铸铁检验标准
铸造公司原材料成品检验标准

铸造公司原材料成品检验标准铸造公司原材料、成品检验标准审批:一、原材料进厂检验对EPC消失模铸件生产中原材料:灰铸铁用生铁、球墨铸铁用生铁、硅铁、锰铁、铬铁、废钢;聚苯乙烯;石英砂和炉衬材料进厂检验规定如下:采用标准:GB/T718—2005《灰铸铁件用生铁》GB1412—85《球墨铸铁件用生铁》GB/T2272—2022《硅铁》GB/T3795—2006《电炉锰铁》GB/T5683—2022《铬铁》GB719—84《生铁化学分析用试样制取方法》GB/T4010—94《铁合金化学分析用试样的采取和制备》Q/BAML002-2022《CF4AL感应电炉酸性炉衬耐火材料》——**环宇石英砂企业标准Q/BAML001-2022《精制石英砂〔粉〕》——**环宇石英砂企业标准1、灰铸铁用生铁的检验:1.1灰铸铁用生铁的检验依据GB/718—2005《灰铸铁件用生铁》标准进行检验,其中化学成分如表1所示,要求C含量不得低于4.1%。
1.2要求对进厂每批灰铸铁用生铁进行检验。
由理化室依照GB/719—84《生铁化学分析用试样制取方法》现场抽样,并制取试样;化验分析后出具《原材料进厂检测及化学分析报告单》。
分析结果合格方能入库,不合格应明确标识,由技术部门负责人决定是让步接受还是退货后进行处理。
表1 灰铸铁用生铁〔摘自GB/T718—2005〕铁号牌号铸34铸30铸26铸22铸18铸14代号Z34Z30Z26Z22Z18Z14化学成分〔%〕C>、4.1Si>3.20~3.60>2.80~3.20>2.40~2.80>2.00~2.40>1.60~2.00>1.25~1.60Mn1组≤0.052>0.50~0.90组3组>0.90~1.30P1级≤0.062级>0.06~0.103级>0.10~0.204级>0.20~0.405级>0.40~0.90S1类≤0.03≤0.042类≤0.04≤0.053类≤0.05≤0.061.3外观质量:规整平滑,根本无毛边。
铸件质量检验标准

铸件质量检验标准铸件是一种常见的生产工艺,广泛用于各个行业和领域。
铸件质量的好坏直接影响产品的性能和可靠性,因此进行铸件质量检验至关重要。
本文将介绍铸件质量检验的标准和方法。
一、铸件质量检验的重要性铸件质量检验的目的是确保铸件的尺寸精度、表面质量和机械性能达到设计要求。
一方面,铸件的尺寸精度和表面质量直接影响产品的装配和使用;另一方面,对于承受重载或高温等极端工况的铸件来说,其机械性能的好坏关系到产品的安全可靠性。
二、铸件质量检验的标准铸件质量检验的标准包括国家标准、行业标准和企业自身标准。
国家标准是根据相关法律法规制定的,具有强制性,是衡量铸件质量的重要依据。
行业标准是在国家标准的基础上,由行业协会或行业组织制定的,作为行业内铸件质量的参考指南。
企业自身标准是企业根据生产情况和需求制定的,用于规范和管理内部质量控制。
在铸件质量检验中,常用的国家标准有《铸造铁件技术条件》、《铸铝合金件技术条件》等,而行业标准包括《汽车铝合金压铸铸件技术规范》、《船用铸铁件技术条件》等。
企业自身标准则根据企业具体的生产工艺和要求制定,例如《XX公司铸件质量检验标准》。
三、铸件质量检验的方法铸件质量检验的方法主要包括外观检查、尺寸检测和性能测试。
1. 外观检查外观检查是铸件质量检验中最简单直观的方法。
通过肉眼观察铸件的外观,检查是否有裂纹、砂眼、气孔、夹渣等缺陷。
外观检查可以用目视检查或借助放大镜进行观察。
2. 尺寸检测尺寸检测是铸件质量检验中最常见的方法。
主要是测量铸件的外形尺寸、孔径尺寸和壁厚尺寸等。
常用的尺寸测量工具有游标卡尺、内径卡尺、外径卡尺、深度尺等。
尺寸检测可以帮助判断铸件是否满足设计要求。
3. 性能测试性能测试是铸件质量检验中最关键的方法,主要包括力学性能测试、化学成分分析和金相组织分析。
力学性能测试主要是测试铸件的拉伸、弯曲、冲击等力学性能。
化学成分分析可以确定铸件的材料成分是否符合要求。
金相组织分析可以观察铸件的金相组织结构,评估其机械性能。
铸件外观检查一般标准
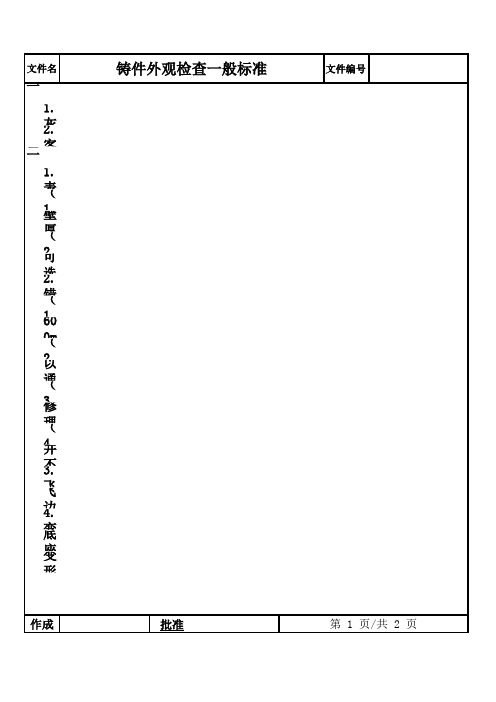
一.适用范围:1.灰铸铁和球墨铸铁件;2.客户有专门要求的以客户要求为准。
二.细 则:1.表面粗糙度:(1)表面粗糙度的凸凹高度差:壁厚10mm 以下要小于0.3mm;壁厚10mm以上要小于0.5mm。
局部超标可以打磨,打磨后再抛丸。
(2)表面粗糙度越细越好,但里面和外面,平面和垂直面要均匀。
可选用典型产品作为比照样板。
2.错箱和涨箱:(1)铸件分型面最大尺寸100mm以内,错箱要小于1mm;100至600mm错箱要小于2mm;600mm以上错箱要小于3.5mm。
(2)如果产品在本厂加工,而且错箱超差能够通过加工修正的,可以通过加工重新修正,但这些产品要分开管理。
(3)非加工面的涨箱,如果能够通过打磨或简单加工去除的,可以修理,但修理后要再抛丸。
(4)加工面出现的涨箱(指在本厂加工的加工面),只要能够去除并不影响其它尺寸,可以算合格毛坯。
3.飞边毛刺:飞边毛刺打磨残留量在0.5mm以下即可。
4.变形、翘曲:底座、盖板类的变形挠度允许量:自由状态放置在平台上,其最大变形量要保证在总长度的0.5%以下,比如600mm长可以3mm以下。
作成第 1 页/共 2 页批准5.气孔、渣眼、砂眼类:(1)加工面不允许有此类缺陷。
