PCB流程简介-全制程
pcb流程简介全制程

表面处理
表面处理是PCB制造中的重要环节,主要目的是提高 PCB的可靠性和性能。
输标02入题
表面处理工艺包括镀金、镀银、喷锡等。镀金可以增 强导电性能和耐腐蚀性,镀银可以提高焊接性能,喷 锡则可以提高可焊性和耐热性。
01
03
在表面处理过程中,需要注意防止表面氧化、变色和 脱落等问题。
05
02
制作
将设计好的PCB图转换为实际电路板, 需要进行覆铜、钻孔、电镀等处理。
03
检测
对制作好的电路板进行检测,包括外 观检测、电气性能检测等,确保质量 合格。
04
组装
将电子元器件焊接到电路板上,完成 PCB的组装。
02
PCB设计
原理图设计
总结词
原理图设计是PCB流程的起始阶段,主要任务是创建电路原理图,将电路的功 能需求转化为图形表示。
确保使用的原材料质量合格, 无缺陷且符合设计要求。
生产过程监控
对PCB制造过程中的各个环节 进行严格监控,确保工艺参数
符合标准。
成品检验
对完成的PCB进行全面的质量 检查,包括外观、尺寸、电气
性能等。
环境条件控制
确保生产环境满足温湿度、清 洁度等要求,以降低品质风险
。
可靠性评估方法
寿命测试
模拟实际使用环境,对 PCB进行长时间运行测试 ,评估其寿命和稳定性。
详细描述
PCB布线是电路板设计的最后阶段,它需要考虑布线的长度、宽度、弯曲半径等 因素,以确保电路的电气性能和可靠性。同时,布线还需要考虑制造工艺的要求 ,以确保生产的可行性和效率。
03
PCB材料选择与处
PCB全制程简介

压膜前
压膜后
8
2. 内层流程
2.3 压膜(Film lamination):
贴膜时,先从干膜上剥下聚乙烯保护膜,然后在加热加压的条件下将干膜抗蚀剂 粘贴在基板上。干膜中的抗蚀剂层受热后变软,流动性增加,借助于热压轮的压 力和抗蚀剂中粘结剂的作用完成贴膜.
压膜前
压膜中
压膜后
Dry Film Structure Base Film (PE)基膜
型号
7628 1506 2116 1080 106
胶含量
42±3% 48 ±3% 52 ±3% 62 ±3% 72 ±3%
压合厚度(inch)
0.00745 0.00619 0.00459 0.00277 0.00210
23
4. 压合流程
4.4 叠板
目的: 将预叠合好的内层板,胶片等板叠
成待压多层板的形式 主要原物料: 铜箔 电镀铜皮;按厚度可分为 1/3OZ(代号T) 1/2OZ(代号H) 1OZ(代号1) RCC(覆树脂铜皮)等
UV光 曝光前
负片底片
曝光后
10
2. 内层流程
2.4 曝光(Exposure):
干膜(dry film)的构造见右图, 1968年由杜邦公司开发出来这 种感旋旋光性聚合物的干膜 后,PCB的制作就进入另一纪元, 到1984年末杜邦的专利到期后 日本的HITACHI也有自己的品 牌问世.
目前碱水溶液显像型为主 制程步骤: 压膜─停置─曝光─停
压 力
可叠多层
热板
钢板 牛皮纸 承载盘
压合机
25
4. 压合流程
4.6 后处理
目的: 经剖半;打靶;捞边;磨边等工序对压合之多层板进行初步外形处理,以便
PCB流程及制程简介
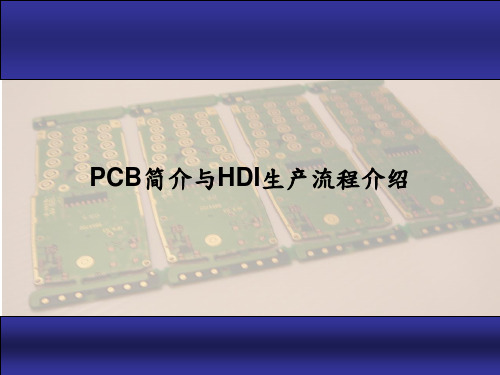
剪边(CNC裁板)-完成压合的板子其边缘都会有溢胶,必须用剪床裁掉以便在后续制程 中作业 方便及避免造成人员的伤害,剪边最好沿着边缘直线内1公分处切下,切太多会 造成电镀夹点 的困扰,最好再用磨边机将四个角落磨圆及边缘毛头磨掉,以减少板子 互相间的刮伤及对槽液 的污染。或者现在很普遍直接以CNC成型机做裁边的作业
氧化路板铜面与胶片结合强度的制程,氧化后的板子表面生成了一层黑色的绒毛层。
10.铆合
PP板
内层板
针对又可能发生的层间移动的多层板而采用 的制程。将多片已经氧化的内层线路板中间 放上夹层胶片后用铆钉将其铆合起来,讲究 正反铆、对称铆的原则。 所谓胶片是由铆钉胶合玻璃纤维布组成,它 在加热的情况下可再软化,再经加热、加压 后硬化,硬化后就不可再软化,胶片的主要 作用是作为线路板的绝缘层和粘合介质。
