烧结工艺讲座
烧结工艺及操作培训讲义
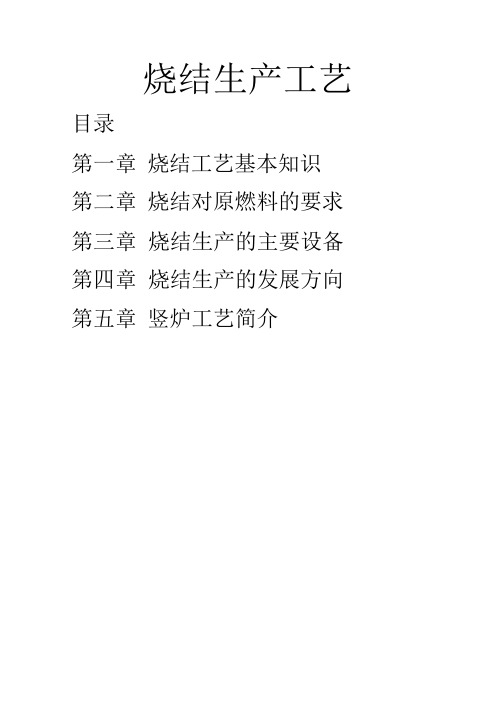
烧结生产工艺目录第一章烧结工艺基本知识第二章烧结对原燃料的要求第三章 烧结生产的主要设备 第四章 烧结生产的发展方向第五章竖炉工艺简介第一章烧结工艺基本常识 第一节 烧结生产的发展及其在冶金工业中的地位一、烧结工艺的产生和发展产生:1、原始的烧结方法只能处理冶金行业中的废弃物、高炉灰、铁皮、硫酸渣,变废为宝。
2、随着钢铁工业的快速发展,矿石的开采量大大增加,而且优质矿石(高含铁量60%以上)越来越少,贫矿越来越多(Fe低25-30%)而优质矿石1.7-1.9t炼一吨,贫矿需3-4吨,而贫矿直接入炉不经济,所以必须经过处理,而经磁选后的铁精粉Fe60%以上,但粒度不符合标准(高炉矿石10-40mm),因此产生了造块工艺发展:最早英国、瑞典、德国、我国在建国以后得到发展600㎡、180㎡、130㎡、90㎡、65㎡、24㎡等;我厂运行4台,2×71.5㎡、2×100㎡;四期技改项目2×200 ㎡ 二、 铁矿粉烧结的意义 (1)通过烧结可为高炉提供化学成分稳定,粒度均匀,还原性好,冶金性能高的优质烧结矿,为高炉优质、高产、低耗、长寿创造良好条件。
(2)去除有害杂质如硫、锌等。
(3)可利用工业生产的废弃物,如高炉炉尘、轧钢皮、硫酸渣、钢渣等。
(4)可回收有色金属和稀有、稀土金属。
三、 烧结矿质量对高炉冶炼有哪些影响? (1)含铁量下降1%焦比上升2% 产量下降3%。
(2)FeO变动1%,焦比1%-1.5%,产量影响1%-5%。
(3)R2(cao/sio2)变化0.10对焦比、产量影响3%-3.5%。
(4)烧结矿的强度:强度不够时,高炉内部容易形成5㎜以下的面子,产量下降0.5%-1.0%,焦比升高0.5%。
(5)烧结矿的还原性、RDI(低温还原粉化)对高炉影响较大。
第二节 烧结方法分类及生产工艺流程 一、烧结的含义 1、烧结定义:所谓烧结,即是将各种粉状含铁原料,按要求配入一定数量的燃料和熔剂,混合均匀制粒后布到烧结设备上点火烧结;在燃料燃烧产生高温和一系列物理化学反应的作用下,混合料中部分易熔物质发生软化、熔化,产生一定数量的液相,铁矿粉或富矿粉在一定的高温作用下,并与其他未熔矿石(返矿)颗粒作用;随着温度的降低,冷却后液相将矿粉颗粒粘结成块,这个过程称为烧结,所得的矿块叫做烧结矿。
烧结工艺基础知识培训讲座

? 3.通过烧结可除去矿石中的S、Zn、Pb、As、K、Na等有害杂 质,减少其对高炉的危害。高炉使用冶炼性能优越的烧结矿后 ,基本上解除了天然矿冶炼中常出现的结瘤故障;同时极大地 改善了高炉冶炼效果。
? 对含铁原料的要求:由于含铁原料物理化学性质对烧结矿质量 影响最大,所以要求含铁原料品位高、成分稳定、杂质少、脉 石成分适宜造渣,粒度适宜。精粉粒度-200目量<80%。
? 富矿粉粒度要求:≤8mm粒级≥85%。工业副产品要求无杂物 ,含铁品位高。
? SiO2含量对烧结矿产质量指标有一定的影响。高硅烧结矿熔 剂的配加量增加,使得烧结混合料制粒性能得到改善,烧结速 度增加,同时烧结的粘结相数量提高,因此烧结矿成品率有所 提高,烧结利用系数提高。
烧结工艺基础知识培训
新疆金特钢铁股份有限公司烧结分厂 培训人:何力虎
2019年3月
第一部分 烧结的定义与意义
? 烧结工艺的产生
? 烧结方法在冶金生产中的应用,起初是为了处理矿山 、冶金、化工厂的废弃物(如富矿粉、高炉除尘、轧 钢皮、均热炉渣、硫酸渣等)以便回收利用。
? 随着钢铁工业的发展,矿石开采量和矿粉的生成量增 加,另由于长期开采和消耗造成能冶炼的富矿越来越 少,贫矿(含铁 25~30%) 直接入炉冶炼很不经济,且 我国贫矿资源约占 80%以上,因此对贫矿进行磁选处 理产生铁精粉,但粉状物料不适合直接冶炼。
? 活性度是指冶金石灰水化的反应速度,即石灰水化后用 4NHCL中和的毫升数。
? 生烧是指未分解的石灰石,其主要成分是CaCO3,不能被 水化。
