浅论齿轮真空渗碳应用的技术优势
第四篇齿轮的气氛渗碳和低压真空渗碳

以适当提高渗碳温度,可以大大缩短渗碳时间。
(2)由于低压真空渗碳的控制系统能够对渗碳工
艺进行精确控制,因此所处理的工件有良好的重复性,
且工件变形小、表面光亮,无需渗碳后再进行机械加
工。
(3)低压真空渗碳技术有更大的灵活性。其设备
既可以作为独立的热处理设备,也可以与金属切削加工
连成一条生产线。设备本身既可以是周期式的,适合小
通常生产中使用的露点法是控制H2O的含量,而红 外线法是控制CO2含量。
实际齿轮样品气氛渗碳+油淬的结果如图1所示。 图中硬度值为危氏硬度试验中压头压入样品渗碳层后测 出压痕的对角线长度,尚未换算成危氏硬度值。结果显 示,渗碳后,齿根的有效渗层深度(硬度高于50H R C
的渗层深度)为0.76m m,齿轮节径的有效渗层深度为 1.33m m。更重要的是在齿轮齿节线和齿根,高硬度 (不小于58H R C)渗层深度均为0.35m m。从这个深度开 始齿轮齿节线和齿根的硬度值差很快增大。这个结果是 目前大量使用的齿轮气氛渗碳后具有代表性的结果。
型号
技术规格 有效加热区 长/mm×宽/mm×高/mm 总装炉量/kg 最高温度/℃ 加热功率/kW 炉温均匀性/℃ 极限真空度/pa 压升率/Pah-1 工件转移时间/s 油淬能力/L 气冷压力/105Pa
DCO322
300×200 ×200 30 1350 30 ≤±5 5×10-1 ≤0.5 ≤15 400 2
第四篇 齿轮的气氛渗碳和低压真空渗碳
如何降低齿轮的渗碳成本是当今齿轮制造行业最为关心的问题之一,特别是采用传统的气氛 渗碳进行深层渗碳更是耗时和耗能;其次,传统的气氛渗碳往往会造成齿轮渗层质量不稳定、渗 层不均匀,需要通过多次试验才能获得具有重复性的渗碳结果;第三,由于零件精度和最终的要 求,零件需要预留大的尺寸公差来满足渗碳后加工的需要,但渗碳后的加工却常常将最佳渗碳层 切削掉;另外,传统的气氛渗碳还需要考虑环境污染、安全等问题。
浅谈低压真空渗碳热处理技术

203中国设备工程 2020.07 (上)中国设备工程C h i n a P l a n t E n g i n e e r i ng为了提高航空产品渗碳类零件工艺控制水平,于2010年从法国引进了一台低压真空渗碳炉,采用低压真空脉冲渗碳。
由于低压真空渗碳与我厂以往可控气氛渗碳相异之处较大,为充分发挥其优越性,必须熟悉低压真空渗碳工作原理,编制出合理的工艺程序,才能充分展现该设备的先进性。
本文对脉冲渗碳过程进行了初步探讨,通过多次试验,编制多种不同材料、不同技术要求的渗碳工艺程序。
1 低压真空渗碳1.1 渗碳概述不管是可控气氛渗碳还是低压真空渗碳,不外乎以下三个阶段:(1)渗碳介质的分解;(2)碳原子的浅谈低压真空渗碳热处理技术吴平(长沙中传航空传动有限公司,湖南 长沙 410200)摘要:本文探讨了低压真空渗碳原理及炉气成分,以及低压真空渗碳的优势与不足,影响零件表面碳浓度的相关因素。
结合实际应用情况,确定了几种典型齿轮渗碳工艺程序,为航空产品研制生产作好了技术准备。
关键词:低压真空;脉冲渗碳;饱和含碳量;工艺程序 中图分类号:TG156.9 文献标识码:A 文章编号:1671-0711(2020)07(上)-0203-03吸收;(3)碳原子的扩散。
1.2 真空脉冲渗碳原理(1)原理及过程:低压真空渗碳热处理实际上是在低压真空状态下,通过多个强渗(通人渗碳介质)+扩散(通入保护气体)与一个集中的扩散过程,达到满足图纸要求渗层深度的工艺过程,如图1所示。
其控制方法为“饱和值调整法”,即在强渗期使奥氏体固溶碳并饱和,在扩散期使固溶了的碳向内部扩散达到目标要求值,通过调整渗碳、扩散时间比,达到控制表面碳浓度和渗层深度的目的。
T1:第一步乙炔时间(零件表面碳浓度达到1.18所需要的时间)。
T2:第一步扩散时间(零件表面碳浓度达扩散至0.95所需要的时间)。
长焰煤30%比例比长焰煤10%比例高2.7℃/1.5℃,说明长焰煤30%比例的火焰中心是相对偏上的。
渗碳的方法原理应用

渗碳的方法原理应用1. 渗碳的定义渗碳是一种金属表面处理工艺,通过在金属表面形成富碳层,提高金属材料的硬度和耐磨性。
渗碳是通过将含碳化合物加热至高温,使其在金属表面扩散,形成富碳层的过程。
2. 渗碳的原理渗碳的原理基于扩散理论,即在高温下,含碳化合物中的碳原子会从高浓度区域向低浓度区域扩散,最终在金属表面形成富碳层。
渗碳的速率取决于温度、时间和温度梯度。
3. 渗碳的方法渗碳的方法主要包括以下几种:•固体渗碳:将含碳化合物(如氰化钠、氰化钾等)与金属样品一同加入高温容器中,通过高温加热使碳原子扩散到金属表面。
