烧结烟气余热利用
莱钢烧结厂265m 2烧结系统环冷烟气的余热利用
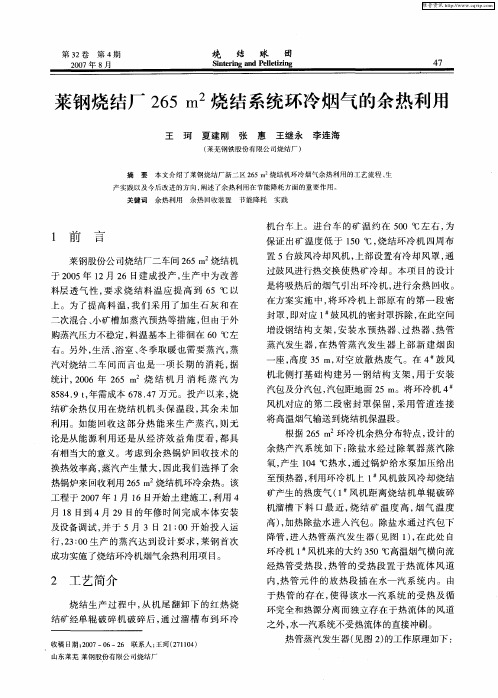
环 冷机 1 机来 的大约 30℃高 温烟气 横 向流 风 5 经 热管受 热 段 , 管 的受 热段 置 于热 流 体 风 道 热 内 , 管元 件 的 放 热 段 插 在 水一 汽 系统 内。 由 热 于热 管 的存 在 , 得 该 水一 汽 系 统 的受 热 及 循 使 环 完全 和热 源分离 而 独立 存 在 于热 流 体 的风 道 之 外 , 汽 系统不 受热 流体 的直接 冲刷 。 水一 热 管蒸 汽发生 器 ( 图 2 的工作原 理如 下 : 见 )
二次混合、 小矿槽加蒸汽预热等措施 , 由于外 但
购蒸 汽压 力不稳 定 , 料温 基 本上 徘 徊在 6 0℃左 右 。另外 , 生活 、 室 、 季取 暖 也需 要 蒸 汽 , 浴 冬 蒸
汽对烧结 二 车 间而 言 也 是 一 项 长 期 的消 耗 , 据 统计 , 06年 25 m 20 6 烧 结 机 月 消 耗 蒸 汽 为 88 . , 需成本 6 84 54 9t年 7 .7万元 。投 产 以来 , 烧 结矿 余热 仅 用 在 烧 结 机 机 头 保 温 段 , 余 未 加 其 利用 。如 能 回收 这 部 分 热 能 来 生 产 蒸 汽 , 无 则
1 过热蒸汽
自 机 部 环冷 下
1
L 整一热 分包 笪 过器j 汽l i
自环 冷 机 1 # 风机高 温烟气
. I翠 气 — 上 对 供 接 壹 烟 L 外 汽 点
根 据 2 5 m 环 冷 机余 热分 布 特点 , 计 的 6 设
一种烧结环冷机烟气余热梯级利用系统
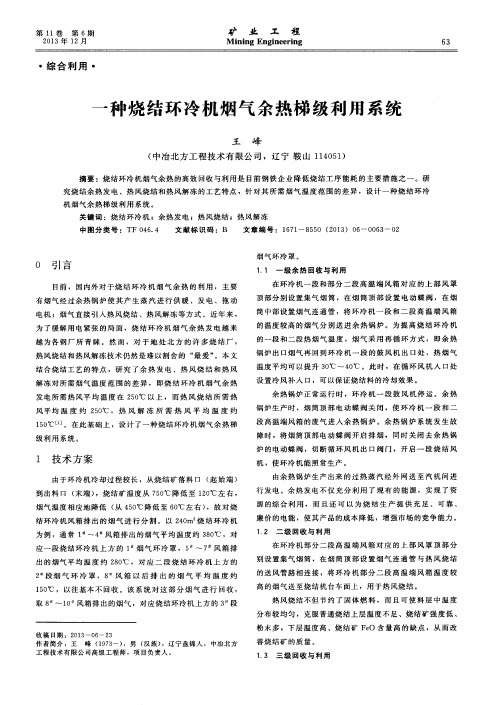
矿 业 工 程
Mi ni ng Eng i n e e r i ng 6 3
・
综合 利用 ・
一
种 烧 结 环 冷 机 烟 气 余 热 梯 级 利 用 系 统
王 峰 ( 中冶北 方工 程技术 有 限公 司 ,辽宁 鞍 山 1 1 4 0 5 1 )
1 . 2 二 级 回 收 与 利 用
应一段烧结环冷 机上方 的 1 烟 气 环 冷 罩 ,5 ~7 风 箱 排
出 的烟 气 平 均 温 度 约 2 8 0  ̄ C,对 应 二 段 烧 结 环 冷 机 上 方 的
在 环 冷 机 部 分 二 段 高 温 端 风 箱 对 应 的 上 部 风 罩 顶 部 分 别 设 置 集 气 烟 筒 ,在 烟 筒 顶 部 设 置 烟 气 连 通 管 与 热 风 烧 结 的送 风 管 路 相 连 接 ,将 环 冷 机 部 分 二 段 高 温 端 风 箱 温 度 较 高 的烟 气 送 至 烧 结 机 台 车 面上 ,用 于 热 风 烧 结 。 热 风 烧 结 不 但 节 约 了 固体 燃 料 ,而 且 可 使 料 层 中 温 度 分 布 较 均 匀 ,克 服 普 通 烧 结 上 层 温 度 不 足 、烧 结 矿 强 度 低 、 粉 末 多 ,下 层 温 度 高 、烧 结 矿 F e O 含 量 高 的缺 点 ,从 而 改
有 烟 气 经 过 余 热 锅 炉 使 其 产 生 蒸 汽 进 行 供 暖 、发 电 、 拖 动
1 . 1 一级 余 热 回 收 与 利 用
在 环 冷 机 一 段 和部 分 二 段 高 温 端 风 箱 对 应 的 上 部 风 罩 顶 部 分 别 设 置 集 气 烟 筒 ,在 烟 筒 顶 部 设 置 电 动 蝶 阀 ,在 烟 筒 中部 设 置 烟 气 连 通 管 ,将 环 冷 机 一 段 和 二 段 高 温 端 风 箱
烧结厂余热利用技术简介

烧结厂余热利用技术简介1. 引言烧结是一种将粉煤灰、石灰石或其它成分相似的原料通过加热使之部分熔化,然后回结固化成块状的冶金过程。
这个过程产生的高温烟气和废热在烧结厂通常都被排放到大气中。
然而,随着对能源资源的需求和环境保护意识的增强,如何有效利用烧结厂的余热已成为研究和开发的重点。
本文将简要介绍几种常见的烧结厂余热利用技术,并分析其优点和局限性。
2. 烧结厂余热利用技术2.1 热交换器技术热交换器技术是一种常见的烧结厂余热利用技术。
热交换器可以将高温烟气中的热能传递给废水、蒸汽或其他介质,以实现能量的回收和利用。
热交换器通常包括换热管道和换热器设备。
热交换器技术的优点在于可以提供连续的热能供应,并减少对外部能源的需求。
然而,此技术的局限性在于热交换器设备的成本较高,维护困难,并且对脏污、腐蚀性介质敏感。
2.2 ORC技术ORC技术(有机朗肯循环)是一种将烧结厂余热转化为电力的技术。
ORC系统通过将高温烟气中的热能转移到有机工质中,然后通过有机工质的蒸汽驱动涡轮发电机产生电力。
与传统蒸汽发电系统相比,ORC技术可以在较低的温度下工作,提高了热能转化的效率。
此外,ORC技术还可以通过调整有机工质的选用来适应不同温度下的余热利用。
然而,该技术需要较高的初投资成本,并且对有机工质的选择和运行维护要求较高。
