机械装配标准和方法
机械装配类型及方法

机器装配的基本概念
上述精度之间的关系: 接触精度和配合精度是距离精度的基础。 位置精度又是相对运动精度的基础。
装配精度与零件精度之间的关系: 一般来说零件精度越高,装配精度就
越容易保证。但装配精度不完全依靠零件精 度来达到,而与装配方法有关。
机器装配的基本概念
要求任何一个零件不再经过修配及补充加工就能满足技术要求装配。零件制造精度要求较高,制造费用大,但 有利于组织装配流水线和专业化协作生产。用于大批、大量生产
3、选配法(不完全互换法)
按照严格的尺寸范围将零件分成若干组,然后将对应的各组 配合件装配在一起,以达到所需要求的装配精度,零件的 制造公差可以适当放大,
机器装配的基本概念
在装配工艺规程设计中,常用装配工艺系统图表示零、部件的 装配流程和零、部件间相互装配关系。
在装配工艺系统图上,每一 个单元用一个长方形框表示,标 明零件、套件、组件和部件的名 称、编号及数量。
在装配工艺系统图上,装配工
作由基准件开始沿水平线自左向 右进行,一般将零件画在上方, 套件、组件、部件画在下方,其 排列次序就是装配工作的先后次 序。
机器装配工艺设计注意事项
A、产品装配操作工序分开,产品应能分解成若干个独立的装 配单元
可组织平行的装配作业,装配周期减少,便于组织多厂合作(组 件、部件等)
长轴做短,用联轴器连接,减少加工难度及装配难度,提高效率 转动件的动平衡,转子单独做,不要放在整机中进行 测试时对整个组件或机器进行测试,不对零件进行测试
图b 结构对比
(4)通过功能合成减少装配零件数目 (5)装配操作可以同时进行 (6)减少结合部件及结合表面 (7)对装配好的组件及产品进行功能测试时无
机械工艺中的机械装配与调试方法
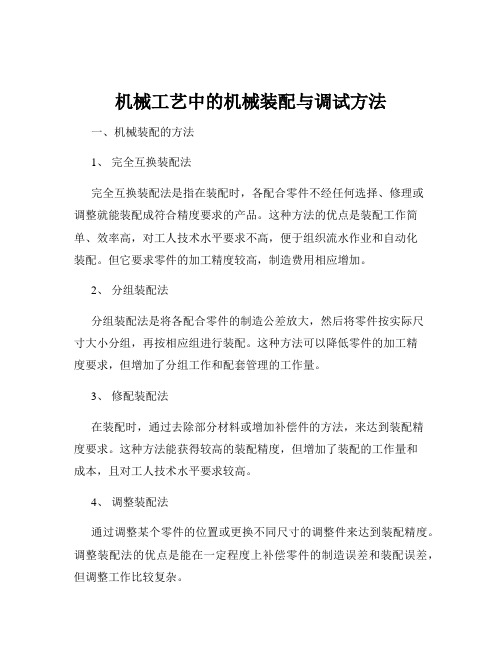
机械工艺中的机械装配与调试方法一、机械装配的方法1、完全互换装配法完全互换装配法是指在装配时,各配合零件不经任何选择、修理或调整就能装配成符合精度要求的产品。
这种方法的优点是装配工作简单、效率高,对工人技术水平要求不高,便于组织流水作业和自动化装配。
但它要求零件的加工精度较高,制造费用相应增加。
2、分组装配法分组装配法是将各配合零件的制造公差放大,然后将零件按实际尺寸大小分组,再按相应组进行装配。
这种方法可以降低零件的加工精度要求,但增加了分组工作和配套管理的工作量。
3、修配装配法在装配时,通过去除部分材料或增加补偿件的方法,来达到装配精度要求。
这种方法能获得较高的装配精度,但增加了装配的工作量和成本,且对工人技术水平要求较高。
4、调整装配法通过调整某个零件的位置或更换不同尺寸的调整件来达到装配精度。
调整装配法的优点是能在一定程度上补偿零件的制造误差和装配误差,但调整工作比较复杂。
二、机械装配的基本要求1、零件的清理和清洗在装配前,要对零件进行清理和清洗,去除表面的毛刺、油污、锈迹等,以保证零件的配合精度和可靠性。
2、零件的正确安装按照装配工艺规程的要求,将零件正确地安装在规定的位置上,注意安装顺序和方向,避免错装和漏装。
3、连接的可靠性连接件如螺栓、螺母、销钉等要拧紧、固定牢固,保证连接的可靠性和稳定性。
4、润滑和密封对于需要润滑的部位,要添加适量的润滑剂;对于需要密封的部位,要采用合适的密封件,确保密封性能良好,防止泄漏。
三、机械调试的方法1、空运转调试在不加载的情况下,让机械系统运转一段时间,检查各运动部件的运转是否平稳、灵活,有无异常噪声和发热现象。
2、负载调试逐渐增加负载,测试机械系统在不同负载下的性能,如工作速度、输出功率、精度等,检查是否满足设计要求。
3、精度调试对机械系统的各项精度指标进行测试和调整,如位置精度、运动精度、几何精度等,通过调整相关部件的位置和参数,使精度达到规定的标准。
