FANUC 0数控机床
(FANUC 0i-mate-TC)数控车床主轴驱动系统的装调

2.
三菱E700变频器参数设置
(1)、三菱E700变频器操作要领
将所有参数 恢复至出厂 值
变更参数设定值
Pr.160 用户参数组读取选择= “1”,用户参数组中未登录 Pr.79 。Pr.77= “1”,禁止写入参数。
需要设置的参数
四、任务检查
(1) 操作数控系统FANUC 0i-mate-TC ,运行模式为“手动”运行模 式,摁下“主轴正转”键,则主轴电机正向旋转。摁下“主轴倍率”增 加键(减少键),主轴转速增大(减小); (2)操作数控系统FANUC 0i-mate-TC ,运行模式为“手动”运行模 式,摁下“主轴反转”键,则主轴电机反向旋转。摁下“主轴倍率”增 加键(减少键),主轴转速增大(减小); ; (3) 操作数控系统FANUC 0i-mate-TC ,运行模式为“手动”运行模式 ,摁下“主轴停”键,则主轴电机停止旋转; (4) 操作数控系统FANUC 0i-mate-TC ,运行模式为“MDI”运行模式, 输入“M03S800”,或者“M04S800”或者“M05”主轴能正确动作。
编码器用在主轴系统上: (1)测主轴转速显示在NC屏幕上; (2)车削螺纹时,不至于乱牙;
(二)MITSUBISHI E700 系列变频器
主轴伺服驱动装置
主轴电机
1. 变频器连接图
变频器
三相异步电机
端 子 、任务实施
(一)电气线路测绘
每一组随机抽检2份PPT课件,并通过PPT汇报展示电气测绘的成 果,教师现场打分。
60 f 1 n 1 s n0 1 s p 1 变频调速 (无级调速)
f=50Hz +
整流器 逆变器
三种电气 调速方法
f1、U1可调 M
FANUC 0 系统部分参数功能说明
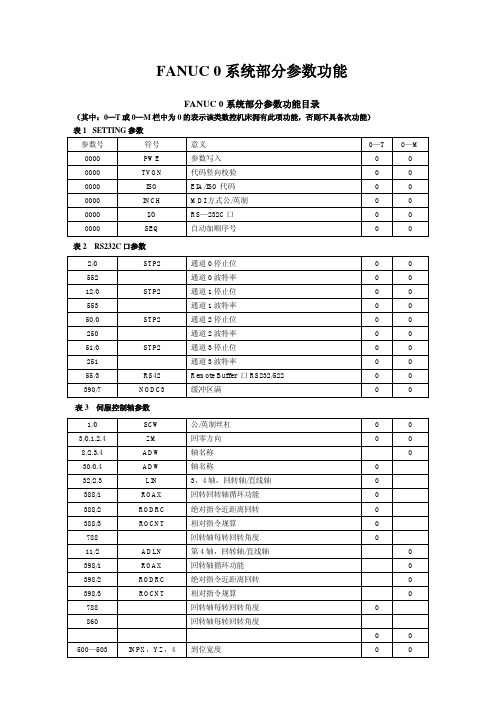
4 ORC
3 TOC
2 DCS
1 PROD
0 DCS
0:不进行自动漂移补偿。
RDRN 1:快移时空运转有效。
0:快移时空运转无效。
DECI 1:返回参考点时,减速信号为“1”时开始减速。
0:返回参考点时,减速信号为“0”时开始减速。
ORC 1:偏置量用直径表示。
0:偏置量用半径表示。
IOF 1:偏置量绝对值输入。
0:偏置量增量值输入。
TOC 1:偏置可补复置键取消。
0:偏置不补复置键取消。
DCS 1:按 MDI 面板上的 START 键可直接启动 CNC 而不必经过机床侧(仅 MDI 状态)。
0:按 MDI 面板上的 START 键向机床侧发信号,当机床侧启动信号返回时,CNC 才启动。
PROD 1:坐标值显示的是编程的位置。
HRPC
用位置编码器 用高分辩率编码器 定向方法(编码器/磁传感器) 内装传感器 位置编码器信号 高分辩率编码器
JGNPMC DPCRAM
用 PMC 显示 PMC 操作菜单 图形显示的绘图坐标系
0
0
0
0
0
0
0
0
0
0
0
0
0
0
0
0
0
参数功能
0001 7 ADFT
6 RDRN
5 DECI
ADFT 1:进行自动漂移补偿。
0:坐标值显示的是加上偏置值的实际位置。
SCW 1:最小指令值为英制(机床为英制) 0:最小指令值为米制(机床为米制)
0002
7
6
5
4
3
2
1
0
NFED TFHD HSLE
FANUC 0i系统数控加工中心机床面板介绍
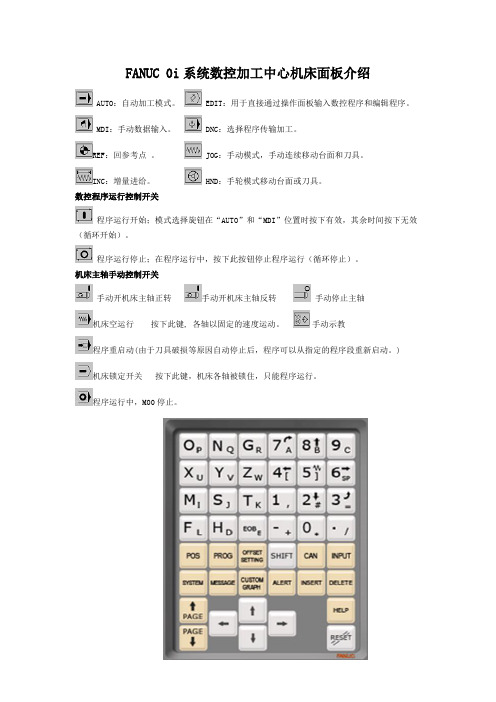
FANUC 0i 系统数控加工中心机床面板介绍AUTO :自动加工模式。
EDIT :用于直接通过操作面板输入数控程序和编辑程序。
MDI :手动数据输入。
DNC :选择程序传输加工。
REF :回参考点 。
JOG :手动模式,手动连续移动台面和刀具。
INC :增量进给。
HND :手轮模式移动台面或刀具。
数控程序运行控制开关程序运行开始;模式选择旋钮在“AUTO ”和“MDI ”位置时按下有效,其余时间按下无效(循环开始)。
程序运行停止;在程序运行中,按下此按钮停止程序运行(循环停止)。
机床主轴手动控制开关手动开机床主轴正转 手动开机床主轴反转 手动停止主轴机床空运行 按下此键, 各轴以固定的速度运动。
手动示教程序重启动(由于刀具破损等原因自动停止后,程序可以从指定的程序段重新启动。
)机床锁定开关 按下此键,机床各轴被锁住,只能程序运行。
程序运行中,M00停止。
编辑键替换键用输入的数据替换光标所在的数据。
紧急停止旋钮删除键删除光标所在的数据;或者删除一个程序或者删除全部程序。
插入键把输入区之中的数据插入到当前光标之后的位置。
取消键消除输入区内的数据。
回车换行键结束一行程序的输入并且换行。
上档键页面切换键程序显示与编辑页面。
位置显示页面。
位置显示有三种方式,用PAGE按钮选择。
参数输入页面。
按第一次进入坐标系设置页面,按第二次进入刀具补偿参数页面。