2.3 废热蒸汽利用技术废热蒸汽利用技术是一种将烧结厂余热转化为蒸汽以供其他生产过程使用的技术。
在烧结厂中,产生的高温烟气可以通过余热锅炉将废热转化为蒸汽,然后再将蒸汽输送到其他工序中进行能量回收。
废热蒸汽利用技术可以减少对外部能源的需求,并提高能源利用效率。
然而,该技术的缺点在于需要较大的设备投资,且对蒸汽管道的要求较高。
3. 总结烧结厂余热利用技术是一种重要的能源回收利用手段,可以减少环境污染,降低能源消耗,提高能源利用效率。
本文介绍了几种常见的烧结厂余热利用技术,并分析了它们的优点和局限性。
无论是热交换器技术、ORC技术还是废热蒸汽利用技术,都需要根据具体的烧结厂情况和需求来选择和应用。
科技成果——烧结废气余热循环利用工艺技术

科技成果——烧结废气余热循环利用工艺技术适用范围钢铁行业烧结行业现状截止2014年,我国大中型烧结机共约600台,年产烧结矿约8亿t,烧结工序的平均能耗为55kgce/t。
烧结废气余热循环利用可节省烧结能耗5%以上,减少烧结CO2排放以及废气排放总量20%以上。
从2012年起,宝钢、宁波钢铁、沙钢等烧结机废气循环改造工程已陆续建成投运。
成果简介1、技术原理烧结低温废气自烧结支管风箱/环冷机排出后,再次被引入、通过烧结料层时,因热交换和烧结料层的自动蓄热作用,可以将其中的低温显热供给烧结混合料,与此同时热废气中的二噁英、PAHs、VOC 等有机污染物在通过烧结料层中高达1200℃以上的烧结带时被激烈分解,NOx在通过高温烧结带时亦能够通过热分解被部分破坏,尽管二噁英、PAHs、VOC等有机污染物在烧结预热带又可能重新合成,但废气循环烧结仍然可以显著减少有机污染物的排放,并大幅度削减废气排放总量。
烧结废气余热循环利用可以富集SO2,提高脱硫效率,并使NOx被降解、二噁英在高温下热解、粉尘被吸附并滞留于料层,减少排入大气的烟气量,降低废气净化装置及运行成本,并提高已有烧结机的产能。
2、关键技术(1)烧结低温余热利用、废气减量、污染物同步脱除的方法、工艺和装置;(2)循环烧结系统在线控制技术包括循环烟温和氧含量调控、烟道防结露、循环风箱组合优化、循环烧结工艺与主工艺衔接等技术;(3)循环烧结过程仿真模型包括烧结终点温度控制、风氧平衡、烧结质量预报与控制、循环烧结传热、节煤量实计、管路优化等子模型;(4)循环烧结条件下配矿结构优化和提产增效技术包括提高废气循环烧结利用系数及烧结矿转鼓强度的方法,提高烧结铁精矿用量和生产率的矿料使用方法等。
4、工艺流程烧结废气余热循环利用工艺流程图主要技术指标1、烧结工艺节能5%以上;2、烟气总量减排20%以上。
技术水平本技术已申请30余项相关专利,目前已授权10项。
2014年11月,在宁钢循环烧结示范工程作为首批低碳技术创新和产业化示范工程通过了国家发改委工程验收组的项目验收。
宝钢集团新疆八一钢铁有限公司新区烧结机组余热利用工程节约能源篇

节约能源篇1 项目概况1.1 建设单位概况宝钢集团新疆八一钢铁有限公司。
1.2 项目概况项目名称:宝钢集团新疆八一钢铁有限公司新区烧结机组余热利用工程建设地点:八钢铁前新区。
项目性质:改建项目项目类型:生产性项目建设规模:1x30MW低温低压补汽凝汽式机组建设内容:用八钢烧结分厂现有2座265m2烧结机,1#265m2烧结机环冷机有效冷却面积为280m2,2#265m2烧结机环冷机有效冷却面积为360m2;1座430m2烧结机,430m2烧结机环冷机有效冷却面积为530m2,本设计回收3座环冷机的低温烟气余热,配置一台33MW凝汽式发电机组进行发电。
建设工期:2011年2月正式开工-2011年12月底正式投产发电,共计10个月。
项目周边环境:拟建八钢新区烧结余热发电33MW机组工程汽轮机区域位于八钢铁前新区,其南侧为高炉干煤棚,北邻在建的铁精粉圆形料仓,东邻新建空压站。
场地东西长约145m,南北最宽处约66m,总占地面积为9570㎡。
拟建场地地势平缓开阔,地形由西南向东北倾斜,平均坡度约1.6%,地面高程在820.46~822.58m。
1.3 建设方案简述1.3.1总平面布置:总平面布置共分两个布置区(主厂房布置区和烧结锅炉布置区)。
主厂房布置区根据八钢总体规划要求布置;烧结锅炉布置区根据烧结余热发电取风位置并结合现场空余场地布置。
1)汽机房区布置主厂房布置区主要布置有自然通风冷却塔、循环水泵房、主厂房,依次由西向东布置于八钢规划区域内。
南侧为高炉干煤棚,北邻在建的铁精粉圆形料仓,东邻新建空压站。
各建构筑物四周设环形道路,满足消防及设备运输要求。
2)1#烧结余热区布置1#烧结余热区主要布置有锅炉控制楼、1#锅炉、1#环冷风机及除尘器。
依次由西向东布置在1#环冷机南侧空地。
锅炉控制楼为1#、2#、3#锅炉共用。
3)2#烧结余热区布置2#烧结余热区主要布置有2#锅炉、2#环冷风机及除尘器。
依次由南向北布置在2#环冷机西侧。
热管技术在烧结机烟气余热回收中的应用

文章编号 : 1 0 0 4 - 8 7 7 4 ( 2 0 1 3 ) 0 3 - 0 0 4 4 - 0 4