最新烧结工艺介绍讲课稿

烧结工艺的简单介绍目前,随着市场竞争的加剧,钢铁工业设备向大型化发展,对原料的要求日益提高,而高炉炼铁生产技术指标的提高,主要依靠入炉原料性质的改善,烧结矿是我国高炉的主要入炉料,因此,保证和提高烧结矿的质量,是保证钢铁工业稳定发展的重要手段。
一、烧结的概念烧结是钢铁生产工艺中的一个重要环节,它是将各种粉状含铁原料,配入适量的燃料和熔剂,加入适量的水,经混合和造球后在烧结设备上使物料发生一系列物理化学变化,将矿粉颗粒黏结成块的过程。
二、烧结矿的来源以及意义铁矿粉造块目前主要有两种方法:烧结法和球团法。
两种方法所获得的块矿分别为烧结矿和球团矿。
球团法通常在选贫矿的地区采用,尤其是北美地区。
而在有天然富矿可以开采使用的地方,烧结法则是一种成本较低的方法,在世界的其它地区被广泛采用。
虽然新的炼铁方法会不断出现,但是烧结矿的需求在很长一段时间内仍将保持在较高的水平。
在我国,高炉入炉的炉料90%以上都是靠烧结法提供的。
因此,铁矿石烧结对我国的钢铁工业有重大的意义。
三、烧结工艺流程介绍经烧结而成的有足够强度和粒度的烧结矿可作为炼铁的熟料。
利用烧结熟料炼铁对于提高高炉利用系数、降低焦比、提高高炉透气性保证高炉运行均有一定意义。
烧结生产的工艺流程如下图所示。
主要包括烧结料的准备,配料与混合,烧结和产品处理等工序。
目前生产上广泛采用带式抽风烧结工艺流程:1、烧结的原材料准备:含铁原料:含铁量较高、粒度<5mm的矿粉,铁精矿,高炉炉尘,轧钢皮,钢渣等。
一般要求含铁原料品位高,成分稳定,杂质少。
熔剂:要求熔剂中有效CaO含量高,杂质少,成分稳定,含水3%左右,粒度小于3mm的占90%以上。
在烧结料中加入一定量的白云石,使烧结矿含有适当的MgO,对烧结过程有良好的作用,可以提高烧结矿的质量。
燃料:主要为焦粉和无烟煤。
对燃料的要求是固定碳含量高,灰分低,挥发分低,含硫低,成分稳定,含水小于10%,粒度小于3mm的占95%以上。
烧结工艺基础知识培训讲座

水分在烧结过程中的行为和作用 烧结料中的水分主要来源于矿石、熔剂、燃料带入的水、混合 料混匀制粒时添加的水、空气中带入的水、燃料中碳氢化合物 燃烧时产生的水以及混合料中矿物分解的化合水。
一、水分的蒸发过程
? 水分在烧结过程中的蒸发可以分为以下几个阶段: ? 预热阶段
当热气体与湿料接触时,在一段很短时间内,蒸发过程进行得 较为缓慢,物料含水量没有多大变化,但物料温度却有了明显 的升高,在这段期间内,热量主要消耗于预热混合料,直至传 给物料的热量与用于汽化的热量之间达到平衡为止,这段时期 通常称为“预热阶段”。
? 常用的配料方法:容积配料法(基于物料具有一定的堆密度, 借助给料设备对添加料的容积进行控制)、重量配料法(按原 料的重量进行配料的一种方法,借助于电子皮带秤和定量给料 自动调节系统来实现自动配料。化学成分配料(借助于X射线 荧光仪分析混合料化学组成,通过电子计算机控制混合料化学 成分波动)
? 影响配料作业的因素
? 起源于资本主义发展较早的英国、瑞典和德国。
? 土烧(平地吹) ----箱式烧结机----环式烧结机 ---带式烧结机
? 1910年第一台带式烧结机在美国投产
? 1949年以前,鞍山建有 10台烧结机,总面积 330 ㎡,但工艺设备落后,生产能力低,最高产量仅 十几万吨。
? 截止2009年,全国钢铁企业拥有烧结机 210台, 总面积3690㎡,年产烧结矿 1.5亿吨。
? 当前世界最大的烧结机为 648㎡(前苏联)。
? 烧结方法的分类
? 按照设备和供风方法的不同可分为以下几种 1、鼓风烧结:平地吹(土烧结) 2、抽风烧结: (1)连续式:带式烧结机和环式烧结机 (2)间歇式:盘式烧结机 3、在烟气中烧结:回转窑烧结和悬浮烧结。
特种陶瓷烧结工艺课件

0
CONVENTIONAL HEATING MICROWAVE HEATING
100
200
300
400
500
600
TIME, MIN.