5. 剥锡-去除做为蚀刻阻剂的
37. 外层AOI
检测外层线路
37. 防焊绿油
用印刷机通过丝网在板表面刷上一层感光油墨,并用烤箱烤干
38. 防焊曝光
39. 防焊显影
40. 文字印刷
40. 化镍金
–其是在被催化的銅面上沉積兩層金屬的製程。利用金低接 觸電阻及不易氧化的特性,對線路提供良好的傳導及保護; 鎳層則是焊錫時之焊點並提供銅金中間緩衝層,避免銅和金 互相的擴散或遷移。
同内层2 为得到良好质量的蚀刻图形,就要确保抗蚀层与基板 表面牢固的结合,要求基板表面无氧化层、油污、灰尘、指印 以及其他的污物。因此在涂布抗蚀层前首先要对板进行表面清 洗并使铜箔表面达到一定的粗化层度
19.干膜压膜
在板表面加热后贴一层感光贴膜,为曝光准备
20.干膜曝光
同4内层曝光
21.次外层显影 22 .AOI 23.棕化 24.叠合 25. 压合 26. x-ray定位孔 27.修边
PCB流程介绍

目的:
粗化铜面,增加与树脂接触表面积; 增加铜面对流动树脂之湿润性; 使铜面钝化,避免发生不良反应;
棕化面SEM
主要原物料:
棕化药液&黑化药液
品質測試項目:
微蝕量測試; 離子污染度測試; 爆板測試(熱應力測試); 棕化拉力測試(結合力測試)
黑化面SEM
PCB製造流程---壓合
棕黑化 組合 铆合 疊合 熱壓 冷壓 後處理
目的: 通过光学反射原理将图像回馈至设备处理,与设定的逻辑判断原则或资料图形相比较, 找出缺点位置 注意事項: 由于AOI所用的测试方式为光學掃描+逻辑比较,一定会存在一些误判的缺点,故需通 过人工加以确认
VRS确认(Verify Repair Station 确认檢修系统):
目的: 通过与AOI连线,将测试资料传给V.R.S,并由人工对AOI的测试缺点进行确认
PCB製造流程---內層
AOI影像擷取工作原理:
類比轉 數位
CCD鏡頭
Lens 光圈
灰階
二值化
反射鏡
Beam splitter
反射鏡
光纖
散射光 直射光 散射光 板子
聚 光 燈 泡
濾光片
PCB製造流程---壓合
壓合流程:
棕黑化 組合 铆合 疊合 熱壓 冷壓 後處理 出貨
目的: 将铜箔(Copper)、胶片(Prepreg)与棕黑化处理后的内层线路板压合成多层板. 棕黑化
裁板(BOARD CUT):
目的: 依制前设计所规划要求,将基板材料裁切成工作所需尺寸 主要原物料: 基板;锯片基板由铜皮和绝缘层压合而成,依要求有不同板厚规格,依铜厚可分为 H/H;1oz/1oz;2oz/2oz等种类
PCB制程工艺简要介绍
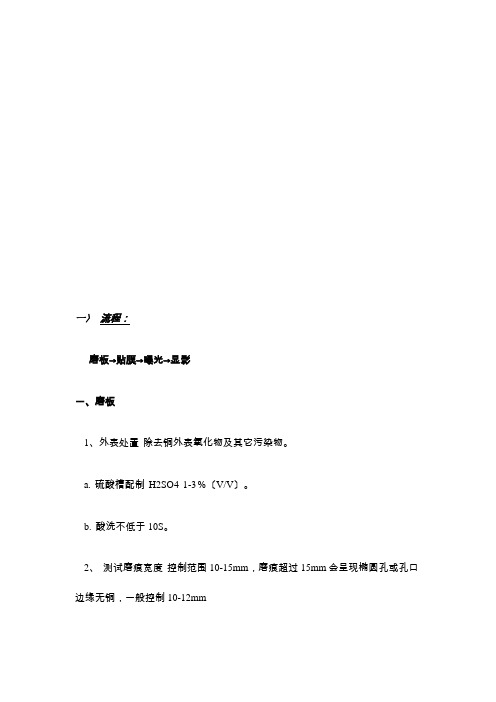
一〉流程:磨板→贴膜→曝光→显影一、磨板1、外表处置除去铜外表氧化物及其它污染物。
a. 硫酸槽配制H2SO4 1-3%〔V/V〕。
b. 酸洗不低于10S。
2、测试磨痕宽度控制范围10-15mm,磨痕超过15mm会呈现椭圆孔或孔口边缘无铜,一般控制10-12mm为宜。
3、水磨试验每日测试水膜破裂时间≥15s,试验说明,在不异条件下磨痕宽度与水膜破裂时间成正比。
4、磨板控制传送速度,间隔1",水压,枯燥温度70-90℃。
二、干膜房1、干膜房洁净度10000级以上。
2、温度控制20-24°C,超出此温度范围容易引起菲林变形。
3、湿度控制60-70%,超出此温度范围也容易引起菲林变形。
4、工作者每次进入干膜房必需穿戴防尘服及防尘靴风淋15-20s。
三、贴膜1、贴膜参数控制a. 温度100-120°C,精细线路控制115-120°C,一般线路控制105-110°C,粗线路控制100-105°C。
b. 速度<3M/min。
c. 压力30-60Psi,一般控制40Psi摆布。
2、本卷须知a. 贴膜时注意板面温度应保持38-40°C,冷板贴膜会影响干膜与板面的粘接性。
b. 贴装前须查抄板面是否有杂物、板边是否光滑等,假设板边毛刺过大会划伤贴膜胶辊,影响使用寿命。
c. 在气压不变情况下,温度较高时可适当加快传送速度,较低时可适当减慢传送速度,否那么会呈现皱膜或贴膜不牢,图形电镀时易发生渗镀。