业
锅
炉
2 0 1 3年第 3期 ( 总第 1 3 9期 )
热管技术在烧结机烟气余热 回收中的应 用
梁 国安 , 邵李 忠
( 1 . 江苏 省特 种设 备安 全监督 检验 研究 院 , 南京 2 1 0 0 3 6 ; 2 . 南京 圣诺 热管 有 限公 司 , 南京 2 1 0 0 0 9 )
能 回收 利用 。随 着 我 国节 能 减 排 工作 的深 人 推进 , 钢铁 工 业面 临 的调 结 构 、 降 能 耗压 力 日益 巨大 。工 业 节能 “ 十二 五 ” 规 划要 求 2 0 1 0年 同 2 0 0 5年 相 比,
1 烧 结 机 烟 气 分 析
1 . 1 烧 结机 烟气 的产 生
国民经济可持续发展有着非常重要的意义。
烧 结是 钢铁 企业 生产过 程 中高炉 矿料 人炉 以前 的准备 工序 。据 统计 , 烧 结 工序 的能 耗 约 占冶 金 总
能耗的 1 2 %, 而其排放 的余热 约 占总能耗热 能的 4 9 %, 回收和利用这些余热 , 显然极为重要。 目前 , 国内很 多科研 院 校 和相 关 企业 在 烧结 成 品 ( 烧 结 矿 热料 ) 显热及烧结冷却机废气 的余热 回收利用方面
高级工程师 , 1 9 8 5年 毕业 于西 安 交通 大 学锅炉专 业 , 后 于南 京工 业 大 学 获得 工
2 .N a n j i n g S h e n g n u o H e a t P i p e C o .L t d . , N a n j i n g 2 1 0 0 0 9 , C h i n a )
烧结烟气循环工艺
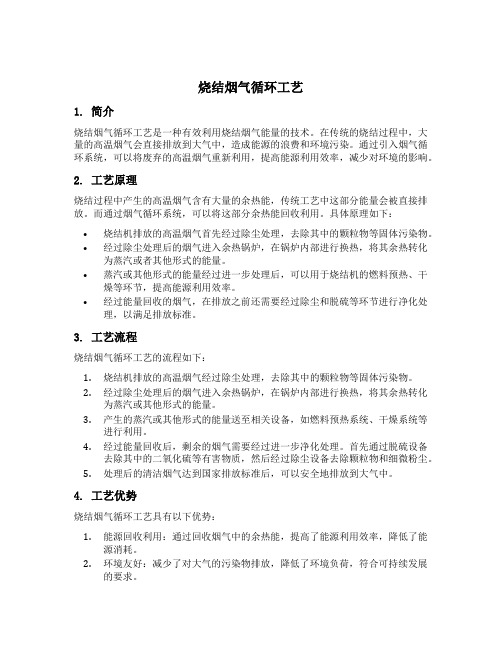
烧结烟气循环工艺1. 简介烧结烟气循环工艺是一种有效利用烧结烟气能量的技术。
在传统的烧结过程中,大量的高温烟气会直接排放到大气中,造成能源的浪费和环境污染。
通过引入烟气循环系统,可以将废弃的高温烟气重新利用,提高能源利用效率,减少对环境的影响。
2. 工艺原理烧结过程中产生的高温烟气含有大量的余热能,传统工艺中这部分能量会被直接排放。
而通过烟气循环系统,可以将这部分余热能回收利用。
具体原理如下:•烧结机排放的高温烟气首先经过除尘处理,去除其中的颗粒物等固体污染物。
•经过除尘处理后的烟气进入余热锅炉,在锅炉内部进行换热,将其余热转化为蒸汽或者其他形式的能量。
•蒸汽或其他形式的能量经过进一步处理后,可以用于烧结机的燃料预热、干燥等环节,提高能源利用效率。
•经过能量回收的烟气,在排放之前还需要经过除尘和脱硫等环节进行净化处理,以满足排放标准。
3. 工艺流程烧结烟气循环工艺的流程如下:1.烧结机排放的高温烟气经过除尘处理,去除其中的颗粒物等固体污染物。
2.经过除尘处理后的烟气进入余热锅炉,在锅炉内部进行换热,将其余热转化为蒸汽或其他形式的能量。
3.产生的蒸汽或其他形式的能量送至相关设备,如燃料预热系统、干燥系统等进行利用。
4.经过能量回收后,剩余的烟气需要经过进一步净化处理。
首先通过脱硫设备去除其中的二氧化硫等有害物质,然后经过除尘设备去除颗粒物和细微粉尘。
5.处理后的清洁烟气达到国家排放标准后,可以安全地排放到大气中。
4. 工艺优势烧结烟气循环工艺具有以下优势:1.能源回收利用:通过回收烟气中的余热能,提高了能源利用效率,降低了能源消耗。
2.环境友好:减少了对大气的污染物排放,降低了环境负荷,符合可持续发展的要求。
3.经济效益显著:回收利用烟气中的余热能,减少了能源消耗,降低了生产成本。
4.技术成熟可靠:烧结烟气循环工艺已经在多个企业得到应用,并取得了显著的经济和环境效益。
5. 应用案例烧结烟气循环工艺已经在许多企业成功应用。
烧结余热回收利用
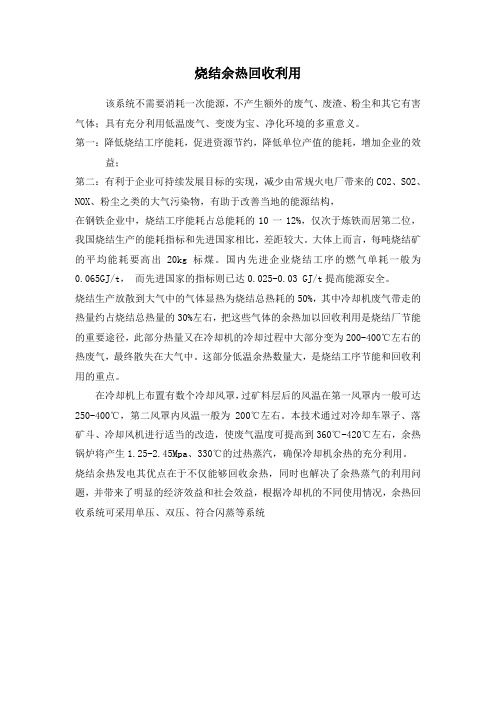
烧结余热回收利用该系统不需要消耗一次能源,不产生额外的废气、废渣、粉尘和其它有害气体;具有充分利用低温废气、变废为宝、净化环境的多重意义。
第一:降低烧结工序能耗,促进资源节约,降低单位产值的能耗,增加企业的效益;第二:有利于企业可持续发展目标的实现,减少由常规火电厂带来的CO2、SO2、NOX、粉尘之类的大气污染物,有助于改善当地的能源结构,在钢铁企业中,烧结工序能耗占总能耗的10一12%,仅次于炼铁而居第二位,我国烧结生产的能耗指标和先进国家相比,差距较大。
大体上而言,每吨烧结矿的平均能耗要高出20kg标煤。
国内先进企业烧结工序的燃气单耗一般为0.065GJ/t,而先进国家的指标则已达0.025-0.03 GJ/t提高能源安全。
烧结生产放散到大气中的气体显热为烧结总热耗的50%,其中冷却机废气带走的热量约占烧结总热量的30%左右,把这些气体的余热加以回收利用是烧结厂节能的重要途径,此部分热量又在冷却机的冷却过程中大部分变为200-400℃左右的热废气,最终散失在大气中。
这部分低温余热数量大,是烧结工序节能和回收利用的重点。
