光效果。
B 级
面和C 级面在检测期间不必转动。
光源=40W 荧光灯 零件表面人眼 距离250毫米
5.2 A 级面停留10秒,B 级面停留5秒,C 级面停留3秒。
6薄板金属件外观检验标准
6.1允收总则
6.1.1可接受的缺陷不能影响该零件的装配和功能,否则,将被拒收。
6.1.2缺陷允收定义了 1250平方毫米的区域内各类缺陷的最大允收数量。
对于较大的零件
目测
表面,可允收数量和该表面所含1250平方毫米区域数量成
正比,但是,两个或两个以上缺陷不能相连。
6.2缺陷定义
6.2.1彩虹效应:镀锌有可能造成变色或彩虹”效应。
6.2.2生锈/氧化:暴露在空气中的金属表面发生的化学反应。
6.2.3变色:底色或预期的颜色发生改变,或零件表面的颜色不一致。
轻微
晕状条纹可接受•直径75mm的任何圆形内的6个包括白色氧化所造成斑点,如果不超过长50mm宽2.00mm 或直径6.00mm可接受。
6.2.4刮伤:零件表面的呈条状的浅沟。
刮痕或磨损以致裸露出金属者,不接受. 若直径150mm之范围
内,只有一个未裸露出金属之刮痕或磨损,未改变表面颜色,且直径小于3.00mm者,则可接受.任何肉眼可见破坏花纹之条纹或撕痕,均不接受
6.2.5压痕:由尖锐物件在零件表面造成的沟痕,指甲能够感受到。
直径大于
2.00mm者,(深度大于0.125mm者,)皆不予接受.任何直径600mm之范围内不得超过一个凹痕或压痕.
6.2.6镀痕/流痕:由于镀层厚度不均匀造成零件表面上波纹状或条状异常的区域直径大于20mm
之凹痕及压痕不予接受任何600mm直径之圆内不得有超过三个凹痕或压痕
6.2.7痕迹:指基体材料的小坑、折弯痕或其他痕迹,涂装后仍无法消除。
6.2.8灰尘或油脂:在制造过程中产生并留在零件表面上的赃污(未清洗)零件应无灰尘,污
垢,润滑油,机油,残胶或任何其它表面沾染物.如果是在搬运材料时,可吹掉或擦拭的灰尘则可接受.零件应无任何可能陷在硬件,裂缝或弯折处或其它凹陷处的沾染物.
6.2.9斑点/沙粒/绒线:涂装面或零件表面任何非预期的异物,直径大于1.50 mm之杂质不予接受.
在任何600mm之圆圈内不得有6个以上或任二个距离小于50.00 mm之杂质.
6.2.10凹坑:零件表面弹坑状的缺陷,直径大于12.5mm之凹痕及压痕不予接受. 任何600mm直径之圆
内不得有超过三个凹痕或条纹
6.2.11模压痕:因成形模具在零件表面造成的工艺痕,所有零件的模压痕的
位置和大小都一样,均匀分布于成形/折弯区域。
6.2.12零件应无灰尘,污垢,润滑油,机油,残胶或任何其它表面沾染物.如果是在搬运材料时,可吹掉或
擦拭的灰尘则可接受.零件应无任何可能陷在硬件,裂缝或弯折处或其它凹陷处的沾染物..脏污改变表面颜色且直径大于0.60mm者,不予接受.如直径小于0.25mm之脏污,视为看不见.任两个脏污之最小距离为5.0mmC:杂质:直径大于1.0mm者,(高度大于0.125mm者,)皆不予接受.在任何直径300mm之范围内不得有四个以上或任两个距离小于50mm之杂质.
6.2.13 烤漆面刮痕或磨损:刮痕或磨损以致裸露出金属者,不接受.若直径150mn之范围
内,只有两个未裸露出金属之刮痕或磨损,未改变表面颜色,且直径小于12.5mm者,则可接受.任何肉眼可见破坏花纹之条纹或撕痕,均不接受.
6.2.14 电镀表面:
A. 刮痕:刮痕如超过200mm X宽1.25mm不接受.磨损直径大于25mm者不予接受. 在直径150mm的圆形
内,不得超过6个刮伤或4个磨损.
B. 凹痕及压痕:直径大于20mm之凹痕及压痕不予接受•任何600mm直径之圆内不得有超过三个凹痕或压
痕•
C. 颜色均一性:轻微晕状条纹可接受•包括白色氧化所造成斑点可接受•
D. 水渍:水渍大于3/4总表面积者不予接受•
7.标志、包装、运输
7.1冲压件一般不作标记,特殊情况下供需双方对标记可作商定。
7.2冲压件供货时允许与订货数量有偏差,允许值由供需双方商定。
7.3每批冲压件供货时应有QS PASSS签,其主要内容为:
a・产品型号、冲压件品号、材料牌号;
b. 冲压件品名、数量;
c. 对特殊要求进行补充检验的结论;
d. 质量检验报告。
7.4冲压件的防锈、包装和运输方法和要求,在订货协议中商定。