产线异常处理流程及技巧
公司制造异常处理流程

公司制造异常处理流程公司制造异常处理流程通常包括以下几个步骤:一、异常检测:-在生产过程中,设备、传感器或人工操作会不断产生数据。
异常检测的第一步是收集这些数据,包括生产线上的传感器数据、设备状态数据、产品质量数据等。
异常检测是制造业中非常重要的一环,它旨在及时识别和捕捉生产过程中的异常情况,以便采取相应的措施来避免或减少不良影响。
以下是对异常检测的详细介绍:1. 数据收集:-在生产过程中,各种设备、传感器和生产线会产生大量数据,包括温度、湿度、压力、振动等各种传感器数据,以及设备状态数据、产品质量数据等。
异常检测的第一步是收集这些数据,通常通过自动化系统或数据采集设备进行实时或定期采集。
2. 数据预处理:-收集到的数据可能存在噪声、缺失值或异常值,因此需要进行数据预处理。
这包括数据清洗(去除噪声和异常值)、填补缺失值、数据转换等操作,以确保数据的准确性和完整性。
3. 特征提取:-在异常检测中,需要从原始数据中提取特征,这些特征可以是统计量、频域特征、时域特征等。
特征提取的目的是将原始数据转换为更具代表性和可分辨性的特征,以便后续的异常检测算法能够更好地识别异常情况。
4. 异常检测算法:-异常检测算法可以采用各种方法,包括基于统计学的方法(如均值、标准差、箱线图等)、基于机器学习的方法(如聚类、支持向量机、神经网络等)、基于规则的方法等。
这些算法可以用来识别数据中的异常模式或行为。
5. 模型训练与评估:-如果使用机器学习或统计模型进行异常检测,需要对模型进行训练和评估。
这包括将数据集划分为训练集和测试集,使用训练集训练模型,并使用测试集评估模型的性能。
6. 实时监测与反馈:-异常检测通常需要实时监测生产过程中的数据,并对异常情况进行及时反馈。
这可能涉及到实时数据流处理、报警系统的触发、以及相关人员的及时介入和处理。
异常检测在制造业中扮演着非常重要的角色,它可以帮助企业及时发现生产过程中的异常情况,减少损失,提高生产效率,保障产品质量。
SMT产线异常处理流程
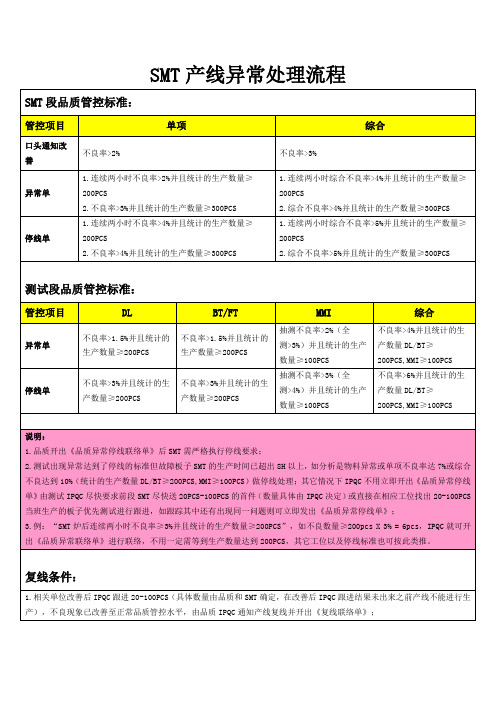
3.注意事项:复现条件成立时,速度要快,可先口头通知再签复线单。
停线后处理事宜:
1.品质部主导停线改善事宜,重点跟踪改善效果的跟进,尽量缩短停线时间;
不良率>6%并且统计的生产数量DL/BT≥200PCS,MMI≥100PCS
说明:
1.品质开出《品质异常停线联络单》后SMT需严格执行停线要求;
2.测试出现异常达到了停线的标准但故障板子SMT的生产时间已超出8H以上,如分析是物料异常或单项不良率达7%或综合不良达到10%(统计的生产数量DL/BT≥200PCS,MMI≥100PCS)做停线处理;其它情况下IPQC不用立即开出《品质异常停线单》由测试IPQC尽快要求前段SMT尽快送20PCS-100PCS的首件(数量具体由IPQC决定)或直接在相应工位找出20-100PCS当班生产的板子优先测试进行跟进,如跟踪其中还有出现同一问题则可立即发出《品质异常停线单》;
3.例:“SMT炉后连续两小时不良率≥3%并且统计的生产数量≥200PCS”,如不良数量≥200pcs X 3% = 6pcs,IPQC就可开出《品质异常联络单》进行联络,不用一定需等到生产数量达到200PCS,其它工位以及停线标准也可按此类推。
复线条件:
1.相关单位改善后IPQC跟进20-100PCS(具体数量由品质和SMT确定,在改善后IPQC跟进结果未出来之前产线不能进行生产),不良现象已改善至正常品质管控水平,由品质IPQC通知产线复线并开出《复线联络单》;
SMT产线异常处理流程
生产异常处理流程

1.目的为更加规范生产现场在发生异常时,能及时准确地反映并能通过相关人员确认、分析、及时解决,确保生产顺利进行特制订此规定。
2.范围适用公司生产中心下辖所有生产线上发生的异常现象。
3.权责3.1生产线组长:负责提出异常与工程部、品质部、PMC配合处理,确认异常是否属实,并按起异常信号指示灯。
3.2工程部:负责结构、设计方面异常分析,提出改善对策。
3.3品质部:负责生产线异常分析,提出改善对策并跟进改善结果及效果确认,对来料进行管控,并对此类异常制定纠正预防措施。
3.4总经办:稽核项目、结构、来料异常的过程及异常解决情况。
3.5采购部:负责对来料异常与供应商的沟通协调异常处理。
3.6PMC部:负责异常产生的生产计划排程重新制定和异常工时的申报。
4.生产线出现异常处理规则及注意事项4.1当生产线不良率超过15%时,立即开起红色信号灯。
4.2工程部、品质部、PMC接到异常信号指示灯(红灯亮)时,10分钟到达生产线信号指示灯现场处理异常。
4.3生产现场发生异常时品质部或工程部确认后,并马上反馈给生产线组长给予指示,如果生产线组长将异常反馈给工程部、品质部在30分钟内没给出指示的,生产线有权停线、待工。
4.4生产线异常发生时,品质部、工程部在30分钟内给出短期解决措施,如需更改工艺或制做工装夹具的工部须在1H内给出解决措施。
4.5如果出现重大品质异常,不能完善解决问题,由工程部知会PMC组织相关部门开会商计解决。
4.6工程部分析异常原因必须要正确、专业、给出解决方案要具有可操作性,并能通过相关部同意方可有效。
4.7出现异常后如果需要更改工艺或返工、生产中心、品质部有权要求工程部作出作业指导书,工程部在4H内作出简易的作业指导书或返工流程给相关部门确认,品质部现场跟进,监督生产作业。
4.8以上整个过程品质部要监督跟进,有任何问题要及时汇报。
4.9因来料异常由品质部判断归属物料不良的,由生产中心将物料退回仓库进行换料。
产线异常处理流程及技巧
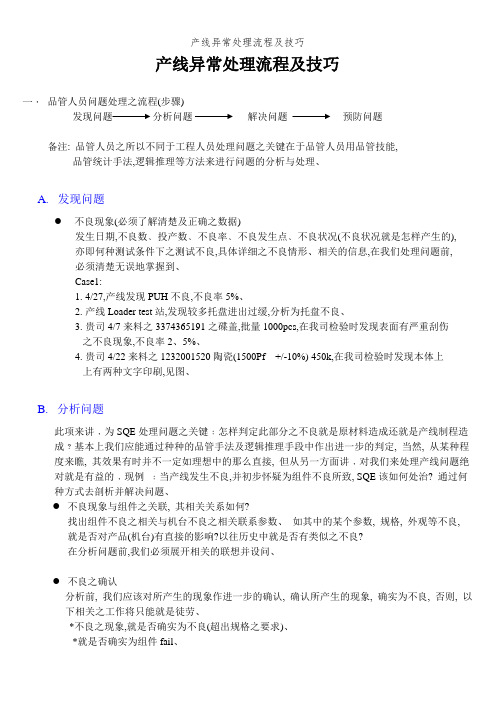
产线异常处理流程及技巧一.品管人员问题处理之流程(步骤)发现问题分析问题解决问题预防问题备注: 品管人员之所以不同于工程人员处理问题之关键在于品管人员用品管技能,品管统计手法,逻辑推理等方法来进行问题的分析与处理、A.发现问题●不良现象(必须了解清楚及正确之数据)发生日期,不良数﹑投产数﹑不良率﹑不良发生点﹑不良状况(不良状况就是怎样产生的),亦即何种测试条件下之测试不良,具体详细之不良情形、相关的信息,在我们处理问题前,必须清楚无误地掌握到、Case1:1.4/27,产线发现PUH不良,不良率5%、2.产线Loader test站,发现较多托盘进出过缓,分析为托盘不良、3.贵司4/7来料之3374365191之碟盖,批量1000pcs,在我司检验时发现表面有严重刮伤之不良现象,不良率2、5%、4.贵司4/22来料之1232001520陶瓷(1500Pf +/-10%) 450k,在我司检验时发现本体上上有两种文字印刷,见图、B.分析问题此项来讲﹐为SQE处理问题之关键﹕怎样判定此部分之不良就是原材料造成还就是产线制程造成﹖基本上我们应能通过种种的品管手法及逻辑推理手段中作出进一步的判定, 当然, 从某种程度来瞧, 其效果有时并不一定如理想中的那么直接, 但从另一方面讲﹐对我们来处理产线问题绝对就是有益的﹐现例﹕当产线发生不良,并初步怀疑为组件不良所致, SQE该如何处治? 