汽车覆盖件拉伸起皱开裂分析及控制.(DOC)
汽车覆盖件拉伸起皱和开裂现象分析及控制措施_梁云荣

汽车覆盖件拉伸起皱和开裂现象分析及控制措施东风汽车公司车身厂(湖北十堰442040)梁云荣[摘要]对汽车覆盖件在拉伸过程中的起皱和开裂现象进行了分析,并从工艺、设计、调整等几个方面较详细地说明了解决零件拉伸起皱、开裂的方法和控制措施。
关键词汽车覆盖件拉伸起皱开裂控制措施[Abstract]It anal y zed the wrinklin g and cr ackin g p heno menon dur in g stretchin g p r ocess of automob ile blanketing pieces.And it amply illuminated the method and controlling measur e to solve the wrinklin g and cr ackin g durin g stretchin g p r ocess b y the as p ects of cr afts,desi g n and ad j ustin g.Keywords auto mobile blanketing pieces,str etching,wrinkling,cracking,contr olling mea-sures的受力及变薄乃至拉断有较大影响,因此也应取较大值,r1在(17~20)t均可。
第2次拉伸凸模圆角r2在(14~16)t均可,最好能等于或近似于成品底部圆角。
第1次拉伸为改善润滑条件,减少摩擦力,应取较大间隙,单面间隙为(1.1~ 1.2)t。
第2次拉伸条件较好,且直筒部分即为成品外壁,因此间隙不应太大,单面间隙取(1.02~ 1.06) t,但应较低碳钢件拉伸间隙大。
4其它问题4.1拉伸速度不锈钢材料的深拉伸,特别是薄壁材料对拉伸速度很敏感,在此极限状态下更应采用低速,第1次拉伸应控制在[9mm/s,速度大可能会造成拉断,第2次拉伸可适当加快,速度在13~14m m/s 均可。
汽车覆盖件拉伸模常见故障及解决

( 2 )在拉深后期单靠压边圈提供的进料阻力是不够的 ,此时凹模 圆角半径小 ,材料经过凹模洞 口时产生 的变形阻力就大,可为侧壁提 供较大的拉应力,使侧壁被拉直,最大限度地减小回弹量 。 ( 3 )较小的凹模圆角半径取值 ,也符合模具设计的一般原则,半 径小 , 放大容易,而半径大,变小则困难。
4 结 束 语
缓 松 现 象 在 直边 侧 壁上 比较 明显 ,其 原 因 是 直 边 部 分 的板 料 在 经 过 凹模 圆角 进 入 凹 模 的 , 必 然 会产 生 弯 曲变 形 。 欲 消 除这 种 变 形 ,侧
汽车覆 盖件在拉伸 的过程会遇到很多方面的情况 ,其解决方法具 体运用起来不应是单纯 、孤立 的,在具体调试操作中还应考虑到诸如 板料 的机械性能,冲床 的成形速度 ,板料及模具的润滑 ,板料定位位 置 ,拉深模 的间隙等各方面因素 。 对汽 车覆盖件 中的拉伸件 ,为 了控制拉深过程中材料流动均匀 ,
变 形 充 分 而 又 不 出 现起 皱 和 拉 裂 ,在 冲 压 上 采 用 措施 的基 本 原 则 是 开 流 和 限 流 。开 流 就 是 在 需要 材 料 流 动 的 地 方 减 小 阻 力 ,使 其 顺 利 流 动 , 以避 免 材 料 变 薄破 裂 。 限流 就 是 在 不 需 要 材 料 流 动 的地 方 增 大 阻
一
点 必 须 注 意 , 并 不是 拉 深 时 A 处 不 开 裂 , 拉 深件 就 是 合 格 的 。对 B 处
而 言 ,其 应 力 状 态 是切 向受 压 ,径 向受拉 ,产 生 的缺 陷 是 B 向 起皱 。为
( 3 )将 凹模圆角半径变大,减小板料进入凹模时的变形阻力,可 有效解决开裂现象。 ( 4 )压边圈平面处于 良好配合状态 ,拉伸是通过凹模平面和压边
汽车覆盖件拉延起皱开裂的影响因素及控制措施

汽车覆盖件拉延起皱开裂的影响因素及控制措施汽车覆盖件是指覆盖在汽车外部的零件,例如车身、车顶、车门等。
在汽车的使用过程中,由于各种因素的影响,这些覆盖件有可能会出现拉延起皱、开裂等问题。
本文将讨论造成这些问题的影响因素,并提出相应的控制措施。
首先,汽车覆盖件的材料选择是影响拉延起皱、开裂等问题的主要因素之一、不同材料的拉伸性能和耐热性能不同,这将直接影响覆盖件在汽车使用过程中的表现。
因此,在设计汽车覆盖件时,应选择具有较好拉伸性能和耐热性能的材料,以降低拉延起皱、开裂等问题的发生几率。
其次,汽车覆盖件的设计也是影响拉延起皱、开裂等问题的重要因素之一、覆盖件的设计应考虑到汽车在运行过程中所受到的各种力的作用,包括风压、振动等。
合理的结构设计可以减少应力集中,并降低覆盖件出现拉延起皱、开裂等问题的风险。
此外,覆盖件的加工工艺也应该注意到材料的拉伸性能,避免因加工过程中产生应力集中而引发问题。
另外,环境因素也会对汽车覆盖件的拉延起皱、开裂等问题产生一定的影响。
气候变化、温度变化等因素都会对覆盖件的性能造成影响。
在环境恶劣的地区,覆盖件容易受到紫外线的辐射、高温的影响,导致材料老化、脆化,从而引发拉延起皱、开裂等问题。
因此,应采取相应的措施来减轻环境因素对覆盖件的影响,例如使用防紫外线涂层、增加材料的耐候性等。
此外,汽车覆盖件的安装也是影响拉延起皱、开裂等问题的重要因素。
在覆盖件的安装过程中,如果安装不当、安装力度不均匀等,会导致覆盖件产生应力集中,进而引发问题。
因此,在安装覆盖件时需要遵循合适的安装方法,并确保安装力度均匀,以减少问题的发生。
综上所述,汽车覆盖件的拉延起皱、开裂等问题受到多种因素的影响,包括材料选择、设计、环境因素和安装等。
为了避免这些问题的发生,应选择耐热性能和拉伸性能较好的材料,进行合理的结构设计,并采取相应的措施来减轻环境因素的影响。
此外,在安装过程中需要注意安装方法和安装力度的均匀性。
