影响锻件质量主要因素
模锻件开裂原因

模锻件开裂原因模锻件开裂的背景和重要性模锻是一种重要的金属成形工艺,广泛应用于航空、汽车、船舶等领域。
然而,模锻件在生产过程中常常会出现开裂问题,这给工业生产带来了严重的经济损失和安全隐患。
因此,了解模锻件开裂的原因及其防范措施对于提高生产质量、降低生产成本具有重要的意义。
模锻件开裂的常见原因1. 材料因素模锻件开裂的一个主要原因是材料的性能不合理或材料质量不达标。
材料的选择应考虑到其热处理能力、塑性变形能力以及抗疲劳性能等。
如果材料的塑性变形能力不足,容易导致应力集中和应力过高,从而引发开裂。
此外,材料中的夹杂物和非金属夹杂物也会导致开裂,因为它们会成为内部的应力集中点。
2. 工艺因素工艺因素是模锻件开裂的主要原因之一。
不正确的锻造温度、锻造速度、锻造压力等参数都会导致模锻件的开裂。
过高的锻造温度和不足的锻造速度会导致过大的变形应力,从而引发开裂。
此外,如果锻造模具的形状和尺寸不合理,也容易导致开裂。
3. 模具设计因素模具设计是模锻件开裂的另一个重要因素。
模具的结构、尺寸以及表面处理对于模锻件的质量和开裂情况起着至关重要的作用。
如果模具的孔径设计过小或者过大,都会导致模锻件的应力不均匀,从而引发开裂。
另外,模具表面的磨损和腐蚀也会对模锻件的质量产生不利影响。
模锻件开裂的防范措施1. 合理选择材料在模锻件的生产过程中,应根据不同的要求选择合适的材料。
材料应具有足够的塑性变形能力和抗疲劳性能,以减少开裂的风险。
同时,应控制材料中的夹杂物和非金属夹杂物的含量,以避免其成为内部应力的集中点。
2. 优化工艺参数合理的工艺参数对于减少模锻件的开裂问题至关重要。
应选择适当的锻造温度、锻造速度和锻造压力,以保证模锻件的变形应力处于可控范围内。
此外,应根据模具的实际情况进行参数的调整和优化,确保模锻件的成形质量。
3. 合理设计模具模具的设计直接影响着模锻件的质量和开裂情况。
应根据模锻件的形状和尺寸合理设计模具,避免模具孔径过小或过大造成应力的集中。
机械制造工艺基础判断题(精)

1.×砂型制作好后必须经烘干才能进行浇注。
2.√ 模样和芯盒是用来制造铸型型腔和型芯的工艺装备。
3.√ 铸型的分型面就是模样的分型面。
4。
√提高型砂和型芯的可塑性,可以减轻铸件冷却收缩时的内应力。
5.√ 一般情况下,直浇道截面应大于横浇道截面,横浇道截面应大于内浇道截面。
6.×冒口的作用是保证浇注时多浇的熔融金属能顺利地溢出。
7.×铸型浇注后应尽快进行落砂,以缩短生产周期。
8.√ 铸件凝固过程中如果补缩不良会引起铸件产生缩孔缺陷。
9.√ 离心铸造主要用于铸造空心回转体铸体。
10.√ 有箱造型时,砂箱是铸型的组成部分。
11.×为提高金属的塑性和降低锻造时的变形抗力,始锻温度越高越好。
12.×为延长锻造时间,减少锻造过程中的加热次数,中锻温度应选的越低越好。
13.√ 金属的塑性越好,其可锻性越好。
14.√ 适当提高金属坯料的加热速度,可降低塑料的烧损和钢材表面的脱碳。
15.√ 坯料在加热过程中受热是否均匀是影响锻件质量的重要因素。
16.×锻件坑冷的冷却速度较灰沙冷的冷却速度慢。
17.×自由锻的扩孔锻造是增大毛坯的内径和减少坯料的外径,从而减小空心毛坯壁厚的一种锻造方法。
18.×空气锤和水压机的吨位是以落下部分的质量来表示的。
19.√ 自由锻产生裂纹缺陷的原因主要是坯料材质不好、加热不充分、锻造温度过低和锻件冷却不当等。
20.√ 胎膜锻时,通常先用自由锻制坯,然后再在胎膜中终端成形。
21.√落料和冲孔都是使板料的一部分与另一部分分离的冲裁方法。
22.×弯形时产生回弹的原因是由于外载荷消失后材料的塑性变形与弹性变形恢复。
23. 电弧焊和气焊都属于熔焊,焊接时使待焊处的母材金属融化并形成焊缝。
24. 压焊是焊接过程中必须对焊件施加压力和加热的焊接方法。
25. 是用直流电焊接时,电弧阳极区的温度高于电弧阴极区的温度,因此必须将焊件接电源正极,焊条接电源负极。
锻件质量控制
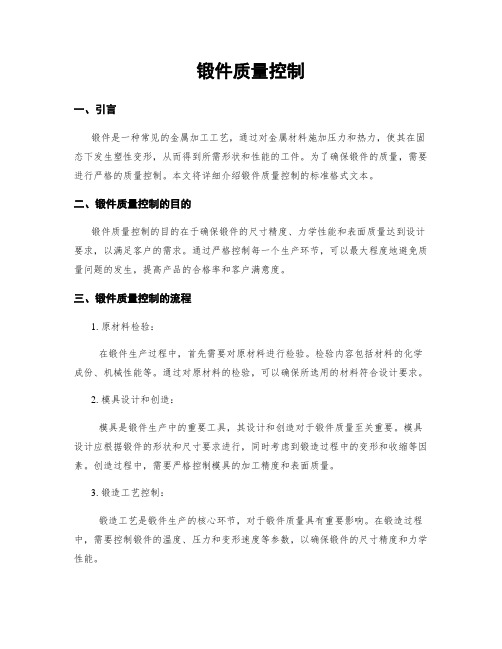
锻件质量控制一、引言锻件是一种常见的金属加工工艺,通过对金属材料施加压力和热力,使其在固态下发生塑性变形,从而得到所需形状和性能的工件。
为了确保锻件的质量,需要进行严格的质量控制。
本文将详细介绍锻件质量控制的标准格式文本。
二、锻件质量控制的目的锻件质量控制的目的在于确保锻件的尺寸精度、力学性能和表面质量达到设计要求,以满足客户的需求。
通过严格控制每一个生产环节,可以最大程度地避免质量问题的发生,提高产品的合格率和客户满意度。
三、锻件质量控制的流程1. 原材料检验:在锻件生产过程中,首先需要对原材料进行检验。
检验内容包括材料的化学成份、机械性能等。
通过对原材料的检验,可以确保所选用的材料符合设计要求。
2. 模具设计和创造:模具是锻件生产中的重要工具,其设计和创造对于锻件质量至关重要。
模具设计应根据锻件的形状和尺寸要求进行,同时考虑到锻造过程中的变形和收缩等因素。
创造过程中,需要严格控制模具的加工精度和表面质量。
3. 锻造工艺控制:锻造工艺是锻件生产的核心环节,对于锻件质量具有重要影响。
在锻造过程中,需要控制锻件的温度、压力和变形速度等参数,以确保锻件的尺寸精度和力学性能。
4. 热处理:锻件在锻造后需要进行热处理,以改善其力学性能和组织结构。
热处理过程中,需要控制加热温度、保温时间和冷却速度等参数,以确保锻件的硬度、强度和韧性等性能指标符合要求。
5. 机械加工:锻件在热处理后需要进行机械加工,以达到最终的尺寸和表面质量要求。
机械加工过程中,需要控制加工精度、刀具磨损情况和切削液的使用等因素,以确保锻件的尺寸精度和表面质量。
6. 检验和测试:在锻件生产的每一个环节中,都需要进行严格的检验和测试。
包括尺寸检验、力学性能测试、表面质量检查等。
通过检验和测试,可以及时发现问题并采取纠正措施,以确保锻件的质量。
7. 记录和分析:每一个生产环节的数据和结果都需要进行记录和分析。
通过对数据和结果的分析,可以找出潜在的问题和改进的空间,为提高锻件质量提供依据。
锻件质量控制

锻件质量控制引言概述:锻件作为一种重要的金属加工工艺,广泛应用于航空、汽车、机械等行业。
