8d报告真难做
手把手教你写客户满意的人为操作失误8D报告

手把手教你写客户满意的人为操作失误8D报告摘要:在商业领域,客户满意度是企业成功的关键因素之一、人为操作失误是客户满意度下降的主要原因之一、本报告将分享一些有效的方法,帮助企业避免人为操作失误,提升客户满意度。
报告内容包括:对人为操作失误的定义和影响、常见的人为操作失误、避免人为操作失误的措施等。
第一部分:引言(100字)客户满意度是企业生存和发展的核心。
然而,让客户满意并不容易,人为操作失误往往是导致客户满意度下降的重要原因之一、本报告将介绍人为操作失误的定义和影响,以及避免人为操作失误的措施,以帮助企业提升客户满意度。
第二部分:人为操作失误的定义和影响(200字)人为操作失误指的是由人员的不当行为或疏忽引起的错误。
这些错误可能包括不正确的操作流程、不准确的信息处理、延误的响应时间等。
人为操作失误对企业的影响不容小觑,它可能导致客户的不满、失去信任以及最终的流失。
因此,减少人为操作失误对于企业来说至关重要。
第三部分:常见的人为操作失误(300字)在客户服务过程中,常见的人为操作失误有很多,包括以下几个方面:1.信息处理错误:员工可能因疏忽处理客户的信息,导致错漏。
2.响应时间延误:员工响应客户请求的时间过长,给客户造成不良印象。
3.服务态度不佳:员工对客户的态度冷淡,缺乏热情和友善。
4.错误的解决办法:员工处理客户问题时,未选择合适的解决方案。
5.信息传递不清:员工之间沟通不畅,导致客户的问题无法及时解决。
第四部分:避免人为操作失误的措施(400字)为了避免人为操作失误,企业可以采取以下措施:1.培训与教育:通过培训员工掌握正确的操作流程和技能,提高他们的专业水平和处理能力。
2.建立明确的规章制度:制定明确的规章制度,明确员工的工作职责和行为准则。
3.引入技术支持:使用先进的技术工具和系统来协助员工处理客户的问题,减少人为操作失误的概率。
4.激励机制:建立激励机制,通过奖励和赞扬来鼓励员工积极向上,提高服务质量。
教会你如何写8D报告63页PPT

31、别人笑我太疯癫,我笑他人看不 穿。(名 言网) 32、我不想听失意者的哭泣,抱怨者 的牢骚 ,这是 羊群中 的瘟疫 ,我不 能被它 传染。 我要尽 量避免 绝望, 辛勤耕 耘,忍 受苦楚 。我一 试再试 ,争取 每天的 成功, 避免以 失败收 常在别 人停滞 不前时 ,我继 续拼搏 。
66、节制使快乐增加并使享受加强。 ——德 谟克利 特 67、今天应做的事没有做,明天再早也 是耽误 了。——裴斯 泰洛齐 68、决定一个人的一生,以及整个命运 的,只 是一瞬 之间。 ——歌 德 69、懒人无法享受休息之乐。——拉布 克 70、浪费时间是一桩大罪过。——卢梭
33、如果惧怕前面跌宕的山岩,生命 就永远 只能是 死水一 潭。 34、当你眼泪忍不住要流出来的时候 ,睁大 眼睛, 千万别 眨眼!你会看到 世界由 清晰变 模糊的 全过程 ,心会 在你泪 水落下 的那一 刻变得 清澈明 晰。盐 。注定 要融化 的,也 许是用 眼泪的 方式。
35、不要以为自己成功一次就可以了 ,也不 要以为 过
8d报告怎么写

8d报告怎么写如何撰写8D报告一、引言8D报告是一种常用于解决问题和改进流程的工具。
通过系统性地描述问题、分析原因和提出解决方案,8D报告可以帮助团队在面对挑战时更加高效地行动。
本文将介绍撰写8D报告的步骤和技巧。
二、问题描述在8D报告的第一部分,你需要准确地描述问题以及其对业务和客户的影响。
问题描述应包括相关数据和背景信息,以便读者能够全面了解当前状况。
三、问题分析在问题分析阶段,你需要对问题进行深入分析,以确定可能的根本原因。
使用常见的问题分析工具,如5为什么法或鱼骨图,可以帮助你识别潜在的原因。
四、根本原因确认在确定潜在原因后,你需要进行验证以确认根本原因。
这可能包括实验、数据收集和专业知识的应用。
确保你的验证过程可靠且可重复,这将有助于提高报告的可信度。
五、解决方案提出在解决方案提出阶段,你需要根据根本原因提出一系列解决方案。
一般来说,解决方案应包括长期和短期的措施,以确保问题能够得到根本解决并提供紧急的临时解决办法。
六、解决方案实施在解决方案实施阶段,你需要详细描述实施方案的具体步骤和时间表。
确保你在描述过程中提供足够的细节,以便读者能够理解实施计划以及相关的资源需求。
七、效果评估在实施解决方案后,你需要评估其效果。
这包括定量和定性的评估指标,以便确定解决方案是否达到了预期的结果。
如果解决方案没有产生预期的效果,你可能需要重新审视问题的根本原因并提出调整方案。
八、预防措施最后,在8D报告的最后一个部分,你需要提出预防措施,以确保问题不再发生。
预防措施可以包括改进流程、培训员工或应用更有效的质量管理工具。
确保你提出的预防措施是可行的并能够被实施。
九、总结总结部分是8D报告的结尾,你可以在此部分回顾所做的工作、总结收获以及提出建议。
确保总结简明扼要,突出报告的关键内容。
十、附录在报告的附录部分,你可以提供一些额外的信息和数据,以支持你在报告中提出的观点和结论。
附录通常包括图表、数据分析、问题的历史记录和其他相关文档。
教你如何做8D报告

