装焊夹具设计规范
夹具标准

3、 装配: 3.1. 紧固螺栓采用内六角螺栓,公制标准件,在钢板厚度允许条件下,内六角头应沉入钢板表面 。 紧固需带弹簧垫圈; 3.2. 尽量从上方和侧面安装螺栓; 3.3. 定位销采用GB120-86标准销,自带装卸螺孔; 4、检测 4.1. 零件的检测采用常规量具检测; 4.2. 部件的检测采用常规检测或3D检测; 4.3. 夹具的整体检测采用3D检测,并出具最终检测报告。 4.4 夹具精度: 4.4.1主定位销的位置度公差:±0.1㎜; 4.4.2定位销的加工精度:直径+0.00~-0.05mm; 4.4.3定位面的装配公差:±0.2㎜; 4.4.4 翻转定位机构的重复定位精度:±0.2㎜(Φ200处㎜); 4.5 移动单元: 4.5.1 带有轴承及防尘装置; 4.5.2.设有限位块; 4.5.3.大型移动机构(重量大于80Kg)采用直线轴承; 4.5.4.小型移动机构采用无油润滑轴承; 5 、定位夹紧单元:
5.1 定位销应二维可调,定位销带定位面的应三维可调; 5.2. 定位夹紧块在定位夹紧方向一维调节; 5.3. 尽可能采用标准支承、定位销、连接块、过渡块和限位块,做成易换、易调整、易维修; 6、 材料表面及热处理: 6.1定位块:一般采用16mm厚的钢板,特殊部位采用19mm厚的钢板,材料采用45钢,调质T235 和发黑处理; 6.2定位销:40Cr钢,表面氧化处理,淬火 HRC55-60 ; 6.3 支承座:采用铸钢支承座,为本公司标准支撑座。 7、夹紧方式: 7.1.采用气缸自动夹紧或嘉手的手动夹钳夹紧; 8、 铭牌及标牌: 8.1. 设备设有本公司铭牌及设备标牌; 8.2. 铭牌固定上底板上。铭牌上标明夹具名称、夹具图号、使用车型、验收日期、制造商名称等 , 使用厚度为1㎜的铝板制做; 9、油漆: 9.1 生产线工装夹具均喷涂磁漆(颜色由买主规定),定位面及定位销要求发黑处理,夹具基准 面 要求防锈处理; 9.2 用颜色区分固定零件和运动零件; 9.3 外购件、标准件、非金属材料、铝件等为本色,不油漆; 9.4 所有的表面氧化零件均不油漆。
焊接夹具设计规范

焊接夹具设计规范焊接夹具设计规范一、目的:规范工程师设计工作,标准化焊接夹具制造工艺。
二、适用范围:适用于本公司所有焊接夹具设计。
三、资料要求:首件打样需提供详细资料.对于焊接夹具需提供GERBER 、实板及要求.对于外厂加工而本厂返修则需提供Gerber及具体数据要求.四,设计要求:1.焊接工装夹具的设计原则:实用性原则、经济性原则、可靠性原则、艺术性原则。
总之针对PCB焊接夹具要求:操作方便,定位准确,简单实用.2。
焊接工装夹具的设计步骤与内容。
A、焊接工装夹具的设计步骤:①根据生产要求,确定实际要焊接元件的数量和位置。
②根据要焊接原件的插装方式初步确定焊接夹具的组装结构。
③根据每一个需要焊接的元件的实际情况,设计夹具的详细结构,如元件避位,元件定位等问题。
B、焊接结构装配方案的确定:总的要求是能够快速实现定位,拿取方便。
焊接夹具的结构大致分为以下两种:①翻转结构。
翻转结构一般用在被焊接元件是在PCB板在正面插装,然后翻转180°焊接的情况。
翻转结构的治具一般都带压盖。
②非翻转结构。
非翻转结构按样式的不同又可分为有压盖结构和无压盖结构。
有压盖结构是指被焊接元件在PCB板的正面插装,然后也在正面焊接,但是需要施加外力把被焊接元件固定在PCB板上的结构。
对被焊接元件施加力的作用的结构一般被称为压盖。
无压盖结构是指被焊接穿孔元件先安装在焊接夹具上,然后再把PCB板定位在焊接夹具上的结构。
此时PCB 上的穿孔刚好被穿孔元件的元件脚穿过。
C、夹具体设计1。
夹具设计的时候要注意,由于电路板上元件较多,不允许压到元件,所以要根据PCB板的实际情况避开元件,包括定位和压紧均是如此.2。
PCB板要放置平整,否则容易造成焊接元件不良,翘起等问题。
第1页。
焊接夹具课程设计说明书.
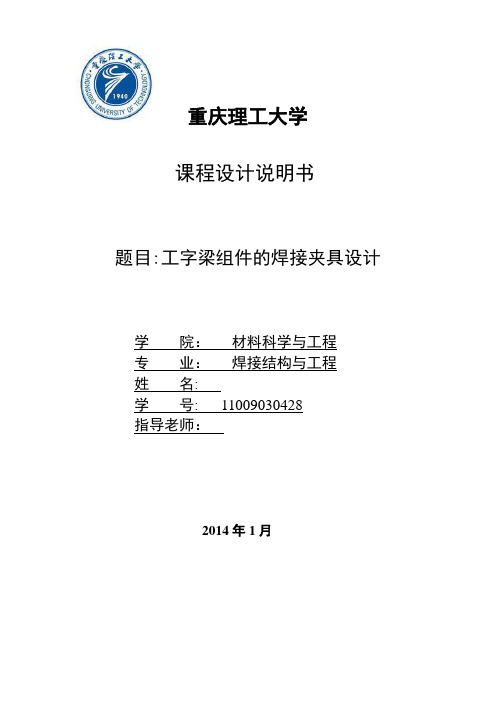
重庆理工大学课程设计说明书题目:工字梁组件的焊接夹具设计学院:材料科学与工程专业:焊接结构与工程姓名:学号: 11009030428指导老师:2014年1月序言 01。
对焊接工装夹具的设计要求 01.1焊接工装夹具的主要作用 (1)2。
焊接结构件的分析 (1)2。
1 焊接产品“钢梁组件”的重点技术要求分析: (1)2.2 采用合理的焊接顺序和方向 (2)3。
夹具设计方案的确定 (2)3。
1 在设计夹具体时应满足以下基本要求: (2)3.2 基准面的选择: (2)3.3 定位方式及元器件选择 (3)3.4 夹紧方式及元器件选择 (4)3。
5 装焊夹具结构 (5)3.6 装焊方案 (5)4。
主要零件设计的说明 (5)4。
1 夹具体 (5)4。
2 手动螺旋夹紧器 (5)4。
3 挡板 (6)4。
4 反变形装置 (6)4.5 垫板 (7)4。
6 销钉 (7)4.7 螺栓 (7)5. 装焊夹具使用说明 (7)5。
1 夹具的操作步骤: (7)5.2 夹具的结构特点: (7)5.3 夹具使用注意事项、保养及维护 (7)6。
本次课程设计总结、体会 (8)参考资料 (8)焊接工装夹具是将焊件准确定位并夹紧,用于装配和焊接的工艺装备.在焊接结构生产中,把用来装配进行定位焊的夹具称为装配夹具:而专门用来焊接焊件的夹具称为焊接夹具:把既用于装配又用于焊接的夹具称为装焊夹具.它们统称为焊接工装夹具。
1。
对焊接工装夹具的设计要求(1)焊接工装夹具应动作迅速,操作方便,操作位置应处在工人容易接近,最宜操的部位。