然而,由于锻件制造过程中存在一系列的复杂因素,如材料性能、工艺参数等,导致锻件质量控制成为一个关键的问题。
本文将从五个方面详细阐述锻件质量控制的重要性和方法。
一、材料选择1.1 材料性能要求:锻件的质量控制首先要从材料选择入手。
根据锻件的使用环境和要求,选择合适的材料。
考虑材料的强度、韧性、耐磨性等特性,确保锻件在使用过程中能够满足要求。
1.2 材料检测方法:采用适当的材料检测方法,如化学成分分析、金相分析、硬度测试等,对原材料进行严格检验,以确保材料的质量符合要求。
1.3 材料热处理:根据锻件的材料和使用要求,进行适当的热处理,如退火、正火、淬火等,以提高材料的力学性能和组织结构,从而提高锻件的质量。
二、工艺参数控制2.1 温度控制:锻件的温度是影响锻件质量的重要因素之一。
在锻造过程中,要控制好锻件的加热温度和保温时间,避免温度过高或过低导致材料的结构破坏或质量问题。
2.2 压力控制:锻造过程中的锻压力度对于锻件的成形和质量控制至关重要。
要根据锻件的形状和材料的特性,合理控制锻压力度,避免过大或过小导致锻件的变形或裂纹等问题。
2.3 冷却控制:锻件的冷却过程也是影响锻件质量的重要因素。
要根据锻件的材料和形状,合理选择冷却介质和冷却速度,避免锻件的变形和内部应力过大,保证锻件的质量。
三、工艺检测3.1 尺寸检测:通过测量锻件的尺寸,判断锻件的成形是否符合要求。
可以采用三坐标测量仪、投影仪等设备进行尺寸检测,确保锻件的几何形状和尺寸精度符合设计要求。
3.2 缺陷检测:通过无损检测方法,如超声波检测、磁粉检测等,对锻件进行缺陷检测,如裂纹、气孔等。
及时发现并修复锻件的缺陷,以提高锻件的质量。
3.3 组织检测:通过金相显微镜等设备,对锻件的金相组织进行观察和分析,判断锻件的组织结构是否均匀、致密,以及是否存在晶粒长大等问题,确保锻件的组织质量符合要求。
42CrMo锻件开裂原因分析与对策

42CrMo锻件开裂原因分析与对策42CrMo材料是作为减速机结构件的一个重要钢种,对于用这种钢材制造的零部件,要求有强度和韧性良好配合的综合机械性能。
由于目前设备、材料及工艺技术操作难于掌握,调质过程中容易使某些零件产生开裂事故,而这些零件与其他零件相比有其明显的特点,只有充分掌握了这些特点才能得到满意的结果。
通常来说,影响锻件调质处理质量的主要因素包括:(1)成分偏析。
42CrMo钢属于中碳合金结构钢,其原材料常存在带状偏析。
当经过热压力加工(锻、轧)后,仍保留有成分偏析,经860。
C 淬火后将出现B±÷M混合组织,而B上的冲击韧性是很差的,这种偏析可从退火组织中看到。
从42CrM。
带状成分偏析能谱分析结果中可以看到铁素体带中的Mo含量比珠光体带中Mo含量高5~6倍,偏析条纹内某些元素的富集十分严重。
(2)气体和夹杂物。
42CrMo钢尤其是大截面的原材料中不可避免地含有气体和夹杂物,对中碳合金结构钢而言,由于碳和合金元素的偏析,即使残余含氢量在1.5~2.0ppm,也可能导致锻件在偏析处产生开裂。
止匕外,铝元素的存在对钢也有害:在酸性钢中,当铝含量>0.005%时,铝在脱氧时形成了具有锐角的氧化物,会大大降低这种钢的塑性;在碱性钢中,当铝含量>0.1%时,铝在钢中形成了沿晶界分布的氮化铝,使钢的室温塑性降低。
(3)锻造温度。
由于42CrMo钢内部有偏析,当42CrMo钢在氧化性气氛中加热接近固相线如42CrMo钢始锻温度在1200~1220o C z在此高温持续时间过长就容易产生析出物或杂质等,偏析的晶界因熔点低就有可能开始熔化,氧通过熔化了的晶界侵入并在晶界上形成氧化物,这样会产生局部过烧,形成随后热加工中的重大缺陷之一。
(4)锻造比。
当锻造比不足,工件中心变形小,偏析和钢锭原铸态组织仍局部保留,常见的就是钢材的偏析、疏松、微孔等缺陷,粗晶也是最常见的缺陷。
锻比过大,机械性能异向性增大,横向机械性能降低较多。
锻件常见缺陷裂纹的原因

锻件常见缺陷裂纹的原因锻件常见缺陷裂纹的原因有很多,主要包括以下几个方面:1. 锻造前材料的缺陷:锻造前原材料中可能存在着各种缺陷,如夹杂物、气孔、夹渣等。
这些缺陷会在锻造过程中被拉长、扭曲或剪切,最终导致锻件出现裂纹。
2. 异常冷却方式:锻件在冷却过程中,如果冷却速度过快或不均匀,会导致锻件内部产生应力集中,从而引发裂纹。
尤其是在大尺寸、复杂形状的锻件中,由于其冷却速度不均匀,容易出现内部裂纹。
3. 冷、热变形不均匀:锻造过程中,如果材料的冷、热变形不均匀,会导致锻件内部应力分布不均匀,从而引发裂纹的产生。
尤其是在复杂形状、壁厚不一的锻件中,易出现材料贫化、过冷区和高应力区,容易引发裂纹。
4. 锻造温度过低或过高:锻造温度是影响锻件质量的关键因素之一。
如果温度过低,会导致材料的硬化能力不足,易发生塑性变形困难,从而引发裂纹;而温度过高,则会导致材料的焊接性能下降,也容易引发裂纹。
5. 压力不均匀:锻造过程中,如果锻压力不均匀,会使锻件中的应力分布不均匀,从而容易产生应力集中和裂纹。
尤其是在薄壁锻件中,容易出现锻压力不均匀的问题,导致裂纹的发生。
6. 锻件设计不合理:锻件的设计是影响锻件质量的重要因素之一。
如果锻件的形状、结构设计不合理,容易导致应力集中,从而引发裂纹的产生。
尤其是在复杂形状、尺寸大的锻件中,设计不合理会增加裂纹发生的概率。
7. 热处理不当:热处理是锻件制造过程中的关键环节,如果热处理不当,会导致锻件中的应力不释放或释放不充分,从而引发裂纹。
此外,热处理时的温度、时间等参数也需要合适,否则也可能导致裂纹的产生。
这些都是导致锻件常见缺陷裂纹的主要原因。
为了降低或避免裂纹的产生,需要从原材料选用、工艺控制、设备维护等方面做好控制和管理。
同时,制定合理的锻造工艺和热处理工艺,合理设计锻件形状和结构,对裂纹的产生起到有力的控制和避免作用。
还需要加强工作人员的培训和技能提升,提高他们的专业水平和质量意识,从而减少裂纹缺陷的发生,提高锻件的质量。
40crni2mo 锻件标准

【40CrNi2Mo 锻件标准:全面解析】1. 40CrNi2Mo 锻件概述40CrNi2Mo 锻件是一种常见的合金钢锻件,具有优良的耐磨性、高强度和耐腐蚀性能。
它通常用于制造机械零部件、轴承、齿轮等重要零件,在工业领域具有广泛的应用。