在本厂加工的产品,加工面孔眼不超过加工量,可以通过加工去除。
(2)非加工面的孔眼可以修补(铁基修补胶)、焊补,但必须符合以下范围:深度小于该部壁厚的三分之一、长或宽小于该部壁厚;数量5处以下。
需要电镀、热镀、粉体涂漆、电泳涂漆的不在此列。
6.表面皱纹:皱纹深度小于0.5mm,长度小于四倍壁厚,可以通过打磨方法处理。
7.冷隔、浇不足:冷隔(汤境)浇不足为废品,不能修补。
8.多肉:掉砂多肉通过铲磨不能恢复原形状的为废品。
9.缺肉:掉砂碰伤浇口根部缺肉,参考孔眼类的修补范围。
10.打磨修补:(1)打磨后残留量保证在0.5mm以下,不允许过度打磨。
(2)局部打磨过度的限度:深1mm长度不超过该部壁厚。
铸件外观质量检验规范
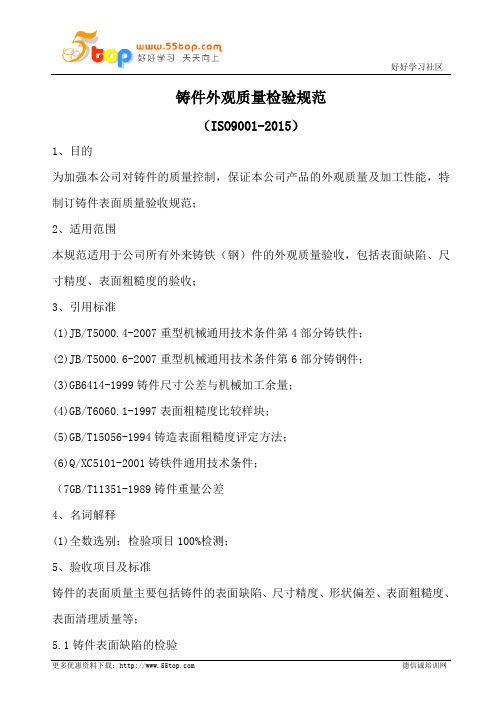
铸件外观质量检验规范(ISO9001-2015)1、目的为加强本公司对铸件的质量控制,保证本公司产品的外观质量及加工性能,特制订铸件表面质量验收规范;2、适用范围本规范适用于公司所有外来铸铁(钢)件的外观质量验收,包括表面缺陷、尺寸精度、表面粗糙度的验收;3、引用标准(1)JB/T5000.4-2007重型机械通用技术条件第4部分铸铁件;(2)JB/T5000.6-2007重型机械通用技术条件第6部分铸钢件;(3)GB6414-1999铸件尺寸公差与机械加工余量;(4)GB/T6060.1-1997表面粗糙度比较样块;(5)GB/T15056-1994铸造表面粗糙度评定方法;(6)Q/XC5101-2001铸铁件通用技术条件;(7GB/T11351-1989铸件重量公差4、名词解释(1)全数选别:检验项目100%检测;5、验收项目及标准铸件的表面质量主要包括铸件的表面缺陷、尺寸精度、形状偏差、表面粗糙度、表面清理质量等;5.1铸件表面缺陷的检验5.1.1表面缺陷检验的一般要求(1)铸件非加工表面上的浇冒口必须清理得与铸件表面同样平整,加工面上的浇冒口残留量应符合技术要求,若无要求,则按表8执行;(2)在铸件上不允许有裂纹、通孔、穿透性的冷隔和穿透性的缩松、夹渣等机械加工不能去除的缺陷;(3)铸件非加工表面的毛刺、披缝、型砂、砂芯等应清理干净;(4)铸件一般待加工表面,允许有不超过加工余量范围内的任何缺陷存在;重要加工面允许有不超过加工余量2/3的缺陷存在,但裂纹缺陷应予清除;加工后的表面允许存在直径*长度*深度小于等于2*2*2的非连片孔洞的铸造缺陷;(5)作为加工基准面(孔)和测量基准的铸件表面,平整度小于等于2.0毫米、粗糙度Ra50以内;(6)铸件表面气孔、砂眼、夹渣面积不大,但比较分散或者有连片麻点的表面不予接收;(7)除技术要求特别注明的铸件外,对于表面有气孔、缩孔、砂眼等缺陷的铸钢件允许补焊,但铸铁件未经允许不得焊补(铸铁件实行一案一判的原则)但补焊面积不允许超过铸件面积的10%,焊接质量应符合JB/T5000.7-2007标准要求,补焊后必须退火、机械性能达到图纸要求,且不得有渗漏及影响外观的缺陷;5.1.2铸件外观质量等级缺陷项目等级A B C飞边不允许飞边高度≤1.5毫米允许不易于伤手的飞边毛刺不允许允许不易于伤手的毛刺允许不易伤手的毛刺孔眼气孔 100cm 2面积内允许直径不大于φ2mm 深度不超过壁厚1/4的孔眼2个,两处距离>60mm ;整个铸件不超过4个100cm 2面积内允许直径不大于φ3mm 深度不超过壁厚1/3的孔眼2处,两处距离>60mm ;整个铸件不超过8个不致于影响强度,其余不做要求 针孔 渣眼 缩孔 不致于影响强度裂纹 不允许 不允许不允许 冷隔 沟槽 夹砂结疤 不允许 100cm 2面积内允许面积不超过8cm 2的缺陷2处;整个铸件不超过4处不致于影响强度 皱皮 不允许 不明显引人注意缩陷不允许不允许 不允许缺肉1、一般零部件采用B 级精度,在检查过程中,如有一个或多个项目超出B 级精度要求的零部件均判定为不合格;2、影响到零部件安全、性能的部位,外观质量采用A 级精度,如果有一个或多个项目超出规定级精度要求的零部件均判定为不合格;5.2铸件尺寸的检验 5.2.1铸件毛坯尺寸公差铸件尺寸公差应按毛坯图或技术条件规定的尺寸公差等级执行,当技术文件未规定尺寸公差时,则应以GB6414为依据,并按照下表选定公差值(粗线框内为推荐使用公差等级);毛坯铸件基本尺寸(mm )尺寸公差等级CT12CT13 CT14 CT15 CT16 ≤10~16 4.4 --- --- --- --- >16~25 4.6 6 8 10 12 >25~40 5.0 7 9 11 14 >40~63 5.6 8 10 12 16 >63~100 6 9 11 14 18 >100~160 7 10 12 16 20 >160~250 8 11 14 18 22 >250~400912162025>400~630 10 14 18 22 28 >630~1000 11 16 20 25 32 >1000~1600 13 18 23 29 37 >1600~2500 15 21 26 33 42 >25004000 17 24 30 38 49 >4000~6300 20 28 35 44 56 >6300~100002332405064注:1、毛坯铸件基本尺寸是指机械加工前毛坯铸件的尺寸,包括加工余量和起模斜度; 2、毛坯基本尺寸按铸件最大尺寸选取,该铸件较小尺寸公差等级与最大尺寸公差等级相同;3、壁厚采用低一级的公差等级;4、公差带应对称于毛坯铸件基本尺寸配置,例:基本尺寸30mm ,CT13公差值为±7mm ;如有特殊要求非对称式配置时,应在技术要求中单独列出公差范围;5.2.2铸件分型面处最大错型值应不得超过表2所示公差值,当需进一步限制错型量时,应从表中选取;公差等级CT 错型值(mm )11~13 1.5 14~162.55.2.3铸件加工余量应符合表的规定,有特殊要求的表面应在技术要求中单独标注加工余量;最大轮廓尺寸加工余量一个面顶面加量≤30 4 2>30~50 5 >50~180 6 >180~315 7 >315~500 8 >500~800 103>800~1250 12 >1250~1600 144>1600~250016>2500~3150 18>3150~4000 205>4000~6300 25>6300~10000 30 7注:1、属于该铸件的较小尺寸的加工余量与最大轮廓尺寸的加工余量相同;2、此表加工余量仅指一个面的加工余量,对于柱面和两面加工的铸件,铸件轮廓尺寸应为最终机械加工后成品尺寸与两倍加工余量之和;5.3表面粗糙度检测表面粗糙度总体检测原则依据图纸要求,当图纸无要求是执行国标GB/T15056;5.3.1一般情况下,表面粗糙度要求Ra50,铸件难以清理的部位,局部允许Ra100,待加工表面允许降低1级;5.3.2.使用面积法作为验收依据面积法常用的比较样块评定铸件表面粗糙度;方法如下:(1)铸造表面粗糙度比较样块应符合GB6060.1-1997标准;(2)按照国标BWZ001-88评定铸件表面粗糙度的等级;(3)铸件的浇道、冒口、修补的残余表面及铸造表面缺陷(如粘砂、结疤等)不列为被检表面;(4)以铸造表面粗糙度比较样块为对照标准,对被检铸件的铸造表面用视觉或触觉的方法进行对比;(5)用样块对比时,应选用适于铸造合金材料和工艺方法的样块进行对比;(6)被检的铸造表面必须清理干净,样块表面和被检表面均不得有锈蚀处;(7)用样块对比时,砂型铸造表面被检点数应符合表的规定;特种铸造表面被检点数应按表8的规定加倍;被检点应平均分布,每点的被检面积不得小于与之对比面的面积;被检铸造表面面积(cm2)<200 200~1000 100~10000 >10000被检点数(个) 不少于2 每200cm2不少于1 每1000cm2不少于1不少于40 (8)当被检铸造表面的粗糙度介于比较样块两级参数值之间者,所确定的被检铸造表面的粗糙度等级为粗的一级;(9)对被检铸造表面,以其80%的表面所达到的最粗表面粗糙度等级,为该铸造表面粗糙度等级;5.3.3铸件表面清理检测5.3.1铸件几何形状必须完整,非加工面上的清理损伤不应大于该处的尺寸偏差,加工面上的损伤不应大于该处加工余量的1/2;5.3.2允许铸件表面有少量的局部低凹或打磨痕迹,在直径不大于8mm,并能保证铸件规定的最小的壁厚;5.3.3为去除铸造缺陷而打磨后的铸件表面粗糙度应与一般铸件表面粗糙度基本一致;5.3.4除特殊情况外,铸件表面允许残留的浇冒口、毛刺,多肉残余量应按表8的要求进行;类别非加工面凸出高度(mm)加工面凸出高度(mm) 外表面非外表面浇冒口残余量-0.5~0.5 <2 <2~4毛刺残余量0 <2 <1~2多肉残余量<1 <2 <25.3.5铸件表面须经过防锈处理,保证在铸件进入面加工时不得有任何的锈蚀;5.3.6铸件表面如有油漆要求的,必须按有关涂装规定执行;5.4铸件重量检测5.4.1对于没有特殊要求的铸件,重量偏差可以不作为验收依据;如果技术条件有要求,供需双方协商后,铸件的重量偏差也应作为验收依据,一般应符合表的规定;公称重量(Kg) ≤200>200~500>500~1000>1000~5000>5000~10000>10000~30000>30000~50000>50000铸件重量上偏差(%)8 7.5 7 6.5 6 5.5 5 4.5。
球墨铸铁金相检测标准2021

球墨铸铁金相检测标准2021
球墨铸铁是一种具有优良机械性能和耐腐蚀性能的铸铁材料,常用于制造汽车零部件、机械设备、管道和阀门等。
金相检测是对材料显微组织进行观察和分析的一种常见方法,以评估材料的质量和性能。
2021年的球墨铸铁金相检测标准主要包括以下几个方面:
1. 显微组织观察,金相检测标准通常要求对球墨铸铁的显微组织进行观察,包括珠光体、铁素体和渗碳体的分布情况、尺寸和形态等。
这些观察可以通过金相显微镜或扫描电镜等设备进行。
2. 化学成分分析,金相检测标准通常还要求对球墨铸铁的化学成分进行分析,包括主要合金元素(如碳、硅、锰、镁等)的含量和分布情况。
这可以通过化学分析方法(如光谱分析、X射线荧光分析等)来完成。
3. 相对密度和孔隙率检测,球墨铸铁的相对密度和孔隙率对其性能有重要影响,因此金相检测标准通常也包括对这些指标的检测要求,可以通过密度计和金相显微镜等设备进行测定。
4. 力学性能测试,金相检测标准还可能包括对球墨铸铁的力学
性能进行测试,如拉伸强度、硬度、冲击韧性等指标的测定,以评估材料的强度和韧性。
总的来说,球墨铸铁金相检测标准旨在通过对材料显微组织、化学成分、密度、孔隙率和力学性能等方面的检测和分析,全面评估球墨铸铁的质量和性能,确保其符合相关标准要求,以满足不同工程和应用的需要。
具体的标准文件可以参考国家标准化管理委员会发布的相关标准文献,以获取最新的标准要求和测试方法。
铸铁探伤标准
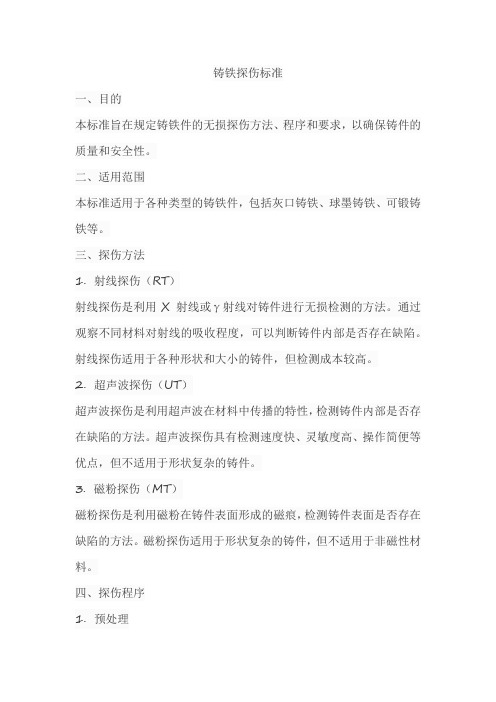
