04炉壳壳体结构用钢板
铸造车间各熔炼用炉的介绍
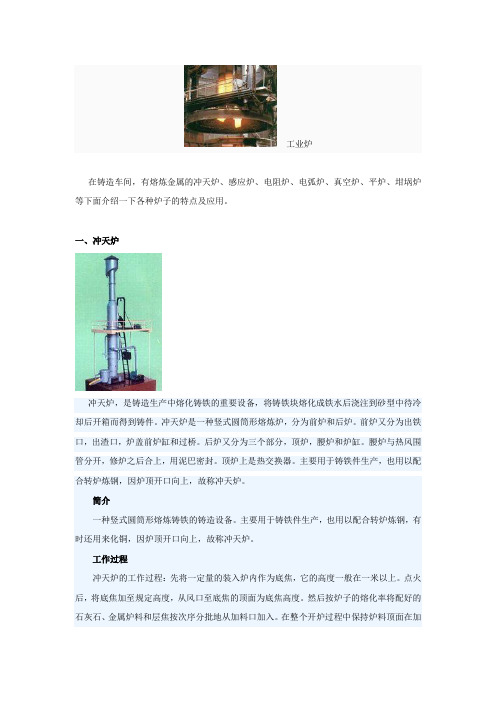
工业炉在铸造车间,有熔炼金属的冲天炉、感应炉、电阻炉、电弧炉、真空炉、平炉、坩埚炉等下面介绍一下各种炉子的特点及应用。
一、冲天炉冲天炉,是铸造生产中熔化铸铁的重要设备,将铸铁块熔化成铁水后浇注到砂型中待冷却后开箱而得到铸件。
冲天炉是一种竖式圆筒形熔炼炉,分为前炉和后炉。
前炉又分为出铁口,出渣口,炉盖前炉缸和过桥。
后炉又分为三个部分,顶炉,腰炉和炉缸。
腰炉与热风围管分开,修炉之后合上,用泥巴密封。
顶炉上是热交换器。
主要用于铸铁件生产,也用以配合转炉炼钢,因炉顶开口向上,故称冲天炉。
简介一种竖式圆筒形熔炼铸铁的铸造设备。
主要用于铸铁件生产,也用以配合转炉炼钢,有时还用来化铜,因炉顶开口向上,故称冲天炉。
工作过程冲天炉的工作过程:先将一定量的装入炉内作为底焦,它的高度一般在一米以上。
点火后,将底焦加至规定高度,从风口至底焦的顶面为底焦高度。
然后按炉子的熔化率将配好的石灰石、金属炉料和层焦按次序分批地从加料口加入。
在整个开炉过程中保持炉料顶面在加料口下沿。
经风口鼓入炉内的空气同底焦发生燃烧反应,生成的高温炉气向上流动,对炉料加热,并使底焦顶面上的第一批金属炉料熔化。
熔化后的铁滴在下落到炉缸的过程中,被高温炉气和炽热的焦炭进一步加热,这一过程称为过热。
随着底焦的烧失和金属炉料的熔化,料层逐渐下降。
每批炉料熔化后,燃料由外加的层焦补充,使底焦高度基本上保持不变,整个熔化过程连续进行。
应用领域:冲天炉主要应用于钢铁、冶金、矿山等行业。
炉料中的石灰石在高温炉气的作用下分解成石灰和二氧化碳。
石灰是碱性氧化物,它能和焦炭中的灰分和炉料中的杂质、金属氧化物等酸性物质结合成熔点较低的炉渣。
熔化的炉渣也下落到炉缸,并浮在铁水上。
在冲天炉内,同时进行着底焦的燃烧、热量的传递和冶金反应 3个重要过程。
根据物理、化学反应的不同,冲天炉以燃烧区为核心,自上而下分为:预热带、熔化带、还原带、氧化带和炉缸等 5个区域。
由于炉气、焦炭和炉渣的作用,熔化后的金属成分也发生一定的变化。
高炉炉壳制作方案
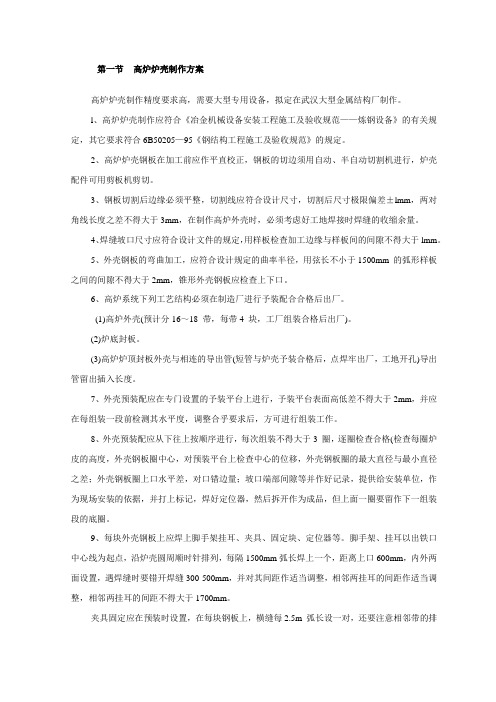
第一节高炉炉壳制作方案高炉炉壳制作精度要求高,需要大型专用设备,拟定在武汉大型金属结构厂制作。
l、高炉炉壳制作应符合《冶金机械设备安装工程施工及验收规范——炼钢设备》的有关规定,其它要求符合6B50205—95《钢结构工程施工及验收规范》的规定。
2、高炉炉壳钢板在加工前应作平直校正,钢板的切边须用自动、半自动切割机进行,炉壳配件可用剪板机剪切。
3、钢板切割后边缘必须平整,切割线应符合设计尺寸,切割后尺寸极限偏差±lmm,两对角线长度之差不得大于3mm,在制作高炉外壳时,必须考虑好工地焊接时焊缝的收缩余量。
4、焊缝坡口尺寸应符合设计文件的规定,用样板检查加工边缘与样板间的间隙不得大于lmm。
5、外壳钢板的弯曲加工,应符合设计规定的曲率半径,用弦长不小于1500mm 的弧形样板之间的间隙不得大于2mm,锥形外壳钢板应检查上下口。
6、高炉系统下列工艺结构必须在制造厂进行予装配合合格后出厂。
(1)高炉外壳(预计分16~18 带,每带4 块,工厂组装合格后出厂)。
(2)炉底封板。
(3)高炉炉顶封板外壳与相连的导出管(短管与炉壳予装合格后,点焊牢出厂,工地开孔)导出管留出插入长度。
7、外壳预装配应在专门设置的予装平台上进行,予装平台表面高低差不得大于2mm,并应在每组装一段前检测其水平度,调整合乎要求后,方可进行组装工作。
8、外壳预装配应从下往上按顺序进行,每次组装不得大于3 圈,逐圈检查合格(检查每圈炉皮的高度,外壳钢板圈中心,对预装平台上检查中心的位移,外壳钢板圈的最大直径与最小直径之差;外壳钢板圈上口水平差,对口错边量;坡口端部间隙等并作好记录,提供给安装单位,作为现场安装的依据,并打上标记,焊好定位器,然后拆开作为成品,但上面一圈要留作下一组装段的底圈。
9、每块外壳钢板上应焊上脚手架挂耳、夹具、固定块、定位器等。
脚手架、挂耳以出铁口中心线为起点,沿炉壳圆周顺时针排列,每隔1500mm弧长焊上一个,距离上口600mm,内外两面设置,遇焊缝时要错开焊缝300-500mm,并对其间距作适当调整,相邻两挂耳的间距作适当调整,相邻两挂耳的间距不得大于1700mm。
转炉炉壳

转炉炉壳
张家口市宣化华冶冶金设备工程有限公司
邓瑞云
转炉炉壳为钢板焊接结构,主要由炉帽、炉身和炉底三部分组成,其连接方式因修炉方式不同而异,有所谓的“死炉帽、活炉底”,“活炉帽、死炉底”和整体炉壳等结构形式。
这里,我们为大冶华鑫实业有限公司制作的转炉炉壳采用“活炉帽、死炉底”的结构形式。
这种结构采用上修法,炉帽和炉身为可拆式,用楔形销钉连接。
炉帽的形状有截锥形和半球形两种。
这里我们采用截锥形,这种结构制造简单。
在吹炼过程中,炉口受炉渣和炉气冲刷侵蚀,容易损坏变形。
为了保持炉口形状、提高炉帽寿命和便于清除炉口处结渣,目前普遍采用了水冷炉口。