进入不同的页面以后,用PAGE 按钮切换。
系统参数页面信息页面,如“报警”图形参数设置页面系统帮助页面复位键翻页按钮(PAGE)向上翻页。
向下翻页。
光标移动(CURSOR)向上移动光标。
向左移动光标。
向下移动光标。
向右移动光标。
输入键输入键把输入区内的数据输入参数页面。
FANUC0M系统数控机床参数丢失的处理

FANUC0M系统数控机床参数丢失的处理FANUC0M系统数控机床参数丢失是一种常见的问题,通常会出现在电
源故障、断电或者误删除参数等情况下。
当参数丢失时,会导致数控机床
无法正常工作,因此需要及时处理。
下面将对FANUC0M系统数控机床参数
丢失的处理方法进行详细介绍。
然后,将参数文件转换为FANUC 0M系统可以识别的格式。
通常,参
数文件会以扩展名“.PAR”或“.LAD”保存。
如果没有相应的文件转换软件,可以尝试使用FANUC提供的Paramater Loader进行转换。
参数转换
完成后,将转换后的文件保存在USB存储设备(如U盘)上。
接下来,将USB存储设备插入到数控机床的USB接口上。
然后,在数控机床的控制面板上找到“EDIT”按钮,按下并保持数秒,然后松开。
此时会显示“PARAMETER”字样。
在弹出的对话框中,选择需要加载的参数文件,并按下“EXEC”按钮
开始加载。
等待加载完成后,数控机床会自动重启,并且参数恢复。
此时,数控
机床应该可以正常工作了。
2.手动输入参数:
首先,需要获得数控机床的参数列表,该列表记录了所有参数及其对
应的值。
可以从机床的使用手册或者FANUC官方网站上找到相应的参数列表。
一般来说,数控机床的参数较多,手动输入需要耐心和耐力。
在输入
参数时,应该仔细核对每个参数的值,以确保准确性。
在所有参数输入完成后,重新启动数控机床。
此时,机床应该可以正常工作了。
fanuc 0i数控车床操作面板

fanuc 0i数控车床操作面板实现数控机床回零(或回参考点)操作一、开机、数控仿真系统进入鼠标左键点击“开始”按钮,在“程序”名目中弹出“数控加工仿真系统”的子名目,在接着弹出的再下级子名目中点击“加密锁治理程序”,如图1-1所示。
图1-1 进入数控加工仿真系统界面加密锁程序启动后,屏幕右下方工具栏中显现的图标,表示加密锁治理程序启动成功。
现在重复上面的步骤,在最后弹出的名目中点击“数控加工仿真系统”,系统弹出“用户登录”界面,如图1-2所示。
图1-2 用户登录界面进入数控加工仿真系统有以下两种方法:点击“快速登录”按钮,直截了当进入。
输入用户名和密码,再点击“登录”按钮后。
二、数控机床(车床或铣床)与系统的选择(FANUC0i)1.选择机床类型打开菜单“机床/选择机床…”,在选择机床对话框中选择操纵系统类型和相应的机床并按确定按钮,现在界面如图1-3所示。
图1-3 选择机床三、数控机床操作面版要紧内容的熟悉为了更好地了解数控车床操作面板上各个按键的功用。
把握数控车床的调整,做好加工前的预备工作,第一需要熟悉面板操作。
1.FANUC 0I MDI键盘操作讲明图1-4 FANUC 0I MDI键盘1)MDI键盘讲明图1-4所示为FANUC0I系统的MDI键盘(右半部分)和CRT界面(左半部分)。
MDI键盘用于程序编辑、参数输入等功能。
MDI键盘上各个键的功能列于表1-1。
表1-1 MDI键盘讲明MDI软键功能软键实现左侧CRT中显示内容的向上翻页;软键实现左侧CRT显示内容的向下翻页。
移动CRT中的光标位置。
软键实现光标的向上移动;软键实现光标的向下移动;软键实现光标的向左移动;软键实现光标的向右移动。
实现字符的输入,点击键后再点击字符键,将输入右下角的字符。
例如:点击将在CRT的光标所处位置输入“O”字符,点击软键后再点击将在光标所处位置处输入P字符;软键中的“EOB”将输入“;”号表示换行终止。
FANUC_0i__数控操作系统数控车削编程指导书 (1)

意义
坐标轴地址指令 附加轴地址指令 附加回转轴地址指令 圆弧起点相对于圆弧中心的坐标指令
G代码A. G00 G01 G02 G03 G04 G10 G11 G20 G21 G27 G28 G32 G34 G36 G37 G40 G41 G42 G50 G52 G53 G54~G59
00
07
刀尖半径左补偿 刀尖半径右补偿 坐标系设定或主轴最大速度设定
01
螺纹车削循环 端面车削循环
00
局部坐标系设定 机床坐标系设定
02
恒表面切削速度控制 恒表面切削速度控制取消 每分钟进给 每转进给
14
选择工件坐标系1~6
05
参考点编程原点
机床原点 机床原点又称机械原点,它是机床坐标系的原点。该点是机床上的 一个固定的点,是机床制造商设置在机床上的一个物理位置,通常用户 不允许改变。机床原点是工件坐标系、机床参考点的基准点。车床的机 床原点为主轴旋转中心与卡盘后端面之交点 。 机床参考点
车床的工件原点
数控车床编程中的坐标 系
