实验的硅热氧化实用的工艺
(4)热氧化

x j xSiO2
掩蔽条件: DSi>>DSiO2
杂质的 DSi T 关系曲线
DSiO2
22
SiO2掩蔽层厚度的确定
硅衬底上的SiO2要能够单做掩膜来实现定域扩散, 需要SiO2满足:
1、 SiO2有一定的厚度;2、 DSi>>DSiO2; 3、且SiO2表面杂质浓度(CS)与Si/SiO界面杂质
二氧化硅膜用途
作为掩蔽膜
离子注入掩蔽 11
二氧化硅膜用途
互连 层间 绝缘 介质
12
二氧化硅膜用途
作为电隔离膜
隔离工艺
13
14
二氧化硅膜用途
作为掩膜; 作为芯片的钝化和保护膜; 作为电隔离膜; 作为元器件的组成部分。
15
SiO2与Si之间完美的界面特性是成就硅 时代的主要原因
TEM照片——单晶硅表面热氧化所得非晶二氧化硅薄膜
生长速率常数 (m2/min)
1.48×10-4
6.2×10-4
38.5×10-4 117.5×10-4 43.5×10-4
133×10-4
生长0.5 微米SiO2 所需时间 (min)
1800
360
63 22 58 18
SiO2的密度 (g/mm)
备注
2.27
2.15
2.21 2.12 2.08 2.05
SiO2 形成
氧化剂流动方向 (如 O2或 H2O)
气流滞流层
SiO2 Si衬底
39
40
热氧化动力学(迪尔-格罗夫模型)
氧化剂输运---气体输运流密度用F1表 主流 粘滞层
Ga; 3. Au在SiO2中扩散系数很小,但由于
氧化实验
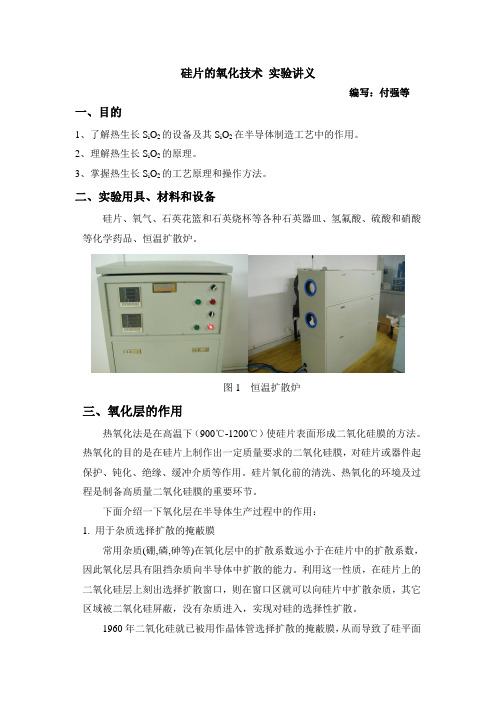
硅片的氧化技术实验讲义编写:付强等一、目的1、了解热生长S i O2的设备及其S i O2在半导体制造工艺中的作用。
2、理解热生长S i O2的原理。
3、掌握热生长S i O2的工艺原理和操作方法。
二、实验用具、材料和设备硅片、氧气、石英花篮和石英烧杯等各种石英器皿、氢氟酸、硫酸和硝酸等化学药品、恒温扩散炉。
图1 恒温扩散炉三、氧化层的作用热氧化法是在高温下(900℃-1200℃)使硅片表面形成二氧化硅膜的方法。
热氧化的目的是在硅片上制作出一定质量要求的二氧化硅膜,对硅片或器件起保护、钝化、绝缘、缓冲介质等作用。
硅片氧化前的清洗、热氧化的环境及过程是制备高质量二氧化硅膜的重要环节。
下面介绍一下氧化层在半导体生产过程中的作用:1. 用于杂质选择扩散的掩蔽膜常用杂质(硼,磷,砷等)在氧化层中的扩散系数远小于在硅片中的扩散系数,因此氧化层具有阻挡杂质向半导体中扩散的能力。
利用这一性质,在硅片上的二氧化硅层上刻出选择扩散窗口,则在窗口区就可以向硅片中扩散杂质,其它区域被二氧化硅屏蔽,没有杂质进入,实现对硅的选择性扩散。
1960年二氧化硅就已被用作晶体管选择扩散的掩蔽膜,从而导致了硅平面工艺的诞生,开创了半导体制造技术的新阶段。
同时二氧化硅也可在注入工艺中,作为选择注入的掩蔽膜。
作为掩蔽膜时,一定要保证足够厚的厚度,杂质在二氧化硅中的扩散或穿透深度必须要小于二氧化硅的厚度,并有一定的余量,以防止可能出现的工艺波动影响掩蔽效果。
2. 缓冲介质层其一:硅与氮化硅的应力较大,因此在两层之间生长一层氧化层,以缓冲两者之间的应力,如二次氧化;其二:也可作为注入缓冲介质,以减少注入对器件表面的损伤。
3. 电容的介质材料电容的计算公式:C=ε0*εr *S/dε0:真空介质常数 εr :相对介电常数S :电容区面积 D :介质层厚度二氧化硅的相对介电常数为3-4。
二氧化硅的耐击穿能力强,温度系数小,是制作电容介质的常用材料。
硅热还原法
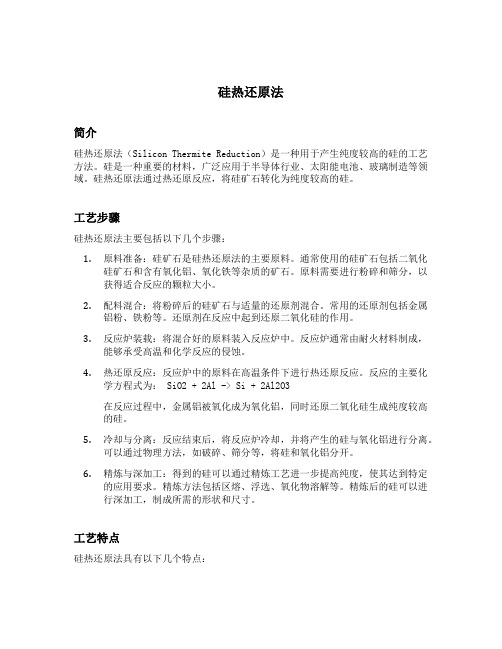
硅热还原法简介硅热还原法(Silicon Thermite Reduction)是一种用于产生纯度较高的硅的工艺方法。
硅是一种重要的材料,广泛应用于半导体行业、太阳能电池、玻璃制造等领域。
硅热还原法通过热还原反应,将硅矿石转化为纯度较高的硅。
工艺步骤硅热还原法主要包括以下几个步骤:1.原料准备:硅矿石是硅热还原法的主要原料。
通常使用的硅矿石包括二氧化硅矿石和含有氧化铝、氧化铁等杂质的矿石。
原料需要进行粉碎和筛分,以获得适合反应的颗粒大小。
2.配料混合:将粉碎后的硅矿石与适量的还原剂混合。
常用的还原剂包括金属铝粉、铁粉等。
还原剂在反应中起到还原二氧化硅的作用。
3.反应炉装载:将混合好的原料装入反应炉中。
反应炉通常由耐火材料制成,能够承受高温和化学反应的侵蚀。
4.热还原反应:反应炉中的原料在高温条件下进行热还原反应。
反应的主要化学方程式为: SiO2 + 2Al -> Si + 2Al2O3在反应过程中,金属铝被氧化成为氧化铝,同时还原二氧化硅生成纯度较高的硅。
5.冷却与分离:反应结束后,将反应炉冷却,并将产生的硅与氧化铝进行分离。
可以通过物理方法,如破碎、筛分等,将硅和氧化铝分开。
6.精炼与深加工:得到的硅可以通过精炼工艺进一步提高纯度,使其达到特定的应用要求。
精炼方法包括区熔、浮选、氧化物溶解等。
精炼后的硅可以进行深加工,制成所需的形状和尺寸。
工艺特点硅热还原法具有以下几个特点:1.高纯度:硅热还原法能够生产高纯度的硅。
在热还原反应中,金属铝能够更好地与氧化硅反应,减少杂质的存在。
通过精炼工艺,还可以进一步提高硅的纯度。
2.制备成本低:硅热还原法的原料成本相对较低。
硅矿石广泛存在于自然界中,是一种取之不尽的资源。
还原剂如金属铝也具有较低的成本,并且可循环利用。
3.工艺简单:硅热还原法的工艺相对简单,不需要复杂的装置和高能耗。
原料的准备和反应炉的装载都比较简便。
同时,反应过程中无需添加其他化学试剂,降低了工艺的复杂性。
实验二十二、硅片氧化工艺实验