特别是手动夹具,其操作力不能过大,操作频率不能过高,操作高度应设在工人最容易用力的部位,当夹具处于夹紧装态时,应能自锁.(2)焊接工装夹具应有足够的装配焊接空间,不能影响焊接操作和焊工观察,不妨碍焊件的装卸,所有的定位原件和夹紧装置应与焊道保持适当距离或者布置在焊件的下方和侧面。
夹紧机构的执行元件应能够伸缩或转位.(3)夹紧可靠,刚性适当,夹紧时不破坏焊件的定位位置和几何形状,夹紧后不使焊件松动滑移,又不使焊件的拘束度过大,产生较大的应力。
焊装夹具的设计基本原则
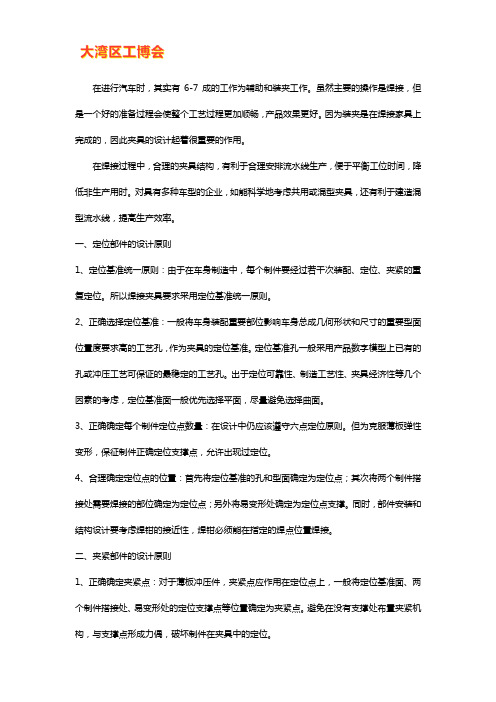
在进行汽车时,其实有6-7成的工作为辅助和装夹工作。
虽然主要的操作是焊接,但是一个好的准备过程会使整个工艺过程更加顺畅,产品效果更好。
因为装夹是在焊接家具上完成的,因此夹具的设计起着很重要的作用。
在焊接过程中,合理的夹具结构,有利于合理安排流水线生产,便于平衡工位时间,降低非生产用时。
对具有多种车型的企业,如能科学地考虑共用或混型夹具,还有利于建造混型流水线,提高生产效率。
一、定位部件的设计原则1、定位基准统一原则:由于在车身制造中,每个制件要经过若干次装配、定位、夹紧的重复定位。
所以焊接夹具要求采用定位基准统一原则。
2、正确选择定位基准:一般将车身装配重要部位影响车身总成几何形状和尺寸的重要型面位置度要求高的工艺孔,作为夹具的定位基准。
定位基准孔一般采用产品数字模型上已有的孔或冲压工艺可保证的最稳定的工艺孔。
出于定位可靠性、制造工艺性、夹具经济性等几个因素的考虑,定位基准面一般优先选择平面,尽量避免选择曲面。
3、正确确定每个制件定位点数量:在设计中仍应该遵守六点定位原则。
但为克服薄板弹性变形,保征制件正确定位支撑点,允许出现过定位。
4、合理确定定位点的位置:首先将定位基准的孔和型面确定为定位点;其次将两个制件搭接处需要焊接的部位确定为定位点;另外将易变形处确定为定位点支撑。
同时,部件安装和结构设计要考虑焊钳的接近性,焊钳必须能在指定的焊点位置焊接。
二、夹紧部件的设计原则1、正确确定夹紧点:对于薄板冲压件,夹紧点应作用在定位点上,一般将定位基准面、两个制件搭接处、易变形处的定位支撑点等位置确定为夹紧点。
避免在没有支撑处布置夹紧机构,与支撑点形成力偶,破坏制件在夹具中的定位。
2、正确确定夹紧力的作用方向:制件在夹具中的夹紧和定位是密切相关的。
夹紧力的作用方向就是向着定位支撑块。
通过定位支撑块的反作用力,使制件与定位块紧密接触。
3、正确决定夹紧力的大小:夹紧力大小应以能克服制件的弹性变形保证定位准确可靠为宜。
焊接制作标准及夹具设计

焊接夹具设计及制造标准总体技术要求:1、所有的夹具均采用气动控制压紧及车型转换方式(特殊规定可采用手动压紧器压紧或不用压紧)。
2、夹具应保证可靠的定位,防止变形,确保装配焊接质量和精度达到产品质量要求。
3、夹具工艺性能优良:各部件装配调整方便、人工焊接易于操作、产品取放方便、有足够的操作空间、操作方便快捷。
4、夹具上产品的高度应在700~800mm之间,对于四周焊接作业困难的应增加360°旋转转盘装置(特殊情况要求还需增加旋转定位锁紧装置)。
5、所有夹具须满足生产纲领的要求。
一、焊接件技术要求:1、焊缝高度不得<5mm、不允许有虚焊脱焊现象、重要部位须采用连续焊缝。
2、焊后清理焊渣、焊缝磨平。
所有部件在焊接后须退火消除应力再进行机加工。
-二、夹具底板1、夹具底板台面全部加工完成后厚度≮20mm,底板与槽钢等加强板料焊接前应校平,留有吊运点或叉车搬运位置,焊后应经退火处理和校平后再进行机加工等后续作业,加工完成后应对台面涂油处理。
2、加强筋规格选用标准(长方形的取最大值):(1)当夹具台面≤1400mm×1400mm时,底板的加强筋应采用10#以上槽钢;(2)当夹具台面>1400mm×1400mm时,底板的加强筋应采用16#以上槽钢;(3)当夹具台面>2000mm×2000mm时,底板的加强筋应采用20#以上槽钢;(4)底座周边的槽钢开口向外,中间加强筋用槽钢的间距不得>700mm.。
3、夹具台面的基准孔及网格坐标线:(1)基准孔:夹具台面上应留有两个坐标系的检测用基准孔,每个方向为两组,每组两个孔,孔径为φ10mm,孔距100mm.(在基准孔附近安装标牌或刻上钢字码,注明坐标数值)(2)网格坐标线:网格坐标线应与产品设计的坐标线对应。
深度及宽度均为0.5mm,间距为200mm.4、夹具台面的周边轮廓尽量与产品零件的轮廓相似,不得有突出的锐角,并尽量往里收,方便操作。
焊接工装夹具技术规范
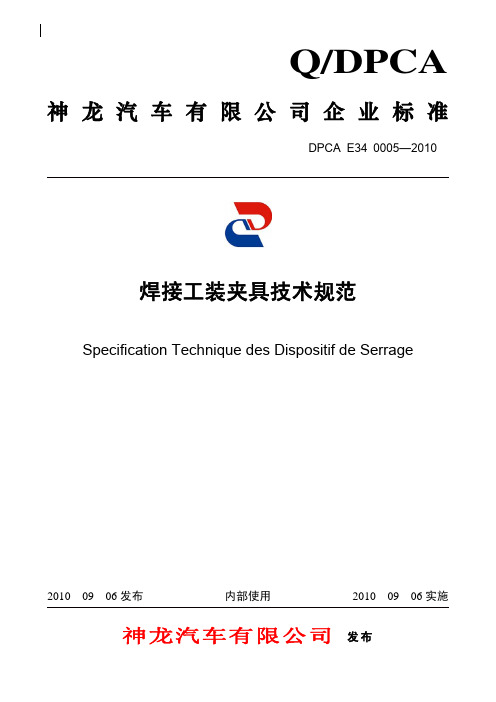
UWH1/STG
黄华 HUANG Hua
参与编制人员 Rédacteur participant
DEPA/DVHL/PPC UWH1/STG UWH1/STG
史江波 SHI Jiangbo 刘景洪 LIU Jinghong 黄华 HUANG Hua
审核会签人员 Vérificateur participant
OR:2010/09/06
I
内部使用
焊装夹具技术规范
DPCA E34 0005—2010
目
目 前
录
录 ...................................................................................................................................................II 言 ................................................................................................................................................. IV