浅谈汽车车身覆盖件深拉成形开裂问题分析
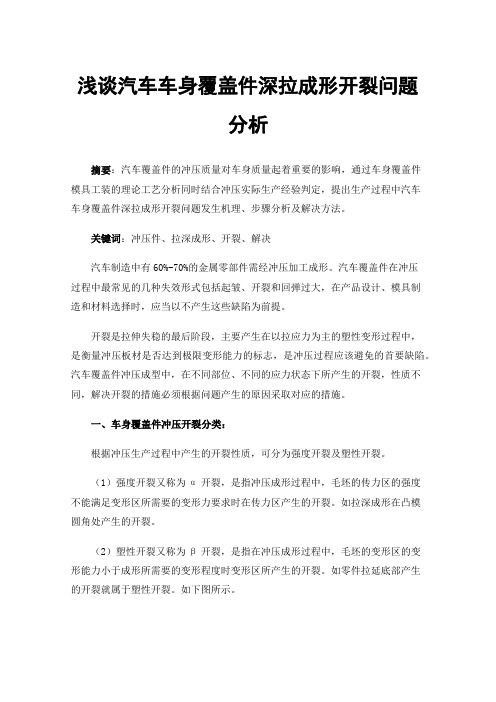
浅谈汽车车身覆盖件深拉成形开裂问题分析摘要:汽车覆盖件的冲压质量对车身质量起着重要的影响,通过车身覆盖件模具工装的理论工艺分析同时结合冲压实际生产经验判定,提出生产过程中汽车车身覆盖件深拉成形开裂问题发生机理、步骤分析及解决方法。
关键词:冲压件、拉深成形、开裂、解决汽车制造中有60%-70%的金属零部件需经冲压加工成形。
汽车覆盖件在冲压过程中最常见的几种失效形式包括起皱、开裂和回弹过大,在产品设计、模具制造和材料选择时,应当以不产生这些缺陷为前提。
开裂是拉伸失稳的最后阶段,主要产生在以拉应力为主的塑性变形过程中,是衡量冲压板材是否达到极限变形能力的标志,是冲压过程应该避免的首要缺陷。
汽车覆盖件冲压成型中,在不同部位、不同的应力状态下所产生的开裂,性质不同,解决开裂的措施必须根据问题产生的原因采取对应的措施。
一、车身覆盖件冲压开裂分类:根据冲压生产过程中产生的开裂性质,可分为强度开裂及塑性开裂。
(1)强度开裂又称为α开裂,是指冲压成形过程中,毛坯的传力区的强度不能满足变形区所需要的变形力要求时在传力区产生的开裂。
如拉深成形在凸模圆角处产生的开裂。
(2)塑性开裂又称为β开裂,是指在冲压成形过程中,毛坯的变形区的变形能力小于成形所需要的变形程度时变形区所产生的开裂。
如零件拉延底部产生的开裂就属于塑性开裂。
如下图所示。
二、开裂问题的理论控制技术分析解决开裂问题,要根据板材冲压变形对冲压件的形状尺寸特点进行详细的变形分析,判断开裂的性质和产生原因,采取针对性措施。
1.强度开裂控制分析强度开裂是传力区传力能力小于变形区毛坯产生的塑性变形和流动所需的力度而产生的,其根本原则就是要使传力区成为强区,变形区成为弱区,通过提高传力区的强度,同时或降低变形区的变形力等措施来解决。
2.塑性开裂理论控制技术分析解决塑性开裂的关键在于通过解决提高材料塑性变形能力,同时或降低变形区所需的变形量来解决塑性开裂问题。
上述是通过理论控制技术分析提出的改善车身覆盖件冲压成形解决方法,冲模设计加工装配后必须经过压力机批量生产对制件质量及模具性能进行综合检测。
汽车覆盖件拉伸起皱和开裂现象分析及控制措施

汽车覆盖件拉伸起皱和开裂现象分析及控制措施汽车覆盖件是指车体外部的保护罩、护板、保险杠、车窗边框、车门外套等部件,这些零件的功能是保护车身结构、增加车体整体美感和减少空气阻力。
然而,在汽车生产和使用过程中,这些覆盖件可能会出现拉伸起皱和开裂的现象。
本文将分析汽车覆盖件拉伸起皱和开裂的原因,并提出相应的控制措施。
首先,汽车覆盖件拉伸起皱和开裂的原因主要有以下几点。
1.材料质量差:汽车覆盖件的材料包括金属、塑料、橡胶等。
如果材料质量有缺陷,如材料硬度不足、脆性大、不耐老化等,就容易出现拉伸起皱和开裂现象。
2.制造工艺不当:汽车覆盖件的制造过程中,如果操作不当、工艺参数不合理,例如成型温度过高或过低、成型速度过快或过慢、冷却方式不当等,都会导致覆盖件的形变和开裂。
3.加工应力过大:在覆盖件的制造过程中,可能涉及到很多的压力和挤压过程,如果加工应力过大,就会导致覆盖件的强度降低,易发生起皱和开裂。
4.环境因素:汽车覆盖件在使用过程中,会受到各种环境因素的影响,包括温度变化、大气湿度、紫外线照射等。
这些因素会导致覆盖件材料的膨胀和收缩,引起拉伸起皱和开裂。
针对上述问题,可以采取以下控制措施来避免汽车覆盖件拉伸起皱和开裂。
1.优化材料选择:选择质量好、性能稳定的材料,确保材料硬度、韧性等物理性能符合要求。
此外,还可以使用耐老化、耐候性好的材料,提高覆盖件的耐用性。
2.优化制造工艺:合理控制制造过程中的温度、速度、压力等参数,确保覆盖件的成型质量。
可以使用模具加热、冷却等手段来控制成型温度和冷却速度,防止拉伸起皱和开裂。
3.优化加工工艺:合理控制加工过程中的压力和挤压过程,避免加工应力过大。
可以采用分次加工、轻加工等方法来减小加工应力,提高覆盖件的强度和稳定性。
4.增加外部保护措施:可以在覆盖件表面涂覆保护涂层,增加抗紫外线和防水性能,预防覆盖件的老化和开裂。
此外,可以增加覆盖件的厚度和加强结构设计,提高其抗拉伸能力。
{财务管理财务知识}汽车覆盖件拉伸起皱和开裂现象分析及控制措施
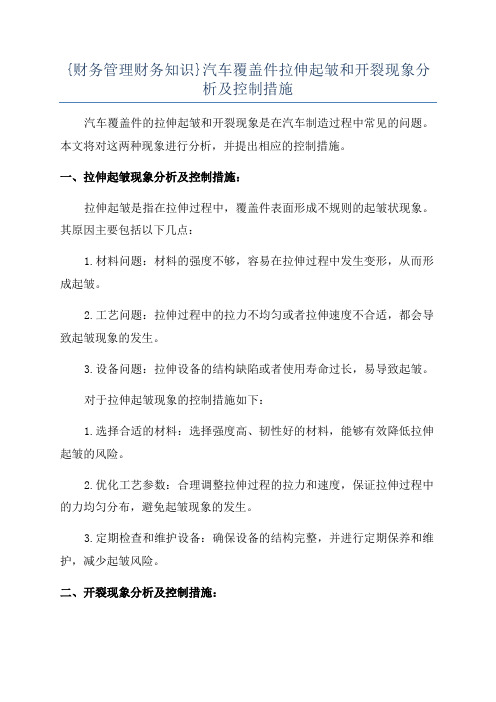
{财务管理财务知识}汽车覆盖件拉伸起皱和开裂现象分析及控制措施汽车覆盖件的拉伸起皱和开裂现象是在汽车制造过程中常见的问题。
本文将对这两种现象进行分析,并提出相应的控制措施。
一、拉伸起皱现象分析及控制措施:拉伸起皱是指在拉伸过程中,覆盖件表面形成不规则的起皱状现象。
其原因主要包括以下几点:1.材料问题:材料的强度不够,容易在拉伸过程中发生变形,从而形成起皱。
2.工艺问题:拉伸过程中的拉力不均匀或者拉伸速度不合适,都会导致起皱现象的发生。
3.设备问题:拉伸设备的结构缺陷或者使用寿命过长,易导致起皱。
对于拉伸起皱现象的控制措施如下:1.选择合适的材料:选择强度高、韧性好的材料,能够有效降低拉伸起皱的风险。
2.优化工艺参数:合理调整拉伸过程的拉力和速度,保证拉伸过程中的力均匀分布,避免起皱现象的发生。
3.定期检查和维护设备:确保设备的结构完整,并进行定期保养和维护,减少起皱风险。
二、开裂现象分析及控制措施:开裂是指覆盖件在拉伸过程中发生裂纹现象。
其原因主要包括以下几点:1.材料问题:材料的内部存在缺陷或者不均匀的晶粒结构,容易导致拉伸时发生裂纹。
2.工艺问题:拉伸过程中的拉伸速度过大或者拉力过高,都会产生应力集中,从而导致开裂。
3.设备问题:拉伸设备的结构问题或者设备的维护不当,容易引起开裂。
针对开裂现象的控制措施如下:1.选择质量好的材料:选择无明显缺陷并具有均匀晶粒结构的材料,能够有效降低开裂风险。
2.控制拉伸工艺参数:合理调整拉伸过程中的拉力和速度,控制应力集中的情况,减少开裂的可能性。