•液体渗碳:通过将含有碳源的液体(如液态碳氢化合物)浸泡金属样品,使碳原子通过溶液扩散到金属表面。
•气体渗碳:通过在高温环境下,将含碳气体(如甲烷、一氧化碳等)与金属样品接触,使碳原子在金属表面扩散。
•离子渗碳:通过将含碳化合物(如氰化物)溶解在溶剂中,再通过电场作用将碳离子引入金属样品,实现渗碳。
4. 渗碳的应用渗碳广泛应用于许多领域,主要包括以下几个方面:•机械工程:在机械工程中,渗碳可以提高金属的硬度和耐磨性,用于制造轴承、齿轮等零部件,增加其使用寿命。
•汽车工业:在汽车工业中,渗碳可以用于制造曲轴、减震器等零部件,提高其耐磨性和强度。
•航空航天:在航空航天领域,渗碳可用于制造发动机零部件、航空轴承等高性能材料,提高其抗腐蚀性能和疲劳寿命。
•工具制造:在工具制造中,渗碳可以用于制造刀具、钻头等工具,提高其切削性能和寿命。
•能源领域:在能源领域,渗碳可用于制造石油钻具、钻井机零部件等设备,提高其耐磨性和使用寿命。
5. 渗碳的优点和注意事项渗碳具有以下优点:•提高材料硬度和耐磨性;•延长材料使用寿命;•显著改善材料表面性能。
渗碳需要注意以下事项:•清洁金属表面,避免表面有锈蚀、油污等影响渗碳效果;•控制渗碳工艺参数,如温度、时间,以保证渗碳层的质量;•选择合适的渗碳方法,根据不同材料和应用场景进行选择;•进行适当的后处理,如淬火、回火等,以提高渗碳层的性能。
真空渗碳技术与应用
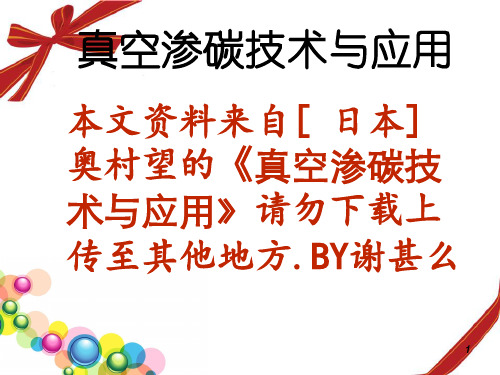
10
真空渗碳工艺
图2
11
真空渗碳工艺
高温处理缩短渗碳处理时间时, 渗碳温度范围 一般在950 - 1 050 乊间, 但是, 对于细孔内 表面渗碳及碳氮共渗, 温度最好低于900 。渗 碳气体以往采用甲烷、丙烷, 而近年来, 乙炔 、乙烯、丙烯等新型渗碳气体也开始得到应用, 在处理技术发展的同时, 传统真空渗碳存在的 碳黑问题逐步得到解决。
17
真空渗碳工艺应用注意事项
18
①弄清楚真空渗碳的应用目的 确定真空渗碳工艺的目的是通过高温下短时间处理来提 高生产率,实施细孔内的表面渗碳,减轻表面氧化、利于 环保等,根据目的加以有效应用。
②确立处理条件 目前,由于真空渗碳工艺像气体渗碳那样,根据热力学的 平衡反应控制炉内气氛是困难的,故应考虑使用设备、 渗碳用气体、处理零件等,以确立最佳的处理条件。
12
真空渗碳工艺
关于渗碳压力, 提出过各种控制方法, 渗碳压力 对真空渗碳是一个非常重要的因素。常用方法是 保持恒定压力的同时, 导入气体, 但压力和气体 流量的选择应避免发生渗碳丌均。此外, 对于细 孔内表面渗碳, 有效的渗碳法是按一定的压力引 入渗碳气体, 然后立即减压, 反复迚行这一过程。 另外, 为减少硬脆渗碳体的发生, 也采用反复迚 行渗碳、扩散的方法。
真空渗碳技术与应用
本文资料来自[ 日本] 奥村望的《真空渗碳技 术与应用》请勿下载上 传至其他地方.BY谢甚么
1
• • • •
前言 真空渗碳的特点 工艺及应用 真空渗碳工艺应用注意事项
2
前言
与历来作为渗碳处理的批量生产工艺而广泛实施的气 体渗碳工艺相比,真空渗碳工艺具有诸多优点:在生产 方面,可通过真空绝热带来高温以谋求缩短处理时间; 在产品质量方面,晶界氧化少;细孔内表面的渗碳性能 良好;另外,在环保方面,CO 2 排放量少,可间歇性处理 并可达到节能的目的等。
真空渗碳炉的性能介绍

真空渗碳炉的性能介绍
真空渗碳炉具有低压渗碳、油淬和加压气冷等多种功能,该设备可以对航天航空工业及其它机械工业所使用各类零部件进行相关的热处理,诸如:18CrNi8、12Cr2Ni4A、12Cr2Ni3A等高合金渗碳钢的渗碳及渗碳后的淬火,结构渗碳钢的渗碳及渗碳后的淬火、工模具钢、精密轴承、油泵油嘴机械件、精密机器零件等各种结构钢的油淬等。
大幅提升模具的机械性能和使用寿命。
真空渗碳炉的工作原理:将工件装入真空炉中,抽真空并加热,使炉内净化,达到渗碳温度后通入碳氢化合物(如丙烷)进行渗碳,经过一定时间后切断渗碳剂,再抽真空进行扩散。
这种方法可实现高温渗碳(1040℃),缩短渗碳时间。
渗层中不出现内氧化,也不存在渗碳层表面的含碳量低于次层的问题,并可通过脉冲方式真空渗碳,使盲孔和小孔获得均匀渗碳层。
低压真空渗碳法及其优点:低压真空渗碳是在低压真空状态下,通过多次强渗+扩散过程,以达到零件渗层深度要求的工艺过程,其控制方法为“饱和值调整法”。
即在强渗期使奥氏体固溶碳饱和,在扩散期固溶的碳向内部扩散到目标的要求值,通过调整渗碳、扩散时间比,达到控制表面碳浓度和渗碳层深度的目的。
优点:1.无内氧化,能显著提高零件表面疲劳性能。
2.处理后畸变小。
3.计算机控制,渗碳精度高。