2. 40CrNi2Mo 锻件的化学成分和机械性能40CrNi2Mo 锻件的化学成分中含有适量的铬、镍和钼等合金元素,这些元素能够提高锻件的硬度和耐磨性。
它的机械性能表现出很高的强度和韧性,满足了工程上的使用要求。
3. 40CrNi2Mo 锻件的热处理工艺热处理是影响40CrNi2Mo 锻件性能的重要因素之一。
通常采用的热处理工艺包括淬火、回火等,通过调整热处理工艺参数,可以使锻件达到理想的组织结构和性能。
4. 40CrNi2Mo 锻件的标准40CrNi2Mo 锻件的生产和质量检验需要符合相应的标准和规范。
国内外对于40CrNi2Mo 锻件的标准主要包括国家标准、行业标准和国际标准等,其中包括了化学成分、机械性能、热处理工艺、检测方法等方面的要求。
5. 40CrNi2Mo 锻件的应用领域由于40CrNi2Mo 锻件具有优秀的性能和可加工性,因此在航空航天、汽车制造、机械制造等领域得到广泛应用。
在航空发动机、重型机械设备、高速列车等领域都有40CrNi2Mo 锻件的身影。
总结回顾:40CrNi2Mo 锻件作为一种重要的合金钢锻件,在工业生产中具有重要的地位和作用。
其优秀的机械性能和热处理工艺使得它在各个领域都得到了广泛应用。
在未来的发展中,随着工业技术的不断进步,相信40CrNi2Mo 锻件将会展现出更多的潜力和机遇。
个人观点和理解:对于40CrNi2Mo 锻件来说,我个人认为其在工业生产中的作用非常重要,尤其是在一些特殊领域的应用。
对于其标准化和质量控制也需要不断加强,以确保其稳定的质量和性能。
以上就是对40CrNi2Mo 锻件的全面解析,希望能对你有所帮助。
40CrNi2Mo 锻件作为一种重要的合金钢锻件,在工业生产中具有重要的地位和作用。
锻件重量计算公式

锻件重量计算公式锻件是一种常见的金属制品,通常用于制造机械零件、汽车零件、航空航天零件等。
在生产过程中,需要对锻件的重量进行准确计算,以便确定原材料的用量和成本,并且保证产品质量。
本文将介绍锻件重量的计算公式及其应用。
一、锻件重量计算公式。
锻件的重量计算公式一般是根据其形状和材料密度来确定的。
常见的锻件形状包括圆柱形、方柱形、圆盘形等,不同形状的锻件重量计算公式也不同。
以下是常见的几种锻件重量计算公式:1. 圆柱形锻件重量计算公式:圆柱形锻件的重量可以通过以下公式来计算:重量(kg)= π r^2 h ρ。
其中,r为锻件底部半径,h为锻件高度,ρ为材料密度。
2. 方柱形锻件重量计算公式:方柱形锻件的重量可以通过以下公式来计算:重量(kg)= l w h ρ。
其中,l为锻件长度,w为锻件宽度,h为锻件高度,ρ为材料密度。
3. 圆盘形锻件重量计算公式:圆盘形锻件的重量可以通过以下公式来计算:重量(kg)= π r^2 t ρ。
其中,r为锻件底部半径,t为锻件厚度,ρ为材料密度。
以上公式是常见的锻件重量计算公式,通过这些公式可以准确计算出不同形状的锻件的重量。
二、锻件重量计算实例。
为了更好地理解锻件重量计算公式的应用,我们可以通过一个实际的计算实例来进行说明。
假设我们需要计算一个圆柱形锻件的重量,该锻件的底部半径为10cm,高度为20cm,材料密度为7.85g/cm^3。
我们可以按照上述的圆柱形锻件重量计算公式来进行计算:重量(kg)= π 10^2 20 7.85 / 1000 = 123.5kg。
通过以上计算,我们可以得出该圆柱形锻件的重量为123.5kg。
三、锻件重量计算的注意事项。
在进行锻件重量计算时,需要注意以下几点:1. 确定锻件的形状,不同形状的锻件需要使用不同的重量计算公式,因此在进行计算之前需要先确定锻件的形状。
2. 确定材料密度,材料密度是影响锻件重量的重要因素,需要根据实际情况准确确定材料密度。
锻件缺陷的原因及处理

锻件缺陷的主要原因及处理一、原材料的主要缺陷及其引起的锻件缺陷锻造用的原材料为铸锭、轧材、挤材及锻坯。
而轧材、挤材及锻坯分别是铸锭经轧制、挤压及锻造加工成的半成品。
一般情况下,铸锭的内部缺陷或表面缺陷的出现有时是不可避免的。
例如,内部的成分与组织偏析等。
原材料存在的各种缺陷,不仅会影响锻件的成形,而且将影响锻件的最终质量。
根据不完全的统计,在航空工业系统中,导致航空锻件报废的诸多原因中,由于原材料固有缺陷引起的约占一半左右。
因此,千万不可忽视原材料的质量控制工作。
由于原材料的缺陷造成的锻件缺陷通常有:1.表面裂纹表面裂纹多发生在轧制棒材和锻制棒材上,一般呈直线形状,和轧制或锻造的主变形方向一致。
造成这种缺陷的原因很多,例如钢锭内的皮下气泡在轧制时一面沿变形方向伸长,一面暴露到表面上和向内部深处发展。
又如在轧制时,坯料的表面如被划伤,冷却时将造成应力集中,从而可能沿划痕开裂等等。
这种裂纹若在锻造前不去掉,锻造时便可能扩展引起锻件裂纹。
2.折叠折叠形成的原因是当金属坯料在轧制过程中,由于轧辊上的型槽定径不正确,或因型槽磨损面产生的毛刺在轧制时被卷入,形成和材料表面成一定倾角的折缝。
对钢材,折缝内有氧化铁夹杂,四周有脱碳。
折叠若在锻造前不去掉,可能引起锻件折叠或开裂。
3.结疤结疤是在轧材表面局部区域的一层可剥落的薄膜。
结疤的形成是由于浇铸时钢液飞溅而凝结在钢锭表面,轧制时被压成薄膜,贴附在轧材的表面,即为结疤。
锻后锻件经酸洗清理,薄膜将会剥落而成为锻件表面缺陷。
4.层状断口层状断口的特征是其断口或断面与折断了的石板、树皮很相似。
层状断口多发生在合金钢(铬镍钢、铬镍钨钢等),碳钢中也有发现。
这种缺陷的产生是由于钢中存在的非金属夹杂物、枝晶偏析以及气孔疏松等缺陷,在锻、轧过程中沿轧制方向被拉长,使钢材呈片层状。
如果杂质过多,锻造就有分层破裂的危险。
层状断口越严重,钢的塑性、韧性越差,尤其是横向力学性能很低,所以钢材如具有明显的层片状缺陷是不合格的。
ta2锻件加工参数
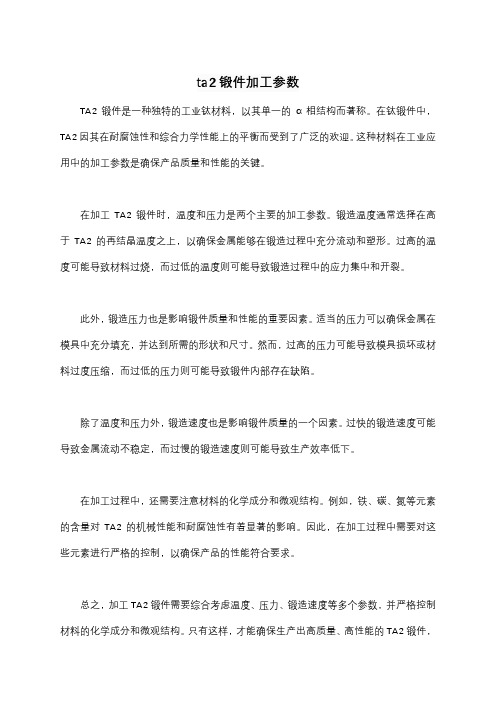
ta2锻件加工参数
TA2锻件是一种独特的工业钛材料,以其单一的α相结构而著称。
在钛锻件中,TA2因其在耐腐蚀性和综合力学性能上的平衡而受到了广泛的欢迎。
这种材料在工业应用中的加工参数是确保产品质量和性能的关键。
在加工TA2锻件时,温度和压力是两个主要的加工参数。
锻造温度通常选择在高于TA2的再结晶温度之上,以确保金属能够在锻造过程中充分流动和塑形。