•特种陶瓷烧结工艺
•42
2 烧结工艺
•特种陶瓷烧结工艺
•43
2 烧结工艺
无添加剂 1700oC, 10 min in H2
添加氧化铬 1700oC, 10 min in H2
5)放电等离子体烧结(SPS)
2 烧结工艺
•特种陶瓷烧结工艺
•37
2 烧结工艺
•特种陶瓷烧结工艺
•38
2 烧结工艺
•特种陶瓷烧结工艺
•39
6)微波烧结
2 烧结工艺
•特种陶瓷烧结工艺
•40
2 烧结工艺
•特种陶瓷烧结工艺
•41
2 烧结工艺
TEMPERATURE, °C
1400 1200 1000
1 烧结理论
•特种陶瓷烧结工艺
•11
1.3 烧结影响因素
1 烧结理论
•特种陶瓷烧结工艺
•12
1.4 烧结阶段
1 烧结理论
•特种陶瓷烧结工艺
•13
1.4 烧结阶段
1 烧结理论
颗粒重排,接触处产生键合,
烧结初期
空隙变形缩小,但固-气总表面
积没有变化。
烧
结
的
传质开始,粒界增大,空隙进
三
烧结中期
一步变形缩小,但保持连同,
•特种陶瓷烧结工艺
•31
2)热压烧结
2 烧结工艺
•热压烧结促进致密化的机 理大概有以下几种: (1) 由于高温下的塑性流动, (2)由于压力使颗粒重排, 使颗粒碎裂以及晶界滑移 而形成空位浓度梯度,(3) 由于空位浓度梯度的存在 而加速了空位的扩散。
烧结新技术培训第二讲镶嵌式烧结工艺
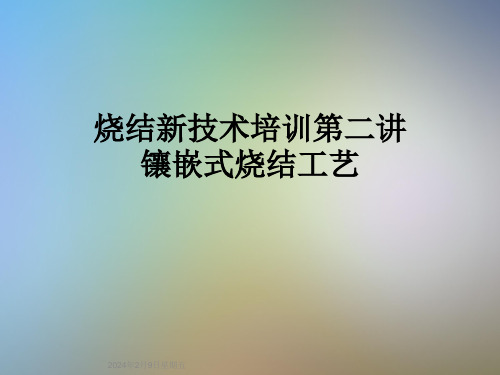
<焦炭燃烧速率>
(5)
方程组中与烧结料层结构有关的参数: ε- 料层的孔隙度,取决于料粒的粒度分布 αs- 传热面积,取决于料粒的直径和形状 ug- 气流速度,取决于料层的孔隙度 kc- 焦炭颗粒的燃烧反应速度,取决于焦炭在料粒中的 存在形式,即添加方式和制粒方式
因此,在MEBIOS烧结工艺中,采用了大颗粒的料粒, 即烧成层,来改善烧结床的透气性和热效率。因此,优 化烧成层的组成、形状和大小与排列方式是使MEBIOS 过程的优点发挥到最大的关键问题。
New Sintering Process through Designing of Composite Granulation & Bed Structure
项目的主要目的: - 研究豆铁矿和针铁矿的特性,了解其在烧结过程中的行 为。 - 针对矿石的特性,进行有关原料混合、造粒、床层结构 的最优化设计和烧结矿冶金性能的基础研究。
燃料种类对烧结过程的影响
按单位质量的发热量排列,从大到小依次为重油、甲烷、 焦炭。 按单位氧消耗量的发热量排列,轧钢皮最大。从抽入料层 中的空气的角度,它是最有效的一种燃料。
即使烧结原料中不含金属铁或低价铁,烧结过程中也会发 生低价铁的氧化放热 加热阶段发生吸热反应和冷却阶段发生放热反应,可以被 用于料层中温度的分布 使用含碳物质和金属铁/低价铁时的烧结料层孔隙度的变化 很不相同,因为前者在燃烧完毕会消失,而后者的体积和 重量却会增加
所以,不仅要控制液相的生产量,而且要通过控制成分来 控制液相的流动性
通过改变焦炭的添加和制粒方式,优化焦炭在料粒中的分 布,达到改善燃烧和传热、烧结反应(包括液相生成、矿 物结晶等)的目的
JFE公司福山5号烧结机 HPS球团烧结矿工艺流程的改造
烧结生产工艺技术讲课1

烧结介绍 烧结原料 烧结工艺及配置 烧结岗位设置 建72㎡烧结机缘由 打造绿色烧结
