酒泉钢铁 酒钢120t LF快速脱硫工艺实践
LF炉快速脱硫

关于LF炉如何快速脱硫的讨论罗小武1.引言在实际的生产中,LF炉冶炼脱硫能力对后续能否生产出合格的产品至关重要。
特别是随着新产品开发的需要,对钢中S含量要求越来越高,对LF炉快速脱硫工艺要求更为严格。
因此在LF炉生产过程中快速有效的脱硫越来越受到我们的重视。
2.脱硫原理分析2.1脱硫过程LF脱硫机理按照冶金学理论脱硫应该按如下步骤进行:(1)在钢-渣界面上,钢水中[FeS]按分配定律进入炉渣。
[FeS]=(FeS) (1-1)(2)渣中(FeS)与渣中自由(CaO)结合为稳定的(CaS)。
(FeS)+(CaO)=(FeO)+(CaS) (1-2) 脱硫基本过程大体分为:硫由钢液内向钢-渣界面迁移;界面的化学反应,硫化物向渣层迁移。
2.2钢水氧化性对脱硫的影响涟钢所采用的LF炉脱硫剂为石灰,其脱硫反应按离子理论可写作:(O2-)+[S]=(S2-)+[O] (1-3) 由上式可知,降低炉渣氧化性促进反应向有利于脱硫的方向进行。
因为钢渣之间存在氧的传质,如果钢水的含氧量较高,必然将影响脱硫反应向右进行。
即钢水的脱氧与脱硫是相互联系的,脱氧良好的钢水可提高渣的脱硫能力,这也是脱硫的前提条件。
2.3炉渣碱度对脱硫的影响炉渣碱度和流动性对脱硫的影响由式(1-3)可知:炉渣中Ca2 +活度越高,越促进脱硫反应的进行。
因此提高炉渣碱度,可促进脱硫反应向右进行。
但是在碱度达到一定程度后,继续提高碱度不利于脱硫,这是因为当( CaO)含量过高后,渣中会有固相质点析出,使炉渣粘度提高,流动性变差,影响了脱硫的动力学条件,使脱硫效果变差。
生产实践中,当炉渣碱度偏高时,采用加精炼渣的办法加以调整。
2.4渣量对脱硫的影响理论分析,渣量越大,对脱硫越有利,但渣量过大,会导致原材料、电能等生产成本的增加,因此实际生产时,需要合理考虑渣量大小,在适当范围内尽量增大渣量。
2.5搅拌强度对于脱硫的影响由于脱硫反应是钢渣界面反应,而钢中[S]向渣中扩散是这个反应的限制环节。
浅谈炼钢120t转炉补炉护炉工艺改进实践
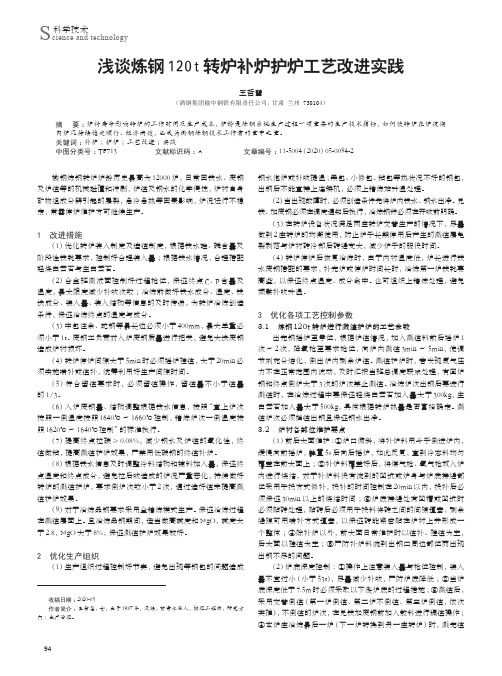
科学技术S cience and technology浅谈炼钢120t转炉补炉护炉工艺改进实践王哲慧(酒钢集团榆中钢铁有限责任公司,甘肃 兰州 730104)摘 要:炉衬寿命影响转炉的工作时间及生产成本,炉龄是炼钢系统生产过程一项重要的生产技术指标,如何使转炉在炉役期内炉况持续稳定顺行、经济高效,已成为榆钢炼钢技术工作者的重中之重。
关键词:补炉;护炉;工艺改进;实践中图分类号:TF713 文献标识码:A 文章编号:11-5004(2020)05-0094-2榆钢炼钢转炉炉龄历史最高为12000炉,日常因铁水、废钢及炉渣等的机械碰撞和冲刷,炉渣及钢水的化学侵蚀,炉衬自身矿物组成分解引起的层裂,急冷急热等因素影响,炉况运行不稳定,常需停炉维护方可继续生产。
1 改进措施(1)优化转炉装入制度及造渣制度,根据铁水硅、磷含量及阶段性铁耗要求,控制好合理装入量;根据铁水情况,合理搭配轻烧白云石与生白云石。
(2)合金班测液面控制好过程枪位,保证终点C、P含量及温度,最大限度减少补吹次数;冶炼前做好铁水成分、温度、铁块成分、装入量、装入结构等信息的及时传递,为转炉冶炼创造条件,保证冶炼终点的温度与成分。
(3)中包注余、砣钢等最长边必须小于400mm,最大单重必须小于1t。
废钢工负责对入炉废钢质量进行把关,避免大块废钢造成炉衬损坏。
(4)转炉停炉间隙大于5min时必须摇炉挂渣,大于20min必须实施喷补或渣补,统筹利用好生产间隙时间。
(5)符合留渣要求时,必须留渣操作,留渣量不小于渣量的1/3。
(6)入炉废钢量、结构调整根据铁水信息,按照“直上炉次按照一倒温度按照1640℃~1660℃控制,精炼炉次一倒温度按照1620℃~1640℃控制”的标准执行。
(7)提高终点拉碳≥0.08%,减少钢水及炉渣的氧化性,终渣做粘,提高溅渣护炉效果,严禁用低碳钢的终渣补炉。
(8)根据铁水信息及时调整冷料结构和辅料加入量,保证终点温度和终点成分,避免拉后吹造成的炉况严重恶化,持续做好转炉的溅渣护炉,要求倒炉次数小于2次,通过造好渣来提高溅渣护炉效果。
唐钢150tLF钢包精炼炉快速脱硫工艺实践

唐钢150tLF钢包精炼炉快速脱硫工艺实践摘要介绍和分析了唐钢150tLF钢包精炼炉冶炼薄板坯连铸钢水时快速脱硫工。