机床坐标系 工件坐标系(编程坐标系)
数控车床使用X轴和Z轴组成直角坐标系,X轴与机床主轴垂直,Z轴与 主轴轴线方向平行,车刀接近工件方向为负方向,离开工件方向为正方向。 根据刀坐和机床主轴位置关系划分,数控车床有前置刀座和后置刀座 之分,相同的编程指令在前刀坐和后刀坐中的运动轨迹是不一样的
停刀点
起刀点
常用MSTF指令
指令 功能 指令 功能 示例 G98模式:F100(每分进给) G99模式:F0.05(每转进给) 使用01号刀和01号刀 表示不使用刀具补偿
M03 M04
M05
主轴正转 主轴反转
FANUC--0系统操作编程说明书

FANUC--0系统操作编程说明书第一篇:编程1.综述1.1可编程功能通过编程并运行这些程序而使数控机床能够实现的功能我们称之为可编程功能。
一般可编程功能分为两类:一类用来实现刀具轨迹控制即各进给轴的运动,如直线/圆弧插补、进给控制、坐标系原点偏置及变换、尺寸单位设定、刀具偏置及补偿等,这一类功能被称为准备功能,以字母G以及两位数字组成,也被称为G代码。
另一类功能被称为辅助功能,用来完成程序的执行控制、主轴控制、刀具控制、辅助设备控制等功能。
在这些辅助功能中,Tx x用于选刀,Sx x x x用于控制主轴转速。
其它功能由以字母M与两位数字组成的M代码来实现。
1.2准备功能本机床使用的所有准备功能见表1.1:表1.1 G代码分组功能*G0001定位(快速移动)*G0101直线插补(进给速度)G0201顺时针圆弧插补G0301逆时针圆弧插补G0400暂停,精确停止G0900精确停止*G1702选择X Y平面G1802选择Z X平面G1902选择Y Z平面G2700返回并检查参考点G2800返回参考点G2900从参考点返回G3000返回第二参考点*G4007取消刀具半径补偿G4107左侧刀具半径补偿G4207右侧刀具半径补偿G4308刀具长度补偿+G4408刀具长度补偿-*G4908取消刀具长度补偿G5200设置局部坐标系G5300选择机床坐标系*G5414选用1号工件坐标系G5514选用2号工件坐标系G5614选用3号工件坐标系G5714选用4号工件坐标系G5814选用5号工件坐标系G5914选用6号工件坐标系G6000单一方向定位G6115精确停止方式*G6415切削方式G6500宏程序调用G6612模态宏程序调用*G6712模态宏程序调用取消G7309深孔钻削固定循环G7409反螺纹攻丝固定循环G7609精镗固定循环*G8009取消固定循环G8109钻削固定循环G8209钻削固定循环G8309深孔钻削固定循环G8409攻丝固定循环G8509镗削固定循环G8609镗削固定循环G8709反镗固定循环G8809镗削固定循环G8909镗削固定循环*G9003绝对值指令方式*G9103增量值指令方式G9200工件零点设定*G9810固定循环返回初始点G9910固定循环返回R点从表1.1中我们可以看到,G代码被分为了不同的组,这是由于大多数的G代码是模态的,所谓模态G代码,是指这些G代码不只在当前的程序段中起作用,而且在以后的程序段中一直起作用,直到程序中出现另一个同组的G代码为止,同组的模态G代码控制同一个目标但起不同的作用,它们之间是不相容的。
数控机床FANUC-Oi系统
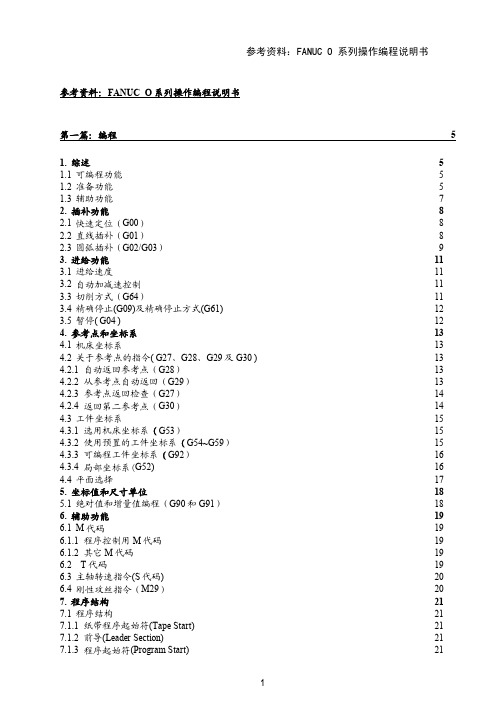
参考资料:FANUC O系列操作编程说明书第一篇:编程5 1.综述5 1.1可编程功能5 1.2准备功能51.3辅助功能72.插补功能8 2.1快速定位(G00)8 2.2直线插补(G01)82.3圆弧插补(G02/G03)93.进给功能11 3.1进给速度11 3.2自动加减速控制11 3.3切削方式(G64)11 3.4精确停止(G09)及精确停止方式(G61) 123.5暂停(G04) 124.参考点和坐标系13 4.1机床坐标系13 4.2关于参考点的指令(G27、G28、G29及G30) 13 4.2.1 自动返回参考点(G28)13 4.2.2 从参考点自动返回(G29)13 4.2.3 参考点返回检查(G27)14 4.2.4 返回第二参考点(G30)14 4.3工件坐标系15 4.3.1 选用机床坐标系(G53)15 4.3.2 使用预置的工件坐标系(G54~G59)15 4.3.3 可编程工件坐标系(G92)16 4.3.4 局部坐标系(G52) 164.4平面选择175.坐标值和尺寸单位185.1绝对值和增量值编程(G90和G91)186.辅助功能19 6.1M代码19 6.1.1 程序控制用M代码19 6.1.2 其它M代码19 6.2T代码19 6.3主轴转速指令(S代码) 206.4刚性攻丝指令(M29)207.