铁矿粉烧结是重要的造矿技术之一。由于开采时产生 大量的铁矿粉,特别是贫铁矿富选促进了铁精矿粉烧结的 生产和发展,使铁矿粉烧结成为规模最大的造块作业。其 物料的处理量约占钢铁联合企业的第二位(仅次于炼铁生 产),能耗仅次于炼铁及轧钢而居第三位,成为现代钢铁 企业的重要生产工序。铁矿粉烧结要求烧结矿具有很好的 物理、冶金性能。烧结矿经历冶炼高温过程,要求有一定 的热强度,即在高温还原气氛下耐压、耐磨及耐热爆裂性 能;烧结矿在高炉内经历物理化学反应,要求它具有良好 的冶金性能,如还原性、软化性、熔滴性等。铁矿粉烧结 技术的困难还在于追求合理的经济效果,因此,铁矿粉烧 结是一门技术复杂的专门学科。
需混合料7971t,按单一矿生产配比:镍
矿粉94%(7324t)、生石灰6%(478t)、
焦粉7%(558t)。
生灰消化除尘
本装置采用了粉尘迷宫运行和流体动力学技术,使
风机产生的有效风力均衡地分配到各除尘管道内部,
使生石灰在消化过程中所产生的热蒸汽和粉尘均匀
的全部经过高压水沫和水箱内部水的处理和过滤,
我厂烧结原料主要是红土镍矿,红土
镍矿资源是硫化镍矿岩体风化―淋滤―沉
积形成的地表风化壳性矿床,和普通铁矿
相比,红土镍矿品位低,二氧化硅含量高,
含水量大,一般都是毛矿,需要进行二次
加工方能使用。
世界上红土镍矿分布在赤道线南北30度以 内的热带国家,集中分布在环太平洋的热带 ――亚热带地区,主要有: 新喀里多利亚镍矿带 印度尼西亚:摩鹿加镍矿带、苏拉威西镍矿带; 菲律宾:巴拉望地区镍矿带; 澳大利亚:昆士兰镍矿带; 巴西:米纳斯吉拉斯镍矿带、戈亚斯镍矿带; 古巴:奥连特镍矿带等。
烧结工艺精讲
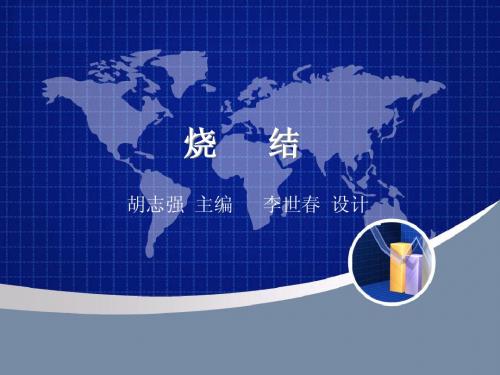
晶粒生长的影响因素
• 1.夹杂物如杂质、气孔等阻碍作用 • 晶界在移动时可能会遇到夹杂物,晶界为了通过夹杂物, 界面能就被降低,降低的量正比于夹杂物的横截面积。通 过障碍以后,弥补界面又要付出能量,结果使界面继续前 进能力减弱,界面变得平直,晶粒生长逐渐停止。 • 2.晶界上液相的影响 • 少量液相使晶界上形成两个新的固-液界面,从而界面移 动的推动力降低,扩散距离增加,因此少量液相可以起到 抑制晶粒长大的作用。但当坯体中有大量液相时,可以促 进晶粒的生长和出现二次再结晶。 • 3.晶粒生长极限尺寸 • 烧结达到气孔的体积分数为10%时,晶粒长大就停止了, 这也是普通烧结中坯体终点密度低于理论密度的原因。
影响烧结的因素
1.原始粉料的粒度 1.原始粉料的粒度 • 从烧结速率考虑:无论在固态或液态的烧结中,细颗粒由 于曲率半径小,从而增加的烧结的推动力—表面能之差, 缩短了原子扩散距离,提高了颗粒在液相中溶解度而导致 烧结过程的加速。 • 从防止二次再结晶考虑:起始颗粒粒径必须细而均匀,如 果细颗粒中有少量大颗粒存在,则易发生晶粒异常生长而 不利用烧结。 • 如果烧结速率与起始粒度的1/3次方成正比,从理论上计 算,当起始粒度从2μm减小到0.5μm,烧结速率将增加64 倍,这相当于粒度小的粉料烧结温度降低了150—300℃。 • 一般氧化物材料最适宜的粉末粒度为0.05—0.5μm。
严格控制温度即保温的重要性
• 当烧结达到晶界移动速率Vb=Vp时,烧结过程已接近完成。 严格控制温度是十分重要的,继续维持Vb=Vp,气孔易迅 速排除而实现致密化。此时烧结体应适当保温,如果再继 续升高温度,由于晶界的速率随温度呈指数增加,必然导 致Vb>>Vp,晶界越过气孔而向曲率中心移动,使气孔包入 晶粒内部,气孔一旦包入晶粒内部,只能通过体积扩散来 排除,而这是十分困难的。 • 随着烧结的进行,气孔逐渐缩小,而气孔内的气压不断增 大,当增加至2γ/r时,即气孔内气压等于烧结推动力, 烧结停止。如果继续升高温度,气孔内的气压继续增大, 这时气孔不仅不能缩小反而膨胀,对致密化不利。 • 烧结如果不采取特殊措施是不可能达到坯体完全致密化的, 如果要获得接近理论密度的制品,必须采用气氛或真空烧 结和热压烧结等方法。