在冷却机上布置有数个冷却风罩,过矿料层后的风温在第一风罩内一般可达250-400℃,第二风罩内风温一般为200℃左右。
本技术通过对冷却车罩子、落矿斗、冷却风机进行适当的改造,使废气温度可提高到360℃-420℃左右,余热锅炉将产生1.25-2.45Mpa、330℃的过热蒸汽,确保冷却机余热的充分利用。
烧结余热发电其优点在于不仅能够回收余热,同时也解决了余热蒸气的利用问题,并带来了明显的经济效益和社会效益,根据冷却机的不同使用情况,余热回收系统可采用单压、双压、符合闪蒸等系统单压系统采用单级进汽汽轮机及单压烧结余热锅炉的单压不补汽系统。
一般余热锅炉排气温度在170℃,排气用于烘干物料。
复合闪蒸单级补汽系统采用补汽式汽轮机的复合闪蒸单级补汽系统,烧结余热锅炉生产主蒸汽同时生产高温热水,高温热水再降压蒸发双压系统采用补汽式汽轮机的双压单级补汽系统,烧结余热锅炉生产两个不同的蒸汽,一为主蒸汽,另一个为低压补汽。
烧结机余热发电技术
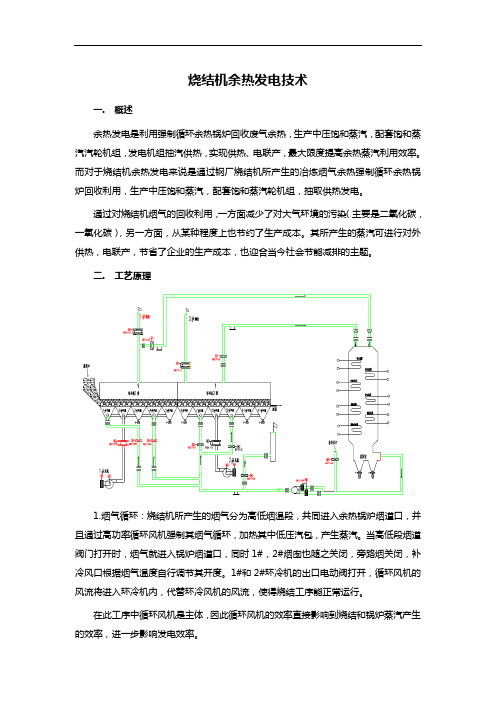
烧结机余热发电技术一.概述余热发电是利用强制循环余热锅炉回收废气余热,生产中压饱和蒸汽,配套饱和蒸汽汽轮机组,发电机组抽汽供热,实现供热、电联产,最大限度提高余热蒸汽利用效率。
而对于烧结机余热发电来说是通过钢厂烧结机所产生的冶炼烟气余热强制循环余热锅炉回收利用,生产中压饱和蒸汽,配套饱和蒸汽轮机组,抽取供热发电。
通过对烧结机烟气的回收利用,一方面减少了对大气环境的污染(主要是二氧化碳,一氧化碳),另一方面,从某种程度上也节约了生产成本。
其所产生的蒸汽可进行对外供热,电联产,节省了企业的生产成本,也迎合当今社会节能减排的主题。
二.工艺原理1.烟气循环:烧结机所产生的烟气分为高低烟温段,共同进入余热锅炉烟道口,并且通过高功率循环风机强制其烟气循环,加热其中低压汽包,产生蒸汽。
当高低段烟道阀门打开时,烟气就进入锅炉烟道口,同时1#,2#烟囱也随之关闭,旁路烟关闭,补冷风口根据烟气温度自行调节其开度。
1#和2#环冷机的出口电动阀打开,循环风机的风流将进入环冷机内,代替环冷风机的风流,使得烧结工序能正常运行。
在此工序中循环风机是主体,因此循环风机的效率直接影响到烧结和锅炉蒸汽产生的效率,进一步影响发电效率。
2.中压水循环:中压锅筒给水是来自汽机房凝结水经过低压除氧器处理后,由中压给水泵打入中压锅筒。
中压给水调节中最为重要的是给水三冲量调节,其调节方式是通过汽包水位,给水流量,主蒸汽流量。
给水三冲量调节中,给水流量的准确度直接影响到调节的准确和稳定度。
因此要进行三冲量的调节,给水流量和蒸汽流量以及水位的校验非常重要。
当主蒸汽温度达到一定值(主要由进入汽机的蒸汽温度决定)时,需要打开减温水调节阀来冷却中压减温汽,降低蒸汽温度,符合进入汽机蒸汽温度的要求。
科技成果——钢铁行业烧结烟气选择性循环净化与余热利用技术

科技成果——钢铁行业烧结烟气选择性循环净化与余热利用技术技术类别减碳技术适用范围钢铁行业,适用于带式烧结机,占地面积1500m2。
行业现状该技术可广泛应用于钢铁行业烧结工序烟气治理,技术适用于新建或改造项目,该技术成果在河钢邯钢完成国内首套示范工程应用,并在河钢集团内部全面推广,在集团下属邯钢、承钢、唐钢新区等子公司实现90%的技术配套率。
成果简介(1)技术原理烧结烟气选择性循环净化与余热利用是根据烧结风箱烟气排放特征(温度、含氧量、烟气量、污染物浓度等)的差异,在不影响烧结矿质量的前提下,选择特定风箱段的烟气循环回烧结台车表面,用于热风烧结。
循环烟气由烧结机风箱引出,经除尘系统、循环主抽风机、烟气混合器后通过密封罩,引入烧结料层,重新参与烧结过程。
烟气显热全部供给烧结混合料进行热风烧结,降低了烧结固体燃料消耗,改善了表层烧结矿质量,提高了烧结矿料层温度均匀性和破碎强度等理化指标。
(2)关键技术1、烧结烟气选择性循环节能减排技术基于烧结烟气分风箱排放特征差异化的特点,选择特定风箱段烟气,经除尘系统、主抽风机、烟气分配器后通过密封罩循环回烧结台车表面重新参与烧结过程,有效削减烟气排放量,降低末端净化设备的处理负荷及成本;解决了烟气温度、含氧量、各污染物浓度对烧结生产原料消耗、产矿质量的影响。
2、CO过程减排技术通过选择性选取高氧、高温段风箱烟气进行循环,通过营造高温、高氧气氛,强化循环烟气中CO在穿透料层时的二次燃烧反应,实现CO过程减排。
3、通过热风烧结效应提升烧结矿质量通过定量分析不同循环工况下烧结过程的温度场分布,优选烧结终点温度升高的循环工况,通过高温循环烟气与烧结床层的直接热交换强化烧结废气低品位余热利用效果,降低了烧结生产过程的固体燃料消耗,高温循环烟气的热风烧结效应使料层上部烧结温度提高、温差降低,减少了热应力,矿物充分结晶、液相量增加,提高了烧结整体成品率及烧结矿强度。
4、流量均配双侧进气密封罩通过工况波动的密封罩压力预测模型,开发了与生产联动的智能化压差反馈调节控制系统,解决传统烟气循环技术布风不均、循环烟气外溢问题。
烧结余热回收利用途径探讨