3.定期检查设备并进行维护:确保拉伸设备的结构完好,并且定期进行设备的维护保养,防止因设备问题导致的开裂。
综上所述,汽车覆盖件的拉伸起皱和开裂现象是在制造过程中容易出现的问题。
通过选择合适的材料、优化工艺参数以及对设备进行定期检查和维护,可以有效控制这两种现象的发生,提高汽车覆盖件的质量和使用寿命。
汽车覆盖件拉深分析及控制措施

2 . 合理增加工艺补加 a ) 采用 里紧外 松的原 则 。 在 凹模 口 覆盖件 大多形 状不规则 , 很 难满 足拉 延成形工艺 的要 求。 为了实现 直线 弯曲变 形 区和 伸长变 形 区应允许 压
拉深 , 避免 出现波纹 皱褶及 裂纹 , 便于后 续工序加 工, 往往要 在工件 的 料 面稍有里紧外松现象 。 基础 上增加 工艺补加部 分, 从而达 到满意 的拉深效 果。 例如 , 绝大 多数 b ) 通过调整 承压块的 高度 来调整间 这种方 法较上述 方法简单 , 但在实际 非封 闭形 状的零件都要 补成封闭形状 , 以利于材料 的流动, 既能增加 零 隙。 件的 刚性 , 又能保证零件在 拉深过程 中不 出现皱 褶等现象 。 合理的 工艺 生产中比较常用 。 补加应满足以下3 方面的要求: ( 5 ) 增加 工艺 凸包 。 起 皱现 象一般 都是 由于没有 或无法 控制料 的 ( 1 ) 工艺补加不仅要保证零件的成形 质量 , 还有 良好的工艺性 , 便于成 流动 , 造 成局部 材料 流动过快 堆积而成 的。 可以根 据皱 褶的特点 , 判 断
形。 ( 2 ) 工艺补加应保证压料面平缓 , 避免出现大的落差。 ( 3 ) 工艺补加应便 材料 的流向, 哪个 方向的料流动过快 , 即可在料流 动的初 始点增加 凸包 于后续的切 边和翻边 工序。 更多的 工艺补加就 是为了零件 的切边和翻 边 或凹坑 , 以增加此处 的流量 , 避 免料的堆 积出现 皱褶。 而增加的。 设计中应根据切边线的位 置确定工艺补加部分 的尺寸, 特 别是 ( 6 ) 调 整压 力机 。 压 力机气 垫的平 行度超 过 l mm, 就会影 响 零件 凹 模 圆角R 处, 直接关系到拉深件 的起皱或开裂 , 所以取值要合 理。 3 . 压料面形 状的确定 的成 形, 在调试前一定要检查 压力机气垫的平行度。 四, 总结
汽车前门内板拉伸起皱开裂问题分析与对策
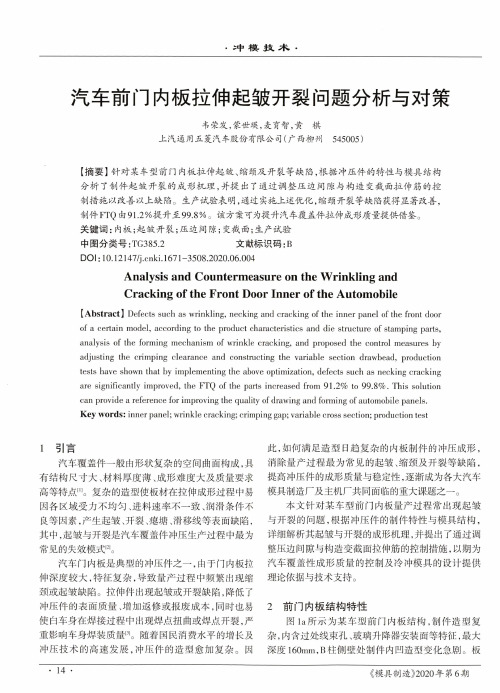
汽车前门内板拉伸起皱开裂问题分析与对策韦荣发,蒙世瑛,麦育智,黄棋上汽通用五菱汽车股份有限公司(广西柳州545005)【摘要】针对某车型前门内板拉伸起皱、缩颈及开裂等缺陷,根据冲压件的特性与模具结构 分析了制件起皱开裂的成形机理,并提出了通过调整压边间隙与构造变截面拉伸筋的控 制措施以改善以上缺陷。
生产试验表明,通过实施上述优化,缩颈开裂等缺陷获得显著改善,制件FTQ由91.2%提升至99.8%。
该方案可为提升汽车覆盖件拉伸成形质量提供借鉴。
关键词:内板;起皱开裂;压边间隙;变截面;生产试验中图分类号:TG385.2 文献标识码:BDOI:10.12147/ki. 1671-3508.2020.06.004Analysis and Countermeasure on the Wrinkling andCracking of the Front Door Inner of the Automobile【Abstract】Defects such as wrinkling, necking and cracking of the inner panel of the front door of a certain model, according to the product characteristics and die structure of stamping parts, analysis of the forming mechanism of wrinkle cracking, and proposed the control measures by adjusting the crimping clearance and constructing the variable section drawbead, production tests have shown that by implementing the above optimization, defects such as necking cracking are significantly improved, the FTQ of the parts increased from91.2% to99.8%. This solution can provide a reference for improving the quality of drawing and forming of automobile panels.Key words:inner panel; wrinkle cracking; crimping gap; variable cross section; production testi引言汽车覆盖件一般由形状复杂的空间曲面构成,具 有结构尺寸大、材料厚度薄、成形难度大及质量要求 高等特点11]。
拉伸件起皱的原因及处理方法
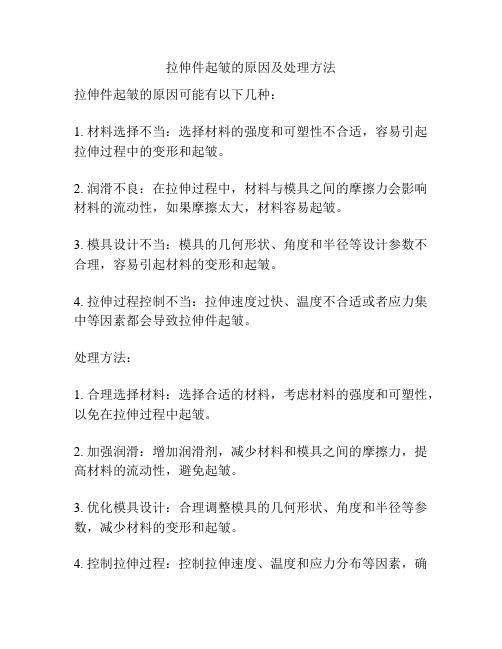
拉伸件起皱的原因及处理方法
拉伸件起皱的原因可能有以下几种:
1. 材料选择不当:选择材料的强度和可塑性不合适,容易引起拉伸过程中的变形和起皱。
2. 润滑不良:在拉伸过程中,材料与模具之间的摩擦力会影响材料的流动性,如果摩擦太大,材料容易起皱。
3. 模具设计不当:模具的几何形状、角度和半径等设计参数不合理,容易引起材料的变形和起皱。
4. 拉伸过程控制不当:拉伸速度过快、温度不合适或者应力集中等因素都会导致拉伸件起皱。