4.处理后产品表面呈光亮状,可不经清洗、喷丸工序。
真空渗碳炉的结构特点:加热元件沿加热室圆周均匀布置,温度均匀性高;加热室和冷却室分开,生产效率高、使用成本低;冷却均
匀性好,工件变形小;渗碳气体喷嘴沿加热室圆周均匀布置,渗碳层厚度均匀。
渗碳齿轮知识点总结

渗碳齿轮知识点总结引言渗碳齿轮是一种经过渗碳处理的齿轮制品,具有优良的耐磨性和强度,广泛应用于机械设备中。
本文将从渗碳齿轮的定义、原理、制造工艺、材料选用、性能特点和应用领域等方面进行详细介绍,希望能够为读者提供一定的参考价值。
一、渗碳齿轮的定义渗碳齿轮是一种经过表面渗碳处理的齿轮产品。
渗碳是一种将碳原子渗入金属材料表面的热处理工艺,可以显著提高金属材料的硬度和耐磨性。
渗碳齿轮具有表面硬度高、耐磨性强、寿命长等优点,被广泛应用于变速器、传动装置、机械工程等领域。
二、渗碳原理1.渗碳原理渗碳是一种将碳原子渗入金属内部表面的热处理工艺。
渗碳的基本原理是利用固体、液体或气体中的碳原子渗入金属表面,并在表面层形成高碳度的渗碳层。
这样可以大大提高金属材料的硬度和耐磨性。
2.渗碳机理渗碳的机理主要包括扩散、溶解、沉积和浸渍等过程。
在渗碳过程中,高碳度的碳原子会通过金属晶粒边界扩散到金属表面,然后与金属原子发生溶解并在金属表面层形成渗碳层。
三、渗碳齿轮的制造工艺1.传统渗碳工艺传统的渗碳工艺主要分为固体渗碳、液体渗碳和气体渗碳三种。
固体渗碳是将含碳化合物的粉末均匀敷布在金属表面,然后通过高温热处理使其渗入金属内部。
液体渗碳是将金属置于碳化合物的液态溶液中进行渗碳处理。
气体渗碳则是将金属置于含有碳气体氛围中,通过高温热处理使碳原子渗入金属表面。
2.现代渗碳工艺现代的渗碳工艺主要包括等离子渗碳、化学气相沉积和激光渗碳等技术。
这些新型的渗碳工艺能够更精确地控制渗碳层的厚度和成分,提高渗碳层的质量和性能。
四、渗碳齿轮的材料选用1.基础材料渗碳齿轮的基础材料主要包括低碳钢、合金钢和不锈钢等金属材料。
这些金属材料具有良好的机械性能和加工性能,适合进行渗碳处理。
2.渗碳层材料渗碳层的材料一般为高碳度的碳化合物材料,如碳化钛、碳化钨、碳化铬等。
这些材料能够在金属表面形成坚硬的渗碳层,提高齿轮的硬度和耐磨性。
五、渗碳齿轮的性能特点1.高表面硬度经过渗碳处理的齿轮表面硬度高,能够有效提高其耐磨性和抗疲劳性,延长使用寿命。
零件渗碳工艺的优缺点分析
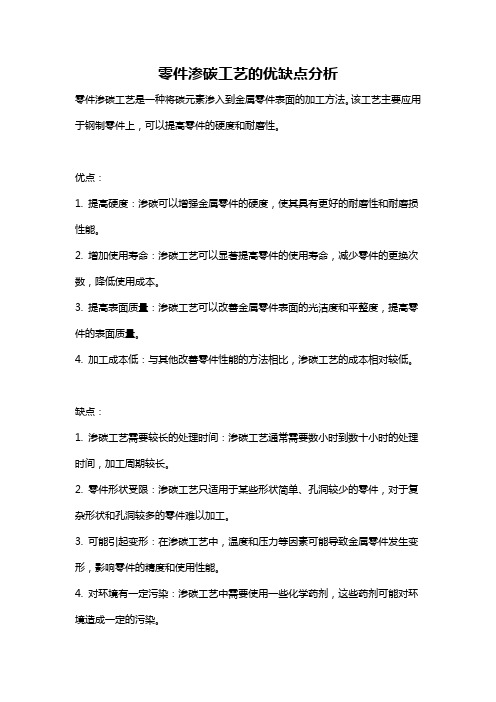
零件渗碳工艺的优缺点分析
零件渗碳工艺是一种将碳元素渗入到金属零件表面的加工方法。
该工艺主要应用于钢制零件上,可以提高零件的硬度和耐磨性。
优点:
1. 提高硬度:渗碳可以增强金属零件的硬度,使其具有更好的耐磨性和耐磨损性能。
2. 增加使用寿命:渗碳工艺可以显著提高零件的使用寿命,减少零件的更换次数,降低使用成本。
3. 提高表面质量:渗碳工艺可以改善金属零件表面的光洁度和平整度,提高零件的表面质量。
4. 加工成本低:与其他改善零件性能的方法相比,渗碳工艺的成本相对较低。
缺点:
1. 渗碳工艺需要较长的处理时间:渗碳工艺通常需要数小时到数十小时的处理时间,加工周期较长。
2. 零件形状受限:渗碳工艺只适用于某些形状简单、孔洞较少的零件,对于复杂形状和孔洞较多的零件难以加工。
3. 可能引起变形:在渗碳工艺中,温度和压力等因素可能导致金属零件发生变形,影响零件的精度和使用性能。
4. 对环境有一定污染:渗碳工艺中需要使用一些化学药剂,这些药剂可能对环境造成一定的污染。
综上所述,零件渗碳工艺具有提高硬度、增加使用寿命、提高表面质量和较低的加工成本等优点,但也存在处理时间较长、零件形状受限、可能引起变形和对环境有一定污染等缺点。
在选择使用该工艺时,需要根据零件的具体情况和要求进行综合考虑。
真空渗碳与传统渗碳比较
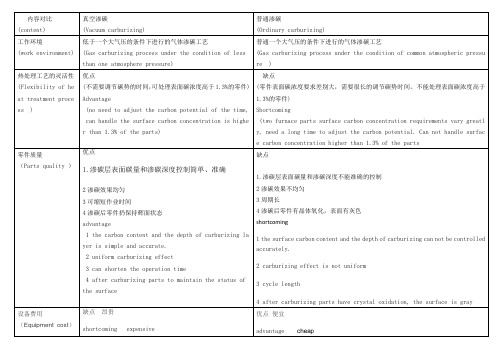
普通渗碳 (Ordinary carburizing) 普通一个大气压的条件下进行的气体渗碳工艺 (Gas carburizing process under the condition of common atmospheric pressu re ) 缺点
热处理工艺的灵活性 (Flexibility of he at treatment proce ss )
内容对比 (content) 工作环境 (work environment)
真空渗碳 (Vacuum carburizing) 低于一个大气压的条件下进行的气体渗碳工艺 (Gas carburizing process under the condition of less than one atmosphere pressure)