教你如何做8D报告1. 什么是8D报告8D报告是指为应对产品质量问题而采用的一种解决方案和报告流程。
它是一种用于记录、分析和解决问题的工具,旨在追踪和改进产品质量问题,并确保类似问题不再发生。
8D报告以8个步骤的形式展开,每个步骤都有特定的要求和任务。
2. 8D报告的步骤第一步:组建团队在问题发生后,首先要组建一个专门的团队来应对问题。
这个团队应该由不同领域的专家组成,可以包括质量工程师、生产经理、技术支持人员等。
团队成员应该具备解决问题所需的技能和知识。
第二步:描述问题在这一步,团队需要清楚地描述问题,包括问题的性质、出现的频率、影响因素等。
团队应该收集足够的信息,并使用适当的工具进行数据分析和问题定位。
第三步:立即采取临时措施为了尽快解决问题,团队需要立即采取一些临时措施来减轻问题的影响。
这些措施可以是暂停生产、对产品进行分类或修复等。
第四步:确定根本原因在这一步,团队需要深入分析问题,并确定导致问题发生的根本原因。
这一步骤可能需要进行更详细的数据收集和分析。
团队可以使用5W1H分析法或鱼骨图等工具进行根本原因分析。
第五步:制定长期措施基于对根本原因的分析,团队需要制定长期措施来避免类似问题的再次发生。
这些措施可以包括修改设计、改进工艺、强化培训等。
措施应该具体、可行,并应与实际情况相适应。
第六步:验证措施的有效性一旦长期措施得以实施,团队需要验证措施的有效性。
验证可以通过实验、测试和数据监控来进行。
团队应该确保措施能够解决问题,并评估其长期可行性。
第七步:预防措施的实施在经过验证后,团队可以开始实施预防措施。
这些措施旨在确保类似问题不再发生,并提高整体质量水平。
预防措施应该经过充分的规划和测试,以确保其有效性和可持续性。
第八步:总结报告最后一步是编写8D报告。
这份报告应该包含问题的描述、根本原因分析、临时措施、长期措施、验证结果和预防措施等。
报告应该清晰、简洁,并包含足够的详细信息和数据支持。
如何编写8D报告
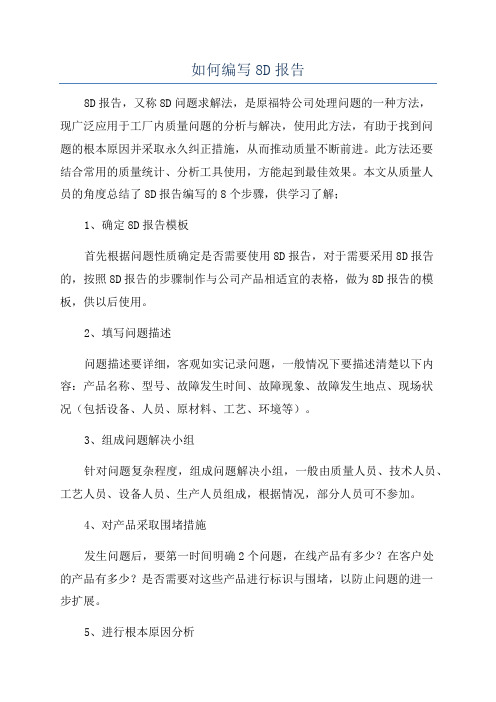
如何编写8D报告8D报告,又称8D问题求解法,是原福特公司处理问题的一种方法,现广泛应用于工厂内质量问题的分析与解决,使用此方法,有助于找到问题的根本原因并采取永久纠正措施,从而推动质量不断前进。
此方法还要结合常用的质量统计、分析工具使用,方能起到最佳效果。
本文从质量人员的角度总结了8D报告编写的8个步骤,供学习了解;1、确定8D报告模板首先根据问题性质确定是否需要使用8D报告,对于需要采用8D报告的,按照8D报告的步骤制作与公司产品相适宜的表格,做为8D报告的模板,供以后使用。
2、填写问题描述问题描述要详细,客观如实记录问题,一般情况下要描述清楚以下内容:产品名称、型号、故障发生时间、故障现象、故障发生地点、现场状况(包括设备、人员、原材料、工艺、环境等)。
3、组成问题解决小组针对问题复杂程度,组成问题解决小组,一般由质量人员、技术人员、工艺人员、设备人员、生产人员组成,根据情况,部分人员可不参加。
4、对产品采取围堵措施发生问题后,要第一时间明确2个问题,在线产品有多少?在客户处的产品有多少?是否需要对这些产品进行标识与围堵,以防止问题的进一步扩展。
5、进行根本原因分析针对问题点,组织人员运行质量工具进行原因分析,一般采用头脑风暴法、鱼骨图、直方图、拆线图、散步图、5WHY分析等工具。
在此步骤值得注意的是:根据分析锁定根本原因后,要进行原因验证,通过人为制造不合格原因重现故障现象,以期证明根本原因的正确性。
6、采取永久纠正措施并执行根本原因确定后,要采取纠正措施对现有产品进行改进,使其成为合格产品,对纠正措施的有效性要进行验证,并留下数据,确保纠正措施采取后,此类故障不再产生。
7、采取预防措施,防止再发生纠正措施采取后,还要根据5WHY分析结果,采取预防措施,将导致不合格的潜在因素全部去除,并将措施文字化、标准化,是期收到长期有效的效果。
8、对永久纠正措施进行确认纠正预防措施采取后,要继续对数据进行统计分的,观察措施采取后是否还有同类型的不合格产生,以确认所采取的纠正预防措施是否有效。
8D报告原理及编写

8D报告原理及编写8D报告是指针对其中一事故、问题或质量缺陷,进行全面深入的分析和解决方案的报告。
8D是指八个字母,代表着报告的八个主要步骤,即确定问题、制定团队、定义缺陷、采取紧急措施、分析根本原因、制定长期解决方案、实施解决方案、总结和评估。
8D方法是一种系统性的质量管理工具,它的目标是通过迅速解决问题,避免类似的问题再次发生,提高产品和服务的质量。
下面将详细介绍8D报告的原理及编写步骤。
一、原理:1.定义问题:明确问题的实质,准确把握问题的范围和影响,确保对问题的理解一致。
2.制定团队:组建由不同部门的专业人员组成的团队,在问题解决过程中能够提供全面的意见和建议。
3.定义缺陷:具体描述问题的性质、外观特征和质量标准,确保问题的描述准确无误。
4.采取紧急措施:在问题发生后,采取必要的紧急措施,控制问题的蔓延程度和影响范围。
5.分析根本原因:通过应用各种质量工具和方法,找出问题的根本原因,以便制定相应的长期解决方案。
6.制定长期解决方案:根据根本原因的分析结果,制定能够解决问题的长期方案,包括对流程、设备、人员等方面的改进措施。
7.实施解决方案:将制定的长期解决方案转化为实际行动,确保解决方案的有效实施。
8.总结和评估:对问题解决的过程和效果进行总结和评估,为类似问题的解决提供经验。
二、编写步骤:1.标题和日期:在报告的开头,明确标注报告的标题和编写日期。
2.问题描述:具体描述问题的性质、外观特征和对业务流程的影响,以确保对问题的理解一致。
3.问题图示:使用图片或示意图等方式,直观地展示问题的外观特征,有助于其他人员对问题的理解和分析。
4.过程步骤:按照8D的八个步骤,逐步描述问题解决的过程和各个步骤的具体操作内容。
5.数据分析:根据问题的性质,收集和分析相关的数据,使用统计方法或质量工具进行定量或定性分析。
6.根本原因分析:使用鱼骨图、五为分析法等工具,找出问题的根本原因,确保解决方案的针对性和有效性。
如何制作8D报告 讲义