处理方法:
1. 合理选择材料:选择合适的材料,考虑材料的强度和可塑性,以免在拉伸过程中起皱。
2. 加强润滑:增加润滑剂,减少材料和模具之间的摩擦力,提高材料的流动性,避免起皱。
3. 优化模具设计:合理调整模具的几何形状、角度和半径等参数,减少材料的变形和起皱。
4. 控制拉伸过程:控制拉伸速度、温度和应力分布等因素,确
保拉伸过程中的稳定性,减少起皱的可能性。
5. 增加支撑和辅助结构:在拉伸件表面添加支撑和辅助结构,提高材料的稳定性,防止起皱。
汽车覆盖件拉伸起皱和开裂现象分析及控制措施_梁云荣
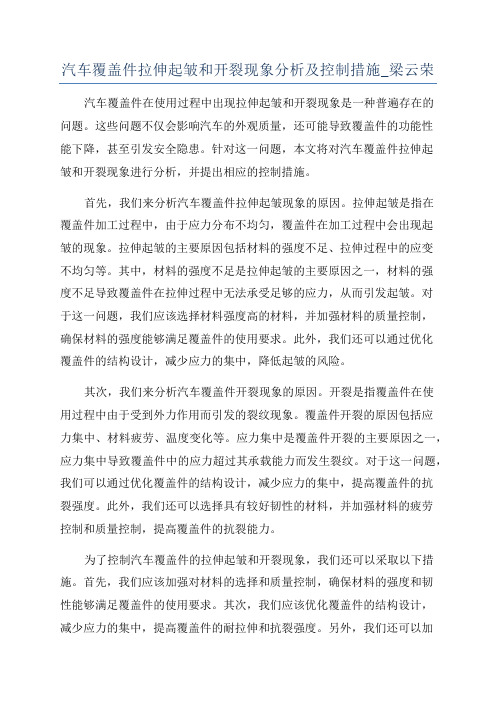
汽车覆盖件拉伸起皱和开裂现象分析及控制措施_梁云荣汽车覆盖件在使用过程中出现拉伸起皱和开裂现象是一种普遍存在的问题。
这些问题不仅会影响汽车的外观质量,还可能导致覆盖件的功能性能下降,甚至引发安全隐患。
针对这一问题,本文将对汽车覆盖件拉伸起皱和开裂现象进行分析,并提出相应的控制措施。
首先,我们来分析汽车覆盖件拉伸起皱现象的原因。
拉伸起皱是指在覆盖件加工过程中,由于应力分布不均匀,覆盖件在加工过程中会出现起皱的现象。
拉伸起皱的主要原因包括材料的强度不足、拉伸过程中的应变不均匀等。
其中,材料的强度不足是拉伸起皱的主要原因之一,材料的强度不足导致覆盖件在拉伸过程中无法承受足够的应力,从而引发起皱。
对于这一问题,我们应该选择材料强度高的材料,并加强材料的质量控制,确保材料的强度能够满足覆盖件的使用要求。
此外,我们还可以通过优化覆盖件的结构设计,减少应力的集中,降低起皱的风险。
其次,我们来分析汽车覆盖件开裂现象的原因。
开裂是指覆盖件在使用过程中由于受到外力作用而引发的裂纹现象。
覆盖件开裂的原因包括应力集中、材料疲劳、温度变化等。
应力集中是覆盖件开裂的主要原因之一,应力集中导致覆盖件中的应力超过其承载能力而发生裂纹。
对于这一问题,我们可以通过优化覆盖件的结构设计,减少应力的集中,提高覆盖件的抗裂强度。
此外,我们还可以选择具有较好韧性的材料,并加强材料的疲劳控制和质量控制,提高覆盖件的抗裂能力。
为了控制汽车覆盖件的拉伸起皱和开裂现象,我们还可以采取以下措施。
首先,我们应该加强对材料的选择和质量控制,确保材料的强度和韧性能够满足覆盖件的使用要求。
其次,我们应该优化覆盖件的结构设计,减少应力的集中,提高覆盖件的耐拉伸和抗裂强度。
另外,我们还可以加强对覆盖件加工过程的控制,减少加工过程中的应力积累,降低拉伸起皱和开裂的风险。
此外,定期维护和检查汽车覆盖件,及时发现和修复潜在的起皱和裂纹问题,也是控制这些问题的有效措施。
汽车覆盖件拉伸起皱和开裂现象分析及控制措施

汽车覆盖件拉伸起皱和开裂现象分析及控制措施来源:CAD世界网作者:梁云荣时间:2005-08-28 点击:3031、引言汽车车身外形是由许多轮廓尺寸较大且具有空间曲面形状的覆盖件焊接而成,因此对覆盖件的尺寸精度和表面质量有较高要求。
车身覆盖件要求表面平滑、按线清晰,不允许有皱纹、划伤、拉毛等表面缺陷,此外还要求具有足够的刚性和尺寸稳定性。
车身表面质量的好坏取决于覆盖件拉伸的结果,而拉伸模是拉出合格覆盖件的关键。
由于影响拉伸件质量的因索主要是起皱、开裂、拉毛和回弹,所以从编制冲压工艺到模具设计都必须认真考虑。
模具制造完毕,在拉伸模调试过程中,还必须对拉伸件的起皱和开裂现象进行仔细分析与研究,并采取相应的措施。
拉伸件在拉伸过程中起皱和开裂的原因很多,主要原因有以下几个方面:(1)拉伸模设计工艺性是否合理。
(2)模具加工质量(表面精度、硬度等)引起的问题。
(3)压力机精度(滑块平行度等)。
(4)板料质量(厚度超差)。
现对上述造成开裂、起皱的原因分别进行讨论。
2、拉伸件加工工艺的确定拉伸件的工艺性是编制覆盖件冲压工艺首先要考虑的问题,只有设计出一个合理的、工艺性好的拉伸件,才能保证在拉伸过程中不起皱、不开裂或少起皱、少开裂。
在设计拉伸件时不但要考虑冲压方向、冲压位置、压料面形状、拉伸筋的形状及配置、工艺补充部分等可变量的设计,还要合理地增加工艺补充部分,正确确定压料面。
各可变量设计之间又有相辅相成的关系,如何协调各变量的关系.是成形技术的关键,要使之不但满足该工序的拉伸,还要满足该工序冲模设计和制造工艺的需要,并给下道熔边、翻边工序创造有利条件,一般应注意以下几个方面。
2.1 冲压方向的确定零件的冲压方向是确定拉伸工艺首先要遇到的问题,它不但决定能否拉伸出满意的拉伸件,而且还影响到工艺补充部分的多少和压料面的形状。
合理确定冲压方向应满足以下3方面的要求。
(1)保证凸模能够进入凹模。
如图1a所示,凹模右方下边的形状向外凸出,最凸出点超过凹模口尺寸,使凸模不能进入凹模,这个拉伸方向是不能进行拉伸的,必须改变拉伸方向,使凸模能够进入凹模。
汽车覆盖件拉伸缺陷分析与整改实践
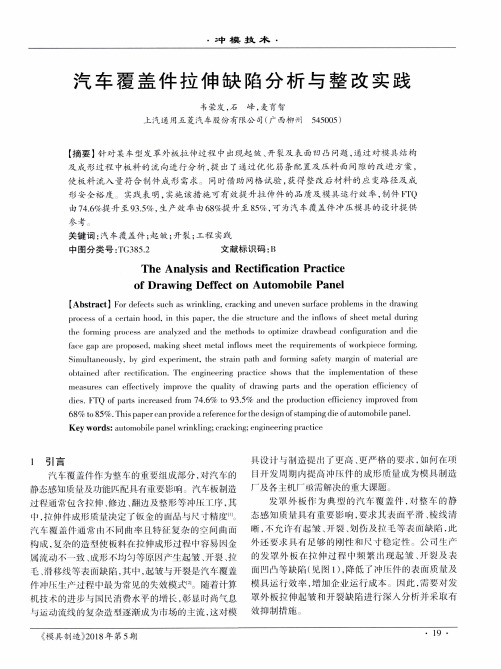
运 动 流 线 的 复 杂造 型 逐 渐 成 为 市场 的 主流 ,这 对 模 效 抑 措 施
参考
关 键 词 :汽 车 覆盖 件 ;起 皱 ;开 裂 ;工程 实践
中图 分类 号 :1"(;385.2
文 献标 识 码 :Ft
The Analysis and Rectification Practice of Drawing Def lect on Autom obile Panel
Ilies.FTQ of l::ml’ts in(.reased fl'Oi11 74.6% tc)93.5% dll cl the 1)rOdU(‘tion el’riciency inlI)roved fronl
68% … 85% .T11is f)aper can provide a reference tile design‘lfs!amping die of’illitonlobile pane1. Key words:a Lilomobile panel wrilikling;cracking;engin e P1’m‘g 【】I’a【 ti(。e