水冷炉口有水箱式和铸铁埋管式两种结构。
这里我们采用的是水箱式水冷炉口,这种结构的冷却强度大,并且容易制造。
炉身为圆筒形,它是整个炉子的承载部分,受力最大。
出钢口设在炉帽和炉身相接处。
炉底根据熔池形状的不同,也有球形和截锥形之分。
这里,我们采用后者,其制造和砌砖都较为简单。
锅炉结构及工作原理

锅炉结构及工作原理一、引言锅炉是一种将水加热转化为蒸汽或者热水的设备,广泛应用于工业生产和民用领域。
本文将详细介绍锅炉的结构和工作原理,以匡助读者更好地理解和应用锅炉。
二、锅炉结构1. 锅炉壳体锅炉壳体是锅炉的主体部份,通常由钢板焊接而成。
它具有足够的强度和刚度,以承受锅炉内部的高温和高压。
壳体内部份为炉膛、燃烧室、过热器、再热器和空气预热器等区域。
2. 炉膛炉膛是燃烧燃料的区域,通常由耐火材料构成。
燃料在炉膛内燃烧产生高温燃烧气体,通过炉膛的上升通道进入过热器。
3. 过热器过热器是将高温燃烧气体的温度提高到设计要求的设备。
它由一系列管子组成,燃烧气体在管子内部流动,通过与管壁的热交换,使燃烧气体的温度升高。
4. 再热器再热器是将高温燃烧气体的温度再次提高的设备。
它与过热器类似,也由一系列管子组成。
燃烧气体在再热器内部流动,通过与管壁的热交换,使燃烧气体的温度再次升高。
5. 空气预热器空气预热器是将燃烧所需的空气预先加热的设备,以提高燃烧效率。
它通常由一系列管子组成,燃烧气体在管子外部流动,空气在管子内部流动,通过管壁的热交换,使空气的温度升高。
6. 锅炉附件锅炉附件包括给水系统、排烟系统、燃料供应系统、燃烧控制系统和安全保护系统等。
它们与锅炉的正常运行密切相关,起着辅助作用。
三、锅炉工作原理1. 燃料燃烧燃料在炉膛内燃烧,产生高温燃烧气体。
燃料可以是固体、液体或者气体,常见的有煤、油和天然气等。
燃烧过程中,燃料与空气混合并点燃,释放出热能。
2. 热能传递高温燃烧气体经过炉膛、过热器、再热器和空气预热器等部份,与水或者热媒进行热交换。
燃烧气体的热能被传递给水或者热媒,使其温度升高。
3. 蒸汽或者热水生成通过热能传递,水或者热媒的温度升高,最终转化为蒸汽或者热水。
蒸汽或者热水可以用于工业生产或者民用供暖等领域。
4. 蒸汽或者热水的利用蒸汽或者热水通过管道输送到需要的地方,用于驱动机械设备、加热或者供暖等用途。
标准规范

一、钢结构设计制作使用的标准(厂房钢结构、框架结构、轻钢结构)1、《建筑结构荷载规范》 GB50009-20012、《钢结构工程设计规范》 GBJ50017-20033、《建筑抗震设计规范》 GB50011-20084、《钢管混凝土结构设计与技术规程规范》 CESC28:905、《冷弯薄壁型钢结构技术规范》 GB50018-20026、《建筑钢结构焊接技术规程》 JGJ81-20027、《钢结构工程施工质量验收规范》 GB50205-20018、《钢结构高强度螺栓连接的设计施工及验收规程》 JGJ82-919、《钢管混凝土设计与施工规程》CECS28:29;10、《门式钢架轻型房屋钢结构技术规程》 CECS102:200211、《建筑钢结构施工手册》12、《钢桁架质量标准》 JG8-199913、《钢桁架检验与验收标准》 JG9-199914、电弧螺柱焊用圆柱头焊钉GB/T10433-2002二、高炉、热风炉制作标准1、《冶金机械设备安装工程施工及验收规范》YBJ208-852、《中厚板超声波检验方法》GB/T2970—20043、《炉壳壳体结构用钢板》Q/ASB 91-2005(鞍钢标准)三、钢结构用钢材标准1、《碳素结构钢》 GB/T700-20062、《低合金高强度结构钢》 GB/T1591-20083、《厚度方向性能钢板》GB5313—19854、《热轧工字钢尺寸、外形、重量及允许偏差》 GB/T706-20085、《热轧槽钢尺寸、外形、重量及允许偏差》 GB/T707-19886、《热轧等边角钢尺寸、外形、重量及允许偏差》GB/T9787-19887、《热轧圆钢和方钢尺寸、外形、重量及允许偏差》GB/T702-20088、《热扎钢板表面质量的一般要求》 GB/T12977四、焊材标准1、《气体保护电弧焊用碳钢、低合金钢焊丝》GB/T8110-20082、《低合金钢药芯焊丝》GB/T17493-20083、《碳素钢焊条》GB5117-19954、《低合金焊条》GB5118-19955、《埋弧焊用碳钢焊丝和焊剂》GB/T5293-19996、《埋弧焊用低合金钢焊丝和焊剂》GB/T12470-2003。
热风炉炉壳及框架制作安装施工方案

目录目录 (1)一、简介 (2)二、施工准备 (3)2.1编制依据 (3)2.2施工平面布置 (4)2。
3生产要素需用计划 (4)2。
4 基础验收 (5)2。
5 基础划线 (6)2。
6 组装临时平台的铺设 (6)2.7 热风炉本体外壳制作、安装方案和程序 (7)2.8 热风炉本体外壳制作、安装总技术要求 (7)2.9 热风炉本体施工通用制作工艺 (8)2.9.1 板材下料 (8)2。
9.2 坡口制作 (9)2。
9。
3 焊接 (9)2.10 热风炉钢结构通用制作工艺 (9)2.10.1排版下料 (10)2.10.2 坡口制作 (10)2。