二.8D报告之内容(讲义)
2.描述问题(Failure Description): A. 向团队说明何时、何地、什么产品,什么问题、 严重程度、不良比率,涉及到的批号,不良周期, 目前状态. B.是否有实物或不良照片,最好是小组成员能看 到不良实物 C.将客户的问题描述转换成厂内易于理解的问题 描述 D.总之,对问题的描述,细节越清楚越好,以便能 准确了解问题本身,便于快速解决
2、厂内该型号0937,0939周期WIP 352 PCS板已无禁止 出货。
3、客户端仓存3234 PCS已安排退回厂内重工处理。 4、退货重工流程为: 退货回厂==》100% X-RAY测量银厚==》超出 标准部份全部挑出报废处理==》外观检查==》化 银后处理清洗==》包装==》出货
二.8D报告之内容(讲义)
二.8D报告之内容(讲义)
6.永久性改善的措施和有效性验证(Verify The Effectiveness of Permanent Actions): A. 当永久对策准备妥当,则可开始执行,并且对永久对 策执行情况作一一验证; B.并观察不良率是否下降至预期目标或问题点至规格之 内,或不良现象完全消除及客户己能完全接受,不再 产生问题。 C.此项由品管或品证人员进行检查执行情况和改善是否 有效。 D.品管或品证需收集数据和掌握执行动态,假如效果不 佳还需按PDCA的循环修订对策。
4.原因分析(Failure Analysis,Define Cause,根本原因及流出原因): the Root
A.以4M1E(人,机,料,法,环)来展开分析,善用原因追溯型之鱼骨图 B.追查生产及品质记录(不可拍出来或假想出来):
(1)在进行根本原因分析之前,须先依据客户提供的基本信息及自己掌 握的信息(出货记录,生产周期等)对当时生产的制程条件/参数展 开调查。通过确认当时生产过程中的各项记录,例:批量单,首件记 录,抽检记录,参数点检记录,设备保养记录,药水添加记录,管制 图等进行分析,推断出4M1E中最有可能造成问题的因子,这个因子就 可能就是造成问题的根本原因。 (2)同时若可行则还可以通过切片,EDS分析,及其他可靠度试验等作 为辅助分析工具。根本原因分析可召集相关责任部门人员一起进行, 群策群力,共同分析.
学习8d报告心得
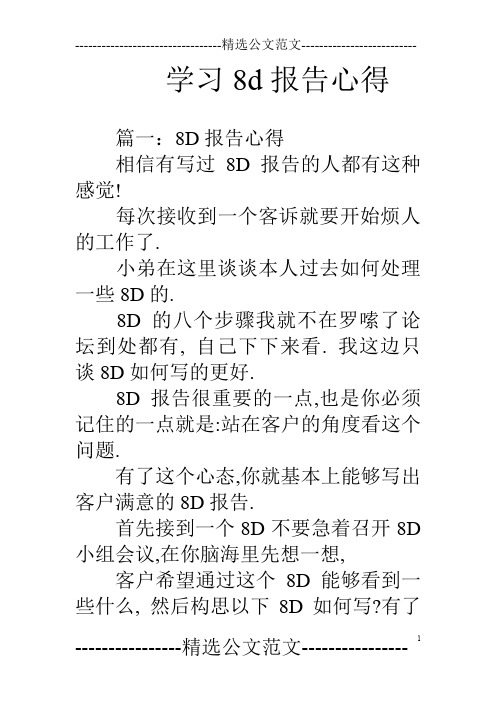
学习8d报告心得篇一:8D报告心得相信有写过8D报告的人都有这种感觉!每次接收到一个客诉就要开始烦人的工作了.小弟在这里谈谈本人过去如何处理一些8D的.8D的八个步骤我就不在罗嗦了论坛到处都有, 自己下下来看. 我这边只谈8D如何写的更好.8D报告很重要的一点,也是你必须记住的一点就是:站在客户的角度看这个问题.有了这个心态,你就基本上能够写出客户满意的8D报告.首先接到一个8D不要急着召开8D 小组会议,在你脑海里先想一想,客户希望通过这个8D能够看到一些什么, 然后构思以下8D如何写?有了框架召开会议及写起8D来就事半功倍.我可以告诉大家客户绝对不希望看到一份问题分析报告.举个简单的例子:一台电视没有信号被客诉.分析问题是:高频头坏了. 很多人在这个时候写8D的时候就在原因分析中简单的写上”高频头坏了”, 接下来的纠正预防措施感觉就没有东西写了,只好写一些”QC加强检验”, “生产过程全检”. 这种敷衍了事的8D相信很多人都不希望看到. 这只能说是一份问题分析报告, 而且还不是全面的.脑海8D框架怎么构思成?1. 看到问题先想问题影响有多大?你需要在8D报告中帮客户进行风险评估, 评估的时候需要不是谈问题出现在哪里, 而是谈问题出现后有什么影响?(如果问题直接影响到人的生命安全的话,建议你什么也别想了,直接将全部产品招回,处理方法后面再想问题出现的概率有多大?把你所评估的风险告诉客户让客户心中有底, 这点是让客户放心的重点.2. 接下来就想想出去的产品如何处理?生产过程的产品如何处理?脑海中一定要有个初步的概念,即使是错的有一定得有. 没有这个概念开小组会议很被动.3. 接下来就是问题分析, 问题分析很关键,建议大家没事就去生产线看看,学习学习,因为熟悉流程对写8D太有帮助了.问题分析不能只是找到原因: 而是需要找到原因的原因.就拿上可例子来说: 高频头不良如果再问个为什么原因就多了,比如:来料器件不稳定, 出货检验漏失, 其他器件的不稳定造成改器件不良等等. 可以用头脑风暴法, 小组在一起讨论. 有了这些造成不良的可能原因接下来就是去证明哪些不良是真正的原因, 证明的方法很多,如试验/检验/测量等这要靠各位平时的工作经验积累. 我就不一一详细说了, 说下去到天亮都没得完. 找出真正的不良原因, 将不是主要造成的原因排除. 如果能够将分析过程进行记录并拍照这样的分析结果相信大家都会认可的.4. 纠正措施只要对真正的不良原因采取相应的解决措施就可以了, 这边提一点就是纠正措施一定要有相关的记录或步骤/作业指导方面的问题附上那就更完美了.5. 预防措施这点是客户比较关注的: 预防措施不仅仅是纵向的预防包括横向的也要预防, 如: 这个产品有这个问题,同类型的其他产品是否有这个问题.这个需要考虑, 因为客户担心的就是在其他产品出现同样的问题. 所以需要大家将有效的预防措施展开.在写整个8D报告的时候问题分析/纠正措施/预防措施是重点, 所以这三步需要附上各位在分析解决过程的证明资料, 你要记住一点, 客户没有监督你在做, 而记录和试验报告就是证明你有认真对待他的客诉的最好证明.还有一些8D反馈的现象是生产过程无法避免的, 而且一定存在的.如: 部件虚焊, 即使你找到真正的原因也没有绝对控制的把握, 我在这里告诉大家一点写这样的8D可以采用比较法. 比如采用客退回来的产品有多少是因为虚焊不良造成的客退,或现在生产过程虚焊的不良率有多少,只要采取措施降低这些不良率,也算是改善,改善前和改善后比较一下,只要懂点这方面知识的客户也不会有什么意见.篇二:8D培训心得8D学习心得通过对8D的学习,我个人觉得8D 报告很重要的一点,也是我们必须记住的一点就是:站在客户的角度看这个问题。
(1)8D报告真难做