【Abstract】Fol’defects suc1 aS w1’inkling, l’8(·kingⅢ1tI LlneVl 11 Sill’ p problenls ill tile drawfllg
IlrIl【‘Pss ot’a(· tall1 l1‘J1)(1 in this paper tile(1 sh’Li e‘hll P Hll(I tim int’hm s‘lf sheet Ill( tal during tl1P { I1‘nlillg 1)r()(·P s Hl’P allalyzed tlll(]the metIlolls to ()I)tiluize {II’HW})1 ̄1tI‘‘(1l】Iigtu‘ati()ll t4ll C]die f l(‘P gap 1 P 1)l1Op()sell,nlaking sheet I1mtal inflows m eet ti re rP(1ull‘PI1lellIs of WOl kpie(’P fm’ru ing. SilIllIhaneously.J)y gi]’(I expel’i FnenI,the sh’ain path Ltlld f(1I’ruing saIely ma1 gl‘n I nlatel’ial are ()1)taine(I at'tel’re【·tification.The ellgineel’i Flg pl’a‘’ti c‘P llOWS that the implelnentation of‘these III( ̄HSLI rU'S 【·al1 effieclively il/iprove the qua卅 y ()f‘l{rauing I Is aⅢI ti re O1)Pl alion eficient} rIf
汽车覆盖件拉伸起皱开裂分析与控制

定期对设备进行 维护和检查,确 保设备处于良好 的工作状态。
加强员工培训,提 高员工对生产过程 中可能出现的异常 情况的敏感度和应 对能力。
建立完善的生产过 程监控体系,对生 产过程中的关键环 节进行实时监控和 记录。
定期进行设备维护和检查
定期进行设备维 护和检查,确保 设备处于良好状 态。
严格控制材料质 量,选用优质材 料,避免因材料 问题导致起皱开 裂。
复合材料:结合 多种材料的优点, 提高综合性能
新工艺研究:探 索新的加工工艺, 降低起皱开裂风 险
新型检测技术的研发与应用
介绍新型检测技术如红外线检测、超声波检测等在汽车覆盖件拉伸起皱开裂检测中的应用。
探讨新型检测技术的优势,如高精度、高效率、非接触等。
分析新型检测技术对汽车覆盖件拉伸起皱开裂控制的影响,如提高控制精度、降低生产成 本等。
湿度控制:保持生产环境的湿 度适中,避免过湿或过干。
清洁度控制:保持生产环境的 清洁度,避免灰尘、杂物等污 染汽车覆盖件。
空气质量控制:确保生产环境 中空气流通,避免有害气体和 异味影响汽车覆盖件的品质。
汽车覆盖件拉伸起皱开裂的预 防措施
加强生产过程监控
对生产过程中的各 个环节进行严格监 控,确保工艺参数 的稳定性和准确性。
汽车覆盖件拉伸起皱开裂会导致车辆的安全性能下降,增加交通事故的风险。
增加生产成本
增加生产成本:由于需要修复或更 换损坏的零件,导致生产成本增加。
损害品牌形象:汽车表面出现质量 问题,会损害品牌形象和消费者对 品牌的信任度。
添加标题
添加标题
添加标题
添加标题
降低产品质量:起皱和开裂会影响 汽车的外观和性能,降低产品质量。
汽车覆盖件拉伸起皱开裂与控制答案
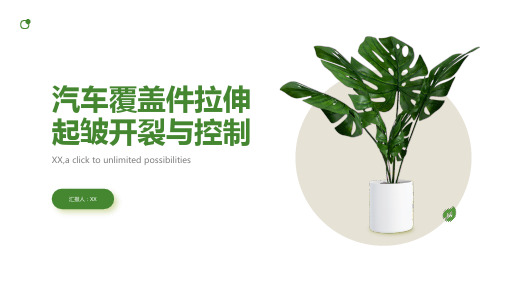
XX,a click to unlimited possibilities
汽车覆盖件拉伸起皱开裂与控制
目录
01
添加目录标题
02
汽车覆盖件拉伸起皱开裂的原因
03
汽车覆盖件拉伸起皱开裂的危害
04
汽车覆盖件拉伸起皱开裂的控制方法
05
汽车覆盖件拉伸起皱开裂的检测与评估
06
汽车覆盖件拉伸起皱开裂的预防措施
07
冲击测试:通过冲击试验机检测材料抵抗冲击的能力
硬度测试:检测材料的表面硬度和整体硬度
弯曲测试:评估材料在弯曲载荷下的性能表现
失效分析评估
检测方法:采用无损检测技术,如超声波检测、X射线检测等
失效判定:根据评估结果,判定汽车覆盖件是否失效,并确定相应的处理措施
预防措施:针对失效原因,采取相应的预防措施,以减少汽车覆盖件拉伸起皱开裂的风险
增加维修和更换成本
降低客户满意度和品牌形象
增加维修成本
降低车辆性能:由于部件的损坏,可能会导致车辆性能下降,例如油耗增加或动力下降。
引发安全问题:如果起皱和开裂涉及到重要的车身结构件,可能会影响车辆的安全性能,例如影响碰撞时的保护效果。
增加维修成本:由于需要修复或更换损坏的部件,导致维修费用增加。
强化质量检测:确保产品质量,减少缺陷
推行精益管理:优化流程,降低成本
07
汽车覆盖件拉伸起皱开裂的研究展望
加强基础理论研究
深入研究汽车覆盖件材料的力学性能,掌握其拉伸、起皱、开裂等行为的本质原因。
加强汽车覆盖件制造工艺的基础理论研究,探索更有效的工艺控制方法。
开展汽车覆盖件材料与工艺的跨学科研究,促进相关领域的交流与合作。
汽车覆盖件拉伸起皱开裂的研究展望
汽车覆盖件成形缺陷分析及控制措施
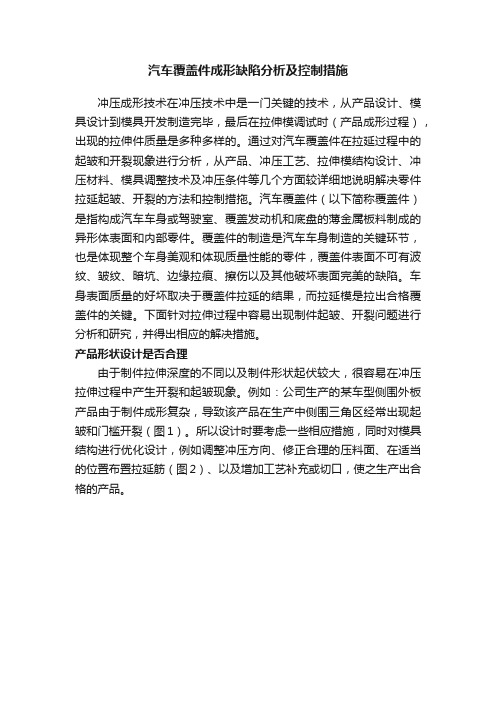
汽车覆盖件成形缺陷分析及控制措施冲压成形技术在冲压技术中是一门关键的技术,从产品设计、模具设计到模具开发制造完毕,最后在拉伸模调试时(产品成形过程),出现的拉伸件质量是多种多样的。
通过对汽车覆盖件在拉延过程中的起皱和开裂现象进行分析,从产品、冲压工艺、拉伸模结构设计、冲压材料、模具调整技术及冲压条件等几个方面较详细地说明解决零件拉延起皱、开裂的方法和控制措拖。