生产实践表明:合理的渣系组成、温度控制、酸溶铝含量、吹氩搅拌及喂线技术是实现快速脱硫的关键技术。
关键词唐钢钢包精炼炉快速脱硫工艺实践0前言对于大多数钢种来说,硫是有害元素。
它在钢中所形成的硫化物降低钢的韧性,硫化锰夹杂是钢基体点腐蚀的发源地,钢的氢脆与钢中硫化物夹杂也有密切关系。
薄板坯连铸由于是在高拉速条件下进行(3.0m/min~6.0m)/min).铸坯厚度薄.浇钢空间狭小,唐钢FTSC工艺薄板坯连铸机又采用复杂横截面的长漏斗型结晶器,为保证连续浇注和薄板坯表面质量,对硫含量提出更高的要求,一般要控制在0.008%以下。
同时.薄板坯连铸的刚性流程还需要时间、温度、节奏的匹配协调。
因此,开发LF钢包精炼炉的快速脱硫工艺是薄板坯连铸短流程生产线的一个重要研究课题。
唐钢在2003年3月开始对LF钢包精炼炉的快速脱硫工艺进行了有针对性的研究.并取得了较好的工艺效果。
1主要设备及技术参数唐钢150t LF钢包精炼炉的主要设备及技术参数见表1:表1 唐钢150t LF炉主要技术参数2唐钢薄板坯连铸钢水精炼工艺流程钢水进站→接底吹氩管→钢包到LF精炼位→测温取样→给电.加渣料.造还原渣→调整钢水成分及酸溶铝→测温取样→成分温度合格→弱吹→喂线→弱吹→钢水到LF炉起吊位→加保温剂→吊包→薄板坯连铸机。
3脱硫的热力学研究3.1脱硫反应在钢一渣界面上的脱硫反应是伴有电子转移的置换反应,其基本式为:[S]+2e=(S -2)为保持电中性.必有一些能释放电子的元素同时经过界面进入渣中,对于铝镇静钢来说.脱硫基本反应为:3(O2-)+3[ S]+2[ Al]=3(S2-)+( A12O3)3.2炉渣的脱硫能力适当增加渣量.可以稀释渣中CaS浓度,加快脱硫速率。
但渣量过大会使炉渣过厚,影响钢渣界面反应。
在实际生产过程中,转炉出钢下渣过多,会影响造白渣过程,从而恶化脱硫过程降低脱硫效率。
准时化生产制度下钢包精炼炉快速脱硫工艺实践
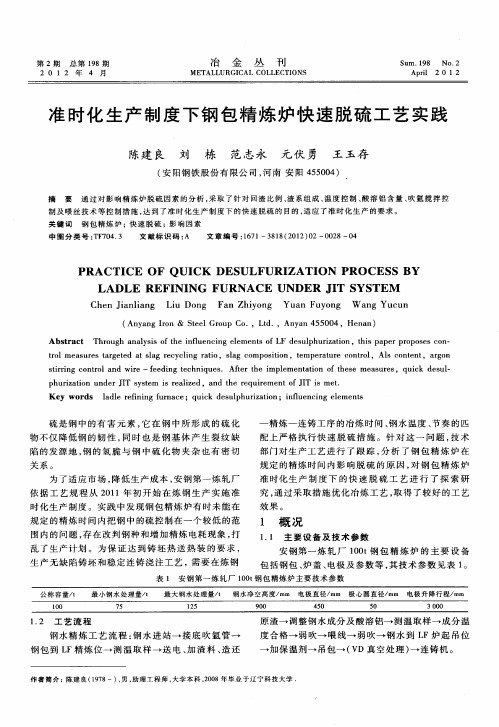
冶 金
丛
刊
S um .1 98
NO. 2
M ETALLURGI CAL C0LLECTI ONS
Aprl 2 0 1 i 2
准 时 化 生 产 制 度 下 钢 包 精 炼 炉 快 速 脱 硫 工 艺 不 利 于 球 形 1 C O 一 7 10 2a A
夹 杂 的上浮 , 不利 于 对 A 夹杂 进 行改 性处 理 , 10 对
稳 定连铸 浇 注工 艺 不利 。
从热 力 学 角 度考 虑 , 硫 反应 是 在 还 原性 气 氛 脱
中进 行 的 , 中 F O含 量 增 加 , 硫 速 率 呈 下 降 的 渣 e 脱 趋 势 , 利 于脱硫 反应 。根 据生 产数据 , 脱硫 反应 不 在 中渣 中 F O含 量 与硫 分 配 系数 的关 系如 图 1所 示 。 e 此外 , 生产 实践 中还 发现 , 中 ( e 在 渣 F O+M O) 于 n 小 1 时, % 脱硫 反应 速 率 显 著提 高 。 因此 挡渣 出钢 、 迅 速 造还原 渣是 保证 准 时化生 产制 度下 的快 速脱 硫 的
硫 是 钢 中 的有 害 元 素 , 在 钢 中所 形 成 的硫 化 它 物 不仅 降低钢 的韧 性 , 时也 是 钢 基 体 产 生 裂 纹 缺 同 陷的发 源 地 , 的氢 脆 与钢 中硫 化 物 夹 杂 也 有 密 切 钢
关系。
一
精 炼一 连 铸工 序 的冶 炼 时间 、 钢水 温 度 、 节奏 的 匹
成本 。炉 渣 的硫容 量 随利 用 次 数 的 升 高而 降 低 , 但
循环 3次 以 内可 以保证 较高 的脱硫 率 。
LF除尘灰应用于120t铁水包KR搅拌脱硫的工艺实践

o f t h e t o t l a c o s t o f d e s u l p h u r i z a t i o n .I n o r d e r t o r e d u c e p r o d u c t i o n c o s t .t h e L F c o l l e c t e d d u s t( / %: 4 . 2~8 . 8 S i O, . 2 6— 4 5 C a O. 7—1 5 Mg O.4—6 T F e 。2 O一4 O Ca C, 。1 0—2 0 A 1 , O , 0 . 0 3~0 . 1 0 P)i s u s e d t o r e p l a c e p a r t o f mi x e d d e s u l p h u r i .