设备费用 (Equipment cost)
优点 便宜 advantage cheap
优点
(不需要调节碳势的时间, 可处理表面碳浓度高于 1.3%的零件) (零件表面碳浓度要求差别大,需要很长的调节碳势时间。不能处理表面碳浓度高于 Advantage (no need to adjust the carbon potential of the time, can handle the surface carbon concentration is highe r than 1.3% of the parts) 优点 1.3%的零件) Shortcoming (two furnace parts surface carbon concentration requirements vary greatl y, need a long time to adjust the carbon potential. Can not handle surfac e carbon concentration higher than 1.3% of the parts
齿轮井式炉渗碳淬火
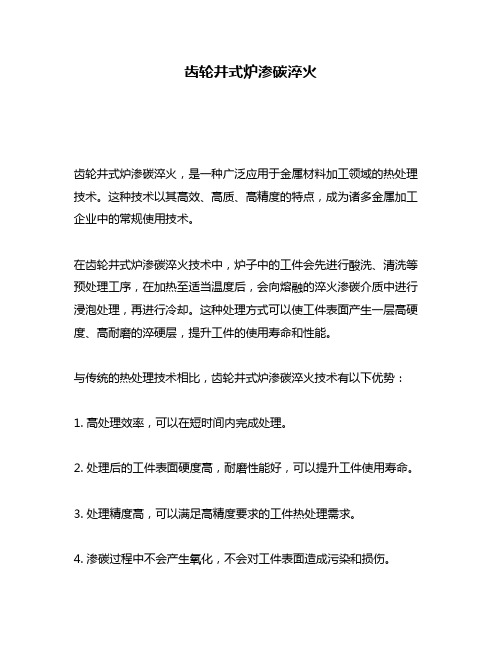
齿轮井式炉渗碳淬火
齿轮井式炉渗碳淬火,是一种广泛应用于金属材料加工领域的热处理技术。
这种技术以其高效、高质、高精度的特点,成为诸多金属加工企业中的常规使用技术。
在齿轮井式炉渗碳淬火技术中,炉子中的工件会先进行酸洗、清洗等预处理工序,在加热至适当温度后,会向熔融的淬火渗碳介质中进行浸泡处理,再进行冷却。
这种处理方式可以使工件表面产生一层高硬度、高耐磨的淬硬层,提升工件的使用寿命和性能。
与传统的热处理技术相比,齿轮井式炉渗碳淬火技术有以下优势:
1. 高处理效率,可以在短时间内完成处理。
2. 处理后的工件表面硬度高,耐磨性能好,可以提升工件使用寿命。
3. 处理精度高,可以满足高精度要求的工件热处理需求。
4. 渗碳过程中不会产生氧化,不会对工件表面造成污染和损伤。
5. 渗碳液的再生利用率高,可以降低处理成本。
总之,齿轮井式炉渗碳淬火技术在金属材料加工领域中有着广泛的应用前景,可以提升金属材料的使用性能和寿命,同时也具有高效、高精度等优点。
《渗碳贝氏体钢在轴承与齿轮中的应用》
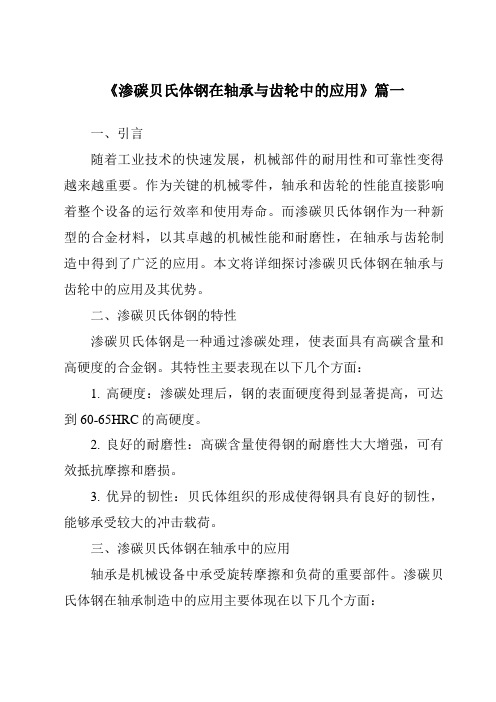
《渗碳贝氏体钢在轴承与齿轮中的应用》篇一一、引言随着工业技术的快速发展,机械部件的耐用性和可靠性变得越来越重要。
作为关键的机械零件,轴承和齿轮的性能直接影响着整个设备的运行效率和使用寿命。
而渗碳贝氏体钢作为一种新型的合金材料,以其卓越的机械性能和耐磨性,在轴承与齿轮制造中得到了广泛的应用。
本文将详细探讨渗碳贝氏体钢在轴承与齿轮中的应用及其优势。
二、渗碳贝氏体钢的特性渗碳贝氏体钢是一种通过渗碳处理,使表面具有高碳含量和高硬度的合金钢。
其特性主要表现在以下几个方面:1. 高硬度:渗碳处理后,钢的表面硬度得到显著提高,可达到60-65HRC的高硬度。
2. 良好的耐磨性:高碳含量使得钢的耐磨性大大增强,可有效抵抗摩擦和磨损。
3. 优异的韧性:贝氏体组织的形成使得钢具有良好的韧性,能够承受较大的冲击载荷。
三、渗碳贝氏体钢在轴承中的应用轴承是机械设备中承受旋转摩擦和负荷的重要部件。
渗碳贝氏体钢在轴承制造中的应用主要体现在以下几个方面:1. 轴套制造:利用其高硬度和耐磨性,制造出能承受高负荷和摩擦的轴套,延长轴承的使用寿命。
2. 滚动体制造:通过精密加工,渗碳贝氏体钢可以制造出高精度的滚动体,提高轴承的旋转精度和承载能力。
3. 抗腐蚀性能:渗碳贝氏体钢具有较好的抗腐蚀性能,能够在恶劣的工作环境中保护轴承免受腐蚀。
四、渗碳贝氏体钢在齿轮中的应用齿轮是传递动力和运动的关键部件,其性能直接影响着设备的传动效率和稳定性。
渗碳贝氏体钢在齿轮制造中的应用主要有以下几点:1. 齿面硬度:渗碳处理后,齿面获得高硬度,提高了齿轮的耐磨性和抗点蚀能力。
2. 强度和韧性:贝氏体组织的形成使得齿轮具有优异的强度和韧性,能够承受较大的冲击载荷。
3. 抗疲劳性能:渗碳贝氏体钢具有较好的抗疲劳性能,能够延长齿轮的使用寿命。
五、结论综上所述,渗碳贝氏体钢以其卓越的机械性能和耐磨性,在轴承与齿轮制造中得到了广泛的应用。
其高硬度和耐磨性使得制造出的轴套、滚动体等部件能够承受高负荷和摩擦,延长了设备的使用寿命。
《渗碳贝氏体钢在轴承与齿轮中的应用》范文

《渗碳贝氏体钢在轴承与齿轮中的应用》篇一一、引言随着现代工业的快速发展,对机械零部件的强度、耐磨性及抗疲劳性等性能的要求越来越高。