实验二十二、硅片氧化工艺实验一.实验目的1.熟悉半导体工艺的一般步骤2.掌握硅片氧化的基本方法和原理,能够熟练使用管式电炉二.实验原理(一)高温氧化及厚度测量氧化是在硅片表面生长一层二氧化硅(SiO₂)膜的过程。
这层膜的作用是:保护和钝化半导体表面:作为杂质选择扩散的掩蔽层;用于电极引线和其下面硅器件之间的绝缘;用作MOS电容和MOS器件栅极的介电层等等。
其实现的方法有:高温氧化(热氧化)、化学气相淀积(CVT)、阳极氧化、溅射等。
氧化即生长在硅片表面上,也向硅片里面延伸,如图1所示。
一般氧化层的45%的厚度是在初始表面上形成,46%是在初始表面以下生成。
通常氧化层的厚度,薄的可以小于500A(栅氧化层),厚的可以大于1000Å(场氧化层)。
氧化的范围为700-1100℃,氧化层的厚度和它的生长进间成比例。
常用的氧化方法是高温氧化。
所以这里,我们着重强调一下高温氧化。
高温氧化就是把硅衬底片置于1000℃以上的高温下,并通入氧化性气体(如氧气、水汽),使衬底本身表面的一层硅氧化成SiO₂。
高温氧化又分为:干氧氧化、湿氧氧化和水汽氧化三种。
实践表明,干氧氧化速率慢,但所得到的二氧化硅层质量较好,且和光刻胶有良好的粘附性(不易“浮胶”),而水汽氧化恰恰相反,氧化速度快,使所得二氧化硅层质量较差,而且过量的水还有腐蚀Si的作用,所以很少单独采用水汽氧化。
但如果在氧中掺入一定量的水汽(就是所谓的湿氧氧化的方法),就在一定程度上解决了氧化速度和氧气质量之间的矛盾,因此不宜于在生长较厚的氧化层时使用。
但终究湿氧氧化生成的二氧化硅层的质量不如干氧氧化的好,且易引起Si表面内杂质再分布。
所以,在生长较厚的氧化层时,往往采用干氧-湿氧-干氧的工艺步骤,这既可以使氧化时间不致过长而能保证工艺对氧化层质量的要求。
(二)高温氧化机理1. 干氧氧化在高温下,氧气与硅接触时是通过以下化学反应在硅表面形成二氧化硅的可见一个氧分子就可以生成一个二氧化硅分子。
半导体制造工艺之硅的氧化概述
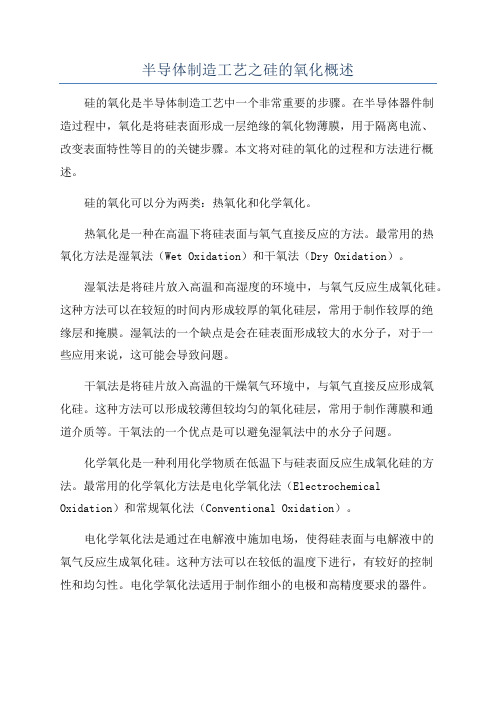
半导体制造工艺之硅的氧化概述硅的氧化是半导体制造工艺中一个非常重要的步骤。
在半导体器件制造过程中,氧化是将硅表面形成一层绝缘的氧化物薄膜,用于隔离电流、改变表面特性等目的的关键步骤。
本文将对硅的氧化的过程和方法进行概述。
硅的氧化可以分为两类:热氧化和化学氧化。
热氧化是一种在高温下将硅表面与氧气直接反应的方法。
最常用的热氧化方法是湿氧法(Wet Oxidation)和干氧法(Dry Oxidation)。
湿氧法是将硅片放入高温和高湿度的环境中,与氧气反应生成氧化硅。
这种方法可以在较短的时间内形成较厚的氧化硅层,常用于制作较厚的绝缘层和掩膜。
湿氧法的一个缺点是会在硅表面形成较大的水分子,对于一些应用来说,这可能会导致问题。
干氧法是将硅片放入高温的干燥氧气环境中,与氧气直接反应形成氧化硅。
这种方法可以形成较薄但较均匀的氧化硅层,常用于制作薄膜和通道介质等。
干氧法的一个优点是可以避免湿氧法中的水分子问题。
化学氧化是一种利用化学物质在低温下与硅表面反应生成氧化硅的方法。
最常用的化学氧化方法是电化学氧化法(Electrochemical Oxidation)和常规氧化法(Conventional Oxidation)。
电化学氧化法是通过在电解液中施加电场,使得硅表面与电解液中的氧气反应生成氧化硅。
这种方法可以在较低的温度下进行,有较好的控制性和均匀性。
电化学氧化法适用于制作细小的电极和高精度要求的器件。
常规氧化法是在含有氧分子的环境中将硅片加热,使得硅表面与氧气反应生成氧化硅。
这种方法适用于制作一般要求的绝缘层和介质。
除了上述的热氧化和化学氧化方法外,还有其他一些特殊的氧化方法,如低温氧化、扩散氧化、快速热氧化等。
这些特殊的氧化方法适用于特定的应用和器件要求。
总结起来,硅的氧化是半导体制造工艺中一个非常重要的步骤。
通过热氧化和化学氧化等方法,可以在硅表面形成不同厚度的氧化硅层,用于隔离电流、改变表面特性等目的。
半导体制造工艺之硅的氧化概述

半导体制造工艺之硅的氧化概述硅是半导体材料中最重要的成分之一,广泛应用于半导体器件的制造中。
在半导体制造工艺中,硅的氧化是一个关键步骤,该过程将硅材料与氧气反应,形成一层氧化硅薄膜。
这一步骤对于半导体器件的性能和可靠性起着至关重要的作用。
硅的氧化过程通常通过热氧化或化学气相沉积(CVD)两种方法实现。
热氧化是最常用的氧化方法之一,它是在高温环境下将硅材料暴露在氧气中进行反应。
反应时,氧气分子会与硅材料的表面发生化学反应,形成一层均匀、紧密的氧化硅薄膜。
这种氧化过程通常在高温(约900-1200摄氏度)下进行,需要较长的时间(几十分钟到几个小时)。
化学气相沉积是另一种常用的氧化方法,它使用气相前体将氧化物沉积在硅表面上。
在这个过程中,硅衬底被放置在一个高温反应室中,气相前体物质被输送到反应室中,并在硅表面上沉积。
一个常用的气相前体是二甲基二氧化硅(DMDSO),它在高温环境下分解成二氧化硅并沉积在硅表面上。
与热氧化相比,化学气相沉积可以在较低的温度和较短的时间内实现氧化过程。
无论是热氧化还是化学气相沉积,氧化过程都可以通过控制氧化温度、氧化时间和氧化气体浓度来调节氧化硅薄膜的厚度。
薄膜的厚度通常在几纳米到几百纳米之间,根据不同的应用需求进行选择。
氧化硅薄膜在半导体制造中具有多种重要功能。
首先,它可以作为保护层,防止杂质和水分进入硅材料,从而提高器件的稳定性和可靠性。
其次,氧化硅还可以作为电路的绝缘层,防止电流泄露和干扰。
此外,氧化硅还可以用作电容层、栅介质层等特定应用。
总之,硅的氧化是半导体制造工艺中一个非常重要的步骤。