第3 4卷第 5期
2 0 1 3年 l 0月
特 殊钢
S P E C I AL S T E E L
Vo 1 . 3 4. No . 5
O c t o b e r 2 0 1 3 ・41 ・
L F除尘 灰 应 用 于 1 2 0 t 铁 水 包 KR搅拌 脱 硫 的 工艺 实践
上 。为降低成本采 用 L F除尘灰 ( / %: 4 . 2~8 . 8 S i O 2 、 2 6—4 5 C a 0、 7~1 5 M [ s O、 4— 6 T F e 、 2 0— 4 0 C a C 2 、 1 0~2 0 A 1 2 O 3 、
0 . 0 3~ 0 . 1 O P ) 替代部分混合脱硫剂 , 用6 0~ 8 O k g 高铝渣 粉 , 7 8 3—1 3 6 5 k g 钙 基混合脱 硫剂 +1 9 0 k g L F除 尘灰对 初始 s含量 0 . 0 3 0 % ~0 . 0 7 0 %的 1 2 0 t 铁水进行 K R搅 拌脱 硫 预 处 理 8 m i n , 其终 点 s含 量 同 样 为 0 . 0 0 1 % 一
LF快速脱硫工艺研究

LF快速脱硫工艺研究摘要:依据LF脱硫机理和热力学原理,结合马钢炼钢厂LF炉的实际,从影响LF炉脱硫的因素、LF造渣工艺、渣系选择等方面,介绍了马钢炼钢厂LF炉快速脱硫的生产实践。
关键词:LF精炼快速脱硫渣系选择在实际的生产中,LF炉冶炼脱硫能力对后续能否生产出合格的产品至关重要。
特别是随着新产品开发的需要,对钢中S含量要求越来越高,对LF炉快速脱硫工艺要求更为严格。
因此在LF炉生产过程中快速有效的脱硫越来越受到我们的重视。
1 LF脱硫原理分析1.1 LF脱硫机理按照冶金学理论脱硫应该按如下步骤进行。
脱硫基本过程大体分为:硫由钢液内向钢-渣界面迁移;界面的化学反应,硫化物向渣层迁移。
1.2 热力学原理造渣脱硫过程中,常采用石灰做为脱硫剂,其脱硫反应按离子理论可写作[1]。
△G0=71965-38T,J/molKs=[aS2-·aO]/[aO2-·aS]=[(%S)·γS2-]/[aO2-·[%S]fS]或[%S]=1/Ks([(%S)·γS2-·aO])/([aO2-·fS](1-4)由式(2-2)可以看出,强化脱硫的热力学条件是:高碱度的渣(即增大aO2-);低氧位或强还原性(即降低aO);降低(%S)(即换渣);以及高温操作(因△H≈71965>0,提高温度使Ks值变大)。
2 影响LF脱硫的因素一般来说影响LF炉脱硫的因素有冶炼周期、钢中酸溶铝浓度及熔渣氧化性、熔渣碱度,吹氩搅拌强度等。
(1)冶炼还原期:LF炉在冶炼阶段的还原期脱硫效果最明显。
还原期从加入还原剂开始至通电结束,故可将精炼渣料提前加入钢包,使精炼渣尽快形成,从而在通电时间不变的情况下,延长还原时间,从而提高脱硫率。
同时,还原期的温度越高对脱硫越有利,这是由于高温是脱硫反应的热力学条件,但过高,渣层变稀,脱硫效果会略有降低。
(2)钢中酸溶铝浓度及熔渣氧:当钢中的酸溶铝在200×10-6左右,脱硫效果显著,当钢中氧性控制(FeO+MnO)小于1%,硫分配系数提高至150以上,脱硫显著。
酒钢转炉出钢脱硫工艺优化

•酒钢科技2019年第2期•酒钢转炉出钢脱硫工艺优化王春江,茹作栋(酒钢集团宏兴股份公司碳钢薄板厂,甘肃,嘉峪关,735100)摘要:转炉出钢结束后向钢包内加入钢渣改质剂,可以降低炉渣氧化性(£(FeO+MnO)的含量),提高转炉出钢脱硫效率。
酒钢宏兴股份公司碳钢薄板厂在120吨转炉出钢后加入钢渣改质剂,研究出钢后加入钢渣改质剂对钢水质量、脱硫能力的影响。
试验结果表明,出钢后加入钢渣改质剂,降低了炉渣氧化性,提高了脱硫效率,改善了钢水质量。
关键词:钢渣改质剂;炉渣氧化性;脱硫效率Optimization of Desulfurization Process for Converter TappingWang Chunjiang,Ru Zuodong(Carbon Steel Sheet Plant of Hongxing Iron&Steel Co.Ltd.,Jiuquan Iron and Steel(Group)Corporation,Jiayuguan,Gansu,735100)Abstract::After tapping of the converter,the steel slag modifier is added into the ladle, which can reduce the oxidizing property of the slag(the content of