10.3 梁、柱的焊接 (11)2.11 热处理 (13)三、制作和安装 (13)3.1 热风炉底板制作安装 (13)3。
2、炉壳板制作 (14)3。
2。
1、炉壳板下料: (14)3.3、炉壳板安装 (16)3.3.1、下部筒体组对、安装 (16)3.3.2、炉箅子组对、安装 (16)3.3.3、热风炉上部筒体的安装 (17)3.3.4、安装注意事项: (17)3.4、热风炉气密性试验 (18)3。
5、热风炉钢结构平台制作安装 (18)4。
1 热风炉炉壳及钢结构平台制作安装进度及保证施工进度的措施 (18)4。
2 热风炉炉壳及钢结构平台制作安装工程质量的保证措施 (19)4。
2。
1 质量方针: (19)4.2.2 质量目标: (19)4.2.3 质量保证体系 (19)4.2。
4 质量职责 (19)4。
2。
5 质量控制程序 (20)4.2.6 建设阶段的质量管理制度 (20)4。
2。
7 竣工验收阶段 (21)4。
3保证安全生产、文明施工及环境保护的措施 (21)4。
3。
1安全保证措施 (21)4。
3。
2 确定安全防范措施 (22)4。
3.3 加强安全生产教育 (22)4.3。
4 加强生产安全技术管理 (22)4.3.5施工现场安全管理 (23)4。
3。
6 认真执行安全检查制度 (23)4。
有机热载体锅炉结构

有机热载体锅炉结构有机热载体锅炉是一种采用有机化合物作为传热介质的热能设备。
它的主要结构由锅炉本体、燃烧室、热交换器、控制系统等组成。
锅炉本体锅炉本体是有机热载体锅炉的主体部分,它包括壳体、炉膛、烟管、热风道等部分。
壳体壳体是有机热载体锅炉的外壳,通常采用钢板焊接而成。
壳体内部设置有燃烧室和热交换器,以完成能量转换。
壳体的外表面通常涂有耐高温的防腐漆,以保证锅炉的耐腐蚀性。
炉膛炉膛是锅炉的燃烧室,它是有机热载体锅炉燃烧能源的地方。
炉膛通常采用圆形或矩形的结构,壁面由耐高温的耐火材料制成,以提高其耐热性。
炉膛顶部通常装有燃料喷嘴和点火器,以实现燃料的自动供给与点火操作。
烟管烟管是锅炉的烟气传导部分,它主要由烟道和水管组成。
烟道通过壳体与燃烧室相连接,烟气通过烟道流经热交换器,以完成能量的传递。
水管则是传热介质的通道,通过水管循环流动,以完成能量的吸收和传递。
热风道热风道主要用于供应空气以维持燃烧的必要氧气。
热风道通常由一条与壳体相接的长管组成,管道内部设置有防火阀门和温度传感器等安全保护设备。
燃烧室燃烧室是有机热载体锅炉的关键部件,通常采用燃气、柴油、煤等作为燃料。
燃料与空气在炉膛中充分混合后,通过点火器点火燃烧,并产生大量热能。
热交换器热交换器是有机热载体锅炉的核心部分,它通过换热方式将烟气中的热量传递给传热介质,从而达到利用热能的目的。
热交换器一般采用平板式、U型管式、蛇形管式、盘式等多种结构形式。
控制系统控制系统是有机热载体锅炉的智能控制中心,它通过对锅炉的温度、压力、烟气排放等重要参数的监测和调节,实现锅炉的智能化自动控制。
锅炉控制系统还应具备故障诊断和报警功能,以确保锅炉的安全性和可靠性。
综上所述,有机热载体锅炉是一种具有高效、能保护环境、升温速度快、升温均匀等优点的锅炉设备。
其复杂的结构和智能化控制系统为其实现高效、安全、可靠的运行提供了有力的保障。
锅炉结构及工作原理

锅炉结构及工作原理一、引言锅炉是一种重要的能源设备,广泛应用于工业、农业、建造等领域。
了解锅炉的结构和工作原理对于正确使用和维护锅炉至关重要。
本文将详细介绍锅炉的结构和工作原理,以匡助读者更好地理解和应用锅炉。
二、锅炉结构1. 锅炉壳体:锅炉壳体是锅炉的主体部份,通常由钢板焊接而成。
它承受锅炉内部的高温高压工作环境,并起到密封和保温的作用。
2. 锅筒:锅筒是锅炉内部的主要压力部件,通常为圆筒形,由钢板制成。
它负责容纳水和蒸汽,并承受锅炉内部的压力。
3. 炉膛:炉膛是锅炉内燃烧的区域,通常位于锅筒的下部。
它提供了燃烧所需的空间,同时也是热量传递的主要区域。
4. 炉排:炉排位于炉膛底部,用于支撑燃料并使其均匀燃烧。
炉排的结构和材料选择对于燃烧效果和锅炉的运行稳定性有重要影响。
5. 烟道:烟道是燃烧产生的烟气排出的通道,通常位于锅筒的上部。
烟道的设计和布置对于烟气的流动和热量传递有重要影响。
6. 烟囱:烟囱是烟气排出至大气的通道,通常位于锅炉的顶部。
烟囱的高度和截面积对于烟气排放和锅炉的燃烧效率有影响。
三、锅炉工作原理1. 燃料燃烧:锅炉的工作原理首先是燃料的燃烧过程。
燃料经过点火后,在炉膛中与空气进行充分混合,并在适当的温度下引燃。
燃烧产生的热量使水在锅筒中加热并转化为蒸汽。
2. 热量传递:燃烧产生的热量通过炉壁和炉筒传递给水。
炉壁和炉筒由于导热性能好,能够将热量迅速传递给水,使水温升高并转化为蒸汽。
3. 蒸汽产生:随着热量的传递,水逐渐加热并转化为蒸汽。
蒸汽的产生与水的温度和压力有关,通常在锅炉中设有水位和压力控制装置,以确保蒸汽的产生和使用的安全性。
4. 蒸汽使用:蒸汽可以用于驱动各种设备,如发机电、风机、泵等。