(1)8D报告真难做
1、你只是讲了流出的原因,但是没有找到根本原因,要查找发生的原因,铁壳脱落,铁壳是怎么固定的,固定的卡扣失效了,配合的尺寸是否有问题,装配的方法、工具有没有问题,有没有装配不到位的防呆措施。
这是主要的调查方向。
2、调查出来的原因进行验证,验证铁壳具体失效的原因,并进行再现试验,验证为什么会有2%的不良发生,而不是大批的发生,(就是偶发或是频发,还是其他原因)
3、如果发生的根本原因有了对策,基本后续就不会流出了,但是也要针对此类缺陷建立验证检查方法,也就是流出对策,同样要从防呆的角度考虑,具体的不良图片、详细信息、影响的问题要添加到作业标准中,同时更改CP\FMEA等控制文件。
4、针对员工检查时间长,视力疲劳问题,应针对性的考虑员工休息,更主要的是将过往的缺陷制作成缺陷收集卡,将所有的不良缺陷、图片、原因、不良的影响进行讲解和公示,针对主要的不良项目制作限度样本、不良样本进行相应工位的悬挂,定期的进行确认,以便于员工的检查一致性。
改善问题主要从问题发生的根源着手,加上防呆性的措施,才能永久的避免问题的再发,记住,“没有解决不了的问题,只有你想不到的方法。
”
另,8D的方法是需要下时间和功夫来理解和揣摩的,往往字面上的理解是不能完全搞明白的,多找一些案例看一看,对于客户提出的刁难性的问题不要排斥,那才是历练你的机会,要好好珍惜。
结合5WHY方法,把你认为的问题连续的问WHY WHY WHY WHY WHY ,找到根本原因,然后再从后往前推,如果能退回去就证明你找到原因了,退不回去那就重新来。
做质量的,证据和数据才是你要讲的,其他的都是虚的,加油吧。
教你如何做8D报告(品质精品)
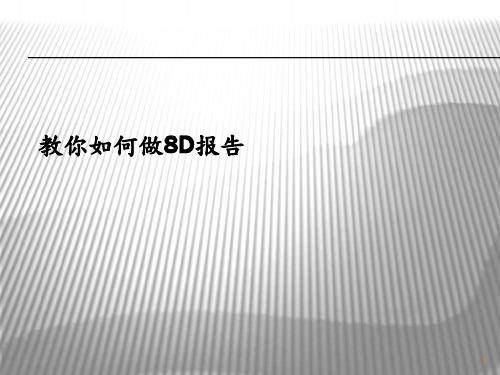
18
也就是我們常說的人, 事, 時, 地, 物
WHAT 什麼事情
WHEN 何時發生 WHO 與誰有關 WHERE 在何處發生
HOW MANY 發生的程度
問題描述
會惡化
是否須緊急處置
19
緊急處置
發生中 Holding
未發生 Sorting
品質問題
已發生
Tracing
20
D2階段 現狀分析(問題細部描述)—收集資料 Fact & Data Finding analysis
24
記錄用查檢表
責任部門
2003年各季LOSS TIME責任分類查檢 表
季度 第一季 第二季 第三季
制 造 1200
1050
890
品保
800
760
780
生管
180
160
100
制工
200
170
185
工程
60
55
78
採購
300
282
300
材倉
50
38
42
合計
2790
2515
2375
合計
3140 2340 440 555 193 882 130 7680
進行真因分析與驗證真因 5、 D5列出選定及驗證永久對策 6、 D6執行永久對策及效果確認 7、 D7防止再發及標準化 8、 D8認知與殘餘潛在問題
4
問題是什么?
當現狀與標准或目標有了差距時, 即遇到了問題
過去
現在
目標 未來
5
盤點工厂現存在的問題
VQA進料檢驗單位 合資單位 業務單位 工程單位 制造單位 IPQC FQC QA QE
(1)8D报告真难做

(1)8D报告真难做这个希望对你有帮助1)写8D报告的基本原则a)使用简单,正确的语言简单,但是能够清晰的说明问题不使用缩略语(或给出全称的说明)b)符合逻辑性一步一步的相互印证,没有前后矛盾的说法,也不要从8D里延伸出新的问题出来。
c)目标读者外行——在某个项目上没有接受过培训的,不具备相关行业背景知识没有技术背景,缺少工程经验的人员说白了就是让白痴也看明白d)多一些“花花草草”的东西多放一些图片,比如各种对策实施的证据,过程记录的证据,在线产品验证的证据。
多采用一些工具,比如鱼骨图,排列图,FTA啊,这样可以唬住一般的客户了e)兼顾顾客的要求和公司的利益了解顾客的心理,在一定程度上去迎合客户的需求,要给客户看出我们很重视这个8D,并且花了很大的精力和财力才采取各项措施。
对公司明显做不到的改善措施/方法,就没有必要列出,但也可以利用客户来推动内部的持续改善。
2)8D方法步骤这个不再啰嗦概念方面的东西,写一些我个人的感受。
a)2D问题描述阶段必须说明所有客户反馈失效的相关信息,失效描述(外观不良,电性能不良…),退回样品信息(品名,型号,数量,批号)失效发生的信息(受入检查,整机测试,老化试验,0km,市场…)和具体的失效分析结果。
通过FA找到失效的真正问题点也是非常关键的,这个对今后的数据分析和原因分析有很大的帮助。
b)3D遏制行动阶段3D通常可以包含以下内容,实施有效的遏制行动来停止问题延续,防止类似不良的产品继续产生并发给客户,可以通过额外/加严的控制(e.g. 100% 全检),将异常信息传达给相关人员,提升其意识和注意,对现有的库存和在线产品进行验证,是否有同样的问题,确认受影响批的生产记录(过程监控的数据(抽样试验的数据,检验数据,测试datalog),合格率数据,过程中不良分类(是否和投诉有关联),前后批次(通常需要3-5批)的合格率数据,不良分类,设备维修记录(异常批没有维修记录,需确认之前一次和之后一次),品种更换记录等)--这些记录的整理非常关键,传说中的Data mining,通过挖掘数据,可能会找到问题的规律。
如何编写8D报告