轴承和齿轮作为机械设备中的关键部件,其性能的好坏直接影响到设备的运行效率和寿命。
而渗碳贝氏体钢以其卓越的机械性能和耐磨性,在轴承与齿轮制造中得到了广泛应用。
本文将详细探讨渗碳贝氏体钢在轴承与齿轮中的应用及其优势。
二、渗碳贝氏体钢的特点渗碳贝氏体钢是一种具有高强度、高耐磨性和良好抗疲劳性的合金钢。
其特点主要包括:1. 高强度:渗碳贝氏体钢经过适当的热处理后,可以获得较高的强度和硬度。
2. 高耐磨性:渗碳处理可以使钢的表面形成一层硬度较高的渗碳层,从而提高其耐磨性。
3. 良好的抗疲劳性:渗碳贝氏体钢具有良好的抗疲劳性能,能够在长时间的使用过程中保持稳定的性能。
三、渗碳贝氏体钢在轴承中的应用轴承是机械设备中承受径向载荷和部分轴向载荷的重要部件。
由于渗碳贝氏体钢具有高强度、高耐磨性和良好的抗疲劳性,因此被广泛应用于轴承制造中。
1. 渗碳贝氏体钢在轴承套圈中的应用:轴承套圈是轴承的主要承载部件,需要承受较大的径向载荷和轴向载荷。
采用渗碳贝氏体钢制造的轴承套圈,能够提高其强度和耐磨性,延长使用寿命。
2. 渗碳贝氏体钢在轴承滚动体中的应用:轴承滚动体是支撑滚动元件的部件,需要具有较高的硬度和耐磨性。
采用渗碳贝氏体钢制造的滚动体,可以保证其长期稳定运行,减少磨损和损坏。
四、渗碳贝氏体钢在齿轮中的应用齿轮是机械设备中传递动力和运动的关键部件,需要承受较大的压力和摩擦力。
因此,齿轮材料的选择对其性能和使用寿命具有重要影响。
1. 渗碳贝氏体钢在齿轮齿面硬化处理中的应用:为了提高齿轮的耐磨性和抗疲劳性,通常需要对齿轮齿面进行硬化处理。
采用渗碳贝氏体钢制造的齿轮,可以通过渗碳处理在其表面形成一层高硬度的渗碳层,从而提高其耐磨性和抗疲劳性。
2. 渗碳贝氏体钢在重载齿轮中的应用:重载齿轮需要承受较大的压力和摩擦力,因此需要具有较高的强度和耐磨性。
高温渗碳用先进齿轮材料制造关键技术及产业化应用

高温渗碳用先进齿轮材料制造关键技术及产业化应用高温渗碳用先进齿轮材料制造关键技术及产业化应用随着工业化进程的不断加速,齿轮作为传动机构中不可或缺的一部分,在各种机械中都有着广泛的应用。
而在高速、高精度、高载荷以及高温等极端环境下,对齿轮材料的要求也越来越高。
其中,高温渗碳用先进齿轮材料正逐渐成为齿轮使用中不可或缺的关键材料之一。
高温渗碳用先进齿轮材料具有什么优势呢?首先,这种材料能够满足在高温下的使用要求,具有一定的强度和硬度,能够保证在高负荷、高速、重载情况下长时间不失效。
其次,该材料经过渗碳处理后表面质量高,摩擦系数小,使用寿命长,能够减少机械故障率。
然而,高温渗碳用先进齿轮材料的制造并不是一件容易的事情。
在生产过程中,需要具备先进的材料加工工艺和设备,以保证材料的均匀性、致密性和高质量。
这中间需要涉及到一系列的关键技术,比如渗碳工艺、材料表面质量控制、热处理工艺等等。
需要不断进行研究和探索,才能够获得更好的材料性能。
为了解决高温渗碳用先进齿轮材料的制造难题,国内外的研究机构和企业纷纷加大了研发投入,尝试着打破技术壁垒,在这一领域里取得突破性进展。
目前国内外已经有不少先进齿轮材料的生产厂家,如SKF、FAG、NSK等等,它们的产品性能稳定、质量可靠,深受广大用户的信赖和好评。
高温渗碳用先进齿轮材料产业化的应用前景非常广阔。
它广泛应用于航空、航天、船舶、重工、石油、化工、矿山等领域,促进了这些领域的发展。
通过生产高品质、高性能的先进齿轮材料,企业们也在不断增强竞争力,找到了自己的市场空间。
总的来说,高温渗碳用先进齿轮材料在制造和应用方面都有其独特的优势和难点,需要未来在研发和生产过程中不断进行探索和突破。
相信在多方的共同努力下,它在未来的应用领域里将会发挥更大的作用。
渗碳名词解释
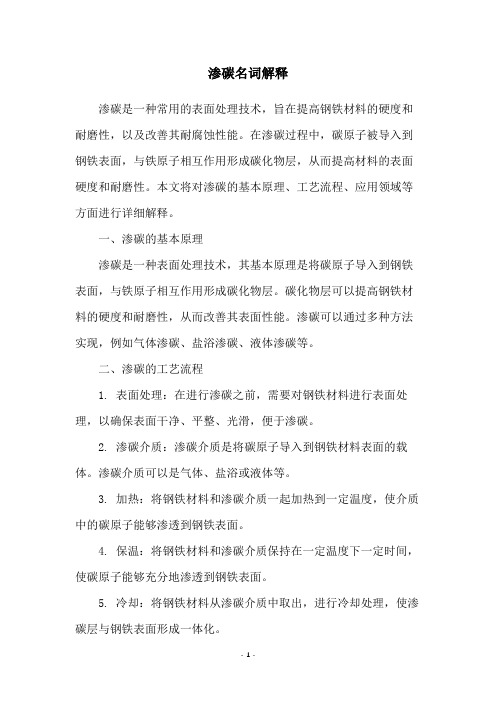
渗碳名词解释渗碳是一种常用的表面处理技术,旨在提高钢铁材料的硬度和耐磨性,以及改善其耐腐蚀性能。
在渗碳过程中,碳原子被导入到钢铁表面,与铁原子相互作用形成碳化物层,从而提高材料的表面硬度和耐磨性。
本文将对渗碳的基本原理、工艺流程、应用领域等方面进行详细解释。
一、渗碳的基本原理渗碳是一种表面处理技术,其基本原理是将碳原子导入到钢铁表面,与铁原子相互作用形成碳化物层。
碳化物层可以提高钢铁材料的硬度和耐磨性,从而改善其表面性能。
渗碳可以通过多种方法实现,例如气体渗碳、盐浴渗碳、液体渗碳等。
二、渗碳的工艺流程1. 表面处理:在进行渗碳之前,需要对钢铁材料进行表面处理,以确保表面干净、平整、光滑,便于渗碳。
2. 渗碳介质:渗碳介质是将碳原子导入到钢铁材料表面的载体。
渗碳介质可以是气体、盐浴或液体等。