通过热氧化或化学气相沉积方法,可以形成一层均匀、紧密的氧化硅薄膜,为半导体器件的性能和可靠性提供良好的基础。
硅的氧化在半导体制造中扮演着关键的角色,它不仅可以形成绝缘层,还可以作为介电材料、隔离层和衬底。
在现代集成电路的制造中,氧化硅通常是制造晶体管的基本材料之一。
硅的氧化过程一般分为两个主要阶段:表面清洗和氧气反应。
半导体制造工艺硅的氧化

半导体制造工艺:硅的氧化在半导体制造工艺中,硅的氧化是一项核心工序,也是制造MOS场效应管和集成电路器件不可缺少的步骤。
硅的氧化可以通过热氧化和化学气相氧化两种方式进行。
本文将对这两种硅的氧化方式进行介绍和探讨。
热氧化热氧化是通过在高温下将硅官能团氧化为SiO2,制造氧化层的一种方法。
在热氧化过程中,硅表面的氧化层与硅相结合,因此氧化层与硅之间没有明显的界面。
这种方法能够在硅表面获得高质量、均匀、致密的氧化层,在制造MOS场效应管和集成电路器件方面得到广泛应用。
热氧化需要将硅样品放置在加热炉中,然后冲入高纯度氧气或氧气混合其他气体,硅样品表面的氧就会与硅互相结合,形成氧化物层。
在这个过程中,温度、氧气流量和时间都是影响氧化层性质的关键参数,它们需要根据所需的氧化层厚度和质量进行优化。
化学气相氧化化学气相氧化又被称为“湿氧化”,是在高温和高湿环境下进行的氧化过程。
在湿氧化过程中,硅表面的Si-H键会和水蒸气反应生成Si-OH基团,然后Si-OH基团再和水蒸气反应生成Si-O-Si键结构,形成氧化层。
相对于热氧化,化学气相氧化加工的硅样品表面质量更好、更稳定、更精确。
在化学气相氧化过程中,氧化层的厚度和质量根据温度、气流等参数进行控制。
化学气相氧化通常使用二氧化硅(SiO2)作为氧化物的源,同时使用水蒸气或其他合适的气体作为基础气体。
对于MOS场效应管和集成电路器件生产来说,硅的氧化是制造过程中重要步骤之一。
热氧化和化学气相氧化是目前最常用的两种硅的氧化方式。
热氧化能够制造出高质量、均匀、致密的氧化层,而湿氧化能够加工出表面质量更好、更稳定、更精确的硅样品。
控制温度、气流和湿度等参数,是实现两种氧化方式精确控制氧化层厚度和质量的关键。
常见的热氧化工艺

二.常见的各种氧化工艺1.热氧化工艺热生长氧化法-将硅片置于高温下,通以氧化的气氛,使硅表面一薄层的硅转变为二氧化硅的方法。
①常见的热氧化工艺类别及特点:a 干氧氧化:干氧氧化法-氧化气氛为干燥、纯净的氧气。
氧化膜质量最好,但氧化速度最慢。
b水汽氧化:水汽氧化法-氧化气氛为纯净的水汽。
氧化速度最快,但氧化膜质量最差。
c湿氧氧化:湿氧氧化法-氧化气氛为纯净的氧气+纯净的水汽。
氧化膜质量和氧化速度均介于干氧氧化和水汽氧化之间。
②常见的热氧化工艺:a方法:常采用干氧-湿氧-干氧交替氧化法。
b工艺条件:温度:高温(常见的为1000℃-1200℃)。
时间:一般总氧化时间超过30分钟。
②氧化生长规律:一般热氧化生长的二氧化硅层厚度与氧化时间符合抛物线规律。
原因是:在氧化时存在氧化剂穿透衬底表面已生成的二氧化硅层的事实。
2.热分解淀积法:(工艺中也常称为低温淀积法或低温氧化法)热分解淀积法-在分解温度下,利用化合物的分解和重新组合生成二氧化硅,然后将生成的二氧化硅淀积在衬底(可为任何衬底)表面上,形成二氧化硅层的方法。
①可见的低温氧化工艺类别及特点:a.含氧硅化物热分解淀积法:多采用烷氧基硅烷进行热分解,分解物中有二氧化硅,在衬底上淀积形成二氧化硅层。
b.硅烷(不含氧硅化物)热分解氧化淀积法:硅烷热分解析出硅原子,与氧化剂(氧气)作用生成二氧化硅,在衬底上淀积形成二氧化硅层。
②常见的低温氧化工艺:a.设备:采用低真空氧化淀积炉。
b.条件:Ⅰ含氧硅化物热分解淀积法:对常用的正硅酸乙酯:T=750℃;真空度为托。
Ⅱ硅烷热分解氧化淀积法:T>300 ℃(实际采用420 ℃),淀积时系统中通入氧气,真空度同上。
③低温氧化生长规律:低温氧化(热分解淀积)生长的二氧化硅层厚度与氧化时间符合线性规律。
原因是:在氧化时是在衬底表面上淀积二氧化硅,不存在氧化剂穿透衬底表面已生成的二氧化硅层的问题。
SiO2的制备方法:热氧化法干氧氧化水蒸汽氧化湿氧氧化干氧-湿氧-干氧(简称干湿干)氧化法氢氧合成氧化化学气相淀积法热分解淀积法溅射法化学汽相淀积(CVD)化学汽相淀积(Chemical Vapor Deposition):通过气态物质的化学反应在衬底上淀积一层薄膜材料的过程CVD技术特点:具有淀积温度低、薄膜成分和厚度易于控制、均匀性和重复性好、台阶覆盖优良、适用范围广、设备简单等一系列优点CVD方法几乎可以淀积集成电路工艺中所需要的各种薄膜,例如掺杂或不掺杂的SiO2、多晶硅、非晶硅、氮化硅、金属(钨、钼)等常压化学汽相淀积(APCVD)低压化学汽相淀积(LPCVD)等离子增强化学汽相淀积(PECVD)化学汽相淀积(CVD)单晶硅的化学汽相淀积(外延):一般地,将在单晶衬底上生长单晶材料的工艺叫做外延,生长有外延层的晶体片叫做外延片二氧化硅的化学汽相淀积:可以作为金属化时的介质层,而且还可以作为离子注入或扩散的掩蔽膜,甚至还可以将掺磷、硼或砷的氧化物用作扩散源低温CVD氧化层:低于500℃中等温度淀积:500~800℃高温淀积:900℃左右多晶硅的化学汽相淀积:利用多晶硅替代金属铝作为MOS器件的栅极是MOS集成电路技术的重大突破之一,它比利用金属铝作为栅极的MOS器件性能得到很大提高,而且采用多晶硅栅技术可以实现源漏区自对准离子注入,使MOS集成电路的集成度得到很大提高。
硅热氧化工艺
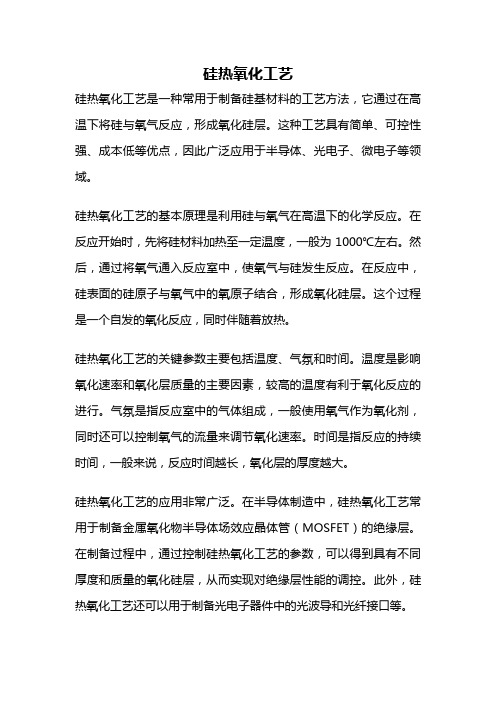
硅热氧化工艺硅热氧化工艺是一种常用于制备硅基材料的工艺方法,它通过在高温下将硅与氧气反应,形成氧化硅层。
这种工艺具有简单、可控性强、成本低等优点,因此广泛应用于半导体、光电子、微电子等领域。