X(FeO+MnO))and improve the desulfurization efficiency of the converter.After tapping of120-ton converter in Carbon Steel Sheeet Plant of JISCO,the steel slag modifier were added into ladle to study the effect of steel slag modifier on the quality of the molten steel and the desulfurization capacity.The test results show that the steel slag modifier is added after tapping,which reduces the oxidization of the slag, improves the desulfurization efficiency,and improves I hr quality of the molten steel.Key words:steel slag modifier;oxidization of the slag;desulfurization efficiency1前言脱硫是转炉炼钢生产过程中的基本任务,在高炉铁水含硫量较高、废钢质量差的生产条件下.过大的脱硫任务将严重影响转炉的生产节奏,给生产组织带来困难。
酒钢120t转炉煤气回收及炉口微差压自动控制
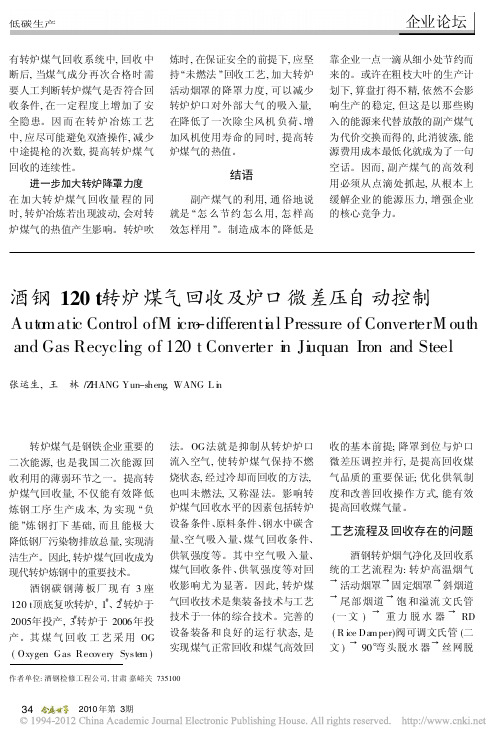
低碳生产企业论坛 2010年第3期有转炉煤气回收系统中,回收中断后,当煤气成分再次合格时需要人工判断转炉煤气是否符合回收条件,在一定程度上增加了安全隐患。
因而在转炉冶炼工艺中,应尽可能避免双渣操作,减少中途提枪的次数,提高转炉煤气回收的连续性。
进一步加大转炉降罩力度 在加大转炉煤气回收量程的同时,转炉冶炼若出现波动,会对转炉煤气的热值产生影响。
转炉吹炼时,在保证安全的前提下,应坚持/未燃法0回收工艺,加大转炉活动烟罩的降罩力度,可以减少转炉炉口对外部大气的吸入量,在降低了一次除尘风机负荷、增加风机使用寿命的同时,提高转炉煤气的热值。
结语副产煤气的利用,通俗地说就是/怎么节约怎么用,怎样高效怎样用0。
制造成本的降低是靠企业一点一滴从细小处节约而来的。
或许在粗枝大叶的生产计划下,算盘打得不精,依然不会影响生产的稳定,但这是以那些购入的能源来代替放散的副产煤气为代价交换而得的,此消彼涨,能源费用成本最低化就成为了一句空话。
因而,副产煤气的高效利用必须从点滴处抓起,从根本上缓解企业的能源压力,增强企业的核心竞争力。
酒钢120t 转炉煤气回收及炉口微差压自动控制Auto matic Control ofM icro -differenti al Pressure of ConverterM outh and Gas Recycli ng of 120t Converter i n Ji uquan Iron and Steel 张运生,王 林/Z HANG Yun-sheng ,WANG L i n作者单位:酒钢检修工程公司,甘肃嘉峪关735100转炉煤气是钢铁企业重要的二次能源,也是我国二次能源回收利用的薄弱环节之一。
提高转炉煤气回收量,不仅能有效降低炼钢工序生产成本,为实现/负能0炼钢打下基础,而且能极大降低钢厂污染物排放总量,实现清洁生产。
因此,转炉煤气回收成为现代转炉炼钢中的重要技术。
酒钢碳钢薄板厂现有3座120t 顶底复吹转炉,1#、2#转炉于2005年投产,3#转炉于2006年投产。
酒钢120 t转炉双渣法少渣炼钢工艺
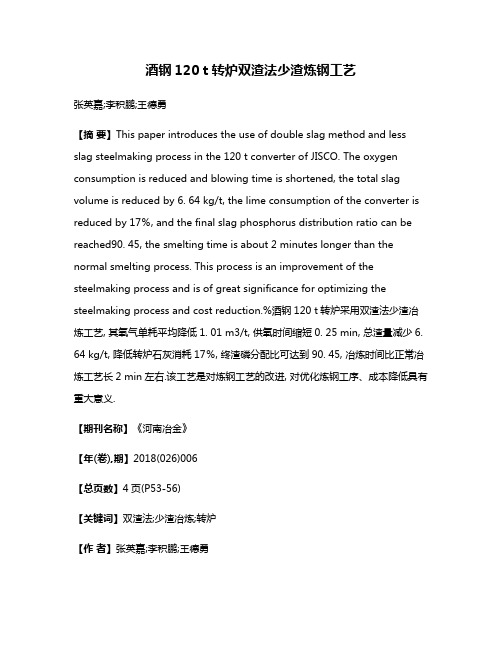
酒钢120 t转炉双渣法少渣炼钢工艺张英嘉;李积鹏;王德勇【摘要】This paper introduces the use of double slag method and less slag steelmaking process in the 120 t converter of JISCO. The oxygen consumption is reduced and blowing time is shortened, the total slag volume is reduced by 6. 64 kg/t, the lime consumption of the converter is reduced by 17%, and the final slag phosphorus distribution ratio can be reached90. 