3. 加热:将钢铁材料和渗碳介质一起加热到一定温度,使介质中的碳原子能够渗透到钢铁表面。
4. 保温:将钢铁材料和渗碳介质保持在一定温度下一定时间,使碳原子能够充分地渗透到钢铁表面。
5. 冷却:将钢铁材料从渗碳介质中取出,进行冷却处理,使渗碳层与钢铁表面形成一体化。
6. 表面处理:对渗碳后的钢铁材料进行表面处理,以去除渗碳介质残留和提高表面质量。
三、渗碳的应用领域1. 机械制造业:渗碳可以提高机械零件的硬度和耐磨性,从而延长其使用寿命。
常见的应用包括齿轮、轴承、齿条等。
2. 汽车制造业:汽车零件需要具备较高的硬度和耐磨性,以保证其安全和可靠性。
渗碳可以提高汽车零件的表面性能,常见的应用包括发动机齿轮、传动轴、曲轴等。
3. 航空航天制造业:航空航天材料需要具备较高的强度和耐磨性,以保证其在极端环境下的工作能力。
渗碳可以提高航空航天材料的表面性能,常见的应用包括发动机叶片、涡轮叶片等。
4. 石油化工制造业:石油化工设备需要具备较高的耐腐蚀性能,以保证其在腐蚀介质中的工作能力。
渗碳可以提高石油化工设备的耐腐蚀性能,常见的应用包括反应器、换热器等。
《渗碳贝氏体钢在轴承与齿轮中的应用》
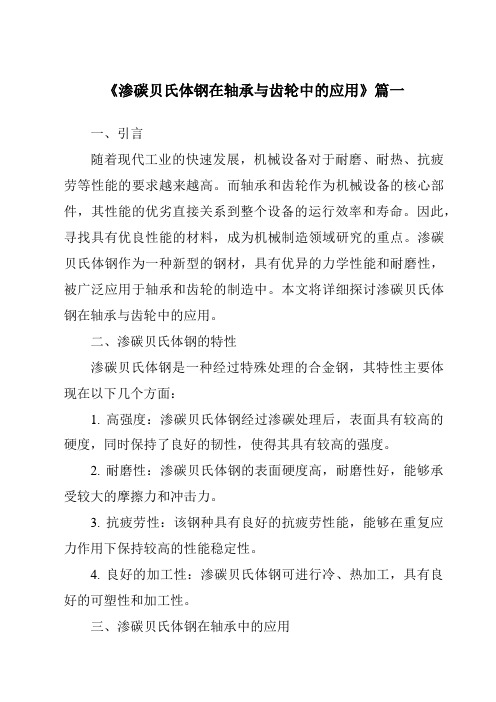
《渗碳贝氏体钢在轴承与齿轮中的应用》篇一一、引言随着现代工业的快速发展,机械设备对于耐磨、耐热、抗疲劳等性能的要求越来越高。
而轴承和齿轮作为机械设备的核心部件,其性能的优劣直接关系到整个设备的运行效率和寿命。
因此,寻找具有优良性能的材料,成为机械制造领域研究的重点。
渗碳贝氏体钢作为一种新型的钢材,具有优异的力学性能和耐磨性,被广泛应用于轴承和齿轮的制造中。
本文将详细探讨渗碳贝氏体钢在轴承与齿轮中的应用。
二、渗碳贝氏体钢的特性渗碳贝氏体钢是一种经过特殊处理的合金钢,其特性主要体现在以下几个方面:1. 高强度:渗碳贝氏体钢经过渗碳处理后,表面具有较高的硬度,同时保持了良好的韧性,使得其具有较高的强度。
2. 耐磨性:渗碳贝氏体钢的表面硬度高,耐磨性好,能够承受较大的摩擦力和冲击力。
3. 抗疲劳性:该钢种具有良好的抗疲劳性能,能够在重复应力作用下保持较高的性能稳定性。
4. 良好的加工性:渗碳贝氏体钢可进行冷、热加工,具有良好的可塑性和加工性。
三、渗碳贝氏体钢在轴承中的应用轴承是机械设备中重要的支承部件,承受着设备的径向和轴向负荷。
由于工作环境恶劣,轴承需要具备高强度、高耐磨、抗疲劳等性能。
渗碳贝氏体钢在这些方面表现出色,因此被广泛应用于轴承制造中。
1. 渗碳贝氏体钢在轴承套圈中的应用:渗碳贝氏体钢制作的轴承套圈具有高硬度和高耐磨性,能够承受较大的负荷和冲击力,提高了轴承的使用寿命。
2. 渗碳贝氏体钢在轴承滚动体中的应用:渗碳贝氏体钢制作的滚动体具有优异的抗疲劳性能,能够在高速、高负荷的工作环境下保持较高的性能稳定性。
四、渗碳贝氏体钢在齿轮中的应用齿轮是机械设备中传递动力的关键部件,需要具备高强度、高耐磨、抗点蚀等性能。
渗碳贝氏体钢在齿轮制造中也得到了广泛应用。
1. 渗碳贝氏体钢在齿轮齿面的应用:渗碳贝氏体钢制作的齿轮齿面具有高硬度和高耐磨性,能够承受较大的摩擦力和冲击力,提高了齿轮的使用寿命。
2. 渗碳贝氏体钢在齿轮整体结构中的应用:渗碳贝氏体钢的抗疲劳性能优异,使得制造出的齿轮能够在重复应力作用下保持较高的性能稳定性,降低了齿轮的失效风险。
《2024年渗碳贝氏体钢在轴承与齿轮中的应用》范文
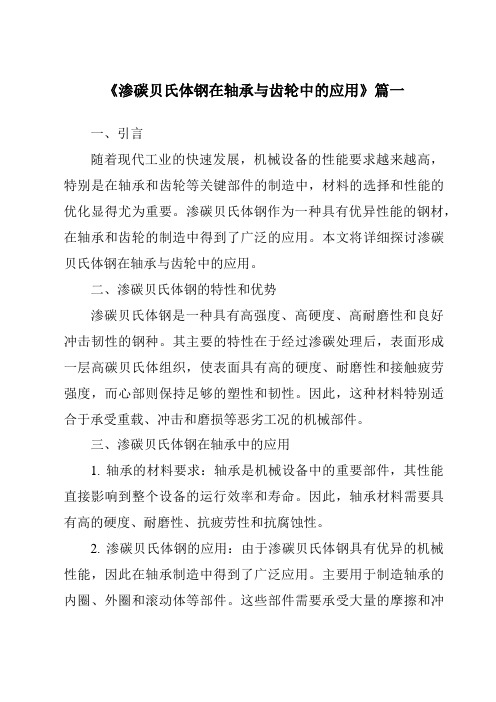
《渗碳贝氏体钢在轴承与齿轮中的应用》篇一一、引言随着现代工业的快速发展,机械设备的性能要求越来越高,特别是在轴承和齿轮等关键部件的制造中,材料的选择和性能的优化显得尤为重要。
渗碳贝氏体钢作为一种具有优异性能的钢材,在轴承和齿轮的制造中得到了广泛的应用。
本文将详细探讨渗碳贝氏体钢在轴承与齿轮中的应用。
二、渗碳贝氏体钢的特性和优势渗碳贝氏体钢是一种具有高强度、高硬度、高耐磨性和良好冲击韧性的钢种。
其主要的特性在于经过渗碳处理后,表面形成一层高碳贝氏体组织,使表面具有高的硬度、耐磨性和接触疲劳强度,而心部则保持足够的塑性和韧性。
因此,这种材料特别适合于承受重载、冲击和磨损等恶劣工况的机械部件。
三、渗碳贝氏体钢在轴承中的应用1. 轴承的材料要求:轴承是机械设备中的重要部件,其性能直接影响到整个设备的运行效率和寿命。
因此,轴承材料需要具有高的硬度、耐磨性、抗疲劳性和抗腐蚀性。
2. 渗碳贝氏体钢的应用:由于渗碳贝氏体钢具有优异的机械性能,因此在轴承制造中得到了广泛应用。
主要用于制造轴承的内圈、外圈和滚动体等部件。