机械工程中的装配与调试规范要求
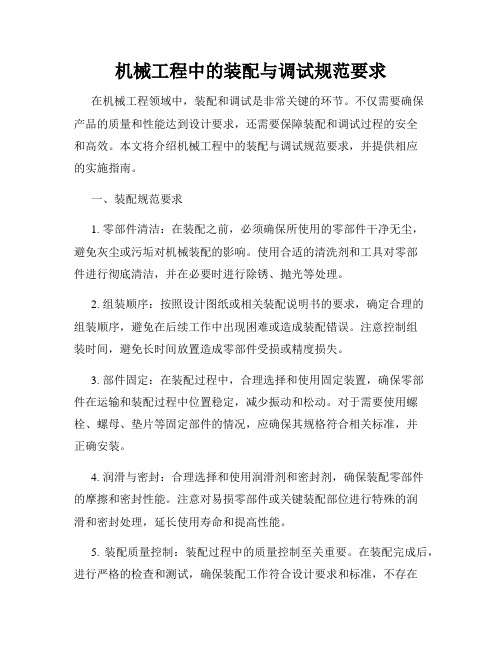
机械工程中的装配与调试规范要求在机械工程领域中,装配和调试是非常关键的环节。
不仅需要确保产品的质量和性能达到设计要求,还需要保障装配和调试过程的安全和高效。
本文将介绍机械工程中的装配与调试规范要求,并提供相应的实施指南。
一、装配规范要求1. 零部件清洁:在装配之前,必须确保所使用的零部件干净无尘,避免灰尘或污垢对机械装配的影响。
使用合适的清洗剂和工具对零部件进行彻底清洁,并在必要时进行除锈、抛光等处理。
2. 组装顺序:按照设计图纸或相关装配说明书的要求,确定合理的组装顺序,避免在后续工作中出现困难或造成装配错误。
注意控制组装时间,避免长时间放置造成零部件受损或精度损失。
3. 部件固定:在装配过程中,合理选择和使用固定装置,确保零部件在运输和装配过程中位置稳定,减少振动和松动。
对于需要使用螺栓、螺母、垫片等固定部件的情况,应确保其规格符合相关标准,并正确安装。
4. 润滑与密封:合理选择和使用润滑剂和密封剂,确保装配零部件的摩擦和密封性能。
注意对易损零部件或关键装配部位进行特殊的润滑和密封处理,延长使用寿命和提高性能。
5. 装配质量控制:装配过程中的质量控制至关重要。
在装配完成后,进行严格的检查和测试,确保装配工作符合设计要求和标准,不存在漏装、错装或装配不规范的情况。
对于涉及安全的机械装配,应进行专门的测试和验证。
二、调试规范要求1. 参数设定:在进行机械设备的调试之前,需要明确设定相关参数,包括速度、压力、温度等。
根据设备的特性和设计要求,合理设定参数范围,并在调试过程中进行逐步调整,确保设备在正常运行范围内。
2. 现场安全:在进行设备调试时,必须严格执行相关的安全操作规程,避免人身伤害和设备损坏。
确保调试区域的环境安全,采取相应的防护措施,并由专业人员进行操作和监控。
3. 系统集成:在设备调试过程中,特别是复杂机械设备的调试,需要确保各个系统之间的良好集成和协调。
在测试和调试过程中,对各个系统进行全面检查和验证,确保其正常运行和完善的协同工作。
机械装配标准与方法
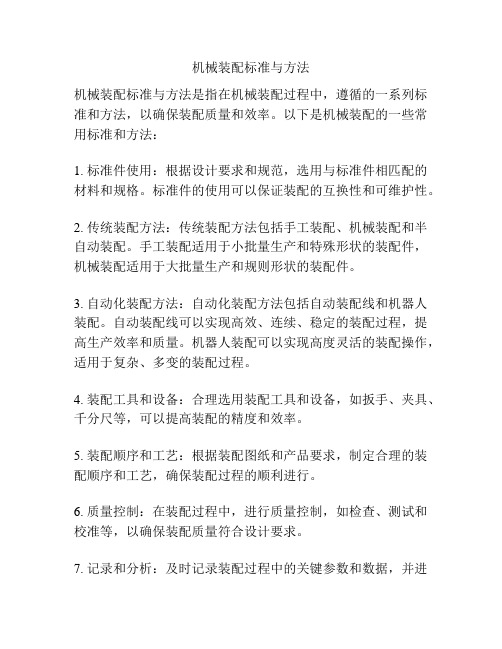
机械装配标准与方法
机械装配标准与方法是指在机械装配过程中,遵循的一系列标准和方法,以确保装配质量和效率。
以下是机械装配的一些常用标准和方法:
1. 标准件使用:根据设计要求和规范,选用与标准件相匹配的材料和规格。
标准件的使用可以保证装配的互换性和可维护性。
2. 传统装配方法:传统装配方法包括手工装配、机械装配和半自动装配。
手工装配适用于小批量生产和特殊形状的装配件,机械装配适用于大批量生产和规则形状的装配件。
3. 自动化装配方法:自动化装配方法包括自动装配线和机器人装配。
自动装配线可以实现高效、连续、稳定的装配过程,提高生产效率和质量。
机器人装配可以实现高度灵活的装配操作,适用于复杂、多变的装配过程。
4. 装配工具和设备:合理选用装配工具和设备,如扳手、夹具、千分尺等,可以提高装配的精度和效率。
5. 装配顺序和工艺:根据装配图纸和产品要求,制定合理的装配顺序和工艺,确保装配过程的顺利进行。
6. 质量控制:在装配过程中,进行质量控制,如检查、测试和校准等,以确保装配质量符合设计要求。
7. 记录和分析:及时记录装配过程中的关键参数和数据,并进
行分析,以改进装配方法和提高装配质量。
总之,机械装配标准与方法是为了确保装配质量和效率,提高产品的可靠性和竞争力。
机械部件与装配的标准与规范
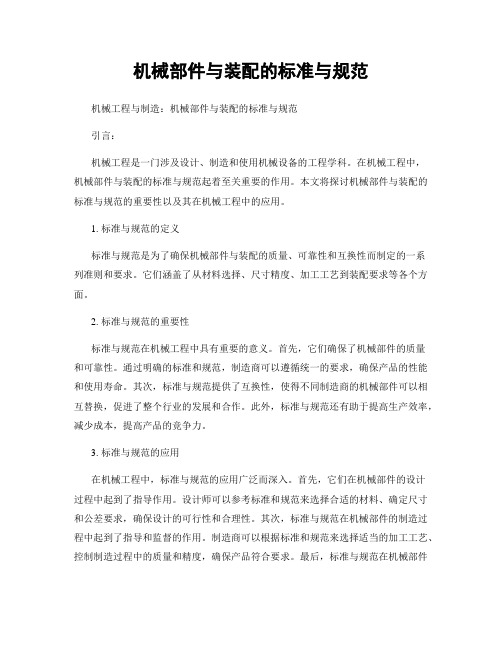
机械部件与装配的标准与规范机械工程与制造:机械部件与装配的标准与规范引言:机械工程是一门涉及设计、制造和使用机械设备的工程学科。