程序结构21 7.1程序结构21 7.1.1 纸带程序起始符(Tape Start) 21 7.1.2 前导(Leader Section) 21 7.1.3 程序起始符(Program Start) 217.1.4 程序正文(Program Section) 21 7.1.5 注释(Comment Section) 21 7.1.6 程序结束符(Program End) 21 7.1.7 纸带程序结束符(Tape End) 22 7.2程序正文结构22 7.2.1 地址和词22 7.2.2 程序段结构227.2.3 主程序和子程序238.简化编程功能25 8.1孔加工固定循环(G73,G74,G76,G80~G89) 25 8.1.1 G73(高速深孔钻削循环)28 8.1.2 G74(左螺纹攻丝循环)29 8.1.3 G76(精镗循环) 29 8.1.4 G80(取消固定循环) 30 8.1.5 G81(钻削循环) 30 8.1.6 G82(钻削循环,粗镗削循环) 31 8.1.7 G83(深孔钻削循环) 31 8.1.8 G84(攻丝循环) 32 8.1.9 G85(镗削循环) 32 8.1.10 G86(镗削循环) 32 8.1.11 G87(反镗削循环) 33 8.1.12 G88(镗削循环) 33 8.1.13 G89(镗削循环) 34 8.1.14 刚性攻丝方式348.1.15 使用孔加工固定循环的注意事项359.刀具补偿功能36 9.1刀具长度补偿(G43,G44,G49) 36 9.2刀具半径补偿36 9.2.1 补偿向量36 9.2.2 补偿值36 9.2.3 平面选择36 9.2.4 G40、G41和G4236 9.2.5 使用刀具半径补偿的注意事项37第二篇:NC操作381.自动执行程序的操作38 1.1CRT/MDI操作面板38 1.1.1 软件键38 1.1.2 系统操作键38 1.1.3 数据输入键38 1.1.4 光标移动键38 1.1.5 编辑键和输入键38 1.1.6 NC功能键38 1.1.6 电源开关按钮39 1.2MDI方式下执行可编程指令39 1.3自动运行方式下执行加工程序39 1.3.1 启动运行程序391.3.2 停止运行程序392.程序验证和安全功能40 2.1程序验证功能40 2.1.1 机床闭锁402.1.2 Z轴闭锁40 2.1.3 自动进给的倍率40 2.1.4 快速进给的倍率40 2.1.5 试运行40 2.1.6 单程序段运行402.2安全功能402.2.1 紧急停止402.2.2 超程检查403.零件程序的输入、编辑和存储41 3.1新程序的注册41 3.2搜索并调出程序41 3.3插入一段程序41 3.4删除一段程序41 3.5修改一个词423.6搜索一个词424.数据的显示和设定43 4.1刀具偏置值的显示和输入43 4.2G54~G59工件坐标系的显示和输入43 4.3NC参数的显示和设定434.4刀具表的修改445.显示功能45 5.1程序显示455.2当前位置显示456.在线加工功能46 6.1有关参数的修改:466.2有关在线加工的操作. 467.机床参数的输入﹑输出478.用户宏B功能49 8.1变量49 8.1.1变量概述498.1.2系统变量508.2算术和逻辑操作55 8.3分支和循环语句56 8.3.1无条件分支(GOTO语句)56 8.3.2条件分支(IF语句)57 8.3.3循环(WHILE语句)57 8.3.4注意58 8.4宏调用58 8.4.1简单调用(G65)58 8.4.2、模调用(G66、G67)60 8.4.3G码调用宏61 8.4.4、M码调用宏618.4.5M码调用子程序62 8.4.6T码调用子程序62 8.5附加说明62附录1:报警代码表641.程序报警(P/S报警) 642.伺服报警653.超程报警664.过热报警及系统报警66第一篇:编程1. 综述1.1 可编程功能通过编程并运行这些程序而使数控机床能够实现的功能我们称之为可编程功能。
FANUC0I数控加工仿真操作步骤

FANUC0I数控加工仿真操作步骤1.确定工件和夹具:在进行数控加工仿真之前,首先需要确定要加工的工件和夹具。
工件是指需要进行加工的产品,夹具是用于夹持工件并保持其位置的装置。
2.创建数控程序:使用数控编程软件,根据工件的设计要求,编写数控程序。
数控程序是一系列指令,用于控制数控机床的运动轨迹和操作参数。
3.导入数控程序:将编写好的数控程序导入到数控仿真软件中。
数控仿真软件可以模拟数控机床的运动,并显示加工过程中的各种信息,如刀具路径、加工深度等。
4.设置刀具:根据工件的设计要求,选择合适的刀具,并进行设置。
刀具的选择决定了加工过程中的切削速度、进给速度等参数。
5.设置工艺参数:根据工件的材料和加工要求,设置相应的工艺参数。
工艺参数包括切削速度、进给速度、切削深度等。
6.进行仿真:通过数控仿真软件,开始进行数控加工仿真。
在仿真过程中,可以观察刀具的运动轨迹,检测加工过程中的错误和问题。
7.优化加工过程:根据仿真结果,对加工过程进行优化。
可以根据仿真结果调整切削速度、进给速度等参数,以提高加工效率和质量。