硅热氧化工艺的基本原理是利用硅与氧气在高温下的化学反应。
在反应开始时,先将硅材料加热至一定温度,一般为1000℃左右。
然后,通过将氧气通入反应室中,使氧气与硅发生反应。
在反应中,硅表面的硅原子与氧气中的氧原子结合,形成氧化硅层。
这个过程是一个自发的氧化反应,同时伴随着放热。
硅热氧化工艺的关键参数主要包括温度、气氛和时间。
温度是影响氧化速率和氧化层质量的主要因素,较高的温度有利于氧化反应的进行。
气氛是指反应室中的气体组成,一般使用氧气作为氧化剂,同时还可以控制氧气的流量来调节氧化速率。
时间是指反应的持续时间,一般来说,反应时间越长,氧化层的厚度越大。
硅热氧化工艺的应用非常广泛。
在半导体制造中,硅热氧化工艺常用于制备金属氧化物半导体场效应晶体管(MOSFET)的绝缘层。
在制备过程中,通过控制硅热氧化工艺的参数,可以得到具有不同厚度和质量的氧化硅层,从而实现对绝缘层性能的调控。
此外,硅热氧化工艺还可以用于制备光电子器件中的光波导和光纤接口等。
除了半导体领域,硅热氧化工艺还在微电子、传感器、太阳能电池等领域有着广泛的应用。
在微电子领域,硅热氧化工艺可以制备微电子器件中的绝缘层和电容层。
在传感器领域,硅热氧化工艺可以制备氧化硅薄膜,用于制备压力传感器、湿度传感器等。
在太阳能电池领域,硅热氧化工艺可以制备太阳能电池的表面反射镀层,提高太阳能电池的光吸收效率。
尽管硅热氧化工艺具有诸多优点和应用前景,但也存在一些问题。
首先,硅热氧化工艺需要较高的温度,这对设备和工艺的稳定性提出了要求。
其次,硅热氧化工艺的氧化速率较慢,需要较长的时间来制备较厚的氧化硅层。
此外,在工艺过程中,还需要对温度、气氛等参数进行严格控制,以保证氧化层的质量和性能。
硅的氧化

姓名:孙铭斌班级:JS1245 学号:201231907011专业:集成电路工程时间:2013年5月19日硅的氧化及二氧化硅硅放在空气中会氧化,在其表面生成SiO₂膜,这种膜厚度一般是30~50nm,是空气中氧和硅进行反应的结果。
进行高温加热时可以得到更厚的SiO₂膜,这种硅氧化膜与水晶或石英相同。
它作为电绝缘材料具有最高的电阻率(~1018Ωcm),而热膨胀系数又小到5~7×10-7了,以及可利用压电效应作稳定的振荡子等,因而一般说来其应用范围是广泛的。
1二氧化硅薄膜的应用SiO₂薄膜在诸多领域得到了很好的应用,如用于电子器件和集成器件、光学薄膜器件、传感器等相关器件中。
利用纳米二氧化硅的多孔性质可应用于过滤薄膜、薄膜反应和相关的吸收剂以及分离技术、分子工程和生物工程等,从而在光催化、微电子和透明绝热等领域具有很好的发展前景。
均匀多孔,孔径分布介于5~50 nm的二氧化硅薄膜的制备及性能表征已成为材料界研究的热点之一。
1.1 微电子领域在微电子工艺中,SiO₂薄膜因其优越的电绝缘性和工艺的可行性而被广泛采用。
在半导体器件中,利用SiO₂禁带宽度可变的特性,可作为非晶硅太阳电池的薄膜光吸收层,以提高光吸收效率;还可作为金属-氮化物-氧化物-半导体(MNSO)存储器件中的电荷存储层,集成电路中CMOS器件和SiGe MOS器件以及薄膜晶体管(TFT)中的栅介质层等。
SiO₂对杂质的扩散起到掩蔽作用。
在集成电路制造中,几种常见的杂质如硼、磷、砷等在SiO₂膜中的扩散要比它们在硅中的扩散慢很多。
因此,在制作半导体器件的各个区时,最常用的方法是首先在硅圆片表面生长一层SiO₂膜,经过光刻、显影后,再刻蚀掉需掺杂区域表面的氧化膜,从而形成掺杂窗口,最终通过窗口选择性地将杂质注入相应的区域中。
随着大规模集成电路器件集成度的提高,多层布线技术变得愈加重要,如逻辑器件的中间介质层将增加到4~5层,这就要求减小介质层带来的寄生电容。
第一章热氧化工艺解读

D-G干氧模型中给出一个值,来补偿初始阶段的过度生长。
湿氧工艺的氧化速率常数
干氧工艺的氧化速率常数
4、参数B和B/A的温度依赖关系 在各种氧化工艺条件下,参数B和B/A都可以确定下来, 并且是扩散系数、反应速率常数和气压等工艺参数的函数。 参数B和B/A可写成Arrhenius函数形式。
B和B/A
■ 参数B的激活能EA取决于氧化剂的扩散系数(D0)的激活能;
物线速率常数
B/A:线性速率常数
图4.2 氧化系数B的阿列尼乌斯图, 湿氧氧化参数取决于水汽浓度(进而 取决于气流量和高温分解条件)
图4.3 氧化系数B/A的阿列尼乌斯图
以干氧氧化为例
TCE:三氯乙烯
4、不同氧化方法的特点 (1) 干氧氧化:氧化速率慢,SiO2膜结构致密、干燥(与光 刻胶粘附性好),掩蔽能力强。 (2) 湿氧氧化:氧化速率快,SiO2膜结构较疏松,表面易有缺 陷,与光刻胶粘附性不良。 (湿氧环境中O2和
H2O的比例是关键参数)
(3) 氢氧合成氧化:氧化机理与湿氧氧化类似,SiO2膜质量取 决于H2,O2纯度(一般H2纯度可达99.9999%,O2纯度
一、二氧化硅(Si02)的性质和用途
(一)SiO2的结构
密度:~2.27g/cm3 分子量:60.09 热氧化方法制备的二氧化硅是无定形结构 (硅的密度:~2.33g/cm3) (硅的原子量:28.09)
分子数密度:2.2 1022 /cm3 (硅的原子数密度:5 1022 /cm3) 4个O原子位于四面体的顶点, Si位于四面体中心。 桥位O原子与2个Si原子键合; 其它O原子只与1个Si键合
5、影响氧化速率的因素 (1) 温度对氧化速率的影响:
温度 B和B/A 氧化速率
半导体制造工艺之硅的氧化概述

湿氧氧化法中,氧气和水蒸气在高温下与硅片反应,生成二 氧化硅层。该方法形成的二氧化硅层具有较低的折射率和较 好的光学性能,适用于制造光学器件和窗口材料等。
干氧氧化法
总结词