烧结余热回收利用途径探讨闫为群 栾 颖(中冶北方工程技术有限公司)摘要 介绍了国内外烧结余热利用情况。
以实际工程为例分析探讨了余热发电的社会效益、环境效益和经济效益,以及烧结余热回收利用的途径,并提出了提高烧结回收余热的技术措施。
关键词 余热 回收 发电 途径M ETHOD TO RECO VER Y W ASTE HEAT FR OM S I NTER I NG PR OCESSYan W eiqun Luan Ying(Northern Engineering&Technol ogy Cor porati on,MCC)ABSTRACT The status of home&abr oad utilizati on methods of waste heat fr om sintering p r ocess is exp lained.Taking p ractical operati ons as examp les,the s ocial,envir on mental and econom ical benefits of power generati on and method t o re2 covery waste heat are analyzed.Some technical measures for i m p r oving waste heat recovery efficiency are recommended. KE Y WO RD S W aste heat Recovery Power generati on M ethod0 前言在“十・五”期间,通过产业政策调整,淘汰小型落后的烧结生产线,单机规模大型化,优化工艺流程及采用节能型设备,强化操作管理等,使我国的烧结技术装备及生产管理水平得到很大提高。
同时,在能源综合利用方面也取得很大进展,对烧结冷却机余热进行回收利用。
烧结大烟道余热回收设备工艺原理

烧结大烟道余热回收设备工艺原理引言伴随着工业化进程的不断加快,工业排放的大量烟尘和高温废气对人类的生存环境造成了很大的危害。
为了减轻环境负担,提升资源利用效率,烧结大烟道余热回收设备逐渐受到广泛关注。
本文将就此设备的原理及其重要性进行详细探讨。
烧结大烟道余热回收设备的定义大烟道排放的烟气温度一般在1000℃左右,所含热量是废气中有机物可燃部分和无机物热辐射吸收的热量。
烧结大烟道余热回收设备利用这一热源,通过热交换,将废气中的热量转移至其他工艺流体,从而实现能量回收和资源利用。
设备组成烧结大烟道余热回收设备主要由余热烟道、余热锅炉、余热水箱、余热回收装置和自控系统组成。
其中,余热烟道是流经余热回收装置的废气通道;余热锅炉的作用是将经过余热回收装置的热水、蒸汽或气体加热至一定温度;余热水箱是储存余热水的设备;余热回收装置是实现废气余热回收的核心设备;自控系统是设备的智能控制中心,实现设备运行的自动化和安全性控制。
烧结大烟道余热回收设备的工艺原理主要包括废气预处理、热回收和余热利用。
在每个步骤中,有必要采用科学的技术措施,以保证设备的稳定性和效率。
1. 废气预处理烧结大烟道排放出的废气含有很高的水分和烟尘等有害物质,对设备正常运行及其余热回收产生不利影响。
因此,为了减少废气的污染物质,需要先对废气进行预处理。
这个过程中可以采用干燥和除尘装置,将废气的温度降低到可以处理的范围内,并去除其中的烟尘和杂质。
2. 热回收废气进入余热回收装置之后,通过导热、对流和辐射等多种方式,将烟气中的热量传递给热介质,以获得所需的热量。
热介质可以是流体、气体或蒸汽等,在传递热量的过程中,需要适当控制热介质流速和传热面积大小,以实现较高的热回收效率。
3. 余热利用热介质在获得热量之后,即可利用余热锅炉进一步提取能量。
通过余热锅炉将热介质加热,使其达到蒸汽或热水的有效温度,进而与其他工艺流体进行热交换。
这样就可以将大烟道排放的废气中的热能重新利用起来,减少能源浪费,提高能源利用效率。
烧结工序节能降耗的技术措施
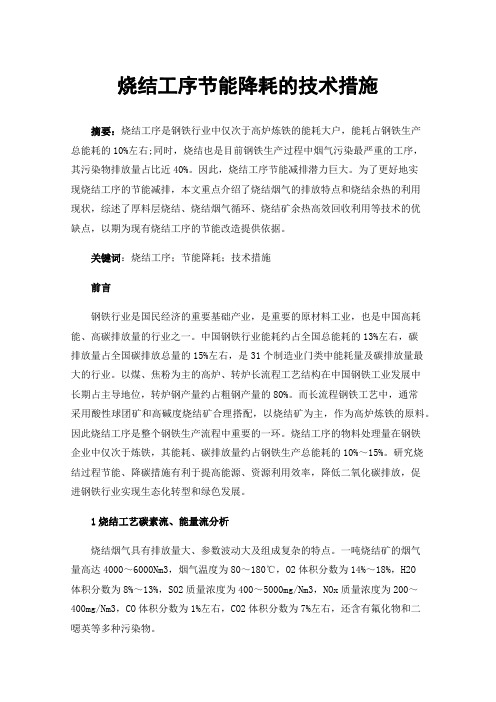
烧结工序节能降耗的技术措施摘要:烧结工序是钢铁行业中仅次于高炉炼铁的能耗大户,能耗占钢铁生产总能耗的10%左右;同时,烧结也是目前钢铁生产过程中烟气污染最严重的工序,其污染物排放量占比近40%。
因此,烧结工序节能减排潜力巨大。
为了更好地实现烧结工序的节能减排,本文重点介绍了烧结烟气的排放特点和烧结余热的利用现状,综述了厚料层烧结、烧结烟气循环、烧结矿余热高效回收利用等技术的优缺点,以期为现有烧结工序的节能改造提供依据。
关键词:烧结工序;节能降耗;技术措施前言钢铁行业是国民经济的重要基础产业,是重要的原材料工业,也是中国高耗能、高碳排放量的行业之一。
中国钢铁行业能耗约占全国总能耗的13%左右,碳排放量占全国碳排放总量的15%左右,是31个制造业门类中能耗量及碳排放量最大的行业。
以煤、焦粉为主的高炉、转炉长流程工艺结构在中国钢铁工业发展中长期占主导地位,转炉钢产量约占粗钢产量的80%。