通过何种方式去剖析并解决问题、●不良现象与组件之关联, 其相关关系如何?找出组件不良之相关与机台不良之相关联系参数、如其中的某个参数, 规格, 外观等不良,就是否对产品(机台)有直接的影响?以往历史中就是否有类似之不良?在分析问题前,我们必须展开相关的联想并设问、●不良之确认分析前, 我们应该对所产生的现象作进一步的确认, 确认所产生的现象, 确实为不良, 否则, 以下相关之工作将只能就是徒劳、*不良之现象,就是否确实为不良(超出规格之要求)、*就是否确实为组件fail、相关的不良之判定,需经验之积累、针对一些比较模糊的规格,希望尽量能量化来定义、如: 杂音的判定,焊锡性不良之判定等、●分析过程及方法: 前提:( 若初步分析为原材不良所致)组件不良确认:a.交叉实验法(尽可能多机种, 多状态, 多次实验作确认, 尽可能比较全面地得到第一信息、)*单体简单比较(单次)*多因子之间比较(机种, F/W, 线别, DISC,厂商,Date Code)*单体多次比较(PCBA, Mega)举例: ( PUH, MOTOR, CHIP-C等)b、借助我们现有之零件测试设备对零件参数作测试确认、这一点要求我们所有的SQE 人员在执行时日常的工作中应不断地提升我们对零件, 产品相关的认知, 不断提升 IQC检验之精准度, 可用性及实效性, 尽可能地从组件本身参数特性及与我们产品之相配性作检测, 如塑料件(尺寸, 实配治具等)、以厂商认可的测试判定方法来进行量化的判定、b.待不良确认后, 用罗辑, QC方法进一步展开原因之深入调查、品管人员在处理问题时,最重要的一点同时也就是最首要的工作就是进行相关数据的收集统计并分析,从而得出我们所需求的信息、*不良现象之集中性? 变羿性? 就是我们考究的重点、在此仅以材料羿常处理查德检表, 以供各位在日常工作中能灵活运用, 势必在处理相关问题时会得心应手、1.问题确认➢不良现象发生之日期, 时间?➢在哪一段时间这不良率DPPM就是多少?➢不良数就是否集中在哪一条件?➢不良数就是否集中在哪一个班?➢不良数就是否集中在哪一产品型号(版别)?➢不良品之DATE CODE 为何? 就是否有信集中之趋势?➢不良数就是否集中在哪一个基板位置?➢以前就是否有类似现象发生过?➢不良就是否集中在哪一个测试治具?➢仪嚣治具就是否有维修或不良?➢不良出现前后, 生产条件就是否有变更(5M: 人,机,材,法,量测)➢其她供货商之供料就是否有类似疵病?➢IQC 之SIP就是否有针对此项疵病作检验?➢IQC就是否有检验仪具与能力?以上经由收集相关资料来进一步判定不良现象之集中性及相关之 QC手法(查检表, 层别法), 对不良问题点作初步的判定并相关对策之实施、不良分析Case1:●手插5条线、●Function test ‘27项’不良、●初步分析为C221电容不良(Chip-C)d、利用前后制程的一致性来推断不良产生之原因、利用各前后制程之测试状况作相应之判定、相关以上不良问题而产生的一种重要的分析方法------实验法、各种实验的实施,能有效地辅助我们进行问题的分析与处理、C、解决问题内部➢满足产线正常生产为第一需求, 利上以上相关判定之信息, 换用其她DATE CODE, 厂商, 批次等料正常上线并追踪。
生产异常处理作业程序
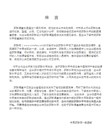
验证:所有问题的解决措施验证由责任部门牵头,相关部门协助,验证数量不少于10pcs,确认问题得到解决的才能交生产批量生产验证,质管部工程师、巡检员跟踪对策在批量生产实施效果并及时反馈情况。
一般问题发生30分钟得不到有效解决时,产线必须上报到车间主任,1小时不能解决的(电话)上报到生产厂长,由生产部经理积极推进问题的处理,跟进处理进度,当2小时内责任部门仍无有效对策的,生产部经理必须向生产总监汇报情况。
验证:所有问题的解决措施验证由责任部门牵头,相关部门协助,验证数量不少于10pcs,确认问题得到解决的才能交生产批量生产验证,质管部工程师、巡检员跟踪对策在批量生产实施效果并及时反馈情况。
在工艺部给出临时措施后,QE要对临时措施有效性进行确认,如对策无效,由工艺部在30分钟内重新制定新的临时对策。
对执行临时对策造成异常公式的,由生产部统计并上报异常工时,由IE进行核算。 QE上质量信息单跟踪责任单位永久措施
生产异常处理作业程序
1.0目的:
1、 目的:为建立各相关部门对生产异常的责任制度,以减少效率损失,特制定本程序。 为产线出现异常时的处理方法提供指导,包括异常发生与解决、内部检讨、原因调查、预防与围堵措施安排实施及产品质量的持续改进,以确保 2、 使用范围:本公司生产过程中异常发生时。 3、 职责:
工艺部:负责对异常的分析,现场处理,临时改善对策提供、改善过程跟进以及改善标准文件的提供。
5、 异常问题反馈处理流程:
5.1 对严重问题处理
生产环节中的质量异常处理流程

生产环节中的质量异常处理流程在生产过程中,质量异常处理流程是确保产品质量符合标准的重要环节之一。
本文将从质量异常的定义、异常处理流程的目的及步骤、质量异常处理的注意事项等方面进行探讨。
一、质量异常的定义质量异常是指在生产过程中出现的与产品质量标准不符的情况。
这些异常可能包括但不限于产品缺陷、工艺问题、材料问题等。
质量异常可能会导致产品出现质量问题,降低产品性能和可靠性。
二、质量异常处理流程的目的及步骤1. 目的质量异常处理流程的主要目的是及时发现、分析和解决生产中出现的异常情况,保障产品质量符合标准要求,提高产品的品质和竞争力。
2. 步骤(1) 异常发现与记录生产环节中的质量异常通常会通过质量管理系统、生产数据监控、质量检验等手段被发现。
一旦发现异常,需要及时记录并进行初步描述,包括异常种类、发生时间、影响范围等信息。
(2) 异常分析异常发生后,需要对其进行深入分析,找出问题的原因和影响因素。
这包括对产品、工艺、设备、操作流程等多个方面进行综合分析,以确定异常的根本原因。
(3) 制定解决方案在分析异常原因的基础上,制定具体的解决方案。
这些方案可能包括调整工艺参数、改进生产设备、更换材料等措施,以达到消除异常、提高产品质量的目的。
(4) 实施解决方案根据制定的解决方案,进行相应的调整和改进,并确保实施过程的有效性。
实施解决方案需要对涉及的工艺、设备、生产线进行调整,并在实施过程中进行跟踪和监控,确保解决方案的有效性。
(5) 验证与评估在解决方案实施后,需要对其效果进行验证和评估。
这包括对产品质量进行检测和评估,以确定解决方案是否取得了预期的效果。
三、质量异常处理的注意事项1. 快速响应生产环节中的质量异常需要快速响应,尽早发现和处理。
及时处理异常可以最大程度地减少产品质量问题的发生,并降低对生产进度和成本的影响。
2. 问题溯源在处理质量异常时,必须进行问题溯源,找出根本原因。
仅仅通过对表面问题的处理是不够的,需要深入分析和探究,以避免类似问题再次发生。
产线异常处理流程及技巧
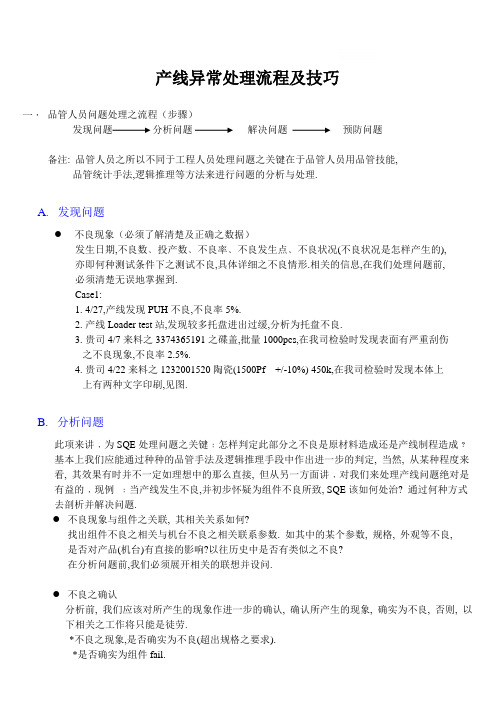