干氧氧化法是利用纯氧气与硅反应生 成二氧化硅的过程。
详细描述
干氧氧化法中,硅片和纯氧气在高温 下反应,生成二氧化硅层。该方法形 成的二氧化硅层具有较高的硬度和较 低的折射率,适用于制造集成电路和 微电子器件等。
SUMMAR Y
04
硅的氧化应用
集成电路制造
集成电路中的隔离技术
在集成电路制造中,硅的氧化被广泛 应用在隔离技术上。通过氧化,可以 将不同器件或电路区域进行隔离,防 止电流的交叉干扰。
保护层形成
在集成电路的制造过程中,硅的氧化 可以形成一层保护层,防止器件受到 环境中的化学物质和物理损伤。
微电子器件制造
详细描述
低功耗氧化技术通常在较低的温度下进行,例如600°C 或更低。这种技术利用特定的工艺条件来降低功耗,同 时保持氧化层的生长速度和稳定性。由于低功耗氧化技 术具有较低的能源消耗和较短的工艺时间,因此它在现 代半导体制造中越来越受到重视,有助于降低生产成本 和提高生产效率。
高k材料的应用
总结词
水汽热氧化法
总结词
水汽热氧化法是利用水汽在高温下与硅反应,生成二氧化硅的过程。
详细描述
水汽热氧化法中,硅片和水汽在高温下反应,生成二氧化硅层。该方法形成的二 氧化硅层具有较高的透过率和较低的折射率,适用于制造光学器件和窗口材料等 。
湿氧氧化法
总结词
湿氧氧化法是在氧气中加入水蒸气,与硅反应生成二氧化硅 的过程。
微型化制造
随着微电子器件的微型化,硅的氧化技术对 于形成微型结构至关重要。通过精确控制氧 化过程,可以制作出更小、更精确的电子器 件。
常见的热氧化工艺
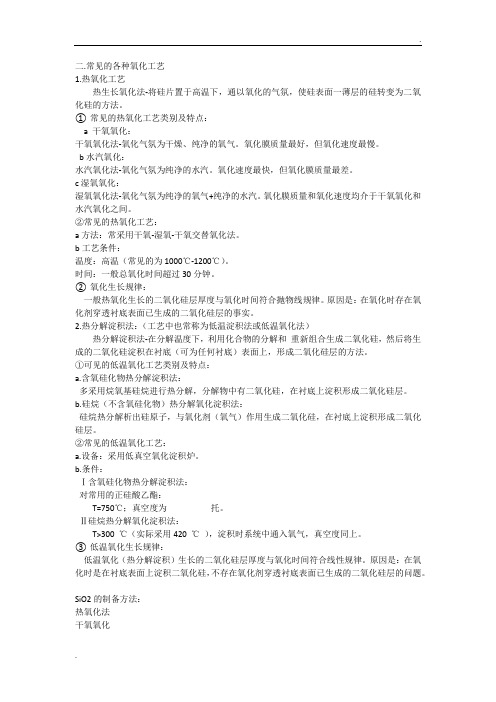
低温氧化(热分解淀积)生长的二氧化硅层厚度与氧化时间符合线性规律。原因是:在氧化时是在衬底表面上淀积二氧化硅,不存在氧化剂穿透衬底表面已生成的二氧化硅层的问题。
SiO2的制备方法:
热氧化法
干氧氧化
水蒸汽氧化
湿氧氧化
干氧-湿氧-干氧(简称干湿干)氧化法
氢氧合成氧化
化学气相淀积法
热分解淀积法
低温CVD氧化层:低于500℃
中等温度淀积:500~800℃
高温淀积:900℃左右
多晶硅的化学汽相淀积:利用多晶硅替代金属铝作为MOS器件的栅极是MOS集成电路技术的重大突破之一,它比利用金属铝作为栅极的MOS器件性能得到很大提高,而且采用多晶硅栅技术可以实现源漏区自对准离子注入,使MOS集成电路的集成度得到很大提高。
常压化学汽相淀积(APCVD)
低压化学汽相淀积(LPCVD)
等离子增强化学汽相淀积(PECVD)
化学汽相淀积(CVD)
单晶硅的化学汽相淀积(外延):一般地,将在单晶衬底上生长单晶材料的工艺叫做外延,生长有外延层的晶体片叫做外延片
二氧化硅的化学汽相淀积:可以作为金属化时的介质层,而且还可以作为离子注入或扩散的掩蔽膜,甚至还可以将掺磷、硼或砷的氧化物用作扩散源
氮化硅的化学汽相淀积:中等温度(780~820℃)的LPCVD或低温(300℃) PECVD方法淀积
物理气相淀积(PVD)
蒸发:在真空系统中,金属原子获得足够的能量后便可以脱离金属表面的束缚成为蒸汽原子,淀积在晶片上。按照能量来源的不同,有灯丝加热蒸发和电子束蒸发两种
溅射:真空系统中充Байду номын сангаас惰性气体,在高压电场作用下,气体放电形成的离子被强电场加速,轰击靶材料,使靶原子逸出并被溅射到晶片上
热氧化工艺

二氧化硅的基本特性 二氧化硅膜的用途 二氧化硅膜的制备方法 热氧化机制 热氧化系统
硅的氧化物及硅酸盐构成了地壳 中大部分的岩石、沙子和土壤、
约占地壳总量的90%以上。
二氧化硅 (SiO2)
二氧化硅广泛存在 于自然界中,与其 他矿物共同构成了 岩石。天然二氧化 硅也叫硅石,是一 种坚硬难熔的固体。
CO2+ Na2SiO3 +H2O==Na2CO3+H2SiO3↓ 2HCl+ Na2SiO3 ==2NaCl+H2SiO3↓ 硅酸部分脱水可形成硅胶。
nH2SiO3===H2n-2kSinO3n-k+kH2O
硅酸盐
☆硅酸盐是构成地壳岩石的主要成分,自然界中存在 的各种质和用途 ■ 热氧化原理(Deal-Grove 模型) ■ 热氧化工艺(方法)和系统 ■ 热氧化工艺的质量检测 参考资料:
《微电子制造科学原理与工程技术》第4章 热氧化 (电子讲稿中出现的图号是该书中的图号)
一、二氧化硅(Si02)的性质和用途
(一)SiO2的结构 热氧化方法制备的二氧化硅是无定形结构
几个概念
① 桥键氧原子
位于四面体之间,为两个硅原子 所共有的氧原子称桥键氧原子。
② 非桥键氧原子
只与一个四面体(硅原子)相连的氧 原子称非桥键氧原子。它还能接受一 个电子以维持八电子稳定结构。
桥键氧越少,非桥键氧越多,二氧化硅网络就越疏松。 通常的二氧化硅膜的密度约为2.20g/cm3
③ 网络调节剂
(2) 掺杂阻挡层(作为杂质扩散的掩蔽膜)
选择二氧化硅的理由:
A 杂质在二氧化硅中的运行速度 低于在硅中的运行速度
B 二氧化硅的热膨胀系数与硅接 近
硅热还原法

硅热还原法硅热还原法是一种常用的冶金技术,主要应用于金属和非金属元素的提取、精炼和合成。
本文将从原理、工艺流程、应用领域等方面对硅热还原法进行详细介绍。
一、硅热还原法的原理硅热还原法是利用还原剂(如纯碳或纯铝)和矿物(如氧化物或氧化物混合物)在高温下反应,使金属元素得以分离和提取。
其中,硅是最常用的还原剂之一,因其具有较高的还原性和稳定性。
在反应过程中,硅与氧化物反应生成气态二氧化硅和对应的金属或合金。
二、硅热还原法的工艺流程1. 原料准备:将所需的氧化物或混合氧化物粉末按比例混合均匀,并加入适量的还原剂(如纯碳或纯铝)。
2. 熔融反应:将混合粉末装入高温反应器中,在惰性气体保护下加热至高温(通常为1500-1800℃),使混合物熔融并发生还原反应。