而长流程钢铁工艺中,通常采用酸性球团矿和高碱度烧结矿合理搭配,以烧结矿为主,作为高炉炼铁的原料。
因此烧结工序是整个钢铁生产流程中重要的一环。
烧结工序的物料处理量在钢铁企业中仅次于炼铁,其能耗、碳排放量约占钢铁生产总能耗的10%~15%。
研究烧结过程节能、降碳措施有利于提高能源、资源利用效率,降低二氧化碳排放,促进钢铁行业实现生态化转型和绿色发展。
1烧结工艺碳素流、能量流分析烧结烟气具有排放量大、参数波动大及组成复杂的特点。
一吨烧结矿的烟气量高达4000~6000Nm3,烟气温度为80~180℃,O2体积分数为14%~18%,H2O体积分数为8%~13%,SO2质量浓度为400~5000mg/Nm3,NOx质量浓度为200~400mg/Nm3,CO体积分数为1%左右,CO2体积分数为7%左右,还含有氟化物和二噁英等多种污染物。
1.1烧结工艺主要功能烧结的生产过程是把精矿粉、燃料(焦粉、无烟煤)和熔剂(石灰石、白云石、生石灰)按一定比例配料混匀后,在烧结机上点火燃烧,利用燃料和铁氧化物氧化反应放出热量,使混合料局部熔化,并将散粒颗粒黏结成块状烧结矿,作为炼铁原料。
烧结机烟道废气余热回收利用

i n g r e c o n s t r u c t i o n
近几 年 我公 司 积极 响应 国 家号 召 , 推 动 循 环
量。
经济 的发 展 , 充 分 利 用 烧 结 环 冷 机 废 气余 热 回收 发电, 先后在 2 0 0 9年 建 设 了 2×3 6 0 m 烧 结 余 热 发 电项 目, 2 0 1 1 年 建设 了 6×1 8 0 m 烧 结余 热发 电
烧结竖冷窑余热锅炉

烧结竖冷窑余热锅炉
烧结竖冷窑余热锅炉是一种利用烧结竖冷窑排放的高温烟气余热进行热能回收的设备。
烧结竖冷窑是用于烧结生产过程的关键设备,其排放的烟气温度通常较高,一般在800℃以上。
这
些高温烟气中所蕴含的大量余热如果不进行回收利用,将会直接排放到大气中造成能源的浪费和环境的污染。
烧结竖冷窑余热锅炉的设计与传统的烟气余热锅炉类似,都是通过烟气和水间的热交换来将烟气中的余热转化为热水或蒸汽。
烧结竖冷窑余热锅炉的主要特点是能够适应烧结竖冷窑的高温烟气特点,具有较高的烟气进口温度和烟气出口温度,以及较大的烟气负荷。
通过利用烧结竖冷窑余热锅炉进行热能回收,可以实现能源的节约和环境的保护。
同时,余热锅炉所产生的热水或蒸汽还可以用于其他工艺过程中的加热或发电,进一步提高能源的利用效率。
因此,烧结竖冷窑余热锅炉在钢铁、冶金和水泥等行业中得到了广泛的应用。
烧结余热锅炉的工作原理

烧结余热锅炉的工作原理
首先,烧结机产生的高温烟气被引导到余热锅炉的烟气进口处。
这些
烟气通常具有较高的温度和压力,因此,在进入余热锅炉前需要通过一个
多级除尘器进行处理,以去除其中的颗粒物和有害气体,保证烟气的干净。
接下来,经过除尘后的烟气进入余热锅炉的余热换热器。
余热换热器
中通常安装有多组烟气余热回收管束,用于与锅炉中的介质进行换热。
这
些管束一般采用强化传热方式,以提高热量传递效率。
同时,余热换热器
的结构也有多种,常见的有壳管热交换器、板式热交换器等等。
在余热换热器中,烟气的热量被传递给介质,使介质升温,而烟气在
传热过程中则降温。
一般而言,介质是水,因此烟气经过余热换热器后会
降温,形成冷烟气。
接着,烟气从余热换热器中排出,并通过烟气出口排放到大气中。
在
这个过程中,通过余热回收,烟气中的热量被充分利用,大大减少了能源
的浪费。
另一方面,介质在余热换热器中被加热,并变为高温高压蒸汽。
这些
蒸汽可以用于多种应用,比如在工业生产中驱动蒸汽涡轮发电机组,产生
电力;也可以用于供热,如为居民供应热水和供暖。
总的来说,烧结余热锅炉的工作原理是通过将烧结机产生的高温烟气
中的热量通过余热换热器传递给介质,使介质升温并转化为蒸汽,从而利
用热能,并将冷烟气排出。
通过这种方式,烧结机的余热得到了充分回收
利用,减少了资源的浪费和环境污染,实现了能源的有效利用。
铁矿烧结烟气循环工艺优缺点分析

铁矿烧结烟气循环工艺优缺点分析摘要:铁矿烧结是钢铁企业对原材料进行处理的必要工序,它能够使铁矿具有优质的冶金功能,提高高炉的生产效率。
但是在铁矿烧结过程中,产生的烟气含有大量的污染物质,其排放量对空气造成了严重的污染。
所以在铁矿烧结过程中应用烟气排放工艺很有必要,其中烟气循环工艺是我国常用的方式。
本文就几种典型的烟气循环工艺的优缺点进行了分析。
关键词:铁矿烧结烟气循环优缺点钢铁行业是我国大气污染重点治理对象,其中铁矿烧结中产生的粉尘、SOx、NOx等的排放对我国大气产生了严重的影响。
钢铁行业如何降低烟气污染物排放量、实现环保是我国目前需要解决的难题。
现今钢铁行业铁矿烧结烟气超低减排技术多种多样,然而利用最多的还是铁矿烧结烟气循环工艺,对降低污染物排放量有着积极的作用。
然而在实际应用中,它也存在着一些缺点需要我们去探讨。