蒸汽的使用范围广泛,根据不同的需求可以进行调节和控制。
四、锅炉的分类根据不同的燃料和工作原理,锅炉可以分为多种类型,如以下几种常见的锅炉:1. 燃煤锅炉:使用煤炭作为主要燃料,通过燃烧产生热能。
锅炉结构及工作原理

锅炉结构及工作原理一、引言锅炉是一种将水或其他液体加热转化为蒸汽或热水的设备,广泛应用于工业生产、供暖和发电等领域。
本文将详细介绍锅炉的结构和工作原理。
二、锅炉结构1. 锅炉壳体:锅炉壳体是锅炉的主体部分,通常由钢板焊接而成。
壳体内部包含水腔和燃烧室等部分。
2. 燃烧系统:燃烧系统包括燃料供给装置、燃烧器和燃烧室。
燃料供给装置将燃料输送到燃烧器,燃烧器将燃料喷射到燃烧室中进行燃烧。
3. 烟气系统:烟气系统包括烟道、烟囱和除尘设备等。
烟道将燃烧产生的烟气引导到烟囱中排出,除尘设备用于净化烟气中的颗粒物和有害气体。
4. 水循环系统:水循环系统包括给水系统、蒸汽系统和循环水系统。
给水系统将水供给锅炉,蒸汽系统将锅炉产生的蒸汽输送到需要的地方,循环水系统将冷却后的水回流到锅炉中继续循环。
5. 控制系统:控制系统用于监测和控制锅炉的运行状态,包括温度、压力、流量等参数的监测和调节。
三、锅炉工作原理1. 燃烧过程:燃料经过燃料供给装置输送到燃烧器中,燃烧器将燃料与空气混合后喷射到燃烧室中。
燃料在燃烧室中与空气发生化学反应,产生热能。
燃烧产生的烟气通过烟道排出,同时加热水腔中的水。
2. 水循环过程:给水通过给水系统进入锅炉,经过加热后转化为蒸汽或热水。
蒸汽通过蒸汽系统输送到需要的地方,热水通过循环水系统回流到锅炉中继续循环。
循环水经过加热后再次转化为蒸汽或热水。
3. 控制过程:控制系统监测锅炉的运行状态,根据设定的参数进行调节。
例如,当锅炉压力过高时,控制系统会自动调节燃料供给量和燃烧器的工作状态,以保持锅炉的正常运行。
四、锅炉的应用领域1. 工业生产:锅炉广泛应用于各种工业生产过程中,如化工、纺织、食品加工等。
锅炉可以提供蒸汽或热水,用于加热、蒸煮、干燥等工艺操作。
2. 供暖系统:锅炉作为供暖系统的核心设备,可以将燃料燃烧产生的热能转化为热水或蒸汽,通过管道输送到建筑物中供暖。
3. 发电厂:锅炉在发电厂中起到热能转化的作用。
锅炉结构及工作原理

锅炉结构及工作原理一、引言锅炉是一种将燃料燃烧产生的热能转化为蒸汽或热水的设备,广泛应用于工业、农业、建筑等领域。
了解锅炉的结构和工作原理对于正确使用和维护锅炉至关重要。
本文将详细介绍锅炉的结构和工作原理。
二、锅炉结构1. 锅炉壳体:锅炉壳体是锅炉的主体部分,通常由钢板焊接而成。
壳体内部包含燃烧室、炉膛、水冷壁、过热器等组件。
2. 燃烧系统:燃烧系统由燃烧器、燃烧室和燃烧控制系统组成。
燃烧器负责将燃料与空气混合并点燃,燃烧室提供燃烧的空间,燃烧控制系统控制燃烧过程的稳定性和效率。
3. 水循环系统:水循环系统包括给水系统、蒸汽系统和排污系统。
给水系统负责将水供给锅炉,蒸汽系统负责收集和输送蒸汽,排污系统负责排放锅炉废水。
4. 辅助设备:锅炉还配备了一些辅助设备,如风机、除尘器、给水泵、循环泵等。
这些设备的作用是提供所需的空气、水和电力等资源,确保锅炉正常运行。
三、锅炉工作原理1. 燃烧过程:燃料经过燃烧器与空气混合后,在燃烧室内点燃。
燃烧产生的高温烟气通过炉膛和水冷壁,将水加热为蒸汽。
2. 蒸汽产生:水在锅炉内部循环,通过给水系统进入锅炉。
热能将水加热至沸点,产生蒸汽。
蒸汽在锅炉内部积聚,通过蒸汽系统输送到需要的地方。
3. 能量转移:燃烧产生的热能通过炉膛和水冷壁将水加热为蒸汽。
过热器进一步加热蒸汽,提高其温度和压力。
蒸汽被输送到需要的地方,释放热能。
4. 排污处理:锅炉废水通过排污系统排放。
废水中的杂质和污染物经过处理,以确保环境的安全和清洁。
四、案例分析以某工业企业的锅炉为例,该锅炉采用燃煤方式进行燃烧。
燃煤过程中,燃烧器将煤粉与空气混合,形成可燃气体。
煤粉燃烧产生的高温烟气经过炉膛和水冷壁,将水加热为蒸汽。
蒸汽通过蒸汽系统输送到生产线,为生产提供动力。
该锅炉的结构包括壳体、燃烧系统、水循环系统和辅助设备。
壳体由钢板焊接而成,具有良好的密封性和强度。
燃烧系统包括燃烧器、燃烧室和燃烧控制系统,确保燃烧过程的稳定性和效率。
炼铁工艺炉壳体结构施工

炼铁工艺炉壳体结构施工1.一般规定1.1施工单位应按设计图纸及技术要求编制详细的施工制作文件或施工方案。
当需修改设计时, 应经设计单位书面同意。
1.2壳体制作、安装材料应符合第5章的要求。
1.3制作、安装所用的计量器具应经计量检定机构检定,并在检定周期(有效期)内使用。
1.4壳体安装前,应根据炉容级别、结构的复杂程度、工期及质量要求、采用新技术的内容,现场平面布置和起重设备能力等编制施工组织设计。
1.5壳体预装和安装时,必须设置安全作业平台、扶梯,操作人员应遵守高空作业的相关规定。
1.6在满足设计要求、现场安装能力、运输界限的条件下,壳体应尽可能最大化块运输至现场。
热风炉高温区段的壳体宜整带出厂。
1.7为防止炉壳在运输过程中变形,出厂时应采取加固措施。