3. 分离提取:在反应结束后,冷却后可得到金属或合金,再通过物理或化学方法进行分离和提取。
三、硅热还原法的应用领域1. 金属元素的提取和精炼:硅热还原法广泛应用于钨、钼、钛、铬等金属元素的提取和精炼。
2. 合成新材料:硅热还原法可以制备出一些新型材料,如碳化硅、氮化硅等。
3. 环保领域:硅热还原法可以将废弃物转化为有用的资源,如利用废旧锂电池中的钴、镍等元素进行回收。
四、硅热还原法的优缺点1. 优点:(1)反应温度高,反应速度快;(2)适用于多种氧化物混合物;(3)产物纯度高,可直接用于制备高纯度金属材料。
2. 缺点:(1)设备投资大,能耗高;(2)反应过程中产生大量二氧化碳等有害气体;(3)部分金属元素难以得到高纯度产品。
五、结语硅热还原法作为一种重要的冶金技术,在金属元素的提取、精炼和合成等方面具有广泛的应用前景。
未来,随着科技的不断发展和进步,硅热还原法也将不断完善和优化,为人类社会的发展做出更大的贡献。
常见的热氧化工艺

1.热氧化工艺热生长氧化法-将硅片置于高温下,通以氧化的气氛,使硅表面一薄层的硅转变为二氧化硅的方法。
①常见的热氧化工艺类别及特点:a 干氧氧化:干氧氧化法-氧化气氛为干燥、纯净的氧气。
氧化膜质量最好,但氧化速度最慢。
b水汽氧化:水汽氧化法-氧化气氛为纯净的水汽。
氧化速度最快,但氧化膜质量最差。
c湿氧氧化:湿氧氧化法-氧化气氛为纯净的氧气+纯净的水汽。
氧化膜质量和氧化速度均介于干氧氧化和水汽氧化之间。
②常见的热氧化工艺:a方法:常采用干氧-湿氧-干氧交替氧化法。
b工艺条件:温度:高温(常见的为1000℃-1200℃)。
时间:一般总氧化时间超过30分钟。
②氧化生长规律:一般热氧化生长的二氧化硅层厚度与氧化时间符合抛物线规律。
原因是:在氧化时存在氧化剂穿透衬底表面已生成的二氧化硅层的事实。
2.热分解淀积法:(工艺中也常称为低温淀积法或低温氧化法)热分解淀积法-在分解温度下,利用化合物的分解和重新组合生成二氧化硅,然后将生成的二氧化硅淀积在衬底(可为任何衬底)表面上,形成二氧化硅层的方法。
①可见的低温氧化工艺类别及特点:a.含氧硅化物热分解淀积法:多采用烷氧基硅烷进行热分解,分解物中有二氧化硅,在衬底上淀积形成二氧化硅层。
b.硅烷(不含氧硅化物)热分解氧化淀积法:硅烷热分解析出硅原子,与氧化剂(氧气)作用生成二氧化硅,在衬底上淀积形成二氧化硅层。
②常见的低温氧化工艺:a.设备:采用低真空氧化淀积炉。
b.条件:Ⅰ含氧硅化物热分解淀积法:对常用的正硅酸乙酯:T=750℃;真空度为托。
Ⅱ硅烷热分解氧化淀积法:T>300 ℃(实际采用420 ℃),淀积时系统中通入氧气,真空度同上。
③低温氧化生长规律:低温氧化(热分解淀积)生长的二氧化硅层厚度与氧化时间符合线性规律。
原因是:在氧化时是在衬底表面上淀积二氧化硅,不存在氧化剂穿透衬底表面已生成的二氧化硅层的问题。
SiO2的制备方法:热氧化法干氧氧化水蒸汽氧化湿氧氧化干氧-湿氧-干氧(简称干湿干)氧化法氢氧合成氧化化学气相淀积法热分解淀积法溅射法化学汽相淀积(CVD)化学汽相淀积(Chemical Vapor Deposition):通过气态物质的化学反应在衬底上淀积一层薄膜材料的过程CVD技术特点:具有淀积温度低、薄膜成分和厚度易于控制、均匀性和重复性好、台阶覆盖优良、适用范围广、设备简单等一系列优点CVD方法几乎可以淀积集成电路工艺中所需要的各种薄膜,例如掺杂或不掺杂的SiO2、多晶硅、非晶硅、氮化硅、金属(钨、钼)等常压化学汽相淀积(APCVD)低压化学汽相淀积(LPCVD)等离子增强化学汽相淀积(PECVD)化学汽相淀积(CVD)单晶硅的化学汽相淀积(外延):一般地,将在单晶衬底上生长单晶材料的工艺叫做外延,生长有外延层的晶体片叫做外延片二氧化硅的化学汽相淀积:可以作为金属化时的介质层,而且还可以作为离子注入或扩散的掩蔽膜,甚至还可以将掺磷、硼或砷的氧化物用作扩散源低温CVD氧化层:低于500℃中等温度淀积:500~800℃高温淀积:900℃左右多晶硅的化学汽相淀积:利用多晶硅替代金属铝作为MOS器件的栅极是MOS集成电路技术的重大突破之一,它比利用金属铝作为栅极的MOS器件性能得到很大提高,而且采用多晶硅栅技术可以实现源漏区自对准离子注入,使MOS集成电路的集成度得到很大提高。
氧化工艺——精选推荐

氧化⼯艺薄膜淀积⼀、介绍在分⽴器件与集成电路制造过程中,需要很多类型的薄膜,这些薄膜主要分为四类:热氧化薄膜、介质、多晶硅以及⾦属膜等:半导体可采⽤多种氧化⽅法,包括热氧化法、电化学阳极氧化法以及等离⼦体反应法。
对于硅来说,热氧化法是最重要的。
在热氧化薄膜中,有两种膜最重要:⼀种是在漏/源极的导通沟道覆盖的栅极氧化膜(gate oxide);⼀种是⽤来隔离其他器件的场氧化膜(field oxide)。
这些膜只有通过热氧化才能获得最低界⾯陷阱密度的⾼质量氧化膜。
⼆氧化硅SiO2和氮化硅Si3N4的介电薄膜作⽤:隔离导电层;作为扩散及离⼦注⼊的掩蔽膜;防⽌薄膜下掺杂物的损失;保护器件使器件免受杂质、⽔⽓或刮伤的损害。
由于多晶硅电极的可靠性由于铝电极,常⽤来制作MOS器件的栅极;多晶硅可以作为杂质扩散的浅结接触材料;作为多层⾦属的导通材料或⾼电阻值的电阻。
⾦属薄膜有铝或⾦属硅化物,⽤来形成具有低电阻值的⾦属连线、欧姆接触及整流⾦属-半导体接触势垒器件。
⼆、原理与⼯艺A、热氧化⼯艺热氧化⼯艺的原理就是在硅衬底上⽣成⾼质量的⼆氧化硅薄膜。
热氧化⼯艺分为⼲氧氧化和湿氧氧化。
反应⽅程式如下:Si+2H2O→SiO2+2H2湿氧氧化Si+O2→SiO2⼲氧氧化热氧化是⾼温⼯艺。
在⾼温下,⼀开始是氧原⼦与硅原⼦结合,⼆氧化硅的⽣长是⼀个线性过程。
⼤约长了500?之后,线性阶段达到极限。