Q/DPCA
神 龙 汽 Biblioteka 有 限 公 司 企 业 标 准DPCA E34 0005—2010
焊接工装夹具技术规范
Specification Technique des Dispositif de Serrage
2010—09—06 发布
内部使用
2010—09—06 实施 发布
神龙汽车有限公司
焊装夹具技术要求

附件:焊装夹具技术要求一、焊装夹具方案规划要求:1. 为了保证在产品加工过程中基准的统一,乙方在做夹具式样书过程中需按照甲方提供的RPS基准系统来确定夹具主定位基准(改造项目需延用原有基准,并保证统一),定位孔及销的主、副性必须与RPS一致;定位面可在RPS同一基准面上进行适当调整(50mm以内,不可切换定位型面;型面变化较大的位臵移动控制在20mm以内),且必须保证前后工序定位基准统一。
如乙方定位基准有其它方案的,会签时提出与甲方RPS的差异清单(详见附件一),经甲方书面同意后方可实施。
甲方提供夹具式样书的,完全按照夹具式样书进行夹具设计与商务报价。
2. 夹具定位方案设计时,需充分考虑件的强度与定位精度,必要时可将RPS中的菱形定位销改为圆形,以及可根据夹具的定位要求在甲方提供的RPS基础上增加定位面,以保证件的精确、稳定定位。
3. 夹具定位方案设计时,需充分考虑夹具的作业性、结构设计的合理性,对甲方提供的工艺文件中要求的夹具结构、工序的划分可根据实际情况提出合理建议,经甲方书面同意后可进行适当的修改。
如乙方未提出异意的,乙方必须保证所设计、制造出来夹具的作业性、定位性完全满足甲方生产要求。
4. 夹具定位方案设计时,需充分考虑每套夹具上增加钣件的防错、防漏装装臵(如左右件、类似件装错,同一个零件不同方位的装反,在总成件下方小零件漏装等),以有效避免错漏装。
5. 夹具在定位方案设计时,补焊夹具根据甲方的焊点布局进行夹具设计,满足焊点在夹具夹紧状态下能够焊接完成。
二、夹具材质及热处理要求1.夹具底座BASE要求采用Q235 A板材和槽钢或方钢焊接而成,槽钢或方钢规格要求如下:ArrayBASE底板的焊缝采用非连续焊缝(焊缝总长度不得小于制件总长的1/2),焊后经热处理退火消除应力(不允许采用机械消除应力)并喷砂处理,退火处理须提供残余应力检测报告。
2.规制块(基准块、压块)采用45#钢,表面淬火处理后硬度值达HRC40~45,表面应进行发黑处理。
焊接夹具设计

制造
1.底板与支座间的定位销孔采用数控镗床或铣床直接加工到位;
2.定位夹紧块的定位夹紧型面采用先切割或数控铣削;
3.支承座、过渡板、定位块的数控定位销孔;
其余非标零件尽可能采用普通加工;
底板的基面加工及刻线采用数控铣床加工。
NOKE标准制
造控制程序
装配
1.紧固螺栓采用内六角螺栓,公制标准件,2.在钢板厚度允许条件下,内六角头应沉入钢板表面。紧固需带弹簧垫圈;尽量从上方和侧面安装螺栓;
3.配有平衡块,转动轻松、灵活。
采用NOKE
标准
夹具
回转
1.采用人工转动;
2.配有分度定位机构和限位挡块;
3.采用标准转台
NOKE
标准
移动
单元
1.带有轴承及防尘装置;
2.设有限位块;
3.大型移动机构(重量大于40kg)采用直线轴承;
4.小型移动机构采用无油润滑轴承;
通用
结构
定位夹紧单元
1.定位销在位置度方向的二维调节;
2、尽可能水平、垂直排管。
3、使用标准汇流板。
4、采用快插接头和软管联接。
5、各类气管快换接头装有防撞盖板,进出气口采用不同颜色区分。
6、对CO2焊接区附近的气管采用硬管或软管加保护。
安全
1.有互锁要求的运动组之间设有气动逻辑互锁,以保护工人安全和工件不受到损坏。
ü典型结构:
焊接夹具标准夹紧单元:
焊接夹具标准定位单元
8.气缸:
焊接夹具设计时,气缸在压紧点处留有5~8mm运动行程余量,防止运动到端点。
9.其它部件:
其余部件设计要求结构简单可靠、维修方便,夹紧件,元器件的选择按选定标准设计。
焊装夹具设计技术规范
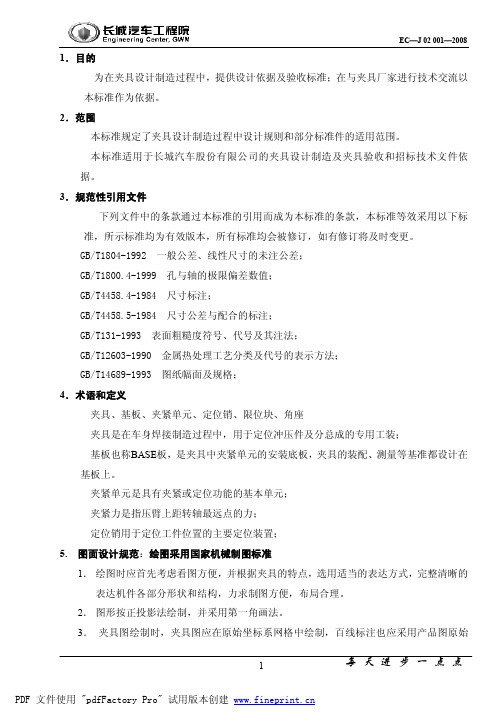
6.4.5 手动夹紧,气动打开的标准机构:
EC—J 02 001—2008
12
每天进步一点点
PDF 文件使用 "pdfFactory Pro" 试用版本创建
6.4.6 手动夹紧,气动打开机构气动原理图的构成:
EC—J 02 001—2008
1.此种类型气缸下部进气口处安装消声器;
2500≥A+B≥1800 采用 12#槽钢 (超大型) 基板厚度 C=25
A+B≥2500
采用 20#槽钢 (超大型) 基板厚度 C=30
注:A 或 B≥1400 时采用中间加强筋,且间距不大于 700mm。周边槽钢设计开口向外;
6.3.3 精度 l 基准面平面度0.1/1000; l 基准槽公差±0.05mm; l 栅格线位置相对基准的误差:0.15/1000; l 基准面粗糙度Ra1.6。
1.目的
EC—J 02 001—2008
为在夹具设计制造过程中,提供设计依据及验收标准;在与夹具厂家进行技术交流以
本标准作为依据。
2.范围
本标准规定了夹具设计制造过程中设计规则和部分标准件的适用范围。
本标准适用于长城汽车股份有限公司的夹具设计制造及夹具验收和招标技术文件依
据。
3.规范性引用文件
下列文件中的条款通过本标准的引用而成为本标准的条款,本标准等效采用以下标
准,所示标准均为有效版本,所有标准均会被修订,如有修订将及时变更。
GB/T1804-1992 一般公差、线性尺寸的未注公差;
GB/T1800.4-1999 孔与轴的极限偏差数值;
GB/T4458.4-1984 尺寸标注;
GB/T4458.5-1984 尺寸公差与配合的标注;