一、铁矿烧结烟气循环工艺概述铁矿烧结烟气循环工艺是在铁矿烧结过程中将烧结产生的一部分烟气再重新烧结,将烟气再进行循环利用。
烟气循环工艺按烧结烟气的来源可以分为两种:内循环和外循环。
内循环是从主抽风机前的风箱支管取风进行循环;外循环是从主抽风机后的烟道取风进行循环。
铁矿烧结烟气循环工艺对烟气污染物进行减排,降低了烟气中有害物质的排出,是我国钢铁行业主要推行的手段。
二、铁矿烧结烟气循环工艺优点烧结烟气循环工艺能够将烟气循环中产生的热量进行合理的利用,做到了节能;并能够降低烟气中有害物质的排放量,降低了对大气的污染程度,做到了减排。
目前烧结烟气循环工艺比较典型的有:能量优化烧结工艺(ESO)、环境型优化烧结工艺(EPOSINT)、低排放能量优化烧结工艺(LEEP)、烧结烟气余热循环工艺。
2.1. 能量优化烧结工艺(ESO)能量优化烧结工艺是将主抽风机排出烟气中的一部分重新引入到烧结工序中,通过吹入空气与循环利用的烟气相混合,剩余部分的烟气则直接排出的一种烟气循环工艺,属于外循环。
这种工艺在荷兰克鲁斯埃莫伊登的工厂首次被使用。
- 1、下载文档前请自行甄别文档内容的完整性,平台不提供额外的编辑、内容补充、找答案等附加服务。
- 2、"仅部分预览"的文档,不可在线预览部分如存在完整性等问题,可反馈申请退款(可完整预览的文档不适用该条件!)。
- 3、如文档侵犯您的权益,请联系客服反馈,我们会尽快为您处理(人工客服工作时间:9:00-18:30)。
4、3 400m2烧结环冷机尾部冷却风余热利用
4、3、1 环冷机烟气系统
400m2烧结机余热发电工程也就是较早建成的同类项目,具备一定代表性。
它采用双压、双进气、一体化除氧器、自然循环余热锅炉;烟气侧采用开式系统+串级冷却方式,余热锅炉排出的烟气直接经引风机排至大气,环冷机高温段采用从低温段烟罩收集的热废气作为烧结矿的冷却风。
由于400m2烧结机规模较大,余热锅炉排出的烟气量约60万Nm3/h,温度130℃,仍有可观的可利用热量。
如果直接排放将造成很大的资源浪费。
本工程拟改变原环冷机烟气循环系统的循环方式,用原余热锅炉排放的烟气代替环冷机3#烟囱收集的低温烟气,作为环冷机1区的冷却风;重新核算风机能力,原1区的循环风机利旧。
3#烟囱收集的低温烟气进入新建设的热水锅炉产生热水进行采暖供热。
环冷机的烟罩第三区段已经进行了绝热、密封的设计,本工程不在对第三区段的烟罩进行改造,通过环冷机的3#烟囱收集的高温烟气引出至余热热水锅炉。
3#烟囱上设置四通管道,配置电动切换蝶阀,热水锅炉正常工作时,打开新增的烟气管道阀门,关闭烟囱阀门及原循环管道阀门,将烟气导入热水锅炉烟道;在热水锅炉停止运行时,关闭烟气进入余热锅炉的阀门,打开烟囱阀门,将烟气直接排入大气;或者打开原循环管道阀门进行原设计的烟气循环冷却。
从环冷机3#烟囱收集的高温烟气进入锅炉,在锅炉内充分换热,产生高温热水。
换热后的烟气降至90℃左右,经引风机后排放烟囱排入
大气。
在原余热锅炉后烟囱上设置三通管道,配置电动切换蝶阀,如采用烟气循环方式时,关闭烟囱阀门将余热锅炉换热后的热废气,通过循环风机及烟气管道将烟气引入环冷机一区。
如采不用烟气循环方式时,打开锅炉后烟囱阀门,将烟气直接排空。
4、3、2环冷机烟气量分配
在保证不影响原400m2烧结余热利用系统的情况下,采用合理的分区方法,尽可能多的利用环冷机三段的高温烟气及余热锅炉排放的烟气。
烧结矿的热力学数据模型
热烧结矿平均比热经验公式为:CP=[0、115+0、257×10-3(T-373)-0、0125×10-5(T-373)2]×4、1868
式中CP—烧结矿的平均比热,单位:kJ/(kg·℃)
T—绝对温度,单位:K。
本工程计算以大气温度20℃时作为基础,废热气收集结果见表
4-1。
表4-1 废烟气收集特性
4、3、3 余热收集的主要措施
主要技术措施有如下几个方面:
(1)烟罩与台车间的密封(收集区域)
采用专有的刚柔性密封技术改造烟罩与台车上缘之间的密封装置。
(2)烟罩及烟囱设置保温层,以减少辐射热损失与对流热损失。
(3)其它漏风点的密封。
4、3、4 流场优化技术
合理设计环冷机烟气收集烟罩,消除死角,压力均等,避免烟罩压力偏差过大,导致局部热风大量外漏,冷风大量内侵,造成热损与温损两种并存的缺陷。
4、3、5 余热收集系统
如前所述,现有的400m2烧结冷却余热发电系统烟气侧采用串级冷却,余热锅炉排出的大量烟气余热未得到利用。
本次拟将串级冷却系统改造为部分循环系统。
具体流程见图4-1。
图4-1:400m2烧结环冷机余热利用流程图
该环冷机未设置1#鼓风机,而就是采用的循环风机。
该风机正常生产时自环冷烟罩3#烟囱吸取热风,非正常情况可自大气吸风。
本次拟将现有的3#烟囱增设一个旁路,将该区段的热废气引至余热水水锅炉,设置电动蝶阀,以便操作切换。
非采暖季节恢复原有的串级冷却方式运行。
余热锅炉烟囱增设两个电蝶阀,一路至循环风机冷风吸入口,一路排至大气。
至大气的蝶阀正常情况下部分关闭,允许余热锅炉排烟一部分排空、一部分至循环风机。