产线异常处理流程及技巧一.品管人员问题处理之流程(步骤)发现问题分析问题解决问题预防问题备注: 品管人员之所以不同于工程人员处理问题之关键在于品管人员用品管技能,品管统计手法,逻辑推理等方法来进行问题的分析与处理.A.发现问题●不良现象(必须了解清楚及正确之数据)发生日期,不良数﹑投产数﹑不良率﹑不良发生点﹑不良状况(不良状况是怎样产生的),亦即何种测试条件下之测试不良,具体详细之不良情形.相关的信息,在我们处理问题前,必须清楚无误地掌握到.Case1:1.4/27,产线发现PUH不良,不良率5%.2.产线Loader test站,发现较多托盘进出过缓,分析为托盘不良.3.贵司4/7来料之3374365191之碟盖,批量1000pcs,在我司检验时发现表面有严重刮伤之不良现象,不良率2.5%.4.贵司4/22来料之1232001520陶瓷(1500Pf +/-10%) 450k,在我司检验时发现本体上上有两种文字印刷,见图.B.分析问题此项来讲﹐为SQE处理问题之关键﹕怎样判定此部分之不良是原材料造成还是产线制程造成﹖基本上我们应能通过种种的品管手法及逻辑推理手段中作出进一步的判定, 当然, 从某种程度来看, 其效果有时并不一定如理想中的那么直接, 但从另一方面讲﹐对我们来处理产线问题绝对是有益的﹐现例﹕当产线发生不良,并初步怀疑为组件不良所致, SQE该如何处治? 通过何种方式去剖析并解决问题.●不良现象与组件之关联, 其相关关系如何?找出组件不良之相关与机台不良之相关联系参数. 如其中的某个参数, 规格, 外观等不良,是否对产品(机台)有直接的影响?以往历史中是否有类似之不良?在分析问题前,我们必须展开相关的联想并设问.●不良之确认分析前, 我们应该对所产生的现象作进一步的确认, 确认所产生的现象, 确实为不良, 否则, 以下相关之工作将只能是徒劳.*不良之现象,是否确实为不良(超出规格之要求).*是否确实为组件fail.相关的不良之判定,需经验之积累.针对一些比较模糊的规格,希望尽量能量化来定义.如: 杂音的判定,焊锡性不良之判定等.●分析过程及方法: 前提:( 若初步分析为原材不良所致)组件不良确认:a.交叉实验法(尽可能多机种, 多状态, 多次实验作确认, 尽可能比较全面地得到第一信息.)*单体简单比较(单次)*多因子之间比较(机种, F/W, 线别, DISC,厂商,Date Code)*单体多次比较(PCBA, Mega)举例: ( PUH, MOTOR, CHIP-C等)b. 借助我们现有之零件测试设备对零件参数作测试确认.这一点要求我们所有的SQE 人员在执行时日常的工作中应不断地提升我们对零件, 产品相关的认知, 不断提升 IQC检验之精准度, 可用性及实效性, 尽可能地从组件本身参数特性及与我们产品之相配性作检测, 如塑料件(尺寸, 实配治具等).以厂商认可的测试判定方法来进行量化的判定.b.待不良确认后, 用罗辑, QC方法进一步展开原因之深入调查.品管人员在处理问题时,最重要的一点同时也是最首要的工作是进行相关数据的收集统计并分析,从而得出我们所需求的信息.*不良现象之集中性? 变羿性? 是我们考究的重点. 在此仅以材料羿常处理查德检表, 以供各位在日常工作中能灵活运用, 势必在处理相关问题时会得心应手.1.问题确认➢不良现象发生之日期, 时间?➢在哪一段时间这不良率DPPM是多少?➢不良数是否集中在哪一条件?➢不良数是否集中在哪一个班?➢不良数是否集中在哪一产品型号(版别)?➢不良品之DATE CODE 为何? 是否有信集中之趋势?➢不良数是否集中在哪一个基板位置?➢以前是否有类似现象发生过?➢不良是否集中在哪一个测试治具?➢仪嚣治具是否有维修或不良?➢不良出现前后, 生产条件是否有变更(5M: 人,机,材,法,量测)➢其他供货商之供料是否有类似疵病?➢IQC 之SIP是否有针对此项疵病作检验?➢IQC是否有检验仪具与能力?以上经由收集相关资料来进一步判定不良现象之集中性及相关之 QC手法(查检表, 层别法), 对不良问题点作初步的判定并相关对策之实施.不良分析Case1:●手插5条线.●Function test ‘27项’不良.●初步分析为C221电容不良(Chip-C)d. 利用前后制程的一致性来推断不良产生之原因.利用各前后制程之测试状况作相应之判定.相关以上不良问题而产生的一种重要的分析方法------实验法.各种实验的实施,能有效地辅助我们进行问题的分析与处理.C. 解决问题内部➢满足产线正常生产为第一需求, 利上以上相关判定之信息, 换用其他DATE CODE, 厂商, 批次等料正常上线并追踪。
工作生产发生异常时的处置流程及处置方法

工作生产发生异常时的处置流程及处置方法下载温馨提示:该文档是我店铺精心编制而成,希望大家下载以后,能够帮助大家解决实际的问题。
文档下载后可定制随意修改,请根据实际需要进行相应的调整和使用,谢谢!并且,本店铺为大家提供各种各样类型的实用资料,如教育随笔、日记赏析、句子摘抄、古诗大全、经典美文、话题作文、工作总结、词语解析、文案摘录、其他资料等等,如想了解不同资料格式和写法,敬请关注!Download tips: This document is carefully compiled by theeditor.I hope that after you download them,they can help yousolve practical problems. The document can be customized andmodified after downloading,please adjust and use it according toactual needs, thank you!In addition, our shop provides you with various types ofpractical materials,such as educational essays, diaryappreciation,sentence excerpts,ancient poems,classic articles,topic composition,work summary,word parsing,copy excerpts,other materials and so on,want to know different data formats andwriting methods,please pay attention!工作生产异常时的处置流程及方法在任何生产环境中,无论规模大小,都可能出现各种预期之外的异常情况。
产线异常处理流程及技巧