焊接夹具设计手册

一概念及名称1 . 基准点及车线的规定一般情况下汽车坐标系的原点规定为车前轮轴心线的中点。
TL或X――表示车长以车前轮为原点向车尾方向为正,向车头方向为负。
BL或Y――表示车宽以车的对称中心线为原点,面对车的行驶方向,向右为正,向左为负。
WL或Z――表示车高以车前轮为原点,向上为正,向下为负。
见图1-1;有时,汽车生产厂家也可自行规定基准点及坐标系的位置。
图1-1由于夹紧位置的需要而将夹紧单元旋转一定角度时,其车线的标注如图1-2,其中α≤45º图1-22.夹紧单元(POST)一个典型的夹紧单元通常包括L板、支板、夹紧臂、定位块、垫片、回转销、定位销、定位销连接板、到位止动块或限位块,、连接板、气缸等。
见图1-3图1-33.夹具一套完整的夹具一般包含若干夹紧单元(POST)、基板(BASE)、举升机构(LIFTER)甚至旋转机构。
根据操作方式可划分为手动夹具、气动夹具及液压夹具;根据控制方式可划分为气控夹具、电控夹具等。
见图1-4(手动夹具), 见图1-5(气动夹具)。
图1-4 图1-5二基板(Base板)Base板一般由槽钢与钢板焊接而成。
槽钢多采用10#、12#、14b#、16#、20#、25b# 等,钢板厚度多采用t=20mm或t=25mm(此为加工完成的厚度,选用毛料时,因考虑加工余量,相应的板厚取t=25mm或t=30mm)。
对于小夹具或滑台等亦可采用t=30~40mm的钢板焊接而成,而对于总拼夹具以及顶盖装焊夹具,其滑台及支架则可采用矩形方管与钢板焊接而成。
1.Base的最大外形尺寸对于Base的设计应充分考虑焊接及加工的工艺性,以及吊装、运输等方便性。
对于只加工顶底两面的普通Base而言,其长度暂不界定,但宽度不得大于2m,能够运输的最大宽度(非Base本身)为2.3m。
见图2-1图2-1而对于较宽大的Base,为了使其便于加工,往往将其划分为若干个Base,Base间则以支架相联接,此时该Base的单侧或双侧就需加工。
一汽大众焊装夹具设计制造规范本
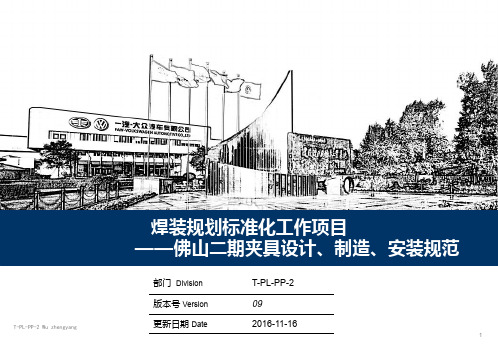
T-PL-PP-2 Wu zhengyang
第一次抽检:全部非标部件加工完成 后,一汽-大众对所有非标部件进行 10%的抽查,如果有不合格项,需要 供应商进行全部检查和重新加工,然 后再进行10%的抽查,直到抽查全部 合格
第二次取样:对非标零件所有使用材 料进行第二次取样,并送一汽大众实 验室检验
6
2.工装规范
2.1 设计规范
2.1.1设计规范概述
1)
1)压紧块:
材料:42CrMo4 淬火HRC60+/-2 表面
硬化 58+4 接触面要求深度>1.2mm
规格:特殊设计,按照零件形面设计接
触面。除零件接触面表面粗糙度为
Rz100。其他工装接触面为Rz25
2×螺栓:M8 DIN912 2×销:φ6
发运前100%检查:夹具组 装完成之后进行发运前检 查,根据检查清单由一汽 大众团队进行检查,100% 全检。不合格项全部整改
设备安装检查:会同使用 部门一起对于安装过程按 照检查清单进行检查,不 合格项全部整改
外购标准件:必须在官方 代理商处购买标准件,标 准件合同签订后需要把相 关信息告知一汽-大众(购 买数量,合同文本)
情况可以使用非标销套
T-PL-PP-2 Wu zhengyang 39D 20629/2
7
2.工装规范
2.1 设计规范
2.1.1设计规范概述
T-PL-PP-2 Wu zhengyang
1) 1)、2)夹紧、支撑块:
材料:42CrMo4 淬火HRC60+/-2 表面
硬化 58+4 接触面要求深度>1.2mm
支撑座与气缸联接紧固螺栓ISO 4762 固定销 ISO 8735 安装组件固定销 ISO 8375。 7、检测孔最少4个,<1700*1700 4个 1700*1700<Base<3200*1700 6个 >3200*1700 8个 检测孔之 间的间距需要保证≤1200。 8、 压臂夹紧点最多3个。 9、车身下部勾销按照14D 300168 MQBA1夹紧方案实施(青岛、佛山项目,其他项目参考其他标 准),勾销锁紧方向按照 14D 300168实施。 10、镜像复制夹具时,有左右区分的外购件不可镜像,右侧定位器要重新调入右侧外购件进行设计。 11、标准件用于安装固定面不允许再加工。 12、 气缸操作手柄只允许使用在手动夹具。 13、安装夹紧臂,按照夹紧臂距离转轴中心线 45mm考虑。 14、抓手与夹紧共用一个位置定位销定位时,使用伸缩缸
焊接夹具设计规范
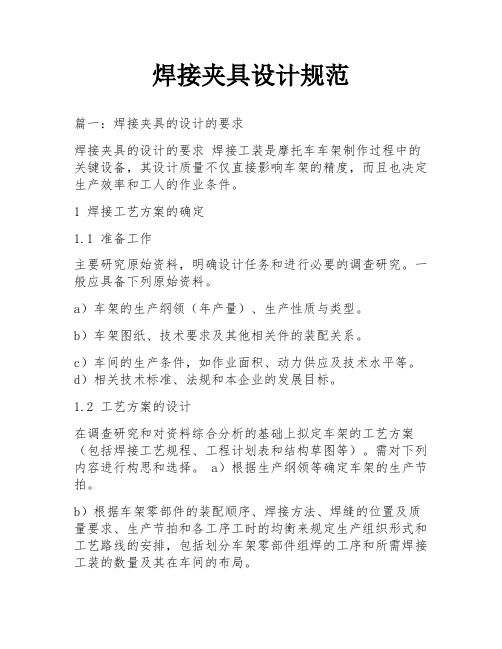
焊接夹具设计规范篇一:焊接夹具的设计的要求焊接夹具的设计的要求焊接工装是摩托车车架制作过程中的关键设备,其设计质量不仅直接影响车架的精度,而且也决定生产效率和工人的作业条件。
1 焊接工艺方案的确定1.1 准备工作主要研究原始资料,明确设计任务和进行必要的调查研究。
一般应具备下列原始资料。
a)车架的生产纲领(年产量)、生产性质与类型。
b)车架图纸、技术要求及其他相关件的装配关系。
c)车间的生产条件,如作业面积、动力供应及技术水平等。
d)相关技术标准、法规和本企业的发展目标。
1.2 工艺方案的设计在调查研究和对资料综合分析的基础上拟定车架的工艺方案(包括焊接工艺规程、工程计划表和结构草图等)。
需对下列内容进行构思和选择。
a)根据生产纲领等确定车架的生产节拍。
b)根据车架零部件的装配顺序、焊接方法、焊缝的位置及质量要求、生产节拍和各工序工时的均衡来规定生产组织形式和工艺路线的安排,包括划分车架零部件组焊的工序和所需焊接工装的数量及其在车间的布局。
c)实现某种功能拟采用的原理和相应的机构。