过高的温度可能导致材料过烧,而过低的温度则可能导致锻造过程中的应力集中和开裂。
此外,锻造压力也是影响锻件质量和性能的重要因素。
适当的压力可以确保金属在模具中充分填充,并达到所需的形状和尺寸。
然而,过高的压力可能导致模具损坏或材料过度压缩,而过低的压力则可能导致锻件内部存在缺陷。
除了温度和压力外,锻造速度也是影响锻件质量的一个因素。
过快的锻造速度可能导致金属流动不稳定,而过慢的锻造速度则可能导致生产效率低下。
在加工过程中,还需要注意材料的化学成分和微观结构。
例如,铁、碳、氮等元素的含量对TA2的机械性能和耐腐蚀性有着显著的影响。
因此,在加工过程中需要对这些元素进行严格的控制,以确保产品的性能符合要求。
总之,加工TA2锻件需要综合考虑温度、压力、锻造速度等多个参数,并严格控制材料的化学成分和微观结构。
只有这样,才能确保生产出高质量、高性能的TA2锻件,
满足各种工业应用的需求。
5CrMnMo钢热锻模热处理工艺
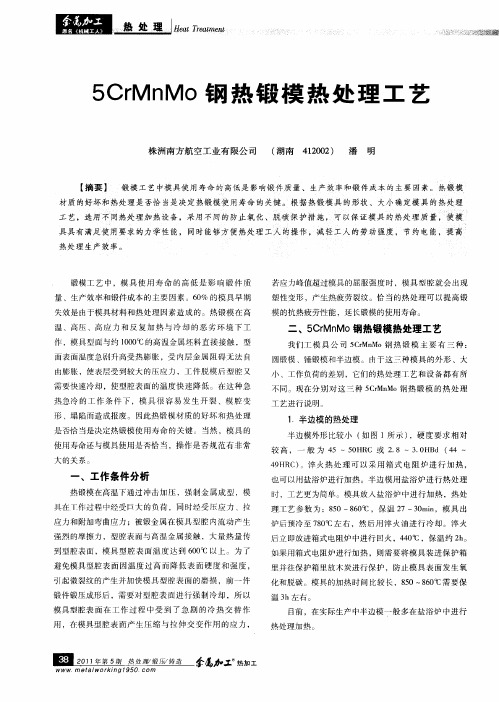
较 高 , 一 般 为 4 ~5 HR 或 2 8 ~ 30 d ( 4 ~ 5 0 C . . HB 4
使用寿命还与模具使用是否恰 当,操作 是否规范 有非 常
大的关系。
一
4 H C 。淬火热 处 理可 以采 用 箱式 电阻炉 进行 加 热 , 9R )
图 l 半边模
3 H C) 5 R 。相 比而 言 ,锤 锻 模 的 体 积 最 大 ,一 般 在 箱 式 球 底 炉 中 进 行 加 热 , 锤 锻 模 的 热 处 理 比 其 他 两 种 更 加 复杂 。
2 .圆锻模的热处理
圆 锻模 外 形 为 圆 柱 彤 ,较 小 的 圆 锻 模 硬 度 要 求 为
也可以用盐浴炉进行加热 。半边模 用盐浴炉进 行热处理 时 ,工 艺更 为简单 。模具放人盐 浴炉 中进行 加热 ,热处 理 T艺 参数 为 :80~80C,保 温 2 5 6 ̄ 7~3 r n 0 i,模 具 出 a
炉后 预 冷 至 7 0 左 右 ,然 后 用 淬 火 油 进 行 冷 却 。 淬 火 8%
、
工作条件分析
热锻模在高温下通过冲击加压 ,强制金属 成型 ,模
具在T作过程中经受巨大的负荷 ,同时经受 压应力 、拉 应力和附加弯曲应 力 ;被锻 金属在模具 型腔 内流 动产生 强烈的摩擦力 ,型腔表 面与高温金属接 触 ,大量 热量传
到 型 腔 表 面 ,模 具 型 腔 表 面 温 度 达 到 60C以上 。 为 了 0 ̄
锻模工 艺 中 ,模具 使 用 寿命 的 高低 是 影 响锻 件 质 量 、生产效率和锻件成本 的主要 因素。6 % 的模具早 期 0 失效是 由于模具材料和热处理 因素造成 的。热锻模在 高 温 、高压 、高 应 力 和反 复加 热 与冷 却 的恶 劣环 境 下 工 作 ,模具型面 与约 10 %的高温金属坯料直接接触 ,型 00
锻造比的计算方法

锻造比的计较办法之五兆芳芳创作锻造比是锻造时金属变形程度的一种暗示办法.锻件的组织和机械性能与良多因素有关,而锻造比是影响锻件质量的最主要因素之一.锻造比以金属变形前后的横断面积的比值来暗示.不合的锻造工序,锻造比的计较办法各不相同.1、拔长时,锻造比为y=F0/F1或y=L1/L0式中F0,L0—拔长前钢锭或钢坯的横断面积和长度;F1 ,L0—拔长后钢锭或钢坯的横截面积和长度.2、镦粗时的锻造比,也称镦粗比或压缩比,其值为y=F1/F0或y=H0/H1F0, H0—镦粗前钢锭或钢坯的横截面积和高度;F1, H1—镦粗后钢锭或钢坯的横截面积和高度.3、对于用铸锭(包含有色金属铸锭)锻制的大型锻件和莱氏体钢锻件,正确选取锻造比有较大的实际意义;对于某些大型锻件的中间坯料,如涡轮盘、压气机盘等的圆饼坯料,轴、框、梁等的预制锻坯,锻造比也有重要的实际意义.锻造比永远是正的,变形前后的面积之比的计较永远是对的,即大面积变形成小面积时,用变形前的面积除以变形后的面积;反之类推.用长度比较时要当心:同形状变形时是可以拿长的除以短的(体积不变定律),不合形状变形时是绝对不成以的,例如八角锭拔长成方形时,只能用八角形除以方形面积.4、以上还应弥补:锻造比分为工序锻造比、火次锻造比和总锻造比.5、当只用拔长或只用镦粗,而进行几回锻造时,则总锻造比等于各次锻造比的乘积,即y总= y1 * y2 * y3 …6、如两次拔长中间镦粗或两次镦粗中间拔长时,总锻造比规则为两次锻造比相加,即y总 = y1 + y2 +…此式中未将中间镦粗或中间拔长的锻造比计较在总锻造比之内.锻造比是自由锻里的一个重要指标,但不是唯一的,在大型锻件锻造中,更注重锻造状态:应变场、温度场等等.如果在很小的进砧量下以每次很小的压缩量锻造,它的心部压实水平远远不如大进砧量、大压下量的锻造状态——小压缩量多次锻压堆集的变形效应都集中在锻件外层,而我们追求的往往是心部资料的压实.对于大型锻件,每每要碰到用户提出“锻造比要大于多少”时,我们总要解释一番,其实关头的仍是看最后的组织检测和探伤情况.至于模锻,更不必拘泥于锻比的数字,计较机模拟变形状态时注重的是“场”的概念,起码是四维的——一个数字没法说清庞杂的变形效应.它只能概略地表述某个主变形标的目的的变形程度.总体来说,就是拔长比依照面积比来计较;镦粗比依照长度比来计较.分段比缺乏2的之间用乘法,大于2的用加法.注意锻比都是指计较主要变形的锻比!另外,锻比只是一个经常使用的名词,现在仿佛有良多资料上说,这个锻比应用不成靠.其实锻件的质量仍是要看锻造压实的效果,以及锻造资料的质量,不要迷信锻比利用锻压机械对金属坯料施加压力,使其产生塑性变形以取得具有一定机械性能、一定形状和尺寸锻件的加工办法.锻压的两大组成部分之一.通过锻造能消除金属的铸态疏松,焊合孔洞,锻件的机械性能一般优于同样资料的铸件.机械中负载高、任务条件严峻的重要零件,除形状较复杂的可用轧制的板材、型材或焊接件外,多采取锻件.锻造按成形办法可分为:①开式锻造(自由锻).利用冲击力或压力使金属在上下两个抵铁(砧块)间产生变形以取得所需锻件,锻造比主要有手工锻造和机械锻造两种.②闭模式锻造.金属坯料在具有一定形状的锻模膛内受压变形而取得锻件,可分为模锻、冷镦、旋转锻、挤压等.按变形温度锻造又可分为热锻(加工温度高于坯料金属的再结晶温度)、温锻(低于再结晶温度)和冷锻(常温).锻造用料主要是各类成分的碳素钢和合金钢,其次是铝、镁、钛、铜等及其合金.资料的原始状态有棒料、铸锭、金属粉末和液态金属等.金属在变形前的横断面积与变形后的模断面积之比称为锻造比.正确地选择锻造比对提高产品质量、下降成本有很大关系.。