这些部件需要承受大量的摩擦和冲击力,而渗碳贝氏体钢的高硬度和耐磨性使其成为理想的材料选择。
四、渗碳贝氏体钢在齿轮中的应用1. 齿轮的材料要求:齿轮是传动系统中的重要部件,其性能直接影响到传动效率和设备运行的平稳性。
因此,齿轮材料需要具有高的硬度、强度、耐磨性和抗疲劳性。
2. 渗碳贝氏体钢的应用:由于渗碳贝氏体钢具有较高的硬度和强度,且表面硬度梯度分布合理,因此在齿轮制造中也有广泛应用。
主要用于制造齿轮的齿面部分,可以有效地提高齿轮的耐磨性和抗疲劳性,延长齿轮的使用寿命。
五、结论综上所述,渗碳贝氏体钢在轴承和齿轮的制造中具有广泛的应用前景。
其优异的机械性能使其能够满足重载、冲击和磨损等恶劣工况下的使用要求。
在轴承应用中,渗碳贝氏体钢主要用于制造内圈、外圈和滚动体等部件;在齿轮应用中,则主要用于制造齿面部分。
低压真空渗碳炉与传统渗碳炉的主要优势和特点比较

书山有路勤为径,学海无涯苦作舟
低压真空渗碳炉与传统渗碳炉的主要优势和特点比较
为了更全面掌握和了解,对有关低压真空渗碳炉与传统渗碳炉的主要优势和特点进行了比较,见下表。
真空渗碳与传统渗碳比较
常规渗碳工艺温度受到炉子性能的影响,最高使用温度被限制在950℃以内,然而真空渗碳炉技术的改善可以将最高使用温度提高到1050℃。
由于渗碳时碳的扩散系数随着温度的提高而加快,渗碳速度可以大幅度提升,使获得同样渗碳深度的时间大大缩短,有利于提高生产效率和降低生产成本。
低压真空渗碳使用温度的提高为提高生产效率提供了先决条件。
为此,在不影响零件力学性能的条件下,采用较高的渗碳温度可明显提高渗碳速度。
常规和真空渗碳的典型工艺的比较见下表。
常规和真空渗碳的典型工艺的比较
采用A
同温度常规渗碳和真空渗碳达到同样有效硬化层深度试验比较
可以看出,为了达到同样的渗碳硬化深度,不仅真空渗碳较常规渗碳节
约74min(生产周期仅为常规82%),而且齿轮经过真空渗碳气淬硬化后表面仍可保持金属本色,没有内氧化发生,变形大幅度减小,为渗碳后期的磨削加工节省了难度和时间,质量水平和使用可靠性成倍提高(据了解,目前汽车行业的高端齿轮箱用齿轮,要求必须采用低压真空渗碳技术生产)。
有人对大于要求渗碳深度1.60mm 的重载货车齿轮进行渗碳时间对比,采用低压真空渗碳总渗碳时间仅为385min,而采用连续可控渗碳炉渗碳总时间需要12h,前者生产周期仅为后者的50%。
这说明在提高渗碳质量的前提下,实际生产周期缩短是非常明显。
齿轮真空绝热管技术

齿轮真空绝热管技术近年来,齿轮真空绝热管技术受到了越来越多的关注和应用。
一、齿轮真空绝热管技术的特点和优势1.传输精度高:采用节流阀齿轮减速结构,使得齿轮绝热管具有精密的传输功能。
2.费用低:采用齿轮减速结构,具有传热能力,而且材料成本也很低。
3.体积小:齿轮绝热管采用封闭式紧固结构,可以安装在有限空间内,减少空间损失。
4.可靠性强:采用密封技术,防止漏气,保证温度的一致,并降低维护部分的磨损。
二、齿轮真空绝热管技术的应用1.冷却系统:由于齿轮绝热管具有低漏率和高散热能力,可以在低温低于设定温度的情况下实现冷却效果,用于汽车冷却系统中。
2.燃烧器系统:采用齿轮绝热管,可以实现有效的火焰传递,从而燃烧更加均匀,提高燃烧效率,同时减少能耗。
3.动力系统:由于齿轮绝热管能够有效地抑制热量扩散,可用于汽车发动机的传热,提高动力系统的工作效率。
4.高精度控制系统:齿轮绝热管可以控制低压和恒温,可用于高精度控制系统,减少精度误差。
三、齿轮真空绝热管技术的未来发展1.面向新能源车辆的应用:齿轮绝热管广泛应用于新能源汽车上,能够有效地抑制热散,更好地节约能源,提高冷却效果。
2.智能控制:通过对齿轮绝热管的精密控制,可以实现更精准的温度控制,并且实现新的智能控制,从而提高工作效率。
3.低温发电技术:齿轮绝热管在低温发电领域具有重要的作用,可以改善发电机的运行环境,从而提高发电效率。
4.绿色环保技术:齿轮绝热管确保了设备的温度精度,有效减少空气污染物排放,有利于环保。
总之,齿轮真空绝热管技术具有传输精度高、费用低、体积小、可靠性强等优点,可以应用于汽车冷却系统、燃烧器系统、动力系统、高精度控制系统等领域,有望在新能源车辆、智能控制、低温发电技术、绿色环保技术等方面取得良好的发展。
齿轮渗碳热处理的意义

齿轮渗碳热处理的意义
齿轮是一种常见的机械零部件,它们在各类工业机械中都具有重要的作用。
由于齿轮在工作过程中需要承受较大的负荷和摩擦,因此它的表面必须具有耐磨、耐腐蚀和耐疲劳的特性,这一点可以通过渗碳热处理来实现。
齿轮渗碳热处理是一种将碳元素注入齿轮表面的加工方式,这种方式可以显著地改善齿轮的物理、化学和力学性质,提高它的硬度、强度和韧性。