如定位与夹紧的方式和机构、焊件的翻转或回转等。
d)各工序所需工装的基本构成、车架零部件的定位、夹紧位置和总体布局,主要零部件的基本结构。
2 焊接工装的设计2.1 焊接工装的设计原则首先是焊接工装满足工艺技术要求,并应便于操作、安全、可靠及满足外观和经济上的要求。
2.2焊接工装的设计要求a)焊接工装应具有动作迅速、操作方便,操作位置应处在工人最容易接近、最易操作的部位。
特别是手动夹具,其操作力不能过大,操作高度应设在工人最易用力的部位,当夹具处于加紧状态时应能自锁,一般操作高度应控制在800~900mm。
b)焊接工装应有足够的装配、焊接空间,不能影响焊接操作和焊接观察,不妨碍焊件装卸。
所有定位元件和夹紧机构的执行元件应可调,即能伸缩和转位。
同时必须保证焊接机头的焊接可达性。
c)夹紧可靠,刚性适当。
加紧时不能破坏焊接件的定位位置和几何形状(如变形、凹陷、划伤等),且要保证夹紧后不能使焊件松动滑移,可以采取压头行程限位、加大压头接触面积或在压头上安装铜、铝、硬塑料衬垫等措施。
焊接夹具设计要点,注意事项
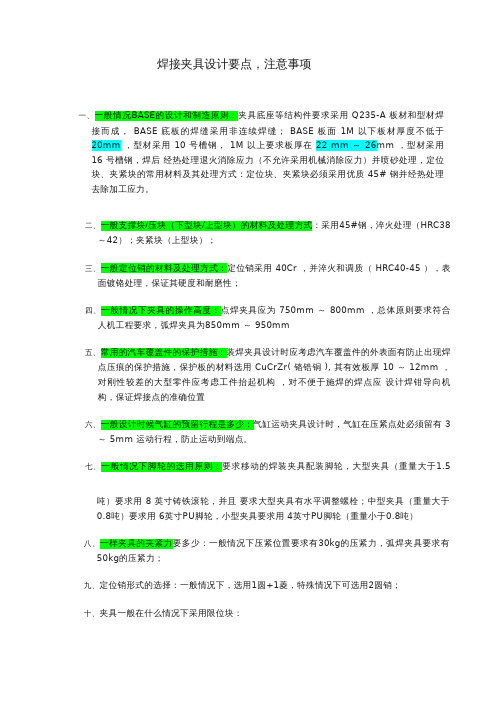
焊接夹具设计要点,注意事项一、一般情况BASE的设计和制造原则:夹具底座等结构件要求采用 Q235-A 板材和型材焊接而成, BASE 底板的焊缝采用非连续焊缝; BASE 板面 1M 以下板材厚度不低于20mm ,型材采用 10 号槽钢, 1M 以上要求板厚在 22 mm ~ 26mm ,型材采用16 号槽钢,焊后经热处理退火消除应力(不允许采用机械消除应力)并喷砂处理,定位块、夹紧块的常用材料及其处理方式:定位块、夹紧块必须采用优质 45# 钢并经热处理去除加工应力。
二、一般支撑块/压块(下型块/上型块)的材料及处理方式:采用45#钢,淬火处理(HRC38~42);夹紧块(上型块);三、一般定位销的材料及处理方式:定位销采用 40Cr ,并淬火和调质( HRC40-45 ),表面镀铬处理,保证其硬度和耐磨性;四、一般情况下夹具的操作高度:点焊夹具应为 750mm ~ 800mm ,总体原则要求符合人机工程要求,弧焊夹具为850mm ~ 950mm五、常用的汽车覆盖件的保护措施:装焊夹具设计时应考虑汽车覆盖件的外表面有防止出现焊点压痕的保护措施,保护板的材料选用 CuCrZr( 铬锆铜 ), 其有效板厚 10 ~ 12mm ,对刚性较差的大型零件应考虑工件抬起机构,对不便于施焊的焊点应设计焊钳导向机构,保证焊接点的准确位置六、一般设计时候气缸的预留行程是多少:气缸运动夹具设计时,气缸在压紧点处必须留有 3~ 5mm 运动行程,防止运动到端点。
七、一般情况下脚轮的选用原则:要求移动的焊装夹具配装脚轮,大型夹具(重量大于1.5吨)要求用 8 英寸铸铁滚轮,并且要求大型夹具有水平调整螺栓;中型夹具(重量大于0.8吨)要求用 6英寸PU脚轮,小型夹具要求用 4英寸PU脚轮(重量小于0.8吨)八、一样夹具的夹紧力要多少:一般情况下压紧位置要求有30kg的压紧力,弧焊夹具要求有50kg的压紧力;九、定位销形式的选择:一般情况下,选用1圆+1菱,特殊情况下可选用2圆销;十、夹具一般在什么情况下采用限位块:1、夹持臂上有基准销时。
焊接夹具设计及制作标准

南京依维柯汽车有限公司第二车身厂焊接夹具设计制作标准编制:余水2010年3月22日焊接夹具设计及制造标准总体技术要求:1、所有的夹具均采用气动控制压紧及车型转换方式(特殊规定可采用手动压紧器压紧或不用压紧)。
2、夹具应保证可靠的定位,防止变形,确保装配焊接质量和精度达到产品质量要求。
3、夹具工艺性能优良:各部件装配调整方便、人工焊接易于操作、产品取放方便、有足够的操作空间、操作方便快捷。
4、夹具上产品的高度应在700~800mm之间,对于四周焊接作业困难的应增加360°旋转转盘装置(特殊情况要求还需增加旋转定位锁紧装置)。
5、所有夹具须满足生产纲领的要求。
一、焊接件技术要求:1、焊缝高度不得<5mm、不允许有虚焊脱焊现象、重要部位须采用连续焊缝。
2、焊后清理焊渣、焊缝磨平。
所有部件在焊接后须退火消除应力再进行机加工。
-二、夹具底板1、夹具底板台面全部加工完成后厚度≮20mm,底板与槽钢等加强板料焊接前应校平,留有吊运点或叉车搬运位置,焊后应经退火处理和校平后再进行机加工等后续作业,加工完成后应对台面涂油处理。
2、加强筋规格选用标准(长方形的取最大值):(1)当夹具台面≤1400mm×1400mm时,底板的加强筋应采用10#以上槽钢;(2)当夹具台面>1400mm×1400mm时,底板的加强筋应采用16#以上槽钢;(3)当夹具台面>2000mm×2000mm时,底板的加强筋应采用20#以上槽钢;(4)底座周边的槽钢开口向外,中间加强筋用槽钢的间距不得>700mm.。
3、夹具台面的基准孔及网格坐标线:(1)基准孔:夹具台面上应留有两个坐标系的检测用基准孔,每个方向为两组,每组两个孔,孔径为φ10mm,孔距100mm.(在基准孔附近安装标牌或刻上钢字码,注明坐标数值)(2)网格坐标线:网格坐标线应与产品设计的坐标线对应。
深度及宽度均为0.5mm,间距为200mm.4、夹具台面的周边轮廓尽量与产品零件的轮廓相似,不得有突出的锐角,并尽量往里收,方便操作。
夹具标准

湖北国瑞智能装备有限公司