d. 切削干膜〔手动贴膜机〕时用力均匀,保持切边整齐,否那么显影后呈现菲林碎等缺陷。
e. 贴膜后须冷却至室温前方可进行曝光。
四、曝光1、光能量a.光能量〔曝光灯管5000W〕上、下灯控制40-100毫焦/平方厘米,用下晒架测试上灯,上晒架测试下灯。
b.曝光级数7-9级覆铜〔Stoffer 21级曝光尺〕,一般控制8级摆布,但此级数须显影后才能反映出来,因此对显影控制要求较严。
APCB-PCB流程简介-全制程

壓合课介绍
• 流程介绍:
铆合
叠板
压合
后处理
X-Ray鑽靶
目的: 将铜箔(Copper)、胶片(Prepreg)与氧化处理后的内层 线路板压合成多层板
2018/11/1
16
壓合课介绍
铆合:(铆合;预叠) 目的:(四层板不需铆钉) 利用铆钉将多张内层板钉在一起, 以避免后续加工时产生层间滑移 主要原物料:铆钉;P/P P/P(PREPREG):由树脂和玻璃纤维 布组成,据玻璃布种类可分为 1060;1080;2116;7628等几种 树脂据交联状况可分为: A阶(完全未固化);B阶(半固化);C 阶(完全固化)三类,生产中使用的 全为B阶状态的P/P
前处理后 铜面状况 示意图
2018/11/1
5
内层课介绍
涂佈(COATING): 目的: 将经处理之基板铜面COATING 方式涂佈上抗蚀油墨 主要原物料:油墨(INK) 溶劑顯像型 半水溶液顯像型 油墨 鹼水溶液顯像型 水溶型油墨主要是由於其組成 中含有機酸根,會與強碱反應 使成為有機酸的鹽類,可被水 溶掉。
注意事项: 避免板边巴里影响品质,裁切后进行磨边,圆角处理 考虑涨缩影响,薄板需送下制程前进行烘烤 裁切须注意机械方向一致的原则
2018/11/1 4
内层课介绍
前处理(PRETREAT): 目的: 去除銅面上的污染物,增 加銅面粗糙度,以利於後續 的壓膜制程 主要原物料:刷輪
铜箔 绝缘层
2018/11/1
14
内层课介绍
黑棕化: 目的: (1)粗化铜面,增加与树脂接触表面积 (2)增加铜面对流动树脂之湿润性 (3)使铜面钝化,避免发生不良反应 • 主要原物料:黑化/棕化药液 • 注意事项: 黑化/棕化膜很薄,极易发生擦花问题,操作时需注意操 作手势
PCB制程(
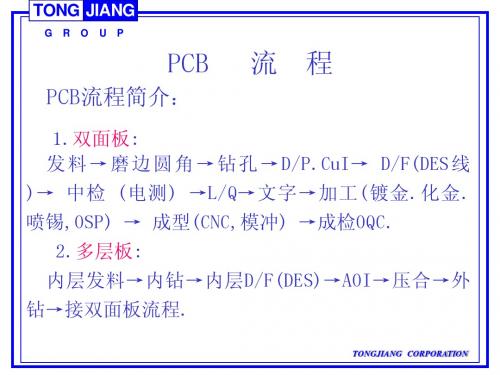
TONG JIANG
G O U P 2、R 孔大原因
改善措施
①将钻头插错 ①有标示的看标示, 无标示的100%测量。 ②钻头断针 ②运用新钻头 3、少孔原因 ①程式有误 ②操作时未按 规定作业 ③断针时底板 未钻透 改善措施 ①底片、麦拉作 确认(工程确认) ②停机时退还 2-3孔作业 ③断针板进行全检.
TONGJIANG CORPORATION
TONG JIANG
G R O U P
裁板(发料)
一.裁板(发料):基板按照客户及工程排版的要求的尺寸,通过裁切的方式 获得. 作业流程:
裁板→磨边→圆角 →下工序
(1) 裁板(发料): ① 发料尺寸公差(土1mm),板厚公差无特别说明为(土0.075mm). ② 基板 常 见规 格 :尺 寸 :36〃*48〃 、40〃*48〃 、42〃*48〃 厚 度:0.4t、 0.6t、0.8t等.铜箔:1/1和H/H及2/2; (2)磨边(厚度1.2t(含)以上板材均适用)在磨边机上磨四边,磨边作用: ①避免滚轮刮伤。 ②减少后制程因板边毛屑造成残膜. (3)圆角:将板四个角磨成圆弧形,以防流入后制程因板角尖锐刮伤板 面. (4)烘板(0.8t以下内层):为消除内应力,减少板内含水量,预防内层缩 水造成内短.烘板条件:150℃/烘烤4小时.
TONGJIANG CORPORATION
TONG JIANG
G R O U P
钻
单双面板(内层)
孔
多层板 上电木板 a.厚度一致 b.无严重弯翘
栽pin a.钻头ф2.95mm pin ф2.95mm 上板(靶孔或印刷孔)
一. 钻孔目的:根据客户所提供的孔径、孔位图,由工程进行排版后,在规定基材尺寸上进行钻孔, 为后续 浸铜做准备.