铸铁探伤标准一、目的本标准旨在规定铸铁件的无损探伤方法、程序和要求,以确保铸件的质量和安全性。
二、适用范围本标准适用于各种类型的铸铁件,包括灰口铸铁、球墨铸铁、可锻铸铁等。
三、探伤方法1. 射线探伤(RT)射线探伤是利用X射线或γ射线对铸件进行无损检测的方法。
通过观察不同材料对射线的吸收程度,可以判断铸件内部是否存在缺陷。
射线探伤适用于各种形状和大小的铸件,但检测成本较高。
2. 超声波探伤(UT)超声波探伤是利用超声波在材料中传播的特性,检测铸件内部是否存在缺陷的方法。
超声波探伤具有检测速度快、灵敏度高、操作简便等优点,但不适用于形状复杂的铸件。
3. 磁粉探伤(MT)磁粉探伤是利用磁粉在铸件表面形成的磁痕,检测铸件表面是否存在缺陷的方法。
磁粉探伤适用于形状复杂的铸件,但不适用于非磁性材料。
四、探伤程序1. 预处理对铸件进行清洗、干燥和打磨等处理,以去除表面杂质和氧化层,确保探伤结果的准确性。
2. 探伤操作根据铸件的大小和形状选择合适的探伤方法,按照探伤设备的操作规程进行探伤操作。
在操作过程中应注意以下几点:a) 确定合适的探伤灵敏度;b) 确保探头与铸件表面紧密贴合;c) 合理选择扫描速度和角度;d) 记录探伤过程中的异常现象。
3. 结果判定和处理根据探伤结果进行判断和处理,包括以下几种情况:a) 合格:铸件内部无缺陷或缺陷在允许范围内,可以判定为合格;b) 不合格:铸件内部存在超出允许范围的缺陷,应判定为不合格;c) 让步接收:对于某些小缺陷,在不影响使用和安全性能的情况下,可考虑让步接收;d) 返修或报废:对于不合格的铸件,应进行返修或报废处理。
返修后应重新进行探伤检测。
hb6578-1992铸件内部针孔检验标准

标题:深度剖析HB6578-1992铸件内部针孔检验标准近年来,随着我国工业领域的快速发展,对于各类材料和制造工艺的要求也越来越高。
在这种情况下,铸件作为一种重要的工业制造品,其质量问题备受关注。
其中,内部针孔是铸件常见的质量缺陷之一,对于检验标准的制定和规范至关重要。
本文将围绕着HB6578-1992铸件内部针孔检验标准展开深度探讨,帮助读者更全面地了解和掌握这一标准的内容和实际应用。
一、HB6578-1992标准概述HB6578-1992标准是我国针对铸件内部针孔缺陷的检验标准,其制定的目的是为了规范铸件生产过程中的质量控制,保证铸件的可靠性和安全性。
该标准主要包括了检验对象、检验方法、评定和接收标准等内容,是铸件生产过程中必不可少的一部分。
在实际应用中,HB6578-1992标准通过对铸件内部的针孔缺陷进行X 射线或射线检测,来评定铸件的质量是否符合标准要求。
检验结果将直接影响铸件的使用性能和安全性,因此对于该标准的理解和运用至关重要。
二、HB6578-1992标准的主要内容分析1. 检验对象HB6578-1992标准明确了适用范围,主要针对各类金属铸件内部的针孔缺陷进行检测和评定。
不同种类的铸件在检验时需要符合不同的要求,如铸铁件、铸钢件、有色金属铸件等,都有相应的检验标准和方法。
2. 检验方法标准中详细描述了针对铸件内部针孔的X射线或射线检测方法。
这些方法包括了检测设备的选择、操作规程、检测条件的设定等,旨在保证检测的准确性和可靠性。
对于不同类型的铸件,还规定了相应的检测参数和标准。
3. 评定和接收标准HB6578-1992标准对于内部针孔缺陷的评定和接收标准也作出了明确的规定。
根据检测结果,将铸件的内部针孔缺陷划分为不同等级,确定了不同等级下的允许针孔数量和大小范围。
这些评定标准对于铸件的质量控制和接收具有重要的指导意义。
三、HB6578-1992标准的应用与展望作为铸件生产和质量控制中的重要标准,HB6578-1992标准的正确理解和应用对于保障铸件质量至关重要。
铸件表面质量验收标准

铸铁件验收项目及标准铸件的表面质量主要包括铸件的表面缺陷、尺寸精度、形状偏差、表面粗糙度、表面清理质量等;1、铸件表面缺陷的检验1.1表面缺陷检验的一般要求1.1.1 铸件非加工表面上的浇冒口必须清理得与铸件表面同样平整,加工面上的浇冒口残留量应符合技术要求,若无要求,则按表8执行;1.1.2 在铸件上不允许有裂纹、通孔、穿透性的冷隔和穿透性的缩松、夹渣等机械加工不能去除的缺陷;1.1.3 铸件非加工表面的毛刺、披缝、型砂、砂芯等应清理干净;1.1.4 铸件一般待加工表面,允许有不超过加工余量范围内的任何缺陷存在;重要加工面允许有不超过加工余量2/3的缺陷存在,但裂纹缺陷应予清除;加工后的表面允许存在直径*长度*深度小于等于2*2*2的非连片孔洞的铸造缺陷;1.1.5 作为加工基准面(孔)和测量基准的铸件表面,平整度小于等于2.0毫米、粗糙度Ra50以内;1.1.6 铸件表面气孔、砂眼、夹渣面积不大,但比较分散或者有连片麻点的表面不予接收;1.1.7 除技术要求特别注明的铸件外,对于表面有气孔、缩孔、砂眼等缺陷的铸钢件允许补焊,但铸铁件未经允许不得焊补(铸铁件实行一案一判的原则)但补焊面积不允许超过铸件面积的10%,焊接质量应符合JB/T 5000.7-2007标准要求,补焊后必须退火、机械性能达到图纸要求,且不得有渗漏及影响外观的缺陷;1.2铸件外观质量等级表1 铸件外观质量等级2、铸件尺寸的检验2.1铸件毛坯尺寸公差铸件尺寸公差应按毛坯图或技术条件规定的尺寸公差等级执行,当技术文件未规定尺寸公差时,则应以GB6414-1999为依据,并按照表2选定公差值(粗线框内为推荐使用公差等级);(单位:mm)表2铸件尺寸公差2.2铸件分型面处最大错型值应不得超过表2所示公差值,当需进一步限制错型量时,应从表3中选取;表3 错型值(GB6414-1999)2.3铸件加工余量应符合表4的规定,有特殊要求的表面应在技术要求中单独标注加工余量;表4 加工余量(单位:mm)3、表面粗糙度检测表面粗糙度总体检测原则依据图纸要求,当图纸无要求是执行国标GB/T15056-1994;3.1一般情况下,表面粗糙度要求 Ra50,铸件难以清理的部位,局部允许Ra100,待加工表面允许降低1级;3.2.