汽车覆盖件(以下简称覆盖件)是指构成汽车车身或驾驶室、覆盖发动机和底盘的薄金属板料制成的异形体表面和内部零件。
覆盖件的制造是汽车车身制造的关键环节,也是体现整个车身美观和体现质量性能的零件,覆盖件表面不可有波纹、皱纹、暗坑、边缘拉痕、擦伤以及其他破坏表面完美的缺陷。
车身表面质量的好坏取决于覆盖件拉延的结果,而拉延模是拉出合格覆盖件的关键。
下面针对拉伸过程中容易出现制件起皱、开裂问题进行分析和研究,并得出相应的解决措施。
产品形状设计是否合理由于制件拉伸深度的不同以及制件形状起伏较大,很容易在冲压拉伸过程中产生开裂和起皱现象。
例如:公司生产的某车型侧围外板产品由于制件成形复杂,导致该产品在生产中侧围三角区经常出现起皱和门槛开裂(图1)。
所以设计时要考虑一些相应措施,同时对模具结构进行优化设计,例如调整冲压方向、修正合理的压料面、在适当的位置布置拉延筋(图2)、以及增加工艺补充或切口,使之生产出合格的产品。
图1 门洞处开裂图2 更改双拉延筋解决拉延模设计工艺性是否合理覆盖件工艺性主要表现在冲压性能、焊接装配性能、操作安全性、材料消耗及性能的要求。
覆盖件的冲压性能,在多数情况下是以拉伸件为先决条件的。
拉伸过程中在设计拉延件时不但要考虑冲压方向、压料面形状、拉延筋形状及布置、工艺补充部分等设计,对于这些方面设计是相辅相成,也是成形技术的关键,所以覆盖件的拉伸模具工艺设计是非常重要的,这不但能决定产品拉伸好坏,而且给下道修边、翻边工序创造有利条件,对于覆盖件工艺设计一般应注意:⑴冲压方向的确定;⑵合理增加工艺补充部分;⑶压料面形状的确定;⑷工艺切口和工艺孔的设置。
浅析汽车覆盖件拉伸起皱开裂现象及控制措施
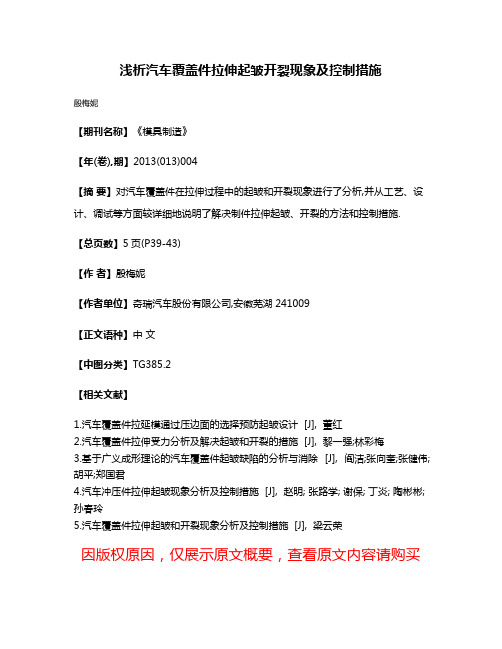
浅析汽车覆盖件拉伸起皱开裂现象及控制措施
殷梅妮
【期刊名称】《模具制造》
【年(卷),期】2013(013)004
【摘要】对汽车覆盖件在拉伸过程中的起皱和开裂现象进行了分析,并从工艺、设计、调试等方面较详细地说明了解决制件拉伸起皱、开裂的方法和控制措施.
【总页数】5页(P39-43)
【作者】殷梅妮
【作者单位】奇瑞汽车股份有限公司,安徽芜湖241009
【正文语种】中文
【中图分类】TG385.2
【相关文献】
1.汽车覆盖件拉延模通过压边面的选择预防起皱设计 [J], 董红
2.汽车覆盖件拉伸受力分析及解决起皱和开裂的措施 [J], 黎一强;林彩梅
3.基于广义成形理论的汽车覆盖件起皱缺陷的分析与消除 [J], 阎洁;张向奎;张健伟;胡平;郑国君
4.汽车冲压件拉伸起皱现象分析及控制措施 [J], 赵明; 张路学; 谢保; 丁炎; 陶彬彬; 孙春玲
5.汽车覆盖件拉伸起皱和开裂现象分析及控制措施 [J], 梁云荣
因版权原因,仅展示原文概要,查看原文内容请购买。
汽车覆盖件拉伸起皱开裂分析及控制..

汽车覆盖件拉延起皱开裂的影响因素及控制措施1引言以车身覆盖件为代表的冲压零件多由复杂的空间自由曲面组成,其成形时坯料上各部分的变形状态比较复杂 , 差别较大 , 各处应力也很不均匀,常出现破裂、起皱、波纹、扭曲、松弛、瘪塘等质量缺陷。
使得汽车覆盖件成为板料成形领域最难成形的零件。
有的浅复杂曲面零件,因在拉深过程拉深变形不充分而起皱,而且造成刚性不足。
为了防止起皱、增加刚性,可采取措施使压料面的材料减少流动或基本不动。
在这种情况下,零件的成形主要是依靠材料的局部变薄而成形的。
故其拉深变形特点基本上与局部变薄拉深相似。
有的零件由于在同一平面上拉深的深度不一致又不对称,沿周边各处变形不均匀,以致发生起皱和拉裂现象。
为了控制拉深过程中材料流动均匀、变形充分而又不出现起皱和拉裂,在冲压上采用的措施基本上是开流和限流。
开流就是在需要材料流动的地方减小阻力,使其顺利流动,以避免材料变薄甚至开裂。
限流就是在不需求材料流动的地方加大阻力,限制其流动,以免多余的材料产生波浪而发生起皱。
开流和限流的目的,都是为了合理控制板料流动,改善覆盖件成形时的力学条件,促使材料各处的变形均匀一致,保证坯料在拉延过程中不起皱,不破裂,提高零件的成形性。
拉延件的工艺性是编制覆盖件冲压工艺首先要考虑的问题,只有设计出一个合理的、工艺性好的拉延件,才能保证在拉延过程中不起皱、不开裂或少起皱、少开裂。
在设计拉延件时不但要考虑冲压方向、压料面形状、拉伸筋的形状等可变量的设计,还要合理地增加工艺补充部分。
各可变量设计之间又有相辅相成的关系,如何协调各变量的关系,是成形技术的关键,要使之不但满足该工序的拉延,还要满足该工序冲模设计和制造工艺的需要,并给下道修边、翻边工序创造有利条件。
2拉延方向的选择在车身覆盖件的工序设计中,拉延方向的选择为第一步,也是关键的一步。
它不但影响拉延时板料的流动和模具结构的设计,决定能否拉出合格的拉延件,而且影响到拉延件深度、压料面形状、工艺补充部分的设计甚至直接影响到后工序。
浅析汽车冲压覆盖件成形时开裂的原因及解决措施
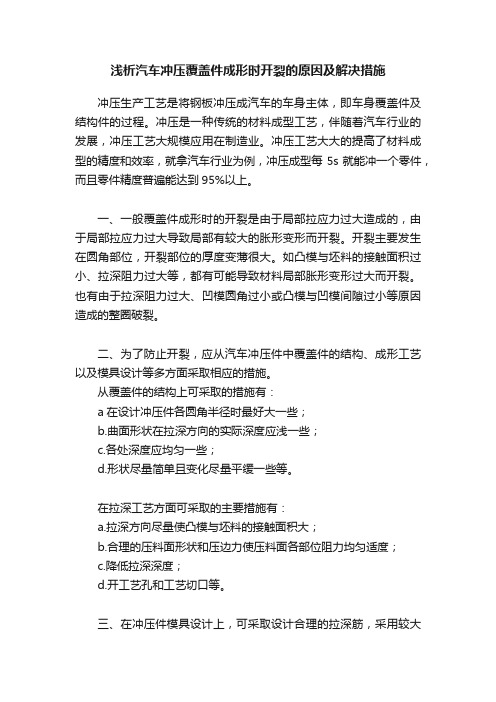
浅析汽车冲压覆盖件成形时开裂的原因及解决措施冲压生产工艺是将钢板冲压成汽车的车身主体,即车身覆盖件及结构件的过程。
冲压是一种传统的材料成型工艺,伴随着汽车行业的发展,冲压工艺大规模应用在制造业。
冲压工艺大大的提高了材料成型的精度和效率,就拿汽车行业为例,冲压成型每5s就能冲一个零件,而且零件精度普遍能达到95%以上。
一、一般覆盖件成形时的开裂是由于局部拉应力过大造成的,由于局部拉应力过大导致局部有较大的胀形变形而开裂。
开裂主要发生在圆角部位,开裂部位的厚度变薄很大。
如凸模与坯料的接触面积过小、拉深阻力过大等,都有可能导致材料局部胀形变形过大而开裂。
也有由于拉深阻力过大、凹模圆角过小或凸模与凹模间隙过小等原因造成的整圈破裂。
二、为了防止开裂,应从汽车冲压件中覆盖件的结构、成形工艺以及模具设计等多方面采取相应的措施。