8.生成加工报告:完成数控加工仿真后,生成加工报告。
加工报告记录了加工过程中的各种信息,如切削速度、进给速度、加工时间等,以供后续参考和分析。
9.调整数控程序:根据仿真结果和加工报告,对数控程序进行调整。
可以通过调整数控程序中的运动轨迹和操作参数,进一步优化加工过程。
10.导出数控程序:完成数控程序的调整后,将最终的数控程序导出到实际的数控机床中进行加工。
总结:FANUC0i数控加工仿真操作步骤包括确定工件和夹具、创建数控程序、导入数控程序、设置刀具和工艺参数、进行仿真、优化加工过程、生成加工报告、调整数控程序和导出数控程序。
这些步骤可以帮助操作人员在加工之前进行全面的模拟和优化,以提高加工效率和质量。
Fanuc 0i 系统数控机床参数设置小经验三则
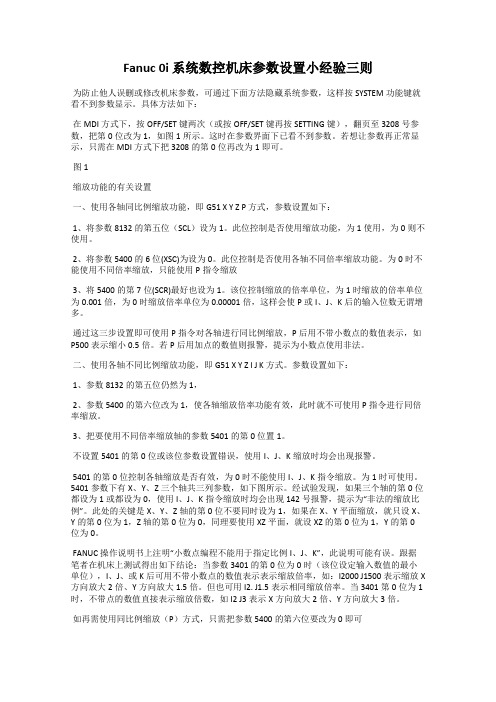
Fanuc 0i 系统数控机床参数设置小经验三则为防止他人误删或修改机床参数,可通过下面方法隐藏系统参数,这样按SYSTEM功能键就看不到参数显示。
具体方法如下:在MDI方式下,按OFF/SET键两次(或按OFF/SET键再按SETTING键),翻页至3208号参数,把第0位改为1,如图1所示。
这时在参数界面下已看不到参数。
若想让参数再正常显示,只需在MDI方式下把3208的第0位再改为1即可。
图1缩放功能的有关设置一、使用各轴同比例缩放功能,即G51 X Y Z P 方式,参数设置如下:1、将参数8132的第五位(SCL)设为1。
此位控制是否使用缩放功能,为1使用,为0则不使用。
2、将参数5400的6位(XSC)为设为0。
此位控制是否使用各轴不同倍率缩放功能。
为0时不能使用不同倍率缩放,只能使用P指令缩放3、将5400的第7位(SCR)最好也设为1。
该位控制缩放的倍率单位,为1时缩放的倍率单位为0.001倍,为0时缩放倍率单位为0.00001倍,这样会使P或I、J、K后的输入位数无谓增多。
通过这三步设置即可使用P指令对各轴进行同比例缩放,P后用不带小数点的数值表示,如P500表示缩小0.5倍。
若P后用加点的数值则报警,提示为小数点使用非法。
二、使用各轴不同比例缩放功能,即G51 X Y Z I J K 方式。
参数设置如下:1、参数8132的第五位仍然为1,2、参数5400的第六位改为1,使各轴缩放倍率功能有效,此时就不可使用P指令进行同倍率缩放。
3、把要使用不同倍率缩放轴的参数5401的第0位置1。
不设置5401的第0位或该位参数设置错误,使用I、J、K缩放时均会出现报警。
5401的第0位控制各轴缩放是否有效,为0时不能使用I、J、K指令缩放。
为1时可使用。
5401参数下有X、Y、Z三个轴共三列参数,如下图所示。
经试验发现,如果三个轴的第0位都设为1或都设为0,使用I、J、K指令缩放时均会出现142号报警,提示为“非法的缩放比例”。
FANUC0系列参数说明

FANUC0系列参数说明
1.PWE:该参数用于设置写入操作时的抑制功能。
当PWE=0时,写入操作会被抑制。
当PWE=1时,写入操作将被执行。
2.PRM:该参数用于设置程序号使用的起始值。
3.GPS:该参数用于设置工件坐标原点和零点的坐标值。
4.MCR:该参数用于设置程序操作时的计加器操作权限。
5.FBL:该参数用于设置回零操作的方式。
当FBL=0时,使用绝对方式回零操作。
当FBL=1时,使用增量方式回零操作。
6.DWE:该参数用于设置从读出程序末尾到回零操作的延迟时间。
7.DRC:该参数用于设置终止程序执行时的停顿时间。
8.TMM:该参数用于设置在MDI模式下,轴移动命令的最大速度。
9.LVX:该参数用于设置程序操作时的数值操作权限。
10.FAD:该参数用于设置快速移动速度的倍率。
11.SIM:该参数用于控制回零操作时是否进行轴的模拟操作。
12.DST:该参数用于设置刀具补偿功能是否可用。
13.HAP:该参数用于设置坐标系交换功能的使用方式。
14.BRK:该参数用于设置追踪控制功能是否可用。
15.TLT:该参数用于设置倾斜轴的角度。
以上是FANUC0系列中的一些常见参数的说明。
这些参数可以根据具体的机床要求进行设置和调整,以实现更精确和稳定的数控加工操作。
发那科0iC数控系统参数

系统全清的根本操作
同时按下[RESET]+[DELETE]按键, 并且给系统上电。直到系统上电启动完 成后松开两个按键,系统SRAM存储器全 清〔参数/偏置量和程序〕完成,全清 后一般会出现报警,见以下图所示。
复位键
删除键
存储器去除操作
存储器全清〔上电同时按下RESET+DEL〕 全清后一般会出现报警 100 〔允许写入参数提示〕 506/507 〔正、负向硬超程报警〕 417 〔伺服参数设定不正确〕 750 〔串行主轴参数设定不正确〕 手动输入系统功能参数 根据FANUC公司提供的出厂参数表正确输入参
标准设定:150