2壳体制作2.1壳体钢板的切割及开孔除设计有规定外,应符合下列规定:1应优先采用数控切割机或半自动切割机进行切割;2低合金钢板的切割应在5℃以上的环境温度下进行,当环境温度等于或低于5℃时,应采取相应的升温措施;3切割边缘必须平整,切割面的表面质量应符合现行行业标准《热切割质量和几何技术规范》JB/T10045的相关规定;4切割后壳体钢板的外形尺寸允许偏差为±2mιn,两对角线长度的允许偏差为3mm,并应考虑留有焊接收缩余量;5钢板的坡口形式及尺寸应符合设计文件的规定;6开孔边缘距现场横向焊缝W50mm及现场竖向焊缝15Omm以内的孔,均应在工厂定位,在现场安装焊接完成后再开孔;7除第6款外的开孔,均应在工厂切割成孔,开孔要求采用自动切割或机械切割。
炉壳辐压成型前后均可开孔,孔周边应磨光,不得留有刻槽或毛刺等缺陷,冷却壁水管孔内外均应倒角 2mm;8现场开孔需采用专用机械。
2.2壳体钢板的弯曲成形应采用弯板机、压力机及旋压机进行,并应符合下列规定:1壳体冷成形时,用弦长不小于1500≡的弧形样板检查上、下口弧度,其间隙不得大于2mm;2热成形时,钢板加热温度为900°C~IOOCTC。
卧式侧吹转炉炉体的主要结构组成

卧式侧吹转炉炉体的主要结构组成
卧式侧吹转炉炉体的主要结构组成如下:
1. 炉壳:炉壳是炉体的外部部分,通常由钢板焊接而成。
炉壳的主要功能是提供炉体的结构支撑和保护内部设备。
2. 炉衬:炉衬是炉体内部的内衬层,通常由耐火砖或耐火浇注料构成。
炉衬的主要功能是承受高温和化学腐蚀,并提供良好的炉腔保温性能。
3. 炉带:炉带是炉体内部的转炉倾斜装置,可以将炉腔倾斜到一定角度。
炉带通常由滚筒和传动装置组成,用于控制转炉的倾斜角度和速度。
4. 吹炉装置:吹炉装置是炉体内部的主要设备,用于将氧气和燃料引入炉腔进行燃烧和冶炼过程。
吹炉装置通常由吹氧设备、燃烧器和炉口装置组成。
5. 出渣装置:出渣装置是炉体内部的设备,用于排出炉腔中产生的渣滓。
出渣装置通常由出渣孔、渣铲和渣车组成。
6. 冷却装置:冷却装置用于冷却炉体和内部设备,以保证炉体的正常运行和延长设备寿命。
冷却装置通常包括水冷壁、水冷炉带、水冷炉壳等。
7. 炉底和底吹设备:炉底是炉体的底部部分,用于支撑和固定炉体。
底吹设备主要用于在炉底喷入氧气,提供底吹气力来控
制炉内反应的进行。
以上是卧式侧吹转炉炉体的主要结构组成,根据具体的炉型和技术要求,还可能包括其他辅助设备和结构。
锅炉结构及工作原理

锅炉结构及工作原理一、引言锅炉是一种重要的能源设备,广泛应用于工业生产和民用领域。
了解锅炉的结构和工作原理对于安全运行和高效利用能源具有重要意义。
本文将详细介绍锅炉的结构和工作原理。
二、锅炉结构1. 锅炉壳体:锅炉壳体是锅炉的主体部分,通常由钢板制成。
它具有足够的强度和刚度来承受内部的压力和温度。
壳体内部通常分为多个燃烧室和水管区域。
2. 燃烧室:燃烧室是锅炉内部进行燃烧的区域。
它通常由炉膛、炉排和燃烧器组成。
燃烧室的设计和结构对于燃烧效率和排放控制至关重要。
3. 水管:水管是锅炉内部传递热能的管道。
它们通常呈弯曲或螺旋形状,以增加热交换的面积。
水管内部流动着循环水,通过与燃烧室内的烟气进行热交换,将水加热为蒸汽。
4. 烟道:烟道是燃烧室和排烟系统之间的通道。
烟气在燃烧室中燃烧后,通过烟道排出。
烟道内部通常设置有烟气余热回收装置,以提高能源利用效率。
5. 辅助设备:锅炉还包括一些辅助设备,如给水系统、除氧器、循环泵、风机和控制系统等。
这些设备的作用是确保锅炉的正常运行和安全性。
三、锅炉工作原理1. 燃烧过程:锅炉的燃烧过程是通过燃料与空气的混合,在燃烧室中进行的。
燃料可以是固体、液体或气体,它们与适量的空气混合后,在燃烧器中点火。
燃烧产生的热能通过燃烧室壁和水管传递给水,使水加热为蒸汽。
2. 热交换过程:水管内的循环水与燃烧室内的烟气进行热交换。
烟气中的热能被水吸收,使水加热。
烟气在烟道中流动,同时也通过烟气余热回收装置,回收部分烟气中的余热,提高能源利用效率。
3. 蒸汽产生:随着水的加热,水逐渐转化为蒸汽。
当蒸汽达到一定压力时,锅炉会自动调节燃烧器的燃料供给,以控制蒸汽产生的速度和压力。
4. 蒸汽应用:产生的蒸汽可以用于多种用途,如发电、供热、蒸汽动力等。
不同的应用需要不同的蒸汽参数,因此锅炉的设计和调节需要根据具体的应用需求进行。
四、锅炉的分类根据不同的工作原理和应用领域,锅炉可以分为多种类型,如以下几种常见的分类:1. 按照工作压力分:低压锅炉、中压锅炉、高压锅炉等。
连续式炭化炉各部件尺寸结构计算过程

连续式炭化炉各部件尺寸结构计算过程
连续式炭化炉是一种用于木材和其他生物质炭化的设备,它由多个部件组成。
以下是计算连续式炭化炉各部件尺寸结构的步骤:
1. 锅炉壳体:炭化炉的壳体应由钢板制成,钢板的尺寸应根据锅炉内径和壁厚来确定。
例如,对于直径2米的炭化炉,壁厚为6毫米,则钢板的尺寸应为(
2.06+0.006×2)×
3.14=12.606米,即需要一块尺寸为12.606米×2米的钢板。