如何编写8D报告培训教材第一部分 8D简介8D及8个步骤,也叫解决问题的8个步骤(规定、规律、纪律)第二部分解决问题的8个步骤一、D0:知道问题1.1 目的主要是为了看此类问题是否需要用8D来解决,如果问题太小,或是不适合用8D来解决的问题,这一步是针对问题发生时候的紧急反应。
1.2 关键要点判断问题的类型、大小、范畴等等。
与D3不同,D0是针对问题发生的反应,而D3是针对产品或服务问题本身的暂时应对措施。
第一次发现该问题是在什么时间?此次问题产生在什么时候?有何特征?覆盖哪些产品?有什么别的不良本应被发现却没有被发现?1.3 范例科研产品部反馈宁波时代电压传感器最外面的那个螺母没有紧固,用手指头轻轻一带就会松脱。
事前调查:型号: NCV4A-1000V/SP4图纸编号:ZSN233D-00-00A发生比例:100%何时发现: 2011.3.29在何处发现:科研产品部涉及范围:所有宁波时代双螺母设计的产品给产品造成的影响:螺母松脱可能造成电气短路二、D1:成立小组2.1 目的成立一个小组,小组成员具备工艺/产品的知识,有配给的时间并授予了权限,同时应具有所要求的能解决问题和实施纠正措施的技术素质。
小组必须有一个小组长(通常列在表格第一位)。
2.2 关键要点成员资格确认,需具备工艺、产品相关的知识;制定小组目标及分工。
2.3 范例三、D2:描述问题3.1 目的用量化的术语详细说明与该问题有关的内/外部顾客抱怨,如什么、地点、时间、程度、频率等。
“什么东西出了什么问题”。
3.2 关键要点收集和组织所有有关数据以说明问题;问题说明是所描述问题的特别有用的数据的总结;审核现有数据,识别问题、确定范围;细分问题,将复杂问题细分为单个问题;问题定义,找到和顾客所确认问题一致的说明;尽量附图说明。
3.3 范例四、D3:临时性抑制措施实施及确认4.1 目的保证在永久纠正措施实施前,将问题与内外部顾客隔离。
4.2 关键要点找出和选择最佳“临时抑制措施”;评价紧急响应措施;决策 ;实施,并作好记录;验证。
品质改善8d报告范文客户投诉了那个8D报告写
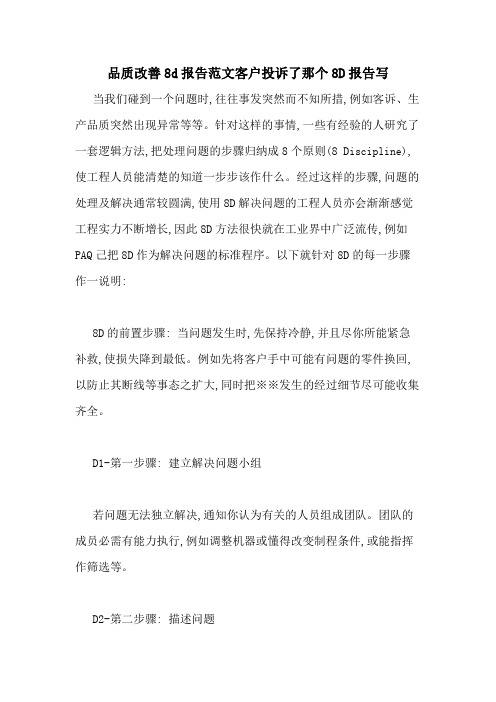
品质改善8d报告范文客户投诉了那个8D报告写当我们碰到一个问题时,往往事发突然而不知所措,例如客诉、生产品质突然出现异常等等。
针对这样的事情,一些有经验的人研究了一套逻辑方法,把处理问题的步骤归纳成8个原则(8 Discipline),使工程人员能清楚的知道一步步该作什么。
经过这样的步骤,问题的处理及解决通常较圆满,使用8D解决问题的工程人员亦会渐渐感觉工程实力不断增长,因此8D方法很快就在工业界中广泛流传,例如PAQ己把8D作为解决问题的标准程序。
以下就针对8D的每一步骤作一说明:8D的前置步骤: 当问题发生时,先保持冷静,并且尽你所能紧急补救,使损失降到最低。
例如先将客户手中可能有问题的零件换回,以防止其断线等事态之扩大,同时把※※发生的经过细节尽可能收集齐全。
D1-第一步骤: 建立解决问题小组若问题无法独立解决,通知你认为有关的人员组成团队。
团队的成员必需有能力执行,例如调整机器或懂得改变制程条件,或能指挥作筛选等。
D2-第二步骤: 描述问题向团队说明何时、何地、发生了什么事、严重程度、目前状态、如何紧急处理、以及展示照片和收集到的证物。
想象你是FBI的办案人员,将证物、细节描述越清楚,团队解决问题将越快。
D3-第三步骤: 执行暂时对策若 ___还未找到,暂时用什么方法可以最快地防止问题?如全检、筛选、将自动改为手动、库存清查等。
暂时对策决定后,即立刻交由团队成员带回执行。
D4-第四步骤: 找出问题 ___找问题 ___时,最好不要盲目地动手改变目前的生产状态,先动动脑。
您第一件事是要先观察、分析、比较。
列出您所知道的所有生产条件(即鱼骨图),逐一观察,看看是否有些条件走样,还是最近有些什么异动?换了夹具吗?换了作业员?换了供应商?换了运输商?修过电源供应器?流程改过? 或比较良品与不良品的检查结果,看看那个数据有很大的差?,尺寸?重量?电压值?C※※?耐电压?等等不良的发生,总是有原因,资料分析常常可以看出蛛丝马迹。
干货|如何写好一份8D报告