锻件质量控制的方法与要点(二)
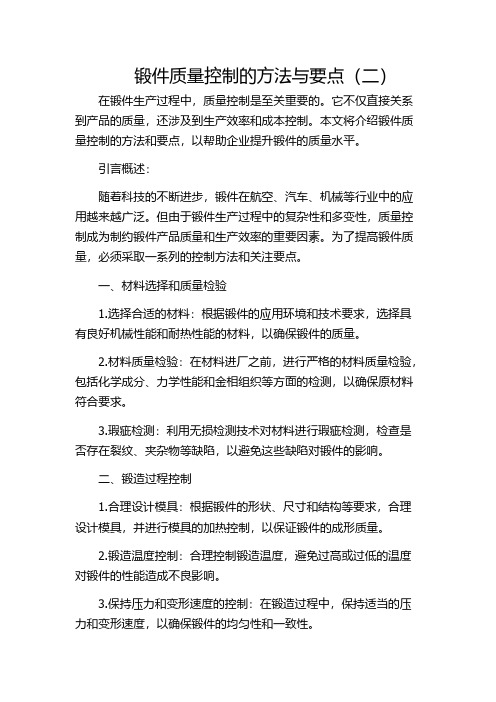
锻件质量控制的方法与要点(二)在锻件生产过程中,质量控制是至关重要的。
它不仅直接关系到产品的质量,还涉及到生产效率和成本控制。
本文将介绍锻件质量控制的方法和要点,以帮助企业提升锻件的质量水平。
引言概述:随着科技的不断进步,锻件在航空、汽车、机械等行业中的应用越来越广泛。
但由于锻件生产过程中的复杂性和多变性,质量控制成为制约锻件产品质量和生产效率的重要因素。
为了提高锻件质量,必须采取一系列的控制方法和关注要点。
一、材料选择和质量检验1.选择合适的材料:根据锻件的应用环境和技术要求,选择具有良好机械性能和耐热性能的材料,以确保锻件的质量。
2.材料质量检验:在材料进厂之前,进行严格的材料质量检验,包括化学成分、力学性能和金相组织等方面的检测,以确保原材料符合要求。
3.瑕疵检测:利用无损检测技术对材料进行瑕疵检测,检查是否存在裂纹、夹杂物等缺陷,以避免这些缺陷对锻件的影响。
二、锻造过程控制1.合理设计模具:根据锻件的形状、尺寸和结构等要求,合理设计模具,并进行模具的加热控制,以保证锻件的成形质量。
2.锻造温度控制:合理控制锻造温度,避免过高或过低的温度对锻件的性能造成不良影响。
3.保持压力和变形速度的控制:在锻造过程中,保持适当的压力和变形速度,以确保锻件的均匀性和一致性。
4.锻件冷却控制:在锻件完成后,进行合理的冷却处理,以消除内部应力,提高锻件的强度和韧性。
5.锻件尺寸和形状控制:通过更细致的模具设计和更精确的锻造工艺控制,实现锻件尺寸和形状的精确控制。
三、热处理和表面处理1.热处理工艺的选择:根据锻件的材料和要求,选择合适的热处理工艺,以改善锻件的组织结构和性能。
2.热处理温度和时间的控制:在热处理过程中,控制温度和时间,确保锻件的热处理效果符合要求。
3.表面处理的选择:根据锻件的应用要求,选择合适的表面处理方式,如表面涂层、镀层等,以提高锻件的耐腐蚀性和装饰性。
四、非破坏性检测和尺寸检验1.非破坏性检测方法的选择:根据锻件的形状和结构,选择合适的非破坏性检测方法,如超声波检测、磁粉检测等,以检测锻件的内部缺陷。
锻模常见的损坏形式及原因
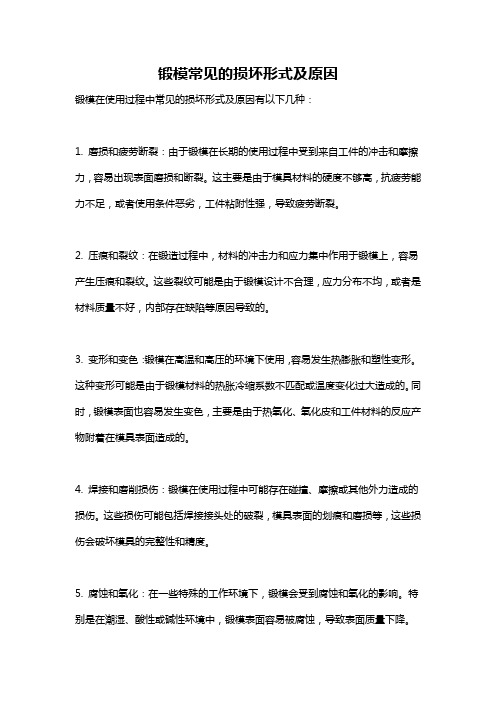
锻模常见的损坏形式及原因锻模在使用过程中常见的损坏形式及原因有以下几种:1. 磨损和疲劳断裂:由于锻模在长期的使用过程中受到来自工件的冲击和摩擦力,容易出现表面磨损和断裂。
这主要是由于模具材料的硬度不够高,抗疲劳能力不足,或者使用条件恶劣,工件粘附性强,导致疲劳断裂。
2. 压痕和裂纹:在锻造过程中,材料的冲击力和应力集中作用于锻模上,容易产生压痕和裂纹。
这些裂纹可能是由于锻模设计不合理,应力分布不均,或者是材料质量不好,内部存在缺陷等原因导致的。
3. 变形和变色:锻模在高温和高压的环境下使用,容易发生热膨胀和塑性变形。
这种变形可能是由于锻模材料的热胀冷缩系数不匹配或温度变化过大造成的。
同时,锻模表面也容易发生变色,主要是由于热氧化、氧化皮和工件材料的反应产物附着在模具表面造成的。
4. 焊接和磨削损伤:锻模在使用过程中可能存在碰撞、摩擦或其他外力造成的损伤。
这些损伤可能包括焊接接头处的破裂,模具表面的划痕和磨损等,这些损伤会破坏模具的完整性和精度。
5. 腐蚀和氧化:在一些特殊的工作环境下,锻模会受到腐蚀和氧化的影响。
特别是在潮湿、酸性或碱性环境中,锻模表面容易被腐蚀,导致表面质量下降。
以上是锻模常见的损坏形式及原因。
为了延长锻模的使用寿命,需要从以下几个方面进行改进和保养:1. 选用合适的锻模材料:选择具有高硬度和高抗疲劳性能的材料,能有效延长锻模的使用寿命。
2. 设计合理的锻模结构:考虑热胀冷缩系数和应力分布,合理设计锻模的结构和几何形状,减少应力集中和变形的可能性。
3. 定期进行维护和保养:定期对锻模进行清洗、涂油防锈和检查,及时更换损坏的零件,保持模具的完整性和精度。
4. 加强模具管理和使用规范:严格按照使用规范进行操作,避免碰撞、摩擦和其他不当使用导致的损伤。
5. 提高模具加工工艺:采用先进的加工工艺,提高锻模的精度和硬度,降低锻模的损伤风险。
综上所述,锻模损坏的形式主要包括磨损、断裂、压痕、裂纹、变形、变色、焊接和磨削损伤、腐蚀和氧化等。
机械制造工艺基础题库

机械制造⼯艺基础题库机械制造⼯艺基础(第六版)试题库绪论⼀、填空题(将正确答案填写在横线上)1、_是应⽤⼴泛的⼯程材料.2、机械制造包括从⾦属材料的制造到制成_后装配到产品上的全过程。
3、制造在制造业中占有⾮常重要的地位.4、按照被加⼯⾦属在加⼯时的状态不同·机械制造通常分为加⼯和加⼯两⼤类。
5、电⽓设备和线路应符合国家有关规定。
⼆、判断题(正确的,在括号内打∨;错误的.在括号内打x)1、机械制造技术的先进程度代表着制造业的⽔平,在⼀定程度上反映了国家⼯业和科技的整体实⼒( )2、在制造业中所采⽤的主要加⼯⽅法就是机械制造。
( )3、利⽤各种特种加⼯设备,完成对普通⾦属、⾼硬度⾦属、有⾊⾦属、⾼精度⾦属零件的加⼯属于⾦属特种加⼯。
( )4.在机械制造过程中,各类机床的操作必须严格遵守机床操作规程.避免发⽣⼈员、⼏床事故。
( )三、选择题(将正确答案的序号填写在括号内)1、下列属于⾼温职业(⼯种)的是( )。
A.磨⼯B.铸造⼯C钳⼯ D.车⼯2、利⽤各种⼿段对⾦属材料进⾏加⼯从⽽得到所需产品的过程称为A.⾦属加⼯B.产品制造C.零件制造D机械制造3.( )属于机械制造中的冷加⼯⼯种。
A.焊⼯B铸造⼯ C.钳⼯ D.车⼯4.下列属于⾦属热加⼯职业(⼯种)的是( )。
A.钳⼯B.车⼯C.锻压⼯D.镗⼯第⼀章铸造§1-1铸造基础⼀、填空题《将正确答案填写在横线上》1.铸造所得到的⾦属⼯件或⽑坯称为。