2. 隔板:连续式炭化炉通常有多个隔板,主要作用是将炭化炉分为多个炭化区域,从而达到连续炭化的效果。
隔板的尺寸应根据炭化炉的内径和高度来确定。
例如,对于直径2米,高度为10米的炭化炉,若分为4个炭化区域,则每个隔板尺寸为2米×2.5米。
3. 炭化炉内筒:炭化炉内筒是炭化区域的主体部分,其尺寸应根据炭化炉内径和高度来确定。
例如,对于直径2米,高度为10米的炭化炉,其内筒尺寸为直径2米、高度为10米的圆柱形。
4. 进出料口:炭化炉的进出料口尺寸应根据每个炭化区域的进出料量来确定,一般情况下,进出料口应大于等于炭化区域的进出料宽度。
例如,对于进出料宽度为1.5米的炭化区域,进出料口宽度应至少为1.5米。
5. 烟气排放口:烟气排放口的尺寸应根据炭化炉的排放要求来确定,一般情况
下,排放口应大于等于炭化炉的产生量。
例如,对于每小时炭化量为1000公斤的炭化炉,其排放口尺寸应至少为1.5米×1米。
以上是计算连续式炭化炉各部件尺寸结构的主要步骤,具体尺寸还需根据实际情况进行调整。
炉体钢结构制造与安装技术要求
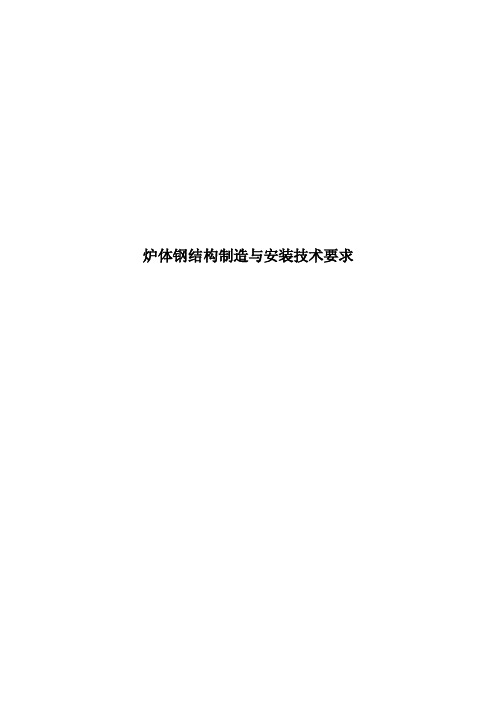
炉体钢结构制造与安装技术要求一说明1、炉体钢结构是加热炉的重要组成部分,一般由炉底钢结构、侧墙钢结构、装料端钢结构、出料端钢结构、炉顶钢结构、烟道钢结构、走梯、平台、换热器外壳、水冷箱、水套、水槽等及其支架、立柱等构件组成。
由于炉底钢结构的横梁制作安装对保证炉子固定梁安装的平面度极为重要,以及在炉底钢结构下部要安装步进梁立柱穿过炉底的开孔与裙式水封刀及其刮渣板,它们与水封槽的制作有一定的配合要求,因此,炉底钢结构的制造与安装精度是炉体钢结构中要求最严格的。
步进梁式加热炉为了缩短施工安装周期,炉体钢结构都设计为组装部件,以确保施工安装顺利进行,因此,所有炉体钢结构的制造与安装精度要求是比较严格的。
2、炉体钢结构用材料1)工业炉钢结构工程所采用的钢材,包括不锈钢等要求耐氧化、耐热的材料,应具有质量证明书,并应符合设计的要求。
当对钢材的质量有疑义时,应按国家现行有关标准的规定进行抽样检验。
2)钢结构工程所采用的连接材料和涂装材料,应具有出厂质量证明书,并应符合设计的要求和国家有关标准的规定。
3)使用的所有材料均应是全新的可以焊接的材料,不得有有损其使用的制造缺陷和外观缺陷,不得有油漆锈迹和氧化铁皮。
4)使用的钢板应当平直、无疤痕和明显变形,外观良好,厚度均匀。
钢板规格应注意选配,尽量减少焊缝。
5)型钢应当在使用前矫直,除图上正常考虑的情况外,型钢不允许对焊成型。
二制造1、炉体钢结构是在制作现场加工成构件(部件)后运往施工现场进行安装的。
制造时应严格按施工图的要求进行制作,各构件的尺寸公差与形位公差在施工图上若有说明按图施工,没有说明则按下表的要求执行。
炉体钢结构制作验收公差标准2、炉底钢结构制作允许公差1)纵向大梁直线度3mm2)炉底立柱顶面与立柱中心线垂直度0.5mm3)炉底片架a 固定立柱孔的位置度±1mmb 炉底片架两端底面扭曲度0.5mm3、侧墙钢结构制作允许公差1)侧墙立柱底板至烧咀开孔中心线的高度±2mm2)侧墙立柱的高度±2mm3)侧墙立柱的间距±2mm4)侧墙立柱的弯曲度±2mm5)侧墙钢板的平面度5mm4、炉顶钢结构制作允许公差1)炉顶横梁螺栓孔位置以炉子中心线为基准,公差为±2mm。
蒸汽发生器炉胆构造
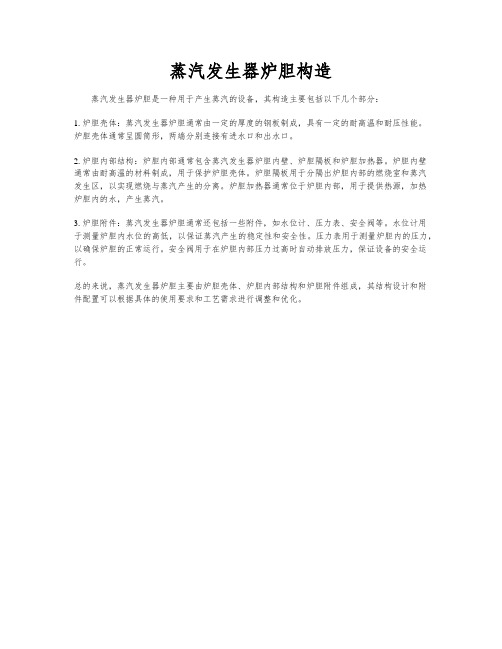
蒸汽发生器炉胆构造
蒸汽发生器炉胆是一种用于产生蒸汽的设备,其构造主要包括以下几个部分:
1. 炉胆壳体:蒸汽发生器炉胆通常由一定的厚度的钢板制成,具有一定的耐高温和耐压性能。
炉胆壳体通常呈圆筒形,两端分别连接有进水口和出水口。
2. 炉胆内部结构:炉胆内部通常包含蒸汽发生器炉胆内壁、炉胆隔板和炉胆加热器。
炉胆内壁通常由耐高温的材料制成,用于保护炉胆壳体。
炉胆隔板用于分隔出炉胆内部的燃烧室和蒸汽发生区,以实现燃烧与蒸汽产生的分离。
炉胆加热器通常位于炉胆内部,用于提供热源,加热炉胆内的水,产生蒸汽。
3. 炉胆附件:蒸汽发生器炉胆通常还包括一些附件,如水位计、压力表、安全阀等。
水位计用于测量炉胆内水位的高低,以保证蒸汽产生的稳定性和安全性。
压力表用于测量炉胆内的压力,以确保炉胆的正常运行。
安全阀用于在炉胆内部压力过高时自动排放压力,保证设备的安全运行。
总的来说,蒸汽发生器炉胆主要由炉胆壳体、炉胆内部结构和炉胆附件组成,其结构设计和附件配置可以根据具体的使用要求和工艺需求进行调整和优化。
高炉炉壳用钢

高炉炉壳用钢
但泽义;邓玉孙
【期刊名称】《钢结构》
【年(卷),期】2008(023)011
【摘要】在分析我国高炉妒壳用钢的使用现状和高炉生产后期炉壳的破坏原因的基础上,针对现行国家标准<高炉炼铁工艺设计规范>(GB 50427-2008)要求高炉一代炉役的工作年限(无中修)达到15年以上的规定,依据炉壳用钢试验研究和生产实践的综合成果,对<钢铁企业冶炼工艺炉技术规范>(送审稿)提出的适应高炉同步长寿的炉壳用钢性能要求和可用于1 000~5 000 m<'3>级高炉炉壳的钢材牌号给予介绍.