45, the smelting time is about 2 minutes longer than the normal smelting process. This process is an improvement of the steelmaking process and is of great significance for optimizing the steelmaking process and cost reduction.%酒钢120 t转炉采用双渣法少渣冶炼工艺, 其氧气单耗平均降低1. 01 m3/t, 供氧时间缩短0. 25 min, 总渣量减少6.64 kg/t, 降低转炉石灰消耗17%, 终渣磷分配比可达到90. 45, 冶炼时间比正常冶炼工艺长2 min左右.该工艺是对炼钢工艺的改进, 对优化炼钢工序、成本降低具有重大意义.【期刊名称】《河南冶金》【年(卷),期】2018(026)006【总页数】4页(P53-56)【关键词】双渣法;少渣冶炼;转炉【作者】张英嘉;李积鹏;王德勇【作者单位】酒钢集团宏兴钢铁股份有限公司甘肃.酒泉 (735100);酒钢集团宏兴钢铁股份有限公司甘肃.酒泉 (735100);酒钢集团宏兴钢铁股份有限公司甘肃.酒泉(735100)【正文语种】中文0 前言相对于传统的单渣法炼钢工艺,双渣法炼钢工艺的特点在于在冶炼过程中倒一次渣。
120吨钢包精炼炉工艺技术操作规程

中天钢铁集团第五炼钢厂中天钢铁集团有限公司120吨LF精炼炉工艺技术操作规程编制:苏旺张文惠宋晓东审核:陈军召万文华徐和平批准:吴献阳编号:生效日期:2010 年12月 1日受控印章:分发号:版本号:1.0 120吨LF精炼炉工艺技术操作规程目录第一部分钢包精炼工艺技术规程1.精炼工艺流程 (1)2.LF主要技术及设备参数 (2)3.LF处理功能及处理钢水类型 (7)4.LF处理前提条件 (8)5.LF工艺路线钢种及目标化学成分 (8)6.LF钢包炉测渣厚标准 (10)7.氩气介质标准 (10)8.钢包吹氩处理标准 (11)9.加热标准 (11)10.测温、取样、定氧标准 (14)11.造渣标准 (15)12.发泡剂加入标准 (15)13.成分微调标准 (16)14.喂丝处理标准 (17)15.钢水保温处理标准 (19)16.LF回余钢水处理标准 (19)17.LF处理工艺路线钢种温度标准 (20)18.电极更换标准 (20)19.加保温剂标准 (20)第二部分钢包精炼工艺操作规程1.操作前的检查与准备 (22)2.检查水冷炉盖有无漏水,炉盖上电极孔陶瓷环能否正常使用 (22)3.测温、取样操作 (23)4.送电加热 (23)5.造渣合金化 (24)6.LF处理结束 (25)7.喂丝操作 (25)8.接、滑电极操作 (26)9.异常情况处理 (27)10.记录 (28)第一部分 钢包精炼工艺技术规程1. 精炼工艺流程1.1 经LF 炉处理的钢水图1 经LF 炉处理的钢水工艺流程图1.2 保温处理的钢水图2 保温处理的钢水工艺流程图注:a) 定氧根据钢种生产技术操作标准要求进行。
b) 对Als 有要求的钢种在钢水到站后喂入铝线。
c) 喂入包芯线根据钢种生产技术操作标准进行。
2.LF主要技术及设备参数表1 LF主要技术及设备参数2.1主要技术参数电极电流密度(国产电极):27A/cm2电极最大电流:45KALF变压器功率(连续负载):26MV A电耗:0.46KWh/t℃LF炉气稀释后的烟气温度:130℃稀释后的烟气流量:60000Nm3/h颗粒度:<2μm:50%;<0.5μm:10%烟尘量:1~2kg/t稀释后烟气平均含尘量:10g/Nm3烟尘成分:主要为CaO,带有部分金属氧化物炉气成分:空气+2%CO22.2主要设备参数2.2.1料仓数量10个容积:12m3×2+4m3×82.2.2称量料斗数量:3个容积: 1.5m32.2.3钢包车车轮数量:4个运行距离:南车/北车15.5m/16.5m钢包车长度: 6.6m钢包车宽度: 4.9m钢包车高度: 2.22m轨距: 4.2m马达数量/功率(每台):2台/22KW2.2.4变压器型号HSSPZ-25000/35型式箱盖式运行方式额定容量时连续运行,超载20%时,连续运行2h额定容量25000kV A+20%一次额定电压35kV 50Hz二次电压395~190V 