在机械工程中,机械部件与装配的标准与规范起着至关重要的作用。
本文将探讨机械部件与装配的标准与规范的重要性以及其在机械工程中的应用。
1. 标准与规范的定义标准与规范是为了确保机械部件与装配的质量、可靠性和互换性而制定的一系列准则和要求。
它们涵盖了从材料选择、尺寸精度、加工工艺到装配要求等各个方面。
2. 标准与规范的重要性标准与规范在机械工程中具有重要的意义。
首先,它们确保了机械部件的质量和可靠性。
通过明确的标准和规范,制造商可以遵循统一的要求,确保产品的性能和使用寿命。
其次,标准与规范提供了互换性,使得不同制造商的机械部件可以相互替换,促进了整个行业的发展和合作。
此外,标准与规范还有助于提高生产效率,减少成本,提高产品的竞争力。
3. 标准与规范的应用在机械工程中,标准与规范的应用广泛而深入。
首先,它们在机械部件的设计过程中起到了指导作用。
设计师可以参考标准和规范来选择合适的材料、确定尺寸和公差要求,确保设计的可行性和合理性。
其次,标准与规范在机械部件的制造过程中起到了指导和监督的作用。
制造商可以根据标准和规范来选择适当的加工工艺、控制制造过程中的质量和精度,确保产品符合要求。
最后,标准与规范在机械部件的装配过程中起到了协调和统一的作用。
装配工程师可以根据标准和规范来安排装配顺序、确定装配工艺,确保装配的准确性和稳定性。
4. 标准与规范的发展与更新随着科技的进步和工程实践的发展,标准与规范也在不断更新和完善。
新材料、新工艺和新技术的出现,使得原有的标准和规范需要进行修订和更新。
此外,全球化的趋势也促使各个国家和地区对标准与规范进行协调和统一,以促进国际贸易和合作。
结论:机械部件与装配的标准与规范在机械工程中具有重要的地位和作用。
它们确保了机械部件的质量和可靠性,提高了生产效率和产品的竞争力。
机械制造中的机械装配与装配工艺

机械制造中的机械装配与装配工艺机械装配是指将各种机械零部件按照特定的顺序和方法进行组装,从而制成完整的机械产品的过程。
在机械制造中,机械装配和装配工艺是非常重要的环节,直接关系到机械产品的品质和性能。
一、机械装配概述机械装配是将加工好的各种零部件进行装配,并通过螺栓、焊接、粘接等方式将其紧固在一起,形成完整的机械产品。
装配的过程中需要考虑各个部件的尺寸、形状、材料等因素,确保装配的精度和稳定性。
此外,还需要根据产品设计要求进行各种连接和传动装置的布置。
二、机械装配的工艺流程1. 零部件检验:在装配之前,需要对零部件进行质量检验,确保其符合设计要求。
包括外观检查、尺寸测量、材料鉴定等。
2. 组装工艺规划:根据产品的设计要求,规划装配的步骤和方法。
确定所需工具、夹具和设备,确保装配过程的顺利进行。
3. 零部件的清洗和润滑:将零部件进行清洗和润滑处理,去除表面的污垢和氧化层,提高装配质量和使用寿命。
4. 零件装配:根据装配要求和图纸,按照顺序逐步进行零部件的装配。
可以采用手工组装、半自动装配或全自动装配等方式。
5. 零部件的固定:在装配过程中,根据需要使用螺栓、紧固件、焊接或粘接等方式将零部件固定在一起。
确保装配的牢固性和稳定性。
6. 产品调试和测试:在装配完成后,对产品进行调试和测试。
检查各个部件的功能是否正常,是否存在问题和缺陷。
7. 产品包装和出厂:在装配完毕并通过测试后,对产品进行包装,保护其免受损坏。
然后出厂交付给用户或销售商。
三、机械装配的关键技术1. 尺寸控制技术:机械装配中,要求各个零部件的尺寸精度达到一定的要求,确保装配的精度和可靠性。
因此,需要使用适当的测量工具和方法,进行尺寸的检测和控制。
2. 工艺参数控制技术:在装配过程中,需控制各项工艺参数,如温度、湿度、力度等,以确保装配的一致性和稳定性。
这需要选择合适的工艺参数,采取相应的控制措施。