举升机构;在100mm以上时,采用一体式举升机构,上升端、下降端碰到限位器都应停止。对不 便于施焊的焊点应设计焊钳导向机构,保证焊接点的准确位置,焊钳导向块的材料选用MC尼龙。 外覆盖件的支撑采用聚氨脂(邵氏硬度60—80)。 1. 29 底座的网格线和基准孔:网格线应与产品设计的坐标线对应。网格线的深度、宽度均为 0.3mm~0.4 mm,其间距为200mm。网格线和基准孔都应以坐标标识出来(都应标出三维坐标 值)。为了便于测量,夹具基准孔在平台上的位置不应与其它装置干涉,夹具基准孔的位置、数 量:在平台上的3处以上, 间距1200mm以内,具体位置、数量在图纸会签时确定。 1. 30夹具基准孔的尺寸、精度 1. 30.1夹具基准孔的直径以及公差为Ф10mmH7 夹具基准孔间的相对位置公差± 0.02mm
增压缸形式
此机构装置用于强度高、易变形的部位,同时具有校正零件的作用。
夹具要求及夹具标准
湖北国瑞智能装备有限公司
2-1.夹具标准
主要定位结构说明:
一般夹紧单元
用于一般的定位和夹紧, 定位块和压头可通过调整垫 片进行调整(3mm),结构 简单、可靠,在夹具应用较 多。
夹具要求及夹具标准
湖北国瑞智能装备有限公司
湖北国瑞智能装备有限公司
焊接夹具要求及夹具标准
夹具要求及夹具标准
湖北国瑞智能装备有限公司
目录
一、夹具要求 二、夹具标准 三、国瑞标准件目录
夹具要求及夹具标准
湖北国瑞智能装备有限公司
一、夹具要求
夹具要求及夹具标准
湖北国瑞智能装备有限公司
1、夹具设计基本要求 1. 1 焊装夹具应满足产品结构、工艺和生产纲领的要求,夹具应有合理的定位夹紧机构和支撑装 置,保证组件定位可靠,焊接质量稳定。 1. 2 夹具地板应涂防飞溅漆,夹具底座板上平面应加工有基准线和基准孔。 1. 3 焊装夹具的定位应与产品图一致,焊装夹具图的各定位基准应有三坐标数据表。 1. 4 焊装夹具的结构设计应参照焊钳标准,根据结构要求也可采用非标焊钳,但必须由招标方认 可,非标焊钳图纸由投标方提供。 1. 5 夹具应有完善的装配定位基准,便于夹具制造、装配、调试和维修。 1. 6 夹具设计应充分考虑操作方便和安全可靠、维护修理方便,应保证焊接装卸方便,使焊接件 处于最佳焊接位置,夹具设计在保证工艺要求和刚度的情况下结构应简单合理。 1. 7 夹具图应有焊装夹具总成图、焊装夹具分总成图、焊装夹具零件图、焊装夹具明细表、焊装 夹具基础图、焊装夹具三维图纸(UG或CATIA格式)。应有三个方向的坐标线(间距为100mm ,),夹具设计图应反映出各定位尺寸、升降装置位置和尺寸以及支撑板型面尺寸。 1. 8 夹具设计图纸制图采用中国制图标准或ISO制图标准,文字采用中文简化字;规格和单位采 用中国工业标准或ISO国际标准。夹具图纸图面应符合招标方要求,夹具总图应有详细的夹具零 件清单(或单独编制)、气动原理图、电控原理图、夹具安装图和三维图纸(电子版)等,夹具 设计图必须完整、正确。
二.对焊接工装夹具的设计要求
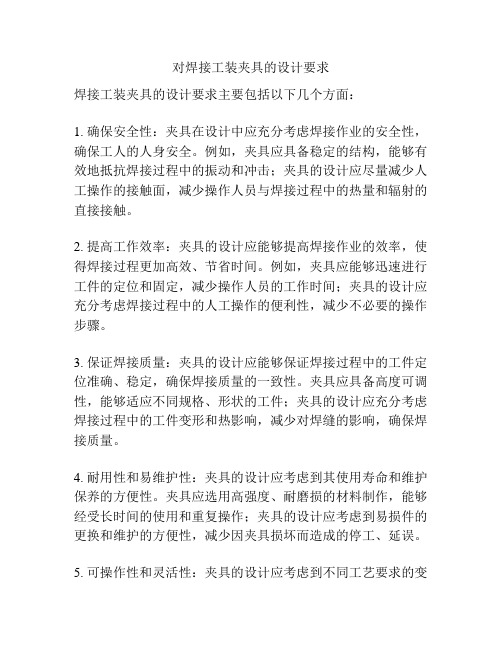
对焊接工装夹具的设计要求
焊接工装夹具的设计要求主要包括以下几个方面:
1. 确保安全性:夹具在设计中应充分考虑焊接作业的安全性,确保工人的人身安全。
例如,夹具应具备稳定的结构,能够有效地抵抗焊接过程中的振动和冲击;夹具的设计应尽量减少人工操作的接触面,减少操作人员与焊接过程中的热量和辐射的直接接触。
2. 提高工作效率:夹具的设计应能够提高焊接作业的效率,使得焊接过程更加高效、节省时间。
例如,夹具应能够迅速进行工件的定位和固定,减少操作人员的工作时间;夹具的设计应充分考虑焊接过程中的人工操作的便利性,减少不必要的操作步骤。
3. 保证焊接质量:夹具的设计应能够保证焊接过程中的工件定位准确、稳定,确保焊接质量的一致性。
夹具应具备高度可调性,能够适应不同规格、形状的工件;夹具的设计应充分考虑焊接过程中的工件变形和热影响,减少对焊缝的影响,确保焊接质量。
4. 耐用性和易维护性:夹具的设计应考虑到其使用寿命和维护保养的方便性。
夹具应选用高强度、耐磨损的材料制作,能够经受长时间的使用和重复操作;夹具的设计应考虑到易损件的更换和维护的方便性,减少因夹具损坏而造成的停工、延误。
5. 可操作性和灵活性:夹具的设计应考虑到不同工艺要求的变
化和工件形状、尺寸的差异。
夹具应具有较大的调节范围和可调性,以适应不同工件的变化需求;夹具的设计应具备一定的灵活性,能够适应工艺流程的变更和工艺参数的调整。
综上所述,焊接工装夹具的设计要求应综合考虑安全性、效率性、质量性、耐用性和灵活性等因素,以实现焊接过程中的高效、安全、稳定的工作。
焊装夹具知识点总结
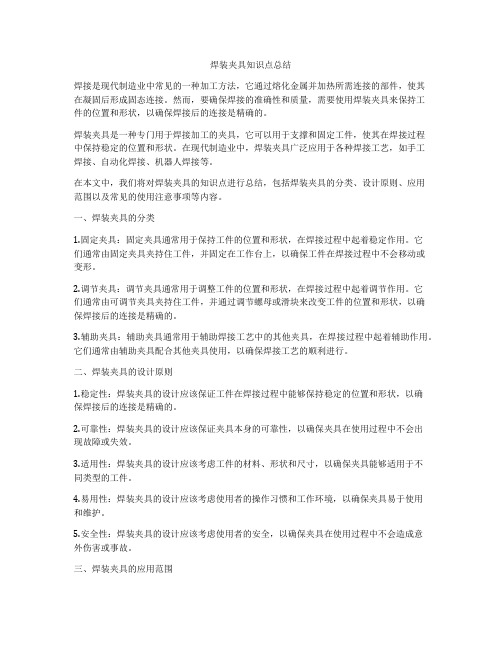
焊装夹具知识点总结焊接是现代制造业中常见的一种加工方法,它通过熔化金属并加热所需连接的部件,使其在凝固后形成固态连接。
然而,要确保焊接的准确性和质量,需要使用焊装夹具来保持工件的位置和形状,以确保焊接后的连接是精确的。
焊装夹具是一种专门用于焊接加工的夹具,它可以用于支撑和固定工件,使其在焊接过程中保持稳定的位置和形状。
在现代制造业中,焊装夹具广泛应用于各种焊接工艺,如手工焊接、自动化焊接、机器人焊接等。
在本文中,我们将对焊装夹具的知识点进行总结,包括焊装夹具的分类、设计原则、应用范围以及常见的使用注意事项等内容。
一、焊装夹具的分类1.固定夹具:固定夹具通常用于保持工件的位置和形状,在焊接过程中起着稳定作用。
它们通常由固定夹具夹持住工件,并固定在工作台上,以确保工件在焊接过程中不会移动或变形。
2.调节夹具:调节夹具通常用于调整工件的位置和形状,在焊接过程中起着调节作用。
它们通常由可调节夹具夹持住工件,并通过调节螺母或滑块来改变工件的位置和形状,以确保焊接后的连接是精确的。
3.辅助夹具:辅助夹具通常用于辅助焊接工艺中的其他夹具,在焊接过程中起着辅助作用。
它们通常由辅助夹具配合其他夹具使用,以确保焊接工艺的顺利进行。
二、焊装夹具的设计原则1.稳定性:焊装夹具的设计应该保证工件在焊接过程中能够保持稳定的位置和形状,以确保焊接后的连接是精确的。