13级50Hz其中:395~345V为恒功率级;345~190V为恒电流级二次额定电流41837A联结组别YNd11阻抗电压8~10%端子出线方式侧出2.2.5电极提升立柱电极分布园直径Φ750mm电极升降最大行程~3000mm(可适当调整)电极升降速度自动上升/下降手动上升/下降6/4.8 m/min 6/4.8 m/min电极调节器性能参数电极响应时间启动时间≤0.15s制动时间≤0.10s非灵敏区5%~10% 2.2.6导电式电极臂电极夹持器直径:Φ750mm铜导电臂中电流密度:<5A/mm2电极夹持器液压缸数量:1个行程:52mm孔径:Φ230mm操作压力:11MPa2.2.7水冷炉盖估计耐材重量:1900kg炉盖外径:Φ4222mm炉盖高度(包括抽气管道):2197mm中心耐材盖下衬/上衬厚度:270/200mm电极孔直径:Φ520mm 观察孔汽缸数量:1个最大行程:220mm孔径:Φ222mm 取样门汽缸数量:1个最大行程:255mm孔径:Φ222mm水冷炉盖升降速度100mm/s水冷炉盖升降行程≥650mm水冷炉盖紧急提升响应时间<5s水冷炉盖升降型式液压升降2.2.8液压系统液压介质水-乙二醇系统工作压力12Mpa系统过滤精度10μ主泵电机容量3×30kW主泵电机转速1000r/min泵额定压力21MPa泵工作压力16 MPa泵流量100L/min循环泵电机容量1×3kW工作压力0.5 MPa流量59L/min冷却水进口压力0.6MPa冷却水进口温度<40℃冷却水出口温度50℃冷却水流量16m3/h蓄能器额定压力21 MPa蓄能器工作压力12 MPa油箱容积3000L2.2.9上料系统上料方式用10t桥吊吊运物料袋或钟式料罐料仓给料方式VVVF电机振动给料称量斗给料方式电机振动给料振动给料器给料能力80t/h称量斗精度≤0.3%加料精度1%加料时间2min皮带机带宽500mm皮带机带速 1.6m/s皮带机输送量80t/h散装料及铁合金料仓材质Q345B3.LF处理功能及处理钢水类型3.1LF钢包炉处理功能3.1.1钢水升温或钢水保温。
LF 精炼炉脱硫效率的生产实践研究

精炼炉脱硫效率的生产实践研究贾黎杰,杜亚伟,王二林(安阳钢铁集团有限责任公司第一炼轧厂,河南安阳)摘要:随着世界经济趋近于信息化的快速发展,现代工农业和科学技术的发展对于钢材的质量要求也越来越高。
本文对于影响钢材中脱硫的因素进行分析,从快速化渣、造渣脱氧及精炼温度等进行探讨。
以便选择合适的方法能够有效的提高精炼脱硫率,保证产品的质量,来适应快速发展的经济时代。
关键词:精炼;脱硫;精炼渣引言安阳钢铁集团公司第一炼轧厂顶底复吹转炉于年月日建成投产,标志着安钢三步走战略的第一步顺利完成。
配合台小方坯连铸机,台板坯连铸机,全连铸生产。
主要冶炼钢种为低合金钢、冷镦钢、钢绞线,小方坯(规格×)、板坯(规格×)。
连铸比,基本形成了复吹转炉→精炼→连铸→铸坯热送的现代化工艺流程。
然而硫是大多数钢材中的有害元素,它不但会引起钢材的脆度,并且还会增加表面的裂纹发生的几率,降低钢材的韧性。
目前精炼炉脱硫工艺已经成为了现代炼钢工艺中不可缺少的重要环节,这种技术的提高不仅可以减少钢材质量缺陷,并且能够减少能源材料和铁合金的消耗。
目前我国的主要脱硫的办法是精炼过程脱硫和渣洗脱硫。
精炼炉脱硫技术.精炼炉脱硫的发展史和功能精炼炉脱硫技术在世纪年代日本率先使用,当时是为了提高钢的质量和纯净度,并且能够降低成本。
将炉外技术用于生产特殊钢当中。
随后慢慢的传入西方的钢铁企业当中并且得到了大力发展和推广。
精炼脱硫的效率也在不断的增加。
通过现在科技的发展,已经能够达到~。
在出钢之前,要尽量去除氧化渣,在钢包之中重新造还原渣,从而保持钢包中依然具有还原性。
降低钢中含有的、、、等一系列元素的含量。
从而避免出现白点、偏析、大颗粒的夹杂物,保证钢材的韧性和抗拉强度。
.国内外精炼炉脱硫技术的对比以前传统的炉外精炼的施工流程为高炉→炼钢炉(转炉)→铸锭,现在已经慢慢的被高炉→铁水处理→炼钢炉→炉外精炼→连铸这新的工艺流程所替代,已经成为了大中型钢铁企业的主要生产工艺流程。
lf炉精炼脱硫效率的提高探究
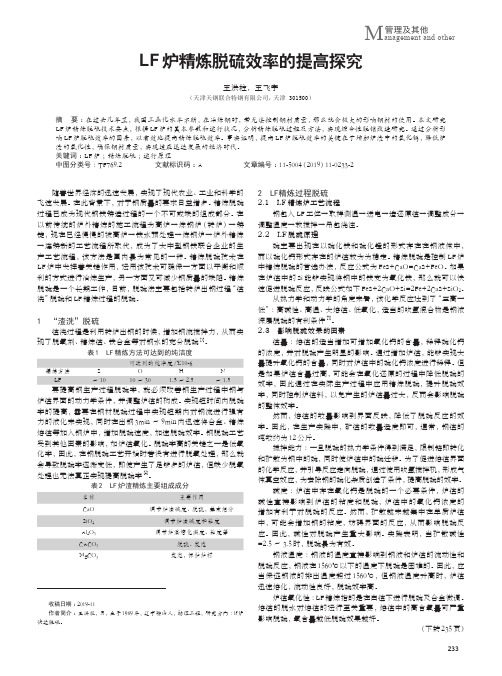
LF 炉精炼脱硫效率的提高探究王洪柱,王飞宇(天津天钢联合特钢有限公司,天津 301500)摘 要:在过去几年里,我国工业化水平不断,在冶炼钢时,若无法控制钢材质量,那么就会极大的影响钢材的使用。
本文研究LF 炉精炼脱硫技术要点,根据LF 炉的基本参数和运行状况,分析精炼脱硫过程及方法,实现综合性脱销改造研究。
通过分析影响LF 炉脱硫效率的因素,以有效地提高精炼脱硫效率。