3. 质量控制技术:机械装配中,需要对质量进行控制,避免出现零部件的缺陷和错误装配等问题。
机械装配标准与方法
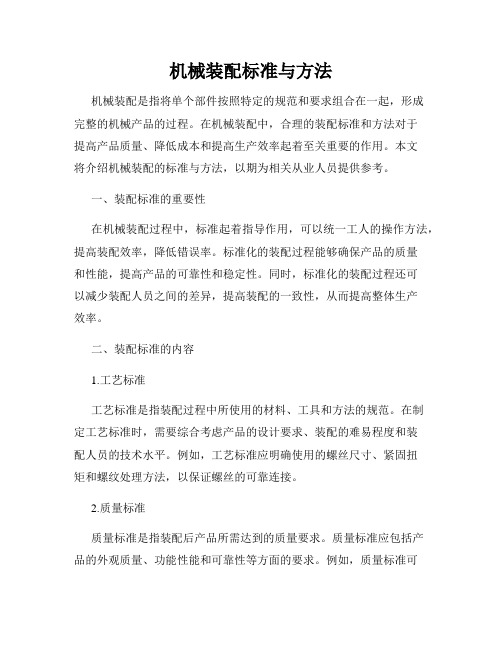
机械装配标准与方法机械装配是指将单个部件按照特定的规范和要求组合在一起,形成完整的机械产品的过程。
在机械装配中,合理的装配标准和方法对于提高产品质量、降低成本和提高生产效率起着至关重要的作用。
本文将介绍机械装配的标准与方法,以期为相关从业人员提供参考。
一、装配标准的重要性在机械装配过程中,标准起着指导作用,可以统一工人的操作方法,提高装配效率,降低错误率。
标准化的装配过程能够确保产品的质量和性能,提高产品的可靠性和稳定性。
同时,标准化的装配过程还可以减少装配人员之间的差异,提高装配的一致性,从而提高整体生产效率。
二、装配标准的内容1.工艺标准工艺标准是指装配过程中所使用的材料、工具和方法的规范。
在制定工艺标准时,需要综合考虑产品的设计要求、装配的难易程度和装配人员的技术水平。
例如,工艺标准应明确使用的螺丝尺寸、紧固扭矩和螺纹处理方法,以保证螺丝的可靠连接。
2.质量标准质量标准是指装配后产品所需达到的质量要求。
质量标准应包括产品的外观质量、功能性能和可靠性等方面的要求。
例如,质量标准可以规定产品的尺寸公差范围、表面光洁度和工作环境下的工作温度范围。
3.检验标准检验标准是指对装配过程中每个环节以及最终产品进行检验的方法和要求。
检验标准可以包括检查装配件的尺寸、外观和连接是否正确,以及对产品进行性能测试和可靠性评估。
三、装配方法的选择1.顺序装配法顺序装配法是指按照装配顺序进行装配的方法。
这种方法通常适用于装配过程中有明确装配顺序要求的情况,例如,装配产品的各个部件之间存在依赖关系,需要按照特定顺序进行组装。
顺序装配法可以避免装配顺序错误导致的拆装和重新装配,提高装配效率。
2.并行装配法并行装配法是指将装配过程中可以并行进行的操作同时进行的方法。
这种方法适用于装配过程中存在独立操作且操作之间没有依赖关系的情况。
并行装配法可以充分利用装配人员和设备资源,提高装配效率。
3.模块化装配法模块化装配法是指先将产品划分为不同的模块,然后分别完成各个模块的装配,最后将各个模块组装在一起的方法。
机械设计基础零件装配和连接方法
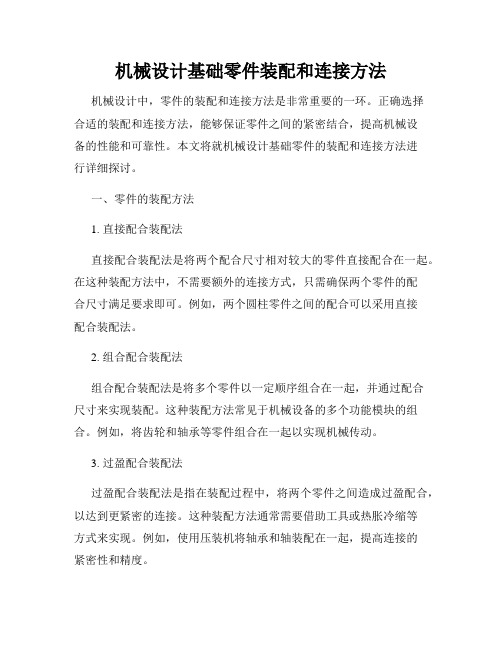
机械设计基础零件装配和连接方法机械设计中,零件的装配和连接方法是非常重要的一环。
正确选择合适的装配和连接方法,能够保证零件之间的紧密结合,提高机械设备的性能和可靠性。
本文将就机械设计基础零件的装配和连接方法进行详细探讨。
一、零件的装配方法1. 直接配合装配法直接配合装配法是将两个配合尺寸相对较大的零件直接配合在一起。
在这种装配方法中,不需要额外的连接方式,只需确保两个零件的配合尺寸满足要求即可。
例如,两个圆柱零件之间的配合可以采用直接配合装配法。
2. 组合配合装配法组合配合装配法是将多个零件以一定顺序组合在一起,并通过配合尺寸来实现装配。
这种装配方法常见于机械设备的多个功能模块的组合。
例如,将齿轮和轴承等零件组合在一起以实现机械传动。
3. 过盈配合装配法过盈配合装配法是指在装配过程中,将两个零件之间造成过盈配合,以达到更紧密的连接。
这种装配方法通常需要借助工具或热胀冷缩等方式来实现。
例如,使用压装机将轴承和轴装配在一起,提高连接的紧密性和精度。
二、零件的连接方法1. 螺纹连接螺纹连接是一种常见的机械零件连接方法。
在螺纹连接中,通过螺纹的相互嵌合,将两个零件牢固地连接在一起。
常见的螺纹连接方式包括螺纹钉、螺纹螺母等。
2. 锁紧连接锁紧连接是为了防止螺纹连接松动而采取的一种措施。
通过在螺纹连接处添加锁紧垫圈、螺母等零件,使连接更加牢固可靠。