产线异常处理流程及技巧一.品管人员问题处理之流程(步骤)发现问题分析问题解决问题预防问题备注: 品管人员之所以不同于工程人员处理问题之关键在于品管人员用品管技能,品管统计手法,逻辑推理等方法来进行问题得分析与处理、A.发现问题●不良现象(必须了解清楚及正确之数据)发生日期,不良数﹑投产数﹑不良率﹑不良发生点﹑不良状况(不良状况就是怎样产生得),亦即何种测试条件下之测试不良,具体详细之不良情形.相关得信息,在我们处理问题前,必须清楚无误地掌握到.Case1:1.4/27,产线发现PUH不良,不良率5%.2.产线Loader test站,发现较多托盘进出过缓,分析为托盘不良.3.贵司4/7来料之3374365191之碟盖,批量1000pcs,在我司检验时发现表面有严重刮伤之不良现象,不良率2。
5%.4.贵司4/22来料之1232001520陶瓷(1500Pf +/—10%) 450k,在我司检验时发现本体上上有两种文字印刷,见图。
B.分析问题此项来讲﹐为SQE处理问题之关键﹕怎样判定此部分之不良就是原材料造成还就是产线制程造成﹖基本上我们应能通过种种得品管手法及逻辑推理手段中作出进一步得判定, 当然, 从某种程度来瞧,其效果有时并不一定如理想中得那么直接,但从另一方面讲﹐对我们来处理产线问题绝对就是有益得﹐现例﹕当产线发生不良,并初步怀疑为组件不良所致, SQE该如何处治?通过何种方式去剖析并解决问题、●不良现象与组件之关联, 其相关关系如何?找出组件不良之相关与机台不良之相关联系参数. 如其中得某个参数, 规格,外观等不良, 就是否对产品(机台)有直接得影响?以往历史中就是否有类似之不良?在分析问题前,我们必须展开相关得联想并设问、●不良之确认分析前, 我们应该对所产生得现象作进一步得确认,确认所产生得现象, 确实为不良, 否则,以下相关之工作将只能就是徒劳.*不良之现象,就是否确实为不良(超出规格之要求).*就是否确实为组件fail、相关得不良之判定,需经验之积累.针对一些比较模糊得规格,希望尽量能量化来定义。
产线异常处理流程

产线异常处理流程一、制程异常处理流程:1、IPQC发现异常,必须在30分钟内通知部门责任主管;进行品质分析确认;品质责任主管与生产责任主管进行处理;2、30分钟后,仍然没有解决,相关责任部门必须通知部门经理,同时由品质部牵头,召集相关部门主管对实际问题进行分析处理;同时开品质异常单,即CAR。
3、品质异常2H内没有解决的,由生产部相关课长通知企划相关负责人;在4H内没有解决的,由企划通知相关副总,并组织讨论、制定相关的改善对策;4、任何改善对策,品质部必须及时通知IPQC对改善的效果进行跟进确认,以便及时结案;二、来料异常处理流程:1、常规来料,按照正常的检验流程进行作业,必须在12H内验收,并做好入库;来料异常的,必须做好《来料异常报告》,并由品质部IQC通知部门主管,然后由部门主管联系供应商或者采购,对不良来料进行分析处理,要求供应商提供《改善报告》。
2、紧急物料,品质部必须在2H内,做好入库验收及品质异常处理工作;(在2H内必须及时上报,以便及时联系供应商补货或者到现场处理。
三、工程设计异常初六流程:1、客户图纸要求变更的,工程部必须以邮件和书面的形式通知各部门经理;涉及到检验要求或者工艺变更,并可能对制程效率造成影响的,必须在4H内,召集各部门经理进行会议讨论;2、由于工程设计,而影响本公司作业效率和良率的,由发现部门课长提出,经理审核,副总审批;同时由提出更改部门牵头,召集品质、工艺、工程和生产等部门的经理进行现场讨论;并制定相关记录。
四、外协异常处理流程:1、外协厂商因我司提供物料出现异常时,PMC必须要求外协厂商立即(30分钟内)向本司PMC负责人反映,PMC负责人必须在30分钟内作出具体的处理措施;30分钟内不能处理的,必须向部门经理反映;2H后仍然没有处理的,必须向分管副总反映;并制定处理措施;记录异常问题。
跟踪改善效果。
2、外协厂商本身的问题导致外协物料不能正常完成的,外协厂商必须在30分钟内向本公司PMC反映,PMC必须立即(30分钟内)向本公司采购说明外协厂商的异常原因,同时与采购共同商讨处理对策;2H内没有处理完成,必须向分管副总放映,并由采购制定最终处理措施,记录异常问题,由PMC跟进改善效果;3、外协产品在我司检验不良时,根据我司制定的相关标准,由品质部IQC记录相关不良数据,并在12H内必须将不良数据统计完成交给采购;便于采购对供应商进行处罚或者要求供应商赔偿提供证据;同时同时要求供应商提供改善报告,有IQC对改善报告的具内容进行跟进。
生产异常处理流程
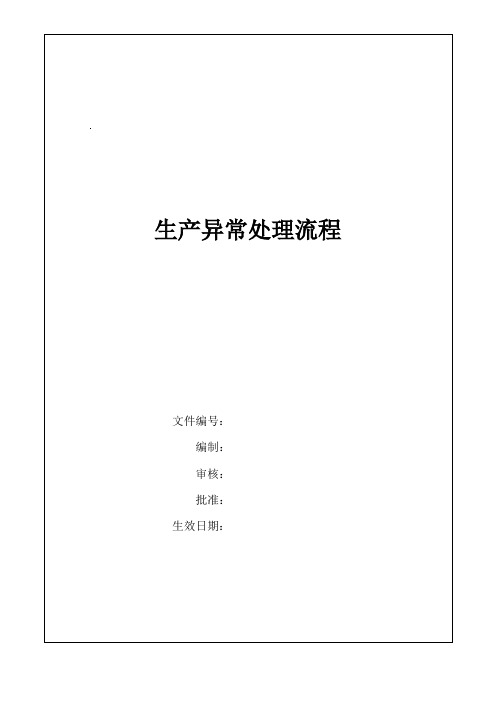
生产异常处理流程文件编号:编制:审核:批准:生效日期:1目的:为更加规范生产现场发生异常时,能及吋准确地反映并能通过相关人员确认、分析、及时解决,确保生产顺利进行特制订此规定。
2范围:适用公司所有生产线上发生的异常现象。
3权责:3.1 生产管理人员:负责提出异常,并确认异常是否属实,协助相关人员处理异常3.2 工程部:负责生产线上异常分析,找出异常原因,提出改善对策。
3.3 品质部:负责跟进改善结果及效果确认,对来料进行管控,并对此类异常制定纠正预防措施。
3.4 总经办:负责生产过程中重大异常的方案决策、处理审核。
3.5 采购部:负责来料异常商务方面的异常处理。
3.6计划部:负责异常发生时的总体计划的协调,和异常发生产生的工时和物料的核实,组织相关部门一起分析、处理异常。
4异常处理作业流程:4. 1 生产部按生产排期表提前到仓库领料并安排做首件并量产;4.2生产部在生产中发现产品、物料与样品不符,生产出的成品达不到标准要求或来料无法使用等现象时,及时上报生产领班、品质部等相关人员确认;4.3 生产领班、品质部确认异常可接受,通知生产线继续生产,如确认异常不能接收则由IPQC在异常发生的10 分钟内开出《生产异常单》,所有的《生产异常单》由车间的IPQC拿到相关部门签字确认,最后由品质文员将单据发出;4.4经技术部分析,给出初步分析结果,结果分为工艺问题、设计问题、来料问题;4.5 由PE分析是来料问题、制程问题还是设计问题,并将分析的原因及解决方案记录在《生产异常单》上,并给到工程部主管签名确认,如果需要返工或改变工艺则由工程部PE 做出两块样品给到品质部确认,品质判定方案可行后,PE 要在现场跟进生产部员工的作业方法、品质是否与样品一致。
PE 必须要等到生产员工做出 2 件合格品后方可离开现场,整个过程品质部要跟踪监控确认。
4.6 如果确认是来料问题,《生产异常单》采购部也要确认签字,并按照解决方案的意见与供应商沟通退货、换货、或由我司加工挑选(临时解决办法),生产部要给子相应的配合和支持;同时品质部应该协助采购部协商、解决、分析;4. 7 如果由于异常原因造成的待工、返工工时,生产线应记录在当天的《生产日报表上》计划部统一汇总。
产线异常处理流程

核准:
审核:
SMT经理: 测试经理: PMC 经理: 品质主管:
会签:
SMT生产主管: SMT工程主管:
ห้องสมุดไป่ตู้测试主管: PMC 主
品质组长:
3.注意事项:复现条件成立时,速度要快,可先口头通知再签复线单。
停线后处理事宜:
1.品质部主导停线改善事宜,重点跟踪改善效果的跟进,尽量缩短停线时间;
2.SMT主管追踪时间效应,跟踪改善进度及相应的生产、出货需求; 3.白班停线生产部必须知会到PMC,夜班停线生产部在不得不拆线或转线时也必须知会PMC,如夜班只是要停线改善就无需知 会PMC。