2.按⽣产⽅法不同.铸造可分为和两⼤类.3.铸造组织,晶粒,铸件的⼒学性能特别是冲击韧度,铸件质量不4.铸造被⼴泛应⽤于机械零件的制造.⼆、判断题(正确的.在括号内打∨;错误的,在括号内打x)( ) 1.将熔融⾦属浇注、压射或吸⼈铸型型腔中,待其凝固后⽽得到⼀定形状和性能铸件的⽅法称为铸造.( ) 2.铸件内部易产⽣缩孔、缩松、⽓孔等缺陷,会导致铸件的⼒学性能特别是冲击韧度低.铸件质量不够稳定。
锻造加工锻件的质量指标

锻造加工锻件的质量指标1.锻造质量概念质量是工业上广泛使用,用来衡量产品品质好坏的术语,它表示成品在技术要求上所达到的水准。
对锻造质量而言,有广义的锻造质量和狭义的锻造质量的区别:广义的锻造质量是按ISO 9000质量体系进行评述,主要包括设计质量、锻造过程的质量控制、锻件质量和质量追溯等内容;而狭义的锻造质量则主要是指锻件所能达到的技术指标(锻件质量),包括零件的尺寸精度和重量偏差、材料的内在质量和表面质量等技术指标。
锻件的质量按技术条件或相关标准进行评定,锻件不仅要达到零件规定的最终用户的要求,还要满足中间环节(如机械切削加工部门)的要求。
在实际生产中,根据锻件符合锻件设计阁样的程度,将锻件分为合格件、返修件、次品和废品。
完全符合于制造技术要求的锻件称为合格锻(制)件,但合格锻件中可能有质量较好与质量较差(等级)之分。
不符合技术要求而需要辅助加工或修整的锻件,称为返修锻件,返修锻件办理回用手续后可流入下道工序。
不符合技术要求,但以后仍可采用的锻件称为次品。
如果锻件不符合技术要求而又难于修整,今后又不可能应用时,这种锻件就称为废品。
废品件应报废,禁止其流入下道工序。
锻造质量问题的评述是一项非常复杂而又牵涉面较广的工作,可以按缺陷产生的原因进行评述,也可以按缺陷的责任进行评述,还可以按缺陷产生的部位进行描述,因而有必要对其进行分类。
(1)按产生缺陷的工序或生产过程分类有条料过程产生的质最缺陷、锻造过程中产生的质蛍缺陷和热处理过程中产生的质量缺陷等。
1)由原材料引起的缺陷。
①由原材料带来的锻件缺陷:裂纹、发裂、缩孔、疏松、杂质、偏析、结疤、气泡、夹渣、砂眼、折叠、刮伤、非金属夹杂、白点等缺陷;②由原材料缺陷在锻造时引发的纵向或横向裂纹、夹层等缺陷;③原材料化学成分存在问题。
2)由下料而产生的缺陷有:端面粗糙不平、端面倾斜和长度不足、端部裂纹、端部毛刺和夹层等。
3)由加热而造成的缺陷有:开裂、氧化和脱碳、过热、过烧和加热不均匀等。
影响锻件质量主要因素

影响锻件质量主要因素一.原材料的化学成分:1. 磷(P)能溶于铁素体中,其固溶强化能力很强,当其融入铁素体后使钢的强度、硬度显著提高,塑性、韧性显著降低。
磷还具有极大的偏析倾向。
2 硫(S)在钢中的溶解度很小,在钢锭的凝固过程中,硫聚集于最后凝固的地方,形成硫化物夹杂,严重影响钢的塑性。
当硫以FeS形式存在时,FeS与Fe 形成易熔共晶体,其熔点为985℃,分布于晶界。
当钢在800-1200℃锻造时,由于晶界处的硫化铁共晶体塑性低或发生熔化,而导致锻件开裂,这种现象称为热脆性。
这种钢必须在1000℃以上长时间退火扩散才能锻造。
若钢中含有足够数量的锰,可以消除硫的有害作用。
3 氮(N)在590℃时,溶解于铁素体的量为0.1%,但在室温时,则降至0.001%以下。
当氮含量较高的钢自高温较快冷却时,铁素体中的氮呈过饱和状态,随后在室温或稍高温度下,氮将逐渐以Fe4N形式析出,使钢的强度、硬度增高,塑性和韧性大为下降,这种现象称为时效脆性。
4 氢(H)在钢中的溶解度随温度的降低而下降,当氢含量较高的钢锭,经锻、轧后较快冷却时,从固溶体析出的氢原子来不及向钢坯表面扩散,而集中在钢内缺陷处形成H2,产生相当大的压力,这种压力在组织应力和热应力的共同作用下,引起氢脆,而出现细微裂纹,即所谓白点。
5 氧(O)在铁素体的溶解度很小,以夹杂物形式存于钢中。
氧化物熔点高、硬而脆,通常分布在晶粒边界,会严重影响钢的塑性,降低疲劳强度。
氧化铁还会与其他夹杂物形成易熔共同体,分布于晶界处,造成钢的热脆性。
6各种合金元素对钢的影响: a.镍(Ni)使钢具有很高的强度、塑性和抗蚀性。
b.Cr能提高钢的强度和硬度,增加耐磨性和耐热性,还能显著提高钢的抗氧化性和抗蚀性。
C.Mo能提高钢的强度和硬度,并略降低塑性和韧性,它最大的特点是使钢具有较高的耐热性。
d.Si一般含量超过2.5%时锻造就比较困难。
e.Mn会提高钢的强度,硬度增强耐磨性和抗磁性而降低韧性。
产品性能指标以及影响因素

四、产品性能主要指标以及影响产品性能的主要因素锻件在使用中总是受外力的作用,其性能除了取决于其所规定化学成分、工艺质量要求外,还可借助不同的热处理方法使之具有优良的综合力学性能,以达到提高锻件质量、减轻锻件重量,延长使用寿命和降低成本的目的。
故对锻件施行适当的热处理是提高与改善材料力学性能的重要手段,必须对其进行力学性能测试,而材料的力学性能(经热处理)是判断锻件热处理质量的重要标志。
我厂常用的力学性能检验指标包括硬度(布氏硬度和洛氏硬度)、抗拉强度、屈服点、屈服强度、比例极限、断后伸长率、断面收缩率、冲击功。
1、硬度试验金属材料的硬度是材料抵抗局部变形,特别是塑性变形、压痕或划痕的能力,也是表示金属软硬程度的判据。
xx氏硬度HBS:淬火钢球压头,压痕大,不能测太硬度的材料,适用于测量退火和正火钢、铸铁、有色金属等材料的硬度。
xx氏硬度HRC:锥角为120°的金刚石圆锥体压头,适用于调质钢、淬火钢、渗碳钢等硬度的测量。
洛氏硬度HRB:Φ1.59mm淬火钢球压头,适用于测量有色金属、铸铁、退火态和正火态钢等。
洛氏硬度与布氏硬度相比压痕小,软硬材料都可以测量,但同样不同标尺之间不可相互比较硬度值的大小。
2、拉伸试验材料在载荷作用下抵抗永久变形和破坏的能力。
在机械制造中常通过拉伸试验测定材料的屈服强度和抗拉强度,作为金属材料强度的主要判据。
(1)屈服点(σs)金属材料出现屈服现象时,在试验期间产生塑性变形而拉伸力不增加的应力点。
亦表示材料发生明显塑性变形时的最低应力值。
(2)抗拉强度(σb)拉伸试验时,相应最大拉伸力时的应力。
亦表示材料能够承受的最大应力值。
(3)断后伸长率(δ)断后标距的残余伸长量(L1-L0)与原始标距长度(L0)之比的百分数。