这种连接方式常见于对振动和冲击要求较高的设备中。
3. 键连接键连接是通过在轴和零件的轴孔上添加键来实现的。
通过键的配合,可在连接中实现转矩的传递。
这种连接方式常用于需要传递一定转矩的零件连接,如齿轮和轴的连接。
4. 焊接连接焊接连接是通过在零件接触面上进行熔化和凝固,使两个零件牢固地连接在一起。
常见的焊接方式包括电弧焊、气体焊等。
这种连接方式适用于连接条件较为恶劣的环境下。
5. 贴合连接贴合连接是指通过在零件的接触面上施加压力,使零件之间的摩擦力达到连接效果。
常见的贴合连接方式包括铆接、压入、插接等。
装配的基本知识和方法
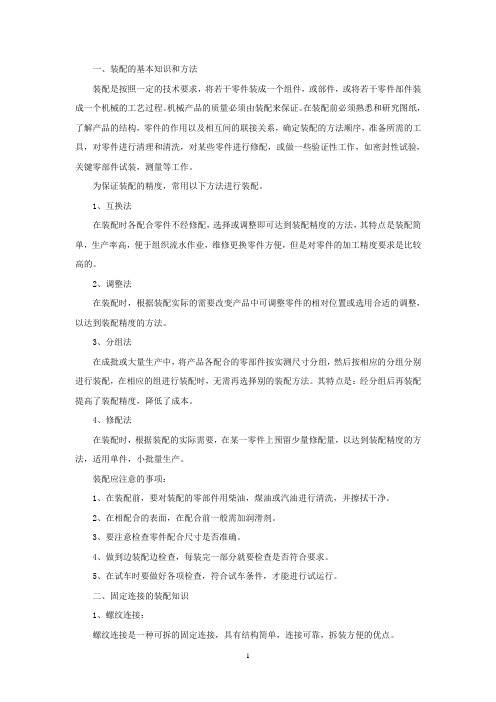
一、装配的基本知识和方法装配是按照一定的技术要求,将若干零件装成一个组件,或部件,或将若干零件部件装成一个机械的工艺过程。
机械产品的质量必须由装配来保证。
在装配前必须熟悉和研究图纸,了解产品的结构,零件的作用以及相互间的联接关系,确定装配的方法顺序,准备所需的工具,对零件进行清理和清洗,对某些零件进行修配,或做一些验证性工作,如密封性试验,关键零部件试装,测量等工作。
为保证装配的精度,常用以下方法进行装配。
1、互换法在装配时各配合零件不经修配,选择或调整即可达到装配精度的方法,其特点是装配简单,生产率高,便于组织流水作业,维修更换零件方便,但是对零件的加工精度要求是比较高的。
2、调整法在装配时,根据装配实际的需要改变产品中可调整零件的相对位置或选用合适的调整,以达到装配精度的方法。
3、分组法在成批或大量生产中,将产品各配合的零部件按实测尺寸分组,然后按相应的分组分别进行装配,在相应的组进行装配时,无需再选择别的装配方法。
其特点是:经分组后再装配提高了装配精度,降低了成本。
4、修配法在装配时,根据装配的实际需要,在某一零件上预留少量修配量,以达到装配精度的方法,适用单件,小批量生产。
装配应注意的事项:1、在装配前,要对装配的零部件用柴油,煤油或汽油进行清洗,并擦拭干净。
2、在相配合的表面,在配合前一般需加润滑剂。
3、要注意检查零件配合尺寸是否准确。
4、做到边装配边检查,每装完一部分就要检查是否符合要求。
5、在试车时要做好各项检查,符合试车条件,才能进行试运行。
二、固定连接的装配知识1、螺纹连接:螺纹连接是一种可拆的固定连接,具有结构简单,连接可靠,拆装方便的优点。
(1)、螺纹连接的预紧螺纹连接的目的是为了紧固可靠,必须保证螺纹之间具有一定的摩擦力矩,是有旋加拧紧力矩后产生的,也就是螺纹之间产生了一定的预紧力,这个力矩一般由装配者按经验控制,重要连接由设计确定。
(2)、螺纹连接的装配与防松一般旋紧后,再用扳手按顺序分2-3次旋紧,法兰端盖等螺纹应按对角轮流旋紧。
机械零部件的装配

机械零部件的装配
一、装配的一般工艺原则 (1)过渡配合和过盈配合零件的装配。 (2)标准件及配合表面的装配。 (3)摩擦表面及密封垫的装配。 (4)零件有某些装配技术要求,如装配间隙、灵
活度、啮合印痕等,应边安装边检查,并随时进行 调整。 (5)装配完毕后进行试运行。 二、常用的装配工艺 常用的装配工艺有清洗、平衡、刮削、螺纹联接、 过盈配合联接、胶接、校正等。此外,还可应用其 他装配工艺,如焊接、铆接、滚边、压圈和浇铸连 接等,以满足各种不同产品结构的需要。
4.滚动轴承的装配 轴承在装配时,应控制和调整适当的游隙,以保证正常
工作并延长轴承使用寿命。不可分离型轴承(如向心球轴 承等)应按座圈配合松紧程度决定其安装顺序。
5.带轮的装配 圆锥轴配合的带轮的装配:将键装在轴上→装入带轮
(键槽对准键)→拧紧轴向固定螺钉;直轴配合的皮带轮 的装配:将键装在轴上→压入带轮(键槽对准键)→用专 用工具或用木锤敲打→拧紧轴向固定螺钉。
谢谢观看!