从覆盖件的结构上可采取的措施有:a在设计冲压件各圆角半径时最好大一些;b.曲面形状在拉深方向的实际深度应浅一些;c.各处深度应均匀一些;d.形状尽量简单且变化尽量平缓一些等。
在拉深工艺方面可采取的主要措施有:a.拉深方向尽量使凸模与坯料的接触面积大;b.合理的压料面形状和压边力使压料面各部位阻力均匀适度;c.降低拉深深度;d.开工艺孔和工艺切口等。
三、在冲压件模具设计上,可采取设计合理的拉深筋,采用较大的模具圆角,使凸模与凹模间隙合理等措施。
四,使用合适的冲压拉伸油或者拉延油,降低开裂,减少浪费.水性拉延油以精制矿物油为基础油,添加抗磨极压剂、防锈剂、润滑剂、抗氧剂、其他助剂等调合而成。
产品广泛适用于汽车覆盖件、车门、车箱等压延成型工艺和碳钢、板材的压延成型加工。
能有效减少工件与模具的摩擦,降低磨损,具有强韧的油膜。
可有效减少划痕、划伤、烧结焊合、破裂等现象的发生。
有助于金属的滑动,利于成型。
具有良好的脱模性能,无卡咬,确保工件边缘光滑无毛刺。
且在高温状态下具有良好的热稳定性。
良好的光洁功能,提高加工精度,保护模具,延长模具寿命。
- 1、下载文档前请自行甄别文档内容的完整性,平台不提供额外的编辑、内容补充、找答案等附加服务。
- 2、"仅部分预览"的文档,不可在线预览部分如存在完整性等问题,可反馈申请退款(可完整预览的文档不适用该条件!)。
- 3、如文档侵犯您的权益,请联系客服反馈,我们会尽快为您处理(人工客服工作时间:9:00-18:30)。
汽车覆盖件拉延起皱开裂的影响因素及控制措施1 引言以车身覆盖件为代表的冲压零件多由复杂的空间自由曲面组成,其成形时坯料上各部分的变形状态比较复杂,差别较大,各处应力也很不均匀,常出现破裂、起皱、波纹、扭曲、松弛、瘪塘等质量缺陷。
使得汽车覆盖件成为板料成形领域最难成形的零件。
有的浅复杂曲面零件,因在拉深过程拉深变形不充分而起皱,而且造成刚性不足。
为了防止起皱、增加刚性,可采取措施使压料面的材料减少流动或基本不动。
在这种情况下,零件的成形主要是依靠材料的局部变薄而成形的。
故其拉深变形特点基本上与局部变薄拉深相似。
有的零件由于在同一平面上拉深的深度不一致又不对称,沿周边各处变形不均匀,以致发生起皱和拉裂现象。
为了控制拉深过程中材料流动均匀、变形充分而又不出现起皱和拉裂,在冲压上采用的措施基本上是开流和限流。
开流就是在需要材料流动的地方减小阻力,使其顺利流动,以避免材料变薄甚至开裂。
限流就是在不需求材料流动的地方加大阻力,限制其流动,以免多余的材料产生波浪而发生起皱。
开流和限流的目的,都是为了合理控制板料流动,改善覆盖件成形时的力学条件,促使材料各处的变形均匀一致,保证坯料在拉延过程中不起皱,不破裂,提高零件的成形性。
拉延件的工艺性是编制覆盖件冲压工艺首先要考虑的问题,只有设计出一个合理的、工艺性好的拉延件,才能保证在拉延过程中不起皱、不开裂或少起皱、少开裂。
在设计拉延件时不但要考虑冲压方向、压料面形状、拉伸筋的形状等可变量的设计,还要合理地增加工艺补充部分。
各可变量设计之间又有相辅相成的关系,如何协调各变量的关系,是成形技术的关键,要使之不但满足该工序的拉延,还要满足该工序冲模设计和制造工艺的需要,并给下道修边、翻边工序创造有利条件。
2 拉延方向的选择在车身覆盖件的工序设计中,拉延方向的选择为第一步,也是关键的一步。
它不但影响拉延时板料的流动和模具结构的设计,决定能否拉出合格的拉延件,而且影响到拉延件深度、压料面形状、工艺补充部分的设计甚至直接影响到后工序。
有些形状复杂的拉延件往往会因为冲压方向选择不当,而拉延不出合格的拉延件,只好改变冲压方向,这将造成整个拉延模的报废,同时还将波及其他工序模具是否修改或重新设计制造。
所以,拉延方向是覆盖件冲压设计中影响范围广的工艺参数之一,拉延时的冲压方向必须周密考虑后确定。
2.1 开始拉延时应尽量使凸模与毛坯的接触状态良好,使各侧边流入凹模的材料均匀。
当凸模与坯料为点接触时,应适当增大接触面积,防止材料因应力集中而造成局部破裂,如图2-1a 。
但也要避免凸模表面与坯料以大平面接触的,否则由于平面上的拉应力值降低,材料得不到充分的塑性变形,影响零件的刚性,并容易起皱。
凸模与毛坯接触的地方应尽量靠近中间,如图2-1b凸模与毛坯的接触点要多而分散,并尽可能分布均匀,防止坯料窜动,如图2-1c2.2 拉延方向的选择应使压料面各部位进料阻力均匀 拉延深度是保证压料面各部位进料阻力的主要条件,因此,选择拉延方向时,应保证拉延深度均匀,深度合理,如图2-2。
2.3 拉延方向有利于后工序的加工设计拉延件形状还必须考虑后工序的加工难度,现以一个零件为例说明: 图2-3为一左右对称冲压加工的零件,若按(a )图的合并所决定的拉延方向,则造成零件拉延深度较深,容易拉毛,而且修边困难;若按图(b )、(c )的形式合并后所决定的冲压方向进行拉延,需拉延两次,拉延深度变浅,修边加工容易,其实仔细分析方案(b )、(c )可以看出,(b )在拉延时,从压料面上补充进材料较为困难,材料容易产生局部变形,而且在冲孔时,斜锲布置空间紧张,而(c )则无上述问题。
图2-1 凸模开始拉延与毛坯的接触状态2.4 应保证凸模能将零件需拉深的部位在一次拉延中完成,不应有凸模接触不到的死角或死区,即尽量使拉深件形状能一次拉深成形。
3 工艺孔和工艺切口当覆盖件的中间部位或成双拉深的连接部位,由于拉深过程中不能从毛坯的外部得到材料的补充而导致零件的局部破裂时,可考虑在工艺补充的适当部位冲出工艺孔或工艺切口,使容易破裂的区域得到材料的补充,克服开裂现象。
如图3-1是D310车型左/右侧边梁,其采用成双拉延的形式生产,但由于中间联结处深度与宽度的比值较大,成型困难,用AUTOFORM模拟时反成型的R部位开裂,在反成型的中间废料部位需增加两处工艺孔,以使材料向外流动。
工艺切口必须设置在容易破裂的区域附近,而这个切口必须布置在工艺补充上,修边线以外,在修边冲孔时将它们冲掉。