PCB全流程范文

PCB全流程范文PCB的全流程包括设计、制造和组装,下面将对每个环节进行详细介绍。
1.设计阶段PCB设计是整个流程的关键步骤,它决定了电路连接、功耗分配、布线风格和信号完整性。
首先,设计师根据电路原理图绘制PCB原理图,将电路的各个元件连接起来。
然后,设计师可以使用CAD软件进行布局设计,将元件合理地安置在PCB板上,并确定连接线的走向。
最后,设计师进行布线操作,即连接元器件的引脚,确保信号能够正确地在电路板上流动。
2.制造阶段制造PCB板需要经历多个步骤,包括材料准备、划线、腐蚀、穿孔、镀铜和掩膜等。
首先,根据设计要求,选择合适的基板材料,如玻璃纤维、陶瓷或聚酰亚胺。
然后,使用光刻胶在基板上进行划线,形成电路图案。
接下来,将划好线的基板放入腐蚀液中,除去未被光刻胶保护的部分铜质,形成电路图案的铜层。
然后,在需要连接的地方进行穿孔,以便将元器件插入PCB板上。
接下来,通过电解过程,在整个电路板表面均匀地镀上一层铜,以保护电路板并改善导电性能。
最后,使用掩膜覆盖铜层,以防止短路和腐蚀。
3.组装阶段在PCB板制造完成后,需要将元器件安装到电路板上。
首先,将元器件插入之前预留的穿孔中,确保引脚正确插入,并使用焊锡将其固定在电路板上。
随后,使用焊接技术将元器件与PCB板的引脚连接起来,如表面贴装技术(SMT)或插针焊接。
在焊接完成后,可以进行电路板的测试和调试,以确保电路能够正常工作。
总结PCB的全流程包括设计、制造和组装。
在设计阶段,设计师绘制原理图、进行布局设计和布线操作。
在制造阶段,根据设计要求选择基板材料,进行划线、腐蚀、穿孔、镀铜和掩膜。
在组装阶段,将元器件插入穿孔中,使用焊接技术将其与PCB板连接,并进行测试和调试。
这些步骤共同构成了PCB的全流程,确保电路板能够正常工作。
比较全的PCB生产工艺流程介绍

比较全的PCB生产工艺流程介绍PCB(Printed Circuit Board)是现代电子产品中不可或缺的一部分,它起到了组织电子元件、连接电路的作用。
下面是一个较全的PCB生产工艺流程介绍。
1.原料准备:PCB生产的原材料主要包括基板材料、导电层材料、覆盖层材料以及焊接材料等。
各种材料需要经过质量检验和筛选。
2.设计:PCB的设计一般是通过电脑辅助设计(CAD)软件进行的。
在设计过程中,需要考虑电路布局、元件安装位置、线路走向等因素。
3.版图制作:根据PCB设计图,进行版图制作。
版图制作包括各种工艺参数的设置,如层间距、线宽、线间距等。
4.印制制作:通过光刻工艺,将设计的电路图形透过掩膜映射到基板上,涂覆光敏化剂,并暴光照射,形成导电图形。
5.蚀刻:将覆盖着光敏化剂的基板浸入蚀刻液中,通过化学反应去除未曝光的光敏化剂,暴露出需要保留的导电层。
6.电镀:在蚀刻后的导电层上进行金属电镀,一般使用铜。
铜层的厚度和均匀性对PCB的性能有重要影响。
7.钻孔:根据PCB设计要求,在特定位置进行钻孔。
钻孔通常使用电脑控制的机械钻床进行。
8.电镀:进行表面处理,保护导电层不被氧化。
常用的表面处理方法包括阻焊、镀金、喷锡等。
9.特殊工艺:一些PCB可能需要特殊的工艺,如层压、压线、贴膜等。
这些工艺的目的是提高PCB的性能和可靠性。
10.组件装配:将PCB上的元件进行焊接,通常使用锡膏和热风或烙铁进行。
11.测试:对PCB进行测试,确保其正常工作。
常见的测试方法有连通性测试、功能性测试等。
12.包装和发货:将已经测试过的PCB进行包装,并按照订单要求进行发货。
总结:以上是一个较全的PCB生产工艺流程介绍。
PCB生产工艺复杂,需要多个环节的配合和准确的操作。
每个环节都非常重要,影响着PCB的质量和可靠性。
随着技术的不断进步,PCB生产工艺也在不断改进,以满足不断变化的市场需求。
PCB流程简介-全制程

*
PB1(電鍍一課)介紹
☺ 化學銅(PTH)
化學銅之目的: 通過化
學沉積的方式時表面沉積
上厚度為20-40 micro
inch的化學銅。
PTH
重要原物料:活化鈀
,鍍銅液
*
PB1(電鍍一課)介紹
☺ 一次銅
一次銅之目的: 鍍上200500 micro inch的厚度的銅 以保護僅有20-40 micro inch厚度的化學銅不被後制 程破壞造成孔破。 重要原物料: 銅球
4L
(完全固化)三类,生产中使用的全为
5L
B阶状态的P/P
*
PA2(压板课)介绍
叠板: 目的: ➢ 将预叠合好之板叠成待压 多层板形式 主要原物料:铜皮 ➢ 电镀铜皮;按厚度可分为 1/3OZ(代号T) 1/2OZ(代号H) 1OZ(代号1) RCC(覆树脂铜皮)等
Layer 1 Layer 2 Layer 3 Layer 4 Layer 5 Layer 6
注意事项: ➢ 避免板边巴里影响品质,裁切后进行磨边,圆角处理 ➢ 考虑涨缩影响,裁切板送下制程前进行烘烤 ➢ 裁切须注意机械方向一致的原则
*
PA1(内层课)介绍
前处理(PRETREAT):
目的: ➢ 去除銅面上的污染物,增
加銅面粗糙度,以利於後續 的壓膜制程
主要原物料:刷輪
铜箔 绝缘层
前处理后 铜面状况 示意图
*
PB1(電鍍一課)介紹
☺ 流程介紹
鑽孔
去毛頭 (Deburr)
去膠渣 (Desmear)
化學銅 (PTH)
一次銅 Panel plating
☺ 目的:
使孔璧上的非導體部分之樹脂及玻璃纤維進行金屬化 方便進行後面之電鍍銅制程,完成足夠導電及焊接之金屬孔璧
PCB制程简介

PCB制程简介壹、PCB名词及源由:为「Printed Circuit Board」的简称,中文称为「印刷电路板」,也有人称为「PWB」(Printed Wiring Board)亦即「印刷线路板」。
顾名思意该产品是以印刷技术制作的电路产品。
在1940年代以前,电器产品以铜线配电的方式生产。
之后PCB 的蓬勃发展,使生产复制速度加快,产品体积得以缩小,方便性提升,单价降低。