机械零部件Leabharlann 装配三、典型零部件的装配工艺 1.键联接的装配 1)松键联接的装配要点 2)楔键联接的装配要点 3)花键联接的装配要点
机械零部件的装配
2.螺纹联接件的装配
机械零部件的装配
3.过盈配合联接的装配 过盈配合主要适用于受冲击载荷零件的联接以及拆卸较
少的零件联接。装配方法主要是采用压力机压入装配和温 差法装配。
机械装配零件标准规范

机械装配零件标准规范1. 引言本文档旨在规范机械装配零件的标准,以确保装配过程的准确性和安全性。
通过遵循这些规范,可以提高装配效率并降低故障率。
2. 材料要求(1)装配零件应使用符合相关标准的高质量材料,以保证零件的耐久性和可靠性。
(2)各种零件的材料要求应根据其特性和用途进行选择,确保其能够承受相应的负荷和压力。
3. 尺寸和公差(1)装配零件的尺寸应符合设计要求,确保与其他零件的配合准确。
(2)适当的公差应考虑到装配过程中的热胀冷缩和其他因素,以保证零件之间的配合和功能的正常运行。
4. 表面处理(1)装配零件的表面处理应符合相关要求,确保零件表面的平整度和光洁度。
(2)适当的表面处理还可以提高零件的耐腐蚀性和抗磨损性能。
5. 装配要求(1)装配过程中应遵循相关的装配顺序,确保零件的正确装配。
(2)装配零件之间的配合应牢固可靠,避免出现松动或连接不牢固的情况。
(3)装配过程中需要注意的特殊要求应根据具体情况进行说明。
6. 质量控制(1)装配零件的质量应进行严格控制,确保零件符合相关标准和要求。
(2)相关质检人员应进行必要的检测和测试,以确保零件的质量和性能。
7. 安全要求(1)在进行机械装配过程中,应注重安全操作,做好相关的防护措施。
(2)保证操作人员的安全教育和培训,使其了解相关安全要求和操作规程。
8. 故障排除(1)在出现装配故障时,应及时进行故障排查,找出问题的原因并进行修复。
(2)故障排除过程中,应记录相关信息并保留相应的故障样品以便进一步分析。
9. 总结机械装配零件标准规范对于确保装配质量和效率起到了重要的指导作用。
通过遵循这些规范,可以降低故障率,提高装配效率,并确保装配过程的安全性。
以上为机械装配零件标准规范的主要内容,具体细节和补充要求请根据具体情况进行进一步制定和完善。
机械装配知识点总结
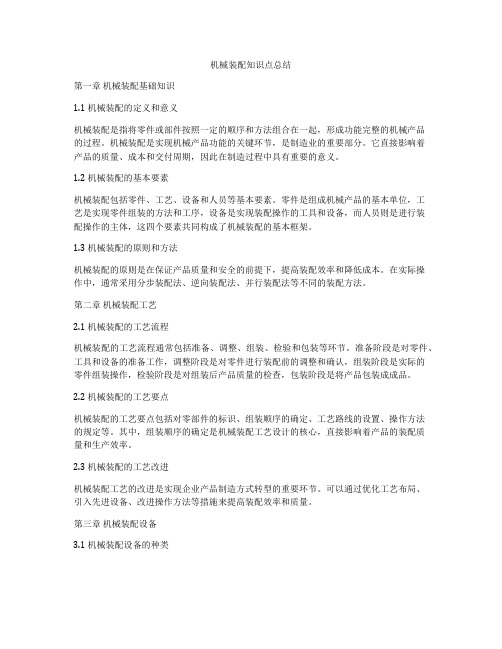
机械装配知识点总结第一章机械装配基础知识1.1 机械装配的定义和意义机械装配是指将零件或部件按照一定的顺序和方法组合在一起,形成功能完整的机械产品的过程。
机械装配是实现机械产品功能的关键环节,是制造业的重要部分。
它直接影响着产品的质量、成本和交付周期,因此在制造过程中具有重要的意义。
1.2 机械装配的基本要素机械装配包括零件、工艺、设备和人员等基本要素。
零件是组成机械产品的基本单位,工艺是实现零件组装的方法和工序,设备是实现装配操作的工具和设备,而人员则是进行装配操作的主体,这四个要素共同构成了机械装配的基本框架。
1.3 机械装配的原则和方法机械装配的原则是在保证产品质量和安全的前提下,提高装配效率和降低成本。
在实际操作中,通常采用分步装配法、逆向装配法、并行装配法等不同的装配方法。
第二章机械装配工艺2.1 机械装配的工艺流程机械装配的工艺流程通常包括准备、调整、组装、检验和包装等环节。
准备阶段是对零件、工具和设备的准备工作,调整阶段是对零件进行装配前的调整和确认,组装阶段是实际的零件组装操作,检验阶段是对组装后产品质量的检查,包装阶段是将产品包装成成品。
2.2 机械装配的工艺要点机械装配的工艺要点包括对零部件的标识、组装顺序的确定、工艺路线的设置、操作方法的规定等。
其中,组装顺序的确定是机械装配工艺设计的核心,直接影响着产品的装配质量和生产效率。
2.3 机械装配的工艺改进机械装配工艺的改进是实现企业产品制造方式转型的重要环节。
可以通过优化工艺布局、引入先进设备、改进操作方法等措施来提高装配效率和质量。
第三章机械装配设备3.1 机械装配设备的种类机械装配设备包括手工装配工具、通用装配设备、自动化装配设备等不同种类。
手工装配工具是适用于小批量和多品种生产的装配工具,通用装配设备适用于中小型企业大批量生产,而自动化装配设备适用于大规模生产和高精度要求的产品。
3.2 机械装配设备的选型原则机械装配设备的选型原则主要包括适应性、稳定性、灵活性和成本等因素。
机械装配工艺标准

机械装配工艺标准
机械装配工艺标准:机械装配工艺标准规范机械结构件装配工艺标准机械结构装配施工工艺标准1适用范围本工艺适用于公司产品机械结构件装配加工的过程,本标准规定了一般机械结构,比如孔轴配合,螺丝、螺栓连接等等装配要求。
本标准适用于机械产品的装配。
2引用标准
(1)JBT5994机械装配基础装配要求
(2)GB5226机床电气设备通用技术条件
(3)GB6557挠性转子的机械平衡
(4)GB6558挠性转子的平衡评定准则
(5)GB7932气动系统通用技术条件
(6)GB7935液压元件通用技术条件
(7)GB9239刚性转子品质许用不平衡的确定
(8)GB10089圆柱蜗杆蜗轮精度
(9)GB10095渐开线圆柱齿轮精度
(10)GB10096齿条精度
(11)GB11365锥齿轮和准双曲面齿轮精度
(12)GB11368齿轮传动装置清洁度3机械装配专业术语3.1.1工艺使各种原材料、半成品成为产品的方法和过程。