为了保持氧化层的⽣长,氧原⼦与硅原⼦必须相互接触。
在⼆氧化硅的热⽣长过程中,氧⽓扩散通过氧化层进⼊到硅表⾯,因此,⼆氧化硅从硅表⾯消耗硅原⼦,氧化层长⼊硅表⾯。
随着氧化层厚度的增加,氧原⼦只有扩散通过更长的⼀段距离才可以到达硅表⾯。
因此从时间上来看,氧化层的⽣长变慢,氧化层厚度、⽣长率及时间之间的关系成抛物线形。
⾼质量的⼆氧化硅都是在800℃~1200℃的⾼温下⽣成,⽽且其⽣成速率极其缓慢。
其中湿氧氧化速率要⾼于⼲氧氧化。
在氧化过程中,硅与⼆氧化硅的界⾯会向硅内部迁移,这将使得Si表⾯原有的污染物移到氧化膜表⾯⽽形成⼀个崭新的界⾯。
- 1、下载文档前请自行甄别文档内容的完整性,平台不提供额外的编辑、内容补充、找答案等附加服务。
- 2、"仅部分预览"的文档,不可在线预览部分如存在完整性等问题,可反馈申请退款(可完整预览的文档不适用该条件!)。
- 3、如文档侵犯您的权益,请联系客服反馈,我们会尽快为您处理(人工客服工作时间:9:00-18:30)。
实验硅热氧化工艺在硅片表面生长一层优质的氧化层对整个半导体集成电路制造过程具有极为重要的意义。
它不仅作为离子注入或热扩散的掩蔽层,而且也是保证器件表面不受周围气氛影响的钝化层,它不光是器件与器件之间电学隔离的绝缘层,而且也是MOS工艺以及多层金属化系统中保证电隔离的主要组成部分。
因此了解硅氧化层的生长机理,控制并重复生长优质的硅氧化层方法对保证高质量的集成电路可靠性是至关重要的。
在硅片表面形成SiO2的技术有很多种:热氧化生长,热分解淀积(即VCD 法),外延生长,真空蒸发,反应溅射及阳极氧化法等。
其中热生长氧化在集成电路工艺中用得最多,其操作简便,且氧化层致密,足以用作为扩散掩蔽层,通过光刻易形成定域扩散图形等其它应用。
一、实验目的1、掌握热生长SiO2的工艺方法(干氧、湿氧、水汽)。
2、熟悉SiO2层在半导体集成电路制造中的重要作用。
3、了解影响氧化层质量有哪些因素。
4、能建立起厚度d和时间t的函数关系。
5、了解形成SiO2层的几种方法及它们之间的不同之处。
二、实验原理热生长二氧化硅法是将硅片放在高温炉内,在以水汽、湿氧或干氧作为氧化剂的氧化气氛中,使氧与硅反应来形成一薄层二氧化硅。
图1和图2分别给出了干氧和水汽氧化装置的示意图。
图1、干氧氧化装置示意图图2、水汽氧化装置示意图将经过严格清洗的硅片表面处于高温的氧化气氛(干氧、湿氧、水汽)中时,由于硅片表面对氧原子具有很高的亲和力,所以硅表面与氧迅速形成SiO 2层。
硅的常压干氧和水汽氧化的化学反应式分别为:Si+O 2—→SiO 2 (2—1) Si+2H 2O —→SiO 2+2H 2↑ (2—2) 如果生长的二氧化硅厚度为χ0(μm),所消耗的硅厚度为χi ,则由定量分析可知:46.00==χχαi(2—3) 即生长1μm 的SiO 2,要消耗掉0.46μm 的Si 。
由于不同热氧化法所得二氧化硅的密度不同,故α值亦不同。
图3示出了硅片氧化前后表面位置的变化。
图3、SiO 2生长对应硅片表面位置的变化当硅片表面生长一薄层SiO 2以后,它阻挡了O 2或H 2O 直接与硅表面接触,此时氧原子和水分子必须穿过SiO 2薄膜到达Si —SiO 2界面才能与硅继续反应生长SiO 2。
显然,随着氧化层厚度的增长,氧原子和水分子穿过氧化膜进一步氧化就越困难,所以氧化膜的增厚率将越来越小。
Deal —Grove 的模型描述了硅氧化的动力学过程。
他们的模型对氧化温度700℃至1300℃,压强0.2至1个大气压(也许更高些),生长厚度300Å至20000Å的干氧和湿氧氧化证明是合适的。
通过多种实验已经证明,硅片在热氧化过程中是氧化剂穿透氧化层向Si —SiO 2界面运动并与硅进行反应,而不是硅向外运动到氧化膜的外表面进行反应,其氧化模型如图4所示。
氧化剂要到达硅表面并发生反应,必须经历下列三个连续的步骤:图4、Deal —Grove 热氧化模型① 从气体内部输运到气体——氧化物界面,其流密度用F 1表示。
② 扩散穿透已生成的氧化层,到达SiO 2—Si 界面,其流密度用F 2表示。
③ 在Si 表面发生反应生成SiO 2,其流密度用F 3表示。
在氧化过程中,由于SiO 2层不断生长,所以SiO 2—Si 界面也就不断向Si 内移动,因此,这里所碰到的是边界随时间变化的扩散问题。
我们可以采用准静态近似,即假定所有反应实际上都立即达到稳定条件,这样变动的边界对扩散过程的影响可以忽略。
在准静态近似下,上述三个流密度应该相等,则有F 1=F 2=F 3 (2—4) 附面层中的流密度取线性近似,即从气体内部到气体——氧化物界面处的氧化剂流密度F 1正比于气体内部氧化剂浓度Cg 与贴近SiO 2表面上的氧化剂浓度Cs 的差,数学表达式为)(1s g g C C h F -= (2—5)其中g h 是气相质量输运(转移)系数。
假定在我们所讨论的热氧化过程中,亨利定律是成立的:即认为在平衡条件下,固体中某种物质的浓度正比于该物质在固体周围的气体中的分压。
于是SiO 2表面的氧化剂浓度Co 正比于贴近SiO 2表面的氧化剂分压Ps ,则有S O HP C = (2—6)H 为亨利定律常数。
在平衡情况下,SiO 2中氧化剂的浓度C *应与气体(主气流区)中的氧化剂分压Pg 成正比,即有C * = HPg (2—7) 由理想气体定律可以得到 KTP C g g = (2—8)KTP C SS =(2—9) 把式(2—6)~(2—9)代入式(2—5)中,则有)(*1O C C h F -= (2—10) HKTh h g =(2—11)其中h 是用固体中的浓度表示的气相质量输运(转移)系数,而式(2—10)是用固体中的浓度表示的附面层中的流密度。