【总页数】3页(P47-49)
【作者】但泽义;邓玉孙
【作者单位】中冶赛迪工程技术股份有限公司,重庆,400013;中冶赛迪工程技术股份有限公司,重庆,400013
【正文语种】中文
【中图分类】TU3
【相关文献】
1.安钢高炉炉壳用钢的研制开发 [J], 欧阳瑜;厚健龙;李力
2.高炉炉壳用钢的开发 [J], 张全通;马建伟;肖彦忠;董鸿飞
3.承钢1号高炉炉壳更换方案探索 [J], 郝瑞朝;商仕金;高亚男
4.宁钢2#2500m3高炉风口大套与炉壳焊缝裂纹的控制 [J], 吴文明
5.浅谈高炉冷却壁钢砖炉壳更换方法及作业要点 [J], 朱志军
因版权原因,仅展示原文概要,查看原文内容请购买。
高炉炉壳安装方案

目录1.工程概况 (2)1.1工程简介 (2)1.2工程特点 (4)1.3工程技术难点 (4)2.方案引用、参考资料 (4)3.工程总体施工流程 (5)4.施工工艺方法 (6)4.1液压提升技术在高炉上的运用 (6)4.2施工方法简述 (7)4.3炉壳组装、平移平面布置简述 (8)4.4炉壳预装台架组装 (9)4.5炉壳滑移托架组装 (9)4.6炉壳组装阶段施工方法 (10)4.7炉壳运输施工方法 (16)4.8炉壳基础上安装施工方法 (20)5.施工进度安排 (27)6.施工劳动力组织计划 (28)7.施工机具、材料计划 (28)7.1施工机具使用计划 (28)7.2施工用材料使用计划 (30)8.质量保证措施 (31)8.1质量管理保证体系 (31)8.2质量管理要求 (32)8.3质量控制要点 (33)9.安全保证措施 (34)9.1安全管理保证体系 (34)9.2安全施工管理要求 (35)9.3施工现场临时用电管理 (36)9.4高空作业安全防护要点 (37)9.5冷却设备安装过程中的安全注意事项 (37)9.6液压牵引安全措施 (37)9.7钢绞线使用安全须知 (38)9.8防火安全管理 (39)9.9交通安全管理 (39)10.文明施工保证措施 (39)1.工程概况1.1工程简介宝钢二号高炉1991年6月投产至今,已近设计使用年限。
目前,宝钢生产对生铁需求量很大,为保证其炼铁系统的生产平衡,宝钢股份决定实施二号高炉易地大修工程,并确定28个月的施工工期。
按以往国内传统的高炉施工工艺,高炉的炉壳体及框架的安装工期已无法压缩,难以保证高炉的预定28个月的施工工期。
因此,在二号高炉易地大修工程中,炉体部分将采用快速安装工艺,以提高施工的进度,保证预定施工工期实现。
所谓炉体快速安装工艺,是将炉壳分成四大段,于高炉基础外进行组装完毕,待高炉上部框架安装完毕后,利用在上部框架45.3米标高圈梁上设置的液压提升装置,将滑移至炉体框架内的炉壳依次提升——焊接——提升,最终将炉壳安装到位,高炉炉壳横缝焊接采用林肯半自动自保护焊,立缝焊接采用KES(SES)电渣焊或林肯自保护自动立焊,炉体上所带设备及材料(除炉壳环缝部位)在炉壳组装阶段,将尽可能多的安装好,随炉壳一同提升。
- 1、下载文档前请自行甄别文档内容的完整性,平台不提供额外的编辑、内容补充、找答案等附加服务。
- 2、"仅部分预览"的文档,不可在线预览部分如存在完整性等问题,可反馈申请退款(可完整预览的文档不适用该条件!)。
- 3、如文档侵犯您的权益,请联系客服反馈,我们会尽快为您处理(人工客服工作时间:9:00-18:30)。
6.1.2 6.2
2
钢板的化学成分允许偏差应符合 GB/T 222 的规定 交货状态
Q/ASB 91-2005
钢板以热轧、TMCP 或正火状态交货。 6.3 6.3.1 6.3.2 力学性能和工艺性能 交货状态钢板的力学性能和工艺性能应符合表 2 的规定。 当钢板不能取全尺寸(10mm×10mm×55mm)的冲击试样时,可用 10mm×7.5mm×55mm
鞍山钢铁集团公司企业标准
Q/ASB 91-2005
炉壳壳体结构用钢板
2005-06-01 发布
2005-06-01 实施
鞍山钢铁集团公司 发布
Q/ASB 91-2005
前
言
为规范炉壳壳体用钢板的生产和管理,在原新轧公司炉壳壳体用钢板技术协议的基础上 制定本标准。 本标准对原炉壳用钢板牌号 ALK42、AG50 和 AC1 进行重新命名,对原技术条件进行规范 处理。 自本标准实施之日起,AJT 17-2003《高炉壳体用 AG50》废止。 本标准的附录 A 为资料性附录。 本标准由鞍钢集团公司科技质量部提出。 本标准由鞍钢集团公司科技质量部归口。 本标准起草单位:鞍钢集团公司科技质量部、鞍钢集团公司厚板厂。 本标准主要起草人:郑英杰、丛津功、陈军平。 本标准的水平等级标记为:Q/ASB 91-2005 Y。
Q/ASB 91-2005
炉壳壳体结构用钢板
1
范围 本标准规定了制造炉壳壳体结构用钢板的尺寸、外形、重量及允许偏差、技术要求、试
验方法、检验规则、包装、标志和质量证明书。 本标准适用于鞍钢生产的炉壳壳体用钢板。 2 规范性引用文件 下列文件中的条款通过本标准的引用而成为本标准的条款。凡是注日期的引用文件,其 随后的所有修改单(不包括勘误的内容)或修订版本均不适用于本标准,然而,鼓励根据本 标准达成协议的各方研究是否可使用这些文件的最新版本。凡是不注日期的引用文件,其最 新版本适用于本标准。 GB/T 222-1984 GB/T 223 GB/T 228 GB/T 229 GB/T 232 GB/T 247 GB/T 2970 GB/T 2975 YB/T 081 Q/ASB 1 3 钢的化学分析用试样取样法及成品化学成分允许偏差
Q/ASB 1 中表 1 的规定。 6 6.1 6.1.1 技术要求 牌号及化学成分 钢的牌号及化学成分(熔炼分析)应符合表 1 的规定。 表1