轴设定〔加/减速〕
PRM1622 切削进给插补后的指数加/减速时间 常数或铃型加/减速时间常数或直线型加/减速 时间常数 标准设定:50
PRM1624 JOG进给时,插补后的指数加/减速 时间常数或铃型加/减速时间常数或直线型加/ 减速时间常数 标准设定:50
轴设定〔加/减速〕
PRM1625 各轴JOG进给的指数函数型加/减速 时的FL速度 标准设定:10
电机代码 PRM2021 根据实际电机参阅资料进展设定电机ID号。 初始化设定时根据此数据进展初始值的计算设 定。
a i F 伺服电机代码
b i S 伺服电机代码
伺服设定
AMR PRM2001 00000000:必须设定为全0。
指令倍乘比 PRM1820 CMR为1/2-1/27时,设定值=1/CMR+100。 CMR为0.5-48时,设定值=2×CMR。
设定参数PRM3190#6=1,设定完成后 会出现000号请关闭电源报警,重新上 电启动,系统启动显示简体中文。
PRM3102#3 繁体汉语 PRM3190#6 简体中文
FANUC 0i系统数控车床概述
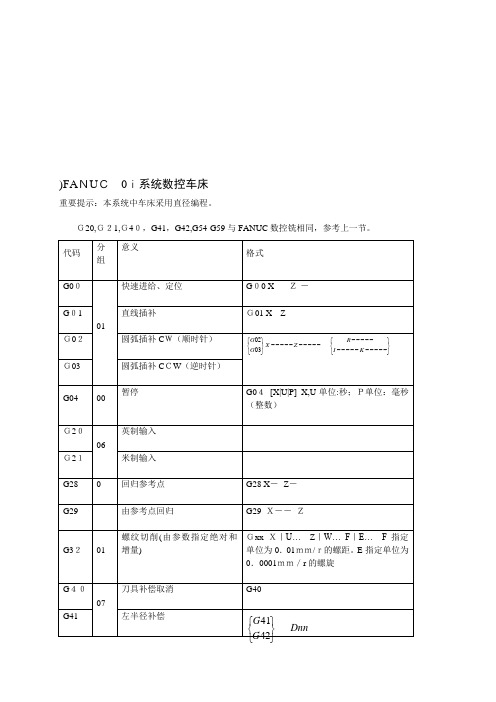
00
精加工循环
G70PnsQnf
G71
外园粗车循环
G71 UΔdRe
G71 PnsQnfUΔu WΔwFf
G72
端面粗切削循环
G72W(Δd) R(e)
G72P(ns) Q(nf)U(Δu) W(Δw) F(f) S(s) T(t)
Δd:切深量
e:退刀量
ns:精加工形状的程序段组的第一个程序段的顺序号
10观察程序轨迹(可参见章节x.6.3“检查运行轨迹”。其中红线代表刀具快速移动的轨迹,绿线代表刀具切削的轨迹)
11自动加工(参见x.6“自动加工方式”)
12使用MDI方式(参见x.7“MDI模式”)
13如何在输入区面板上输入编辑程序(参见x.5.3“编辑程序”)
x:根据不同的机床面板和控制系统,x的值为3-13。
Δi:X方向的移动量
Δk:Z方向的切深量
Δd:孔底的退刀量
f:进给速度
G75
内径/外径切断循环
G75 R(e)
G75X(U)_Z(W)_P(Δi)Q(Δk)R(Δd)F(f)
G76
复合形螺纹切削循环
G76P(m)(r)(a)Q(Δdmin) R(d)
G76X(u)_Z(W)_R(i) P(k)Q(Δd)F(l)
m:最终精加工重复次数为1—99
r:螺纹的精加工量(倒角量)
a:刀尖的角度(螺牙的角度)可选择80,60,55,30,29,0六个种类
m,r,a;同用地址P一次指定
Δdmin:最小切深度
i:螺纹部分的半径差
k:螺牙的高度
Δd:第一次的切深量
l:螺纹导程
G90
01
直线车削循环加工
G90X(U)--- Z(W)-来自-F---nf:精加工形状的程序段组的最后程序段的顺序号
FANUC-0iT系统数控车床操作
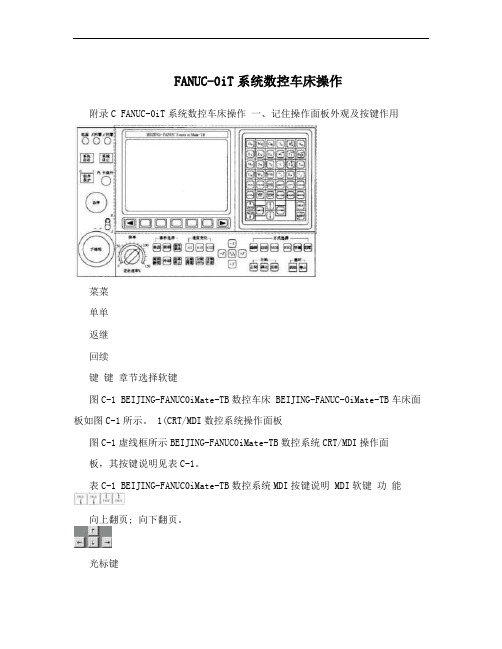
FANUC-0iT系统数控车床操作附录C FANUC-0iT系统数控车床操作一、记住操作面板外观及按键作用菜菜单单返继回续键键章节选择软键图C-1 BEIJING-FANUC0iMate-TB数控车床 BEIJING-FANUC-0iMate-TB车床面板如图C-1所示。
1(CRT/MDI数控系统操作面板图C-1虚线框所示BEIJING-FANUC0iMate-TB数控系统CRT/MDI操作面板,其按键说明见表C-1。
表C-1 BEIJING-FANUC0iMate-TB数控系统MDI按键说明 MDI软键功能向上翻页; 向下翻页。
光标键地址字符键。
点击键后再点击字符键,将输入右下角的字符;用“EOB”输入“;”,表示程序段结束等。
数字字符键。
点击键后再点击字符键,将输入右下角的字符。
465显示坐标值进入程序编辑和显示画面设定、显示刀具补偿值和其他数据。
系统参数的设定及显示显示各种信息用户宏画面或图形的显示字符下档切换键删除CRT最下输入行显示的最后一个字符将CRT最下输入行显示出来的数据移入到寄存器光标所在编辑单位的替换在光标后插入编辑单位删除光标所在编辑单位显示如何操作机床,可在CNC发生报警时提供报警的详细信息。
CNC复位,解除报警;当自动运行时,按此键所有运动都停止。
2(数控车床遥控操作面板图C-1除虚线框所示面板是BEIJING-FANUC0iMate-TB系统CKA6150数控车床遥控操作面板,其按键说明见表C-2。
表C-2 按键说明按钮名称功能说明数控系统电源开关启动数控系统数控系统电源开关关闭数控系统466启动:自动运行开始,系统处于“自动运行”或“MDI”位置时有效,其循环启动/停止余方式下无效。
停止:自动运行停止,进给保持。
超程解锁机床超程释放,与点动键同时按。
在手动方式下,按下此钮,系统进入快速按钮手动快速移动状态。
手动进给按钮手动进给点动。