使用面积法作为验收依据面积法常用的比较样块评定铸件表面粗糙度;方法如下:3.2.1 铸造表面粗糙度比较样块应符合GB6060.1-1997标准;3.2.2 按照国标BWZ001-88评定铸件表面粗糙度的等级;3.2.3 铸件的浇道、冒口、修补的残余表面及铸造表面缺陷(如粘砂、结疤等)不列为被检表面;3.2.4 以铸造表面粗糙度比较样块为对照标准,对被检铸件的铸造表面用视觉或触觉的方法进行对比;3.2.5 用样块对比时,应选用适于铸造合金材料和工艺方法的样块进行对比;3.2.6 被检的铸造表面必须清理干净,样块表面和被检表面均不得有锈蚀处;3.2.7 用样块对比时,砂型铸造表面被检点数应符合表7的规定;特种铸造表面被检点数应按表8的规定加倍;被检点应平均分布,每点的被检面积不得小于与之对比面的面积;表7 被检铸造表面最低检测数3.2.8 当被检铸造表面的粗糙度介于比较样块两级参数值之间者,所确定的被检铸造表面的粗糙度等级为粗的一级;3.2.9 对被检铸造表面,以其80%的表面所达到的最粗表面粗糙度等级,为该铸造表面粗糙度等级;3.3铸件表面清理检测3.3.1 铸件几何形状必须完整,非加工面上的清理损伤不应大于该处的尺寸偏差,加工面上的损伤不应大于该处加工余量的1/2;3.3.2允许铸件表面有少量的局部低凹或打磨痕迹,在直径不大于 8mm,并能保证铸件规定的最小的壁厚;3.3.3为去除铸造缺陷而打磨后的铸件表面粗糙度应与一般铸件表面粗糙度基本一致;3.3.4除特殊情况外,铸件表面允许残留的浇冒口、毛刺,多肉残余量应按表8的要求进行;表8 浇冒口、毛刺、多肉等允许残留量值3.3.5铸件表面须经过防锈处理,保证在铸件进入面加工时不得有任何的锈蚀;3.3.6铸件表面如有油漆要求的,必须按有关涂装规定执行;4、铸件重量检测对于没有特殊要求的铸件,重量偏差可以不作为验收依据;如果技术条件有要求,供需双方协商后,铸件的重量偏差也应作为验收依据,一般应符合表6的规定;表6 铸件重量偏差。
球墨铸铁标准

球墨铸铁标准球墨铸铁是一种具有高强度、高韧性和良好耐腐蚀性能的材料,广泛应用于各种机械设备、建筑和市政工程等领域。
为了确保球墨铸铁产品的质量,各国都制定了相关的标准。
本文将介绍常见的球墨铸铁标准。
1. 国际标准1.1 ISO 1083: Spheroidal graphite cast ironsISO 1083是国际标准化组织(ISO)制定的球墨铸铁标准。
该标准对球墨铸铁的化学成分、机械性能和其他要求进行了规定。
其中包括球墨铸铁的各类级别、硬度要求、拉伸强度、冲击韧性等。
1.2 ISO 185: Grey cast ironsISO 185是ISO制定的灰铸铁标准,其中也包含了一些对球墨铸铁的要求。
该标准对灰铸铁和球墨铸铁的组织、力学性能、化学成分等进行了规定,并提供了一些有关材料检测的方法。
2. 欧洲标准2.1 EN 1563: Founding - Spheroidal graphite cast ironsEN 1563是欧洲标准化组织(CEN)制定的球墨铸铁标准。
该标准规定了球墨铸铁的材料级别、化学成分、机械性能和质量检测方法。
同时,该标准还分别对可用于不同工程领域的球墨铸铁进行了分类和要求。
2.2 EN 1561: Founding - Grey cast ironsEN 1561是CEN制定的灰铸铁标准,同样也包含了对球墨铸铁的一些要求。
该标准对灰铸铁和球墨铸铁的化学成分、机械性能、检验方法等进行了规定,并提供了不同环境条件下的使用温度范围。
3. 美国标准3.1 ASTM A536: Standard Specification for Ductile Iron CastingsASTM A536是美国材料与试验协会(ASTM)制定的球墨铸铁标准。
该标准覆盖了球墨铸铁的材料分类、化学成分、机械性能、试验方法等。
其中也对球墨铸铁的各类级别、硬度要求、拉伸强度等进行了规定。
3.2 ASTM A48: Standard Specification for Gray Iron CastingsASTM A48是ASTM制定的灰铸铁标准,其中也包含了对球墨铸铁的一些要求。
铸件表面质量验收标准