该方式与320m2烧结冷却余热发电现有烟气系统相同,在生产上完全可行。
经测算,废气收集成果见表4-2。
表4-2 余热收集特性表
4、3、6 余热回收装置
该系统余热回收装置与320m2结构、类型相同,只就是供热量不同,在此不再赘述。
设计压力1、6MPa,供回水温度66、5/49℃,热水循环流量约390、0t/h,供热功率8、0MW。
余热锅炉烟气阻力约450Pa,排烟温度91、5±3℃。
余热热水锅炉放水接入现有的余热锅炉排污扩容系统。
4、3、7 废气排放系统
由余热锅炉排出的烟气被引风机抽吸,经烟囱排至大气。
风机入口配置电动调节风门,风机采用变频调速电机拖动。
风机后设置钢制烟囱一座,直径2、6m,高度暂定40m。
4、4 320 m2烧结环冷机尾部冷却风余热利用
4、4、1带冷机烟气系统
320m2烧结机余热发电工程建成较早,为国内第二套同类项目、国内第一套独立知识产权的烧结矿冷却余热发电装置。
它采用双压、单进气、强制循环余热锅炉,烟气采用部分循环。
目前320m2烧结冷却余热发电系统仅利用了带冷机的1#烟囱高温段烟气及2#烟囱部分中温段烟气,其余的高温烟气处于放空状态,造成能源浪费与大气的热污染。
经实地调研与现场数据核算,带冷机3#烟囱的排放的年平均温度在220℃左右,该处高温烟气可作为优质采暖热源加以利用。
本工程拟对带冷机的烟罩第三区段进行绝热、密封、隔断改造,收集的高温烟气通过带冷机的3#烟囱引出至余热热水锅炉。
3#烟囱上设置三通管道,配置电动切换蝶阀,正常工作时,打开烟气管道阀门,关闭烟囱阀门,将烟气导入热水锅炉烟道;在热水锅炉停止运行时,关闭烟气进入余热锅炉的阀门,打开烟囱阀门,将烟气直接排入大气。
从带冷机3#烟囱收集的高温烟气进入锅炉,在锅炉内充分换热,产生高温热水。
换热后的烟气降至90℃左右,经引风机后排放烟囱排入大气。
具体流程见图4-2。
图4-2:320m2烧结环冷机余热利用流程图
4、4、2 带冷机烟气量分配
在保证不影响原320m2烧结余热利用系统的情况下,采用合理的分区方法,尽可能多的利用带冷机三段的高温烟气。
烧结矿的热力学数据模型
热烧结矿平均比热经验公式为:CP=[0、115+0、257×10-3(T-373)-0、0125×10-5(T-373)2]×4、1868
式中CP—烧结矿的平均比热,单位:kJ/(kg·℃)
T—绝对温度,单位:K。
本工程计算以大气温度20℃时作为基础,废热气收集结果见表4-3。
4、4、3 余热收集采取的主要措施与流场优化技术同400 m2烧结机余热回收。
4、4、4 320 m2余热收集系统
如前所述,现有的320m2烧结冷却余热发电仅利用了废气温度较高烟罩区段,其余处于放空状态,经实地调研与测算,该废气可作为优质采暖热源。
本次拟对烟罩第三区段进行绝热、密封、隔断改造,收集的热废气通过3#烟囱引出至余热热水锅炉,作为载热体。
3#烟囱增设电动蝶阀两套,一路去大气,一路去余热锅炉。
非采暖季节废气直接排至大气,余热热水锅炉停用。
新增的系统对现有的余热发电系统无任何不利影响,在工艺上近乎独立。
结合现有余热发电系统,测算余热收集成果见表4-4。
4、4、5 320m2余热回收装置
采用双集箱、立式烟道、螺旋翅片管热水锅炉,设计压力1、6MPa,供回水温度66、5/49℃,热水循环流量约515、0t/h,供热功率10、6MW。
余热锅炉烟气阻力约450Pa,排烟温度91、5±3℃。
锅炉设置燃气脉冲吹灰装置,与烧结发电余热锅炉吹灰装置相同,保证余热锅炉性能长期稳定。
余热锅炉设有安全阀、排气阀、放水阀等必要的附属设施,配有完善的检测仪表。
余热热水锅炉放水接入现有的余热锅炉排污扩容系统。
4、4、6 废气排放系统
由余热锅炉排出的烟气被引风机抽吸,经烟囱排至大气。
风机入口配置电动调节风门,风机采用变频调速电机拖动。
风机后设置钢制烟囱一座,直径2、4m,高度暂定40m。
4、5 供热系统
4、5、1 系统构成
本次拟将深度利用的热废气合建成一个供热站,分成两个系统。
每套系统均设置开一备一的热水循环泵两台,变频驱动;每套系统均设开一备一的补水定压泵两台,变频驱动;两套系统合用一座补水定
压水箱。
系统补水来自生产新水,送至补水箱,设置水位控制装置及流量测量计算装置。
4、5、2 供热站
本工程建设一处供热站,分为水泵间与配电间;其中配电间设有控制室;采用单层结构。
水泵间布置有4台热水循环泵、4台补水定压泵、一座补水箱与两套加药装置;设有检修所需的起重设备。
4、5、3 热力管网
供热站与热用户接口设在1750m3高炉冲渣水供热站处,采用母管制式,供热母管设有热量计;设有供回水管各一条,采用架空敷设。
供热站与热源之间采用双供单回方式,320m2与400m2分别供水,锅炉出水合并至一条母管,连接至泵站;管道选用螺旋焊接管,拟采用直埋方式敷设。
系统总循环水量约900m3/h,供回水温度设计值为65℃/50℃。
供水系统设计压力1、6MPa。
4、6 工艺流程图
工艺流程图见图4-3。
图4-3 工艺流程图。