(4)断面收缩率(ψ)试样拉断后横截面积的最大缩减量(S0-S1)与试样原始横截面积(S0)的百分比(5)屈服强度(σ0.2)试样发生屈服现象时的应力值,屈服点S的应力值称为屈服强度σS,表征材料开始发生明显的塑性变形。
锻造常见缺陷及原因
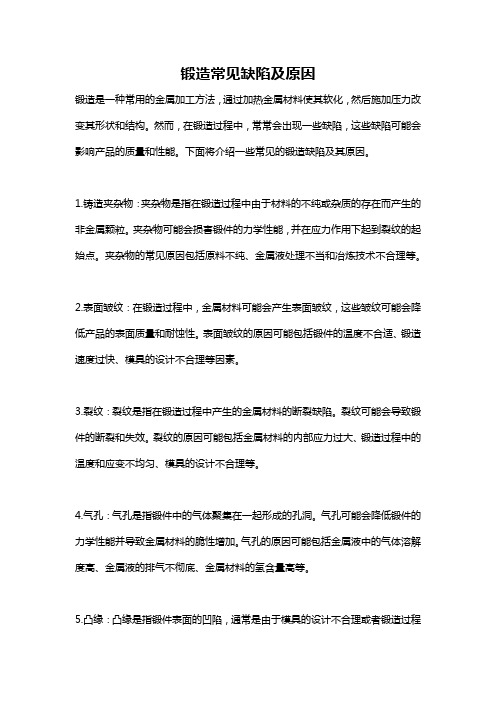
锻造常见缺陷及原因锻造是一种常用的金属加工方法,通过加热金属材料使其软化,然后施加压力改变其形状和结构。
然而,在锻造过程中,常常会出现一些缺陷,这些缺陷可能会影响产品的质量和性能。
下面将介绍一些常见的锻造缺陷及其原因。
1.铸造夹杂物:夹杂物是指在锻造过程中由于材料的不纯或杂质的存在而产生的非金属颗粒。
夹杂物可能会损害锻件的力学性能,并在应力作用下起到裂纹的起始点。
夹杂物的常见原因包括原料不纯、金属液处理不当和冶炼技术不合理等。
2.表面皱纹:在锻造过程中,金属材料可能会产生表面皱纹,这些皱纹可能会降低产品的表面质量和耐蚀性。
表面皱纹的原因可能包括锻件的温度不合适、锻造速度过快、模具的设计不合理等因素。
3.裂纹:裂纹是指在锻造过程中产生的金属材料的断裂缺陷。
裂纹可能会导致锻件的断裂和失效。
裂纹的原因可能包括金属材料的内部应力过大、锻造过程中的温度和应变不均匀、模具的设计不合理等。
4.气孔:气孔是指锻件中的气体聚集在一起形成的孔洞。
气孔可能会降低锻件的力学性能并导致金属材料的脆性增加。
气孔的原因可能包括金属液中的气体溶解度高、金属液的排气不彻底、金属材料的氢含量高等。
5.凸缘:凸缘是指锻件表面的凹陷,通常是由于模具的设计不合理或者锻造过程中的卡位不良而引起的。
凸缘会降低锻造件的密封性和耐蚀性。
6.尺寸偏差:尺寸偏差是指锻造件的实际尺寸与设计尺寸之间的差异。
尺寸偏差可能会影响锻件的装配和使用,降低产品的功能性。
尺寸偏差的原因可能包括模具的磨损、材料的收缩率不均匀、锻造机床的精度不高等。
以上是一些常见的锻造缺陷及其原因。
为了避免这些缺陷的出现,可以通过优化锻造过程,提高金属材料的质量,改进模具设计和锻造工艺等手段来减少缺陷的发生。
同时,对于已经出现的缺陷,可以通过修复和加工的方法来消除或者修复。
锻件质量控制
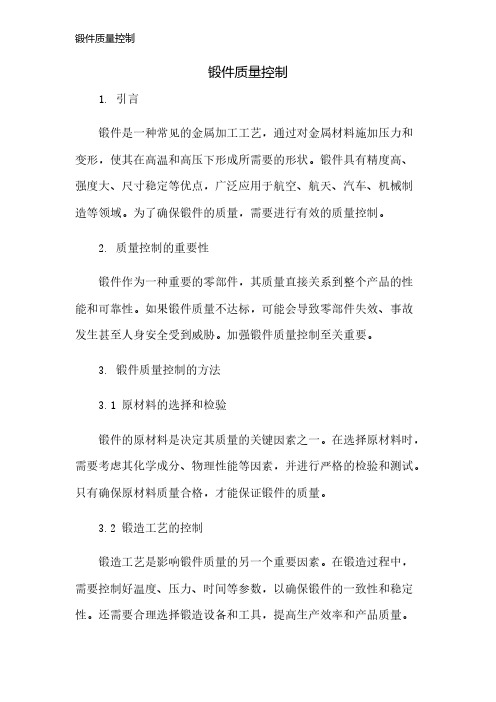
锻件质量控制1. 引言锻件是一种常见的金属加工工艺,通过对金属材料施加压力和变形,使其在高温和高压下形成所需要的形状。
锻件具有精度高、强度大、尺寸稳定等优点,广泛应用于航空、航天、汽车、机械制造等领域。
为了确保锻件的质量,需要进行有效的质量控制。
2. 质量控制的重要性锻件作为一种重要的零部件,其质量直接关系到整个产品的性能和可靠性。
如果锻件质量不达标,可能会导致零部件失效、事故发生甚至人身安全受到威胁。
加强锻件质量控制至关重要。
3. 锻件质量控制的方法3.1 原材料的选择和检验锻件的原材料是决定其质量的关键因素之一。
在选择原材料时,需要考虑其化学成分、物理性能等因素,并进行严格的检验和测试。
只有确保原材料质量合格,才能保证锻件的质量。
3.2 锻造工艺的控制锻造工艺是影响锻件质量的另一个重要因素。
在锻造过程中,需要控制好温度、压力、时间等参数,以确保锻件的一致性和稳定性。
还需要合理选择锻造设备和工具,提高生产效率和产品质量。
3.3 热处理的控制热处理是锻件质量控制的重要环节,可以改善锻件的结构和性能。
通过控制加热温度、保温时间和冷却方式等参数,可以使锻件达到所需的力学性能和组织结构。
还需要对热处理过程进行严格监控和检验,确保锻件质量合格。
3.4 检测和检验的方法为了确保锻件质量,需要对其进行全面的检测和检验。
常用的检测方法包括金相检测、硬度测试、超声波检测等。
通过这些方法,可以对锻件的尺寸、形状、缺陷等进行评估,及时发现问题并采取相应的措施。
3.5 质量记录和跟踪在整个生产过程中,需要做好锻件的质量记录和跟踪。
记录包括原材料的批次、加工参数、检测结果等信息,以便于追溯锻件的质量来源。
通过跟踪,可以及时了解锻件的生产情况和质量状况,及时纠正问题,提高产品的质量和信誉度。
4.锻件质量控制是确保产品质量和安全的重要环节。
通过选择合适的原材料、控制锻造工艺和热处理过程、采用有效的检测方法,并做好质量记录和跟踪,可以有效提高锻件的质量,并满足用户的需求。
- 1、下载文档前请自行甄别文档内容的完整性,平台不提供额外的编辑、内容补充、找答案等附加服务。
- 2、"仅部分预览"的文档,不可在线预览部分如存在完整性等问题,可反馈申请退款(可完整预览的文档不适用该条件!)。
- 3、如文档侵犯您的权益,请联系客服反馈,我们会尽快为您处理(人工客服工作时间:9:00-18:30)。
影响锻件质量主要因素
一.原材料的化学成分:
1. 磷(P)能溶于铁素体中,其固溶强化能力很强,当其融入铁素体后使钢的强度、硬度显著提高,塑性、韧性显著降低。
磷还具有极大的偏析倾向。
2 硫(S)在钢中的溶解度很小,在钢锭的凝固过程中,硫聚集于最后凝固的地方,形成硫化物夹杂,严重影响钢的塑性。
当硫以FeS形式存在时,FeS与Fe 形成易熔共晶体,其熔点为985℃,分布于晶界。
当钢在800-1200℃锻造时,由于晶界处的硫化铁共晶体塑性低或发生熔化,而导致锻件开裂,这种现象称为热脆性。
这种钢必须在1000℃以上长时间退火扩散才能锻造。
若钢中含有足够数量的锰,可以消除硫的有害作用。
3 氮(N)在590℃时,溶解于铁素体的量为0.1%,但在室温时,则降至0.001%以下。
当氮含量较高的钢自高温较快冷却时,铁素体中的氮呈过饱和状态,随后在室温或稍高温度下,氮将逐渐以Fe4N形式析出,使钢的强度、硬度增高,塑性和韧性大为下降,这种现象称为时效脆性。
4 氢(H)在钢中的溶解度随温度的降低而下降,当氢含量较高的钢锭,经锻、轧后较快冷却时,从固溶体析出的氢原子来不及向钢坯表面扩散,而集中在钢内缺陷处形成H2,产生相当大的压力,这种压力在组织应力和热应力的共同作用下,引起氢脆,而出现细微裂纹,即所谓白点。
5 氧(O)在铁素体的溶解度很小,以夹杂物形式存于钢中。
氧化物熔点高、硬而脆,通常分布在晶粒边界,会严重影响钢的塑性,降低疲劳强度。
氧化铁还会与其他夹杂物形成易熔共同体,分布于晶界处,造成钢的热脆性。
6各种合金元素对钢的影响: a.镍(Ni)使钢具有很高的强度、塑性和抗蚀性。