铸铁件验收项目及标准铸件的表面质量主要包括铸件的表面缺陷、尺寸精度、形状偏差、表面粗糙度、表面清理质量等;1、铸件表面缺陷的检验1.1表面缺陷检验的一般要求1.1.1铸件非加工表面上的浇冒口必须清理得与铸件表面同样平整,加工面上的浇冒口残留量应符合技术要求,若无要求,则按表8执行;1.1.2在铸件上不允许有裂纹、通孔、穿透性的冷隔和穿透性的缩松、夹渣等机械加工不能去除的缺陷;1.1.3铸件非加工表面的毛刺、披缝、型砂、砂芯等应清理干净;1.1.4铸件一般待加工表面,允许有不超过加工余量范围内的任何缺陷存在;重要加工面允许有不超过加工余量2/3的缺陷存在,但裂纹缺陷应予清除;加工后的表面允许存在直径*长度*深度小于等于2*2*2的非连片孔洞的铸造缺陷;1.1.5作为加工基准面(孔)和测量基准的铸件表面,平整度小于等于2.0 毫米、粗糙度Ra50以内;1.1.6铸件表面气孔、砂眼、夹渣面积不大,但比较分散或者有连片麻点的表面不予接收;1.1.7除技术要求特别注明的铸件外,对于表面有气孔、缩孔、砂眼等缺陷的铸钢件允许补焊,但铸铁件未经允许不得焊补(铸铁件实行一案一判的原则)但补焊面积不允许超过铸件面积的10%,焊接质量应符合JB/T 5000.7-2007标准要求,补焊后必须退火、机械性能达到图纸要求,且不得有渗漏及影响外观的缺陷;1.2铸件外观质量等级表1 铸件外观质量等级1、一般零部件采用B级精度,在检查过程中,如有一个或多个项目超出B级精度要求的零部件均判定为不合格;2、影响到零部件安全、性能的部位,外观质量采用A级精度,如果有一个或多个项目超出规定级精度要求的零部件均判定为不合格;2、铸件尺寸的检验2.1铸件毛坯尺寸公差铸件尺寸公差应按毛坯图或技术条件规定的尺寸公差等级执行,当技术文件未规定尺寸公差时,则应以GB6414-1999为依据,并按照表2选定公差值(粗线框内为推荐使用公差等级);表2铸件尺寸公差(单位:mm)2.2铸件分型面处最大错型值应不得超过表2所示公差值,当需进一步限制错型量时,应从表3中选取;表 3 错型值(GB6414-1999)2.3铸件加工余量应符合表4的规定,有特殊要求的表面应在技术要求中单独标注加工余量;表4加工余量(单位:mm)3、表面粗糙度检测表面粗糙度总体检测原则依据图纸要求,当图纸无要求是执行国标GB/T15056-1994;3.1一般情况下,表面粗糙度要求Ra50,铸件难以清理的部位,局部允许 Ra100,待加工表面允许降低1级;3.2.使用面积法作为验收依据面积法常用的比较样块评定铸件表面粗糙度;方法如下:3.2.1铸造表面粗糙度比较样块应符合GB6060.1-1997标准;3.2.2按照国标BWZ001-88评定铸件表面粗糙度的等级;3.2.3铸件的浇道、冒口、修补的残余表面及铸造表面缺陷(如粘砂、结疤等)不列为被检表面;3.2.4以铸造表面粗糙度比较样块为对照标准,对被检铸件的铸造表面用视觉或触觉的方法进行对比;3.2.5用样块对比时,应选用适于铸造合金材料和工艺方法的样块进行对比;3.2.6被检的铸造表面必须清理干净,样块表面和被检表面均不得有锈蚀处;3.2.7用样块对比时,砂型铸造表面被检点数应符合表7的规定;特种铸造表面被检点数应按表8的规定加倍;被检点应平均分布,每点的被检面积不得小于与之对比面的面积;表7 被检铸造表面最低检测数3.2.8当被检铸造表面的粗糙度介于比较样块两级参数值之间者,所确定的被检铸造表面的粗糙度等级为粗的一级;3.2.9对被检铸造表面,以其80%的表面所达到的最粗表面粗糙度等级,为该铸造表面粗糙度等级;3.3铸件表面清理检测3.3.1铸件几何形状必须完整,非加工面上的清理损伤不应大于该处的尺寸偏差,加工面上的损伤不应大于该处加工余量的1/2;3.3.2允许铸件表面有少量的局部低凹或打磨痕迹,在直径不大于8mm,并能保证铸件规定的最小的壁厚;3.3.3为去除铸造缺陷而打磨后的铸件表面粗糙度应与一般铸件表面粗糙度基本一致;3.3.4除特殊情况外,铸件表面允许残留的浇冒口、毛刺,多肉残余量应按表 8的要求进行;表8 浇冒口、毛刺、多肉等允许残留量值3.3.5铸件表面须经过防锈处理,保证在铸件进入面加工时不得有任何的锈蚀;3.3.6铸件表面如有油漆要求的,必须按有关涂装规定执行;4、铸件重量检测对于没有特殊要求的铸件,重量偏差可以不作为验收依据;如果技术条件有要求,供需双方协商后,铸件的重量偏差也应作为验收依据,一般应符合表6的规定;表6铸件重量偏差。
铸铁的标准

铸铁的标准
铸铁是一种强度较高、耐磨、抗压、抗震动和耐腐蚀的合金材料,主要由铸铁石墨和铁碳相组成。
铸铁的标准可以分为以下几个方面:
1. 化学成分标准:铸铁的化学成分主要包括碳、硅、锰、磷、硫等元素,不同应用领域和要求会有不同的化学成分标准。
2. 机械性能标准:铸铁的机械性能主要包括强度、韧性、硬度等指标,如抗拉强度、屈服强度、伸长率等。
3. 外观质量标准:铸铁的外观质量标准主要包括缺陷、表面粗糙度等方面的要求,如气孔、夹杂物、砂眼等。
4. 尺寸精度标准:铸铁零件的尺寸精度标准包括几何形状、尺寸公差、加工余量等要求。
此外,根据不同国家和行业的标准要求,铸铁还有一些特定的标准,如美国ASTM标准,欧洲EN标准以及中国GB标准等。
总之,铸铁的标准主要包括化学成分、机械性能、外观质量、尺寸精度等方面的要求,目的是确保铸铁材料在使用过程中能够满足相应的要求和性能。
球墨铸铁国家标准要求(概要)

球墨铸铁国家标准要求(概要)球墨铸铁国家标准要求(概要)1. 引言球墨铸铁是一种具有良好机械性能和性价比优势的材料,被广泛应用于各个领域。
为保证球墨铸铁产品的质量和安全性,制定国家标准是必要的。
2. 材料要求国家标准对球墨铸铁的材料要求进行了规定,包括以下方面:- 化学成分:规定了球墨铸铁中各元素的含量范围,确保材料的化学稳定性。
- 机械性能:要求球墨铸铁在拉伸强度、屈服强度、延伸率等方面满足标准要求,以保证产品的强度和可靠性。