通过SiO 2层的流密度F 2就是扩散流密度,数学表达式为 OiO X C C DF --=2 (2—12) D 为氧化剂在SiO 2中的扩散系数,Co 和C i 分别表示SiO 2表面和SiO 2—Si 界面处的氧化剂浓度,X O 为SiO 2的厚度。
如果假定在SiO 2—Si 界面处,氧化剂与Si 反应的速率正比于界面处氧化剂的浓度C i ,于是有i S C K F =3 (2—13) K S 为氧化剂与Si 反应的化学反应常数。
根据稳态条件F 1=F 2=F 3,再经过一定的数学运算,可得到C i 和C o 的具体表达式DX K h K C C OS S i ++=1*(2—14)DX K h K CD X K C O S S O S O ++⎪⎭⎫ ⎝⎛+=11* (2—15)当上面两式中扩散系数D 极大或极小时,硅的热氧化存在两种极限情况。
当D 非常小时,C i →0,C o →C *,这种情况称为扩散控制态。
它导致通过氧化层的氧化输运流量比在Si —SiO 2界面处反应的相应流量来得小(因为D 小),因此氧化速率取决于界面处提供的氧。
第二种极限情况是D 非常大时,hK C C C S o i +==1*(2—16)此时称为反应控制态。
因为在Si —SiO 2界面处提供足够的氧,氧化速率是由反应速率常数K S 和C i (等于C 0)所控制。
为了计算氧化层生长的速率,我们定义N 1为进入单位体积氧化层中氧化的分子数,由于每立方厘米氧化层中SiO 2分子密度为2.2×1022个,每生成一个SiO 2分子需要一个氧分子,或者两个水分子,这样对氧气氧化来说N 1为2.2×1022/cm 3,对水汽氧化来说N 1为4.4×1022/cm 3。
随着SiO 2不断生长,界面处的Si 也就不断转化为SiO 2中的成份,因此Si 表面处的流密度也可表示为dtdX N F O13= (2—17) 把(2—14)式代入到(2—13)式中,并与上式联立,则得到SiO 2层的生长厚度与生长时间的微分方程DX K h K C K F dtdX N O S S S O++==1*31(2—18)这个微分方程的初始条件是X 0(0)=X i ,X i 代表氧化前硅片上原有的SiO 2厚度。
这样的初始条件适合两次或多次连续氧化的实际情况。
微分方程(2—18)的解给出了SiO 2的生长厚度与时间的普遍关系式。
)(2τ+=+t B AX X O O(2—19) 其中)11(2hK D A S += (2—20) 1*2N DC B = (2—21)BAX X ii +=2τ (2—22)A 和B 都是速率常数。
方程(2—19)的解为⎪⎪⎪⎭⎫⎝⎛-++=14122B A t A X O τ(2—23)在氧化过程中,首先是氧化剂由气体内部扩散到二氧化硅界面处。
因为在汽相中扩散速度要比在固相中大得多,所以扩散到二氧化硅与气体界面处的氧化剂是充足的,也就是说SiO 2的生长速率不会受到氧化剂在汽相中输运(转移)速度的影响。
因此,SiO 2生长的快慢将由氧化剂在SiO 2种的扩散速度以及与Si 反应速度中较慢的一个因素所决定,。
即存在上面叙述过的扩散控制和表面化学反应控制两种极限情况。
从SiO 2厚度与生长时间的普遍关系式(2—23)中也可以得到上述两种极限情况。
当氧化时间很长,即t >>τ和t>>B A 42时,则SiO 2生长厚度与时间的关系式可简化为)(2τ+=t B X O(2—24) 这种情况下的氧化规律称抛物型规律,B 为抛物型速率常数。
由(2—21)式可以看到,B 与D 成正比,所以SiO 2的生长速率主要由氧化剂在SiO 2中的扩散快慢所决定,即为扩散控制。
当氧化时间很短,即(t +τ)<<B A 42,则SiO 2的厚度与时间的关系式可简化为)(τ+=t ABX O (2—25) 这种极限情况下的氧化规律称线性规律,B/A 为线性速率常数,具体表达式为1*N C h K h K A BS S ⋅+= (2—26) 表1:硅的湿氧氧化速率表2:硅的干氧氧化速率表1和表2分别为硅湿氧氧化和干氧氧化的速率常数。
图5和图6分别为干氧氧化层厚度与时间的关系和湿氧氧化层厚度与时间的关系。
图5、(111)硅干氧氧化层厚度与时间的关系图6、(111)硅湿氧氧化层厚度与时间的关系由表1和表2以及图5和图6可见,湿氧氧化速率比干氧氧化速率快得多。
虽然干氧方法的生长速度很慢,但生长的SiO2薄膜结构致密,干燥,均匀性和重复性好,且由于SiO2表面与光刻胶接触良好,光刻时不易浮胶。
而湿氧氧化速率虽然快,但在氧化后的Si片表面存在较多的位错和腐蚀坑,而且还存在着一层使SiO2表面与光刻胶接触差的硅烷醇(Si—OH),因此在生产实践中,普遍采用干氧→湿氧→干氧交替的氧化方式。
这种干、湿氧的交替氧化方式解决了生长速率和质量之间的矛盾,使生长的SiO2薄膜更好地满足实际生产的要求。
氧化层质量的检测包括:测量膜厚、折射率、氧化层中可动正电荷密度、Si—SiO2界面态密度、氧化层的漏电及介质击穿等。
三、实验装置1、扩散氧化炉2、椭偏仪3、高频C—V测试仪四、实验步骤1、取5片清洗的Si样片,用镊子夹到石英舟上。
将炉温控制在1150℃,并通入干O2,流量为500ml / 分钟。
将石英舟缓慢推入炉中恒温区,分别以5分钟、10分钟、20分钟、40分钟、60分钟五种不同时间生长厚度不同的SiO2层。
2、另外取一片清洁Si片,再同样温度下,通湿O2进行氧化,水温控制在95℃,时间为20分钟。
3、用椭偏仪并结合干涉法分别测量上述各氧化层的厚度,并作图求出1150℃下干氧氧化速率常数。
4、比较同样时间,同样温度下干、湿氧化薄膜厚度的差别。
5、用B—T、C—V法测量1150℃,60分钟干氧生长的氧化层中的可动正离子密度。