貳、PCB制作的进化史:一、1936年以前以铜线配电或以金属融熔覆盖于绝缘板表面来制作PCB。
二、1936年以后将覆盖有金属的绝缘基板以耐蚀油墨作区域选别,将不要的区域以蚀刻的方法去除,这样的做法叫做“Subtractive Method”或“Print & Etch”。
三、1960年以后,电唱机/录音机/录像机等产品市埸,陆续采用了“双面贯通孔”的电路板制造技术,于是耐热及尺寸安定的“环氧树脂基板”被大量采用,至今仍为电路板制作的主要树脂基材。
參、PCB的应用:一、信息类:各类型计算机(如笔记型计算机、桌上型计算机)、显示器、列表机、扫瞄器等。
二、通讯类:行动电话、便携式传呼器、通讯网络系统、调制解调器等。
三、消费性产品类:电视机、录放机、电动玩具、收录音机、复印机等。
肆、PCB的种类:一、以层别划分可分为:1.单层板2.双面板:上下两面使用镀通孔导通。
3.多层板:a.贯穿孔 b.盲孔 c.埋孔。
二、以板材特性可分为:1.软板2.硬板:a.FR4 b.FR5…等。
三、以环保特性可分为:有卤素及无卤素板。
除以上各类别的划分外,又因有许多种特有的加工方法及特性的不同而可划分出许多种的种类如:喷锡、镀金、有机护铜(ENTEK)、增层板(Sequential)、高密度互连板(HDI)、薄板、阻抗控制板…等。
一、制作流程:二、制造流程:由于PCB制造流程相当的长,要有整体的概念就必须先以制造的目的,由浅入深来介绍相关的制程,才容易明了各制程的精髓。
pcb制程流程

PCB制程流程主要包括以下步骤:
裁板:将PCB基板裁剪成生产尺寸。
前处理:清洁PCB基板表面,去除表面污染物。
压膜:将干膜贴在PCB基板表层,为后续的图像转移做准备。
曝光:使用曝光设备利用紫外光对覆膜基板进行曝光,从而将基板的图像转移至干膜上。
DE:将进行曝光以后的基板经过显影、蚀刻、去膜,进而完成内层板的制作。
内检:检测及维修板子线路。
压合:将多个内层板压合成一张板子。
钻孔:按照客户要求利用钻孔机将板子钻出直径不同,大小不一的孔洞,使板子之间通孔以便后续加工插件,也可以帮助板子散热。
一次铜:为外层板已经钻好的孔镀铜,使板子各层线路导通。
外层:为方便后续工艺做出线路。
二次铜与蚀刻:二次镀铜,进行蚀刻。
以上步骤完成后,PCB制作流程基本完成。
PCB工艺流程说明

一.双面板工艺流程:覆铜板(CCL)下料(Cut)→钻孔(Drilling)→沉铜(PTH)→全板镀铜(Panel Plating)→图形转移(Pattern)油墨或干膜→图形电镀(Pattern plating)→蚀刻(Etch)→半检IQC→丝印阻焊油墨和字符油墨(SS)或贴阻焊干膜→热风整平或喷锡(HAL)→外形(Pounching)→成检(FQC)→电测试E-TEST→包装(Packaging)二.多层板工艺流程:内层覆铜板(CCL)铜箔(Copper Foil)下料(Cut)→内层图形制作(Inner-layer Pattern)→内层蚀刻(Inner-layer Etch)→内层黑氧化(Black-oxide)→层压or压合制程→钻孔(Drilling)→沉铜(PTH)→全板镀铜(Panel Plating)→外层蚀刻(Outer-layer Etch)→半检IQC→丝印阻焊油墨和字符油墨(SS)或贴阻焊干膜→热风整平或喷锡(HAL)→外形(Pounching)→成检(FQC)→电测试E-TEST→包装(Packaging)=三.流程说明:①下料:从一定板厚和铜箔厚度的整张覆铜板大料上剪出便于加工的尺寸,重量减少大约10-15%;②钻孔:在板上按电脑钻孔程序钻出导电孔或插件孔;板重量大约减少5%;③沉铜:在钻出的孔内沉积一层薄薄的化学铜,厚度大约在0。
3-2um,重量增加较少,目的是在不导电的环氧玻璃布基材(或其他基材)通过化学方法沉上一层铜,便于后面电镀导通形成线路;④全板镀铜:主要是为加厚保护那层薄薄的化学铜以防其在空气中氧化,形成孔内无铜或破洞;⑤图形制作(图形转移):包括内层图形制作,在板上贴上干膜或丝印上图形抗电镀油墨,经曝光,显影后,做出线路图形;重量减少较小。
⑥图形电镀:在已做好图形线路的板上进行线路加厚镀铜,使孔内和线路铜厚达到一定厚度,可以负载一定的电流;重量增加大约15%;⑦蚀刻:包括内层蚀刻,褪掉图形油墨或干膜,蚀刻掉多余的铜箔从而得到导电线路图形;⑧层压:把内层与半固化片,铜箔叠合一起经高温压制成多层板,4层板需要一张内层,两张铜箔;6层板需要两张内层,两张铜箔。
PCB电镀制程讲解(完整工艺介绍)

阳卢 俨 组槽道水舍生成Sn02舆纪的沉溅
物 物
SnCL-
8. 活化期 具有高鱼雷荷密度的锡纪廖髓,官能提供孔内所需的组 髓媒,而能舆化堕铜有具好且细致的括合肤况
þ
'
操作参敷及倏件 :
10. 化堕铜
是使程温前庭理后的板子得到孔内金属化效果的溶液
原理:
Pd主反雁:
Pd
þ
'
组崩媒的氧化渥原反腹式
'
'
硫酸
硫酸的主要作用是增加溶液的尊重性,硫酸的漉度 封镀液的分散能力和镀唐的楼械性能均有影警 . 硫酸渥 度太低,镀液分散能力下降,镀庸光亮范圄街小,硫酸漉 度太高,虽在然镀液分散能力较好,但镀唐的脆性降低,一
般担裂在 2()() 士 15g 门
氯离庄子
是隐植活化膏。,它可以需助铜隐撞正常溶解,首漉度低 于 20mg/L峙,舍崖生倏放粗糙镀盾,易出项主十孔和烧焦; 首漠度温高峙,镀屠光亮度下降,低琶济LE镀眉袭暗;如 果遇量 ,踢槌表面舍出现一屠白色膜,即赐植钝化, 一般 担裂在 20-80PPM
脱皮
屋生根源 :1.磨刷效果不佳服物、氧化、廖胁未除盏 2. 微触不足括合力不好 3. 板子在空氯中滴水暗固沮丧氧化最重
~理方式 :幸自靡
起泡
崖生根源 :1.煞琶铜液有罔崽 2. 基板吸有禁液或水氯
庭理方式 :微触重工或辍靡
拙别:ñ:tJ
铜渣
屋生根源 :1.铜球及PCB:f:卓缸 2. 隔植袋破损 3. 镀空斟
H 二次踊镀
PP;γfERN PLAT lNG
触 4」
.