2.可靠性:焊装夹具的设计应该保证夹具本身的可靠性,以确保夹具在使用过程中不会出现故障或失效。
3.适用性:焊装夹具的设计应该考虑工件的材料、形状和尺寸,以确保夹具能够适用于不同类型的工件。
4.易用性:焊装夹具的设计应该考虑使用者的操作习惯和工作环境,以确保夹具易于使用和维护。
5.安全性:焊装夹具的设计应该考虑使用者的安全,以确保夹具在使用过程中不会造成意外伤害或事故。
三、焊装夹具的应用范围1.汽车制造:在汽车制造过程中,焊装夹具广泛应用于车身焊接、底盘焊接、零部件焊接等方面,以确保汽车的结构和质量。
- 1、下载文档前请自行甄别文档内容的完整性,平台不提供额外的编辑、内容补充、找答案等附加服务。
- 2、"仅部分预览"的文档,不可在线预览部分如存在完整性等问题,可反馈申请退款(可完整预览的文档不适用该条件!)。
- 3、如文档侵犯您的权益,请联系客服反馈,我们会尽快为您处理(人工客服工作时间:9:00-18:30)。
装焊夹具设计标准规范序言装焊夹具是在汽车车身的工序组装过程中,保证各相关零部件快速准确定位;在工序焊接过程中,保持各件正确的相对位置,保证足够的焊接操作空间;在完成工序焊接工作之后,保证工序成品能方便、快速地取出;进而确保车身焊接制造的几何精度,提高生产效率所必需的工艺装备。
随着汽车工业发展的日新月异,装焊夹具的设计和制造水平也在不断地提高,并且从一个方面成为体现车身制造工艺水平的重要标志。
制定本标准的目的在于为本公司内部确立一个装焊夹具设计、制造方面的大略原则。
在接受客户定单时,对于涉及相关技术性的条目,如果客户无特殊要求,则依本标准的原则进行设计和制造;如果客户另有标准,则依客户提出的要求进行。
1.装焊夹具设计、制造工作流程工艺分析并根据客户要求编制仕样书(如果客户已有仕样书,此过程可以省却)→仕样书会签→投入总成图设计(3D)→总成图会签→零、部件设计出图(2D)→投入机加工制造→装配→机能验证→检测→最终定位装配→保护→喷(涂)漆→客户初验收→包装出厂→现场调试、交货(客户终验收)2.设计工作内容2.1 完成夹具机械部分的设计,其中包括:2.1.1完成夹具机械结构及零部件设计。
2.1.2根据工序焊点位置和焊钳样式,在夹具图中进行焊钳动作模拟,并且对干涉部位进行避让修正。
2.2完成气动部分设计,其中包括:2.2.1完成气动原理图设计,列出动作程序时间表。
2.2.2在原理图的明细表中,列出所需气动元件的名称、规格型号、数量及制造或代理厂商。
2.3编制明细表,其中包括:2.3.1自制或外协加工件明细表2.3.2标准件、外购件明细表2.4图纸格式及表述内容2.4.1图纸格式(另附图说明)2.4.2总成图和分总成图均采用总成图标题栏的格式,零件图采用零件图的格式,气动原理图采用总成图的格式。
2.4.3需要在总成图中表述的内容为:工装的总体布局;工装的总体功能及各分总成之间动作配合关系;工装的总体轮廓尺寸及大致装配要求;工装总体的包装、起重、运输要求;对于左右对称制造的工装,需要在总成图中予以说明。
2.4.4需要在分总成图中表述的内容为:本分总成具体的装配位置及精度要求;本分总成所含各零件的名称、数量、相互位置关系及装配技术要求;本分总成所含标准件的名称、数量、规格型号要求。
2.4.5需要在零件图中表述的内容为:零件的结构尺寸及加工精度、表面粗糙度要求;零件的热处理要求。
3.仕样书的编制3.1仕样书的格式(另附图说明)3.2仕样书内容的填写3.2.1产品及零部件的名称和图号,按客户提供的名称和图号填写。
3.2.2是指仕样书本身的编号,一般按照项目分类后各具体项目所含内容的数量按顺序编写。
编号内容分为三段:(□□□_□□□_□□□)第一段为项目代号,第二段为工装类型代号,第三段为顺序号。
3.2.3布局方案采用简图加文字说明的形式,必要时对各局部的具体形式在附页的图表中作进一步说明。
3.2.4在操作过程一栏中,要简要地将工序组成件、选用的焊钳形式(型号)列出,并且对操作顺序简要说明。
3.2.5仕样书的附页,主要是对布局方案中各局部点的具体形式用简图作进一步说明,其中包括采用的定位、压紧及调整方式等。
4.基准的确立4.1坐标系的确立4.1.1夹具设计的坐标系原则上与车身设计坐标系一致。
以汽车前轴中点为坐标原点,向上为Z坐标正向,向后为X坐标正向,面向前方右侧为Y坐标正向;反向为负。
4.1.2当需要在某些特殊部位(如前柱上部、侧围后部、前门上部等)布置夹紧点时,为了方便尺寸标注,需要把局部坐标旋转变换。
原则上所采用的旋转基点(轴),应取在车身设计坐标50线倍数的交点上。
4.2设计及制造基准4.2.1原则上设计基准与制造及装配基准应该一致,并且以车身设计坐标为原始基准。
4.2.2对于夹具的基板,其上表面为基准面,并且与车身坐标一个方向上的百线重合。
沿基板表面是车身坐标的另外两个方向,应加工出两道互相垂直的基准槽(也可以根据用户要求做成基准孔),并用钢印予以标记。
基准槽和基准孔形式如图所示,必要时还可以在基板表面纵横两个方向上打刻间隔200毫米的坐标网格线,作为辅助测量基准。
基板上的三维坐标基准即是整套夹具的基准。
4.2.3对于定位支座,高度方向的基准是支座底面,其余两个方向的基准分别是支座对称中心和底面安装基准销孔中心线。
如图所示4.2.4对于定位支承板,高度方向的基准是基准销孔中心线,其余两个方向的基准分别是安装孔对称中心和与定位支座的结合面。
4.2.5定位销座的基准是其与调整垫片的结合面。
4.2.6定位块的基准是安装底面。
5.定位销的设计5.1定位销的基本结构定位销的结构要素分为三部分:即导入部分、工作部分、装配部分。
5.1.1为了便于定位销与工件定位孔之间的导入,通常将定位销的导入部分设计成锥体,锥角根据不同使用情况分为30°和60°。