有级调整进给速度,实际进给速度=进给倍率开关编程进给速度(F值)×倍率百分比摇手轮时:表示手轮移动倍率选钮,×1、×10、×100分别代表手轮转过一个刻度时机床的移动量为0.001mm、手轮倍率、 0.01mm、0.1mm;坐标轴增量值按键按坐标轴键时:表示增量进给,×1、×10、×100分别代表按一下坐标轴键机床的移动量为0.001mm、0.01mm、0.1mm。
fanuc 数控车 0号INI参数定义

fanuc 数控车0号INI参数定义FANUC系统有很丰富的机床参数,为数控机床的安装调试及日常维护带来了方便条件。
根据多年的实践,对常用的机床参数在维修中的应用做一个介绍。
1、手摇脉冲发生器损坏。
一台FANUC 0TD数控车床,手摇脉冲发生器出现故障,使对刀不能进行微调,需要更换或修理故障件。
当时没有合适的备件,可以先将参数900#3置“0”,暂时将手摇脉冲发生器不用,改为用电动按钮单脉冲发生器操作来进行刀具微调工作。
等手摇脉冲发生器修好后再将该参数置“1”。
2、当机床开机后返回参考点时出现超行程报警。
上述机床在返回参考点过程中,出现510或511超程报警,处理方法有两种:(1)若X轴在返回参考点过程中,出现510或是511超程报警,可将参数0700LT1X1数值改为+99999999(或将0704LT1X2数值修改为-99999999)后,再一次返回参考点。
若没有问题,则将参数0700或0704数值改为原来数值。
(2)同时按P和CAN键后开机,即可消除超程报警。
3、一台FANUC 0i数控车床,开机后不久出现ALM701报警。
从维修说明书解释内容为控制部上部的风扇过热,打开机床电气柜,检查风扇电机不动作,检查风扇电源正常,可判定风扇损坏,因一时购买不到同类型风扇,即先将参数RRM8901#0改为“1”先释放ALM701报警,然后在强制冷风冷却,待风扇购到后,再将PRM8901改为“0”。
4、一台FANUC 0M数控系统加工中心,主轴在换刀过程中,当主轴与换刀臂接触的一瞬间,发生接触碰撞异响故障。
分析故障原因是主轴定位不准,造成主轴头与换刀臂吻合不好,无疑会引起机械撞击声,两处均有明显的撞伤痕迹。
经查,换刀臂与主轴头均无机械松动,且换刀臂定位动作准确,故采用修改N6577参数值解决,即将原数据1525改为1524后,故障排除。
5、密集型参数0900~0939维修法。
按FANUC 0MC操作说明书的方法进行参数传输时,密集型参数0900~0939必须用MDI方式输入很不方便。
FANUC-0i-Mate-D数控系统机床常用参数
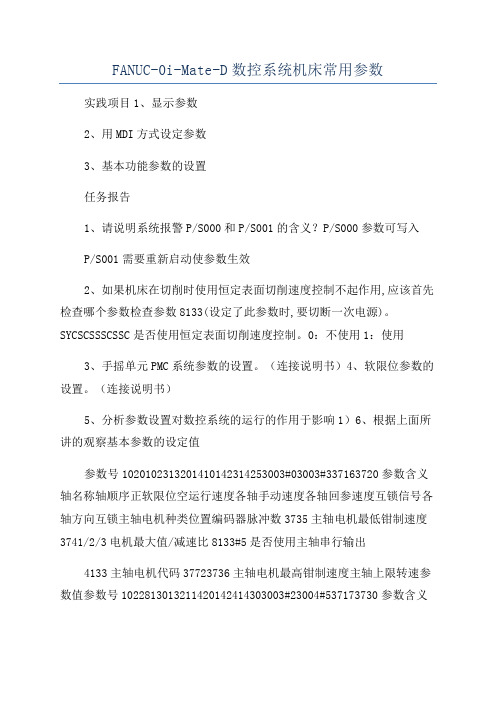
FANUC-0i-Mate-D数控系统机床常用参数实践项目1、显示参数
2、用MDI方式设定参数
3、基本功能参数的设置
任务报告
1、请说明系统报警P/S000和P/S001的含义?P/S000参数可写入
P/S001需要重新启动使参数生效
2、如果机床在切削时使用恒定表面切削速度控制不起作用,应该首先检查哪个参数检查参数8133(设定了此参数时,要切断一次电源)。
SYCSCSSSCSSC是否使用恒定表面切削速度控制。
0:不使用1:使用
3、手摇单元PMC系统参数的设置。
(连接说明书)
4、软限位参数的设置。
(连接说明书)
5、分析参数设置对数控系统的运行的作用于影响1)
6、根据上面所讲的观察基本参数的设定值
参数号1020102313201410142314253003#03003#337163720参数含义轴名称轴顺序正软限位空运行速度各轴手动速度各轴回参速度互锁信号各轴方向互锁主轴电机种类位置编码器脉冲数3735主轴电机最低钳制速度3741/2/3电机最大值/减速比8133#5是否使用主轴串行输出4133主轴电机代码37723736主轴电机最高钳制速度主轴上限转速参数值参数号1022813013211420142414303003#23004#537173730参数含义
轴属性CNC控制轴数负软限位各轴快移速度各轴手动快移速度最大切削进给速度各轴互锁信号超程信号个主轴放大器号模拟输出增益参数值。
FANUC0系列数控系统的功能特点及主要应用机床

FANUC 0系列数控系统的功能特点及主要应用机床FANUC 0系列分别有A、B、C、D等产品,各产品又有不同。
在这四种产品中,目前在国内使用最多的是普及型FANUC 0-D和全功能型FANUC 0-C两个系列。
FANUC 0系统由CNC基本配置,主轴和进给伺服单元以及相应的主轴电动机和进给电动机,CRT显示器,系统操作面板,机床操作面板,附加的输入/输出接口板(B2),电池盒,手摇脉冲发生器等部件组成。
其中的CNC基本配置又由主印制电路板(PCB)、存储器板、图形显示板、可编程机床控制器板(PMC-M)、伺服轴控制板、输入/输出接口板、子CPU(中央处理器)板、扩展的轴控制板、数控单元电源和DNC控制板组成,各板插在主印制电路板上,与CPU 的总线相连。