烧结技术讲稿
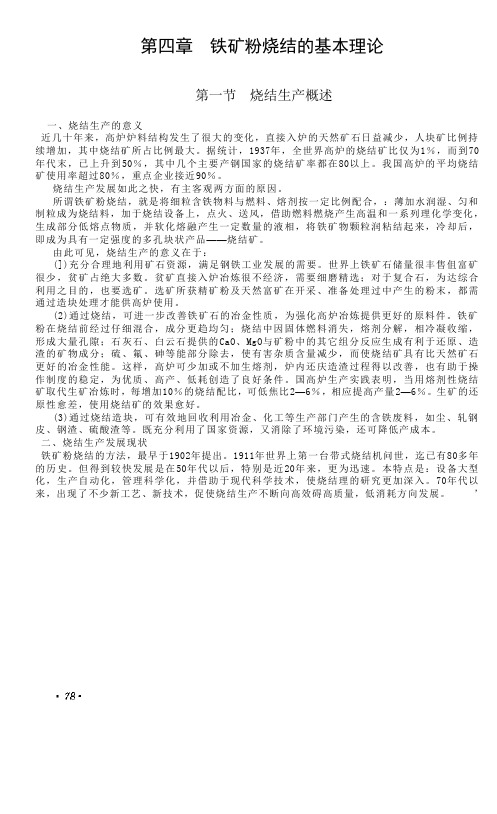
第四章铁矿粉烧结的基本理论第一节烧结生产概述一、烧结生产的意义近几十年来,高炉炉料结构发生了很大的变化,直接入炉的天然矿石日益减少,人块矿比例持续增加,其中烧结矿所占比例最大。
据统计,1937年,全世界高炉的烧结矿比仅为1%,而到70年代末,已上升到50%,其中几个主要产钢国家的烧结矿率都在80以上。
我国高炉的平均烧结矿使用率超过80%,重点企业接近90%。
烧结生产发展如此之快,有主客观两方面的原因。
所谓铁矿粉烧结,就是将细粒含铁物料与燃料、熔剂按一定比例配合,:薄加水润湿、匀和制粒成为烧结料,加于烧结设备上,点火、送风,借助燃料燃烧产生高温和一系列理化学变化,生成部分低熔点物质,并软化熔融产生一定数量的液相,将铁矿物颗粒润粘结起来,冷却后,即成为具有一定强度的多孔块状产品——烧结矿。
由此可见,烧结生产的意义在于:(])充分合理地利用矿石资源,满足钢铁工业发展的需要。
世界上铁矿石储量很丰售伹富矿很少,贫矿占绝大多数。
贫矿直接入炉冶炼很不经济,需要细磨精选;对于复合石,为达综合利用之目的,也要选矿。
选矿所获精矿粉及天然富矿在开采、准备处理过中产生的粉末,都需通过造块处理才能供高炉使用。
(2)通过烧结,可进一步改善铁矿石的冶金性质,为强化高炉冶炼提供更好的原料件。
铁矿粉在烧结前经过仔细混合,成分更趋均匀;烧结中因固体燃料消失,熔剂分解,相冷凝收缩,形成大量孔隙;石灰石、白云石提供的CaO、MgO与矿粉中的其它组分反应生成有利于还原、造渣的矿物成分;硫、氟、砷等能部分除去,使有害杂质含量减少,而使烧结矿具有比天然矿石更好的冶金性能。
这样,高炉可少加或不加生熔剂,炉内还庆造渣过程得以改善,也有助于操作制度的稳定,为优质、高产、低耗创造了良好条件。
国高炉生产实践表明,当用熔剂性烧结矿取代生矿冶炼时,每增加10%的烧结配比,可低焦比2—6%,相应提高产量2—6%。
生矿的还原性愈差,使用烧结矿的效果愈好。
(3)通过烧结造块,可有效地回收利用冶金、化工等生产部门产生的含铁废料,如尘、轧钢皮、钢渣、硫酸渣等。
烧结工艺技术培训PPT演示课件
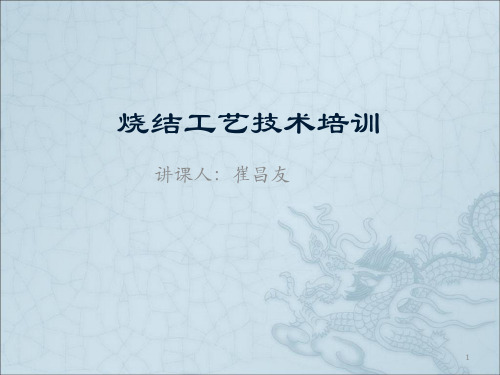
烧结的目的和意义
1、能保证高炉料柱的透气性和降低高炉焦比
2、能去除铁矿中的有害元素。 3、能“废物利用”,如高炉炉尘,转炉炉尘等 总之,能使高炉冶炼达到高产、优质、低耗和长 寿的目的。
4
生产工艺流程
5
烧结厂技术经济指标
1、烧结机生产能力指标,它包括利用系数、 台时产量、作业率、运转台时、事故率等
10
烧结配料
它分为配料目的、要求和方法等
11
配料的目的
1、保证烧结矿的化学成分和物理性质稳定, 满足高炉冶炼要求。
2、保证烧结料具有良好的透气性以获得较 高的烧结生产率。
12
配料的要求
1、准确,把实际下料量的波动值控制在允 许的范围内,不发生大的偏差。
2、保证烧结矿的含铁量、碱度、亚铁和含 硫量等主要指标控制在规定的范围内。