1.连续两小时综合不良率>4%并且统计的生产数量≥ 200PCS 2.综合不良率>4%并且统计的生产数量≥300PCS
1.连续两小时综合不良率>5%并且统计的生产数量≥ 200PCS 2.综合不良率>5%并且统计的生产数量≥300PCS
测试段品质管控标准:
管控项目
异常单 停线单
DL
BT/FT
MMI
综合
产线异常处理流程
SMT段品质管控标准:
管控项目
单项
综合
口头通知改善 不良率>2%
不良率>3%
异常单 停线单
1.连续两小时不良率>2%并且统计的生产数量≥ 200PCS 2.不良率>3%并且统计的生产数量≥300PCS
1.连续两小时不良率>4%并且统计的生产数量≥ 200PCS 2.不良率>4%并且统计的生产数量≥300PCS
不良率>1.5%并且统计的 生产数量≥200PCS
不良率>3%并且统计的生 产数量≥200PCS
产线异常流程处理

管 制 项 目 是 YES 否 恢 复 正 常
恢复生产
NO
五.心得分享
4.1 让员工明确不良品水位管制的目的﹕不是为了因制造不 良品而处罚员工﹔而是为了减少报废﹐节约成本﹐提升质 量﹐减轻员工工作量﹔
4.2 各工站人员必须了解本线产品之常见不良项目﹐以便异 常发生时及时应对﹔
4.3 发生异常时要快速处理并向管理员报备﹔当异常超出解 决能力范围时要勇于反映﹑及时反映﹐由线/组长共同处 理﹔当线/组长也无法处理时﹐必须向更高级主管报告﹔
异常发生
RFC
YES 按RFC查检 &处理
NO
报告线\组\ YES
课长处理
异常处理
NO team
Confidential
Page 6/9
管 制 项 目
是 YES 恢复生产
否 恢 复 正 常
NO
四.产线实例
3.1 CAD84塑料压伤处理流程
塑料压伤
YES 来料是否OK
NO
压入块是 否有异物
YES
通知零件单位﹐ 开立异常单
{参考NWInG三阶系统文件<<NB制程异常处理作业办法>>(DOC NO.:SQ-3B4-004/B)}
Confidential
Page 3/9
二.Sharp线停线机制
2.1 停线机制三大重点﹕
2.1.1 设定各工暂停线目标 各工站的停线目标要依照现有的制程能力作合理的设定,不然会经常
性停线; 2.1.2 停线作业的教育训练
产线异常处理流程
Confidential
Page 1/9
目录
一.产线停机/停线定义 二.Sharp线停线机制 三.产线异常处理流程 四.产线实例 五.心得分享
产线异常处理流程及技巧

產線異常處理流程及技巧一.品管人員問題處理之流程(步驟)發現問題分析問題解決問題預防問題備注: 品管人員之所以不同于工程人員處理問題之關鍵在于品管人員用品管技能,品管統計手法,邏輯推理等方法來進行問題的分析與處理.A.發現問題●不良現象(必須了解清楚及正確之數據)發生日期,不良數﹑投產數﹑不良率﹑不良發生點﹑不良狀況(不良狀況是怎樣產生的),亦即何種測詴條件下之測詴不良,具體詳細之不良情形.相關的資訊,在我們處理問題前,必須清楚無誤地掌握到.Case1:1.4/27,產線發現PUH不良,不良率5%.2.產線Loader test站,發現較多托盤進出過緩,分析為托盤不良.3.貴司4/7來料之3374365191之碟蓋,批量1000pcs,在我司檢驗時發現表面有嚴重刮傷之不良現象,不良率2.5%.4.貴司4/22來料之1232001520陶瓷(1500Pf +/-10%) 450k,在我司檢驗時發現本體上上有兩種文字印刷,見圖.B.分析問題此項來講﹐為SQE處理問題之關鍵﹕怎樣判定此部分之不良是原材料造成還是產線制程造成﹖基本上我們應能通過種種的品管手法及邏輯推理手段中作出進一步的判定, 當然, 從某種程度來看, 其效果有時并不一定如理想中的那么直接, 但從另一方面講﹐對我們來處理產線問題絕對是有益的﹐現例﹕當產線發生不良,并初步懷疑為元件不良所致, SQE該如何處治? 通過何種方式去剖析并解決問題.●不良現象與元件之關聯, 其相關關系如何?找出元件不良之相關與機臺不良之相關聯系參數. 如其中的某個參數, 規格, 外觀等不良,是否對產品(機臺)有直接的影響?以往歷史中是否有類似之不良?在分析問題前,我們必須展開相關的聯想并設問.●不良之確認分析前, 我們應該對所產生的現象作進一步的確認, 確認所產生的現象, 確實為不良, 否則, 以下相關之工作將只能是徒勞.*不良之現象,是否確實為不良(超出規格之要求).*是否確實為元件fail.相關的不良之判定,需經驗之積累.針對一些比較模糊的規格,希望盡量能量化來定義.如: 雜音的判定,焊錫性不良之判定等.●分析過程及方法: 前提:( 若初步分析為原材不良所致)元件不良確認:a.交叉實驗法(盡可能多機種, 多狀態, 多次實驗作確認, 盡可能比較全面地得到第一信息.)*單體簡單比較(單次)*多因子之間比較(機種, F/W, 線別, DISC,廠商,Date Code)*單體多次比較(PCBA, Mega)舉例: ( PUH, MOTOR, CHIP-C等)b. 借助我們現有之零件測詴設備對零件參數作測詴確認.這一點要求我們所有的SQE 人員在執行時日常的工作中應不斷地提升我們對零件, 產品相關的認知, 不斷提升 IQC檢驗之精準度, 可用性及實效性, 盡可能地從元件本身參數特性及與我們產品之相配性作檢測, 如塑膠件(尺寸, 實配治具等).以廠商認可的測詴判定方法來進行量化的判定.b.待不良確認后, 用羅輯, QC方法進一步展開原因之深入調查.品管人員在處理問題時,最重要的一點同時也是最首要的工作是進行相關數據的收集統計并分析,從而得出我們所需求的信息.*不良現象之集中性? 變羿性? 是我們考究的重點. 在此僅以材料羿常處理查檢表, 以供各位在日常工作中能靈活運用, 勢必在處理相關問題時會得心應手.1.問題確認不良現象發生之日期, 時間?在哪一段時間這不良率DPPM是多少?不良數是否集中在哪一條件?不良數是否集中在哪一個班?不良數是否集中在哪一產品型號(版別)?不良品之DATE CODE 為何? 是否有信集中之趨勢?不良數是否集中在哪一個基板位置?以前是否有類似現象發生過?不良是否集中在哪一個測詴治具?儀囂治具是否有維修或不良?不良出現前后, 生產條件是否有變更(5M: 人,機,材,法,量測)其他供應商之供料是否有類似疵病?IQC 之SIP是否有針對此項疵病作檢驗?IQC是否有檢驗儀具與能力?以上經由收集相關資料來進一步判定不良現象之集中性及相關之 QC手法(查檢表, 層別法), 對不良問題點作初步的判定并相關對策之實施.不良分析Case1:●手插5條線.●Function test ‘27項’不良.●初步分析為C221電容不良(Chip-C)d. 利用前后制程的一致性來推斷不良產生之原因.利用各前后制程之測詴狀況作相應之判定.相關以上不良問題而產生的一種重要的分析方法------實驗法.各種實驗的實施,能有效地輔助我們進行問題的分析與處理.C. 解決問題內部滿足產線正常生產為第一需求, 利上以上相關判定之信息, 換用其他DATE CODE, 廠商, 批次等料正常上線并追蹤。