- 微观结构:规定了球墨铸铁的组织要求,如球化率、球墨形态等,以提高材料的耐腐蚀性和耐磨性。
3. 技术要求国家标准对球墨铸铁产品的技术要求也进行了规定,包括以下方面:- 外观质量:要求球墨铸铁产品表面无明显缺陷、夹杂物和气孔等,并规定了允许的表面质量等级。
- 尺寸偏差:规定了球墨铸铁产品的尺寸偏差范围,确保产品的准确度和一致性。
- 热处理:要求球墨铸铁产品在热处理过程中达到规定的硬度、韧性等性能要求。
- 表面处理:规定了球墨铸铁产品的表面处理方法,如除锈、喷漆等,以提高产品的外观和耐久性。
4. 检验方法国家标准还规定了球墨铸铁产品的检验方法,确保产品的质量和符合标准要求。
检验方法包括化学成分分析、机械性能测试、显微组织观察等。
5. 标志和包装国家标准对球墨铸铁产品的标志和包装也进行了规定,以确保产品在运输和使用过程中的安全和易识别性。
以上是球墨铸铁国家标准要求的概要内容。
详情请参阅具体的国家标准文件。
请注意:本文档为概要,不对具体标准要求内容做详细解读和整理,请以官方发布的国家标准文件为准。
铸铁件检验规程
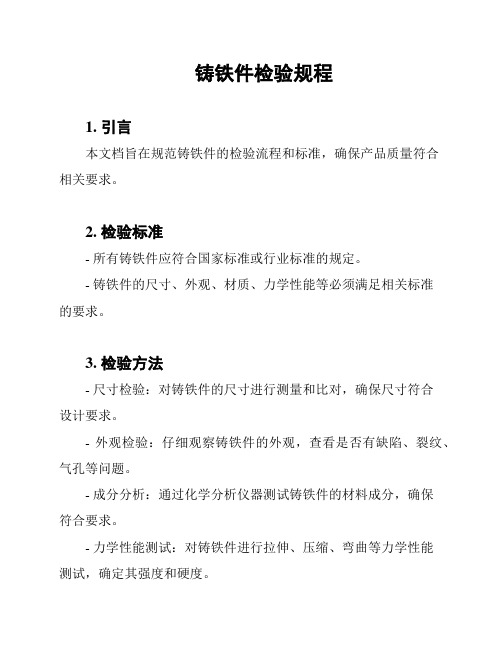
铸铁件检验规程1. 引言本文档旨在规范铸铁件的检验流程和标准,确保产品质量符合相关要求。
2. 检验标准- 所有铸铁件应符合国家标准或行业标准的规定。
- 铸铁件的尺寸、外观、材质、力学性能等必须满足相关标准的要求。
3. 检验方法- 尺寸检验:对铸铁件的尺寸进行测量和比对,确保尺寸符合设计要求。
- 外观检验:仔细观察铸铁件的外观,查看是否有缺陷、裂纹、气孔等问题。
- 成分分析:通过化学分析仪器测试铸铁件的材料成分,确保符合要求。
- 力学性能测试:对铸铁件进行拉伸、压缩、弯曲等力学性能测试,确定其强度和硬度。
- 非破坏性检测:采用超声波、磁粉、射线等非破坏性检测方法,发现内部缺陷和隐蔽问题。
4. 检验流程1. 准备工作:准备检验仪器、标准样品等必要设备和材料。
2. 尺寸检验:按照标准要求对铸铁件的尺寸进行检测。
3. 外观检验:用肉眼观察铸铁件的外观,发现任何缺陷或异常。
4. 成分分析:采集铸铁件样品进行化学分析,确认材料成分。
5. 力学性能测试:根据标准要求进行力学性能测试。
6. 非破坏性检测:根据需要进行相应的非破坏性检测。
7. 结果评定:根据检测结果,评定铸铁件是否合格。
8. 记录和报告:将检验结果记录并制作报告,保存备查。
5. 检验记录与报告- 检验过程中的数据、观察结果和评定意见应当记录并保存。
- 不合格的铸铁件应当注明问题所在,并提出修复或退货的建议。
- 检验报告应当详细描述被检铸铁件的信息、检验结果及评定意见。
6. 检验责任- 检验工作由经过培训和合格考核的专业人员负责。
- 检验人员应遵守相关规程、标准和操作要求,严格把控检验质量。
7. 术语及定义- 根据《铸铁件检验术语及定义》(可参考国家标准或行业标准)规定进行术语和定义的理解和解释。
8. 附录- 相关国家标准或行业标准的引用。
- 检验仪器与设备的清单。
---以上为《铸铁件检验规程》的内容概要,该规程旨在确保铸铁件的质量符合要求,同时规范了检验流程和标准。
铸铁件通用检验标准【精选文档】
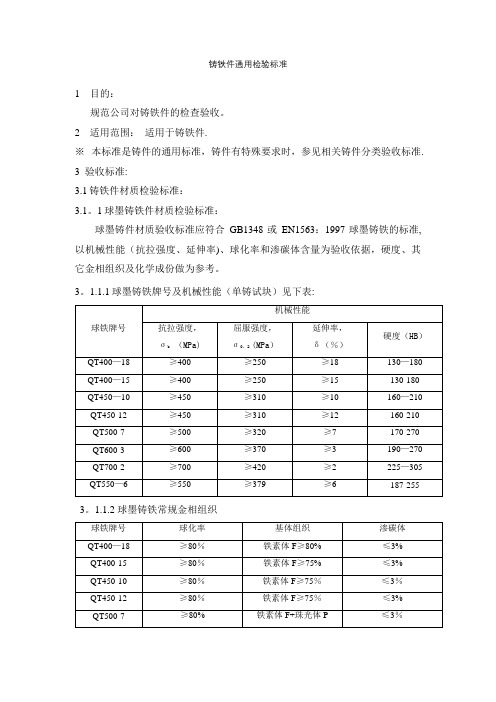
1目的:规范公司对铸铁件的检查验收。
2适用范围:适用于铸铁件.※本标准是铸件的通用标准,铸件有特殊要求时,参见相关铸件分类验收标准.3 验收标准:3.1铸铁件材质检验标准:3.1。
1球墨铸铁件材质检验标准:球墨铸件材质验收标准应符合GB1348或EN1563:1997球墨铸铁的标准,以机械性能(抗拉强度、延伸率)、球化率和渗碳体含量为验收依据,硬度、其它金相组织及化学成份做为参考。
3。
1.1.1球墨铸铁牌号及机械性能(单铸试块)见下表:3。
1.1.2 球墨铸铁常规金相组织3。
1.1.3球墨铸铁化学成份3.1.2灰铸铁件材质检验标准:灰铸件材质验收标准应符合GB9439或EN 1561:1997灰铸铁件的标准,以机械性能(抗拉强度)和硬度为验收依据,金相组织及化学成份做为参考.3.1。
2。
1灰铸铁牌号及机械性能(单铸试块)见下表:3. 1。
2。
2 灰铸铁常规金相组织3。
1.2。
3灰铸铁化学成份3.1。
3 材质检验取样规范3。
1。
3。
1机械性能检查:机械性能测试的试棒,每班次每种牌号至少浇一组,有新产品时增加一组,每组浇三根,若铸件进行退火处理,必须连同试棒(试块)一同进行热处理(若是渗碳体超标需热处理的件,按热处理后铸件本体的金相组织来验收)。
机械性能试验:二根用于生产厂测试性能(第一根合格则该批次合格,余下试棒留存(留有生产日期、包次标识),在工厂存放,存放期三年;若第一根试棒不合格,测试剩余二根,若第二根不合格则该批次产品全部报废;若第二根合格,应加试第三根,合格则判定该炉产品合格,若第三根不合格则该批次产品全部报废).材质检测报告存根(原始记录)保留11年。
常规灰铸铁试棒见下图:常规球墨铸铁试棒见下图:大小连杆试棒见下图:ASTM536标准(美标)试棒见下图3.1.3。
2金相组织检查:球铁铸件从每包铁水的最后一型附铸金相试块或铸件本体进行检验,依次往前直到合格(或本包铁水所浇铸件检验完)为止。
铸铁件验收标准
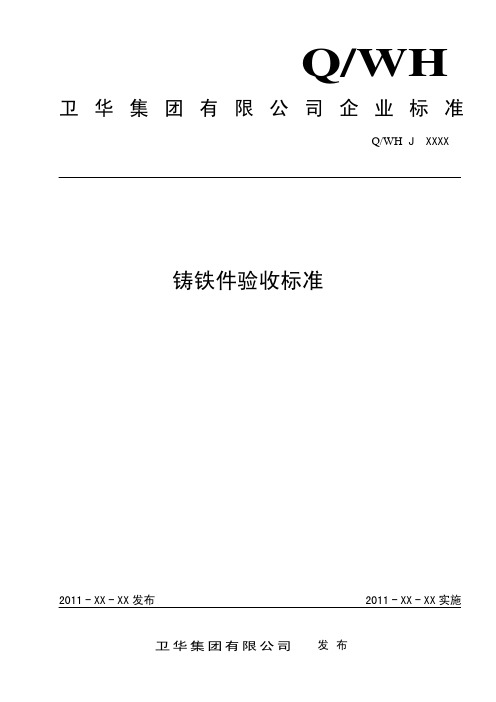
卫华集团有限公司企业标准
Q/WH J—XXXX
铸铁件验收标准