- 1、下载文档前请自行甄别文档内容的完整性,平台不提供额外的编辑、内容补充、找答案等附加服务。
- 2、"仅部分预览"的文档,不可在线预览部分如存在完整性等问题,可反馈申请退款(可完整预览的文档不适用该条件!)。
- 3、如文档侵犯您的权益,请联系客服反馈,我们会尽快为您处理(人工客服工作时间:9:00-18:30)。
机械装配标准与方法第一节零部件的清洗一、装配前应了解设备的结构、装配技术和工艺要求。
对需要装配的零、部件配合尺寸、相关精度、配合面、滑动面应进行复查和清洗处理,并应按照标记及装配顺序进行装配。
二、清洗设备及装配件表面的防锈油脂,宜采用下列方法:1、对设备及大、中型部件的局部清洗,宜采用现行国家标准《溶剂油》、《航空洗涤汽油》、《轻柴油》、乙醇和金属清洗剂进行擦洗和涮洗;金属清洗剂应符合本规范附录十一的规定。
2、对中、小型状较复杂的装配件,可采用相应的清洗液浸泡、浸洗时间随清洗液的性质、温度和装配件的要求确定,宜为2-20min,且宜采用多步清洗法或浸、涮结合清洗;采用加热浸洗时,应控制清洗液温度;被清洗件不得接触容器壁。
3、对形状复杂、污垢粘附严重的装配件宜采用溶剂油、蒸汽、热空气、金属清洗剂和三氯乙烯等清洗液进行喷洗;对精密零件、滚动轴承等不得用喷洗法。
4、当对装配件进行最后清洗时,宜采用超声波装置,并宜采用溶剂油、清洗汽油、轻柴油、金属清洗剂和三氯乙烯等进行超声波清洗。
5、对形状复杂、油垢粘附严重、清洗要求高的装配件,宜采用溶剂油、清洗汽油、轻柴油、金属清洗剂、三氯乙烯和碱液等进行一喷联合清洗。
三、设备加工表面上的防锈漆,应采用相应的稀释剂或脱漆剂等溶剂进行清洗。
四、设备零、部件经清洗后,应立即进行干燥处理,并应采取防返锈措施。
五、设备组装时,一般固定结合面组装后,应用0.05mm塞尺检查,插入深度应小于0.2mm移动长度应小于检验长度的1/10;重要的固定结合面紧固后,用0.04mm塞尺检查,不得插入;特别重要的固定结合面,紧固前后均不得插入。
六、带有内腔的设备或部件在封闭前,应仔细检查和清理,其内部不得有任何异物。
七、对安装后不易拆卸、检查、修理的油箱或水箱、装配前应作渗漏和气密检查。
第二节螺栓、键、定位销的装配一、装配螺栓时,应符合下列要求:1、紧固时,宜采用呆扳手,不得使用打击法和超过螺栓许用应力。
2、螺栓头、螺母与被连接件的接触应紧密,对接触面积和接触间隙有特殊要求的,尚应按技术规定要求进行检验。
3、有预紧力要求的连接应按装配规定的预紧力进行预紧,可选用机械、液压拉伸法和加热法;钢制螺栓加热温度不得超过400℃。
4、螺栓与螺母拧紧后,螺栓应露出螺母2-4个螺距;沉头螺钉拧紧后,钉头应埋入机件内,不得外露。
5、有锁紧要求的,拧紧后应按其技术规定锁紧;用双螺母锁紧时,薄螺母应装在厚螺母之下;每个螺母下面不得用2个相同垫圈。
二、不锈钢、铜、铝等材质的螺栓装配时,应在螺纹部分涂抹润滑剂。
三、有预紧力要求的螺栓连接,其预紧力可采用下列方法测定:1、应利用专门装配工具中的扭力扳手、电动或气动扳手等,直接测得数值。
2、测量螺栓拧紧后伸长的长度Lm(图1)应按下式计算:Lm=Ls+P0/C L式中Lm—螺栓伸长后的长度(mm);Ls —螺栓与被连接间隙为零时的原始长度(mm);P0 —预紧力为设计或技术文件中要求的值(N)C L —螺栓刚度,可按本规范附录十四的规定计算。
图1 伸长后的螺栓四、装配精制螺栓和高强度螺栓前,应按设计要求检验螺孔直径的尺寸和加工精度。
五、高强螺栓在装配前,应按设计要求检查和处理被连接件的结合面;装配时,结合面应干燥,不得在雨中装配。
六、高强螺栓及其紧固件应配套使用。
旋紧时,应分两次拧紧,初拧扭距值不得小于终拧扭距值的30%;终拧扭距值应符合设计要求,并按下式计算:M=K(P+△P)·d式中M—终拧扭距值(N·m);P—设计预拉力(KN);△P—预紧力损失值,宜为预拉力值的5%—10%(KN);K—扭距系数,可取—;d—螺栓公称直径(mm)七、装配扭剪型高强螺栓应分两次拧紧,直至将尾部卡头拧掉为止,其终拧扭距可不进行核算。
八、现场配制的各种类型的键,均符合国家现行标准《装配通用技术条件》规定的尺寸和精度。
键用型钢的抗拉强度不应小于588N/mm2。
九、键的装配应符合下列要求:1、键的表面应无裂纹、浮锈、凹痕、条痕及毛刺,键和键槽的表面粗糙度、平面度和尺寸在装配前均应检验。
2、普通平键、导向键、薄型平键和半圆键,两个侧面与键槽应紧密接触,与轮毂键槽底面不接触。
3、普通楔键和钩头楔键的上、下面应与轴和轮毂的键槽底面紧密接触。
5、切向键的两斜面间以及键的侧面与轴和轮毂键槽的工作面间,均应紧密接触;装配后,相互位置应采用销固定。
十、销的装配应符合下列要求:1、检查销的型式和规格,应符合设计及设备技术文件的规定。
2、有关连接机件及其几何精度经调整符合要求后,方可装销。
3、装配销时不宜使销承受载荷,根据销的性质,宜选择相应的方法装入;销孔的位置应正确。
4、对定位精度要求高的销和销孔,装配前检查其接触面积,应符合设备技术文件的规定;当无规定时,宜采用其总接触面积的50%-75%。
5、装配中,当发现销和销孔不符合要求时,应铰孔,另配新销;对定位精度要求高的,应在设备的几何精度符合要求或空运转实验合格后进行。
第三节联轴器装配一、凸缘联轴器(图2)装配时,两个半联轴器端面应紧密接触,两轴心的径向位移不应大于0.03mm。