b.Cr能提高钢的强度和硬度,增加耐磨性和耐热性,还能显著提高钢的抗氧化性和抗蚀性。
C.Mo能提高钢的强度和硬度,并略降低塑性和韧性,它最大的特点是使钢具有较高的耐热性。
d.Si一般含量超过2.5%时锻造就比较困难。
e.Mn会提高钢的强度,硬度增强耐磨性和抗磁性而降低韧性。
二、钢锭的质量
1. 冶炼方式冶炼的方式:碱性平炉、酸性平炉和电炉冶炼。
a 碱性平炉:优点是对炉料要求不高,可排除大量的硫、磷夹杂元素,但氢的含量较高。
钢中的非金属夹杂物主要是氧化物和硫化物。
b 酸性平炉:不易去除硫、磷,因此对原料要求较高,应预先进行精选。
含氢量较低。
钢中的非金属夹杂物主要是硅酸盐,且呈球状分布。
c 碱性电炉冶炼:与碱性平炉冶炼相似,但周期短,不受炉气污染的影响。
e若以上的方法无法满足使用要求,可采用真空精炼法和电渣重溶法。
2. 我国锻造用大型钢锭有两种规格,一种是普通锻件用的4%锥度、高径比为1.8-2.3、冒口比例为17%的钢锭;另一种是优质锻件用的11-12%锥度、高径比为1.5左右、冒口比例为20%-24%的钢锭。
3. 锭身呈多角形的钢锭,凝固均匀,有效防止角偏析。
钢锭愈大,锭身角数愈多,有八角形、十二角形和十四角形。
锭身锥度的增加有利于钢液中的尖杂物和气体上浮,有利于凝固补缩和减少偏析程度。
4. 铸锭的过程对钢锭质量有很大的影响,钢液流入盛钢桶后,为了使夹杂上浮和排除气体,必须静置一段时间。
浇注分为上浇注和下浇注,下注法容易混进夹杂,因此大型钢锭普遍采用上注法。
5. 钢锭底部和冒口占钢锭重量的5%-7%和18%-25%,对于合金钢,切除的冒口应占钢锭的25%-30%,底部占7%-10%。
6. 钢锭的几种缺陷
a.偏析:钢锭内部化学成分和杂质分布的不均匀性称为偏析。
偏析是钢液凝固时选择结晶的产物。
偏析分为树枝状偏析(或称显微偏析)和区域偏析(或称低倍偏析)两种。
树枝状偏析通过锻造和锻后热处理可以消除。
b.夹杂:钢锭内部不溶解于基体金属的非金属化合物,经过热、冷处理仍不能消失。
通常有:硅酸盐、硫化物和氧化物。
夹杂物破坏金属的连续性,在应力作用下夹杂与基体金属间产生应力集中,并容易发生显微裂纹,必然要降低锻件的机械性能。
c.气体含量(纯净度):氢、氧、氮等气体时通过炉料和炉气溶入钢液的,氧和氮在钢锭中是以氧化物和氮化物出现的,氢是以原子状态存在的。
氢是钢锭中危害最大的气体。
氢在钢中的溶解度随温度下降而减低,铸锭时在凝固过程中超过溶解度的氢来不及从钢锭中析出,仍以原子状态过饱和地固溶于钢中,随后部分地扩散到钢锭的孔隙内,并结合成分子,从而构成锻件产生白点的根本原因。
自采用钢液真空处理技术以来,危害气体已基本能够消除。
d.缩孔和疏松:缩孔在冒口区形成,由于没有钢液补充而造成不可避免的缺陷。
锻造时应将冒口和缩孔一并切除,否则因缩孔不能锻合而造成内部裂纹。
疏松是由于晶间钢液最后凝固收缩造成的晶间空隙和钢液凝固过程析出气体构成的显微孔隙。
疏松使钢锭组织致密程度下降,影响锻件的机械性能,因此在锻造时要求增大变形程度,以便锻透钢锭,将疏松消除。
三、锻造工艺
1.在考虑锻造温度时,要考虑毛坯与工模具接触过程中的温降,要对工模具进行预热。
2.对难变形合金程度高的合金,应尽量采用慢速变形,并控制每一锤击或压力机的每一行程变形量,一般控制在20%左右,对速度敏感的材料,选择变形速度要同时考虑温度效应。
3.闭式模锻的塑性比开式模锻好,而开式模锻又比自由锻好,在自由锻工序中,型砧拔长和带圈的镦粗要比平砧拔长和不带圈镦粗更能发挥金属的塑性。
4.低塑性拔长时,应注意选择合适的送进比,送进比太小时,变形集中在上下部,中心都锻不透,并沿轴向产生拉应力,导致内部横向裂纹产生。
在镦粗时,常用软衬垫镦粗或叠镦(用于锻薄饼形零件),以改善变形的不均匀性,防止产生表面裂纹。
5.在考虑锻造工艺时特别是最后一火的锻造时,应尽量避免在临界变形程度下进行,以免得到粗大晶粒组织。
具体来说,高温下金属塑性好,变形抗力小,应采用远大于临界变形程度的较大变形量锻造;低温修正时采用低于临界变形程度的小变形量进行局部修整。
6.若因温度和变形程度选择不当而得到粗大晶粒时,可利用热处理相变细化晶粒组织,但对于热处理中不发生相变的钢种,如奥氏体钢,就必须在锻造过程中获得细小而均匀的晶粒组织,因此对这样的材料在锻造时须加倍注意。
7.由于热变形形成纤维组织,会使金属的力学性能出现异向性,即纵向力学性能指标中的A,Z,Ak比横向相应的指标大得多,两个方向上的强度Rm。
Re差别不大。
8.热变形对力学性能的提高是有限的,研究表明:当锻比不大于5时,金属的力学性能提高较快,而且金属力学性能的异向性不明显,而当锻造比大于5时,纤维组织造成的力学性能异向性将随着锻造比的加大越来越明显地表现出来,纵向力学性能提高甚微,横向力学性能则急剧下降。
因此采用过大的变形程度对锻
件质量有害无益。
9. 锻件的冷却:钢的化学成分越单纯,则允许的冷却速度越快,反之亦然。
对于中小型碳钢和低合金钢锻件,在锻后均采取冷却速度较快的空冷方法。
而合金成分复杂的合金钢锻件,在锻后则采取冷却速度缓慢的坑冷或炉冷的方法。
a.对于含碳较高的钢(碳素工具钢,合金工具钢及轴承钢)如果锻后采取缓慢冷却,在晶界会析出网状碳化物,将严重影响锻件使用性能,因此这类钢的锻件冷却,在锻后先用空冷、鼓风或喷雾快速冷却到700度,然后再把锻件放入坑中或炉中缓慢冷却。
b.对于没有相变的钢(奥氏体钢、铁素体钢),由于锻件的冷却过程无相变,可采用快速冷却。
同时为了锻后获得单相组织,以及防止铁素体钢475度脆性,也要求快速冷却,所以这类钢的锻件冷却通常采用空冷方法。
c.对于空冷自淬钢(如高速钢,不锈钢,高合金工具钢)因空冷就能发生马氏体的相变,会引起较大的组织应力而很容易产生冷却裂纹,所以这类钢锻后必须缓慢冷却。
d.对于白点敏感的钢(如铬镍钢34CrNiMo)为了防止冷却过程产生白点,应按一定冷却规范进行炉冷。
e.通常用钢材锻成的锻件在锻后的冷却速度比用钢锭锻成的锻件在锻后的冷却速度快。
f.一般断面尺寸大的锻件,因冷却过程温度应力大,锻后应缓慢冷却,反之对于断面尺寸过小的锻件,锻后可以快速冷却。
g.当锻件锻后冷却允许空冷,则不必采取中间冷却。
10. 合理制定加热保温规程并严格执行,防止产生过烧和过热等现象。