化学成分,% 牌号 C 0.12~ ALK420 0.18 0.09 ALK470 ~0.13 0.14~ ALK490 0.18 0.60 1.60 0.025 0.005 0.04 0.30 0.30~ 1.20 1.40~ 0.025 ≤ 0.010 ≤ 0.04 0.01~ — 0.02 0.35 ≤ — — 0.060 0.008 0.40 0.10~ 0.80 1.00~ 0.025 ≤ 0.010 ≤ 0.02~ 0.15~ — 0.05 0.30 0.020~ 0.03~ Si 0.15~ Mn 0.50~ P ≤ S ≤ — — — — 0.60 0.10~ — 0.008 ≤ 0.045 0.008 ≤ Nb Cr Ti V Mo 0.45~ Als 0.015~ N ≤
ቤተ መጻሕፍቲ ባይዱ
小尺寸冲击试样代替,其冲击功规定值不小于表 2 规定值的 5/6。 6.3.3 冲击值为一组 3 个试样试验结果的算术平均值,允许有一个试样的试验结果小于规定
值,但不得小于规定值的 70%。 6.3.4 超声波探伤
钢板应按 GB/T 2970 逐张进行超声波探伤检查,合格级别为Ⅱ级。 表2
拉伸试验 断后 下屈服强度 抗拉强度 Rel Rm 伸长率 A MPa MPa % ALK420 10~50 ≥245 420~530 ≥22 ALK470 50~80 ≥275 470~570 ≥21 40~60 ≥295 490~610 ALK490 ≥20 61~80 ≥275 470~590 注:拉伸、弯曲试验取横向试样,冲击试验取纵向试样。 牌号 板厚 mm 180°弯曲试验 弯心直径 2a 2a 2a V 型冲击 试验温度 ℃ -20 -20 -20 冲击功 J ≥34 ≥34 ≥34
线与一个轧制面的距离) 。 表3
序号 1 2 3 4 5 检验项目 化学成分 拉伸试验 弯曲试验 冲击试验 超声波探伤 取样数量(个) 1/每炉 1/批 1/批 3/批 逐张 取样方法 GB/T 222 GB/T 2975 GB/T 2975 GB/T 2975 — 试验方法 GB/T 223,GB/T 4336 GB/T 228 GB/ T232 GBT 229 GB/T 2970 3
4
Q/ASB 91-2005
附录 A (资料性附录) 本标准牌号与原技术条件牌号对照表
本标准牌号 ALK420 ALK470 ALK490 原技术条件牌号 AC1 ALK42 AG50 用途 热风炉壳体结构 转炉壳体结构 高炉壳体结构
5
4.2
标记示例 按 Q/ASB 91 交货的牌号为 ALK420、厚度 40mm、宽度 3500mm、长度 8000mm 的热轧钢板 Q/ASB 91-2005 ALK420 40×3500×8000
5
尺寸、外形、重量及允许偏差 钢板的尺寸、外形、重量及允许偏差应符合 Q/ASB 1 的规定,其中厚度允许偏差应符合
6.4 6.4.1
表面质量 钢板切割端面不应有分层。钢板表面目视检查不应有裂纹、气泡、夹杂、结疤、折叠
和氧化铁皮压入等有害缺陷。 6.4.2 6.4.3 钢板表面允许存在不妨碍检查表面缺陷的薄层氧化铁皮、铁锈。 钢板表面存在有害缺陷时, 允许用修磨方法清除, 但修磨深度不得大于钢板的厚度公
差之半。修磨处应平滑过渡,并应保证钢板厚度的最小值。 7 7.1 7.2 7.3 7.4 试验方法 钢板的表面质量应目视检查。 钢板的尺寸和外形用合适的测量工具检查。 每批钢板的检验项目、取样数量、取样方法和试验方法应符合表 3 的规定。 对于厚度大于 40mm 的钢板,拉伸、冲击试验试样应在钢板厚度的 1/4 处取(试样的轴
个试样的平均值不应小于规定值,允许有不超过 2 个试样的单个值低于规定值,且低于规定 值 70%的试样不应多于 1 个。 8.3.2 如果拉伸和弯曲试验结果不符合标准要求时, 则从同一批中再取双倍数量的试样进行
该不合格项目的复验。 8.3.3 复验结果(包括该项目试验所要求的所有指标)合格,则该批合格;复验结果(包括
Q/ASB 91-2005
8 8.1
检验规则 组批 钢板应成批验收。每批应由同一牌号、同一炉号、同一规格、同一热处理制度的钢板组
成。每批钢板重量不大于 40 吨。 8.2 取样数量 钢板每批检验的取样数量按表 3 的规定。 8.3 8.3.1 复验与判定规则 冲击试验初验不合格时,应从同一张钢板上再取一组 3 个试样进行试验,前后二组 6
该项目试验所要求的所有指标)即使有一个指标不合格,则复验不合格。 8.3.4 如复验不合格, 则已做试验且试验结果不合格的单件不能验收, 但该批中未做试验的
单件可逐件重新提交试验和验收。 8.4 数值修约 数值修约规则按 YB/T 081 的规定进行。 9 9.1 包装、标志和质量证明书 每张钢板应打印或喷印以下信息: 钢的标准号、牌号、熔炼号、批号、规格尺寸、厂标。 9.2 其它应符合 GB/T 247 的有关规定。
冶金技术标准的数值修约与检验数值的判定原则 热轧中厚钢板尺寸、外形、重量及允许偏差
牌号表示方法 炉壳钢的牌号由鞍钢、炉壳的汉语拼音首位字母及抗拉强度三个部分组成。 例如:A LK 490
抗拉强度级别(MPa) 炉壳 鞍钢
1
Q/ASB 91-2005
4 4.1
订货信息 订货时,用户须提供下列信息: a) 标准号; b) 牌号; c) 规格尺寸; d) 交货状态; e)重量; f)用途; g) 特殊要求。
钢铁及合金化学分析方法 金属材料 室温拉伸试验方法(eqv ISO 6892:1998) 金属夏比缺口冲击试验方法(eqv ISO148:1983、ISO83:1976) 金属材料 弯曲试验方法(eqv ISO 7438:1985) 钢板和钢带检验、包装、标志及质量证明书的一般规定 厚钢板超声波检验方法 钢及钢产品 力学性能试验取样位置及试样制备(eqv ISO 377:1997)