梭查
INSPECTION
纫J 锡铅
TIL STRIPPING
PCB制造工艺流程
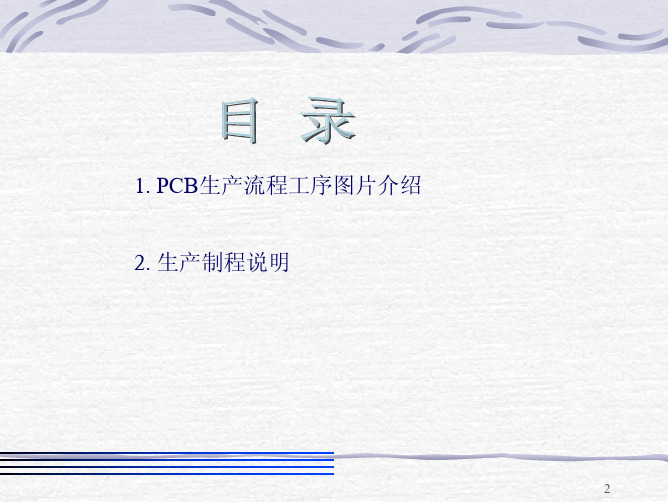
已钻孔 (Been Drilled)
QA检查 (QA Inspection )
下工序 (Next Process)
2
2.5钻孔
2.5.1流程说明
利用钻咀的高速旋转和落速,在PCB 板面加工出客户所需要的孔;线路板中孔主要用于 线路中元件面与焊接面及层与层之间的导通、IC引脚的插装;
1 1和2层之间导通
线路开短/路、线路缺口、干膜碎、偏位、线幼
8
1.6、图形电镀 &蚀刻 (Pattern Plating&Etching)
干膜板 (Finished Dry-film )
图形电镀 (Pattern Plating )
待蚀刻 (Finished Plating )
退膜 (Peeling Dry-film )
因此在蚀刻过程中,随着铜的溶解,应不断补充氨水和氯化铵。
2.3.2 控制要点 A、蚀刻:速度、温度(48-52℃)压力(1.2-2.5kg/cm2)
B、退膜:44-54℃ 8-12% NaOH溶液
2.3.3常见问题
蚀刻不净、蚀刻过度
7
1.2、压合 (Lamination)
开半固化片 (Pre-preg Cutting)
体。
盖板
压合叠板方式(如图)
牛皮纸
2.4.2控制要点
铜箔
A、棕化:各药水槽浓度、温度,
传送速度
B、压合:叠层结构、热压机参数 PP
钢板
2.4.3常见问题 棕化不良、压合白点、 滑板、板面凹痕
芯板
牛皮纸 底盘
1
1.3、钻孔 (Drilling)
待钻孔 (Waiting Drilling)
钻孔 (Drilling)
PCB工艺流程简介
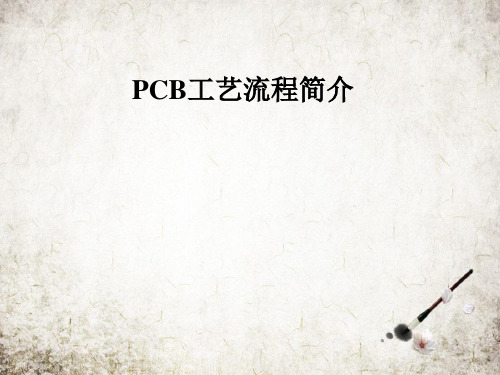
一次銅
☺ 流程介绍:
外层线路
前处理
压膜
曝光
显影
☺ 目的:
利用光化学原理,将线路图形通过以感光材料转形式移到 印制板上,形成一种抗蚀或抗电镀的掩膜图像。
外层线路
☺ 前处理(Pre-treatment):
制程目的:去除铜面上的污染物,增加铜面粗糙度,提高抗蚀或 抗电镀掩膜与板面的附着力。 主要设备:针刷磨板机 主要物料:刷轮
铜为2—4OZ的碱性直蚀板; AQ-3058:主要用于电厚镍金板。
外层线路
☺ 曝光(Exposure):
制程目的: 通过底片进行图形转移,在干膜上曝出客戶所需的线路图形。 主要设备:曝光机 主要物料:底片
➢ 外层所用底片与内层相反, 为负片,底片黑色为线路,白色 为底板(白底黑线) ➢ 白色的部分紫外光透射过去, 干膜发生聚合反应,不能被显 影液洗掉
重要的原物料:刷轮
除胶渣/化学沉铜/全板电镀
☺ 除胶渣(Desmear):
smear形成原因:鑽孔時造成的高溫超過玻璃化轉移溫度
(Tg值),而形成融熔狀,產生膠渣。
Desmear之目的:裸露出各層需互連的銅環,另膨松劑
可改善孔壁結構,增強電鍍銅附著力。
重要的原物料:KMnO4(除膠劑)
除胶渣/化学沉铜/全板电镀
☺ 目的:
将铜层厚度镀至客户所需求的厚度
镀锡
图形电镀
☺ 二次镀铜:
目的:將显影后的裸露 铜面的厚度加厚,以达到客 戶所要求的銅厚。 重要原物料:铜球、
电镀药水
乾膜
铜厚FA监控
二次銅
图形电镀
☺ 镀锡:
目的:在鍍完二次銅的 表面镀上一层锡保护,做为 蚀刻时的保护剂。 重要原物料:锡条、
全流程培训12

多层之内层工序介绍
内层制作工艺流程
Inner Board Cutting 内层开料
Baking Chemical Clean 焗板 化学清洗
Resists Lamination /Roller Coating 辘干膜/辘感光油
Exposure 曝光
DES 显影/蚀板
☺Inner Middle Inspection
步骤一:Developing(显影)
▪ 步骤二:Etching(蚀刻)
▪ 步骤三:Stripping(褪膜)
11
多层之内层工序介绍
内层蚀刻(DES)
步骤二:已完成蚀刻段的内层芯板(Core)
12
多层之内层工序介绍
蚀刻(ETCHING):
目的: ➢ 利用药液将显影后露出的