5.1.2定位销工作部分的公称直径一般为工件定位孔直径-0.2 毫米。
记做:d=D-0.2。
5.1.3定位销的公差定位销的公差设定为:dh85.1.4定位销的伸出长度定位销伸出定位孔的长度一般定在5mm。
5.1.5定位销的紧固方式a.外螺纹-螺母紧固型b.内螺纹-螺钉紧固型c.紧定螺钉紧固型5.1.6定位销的装配精度定位销的装配配合通常取为H7/f75.2定位销的材料及热处理要求5.2.1定位销的材料为45钢5.2.2定位销的淬火硬度为HRC535.2.3定位销最终加工完成后要求煮黑处理5.3定位销的布置和调整5.3.1原则上对于一个工件,其主、辅定位销的轴线要求平行;不同工件的定位销之间,其轴线也要求尽量平行。
遇特殊情况,则需要采用可以滑动的活销处理。
5.3.2一般情况下,将定位销座在其定位平面上设计成二维可调的结构。
每一个方向上的调整量为3毫米。
5.3.3定位销座的调整通过调整垫片来实现,垫片的厚度分为:0.3毫米,0.5毫米,1毫米等规格,垫片表面要求光洁、平整、无毛刺。
5.4滑动定位销结构在一些特殊情况下,为了便于定位销的退出和工件的装卸,需要将定位销与销座之间的结构设计成滑动的。
其中有:5.4.1手动滑槽式:如图所示,定位销与芯轴装配在一起,销座的芯轴套上铣有导槽,拨动与芯轴相连的手柄,将芯轴推至上位后转动一个角度将手柄卡住,定位销即可保持在工作位置上。
这种结构占用空间小,常用于局部空间受到限制的场合。
一般情况下,手柄可以用螺钉代用。
5.4.2连杆推拉式:如图所示,将定位销直接固定在推拉式快速夹紧器的芯轴,搬动夹紧器的手柄,即可实现定位销的轴向位置变换。
操作快捷、方便。
5.4.3气动定位销:将定位销与气缸杆连接起来,靠气缸活塞杆的动作实现定位销的轴向位置变换。
这种结构的优势在于:a.可以实现远程控制b.可以实现群体控制因此,这种结构形式最适用于:a.手动不易达到的位置b.需要滑动定位销数量较多的情况5.5摆动定位销在一般的夹具设计中,定位销的应用情况都是定位销相对固定,工件置于定位销之上。
但在有些场合,则需要先粗略地使工件就位,然后再用定位销精确定位,定位销置于工件之上。
为了能方便地实现工件的装夹和取出,常常把定位销座设计成摆动式的,最常见的情况是,把定位销直接装在压紧臂上。
5.6定位销设计中需注意的问题5.6.1由于需要定位的零件大多数都是薄板件,为避免干涉,在设计定位销的工作位置时,要使定位销的根部与定位孔边保留一段距离。
如图示:5.6.2对于大直径定位销,当Φd>32时,可以把销的柱面取平一小部分,以利于定位销进、出定位孔。
如图示:5.6.3对于摆动定位销,其摆动中心原则上应该与定位孔处于同一平面内,以避免干涉。
5.6.4在定位销倾斜使用的情况下,尺寸标注不要标在空间点上。
如图示:5.6.5在滑动销被水平放置或接近水平放置时,要注意加防护盖,以避免焊接飞溅伤及导向部位。
当滑动销垂直使用时,导向轴端面要高出导向套端面,避免飞溅和垃圾进入导向面之间。
6.定位支座的设计6.1定位支座的基本结构及材料通常定位支座采用焊接结构,根据采用材料的形式不同,又大略分为纯钢板式结构和钢板-型材混合式结构两种类型。
6.1.1纯钢板式结构这种结构一般由立面板、底面板、加强筋板三个基本单元组合焊接而成,材料为A3板。
立面板和底面板加工后的板厚为14毫米,加强筋板厚度为8毫米。
这种支座的底面部位一般直接与基板连接,也可以安装在辅助支座上,立面部位安装定位支承板,是夹具定位夹紧系统中的关键零件。
6.1.2钢板-型材混合式结构这种结构一般由底面板、支承部分、上连接部分三个基本单元组合焊接而成。
其中底面板和上连接部分的材料采用A3板;支承部分采用型材,根据不同的用途,可以有角钢、槽钢、圆管、方管等多种选择。
这种结构形式可以在多种用途的支座中被采用,可以用作单纯的定位销座,也可以用做辅助支座。
6 .1 .3 铸造结构6.2定位支座的相关技术要求6.2.1定位支座的加工过程要求定位支座的加工过程要遵循:下料→毛坯焊接→时效处理→清理焊渣→喷防锈底漆→机械加工的步骤进行。
6.2.2定位支座的形状及位置精度要求定位支座各加工表面之间要有形位公差要求,其中互相垂直的表面,垂直度误差为0.05毫米;互相平行的表面,平行度误差为0.05毫米;各表面本身的平面度误差为0.05毫米。
6.2.3定位支座加工面之间的尺寸精度对于具有互相垂直加工表面的支座,其中一个面上的基准销孔中心与另一个表面之间的尺寸公差为±0.05毫米;对于具有互相平行加工表面的支座,两个表面之间的尺寸公差为±0.05毫米;两个基准销孔之间的尺寸公差为±0.02毫米。
6.2.4定位支座的表面粗糙度要求原则上,与焊口接触的表面均被视为非加工表面,粗糙度为;作为安装基准的表面,粗糙度为;其它只与轮廓尺寸相关的表面,粗糙度为。
7.定位支承板的设计7.1定位支承板的结构要素及材料定位支承板的基本结构要素为:a.保持本身安装位置的安装基准面、基准孔b.保持下一级定位单元位置的安装基准面、基准孔定位支承板的设计,主要是围绕着确立两组要素之间的相互位置这个中心点来进行。
定位支承板的材料为A3板。
7.2定位支承板的相关技术要求7.2.1定位支承板的形状及位置精度要求分别属于两组要素的加工表面,当两面平行时,平行度误差为0.05毫米;当两面垂直时,垂直度误差为0.05毫米;表面本身的平面度误差为0.05毫米。
7.2.2定位支承板的尺寸精度要求分别属于两组要素的安装基准面、基准孔之间的尺寸公差为±0.05毫米。
7.2.3定位支承板的表面粗糙度要求用作安装基准的表面(包括基准销孔),粗糙度为;其它只与轮廓尺寸相关的表面(包括螺栓过孔),粗糙度为。