干货|如何写好一份8D报告一.什么是8D1.什么是8D8D 的原名叫做 8 Disciplines,又称团队导向问题解决方法。
•此方法以团队运作导向以事实为基础,避免个人主见之介入,使问题之解决能更具条理。
•面对问题应群策群力,互相帮助、相互提拔、如此才能彻底解决问题。
2.8D的作用•通过建立小组训练内部合作的技巧。
•提供问题有效解决的方法。
•防止相同或类似问题的再发生。
•提高顾客满意度,增强其对供方的产品和过程的信心。
3.何时采用8D1.重复发生,一直没有解决的问题2.比较重大的制程品质问题3.客户要求回复的品质投诉二、8D步骤D0.问题初步了解问题初步了解(立项和准备工作)•鉴定是否有进行8D 的必要;•立项和确定主题;•收集资料。
此过程尽量获取内部和外部的问题信息、数据、进行初步的分析和方案策划。
D1建立小组建立一个小组来解决问题和执行纠正计划,小组成员应具有过程和/或产品知识、分配的时间、权威和需要的技能。
建立小组需要考虑的要素:•小组的领导:谁来推动?•小组的资源:谁提供支持?•小组的成员:合作及分工?•人员的数量:多少为宜?选择小组成员的准则:D2问题描述以客户的角度和观点详细描述其所感受到的问题现象,将所遭遇的问题,以量化的方式,明确出所涉及的人,事,时,地,为何,如何,多少。
问题描述方法:5W/2HD3临时对策定义、验证和执行临时控制行动,保证在永久纠正措施实施前,将问题与内外部顾客隔离。
需要考虑的问题:1.防止继续产生不良品(减少不良品产生)。
2.减小产生的不良和后续可能产生不良对客户的影响。
确定并执行应先采取的临时措施,以遏制外界/内部客户问题的扩大。
•临时措施的确定应考虑从供应商零件库存---供应商零件在途品--内部零件/材料—生产制程—仓库储存—交付在途品—客户端减少和降低(消除)后果的产生。
•临时措施一直要持续实施至后续的永久对策的执行有效后,方可撤消。
•临时措施实施中,应及时跟踪和验证其效果。
8d报告编写方法及技巧

8d报告编写方法及技巧
1. 哎呀,8D 报告编写可真是有窍门的呀!就像建房子得先打牢基础一样。
比如说,问题描述得像警察破案那样详细准确才行呀!不然怎么能找到根本原因呢?
2. 8D 报告里的团队组建可太重要啦!这就好比打篮球要有默契的队友。
你想想,如果队友之间都不配合,那还怎么赢比赛?就像我们做报告,大家得齐心呀!
3. 原因分析这一块呀,得像侦探找线索一样仔细!例如找机器故障原因,每个细节都不能放过,不然怎么能修好呢?是不是这个理儿呀?
4. 对策制定要巧妙呀!就如同医生开处方,得对症下“药”。
要是胡乱开对策,那不就白忙乎啦,能解决问题吗?肯定不行呀!
5. 实施对策可别马虎哟!好比跑步比赛,到了冲刺阶段可不能掉链子。
一旦实施不到位,前面做的不都白费啦?
6. 效果确认要认真仔细呀!这就跟考试检查试卷一样重要。
不确认好效果,怎么知道我们做对了没有呢?你说是不是?
7. 防止再发这步可不能忘呀!就好像给机器上保险。
如果不做好预防,那问题不是还可能再出现嘛!要长点心呀!
8. 8D 报告整个过程就像是一场战斗,每个环节都紧密相连,少了哪个都不行呀!所以大家一定要掌握好方法和技巧,才能做出完美的 8D 报告呀!
我的观点结论是:8D 报告编写需要严谨认真,每个步骤都要做到位,只有这样才能真正发挥它的作用,解决问题。
高手教你做出漂亮的8D报告

高手教你做出漂亮的8D报告8D报告起源于美国福特汽车公司,是一种处理质量问题的方法,凡是福特公司的供应商遇到问题必须强制用这种方法解决。
应用8D报告工作法,能够发现真正肇因,并采取针对性措施加以消除,执行永久性矫正措施。
今天,小编就手把手教大家做出漂亮的8D报告。
后来因这方法处理质量问题效果显著,其他行业也开始应用起来。
今天,小编就手把手教大家做出漂亮的8D报告。
D1、成立小组8D的原名叫做团队导向问题解决步骤,即使一个人能力再强文笔再好,没有团队做支撑的8D报告都是失败的。
8D小组需要由具备产品及制程知识,能支配时间,且拥有职权及技能的人士组成,同时指定一名8D团队组长。
D2、问题描述8D报告的问题描述要具体、详尽,使用质量的5W2H就可以很好的描述问题。
5W是指when、who、where、what、why,即什么时间、客户是谁、地点是哪里、发生了什么事情、为什么会发生。
2h 是指how、how many,即问题的数量是多少,对客户产生了什么影响。
问题描述的清楚,才能便于问题的更好解决。
所以不能简简单单的一句话描述问题。
D3、应急措施8D报告为什么需要应急措施,通俗的说,就是现在着火了,应该怎么处理。
提出应急方案。
迅速帮客户处理问题,保证客户生产线不受影响而停线。
这过程需要多与客户沟通,及时反馈信息。
避免出了问题,还处处隐瞒,躲避责任的现象。
D4、根本原因分析查找真正的原因,只有找到真因,方可有效解决问题。
如果仅仅只是糊弄应付了事,则没有意义。
D5、纠正预防措施在生产前测试方案,并对方案进行评审以确定所选的校正措施能够解决客户问题,同时对其它过程不会有不良影响。
其关键要点有:重新审视小组成员资格;决策,选择最佳措施;重新评估临时措施,如必要重新选择;验证;管理层承诺执行永久纠正措施;控制计划。
D6、永久对策如何再发防止,如何防呆?如何从系统上避免不良不发生。
这里欢迎大家推出你们公司成功的防错方案,供大家学习。
一步步教会你做:8d报告