图2 凸缘联轴器二、弹性套柱销联轴器(图3)装配时,两轴心径向位移、两轴线倾斜和端面间隙的允许偏差应符合表1的规定。
图3 弹性套柱销联轴器弹性套柱销联轴器装配允许偏差表1联轴器外形最大尺寸D (mm)两轴心径向位移(mm)两轴线倾斜端面间隙s(mm)7110002~480951061303~51601902244~62503154004755~7600三、弹性柱销联轴器(图4)装配时,两轴心径向位移、两轴线倾斜和端面间隙的允许偏差应符合表2规定。
图4 弹性柱销联轴器弹性柱销联轴器装配允许偏差表2联轴器外形最大直径D (mm)两轴心径向位移(mm)两轴线倾斜端面间隙s (mm)90~16010002~3 195~200~4280~3203~5360~4104~64805~75406~8630四、 弹性销轴齿式联轴器(图5)装配时,两轴心径向位移、两轴线倾斜和端面间隙的允许偏差应符合表3的规定。
图5 弹性柱销目齿式联轴器 弹性柱销齿式联轴器装配允许偏差 表3联轴器外形最大直径D(mm )两轴心径向位移(mm )两轴线倾斜端面间隙s (mm )78~118 1000158~260 4~5 300~515 6~8 560~770 10 860~1158 13~15 1440~164018~20五、 齿式联轴器(图6)装配时应符合下列要求:1、装配时两轴心径向位移、两轴线倾斜和端面间隙的允许偏差应符合表4规定。
2、联轴器的内、外齿的啮合应良好,并在油浴内工作,其中小扭距、低转速的应选用符合国家现行标准《锂基润滑脂》的ZL -4润滑脂,大扭距、高转速的应选用符合国家现行标准《齿轮油》的HL20、HL30润滑油,并不得有漏油现象。
图6 齿式联轴器齿式联轴器装配允许偏差表4联轴器外形最大直径D(mm)两轴心径向位移(mm)两轴线倾斜端面间隙s (mm)170~18510002~4 220~250290~43010005~7 490~5901000680~7807~10六、梅花形弹性联轴器(图7装配时,两轴心径向位移、两轴线倾斜和端面间隙的允许偏差应符合表5的规定。
图7 梅花形弹性联轴器梅花形弹性联轴器装配允许偏差表5联轴器外形最大直径D(mm)两轴心径向位移(mm)两轴线倾斜端面间隙s (mm)501/10002~470~105125~1703~6200~2302606~8300~40010007~9七、当测量联轴器端面间隙时,应使两轴窜动到端面间隙为最小尺寸的位置。
第四节制动器装配一、盘式制动器装配应符合下列要求:1、制动盘的端面跳动不应大于0.5mm。
2、同一副制动器两闸瓦工作面的平行度不应大于0.5mm。
3、同一副制动器的支架端面与制动盘中心线平面间距离h(图8)的允许偏差为±0.5mm;制动器支架端面与制动盘中心平面的平行度不得大于0.2mm。
4、闸瓦与制动盘的间隙应均匀,其值宜为1mm。
5、各制动器制动缸的对称中心与主轴轴心在铅垂面内的重和度△值不应大于3mm。
(图9)图8 盘式制动器支架1-支架;2-筒体;3-闸瓦;4-制动盘中心面;5-制动盘图9 盘式制动器二、瓦块式制动器装配时,应符合下列要求:1、制动器各销轴应在装配前清洗洁净,油孔应畅通;装配后应转动灵活,无阻滞现象。
2、同一制动轮的两闸瓦中心应在同一平面内,其允许偏差不得大于2mm。
3、闸座各销轴轴线与主轴轴线的铅垂面M-M间的水平距离b的允许偏差为±1mm。
4、闸座各销轴轴线与主轴轴线水平面N-N的垂直距离h的允许偏差为±1mm。
5、闸瓦铆钉应低于闸皮表面2mm;制动梁与挡绳板不应相碰,其间隙c 值应小于5mm。
6、松开闸瓦时,制动器的闸瓦间隙s应均匀,且不应大于2mm。
7、制动时,闸瓦与制动轮接触良好、平稳;各闸瓦在长度和宽度方向与制动轮接触不得小于80%。
8、油压或气压制动时,达到额定压力后,在10min内压力降不应大于。
图10 瓦块制动器1—闸瓦;2—制动轮;3—制动梁;4—卷筒三、带式制动器(图11)各连接销轴应灵活,无卡住现象;摩擦内衬与钢带铆接应牢固,不得松动。
铆钉头应埋于内衬内,其铆钉头与内衬表面的距离不得小于1mm;制动带退距ε值应按表6选取。
图11 带式制动器带式制动器退距ε值表6制动轮直径D(mm)制动带退距ε(mm)100~2003001400~500~600~800第五节具有过盈的配合件装配一、在常温下装配时应将配合面清洗洁净,并涂一薄层不含二硫化钼添加剂的润滑油;装入时用力应均匀,不得直接打击装配件。
二、纵向过盈连结的装配宜采用压装法。
压装设备的压力,宜为压入力的-倍;压入或压出速度不宜大于5㎜/s。
压入后24h内,不得承受负载。
压入力可按下列公式计算:Pxi= Pfmax·π·df·Lf·μ式中Ca、Ci——系数,由现行国家标准《公差与配合过盈配合计算和选用》GB5371-85表4中查得;Qa——包容件直径比;Pxi——压入力(N);Pfmax——最大结合力(N);df——结合直径(mm);Lf——结合长度(mm);μ——摩擦系数qi——被包容件直径比;va——包容件泊松比;vi——被包容件泊松比——最大过盈量(mm);Ea——包容件弹性模量;Ei——被包容件弹性模量;三、用液压充油法装配配合件时,应先按技术要求检查配合面的表面粗糙度。
当无规定时,其粗糙答应在-μm之间。
对油沟、棱边应刮修倒圆。
四、横向过盈连结的装配宜采用温差法,并应符合下列要求:1、加热包容件时,加热应均匀,不得产生局部过热。