不要忽视燃料燃烧后灰分的化学成分,如 焦抹灰分里大约含一半的二氧化硅并含有 少量的氧化钙。
最好利用计算机计算
17
烧结料的混合
烧结料混合的目的: 一是将配好的各种原料充分混匀,获得化
学成分均一的混合料。 二是对混合料加水润湿和制粒,通入蒸汽
预热获得必要的料温。
混匀和制粒的方法: 1、一段混合法 2、二段混合法
22
布混合料
布混合料的要求: 1、布料应连续供给,防止中断,保持料层厚
度一定。 2、按规定的料层厚度布料,沿台车长度和宽
度方向料面平整。 3、沿台车高度方向,混合料的粒度、成分分
布合理,能适应烧结过程的内在规律。 4、保证布到台车上的料具有一定的松散性,
防止产生堆积和压紧。
23
影响布料均匀的因素
20
布料
烧结厂生产工艺讲座
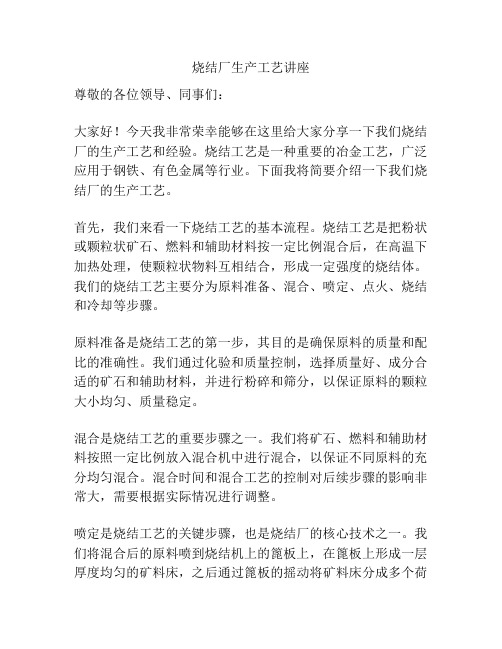
烧结厂生产工艺讲座尊敬的各位领导、同事们:大家好!今天我非常荣幸能够在这里给大家分享一下我们烧结厂的生产工艺和经验。
烧结工艺是一种重要的冶金工艺,广泛应用于钢铁、有色金属等行业。
下面我将简要介绍一下我们烧结厂的生产工艺。
首先,我们来看一下烧结工艺的基本流程。
烧结工艺是把粉状或颗粒状矿石、燃料和辅助材料按一定比例混合后,在高温下加热处理,使颗粒状物料互相结合,形成一定强度的烧结体。
我们的烧结工艺主要分为原料准备、混合、喷定、点火、烧结和冷却等步骤。
原料准备是烧结工艺的第一步,其目的是确保原料的质量和配比的准确性。
我们通过化验和质量控制,选择质量好、成分合适的矿石和辅助材料,并进行粉碎和筛分,以保证原料的颗粒大小均匀、质量稳定。
混合是烧结工艺的重要步骤之一。
我们将矿石、燃料和辅助材料按照一定比例放入混合机中进行混合,以保证不同原料的充分均匀混合。
混合时间和混合工艺的控制对后续步骤的影响非常大,需要根据实际情况进行调整。
喷定是烧结工艺的关键步骤,也是烧结厂的核心技术之一。
我们将混合后的原料喷到烧结机上的篦板上,在篦板上形成一层厚度均匀的矿料床,之后通过篦板的摇动将矿料床分成多个荷载,然后进行点火。
通过喷定,我们可以使原料在矿料床的重力和风力作用下形成适当的孔隙结构,为后续的烧结提供条件。
烧结是烧结工艺的核心步骤。
点火后,我们将矿料床加热到一定温度,矿石中的结晶水和化学结合水蒸发,氧化反应发生,烧结过程中产生的热量使矿石颗粒之间形成一定联系。
矿石颗粒在高温下熔结,形成一定强度的烧结体。
烧结结束后,需要对烧结体进行冷却。
我们采用风冷和水冷相结合的方式进行冷却。
通过控制冷却速率,可以使烧结体的结构更加稳定,提高其机械强度和冷热韧性。
以上就是我们烧结厂的生产工艺的基本流程。
当然,烧结工艺的具体实施还需要根据不同的矿石性质、产品要求和设备状况进行调整和优化。
为了提高生产效率和产品质量,我们不断引进新技术、新设备,并加强管理,改善工艺流程。
硬质合金烧结工艺
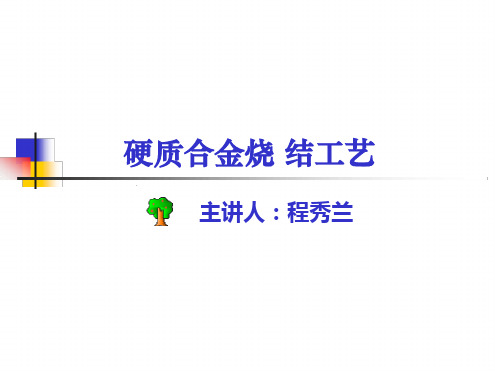
2) 影响碳化钨晶粒长大的因素
1.液相数量 影响液相数量的主要因素是: a. 烧结温度
影响液相数量的主要因素是:
a.烧结温度
b.含钴量 c.含碳量
②混合料的状态
? a.原始粉末的粒度 ? b.粒度分布均匀性 ? c.磨碎程度
相;碳量过剩,则为WC+C+ 液相;碳适量,则为WC+ 液相。
? 1.1.4. 冷却阶段(烧结温度~室温)
? 冷却速度只影响γ 相成分,不影响组织,最终组织为 WC+ γ。 ? WC-TiC- CO合金的烧结:与WC – CO 合金的烧结基本类似 。其主要区别表现 在液相的成分,出现液相的温度和所得 合金组织的不同。