FANUC 0系列产品有以下特点:(1)采用高速的微处理器芯片FANUC的0系列产品使用Intel 80386芯片,1988年以后的产品改用使用Intel 80486DX2。
(2)采用高可靠性的硬件设计及全自动化生产制造该产品采用了高品质的元器件,并且大量采用了专用VLSI超大规模集成电路芯片,在一定程度上提高了数控系统的可靠性和系统的集成度。
使用表面安装元件(SMD),进一步提高了数控系统的集成度,使数控系统的体积大幅度减小。
(3)丰富的系统控制功能在系统的功能上具有刀具寿命管理、极坐标插补、圆柱插补、多边形加工、简易同步控制、Cf轴控制(主轴回转由进给伺服电动机实现,回转位置可与其他进给轴一起参与插补)和Cs轴控制(主轴电动机不是进给伺服电动机,而是FANUC 主轴电动机,由装在主轴上的编码器检测主轴位置,可与其他进给轴一起参与插补)、串行和模拟的主轴控制、主轴刚性攻丝、多主轴控制功能、主轴同步控制功能、PLC梯形图显示和PLC梯形图编辑功能(需要编程卡)、PLC轴控制功能等。
该系统除了通用的宏程序功能以外,还增加了定制型用户宏程序,这样为用户提供了更大的个性化设计的空间。
- 1、下载文档前请自行甄别文档内容的完整性,平台不提供额外的编辑、内容补充、找答案等附加服务。
- 2、"仅部分预览"的文档,不可在线预览部分如存在完整性等问题,可反馈申请退款(可完整预览的文档不适用该条件!)。
- 3、如文档侵犯您的权益,请联系客服反馈,我们会尽快为您处理(人工客服工作时间:9:00-18:30)。
FANUC0数控车床(设原点为端面中心)
1、机床-选择机床-FANUC0-车床-标准
2、俯视图-视图-视图选项-左键平移,右键旋转
3、零件-定义毛坯-低碳钢圆柱形-修改数据
4、放置零件-选择零件-安装
5、机床-选择刀具-D型第一把95º
6、REF-“+”(X~Z)-两灯亮回参考点
7、JOG-start-stop-MDI-PROGRAM-M04(Input)-start(上)
8、JOG-“-”(X~Z靠近工件)-调进给速度
9、试切外圆毛坯-POS-记X值如214.720-stop
10、测量-剖面图测量-否-点击试切段-标号4-记X值如46.042(直径)-退出
11、MENUOf SET-GEOMETRY(几何形状补偿,第二个键)-输入X168.678
12、POS-start(下)-“+”-切端面-记Z如188.4
附:另一种刀补输入MX46.042、MZ0
13、MENUOf SET-第三个键-G54~G59-选G55输入X168.678、Z188.4-PROGROM-EDIT(编程)
/直接EDIT(编程)
/调程序:DNC-机床-DNC传送-打开-PROGROM-输入程序名如O1234-回车-EDIT-修改程序-Outputstart
14、PROGRAM-RESET-AUTO(Off)
FANUC0数控铣床(原点为毛坯表面中心点)
1、选择机床-FANUC0-铣床-标准
2、视图-去掉罩子;左键平移,右键旋转;仿真倍率可增加
3、定义毛坯如X250Y250Z100-安装夹具-选择零件、夹具(工艺板)
4、放置零件-安装压板-任选一个
5、REF-X向+、Y向+、Z向+-三灯亮回参考点
6、机床-基准工具-选刚性靠棒(第一个、底座为直径14);寻边界(第二个)
7、JOG-Z向-、X向-、Y向-
8、X向-(碰)-塞尺检查1mm-STEP/HANDLE-X100(-为太紧、+为太松)-X10(-为太紧、+为太松)-X1(寻合适点)-记X1为-367.000-收回塞尺-求X=X1-0.5×14-塞尺1mm-0.5×250=-500
9、JOG-Y向+-X向-左视图
10、Y向-(碰)-塞尺检查1mm-STEP/HANDLE-X100(-为太紧、+为太松)-X10(-为太紧、+为太松)-X1(寻合适点)-记Y1为-282.000-收回塞尺-求Y=Y1-0.5×14-塞尺1mm-0.5×250=-415 11、拆除工具-抬高夹具-机床-选择刀具-序号2第一把(直径16,长度100)
12、JOG-Y向-
13、Z向-(碰)-塞尺检查1mm-STEP/HANDLE-X100(-为太紧、+为太松)-X10(-为太紧、+为太松)-X1(寻合适点)-记Z1为-277.000-收回塞尺-求Z=Z1-塞尺1mm=-278
14、MENUOf SET-OFSET DATA-输入8(刀具半径补偿为0.5×16=8)
15、MENUOf SET-OFSET HEIGHT(长度补偿即换刀)
15、MENUOf SET-OFSET G54~G59-如选G55:X-500、Y-415、Z-278-EDIT/直接EDIT(编程)/调程序:DNC-机床-DNC传送-打开-PROGROM-输入程序名如O1234-回车-EDIT-修改程序-Outputstart
16、PROGRAM-RESET-AUTO(Off)。