事实证明,提高LF 炉脱硫效率的关键在于增加炉渣中的氧化钙,降低炉渣的氧化性,确保钢材质量,实现适应迅速发展的经济时代。
关键词:LF 炉;精炼脱硫;运行原理中图分类号:TF769.2 文献标识码:A 文章编号:11-5004(2019)11-0233-2收稿日期:2019-11作者简介:王洪柱,男,生于1989年,辽宁鞍山人,助理工程,研究方向:lf 炉快速脱硫。
随着世界经济的迅速发展,实现了现代农业、工业和科学的飞速发展。
在此背景下,对于钢质量的要求日益增多。
精炼脱硫过程已成为现代钢铁铸造过程的一个不可或缺的组成部分。
在以前传统的炉外精炼的施工流程为高炉→炼钢炉(转炉)→铸锭,现在已经慢慢的被高炉→铁水预处理→炼钢炉→炉外精炼→连铸新的工艺流程所取代,成为了大中型钢铁联合企业的生产工艺流程,该方法是国内最为常见的一种。
精炼脱硫技术在LF 炉中发挥着关键作用,运用该技术可确保一方面以平衡和顺利的方式进行冶炼生产,另一方面又可减少钢质量的缺陷。
精炼脱硫是一个长期工作,目前,脱硫法主要包括转炉出钢过程“渣洗”脱硫和LF 精炼过程的脱硫。
1 “渣洗”脱硫渣洗过程是利用转炉出钢的时候,增加钢流搅拌力,从而实现了脱氧剂、精炼渣、铁合金等对钢水的充分脱硫[1]。
表1 LF 精炼方法可达到的纯洁度可达到的纯净度/X10-6精炼方法S O H NLF~1010~30 1.5~2.5~1.5要提高钢生产过程脱硫率,就必须改善钢生产过程中钢与炉渣界面的动力学条件,并调整炉渣的构成。
- 1、下载文档前请自行甄别文档内容的完整性,平台不提供额外的编辑、内容补充、找答案等附加服务。
- 2、"仅部分预览"的文档,不可在线预览部分如存在完整性等问题,可反馈申请退款(可完整预览的文档不适用该条件!)。
- 3、如文档侵犯您的权益,请联系客服反馈,我们会尽快为您处理(人工客服工作时间:9:00-18:30)。
120t LF快速脱硫工艺实践
李积鹏成东全杨鑫吕钢
酒泉钢铁集团有限责任公司碳钢薄板厂,甘肃嘉峪关735100
摘要:本人介绍和分析了碳钢薄板厂120t精炼薄板坯连铸钢水时的快速脱硫工艺,生产实践表明,合理的渣系组成、温度控制、酸溶铝含量及吹氩搅拌是实现快速脱硫的关键技术。
关键词:LF 脱硫工艺实践
薄板坯连铸由于是在高拉速条件下(3.0-6.0m/min)进行,铸坯厚度薄,浇钢空间狭小,又采用复杂横截面的长漏斗型结晶器,为保证连续浇铸和薄板坯表面质量,对硫含量提出了更高的要求,一般要控制W(S)<0.010%,同时,薄板坯连铸的生产还需要时间节奏、温度的协调匹配。
因此,开发LF快速脱硫工艺是薄板坯连铸短流程生产线的一个重要研究课题。
自2008年以来,碳钢薄板厂对 LF快速脱硫工艺进行了有针对性的研究,取得了较好的效果。
1.LF设备主要参数
碳钢薄板厂120t LF主要参数如下。
2.薄板坯连铸钢水精炼工艺流程
钢水进站→自动或手动接底吹氩管→喂入铝线→钢包开至LF处理位→测温取样→加渣料、送电升温、造还原渣→调整钢水成分→测温取样→弱吹→钙处理→静吹5—8min→成分温度合格→加保温剂→钢包开至起吊位→吊包→薄板坯连铸机
3.脱硫的热力学动力学研究
3.1 脱硫反应
在钢—渣界面上的脱硫反应是伴有电子转移的置换反应,其基本式为:
[S]+2e=(S2-)
为保持电极中性,必有一些能释放电子的元素同时经过界面进入渣中,对于铝镇静钢来说,脱硫基本反应为:
3(O2-)+3[S]+2[Al]=3(S2-)+(Al2O3)
3.2炉渣的脱硫能力
适当增加渣量,可以稀释渣中CaS浓度,加快脱硫速度。
但渣量过大会使炉渣过厚,影响钢渣界面反应。
在实际生产过程中,由于转炉渣中FeO含量高,出钢下渣过多,会影响造白渣过程,从而恶化脱硫过程降低脱硫效率。
因此,在生产实践中转炉出钢下渣量要求小于5kg/t。
从热力学角度考虑,脱硫反应是在还原性气氛中进行,渣中FeO含量高不利于脱硫反应。
根据生产数据,在脱硫反应中渣中FeO含量与硫分配系数的关系如图1所示。
此外,在生产实践中还发现,渣中W(FeO+MnO)<1%时,脱硫反应速率显著提高。
图1 渣中FeO含量与硫分配系数的关系
3.3钢水温度
提高钢水温度有利于脱硫反应的进行,同时可以加快渣料溶化速度,改善钢水流动性,加快渣钢反应速度,从而加速脱硫。
生产实践表明,钢水温度低于1560℃时,脱硫速度明显降低;钢水温度高于1560℃时,渣料溶化快,炉渣流动性好,脱硫反应快。
因此,根据我厂实际情况,要求转炉钢水进站温度不低于1530℃,且进站后快速进行升温。
3.4钢中酸溶铝含量
经计算,钢中W(Al)<70×10-6时,钢水W(O)>20×10-6,不利于脱硫反应的进行。