? 烧结主要是物理过程,烧结体 致密化,碳化物晶粒长大,粘 结相成分的变化以及合金结构 的形成等。
图1W-C-C O系状态图在凝固温度下的等温切面
1. 1 烧结过程四阶段及相应的组织转变
1.1.1. 脱蜡预烧阶段(<800℃) 1) 成形剂的脱除 2) 粉末表面氧化物还原 3) 粉末颗粒相互之间的状态发生变化 1.1.2. 固相烧结阶段(800℃~共晶温度) ? 共晶温度是指缓慢升温时,烧结体中开始出现共晶液相的温度,对
图3 YG15合金烧结时试样长度为 50.5毫米的收缩过程 1—舟皿上层试样 2—舟皿下层试 样
? 1.2烧结体的致密化
? 1.2.1.致密化机理:致密化机理是流动过程 。
? 1) 固相烧结时的扩散与塑性流动 ? 2)液相烧结时的重排、溶解——析出与界面结构的形成 ? ①重排: ? 必要前提: ? ② 溶解-析出 ? ③界面结构的形成
烧结工艺讲座

二、烧结发展概况
1、烧结发展概况 烧结的历史虽已有一个多世纪,但相对冶炼史,它还是一个年 青的小伙子。它起源于资本主义发展较早的英国、瑞典和德国。大 约1870年开始,这些国家就开始“土烧结”或使用烧结锅。美国在 1892年也出现烧结锅,1905年美国曾用大型烧结锅处理高炉炉尘。 世界上第一台带式烧结机于1910年在美国诞生。烧结机的面积为 8.325㎡(1.07m×7.78m),用来处理高炉炉尘,日产烧结矿140t。 它的出现,是烧结史上的重大革命。 但二十世纪五十年代以前,由于钢铁工业发展缓慢,天然富矿 充足,所以烧结生产的发展不快。随着钢铁工业发展,天然富矿减 少,选矿兴起,粉、精矿增加,烧结工业迅速发展。特别近三十年, 为了拓宽含铁资源,采用“精料方针”提高高炉效益,即所谓“七 分原料三分操作”,烧结更是迅猛发展。工艺流程不断完善,规模 不断大型化,技术愈趋现代化。
5.4 混合料的烧结
烧结作业是烧结生产工艺的中心环节,是检验并反映上 述工艺质量的一个工序,也是烧结生产最终产品的工序。 采用带式烧结机抽风烧结时,其工作过程如下:当 空台车运行到烧结机头部的布料机下面时,辅底料和烧结 混合依次装在台车上,经过点火器时混合 料中的固体然料 被点然,与此同时,台车下部的真空室开始抽风,使烧结 过程自上而下地进行,控制台车速度,保证台车到达机尾 时,全部料都已烧结完毕,粉状物料变成块状的烧结矿, 当台车从机尾进入弯道时,烧结矿被卸下来。空台车靠自 重或尾部星轮驱动,沿下轨道回到烧结机头部,在头部星 轮作用下,空台车被提升到上部轨道,又重复布料、点火、 烧卸矿等工艺环节。
在我国烧结矿的冷却方式主要有鼓风冷却、抽风冷却 和机上冷却几种。我厂采用环冷机鼓风冷却,冷却后的温 度要求低于150℃,便于下步烧结矿的运输。
一、烧结基本原理精讲

一、烧结(1)、烧结基本原理烧结是粉末冶金生产过程中最基本的工序之一。
烧结对最终产品的性能起着决定性作用,因为由烧结造成的废品是无法通过以后的工序挽救的;相反,烧结前的工序中的某些缺陷,在一定的范围内可以通过烧结工艺的调整,例如适当改变温度,调节升降温时间与速度等而加以纠正。
烧结是粉末或粉末压坯,加热到低于其中基本成分的熔点温度,然后以一定的方法和速度冷却到室温的过程。
烧结的结果是粉末颗粒之间发生粘结,烧结体的强度增加。
在烧结过程中发生一系列物理和化学的变化,把粉末颗粒的聚集体变成为晶粒的聚结体,从而获得具有所需物理,机械性能的制品或材料。