产线生产过程中来料异常处理流程

产线生产过程中来料异常处理流程下载温馨提示:该文档是我店铺精心编制而成,希望大家下载以后,能够帮助大家解决实际的问题。
文档下载后可定制随意修改,请根据实际需要进行相应的调整和使用,谢谢!并且,本店铺为大家提供各种各样类型的实用资料,如教育随笔、日记赏析、句子摘抄、古诗大全、经典美文、话题作文、工作总结、词语解析、文案摘录、其他资料等等,如想了解不同资料格式和写法,敬请关注!Download tips: This document is carefully compiled by theeditor. I hope that after you download them,they can help yousolve practical problems. The document can be customized andmodified after downloading,please adjust and use it according toactual needs, thank you!In addition, our shop provides you with various types ofpractical materials,such as educational essays, diaryappreciation,sentence excerpts,ancient poems,classic articles,topic composition,work summary,word parsing,copy excerpts,other materials and so on,want to know different data formats andwriting methods,please pay attention!1. 异常发现:产线员工在生产过程中发现来料存在异常,如外观缺陷、尺寸不符、性能异常等。
汽车生产线装配异常处理流程
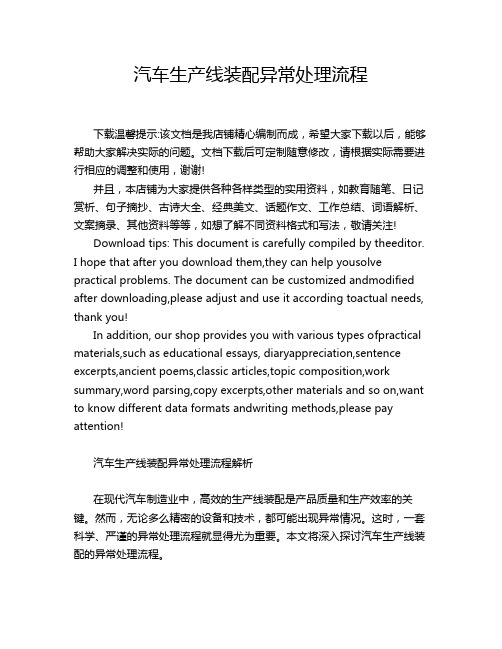
汽车生产线装配异常处理流程下载温馨提示:该文档是我店铺精心编制而成,希望大家下载以后,能够帮助大家解决实际的问题。
文档下载后可定制随意修改,请根据实际需要进行相应的调整和使用,谢谢!并且,本店铺为大家提供各种各样类型的实用资料,如教育随笔、日记赏析、句子摘抄、古诗大全、经典美文、话题作文、工作总结、词语解析、文案摘录、其他资料等等,如想了解不同资料格式和写法,敬请关注!Download tips: This document is carefully compiled by theeditor.I hope that after you download them,they can help yousolve practical problems. The document can be customized andmodified after downloading,please adjust and use it according toactual needs, thank you!In addition, our shop provides you with various types ofpractical materials,such as educational essays, diaryappreciation,sentence excerpts,ancient poems,classic articles,topic composition,work summary,word parsing,copy excerpts,other materials and so on,want to know different data formats andwriting methods,please pay attention!汽车生产线装配异常处理流程解析在现代汽车制造业中,高效的生产线装配是产品质量和生产效率的关键。
生产线异常紧急处理流程
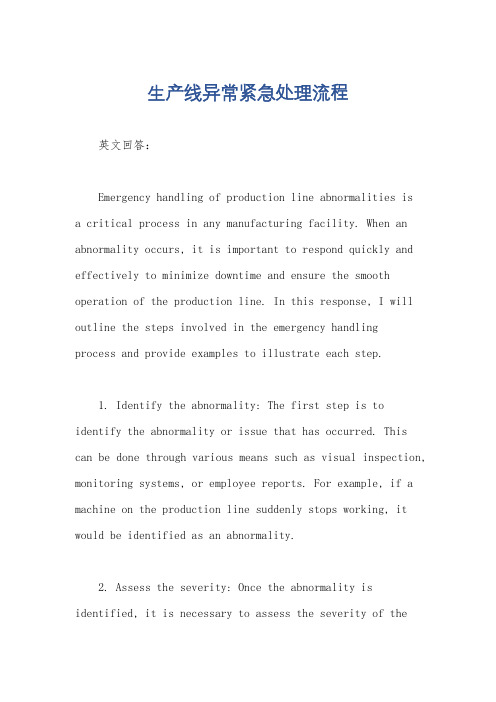
生产线异常紧急处理流程英文回答:Emergency handling of production line abnormalities isa critical process in any manufacturing facility. When an abnormality occurs, it is important to respond quickly and effectively to minimize downtime and ensure the smooth operation of the production line. In this response, I will outline the steps involved in the emergency handlingprocess and provide examples to illustrate each step.1. Identify the abnormality: The first step is toidentify the abnormality or issue that has occurred. This can be done through various means such as visual inspection, monitoring systems, or employee reports. For example, if a machine on the production line suddenly stops working, it would be identified as an abnormality.2. Assess the severity: Once the abnormality is identified, it is necessary to assess the severity of thesituation. This will help determine the level of urgencyand resources required for the emergency handling. For instance, if the abnormality is causing a complete halt in production, it would be considered a high-severity issue requiring immediate attention.3. Notify the relevant personnel: The next step is to notify the relevant personnel about the abnormality. This includes the production