铜蚀掉,形成内层线路图 形 主要原物料:蚀刻药液 (CuCl2)
34
多层之层压工序介绍
3.4 铜箔
------压延铜箔是由铜锭经热压、韧化、刨削去垢
、
冷轧、连续轫化、酸洗、最后压延及脱脂干
燥等得到原始压延铜箔,再经粗化及防锈处
理后得到商品化的铜箔。
------电镀铜箔是将硫酸铜溶液在滚轮式的电镀槽
中于巨大滚轮表面镀得连续铜层,然后再经
粗化、耐热处理及防锈处理后得到商品化的
树脂+硬化剂+催化剂+柔化剂
A-Stage Varnish + 玻璃纤维布 适度烘烤
B-Stage半固化片 高温高压
C-Stage硬化树脂
29
多层之层压工序介绍
2.3 常见四层板结构 外压铜箔结构(Foil Construction)
- Foil
- Prepreg - Core(C/C) - Prepreg - Foil
PCB基本流程教材

PCB基本流程1. 多层板流程裁板(CT)→内层(DI)→压合(ML)→钻孔(NC)→电镀(CU)→外层(DF)→拒焊(KE)→文字(SM)→表面处理→成型(PN/RT)→电测(OS2)→外观检验(VI)→包装出货(PK)裁板(CT)CT→四个角做出倒角→板面喷墨做标记→(磨边)CT作用: 把大张原板裁切成working pnl size. 喷墨: 板面喷出工程号,批号,板厚,铜厚等. 磨边: 多层板,20mil以上的Core CT会安排磨边;双面板,若须磨边,由下一站(NC)自行安排磨边.注:因经向与纬向涨缩不一致,故Core与PP裁切时, 经纬向要一致内层(DI)作用:做出内层图形流程:前处理→压膜→曝光→显影→蚀刻→除胶→冲孔→AOIa.前处理:清洁&粗化铜面(有利于铜面与干/湿膜接触)b.压膜:压干膜或湿膜干膜比板子尺寸小一点,如板子尺寸16”,干膜则15.75”, 湿膜与板子一样大.c.对片曝光: 通过紫外线将底片上的图形转移到板面上对片:保证两内层底片的对准度对片曝光做法(1):手动对片曝光: 底片手动对位,手动放板(2):半自动曝光机: 底片机器自动对位,手动放板(3):自动曝光机: 底片机器自动对位,自动放板d.显影:目的: 把未聚合的干膜去除.e.蚀刻:将没有干膜盖住的铜蚀刻掉f.除胶:将铜面上聚合的干膜去掉.g.冲孔: 冲出后制程所需定位孔,如:1)AOI测试用的定位孔;2)压合定位孔等冲孔有以下三种方式:1)2CCD:抓取两短边中间之太阳PAD,对位OK后冲出压合用4组方Pin孔和铆合孔;2)8CCD:抓取长边共8个对位PAD,对位OK后冲出压合用4组方Pin孔和铆合孔;精度最高3)单轴CCD: 抓取宇资PAD,相应打出宇资 PAD对应位置的孔,即ML用的铆合孔h. AOI: 自动光学检验, 根据光学检验来判断板子的缺陷.补充:a. 蚀刻因子:是指正蚀刻深度与侧蚀凹度的比值蚀刻因子在蚀刻中是一个十分重要的数值,蚀刻因子越高,线路的实影虚影的宽度就越接近,则蚀刻的品质就越好.b. 水池效应水池效应是指在板子的板面上,蚀刻液在板边的流动比中间好,中间部份的蚀刻药液不能及时的流动而滞流在板子中间,这样中间部份新鲜的蚀刻液不能及时咬蚀铜面,使中间的铜被咬蚀量比板边差的现象压板(ML)1.3.1作用: 保证内层Thin Core对准度情况下,将Thin Core、PP、外层铜箔压合在一起,做成多层板1.3.2 流程:黑氧化/棕化内层基板→铆合/叠合→压板→拆板1.3.2.1 黑/棕化作用: a.粗化铜面, 增加与树脂的结合力 b.形成的氧化面阻止铜面与树脂里的固化剂Dicy反应产生水汽.选择黑/棕化是由PP材质决定. 根据板子的结合力,黑化比棕化好.1.3.2.2 铆合/PIN定位i).使层与层之间定位,达到层与层对位精度ii).依照设计叠法完成板子的叠法组合铆合/PIN定位方式:(1).手动铆合:利用冲孔冲出的铆合孔打铆钉. (2).自动铆合:利用内层冲孔冲出的4个方位孔定位,可以任意选择位置打铆钉.(3).热铆:利用内层冲孔的4个方位孔定位,将热铆PAD加热. (4). PIN定位: 直接用PIN定位压合.1.3.2.3 压合压合方式:OEM,PINLAM,ADARA,仓压.其中仓压主要用于做HEATSINK 板. PINLAM:用PIN定位,叠合后再压合.OEM:经铆合,点胶,叠合后再压合.ADARA压合:热压:加热,加压冷压:释放应力.1.3.2.4拆板: 完成板子与治具的分离NC1.4.1.