一步步教会你做:8D报告提到8D,大家会说出哪8个步骤,但是需真正去理解其精髓。
因为在工作中我们需要的是一份能真正对问题解决改善有效果的实质性8D报告,而不是一份文件。
8D起源于福特公司处理质量问题的一种方法。
凡是福特公司的供应商遇到问题必须强制用这种方法。
后来这方法好,其他的非福特公司的供应商也引进这方法处理问题。
就这样家喻户晓,各行业通吃。
而且不仅仅解决工作问题,解决家庭生活问题也很有效。
在这里仅分享下8D在处理质量问题上的应用。
1D0 现象及应急反应活动根据现象评估8D过程是否需要。
如果有必要,采取紧急反应行动(ERA)来保护顾客,并开始8D过程。
8D过程区别了症状和问题。
适用标准的大部分是症状。
没有症状,不会知道有问题。
症状是一个显示存在一个或多个问题的可测量的事件或结果。
这个事件的后果必须被一个或多个顾客经历;问题是指同期望有偏差或任何由未知原因引起的有害的后果;症状是问题的显示。
当收到投诉信息时,质量部门应尽量在客户投诉报告上确认以下信息以便展开调查:·产品编号及品名·客户名称,联系人及地址·缺陷描述,不合格品数量·追溯信息,如LOT NO,发货单编号等·索赔应尽量取得车型等信息如有,应从客户处得到样品,照片,标签及不合格率等必要的信息。
如是芯体泄露或严重投诉,收到投诉的人应立即通知质量经理及总经理。
QE应在收到投诉一个工作日内与客户联系。
应就以下信息与客户沟通:·跨部门小组及联系方式·确认已得到的信息·调查问题所必需的其他信息·应急措施的进展·应急措施及纠正措施的预期完成时间·任何其它的客户要求,如,了解问题进展和期望的交货·所有与客户之间的回复均应记录。
QE根据得到信息,依据三现主义(现场,现物,现象)来确认不良状况;如果是可以目视的不良,尽量取得照片或样品(确认现物);对于不良发生场所状况尽量收集详细的情报(确认现场,现象)。
技巧|8D报告你真的会写吗?不服请看!

技巧|8D报告你真的会写吗?不服请看!据说已经有99%的会员绑定了微信,一键登录6SQ,还没绑定的,肯定是账号和密码都忘了,点击绑定!论坛里看到很多8D报告的资料分享也有介绍自己公司的8D报告。
但是大家认为自己的8D报告怎么样?我们需要一份能真正对问题解决改善有效果的实质性8D报告,而不是一份文件。
我准备把各个质量工具,QC手法逐个分解下。
我相信我的细微分解,会比国内知名网站下载的知识要好。
对于初学者,可以更容易听懂和接受;对于老手,可以对照下,看看是否需要这样做8D更加好,说的不到之处,拍砖无妨。
提到8D,大家会说出哪8个步骤,但是需真正去理解其精髓。
首先说8D起源于福特公司处理质量问题的一种方法。
凡是福特公司的供应商遇到问题必须强制用这种方法。
后来这方法好,其他的非福特公司的供应商也引进这方法处理问题。
就这样家喻户晓,各行业通吃。
而且不仅仅解决工作问题,解决家庭生活问题也很有效。
D0.问题导向这是接受客户的投诉。
要懂得捕捉信息。
正确的客户会发投诉单,投诉单有照片,获取什么问题,批次号这些信息。
为8D做准备。
接到客户的投诉。
比如邮件。
因为客户投诉,一般来看都严重。
所以接到客户投诉,需在2小时内回复客户邮件,说“客户你好,我已收到你的邮件,信息已知悉,对于出现这样的问题,给你们带来不便,很是抱歉,我们正在着手解决,在**时间回你8D报告”。
这样的回复很有意义。
有公司接到客户投诉后,火急火燎,也很重视,但问题查起来和解决需要时间,于是开始查原因,等一切查好,3天过去了,你说客户会怎么想。
“这供应商接我投诉后,一点反应没有,在干什么”。
这样客户那里急的要命,你这里几天没有反应,换位思考,你说急不急人。
所以要及时给客户回复,讲明你对他们的投诉问题的处理正在进行中,给客户吃定心丸。
D1.成立小组这个很重要。
我刚开始接触8D的时候,在公司做8D报告,就是完全自己一个人做。
小组成员随便写几个人,而那些人都不懂8D,也没有参与这个问题改善。
如何写8d报告