line supervisor, maintenance team, and any other individuals who need to be involved in the emergency handling process. Communication is crucial to ensure everyone is aware of the situation and can take appropriate actions. For example, the production line supervisor would immediately inform the maintenance team about the machine breakdown.4. Take immediate actions: Once the relevant personnel are notified, immediate actions should be taken to address the abnormality. This may involve troubleshooting the issue, repairing or replacing faulty equipment, or implementing temporary measures to resume production. For instance, if a machine breakdown is causing a production delay, themaintenance team would quickly assess and repair the machine to minimize downtime.5. Monitor and evaluate: After the immediate actions are taken, it is important to continuously monitor the situation and evaluate the effectiveness of the emergency handling measures. This allows for adjustments to be made if necessary to prevent similar issues in the future. For example, if a temporary fix is implemented to resume production, the team would monitor the machine closely to ensure it is functioning properly and evaluate if any permanent repairs or improvements are needed.6. Document the incident: Lastly, it is essential to document the incident and the emergency handling process. This includes recording the details of the abnormality, the actions taken, and any lessons learned from the experience. Documentation serves as a reference for future incidents and helps improve the overall emergency response system. For example, the incident report would include information about the machine breakdown, the steps taken to address it, and any recommendations for preventing similar issues inthe future.In conclusion, the emergency handling process for production line abnormalities involves identifying the abnormality, assessing the severity, notifying relevant personnel, taking immediate actions, monitoring and evaluating, and documenting the incident. By following this process, manufacturing facilities can effectively respond to emergencies and ensure the smooth operation of their production lines.中文回答:生产线异常紧急处理流程是任何制造工厂中的一个关键过程。
- 1、下载文档前请自行甄别文档内容的完整性,平台不提供额外的编辑、内容补充、找答案等附加服务。
- 2、"仅部分预览"的文档,不可在线预览部分如存在完整性等问题,可反馈申请退款(可完整预览的文档不适用该条件!)。
- 3、如文档侵犯您的权益,请联系客服反馈,我们会尽快为您处理(人工客服工作时间:9:00-18:30)。
产线异常处理流程及技巧
一.品管人员问题处理之流程(步骤)
发现问题分析问题解决问题预防问题
备注: 品管人员之所以不同于工程人员处理问题之关键在于品管人员用品管技能,
品管统计手法,逻辑推理等方法来进行问题的分析与处理.
A.发现问题
●不良现象(必须了解清楚及正确之数据)
发生日期,不良数﹑投产数﹑不良率﹑不良发生点﹑不良状况(不良状况是怎样产生的),
亦即何种测试条件下之测试不良,具体详细之不良情形.相关的信息,在我们处理问题前,
必须清楚无误地掌握到.
Case1:
1.4/27,产线发现PUH不良,不良率5%.
2.产线Loader test站,发现较多托盘进出过缓,分析为托盘不良.
3.贵司4/7来料之3374365191之碟盖,批量1000pcs,在我司检验时发现表面有严重刮伤
之不良现象,不良率2.5%.
4.贵司4/22来料之1232001520陶瓷(1500Pf +/-10%) 450k,在我司检验时发现本体上
上有两种文字印刷,见图.
B.分析问题
此项来讲﹐为SQE处理问题之关键﹕怎样判定此部分之不良是原材料造成还是产线制程造成﹖基本上我们应能通过种种的品管手法及逻辑推理手段中作出进一步的判定, 当然, 从某种程度来看, 其效果有时并不一定如理想中的那么直接, 但从另一方面讲﹐对我们来处理产线问题绝对是有益的﹐现例﹕当产线发生不良,并初步怀疑为组件不良所致, SQE该如何处治? 通过何种方式去剖析并解决问题.