具体来说,渗碳热处理可以有效提高齿轮的耐磨性、耐腐蚀性和抗疲劳性,减少表面裂纹和磨损。
此外,齿轮渗碳热处理还可以增加其表面的蓝色,使其具有更好的美观度和质感,符合现代企业对于高品质产品的要求。
由此可见,齿轮渗碳热处理在工业领域中具有重要的意义,它不仅可以提高齿轮的性能和品质,也可以提高生产线的效率和通过率。
总之,齿轮渗碳热处理是一种必不可少的工业加工方式,它可以有效提高齿轮的物理、化学和力学性质,具有重要的意义。
在今后的工业生产过程中,我们应该更加注重这种加工方式的应用,把高品质、高效率、高稳定性视为最终目标,为工业的发展做出更大的贡献。
浅谈机床渗碳件渗层深度与性能

浅谈机床渗碳件渗层深度与性能前言在机床零件中,渗碳件占有相当的比例,特别是齿轮、轴、套类等零件。
渗碳质量直接影响机床的精度和寿命,而渗层的表层碳含量,渗层深度,渗碳淬火回火后的硬度以及表层与心部组织,则是衡量渗碳件性能的重要指标。
根据这些指标的测定,选出最合适的渗层深度,最优化的工艺。
备料及制样2.1制样分组根据我厂具体情况,本试验选钢为20Cr。
20Cr钢的化学成分(W%)及Ac1,Ac3(℃):C(0.17-0.24)Si(0.17-0.37)Mn(0.5-0.8)Cr(0.7-1.00),Ac1(766)、Ac3(838)。
经过对渗碳件渗层深度要求的统计,筛选出具有代表性的三个渗层范围,并将试样分组,编号分别为A、B、C。
A组:渗层深度为0.6-0.8mm,B组:渗层深度为0.9-1.3mm,C组:渗层深度为1.3-1.7mm。
2.2试样种类尺寸及数量,并打上相应编号金相试样:φ12X30 每样号3件,共9件硬度试样:φ20X12 每样号3件,共9件冲击试样:10X10X55 每样号3件,共9件3.热处理阶段3.1渗碳工艺由于碳在铁素体中的溶解度较小,而在奥氏体中的溶解度较大,所以渗碳必须在Ac3以上的温度,使钢在奥氏体状态下进行。
渗碳温度越高,渗碳层越深。
但过高的渗碳温度将导致晶粒粗化,表层碳浓度过高而形成网状碳化物,并在淬火后形成大量残余奥氏体,增加了淬火后的变形、开裂倾向。
因此,选择适合的渗碳温度尤为重要。
选择渗碳温度为920℃。
根据A、B、C的三个渗层深度,渗剂为煤油,渗碳时间分别为3-5h;5-8h;8-11h。
渗碳工艺如下:组别A,渗碳温度920℃,时间3h,炉冷至840℃坑冷。
组别B,渗碳温度920℃,时间7h,炉冷至840℃坑冷。
组别C,渗碳温度920℃,时间10h,炉冷至840℃坑冷。
3.2淬火、回火工艺为使渗碳件具有表面高硬度,高耐磨性和良好的心部韧性,渗碳件在渗碳后必须进行恰当的淬火、回火才能达到要求。
真空炉渗碳淬火

真空炉渗碳淬火真空炉渗碳淬火是一种先进的热处理技术,通过将零件放入真空炉内,在加热的同时注入适量的碳元素,以提高零件的硬度和耐磨性。
经过渗碳后,零件在淬火过程中能够形成强化的炭化层,提高零件的强度和耐久性。
以下是详细的中文介绍。
真空炉渗碳淬火的工艺流程通常包括6个步骤:1. 预处理:首先需要对待处理零件进行清洗、去油和表面处理,以防止在渗碳和淬火过程中出现不良的化学反应。
2. 加热:将清洗后的零件放入真空炉中进行加热,通常的加热温度为800°C-1000°C。
3. 渗碳:在加热的同时,通过向真空炉中注入适量的天然气或液体碳化剂,以实现零件表面的渗碳。
4. 等温保温:渗碳完成后,需要将零件保持在高温状态下,以确保渗碳元素充分扩散到零件表面。
5. 淬火:在等温保温结束后,将零件快速冷却,以产生强化的炭化层和改善材料的性能。
6. 退火:淬火后需要进行退火处理,以消除由于淬火过程产生的残余应力,防止零件变形和开裂。
相比传统的热处理方法,真空炉渗碳淬火有以下优势:1. 良好的渗碳效果:真空炉渗碳淬火能够实现零件表面的均匀渗碳,形成厚度均匀、致密的炭化层。
2. 精确的控制窑内气氛:由于真空炉可以精确控制炉内气氛,不会产生杂质等不良反应,能够控制零件的化学成分和物理性质。
3. 提高零件硬度和耐磨性:经过真空炉渗碳淬火处理的零件,具有较高的硬度和耐磨性,能够有效地抵抗磨损和压力的影响。
4. 适用范围广:真空炉渗碳淬火可以用于各种形状和大小的零件,有效地提高了零件的使用寿命和可靠性。
真空炉渗碳淬火技术通常应用于以下领域:1. 汽车工业:用于发动机配件、变速器零件、离合器零件等。
2. 航空工业:用于发动机叶轮、涡轮叶片、高温轴承等。
3. 机械工业:用于大型齿轮、轴承、液压缸、钢筋和零件表面硬化等。
4. 其他工业:用于焊接部件、金属零件、模具和不锈钢等材料的热处理。
总之,真空炉渗碳淬火技术是一种高效的热处理工艺,能够提高零件的硬度和耐磨性,增加零件的使用寿命和可靠性,具有广泛的应用前景。