如何写8d报告在工作中,很多人接触到了8D报告这个概念,但对于如何写一份高质量的8D报告,却常常感到困惑。
本文将从准备、分析、解决问题等多个方面,分享如何写一份优秀的8D报告。
一、准备阶段在动笔写8D报告之前,首先需要对待解决的问题进行全面的准备。
这包括收集相关数据和信息,分析问题的根源,确定问题的影响范围等。
只有在充分了解问题的基础上,才能有针对性地处理,并为报告提供准确的数据支持。
二、问题描述在写8D报告的第一部分,需要清楚地描述问题的背景、发生的情况和影响。
这一部分可以从以下几个方面展开:1. 问题发生的时间、地点和频率;2. 问题对产品质量和客户满意度的影响;3. 可能引起此问题的原因等。
三、分析原因在报告的第二部分,需要对问题的根本原因进行深入分析。
这一部分中可以采用常用的问题解决方法,如鱼骨图(Ishikawa Diagram)或5W2H等。
通过此类分析工具,可以明确问题发生的具体原因,为下一步的解决方案提供依据。
四、解决方案解决问题是8D报告的核心内容,也是读者最关心的部分之一。
在写解决方案的部分,建议采用以下结构:1. 描述解决方法:具体介绍解决问题所采用的方法,包括技术改进、流程优化或人员培训等;2. 实施计划:制定详细的实施计划,包括时间、人员和资源的安排,确保解决方案能够顺利执行;3. 预期效果:预估解决方案实施后的效果,即问题是否得到了解决,效果是否满足期望;4. 风险评估:识别实施解决方案过程中可能存在的风险,并提供相应的应对措施。
五、效果验证写8D报告的最后一部分是效果验证。
在这一部分中,需要详细说明解决方案的效果是否满足预期,并展示相关数据的对比等。
同时,还可以探讨问题是否真正得到了根治,以及可能出现的改进空间。
六、总结和反思通过对8D报告的准备、问题描述、分析原因、解决方案和效果验证的展开,文章的主要内容已经完成。
最后,可以在报告的结尾做一个总结和反思。
总结可以回顾整个解决问题的过程,并强调取得的成果和经验教训。
- 1、下载文档前请自行甄别文档内容的完整性,平台不提供额外的编辑、内容补充、找答案等附加服务。
- 2、"仅部分预览"的文档,不可在线预览部分如存在完整性等问题,可反馈申请退款(可完整预览的文档不适用该条件!)。
- 3、如文档侵犯您的权益,请联系客服反馈,我们会尽快为您处理(人工客服工作时间:9:00-18:30)。
8d报告真难做
这个希望对你有帮助
1)写8D报告的基本原则
a)使用简单,正确的语言
简单,但是能够清晰的说明问题
不使用缩略语(或给出全称的说明)
b)符合逻辑性
一步一步的相互印证,没有前后矛盾的说法,也不要从8D里延伸出新的问题出来。
c)目标读者
外行——在某个项目上没有接受过培训的,不具备相关行业背景知识
没有技术背景,缺少工程经验的人员
说白了就是让白痴也看明白
d)多一些“花花草草”的东西
多放一些图片,比如各种对策实施的证据,过程记录的证据,在线产品验证的证据。
多采用一些工具,比如鱼骨图,排列图,FTA啊,这样可以唬住一般的客户了
e)兼顾顾客的要求和公司的利益
了解顾客的心理,在一定程度上去迎合客户的需求,要给客户看出我们很重视这个8D,并且花了很大的精力和财力才采取各项措施。
对公司明显做不到的改善措施/方法,就没有必要列出,但也可以利用客户来推动内部的持续改善。
2)8D方法步骤
这个不再啰嗦概念方面的东西,写一些我个人的感受。
a)2D问题描述阶段
必须说明所有客户反馈失效的相关信息,失效描述(外观不良,电性能不良…),退回样品信息(品名,型号,数量,批号)
失效发生的信息(受入检查,整机测试,老化试验,0km,市场…)和具体的失效分析结果。
通过FA找到失效的真正问题点也是非常关键的,这个对今后的数据分析和原因分析有很大的帮助。
b)3D遏制行动阶段
3D通常可以包含以下内容,实施有效的遏制行动来停止问题延续,防止类似不良的产品继续产生并发给客户,可以通过额外/加严的控制(e.g. 100% 全检),将异常信息传达给相关人员,提升其意识和注意,对现有的库存和在线产品进行验证,是否有同样的问题,确认受影响批的生产记录(过程监控的数据(抽样试验的数据,检验数据,测试datalog),合格率数据,过程中不良分类(是否和投诉有关联),前后批次(通常需要3-5批)的合格率数据,不良分类,设备维修记录(异常批没有维修记录,需确认之前一次和之后一
次),品种更换记录等)--这些记录的整理非常关键,传说中的Data mining,通过挖掘数据,可能会找到问题的规律。
3D中还有一个重要的步骤就是“初始的风险评估”,评估是否需要召回或隔离,以此避免避免更多的可能存在失效产品被使用。
c)4D原因分析阶段
原因分析我们通常采用5WHY、鱼刺图、FTA的方法,个人觉得这些方法是非常好的,可以找到真正的原因。
我最恨的就是一句话两句话的原因。
原因分析不清,不管是对8D 报告来说还是对问题解决来说,完全失败。
很多偶发的问题可能是找不到原因的,那么FTA就提供了很好的帮助,通过头脑风暴把大家的意见结合起来,对每个可能性进行排查。
这些可能性有的会被推翻,有的会被证实。
证实还是证伪通常根据之前的数据分析,历史记录和再现试验来验证(也可以根据你的需求哦,^_^),通常这样的发生率很小案列,最终找不到原因的时候,都是挑一个可能发生的,公司容易改进的(或者确实需要改进的),做为发生原因来回答客户。
为了便于客户的理解,我们可以制作一些图片来说明失效的机理,必要时候用动画也是可以的。
为了说明模具如何把产品冲偏,用动画或图片的效果要远远好于文字说明。
需要注意的是,原因分析要和问题描述相吻合,也就是说,这个原因确实可以引起这个现象,然后进行再现试验,再现之后,产品确实出现了和投诉一样的失效模式和现象,这样我们才认可这个原因分析到位了。
当然,不合格的产品为什么从公司流出也是需要考量的,比如有的缺陷在测试时候不能筛选,我们以后改善以后如何保证筛选出来。
还有一点,大厂往往比较在意的,就是系统方面的原因分析,这对汽车工业来说,那是一定需要了。
Machine –e.g.设备设定,参数没有优化,设备放行的标准,设备的管理维护不足…
Material –e.g. 材料规范/公差不适宜,受入检查方法不合适,供应商认定有不足…
Method –e.g. 方法/流程没有优化,混乱的指令,没有定义相关规范和检查项目…
Man –e.g. 人为错误,无效的培训,违反纪律对一些重复发生的问题,客户往往会比较纠结你为什么以前的原因
分析没有分析到,这个时候,FTA就起作用了,可以通过FTA 的分析把相同的现象引到不相同的原因上,当然,我们也要据理力争,不是所有的缺陷都可以消失或者预防到的,特别是制造过程中。
如果做到了没有缺陷、不合格品流出,应该不是什么大问题。
想想看,航天工业目前也不能做到零缺陷。
我们只能把能想到的,预防起来。
d)5D纠正措施阶段
几个关键点如下:
包括针对发生原因/流出原因/系统原因,都是需要采取纠正措施的,另外需要考虑防呆方法的运用,比如人为错误的问题,是否需要增加装置,来保证人即使想出错也不可以。
(工人可能会提前打开烘箱,这样产品受热的时间会不够影响性能,但通过增加电子锁,烘箱一定在时间足了以后,自动打开,就可以防呆。
)
纠正措施前后的对比也是必须的,我们看到一些报告中写“加强检验”或“加强控制”等,这个说的是不清楚的,一定要说清楚,加强前是怎么样,加强后怎么样,列个表,既清楚,又符合我之前说的“花花草草”原则。
纠正措施是否有负面效应?这点需要考虑,同时在报告
中,要把执行的时间和责任人,当前对策的执行状态写清楚。
同时,在这条里,可以写上采取上述纠正措施后的验证结果或者验证计划(甘特图应该是比较好的工具),当然,也有人写在6D里,我个人觉得只要考虑到这点,就可以了,放D5还是D6,我也没有意见,不知各位高手有和见解。
e)7D 预防再发阶段
一定要考虑横向展开,也就是所谓的fan out,对所有可能产生同样问题的产品/PKG/设备/生产线/工序标准化和展
开相关的纠正措施。
比如A工序的维修员在修了设备后有一个螺丝忘记拧了,改善措施是建立一套设备维修以后针对设备/产品进行首检的机制,那么我们当然要横向展开到所有的工序所有的设备,同时还考虑到除了维修以后的验证,还有设备突然停机(停电,停气,死机),更换产品品种,长期设备闲置后开启等,这些建立的一整套的检查清单。
各种文件的升版也很重要,这个倒不在客户评价你的8D中体现,往往在客户现场审核的时候,找出当时的报告,看看你是否把对策文件化之类,如果一开始没有做好,那也比较麻烦。
特别提出,FMEA是一定需要进行评审的,通常也是需要升版相关内容的,比如RPN的重新评价,更新控制措施等。