钢水的脱氧与脱硫是相互联系的,脱氧良好的钢水可提高炉渣的脱硫能力,钢水深脱氧是深脱
硫的必要条件,并符合以下规律:
][][30O S a W =
式中a [O ]指钢水中氧的活度。
通过统计分析生产数据,钢中酸溶铝含量与脱硫率的关系如图2所示。
图2 酸溶铝含量与脱硫率的关系
从图2可以看出,钢中W(Al)>200×10-6时脱硫率显著提高,若再提高钢中酸溶铝含量,
则脱硫率提高不明显。
因此,要求转炉到LF 钢中W(Al)要大于150×10-6。
3.5 CaF 2含量 CaF 2本身没有脱硫能力,但加入炉渣中可使脱硫速率显著提高,这说明CaF 2在脱硫过程中可以起到类似于催化剂的作用,其机理是:①CaF 2可以于网状硅酸盐发生反应,提供少量的O 2-,使渣中自由O 2-增多;②CaF 2能显著降低炉渣熔点,改善动力学条件,使硫容易向CaO 等破网组元固相扩散;③氟离子可以破坏硅酸盐赖以结合的化学键,形成空隙,使硫更容易扩散到CaO 等金属氧化物内部。
最终的结果是随着CaF 的增加,脱硫速度和脱硫率都大大提高。
3.6 吹氩搅拌
氩气搅拌可以增大钢—渣反应界面,增加钢渣反应的几率,加快反应速度。
从动力学角度分析,钢包精炼炉中脱硫反应的限制环节是钢液本体向钢—渣界面的传质过程,因此加大气量搅拌有利于提高脱硫反应速度。
文献
[2]指出,脱硫时钢水搅拌能一般大于7000W/t ,
钢水搅拌能计算公式如下: )]1046.11ln(1[18.60
50101P H T T W T Q g Ar -⨯++-=ε 式中,Q Ar 为氩气流量,m 3/h ;T 1、T 0分别为钢水和氩气的温度,K ;H 为吹氩深度,m ;P 0
为氩气压力,Pa ;W g 为钢水重量,t 。
在我厂LF精炼条件下,吹氩脱硫阶段的平均搅拌能约为6500W/t,基本满足脱硫工艺的要求。
3.7钙处理
钙处理的目的主要是对钢水中Al2O3夹杂进行变性球化处理,使之形成12CaO·7 Al2O3夹杂,防止中间包浸入式水口堵塞,一般要求钢水中Ca/Al>0.1。
通过对喂CaSi线前后钢水取样分析表明,喂CaSi线后钢水可近一步深脱硫,平均脱硫率为13.5%。
4.快速脱硫工艺的开发与实践
根据理论分析及实际生产情况,合理的渣系组成、温度控制、钢中酸溶铝含量、吹氩搅拌及喂线技术是实现LF快速脱硫的关键技术。
因此,制定了如下工艺路线:
(1)造渣制度:根据实际情况及成本因素,我厂120t LF精炼渣料实际消耗为石灰6~10kg/t;萤石1.5~3 kg/t;预熔精炼渣3~4kg/t;石灰:萤石=4:1。
表2为合理的渣系成分以及实际控制的渣系成分。
在实际生产中还发现,越早造白渣,脱硫效率越高,因此要求钢水进站后立即喂铝线脱氧,一次送电结束后要求成渣。
表2 渣系成分控制情况
W(CaO) W(Al2O3) W(FeO+MnO) W(SiO2) W(MgO)
合理的渣系成分 50~60 20~30 <1 6~8 ——
实际渣系成分 50~60 15~25 <1.5 4~8 5~8 (2)温度制度:我厂要求进LF精炼站钢水温度>1530℃,过程温度控制在1580℃~1620℃。
从图3可以看出,温度<1560℃时,脱硫率将会明显降低。
图3 钢水温度与脱硫率的关系
(3)酸溶铝含量控制:要求进LF精炼站钢水W(Al)>200×10-6,过程W(Al)控制在300—600×10-6。
从实际情况看,脱硫率良好。
(4)氩气搅拌制度:为保证脱硫及去除夹杂物,要求脱硫阶段底吹吹开度700—900mm;均匀成分温度及送电升温时,底吹吹开度400—600mm;钙处理前后静(软)吹时,底吹吹
开度200—300mm,避免钢水液面裸露而被二次氧化。
(5)钙处理制度:一般要求钙处理前钢中W(S)<0.010%,钙处理完毕后,Ca/Al>0.1,静吹时间8—12min。
5.工艺效果
采用快速脱硫工艺后,我厂LF脱硫周期明显缩短,能满足薄板坯连铸生产节奏的要求,为稳定薄板坯连铸生产提供了保障。
6.结语
6.1降低渣中 FeO的含量是实现快速深脱硫的关键环节,转炉工序应采取措施尽量减少下渣量,挡渣出钢,LF炉在最短时间内造好白渣,为实现快速深脱硫创造良好的条件。
6.2合理控制精炼处理过程中的温度,为快速脱硫创造良好的热力学条件。
6.3在 LF处理过程中,各环节吹氩搅拌强度的控制对脱硫效果有很大的影响,因此,合理控制吹氩强度也是快速深脱硫工艺的关键所在。
[参考文献]
[1] 周宏.硫在CaO-AlO系熔渣与钢液间的分配率[J].钢铁,1995
[2] 韩其勇.冶金过程动力学[M].北京:冶金工业出版社,1998.。