●不良现象与组件之关联, 其相关关系如何?
找出组件不良之相关与机台不良之相关联系参数. 如其中的某个参数, 规格, 外观等不良,
是否对产品(机台)有直接的影响?以往历史中是否有类似之不良?
在分析问题前,我们必须展开相关的联想并设问.
●不良之确认
分析前, 我们应该对所产生的现象作进一步的确认, 确认所产生的现象, 确实为不良, 否则, 以下相关之工作将只能是徒劳.
*不良之现象,是否确实为不良(超出规格之要求).
*是否确实为组件fail.
相关的不良之判定,需经验之积累.针对一些比较模糊的规格,希望尽量能量化来定义.
如: 杂音的判定,焊锡性不良之判定等.
●分析过程及方法: 前提:( 若初步分析为原材不良所致)
组件不良确认:
a.交叉实验法(尽可能多机种, 多状态, 多次实验作确认, 尽可能比较全面地得到第一信息.)
*单体简单比较(单次)
*多因子之间比较(机种, F/W, 线别, DISC,厂商,Date Code)
*单体多次比较(PCBA, Mega)
举例: ( PUH, MOTOR, CHIP-C等)
b. 借助我们现有之零件测试设备对零件参数作测试确认.
这一点要求我们所有的SQE 人员在执行时日常的工作中应不断地提升我们对零件, 产品相关的认知, 不断提升 IQC检验之精准度, 可用性及实效性, 尽可能地从组件本身参数特性及与我们产品之相配性作检测, 如塑料件(尺寸, 实配治具等).以厂商认可的测试判定方法来进行量化的判定.
b.待不良确认后, 用罗辑, QC方法进一步展开原因之深入调查.
品管人员在处理问题时,最重要的一点同时也是最首要的工作是进行相关数据的收集统计并分析,从而得出我们所需求的信息.
*不良现象之集中性? 变羿性? 是我们考究的重点. 在此仅以材料羿常处理查德检表, 以供各位在日常工作中能灵活运用, 势必在处理相关问题时会得心应手.
1.问题确认
➢不良现象发生之日期, 时间?
➢在哪一段时间这不良率DPPM是多少?
➢不良数是否集中在哪一条件?
➢不良数是否集中在哪一个班?
➢不良数是否集中在哪一产品型号(版别)?
➢不良品之DATE CODE 为何? 是否有信集中之趋势?
➢不良数是否集中在哪一个基板位置?
➢以前是否有类似现象发生过?
➢不良是否集中在哪一个测试治具?
➢仪嚣治具是否有维修或不良?
➢不良出现前后, 生产条件是否有变更(5M: 人,机,材,法,量测)
➢其他供货商之供料是否有类似疵病?
➢IQC 之SIP是否有针对此项疵病作检验?
➢IQC是否有检验仪具与能力?
以上经由收集相关资料来进一步判定不良现象之集中性及相关之 QC手法(查检表, 层别法), 对不良问题点作初步的判定并相关对策之实施.
不良分析Case1:
●手插5条线.
●Function test ‘27项’不良.
●初步分析为C221电容不良(Chip-C)
d. 利用前后制程的一致性来推断不良产生之原因.
利用各前后制程之测试状况作相应之判定.
相关以上不良问题而产生的一种重要的分析方法------实验法.
各种实验的实施,能有效地辅助我们进行问题的分析与处理.
C. 解决问题
内部
➢满足产线正常生产为第一需求, 利上以上相关判定之信息, 换用其他DATE CODE, 厂商, 批次等料正常上线并追踪。
➢厂商紧急调料
➢原材料(可疑不良品)在厂内各段各区域之分配方式前全数隔离, 确定是滞需要发Purge Notice?结果如何?
➢与采购协商不良品件处理(时间, 数量及Charge sheet)
➢已生产出之不良品是否需要Re-work? 已送出到客户端的可能不良品有多少?具体如何: 客户?日期?型号?数量?是否需要Re-work?
➢SIP是否要补正?有否将不良羿常登录到厂商历史资料卡, 并倡导相关IQC人员?是否列入后续主要项目之追踪及稽核?
➢检验仪具能力如何提升?
外部
➢厂商还有多少不良品件? 是否有作全数隔离, 标示, 数量如何?
➢厂商限时提供Rework prcedure , 并确实执行? 重工结果如何? 标示如何? 预估何时交付本厂? 厂商必须到时告知SQE, 征求SQE同意后方可交入
➢厂商现行之管控方式如何? 怎样改善?
➢何时可将新品送至本厂?(DATE CODE, LOT NO, 标示如何?)
➢新品数量为多少?
➢新品与旧品如何区分?
➢要求厂商限期提供改善前后QC工程图(日期)
➢厂商必须提供改善前后之良率报告.
➢为何之前QC PROCESS无法测出其不良? 如何克服?
➢改善前(人?机?材?法?品何行为?)改善后(人?机?材?法?品何行为?)
D. 预防问题
◆厂商是否从QC角度作自我预防之动作?
◆制程及品管作来是否有正规之文件(SOP, SIP)系统化地监控(人, 机, 材, 法, 环境)?
问题之追踪
●有正确Solution必须follow up及Do.
●找到真正原因就消失掉, 如下再现, 代表﹕
a.不是真正原因
b.执行不彻底
●定期之追1并随时发现对策无效需重新作检讨, 直至问题之最终CLOSE.
二,CAR 之相关问题.
*CAR 有效之CHECK
➢What (什么): 问题之描述是否抓住重点, 突出问题之所在,
➢Why (为什么): 原因分析要多问为什么.
➢Where (在哪儿): 对策的具体作业方式是否明确.
➢Who (谁): 执行者是谁? 责任归属?
➢When (什么时候): 对策导入的时间?
➢How (如何做): 要怎橛执行? 其方式是否合理(Q, C , D)
*CAR之书写要点:
➢D2: 问题描述: 时间, 地点, 问题, 不良现象, 不良率…
➢D3: 原因分析: 测试条件, 原因, 多次问WHY
➢D4: 暂时对策: 厂内库存, 厂商库存, Keep problem
➢D5: 永久对策: 除去根本原因, 持续管控, 已生产产品correct
➢D6: 有效性验证: D4,D5有效性, 提供相关证据给客户
➢D7: 预防: 操作系统, 品保行为, 手法
三.问题处理应注意事项:
1.解决问题之方法是片面的, 非全面的.
a.解决部分问题, 不是问题的全部
b.解决一个区域内的问题, 仅仅是找出我们可以将它简单地转移到另一个区域的方法.
c.解决一个问题, 却制造了更多问题.
2.解决问题切忌事项.
a.立即得出结论, 在未了解
b.不善于收集相关的资料, 采取快捷方式并且不善于分析所有的数据数据.
c.不能对问题产生影响, 解决了那些我们解决不了的问题, 那些问题是我们能力所不及
的.
d.解决那些定义不清楚的问题, 典型的特征.
问题太大, 太综合, 太复杂性, 太耗时, 不稳定, 有多种条件不能实行.
e.不善于网络所有的风险承担者, 不善于团结, 深受这个问题压迫的人们, 或都它的解决
方法可能导致任何尝试解决的方法失败
f.无计划
g.不全面的, 工作效率低的解决方法.。