工艺切口一般在成形过程中切出,它可充分利用材料的塑性,即在成形开始阶段利用材料径向延伸,然后切出工艺切口,利用材料切向延伸,这样成形深度可以深一些。
在成形过程中切工艺切口时,并不希望切割材料与制件本体完全分离,切口废料可在以后的修边工序中一并切除。
否则,将产生从冲模中清除废料的困难。
工艺切口图3-1 左/右侧边梁反成型处增加工艺切口工艺孔一般在拉深前的落料冲孔工序中完成,如D310车型门里板的侧窗处。
图3-2 门里板的落料冲孔毛坯工艺切口、工艺孔的布置及其大小和形状要视其所处的区域情况和其向外补充材料的要求而定。
一般应注意以下几点:(1)切口应与制件局部形状相适应,以使材料合理流动。
(2)切口之间应留有足够的搭边,以使凸模张紧材料,保证成形清晰,避免波纹等缺陷,而且修边后可获得良好的窗口、翻边、孔缘质量。
(3)工艺切口在拉深过程中冲出时,要注意冲孔的时间,如果过早切口会使拉深件出现皱纹;太晚则达不到切口的目的。
(4)切口或冲孔的数量、大小和形状,要根据所处的位置和变形要求,通过试料来确定。
(5)切口的切断部分应临近容易破裂的区域,使各处材料变形趋于均匀,否则不一定能防止裂纹产生。
4 压料面的选择在复杂曲面大型零件的拉深与成形中,在模具上都要设有压料面。
压料面是工艺补充部分的一个组成部分,即凹模圆角半径R 凹以外的一部分。
凸模对坯料开始拉深前,压料圈将拉深坯料压紧在凹模压料面上。
压料面的形状不但要保证压料面上的材料不皱,而且应尽量造成凸模下的材料能下凹以降低拉延深度,并保证拉入凹模里的材料不皱不裂。
压料面一般有两种:一种是压料面就是零件本身的法兰面,另一种则是由工艺补充部分而形成,压料面的形状多数是曲面的。
选择压料面的原则:1)压料面应尽量平整,不能有鼓起、凹坑和皱褶,在坯料被压紧时,应不产生折皱。
2)压料面应尽量处于水平位置。
这样有利于金属流动,便于拉深工作,如图4-1所示。
3)压料面应与凸模的形状保持一定几何关系,保证在拉深过程中,坯料始终处于张紧状态,并能平稳地、逐次地包拢凸模,以防产生裂纹及皱纹。
因此压料面在展开后应保证如下关系:L>L1 β>α式中 L ——凸模表面展开长度;L1——压料面展开长度;α—凸模表面夹角,α<180°; β—压料面平面夹角,β<180°。
如图4-2所示为压料面展开长度比凸模表面展开长度短(L>L1)示意图。
这样凸模对毛坯可以拉深,但还不一定保证最后不形成波纹及起皱。
如图4-3所示的压料面形状,虽然L>L1,但压料面夹角β比凸模表面夹角α小,因此凸模从开始拉深到最后的过程中,几个瞬间位置的压料面展开长度比凸模表面展开长度长,形成的皱纹比较大。
故这样的压料面是不能采用的。
故防皱条件是:L>L1及β>α。
若不能满足这一条件,要考虑改变压料面,或在拉深件底部设置筋或反成形形状吸收余料。
图4-1 压料面与拉深方向 的相对位置 1-压料圈 2-凹模 3-凸模 图4-2 压料面展开长度 与凸模表面展开长度比较图4-3 压料面形状4)压料面应使成形深度小且各部分深度接近一致。
这种压料面可保证各部分进料阻力均匀,使材料流动和塑性变形趋于均匀,减小成形难度。
进料阻力不均匀,在拉深过程中毛坯可能沿凸模顶部窜动,严重时会产生破裂和皱纹。
而达到进料阻力均匀的一个前提条件就是拉深深度均匀。
5)压料面应使毛坯在拉深成形和修边工序中都有可靠的定位,并考虑送料和取料的方便。
在实际工作中,上述各项原则不能同时达到时,应根据具体情况决定取舍。
5. 工艺补充形状覆盖件的形状复杂,结构不对称,为了获得成形性良好的拉延件,有时需将覆盖件上的翻边展开,将孔补满,再加上工艺补充部分使覆盖件形成一个封闭的零件,通过这些措施,使覆盖件的成形条件得到改善,从而保证覆盖件的拉延质量。
但是,因为拉延后要将工艺补充部分修掉,所以要在能够拉延出满意的拉延件的条件下,尽可能地减少工艺补充部分,降低材料消耗。
5.1 拉延台阶的设定拉延台阶属于工艺补充设计的一个重要内容,它具有以下作用:1)若按覆盖件凸缘设定压料面,就可能使压料面凸凹不平,当深度差剧烈时,会出现开裂、起皱现象,设定拉延台阶,可获得加工性良好的压料面,利于成形质量。
2)对于一些覆盖件,其侧壁易出现体皱纹,滑伤、冲击线、翘曲、松弛等缺陷,解决这些缺陷的办法,一般是通过拉延台阶,使材料充分变形。
3)在后工序中,零件次村往往在修边时,零件与模具形状不易重合,设定拉延台阶有利于零件定位,同时可将那些需要斜锲修边的地方,改成垂直修边。
5.2 拉延台阶高度和宽度的关系图5-1表示了拉延台阶在拉延过程中的情况:W>H:即拉延台阶宽,其效果减弱,故易出现冲击线和滑伤。
W≈H:为理想的拉延台阶。
W<H:即拉延台阶相对于深度大,材料在凸模与凹模的约束中,会在加工是出现破裂。
5.3 几个案例图5-2所示的零件边缘有很大的高差,故设定了拉延台阶,压料面的形状得到了缓和,成形效果较好。
但将压料面完全取成平面,则会在零件后部R处也会出现拉延台阶,R处将出现皱纹,同时台阶相对其宽度较深,反而不利于拉延。
图5-3所示零件周围边缘的修边形状凸凹不规矩,可通过设定拉延台阶,得到平坦的压料面。
图5-4所示碟形零件,修边时,拉延件不易与模具重合,设计拉延台阶利于修边时定位,而且台阶设定后,材料变形充分,零件刚性好,不易回弹。
必须注意的是,圆角R易出现皱纹,因此,R1<R2,这对防止皱纹出现是重要的。
图5-5所示零件,冲击线较易出现在零件侧壁,对外观质量有所影响,若增设拉延台阶,可扩大凹模口,使冲击线出现在零件的底部,同时产生较强的拉力。
总之,应根据覆盖件的具体情况,综合考虑压料面、拉延深度、拉延方向等诸多因素,上述设定拉延台阶方法,只是工艺补充方面一些典型的例子,在实际工作,还需灵活掌握应用。
6 拉延筋技术6.1 拉延筋的作用拉延筋是板料拉深成形中的主要控制手段之一,较之其它控制手段具有简单方便,易于实现等优点。
它能更加稳定、有效、灵活、均匀地控制压料力。
随着冲压制件的复杂程度和难度的不断增加,拉深筋的设置和调整已成为拉深模具设计及试模过程中的关键技术。