作用: 钻孔,捞边,打地球孔,测板厚等1.4.2.流程多层板: ML→铣流胶→双轴X-Ray打定位孔→捞边→磨边→测板厚→钻孔→ CUa. 铣流胶: 铣掉ML后方pin孔口之流胶(限于Pin-lam流程);b. 双轴X-RAY打定位孔﹕依照内层钻出捞边&钻孔之定位孔﹐并可以精确测量内层缩拉之数据;c. 捞边﹕去除ML后板边流胶,铜箔,捞出外层作业外形;d. 磨边﹕去除板边锋利边角﹐方便后制程作业;e. 测板厚﹕测量板厚是否在规格内﹐是否有叠错PP/内层;f. NC钻孔﹕根据客户设计之孔位, 孔径作出钻孔程式后,由电脑钻床依据程式钻孔于覆铜板上双面板: (磨边)→短边打出定Pin孔→钻孔注:厚的板子NC要磨边,如63mil以上. 薄的不用磨边。
- 1、下载文档前请自行甄别文档内容的完整性,平台不提供额外的编辑、内容补充、找答案等附加服务。
- 2、"仅部分预览"的文档,不可在线预览部分如存在完整性等问题,可反馈申请退款(可完整预览的文档不适用该条件!)。
- 3、如文档侵犯您的权益,请联系客服反馈,我们会尽快为您处理(人工客服工作时间:9:00-18:30)。
PCB流程简介-全制程
1. 前言
PCB(Printed Circuit Board),即印刷电路板,是电子产品中不可缺少的重要组成部分之一。
PCB流程是指制作PCB的全过程,包括原料采购、设计、布局、制版、生产、组装和测试等多个环节。
本文将对PCB流程进行全面的简介和介绍。
2. PCB制作流程
PCB制作流程可以大致分为如下几个步骤:
2.1. 原料采购
在PCB制作流程中,原料采购是一个至关重要的环节。
常见的PCB 制作所需原材料包括电路板基材、薄铜箔、印刷墨水等。
在采购时需要注意选择高质量的原材料供应商,并对原料进行严格的质量检验。
2.2. 设计和布局
PCB设计是整个流程中重要的阶段之一。
在这个阶段,设计师会使用专业的电路设计软件,根据电子产品的功能要求和电路原理图进行PCB电路板的设计和布局。
设计师需要考虑电路板的大小、层次、电路连接、电源布局等因素,并与其他硬件模块进行兼容性和接口匹配的设计。
2.3. 制版
制版是将PCB设计文件转化成实际可用的制板文件的过程。
在这个阶段,设计师会将PCB设计文件输出为Gerber文件,并将Gerber文件发送给制板厂家。
制板厂家会根据Gerber文件进行图形的翻版和制版,最终得到制版后的电路板。
2.4. 生产和组装
生产和组装是将制版的电路板进行生产和组装的过程。
在这个阶段,制板厂家会采用先进的生产工艺和设备,将电路板上的电子元器件和
连接线进行焊接和组装。
生产和组装的目标是将电路板上的各个元器
件正确地安装到预定位置,并确保电路板的良好连接和可靠性。
2.5. 测试和质检
测试和质检是确保PCB质量和性能的关键环节。
在这个阶段,制板厂家会进行全面的测试和质检,包括电气测试、可靠性测试和功能测
试等。
只有通过了严格的测试和质检,才能确保PCB的质量和可靠性。
3. PCB制作的注意事项
在PCB制作流程中,需要注意以下几个重要的事项:
3.1. 设计准则
在进行PCB设计和布局时,应遵循一些设计准则,如规避电源干扰、保持信号完整性、合理布局元器件和线路等。
设计师需要熟悉这些准则,并在设计过程中充分考虑它们。
3.2. 质量控制
质量控制是确保PCB质量和性能的关键环节。
制板厂家应采用先进的生产工艺和设备,并建立完善的质量控制体系,确保产品质量符合
规范和客户要求。
3.3. 环境保护
在PCB制作过程中,需要注意环境保护和资源节约。
制板厂家应合
法排放废水和废气,并采取有效措施以减少对环境的污染和损害。
3.4. 法规合规
PCB制作涉及到一系列法规和标准,如RoHS指令、REACH法规等。
制板厂家应遵守相关法规和标准,确保产品合规性并提供相应的合规
报告。
4. 结语
PCB流程是制作PCB的全过程,包括原料采购、设计和布局、制版、生产和组装、测试和质检等多个环节。
PCB制作需要遵循一定的设计
准则、质量控制、环境保护和法规合规要求。
通过合理的PCB流程和
严格的质量管理,可以确保PCB产品的质量和可靠性。