2011 - XX - XX 发布
2011 - XX - XX 实施
卫华集团有限公司 发 布
前言
请增加“本标准按照 GB/T 1.1-2009 给出的规则起草。” 本标准由卫华集团有限公司提出。 本标准由卫华集团技术标准化分委员会归口。 本标准主要起草单位:郑州卫华工程机有限公司技术部。 本标准主要起草人:代富贵。 本标准于 2011 年 月首次发布。
3
Q/WH J—XXXX
QT450-10 QT450-12 QT500-7 QT600-3 QT700-2 QT550-6
3.4-3.9 2.6-3.1 ≤0.3 ≤0.07 ≤0.03 0.025-0.06 0.02-0.04 3.4-3.9 2.6-3.1 ≤0.3 ≤0.07 ≤0.03 0.025-0.06 0.02-0.04 3.4-3.9 2.6-3.0 ≤0.45 ≤0.07 ≤0.03 0.025-0.06 0.02-0.04 3.2-3.7 2.4-2.8 0.4-0.5 ≤0.07 ≤0.03 0.025-0.06 0.02-0.04 3.2-3.7 2.3-2.6 0.5-0.7 ≤0.07 ≤0.03 0.025-0.06 0.02-0.04 3.4-3.9 2.6-3.0 0.1-0.4 ≤0.06 ≤0.03 0.025-0.06 0.02-0.04
400~ 630
630~ 1000
3.6
4.0
3.3 铸件外观质量 3.3.1 铸字、标识:铸件上所要求的铸字、标识必须完整、清晰、正确,符合图纸要求。 3.3.2 浇冒口、飞边残留高度:铸件上浇冒口、披缝等要清理干净,最大残留高度不超过 4mm。 3.3.3 表面粗糙度:铸件表面应光滑、平整,表面有粘砂、氧化皮、锈蚀等应清理干净,表面粗糙度 应小于 Ra25。表面各种飞刺的面积不允许超过 200X20 mm ,否者必须退回返工修理。 3.4 铸件外观尺寸
生铁检验标准

生铁检验标准生铁检验标准1、适用范围适用于本公司采购铸造熔炼作业用生铁的检验。
2、种类原材料生铁的种类是铸造用生铁和球墨铸铁用生铁。
3、质量标准 3.1化学成分:铸造用生铁(GB/T 718),其化学成分如表1所示;球墨铸铁用生铁(GB/T1412),其化学成分如表2。
表 1表 2由供应部将采购生铁牌号、批量通知化验室,化验员从本批生铁的不同堆放部位中随机采样,一块生铁作为一个样品。
3.2 外观及大小3.2.1要求块度在3Kg-10Kg 左右,10Kg 以上块度含量不超过3%;铁种铸造用生铁铁号牌号铸22 铸18 铸14 让步接收标准代号 Z22Z18 Z14化学成分%C >3.3>3.3 Si >2.0~2.4 >1.6~2.0>1.25~1.6>1.1~1.24 Mn 2组 0.50~0.90 >0.3~0.49 P 2级 0.06~0.10 0.06~0.10 S2类≤0.04≤0.05 ≤0.07铁种球墨生铁铁号牌号球10 球12 球16 让步接收标准代号 Q10Q12 Q16化学成分 %C >3.3 >3.8Si ≤1.0 >1.0~1.4 >1.4~1.8Mn 2组>0.2~0.50.51~0.6P 2级>0.06~0.08 S2类>0.03~0.043.2.2生铁外观无粘附炉渣、砂粒、油污、铁锈和腐蚀,每100块含量不超过5块。
4、检查及试验4.1检查批量及单位的构成4.1.1检查批量:检查批量以每种牌号生铁每天的交货量为一个批量。
4.1.2检查单位:以一块生铁为1个检查单位。
4.2检查顺序、检查项目、检查方式如表2;表2注:供方应在每批交货中附质量合格证明书(注明:供方名称、生铁的型号、类别、以及相应的化学成分等),且每半年提供国家或第三方公认试验机构的试验报告。
4.3 抽样规定:根据以下所规定的检验方式每批进行理化检验。
≤20吨取三个样品>20吨取四个样品由供应部将采购生铁牌号、批量通知化验室,化验员按《抽样标准》从本批生铁的不同堆放部位中随机采样,以一块生铁作为一个样品。
铸铁的国标
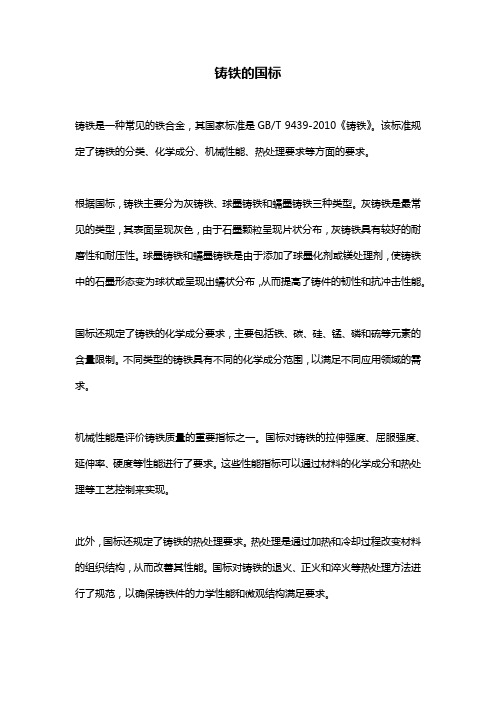
铸铁的国标
铸铁是一种常见的铁合金,其国家标准是GB/T 9439-2010《铸铁》。
该标准规定了铸铁的分类、化学成分、机械性能、热处理要求等方面的要求。
根据国标,铸铁主要分为灰铸铁、球墨铸铁和蠕墨铸铁三种类型。
灰铸铁是最常见的类型,其表面呈现灰色,由于石墨颗粒呈现片状分布,灰铸铁具有较好的耐磨性和耐压性。
球墨铸铁和蠕墨铸铁是由于添加了球墨化剂或镁处理剂,使铸铁中的石墨形态变为球状或呈现出蠕状分布,从而提高了铸件的韧性和抗冲击性能。
国标还规定了铸铁的化学成分要求,主要包括铁、碳、硅、锰、磷和硫等元素的含量限制。
不同类型的铸铁具有不同的化学成分范围,以满足不同应用领域的需求。
机械性能是评价铸铁质量的重要指标之一。
国标对铸铁的拉伸强度、屈服强度、延伸率、硬度等性能进行了要求。
这些性能指标可以通过材料的化学成分和热处理等工艺控制来实现。
此外,国标还规定了铸铁的热处理要求。
热处理是通过加热和冷却过程改变材料的组织结构,从而改善其性能。
国标对铸铁的退火、正火和淬火等热处理方法进行了规范,以确保铸铁件的力学性能和微观结构满足要求。
总的来说,GB/T 9439-2010《铸铁》是对铸铁的分类、化学成分、机械性能和热处理要求的国家标准。
通过遵循该标准,可以保证铸铁的质量和性能符合规定,从而满足各种工程和制造领域的需求。