烧结时,除了粉末颗粒联结外,还可能发生致密化,合金化,热处理,联接等作用。
人们一般还把金属粉末烧结过程分类为:1、单相粉末(纯金属、古熔体或金属化合物)烧结;2、多相粉末(金属—金属或金属—非金属)固相烧结;3、多相粉末液相烧结;4、熔浸。
通常在目前PORITE微小轴承所接触的和需要了解的为前三类烧结。
通常在烧结过程中粉末颗粒常发生有以下几个阶段的变化:1、颗粒间开始联结;2、颗粒间粘结颈长大;3、孔隙通道的封闭;4、孔隙球化;5、孔隙收缩;6、孔隙粗化。
上述烧结过程中的种种变化都与物质的运动和迁移密切相关。
理论上机理为:1、蒸发凝聚;2、体积扩散;3、表面扩散;4、晶间扩散;5、粘性流动;6、塑性流动。
(2)、烧结工艺2-1、烧结的过程粉末冶金的烧结过程大致可以分成四个温度阶段:1、低温预烧阶段,在此阶段主要发生金属的回复及吸附气体和水分的挥发,压坯内成形剂的分解和排除等。
在PORITE微小铜、铁系轴承中,用R、B、O(Rapid Burning Off)来代替低温预烧阶段,且铜、铁系产品经过R、B、O 后会氧化,但在本体中可以被还原,同时还可以促进烧结。
2、中温升温烧结阶段,在此阶段开始出现再结晶,首先在颗粒内,变形的晶粒得以恢复,改组为新晶粒,同时颗粒表面氧化物被完全还原,颗粒界面形成烧结颈。
烧结生产工艺流程知识讲解
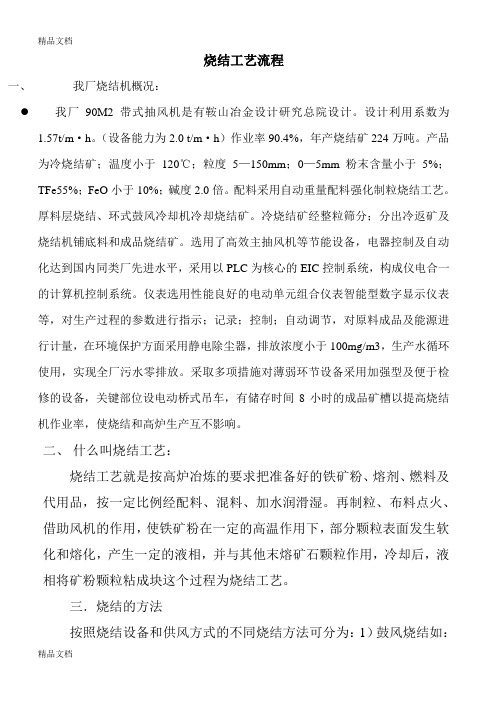
烧结工艺流程一、我厂烧结机概况:我厂90M2带式抽风机是有鞍山冶金设计研究总院设计。
设计利用系数为1.57t/m·h。
(设备能力为2.0 t/m·h)作业率90.4%,年产烧结矿224万吨。
产品为冷烧结矿;温度小于120℃;粒度5—150mm;0—5mm粉末含量小于5%;TFe55%;FeO小于10%;碱度2.0倍。
配料采用自动重量配料强化制粒烧结工艺。
厚料层烧结、环式鼓风冷却机冷却烧结矿。
冷烧结矿经整粒筛分;分出冷返矿及烧结机铺底料和成品烧结矿。
选用了高效主抽风机等节能设备,电器控制及自动化达到国内同类厂先进水平,采用以PLC为核心的EIC控制系统,构成仪电合一的计算机控制系统。
仪表选用性能良好的电动单元组合仪表智能型数字显示仪表等,对生产过程的参数进行指示;记录;控制;自动调节,对原料成品及能源进行计量,在环境保护方面采用静电除尘器,排放浓度小于100mg/m3,生产水循环使用,实现全厂污水零排放。
采取多项措施对薄弱环节设备采用加强型及便于检修的设备,关键部位设电动桥式吊车,有储存时间8小时的成品矿槽以提高烧结机作业率,使烧结和高炉生产互不影响。
二、什么叫烧结工艺:烧结工艺就是按高炉冶炼的要求把准备好的铁矿粉、熔剂、燃料及代用品,按一定比例经配料、混料、加水润滑湿。
再制粒、布料点火、借助风机的作用,使铁矿粉在一定的高温作用下,部分颗粒表面发生软化和熔化,产生一定的液相,并与其他末熔矿石颗粒作用,冷却后,液相将矿粉颗粒粘成块这个过程为烧结工艺。
三.烧结的方法按照烧结设备和供风方式的不同烧结方法可分为:1)鼓风烧结如:烧结锅、平地吹;2)抽风烧结:①连续式如带式烧结机和环式烧结机等;②间歇式如固定式烧结机有盘式烧结机和箱式烧结机,移动式烧结机有步进式烧结机;3)在烟气中烧结如回转窑烧结和悬浮烧结。
四.烧结矿的种类:CaO/SiO2小于1为非自熔性烧结矿;碱度为1-1.5是自熔性烧结.矿碱度为1.5~2.5是高碱度烧结矿;大于2.5是超高或熔剂性烧结矿。